- 1Key Laboratory of Fluid and Power Machinery, Ministry of Education, School of Materials Science and Engineering, Xihua University, Chengdu, China
- 2Materials Research and Education Center, Department of Mechanical Engineering, Auburn University, Auburn, AL, United States
- 3College of Mechanical and Electrical Engineering, Shaanxi University of Science & Technology, Xi'an, China
Tribological behaviors of Si3N4 ceramic sliding against titanium alloy at different normal loads under seawater lubricated conditions are investigated on a pin-on-disc tester. Generally, for Si3N4/titanium alloy pair, the friction coefficient increases from 0.43 to 0.67 with load increasing (from 10 to 30N). Correspondingly, the wear rate is in the consistent case. When Si3N4 slides against titanium alloy, the wear mechanism is dominated by mechanical wear even though under seawater lubrication. With load increasing, the shear force of solid shear (τs × Ar) and furrow drag (S × Pe)(S × Pe) aggravated, which should be responsible for the rising trend of friction coefficient and wear rate.
Introduction
It is well known that, the energy and environment crisis have been brought by the industrial development and increasing pollution. In this case, people have paid more and more attention to how to explore the ocean resources by utilizing the marine devices (Liu et al., 2013, 2015). Among these devices, some pumps, open drive system and some blades are all exposed to seawater during the service process, and subjected to corrosion, friction and wear. Especially, the tribological characteristics of the moving components have a significant influence on the smooth running and service life (Min et al., 2014; Wang et al., 2016). For example, seawater hydraulic drive is a key technology in ocean exploitation and widely applied in deep-sea submergence vehicle, underwater robot, submarine oil production system, and so on. This system requires high-performance frictional pair materials (Jia et al., 2004).
Recently, the marine mating components were generally fabricated from metal materials. For instance, titanium alloys, such as Ti6Al4V, possess and excellent corrosion resistance in seawater and are widely used in marine. But, self-mated metal pairs usually represented the severe adhesive wear, and the metal materials beared the electrochemical corrosion just because of their intrinsic (Wu et al., 2016; Ye et al., 2017). Compared with metals, the ceramic materials represented high hardness, high strength, and excellent corrosion resistance and outstanding tribological performance (Jianxin et al., 2006). So, more scientists focused on studying the tribocorrosion behavior of metals sliding against ceramics, which was considered to act as an inert antagonist in the tribocorrosion systems (Chen and Yan, 2012).
Among the ceramic materials, silicon nitride ceramics possess good overall performance (e.g., high hardness, high strength, low density, low thermal conductivity, low chemical activity, and high wear resistance), which promotes these applied as rolling bearing, machine tools, sliding bearing in water pumps. Until recently, some scholars have investigated the tribological properties of Si3N4-Ceramic and Si3N4-metal pairs in pure water environments, and the research results showed low friction and wear of silicon nitride against ceramic were obtained in water environment (Jahanmir and Fischer, 1988). The previous scholars found that, the formation of slica tribochemical film would be benefit to ultra-low friction and wear of self-mated silicon nitride ceramics (Tomizawa and Fischer, 1987). When silicon nitride ceramic slid against gray cast iron, low friction coefficient of 0.002 was obtained. And, the authors held that the research results was attributed to the tribochemical products and graphite (which was originated from gray cast iron; Gao et al., 1997). Also, other scholars further investigated the influence of sliding speed and surface roughness on the tribological properties of Si3N4/Si3N4 pairs in pure water, and found that the chemical wear ratio was related to sliding speed, but independent of roughness (Saito et al., 2001). Meanwhile, when Si3N4 slid against Al2O3, the wear mechanism was transferred from mechanical wear to tribochemical wear with the increase of sliding time (Balarini et al., 2016). As described above, for silicon nitride sliding pairs, lower friction coefficients and wear rated were obtained under water lubrication.
Now, scholars started to focus on the friction and wear of ceramic materials under marine condition. Liu studied on the tribological performance of silicon nitride sliding against 316 stainless steel, and the friction coefficient of 0.16 was obtained in seawater and friction coefficient of 0.48 was obtained in pure water (Liu et al., 2013). Meanwhile, when Cr/GLC film slid against Si3N4 ceramic, the low friction coefficient of 0.06 was obtained, which attributed to the tribochemical products (Wang et al., 2016). As described above, at present some scholars have paid more attention to the tribological Si3N4 ceramic in seawater, but the mating materials, the sliding condition and the research results were not coincident. The systematicness and consistency of current researches were not still enough.
In this paper, the silicon nitride ceramic materials have been prepared by the method of hot-pressed sintering, and the titanium alloy was selected as the mating materials. The tribological properties of Si3N4/Ti6Al4V were measured by a vertical tribotester under seawater lubrication condition. The influence mechanism of normal load on the friction and wear behaviors was further discussed. This study could provide a certain guidance to develop mating components with excellent friction and wear properties under ocean environment.
Experimental Details
Test Rig and Materials
Friction and wear tests were carried out on a vertical universal pin-on-disc device, where an upper pin slides a bottom disc in artificial seawater environment. The disc was fixed, and the pin specimen rotated at a certain velocities. The schematic diagram of the device is illustrated in Figure 1. A normal load was applied on the stationary disc and the friction force was continuously measured using a strain gauge.
Si3N4 powder, Al2O3 powder, and Y2O3 powder were used to fabricate the ceramic composites. Si3N4 powder (with the particle size of 0.5 μm and the purity of 90% α- Si3N4) was utilized as the baseline material. Al2O3 powder (with the particle size of 1–2 μm and the purity of 99.9%) and Y2O3 powder (with the particle size of 1 μm and the purity of 99.9%) were utilized as sintering additives. Meanwhile, the volume fractions of Al2O3 and Y2O3 as sintering additives were 6 and 4%. The combined powders were mixed and ball-milled in alcohol for 24 h. The specimens of silicon nitride ceramics were sintered by hot-pressing in N2 at a temperature of 1,800oC and with a hot-pressure of 30MPa in a graphite die. Figure 2 shows the microstructure of Si3N4 ceramic, composed of elongated β-Si3N4. The density of Si3N4 ceramic was 3.31 g/cm3, the Vickers hardness was 19.9 GPa, and the fracture toughness was 8.01 MPa·m1/2.
The dimensions of ceramic pin specimens were 5 × 5 ×10 mm. The pin specimen surfaces are ground to a surface roughness of <0.5 μm. The dimensions of titanium alloy discs were a diameter of 44 mm and a thickness of 6 mm. The titanium alloy disc was made from Ti6Al4V alloy. The disc specimen surfaces were ground to a surface roughness of <0.8 μm. The density of disc specimen is 4.52 g/cm3, and the hardness was HRC25.
Procedure
The tests were conducted in artificial seawater at room temperature with normal loads of 10, 20, and 30 N and a sliding speed of 1,000 r/min (namely, 1.73 m/s). The seawater was prepared according to ASTM D1141-98, and the chemical composition of seawater was shown in Table 1.
The sliding distance was set to be 1,000 m. The friction coefficient was recorded automatically at the steady-state sliding. Volume wear rate of specimens were determined by using equation: Vm = Δm/ρNS, where Δm was the weight differences before and after sliding were measured by a microbalance with a high precision (0.1 mg), ρ was the density of specimens, N was the normal load and S was the sliding distance. Three samples were run to obtain average friction coefficient and wear rate under the test condition.
Results and Discussion
Tribological Behaviors of Silicon Nitride/Titanium Alloy Sliding Pairs
Figure 3 shows the friction coefficients and wear rates of Si3N4/titanium alloy sliding pairs at different loads. From Figure 3A, it can be seen that, with the increase of load, the friction coefficient increased from 0.43 for 10 N to 0.67 for 30 N. Similarly, it can be found from Figure 3B that the wear rate of Si3N4 pin also increased with the increase of load, and the wear rate are all at the magnitude of 10−6 mm3/Nm. Compared with the wear rates of pin, the wear rates of titanium alloy are higher and all at the magnitude of 10−5 mm3/Nm. Obviously, the increase of load deteriorated to both of the friction and wear properties of Si3N4/titanium alloy in seawater.
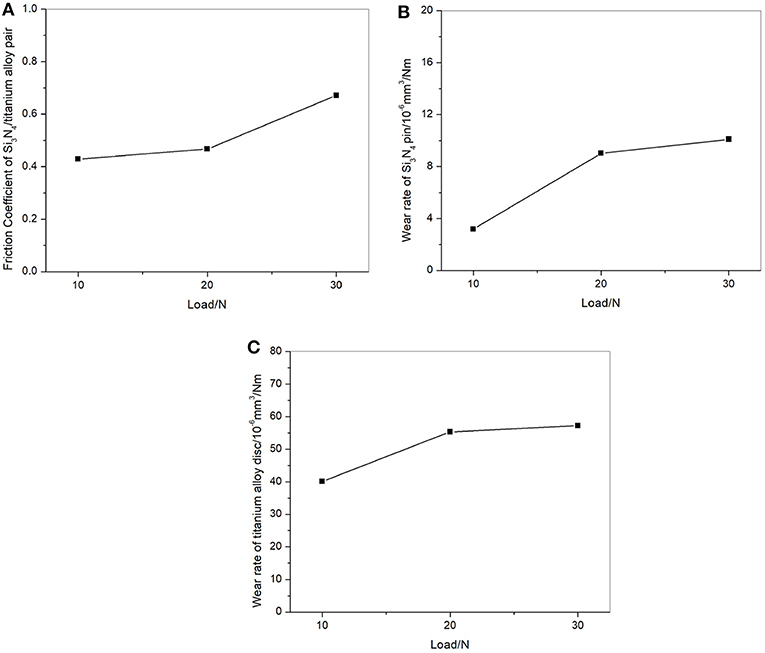
Figure 3. Titanium alloy in sliding contact against Si3N4 in seawater, (A) Friction coefficient, (B) wear rate of pin specimen, (C) wear rate of disc specimen.
Figure 4 shows the worn surfaces of titanium alloy disc sliding against Si3N4 pin at the different loads. From the figures, it can be seen that, at a low load of 10 N, wear surface was relatively smooth and contained a few micro grooves filled with a little spalling particles. When the load reached to 20 N, plastic deformation and more significant furrow was discovered from the worn surface of titanium alloy. And, at the load of 30 N, the worn surface of titanium alloy presented the severe plastic deformation and furrow with greater depth and width. While, it is interesting that no significant tribochemical film could be observed. Maybe, under this test condition, the tribochemical products were difficult to form a continuous surface film. XPS results of titanium alloy against Si3N4 pin at a load of 10 N were shown in Figure 5. The XPS results confirm the formation of tribochemical products of SiO2 and TiO2. So, it can be concluded that some tribochemical products formed during the friction process, but a continuous and significant tribofilm did not form on the wear surfaces.
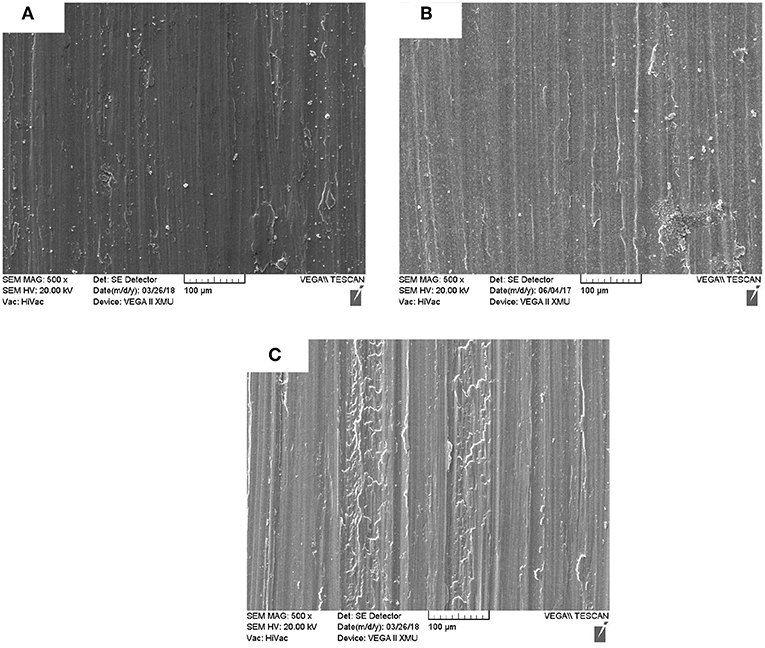
Figure 4. SEM images of titanium alloy disc against Si3N4 pins at the loads of (A) 10N, (B) 20N, and (C) 30N in seawater.
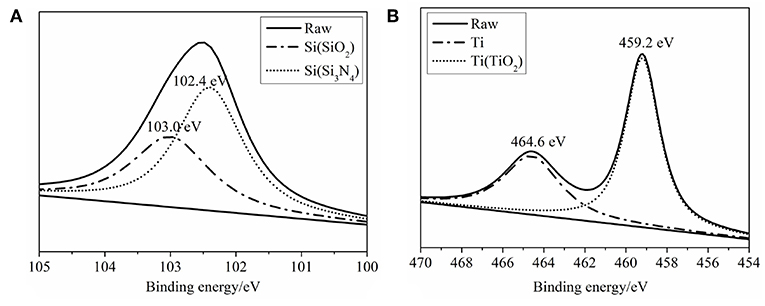
Figure 5. XPS results of the worn surface of the titanium alloy disc against the silicon nitride pin at a load of 10 N: (A) Si2p and (B) Ti2p.
Figure 6 shows the worn surfaces of corresponding Si3N4 pin. As shown in Figure 6, metal transferred film and weaken crack can be observed on the worn surfaces of Si3N4 pin against titanium alloy disc at the load of 10 N (see Figure 6A); with the increase of load, besides transferred film, plastic deformation and furrows gradually are observed in Figures 6B,C. Figure 7 shows EDS results of the transferred layer on the worn surface of Si3N4 pin against titanium alloy disc at a load of 10 N. From this figure, it can be seen that the transferred layer area is mainly composed of Ti, V, Al, Si and O and so on. The results indeed confirm the formation of transferred layer.
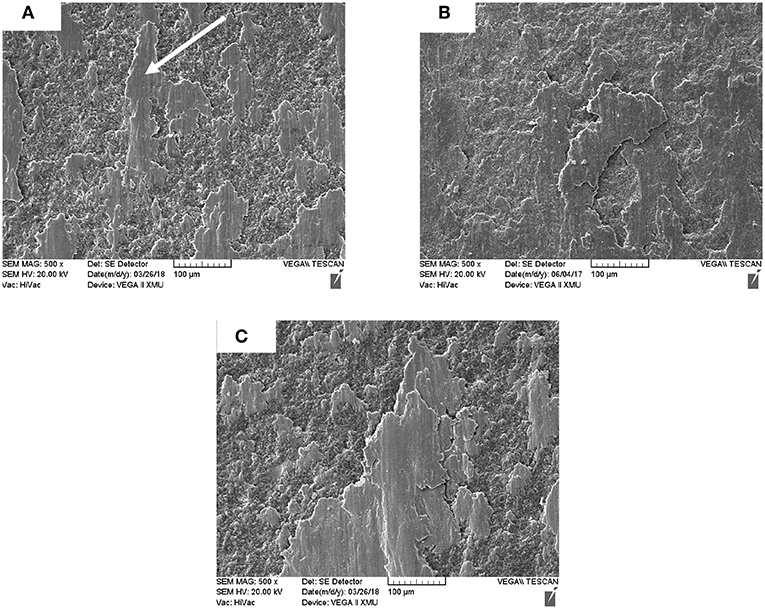
Figure 6. SEM images of Si3N4 pins against titanium alloy disc at the loads of (A) 10N, (B) 20N, and (C) 30N in seawater.
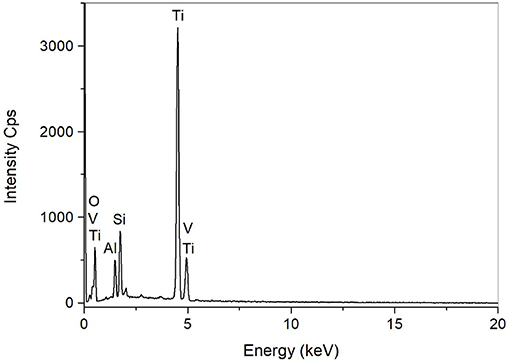
Figure 7. EDS results of transferred layer on the Si3N4 pin against titanium alloy disc at a load of 10N.
It was well known that, during friction process of ceramic/metal sliding pairs, the hard micro-bulges would plow the metal surface, and so that then some metal transferred layer would form on the ceramic surface (Hua et al., 2008; Chen et al., 2010, 2019). The metal transferred layer repeatedly formed and peeled off, which contributed to the wear of ceramic and metal. In this study, it can be clearly seen that obvious transferred layer formed on the silicon nitride ceramic surface (as shown in Figure 6). Simultaneously, even though a continuous tribofilm cannot be obviously observed, the results indicated that some tribochemical products formed on the wear surfaces (as shown in Figure 5). So, the wear surface morphology can be schematically shown in Figure 8. From the figure, it can be seen that the ceramic pin surface morphology was composed of transferred layer, ceramic surface, and some tribochemical products.
In our study, under seawater lubrication, the adsorbed water film, tribochemical products, and transferred layer would inhibit the direct contact of surface micro-bulges at a certain degree. Meanwhile, the direct contact of some micro-bulges would result in adhesion, abrasive wear and wear debris. From Figures 4, 6, it can be observed that, for Si3N4/titanium alloy pair sliding in seawater, at a lower load, metal transferred film on the ceramic pin and smoother metal disc surface could be observed (see Figures 4A, 6A). At a higher load, more significant transferred film on the ceramic pin and rough metal disc surface appear (see Figures 4C, 6C). The contact mode can be shown in Figure 9. Obviously, combined with the friction and wear results, the direct contact of surface micro-bulges would aggravate with the increase of load, and the source of friction force would alter.
According to classical adhesion theory (Bhushan, 1996, 2006), the average friction force(F)at the interface between ceramic and metal can be originated from Fs is the shear force at the direct contact solid surface, Fp is the furrow drag, and FlFl is the shear force at the liquid surface. Meanwhile, Fs can be calculated according to the equationτs. Where, Ar is the sum of real solid contact area for load, and τs is critical shear stress at the direct contact interface between two bodies. Similarly, the shear force at the liquid surface can be calculated as Fl = Al × τl. Meanwhile, the furrow drag can be calculated as Fp = S × Pe. Where, S is furrow area, and Pe is furrow drag per unit area.
In this study, even some tribochemical products formed on the wear surface, but the tribochemical products might not efficiently protect and lubricate the wear surfaces. In such a setting, with the lubrication of seawater, the friction force should be calculated as follows:
Combined with the friction and wear behaviors, it can be concluded that, the shear stress of solid and furrow drag should play a leading role. So, the equation can be transformed to F ≈ Ar × τs + S × Pe.
Some predecessors have indicated the existence of water or surface film had significant influence to the adhesion theory (Skopp et al., 1995; Deng and Cao, 2007). But, this lubrication effect was not observed in this study. In this case, if the surface contact state is elastoplastic contact, the friction coefficients of the pairs can be expressed as:
According to this equation and experimental phenomenon, with the increase of load, the direct contact area between the micro-bulges of ceramic and metal surface aggravated, and the adhesive wear and furrow drag became more serious. Even under the lubrication and cooling of seawater, the friction coefficients and wear rates increased with the increase of load.
Conclusions
1. The normal load influences the tribological behaviors of Si3N4 sliding pairs under seawater considerably. The friction coefficient of Si3N4/titanium alloy pairs increases with the increase of normal load at a range from 0.43 to 0.67.
2. For Si3N4/titanium alloy pairs, with the increase of load, the shear stress between direct solid contact and furrow drag aggravated. Even under the lubrication and cooling of seawater, the friction coefficients, and wear rates increased with the increase of load.
3. The tribochemical products did not effectively protect and lubricated the wear surfaces. The wear mechanism of Si3N4 slides against titanium alloy is dominated by mechanical wear even though under seawater lubrication.
Data Availability
The raw data supporting the conclusions of this manuscript will be made available by the authors, without undue reservation, to any qualified researcher.
Author Contributions
JZ and SM: conceptualization. WC and MZ: methodology. WC: formal analysis. JZ and SM: investigation. HL: resources. ZW: data curation. JZ and WC: writing–original draft preparation. JZ and SM: writing–review, editing, and supervision. SM and WC: project funding acquisition.
Conflict of Interest Statement
The authors declare that the research was conducted in the absence of any commercial or financial relationships that could be construed as a potential conflict of interest.
Acknowledgments
The authors are thankful for the funding provided by Natural Science Foundation of Shaanxi Province, China (grant number No. 2018JM5056) and Sichuan Science and Technology Program (Nos. 2019JDTD0024 and 2019ZHCG0048), Military and civilian integration project of Sichuan province (No. zyf-2018-089), Yibin Science and Technology Program (Nos. 2018YG05 and 2017YG02), Chunhui Project from Education Ministry of China (No. Z2017066), and Scientific Research Fund of Sichuan Education Department, China (No. 18ZA0445). Xihua Scholars program of Xihua University.
References
Balarini, R., Strey, N. F., Sinatora, A., and Scandian, C. (2016). The influence of initial roughness and circular axial run-out on friction and wear behavior of Si3N4–Al2O3 sliding in water. Tribol. Int. 101, 226–233. doi: 10.1016/j.triboint.2016.04.005
Bhushan, B. (1996). Contact mechanics of rough surface in tribology. Appl. Mech. Rev. 49, 275–298. doi: 10.1115/1.3101928
Chen, J., and Yan, F. (2012). Tribocorrosion behaviors of Ti-6Al-4V and Monel K500 alloys sliding against 316 stainless steel in artificial seawater. Trans. Nonferrous Metals Soc. China 22, 1356–1365. doi: 10.1016/S1003-6326(11)61326-5
Chen, W., Gao, Y., Chen, C., and Xing, J. (2010). Tribological characteristics of Si3N4–hBN ceramic materials sliding against stainless steel without lubrication. Wear 269, 241–248. doi: 10.1016/j.wear.2010.04.003
Chen, W., Wang, K., Liu, X., He, N., Xin, H., and Hao, W. (2019). Investigation of the friction and wear characteristics of Si3N4-hBN ceramic composites under marine atmospheric environment. Int. J. Refract. Met. Hard Mat. 81, 345–357. doi: 10.1016/j.ijrmhm.2019.03.014
Deng, J. X., and Cao, T. K. (2007). Self-lubricating mechanisms via the in situ formed tribofilm of sintered ceramics with CaF2 additions when sliding against hardened steel. Int. J. Refract. Met. Hard Mater. 25, 189–197. doi: 10.1016/j.ijrmhm.2006.04.010
Gao, Y. M., Fang, L., Su, J. Y., and Xie, Z. G. (1997). Investigation on the components and the formation of a tribological film in the Si3N4-gray sliding pair lubricated with distilled water. Wear 206, 87–93. doi: 10.1016/S0043-1648(96)07358-9
Hua, M., Wei, X. C., and Li, J. (2008). Friction and wear behavior of SUS 304 austenitic stainless steel against Al2O3 ceramic ball under relative high load. Wear 265, 799–810. doi: 10.1016/j.wear.2008.01.017
Jahanmir, S., and Fischer, T. E. (1988). Friction and wear of silicon nitride lubricated by humid air, water, hexadecane and hexadecane C 0.5 percent stearic acid. STLE Trans. 31, 32–43. doi: 10.1080/10402008808981795
Jia, J., Chen, J., Zhou, H., Wang, J., and Zhou, H. (2004). Friction and wear properties of bronze-graphite composite under water lubrication[J]. Tribol. Int. 37, 423–429. doi: 10.1016/j.triboint.2003.12.013
Jianxin, D., Tongkun, C., Zeliang, D., Jianhua, L., Junlong, S., and Jinlong, Z. (2006). Tribological behaviors of hot-pressed Al2O3/TiC ceramic composites with the additions of CaF2 solid lubricants. J. Eur. Ceram. Soc. 26, 1317–1323. doi: 10.1016/j.jeurceramsoc.2005.02.010
Liu, N., Wang, J., Chen, B., and Yan, F. (2013). Tribochemical aspects of silicon nitride ceramic sliding against stainless steel under the lubrication of seawater. Tribol. Int. 61, 205–213. doi: 10.1016/j.triboint.2013.01.011
Liu, Y., Xufeng, Z., Defa, W., Donglin, L., and Xiaohui, L. (2015). Study on the control methods of a water hydraulic variable ballast system for submersible vehicles. Ocean Eng. 108, 648–661. doi: 10.1016/j.oceaneng.2015.08.045
Min, C., Nie, P., Song, H.-J., Zhang, Z., and Zhao, K. (2014). Study of tribological properties of polyimide/graphene oxide nanocomposite films under seawater-lubricated condition. Tribol. Int. 80, 131–140. doi: 10.1016/j.triboint.2014.06.022
Saito, T., Hosoe, T., and Honda, F. (2001). Chemical wear of sintered Si3N4, hBN and Si3N4-hBN composites by water lubrication. Wear 247, 223–230. doi: 10.1016/S0043-1648(00)00539-1
Skopp, A., Woydt, M., and Habig, K. H. (1995). Tribological behavior of silicon nitride materials under unlubricated sliding between 22 °C and 1000 °C. Wear 181–183, 571–580. doi: 10.1016/0043-1648(95)90173-6
Tomizawa, H., and Fischer, T. E. (1987). Friction and wear of silicon nitride and silicon carbide in water: hydrodynamic lubrication at low sliding speed obtained by tribochemical wear. ASLE Trans. 30, 41–46. doi: 10.1080/05698198708981728
Wang, C., Ye, Y., Guan, X., Hu, J., Wang, Y., and Li, J. (2016). An analysis of tribological performance on Cr/GLC film coupling with Si3N4, SiC, WC, Al2O3 and ZrO2 in seawater. Tribol. Int. 96, 77–86. doi: 10.1016/j.triboint.2015.12.010
Wu, D., Liu, Y., Li, D., Xufeng, Z., and Ren, X. (2016). The applicability of WC-10Co-4Cr/Si3N4 tribopair to the different natural waters. Int. J. Refract. Metals Hard Mater. 54, 19–26. doi: 10.1016/j.ijrmhm.2015.06.016
Keywords: friction, wear, seawater, Si3N4, titanium alloy
Citation: Zhang J, Wang Z, Chen W, Liao H, Zeng M and Ma S (2019) Wear in Silicon Nitride Sliding Against Titanium Alloy Pairs at Different Loads Under Artificial Seawater Lubrication. Front. Mater. 6:155. doi: 10.3389/fmats.2019.00155
Received: 28 March 2019; Accepted: 18 June 2019;
Published: 04 July 2019.
Edited by:
Rajesh Adhikari, Institut National de la Recherche Scientifique (INRS), CanadaReviewed by:
Dae-Eun Kim, Yonsei University, South KoreaGuangneng Dong, Xi'an Jiaotong University, China
Copyright © 2019 Zhang, Wang, Chen, Liao, Zeng and Ma. This is an open-access article distributed under the terms of the Creative Commons Attribution License (CC BY). The use, distribution or reproduction in other forums is permitted, provided the original author(s) and the copyright owner(s) are credited and that the original publication in this journal is cited, in accordance with accepted academic practice. No use, distribution or reproduction is permitted which does not comply with these terms.
*Correspondence: Jianjun Zhang, empqeGp0dUAxNjMuY29t; Sude Ma, bWFzdWRlMjAwN0AxNjMuY29t