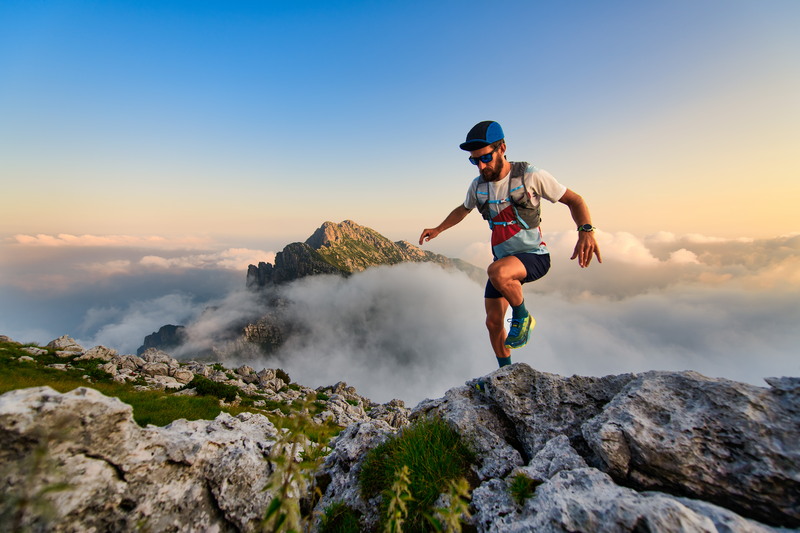
94% of researchers rate our articles as excellent or good
Learn more about the work of our research integrity team to safeguard the quality of each article we publish.
Find out more
MINI REVIEW article
Front. Mater. , 12 April 2019
Sec. Semiconducting Materials and Devices
Volume 6 - 2019 | https://doi.org/10.3389/fmats.2019.00062
This article is part of the Research Topic Frontiers in Materials: Rising Stars View all 56 articles
The article summarizes the scientific progress that has occurred in the past several years in regard to the preparation of carbon nanofibers from lignin as a low-cost environmentally-friendly raw material using electrospinning. It presents an overview of using lignin, electrospinning, and carbonization to convert lignin to carbon nanofibers. Lignin is a renewable source for carbon material, and it is very abundant in nature. It is mostly produced as a byproduct from the paper industry and biomass fractionation. Despite its extensive availability and beneficial properties, only a few studies have reported on its use in electronic applications. Lignin-based carbon nanofibers have a high surface area, high porosity, and good electrical conductivity; thus, it is proposed that they are suitable for future energy storage applications.
Electrospun carbon nanofibers (ECNFs) are part of a technological revolution due to their operational simplicity and extraordinary properties, such as being lightweight, having a high surface area, and exhibiting good thermal and electrical conductivity (Lallave et al., 2007). ECNFs have a wide range of applications in areas such as energy conversion and storage (Peng et al., 2016), sensing and diagnostics (Huang et al., 2010), aerospace (Wu et al., 2013), and micro/nano electromechanical systems (Arshad et al., 2011). However, the widespread use of ECNFs is limited due to the high cost of the precursor material and the low yield. Currently, polyacrylonitrile (PAN), produced from depleting petroleum resources, is the prevalent precursor material used to produce ECNFs (Inagaki et al., 2012). The solvents required to convert electrospun nanofibers from the PAN precursor polymer, i.e., dimethylformamide (DMF), are toxic. Therefore, it is essential to develop an alternative, greener precursor material based on renewable plant-based materials.
Lignin, a natural polymer present in lignocellulosic plants, is one of the best substitute materials for producing carbon nanofibers (Baker and Rials, 2013). According to a recent research report, the lignin market is growing at a compound annual growth rate (CAGR) of 2.2%, and it is estimated to generate revenues of 913.1 million USD by 2025 (Grand View Research Inc., 2017). Using the electrospinning method, dissolved lignin suspensions can be processed into submicron and nanoscale fibers. After Lallave et al. (2007) reported the use of electrospinning for fabricating lignin-based carbon fibers, the number of studies related to converting lignin into carbon nanofibers has steadily grown. The recent progress in lignin-based carbon nanofibers has substantially increased the intention of using them for technical applications, such as energy storage (dye-sensitized solar cells [DSCC], batteries, capacitors, and supercapacitors) (Fang et al., 2017). An ISI Web of Science literature search showed that, currently, only 61 research papers have been published on lignin, electrospinning, and carbon fibers. Researchers in Republic of China, the United States, and Canada have been most active in this field.
This literature review focuses on the preparation of lignin-based carbon nanofibers using electrospinning for electronic applications. The lignin-based carbon nanofibers have unique properties that could be used for developing value-added applications, such as a low-cost, “green” carbon material for energy storage.
Lignin is a natural biopolymer that mainly consists of three common monomeric units: coniferyl alcohol, p-coumaryl alcohol, and sinapyl alcohol. Lignin provides structure and strength, and it has antioxidative and antimicrobial properties; it also stores energy in a plant (Boerjan et al., 2003). Lignin is very promising as a low-cost carbon precursor material (Rosas et al., 2014); it is a renewable resource and it has a carbon-rich phenolic chemical structure (Boudet et al., 2003). While lignin is produced in large quantities as a byproduct in the paper industry and in biomass fractionation (Kadla et al., 2002), it has few applications other than energy recovery. All lignocellulosic plants contain lignin, making it one of the most common biopolymers on earth. Typically, lignin is separated from wood, which contains ~30% lignin. The Kraft and Organosolv processes are the most common delignification methods for lignin isolation (Shi et al., 2018). The Kraft process uses sodium hydroxide and sodium sulfide to extract lignin; the Organosolv process uses organic solvents, such as methanol, ethanol, and acetic acid, or their aqueous solutions, for extraction. Additionally, large amounts of lignin are generated in bioethanol production (Matsushita et al., 2009).
A suitable spinning solution is essential for the electrospinning of nanofibers. The most important properties of the spinning solution that affect the quality of the electrospun fibers are its electrical conductivity, surface tension, and viscosity (Ramakrishna, 2005). Lower or higher viscosity than is required results in the formation of beads or no fibers at all. In the first publication on the electrospinning of lignin, Lallave et al. (2007) used a lignin:ethanol solution at a w/w ratio of 1:1 with a viscosity range between 350 and 400 cPs to fabricate lignin fibers without any additional polymer. The addition of phosphoric acid, H3PO4, into a similar lignin:ethanol solution (H3PO4:lignin:ethanol–weight ratio: 0.3:1:1) resulted in more curly fibers with a diameter ≤1 μm (García-Mateos et al., 2018). García-Mateos et al. (2018) suggested that H3PO4 is the reason for the curly fibers because of the increased viscosity of 450 cPs and the increased electrical conductivity of the spinning solution. Polymers are more commonly used as processing aids to achieve the necessary chain entanglement for electrospinning of nanofibers. In order to produce “green” nanofibers, water soluble polymers, such as polyethylene oxide (PEO) and polyvinyl alcohol (PVA), are preferred for the preparation of the lignin-based carbon nanofibers (Poursorkhabi et al., 2015). In addition to water soluble polymers, lignin-PAN solutions with DMF as a solvent have been used in electrospinning (Seo et al., 2011). Seo et al. (2011) observed that increasing the lignin content from 50 to 80 wt% decreased the viscosity and conductivity of the solution, leading to beads and thicker fibers in electrospinning.
Electrospinning is a simple, productive technique used to fabricate highly functional micro- and nanometer scale (0.01–10 μm) fibers. These fibers have significant advantages: they are extremely lightweight, their fabrication cost is low, and they have a large aspect ratio, reduced defects (small diameter), high molecular orientation, and high flexibility in surface functionality. When a high-voltage electric field is applied to a polymer solution, fibers are initiated at the tip of a “Taylor cone.” In the beginning, the fiber path is almost straight (a stable region). After a specific distance, the fiber path becomes complex (a bending instability region) (Yarin et al., 2001). A significant decrease in the fiber diameter occurs in the instability region (Reneker and Yarin, 2008). The reasons for this bending instability are explained by Earnshaw's theorem. Figure 1A shows the basic principle of the electrospinning process, and Figures 1B–D shows the electrospun lignin/PVA nanofiber mat at different post-processing stages.
Figure 1. Preparation of lignin-based electrospun carbon nanofibers (ECNFs), their structure and electrochemical properties. (A) Schematic of electrospinning of the lignin/PVA suspension (75/25) and electrospun lignin/PVA nanofibers before post-processing, after stabilization, and after carbonization; (B–D) methods which are used to reach very high specific surface area on the carbon fibers: (B) KOH treatment prior the carbonization process resulting in a mesoporous carbon nanofiber by Ago et al. (2016) reproduced under the terms of the Creative Commons Attribution (CC BY 3.0) license, (C) magnesium nitrate treated ECNFs resulting in carbon nanofibers with improved porosity, surface area and electrochemical performance by Ma et al. (2018) with permission from Elsevier, (D) nickel cobaltite (NiCo2O4) decorated ECNFs which resulted in high specific surface area and high specific capacitance by Lei et al. (2017) with permission from Elsevier; (E–G) electrochemical characterization of lignin-based ECNFs as electrode material using three-electrode cell configuration in 0.5 M Na2SO4 electrolyte by Ago et al. (2016) reproduced under the terms of the Creative Commons Attribution (CC BY 3.0) license: (E) cyclic voltammograms at varying scan rates; (F) galvanostatic charge/discharge curve at varying current densities, (G) cycling stability of ECNFs and powder at 10 mV s−1.
Adjusting the electrospinning processing parameters, such as the voltage, feed rate, needle type, and the tip-to-collector distance, affects the properties of electrospun lignin nanofibers. Using a co-axial and tri-axial spinneret, solid, and hollow nanofibers from the lignin:ethanol solution were prepared using a tip-to-collector distance of 20–25 cm, a potential difference of 12 kV, and variable feed rates (Lallave et al., 2007). Similar processing conditions (12 kV potential difference, 20–25 cm tip-to-collector distance, and feed rates of 0.06 and 0.8 mL/h) were used to prepare nanofibers from a platinum (Pt)-doped lignin:ethanol solution (Ruiz-Rosas et al., 2010). Dallmeyer et al. (2010) found that the addition of PEO could result in the transition from the electrospray of lignin to the formation of uniform fibers. They used the operating tip-to-collector distance of 14–20 cm, a potential difference of 9–14 kV, and a feed rate of 0.03 mL/min.
Stabilization is an intermediate step in the conversion of lignin-based ECNFs. In this step, the electrospun fibrous mat undergoes cyclization, oxidation, and dehydrogenation. Consequently, the intermolecular atomic bonding pattern is rearranged and the lignin transforms from a thermoplastic into a thermoset-type material at temperature range of about 200–300°C (Dallmeyer et al., 2014). Moreover, the volatile byproduct, is removed. A lower heating ramp of 0.05–5°C min−1 is preferred in the stabilization condition to achieve complete oxidation of the fibrous mat (Huang, 2009). If the stabilization condition is not properly maintained, the fibers could melt during the carbonization procedure (Seo et al., 2011). For safe handling, slow heating and a long duration are recommended during the stabilization procedure. As an outcome of the stabilization procedure, the size of the fibrous mat shrinks and the color slightly darkens. For example, Lallave et al. (2007) stabilized the fiber mat in air at 0.25°C min−1 from room temperature to 200°C for 24 h. Lignin was oxidized and the fiber weight was reduced (81 wt%) due to the release of water. No fusion of the fibers was obtained after stabilization, and the fiber size (diameter) in the resulting product was similar to the size of the original mat. You et al. (2015) shortened the stabilization time from 38 to 3 h using hexamethylenetetramine. According to Yen and Chang (2016), stabilization is a crucial step because it prevents fiber fusion and rupture in the subsequent carbonization step. In contrast, Cho et al. (2018) reported that it is possible to obtain uniform lignin-based carbon nanofibers without the thermal stabilization step by adding small amounts of nanocrystalline cellulose.
Carbonization is the final step in the conversion of lignin-based ECNFs. Here, the carbon atoms are cross-linked at temperature ranging from 600 to 1,500°C in an inert atmosphere. The non-carbon elements evaporate as a mixture of different gases in the applied high temperature range. The remaining mat is nearly 100% pure ECNFs. As an outcome of the carbonization procedure, the size of the fibrous mat shrinks more and the color becomes black. Moreover, a decrease in the fiber diameter has been observed as the carbonization temperature increases (Ruiz-Rosas et al., 2010). A higher carbonization temperature has been found to result in a higher degree of structural ordering in carbon (Rodríguez-Mirasol et al., 1996), and lignin-based carbon fibers with higher electrical conductivity were obtained by increasing the carbonization temperature from 600 to 900°C (Aslanzadeh et al., 2017).
Lignin-based carbonized carbon fibers have been reported to have a high specific surface area, high porosity, high electrical conductivity, good mechanical properties, high oxidation resistance, and superior thermal stability. These unique properties of lignin-based ECNFs make them ideal resources for low-cost energy storage applications, especially as green electrode materials for supercapacitors. Supercapacitors are considered to be very promising devices for energy storage due to their high power density, long cycling stability/durability, short charging times, and environmental friendliness (Ma et al., 2018). Table 1 summarizes recent studies on the use of lignin-based ECNFs in energy storage applications showing the material combination used for the electrospinning, the carbonization temperatures, the surface activating agents that were used, the surface area measured by the Brunauer-Emmett-Teller (BET) method, the electrolyte used, and the specific capacitance for energy storage applications.
Lai et al. (2014b) reported on the properties of ECNFs from a lignin–PVA nanofiber mat followed by stabilization and carbonization to be used in supercapacitors. The carbonized mat was found to be highly effective as binder-free electrodes. The gravimetric capacitance of 64 Fg−1 was achieved at a current density of 400 mAg−1 and 50 Fg−1 at 2,000 mAg−1. The membrane showed a capacitance retention of 10% after 6,000 cycles of charge/discharge. Ago et al. (2016) reported on the conversion of lignin-PVA fiber mats into a mesoporous carbon fiber mat for supercapacitor electrode. The fiber mat was stabilized at 250°C; it was then impregnated with potassium hydroxide (KOH), and then carbonized at 900°C. The resulting fiber mat exhibited a high surface area, up to 2005 m2g−1, and a large pore volume, 0.7 cm3g−1 with 70% mesoporosity, which greatly improved the material's electrochemical performance (Figures 1B,E,F). The specific capacitance of 205 Fg−1 was measured, and 83% of the capacity could be maintained after 1,500 cycles and Figure 1G).
Ma et al. (2016) applied manganese (IV) dioxide (MnO2) nanowhiskers for the decoration of carbonized ECNFs from the lignin–PVA mat, and then tested this material as an electrode material for supercapacitors. The small fiber diameters of 200 nm and the high surface area of 583 m2g−1 exhibited superior supercapacitor performance with a high gravimetric capacitance of 83.3 Fg−1, as well as an energy density of 84.3 WhKg−1 and a power density of 5.72 kWkg−1, making the material suitable for application in a high-performance supercapacitor. The improved supercapacitor performances were explained by the MnO2 surface coating, which provided high specific/gravimetric capacitance and a large reaction surface area, resulting in fast reaction kinetics. Same authors, Ma et al. (2018) used magnesium nitrate hexahydrate (Mg(NO3)·6H2O) as an additive in lignin-polyvinylpyrrolidone (PVP)-based carbon nanofibers resulting in a carbon nanofiber mat with a specific surface area of 1,140 m2g−1, increased mesoporosity (2–4 nm pore size) (shown in Figure 1C), and specific capacitance of 248 F/g−1 at a current density of 0.2 Ag−1. They also reported a good cycling stability of 97% capacitance retention after 1,000 cycles.
Deposition of silver (Ag) nanoparticles to lignin-PVA derived ECNFs was reported as a cost-effective and highly efficient electrocatalyst in alkaline fuel cells; the suitable activating agent can provide additional functionality as well as higher crystallinity due to the particle size growth (Lai et al., 2014a). That study observed the electrochemical activity of Ag/ECNFs electrocatalyst systems toward oxygen reduction reaction; they found that the mass activity of 15 wt% Ag/ECNFs system was 119 mAmg−1. You et al. (2015) reported the fabrication of lignin-based activated carbon fibers (ACFs), without using an additional polymer, followed by stabilization, carbonization, and steam activation for electric double layer capacitor application. The nitrous oxide (N2) adsorption and desorption measurement indicated that the ACFs had a high specific surface area of 2,185 m2g−1 and large pores (0.5–1.3 nm range). These favored the good electrical capacitance of 133.3 Fg−1 at a current density of 1 Ag−1. Wang et al. (2017) used iron oxide (Fe2O3 and Fe3O4) particles to decorate acetic acid lignin–PEO based carbon nanofibers, and then used the carbon nanofibers as an electrode material for a pseudocapacitor. The iron oxide-lignin based composite ECNF showed excellent electrochemical performance due to the reversible multi-electron redox faradaic reactions. The specific capacitance of 72.1 Fg−1 at a constant current density of 500 mAg−1 was achieved. Hu et al. (2014) used a KOH solution to activate lignin-PEO–based carbon fibers as the electrode material for a supercapacitor. The prepared ACFs showed a high microporosity (0.75 nm pore size) and high specific capacitance (344 Fg−1) at a low electrode mass of 1.8 mg and a scan rate of 10 mVs−1. ACFs also showed a low equivalent series resistance (ESR) of 1.71 Ω and outstanding cycling stability. Recently, Lei et al. (2017) decorated nickel cobaltite (NiCo2O4) on carbon nanofibers of lignin-PAN blend solution using the hydrothermal method, and then utilized the material as a flexible electrode for an asymmetric supercapacitor (Figure 1D). They obtained the following electrochemical properties: a specific capacitance of 1,757 Fg−1 at 2 mAcm−2 and an excellent cycling stability with ~138% capacitance retention after 5,000 cycles at 7 mAcm−2. Comparing these numbers with PAN-based carbon nanofibers in Table 1 the lignin based carbon fibers show promising electrochemical performance.
Zhao et al. (2018) prepared a flexible carbon nanofiber mat from a lignin-PVA solution and used it as a binder-free counter electrode for DSCC, instead of supercapacitors. The mat was carbonized at 1,500°C, and it was reported to have a relatively high specific surface area of 941 m2g−1; it also provided a maximum photoelectric conversion efficiency of up to 7.6% due to its high specific surface area and low charge transfer resistance, which is of the same magnitude as the conventional and expensive Pt material used for DSSC.
Developments in the manufacture and properties of lignin-based carbon nanofibers has significantly increased the intention of their use for technical applications, such as green electrode materials for energy storage applications. Green carbon nanofibers prepared using the electrospinning technique have been shown to have a high surface area, high porosity, high electrical conductivity, and superior graphite content. This brief literature review provides a step-by-step understanding of the lignin material, the preparation of the spinning solution, the electrospinning parameters, and the conversion process involved in the preparation of green carbon nanofibers. It also includes a concise summary of the recent electrochemical studies on lignin-based carbon nanofibers for energy storage applications. In the near future, a more detailed study about electrospinning of native lignin-based carbon nanofibers needed in order to implement for an exciting possibility as a “greener” electrode material.
All authors listed have made a substantial, direct and intellectual contribution to the work, and approved it for publication.
The authors declare that the research was conducted in the absence of any commercial or financial relationships that could be construed as a potential conflict of interest.
The authors gratefully acknowledge Business Finland for the financial support it provided through the Grelectronics research project. The Swedish partners thank Bio4Energy, a Swedish strategic research program, and the Swedish Research Council (VR) for their financial support.
Ago, M., Borghei, M., Haataja, J. S., and Rojas, O. J. (2016). Mesoporous carbon soft-templated from lignin nanofiber networks: microphase separation boosts supercapacitance in conductive electrodes. RSC Adv. 6, 85802–10. doi: 10.1039/C6RA17536H
Arshad, S. N., Naraghi, M., and Chasiotis, I. (2011). Strong carbon nanofibers from electrospun polyacrylonitrile. Carbon 49, 1710–19. doi: 10.1016/j.carbon.2010.12.056
Aslanzadeh, S., Ahvazi, B., Boluk, Y., and Ayranci, C. (2017). Carbon fiber production from electrospun sulfur free softwood lignin precursors. J. Eng. Fibers Fabrics 12, 33–43. doi: 10.1177/155892501701200405
Baker, D. A., and Rials, T. G. (2013). Recent advances in low-cost carbon fiber manufacture from lignin. J. Appl. Poly. Sci. 130, 713–28. doi: 10.1002/app.39273
Boerjan, W., Ralph, J., and Baucher, M. (2003). Lignin biosynthesis. Annu. Rev. Plant Biol. 54, 519–46. doi: 10.1146/annurev.arplant.54.031902.134938
Boudet, A. M., Kajita, S., Grima-pettenati, J., and Goffner, D. (2003). Lignins and lignocellulosics : a better control of synthesis for new and improved uses. Trends Plant Sci. 8, 576–81. doi: 10.1016/j.tplants.2003.10.001
Cho, M., Karaaslan, M., Chowdhury, S., Ko, F., and Renneckar, S. (2018). Skipping oxidative thermal stabilization for lignin-based carbon nanofibers. ACS Sustain. Chem. Eng. 6, 6434–44. doi: 10.1021/acssuschemeng.8b00209
Dallmeyer, I., Ko, F., and Kadla, J. F. (2010). Electrospinning of technical lignins for the production of fibrous networks. J. Wood Chem. Technol. 30, 315–29. doi: 10.1080/02773813.2010.527782
Dallmeyer, I., Lin, L. T., Li, Y., Ko, F., and Kadla, J. F. (2014). Preparation and characterization of interconnected, kraft lignin-based carbon fibrous materials by electrospinning. Macromol. Mater. Eng. 299, 540–51. doi: 10.1002/mame.201300148
Fang, W., Yang, S., Wang, X.-L., Yuan, T.-Q., and Sun, R.-C. (2017). Manufacture and application of lignin-based carbon fibers (LCFs) and lignin-based carbon nanofibers (LCNFs). Green Chem. 19, 1794–1827. doi: 10.1039/C6GC03206K
García-Mateos, F. J., Berenguer, R., Valero-Romero, M. J., Rodríguez-Mirasol, J., and Cordero, T. (2018). Phosphorus functionalization for the rapid preparation of highly nanoporous submicron-diameter carbon fibers by electrospinning of lignin solutions. J. Mater. Chem. A 6, 1219–33. doi: 10.1039/C7TA08788H
Grand View Research Inc. (2017). Lignin Market Analysis By Product (Ligno-Sulphonates, Kraft Lignin, Organosolv Lignin) By Application (Macromolecules, Aromatics), By Region (North America, Europe, Asia Pacific, Central & South America, MEA), And Segment Forecasts, 2018 - 2025. Available online at: https://www.grandviewresearch.com/press-release/global-lignin-market (accessed September 21, 2018).
Hu, S., Zhang, S., Pan, N., and Hsieh, Y.-L. (2014). High energy density supercapacitors from lignin derived submicron activated carbon fibers in aqueous electrolytes. J. Power Sources 270 , 106–12. doi: 10.1016/j.jpowsour.2014.07.063
Huang, J., Liu, Y., and You, T. (2010). Carbon nanofiber based electrochemical biosensors: a review. Anal. Methods 2, 202–11. doi: 10.1039/b9ay00312f
Huang, X. (2009). Fabrication and properties of carbon fibers. Materials 2, 2369–2403. doi: 10.3390/ma2042369
Inagaki, M., Yang, Y., and Kang, F. (2012). Carbon nanofibers prepared via electrospinning. Adv. Mater. 24, 2547–66. doi: 10.1002/adma.201104940
Kadla, J. F., Kubo, S., Venditti, R. A., Gilbert, R. D., Compere, A. L., and Griffith, W. (2002). Lignin-based carbon fibers for composite fiber applications. Carbon 40, 2913–20. doi: 10.1016/S0008-6223(02)00248-8
Kim, C., Ngoc, B. T. N., Yang, K. S., Kojima, M., Kim, Y. A., Kim, Y. J., et al. (2007). Self-sustained thin webs consisting of porous carbon nanofibers for supercapacitors via the electrospinning of polyacrylonitrile solutions containing zinc chloride. Adv. Mater. 19, 2341–46. doi: 10.1002/adma.200602184
Lai, C., Kolla, P., Zhao, Y., Fong, H., and Smirnova, A. L. (2014a). Lignin-derived electrospun carbon nanofiber mats with supercritically deposited ag nanoparticles for oxygen reduction reaction in alkaline fuel cells. Electrochim. Acta 130, 431–38. doi: 10.1016/j.electacta.2014.03.006
Lai, C., Zhou, Z., Zhang, L., Wang, X., Zhou, Q., Zhao, Y., et al. (2014b). Free-standing and mechanically flexible mats consisting of electrospun carbon nanofibers made from a natural product of alkali lignin as binder-free electrodes for high-performance supercapacitors. J. Power Sources 247, 134–41. doi: 10.1016/j.jpowsour.2013.08.082
Lai, C.-C., and Lo, C.-T. (2015). Preparation of nanostructural carbon nano fi bers and their electrochemical performance for supercapacitors. Electrochim. Acta 183, 85–93. doi: 10.1016/j.electacta.2015.02.143
Lallave, M., Bedia, J., Ruiz-Rosas, R., Rodríguez-Mirasol, J., Cordero, T., Otero, J. C., et al. (2007). Filled and hollow carbon nanofibers by coaxial electrospinning of alcell lignin without binder polymers. Adv. Mater. 19, 4292–96. doi: 10.1002/adma.200700963
Lei, D., Li, X.-D., Seo, M. K., Khil, M.-S., Kim, H.-Y., and Kim, B.-S. (2017). NiCo2O4 nanostructure-decorated PAN/lignin based carbon nanofiber electrodes with excellent cyclability for flexible hybrid supercapacitors. Polymer 132, 31–40. doi: 10.1016/j.polymer.2017.10.051
Ma, C., Li, Z., Li, J., Fan, Q., Wu, L., Shi, J., et al. (2018). Lignin-based hierarchical porous carbon nanofiber films with superior performance in supercapacitors. Appli. Surf. Sci. 456, 568–76. doi: 10.1016/j.apsusc.2018.06.189
Ma, X., Kolla, P., Zhao, Y., Smirnova, A. L., and Fong, H. (2016). Electrospun lignin-derived carbon nanofiber mats surface-decorated with MnO2 nanowhiskers as binder-free supercapacitor electrodes with high performance. J. Power Sources 325, 541–48. doi: 10.1016/j.jpowsour.2016.06.073
Matsushita, Y., Inomata, T., Hasegawa, T., and Fukushima, K. (2009). Solubilization and functionalization of sulfuric acid lignin generated during bioethanol production from woody biomass. Bioresource Technol. 100, 1024–26. doi: 10.1016/j.biortech.2008.07.026
Niu, H., Zhang, J., Xie, Z., Wang, X., and Lin, T. (2011). Preparation, structure and supercapacitance of bonded carbon nanofiber electrode materials. Carbon 49, 2380–88. doi: 10.1016/j.carbon.2011.02.005
Peng, S., Li, L., Lee, J. K. Y., Tian, L., Srinivasan, M., Adams, S., et al. (2016). Electrospun carbon nanofibers and their hybrid composites as advanced materials for energy conversion and storage. Nano Energy 22, 361–95. doi: 10.1016/j.nanoen.2016.02.001
Poursorkhabi, V., Mohanty, A. K., and Misra, M. (2015). Electrospinning of aqueous lignin/poly(Ethylene Oxide) complexes. J. Appli. Polym. Sci. 132:41260. doi: 10.1002/app.41260
Ramakrishna, S. (2005). An Introduction to Electrospinning and Nanofibers. World Scientific Publishing. 396. doi: 10.1142/5894
Reneker, D. H., and Yarin, A. L. (2008). Electrospinning jets and polymer nanofibers. Polymer 49, 2387–2425. doi: 10.1016/j.polymer.2008.02.002
Rodríguez-Mirasol, J., Cordero, T., and Rodríguez, J. J. (1996). High-temperature carbons from kraft lignin. Carbon 34, 43–52. doi: 10.1016/0008-6223(95)00133-6
Rosas, J. M., Berenguer, R., Valero-Romero, M. J., Rodriguez-Mirasol, J., and Cordero, T. (2014). Preparation of different carbon materials by thermochemical conversion of lignin. Front. Mater. 1:29. doi: 10.3389/fmats.2014.00029
Ruiz-Rosas, R., Bedia, J., Lallave, M., Loscertales, I. G., Barrero, A., Rodríguez-Mirasol, J., et al. (2010). The production of submicron diameter carbon fibers by the electrospinning of lignin. Carbon 48, 696–705. doi: 10.1016/j.carbon.2009.10.014
Seo, D. K., Jeun, J. P., Kim, H. B., and Kang, P. H. (2011). Preparation and characterization of the carbon nanofiber mat produced from electrospun PAN/lignin precursors by electron beam irradiation. Rev. Adv. Mater. Sci. 28, 31–34. Available online at: www-proxy.ipme.ru/e-journals/RAMS/no_12811/08_paper.pdf
Shi, X., Wang, X., Tang, B., Dai, Z., Chen, K., and Zhou, J. (2018). Impact of lignin extraction methods on microstructure and mechanical properties of lignin-based carbon fibers. J. Appl. Polym. Sci. 135. doi: 10.1002/app.45580
Wang, L., and Aorigele Sun, Y. (2017). Preparation of iron oxide particle-decorated lignin-based carbon nanofibers as electrode material for pseudocapacitor. J. Wood Chem. Technol. 37, 423–32. doi: 10.1080/02773813.2017.1310900
Wu, X.-F., Rahman, A., Zhou, Z., Pelot, D. D., Sinha-Ray, S., Chen, B., et al. (2013). Electrospinning core-shell nanofibers for interfacial toughening and self-healing of carbon-fiber/epoxy composites. J. Appl. Polym. Sci. 129, 1383–93. doi: 10.1002/app.38838
Yarin, A. L., Koombhongse, S., and Reneker, D. H. (2001). Bending instability in electrospinning of nanofibers bending instability in electrospinning of nanofibers. J. Appli. Phys. 89, 3018–26. doi: 10.1063/1.1333035
Yen, S.-H., and Chang, F.-C. (2016). Effects of fiber processing conditions on the yield, carbon content, and diameter of lignosulfonate-based carbon fibers. BioResources 11, 10158–72. doi: 10.15376/biores.11.4.10158-10172
You, X., Koda, K., Yamada, T., and Uraki, Y. (2015). Preparation of electrode for electric double layer capacitor from electrospun lignin fibers. Holzforschung 69, 1097–1106. doi: 10.1515/hf-2014-0262
Keywords: lignin, electrospinning, carbonization, carbon nanofibers, energy storage
Citation: Kumar M, Hietala M and Oksman K (2019) Lignin-Based Electrospun Carbon Nanofibers. Front. Mater. 6:62. doi: 10.3389/fmats.2019.00062
Received: 18 January 2019; Accepted: 26 March 2019;
Published: 12 April 2019.
Edited by:
Zoltán Kónya, University of Szeged, HungaryReviewed by:
Sápi András, University of Szeged, HungaryCopyright © 2019 Kumar, Hietala and Oksman. This is an open-access article distributed under the terms of the Creative Commons Attribution License (CC BY). The use, distribution or reproduction in other forums is permitted, provided the original author(s) and the copyright owner(s) are credited and that the original publication in this journal is cited, in accordance with accepted academic practice. No use, distribution or reproduction is permitted which does not comply with these terms.
*Correspondence: Kristiina Oksman, a3Jpc3RpaW5hLm9rc21hbkBsdHUuc2U=
Disclaimer: All claims expressed in this article are solely those of the authors and do not necessarily represent those of their affiliated organizations, or those of the publisher, the editors and the reviewers. Any product that may be evaluated in this article or claim that may be made by its manufacturer is not guaranteed or endorsed by the publisher.
Research integrity at Frontiers
Learn more about the work of our research integrity team to safeguard the quality of each article we publish.