- 1Center for Marine Materials Corrosion and Protection, College of Materials, Xiamen University, Xiamen, China
- 2Sinopec Energy and Environmental Engineering Co. Ltd, Wuhan, China
Carbon capture and storage (CCS) combined with CO2-enhanced oil recovery (EOR), has been recently viewed as an economical and effective method for the reduction of carbon emissions. However, corrosion is a challenging issue in the whole chain process of CO2-EOR production if water presents and mild steel pipeline is used. In this paper, the corrosion risk of pipeline at different stages of CO2-EOR production is systematically assessed based on a detailed analysis of the fluid characteristics. According to the fluid state of CO2, water and crude oil, current understandings on the corrosion behavior of steel materials in multiphase flow conditions are reviewed. Furthermore, the intermittent water wetting phenomena and the fluid behavior of water droplets or clusters in an electrolyte/non-electrolyte emulsion are correlated with the steel corrosion performance, providing new insights into the corrosion phenomena. Besides application of corrosion resistant materials and corrosion inhibitors, tailoring of processing parameters, such as enhancing the water entrainment, shortening the water contact time, and reducing the solution corrosivity, is highly recommended as an effective method for corrosion control in aggressive CO2-EOR production conditions. Based on these, some important future research topics on the corrosion in multiphase fluids are suggested.
Background
Our daily life is closely relied on the technological advancement of a carbon-based civilization. Over eighty percent of the global energy consumption in 2015 is fossil fuels, i.e., coal (29.2%), crude oil (32.9%), and natural gas (23.8%), from which a direct emission of about 36 billion tons of carbon dioxide has become a great challenge in combating its possible environmental impacts. Carbon Capture and Sequestration (CCS) is one of the most promising ways for reducing the buildup of greenhouse gas emissions in the atmosphere.
Combined with CCS techniques, CO2 enhanced oil recovery (EOR) has proved to be currently applicable in China for reducing CO2 emissions (Zhang et al., 2013; Lv et al., 2015). The CO2-EOR technique may produce a net zero emission of CO2, as it can store carbon underground during oil production. Therefore, the crude oil comes from CO2-EOR is generally termed as “carbon negative oil” (Hornafius and Hornafius, 2015). A significant improvement of oil production can be observed with CO2 injection into reservoirs compared to the conventional water injection production. In a pilot scale CCS-EOR project in Shengli oilfield, the improved efficiency of crude oil is around 8% and the dynamic ratio of carbon storage in reservoir conditions is around 50% (Lv et al., 2015). It provides a green and economical way to improve oil production in an old oilfield.
However, corrosion is a big concern in operating a CO2-EOR project, as CO2 becomes corrosive to steel-based facilities when it meets water. For example, in the CO2-EOR production section of Shengli oilfield, the presence of a large amount of CO2 in the production fluids has resulted in an abrupt increase of pipeline leakages within the initial 3 years after the injection of CO2 into reservoirs (Wang et al., 2015), revealing an averaged corrosion rate of pipeline materials higher than 1.0 mm/y (Zhang J. et al., 2012; Wang Z. M. et al., 2014). According to the field experience from Chevron, the coated tubes can only service for 50 months in CO2-injection well conditions (IEAGHG, 2010). Similar damage induced by the presence of high partial pressure of CO2 has also been reported in other CO2-EOR projects (Tzimas et al., 2005; Singh et al., 2010). The corrosion performance of different materials in CO2-containing aqueous solutions has been systematically investigated, and some strategies on corrosion control in CCS and CO2-EOR production have been suggested based on field experiences (Sim et al., 2014b; Wang et al., 2015). The use of corrosion-resistant alloys (CRA) and corrosion inhibitors is regarded as two of the important ways to mitigate corrosion in aggressive CO2 conditions (IEAGHG, 2010). However, in operating a large-scale CO2-EOR project, corrosion management should be systematically considered at the design and operation stages, which could significantly minimize the cost. Therefore, the corrosion risk of pipeline materials should be carefully evaluated. In this paper, we summarize the current views on corrosion evaluation and control of the CO2-containing multiphase flow pipelines in CCS-EOR production, based on which some ideas on corrosion management in the whole chain process of a CCS-EOR project are discussed.
Field Analysis
Whole Chain Process
There has been a long history of the trial application of CO2-EOR technique in oil and gas industry. However, the combination of this technique with CCS was recently adopted. As illustrated in Figure 1, the whole chain can be divided into carbon capture, CO2 transportation, CO2 injection, and oil production, during which a great portion of CO2 are permanently stored underground and the other is reutilized in the recycling process. In this whole chain process, CO2 can be viewed as a feedstock and crude oil is the product. When the net emission of CO2 is less than zero, i.e., the amount of CO2 stored underground is larger than that produced after burning the CO2-EOR crude oil, the crude oil will become “carbon negative.”
Currently, corrosion is one of the big concerns for wide application of the CCS-EOR technique, as water may be acidified in a CO2-containing environment. The presence of crude oil could vastly change the corrosion performance of steel materials, implying that the fluid structure may significantly affect corrosion. Therefore, the state of water and the fluid properties will be highlighted in this paper.
Fluid Properties
Pressure and Temperature
Pressure and temperature are two important parameters that determine the properties of the CO2-containing fluids, including the state of CO2 phase, solubility, and pH-values, as well as the properties of crude oils. The diagram of pressure and temperature of CO2 phase is illustrated in Figure 2, where pressure refers to the partial pressure of CO2. A transitional point at 7.31 MPa and 31.06°C is indicated and the liquid phase, supercritical phase and gas phase of CO2 are separated by black lines, as labeled in Figure 2.
CO2 can be transported in different states, but a single-phase state is preferred in pipeline for a security reason. Generally, a supercritical phase or a gas phase is selected, since it needs less energy for long-distance transportation. In some cases, CO2 is liquefied to a small volume and transported by tanks. Liquid CO2 may also be encountered when CO2 is transported in a supercritical state, as the failure of the heat-resistant coatings on the outside surface of a pipeline may result in a decrease of temperature below the critical point. Generally, the pressure of CO2 transportation pipeline is in a range from 5 to 20 MPa. A high pressure can increase the efficiency of transportation. The temperature may vary in a wide range from below 20°C up to 50°C, depending on the heating or cooling conditions.
CO2 injection may need a pressure higher than 10 MPa at wellhead and the pressure will be further increased with depth from wellhead. As reported in a previous paper (Wang and Song, 2018), at a depth of 3,000 m, the pressure can be higher than 35 MPa, which is certainly determined by the injection rate and the pressure at wellhead. Temperature is closely relied on the depth profile of the ground temperature. According to the field experience in Shengli oilfield, a supercritical state could be kept during continuous injection deeper than 700 m if CO2 was initially injected in a liquid state. A higher injection rate will push the transitional point to a deeper site in well conditions. The ranges of temperature and pressure of CO2 fluid in a typical well are schematically shown in Figure 2.
In an oil production well, the distributions of pressure and temperature are dependent on well depth. At the wellbore, temperature and pressure reach their highest values, where CO2 may be in a supercritical or gas state. As flowing from the well bottom to wellhead, both of the pressure and temperature of the fluids gradually decrease. In some cases, temperature may decrease below 30°C at wellhead and pressure below 1.0 MPa. The fluid must be heated and pressurized in the following transportation process. Different from a CO2 injection well, the fluid in an oil production well is generally a complex mixture of oil, water and gas. In CO2-EOR production, the content of CO2 in gas phase can be as high as 70% in volume (Wang et al., 2015).
The oil gathering and transportation system is generally operated at a pressure from 0.3 to 2.0 MPa, relatively low compared to the pressure in well conditions. Its temperature is generally lower than 60°C, but for some highly viscous crude oil it may reach 80°C for obtaining a good fluidity. Therefore, the CO2-containing aqueous phase in oil transportation pipeline is usually less corrosive than that in oil production well. It is obvious that the flow pattern in a horizontal pipe or a slightly inclined pipe for crude oil transportation is generally different from that in a vertical well tube.
CO2 Phase
In CO2 transportation and injection, the state of CO2 phase is determined by its pressure and temperature. As shown in Figure 2, the supercritical state of CO2 may be widely encountered in the CO2 transportation, injection, and oil production processes. Depending on the technology of carbon capture and the resource of CO2, trace amounts of impurity gases may remain in the CO2 after purification. These impurities generally include water, O2, SOx, NOx, and H2S. Water is the most common impurity compound in CO2 during transportation and injection, whose concentration limit is recommended to be <500 ppm. Although these impurities are generally controlled at a very low level, they may affect steel corrosion in water-containing supercritical (SC) CO2 conditions.
In the oil production and transportation stages, CO2 gas is mixed with natural gas at a fraction around 30~70 vol.%, according to the CO2-EOR production in Sinopec Shengli oilfield (Wang et al., 2015). At the initial stage of injection, the fraction of CO2 is similar to that of the conventional oil production, as CO2 has not migrated to the production well. After continuous injection for months, a sharp increase of the fraction of CO2 can be observed, finally reaching a value around 50~70% in volume fraction. In this case, besides acidifying the aqueous phase, the large volume of CO2 gas may also affect the flow patterns.
Water Phase
During CCS and EOR production, water is saturated with CO2 forming carbonic acid. The pH-value of the aqueous solution is depending on the partial pressure of CO2 and the temperature, as well as the salinity of solution (Nesic, 2007); a linear relationship can be observed between pH-value and CO2 pressure. It should be noticed that the diffusion coefficient of CO2 in water is around 10−8 m2/s in stagnant conditions, according to which it needs several to tens of minutes to diffuse through the bulk solution layer (Grogan et al., 1988; Farajzadeh et al., 2009). However, in a multiphase flow condition the saturation of CO2 in water can be greatly accelerated owing to the well-known migration mechanism. It should be noticed that CO2 corrosion is generally controlled by cathodic reactions, where different kinds of ionic species (such as H+, , and even H2CO3) would be participated in the reduction process depending on pH-values (Nesic, 2007). The formation of corrosion product layer mainly relies on the local solution chemistry at the vicinity near the steel surface where the concentrations of ferrous ion and are above the solubility limit of FeCO3 for precipitation (Nesic et al., 2004; Ingham et al., 2012; Bian et al., 2015). In turn, the formation of FeCO3 layer will retard the anodic reaction depending on its morphology and protectiveness (Barker et al., 2018). The presence of a trace amount of S2− (Yang et al., 2017) and Ac− (Amri et al., 2010) ions in aqueous phase can change the formation and the stability of FeCO3 layers.
Crude Oil
Crude oil is a complex mixture of hydrocarbons and it is generally categorized into three types according to its density. A heavy crude oil has an American Petroleum Institute (API) gravity lower than 20, a medium crude oil has an intermediate API gravity of 20–34, while a light crude oil has an API gravity higher than 34. The API gravity is a factor inversely proportional to the density of crude oil. It is generally accepted that heavier oils are more protective than lighter ones with regard to corrosion (De Waard et al., 2003). Another way to classify crude oils is based on the proportions of the organic compounds (Sokolova et al., 1992), such as paraffin, aromatic compounds, and naphthenic compounds. These compounds may have a profound effect on the wettability of crude oil and the chemistry of brine solutions (Efird et al., 2004), thus affecting pipeline corrosion.
The presence of CO2 may change the properties of crude oil. The solubility of CO2 in a crude oil is generally many times higher than that in water (Rostami et al., 2017). The incorporation of CO2 may induce a volume expansion of crude oil (Yang et al., 2013). The viscosity of crude oil vastly decreases with increasing pressure, as more CO2 and natural gas can be dissolved into crude oil (Freitag, 2018). A beneficial effect of low viscosity has been reported in multiphase flow loop tests (Kanwar, 1994; Jepson and Menezes, 1995) and recently observed in an oil/water alternate wetted condition (Wang et al., 2019a). These observations are particularly interesting for corrosion evaluation under well conditions where the oil viscosity may be vastly changed with temperature and pressure. One should also notice that a lower viscosity may lead to an easier separation of oil and water and it is harmful for the corrosion mitigation in water-in-oil (w/o) emulsions or dispersions.
Solid Particle and Scale Deposition
Besides the oil, water and gas phases, solid particles may also be presented in CO2-EOR production fluids. The solid phase may come from the reservoir and the precipitation of scales due to variation of brine chemistry. Generally, extremely large (>1 mm) solid particles are rarely observed in the oil and water transportation systems, as a number of filters are equipped on pipeline ahead of a pump. However, in the well conditions or the deep-sea pipeline, where the removal of sand becomes economically unacceptable, erosion corrosion may be encountered (Pouraria et al., 2016). The precipitation of scales on a pipeline surface can be encountered in CO2-containing fluids, especially in a water treatment system, where the CO2 partial pressure and pH-value have greatly changed, breaking the balance of brine chemistry. This would produce an under-deposit corrosion problem.
Corrosion Risk Analysis
CO2 Transportation and Injection
Corrosion can only occur when CO2 meets water. Therefore, the concentration of water in CO2 during transportation and injection is generally controlled below a critical value. There are several recommendations according to successful project experiences, as summarized in Table 1. For example, a recommended value of H2O in dense phase CO2 was 500 ppm in the DYNAMIS project (de Visser et al., 2008). Below this concentration, it was believed that corrosion would not be a problem during CO2 transportation and injection conditions (Cole et al., 2011; Sandana et al., 2012; Jacobson, 2014). However, in case of CO2 and water being alternately injected into reservoirs to reduce CO2 migration, the well tubes may suffer from serious corrosion damage (IEAGHG, 2010). Occasional ingress of water into the transportation pipeline may also induce corrosion.
Another possibility of water ingress is originated from the diffusion of water after injection stops. Theoretically, this takes a few months to form a water saturated CO2 phase in the well tube usually within a length of several and tens of meters from wellbore, since the diffusion of water in stagnant CO2 is relatively slow. However, in a long-term sealed well, corrosion induced by water diffusion from the reservoirs must be considered. Even though cement sealing outside the casing pipe is generally believed to be a robust protective layer, it should be borne in mind that CO2 is actually very corrosive to cement, which has not been widely realized in engineering. After long-term carbonation, the originally protective cement layer might have failed much earlier than expected (Kutchko et al., 2007; Carpenter et al., 2011).
There are many reported damage cases of CO2 transportation pipelines and injection well tubes induced by corrosion. According to the CO2-EOR projects in the United States since 1970s, aggressive corrosion damage has been observed in CO2 injection wells in a water-alternate-gas (WAG) injection condition, although corrosion resistant alloys and liners were adopted for corrosion protection (IEAGHG, 2010). For CO2 transportation pipelines, corrosion induced damage at the pipeline bottom has also been encountered in the practical operation in east China, owing to the accumulation of the remaining water in CO2 phase.
Oil Production Well
The produced fluid is complex and its corrosiveness is determined by many factors, such as the fraction of CO2, pH-value, states of oil, water content and water chemistry. Different from conventional oil production, the well fluid contains a large fraction of CO2 in CO2-EOR production. As estimated from a previous reference (Choi and Nešić, 2011), the pH-value at wellbore condition can be as low as 3.0. A greater depth of the well tube can result in a higher partial pressure of CO2, which indicates a higher corrosion risk at deeper sites. It should also be noticed that the gas-to-liquid ratio becomes extremely high once a large amount of CO2 gas is presented in the well tube. It has been reported that the gas-to-liquid ratio could be as high as several hundreds (Wang et al., 2015). Therefore, a highly stirred oil-water-gas three phase flow is a predominant feature of the CO2-EOR production fluid. A complete mixture of oil and water may reduce the corrosion risk of well tubes (Cai et al., 2012; Wang et al., 2015), owing to the inhibition effect of crude oil on corrosion. As stated above, the viscosity reduction in oil well conditions may also reduce the corrosion risk of well tubes. Moreover, the accumulation of corrosion released ferrous ion in well tube may in return affect corrosion of steel materials (Bian et al., 2015), through formation of a protective iron carbonate layer. All these make the corrosion process extremely complicated.
Oil Gathering and Transportation
The produced fluid is subsequently transported by pipelines to a treatment station for separation. Different from the well condition, the transportation pipeline is generally in a horizontal or inclined direction. Its corrosion risk is highly dependent on the mixing state of oil and water, which is determined by the flow parameters (Sarica and Zhang, 2008; Kee et al., 2014), such as the flow rate, fraction and fluidity of different phases and the pressure and temperature of the system. The settlement of free water at the bottom of pipeline can initiate corrosion (Jiang and Cheng, 2013; Wang Z. L. et al., 2014). A large gas-to-liquid ratio will further complicate the mixing state of oil, water, and gas (Wang et al., 2015), which can also result in a significantly increased actual flow velocity of the liquid phase. On one hand, this may lead to flow-accelerated corrosion if water cannot be completely entrained into the oil phase or erosion-corrosion damage when solid particles are involved in the transportation. On the other hand, a mixture of oil and water may reduce the corrosion at the pipeline bottom, as the water phase may be highly dispersed and thus continuous water wetting of the steel surface is avoided.
Water Treatment
CO2 cannot be completely removed from water phase after separation of the produced fluid at the treatment station. The partial pressure of CO2 may be reduced significantly from ~1.0 MPa or higher to <0.2 MPa, and the dissolved CO2 gas may evolve from the aqueous phase. However, the left fluid remains corrosive to mild steel. Without the presence of crude oil, the CO2 containing aqueous fluid can become even more aggressive to steel. It can also be less corrosive as the transportation temperature and pressure are lower than the oil production and transportation systems.
In some cases, alkaline solution may be introduced to neutralize the CO2 containing solution, further reducing its corrosiveness. However, neutralization of the CO2 containing fluid may induce a scaling problem, owing to the presence of Ca2+ and Mg2+ ions. Generally, these scale forming cations are dissolved from the reservoir rocks in CO2-EOR conditions. Once the salt scale is formed and attached on the inner surface of pipeline, under-deposit corrosion and crevice corrosion will occur, leading to localized corrosion damage of the pipeline in CO2-containing environments (Zhang et al., 2016). A complicated corrosion product layer may be formed owing to the incorporation of Ca2+ and Mg2+ cations, which may have improved protectiveness or increased pitting susceptibility (Esmaeely et al., 2013; Tavares et al., 2015). Recently, Shamsa et al. (2019) identified the corrosion products on X65 carbon steel as FexCayCO3 in the presence of Ca2+ cations. The stoichiometry of FexCayCO3 could vary with immersion time. They also pointed out that incorporation of the Ca2+ cations in the corrosion product layer may lead to severe localized corrosion damage at a low temperature relevant to oil production (generally below 80°C in the gathering and transportation system).
Multiphase Flow Corrosion
Single-Phase CO2
In the temperature range of oil production, completely dry CO2 is not corrosive to steel. Direct carbonation of steel materials by CO2 can only occur at a high temperature (Cao et al., 2012). As mentioned above, CO2 is generally transported and injected into wells in a dense phase state, for example, the supercritical state. The presence of a trace amount of water in the dense phase CO2 is the origin of corrosion; the formation of CO2 saturated water layer on steel surface triggers corrosion. In this case, corrosion will be very slight, since this water layer can quickly become saturated with ferrous ion and an iron carbonate layer can be easily formed on the steel surface. The variation of local temperature and pressure is believed to be the primary cause of forming droplets or a water layer on steel surfaces (Choi and Nešić, 2011), just like that in a wet natural gas pipeline. However, CO2 fluids can have a very high density, vastly different from natural gas. As seen from Figure 3, the density of CO2 can be higher than 800 kg/m3 in a certain depth in the injection well. Therefore, in a flow condition, such a dense-phase CO2 may behave more like an oil phase rather than a natural gas phase.
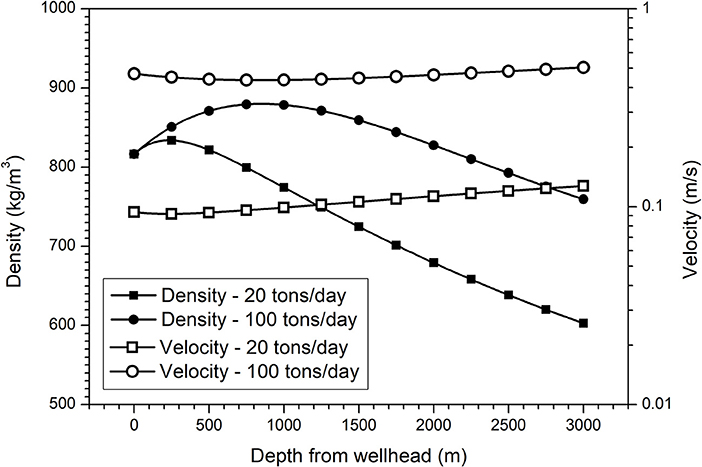
Figure 3. Distribution of density and velocity of CO2 fluid as a function of well depth at different injection flow rates, which was calculated based on the field condition of an injection well in Shengli oilfield, where the injection temperature and pressure of CO2 fluid at wellhead were −20°C and 10 MPa, respectively (Wang and Song, 2018).
Recently, it was found that the corrosion morphology was highly relied on the flow rate and the degree of water saturation (Liu et al., 2018); a higher flow rate and a higher degree of water saturation produced larger corrosion product particles and patches, implying a possible corrosion mechanism related to the direct bombardment of water droplets on steel surfaces and these droplets are likely entrained in the dense CO2 phase, rather than directly nucleated on steel surfaces. In SC CO2 fluids, the entrainment of these water-rich clusters (or droplets) is possible and the presence of such water-rich heterogeneities in wet SC CO2 has been identified by near-infrared spectroscopy (Wang et al., 2013) and radial distribution function method (Glezakou et al., 2010). Above the solubility limit of water in SC CO2, the water-CO2 mixture may form stable water-in-SC CO2 micro-emulsions (Lee et al., 1999). Below the saturation limit, the formation of a weak Lewis acid-base H2O:CO2 complex (Thanthiriwatte et al., 2012; Wang et al., 2013) has been reported in SC CO2 media. As illustrated in Figure 3, depending on the flow rate in transportation and injection, the velocity of a CO2 fluid can be in a wide range from <0.1 to 0.5 m/s or higher. Obviously, decreasing the velocity of CO2 can reduce the impact of water droplets on steel surface, thus reducing the corrosion risk (Bian et al., 2015). Therefore, to get a high transportation efficiency, pressurizing the CO2 fluid is better than improving its flow velocity from a corrosion view.
Besides the influence of flow rate and water concentration, it has been reported that some impurity gases may also significantly change the corrosion morphology and increase the corrosion rate. To date, the corrosion performance of steel in presence of trace amounts of O2 (Xiang et al., 2013; Hua et al., 2014b), SOx, NOx (Ayello et al., 2010; Dugstad et al., 2013a), H2S (Choi et al., 2015; Sun et al., 2016b), and their mixtures (Choi et al., 2010; Dugstad et al., 2013b; Ruhl and Kranzmann, 2013; Xiang et al., 2013) have been extensively investigated. The results show that these impurity gases may greatly change the water limit for triggering corrosion, as they exacerbates corrosion by influencing corrosion products and participating in corrosion processes. However, it should be noticed that the presence of impurities may also change the stability of the water-CO2 mixture in a supercritical state (Mohitpour et al., 2012). Visualization tests should be conducted to further explore the initial corrosion and water settlement in SC CO2 environments. This may finally lead to a better management of the corrosion risk in CO2 transportation and injection pipelines.
Water-CO2 Slugs
Although CO2 is dried prior to transportation, water ingress may happen in some occasional conditions. It has been reported that the corrosion rate of mild steel in a dense-phase CO2-water flowing conditions can be as high as several to tens of mm/y depending on their fluid parameters (Dugstad et al., 2011a; Barker et al., 2017), because the aqueous solution was saturated with high pressure CO2. There are many experimental results on the corrosion rates and corrosion morphologies of steel materials in high-pressure CO2 environments (Cui et al., 2006; Cao et al., 2012; Zhang Y. et al., 2012; Hua et al., 2015), from which it can be deduced that the steel materials suffer from severe corrosion attack and the flow can vastly accelerate corrosion (Dugstad et al., 2011a; Wei et al., 2018) in the presence of a bulk volume of water during the transportation of dense-phase CO2.
In practice, CO2 and water may also be alternatively injected into wells (Rogers and Grigg, 2001; Lv et al., 2015; Dang et al., 2016). For example, in Shengli oilfield, the water alternating gas (WAG) injection technique is planned to be adopted after a further verification in the pilot-scale CO2-EOR project (Lv et al., 2015). This WAG injection process can to some extent retard gas-migration under reservoir conditions (Dugstad et al., 2011b). By adjusting the WAG ratio, a maximum ratio of the oil production to CO2 injection could be reached (Dai et al., 2014). However, the alternating exposure of the pipe inner wall to water and CO2 fluids can result in severe corrosion damage. According to field experiences, the water phase may linger for a long time in crevices or dead spots after dry conditions were restored (IEAGHG, 2010), leading to a corrosion problem in aggressive well environments. Temperature and pressure are believed to be the critical factors in corrosion (De Waard et al., 1991), since they directly determine the solubility of water in CO2 and the pH-value of the water layer (Choi and Nešić, 2011). During the WAG injection process, corrosion occurs when the CO2 slug begins to drive down the previous water slug, leaving a water layer on the pipe inner wall being acidified by flowing CO2. Recently, Wang and Song theoretically evaluated the corrosion risk of steel materials in such WAG conditions by assuming that the steel surfaces were periodically exposed to the wet/dry cycles in CO2 fluids and the corrosion was dependent on the dissolution of CO2 in the water layer (Wang and Song, 2018). In their simulation work, the time of forming a CO2 saturated water layer was simiply determined by the diffusion rate of CO2 through the layer, which was assumed to be very fast and genrally less than several minutes (Grogan et al., 1988; Farajzadeh et al., 2009), having little influence on the overall corrosion performace. Therefore, the long-term corrosion behavior relied on the time for drying the steel surface by flowing “dry” CO2, and the amount of water absorbed by the “dry” CO2 fluid was critical for determing corrosion risk, where the “dry” CO2 meant that the water concentration in CO2 phase was far below its saturation limit, a shorter drying time meant a less exposure of steel surface to the CO2 saturated corrosive water, and corrosion was supposed to cease when the water layer was completely absorbed into the CO2 fluid. In this way, they concluded that the alternate period determined the long-term corrosion performance. The injection rate of CO2 fluid is another critical factor influencing the distributions of temperature and pressure in well (Lindeberg, 2011; Ruan et al., 2013) and it also affects the drying time of the water layer along the pipe internal wall.
Oil-Water Mixtures
The presence of crude oil may reduce the corrosion risk of CO2-EOR pipelines. The corrosion performance of pipeline may be influenced by crude oil's physical properties, such as its density (Lotz et al., 1991; De Waard et al., 2003; Papavinasam et al., 2007), viscosity (Kanwar, 1994; Jepson and Menezes, 1995; Papavinasam et al., 2007), conductivity (Craig, 1998), and wettability (Craig, 1996; Smart, 2001; Efird et al., 2004). Recently, Wang and Zhang (2016) summarized four different mechanisms for the inhibition effect of crude oil on corrosion: (1) water entrainment, (2) crude oil wetting, (3) soluble chemical partitioning, and (4) corrosion product layer modification. De Waard et al. (2003) found that heavy oil was less corrosive than light one in an oil-water two-phase flow condition, which could be attributed to the formation of w/o dispersions (Xu, 2007). A simple notion for corrosion risk analysis has been proposed based on the assumption that corrosion would occur only when free water was separated from w/o emulsion during transportation (Wang Z. L. et al., 2014). At some extremely high water cuts, w/o emulsion can also be formed. For example, the experimentally measured emulsion inversion point (EIP) is generally reported to be as high as 70 wt.% (Fingas and Fieldhouse, 2004; Wang Z. L. et al., 2014), which means that a w/o emulsion can be formed at a relatively high water cut under sufficiently stirred conditions. Free water will be separated within a very short period from a w/o dispersed fluid when the flow is slower than a critical velocity (Xu, 2007). In practical oil production, it is hard to completely emulsify the oil-brine mixtures with a very high water concentration. Generally, a w/o emulsion containing <30 wt.% water is relatively stable under flow conditions (Fingas and Fieldhouse, 2004).
The occurrence of corrosion may be related to the droplet behavior in a w/o emulsion or dispersion, and the droplets may grow to larger ones during transportation, leading to the settlement on pipeline bottom. According to Stokes equation, the settlement rate (Vt) of water droplets in a w/o emulsion can be expressed as (Frising et al., 2006),
where dt is the mean diameter of droplets at a test condition, g is the gravitational acceleration, ρw and ρo are the densities of water and oil phases, and μ is the viscosity of oil-water mixtures. It is clear that a larger water droplet is easier to settle down in a lighter oil-water mixture. It should also be noticed that the formation of a stable emulsion may significantly increase the fluid viscosity (Xu, 2007; Wang Z. L. et al., 2014), thus retarding the settlement of water droplets. In practical uses, the theoretical analysis must be verified by the stability of emulsion samples in field conditions. Recently, Paolinelli et al. (2018) examined the correlation of water droplet size distribution with different fluid parameters (flow rate, pressure drop, oil types, and fraction of water) after a globe valve on a pipe flow loop and compared with theoretical analysis, and gave some reasonable hints for the control of water droplets in flow conditions. In this way, before the settlement of water droplets or the formation of water layer at pipeline bottom, corrosion could be totally retarded during the long-distance transportation of oil-water emulsion and a fast transportation could shorten the time from wellhead to treatment station (Wang Z. L. et al., 2014), beneficial for reducing the corrosion risk.
At a higher water cut, where total entrainment of water droplets becomes impossible, the steel surface will be intermittently wetted by water. Flow loop tests indicated that the corrosion rate was retarded under intermittent water wetting conditions compared to continuous water wetting (Li et al., 2006). In a flow condition, the intermittent wetting behavior closely depends on the flow pattern characteristics (Nesic and Carroll, 2003). Several studies have demonstrated that with increasing flow rate, the steel surface can be changed from continuous water wetting to intermittent wetting or even continuous oil wetting (Nesic and Carroll, 2003; Cai et al., 2012), hence reducing the corrosion risk at the pipeline bottom. The intermittent wetting by oil and water at steel surface has been verified by various sensors in flow loop tests (Fordham et al., 1999; Zong et al., 2010; Luo et al., 2017). Efforts have been made to monitor the wetting and corrosion phenomena by electrochemical noise method in oil-water mixtures (Bouazaze et al., 2005). However, the electrochemical noise signals are much complicated. A quantitative and controllable method is urgently needed for analyzing the dynamic wetting and corrosion phenomena in one test. To further reveal the corrosion phenomena in oil-water intermittent conditions, Wang et al. (2019a) recently proposed an “alternate wetting cell” to record the current signals under anodic polarization with a rotating electrode. With a controllable movement of the oil/water interface relative to electrode, it can simplify the intermittent flow pattern as the alternate wetting of the electrode surface by oil and water, as illustrated in Figure 4. The actual wetting state could be presented as a series of oil and water slugs (see Figure 4A). Interestingly, there is a delay in the actual oil wetting time (tao) and the actual water wetting time (taw), which can be confirmed by the anodic current peaks in Figure 4B. The height and width of the current peaks could reflect the corrosion and water wetting on the electrode surface, respectively. Their results indicate that a slow flow and a short alternate period can generate high corrosion mitigation efficiency. The “alternate wetting cell” method provides a possible way to describe the correlation between corrosion and wetting under a controllable manner and a new insight into the corrosion phenomena in a complicated system. It can be used for the evaluation of corrosion inhibitors in an oil-water system (Wang et al., 2019b).
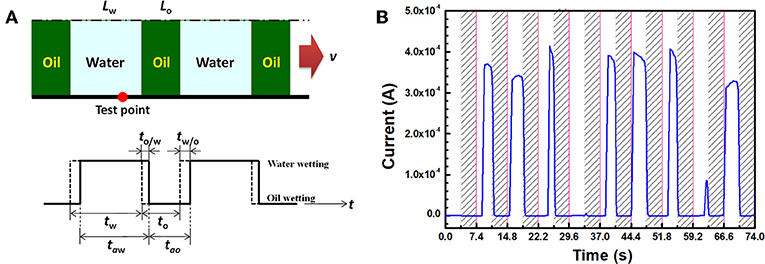
Figure 4. (A) Simplification of intermittent flow pattern as an “alternate slug model” and (B) the anodic current transient detected on a rotating disk electrode alternately wetted by oil and water by the “alternate wetting cell” test method (Wang et al., 2019a). In (A), tw is the time of water slug passing though the test point, tw/o is the time of water-replacing-oil, and to/w is the time of oil-replacing-water. In (B), the rotation is 600 rpm, the alternate period is 7.4 s for the current response and the applied anodic potential is +100 mV vs. open circuit potential.
The covering effect of crude oil at the steel surface is widely accepted as the origin for corrosion inhibition. However, a thin layer of crude oil at the steel surface is unstable to prevent corrosion for a long time. For example, Wang Z. L. et al. (2014) observed that a crude oil layer could only persist for about 15 min on a vertically placed steel surface in a stagnant condition. The heterogeneous adsorption of crude oil on steel surface may induce localized corrosion (Sun et al., 2016a). The degree of localized corrosion may be vastly different from the averaged corrosion rate in oil-brine mixed conditions (Choi et al., 1989; Sun et al., 2016a), but this phenomenon and its mechanisms have not been clearly addressed. Some soluble organic compounds in crude oil can also decisively reduce the corrosion rate in a manner like corrosion inhibitors (Efird and Jasinski, 1989; Castillo et al., 2000; Ayello et al., 2013) and they may produce a possible hybrid effect on corrosion products (Mendez et al., 2001; Yang et al., 2014; Taleb et al., 2017).
Oil-Water-Gas/Solid Flow
The multiphase fluids are commonly encountered in CO2-EOR production, in which a large fraction of CO2 in the gas phase is involved. Previous efforts were mainly focused on the relationship between corrosion and the flow characteristics of a gas-liquid two-phase flow. Although very limited number of studies have been focused on the corrosion phenomena in CO2-EOR multiphase flow conditions, the results regarding corrosion in conventional oil production can be employed for reference. For instance, in a slug flow, the corrosion risk of pipelines can be closely related to the superficial gas velocity (Maley, 1997; Kang et al., 1999), slug frequency (Kang et al., 1996; Maley, 1997; Wang et al., 2015), and Froude number (Kang et al., 1996; Chen and Jepson, 1999). Generally, direct visualization is used to determine the flow patterns. Other methods are also widely accepted, for examples, pressure drop (Sotgia et al., 2008), wetting behavior (Cai et al., 2012), and phase density distribution (Hoffmann and Johnson, 2011). Currently, many research institutes have developed multiphase flow loops for corrosion tests (Kouba and Jepson, 1990; Nyborg, 1998; Li et al., 2006; Zheng et al., 2008; Wang et al., 2015). Based on the flow loop tests, the relationship between corrosion and flow characteristics has been built. It was found that a higher slug frequency may increase the corrosion rate of pipelines, owing to a sharp increase in the local wall shear stress (Yang et al., 2010), which was viewed as an important parameter in corrosion (Wang et al., 2002; Zheng et al., 2008). A higher shear stress may enhance the local corrosion kinetics or damage the corrosion products (Schmitt et al., 2000; Li et al., 2016). It was also observed that a higher gas flow rate could reduce the pressure drop and lower the frequency of liquid slugs at a constant liquid velocity (Kang et al., 1999; Villarreal et al., 2006; Wang et al., 2015), thus reducing the corrosion risk.
In conducting a flow loop experiment, oil and water may be emulsified during a long-term cyclic test if crude oil was used. The heavier the crude oil is, the easier it can be emulsified. At a fixed pump input fraction of oil and water, the entrainment of water in oil phase may increase the actual water fraction of input fluids. It has been reported that a significantly large amount of water can be entrained into the crude oil phase after 3 days of the cycle test in a closed flow loop (Wang and Zhang, 2016). No free water can be separated from the oil-water mixture within a short period after the cyclic test. Emulsification is the main reason for the use of white oil, instead of crude oil, in most multiphase flow loop tests. To overcome the emulsification problem, a multiphase flow loop was built in a treatment station of Shengli oilfield, where the oil, water and gases were separately introduced into the test loop from the production pipelines and then went back to the production system via the output pipeline after corrosion test. The input of oil, water and gas was also driven by pumps and the process was similar to that of a laboratory-scale setup reported previously (Wang et al., 2015). The only difference is that the mixed fluids after going through the corrosion test section directly flows into the oil production system and never goes back to the pipe section for corrosion tests. Using this “open” flow loop system, field corrosion was monitored at the steel pipe bottom. The corrosion rate can be automatically converted from the galvanic current of a commercial corrosion probe, which has been previously used for corrosion monitoring in an oil-water system (Wang Z. L. et al., 2014). A flat sheet of 20# steel was used as the corrosion probe and the diameter of the pipeline was 80 mm. With changing water cut, a series of field conditions can be simulated.
One may notice that CO2-EOR production fluids generally contain an extremely high fraction of gas phase with a gas-to-liquid ratio over 200, in which CO2 gas can reach a volume fraction of 70% in the gas phase (Wang et al., 2015). Under such a high gas-to-liquid ratio, oil and water may be strongly stirred during transportation, and corrosion can be reduced once the oil phase reaches the bottom of pipeline. In Figure 5, the influence of gas-to-liquid ratio on corrosion was further verified at different water cuts in filed conditions. The corrosion rate initially increased and then decreased after the gas-to-liquid ratio increased to a critical value, depending on the water cuts. A higher water cut generally leads to a transition point at a higher gas-to-liquid ratio. However, when the gas-to-liquid ratio is higher than 20, corrosion will be obviously reduced. The result agrees with the theoretical analysis of corrosion mitigation in oil-water-gas three-phase flow conditions (Wang et al., 2015). This is also consistent with the notion that corrosion can be mitigated in an oil-brine mixed flow by increasing turbulence to generate oil wetting (Wicks and Fraser, 1975; Cai et al., 2012). Under a high pressure, the dissolved gas may reduce the viscosity of crude oil, thus changing the flow pattern and the wetting behavior in pipeline (Luo et al., 2017).
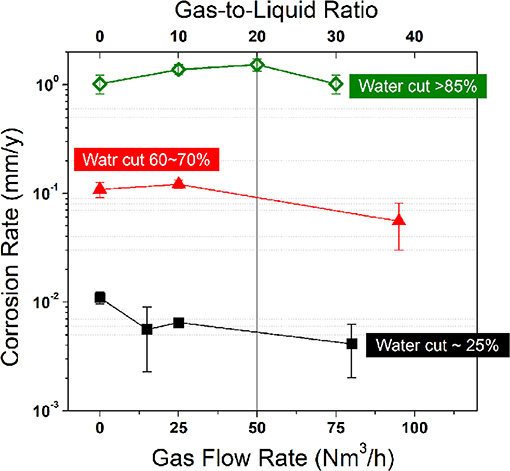
Figure 5. The measured corrosion rate as a function of gas flow rate (or Gas-to-liquid ratio) at different water cuts obtained from the multiphase flow loop test at 0.3 MPa in field condition of Shengli oilfield. The crude oil was heavy oil with a density of 0.92 g/cm3 at 20°C and a viscosity of 135.3 mPas at the operation temperature of 60°C. The fraction of CO2 in gas phase was around 50 vol.%. For the present field test, the liquid flow rate was 4.5 m3/h. The input fluid was controlled by pumps and the water cut was experimentally estimated by on-site sampling of the oil-water mixtures.
Sand or solid particles in CO2-EOR fluids may induce erosion or localized corrosion problem. Generally, in the CO2 injection and water treatment processes, no sand or solid particle is involved. The influence of sand or solid particle on corrosion is usually considered in presence of crude oil. The simulation work from Landry et al. (2012) suggested that the settlement of solid particles is much easier onto the pipeline bottom and water may also be accumulated around such solid particles forming a locally water-rich environment. In this condition, corrosion may be preferentially initiated around the solid particle (Han et al., 2013). Tang et al. (2008) observed severe erosion-corrosion damage on steel surface and the contribution of erosion was measured to be around 70% in the oil-sand slurry with different sand concentrations. However, Stack and Abdulrahman (2012) reported the movement behavior of sand particles sealed by an oil layer, which produces a weaker impact on steel surface, and thus reduce the mechanical and electrochemical attacks. A further analysis is essential for understanding the corrosion behavior associated with sand particles and crude oils, which will be helpful to the field corrosion management in CO2-EOR well and deep-sea conditions.
Correlating Corrosion With Fluid Structures
Corrosion control in multiphase flow conditions is technically challenging, owing to the complexity of fluid. In CO2-EOR production, the multiphase flow is generally relevant to an oil-water mixture or a dense phase CO2 containing a trace amount of water, which attributes to oil production and CO2 injection, respectively. Here, these two cases can both be termed as water/non-electrolyte mixture. In a previous paper, Liu et al. (2018) believed that the state of water in SC CO2 phase might behave like the w/o emulsion or dispersion, where a corrosion mechanism was proposed in SC CO2 environment regarding the impact of water droplets on steel surfaces. It implies that the density and velocity of water clusters in SC CO2 phase determine the corrosion morphology. Although the corrosion propagation has not been directly monitored, the observation of different types of corrosion product particles on steel surfaces after autoclave test can verify this microscopic mechanism. Actually, similar circular-shaped corrosion product particles can also be observed on steel surface after corrosion in a w/o emulsion for a short period (e.g., 72 h), as typically illustrated in Figure 6. For a longer period, the corrosion product particles may be merged to become large patches, finally forming a layer of FeCO3. It seems that these corrosion product particles are probably originated from the attachment of corrosive water droplets. Presently, the direct links between the sizes of corrosion product particles and water droplets are still not clear. It is interesting that the corrosion morphologies of steel surface are similar in different types of fluids. It is quite possible that the water droplets or clusters present in the w/o emulsion (Wang Z. L. et al., 2014) and the water containing SC CO2 (McGrail et al., 2009; Thanthiriwatte et al., 2012; Wang et al., 2013) result in the corrosion product particles on steel surfaces. As proposed by Liu et al. (2018) in CO2 fluid, the flow and wetting behavior of water clusters are the origin of corrosion damage. This mechanism could be extended to interpret the corrosion performance of steel samples in various electrolyte/non-electrolyte mixtures. This provides a new view on corrosion prediction in complex conditions, where water is highly dispersed in a non-conductive fluid.
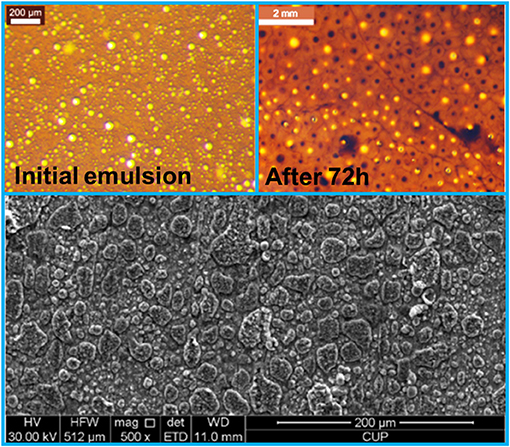
Figure 6. Microscopic images of a water-in-oil emulsion with a water cut of 70 wt.% before and after corrosion test and the corrosion morphology of P110 steel surface after autoclave test for 72 h at a CO2 pressure of 10 MPa, 80°C. The initial emulsion was prepared by mixing oil and water at a stirring rate of 1,200 rpm in an emulsifier. The “after 72 h” refers to the state of the emulsion after autoclave test. The oil's density is about 0.88 g/cm3 (Wang Z. L. et al., 2014) and the brine solution is similar to the CO2-EOR production water in Shengli oilfield (Zhang J. et al., 2012; Wang et al., 2015). The image of emulsions was observed using a stereomicroscope (as described in Wang Z. L. et al., 2014) and the corrosion morphology was detected by a Scanning electron microscope.
The similarity in corrosion mechanism could be firstly testified by the dependence of corrosion rate on water concentration. As an example, Figure 7 illustrates the corrosion rate of steel samples in different mixtures, such as w/o emulsion and water containing SC CO2, where it presents a linear relationship with water concentration. Such a linear dependence of corrosion rate on water concentration could be found in a wide range of water concentrations, regardless of the experimental conditions, which was also observed in correlating the weight-loss data with water concentrations in a SC CO2 environment when the water concentration is higher than 1,000 ppmw (Sim et al., 2014a). It also reported that the conductivity of a w/o emulsion presented a linear relationship with water concentrations (Craig, 1998). This may be related to the impact of moving water droplets or clusters on steel surfaces. Generally, a higher water concentration may generate a larger volume of water droplets in mixed fluids (Plasencia et al., 2013). Compared with a SC CO2 fluid, crude oil can entrain a larger volume of water droplets, and thus the corrosion rate was not significantly increased at high water concentrations. This could be explained by the difference in wettability at steel surface. The oil phase is more effective than the dense CO2 phase against the adsorption of water droplets on steel surfaces.
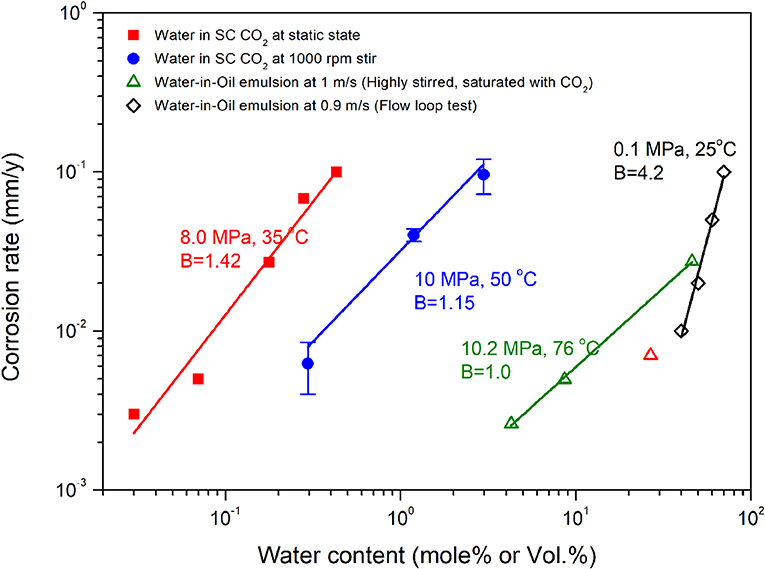
Figure 7. The dependence of corrosion rate on water concentration in different electrolyte/non-electrolyte binary systems. The red solid square and the blue solid circle refer to the corrosion data in SC CO2 environment according to Hua et al. (2014a) and Liu et al. (2018). The green open triangle and the black open rhombus refer to the corrosion rates in w/o emulsions or mixtures according to Sun et al. (2016a) and Li (2009). B represents the slope of the fitted line of the experimental data points in a log coordinate system.
In multiphase flow corrosion, the state of fluid structure has not been systematically investigated. Water entrainment and water settlement are the control steps in corrosion. The entrainment of water in crude oil is believed to be beneficial in corrosion mitigation (Wicks and Fraser, 1975; Craig, 1996; De Waard et al., 2003; Cai et al., 2012). Following this idea, methods to stabilize water in SC CO2 emulsions might also be effective in preventing pipeline corrosion, which has been widely investigated in food and purification industries. However, to date no effort has been made to tailor the SC CO2 fluid for a corrosion mitigation purpose. If it works, this method can be applied in CO2 transportation and injection systems.
Control Strategies
It should be noticed that the operation conditions for CO2 transportation, injection and oil production are different. As summarized in Table 2, their control strategies cannot be the same. Generally speaking, CRAs are most effective, which have been attempted in many projects (IEAGHG, 2010). For example, in a pilot-scale CO2-EOR project in Shengli oilfield, stainless steels were employed for the CO2 injection well tubes. There is no doubt that the use of CRAs is a safe choice when we have little knowledge on the corrosion risk of an operation system, but it is economically unacceptable. Coatings and liners are also adopted in CO2-EOR production wells (IEAGHG, 2010), but there are still challenging problems, such as blistering and detachment in deep well conditions.
Recently, several kinds of corrosion inhibitors were tested in simulated CO2 injection or transportation conditions (Turgoose et al., 2014; Choi et al., 2017; Xiang et al., 2017; Cen et al., 2019), which may theoretically be a reasonable choice in the aggressive environments. However, the corrosion inhibitors should be effective in high temperature conditions. Corrosion inhibitors have also been widely used in water injection systems where CO2 was involved. The presence of crude oil in the CO2-EOR production system may poison the inhibitors (Gulbrandsen and Kvarekval, 2007; Horsup et al., 2010), reducing their effectiveness. Therefore, the evaluation of corrosion inhibitors in oil-water mixed fluids becomes critical for the practical inhibitor selection (Li et al., 2014, 2016; Wang et al., 2019b). Presently, there is still lack of effective and applicable methods for the evaluation of corrosion inhibitors in oil-water mixed conditions (ASTM G202−12, 2016), which generally relies on a large-scale multiphase flow loop test (Salama and Brown, 2009; Cai et al., 2012; Wang and Zhang, 2016). Most recently, Wang et al. provided a possible method for the fast evaluation of corrosion inhibitors in oil/water alternate conditions by using a specially designed “Alternate Wetting Cell” (Wang et al., 2019a), with which a kind of ODD corrosion inhibitor has been evaluated to be effective (with a high inhibition efficiency of 99.9%) in oil-water media (Wang et al., 2019b). In a multiphase flow environment containing crude oil, the wettability at the oil/water/pipe interface and the emulsion state might be changed by the addition of a trace amount of organic agents, such as corrosion inhibitors (Foss et al., 2009; Li et al., 2014; Wang et al., 2019b) or some surfactant chemicals (Wang Z. L. et al., 2014; Quej-Ake et al., 2018), finally enhancing or decreasing the corrosion mitigation efficiency of crude oil.
To our knowledge, managing the process parameters is one of the most attractive methods for corrosion control in CO2-EOR production (Wicks and Fraser, 1975; Kang et al., 1996; Cai et al., 2012; Wang et al., 2015), as it is generally applicable, effective and inexpensive, but the control strategies must be relied on a deep understanding of the corrosion performance and corrosion mechanism of pipeline materials (Store et al., 2011). For example, to avoid corrosion damage of pipelines, CRAs were usually used and water was strictly limited below a very low concentration in an early pilot CO2-EOR project because of little knowledge on steel corrosion in a dense CO2 phase. Currently, it is generally believed that corrosion will not be a problem if there is no free water or water droplet settlement on the pipeline bottom. However, the critical water concentration threshold to trigger corrosion can be different, depending on pressure, temperature, flow rate, as well as the concentrations of impurities. Nevertheless, limiting water concentration is still the best choice for corrosion mitigation in CO2 transportation (Sim et al., 2014b; Barker et al., 2017). It can be deduced from the experimental simulation that pressurizing CO2 could extend the solubility of water (Wang and Song, 2018) and thus reduce the possibility of water wetting on steel surface. Slowing down the flow rate may reduce the probability of the bombardment of water clusters entrained in dense phase CO2, and thus decrease the density of iron carbonate particles on steel surface (Liu et al., 2018). In this way, transporting water containing CO2 at a high pressure and with a slow rate may be helpful for corrosion mitigation. In a WAG CO2 injection process, reducing the alternate frequency and increasing the injection rate can extend the service lifetime of well tube (Wang and Song, 2018). Obviously, tailoring the processing parameters in CO2 transportation and injection should be cautious as the environmental variation may totally change the control strategies.
In oil production, if water could be completely entrained into crude oil, corrosion would cease. Therefore, an effective method is to separate free water from crude oil before transportation. It would be safe if crude oil can be transported to the terminal station before de-emulsification and water settlement. In this way, a fast transportation seems to be beneficial. At the same time, a high flow rate stirs the fluid, hindering the deposition of free water. Similarly, a high gas-to-liquid ratio is also recommended to obtain a turbulent state and reduce the wetting of water at pipeline bottom (Wang et al., 2015). These control strategies are relevant to the management of flow patterns of oil, water and gas in pipeline. In some extreme conditions, emulsification of water into oil may be applicable in reducing the corrosion risk during long-distance transportation. It should be noticed that depressurizing may also reduce the corrosiveness of the CO2-containing fluids, which can be employed in the oil transportation and the water treatment stages.
Summary and Future Ideas
In this review, the corrosion of pipeline in CO2-EOR production is systematically analyzed from a fluid perspective. Firstly, the corrosion risk of pipeline at different stages of CO2-EOR production was evaluated relevant to the fluid properties. It identified that the presence of water in fluid was the key for triggering corrosion. In CO2 transportation and injection systems, although water was generally limited well below its saturation limit, the occasional water ingress or the alternate water slug may induce corrosion damage. In oil production and transportation systems, the presence of crude oil may reduce corrosion, while the flow pattern and the mixing state of oil and water were critical for determining the corrosion risk of well tubes and pipelines. In water treatment stage, the scaling problem should be noticed with a reduction in CO2 partial pressure. After a review of the corrosion behavior of steel materials in multiphase flow conditions according to the fluid states of CO2, water and crude oil, corrosion was supposed to be correlated with the fluid structure, in which the dependence of the corrosion rate on water concentrations was attributed to the fluid behavior of water droplet or clusters in an electrolyte/non-electrolyte binary system. An alternate wetting test method was introduced for better understanding the corrosion phenomena in oil/water intermittent flow. Finally, the corrosion control strategies were summarized. Besides the application of corrosion resistant materials and corrosion inhibitors, tailoring the processing parameter was suggested to be an attractive method for preventing corrosion in aggressive CO2-EOR production conditions. For the CO2 transportation and injection systems, limiting water concentrations, slowing down the flow rate and reducing contact time would be beneficial for corrosion mitigation. For the oil production system, enhancing the water entrainment, increasing the turbulence of flow and mitigating the corrosive environment would be helpful.
Future studies on multiphase flow corrosion associated with CO2-EOR production should address the flowing issues:
(1) Broadening ideas on corrosion control for aggressive CO2-saturated oil-water mixed fluids, for example, exploring the possibility of using oil/water alternate slugs to reduce corrosion risk of the pipeline bottom.
(2) Selection of suitable emulsifier agents in water-SC CO2 environments to extend the water limits for a secure transportation and injection of CO2.
(3) Deciphering the microscopic origin of corrosion initiation and propagation and their relationship with fluid structure in a binary mixed system.
(4) Developing new electrochemical and analytical methods in badly conductive and harsh environments, such as the water containing SC CO2 and the oil-water mixtures.
Author Contributions
ZW and G-LS wrote and finalized the paper. ZW and JZ collected and analyzed the field data.
Funding
This work was supported by the National Science Foundation of China under grant No. 51671163, the Natural Science Foundation of Fujian Province (Grant No. 2019J01031), and part of the experimental work was founded by the Technology Development Project of Shengli Oilfield Company (No. YKD1503).
Conflict of Interest
The authors declare that the research was conducted in the absence of any commercial or financial relationships that could be construed as a potential conflict of interest.
References
Amri, J., Gulbrandsen, E., and Nogueira, R. P. (2010). Propagation and arrest of localized attacks in carbon dioxide corrosion of carbon steel in the presence of acetic acid. Corrosion 66:035001. doi: 10.5006/1.3359618
ASTM G202−12 (2016). Comparison of Laboratory Methodologies to Evaluate Corrosion Inhibitors for Oil and Gas Pipelines. West Conshohocken: ASTM International.
Ayello, F., Evans, K., Thodla, R., and Sridhar, N. (2010). Effect of Impurities on Corrosion of Steel in Supercritical CO2. NACE Corrosion. San Antonio, TX: NACE International. doi: 10.1115/IPC2010-31053
Ayello, F., Robbins, W., Richter, S., and Nešić, S. (2013). Model compound study of the mitigative effect of crude oil on pipeline corrosion. Corrosion 69, 286–296. doi: 10.5006/0631
Barker, R., Burkle, D., Charpentier, T., Thompson, H., and Neville, A. (2018). A review of iron carbonate (FeCO3) formation in the oil and gas industry. Corrosion Sci. 142, 312–341. doi: 10.1016/j.corsci.2018.07.021
Barker, R., Hua, Y., and Neville, A. (2017). Internal corrosion of carbon steel pipelines for dense-phase CO2 transport in carbon capture and storage (CCS)–a review. Int. Mater. Rev. 62, 1–31. doi: 10.1080/09506608.2016.1176306
Bian, C., Wang, Z. M., Han, X., Chen, C. F., and Zhang, J. (2015). Electrochemical response of mild steel in ferrous ion enriched and CO2 saturated solutions. Corrosion Sci. 96, 42–51. doi: 10.1016/j.corsci.2015.03.015
Bouazaze, H., Huet, F., and Nogueira, R. P. (2005). A new approach for monitoring corrosion and flow characteristics in oil/brine mixtures. Electrochim. Acta 50, 2081–2090. doi: 10.1016/j.electacta.2004.08.051
Cai, J. Y., Li, C., Tang, X. P., Ayello, F., Richter, S., and Nesic, S. (2012). Experimental study of water wetting in oil–water two phase flow—horizontal flow of model oil. Chem. Eng. Sci. 73, 334–344. doi: 10.1016/j.ces.2012.01.014
Cao, G., Firouzdor, V., Sridharan, K., Anderson, M., and Allen, T. R. (2012). Corrosion of austenitic alloys in high temperature supercritical carbon dioxide. Corrosion Sci. 60, 246–255. doi: 10.1016/j.corsci.2012.03.029
Carpenter, M., Aarnes, J., Coleman, D., and Levett, B. (2011). Guideline for the Risk Management of Existing Wells at CO2 Geological Storage Sites. Det Norske Veritas. DNV Report No. 2011–0448.
Castillo, M., Rincon, H., Duplat, S., Vera, J., and Baron, E. (2000). Protective Properties of Crude Oils in CO2 and H2S Corrosion. Orlando, FL: NACE International.
Cen, H., Cao, J., Chen, Z., and Guo, X. (2019). 2-Mercaptobenzothiazole as a corrosion inhibitor for carbon steel in supercritical CO2-H2O condition. Appl. Surf. Sci. 476, 422–434. doi: 10.1016/j.apsusc.2019.01.113
Chen, Y., and Jepson, W. P. (1999). EIS measurement for corrosion monitoring under multiphase flow conditions. Electrochim. Acta 44, 4453–4464. doi: 10.1016/S0013-4686(99)00160-7
Choi, H. J., Cepulis, R. L., and Lee, J. B. (1989). Carbon dioxide corrosion of L80 grade tubular in flowing oil-brine two-phase environments. Corrosion 45, 943–950. doi: 10.5006/1.3585005
Choi, Y.-S., Hassani, S., Vu, T. N., and Nesic, S. (2015). Effect of H2S on the Corrosion Behavior of Pipeline Steels in Supercritical and Liquid CO2 Environments. NACE Corrosion. Dallas, TX: NACE International. doi: 10.5006/2026
Choi, Y.-S., Hassani, S., Vu, T. N., Nesic, S., Abas, A. Z. B., Nor, A. M., et al. (2017). Corrosion Inhibition of Pipeline Steels under Supercritical CO2 Environment. NACE Corrosion. New Orleans, LA: NACE International.
Choi, Y.-S., and Nešić, S. (2011). Determining the corrosive potential of CO2 transport pipeline in high pCO2-water environments. Int. J. Greenhouse Gas Control 5, 788–797. doi: 10.1016/j.ijggc.2010.11.008
Choi, Y. S., Nesic, S., and Young, D. (2010). Effect of impurities on the corrosion behavior of CO2 transmission pipeline steel in supercritical CO2-water environments. Environ. Sci. Technol. 44, 9233–9238. doi: 10.1021/es102578c
Cole, I. S., Corrigan, P., Sim, S., and Birbilis, N. (2011). Corrosion of pipelines used for CO2 transport in CCS: Is it a real problem? Int. J. Greenhouse Gas Control 5, 749–756. doi: 10.1016/j.ijggc.2011.05.010
Craig, B. (1998). Predicting the conductivity of water-in-oil solutions as a means to estimate corrosiveness. Corrosion 54, 657–662. doi: 10.5006/1.3287645
Cui, Z. D., Wu, S. L., Zhu, S. L., and Yang, X. J. (2006). Study on corrosion properties of pipelines in simulated produced water saturated with supercritical CO2. Appl. Surf. Sci. 252, 2368–2374. doi: 10.1016/j.apsusc.2005.04.008
Dai, Z., Middleton, R., Hari, V., Fessenden-Rahn, J., Bauman, J., Pawar, R. S.-, et al. (2014). An integrated framework for optimizing CO2 sequestration and enhanced oil recovery. Environ. Sci. Technol. Lett. 1, 49–54. doi: 10.1021/ez4001033
Dang, C., Nghiem, L., Nguyen, N., Chen, Z., and Nguyen, Q. (2016). Evaluation of CO2 low salinity water-alternating-gas for enhanced oil recovery. J. Nat. Gas Sci. Eng. A 35, 237–258. doi: 10.1016/j.jngse.2016.08.018
de Visser, E., Hendriks, C., Barrio, M., Molnvik, M. J., de Koeijer, G., Liljemark, S., et al. (2008). Dynamics CO2 quality recommendations. Int. J. Greenhouse Gas Control 2, 478–484. doi: 10.1016/j.ijggc.2008.04.006
De Waard, C., Lotz, U., and Milliams, D. E. (1991). Predictive model for CO2 corrosion engineering in wet natural gas pipelines. Corrosion 47, 976–985. doi: 10.5006/1.3585212
De Waard, C., Smith, L. M., and Craig, B. D. (2003). The Influence of Crude Oils on Well Tubing Corrosion Rates. San Diego, CA: NACE Corrosion.
Dugstad, A., Halseid, M., and Morland, B. (2013a). Effect of SO2 and NO2 on corrosion and solid formation in dense phase CO2 pipelines. Energy Proc. 37, 2877–2887. doi: 10.1016/j.egypro.2013.06.173
Dugstad, A., Halseid, M., Morland, B., and Sivertsen, A. O. (2013b). Corrosion in dense phase CO2 - the impact of depressurisation and accumulation of impurities. Energy Proc. 37, 3057–3067. doi: 10.1016/j.egypro.2013.06.192
Dugstad, A., Morland, B., and Clausen, S. (2011a). Corrosion of transport pipelines for CO2-Effect of water ingress. Energy Proc. 4, 3063–3070. doi: 10.1016/j.egypro.2011.02.218
Dugstad, A., Morland, B., and Clausen, S. (2011b). Geochemical investigation of the combined effect of injecting low salinity water and carbon dioxide on carbonate reservoirs. Energy Proc. 4, 3063–3070. doi: 10.1016/j.egypro.2014.11.800
Efird, K. D., and Jasinski, R. J. (1989). Effect of the crude oil on corrosion of steel in crude oiI/brine production. Corrosion 45, 165–171. doi: 10.5006/1.3577835
Efird, K. D., Smith, J. L., Blevins, S. E., and Davis, N. D. (2004). The Crude Oil Effect on Steel Corrosion Wettability Preference and Brine Chemistry. NACE Corrosion. Houston, TX: NACE International.
Esmaeely, S. N., Choi, Y. S., Young, D., and Nesic, S. (2013). Effect of calcium on the formation and protectiveness of iron carbonate layer in CO2 corrosion. Corrosion 69, 912–920. doi: 10.5006/0942
Farajzadeh, R., Zitha, P. L. J., and Bruining, J. (2009). Enhanced mass transfer of CO2 into water: experiment and modeling. Ind. Eng. Chem. Res. 48, 6423–6431. doi: 10.1021/ie801521u
Fingas, M., and Fieldhouse, B. (2004). Formation of water-in-oil emulsions and application to oil spill modelling. J. Hazard. Mater. 107, 37–50. doi: 10.1016/j.jhazmat.2003.11.008
Fordham, E. J., Ramos, R. T., Holmes, A., Simonian, S. S.-, Huang, M., and Lenn, C. P. (1999). Multi-phase-fluid discrimination with local fibre-optical probes: III. Three-phase flows. Meas. Sci. Technol. 10, 1347–1352. doi: 10.1088/0957-0233/10/12/333
Foss, M., Gulbrandsen, E., and Sjoblom, J. (2009). Effect of corrosion inhibitors and oil on carbon dioxide corrosion and wetting of carbon steel with ferrous carbonate deposits. Corrosion 65, 3–14. doi: 10.5006/1.3319113
Freitag, N. P. (2018). Similarity of the effect of different dissolved gases on heavy-oil viscosity. SPE Reserv. Eval. Eng. 2018:189456. doi: 10.2118/189456-PA
Frising, T., Noik, C., and Dalmazzone, C. (2006). The liquid/liquid sedimentation process: from droplet coalescence to technologically enhanced water/oil emulsion gravity separators: a review. J. Dispersion Sci. Technol. 27, 1035–1057. doi: 10.1080/01932690600767098
Glezakou, V.-A., Rousseau, R., Dang, L. X., and McGrail, B. P. (2010). Structure, dynamics and vibrational spectrum of supercritical CO2 /H2O mixtures from ab initio molecular dynamics as a function of water cluster formation. Phys. Chem. Chem. Phys. 12, 8759–8771. doi: 10.1039/b923306g
Grogan, A. T., Pinczewski, V. W., and Ruskauff, G. J. (1988). Diffusion of CO2 at reservoir conditions: models and measurements. SPE Reserv. Eng. 3, 93–102. doi: 10.2118/14897-PA
Gulbrandsen, E., and Kvarekval, J. (2007). Effect of oil-in-water emulsions on the performance of carbon dioxide corrosion inhibitors. Corrosion 63, 187–196. doi: 10.5006/1.3278343
Han, D., Jiang, R. J., and Cheng, Y. F. (2013). Mechanism of electrochemical corrosion of carbon steel under deoxygenated water drop and sand deposit. Electrochim. Acta 114, 403–408. doi: 10.1016/j.electacta.2013.10.079
Hoffmann, R., and Johnson, G. W. (2011). Measuring phase distribution in high pressure three-phase flow using gamma densitometry. Flow Meas. Instrument. 22, 351–359. doi: 10.1016/j.flowmeasinst.2011.02.005
Hornafius, K. Y., and Hornafius, J. S. (2015). Carbon negative oil: a pathway for CO2 emission reduction goals. Int. J. Greenhouse Gas Control 37, 492–503. doi: 10.1016/j.ijggc.2015.04.007
Horsup, D. L., Clark, J. C., Binks, B. P., Fletcher, P. D. L., and Hicks, J. T. (2010). The fate of oilfield corrosion inhibitors in multiphase systems. Corrosion 66:036001. doi: 10.5006/1.3359624
Hua, Y., Barker, R., Charpentier, T., Ward, M., and Neville, A. (2015). Relating iron carbonate morphology to corrosion characteristics for water-saturated supercritical CO2 systems. J. Supercritical Fluids 98, 183–193. doi: 10.1016/j.supflu.2014.12.009
Hua, Y., Barker, R., and Neville, A. (2014a). Effect of temperature on the critical water content for general and localised corrosion of X65 carbon steel in the transport of supercritical CO2. Int. J. Greenhouse Gas Control 31, 48–60. doi: 10.1016/j.ijggc.2014.09.026
Hua, Y., Barker, R., and Neville, A. (2014b). Understanding the influence of SO2 and O2 on the corrosion of carbon steel in water-saturated supercritical CO2. Corrosion 71, 667–683. doi: 10.5006/1504
IEAGHG (2010). Corrosion and Selection of Materials for Carbon Capture and Storage. International Energy Agency. Available online at: https://hub.globalccsinstitute.com/publications/corrosion-and-materials-selection-ccs-systems/overview
Ingham, B., Ko, M., Laycock, N., Burnell, J., Kappen, P., Kimpton, J. A., et al. (2012). In-situ synchrotron X-ray diffraction study of scale formation during CO2 corrosion of carbon steel in sodium and magnesium chloride solutions. Corrosion Sci. 56, 96–104. doi: 10.1016/j.corsci.2011.11.017
Jacobson, G. A. (2014). Pipeline corrosion issues related to carbon capture, transportation and storage. Mater. Perform. 53, 24–31. Available online at: http://www.materialsperformance.com/articles/material-selection-design/2015/08/pipeline-corrosion-issues-related-to-carbon-capture-transportation-and-storage
Jepson, W. P., and Menezes, R. (1995). The Effects of Oil Viscosity on Sweet Corrosion in Multiphase Oil, Water/Gas Horizontal Pipelines. NACE Corrosion. Orlando, FL: NACE International.
Jiang, R. J., and Cheng, Y. F. (2013). Mechanism of electrochemical corrosion of steel under water drop. Electrochem. Commun. 35, 8–11. doi: 10.1016/j.elecom.2013.07.019
Kang, C., Jepson, W. P., and Gopal, M. (1999). Effect of drag-reducing agent on slug characteristics in multiphase flow in inclined pipes. J. Energy Resour. Technol. 121, 86–90. doi: 10.1115/1.2795073
Kang, C., Wilkens, R. J., and Jepson, W. P. (1996). The Effect of Slug Frequency on Corrosion in High-Pressure, Inclined Pipelines. Denver, CO: NACE Corrosion.
Kanwar, S. (1994). Study and Modeling of Sweet Corrosion of Multiphase Mixtures in a Horizontal Pipeline (Master's thesis). Ohio University, Athens, OH.
Kee, K. E., Richter, S., Babic, M., and Nesic, S. (2014). Flow Patterns and Water Wetting in Oil-Water Two Phase Flow - A Flow Loop Study. NACE-Corrosion. San Antonio, TX: NACE International.
Kouba, G. E., and Jepson, P. (1990). The flow of slugs in horizontal, two-phase pipelines. J. Energy Resour. Technol. 112, 20–24. doi: 10.1115/1.2905707
Kutchko, B. G., Strazisar, B. R., Dzombak, D. A., Lowry, G. V., and Thaulow, N. (2007). Degradation of well cement by CO2 under geologic sequestration conditions. Environ. Sci. Technol. 41, 4787–4792. doi: 10.1021/es062828c
Landry, X., Runstedtler, A., Papavinasam, S., and Place, T. D. (2012). Computational fluid dynamics study of solids deposition in heavy oil transmission pipeline. Corrosion 68, 904–912. doi: 10.5006/0444
Lee, T. C. Jr., Psathas, P. A., and Johnston, K. P. (1999). Water-in-carbon dioxide emulsions: formation and stability. Langmuir 15, 6781–6791. doi: 10.1021/la9903548
Li, C. (2009). Effect of Corrosion Inhibitor on Water Wetting and Carbon Dioxide Corrosion in Oil-Water Two-Phase Flow (Ph.D. thesis). Ohio University, Athens, OH.
Li, C., Richter, S., and Nešić, S. (2014). How do inhibitors mitigate corrosion in oil-water two-phase flow beyond lowering the corrosion rate? Corrosion 70, 958–966. doi: 10.5006/1057
Li, C., Tang, X. P., Ayello, F., Cai, J. Y., and Nesic, S. (2006). Experimental Study on Water Wetting and CO2 Corrosion in Oil-Water Two-Phase Flow. San Diego, CA: NACE Corrosion.
Li, W., Pots, B. F. M., Brown, B., Kee, K. E., and Nesic, S. (2016). A direct measurement of wall shear stress in multiphase flow - Is it an important parameter in CO2 corrosion of carbon steel pipelines? Corrosion Sci. 110, 35–45. doi: 10.1016/j.corsci.2016.04.008
Lindeberg, E. (2011). Modelling pressure and temperature profile in a CO2 injection well. Energy Proc. 4, 3935–3941. doi: 10.1016/j.egypro.2011.02.332
Liu, A. Q., Bian, C., Wang, Z. M., Han, X., and Zhang, J. (2018). Flow dependence of steel corrosion in supercritical CO2 environments with different water concentrations. Corrosion Sci. 134, 149–161. doi: 10.1016/j.corsci.2018.02.027
Lotz, U. L., Bodegom, V., and Ouwehand, C. (1991). The effect of type of oil or gas condensate on carbonic acid corrosion. Corrosion 47, 635–645. doi: 10.5006/1.3585301
Luo, X., Lü, G., Zhang, W., He, L., and Lü, Y. (2017). Flow structure and pressure gradient of extra heavy crude oil-water two phase flow. Exp. Thermal Fluid Sci. 82, 174–181. doi: 10.1016/j.expthermflusci.2016.11.015
Lv, G., Li, Q., Wang, S., and Li, X. (2015). Key techniques of reservoir engineering and injection-production process for CO2 flooding in China's SINOPEC Shengli Oilfield. J. CO2 Utilization 11, 31–40. doi: 10.1016/j.jcou.2014.12.007
Maley, J. (1997). Slug flow characteristics and corrosion rates in inclined high pressure multiphase flow pipes (Master degree). Ohio University, Athens, OH.
McGrail, B. P., Schaef, H. T. V., Glezakou, A., Dang, L. X., and Owen, A. T. (2009). Water reactivity in the liquid and supercritical CO2 phase: has half the story been neglected? Energy Proc. 1, 3415–3419. doi: 10.1016/j.egypro.2009.02.131
Mendez, C., Duplat, S., Hernandez, S., and Vera, J. (2001). On the Mechanism of Corrosion Inhibition by Crude Oils. Houston, TX: NACE Corrosion.
Mohitpour, M., Seevam, P., Botros, K. K., Rothwell, B., and Ennis, C. (2012). Chapter 5: Pipeline Transportation of Carbon Dioxide Containing Impurities. ASME Press. doi: 10.1115/1.859834
Nesic, S. (2007). Key issues related to modelling of internal corrosion of oil and gas pipelines – A review. Corrosion Sci. 49, 4308–4338. doi: 10.1016/j.corsci.2007.06.006
Nesic, S., and Carroll, F. (2003). Horizontal rotating cylinder-A compact apparatus for studying the effect of water wetting on carbon dioxide corrosion of mild steel. Corrosion 59, 1085–1095. doi: 10.5006/1.3277528
Nesic, S., Xiao, Y., and Pots, B. F. M. (2004). A Quasi 2-D Localized Corrosion Model. NACE Corrosion. New Orleans, FL: NACE International.
Nyborg, R. (1998). Initiation and Growth of Mesa Corrosion Attack During CO2 Corrosion of Carbon Steel. NACE Corrosion. San Diego, CA: NACE International.
Oosterkamp, A., and Ramsen, J. (2008). State-of-the-art overview of CO2 pipeline transport with relevance to offshore pipelines. Polytech Report No.: POL-O-2007-2138-A. Available online at: https://www.researchgate.net/publication/228688545_State-of-the-Art_Overview_of_CO_2_Pipeline_Transport_with_Relevance_to_Offshore_Pipelines
Paolinelli, L. D., Rashedi, A., and Yao, J. (2018). Characterization of droplet sizes in large scale oil-water flow downstream from a globe valve. Int. J. Multiphase Flow 99, 132–150. doi: 10.1016/j.ijmultiphaseflow.2017.09.014
Papavinasam, S., Doiron, A., Panneerselvam, T., and Revie, R. W. (2007). Effect of hydrocarbons on the internal corrosion of oil and gas pipelines. Corrosion 63, 704–712. doi: 10.5006/1.3278419
Plasencia, J., Pettersen, B., and Nydal, O. J. (2013). Pipe flow of water-in-crude oil emulsions: effective viscosity, inversion point and droplet size distribution. J. Petrol. Sci. Eng. 101, 35–43. doi: 10.1016/j.petrol.2012.11.009
Pouraria, H., Seo, J. K., and Paik, J. K. (2016). A numerical study on water wetting associated with the internal corrosion of oil pipelines. Ocean Eng. 122, 105–117. doi: 10.1016/j.oceaneng.2016.06.022
Quej-Ake, L. M., Contreras, A., and Aburto, J. (2018). The effect of non-ionic surfactant on the internal corrosion for X52 steel in extra-heavy crude oil-in-water emulsions. Anti Corrosion Methods Mater. 65, 234–248. doi: 10.1108/ACMM-03-2017-1770
Race, J. M., Wetenhall, B., Seevam, P. N., and Downie, M. J. (2012). Towards a CO2 pipeline specification: defining tolerance limits for impurities. J. Pipeline Eng. 11, 173–190. Availble online at: https://pureportal.strath.ac.uk/en/publications/towards-a-co2-pipeline-specification-defining-tolerance-limits-fo
Rogers, J. D., and Grigg, R. B. (2001). A literature analysis of the WAG injectivity abnormalities in the CO2 process. SPE Reserv. Eval. Eng. 4, 375–386. doi: 10.2118/73830-PA
Rostami, A., Arabloo, M., Kamari, A., and Mohammadi, A. H. (2017). Modeling of CO2 solubility in crude oil during carbon dioxide enhanced oil recovery using gene expression programming. Fuel 210, 768–782. doi: 10.1016/j.fuel.2017.08.110
Ruan, B., Xu, R., Wei, L., Ouyang, X., Luo, F., and Jiang, P. (2013). Flow and thermal modeling of CO2 in injection well during geological sequestration. Int. J. Greenhouse Gas Control 19, 271–280. doi: 10.1016/j.ijggc.2013.09.006
Ruhl, A. S., and Kranzmann, A. (2013). Investigation of pipeline corrosion in pressurized CO2 containing impurities. Energy Proc. 37, 3131–3136. doi: 10.1016/j.egypro.2013.06.199
Salama, M., and Brown, B. (2009). Factors Affecting CO2 Corrosion and Inhibitor Effectiveness Using Multi-phase Flow Loop. NACE-Corrosion. Atlanta, GA: NACE International.
Sandana, D., Hadden, M., Race, J., and Charles, E. (2012). Transport of gaseous and dense carbon dioxide in pipelines: is there an internal corrosion risk? J. Pipeline Eng. 11, 229–238. Available online at: https://pureportal.strath.ac.uk/en/publications/transport-of-gaseous-and-dense-phase-carbon-dioxide-is-there-an-i
Sarica, C., and Zhang, H. (2008). DOE Final Report: Development of Next Generation Multiphase Pipe Flow Prediction Tools. Tulsa, OK: The University of Tulsa.
Schmitt, G., Bosch, C., Mueller, M., and Siegmund, G. (2000). A Probabilistic Model for Flow Induced Localized Corrosion. NACE Corrosion. Orlando, FL: NACE International: 00049.
Shamsa, A., Barker, R., Hua, Y., Barmatov, E., Hughes, T. L., and Neville, A. (2019). The role of Ca2+ ions on Ca/Fe carbonate products on X65 carbon steel in CO2 corrosion environments at 80 and 150oC. Corrosion Sci. 156, 58–70. doi: 10.1016/j.corsci.2019.05.006
Sim, S., Bocher, F., Cole, I. S. X.-, Chen, B., and Birbilis, N. (2014a). Investigating the effect of water content in supercritical CO2 as relevant to the corrosion of carbon capture and storage pipelines. Corrosion 70, 185–195. doi: 10.5006/0944
Sim, S., Cole, I. S., Choi, Y. S., and Birbilis, N. (2014b). A review of the protection strategies against internal corrosion for the safe transport of supercritical CO2 via steel pipelines for CCS purposes. Int. J. Greenhouse Gas Control 29, 185–199. doi: 10.1016/j.ijggc.2014.08.010
Singh, R., Eng, M. S., and Mweldi, I. (2010). “Enhanced oil recovery and CO2 corrosion a challenge,” in 2010 China International Pipeline Forum (Langfang), 162–171.
Smart, J. S. (2001). Wettability- A major factor in oil and gas system corrosion. Mater. Perform. 40, 54–59. Available online at: https://jglobal.jst.go.jp/en/detail?JGLOBAL_ID=200902186387082008&rel=0
Sokolova, I. M., Abryutina, N. N., Punanov, V. G., and Petrov, A. A. (1992). Chemical classification of naphthenic condensates and oils. Organ. Geochem. 19, 1–11. doi: 10.1016/0146-6380(92)90023-Q
Sotgia, G., Tartarini, P., and Stalio, E. (2008). Experimental analysis of flow regimes and pressure drop reduction in oil–water mixtures. Int. J. Multiphase Flow 34, 1161–1174. doi: 10.1016/j.ijmultiphaseflow.2008.06.001
Stack, M. M., and Abdulrahman, G. H. (2012). Mapping erosion–corrosion of carbon steel in oil–water solutions: effects of velocity and applied potential. Wear 274–275, 401–413. doi: 10.1016/j.wear.2011.10.008
Store, M., Passade-Boupat, N., Bonis, M., and Adams, B. (2011). Inhibitive Properties of Crude Oils: Can We Count on Them? Houston, TX: NACE Corrosion.
Sun, J., Sun, C., Zhang, G., Zhao, W., and Wang, Y. (2016a). Effect of water cut on the localized corrosion behavior of P110 tube steel in supercritical CO2/oil/water environment. Corrosion 72, 1470–1482. doi: 10.5006/1926
Sun, J. B., Sun, C., Zhang, G. A., Li, X. D., Zhao, W. M., Jiang, T., et al. (2016b). Effect of O2 and H2S impurities on the corrosion behavior of X65 steel in water-saturated supercritical CO2 system. Corrosion Sci. 107, 31–40. doi: 10.1016/j.corsci.2016.02.017
Taleb, W., Pessu, F., Wang, C., Charpentier, T., Barker, R., and Neville, A. (2017). Siderite micro-modification for enhanced corrosion protection. NPJ Mater. Degrad. 1:13. doi: 10.1038/s41529-017-0014-1
Tang, X., Xu, L. Y., and Cheng, Y. F. (2008). Electrochemical corrosion behavior of X-65 steel in the simulated oil-sand slurry. II: Synergism of erosion and corrosion. Corrosion Sci. 50, 1469–1474. doi: 10.1016/j.corsci.2008.01.019
Tavares, L. M., da Costa, E. M., Andrade, J. J. D., Hubler, R., and Huet, B. (2015). Effect of calcium carbonate on low carbon steel corrosion behavior in saline CO2 high pressure environments. Appl. Surf. Sci. 359, 143–152. doi: 10.1016/j.apsusc.2015.10.075
Thanthiriwatte, K. S., Duke, J. R., Jackson, V. E., Felmy, A. R., and Dixon, D. A. (2012). High-level Ab initio predictions of the energetics of mCO2 ·(H 2 O) n (n = 1-3, m = 1-12) clusters. J. Phys. Chem. A 116,: 9718–9729. doi: 10.1021/jp306594h
Turgoose, S., John, G., Flynn, M., Kadir, A. A., Economopoulos, G., and Dicken, G. (2014). Corrosion Inhibition in Supercritical Carbon Dioxide Systems Containing Water. NACE Corrosion. San Antonio, TX: NACE International.
Tzimas, E., Georgakaki, A., Garcia, C. C., and Peteves, S. D. (2005). Enhanced Oil Recovery Using Carbon Dioxide in the European Energy System. Petten: Institute for Energy.
Villarreal, J., Laverde, D., and Fuentes, C. (2006). Carbon-steel corrosion in multiphase slug flow and CO2. Corrosion Sci. 48, 2363–2379. doi: 10.1016/j.corsci.2005.09.003
Wang, H., Cai, J., Bosch, C., Jepson, W., and Hong, T. (2002). Enhanced Mass Transfer and Wall Shear Stress in Multiphase Slug Flow. Denver, CO: NACE Corrosion.
Wang, Z., Felmy, A. R., Thompson, C. J., Loring, J. S., Joly, A. G., Rosso, K. M., et al. (2013). Near-infrared spectroscopic investigation of water in supercritical CO2 and the effect of CaCl2. Fluid Phase Equil. 338, 155–163. doi: 10.1016/j.fluid.2012.11.012
Wang, Z. L., Zhang, J., Wang, Z. M., Zhou, L., Han, X., Li, Q. F., et al. (2014). Emulsification reducing the corrosion risk of mild steel in oil-brine mixtures. Corrosion Sci. 86, 310–317. doi: 10.1016/j.corsci.2014.06.009
Wang, Z. M., Han, X., Zhang, J., and Wang, Z. L. (2014). In-situ observation of CO2 corrosion under high pressure. Corros. Eng. Sci. Tech. 49, 352–356. doi: 10.1179/1743278213Y.0000000144
Wang, Z. M., Liu, X. T., Han, X., and Zhang, J. (2015). Managing internal corrosion of mild steel pipelines in CO2 enhanced oil recovery multiphase flow conditions. Energy Technol. 3, 225–233. doi: 10.1002/ente.201402159
Wang, Z. M., Lun, Q. Y., Wang, J., Han, X., Zhang, J., and Song, G. L. (2019a). Corrosion mitigation behavior of an alternately wetted steel electrode in oil/water media. Corrosion Sci. 152, 140–152. doi: 10.1016/j.corsci.2019.03.008
Wang, Z. M., and Song, G.-,L. (2018). An Analytical model for the corrosion risk of water alternating gas injection wells in CO2 enhanced oil recovery. Adv. Theory Simul. 1:1800041. doi: 10.1002/adts.201800041
Wang, Z. M., Song, G.-L., Wang, J., Han, X., and Zhang, J. (2019b). Fast Evaluation of Corrosion Inhibitors Used in Oil/Water Mixed Fluids. NACE Corrosion. Nashville, TN: NACE International.
Wang, Z. M., and Zhang, J. (2016). Corrosion of multiphase flow pipelines: the impact of crude oil. Corrosion Rev. 34, 17–40. doi: 10.1515/corrrev-2015-0053
Wei, L., Pang, X., and Gao, K. (2018). Effect of flow rate on localized corrosion of X70 steel in supercritical CO2 environments. Corrosion Sci. 136, 339–351. doi: 10.1016/j.corsci.2018.03.020
Wicks, M., and Fraser, J. P. (1975). Entrainment of water by flowing oil. Materials Perform. 14, 9–12.
Xiang, Y., Long, Z. W., Li, C., Huang, H., and He, X. (2017). Inhibition of N80 steel corrosion in impure supercritical CO2 and CO2-saturated aqueous phases by using imino inhibitors. Int. J. Greenhouse Gas Control 63, 141–149. doi: 10.1016/j.ijggc.2017.05.010
Xiang, Y., Wang, Z., Xu, M. H., Li, Z., and Ni, W. D. (2013). A mechanistic model for pipeline steel corrosion in supercritical CO2-SO2-O2-H2O environments. J. Supercrit. Fluids 82, 1–12. doi: 10.1016/j.supflu.2013.05.016
Xu, X. X. (2007). Study on oil–water two-phase flow in horizontal pipelines. J. Petrol. Sci. Eng. 59, 43–58. doi: 10.1016/j.petrol.2007.03.002
Yang, D. R., Rosas, O., and Castaneda, H. (2014). FeCO3 layer evolution for API 5L X52 steel in carbon dioxide-saturated NaCl brine in the presence of 1-decyl-3-methyrimidazolium chloride. Corrosion Sci. 87, 40–50. doi: 10.1016/j.corsci.2014.05.021
Yang, M., Wang, Z. M., Han, X., and Zhang, J. (2017). Corrosion inhibition by the trace amount of sulphide ion in CO2-saturated brine solutions. Corrosion Eng. Sci. Technol. 52, 73–79. doi: 10.1080/1478422X.2016.1216661
Yang, Y., Brown, B., Nesic, S., Gennaro, M. E., and Molinas, B. (2010). Mechanical Strength and Removal of a Protective Iron Carbonate Layer Formed on Mild Steel in CO2 Corrosion. San Antonio, TX: NACE Corrosion.
Yang, Z., Li, M., Peng, B., Lin, M., and Dong, Z. (2013). Volume expansion of CO2 + oil at near critical and supercritical conditions of CO2. Fuel 112, 283–288. doi: 10.1016/j.fuel.2013.04.037
Zhang, J., Wang, Z. L., Wang, Z. M., and Han, X. (2012). Chemical analysis of the initial corrosion layer on pipeline steels in simulated CO2-enhanced oil recovery brines. Corrosion Sci. 65, 397–404. doi: 10.1016/j.corsci.2012.08.045
Zhang, Y., Pang, X., Qu, S., Li, X., and Gao, K. (2012). Discussion of the CO2 corrosion mechanism between low partial pressure and supercritical condition. Corrosion Sci. 59, 186–197. doi: 10.1016/j.corsci.2012.03.006
Zhang, Y. N., Wang, T. L., Han, X., Wang, Z. M., and Zhang, J. (2016). Corrosion of artificial rock layer covered steel electrodes in a CO2 environment: the influence of permeability. Corrosion Sci. 105, 190–201. doi: 10.1016/j.corsci.2016.01.017
Zhang, Y. Y., Zhang, Y., and Zhang, J. (2013). Environmental impacts of Carbon capture, transmission, enhanced oil recovery and sequestration: an overview. Environ. Forensics 14, 301–305. doi: 10.1080/15275922.2013.843616
Zheng, D. H., Che, D. F., and Liu, Y. H. (2008). Experimental investigation on gas–liquid two-phase slug flow enhanced carbon dioxide corrosion in vertical upward pipeline. Corrosion Sci. 50, 3005–3020. doi: 10.1016/j.corsci.2008.08.006
Keywords: CCS, CO2-EOR, multiphase flow corrosion, corrosion mechanism, pipeline
Citation: Wang ZM, Song G-L and Zhang J (2019) Corrosion Control in CO2 Enhanced Oil Recovery From a Perspective of Multiphase Fluids. Front. Mater. 6:272. doi: 10.3389/fmats.2019.00272
Received: 20 February 2019; Accepted: 16 October 2019;
Published: 01 November 2019.
Edited by:
Wei Gao, The University of Auckland, New ZealandReviewed by:
Wolfram Fürbeth, DECHEMA Forschungsinstitut (DFI), GermanyGuangyu Sun, China University of Petroleum (Huadong), China
Copyright © 2019 Wang, Song and Zhang. This is an open-access article distributed under the terms of the Creative Commons Attribution License (CC BY). The use, distribution or reproduction in other forums is permitted, provided the original author(s) and the copyright owner(s) are credited and that the original publication in this journal is cited, in accordance with accepted academic practice. No use, distribution or reproduction is permitted which does not comply with these terms.
*Correspondence: Zi Ming Wang, em13YW5nQHhtdS5lZHUuY24=; Guang-Ling Song, Z3VhbmdsaW5nLnNvbmdAaG90bWFpbC5jb20=