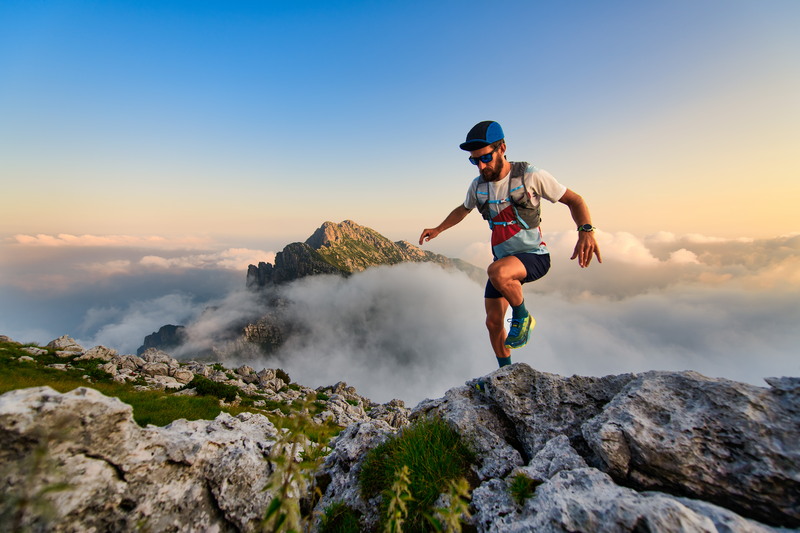
95% of researchers rate our articles as excellent or good
Learn more about the work of our research integrity team to safeguard the quality of each article we publish.
Find out more
EDITORIAL article
Front. Mater. , 20 August 2019
Sec. Mechanics of Materials
Volume 6 - 2019 | https://doi.org/10.3389/fmats.2019.00199
This article is part of the Research Topic Multiscale lattices and composite materials: Optimal design, modeling and characterization View all 15 articles
Editorial on the Research Topic
Multiscale Lattices and Composite Materials: Optimal Design, Modeling and Characterization
The Research Topic “Multiscale lattices and composite materials:” (MLCM) is focused on the optimal design, modeling, and characterization of novel lattices, composite materials, and structures at different scales, through the control of the internal architecture of the system.
A fundamental goal of this article collection is the study of mechanical metamaterials that are able to form next-generation-generation cellular solids; lattice materials, multiscale composites; and structural-scale systems. The collection took inspiration from the peculiar behaviors exhibited by structured materials at multiple scales (Bosia et al., 2018). The latter include, for example, high stiffness, strength, and toughness at extremely low densities (Meza et al., 2014), phononic band-gaps (Lu et al., 2009), sound control ability (Cummer et al., 2016); negative effective mass density (Liu et al., 2000); localized confined waves (Theocharis et al., 2013), to name but a few examples. The research reported devoted special attention to the creation of complex mechanical systems with properties derived mainly from their geometric design rather than their chemical composition (Cummer et al., 2016; Bertoldi et al., 2017). Also investigated was the use of multiscale lattices to optimally design reinforcing elements for novel composite materials (Fleck et al., 2010; Li et al., 2014). The chosen modeling and experimental approaches were able to predict and characterize the intrinsically complex mechanical behavior of the analyzed systems through multiscale techniques.
The papers forming the MLCM collection can be grouped into two basic categories. The first of these is centered around the design, modeling, and characterization of lattice structures at different scales, through the maximization of the frequency bandgap width at suitable center frequencies (Arretche and Matlack; Bacigalupo et al.); the optimal design and mechanical modeling of tensegrity metamaterials (De Tommasi et al.), superstable pre-stressed networks (Kelly et al.), graphene sheets (Genoese et al.); dome-shaped auxetic metamaterials (Easey et al.); and solar façades that employ dynamic sunscreens with tensegrity architecture (Babilio et al.). This first group of papers also includes contributions dealing with the development of non-destructive testing and structural health monitoring techniques that make use of guided elastic waves (Miniaci et al.), as well as the experimental characterization of the microstructure of the Nephila dragline silk (Stehling et al.).
A second category focuses on the modeling and characterization of novel composite materials, with emphasis on the mechanical properties, for example, of bamboo fiber-reinforced composites (Javadian et al.); the effects of defects, porosity, and damage on the mechanical properties of metallic materials to be employed in additive manufacturing processes (Goodall et al.); the macroscopic response of micropolar continua with anisotropic microstructure (Fantuzzi et al.); the addition of lattice-shaped inclusions to metaconcretes (Briccola et al.); and the propagation of pressure waves in three-dimensional arrangements of coated spheres (Dupont et al.).
Our hope is that the research presented in this collection will stimulate new and exciting research in the fields of mechanical metamaterials and multiscale composite materials and structures, through an integrated approach that includes the design and the mechanical modeling of real-scale, or reduced-scale prototypes; the optimal control of suitable design variables; and the experimental validation of the theoretical predictions.
All authors listed have made a substantial, direct and intellectual contribution to the work, and approved it for publication.
The authors declare that the research was conducted in the absence of any commercial or financial relationships that could be construed as a potential conflict of interest.
The handling editor declared a past collaboration with the authors FF, CD.
Bertoldi, K., Vitelli, V., Christensen, J., and Van Hecke, M. (2017). Flexible mechanical metamaterials. Nat. Rev. Mater. 2:17066. doi: 10.1038/natrevmats.2017.66
Bosia, F., Krushynska, A. O., Miniaci, M., Morvan, B., and Pugno, N. M. (2018). Editorial: advances in mechanical metamaterials. Front. Mater. 5:56. doi: 10.3389/fmats.2018.00056
Cummer, S. A., Christensen, J., and Alu, A. (2016). Controlling sound with acoustic metamaterials. Nat. Rev. Mater. 1:16001. doi: 10.1038/natrevmats.2016.1
Fleck, N. A., Deshpande, V. S., and Ashby, M. F. (2010). Micro-architectured materials: past, present and future. Proc. R. Soc. A 466, 2495–2516. doi: 10.1098/rspa.2010.0215
Li, J., Wu, Z., Huang, C., and Li, L. (2014). Multiscale carbon nanotube-woven glass fiber reinforced cyanate ester/epoxy composites for enhanced mechanical and thermal properties. Compos. Sci. Technol. 104, 81–88. doi: 10.1016/j.compscitech.2014.09.007
Liu, Z., Zhang, X., Mao, Y., Zhu, Y. Y., Yang, Z., Chan, C. T., et al. (2000). Locally resonant sonic materials. Science 289, 1734–1736. doi: 10.1016/S0921-4526(03)00487-3
Lu, M. H., Feng, L., and Chen, Y. F. (2009). Phononic crystals and acoustic metamaterials. Mater. Today 12, 34–42. doi: 10.1016/S1369-7021(09)70315-3
Meza, L. R., Das, S., and Greer, J. R. (2014). Strong, lightweight, and recoverable three-dimensional ceramic nanolattices. Science 345, 1322–1326. doi: 10.1126/science.1255908
Keywords: lattice materials, mechanical metamaterials, innovative composites, multiscale mechanics, structural health monitoring, hyperspectral imaging
Citation: Fraternali F, Daraio C and Rimoli J (2019) Editorial: Multiscale Lattices and Composite Materials: Optimal Design, Modeling and Characterization. Front. Mater. 6:199. doi: 10.3389/fmats.2019.00199
Received: 20 May 2019; Accepted: 05 August 2019;
Published: 20 August 2019.
Edited by:
Nicola Maria Pugno, University of Trento, ItalyReviewed by:
Marco Miniaci, Swiss Federal Laboratories for Materials Science and Technology, SwitzerlandCopyright © 2019 Fraternali, Daraio and Rimoli. This is an open-access article distributed under the terms of the Creative Commons Attribution License (CC BY). The use, distribution or reproduction in other forums is permitted, provided the original author(s) and the copyright owner(s) are credited and that the original publication in this journal is cited, in accordance with accepted academic practice. No use, distribution or reproduction is permitted which does not comply with these terms.
*Correspondence: Fernando Fraternali, Zi5mcmF0ZXJuYWxpQHVuaXNhLml0
Disclaimer: All claims expressed in this article are solely those of the authors and do not necessarily represent those of their affiliated organizations, or those of the publisher, the editors and the reviewers. Any product that may be evaluated in this article or claim that may be made by its manufacturer is not guaranteed or endorsed by the publisher.
Research integrity at Frontiers
Learn more about the work of our research integrity team to safeguard the quality of each article we publish.