- 1Department of Materials and Polymer Engineering, Faculty of Engineering, Hakim Sabzevari University, Sabzevar, Iran
- 2Institute of Fundamental Technological Research, Polish Academy of Sciences, Warsaw, Poland
- 3Chemical Engineering Department, Faculty of Petroleum and Petrochemical Engineering, Hakim Sabzevari University, Sabzevar, Iran
- 4Material Science Division, Department of Engineering Sciences and Mathematics, Luleå University of Technology, Luleå, Sweden
- 5Centre for Nanofibers and Nanotechnology, Department of Mechanical Engineering, National University of Singapore, Singapore, Singapore
Among the different polymeric membranes, electrospun membranes have shown promising performance for filtration applications through the facile and controlled preparation method leading to tailored material structure. Furthermore, multilayered bio-based electrospun membranes exhibited superior filtration performance, considering they are eco-friendly with superior mechanical properties and better adsorption efficiency compared to the single-layered electrospun membranes. The aim of this mini-review is to reveal the current state-of-art development of multilayered bio-based electrospun membranes and to provide new insights into the future of tailored membranes toward practical applications.
Introduction
The rapid development of industries has led to particulate matter pollution that poses serious threats to the global environment, resources, and public health. Polymeric membranes are attracting attention for their efficient filtration of pollutants and microorganisms from many resources such as water, air, food, and microbiological fluids because of their high mechanical strength, their chemical, thermal, and corrosion resistance, and their minimal production of harmful by-products (Gandavadi et al., 2019; Lv et al., 2019; Ma et al., 2019a). Among the different polymeric membranes, bio-based polymers, i.e., cellulose nanofibers (CNFs), cellulose nanocrystals (CNCs), chitosan, and protein-based nanofibers, all gleaned from renewable resources, have shown superior performance during the filtration of water and microbiological fluids (Charcosset, 2012; Lv et al., 2018). Bio-based membranes have been developed and adopted to overcome the drawbacks of conventional polymeric materials. Additionally, they offer better production rates, more efficient adsorption, and greater potential in filtration performance. Several bio-based polymers have been employed and investigated for filtration purposes in pristine nature or after some modification, such as grafting, blending, and using custom-tailored copolymers in order to enhance the membrane performance. Bio-based polymers, such as poly(vinyl alcohol) (PVA), cellulose acetate (CA), polylactic acid (PLA), poly(glycolic acid), and chitosan, have been studied, since these polymers are eco-friendly, biocompatible and biodegradable, and have higher hydrophilicity and consequently lower membrane fouling features (Ma et al., 2011a; Sencadas et al., 2012; Mi et al., 2014; Wei et al., 2014).
Various methods such as casting technologies, interfacial polymerization, phase inversion, controlled stretching of thin polymeric films, and electrospinning are used to produce both dense and porous membranes. The porous membranes are normally categorized based on their average pore size. The pore size ranges from 0.1 to 5 μm in microfiltration (MF) for the removal of particles such as bacteria and protozoa, and between 0.01 and 0.1 μm in ultrafiltration (UF) membranes for the eradication of proteins, viruses, colloids, and emulsified oils. Furthermore, nanofiltration (NF) and reverse osmosis (RO) membranes are used for the removal of particles in the range of 1–10 nm and 0.1–1 nm, respectively (Suja et al., 2017). Figure 1A schematically shows the pore size ranges of MF, UF, NF, and RO processes. Among the methods for fabrication of porous polymeric membranes, electrospinning is one of the easiest and most cost-efficient techniques to produce fibrous membranes with a wide range of fiber diameter and porosity for the filtration of polluted water, air, considering the ability for bactericidal activity and dye scavenging (Lv et al., 2018; Ma et al., 2019b). Although the electrospun fibrous membranes offer a highly porous non-woven structure, making them suitable for MF, UF, and even NF, they usually exhibit poor mechanical strength due to weak fiber–fiber connections via physical entanglements. Furthermore, the biofouling issues are another drawback of electrospun membranes. Several approaches such as nanomaterial incorporation (Vijay Kumar et al., 2019), as well as surface chemistry manipulation or using bio-based polymers (Liu Z. et al., 2019; Lv et al., 2019; Zhu et al., 2019), have been investigated to address the aforementioned shortcomings. Multilayered electrospun membranes have been proposed to facilitate the combination of electrospun nanofibers with bio-based nanoparticles and nanowhiskers to overcome such obstacles (Qin and Wang, 2008).
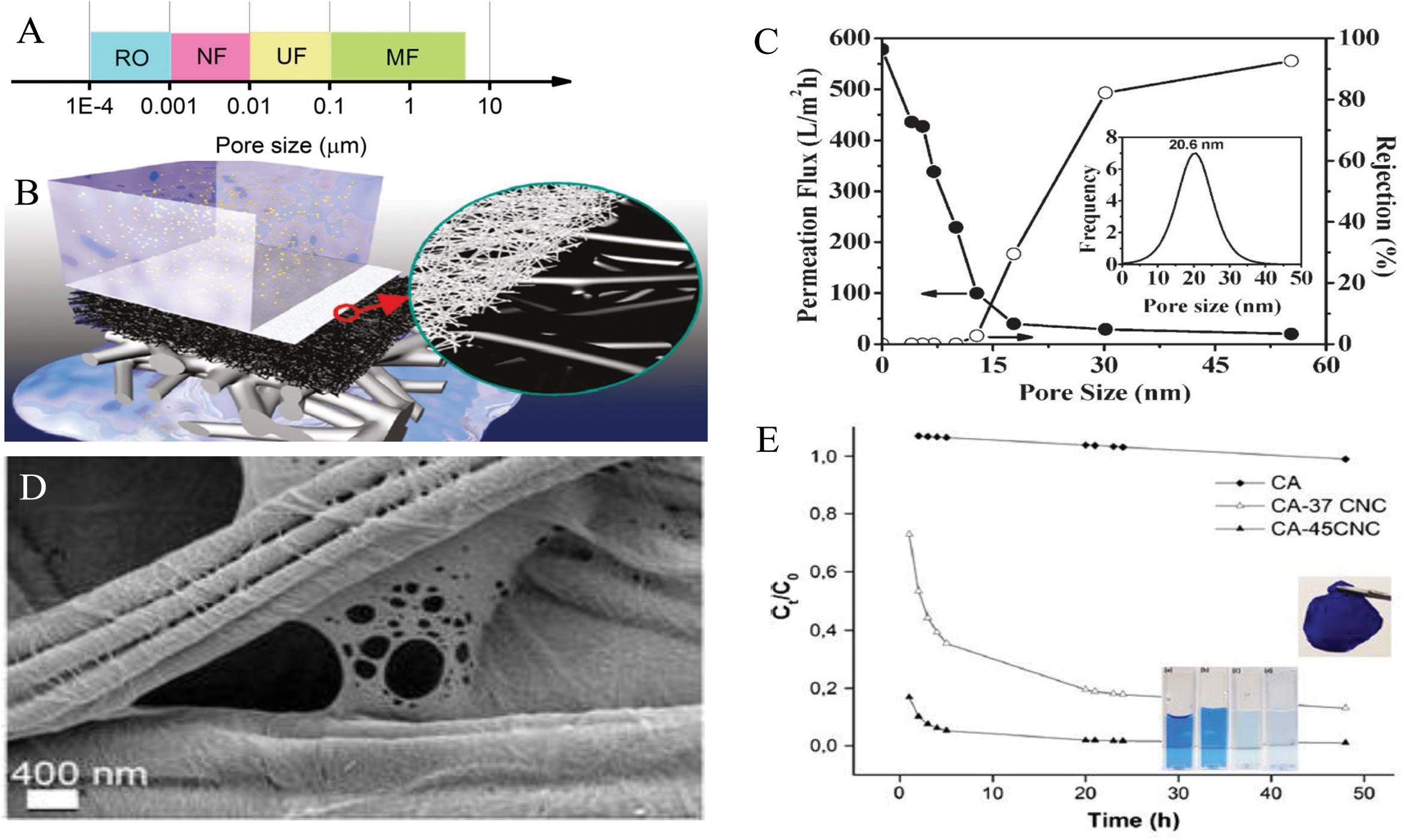
Figure 1. (A) The pore sizes of MF, UF, NF, and RO processes. (B) Schematic illustration of the three-layered fibrous membrane, and (C) its filtration performance (Ma et al., 2011b), reproduced with permission from the American Chemical Society. (D) The SEM image of the electrospun CA nanofibers coated by CNCs, and (E) its filtration performance as a function of CNC content during the time (Goetz et al., 2018), reproduced under the terms of the Creative Commons Attribution (CC BY 3.0) license.
Multilayered fibrous membranes are usually composed of various layers, where each layer is separately fabricated to designed pore size and desired surface characteristics. The first layer is usually prepared in a way to perform pre-filtration and provide high mechanical strength during the high flux filtration. On the other hand, the pore size and adsorption selectivity of the next layers are designed based on the application (Liu X. et al., 2019). Furthermore, deposition of the functionalized nanomaterials, on the mid or top layer, provides efficient adsorption performance to eliminate contaminants such as bacteria, viruses, heavy metal ions, dyes, and toxins (Karim et al., 2017; Araga and Sharma, 2019). The past few decades attempted to industrialize the electrospinning technique as the most versatile method for the production of nanofibrous networks. However, the goal still remains to be achieved. Taking into account the practical applications, weak mechanical performance is a serious obstacle that is yet to be overcome. In general, as a result of the incomplete orientation of polymeric chains along the fiber axis, tensile strength and Young’s modulus of non-woven electrospun mats do not exceed 300 MPa and 3 GPa, respectively (Yao et al., 2014). Due to insufficient strength, there is a high risk for the users in the case of filter splitting. Filter split would also lead to the shortening of the functionality of the membrane, which would be economically detrimental (Zhu et al., 2017).
An ISI Web of Science literature search revealed that several review articles have been published on the development of single-layered electrospun membranes for filtration applications (Suja et al., 2017; Zhu et al., 2017; Nabeela Nasreen et al., 2019). However, these studies neither focus on state-of-art multilayered membranes nor on bio-based electrospun membranes. Therefore, the current mini-review is directed toward tailored pore size and size distribution in the electrospun membranes and the recent developments in the two- and three-layer bio-based nanofibrous membranes.
Tailored Membrane Structure for Filtration Application
Electrospun nanofibers have attracted substantial attention in numerous applications such as filtration (Bassyouni et al., 2019), tissue engineering (Kouhi et al., 2019), wound dressing (Rezvani Ghomi et al., 2019), encapsulation for drug delivery operation (Ranjbar-Mohammadi et al., 2016), and self-healing (Neisiany et al., 2017), because of their facile and cost-efficient fabrication method and special features (Mohammadzadehmoghadam and Dong, 2019). Electrospinning offers versatile production of fibers with diameters in the order of 10 nanometers to several micrometers from a variety of raw materials (Kumar et al., 2019). Moreover, electrospun membranes have several advantages for filtration application due to their high amount of porosity (approximately 80%), including both open and interconnected pore structures and high specific surface area. The classic electrospinning setup involves a high voltage power source, a syringe pump to precisely feed the polymer solution, a grounded collector, an electrically conductive spinneret, and a polymer solution to be electrospun. While the process looks simple, the electro-hydrodynamic and rheological interactions make it complicated (Lee et al., 2018). The processing parameters (such as the applied voltage, feed rate, and air gap) as well as polymer solution parameters (such as concentration, conductivity, and viscosity of solution, molecular weight of the polymer, and solvent evaporation characteristics), and environmental parameters (temperature and humidity) deterministically dictate the spinnability and the prepared fiber characteristics (Huang et al., 2003).
In the case of MF, UF, and NF, the pore size of the membrane controls the filtration performance. Ma et al. (2011a) showed that for a randomly oriented electrospun nanofiber mat, when the membrane porosity was constantly kept at ca. 80 vol%, the pore size of the nanofibrous membrane had a precise correlation with the diameter of the electrospun fibers. The authors reported the average pore size of the nanofibrous membranes to be ca. 3 ± 1 times the nanofiber average diameter. Furthermore, the maximum pore size of the nanofibrous membrane was ca. 10 ± 2 times the nanofiber average diameter (Ma et al., 2011a). Therefore, with simple alteration of the electrospinning effective parameters (e.g., solution and operation parameters), a wide range of average nanofiber diameter and consequently pore size can be designed and obtained.
Additionally, specific molecule or ligand immobilization onto the membrane surfaces leads to affinity membranes with selectively captured targeted molecules for use in technologically advanced processes such as membrane filtration and fixed-bed liquid chromatography (Park et al., 2007; Esmaeely Neisiany et al., 2020). This immobilization allows for the purification of molecules according to the differences in biological functions or physical/chemical properties rather than molecular size (Ma et al., 2006). Several ligands, proteins, and enzymes were immobilized on a broad range of biodegradable electrospun polymers (such as PVA, PGA, and PLA) depending on the requirement. An affinity membrane that simultaneously combines size-based filtration and high selectivity is now an attractive approach for purifying and filtering biological fluids (Fu et al., 2018; Ng et al., 2019).
Layered Electrospun Nanofibrous Membranes
As discussed in the section “Tailored Membrane Structure for Filtration Application,” electrospun membranes have some limitations, including low mechanical properties and thermal and chemical stability (Barhate and Ramakrishna, 2007). To overcome these drawbacks, the addition of different nanomaterials into the spinning solution has been widely tested (Enayati et al., 2019). However, the addition of a high volume of reinforcing fibers creates difficulties in the electrospinning process and significantly decreases the properties of the prepared nanofibers (Naseri et al., 2015). Therefore, multilayered electrospun membranes were proposed as a potential alternative for the easier combination of electrospun nanofibers with bio-based nanoparticles and nanowhiskers to address the above-mentioned shortcomings, i.e., low mechanical strength and fouling. Figure 1B schematically presents a three-layered fibrous membrane (including a supporting layer), which usually consists of conventional microfibers, an electrospun mid-layer, and a top barrier layer. Figure 1C presents the filtration performance of this membrane, which is composed of microfibers, electrospun nanofibers, and CNFs as a top barrier layer (Ma et al., 2011b). Comprehensive research on the development of multilayered electrospun membranes has been carried out by Hadi et al. (2019) at Stony Brook University in the United States. Most of the researches have employed non-biodegradable polymers such as polyacrylonitrile (PAN), polyvinylidene fluoride (PVDF), and polysulfone (PSU) (Díez et al., 2018). Goetz et al. (2018) at Luleå University of Technology in Sweden, and Zhao et al. (2019) in China investigated the development of fully bio-based multilayered electrospun membranes, which were subsequently reviewed. However, most of the research on multilayered electrospun membranes has been based on the combination of synthesized and bio-based polymers. These types of membranes for air filtration were comprehensively reviewed by the Huang group (Zhu et al., 2017; Lv et al., 2018). Table 1 summarizes the details of the reported multilayered membranes composed of synthesized, poly (ethylene terephthalate) (PET) and PAN, and bio-based polymers.
Goetz et al. (2018) infused chitin nanocrystals onto the electrospun CA mesofibers. The prepared hierarchical structure showed a wide range of pore sizes due to the combination of electrospun CA mesofibers (fiber diameter of 0.5–3.3 μm) and chitin nanocrystals (diameter of 10–30 nm). This led to the development of multilayered biodegradable membranes with 10 nm pore sizes. The incorporation of the chitin nanocrystals at the junction points of the electrospun CA mesofibers increased the mechanical strength and modulus of the two-layered membranes by 131 and 340%, respectively, compared to single-layered CA electrospun mesofibers. Furthermore, the hydrophobic nature of the CA mats changed to super hydrophilic upon incorporation of the chitin nanocrystals. This consequently decreased biofilm formation and abiotic fouling significantly. The prepared multilayered biodegradable membrane showed potential in MF of biological and organic contaminants from the water.
Recently, Nair and Mathew (2017) reported a combination of electrospinning and electrospraying techniques to fabricate a bilayer composite membrane based on the electrospun CA membrane coated by CNCs for cationic dye adsorption. The authors showed that the combination of electrospinning and electrospraying improved the availability of the CNCs on the surfaces of the electrospun CA nanofibers compared to the embedding of CNCs into the electrospun solution. This consequently enabled efficient dye adsorption due to higher surface area. Elsewhere, Goetz et al. (2018) developed a layered membrane structure wherein electrospun CA nanofibers were impregnated with several concentrations of CNCs. Figure 1D displays the SEM micrograph of the CA nanofibers coated by CNCs. It can be observed that a wide range of porosities was induced after the coating of the electrospun CA nanofibrous membrane by a very fine CNC layer (diameter of 5–10 nm). The hierarchical structure considerably enhanced the mechanical properties, surface area, hydrophilicity, and filtration performance of the membrane, compared to the neat CA electrospun nanofibrous membrane. The filtration performance of the membrane substantially increased by the incorporation of CNC and increasing the CNC content, as well (Figure 1E).
Zhao et al. (2019) created a fully bio-based three-layered electrospun membrane via electrospinning of poly(3-hydroxybutyrate-co-3-hydroxyvalerate) (PHBV) and CA, followed by the casting of chitosan. PHBV was selected as a fibrous substrate due to its good biodegradability and spinnability. Since PHBV fibers were not fine enough to provide the filtration demand, they were covered by electrospun CA nanofibers as a mid-fibrous supporting layer. The prepared two-layered electrospun membranes, with different fiber diameters, introduced a high porosity and interconnected pores, while the chitosan top barrier layer, prepared via the phase inversion technique, and improved the rejection ratio of the membrane. Furthermore, the chitosan functional groups improved the membrane efficiency by adsorbing metal ions or other contaminants from water.
Conclusion and Future Insights
The development of multilayered electrospun membranes offers an opportunity for filtration applications, including MF, UF, NF, RO, and FO, as well as adsorption of heavy metal ions. The high porosity of the electrospun layer (approximately 80%) offers higher flux, reducing the energy consumption, in comparison with conventional membranes. On the other hand, incorporation of nanosized biomaterials such as cellulose, with an average diameter of 5–10 nm, yields a wide pore size distribution for capturing very fine particles, even with 30 nm diameters. In addition, the hydrophilic nature of cellulose considerably decreases the fouling of the membrane and makes it more biocompatible and biodegradable. However, more research is required to develop a fully biodegradable multilayer electrospun membrane with a wide range of pore sizes. Besides the PVA, CA, and chitosan, other bio-based polymers can be investigated for the fabrication of the electrospun nanofibrous layers with specific applications. From the economic point of view, it is required to exploit other cost-efficient nanofiber fabrication approaches, particularly in preparing tailored nanofibers, such as solution blowing, co-axial electrospinning, and centrifugal spinning. This will consequently address the concerns of the various industries regarding the development of low-cost, non-toxic, and environmentally friendly nanofibrous membranes. Finally, it would be necessary to comprehensively explore the filtration performance of such electrospun membranes and address the global concerns on widespread air polluting sources.
Author Contributions
RN, ME, AK-B, and OD summarized the literature and wrote a major part of the manuscript. OD and SR conducted the deep review, editing, guidance, and supervision. All authors have read and approved the article for publication.
Conflict of Interest
The authors declare that the research was conducted in the absence of any commercial or financial relationships that could be construed as a potential conflict of interest.
References
Araga, R., and Sharma, C. S. (2019). Amine functionalized electrospun cellulose nanofibers for fluoride adsorption from drinking water. J. Polym. Environ. 27, 816–826. doi: 10.1007/s10924-019-01394-2
Barhate, R. S., and Ramakrishna, S. (2007). Nanofibrous filtering media: filtration problems and solutions from tiny materials. J. Membr. Sci. 296, 1–8. doi: 10.1016/j.memsci.2007.03.038
Bassyouni, M., Abdel-Aziz, M. H., Zoromba, M. S., Abdel-Hamid, S. M. S., and Drioli, E. (2019). A review of polymeric nanocomposite membranes for water purification. J. Ind. Eng. Chem. 73, 19–46. doi: 10.1016/j.jiec.2019.01.045
Charcosset, C. (2012). “1 - Principles on membrane and membrane processes,” in Membrane Processes in Biotechnology and Pharmaceutics, ed. C. Charcosset (Amsterdam: Elsevier), 1–41. doi: 10.1016/b978-0-444-56334-7.00001-0
Díez, B., Amariei, G., and Rosal, R. (2018). Electrospun composite membranes for fouling and biofouling control. Ind. Eng. Chem. Res. 57, 14561–14570. doi: 10.1021/acs.iecr.8b04011
Enayati, M. S., Neisiany, R. E., Sajkiewicz, P., Behzad, T., Denis, P., and Pierini, F. (2019). Effect of nanofiller incorporation on thermomechanical and toughness of poly (vinyl alcohol)-based electrospun nanofibrous bionanocomposites. Theor. Appl. Fract. Mech. 99, 44–50. doi: 10.1016/j.tafmec.2018.11.006
Esmaeely Neisiany, R., Enayati, M. S., Sajkiewicz, P., Pahlevanneshan, Z., and Ramakrishna, S. (2020). Insight into the current directions in functionalized nanocomposite hydrogels. Front. Mater. 7:25. doi: 10.3389/fmats.2020.00025
Fu, Q., Duan, C., Yan, Z., Si, Y., Liu, L., Yu, J., et al. (2018). Electrospun nanofibrous composite materials: a versatile platform for high efficiency protein adsorption and separation. Compos. Commun. 8, 92–100. doi: 10.1016/j.coco.2017.11.007
Gandavadi, D., Sundarrajan, S., and Ramakrishna, S. (2019). Bio-based nanofibers involved in wastewater treatment. Macromol. Mater. Eng. 304:1900345. doi: 10.1002/mame.201900345
Goetz, L. A., Naseri, N., Nair, S. S., Karim, Z., and Mathew, A. P. (2018). All cellulose electrospun water purification membranes nanotextured using cellulose nanocrystals. Cellulose 25, 3011–3023. doi: 10.1007/s10570-018-1751-1
Hadi, P., Yang, M., Ma, H., Huang, X., Walker, H., and Hsiao, B. S. (2019). Biofouling-resistant nanocellulose layer in hierarchical polymeric membranes: synthesis, characterization and performance. J. Membr. Sci. 579, 162–171. doi: 10.1016/j.memsci.2019.02.059
Huang, Z.-M., Zhang, Y. Z., Kotaki, M., and Ramakrishna, S. (2003). A review on polymer nanofibers by electrospinning and their applications in nanocomposites. Compos. Sci. Technol. 63, 2223–2253. doi: 10.1016/s0266-3538(03)00178-7
Karim, Z., Hakalahti, M., Tammelin, T., and Mathew, A. P. (2017). In situ TEMPO surface functionalization of nanocellulose membranes for enhanced adsorption of metal ions from aqueous medium. RSC Adv. 7, 5232–5241. doi: 10.1039/c6ra25707k
Kouhi, M., Jayarama Reddy, V., Fathi, M., Shamanian, M., Valipouri, A., and Ramakrishna, S. (2019). Poly (3-hydroxybutyrate-co-3-hydroxyvalerate)/fibrinogen/bredigite nanofibrous membranes and their integration with osteoblasts for guided bone regeneration. J. Biomed. Mater. Res. A 107, 1154–1165. doi: 10.1002/jbm.a.36607
Kumar, M., Hietala, M., and Oksman, K. (2019). Lignin-based electrospun carbon nanofibers. Front. Mater. 6:62. doi: 10.3389/fmats.2019.00062
Lee, J. K. Y., Chen, N., Peng, S., Li, L., Tian, L., Thakor, N., et al. (2018). Polymer-based composites by electrospinning: preparation & functionalization with nanocarbons. Prog. Polym. Sci. 86, 40–84. doi: 10.1016/j.progpolymsci.2018.07.002
Liu, X., Ma, H., and Hsiao, B. S. (2019). Interpenetrating nanofibrous composite membranes for water purification. ACS Appl. Nano Mater. 2, 3606–3614. doi: 10.1021/acsanm.9b00565
Liu, Y., Wang, R., Ma, H., Hsiao, B. S., and Chu, B. (2013). High-flux microfiltration filters based on electrospun polyvinylalcohol nanofibrous membranes. Polymer 54, 548–556. doi: 10.1016/j.polymer.2012.11.064
Liu, Z., Ma, W., Zhang, M., Zhang, Q., Xiong, R., and Huang, C. (2019). Fabrication of superhydrophobic electrospun polyimide nanofibers modified with polydopamine and polytetrafluoroethylene nanoparticles for oil–water separation. J. Appl. Polym. Sci. 136:47638. doi: 10.1002/app.47638
Lv, D., Wang, R., Tang, G., Mou, Z., Lei, J., Han, J., et al. (2019). Ecofriendly electrospun membranes loaded with visible-light-responding nanoparticles for multifunctional usages: highly efficient air filtration, dye scavenging, and bactericidal activity. ACS Appl. Mater. Interfaces 11, 12880–12889. doi: 10.1021/acsami.9b01508
Lv, D., Zhu, M., Jiang, Z., Jiang, S., Zhang, Q., Xiong, R., et al. (2018). Green electrospun nanofibers and their application in air filtration. Macromol. Mater. Eng. 303:1800336.
Ma, H., Burger, C., Hsiao, B. S., and Chu, B. (2011a). Ultra-fine cellulose nanofibers: new nano-scale materials for water purification. J. Mater. Chem. 21, 7507–7510.
Ma, H., Burger, C., Hsiao, B. S., and Chu, B. (2011b). Ultrafine polysaccharide nanofibrous membranes for water purification. Biomacromolecules 12, 970–976. doi: 10.1021/bm1013316
Ma, W., Ding, Y., Zhang, M., Gao, S., Li, Y., Huang, C., et al. (2019a). Nature-inspired chemistry toward hierarchical superhydrophobic, antibacterial and biocompatible nanofibrous membranes for effective UV-shielding, self-cleaning and oil-water separation. J. Hazardous Mater. 384:121476. doi: 10.1016/j.jhazmat.2019.121476
Ma, W., Zhang, M., Liu, Z., Kang, M., Huang, C., and Fu, G. (2019b). Fabrication of highly durable and robust superhydrophobic-superoleophilic nanofibrous membranes based on a fluorine-free system for efficient oil/water separation. J. Membr. Sci. 570-571, 303–313. doi: 10.1016/j.memsci.2018.10.035
Ma, Z., Masaya, K., and Ramakrishna, S. (2006). Immobilization of Cibacron blue F3GA on electrospun polysulphone ultra-fine fiber surfaces towards developing an affinity membrane for albumin adsorption. J. Membr. Sci. 282, 237–244. doi: 10.1016/j.memsci.2006.05.027
Mi, X., Vijayaragavan, K. S., and Heldt, C. L. (2014). Virus adsorption of water-stable quaternized chitosan nanofibers. Carbohyd. Res. 387, 24–29. doi: 10.1016/j.carres.2014.01.017
Mohammadzadehmoghadam, S., and Dong, Y. (2019). Fabrication and characterization of electrospun silk fibroin/gelatin scaffolds crosslinked with glutaraldehyde vapor. Front. Mater. 6:91. doi: 10.3389/fmats.2019.00091
Nabeela Nasreen, A. S., Sundarrajan, S., Syed Nizar, A. S., and Ramakrishna, S. (2019). Nanomaterials: solutions to water-concomitant challenges. Membranes 9:40. doi: 10.3390/membranes9030040
Nair, S. S., and Mathew, A. P. (2017). Porous composite membranes based on cellulose acetate and cellulose nanocrystals via electrospinning and electrospraying. Carbohyd. Polym. 175, 149–157. doi: 10.1016/j.carbpol.2017.07.048
Naseri, N., Mathew, A. P., Girandon, L., Fröhlich, M., and Oksman, K. (2015). Porous electrospun nanocomposite mats based on chitosan–cellulose nanocrystals for wound dressing: effect of surface characteristics of nanocrystals. Cellulose 22, 521–534.
Neisiany, R. E., Lee, J. K. Y., Khorasani, S. N., and Ramakrishna, S. (2017). Towards the development of self-healing carbon/epoxy composites with improved potential provided by efficient encapsulation of healing agents in core-shell nanofibers. Polym. Test. 62, 79–87.
Ng, I. S., Song, C. P., Ooi, C. W., Tey, B. T., Lee, Y.-H., and Chang, Y.-K. (2019). Purification of lysozyme from chicken egg white using nanofiber membrane immobilized with Reactive Orange 4 dye. Int. J. Biol. Macromol. 134, 458–468. doi: 10.1016/j.ijbiomac.2019.05.054
Park, K., Ju, Y. M., Son, J. S., Ahn, K.-D., and Han, D. K. (2007). Surface modification of biodegradable electrospun nanofiber scaffolds and their interaction with fibroblasts. J. Biomater. Sci. Polym. Ed. 18, 369–382.
Qin, X.-H., and Wang, S.-Y. (2008). Electrospun nanofibers from crosslinked poly(vinyl alcohol) and its filtration efficiency. J. Appl. Polym. Sci. 109, 951–956.
Ranjbar-Mohammadi, M., Zamani, M., Prabhakaran, M. P., Bahrami, S. H., and Ramakrishna, S. (2016). Electrospinning of PLGA/gum tragacanth nanofibers containing tetracycline hydrochloride for periodontal regeneration. Mater. Sci. Eng. C 58, 521–531. doi: 10.1016/j.msec.2015.08.066
Rezvani Ghomi, E., Khalili, S., Nouri Khorasani, S., Esmaeely Neisiany, R., and Ramakrishna, S. (2019). Wound dressings: current advances and future directions. J. Appl. Polym. Sci. 136:47738.
Sencadas, V., Correia, D. M., Ribeiro, C., Moreira, S., Botelho, G., Gómez Ribelles, J. L., et al. (2012). Physical-chemical properties of cross-linked chitosan electrospun fiber mats. Polym. Test. 31, 1062–1069.
Suja, P. S., Reshmi, C. R., Sagitha, P., and Sujith, A. (2017). Electrospun nanofibrous membranes for water purification. Polym. Rev. 57, 467–504.
Tang, Z., Wei, J., Yung, L., Ji, B., Ma, H., Qiu, C., et al. (2009). UV-cured poly(vinyl alcohol) ultrafiltration nanofibrous membrane based on electrospun nanofiber scaffolds. J. Membr. Sci. 328, 1–5.
Vijay Kumar, V., Ramakrishna, S., Kong Yoong, J. L., Esmaeely Neisiany, R., Surendran, S., and Balaganesan, G. (2019). Electrospun nanofiber interleaving in fiber reinforced composites—Recent trends. Mater. Des. Process. Commun. 1:e24.
Wang, X., Yeh, T.-M., Wang, Z., Yang, R., Wang, R., Ma, H., et al. (2014). Nanofiltration membranes prepared by interfacial polymerization on thin-film nanofibrous composite scaffold. Polymer 55, 1358–1366.
Wang, Z., Ma, H., Chu, B., and Hsiao, B. S. (2017). Fabrication of cellulose nanofiber-based ultrafiltration membranes by spray coating approach. J. Appl. Polym. Sci. 134:44583.
Wei, Z., Zhao, H., Zhang, J., Deng, L., Wu, S., He, J., et al. (2014). Poly(vinyl alcohol) electrospun nanofibrous membrane modified with spirolactam–rhodamine derivatives for visible detection and removal of metal ions. RSC Adv. 4, 51381–51388.
Yang, R., Aubrecht, K. B., Ma, H., Wang, R., Grubbs, R. B., Hsiao, B. S., et al. (2014). Thiol-modified cellulose nanofibrous composite membranes for chromium (VI) and lead (II) adsorption. Polymer 55, 1167–1176.
Yao, J., Bastiaansen, W. M. C., and Peijs, T. (2014). High strength and high modulus electrospun nanofibers. Fibers 2, 158–186.
Zhao, X., Liu, Y., Shuai, Z., and Wang, C. (2019). Preparation and performance of three-layered structure composite membrane for heavy metal ions and hazardous dyes rejection. Polym. Eng. Sci. 59, E322–E329.
Zhu, M., Han, J., Wang, F., Shao, W., Xiong, R., Zhang, Q., et al. (2017). Electrospun nanofibers membranes for effective air filtration. Macromol. Mater. Eng. 302:1600353.
Keywords: electrospinning, nanofibers, tailored membrane, bio-based multilayered membranes, filtration
Citation: Neisiany RE, Enayati MS, Kazemi-Beydokhti A, Das O and Ramakrishna S (2020) Multilayered Bio-Based Electrospun Membranes: A Potential Porous Media for Filtration Applications. Front. Mater. 7:67. doi: 10.3389/fmats.2020.00067
Received: 03 October 2019; Accepted: 04 March 2020;
Published: 08 April 2020.
Edited by:
Miroslav Slouf, Institute of Macromolecular Chemistry (ASCR), CzechiaCopyright © 2020 Neisiany, Enayati, Kazemi-Beydokhti, Das and Ramakrishna. This is an open-access article distributed under the terms of the Creative Commons Attribution License (CC BY). The use, distribution or reproduction in other forums is permitted, provided the original author(s) and the copyright owner(s) are credited and that the original publication in this journal is cited, in accordance with accepted academic practice. No use, distribution or reproduction is permitted which does not comply with these terms.
*Correspondence: Rasoul Esmaeely Neisiany, ci5lc21hZWVseUBoc3UuYWMuaXI=