- 1Materials Science and Nanoengineering, Rice University, Houston, TX, United States
- 2Civil and Environmental Engineering, Rice University, Houston, TX, United States
- 3C-Crete Technologies LLC, Stafford, TX, United States
Nature-inspired ensemble of organic and inorganic constituents, such as that found in the microstructure of nacre and dactyl clubs of Mantis shrimp, has evolved into the model system for the structural design of industrial composites. This novel design concept, which helps attaining the balance between strength, toughness and ductility, has not only induced a paradigm shift in the synthesis of advanced materials such as graphene-based composites but also, in the development of more abundant, low-cost materials such as cement and concretes. The advance in synthetic techniques and the advent of new manufacturing technologies such as 3D printing has enabled effective integration of cementitious materials with soft materials across various length scales. Furthermore, novel functional properties such as self-healing have also been materialized based on a variety of strategies. This review will provide the comprehensive overview on the ongoing research efforts, encompassing 3D printing, self-healing strategies and integration of C-S-H with organic components, all of which are actively exploited in synthesizing bioinspired, multifunctional cementitious materials.
Introduction
Nature provides a large pool of living examples, where materials with distinct types of properties are orchestrated with each other synergistically at various length scales. The unique structural arrangement coupled with bioinspired compositional properties often induces exceptional mechanical properties at macroscale. Notable examples encompass a nacre, where strong, platelet-shaped calcium carbonate minerals are periodically stacked upon each other and organic materials, totaling only 5% of the material's entire composition, exist between the platelets. As illustrated in Figure 1, this tiny fraction of the organic components serves as a major driving force behind the exceptional mechanical properties, which are marked by high strength and high toughness (Sakhavand and Shahsavari, 2015; Wegst et al., 2015).
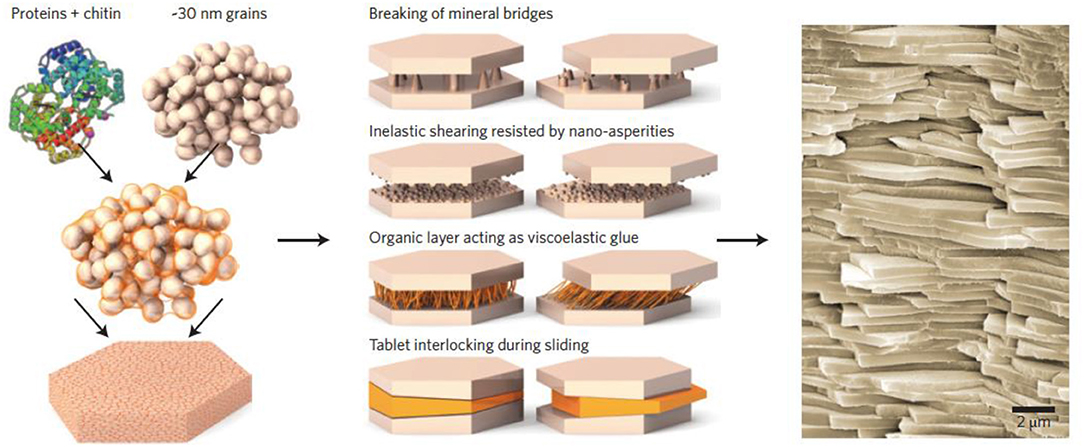
Figure 1. Structural features of a nacre leading to enhanced fracture resistance at different length scales. Figure adapted from Wegst et al. (2015), with permission from Springer Nature.
Human bones are also marked by the close interplay between two constituent nanophases, hydroxyapatite nanocrystals and collagen fibrils, thereby introducing multiple toughening mechanisms across different length scales (Wegst et al., 2015). Intrinsic toughening, characterized by plasticity, which is primarily caused by fibrillar sliding governs the toughening process at nano and sub-micron scale. Extrinsic toughening mechanisms, largely induced by crack bridging and crack deflections dominate at a larger, micro and macro scale. Human teeth are also perfect examples, where organic and inorganic components are arranged synergistically to overcome inherent mechanical shortcomings of the latter. Cracks initiated in enamel, the highly mineralized, brittle component of teeth are arrested at a junction between enamel and dentin. Dentin the inner component of teeth exhibit distinct types of structural arrangement at different length scales While it shows bone-like arrangement marked by a matrix of mineralized fibrils at nanoscale, it consists of dentinal tubules surrounded by mineral, which introduces extrinsic toughening mechanism via creation of microcracks upon loading. Spider silk also shows structural arrangement of distinct types of materials, characterized by beta-sheet nanocrystals confined within semi-amorphous protein matrix. The elastic matrix phase plays critical roles during small mechanical deformation while the crystalline phases play major roles during larger deformation (Nova et al., 2010).
Overall, the strength-enhancing bioinspired features, coupled with novel functional properties found in nature such as self-healing are now being actively employed as a design guideline for material scientists. Those bioinspired strategies can now be implemented using a variety of synthetic techniques and also, newly rising manufacturing technologies including 3D printing.
Cementitious materials, including concretes, which are the most widely employed synthetic material on the planet, are strong, cost-effective but highly brittle and thus, greater diversity in industrial applications is being impeded. The high brittleness in turn induces high susceptibility toward the formation of small-scale cracks, which if left unhealed, can induce rapid propagation and ultimately, results in a complete failure of entire structures. Since cementitious materials are ubiquitous in today's modern infrastructures, implementation of bioinspired structural features to overcome their inherent mechanical shortcomings has been the ultimate goal for numerous research efforts. For example, advanced synthetic techniques have enabled fine-tuning of structural and compositional features of their most fundamental building units and also, the advent of novel manufacturing technologies such as 3D printing has enabled automatized, facile production of bioinspired reinforcement materials for concretes.
This review provides an overview on the ongoing research efforts, which are currently devoted to implementing bioinspired structural concepts using cementitious materials. The review discusses the current status of research in each major strategy and also, states the major obstacles in applying the aforesaid concepts at large-scale construction sites. The research efforts can be broadly divided into three major areas, self-healing, 3D printing, and the synthesis of bioinspired calcium-silicate-hydrate (Table 1), the most basic building blocks of cementitious materials.
Self-Healing Cementitious Materials
One of the most exciting phenomena observed in many of living organisms is self-healing capability. For example, bones in vertebrates undergo a series of healing steps upon the occurrence of damage, with bone cells known as osteoclasts and osteoblasts working in tandem with each other to eventually secrete extracellular matrix at the wound site, which undergoes mineralization to wrap up the healing process (Cremaldi and Bhushan, 2018). Furthermore, when skin and blood vessels underneath the skin are damaged, blood platelets reach the damaged site, initially forming a plug and subsequently, they become activated by collagen to undergo coagulation with fibrin, eventually forming a clot to prevent further blood loss1. Although the real skin repair process involves a greater number of different chemicals and much more complex sequence of chemical reactions, similar concept has also been applied for inanimate materials. Artifical “stores” in the form of microcapsules, tubes or network of microchannels can be embedded inside matrix, thereby carrying multiple types of healing agents, which become released upon damage and undergo further reactions to heal the damaged region.
Concretes, unlike majority of inanimate materials, possess the ability to recover from small-scale cracks via autogenous healing (Van Tittelboom and De Belie, 2013). This is possible due to the coexistence of multiple phases, which, even when the hardening process of concretes is complete, can undergo further reactions to yield strength-giving or space-filling phases. For example, unhydrated clinker phases, such as tricalcium silicate (C3S) and dicalcium silicate (C2S) can react with water entering through micro- or millimeter-sized cracks to produce more of calcium-silicate-hydrate, C-S-H, which is the primary, strength-giving binder phase of concretes (Van Tittelboom and De Belie, 2013). Portlandite Ca(OH)2, another product from the hydration of Portland cement, can also react with carbon dioxide dissolved in water to produce space-filling minerals of calcium carbonate (Possan et al., 2017). Despite this inherent ability to self-heal without autonomous agents, the size and the total number of cracks, which could be healed by this autogenous healing are restricted. Consequently, researchers proposed autonomous and simultaneously, novel and tailored strategies for self-healing cement-based materials. Over the past decade, remarkable progress has been attained, eventually reaching the point where the combination of those strategies has been evaluated at full-construction sites, thereby exhibiting promising potentials (Teall et al., 2016).
Glass Tube-Based Approach
The early efforts in implementing self-healing concretes were primarily focused on manually embedding thin hollow glass tubes filled with external healing agents inside concretes. Cracking would naturally fracture the tubes thereby prompting the release of inner contents to the damaged areas (Dry, 1994; Van Tittelboom and De Belie, 2013). This basic concept somewhat resembles the network of blood vessels existing underneath human skin, where external cut would trigger the release of blood and clotting at damaged areas. This “network-inside-matrix” concept has also been successfully employed for polymeric materials (Toohey et al., 2007).
However, incorporating cargo-loaded glass tubes inside concretes has numerous shortcomings. For example, polymeric agents filled inside tubes are often too viscous at ambient conditions and consequently, they would not possess sufficient flowability to penetrate into microcracks and induce sufficient self-healing effects. This is verified by the recent work, where Van Belleghem et al. found that polyurethane with lower viscosity induces higher surface coverage and also, higher self-healing efficiency in cementitious mortar samples (Van Belleghem et al., 2018). Furthermore, glass tubes, which are often employed as carriers are brittle and thus, they could possibly undergo premature fracture during vigorous mixing procedures rather than fracturing exclusively upon the formation of cracks. In the light of those shortcomings, new types of microscopic carriers coupled with wide variations in types of healing agents, have been developed.
Hu et al. incorporated miniaturized glass tubes (30 mm length and 8 mm diameter) filled with a mixture of polyurethane, which is one-component healing agent with high viscosity and acetone, which serves as a viscosity-decreasing agent (Hu et al., 2018). The authors confirmed that acetone decreased the overall viscosity to a sufficient level, which eventually led to filling of the crack with the size of 300 um.
Capsule-Based Approach
Microscopic carriers or capsules from more elastic types of materials have also been developed using various processing techniques such as polymer extrusion. Dong et al. synthesized polymer-based, core-shell type microcapsules with the size ranging between 400~1,200 um using extrusion-spheronization technique and endowed the capsules with pH-responsive behavior, which triggers release and chemical dissociation of the inner self-healing contents (Dong et al., 2015). When the authors placed the microcapsules in calcium hydroxide solutions, which were employed to simulate concrete pore solutions, high pH values served as external stimulus. They triggered release of the core content, sodium monofluorophophate, which subsequently dissociates into its constituent ions, Na+ and PO3F2−.
Since the survival of those external capsules during the vigorous mixing process and also, during casting procedures is critical for this capsule-based methodology, researchers also developed new evaluation techniques for self-healing efficiency. Araujo et al. extruded microscale poly(methyl methacrylate) capsules with the width less than a millimeter using a single screw extruder (Araujo et al., 2018). The authors encapsulated an accelerating agent inside those PMMA capsules and backtracked the number of capsules broken during the mixing process by quantifying the accelerating effect observed during the setting process.
In order to increase the survival ratio of the external capsules, Hilloulin et al. extruded three different types of polymeric capsules, poly(lactic acid), polystyrene and Poly(methyl methacrylate/n-butyl methacrylate), all of which possess low glass transition temperatures below 100°C, using a twin screw extruder (Hilloulin et al., 2015). The authors applied heat to raise the temperature beyond their glass transition temperatures, in order to induce a switch in mechanical behavior from brittle to elastomeric states. This heat-induced “brittle-to-rubbery” transition ultimately increased the survival ratio of the capsules even in a high temperature concrete mixing. Certain fractions of heat-treated P(MMA/n-BMA) based capsules were found to possess a well-balanced and optimized mechanical properties, enabling them to survive vigorous mixing procedure and simultaneously, become successfully fractured upon the formation of cracks during 3-point bending loading.
In addition to the aforementioned extrusion-based synthesis of polymeric capsules, solution-based polymerization has also been used to synthesize polymeric capsules with even smaller ranges of sizes below one millimeter. Pelletier encapsulated sodium silicate solution in polyurethane microcapsules, with the size of 40~800 μm using in situ interfacial polymerization (Pelletier et al., 2011). The authors artificially introduced microcracks in cement mortar samples and measured the flexural strengths, which were found to be at least 10% higher for the cement mortar samples containing the microcapsules compared to control samples without external agents.
Advanced and innovative technique has also been employed to synthesize core-shell type microcapsules for self-healing concretes. Yang et al. prepared sulfonated polystyrene (PS) particles and dispersed them in a oil/water solution, where the oil is comprised of methyl methacrylate (MMA), triethylborane and tetraethylorthosilicate (TEOS) (Yang et al., 2011). The PS particles become attracted to the oil droplets and sulfonated groups on surfaces of the particles serve as catalysts for the hydrolysis and condensation of TEOS, thereby synthesizing silica microcapsules, which encapsulate MMA monomer. Uniaxial fatigue testing revealed that the microcapsules served to enhance crack resistance in cementitious mortar samples reinforced with carbon microfiber.
Bacteria-Based Approach
Although the abovementioned capsule-based approach has been widely employed for various types of materials, certain self-healing strategies have been designed exclusively for cementitious materials. One example is bacteria based self-healing. Bacterial species, like many other microorganisms, can perform a wide range of chemical conversions if they are provided with the appropriate chemical substrate and the appropriate conditions.
Jonkers and Schlangen confirmed the potential of applying bacterial species for self-healing concretes by directly adding bacterial spores along with calcium lactate during the concrete mixing process (Jonkers and Schlangen, 2008). The authors saw that naturally-formed calcite (CaCO3) minerals were much more pronounced in size than those formed from intact concretes. Jonkers and Schlangen subsequently confirmed that the strategy based on the addition of bacterial spores along with the mineral substrate, calcium lactate, exhibits high CaCO3-forming capacity on cracked surfaces of young-aged concrete samples (Jonkers and Schlangen, 2008). On the other hand, the authors also confirmed the inability of the bacterial spores to survive the long curing age (~28 days), thereby confirming both promising potentials and limitations of bacterial-based self-healing strategy.
Since the aforementioned early attempts in applying bacterial-based self-healing, a large number of subsequent research efforts have been directed toward overcoming the key restrictions, which impede widespread materialization at practical scales. Luo et al. found numerous factors, which influence the efficiency of bacteria-based self-healing, including the crack width, curing condition and the age of concrete at the time of crack formation (Luo et al., 2015). Herein, the authors confirmed via the electron microscopy that at the initial and 20 day period, bacterial self-healing system exhibited different self-healing capacity for different crack widths, 0.3 and 0.8 mm, inducing only partial degree of healing for the latter. Also, the authors found that curing in water was more effective in inducing healing phenomenon than wet curing.
Tziviloglou et al. encapsulated bacterial spores, calcium lactate and yeast extract inside lightweight aggregates via a vacuum-induced incorporation and used them as replacement for normal sand in preparing cementitious mortar (Tziviloglou et al., 2016). Self-healing capability was evaluated by introducing a crack with the width of 350 um using three-point bending test and measuring water permeability test. The test proved that the self-healing system induced less water flow compared to the intact mortar samples. Although the bacteria-loaded aggregates decreased compressive strengths compared normal sand aggregates, they verified their potential to serve as carriers for bacterial-based healing agents.
Novel monitoring techniques were also introduced to further enhance the efficiency of bacterial-based self-healing system. Liu et al. employed coda wave interferometry to evaluate and quantify the degree of self-healing induced by the formation of CaCO3 in a non-destructive way (Liu et al., 2016).
Shape-Memory Polymer-Based Approach
Certain natural materials can alter their shapes in response to external stimuli. This is often observed for plant-based materials such as branches of trees and pine cones, which can control orientations of their constituent fibers to adopt different structural states (Studart and Erb, 2014). Albeit being based on a different type of mechanism, certain petroleum-based polymers, including polyethylene terephthalate (PET) tendons also exhibit shape changes upon external stimuli. While PET polymer undergoes certain processing techniques, its constituent molecules are aligned and subsequently frozen, thereby developing shrinkage potential. Consequently, the external application of heat induces shrinkage of the tendons. The aforesaid heat-responsive shape memory polymer can be incorporated in concrete structures as reinforcement materials and induce self-healing when cracks are formed. The strategy is based on the mechanism that once cracks are formed, external heat stimulus can be applied to induce a shape change that facilitates closing the cracks and strength recovery. Jefferson employed PET tendons as prestressing tendons and evaluated their ability to close cracks upon heating and induce strength recovery (Jefferson et al., 2010). As illustrated in Figure 2, the shrinkage potential developed during heating and cooling procedure induces shrinkage upon heating, thereby exerting a compressive force on cracked faces.
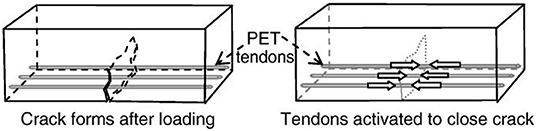
Figure 2. Self-healing of a concrete induced by shrinkage of PET tendons with shape-memory capability. Figure reproduced from Jefferson et al. (2010), with permission from Elsevier.
After the validity and potential of the strategy using shape memory polymer were first verified, the subsequent efforts were devoted to improving the method further by implementing new additional ideas. Teall et al. encapsulated the assembly of PET filaments inside heat distribution layer, equipped with nichrome wire coiling around on the outer surface and placed the assemblies inside concrete beams to confirm if electrical currents can serve as external stimulus for a shape change (Teall et al., 2018). The authors found that the tendons not only induced around 85% crack closure in unreinforced concretes but they also enhanced the overall stiffness of the concrete samples.
Overall, the large depth and breadth of the proposed self-healing strategies and a large number of research efforts devoted to each strategy eventually led to full-scale trials. Various self-healing concepts described above have been implemented at real construction sites via EPSRS funded research project, named as “Materials for Life (M4L)” (Davies et al., 2018). The project built several concrete panels, each of which was designed to evaluate one of the three representative self-healing concepts for concretes discussed above, capsule-based approach, shape-memory polymer and bacteria-based concretes. Implementation of this project, evaluating formerly lab-based self-healing strategies at a large-scale itself can be seen as a huge step forward. Despite this remarkable progress, there still exists major obstacles in attaining widespread commercialization. Although the effectiveness of the self-healing strategies has been notably improved when viewed from technical perspective at lab- and a pilot-scale, attaining economic feasibility for continuous, and widespread use at real world-scale still remains a challenge.
3D Printing
General Introduction to 3D Printing
As stated in the Introduction, natural materials often exhibit exceptional mechanical properties stemming from the interplay between different types of materials. Furthermore, their constituent materials often adopt specific geometries and orientations with respect to each other in order to maximize beneficial effects on macroscale mechanical properties. The advent of advanced manufacturing technologies, such as 3D printing, has now enabled the implementation of those bioinspired features for cement-based structures. 3D printing is a modern, generic term for an automated layer-by-layer assembly, where various types of industrial materials including polymer, metal and ceramic are directly employed as constituents of printing “ink” and thin layers are deposited in sequential steps. Overall, the global market for 3D printing is expanding rapidly owing to an increase in the range of types of print materials and also, to the advent of different techniques ranging from stereolithography, fused deposition modeling and selective laser sintering (Du et al., 2018; Snikhovska, 2019). For example, bioactive, ceramic based scaffolds have been 3D printed for utilization in bone repair and the ongoing research efforts are devoted to ultimately attaining widespread practical applications (Du et al., 2018).
The idea of applying 3D printing for cementitious materials was materialized as early as 1997, when Pegna performed a sequential layer-by-layer deposition of Portland cement and sand and applied post-steam curing to prompt hardening process (Pegna, 1997; Shahsavari and Hwang, 2017). Since then, 3D printing in construction industry has branched into different types of techniques emcompassing controur crafting, D-shape technology and concrete printing, with the ongoing research efforts to enhance practical applicability at real construction sites (Bos et al., 2016). Once the latter is attained, shelters can be provided at underdeveloped, homeless regions in a short amount of time and tall buildings could be finally printed, saving cost, and time required for manual construction.
One of the most renowned 3D printing techniques in construction industry is contour crafting, which is computer-controlled and originally developed by Hager et al. (2016). Herein, cementitious paste with the optimized composition, which in turn leads to the appropriate rheology for 3D printing is extruded through a nozzle and two trowels, which constitute important parts of the nozzle system constrain the flow of the extruded ink in situ to ensure a smooth surface (Khoshnevis and Bekey, 2002; Hwang and Khoshnevis, 2004). The proper application of this cement-based, 3D printing technique started with the creation of small-scale sections having the size of around 10 inches and the technique was later developed further to create a two-feet tall, five-feet long concrete wall as illustrated in Figure 3 (Hwang and Khoshnevis, 2004).
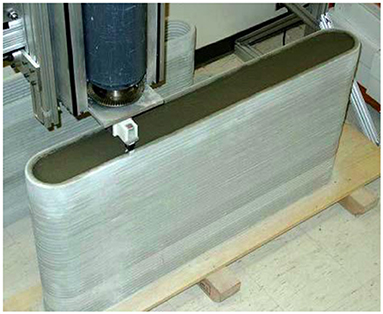
Figure 3. Concrete wall synthesized via contour crafting technique. Figure adapted from Hwang and Khoshnevis (2004), with permission from Int. J. Industrial and Systems Engineering.
The active, ongoing research efforts encompass coupling software-based technologies with contour crafting in order to take the efficiency to a next level. Davatalab et al. recently introduced a software platform called “A Planning and Operations Control Software for Automated Construction” (PROSAC), which can be employed to link information from building information modeling (BIM) with contour crafting (Davtalab et al., 2018). Zhang et al. introduced a new 3D printing system where multiple robots work together on a single structure. This indicates a potential for utilizing 3D printing for full scale construction (Zhang X. et al., 2018).
3D Printable Cementitious Mix
The major research efforts in cement-based 3D printing were focused on obtaining appropriate rheological properties of the print ink, which would ensure sufficient flowability closely linked to successful extrusion without compromising buildability and mechanical properties of the final object. Two of the critical factors for successful extrusion of cement-based ink are pumpability, which represents how readily the paste material can be pumped from storage to the point of extrusion and buildability, which implies the degree of stability for the sequential deposition of extruded layers (Weng et al., 2018; Zhang Y. et al., 2018). Fresh properties of a novel 3D printing concrete ink. Both factors are highly correlated with rheological behavior of the cement-based and thus, a large number of research efforts has been devoted to optimizing its rheological properties by altering its composition.
Weng et al. employed a gradation technique based on Fuller-Thompson theory for sand aggregates and also, packing fraction based on Mercy-Percy model in preparing the cementitious mix for 3D printing (Weng et al., 2018). The authors compared the “Fuller-Thompson”-based gradation with other known gradation techniques, which are uniform gradations and gap gradations. They investigated and compared the gradation-induced rheological behavior between the samples, revealing that the Fuller-Thompson-based gradation was evidently more effective in enhancing buildability of the cementitious mix for 3D printing.
Among the research efforts to optimize composition of the mix for 3D printing, a large proportion has also been directed toward utilizing industrial waste as a part of the ink composition. This would ultimately enhance eco-friendliness of the slurry material due to the decreased utilization of Portland cement and increased recycling of the waste. Furthermore, it would facilitate reducing the cost issues associated with 3D printing in construction industry. In general, industrial waste such as fly ash, rice husk and ground blast furnace slag, has been subjected to active research as potential candidates for replacement of Portland cement, whose production is carbon dioxide intensive (Barnett et al., 2006; Habeeb and Mahmud, 2010; Hwang and Shahsavari, 2018).
Ma et al. partially replaced sand in cement mortar with copper tailing, the industrial waste from mining industry and evaluated 3D printing-related properties of the resultant mortar (Ma et al., 2018). The authors varied the replacement ratio from 0 to 50% and investigated the resultant effect on 3D printing-related properties, encompassing flowability, extrudability, and buildability. They found that owing to the fine particulate size of copper tailing, increasing the ratio of replacement favored flowability while it degraded the buildability. In general, the overall printability of the cementitous mix is dependent on a series of factors, which at large, can be divided into material properties including strength, flowability, and stiffness and processing conditions such as print path and extrusion rate. The aforementioned material properties and processing conditions are often interrelated with each other. Consequently, the authors evaluated the printability of this environmentally-friendly mortar by obtaining two critical coefficients, buildability and extrudability, based on various types of parameters mentioned above, thereby proposing a new design scheme for 3D printable cementitious mix.
Panda et al., also prepared geopolymer-based mix for 3D printing using fly ash F and ground granulated blast-furnace slag and utilized the paste to perform a computer-controlled, layer-by-layer deposition (Panda et al., 2017). The printed object exhibited a direction-dependent enhancement in compressive strengths, thereby verifying the potential of using geopolymer-based ink as environmentally-friendly mortar for 3D printing.
Prompted by the large availability of 3D printing instruments for research purposes and also, the notable progress in enhancing printability using various types of cement-based mixes as depicted above, research efforts have also been devoted to attaining bioinspired, cementitious composites based on 3D printing.
Bio-Inspired, 3D-Printed Cementitious Composites
One way of applying 3D printing for bioinspired cementitious composites is utilizing cement-based mortar directly as print ink and creating structures with biomimetic complex geometries. The exceptional mechanical properties of natural materials or body parts of living organisms arise not only from the mere coexistence of organic and inorganic materials but in many cases, also from unique geometrical complexities at various length scales. Dactyl clubs of Mantis shrimp are the perfect, representative example, where the helicoidal arrangement of soft organic components serves as the foundation for exceptional toughness (Weaver et al., 2012). In the “impact” region of the dactyl clubs, which constitute the outermost parts, are primarily composed of hard, hydroxyapatite crystallites arranged in specific orientations, which favor the overall rigidity. Furthermore, the “periodic” region located underneath the impact region is marked by the helicoidal arrangement of chitin fibrils, which introduces helicoidal and thus, more tortuous pathways for crack propagation.
Cement-based paste can be directly utilized as an ink for 3D printing and bioinspired structures with complex geometrical features such as honeycomb or Bouligand architecture with varying pitch angles can be created as shown in Figure 4 (Moini et al., 2018). Martin et al. also applied 3D magnetic printing to synthesize a polymer/ceramic composite where the ceramic fillers are arranged in specific orientations inside polymer matrix, thereby inducing a direction-dependent mechanics in composites (Martin et al., 2015). The individual cases above have verified the potential of utilizing 3D printing technique to endow cementitious materials with bioinspired, geometric complexities as those seen in living organisms. Nevertheless, the aforesaid cases have been implemented at a laboratory-scale and various challenges regarding cement-based 3D printing need to be overcome in order to accomplish bioinspired, structural complexities at a larger scale.
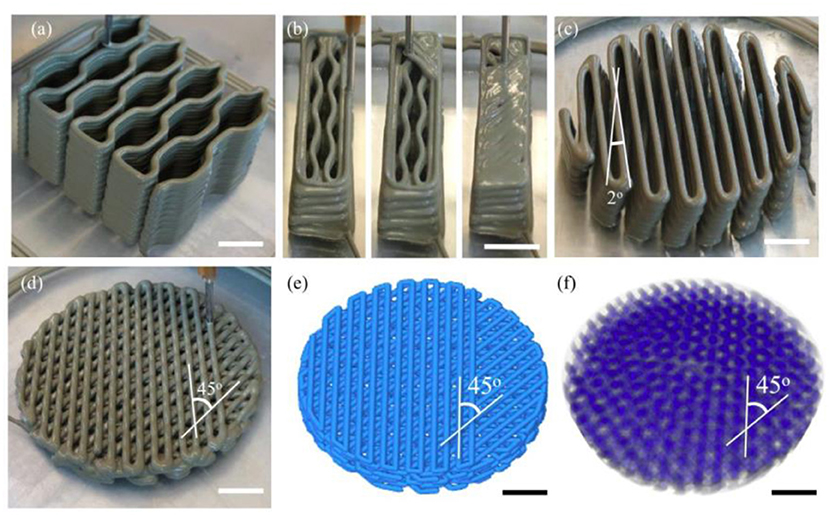
Figure 4. 3D printed cementitious structures with complex geometries. (Scale bar−10 mm) Figure adapted from Moini et al. (2018), with permission from John Wiley and Sons. (a–f) Different printed morphologies along with respective schematics.
3D-Printed Reinforcement Materials With Biomimetic Features
3D printing can also be used to print “reinforcement” materials with biomimetic features, which can be incorporated inside concretes to enhance mechanical properties. They often perform their strength-enhancing functions by introducing additional failure mechanisms during mechanical loading. Certain types of materials, including polymer are widely established as a material source for 3D printing and thus, polymeric fibers with a greater variety of bioinspired structural features, such as auxetic or hierarchical properties can be synthesized.
Rosewitz et al. 3D-printed acrylonitrile butadiene (ABS)-based mesh, with the geometry of individual unit cells ranging from reentrant, “bow-tie” to tubular structures, thereby exhibiting auxetic behavior i.e., Negative Poisson's ratio upon mechanical loading (Rosewitz et al., 2019). Auxetic behavior is observed by several living organisms in nature, for example in skin of salamander and also, in cat's skin, which exhibits out-of-plane auxetic behavior (Veronda and Westmann, 1970; Santulli and Langella, 2016). Mechanical evaluation after 7 days of curing revealed that the auxetic reinforcement, also with the “brick-and-mortar” geometry increased the flexural strength, toughness and compressive strength via newly introduced failure mechanisms. The reinforcement triggered lateral shear failure as verified by the sliding of layers during fracture, while the intact cementitious samples exhibited shear failure in diagonal directions.
Similarly, Xu et al., also 3D printed polymeric meshes composed of repeating triangular cells using renowned fused-deposition modeling (FDM) technique and incorporated the meshes inside cementitious mortar beam (Xu et al., 2019). The authors varied the size of individual, triangular unit cells and performed tensile, as well as four-point bending test to reveal the effects of those polymeric meshes on the overall mechanical properties. It was found that the polymeric meshes can induce strain hardening and also enhance ductility via crack-bridging effect, which accompanies the formation of multiple cracks near the failure point.
Structural hierarchy is one of the key biomimetic features observed in natural materials including the red abalone, where mineral bridges connecting individual aragonite tablets exist in addition to the organic layers comprising chitin proteins in the interlayer spaces (Sun and Bhushan, 2012). 3D printing has opened up the door toward introducing such hierarchical structures within cementitious composites. Farina et al., 3D printed both polymeric and metallic fibers with structural hierarchies, with the first level of hierarchy induced by small lattices attached on the surface and the second level attained by fractal geometries formed by those lattices along the fiber (Farina et al., 2016). The authors found that the fibers with higher degree of surface roughness induce shear failure mechanism while the smooth fibers undergo flexural failures during three-point bending test.
The advance in manufacturing technologies such as 3D printing has enabled the implementation of such naturally-observed geometrical complexities using industrial building blocks. Martin et al. applied 3D magnetic printing to synthesize a polymer/ceramic composite where the ceramic fillers are arranged in specific orientations inside polymer matrix and this verifies that 3D printing can induce a direction-dependent mechanics in composites (Martin et al., 2015).
In this section, two distinct ways of exploiting 3D printing techniques for bio-inspired, cementitious structures have been discussed. The first way is creating a biomimetic structure using cementitious slurry directly as print ink and the second way is printing reinforcement materials with unique bioinspired features and incorporating them inside concretes afterwards. In addition to those two general routes, polymer-reinforced concretes have also been directly extruded using cementitious mix composed of high-density polyethylene fibers. Ogura et al. applied an extrusion-based 3D printing to create a seven-layered, cement-based composite wall containing high density polyethylene microfibers and the mechanical evaluation on tensile and compressive strength was performed after 28 days of curing (Ogura et al., 2018). The evaluation confirmed that larger strain capacity was attained for the cementitious-HDPE composite under tensile loading with the formation of multiple cracks.
Overall, several challenges need to be overcome to render the automated 3D printing process to construction industry more widespread. Despite several successes in creating full-construction scale components via 3D Printing and the upward trend in the number of relevant projects worldwide, current extrusion-based 3D printing requires expert control on the usage of equipment and preparation of the printing materials (Buswell et al., 2018). Furthermore, ensuring reliability in materializing the pre-designed geometry of the component during the printing process remains a challenging task, since material properties, such as rheology and setting time of the printing ink as well as processing parameters can affect final shape of the structure.
Synthesis and Biomimetic Modification of C-S-H
Another bioinspired strategy for cementitious materials is the bottom-up approach, where the most fundamental building blocks, called calcium-silicate-hydrate abbreviated as C-S-H are synthesized and their structural, physicochemical, and size properties are engineered at a microscopic scale. This enables controlled integration of the most fundamental building units of cementitious materials with organic components even from the length scale as microscopic as nano- and submicron scale. This integration of different types of materials from a microscopic scale is the common feature observed in natural materials. Structural, compositional and morphological properties of C-S-H can now be engineered and optimized for the subsequent assembling process, which would ultimately lead to enhanced mechanical properties at macroscale. Synthetic C-S-H can be produced via several routes including slurry-phase reaction between calcium oxide and silica, mechanochemical synthesis using a vibration mill and solution-based synthesis between calcium nitrate and sodium silicate (Sasaki et al., 2005; Foley et al., 2012; Mogghaddam et al., 2017).
The synthesis of hybrid, organic-inorganic composites composed of C-S-H particles as inorganic components can be attained via two major experimental routes. It can either occur in one step, whereby organic components are incorporated during the actual synthesis of C-S-H. The second route can occur in two separate stages, where the integration of organic components with C-S-H is attained following the synthesis of C-S-H. In the second route, synthesized C-S-H particles can be integrated with organic components via various assembly techniques including self-assembly and pressure-induced assembly.
Synthesis of C-S-H/Polymer Composites
Matsuyama and Young incorporated cationic and anionic polymer with high molecular weights within the structure of quasicrystalline C-S-H at varying Ca/Si ratios and studied the nature of interactions using a variety of characterization techniques encompassing (Jefferson et al., 2010) Si nuclear magnetic resonance magic angle spinning and Fourier Transform Infrared Spectroscopy (Matsuyama and Young, 1999a,b). Expansion of basal spacing within the structure of a C-S-H crystallite, which in turn indicates the interlayer intercalations within the structure of C-S-H was observed for both cationic and anionic polymers, including poly (diallyldimethylammonium chloride) (PDC), poly(4-vinylbenzyltrimethylammonium chloride) (PVC), and poly(methacrylic) acid.
Similar to the work above performed by Matsuyama and Young, Pelliser et al. also added poly(diallyldimethylammonium chloride) during the synthesis of C-S-H using direct precipitation method and found the sign of its intercalation between the C-S-H lamellae based on XRD analysis (Pelisser et al., 2010). The authors also verified via nanoindentation testing that the polymer-induced structural change led to a decrease in packing density of C-S-H at mesoscale, thereby leading to a decrease in indentation hardness and elastic modulus.
In contrast to the previous reports on C-S-H/polymer composites implying the intercalation of polymeric molecules within the layered structure of C-S-H, Merlin et al. did not find an as-evident sign of nanoscale and intercalative interactions for cationic and anionic polymers (Merlin et al., 2002). Instead, the authors found the sign of mesocale interactions between polymer and C-S-H crystallites instead of nanoscale intercalation within the structure of each C-S-H crystallite.
Alizadeh et al. also incorporated aniline during the synthesis of C-S-H based on the reaction between calcium oxide and silica in water and the resultant C-S-H/aniline composite was further subjected to the reaction with ammonium persulfate, thereby prompting homopolymerization of aniline (Alizadeh et al., 2010). This two-step process, where compositing C-S-H with organic monomer was followed by polymerization, resulted in the formation of C-S-H/polyaniline composite.
Aside from simply adding polymeric materials during the solution-based synthesis of C-S-H as described above, creative techniques for the synthesis of C-S-H/polymer nanocomposites have also been introduced at a laboratory scale. Kamali and Ghahremaninezhad applied the layer-by-layer assembly technique using two types of solutions, one containing cationic polymer such as poly(ethyleneimine) along with calcium nitrates and another type, containing negatively charged polymer such as poly(sodium 4-styrenesulfonate) (PSS) along with sodium silicates (Kamali and Ghahremaninezhad, 2018). The authors found via atomic force microscope (AFM)-based nanoindentation that the C-S-H/polymer composite synthesized using this layer-by-layer assembly exhibits similar indentation properties to the previously reported values of C-S-H polymer composites.
Picker et al. created a mesocrystalline, organic-inorganic superstructure from a colloidal solution of C-S-H, stabilized by polymeric materials (Picker et al., 2017). Two types of copolymer, PVP-co-PAA and PAAm-co-PAA were employed as organic dispersants, preventing the random aggregation of colloidal C-S-H particles. Controlled self-assembly was induced via a pH increase or via regulating the C-S-H/polymer ratio, ultimately leading to the formation of a hybrid, crystalline superstructure. A long-range order extending over the scale of millimeters was observed. The layered structure composed of inorganic C-S-H and polymeric materials resembles the microstructure of a nacre, which contains calcium carbonate platelets stacked upon each other with organic components existing at interfaces. Mechanical evaluation of the crystals using nanoindentation and bending test based on a focused ion beam microscope revealed that the hybrid C-S-H/polymer crystals exhibit much more elastic behavior and also, higher flexural strength compared to cement paste. The results verify the potential of synthesizing hybrid, biomimetic superstructures, which can directly enhance mechanical properties.
The advance in synthetic techniques has now enabled the synthesis of C-S-H particles with specific, well-designed properties such as morphology, meso- or nanoporosity, and varying Ca/Si molar ratios, which are closely related to structural and mechanical properties. Specific, well-defined morphology can facilitate inducing a nacre-like microstructure, marked by repeating, stacked patterns of similarly-shaped minerals. Furthermore, meso- or nano-porosity can facilitate inducing submicron or micro-scale integration of inorganic C-S-H with organic materials using, for example, infiltration techniques.
Synthesis of CS-Based Particles With Specific Morphologies
Mogghadam et al. employed a seed-mediated, surfactant-assisted approach to attain specific, well-defined morphology for C-S-H (Mogghaddam et al., 2017). The authors employed naturally formed calcite particles in aqueous solution as basic seeds, thereby prompting heterogenous nucleation and growth of C-S-H on top of them. Mechanical evaluation from the state of single, individual particles to assembled, compacted state revealed that that the well-defined, rectangular morphology exerts positive effects on mechanical properties across different length scales. If the technique is developed further and a larger yield of C-S-H with well-defined cubic morphology can be produced at a large scale with acceptable economic feasibility in future, the particles could be assembled with organic components to produce a nacre-mimetic cementitious composite for applications in real construction sites.
Hwang et al. employed porous calcium silicate-based (CS) particles with well-defined, spherical morphology and employed them as the most basic building blocks for a heat-responsive, self-healing composite. The particles had similar composition to C-S-H, narrow distribution in size between 200 and 300 nm and also, narrow distribution in pore size around 3 nm. The authors integrated the particles with epoxy-based, heat responsive self-healing system, thereby synthesizing organic-inorganic hybrid particles (Hwang et al., 2017). The composite produced by compacting those hybrid particles showed superior micromechanical properties compared to the composite comprised of only CS particles with organic components and also, the composite exhibited heat-responsive, self-healing behavior.
Computational Approach on Studying C-S-H/Polymer Composites
In designing bioinspired, C-S-H/polymer composites, computational techniques encompassing molecular dynamics and atomistic simulation play enormous roles in revealing the nature of interactions at various length scales (Zhou et al., 2017). Particularly, molecular dynamics has been a powerful tool for studying varying degrees of affinities between C-S-H, which lacks long-range structural order and organic polymer. The technique has often been employed for finding the dominant mechanism of interactions.
Zhou et al. employed molecular dynamics to study the nature of interactions between C-S-H and three different types of polymer, poly(acrylic acid) (PAA), poly (vinyl alcohol) and poly (ethylene glycol), all of which have been investigated experimentally as an organic component for C-S-H/polymer composites (Zhou et al., 2018). The authors found that PAA exhibits the strongest interaction among the three types of polymer, primarily via bonding between calcium from C-S-H and double bonded oxygen of carboxylic acid.
Sakhavand et al. also studied the interaction between poly(vinyl alcohol), which had been composited with C-S-H numerous times in previous experimental studies and tobermorite, the crystalline analog of C-S-H. Tobermorite is often adopted as a model system for C-S-H (Tao and Shahsavari, 2017; Zhang et al., 2017). The authors employed the combination of various computational techniques including molecular dynamics and the first-principles study, thereby finding that the maximum toughness, instead of shear strength, dominates the breaking process of interfacial hydrogen bonds, which form the primary route for interaction between the two types of constituent materials (Sakhavand et al., 2013).
The same authors also devised the universal composition-structure-property map for hybrid, “brick-and-mortar”-type composites based on only four dimensionless parameters, encompassing those, which define platelet dissimilarity and symmetry of elastic stress distributions (Sakhavand and Shahsavari, 2015). The map, as shown in Figure 5, was proposed as a possible “design tool” for the synthesis of nacre-mimetic composites since it enables quantifying strength and toughness of any type of nacre-mimetic structures, thereby verifying the potential of producing synthetic, biomimetic cementitious composites with mechanical properties tailored for specific industrial applications.
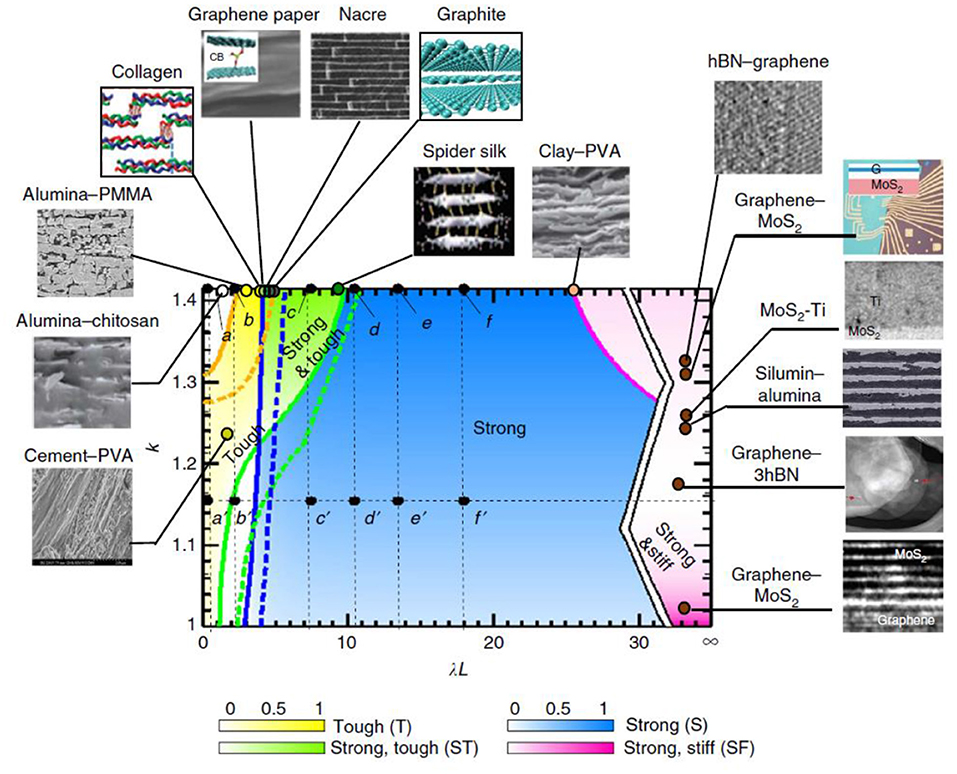
Figure 5. Universal map for mechanical properties of nacre-mimetic hybrid structures obtained based on dimensionless parameters. Figure reproduced from Sakhavand and Shahsavari (2015), with permission from Springer Nature.
Conclusions
The review has provided an extensive insight into three major areas of research efforts, self-healing, 3D printing and nano/mesoscale integration of organic materials with C-S-H, all of which have been actively exploited in attaining novel, biomimetic cementitious materials. Bioinspired materials often characterized by the unique microstructural arrangement of soft and hard materials as observed in nacre and human bones. Furthermore, bioinspired features in nature also encompass self-healing capability, auxetic behavior, and geometrical complexities at various length scale. The advance in synthetic techniques such as the controlled self-assembly of C-S-H with organic materials and seed-mediated synthesis of C-S-H has led to the production of C-S-H or calcium silicate-based materials with well-defined morphological properties and also, successful integration of C-S-H with organic materials. Furthermore, the decade-long research efforts to optimize material and process parameters of cement-based 3D printing have introduced novel routes for biomimetic implementation, for example, creating polymeric reinforcement materials with hierarchical and auxetic features. The three major areas introduced in this review, self-healing, 3D printing, and the integration of C-S-H with organic materials have all led to notable progress based on a variety of implementation strategies.
In order to accomplish further widespread commercialization of aforesaid strategies, self-healing concepts in particular, further efforts need to be devoted to enhancing their cost-effectiveness. For example, despite the aforesaid success in generating a large number of self-healing agent-loaded microcapsules and incorporating them inside concrete panels during field trials, the production cost for these hybrid cementitious composites could become incredibly high if the scale become even larger. Consequently, the development of cost-effective, mass production technique for healant-loaded microcapsules could be one of the bottlenecks in materializing widespread application of capsule-based self-healing strategy for concretes at large scale. Furthermore, if the trial scale become larger, evaluating the effectiveness of the embedded self-healing systems could also become challenging. This is because conventional techniques for strength testing and crack introduction would become more difficult to implement if the test scale becomes larger than the field trials recently performed via the “Materials for Life” project. Therefore, appropriate evaluation techniques should also be devised for large-scale self-healing.
Author Contributions
RS designed the review subjects and logistics. SH and RS wrote the manuscript.
Conflict of Interest
The authors declare that the research was conducted in the absence of any commercial or financial relationships that could be construed as a potential conflict of interest.
Footnote
1. ^Boundless.com: Hemostasis. CC BY-SA: Attribution-ShareAlike.
References
Alizadeh, A. R., Beaudoin, J. J., Raki, L., and Terskikh, V. (2010). C–S–H/polyaniline nanocomposites prepared by in situ polymerization. J. Mater. Sci. 46, 460–467. doi: 10.1007/s10853-010-4918-1
Araujo, M., Chatrabhuti, S., Gurdebeke, S., Alderete, N., Van Tittelboom, K., Raquez, J. M., et al. (2018). Poly(methyl methacrylate) capsules as an alternative to the “proof-of-concept” glass capsules used in self-healing concrete. Cement Concrete Composites 89, 260–271. doi: 10.1016/j.cemconcomp.2018.02.015
Barnett, S. J., Soutsos, M. N., Millard, S. G., and Bungey, J. H. (2006). Strength development of mortars containing ground granulated blast-furnace slag: Effect of curing temperature and determination of apparent activation energies. Cement Concrete Res. 36, 434–440. doi: 10.1016/j.cemconres.2005.11.002
Bos, F., Wolfs, R., Ahmed, Z., and Salet, T. (2016). Additive manufacturing of concrete in construction: potentials and challenges of 3D concrete printing. Virtual Phys. Prototyp. 11, 209–225. doi: 10.1080/17452759.2016.1209867
Buswell, R. A., Leal de Silva, W. R., Jones, S. Z., and Dirrenberger, J. (2018). 3D printing using concrete extrusion: a roadmap for research. Cement Concrete Res. 112, 37–49. doi: 10.1016/j.cemconres.2018.05.006
Cremaldi, J. C., and Bhushan, B. (2018). Bioinspired self-healing materials: lessons from nature. Beilstein J. Nanotechnol. 9, 907–935. doi: 10.3762/bjnano.9.85
Davies, R., Teall, O., Pilegis, M., Kanellopoulos, A., Sharma, T., Jefferson, A., et al. (2018). Large scale application of self-healing concrete: design, construction, and testing. Front. Mater. 5:51. doi: 10.3389/fmats.2018.00051
Davtalab, O., Kazemian, A., and Khoshnevis, B. (2018). Perspectives on a BIM-integrated software platform for robotic construction through Contour Crafting. Automat. Construct. 89, 13–23. doi: 10.1016/j.autcon.2018.01.006
Dong, B., Wang, Y., Fang, G., Han, N., Xing, F., and Lu, Y. (2015). Smart releasing behavior of a chemical self-healing microcapsule in the stimulated concrete pore solution. Cement Concrete Composites 56, 46–50. doi: 10.1016/j.cemconcomp.2014.10.006
Dry, C. (1994). Matrix cracking repair and filling using active and passive modes for smart timed release of chemicals from fibers into cement matrices. Smart Mater. Struct. 3:118. doi: 10.1088/0964-1726/3/2/006
Du, X., Fu, S., and Zhu, Y. (2018). 3D printing of ceramic-based scaffolds for bone tissue engineering: an overview. J. Mater. Chem. B. 6, 4397–4412. doi: 10.1039/C8TB00677F
Farina, I., Fabbrocino, F., Carpentieri, G., Modano, M., Amendola, A., Goodall, R., et al. (2016). On the reinforcement of cement mortars through 3D printed polymeric and metallic fibers. Composites Part B Eng. 90, 76–85. doi: 10.1016/j.compositesb.2015.12.006
Foley, E. M., Kim, J. J., and Reda Taha, M. M. (2012). Synthesis and nano-mechanical characterization of calcium-silicate-hydrate (C-S-H) made with 1.5 CaO/SiO2 mixture. Cement Concrete Res. 42, 1225–1232. doi: 10.1016/j.cemconres.2012.05.014
Fratzl, P., and Barth, F. G. (2009). Biomaterial systems for mechanosensing and actuation. Nature 462, 442–448. doi: 10.1038/nature08603
Fratzl, P., Elbaum, R., and Burgert, I. (2008). Cellulose fibrils direct plant organ movements. Faraday Discuss. 139, 275–282; discussion: 309–325, 419–420. doi: 10.1039/b716663j
Habeeb, G. A., and Mahmud, H. B. (2010). Study on properties of rice husk ash and its use as cement replacement material. Mater. Res. 13, 185–190. doi: 10.1590/S1516-14392010000200011
Hager, I., Golonka, A., and Putanowicz, R. (2016). 3D printing of buildings and building components as the future of sustainable construction? Proc. Eng. 151, 292–299. doi: 10.1016/j.proeng.2016.07.357
Hilloulin, B., Van Tittelboom, K., Gruyaert, E., De Belie, N., and Loukili, A. (2015). Design of polymeric capsules for self-healing concrete. Cement Concrete Composites 55, 298–307. doi: 10.1016/j.cemconcomp.2014.09.022
Hu, Z.-X., Hu, X.-M., Cheng, W.-M., Zhao, Y.-Y., and Wu, M.-Y. (2018). Performance optimization of one-component polyurethane healing agent for self-healing concrete. Construct. Building Materials 179, 151–159. doi: 10.1016/j.conbuildmat.2018.05.199
Hwang, D., and Khoshnevis, B. (2004). “Concrete wall fabrication by contour crafting,” in The 21st ISARC (Jeju). doi: 10.22260/ISARC2004/0057
Hwang, S., and Shahsavari, R. (2018). High calcium cementless fly ash binder with low environmental footprint: optimum Taguchi design. J. Am. Ceramic Soc. 102, 2203–2217. doi: 10.1111/jace.15873
Hwang, S. H., Miller, J. B., and Shahsavari, R. (2017). Biomimetic, strong, tough, and self-healing composites using universal sealant-loaded, porous building blocks. ACS Appl. Mater. Interfaces 9, 37055–37063. doi: 10.1021/acsami.7b12532
Jefferson, A., Joseph, C., Lark, R., Isaacs, B., Dunn, S., and Weager, B. (2010). A new system for crack closure of cementitious materials using shrinkable polymers. Cement Concrete Res. 40, 795–801. doi: 10.1016/j.cemconres.2010.01.004
Jonkers, H. M., and Schlangen, E. (2008). “Development of a bacteria-based self healing concrete,” in Tailor Made Concrete Structures, eds J. C. Walraven and D. Stoelhorst (London: Taylor and Francis Group). doi: 10.1201/9781439828410.ch72
Kamali, M., and Ghahremaninezhad, A. (2018). A study of calcium-silicate-hydrate/polymer nanocomposites fabricated using the layer-by-layer method. Materials 11:527. doi: 10.3390/ma11040527
Khoshnevis, B., and Bekey, G. (2002). “Automated construction using contour crafting – applications on earth and beyond,” in The 19th ISARC (Washington, DC), 489–495. doi: 10.22260/ISARC2002/0076
Liu, S., Bundur, Z. B., Zhu, J., and Ferron, R. D. (2016). Evaluation of self-healing of internal cracks in biomimetic mortar using coda wave interferometry. Cement Concrete Res. 83, 70–78. doi: 10.1016/j.cemconres.2016.01.006
Luo, M., Qian, C., and Li, R. (2015). Factors affecting crack repairing capacity of bacteria-based self-healing concrete. Construct. Build. Mater. 87, 1–7. doi: 10.1016/j.conbuildmat.2015.03.117
Ma, G., Li, Z., and Wang, L. (2018). Printable properties of cementitious material containing copper tailings for extrusion based 3D printing. Construct. Build. Mater. 162, 613–627. doi: 10.1016/j.conbuildmat.2017.12.051
Martin, J. J., Fiore, B. E., and Erb, R. M. (2015). Designing bioinspired composite reinforcement architectures via 3D magnetic printing. Nat. Commun. 6:8641. doi: 10.1038/ncomms9641
Matsuyama, H., and Young, J. F. (1999a). Synthesis of calcium silicate hydrate/polymer complexes: Part 1. Anionic and nonionic polymers. J. Mater. Res. 14, 3379–3388. doi: 10.1557/JMR.1999.0458
Matsuyama, H., and Young, J. F. (1999b). Synthesis of calcium silicate hydrate/polymer complexes: Part II. Cationic polymers and complex formation with different polymers. J. Mater. Res. 14, 3389–3396. doi: 10.1557/JMR.1999.0459
Merlin, F., Lombois, H., Joly, S., Lequeux, N., Halary, J.-L., and Van Damme, H. (2002). Cement-polymer and clay-polymer nano- and meso-composites: spotting the difference. J. Mater. Chem. 12, 3308–3315. doi: 10.1039/B205279M
Mogghaddam, S. E., Hejazi, V., Hwang, S., Sreenivasan, S., Miller, J., Shi, B., et al. (2017). Morphogenesis of cement hydrate. J. Mater. Chem. A 5, 3798–3811. doi: 10.1039/C6TA09389B
Moini, M., Olek, J., Youngblood, J. P., Magee, B., and Zavattieri, P. D. (2018). Additive manufacturing and performance of architectured cement-based materials. Adv. Mater. 30:e1802123. doi: 10.1002/adma.201802123
Nova, A., Keten, S., Pugno, N. M., Redaelli, A., and Buehler, M. J. (2010). Molecular and nanostructural mechanisms of deformation, strength and toughness of spider silk fibrils. Nano Lett. 10, 2626–2634. doi: 10.1021/nl101341w
Ogura, H., Nerella, V. N., and Mechtcherine, V. (2018). Developing and testing of Strain-Hardening Cement-Based Composites (SHCC) in the context of 3d-printing. Materials. 11, 1375–1385. doi: 10.3390/ma11081375
Panda, B., Paul, S. C., Hui, L. J., Tay, Y. W. D., and Tan, M. J. (2017). Additive manufacturing of geopolymer for sustainable built environment. J. Clean. Prod. 167, 281–288. doi: 10.1016/j.jclepro.2017.08.165
Pegna, J. (1997). Exploratory investigation of solid freeform construction. Automat. Construct. 5, 427–437. doi: 10.1016/S0926-5805(96)00166-5
Pelisser, F., Gleize, P. J. P., and Mikowski, A. (2010). Effect of poly(diallyldimethylammonium chloride) on nanostructure and mechanical properties of calcium silicate hydrate. Mater. Sci. Eng. A 527, 7045–7049. doi: 10.1016/j.msea.2010.07.057
Pelletier, M. M., Brown, R., Shukla, A., and Bose, A. (2011). Self-Healing Concrete with a Microencapsulated Healing Agent. https://pdfs.semanticscholar.org/e48b/937bde7c53ce059d464822ebc837a31647dc.pdf (accessed September 3, 2020).
Picker, A., Nicoleau, L., Burghard, Z., Bill, J., Zlotnikov, I., Labbez, C., et al. (2017). Mesocrystalline calcium silicate hydrate: a bioinspired route toward elastic concrete materials. Sci. Adv. 3:e1701216. doi: 10.1126/sciadv.1701216
Possan, E., Thomaz, W., Aleandri, G. A., Felix, E. F., and dos Santos, A. C. P. (2017). CO2 uptake potential due to concrete carbonation: a case study. Case Stud. Construct. Mater. 6, 147–161. doi: 10.1016/j.cscm.2017.01.007
Prawoto, Y. (2012). Seeing auxetic materials from the mechanics point of view: a structural review on the negative Poisson's ratio. Comput. Mater. Sci. 58, 140–153. doi: 10.1016/j.commatsci.2012.02.012
Rosewitz, J. A., Choshali, H. A., and Rahbar, N. (2019). Bioinspired design of architected cement-polymer composites. Cement Concrete Composites 96, 252–265. doi: 10.1016/j.cemconcomp.2018.12.010
Sakhavand, N., Muthuramalingam, P., and Shahsavari, R. (2013). Toughness governs the rupture of the interfacial H-bond assemblies at a critical length scale in hybrid materials. Langmuir 29, 8154–8163. doi: 10.1021/la4014015
Sakhavand, N., and Shahsavari, R. (2015). Universal composition-structure-property maps for natural and biomimetic platelet-matrix composites and stacked heterostructures. Nat. Commun. 6:6523. doi: 10.1038/ncomms7523
Santulli, C., and Langella, C. (2016). Study and development of concepts of auxetic structures in bio-inspired design. Int. J. Sust. Design 3, 1443–1453. doi: 10.1504/IJSDES.2016.078947
Sasaki, K., Masuda, T., Ishida, H., and Mitsuda, T. (2005). Synthesis of calcium silicate hydrate with Ca/Si = 2 by mechanochemical treatment. J. Am. Ceramic Soc. 80, 472–476. doi: 10.1111/j.1151-2916.1997.tb02853.x
Shahsavari, R., and Hwang, S. (2017). Innovative concretes provide the ultimate solution for rising construction costs and environmental footprint. Am. Ceramic Soc. Bull. 97, 2–8. Available online at: https://pdfs.semanticscholar.org/91b0/06945446e9fbaef01d60c9c391ed454db506.pdf
Snikhovska, K. (2019). The Different Types of 3D Printing Technology. Available online at: penandplastic.com (accessed September 3, 2020).
Studart, A. R., and Erb, R. M. (2014). Bioinspired materials that self-shape through programmed microstructures. Soft Matter 10, 1284–1294. doi: 10.1039/C3SM51883C
Sun, J., and Bhushan, B. (2012). Hierarchical structure and mechanical properties of nacre: a review. RSC Adv. 2, 7617–7632. doi: 10.1002/chin.201250224
Tao, L., and Shahsavari, R. (2017). Diffusive, displacive deformations and local phase transformation govern the mechanics of layered crystals: the case study of tobermorite. Sci. Rep. 7:5907. doi: 10.1038/s41598-017-05115-4
Teall, O., Davies, R., Pilegis, M., Kanellopoulos, A., Sharma, T., Paine, K., et al. (2016). Self-healing concrete full-scale site trials,” in 11th fib International PhD Symposium in Civil Engineering (Tokyo: The University of Tokyo), 639–646.
Teall, O., Pilegis, M., Davies, R., Sweeney, J., Jefferson, T., Lark, R., et al. (2018). A shape memory polymer concrete crack closure system activated by electrical current. Smart Mater. Struct. 27, 1–12. doi: 10.1088/1361-665X/aac28a
Toohey, K. S., Sottos, N. R., Lewis, J. A., Moore, J. S., and White, S. R. (2007). Self-healing materials with microvascular networks. Nat. Mater. 6, 581–585. doi: 10.1038/nmat1934
Tziviloglou, E., Wiktor, V., Jonkers, H. M., and Schlangen, E. (2016). Bacteria-based self-healing concrete to increase liquid tightness of cracks. Construct. Build. Mater. 122, 118–125. doi: 10.1016/j.conbuildmat.2016.06.080
Van Belleghem, B., Gruyaert, E., Van Tittelboom, K., Moerman, W., Dekeyser, B., Van Stappen, J., et al. (2018). Effect of polyurethane viscosity on self-healing efficiency of cementitious materials exposed to high temperatures from sun radiation. J. Mater. Civil Eng. 30, 1–12. doi: 10.1061/(ASCE)MT.1943-5533.0002360
Van Tittelboom, K., and De Belie, N. (2013). Self-healing in cementitious materials-a review. Materials 6, 2182–2217. doi: 10.3390/ma6062182
Veronda, D. R., and Westmann, R. A. (1970). Mechanical characterization of skin-finite deformations. J. Biomech. 3, 111–124. doi: 10.1016/0021-9290(70)90055-2
Weaver, J. C., Milliron, G. W., Miserez, A., Evans-Lutterodt, K., Herrera, S., Gallana, I., et al. (2012). The stomatopod dactyl club: a formidable damage-tolerant biological hammer. Science 336, 1275–1280. doi: 10.1126/science.1218764
Wegst, U. G., Bai, H., Saiz, E., Tomsia, A. P., and Ritchie, R. O. (2015). Bioinspired structural materials. Nat. Mater. 14, 23–36. doi: 10.1038/nmat4089
Weng, Y., Li, M., Tan, M. J., and Qian, S. (2018). Design 3D printing cementitious materials via Fuller Thompson theory and Marson-Percy model. Construct. Build. Mater. 163, 600–610. doi: 10.1016/j.conbuildmat.2017.12.112
Xu, Y., Schlangen, E., and Savija, B. (2019). “Creating Strain Hardening Cementitious Composites (SHCCS) through use of additively manufactured polymeric meshes as reinforcement,” in 10th International Conference on Fracture Mechanics of Concrete and Concrete Structures, eds G. Pijaudier-Cabot, P. Grassl, and C. La Borderie (Bayonne). doi: 10.21012/FC10.235158
Yang, Z., Hollar, J., He, X., and Shi, X. (2011). A self-healing cementitious composite using oil core/silica gel shell microcapsules. Cement Concrete Composites 33, 506–512. doi: 10.1016/j.cemconcomp.2011.01.010
Zhang, N., Carrez, P., and Shahsavari, R. (2017). Screw-dislocation-induced strengthening-toughening mechanisms in complex layered materials: the case study of tobermorite. ACS Appl. Mater. Interfaces 9, 1496–1506. doi: 10.1021/acsami.6b13107
Zhang, X., Li, M., Lim, J. H., Weng, Y., Tay, Y. W. D., Pham, H., et al. (2018). Large-scale 3D printing by a team of mobile robots. Automat. Construct. 95, 98–106. doi: 10.1016/j.autcon.2018.08.004
Zhang, Y., Zhang, Y., Liu, G., Yang, Y., Wu, M., and Pang, B. (2018). Fresh properties of a novel 3D printing concrete ink. Construct. Build. Mater. 174, 263–271. doi: 10.1016/j.conbuildmat.2018.04.115
Zhou, Y., Hou, D., Geng, G., Feng, P., Yu, J., and Jiang, J. (2018). Insights into the interfacial strengthening mechanisms of calcium-silicate-hydrate/polymer nanocomposites. Phys. Chem. Chem. Phys. 20, 8247–8266. doi: 10.1039/C8CP00328A
Keywords: cement-based materials, bio-inspired materials, organic-inorganic composites, mechanical properties, cement, biomaterial, toughness, hybrid materials
Citation: Shahsavari R and Hwang SH (2020) Bioinspired Cementitious Materials: Main Strategies, Progress, and Applications. Front. Mater. 7:62. doi: 10.3389/fmats.2020.00062
Received: 02 September 2019; Accepted: 28 February 2020;
Published: 20 March 2020.
Edited by:
Laura Maria Vergani, Politecnico di Milano, ItalyReviewed by:
Chuying Ma, Pennsylvania State University (PSU), United StatesJae-Young Jung, University of California, San Francisco, United States
Copyright © 2020 Shahsavari and Hwang. This is an open-access article distributed under the terms of the Creative Commons Attribution License (CC BY). The use, distribution or reproduction in other forums is permitted, provided the original author(s) and the copyright owner(s) are credited and that the original publication in this journal is cited, in accordance with accepted academic practice. No use, distribution or reproduction is permitted which does not comply with these terms.
*Correspondence: Rouzbeh Shahsavari, Um91emJlaEBjY3JldGV0ZWNoLmNvbQ==