- 1Department of Physics, Center for Ionics University of Malaya, University of Malaya, Kuala Lumpur, Malaysia
- 2UM Power Energy Dedicated Advanced Centre (UMPEDAC), University of Malaya, Kuala Lumpur, Malaysia
Epoxy-TiO2 nanocomposite coatings were prepared by the utilization of the solution intercalation method with the presence of the sonication process and the influence of embedding different loading ratios of TiO2 nanoparticles within neat epoxy resin was investigated. To further improve the corrosion protection performance and to fulfill the hydrophobicity of the developed coated surfaces, the epoxy polymeric resin was modified with polydimethylsiloxane (PDMS) and different loading ratio of TiO2 nanoparticles was intoduced to the modified polymeric matrix to fabricate PDMS modified epoxy nanocoposite coating sytems. All developed coating systems were characterized by means of Fourier transform infrared (FTIR) spectroscopy and differential scanning calorimetry (DSC) to investigate the chemical structure and the glass transition temperatures (Tg) of the developed coating systems, respectively. The morphology, topology, optical properties, and the wettability were also examined by field emission scanning electron microscope (FESEM), energy dispersive X-rays analyzer (EDX), atomic force microscopy (AFM), ultraviolet-visible spectroscopy (UV-vis), and contact angle measurement (CA), respectively. Moreover, the electrochemical behavior and the barrier properties of the developed coating films were investigated via electrochemical impedance spectroscopy (EIS). The findings revealed a good curing level with higher Tg values for all developed nanaocompsoite coating systems and confirmed the efficiency of the sonication process in developed well-dispersed TiO2 within the polymeric matrix. Also, the obtained results revealed the ability of certain amount of TiO2 nanoparticles in enhancing the corrosion protection performance of epoxy based coating systems. The compatibility of epoxy resin, PDMS, and TiO2 nanoparticles was also confirmed by achieving the hydrophobicity and obtaining the best corrosion protection performance.
Introduction
Due to atmospheric interaction with the environment, corrosion can be defined as the degradation of metallic material via electrochemical reaction on its surface, where it can cause damage and destruction of the material. Moreover, it can lead to an economic burden to a country and put risk to human being's health and safety. Preservation to protect metallic material by applying protective coating is the best practice to overcome most of the corrosion issues and consequences across the globe. The polymeric coating is to provide barrier property on material surface and has been an outstanding choice for anticorrosion purpose due to its production accessibility. However, polymer resin has its shortcoming sustainability that it contains free volume, micro-voids, and exhibits hydrophilicity due to their polar group which gives strong affinity toward water molecules (Ammar et al., 2016b; Guo et al., 2018). These drawbacks lead corrosion process through diffusion of corrosive agents such as oxygen, water molecules, and aggressive anions, create deterioration pathways to reach the coating-metal interface. This action is known as penetration which caused localized corrosion on the material surface that responsible for the damage via hydrolytic degradation (Zaarei et al., 2008; Heidarian et al., 2010; Brusciotti et al., 2013; Verma et al., 2019). A huge number of researches have been done to improve the barrier properties of the polymeric coating in the past decades (Dolatzadeh et al., 2011; Heidarian et al., 2011; Shen and Zuo, 2014; Matin et al., 2015; Mohamad Saidi et al., 2018; Zheng et al., 2019). By incorporating nano-sized fillers into the polymer resin, it is aimed that this effort will enhance the anticorrosion and barrier properties of the polymer coating via various mechanisms, such as filling up the pores and reducing the matrix defects, bowing, bridging and deflecting the cracks (Ammar et al., 2016c). Also, the inorganic nano-sized filler tends to function as a connecting bridge linking between the matrix molecules, thus reducing the total free volume and promotes cross-linking (Shi et al., 2009; Heidarian et al., 2010; Atta et al., 2019). These mechanisms, in turn, delay the penetration activity which slows down the diffusion of corrosive agents in the coating layer from reaching to the coating-metal interface, thus decreasing the corrosion rate on the material surface. One of the utilizable nano-size filler is Titanium dioxide (TiO2) nanoparticles which have been used extensively due to its ability to provide a photocatalytic effect (Liqiang et al., 2003). This means that it is capable to release a huge number of electrons when exposed to ultraviolet light radiation. These electrons then initiate the photo-induced redox reaction on the corrosion causing agents that are adsorbed on the coating surface, further curbing corrosion reaction. Worth to note that ultraviolet light can release radicals which will be able to break the molecular structure of neat polymeric coating layer. Nevertheless, this mechanism provides it an antimicrobial property to kill bacteria that are present on the coating surface, which may also act as corrosion causing agent (Fu et al., 2005; Evans and Sheel, 2007). By that, TiO2 nanoparticles are extensively used due to their anti-fouling, self-cleaning and also odor-inhibition properties resulting from the photocatalytic effect they exhibit.
However, due to the high porosity and hydrophilicity properties possessed by the polymer resin, it drags down the performance of anticorrosion properties by the developed coating system as water molecule is one of the most easily be-in-contact corrosions causing agent. Silicones are categorized as a type of high-valued polymers due to its capability to affect the efficacy of various applications in the industrial field (Eduok et al., 2017; Liao et al., 2018). It gives a significant impact on the industrial applicated due to its molecular structure that may exist in assorted forms (Pouget et al., 2009). Silicone polymers are widely used as polydimethylsiloxane (PDMS) which is an inorganic polymer and has the properties of being hydrophobic contributed by its non-polar -CH3 group that gives the coating low surface energy (Ammar et al., 2017). Massive research works have been conducted in the past few years (Sung and Lin, 1997; Velan and Bilal, 2000; Ahmad et al., 2005) to determine the optimum mixing ratio between epoxy resin and PDMS. It has been agreed that the mixing ratio of 90:10 w/w gives the most optimum performance, especially on the research outcome performed by Ananda Kumar together with his research team (Kumar and Narayanan, 2002; Kumar et al., 2002, 2006; Duraibabu et al., 2014).
In this study, a simple preparation method was developed to prepare the epoxy-TiO2 nanocomposite coating systems. As a result, a homogeneous solution with different TiO2 loading ratios incorporated in epoxy resin was successfully prepared. Then, additional systems were amended with PDMS as modifier into epoxy-TiO2 nanocomposite to develop epoxy-PDMS hybrid polymeric coating systems. The aims for both developed coating systems are to study the effect of low concentration of TiO2 in two different polymeric based, epoxy and epoxy-PDMS matrices. The structure, thermal, and optical properties of all developed coating systems were investigated by FTIR, DSC, and UV-Vis, respectively. Moreover, FESEM, EDX, and AFM were employed to reveal the morphologies of the developed systems. The wettability of the resultant systems was determined by using contact angle method. As for, the barrier properties of the developed coating systems and the corrosion protection performance were investigated via EIS after exposing the cold rolled mild steel coated substrates to 3.5% NaCl solution up to 30 days.
Experimental
Materials
Epoxy resin (EPIKOTE 828) produced from a polycondensation reaction between bisphenol A and epichlorohydrin with an equivalent weight of 184–190 g/eq and viscosity of 12,000–14,000 cP at room temperature was purchased from Asachem (Malaysia) and used as the base resin. Modifier used was hydroxyl-terminated polydimethylsiloxane (HT-PDMS) with a viscosity of 750 cSt and a density of 0.97 g/ml at room temperature was supplied by Sigma-Aldrich (Malaysia) and used as the modifier for the epoxy resin. In order to develop the hybrid epoxy-PDMS polymeric matrix, 3-aminopropyltriethoxysilane (KBE-903) purchased from Shin-Etsu Chemical Co. Ltd (Japan) was used as the coupling agent. The development of all nanocomposite coating systems was carried out via the utilization of titanium (IV) oxide nanoparticles of anatase crystalline structure with diameter <25 nm and density of 3.9 g/mL at room temperature which was supplied by Sigma-Aldrich (Malaysia). Cycloaliphatic amine with an amine value of 260–285 mg KOH/g and an equivalent weight of 113 g/eq and acted as the curing agent and purchased from Hexion (Malaysia). All listed chemicals were used as received from the supplier without any further modification or purification.
Substrates Preparation and Coating Application
Cold rolled mild steel substrates with dimensions of 5 × 7.5 × 0.1 cm were employed as the tested substrate to be coated. The steel panels were first degreased and cleaned using acetone then the pretreated specimens were subjected to sandblasting process according to ASTM D609 standard to achieve Sa 2 surface profile followed by wiping the resulted surfaces with acetone once again to clean off the dust and any other impurities deposited from the sandblasting process. The brushing method was used to developed all coating films which were kept to dry for 7 days at room temperature. The dry film thickness was selected to be in the range of 75 ± 5 μm and was tested via using Elcometer 456 thickness gauge for three replicate coated panels. The coated steel substrates were used to perform FESEM and EIS tests. However, free films were cast onto Teflon plates in order to obtain FTIR testing samples. Transparent glass plates with a size of 2.54 × 7.62 × 0.12 cm were also prepared and subjected to one side coating in order to perform AFM, contact angle measurements and ultraviolet-visible spectroscopy tests.
Preparation of Coating Systems
Neat epoxy coating system designated as (E) and cured with cycloaliphatic amine at mixing ratio (10:6) was developed and used as the reference system. The epoxy and curing agent blend was subjected to continuous stirring for 15 min at 750 rpm prior to the coating application. Different loading ratio of TiO2 nanoparticles specifically, 0.1, 0.2, and 0.3 wt. % were utilized in order to prepare three different systems of epoxy-based nanocomposite coating systems named as ET1, ET2, and ET3, respectively. For this end, the different loading ratios of TiO2 nanoparticles were first introduced to the calculated amount of the cycloaliphatic amine curing agent with the assistance of sonication process for 30 min. Then the epoxy resin was added and the resulting blend was subjected to sonication process for 10 min followed by constant stirring for 15 min at 750 rpm. Better dispersion state of the TiO2 nanoparticles was expected to be achieved by introducing the nanofillers to the curing agent first followed by mixing the resulting blend with the epoxy base resin. This idea was supported by the 2017 work of Pourhashem et al., that reported the efficiency of this method in developing better dispersion of graphene oxide nanosheets within epoxy resin with the presence of polyamide curing agent which is characterized with lower viscosity comparing to epoxy resin (Pourhashem et al., 2017). To further improve the corrosion protection performance and to fulfill the hydrophobicity of the developed coated surfaces, the epoxy resin was modified with PDMS at (9:1) mixing ratio with the presence of 3-aminopropyltriethoxysilane as a coupling agent. Prior to the addition of the curing agent, epoxy resin, PDMS, and a stoichiometric equivalent of 3-aminopropyltriethoxysilane were mixed using a glass rod until the mixture appeared to be homogeneous. Then the resulting blend together with the calculated amount of cycloaliphatic amine curing agent was magnetically stirred for 15 min at 750 rpm and then applied on both sides of cold rolled mild steel substrate as EP coating system. Then, the modified epoxy-PDMS polymeric blend was used as the host matrix for different loading ratios of TiO2 nanoparticles specifically, 0.1, 0.2, and 0.3 wt. % in order to fabricate EPT1, EPT2, and EPT3 nanocomposite coating systems, respectively. The TiO2 nanoparticles and cycloaliphatic amine blends were subjected to 30 min of sonication process prior to the addition of epoxy resin, PDMS and 3-aminopropyltriethoxysilane. The resulting mixtures were then subjected to sonication process for 10 min and mechanical stirring for 15 min at 750 rpm.
Characterization
Fourier Transform Infrared Spectroscopy (FTIR)
Fourier transform infrared spectroscopy (FTIR) was utilized for structural analysis. ATR-Nicolet iS10 Spectrometer from Thermo Fisher Scientific (USA) was used to obtain FTIR transmission spectra with a 32-scan data accumulation between the wavenumber of 400–4,000 cm−1 at a resolution of 4.0 cm−1 was acquired for all recorded spectra.
Differential Scanning Calorimetry (DSC)
The glass transition temperatures (Tg) of all developed coating systems was investigated by differential scanning calorimetry (DSC) using Perkin Elmer DSC800 (USA). The temperature range was varied from 25°C to 300°C with heat rate at 20°C/min under nitrogen condition with flow rate with 20 ml/min.
Field Emission Scanning Electron Microscope (FESEM)
The surface morphology and the dispersion state of the nano TiO2 nanoparticles within the polymeric matrix was investigated by using field emission scanning electron microscopy (FESEM) FEI Quanta 450 FEG equipped with an energy dispersive X-rays analyzer (EDX) for elements mapping. It is worth to be mentioned that the coated steel panels were subjected to the application of a thin layer of a platinum coating before carried out the tests in order to minimize the charging effects.
Atomic Force Microscopy
A Bruker Multimode 8 AFM was employed for topography imaging and to measure the surface roughness of all coating systems. The measurement of the effect of TiO2 nanoparticle in the coating system was conducted in the contact mode equipped with Scan Asyst-Air (Bruker) SPM tip (0.4 N/m spring constant). The 3D 5 μm2 scanned areas were sampled at 769 equidistant points at a low scan rate of 1 Hz.
Ultraviolet-Visible (UV-Vis) Spectroscopy
To determine the photocatalytic effects of the incorporated TiO2 nanoparticles, ultraviolet-visible (UV-vis) spectroscopy was used with UV-3101PC (Shimadzu, Kyoto, Japan) UV-vis spectrometer in transmission mode at a wavelength range of 200–800 nm on medium-speed scanning. The UV-vis spectrometer was set in absorbance mode at the wavelength between 200 and 800 nm range and medium scanning speed. Measurements were carried out on a set of three different replicate coated glass plates.
Contact Angle (CA) Measurement
Contact Angle (CA) measurements were conducted in order to evaluate the wettability of coated surfaced and distinguish the effects of the embedded TiO2 nanoparticles and modification epoxy resin with PDMS on the surface hydrophobicity state. By using Optical Contact Angle 15EC (Germany) instrument, the static contact angles were obtained by placing 5 drops of 9 μL distilled water at five different points on each coating samples with the use of a needle that located close enough to the coated surface to render the kinetic energy of the droplets negligible. Measurements were repeated for three times on three different coated samples. The results in the form of images were captured instantly and the average of five measurements was reported with <1° measurement error.
Electrochemical Impedance Spectroscopy (EIS)
In order to evaluate the anticorrosion performance and the barrier properties for all the developed coating systems, electrochemical impedance spectroscopy (EIS) was employed. The EIS was brought in action using a classical three electrode system consisting of 3 cm2 area of the coated sample exposed to 3.5% NaCl distilled water solution as working electrode, a saturated calomel electrode SCE as a reference electrode and pyrolytic graphite electrode functioning as a counter electrode. All the components and connections were placed inside a Faraday cage to minimize external noise during measurement. Gamry PCI4 G300 potentiostat with 100 kHz−10 mHz frequency range at open circuit potential with a sinusoidal AC perturbation of 10 mV root mean square (rms) potential perturbation was used to perform the tests was utilized to complete the test. All the data obtained from EIS were analyzed by Gamry Echem Analyst of Version 6.03. EIS measurements were found to be reproducible after repeating the tests for three different coated substrates.
Results and Discussion
Fourier Transform Infrared Spectroscopy (FTIR)
Figure 1A shows the FTIR spectra for TiO2 nanoparticles, epoxy resin, and epoxy-TiO2 nanocomposite coating systems. Most of the peaks in the coating systems can be traced back to the epoxy resin. Note that the epoxy resin spectrum in Figure 1A is the uncured epoxy resin.
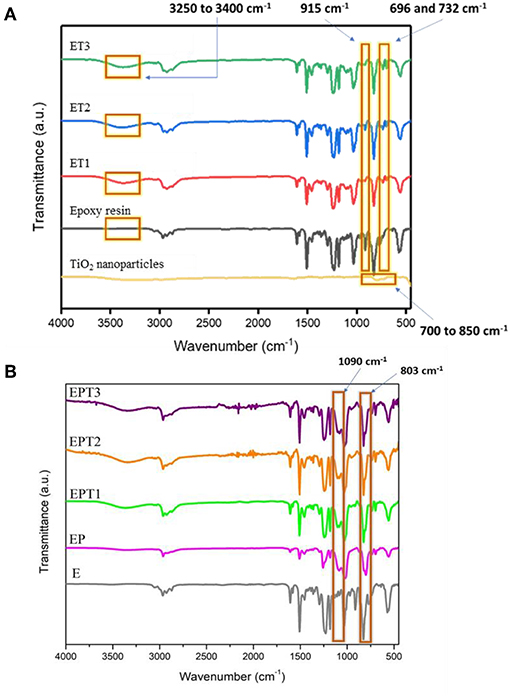
Figure 1. FTIR spectrum for (A) TiO2 nanoparticles, epoxy resin, and all developed epoxy-TiO2 nanocomposite coating systems and (B) for E, EP, EPT1, EPT2, and EPT3 coating systems.
The FTIR spectrum of TiO2 nanoparticle with anatase crystalline structure showed a broad peak at 700–850 cm−1 and was attributed to Ti-O stretching vibration (Vasei et al., 2014). With the incorporation of TiO2 nanoparticles into epoxy resin (ET1, ET2, and ET3), it can be slightly observed on the overlapping peaks that occurred between 700 and 850 cm−1 due to low percentage of TiO2 nanoparticles presence in the epoxy matrix. Compared with epoxy resin spectrum, the absorption band at 696–732 cm−1 varies with the nanocomposites were corresponded to Ti-O-Ti linkages in conjunction with the amine group of curing agent and epoxy matrix. This proves that TiO2 nanoparticles are successfully obtained and incorporated into the organic matrix as the epoxy resin is being cured.
The absorption peak at 915 cm−1 of unmodified epoxy resin indicates the C-O deformation in the epoxide group, however, the decreased in the intensity of the peak at 915 cm−1 in the spectra of cured nanocomposite systems evincing the opening of the epoxide ring during curing reaction. Many studies have reported the curing reactivity of epoxy resin by using amine curing agents (Ansari et al., 2014; Moura et al., 2018). As reported by Ma et al., the curing state of epoxy resin with diamine curing agent at room temperature could be assigned to the disappearance of the absorption peak at 915 cm−1 in the cured neat epoxy (Ma et al., 2017). Also, the emergence of a new peak at 3,250–3,400 cm−1 in the cured systems instead of unmodified epoxy resin affirmed the existence of secondary amine, which is due to the stretching of the N-H bond. These peaks further assured the curing agent successfully functioned to cure the coating mixture into a film. This to be said that almost all epoxy resins are converted into insoluble solid film due to the formation of three-dimensional thermoset networks by curing agent during the curing period (Shi et al., 2009; Ma et al., 2017).
Figure 1B depicts the FTIR spectra for unmodified epoxy resin (E), epoxy-PDMS hybrid (EP), and PDMS modified epoxy nanocomposite coating systems which are EPT1, EPT2, and EPT3. Note that 3-Aminopropyltriethoxysilane (3-APS) was used to link between epoxy and PDMS resins, thus, the cross-linking between the two polymers can be observed at some fundamental peaks. With the peaks that originate from the consequences of curing reaction as mentioned earlier still to be seen here, the new emerging peak at 803 and 1,090 cm−1 is ascribed to the stretching of Si-O-Si and Si-C bond which is not seen in the unmodified epoxy resin. This affirmed that PDMS was successfully incorporated with epoxy forming the desired hybrid coating systems. The coupling mechanism between epoxy and PDMS can be divided into two stages where the first stage involves the opening of the epoxide ring to react with the amino group of the 3-APS, where the primary amine tends to transform to the tertiary amine. During the second stage, PDMS tends to react with epoxy by the endorsement of the alkoxy group in 3-APS, forming the final modified epoxy-silicone structure. Moreover, the disappearance of the band 915 cm−1 of the unmodified epoxy spectrum has attributed the opening of the epoxide ring which revealed the intercalation of the curing agent in the epoxy matrix. A similar observation of cured epoxy-PDMS has also been reported by Ammar et al. (2016b). Also form Figure 1B, it can be seen the intensity spectra of EPT1, EPT2, and EPT3 are slightly increased as the amount of TiO2 increased. This to be said that the presence of TiO2 nanoparticle within the hybrid polymer matrices is observable on the overlapping peaks occurred between 700 and 850 cm−1 as in ET systems (Figure 1A). Dan et al. (2018) have reported the possible reason for weak peak appearance which almost invisible on these peaks could be due to the low content of TiO2 filler in the host domain and possibly can be observed at high loading concentration of TiO2, that is, 10 wt.%.
Differential Scanning Calorimetry (DSC)
The DSC thermographs of E, EP, and all TiO2 nanocomposite coating systems were illustrate in Figures S1–S8. Moreover, the glass transition temperatures (Tg) values were tabulated in Table 1. A single glass transition temperature was observed in all reported thermographs which indicate the good curing state of the coating films and the proper crosslinking among the coating components (Radoman et al., 2014; Ammar et al., 2016b). However, the changes in the Tg values could be utilized as an indicator that illustrates the influences of PDMS and TiO2 nanoparticles on the cross-linked structure of the epoxy polymeric matrix. As tabulated in Table 1, the incorporation 0.1 wt. % of TiO2 nanoparticles within the epoxy polymeric matrix had the most pronounced effect on the Tg value which increased from 127.9°C for neat epoxy coating system to ~144°C ET1. Similar observations were reported by Radoman et al. (2015), who claimed that the epoxy resin is able to exhibit higher Tg values when it reinforced with TiO2 nanoparticles due to the role of these particles in reducing the segments mobility at the nanoparticles-epoxy interfaces by the presence of physical attractive interactions.
Apart from that, further increasing the concentration of TiO2 nanoparticles within the epoxy host matrix did not result in higher Tg values, contrarily, relatively lower Tg values, comparing to ET1 coating system, were recorded for ET2 and ET3 systems. This reduction in the Tg values could be ascribed to the insufficient dispersion of TiO2 nanoparticles and its tendency to agglomerate and cluster at the high concentrations. This trend of the nanoparticles physically hinders the curing process of the coating system by blocking the formation of the continuous crosslinked network, hence, increasing the free volume and the mobility of the segments (Polizos et al., 2011; Kumar et al., 2016).
On the other hand, modifying the epoxy resin with PDMS has also influence the glass transition temperature of the resultant coating system which recorded an increment in the Tg value at 134.3°C. This was found in good correlation with FTIR results and further confirmed the good crosslinked structure among epoxy and PDMS resin. The effects of the TiO2 nanoparticles on the thermal properties of the PDMS-epoxy polymeric matric were found to be similar to their influences to the neat epoxy polymeric matrix as the coating system with 0.1 wt. % of TiO2 loading ratio, EPT1, demonstrated the highest Tg value. Whereas, higher concentrations of TiO2 nanoparticles reduce the Tg values due to the agglomeration tendency of the nanoparticles.
Surface Morphology
In order to examine the dispersion state of the embedded TiO2 nanoparticles within the epoxy polymeric matrix, FESEM, and EDX techniques were utilized and the recorded images were illustrated in Figure 2. In addition to studying the distribution of the nanoparticles within the surface area, the surface properties, and phase distribution can be evaluated via FESEM. Moreover, the EDX mapping helps on gaining more understanding about the element distribution in the coating film and investigating the dispersion state of TiO2 nanoparticles at the specimen surface. All developed epoxy-based nanocomposite coatings demonstrated surfaces free of microcracks or phase separation which is clear evidence on the effectiveness of the curing process. Moreover, the vital role of the sonication process was observed in all FESEM images that revealed a good dispersion of the nanoparticles. Due to the attraction among the nanoparticles and its tendency to form relatively larger agglomerated particles, the agglomeration increases as the TiO2 nanoparticle loading ratio exceeds 0.1 wt. %. Moreover, the proper dispersion state of TiO2 nanoparticles was further confirmed by EDX mapping results which illustrate the distribution of Ti element on the coated surfaces. In addition, the surface morphology of the TiO2 nanocomposite coatings that developed after modifying the epoxy host matrix with PDMS resin was investigated and the FESEM and EDX images were illustrated in Figure 3. Surface free of cracks and phase separation confirms the compatibility of the coating components and the good curing level of the coating films. However, it was noticed that as the loading ratio of the TiO2 nanoparticles increase, larger clusters were observed in the FESEM images especially for EPT3 coating systems. That could be attributed due to the tendency of the nanoparticles to agglomerate at the high loading ratio and to the increase of the particles amount within the unit area. EDX mapping images were also collected for this set of samples and the results reveled the existence of well-dispersed Ti element within the coating film which is considered as a clear evidence on the appropriate introduction of TiO2 nanoparticles within the hybrid PDMS-epoxy polymeric matrix.
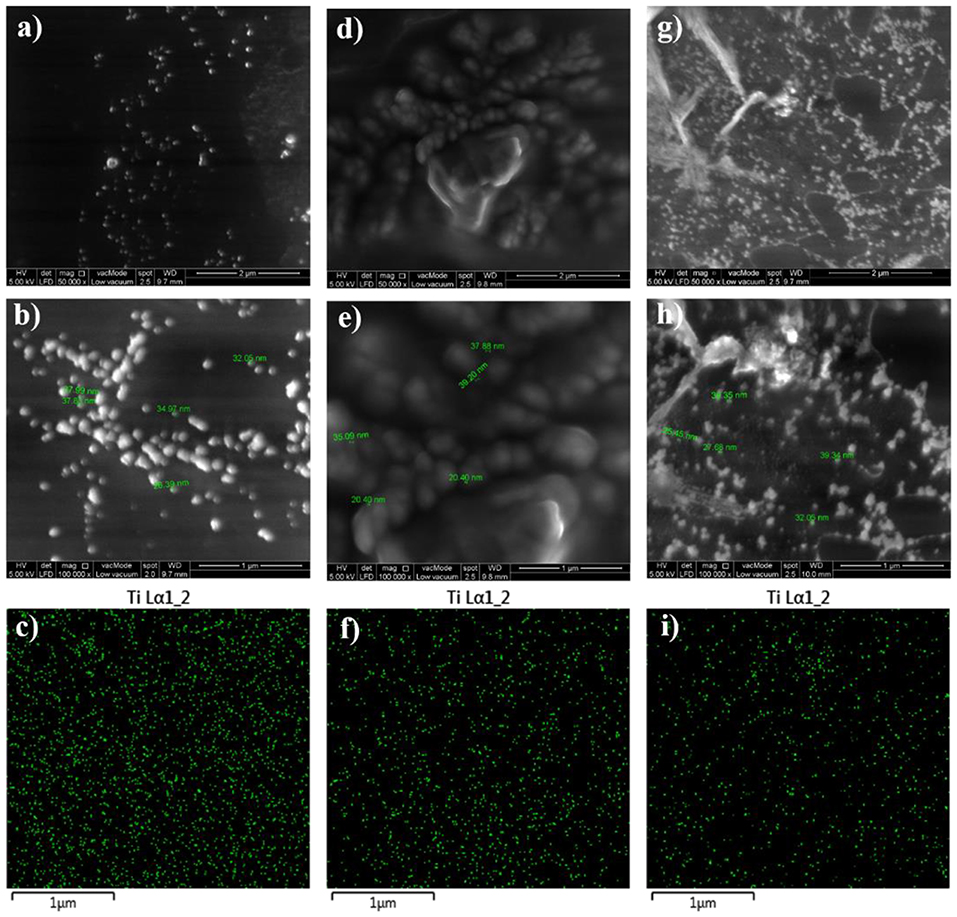
Figure 2. FESEM images at x50000 and x100000 magnifications together with EDX mapping images for ET1 (a–c), ET2 (d–f), and ET3 (g–i).
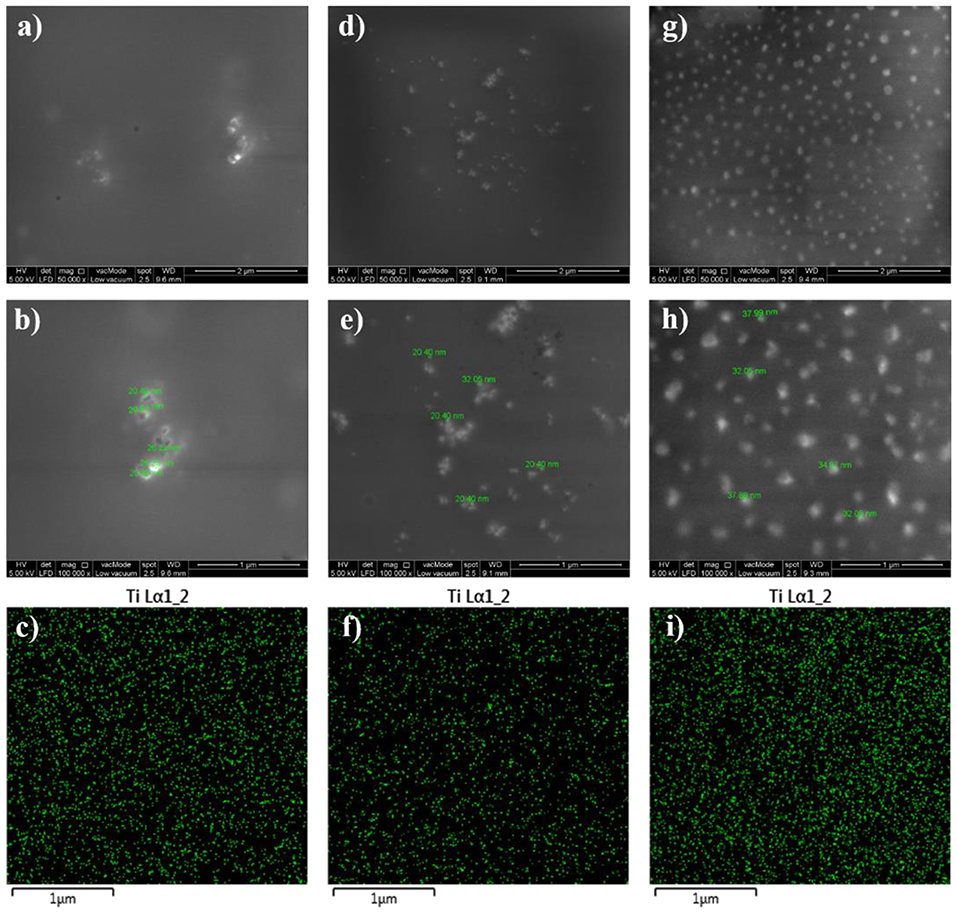
Figure 3. FESEM images at x50000 and x100000 magnifications together with EDX mapping images for EPT1 (a–c), EPT2 (d–f), and EPT3 (g–i).
Atomic Force Microscopy (AFM)
The topological properties of the developed coating systems and the changes in the surface roughness were investigated by means of AFM. Figure 4 illustrates the 3 D topographical images of neat epoxy and all developed epoxy-TiO2. nanocomposite coating systems. The AFM result of the neat epoxy coating system revealed a root mean square height (Sq) equal to 15.5 nm, whereas, Sq values at 2.5, 3.6, and 10.2 nm were recorded to ET1, ET2, and ET 3 coating systems, respectively. The high surface roughness of the neat epoxy coating system could be attributed to the solvent evaporation during the curing period of the epoxy coating film which led to the formation of some holes that reduces the surface evenness (Dan et al., 2018). In contrary, a significant reduction on the surface roughness was realized after the incorporation of TiO2 nanoparticles within the epoxy polymeric matrix especially for 0.1 and 0.2 wt. % loading ratios. That, in turn, could be considered as strong evidence on the proper dispersion state of the nano TiO2 particles and the efficiency of the sonication process in developing a good level of dispersion state and further improving the cross-linked structure by releasing the trapped solvent from the nano-polymeric blend. However, higher surface roughness was recorded with the application of the ET3 coating system due to tendency of the TiO2 nanoparticles to agglomerate at the higher loading ratio, therefore, increasing the cluster size of the particles (Goyat et al., 2018).
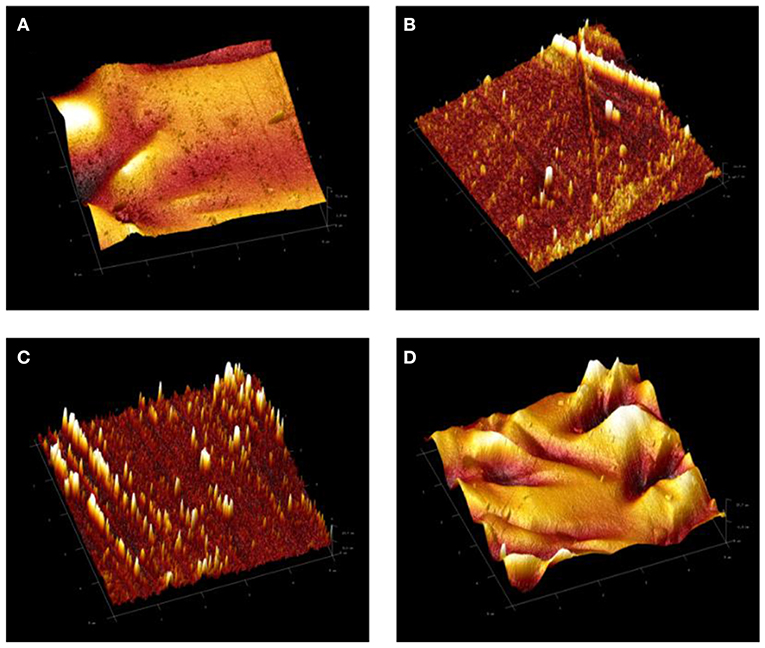
Figure 4. 3D atomic force microscopy (AFM) images of (A) neat epoxy, E, coating system and (B) ET1, (C) ET2, and (D) ET3 epoxy-TiO2 nanocomposite coating systems.
The influences of modifying the epoxy base resin with PDMS, with and without the presence of TiO2 nanoparticles, on the surface roughness of the resultant coated surfaces was also investigated by means of AFM and the findings in the form of 3 D topographical images were illustrated in Figure 5. Sq values of 5.8, 5.6, 4.1, and 12.6 nm were recorded for EP, EPT1, EPT2, and EPT3 coating systems, respectively. Comparing the Sq value of neat epoxy coating system, the addition of the PDMS has significantly reduced the roughness which could be corresponded to the greater level of crosslinking with the achievement of the better curing process. This observation was found in strong agreement with FTIR results and further confirm the compatibility among epoxy and PDMS resins. In the case of the addition 0.1 and 0.2. wt. % TiO2 nanoparticles within the PDMS modified epoxy matrix, the AFM results did not show considerable alterations among the surface roughness which indicate the good dispersion state. However, increasing the loading ratio up to 0.3 wt. % led to change the nature of the surface toward more roughness due to the existence of a greater number of TiO2 nanoparticles within the unit area, therefore, agglomeration formation.
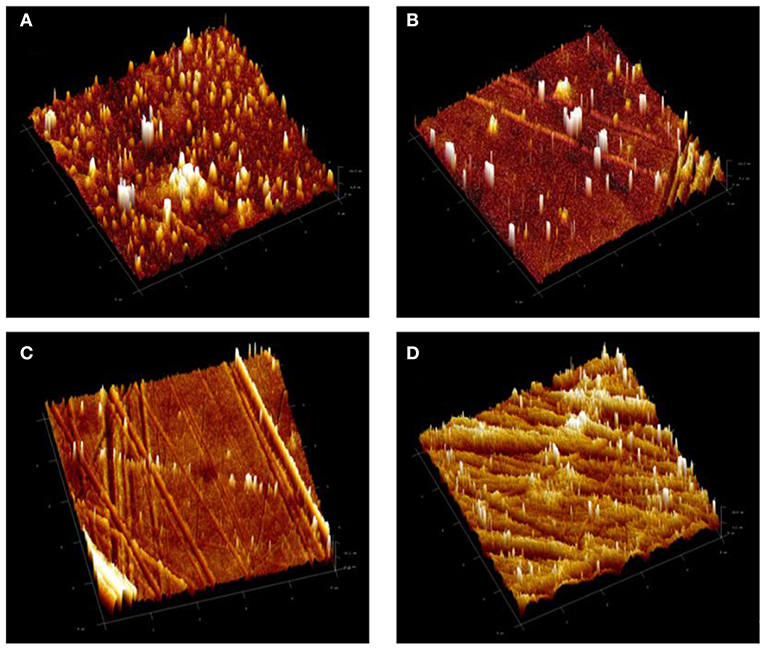
Figure 5. 3D atomic force microscopy (AFM) images of (A) PDMS modified epoxy, EP, coating system and (B) EPT1, (C) EPT2, and (D) EPT3 PDMS modified epoxy-TiO2 nanocomposite coating systems.
Ultraviolet-Visible (UV-Vis) Spectroscopy
Ultraviolet-visible (UV-vis) spectroscopy was used to determine the optical properties of TiO2 nanoparticles within the epoxy polymeric matrix. Figure 6 shows the UV-vis absorbance spectra of all developed coating systems. As TiO2 have a wide bandgap between valence and conduction band of 3.2 eV, it tends to absorb shorter wavelength with high energy to excite its electron (Pugachevskii, 2013), typically at the UV range below 400 nm where it does not have a specific peak within this region (Gouda and Aljaafari, 2012; Karkare, 2014; Rathod and Waghuley, 2015). Therefore, when TiO2 nanoparticles have been incorporated within the epoxy coating, it tends to broaden the absorption region of the epoxy and significantly enhance the existing absorption intensity at around 250 nm, which is also within the TiO2 absorption range. It can be seen that the absorption at UV range is enhanced with the incorporation of TiO2 nanoparticles. However, as the loading ratio of incorporated TiO2 nanoparticle increased, the UV absorption intensity at around 250 nm shows a lowering trend, this is due to the fact that UV-vis absorbance highly depends on the TiO2 particle size (Kormann et al., 1988; Gutierrez et al., 2008). The lowering of the absorbance intensity arises from composites' cluster morphology. The absorption intensity of all coating system developed using epoxy-PDMS hybrid polymeric matrix namely, EP, EPT1, EPT2, and EPT3 is lower compared to neat epoxy coating. This can be attributed due to the formation of intercalation network among the two polymers and changed the conformational structure of neat epoxy coating. However, when the TiO2 nanoparticles were embedded within the epoxy-PDMS hybrid matrix, broadening, and increasing of absorption intensity at the same wavelength peak observed as the amount of TiO2 nanoparticles increased. This observation can further confirm that TiO2 nanoparticle tends to enhance the UV absorption within their active absorption region. Due to its light-respond capability, it can be suggested on the future work that the presence of TiO2 nanoparticle in coating development can improve the photogenerated cathodic protection of metals and might help from discoloration of coating product under UV illumination.
Contact Angle (CA) Measurement
Water contact angle measurements (CA) were carried out for all prepared coating systems in order to investigate the wettability state of the developed coated surfaces and to determine the roles of the incorporated PDMS resin and the embedded TiO2 nanoparticles in manipulating the wettability characters of epoxy-based coatings. Table 2 tabulate all contact angle values with its correspondent drop image at the respective coating surfaces. The hydrophilic nature of the epoxy coatings was confirmed as the substrate coated with the E coating system demonstrated a CA value equal to ~63°. The introducing TiO2 nanoparticles within the epoxy polymeric matrix was able to enhance the wettability of the coating film toward more hydrophobicity. However, as the surface is characterized as a hydrophobic surface when the contact angle values reach or exceed 90°, none of the utilized loading ratios of TiO2 nanoparticles has resulted in that. Despite that, an increase of ~14° in the CA values was gained by the surface coated with the ET1 coating system further confirm the excellent dispersion state of the 0.1 wt. % TiO2 nanoparticles among the epoxy matrix. This observation could be attributed due to the fact that the existence of the appropriate amount of inorganic nanoparticles within the polymeric based coating system could alter the surface roughness and results in more hydrophobicity (Park et al., 2014). It was interesting to note that CA results were found to be in strong agreement with AFM findings as the substrate coated with E coating systems shows a higher value of surface roughness. This explains the lower contact value of neat epoxy coating system since the rougher surface area will lead to the spreading of the water droplet among the grooves (Asadi et al., 2019). While the incorporation of TiO2 nanoparticles, with the assist of the sonication process, resulting in a lower degree of surface roughness, hence, shifting the wettability state toward more hydrophobic nature (Vázquez-Velázquez et al., 2018). It is worth mentioning that no further improvement was realized with the application of ET2 and ET3 coating systems due to the tendency of the nanoparticles at the higher loading rates to agglomerate and affect the bulk properties rather than the surface characteristics (Ramezanzadeh et al., 2011).
A hydrophobic surface was recorded after the application of EP coating with CA value almost reached 100°. This result was in complete agreement with finding reported by many researchers who proved the ability of PDMS resin to enhance the hydrophobicity of epoxy coatings due to its low surface energy (Eduok et al., 2017). The highest CA value obtained by EPT1 coating system which further confirms the compatibility among the coating components, the good cross-linked structure of the coating film and proper dispersion of TiO2 nanoparticles with the hybrid epoxy-PDMS polymeric matrix.
Electrochemical Impedance Spectroscopy (EIS)
Electrochemical impedance spectroscopy was performed to investigate the effects of adding different loading ratios of TiO2 nanoparticles on the barrier properties and the corrosion protection performance of the epoxy-based coating systems. Moreover, EIS was also utilized to investigate the role of PDMS in improving the electrochemical behavior of epoxy coating and epoxy-TiO2 nanocomposite coating against corrosion. After exposing the coated samples to 3.5% NaCl solution, the EIS measurements were carried out periodically and the collected results were presented graphically with Bode and Nyquist plots after 1 and 30 days of immersion time.
To explain the electrochemical behavior of all developed coating systems after different periods of immersion time, two models of the equivalent circuits were utilized and illustrated in Figure 7. As the exposure time elapsed, the electrolyte attempted to penetrate through the coating film toward the coating—substrate interface causing the initiation of the corrosion reaction. However, the corrosion protection obtained by the coating film at this stage could be understood by analyzing the electrochemical response with the assist of Model A of the equivalent circuit which composes of the following elements: a resistor Rpo and a constant phase element (CPEpo), which describes the electrolyte resistance through the film pores, and its associated (CPEpo). Also, this model includes a parallel combination of a resistor which represents the charge transfer resistance (Rct) and constant phase element as the double layer capacitance (CPEdl). The aforementioned components represent the resistance obtained by the coating film against the corrosion reaction. In order to distinguish the coating systems that are unable to withstand corrosion and failed in isolating the substrate's surface to be in direct contact with the penetrated electrolyte, Model B of the equivalent circuit was introduced. In addition to the previous elements that used to build up Model A, new constant phase element and resistor were added to Model B namely constant phase element of corrosion products diffusion capacitance (CPEdiff) and corrosion products diffusion resistance (Rdiff). Hence, by mean of Model B, the resistance obtained by the coating film against the diffusion of the corrosion products from the substrate active sites at the coating-substrate interface could be represented. It is worth mentioning that both proposed equivalent circuit models include a resistor element Rs which serves as the solution resistance and had no significant technical or theoretical information about the developed coating systems, therefore, it was not included in this study (Ammar et al., 2016c).
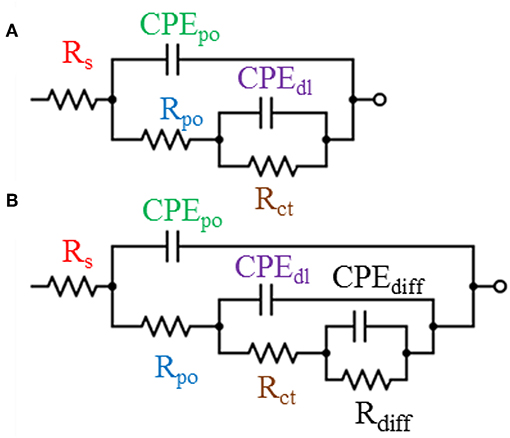
Figure 7. The equivalent circuit models used to perform the fitting for EIS graphs and (A,B) represent the designations of the models that used.
Figure 8 illustrates the Bode and Nyquist plots for neat epoxy and all developed epoxy-TiO2 nanocomposite coating systems after 1 day of immersion time. Even after this short period of exposure, the poor barrier properties and weak corrosion protection performance was obvious for E coating system as two-time constants and corresponded two semicircles was observed in Bode and Nyquist pots, respectively. Model B of the equivalent circuit was found to obtain the best numerical fitting for the EIS data which further indicates the initiation of the corrosion process and the formation of the corrosion products that cause the delamination of the coating film from the metal substrate. Similar observations were published by Pourhashem et al., who have investigated the corrosion protection performance of epoxy-based coating systems applied to mild steel substrates. The reported results indicate the poor barrier properties of neat epoxy coating system after only 1 day of exposure time to 3.5% NaCl electrolyte even when it is applied at a larger thickness up to 150 ± 10 μm (Pourhashem et al., 2017). Moreover, the weak corrosion protection performance of epoxy based coating systems after such a short period of immersion time was reported by several researchers who studied the performance of neat epoxy coating films that applied with different thickness specifically at 120 μm (Chang et al., 2014), 130 μm (Li et al., 2015), and 250 μm (Wang et al., 2018).
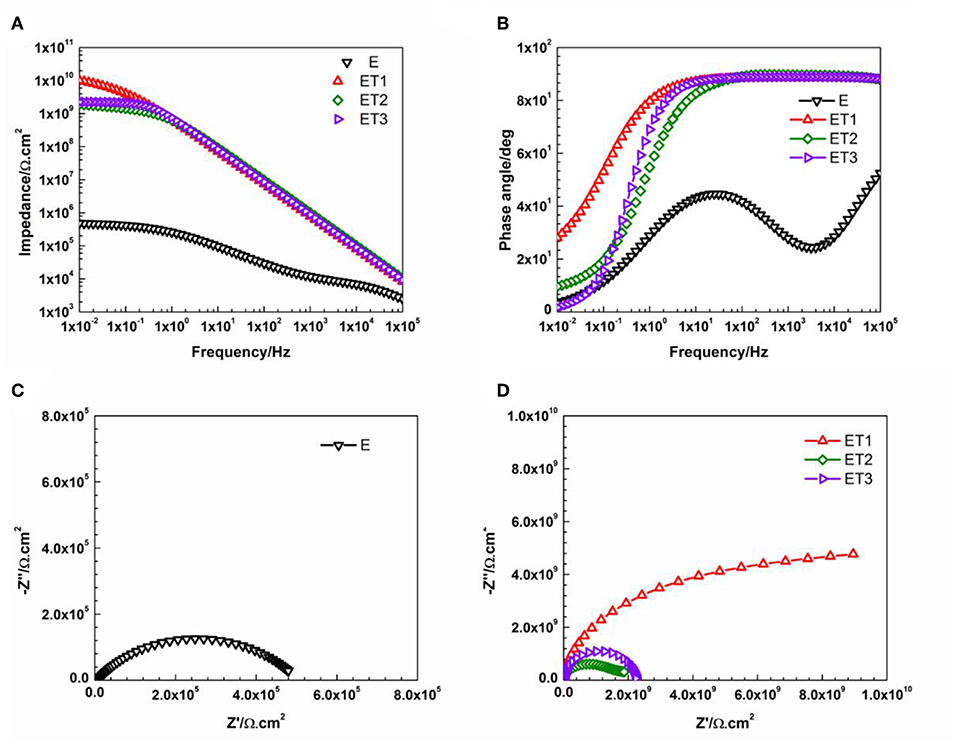
Figure 8. Representative (A) Bode plots and (B) phase angle plots for all prepared epoxy-based coating systems, (C) Nyquist plot for E coating system, and (D) Nyquist plots for all epoxy-TiO2 nanocomposite coating systems after 1 day of immersion.
However, the incorporation of different loading rates of TiO2 nanoparticles within the epoxy polymeric matrix has significantly enhanced the barrier properties of the coating films as only a slight bending of the Bode plots at the low-frequency region, as well as, one semicircle in the Nyquist plots which both fitted with model A of the equivalent circuit. These findings could be attributed to the vital role of the incorporated TiO2 nanoparticles in modifying the network structure of the epoxy polymeric matrix where the embedded nanoparticles contributed in reorganizing the polymeric matrix by the physical interactions due to Van Der Waal's force that helps in closing up the pores of the epoxy matrix, hence, forcing the penetrated electrolyte to travel a longer distance in order to reach the substrate surface and lead to the corrosion reaction initiation (Ramezanzadeh et al., 2016b; Basiru et al., 2018). However, as the immersion time elapsed and reached 30 days, only ET1 coating system which loading with 0.1 wt. % of TiO2 nanoparticles manage to obtain performance stability and perfectly protect the steel substrate from being corroded. The observation of Bode and Nyquist plots of ET1 coating systems, illustrated in Figure 9, interestingly demonstrated no changes over the immersion time period and still holding the ability to be fitted by means of Model A of the equivalent circuit. This, in turn, implied that this small amount of TiO2 nanoparticles was sufficient to enhance the overall performance of the coating film as the EIS finding was in strong agreement with all previously reported results.
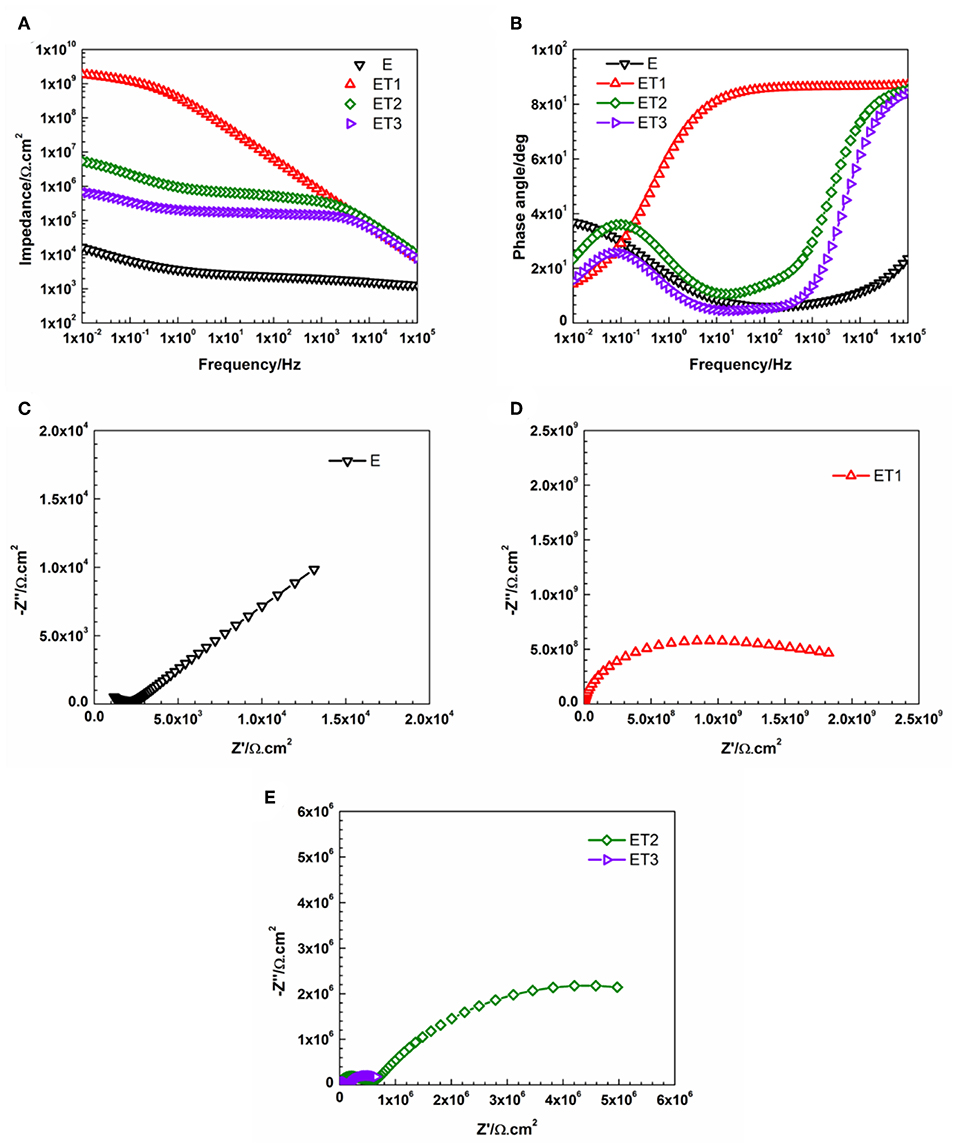
Figure 9. Representative (A) Bode plots and (B) phase angle plots for all prepared epoxy-based coating systems, (C) Nyquist plot for E coating system, (D,E) Nyquist plots for all epoxy-TiO2 nanocomposite coating systems after 30 days of immersion.
On the other hand, all other developed coating systems namely, E, ET2, and ET3, failed to obtain the desired protection performance against corrosion as two-time constants in Bode plots and two semicircles in Nyquist plots were observed and Model B of the equivalent circuit was utilized to obtain the fitting. The poor corrosion protection performance of E coating system could be attributed to the weak barrier properties of the epoxy polymeric matrix due to the presence of voids at the coating film surface and pores through the bulk structure of the coating layer. Yi et al. (2018) reported that the creation of the voids and the pores is due to the evaporation of the solvent during the curing process and the shrinkage of the coating layer. Moreover, the existence of these pores increases the free volume within the epoxy polymeric matrix and consider the main responsible of the creation of the diffusion pathways that permit the corrosive agents to penetrate through the coating film, hence, the degradation of the corrosion protection ability (Ramezanzadeh et al., 2016a). The most pronounced effect of TiO2 nanoparticles was realized with its loaded at 0.1 wt. %, within ET1 coating system. That could be attributed to the proper dispersion of the nano reinforcing agents within the polymeric matrix, hence, reducing the porosity and zigzagging the diffusion pathway. However, the EIS findings revealed that the further addition of TiO2 nanoparticles did not significantly enhance the corrosion protection performance of the polymeric matrix. The 2016 work of Kumar et al., discuss the effects of different concentrations of TiO2 nanoparticles on the epoxy matrices and have concluded that the higher loading ratios of TiO2 could affect its dispersion state and led to the formation of larger clusters, hence, alter the contact among the nanoparticles and the epoxy matrix and narrow their interaction that is essential for the interfacial adhesion (Kumar et al., 2016). Furthermore, the numerical values of all parameters that have been obtained by fitting the EIS data of E coating system and all epoxy-TiO2 nanocomposite coating systems after 1 and 30 days of immersion time with its respective equivalent circuit models were tabulated in Tables S1, S2, respectively.
Recently, several studies confirmed the development of better corrosion protection performance of polymeric based coating systems that possess hydrophobic nature (Huang et al., 2019; Zhang et al., 2019; Zhu et al., 2019). Therefore, the wettability of the developed coated surfaces become to be considered as one of the indicators about the corrosion protection ability of the coating system. In this study, attempts have been made to enhance the hydrophobicity by modifying the epoxy base resin with PDMS. From Figures 10, 11, which represent the Bode and Nyquist plots of E, EP and all PDMS modified epoxy nanocomposite coating systems after 1 and 30 days of immersion time, respectively, it can be seen that utilizing PDMS resin as a modifier have enhanced the barrier properties of the coating film and ensure the performance stability of the coating system over the whole periods of immersion time. Even though the EIS data for EP coating system was found to be perfectly fitted with Model A of the equivalent circuit after 1 and 30 days of immersion time, but the bending of the Bode plot at the high-frequency region and the small diameter of the semicircle in the Nyquist plot indicate a fair corrosion ability. Similar observations were reported by Ammar et al. who utilized the breakpoint frequency concept to the analysis the stability of the epoxy-PDMS hybrid coating system and concluded with that fact that as the immersion time elapsed, larger resistive region and relatively smaller capacitive region are observed in the area under the Bode plot which resulted from the shifting of the breakpoint frequency values toward the higher frequencies region, hence a reduction of the barrier properties of the coating film is occurring (Ammar et al., 2017).
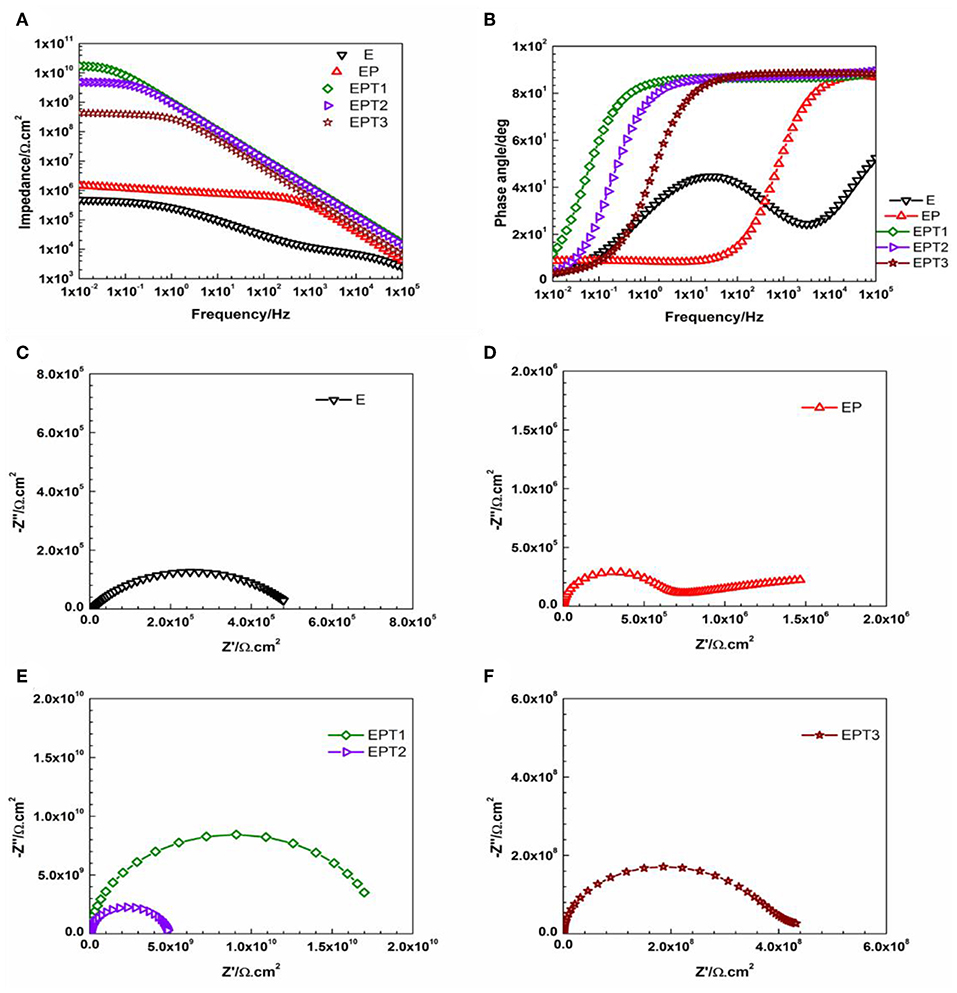
Figure 10. Representative (A) Bode plots and (B) phase angle plots for E, EP, and all PDMS modified epoxy nanocomposite coatings, and Nyquist plots for (C) E, (D) EP, (E) EPT1 and EPT2, (F) EPT3 coating systems after 1 day of immersion.
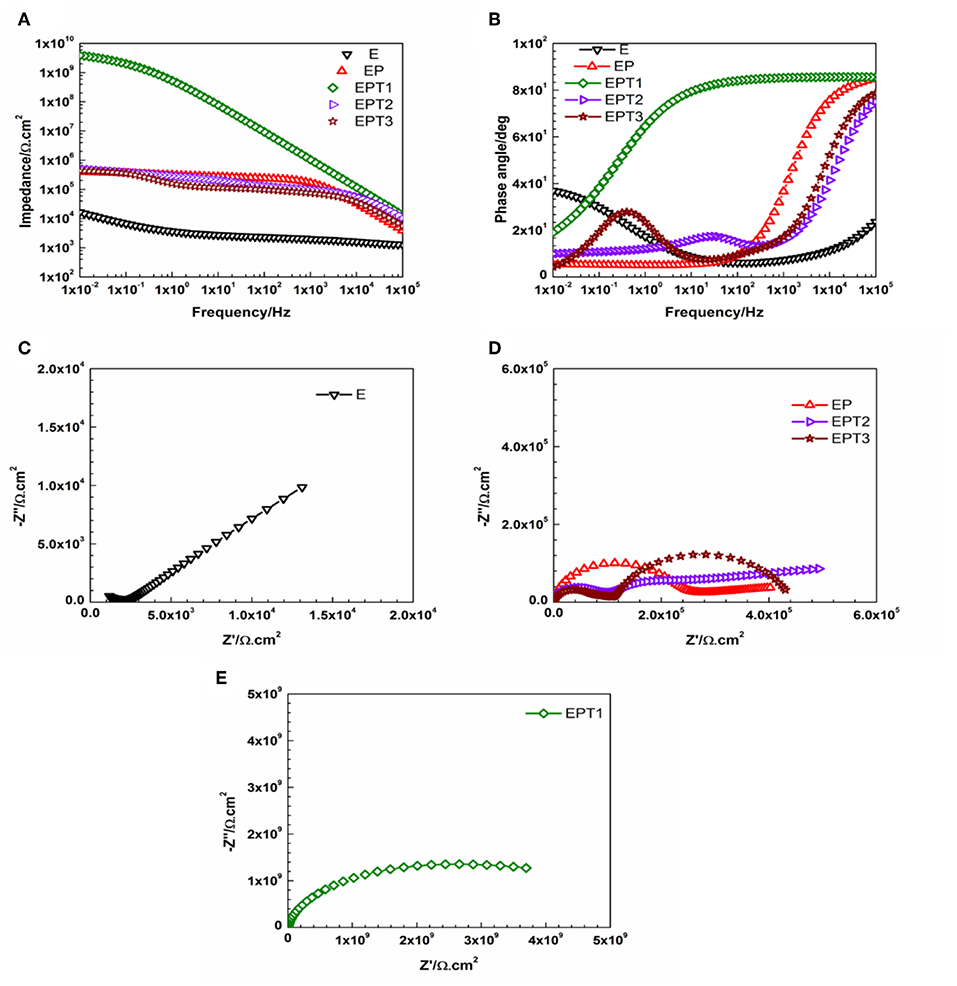
Figure 11. Representative (A) Bode plots and (B) phase angle plots for E, EP, and all PDMS modified epoxy nanocomposite coatings, and Nyquist plots for (C) E, (D) EP, EPT2, and EPT3, (E) EPT1 coating systems after 30 days of immersion.
Among all developed EP nanocomposite coating systems, the most pronounced enhancement was recorded for EPT1 coating system as a Bode plot with slight bending at the low-frequency region and Nyquist plot with one semicircle after 1 and 30 days of immersion time indicate the capacitive behavior and the stability of the coating film over the whole period of exposure without any significant signs for coating deterioration or loss of the intact barrier properties. Model A of the equivalent circuit was used to obtain the numerical fitting for both EIS graphs after 1 and 30 days of immersion time. Furthermore, it was interesting to notice that 0.1 wt. % of TiO2 nanoparticles was found to be the optimum loading ratio that results in the best corrosion protection performance for both utilized polymeric matrices namely, neat epoxy and PDMS modified epoxy matrix. Apart from that, more stability against corrosion was realized for EPT1 coating system with higher impedance values over the whole periods of immersion. This could be attributed due to the role of the PDMS modifier in obtaining the hydrophobicity to the coating film. The relation among the hydrophobic character of the coated surface and its barrier properties could be explained as increasing the hydrophobicity will lead to minimizing the areas of the surface that are in direct contact with the aqueous electrolyte solution, hence, reducing the electrolyte absorption within the coating film and enhance its barrier properties. Moreover, the existence of good dispersed TiO2 nanoparticles within the PDMS modified epoxy marix magnified the protection obtained by the coating film against the pentation of the electrolyte toward the coating—substrate interface by filling up the matrix pores and zigzagging the diffusion pathways (Ammar et al., 2016a). However, as in epoxy-TiO2 nanocomposites that mentioned above, further increasing the loading ratio of TiO2 nanoparticles up to 0.2 and 0.3 wt. % did not show any additional improvement to the corrosion protection performance which could also attributed to the tendency of the nanoparticles to agglomerate at the high loading ratios. Furthermore, the numerical values of all parameters that have been obtained by fitting the EIS data of E, EP, and all PDMS modified epoxy nanocomposite coating systems after 1 and 30 days of immersion time with its respective equivalent circuit models were tabulated in Tables S3, S4, respectively.
In the ideal coating system, the applied layer covers the enter surface area of the specimen and acts as a perfect capacitor. However, as the electrolyte penetrates and reaches the substrate, it tends to settle in the microporous at the coating-substrate interface and leads to promote the corrosion process. Hence, the performance at these spots is considered as a resistive behavior. Therefore, analyzing the areas under the bode plot and its interpretations, with the assist of breakpoint frequency values, could play a vital role in obtaining a better understanding of corrosion processes at the coating—substrate interfaces and its implications for film delamination and loss of adhesion that lead to the degradation of the protection system. Zhang et al. (2007) have investigated the delamination of TiO2-epoxy nanocomposite coating system based on the relation suggested by Hirayama and Haruyama (1991):
Where, S is the ratio of delaminated area to the original area, ρ is the coating resistivity and ε is the dielectric constant. Hence, the breakpoint frequency and its changes over the different period of immersion time for a giving coating system is proportional to the delaminated area. To that end, the impedance and phase angles values were plotted as functions to their frequencies. After that, the intersection of the breakpoint frequency (fb), which is defined as the frequency at 45° phase angle, with the impedance curve was considered to distinguish the different areas under the Bode plots.
With respect to the immersion time, the performance of the applied coatings could be evaluated based on the regions under the Bode plot. An intact character of the coating system is realized when the phase angle remains higher than 45° over the whole tested frequency range the area under the Bode plot is recognized as a capacitive region. While in the case of observing two areas under the Bode plot namely, capacitive and resistive regions, coating film undergoing corrosion is considered (Javidparvar et al., 2019). The failure of the coating system is confirmed when only a resistive region is observed below the Bode plot. Figures 12A–D illustrate the areas under Bode plot for E and ET1 coating systems based on its fb values after 1 and 30 days of immersion. While the plots of ET2 and ET3 were illustrated in Figures S9, S10. Figure 12A shows both capacitive and resistive areas under the Bode plot of the E coating system after 1 day of immersion time. As the immersion time elapsed, only the resistive region was observed in Figure 12B which further indicates the poor corrosion protection performance of neat epoxy coating system. Apart from that, the incorporation 0.1 wt. % of TiO2 nanoparticles within the epoxy polymeric matrix has significantly enhanced the barrier properties of the coating film as the lower value of breakpoint frequency was recorded, hence, relatively smaller resistive regions in the low-frequency range and larger capacitive regions are observed in Figures 12C,D. No further improvement was realized with increasing the TiO2 concentrations within the epoxy polymeric matrix as higher fb values and increased size of the resistive regions over the capacitive regions were recorded in Tables S1, S2 and Figures S11, S12.
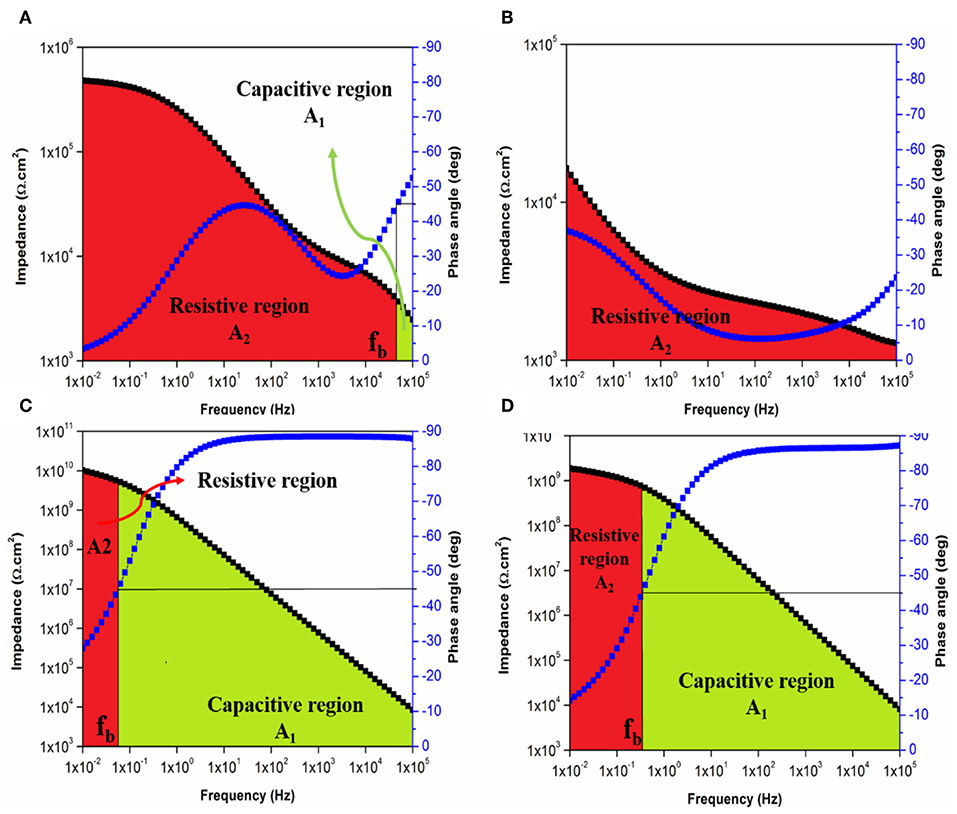
Figure 12. Bode plot with breakpoint frequency determination of E coating system after (A) 1 day and (B) 30 days and of ET1 coating system after (C) 1 day and (D) 30 days of immersion with the corresponding capacitive (A1) and resistive (A2) regions.
In the same manner, the influences of PDMS on the TiO2-epoxy nanocomposite coating systems were discussed by means of breakpoint frequencies and the areas under Bode plots were illustrated in Figures 13A–D for EP and EPT1 coating systems. Whereas, Figures S11, S12 show the areas under bode plots of EPT2 and EPT3, respectively. Comparing to the neat epoxy coating system, modifying the epoxy resin with PDMS has resulted in shifting the fb values toward the lower frequency region, therefore, increases the size of the capacitive region over the resistive region as observed in Figures 13A,B. The most pronounced improvement was realized, in Figure 13C, for EPT1 coating system as the lowest fb values, the largest capacitive region and smallest resistive region were recorded after 1 day of immersion time. Moreover, the remarkable stability of the aforementioned coating system against the initiation of corrosion whereby the coating layer successfully prevented the penetration of corrosive agents was confirmed due to the non-significant changes in the fb values up to 30 days of immersion time. However, no further improvement was recorded as the loading ratio of TiO2 nanoparticles reached 0.2 and 0.3 wt. % due to the tendency of the nanoparticles to agglomerate and form larger clusters.
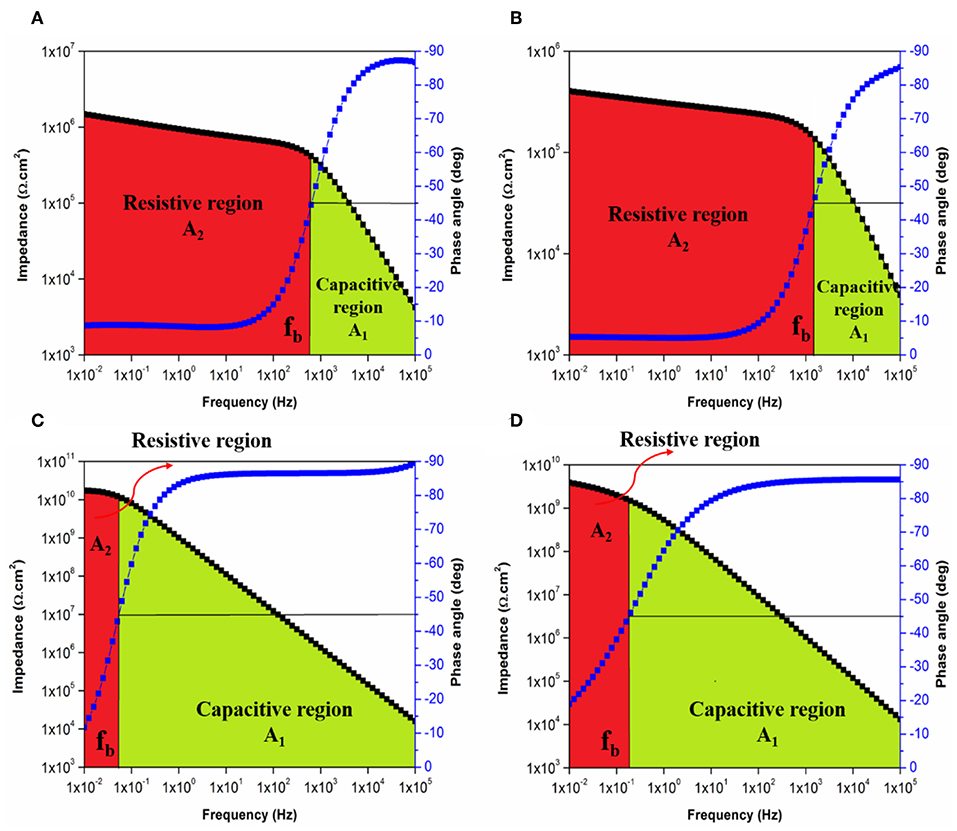
Figure 13. Bode plot with breakpoint frequency determination of EP coating system after (A) 1 day and (B) 30 days and of EPT1 coating system after (C) 1 day and (D) 30 days of immersion with the corresponding capacitive (A1) and resistive (A2) regions.
Conclusion
Different loading ratios of TiO2 nanoparticles were introduced within epoxy resin by the utilization of the solution intercalation method with the presence of the sonication process. Several characterization techniques were employed to evaluate the overall performance of the developed nanocomposite coating systems. FTIR and DSC results revealed the achievement of proper crosslinked structure of the epoxy-based coating systems with the presence of cycloaliphatic amine curing agent and the observation of single glass transition temperature in all recorded thermographs. Moreover, the dispersion state of TiO2 nanoparticles within the epoxy was investigates by FESEM and EDX. The Findings confirmed the efficiency of the sonication process and room temperature curing process in achieving good desperation of TiO2 nanoparticles especially when it is loaded at 0.1 wt. %. The incorporation of TiO2 nanoparticles demonstrated a photocatalytic effect on the coating film as increased the absorbance at UV region. Lower surface roughness, higher CA values and better corrosion protection performance were recorded for all TiO2 nanocomposite coating systems and the most pronouncing effect was realized with the utilization of 0.1 wt. % loading ratio. The reported finding revealed the compatibility of TiO2 nanoparticles to be embedded within the epoxy matrix and its ability to physically interact with the epoxy network resulting in high Tg values and better barrier properties via reducing the porosity and zigzagging the diffusion pathway of the polymeric matrix. Furthermore, PDMS resin was used to modified the epoxy-based resin and the hybrid polymeric matric was used to host different loading ratio of TiO2 nanoparticles. Similiter to epoxy-TiO2 nanocomposites, good curing level with proper dispersion state of TiO2 nanoparticles were recorded with the presence of PDMS modifier. The low surface energy of PDMS resin led to alter the wettability of the epoxy resin toward more hydrophobic character. Moreover, 0.1 wt. % of TiO2 nanoparticles was also confirmed to be the optimum concentration that significantly enhanced the barrier properties and corrosion protection ability of the coating film. Therefore, PDMS resin was confirmed to be a suitable modifier that is able to enhance the hydrophobicity of the resulting coated surfaces without alter the curing level, glass transition temperature, dispersion state and the corrosion protection performance of TiO2-epoxy nanocomposite coating systems.
Data Availability Statement
All datasets generated for this study are included in the article/Supplementary Material.
Author Contributions
AS, CC, and IW prepared the samples, carried out the characterizations, data analysis, and wrote the manuscript. SB and VB assisted in performing the tests and data analysis. RK and RS supervised the overall research work and finalized the manuscript.
Conflict of Interest
The authors declare that the research was conducted in the absence of any commercial or financial relationships that could be construed as a potential conflict of interest.
Acknowledgments
Authors would like to thank the University of Malaya and the Ministry of Education, Malaysia for supporting this study by providing the fundamental research grants FP036-2018A and IIRG007C-19IISS.
Supplementary Material
The Supplementary Material for this article can be found online at: https://www.frontiersin.org/articles/10.3389/fmats.2019.00336/full#supplementary-material
References
Ahmad, S., Gupta, A., Sharmin, E., Alam, M., and Pandey, S. (2005). Synthesis, characterization and development of high performance siloxane-modified epoxy paints. Prog. Org. Coat. 54, 248–255. doi: 10.1016/j.porgcoat.2005.06.013
Ammar, S., Ramesh, K., Ma, I., Farah, Z., Vengadaesvaran, B., Ramesh, S., et al. (2017). Studies on SiO2-hybrid polymeric nanocomposite coatings with superior corrosion protection and hydrophobicity. Surf. Coat. Technol. 324, 536–545. doi: 10.1016/j.surfcoat.2017.06.014
Ammar, S., Ramesh, K., Vengadaesvaran, B., Ramesh, S., and Arof, A. (2016a). Formulation and characterization of hybrid polymeric/ZnO nanocomposite coatings with remarkable anti-corrosion and hydrophobic characteristics. J. Coat. Technol. Res. 13, 921–930. doi: 10.1007/s11998-016-9799-z
Ammar, S., Ramesh, K., Vengadaesvaran, B., Ramesh, S., and Arof, A. (2016b). Amelioration of anticorrosion and hydrophobic properties of epoxy/PDMS composite coatings containing nano ZnO particles. Prog. Org. Coat. 92, 54–65. doi: 10.1016/j.porgcoat.2015.12.007
Ammar, S., Ramesh, K., Vengadaesvaran, B., Ramesh, S., and Arof, A. (2016c). A novel coating material that uses nano-sized SiO2 particles to intensify hydrophobicity and corrosion protection properties. Electrochim. Acta 220, 417–426. doi: 10.1016/j.electacta.2016.10.099
Ansari, F., Galland, S., Johansson, M., Plummer, C. J., and Berglund, L. A. (2014). Cellulose nanofiber network for moisture stable, strong and ductile biocomposites and increased epoxy curing rate. Compos. Part A 63, 35–44. doi: 10.1016/j.compositesa.2014.03.017
Asadi, F., Jannesari, A., and Arabi, A. (2019). Epoxy siloxane/ZnO quantum dot nanocomposites: Model-fitting and model-free approaches to kinetic analysis of non-isothermal curing process. Progr. Org. Coat. 135, 270–280. doi: 10.1016/j.porgcoat.2019.06.006
Atta, A. M., Mohamed, N. H., Rostom, M., Al-Lohedan, H. A., and Abdullah, M. M. (2019). New hydrophobic silica nanoparticles capped with petroleum paraffin wax embedded in epoxy networks as multifunctional steel epoxy coatings. Prog. Org. Coat. 128, 99–111. doi: 10.1016/j.porgcoat.2018.12.018
Basiru, Y., Ammar, S., Ramesh, K., Vengadaesvaran, B., Ramesh, S., and Arof, A. (2018). Corrosion protection performance of nanocomposite coatings under static, UV, and dynamic conditions. J. Coat. Technol. Res. 15, 1035–1047. doi: 10.1007/s11998-017-0038-z
Brusciotti, F., Snihirova, D. V., Xue, H., Montemor, M. F., Lamaka, S. V., and Ferreira, M. G. (2013). Hybrid epoxy–silane coatings for improved corrosion protection of Mg alloy. Corros. Sci. 67, 82–90. doi: 10.1016/j.corsci.2012.10.013
Chang, K.-C., Hsu, M.-H., Lu, H.-I., Lai, M.-C., Liu, P.-J., Hsu, C.-H., et al. (2014). Room-temperature cured hydrophobic epoxy/graphene composites as corrosion inhibitor for cold-rolled steel. Carbon 66, 144–153. doi: 10.1016/j.carbon.2013.08.052
Dan, S., Gu, H., Tan, J., Zhang, B., and Zhang, Q. (2018). Transparent epoxy/TiO2 optical hybrid films with tunable refractive index prepared via a simple and efficient way. Prog. Org. Coat. 120, 252–259. doi: 10.1016/j.porgcoat.2018.02.017
Dolatzadeh, F., Moradian, S., and Jalili, M. M. (2011). Influence of various surface treated silica nanoparticles on the electrochemical properties of SiO2/polyurethane nanocoatings. Corros. Sci. 53, 4248–4257. doi: 10.1016/j.corsci.2011.08.036
Duraibabu, D., Ganeshbabu, T., Manjumeena, R., and Dasan, P. (2014). Unique coating formulation for corrosion and microbial prevention of mild steel. Prog. Org. Coat. 77, 657–664. doi: 10.1016/j.porgcoat.2013.12.002
Eduok, U., Faye, O., and Szpunar, J. (2017). Recent developments and applications of protective silicone coatings: a review of PDMS functional materials. Prog. Org. Coat. 111, 124–163. doi: 10.1016/j.porgcoat.2017.05.012
Evans, P., and Sheel, D. (2007). Photoactive and antibacterial TiO2 thin films on stainless steel. Surf. Coat. Technol. 201, 9319–9324. doi: 10.1016/j.surfcoat.2007.04.013
Fu, G., Vary, P. S., and Lin, C.-T. (2005). Anatase TiO2 nanocomposites for antimicrobial coatings. J. Phys. Chem. B 109, 8889–8898. doi: 10.1021/jp0502196
Gouda, M., and Aljaafari, A. I. (2012). Augmentation of multifunctional properties of cellulosic cotton fabric using titanium dioxide nanoparticles. Adv. Nanopart. 1, 29–36. doi: 10.4236/anp.2012.13005
Goyat, M., Rana, S., Halder, S., and Ghosh, P. (2018). Facile fabrication of epoxy-TiO2 nanocomposites: a critical analysis of TiO2 impact on mechanical properties and toughening mechanisms. Ultrason. Sonochem. 40, 861–873. doi: 10.1016/j.ultsonch.2017.07.040
Guo, J., Yuan, S., Jiang, W., Lv, L., Liang, B., and Pehkonen, S. O. (2018). Polymers for combating biocorrosion. Front. Mater. 5:10. doi: 10.3389/fmats.2018.00010
Gutierrez, J., Tercjak, A., Garcia, I., Peponi, L., and Mondragon, I. (2008). Hybrid titanium dioxide/PS-b-PEO block copolymer nanocomposites based on sol–gel synthesis. Nanotechnology 19:155607. doi: 10.1088/0957-4484/19/15/155607
Heidarian, M., Shishesaz, M., Kassiriha, S., and Nematollahi, M. (2010). Characterization of structure and corrosion resistivity of polyurethane/organoclay nanocomposite coatings prepared through an ultrasonication assisted process. Prog. Org. Coat. 68, 180–188. doi: 10.1016/j.porgcoat.2010.02.006
Heidarian, M., Shishesaz, M., Kassiriha, S., and Nematollahi, M. (2011). Study on the effect of ultrasonication time on transport properties of polyurethane/organoclay nanocomposite coatings. J. Coat. Technol. Res. 8, 265–274. doi: 10.1007/s11998-010-9297-7
Hirayama, R., and Haruyama, S. (1991). Electrochemical impedance for degraded coated steel having pores. Corrosion 47, 952–958. doi: 10.5006/1.3585208
Huang, W., Xiao, Y., Huang, Z., Tsui, G. C., Yeung, K., Tang, C., et al. (2019). Super-hydrophobic polyaniline-TiO2 hierarchical nanocomposite as anticorrosion coating. Mater. Lett. 258:126822. doi: 10.1016/j.matlet.2019.126822
Javidparvar, A. A., Naderi, R., and Ramezanzadeh, B. (2019). Epoxy-polyamide nanocomposite coating with graphene oxide as cerium nanocontainer generating effective dual active/barrier corrosion protection. Compos. Part B Eng. 172, 363–375. doi: 10.1016/j.compositesb.2019.05.055
Karkare, M. M. (2014). “Estimation of band gap and particle size of TiO2 nanoparticle synthesized using sol gel technique,” in 2014 International Conference on Advances in Communication and Computing Technologies ICACACT 2014 (Mumbai: IEEE), 1–5. doi: 10.1109/EIC.2015.7230747
Kormann, C., Bahnemann, D. W., and Hoffmann, M. R. (1988). Preparation and characterization of quantum-size titanium dioxide. J. Phys. Chem. 92, 5196–5201. doi: 10.1021/j100329a027
Kumar, K., Ghosh, P., and Kumar, A. (2016). Improving mechanical and thermal properties of TiO2-epoxy nanocomposite. Compos. Part B Eng. 97, 353–360. doi: 10.1016/j.compositesb.2016.04.080
Kumar, S. A., Alagar, M., and Mohan, V. (2002). Studies on corrosion-resistant behavior of siliconized epoxy interpenetrating coatings over mild steel surface by electrochemical methods. J. Mater. Eng. Perform. 11, 123–129. doi: 10.1361/105994902770344178
Kumar, S. A., Balakrishnan, T., Alagar, M., and Denchev, Z. (2006). Development and characterization of silicone/phosphorus modified epoxy materials and their application as anticorrosion and antifouling coatings. Prog. Org. Coat. 55, 207–217. doi: 10.1016/j.porgcoat.2005.10.001
Kumar, S. A., and Narayanan, T. S. (2002). Thermal properties of siliconized epoxy interpenetrating coatings. Prog. Org. Coat. 45, 323–330. doi: 10.1016/S0300-9440(02)00062-0
Li, P., He, X., Huang, T.-C., White, K. L., Zhang, X., Liang, H., et al. (2015). Highly effective anti-corrosion epoxy spray coatings containing self-assembled clay in smectic order. J. Mater. Chem. A 3, 2669–2676. doi: 10.1039/C4TA06221C
Liao, M., Schneider, A. F., Laengert, S. E., Gale, C. B., Chen, Y., and Brook, M. A. (2018). Living synthesis of silicone polymers controlled by humidity. Eur. Polym. J. 107, 287–293. doi: 10.1016/j.eurpolymj.2018.07.023
Liqiang, J., Xiaojun, S., Weimin, C., Zili, X., Yaoguo, D., and Honggang, F. (2003). The preparation and characterization of nanoparticle TiO2/Ti films and their photocatalytic activity. J. Phys. Chem. Solids 64, 615–623. doi: 10.1016/S0022-3697(02)00362-1
Ma, I. W., Sh, A., Ramesh, K., Vengadaesvaran, B., Ramesh, S., and Arof, A. (2017). Anticorrosion properties of epoxy-nanochitosan nanocomposite coating. Prog. Org. Coat. 113, 74–81. doi: 10.1016/j.porgcoat.2017.08.014
Matin, E., Attar, M., and Ramezanzadeh, B. (2015). Investigation of corrosion protection properties of an epoxy nanocomposite loaded with polysiloxane surface modified nanosilica particles on the steel substrate. Prog. Org. Coat. 78, 395–403. doi: 10.1016/j.porgcoat.2014.07.004
Mohamad Saidi, N., Shafaamri, A. S., Wonnie Ma, I. A., Kasi, R., Balakrishnan, V., and Subramaniam, R. (2018). Development of anti-corrosion coatings using the disposable waste material. Pigment Resin Technol. 47, 478–484. doi: 10.1108/PRT-03-2018-0030
Moura, J. H. L., Heinen, M., da Silva, R. C., Martini, E. M., and Petzhold, C. L. (2018). Reinforcing anticorrosive properties of biobased organic coatings through chemical functionalization with amino and aromatic groups. Prog. Org. Coat. 125, 372–383. doi: 10.1016/j.porgcoat.2018.09.021
Park, E. J., Yoon, H. S., Kim, D. H., Kim, Y. H., and Kim, Y. D. (2014). Preparation of self-cleaning surfaces with a dual functionality of superhydrophobicity and photocatalytic activity. Appl. Surf. Sci. 319, 367–371. doi: 10.1016/j.apsusc.2014.07.122
Polizos, G., Tuncer, E., Sauers, I., and More, K. L. (2011). Physical properties of epoxy resin/titanium dioxide nanocomposites. Polym. Eng. Sci. 51, 87–93. doi: 10.1002/pen.21783
Pouget, E., Tonnar, J., Lucas, P., Lacroix-Desmazes, P., Ganachaud, F., and Boutevin, B. (2009). Well-architectured poly (dimethylsiloxane)-containing copolymers obtained by radical chemistry. Chem. Rev. 110, 1233–1277. doi: 10.1021/cr8001998
Pourhashem, S., Vaezi, M. R., Rashidi, A., and Bagherzadeh, M. R. (2017). Exploring corrosion protection properties of solvent based epoxy-graphene oxide nanocomposite coatings on mild steel. Corros. Sci. 115, 78–92. doi: 10.1016/j.corsci.2016.11.008
Pugachevskii, M. (2013). Ultraviolet absorption spectrum of laser-ablated titanium dioxide nanoparticles. Tech. Phys. Lett. 39, 36–38. doi: 10.1134/S1063785013010239
Radoman, T. S., DŽunuzović, J. V., Jeremić, K. B., Grgur, B. N., Miličević, D. S., Popović, I. G., et al. (2014). Improvement of epoxy resin properties by incorporation of TiO2 nanoparticles surface modified with gallic acid esters. Mater. Design 62, 158–167. doi: 10.1016/j.matdes.2014.05.015
Radoman, T. S., Terzić, N., Spasojević, P. M., DŽunuzović, J. V., Marinković, A. D., Jeremić, K. B., et al. (2015). Synthesis and characterization of the surface modified titanium dioxide/epoxy nanocomposites. Adv. Technol. 4, 7–15. doi: 10.5937/savteh1501007R
Ramezanzadeh, B., Attar, M., and Farzam, M. (2011). A study on the anticorrosion performance of the epoxy–polyamide nanocomposites containing ZnO nanoparticles. Prog. Org. Coat. 72, 410–422. doi: 10.1016/j.porgcoat.2011.05.014
Ramezanzadeh, B., Haeri, Z., and Ramezanzadeh, M. (2016a). A facile route of making silica nanoparticles-covered graphene oxide nanohybrids (SiO2-GO); fabrication of SiO2-GO/epoxy composite coating with superior barrier and corrosion protection performance. Chem. Eng. J. 303, 511–528. doi: 10.1016/j.cej.2016.06.028
Ramezanzadeh, B., Niroumandrad, S., Ahmadi, A., Mahdavian, M., and Moghadam, M. M. (2016b). Enhancement of barrier and corrosion protection performance of an epoxy coating through wet transfer of amino functionalized graphene oxide. Corros. Sci. 103, 283–304. doi: 10.1016/j.corsci.2015.11.033
Rathod, P., and Waghuley, S. (2015). Synthesis and UV-Vis spectroscopic study of TiO2 nanoparticles. Int. J. Nanomanuf. 11, 185–193. doi: 10.1504/IJNM.2015.071925
Shen, S., and Zuo, Y. (2014). The improved performance of Mg-rich epoxy primer on AZ91D magnesium alloy by addition of ZnO. Corros. Sci. 87, 167–178. doi: 10.1016/j.corsci.2014.06.020
Shi, X., Nguyen, T. A., Suo, Z., Liu, Y., and Avci, R. (2009). Effect of nanoparticles on the anticorrosion and mechanical properties of epoxy coating. Surf. Coat. Technol. 204, 237–245. doi: 10.1016/j.surfcoat.2009.06.048
Sung, P.-H., and Lin, C.-Y. (1997). Polysiloxane modified epoxy polymer networks—I. Graft interpenetrating polymeric networks. Eur. Polym. J. 33, 903–906. doi: 10.1016/S0014-3057(96)00214-5
Vasei, M., Das, P., Cherfouth, H., Marsan, B., and Claverie, J. P. (2014). TiO2@ C core-shell nanoparticles formed by polymeric nano-encapsulation. Front. Chem. 2:47. doi: 10.3389/fchem.2014.00047
Vázquez-Velázquez, A., Velasco-Soto, M., Pérez-García, S., and Licea-Jiménez, L. (2018). Functionalization effect on polymer nanocomposite coatings based on TiO2-SiO2 nanoparticles with superhydrophilic properties. Nanomaterials. 8, 369. doi: 10.3390/nano8060369
Velan, T. T., and Bilal, I. M. (2000). Aliphatic amine cured PDMS-epoxy interpenetrating network system for high performance engineering applications—Development and characterization. Bull. Mater. Sci. 23, 425–429. doi: 10.1007/BF02708394
Verma, S., Mohanty, S., and Nayak, S. (2019). A review on protective polymeric coatings for marine applications. J. Coat. Technol. Res. 16, 307–338. doi: 10.1007/s11998-018-00174-2
Wang, C., Wang, H., Hu, Y., Liu, Z., Lv, C., Zhu, Y., et al. (2018). Anti-corrosive and scale inhibiting polymer-based functional coating with internal and external regulation of TiO2 Whiskers. Coatings 8:29. doi: 10.3390/coatings8010029
Yi, C., Rostron, P., Vahdati, N., Gunister, E., and Alfantazi, A. (2018). Curing kinetics and mechanical properties of epoxy based coatings: the influence of added solvent. Prog. Org. Coat. 124, 165–174. doi: 10.1016/j.porgcoat.2018.08.009
Zaarei, D., Sarabi, A. A., Sharif, F., and Kassiriha, S. M. (2008). Structure, properties and corrosion resistivity of polymeric nanocomposite coatings based on layered silicates. J. Coat. Technol. Res. 5, 241–249. doi: 10.1007/s11998-007-9065-5
Zhang, H., Bao, W., Deng, Z., Zhang, S., and Ji, Z. (2019). Next-generation composite coating system: nanocoating. Front. Mater. 6:72. doi: 10.3389/fmats.2019.00072
Zhang, X., Wang, F., and Du, Y. (2007). Effect of nano-sized titanium powder addition on corrosion performance of epoxy coatings. Surf. Coat. Technol. 201, 7241–7245. doi: 10.1016/j.surfcoat.2007.01.042
Zheng, S., Bellido-Aguilar, D. A., Huang, Y., Zeng, X., Zhang, Q., and Chen, Z. (2019). Mechanically robust hydrophobic bio-based epoxy coatings for anti-corrosion application. Surf. Coat. Technol. 363, 43–50. doi: 10.1016/j.surfcoat.2019.02.020
Keywords: epoxy, polydimethylsiloxane (PDMS), TiO2 nanoparticles, nanocomposite coatings, hydrophobic, electrochemical impedance spectroscopy (EIS)
Citation: Shafaamri A, Cheng CH, Wonnie Ma IA, Baig SB, Kasi R, Subramaniam R and Balakrishnan V (2020) Effects of TiO2 Nanoparticles on the Overall Performance and Corrosion Protection Ability of Neat Epoxy and PDMS Modified Epoxy Coating Systems. Front. Mater. 6:336. doi: 10.3389/fmats.2019.00336
Received: 21 March 2019; Accepted: 06 December 2019;
Published: 13 January 2020.
Edited by:
Flavio Deflorian, University of Trento, ItalyReviewed by:
Benjamin Salas Valdez, Universidad Autónoma de Baja California, MexicoSébastien Touzain, Université de la Rochelle, France
Copyright © 2020 Shafaamri, Cheng, Wonnie Ma, Baig, Kasi, Subramaniam and Balakrishnan. This is an open-access article distributed under the terms of the Creative Commons Attribution License (CC BY). The use, distribution or reproduction in other forums is permitted, provided the original author(s) and the copyright owner(s) are credited and that the original publication in this journal is cited, in accordance with accepted academic practice. No use, distribution or reproduction is permitted which does not comply with these terms.
*Correspondence: Ammar Shafaamri, YW1tYXJzaGFmYWFtcmlAdW0uZWR1Lm15; Ramesh Kasi, cmFtZXNoa2FzaUB1bS5lZHUubXk=