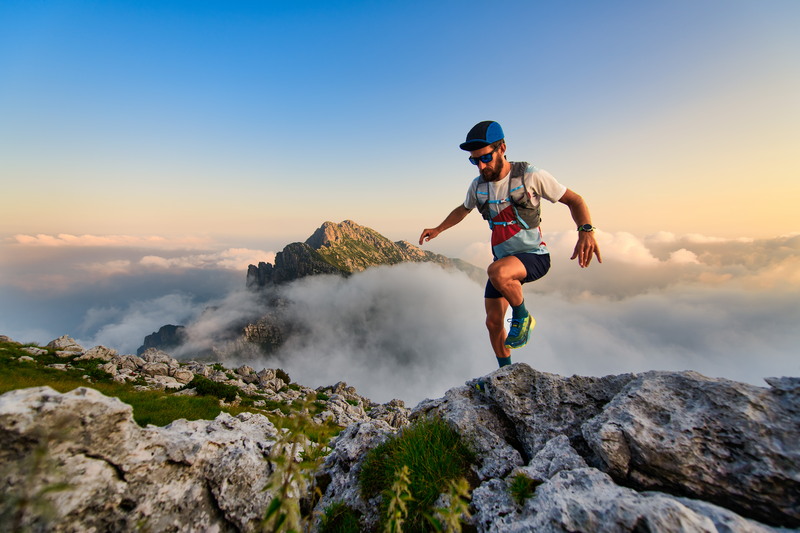
94% of researchers rate our articles as excellent or good
Learn more about the work of our research integrity team to safeguard the quality of each article we publish.
Find out more
ORIGINAL RESEARCH article
Front. Mater. , 24 March 2017
Sec. Ceramics and Glass
Volume 4 - 2017 | https://doi.org/10.3389/fmats.2017.00008
This article is part of the Research Topic Ultrastrong Glasses: Improving Mechanical Properties of Disordered Solids through Topo-Chemical Engineering View all 14 articles
Scratch-induced cracking is a serious problem for the use of glass products. At the scratch process, both median (vertical to the glass surface) and lateral (horizontal to the glass surface) cracks are formed. In this study, morphology of the scratch-induced cracks in a commercial soda-lime-silica glass was investigated by the scanning electron microscopy for the specimen broken across the scratch groove. Scratch test was carried out using a Knoop indenter in water and in dehydrated heptane. When scratch speed was 70 × 10−6 m s−1, length of both vertical and horizontal cracks was proportional to the normal load at scratching, and environmental dependence was not observed. When scratch speed was increased with the constant normal load of 200 g, length of both cracks was decreased. In the case of horizontal crack, no environmental effect was observed. On the other hand, length of the vertical crack scratched in water was much longer than that in heptane. At very high scratch speed as high as 1,000 × 10−6 m s−1, no vertical crack was formed in the heptane. These differences between horizontal and vertical cracks should be due to the differences of crack initiation position and the influence of subcritical crack growth to these cracks.
Scratch-induced crack formation in glass is important for grinding process in glass-related industry and for degradation of strength in practical use. However, study about it is few. After the pioneering works by Bulusara and Chandrasekar (1997) about soda-lime-silica glass together with sapphire and polycrystalline spinel and by Li et al. (1998) about soda-lime-silica glass, some important studies were carried out. Le Houérou et al. (2003) show the transition from ductile to brittle deformation with applied load up to the chipping region for soda-lime-silica glass and proposed a model about crack formation based on linear fracture mechanics. We are focusing the crack initiation load and studied its composition dependence for borosilicate, aluminosilicate, and some commercial glasses together with the environmental effect (Yoshida et al., 2001, 2004, 2005). In these studies, we found that the composition dependence of crack initiation load at scratching process [scratch resistance (SR)] is different from that at indentation process [crack resistance (CR)]. For example, CR of silica glass is about one order of magnitude higher than that of soda-lime-silica glass, but SR for these two glasses are in the same order. In addition, variation of the composition dependence of SR is much smaller than that of CR. Recently, in focusing the degradation behavior of cover glass in mobile electronic devices, scratch behavior of surface-strengthened glasses were reported (Gross, 2012; Schneider et al., 2012; Surdyka et al., 2014). High load scratch behavior as a model of grinding process was also reported recently (Gu and Yao, 2011; Bandyopadhyay et al., 2012).
However, most of the studies were focused only on the lateral crack parallel to the glass surface, and study about median crack normal to the glass surface is few. This is because of the fact that the formation of lateral cracks is easy to distinguish from the top surface, but the formation of median cracks is not. However, both of these cracks are important. In the case of scribing and bending process for cutting of glass sheet, deep median cracks are favored, but the existence of lateral cracks result in chipping and decrease of the edge strength. On the other hand, in the case of grinding process to make smooth surface, formation of lateral cracks are favored, but the formation of median cracks causes the decrease of surface strength. Therefore, studying the parameters controlling the formation of these two crack types is necessarily for improving the reliability of glass products.
In this study, morphology of cracks formed by scribing process was investigated by SEM observation of the cross section of scratched specimens. Effects of vertical load, scribing speed, and scribing environment are examined.
In this study, commercial soda-lime-silica glass made as slide glass for optical microscopy (Matsunami Glass Industry Ltd.) was scratched by Knoop indenter. A lab-made scratch tester reported previously (Yoshida et al., 2005) was used. Size of the sample was about 26 mm in length, 10 mm in width, and 1 mm in thickness. After introducing two slits at the both sides of the specimen, a crack was introduced at the opposite side to the scratch test surface by a diamond glass cutter to assist the bend break process. Shape of the specimen is schematically drawn in Figure 1. After that, scratch test was carried out in water or dehydrated heptane at room temperature with a Knoop indenter. Normal load at scratch test was 50, 100, 200, and 300 gf, and the scratch speed was 70, 200, 500, and 1,000 μm s−1. After the scratch test, arisen groove was covered with cyanoacrylate glue to prevent humidity and/or residual stress-induced slow crack growth (SCG) at the handling process described below. Then, the specimen was broken normal to the scratch groove by bending the specimen. The crack introduced before the scratch test was used as the origin of this bending fracture, and the scratched surface of the specimen suffered a compressive stress at the breaking process. Broken cross section of the specimen was coated with gold thin layer and served for SEM observation by using an S-3000N SEM (Hitachi High-Tech. Co. Ltd.). SEM observation was carried out within 3 h after the scratch test. All of the experiments were carried out 20 times for one condition.
Figure 2 shows an example of the cross section of scratch groove and cracks. There are two types of cracks under the groove. One is the median crack, which is almost normal to the glass surface, and the other is the lateral crack, which is almost parallel to the glass surface. In this study, as is shown in Figure 2, we define the length of median crack as vertical length of this crack, C, and that of lateral crack as the average length of the two horizontal cracks, C1.
Figures 3A,B show the general trend of the crack formation when scratched in water (Figure 3A) and in heptane (Figure 3B) as functions of applied normal load and scratching speed. In the case of low normal loads, medium crack is formed at low scratch speed, and lateral crack is formed at high scratch speed. There is a transition region where both of two cracks form. On the other hand, in the case of high normal loads, both median and lateral cracks are formed at low scratch speed, and lateral crack are formed at high scratch speed without forming median cracks.
Figure 3. General trend of the crack formation as functions of scratch speed and applied normal load when scratched (A) in water and (B) in heptane.
Figures 4A,B show the average crack length as a function of scratch speed when scratched at 200 gf, relatively high load, scratched in water (Figure 4A) and in heptane (Figure 4B). In both environments and in both types of cracks, crack length decreased with the scratch speed. As we mentioned above, median crack did not form in heptane at high scratch speed. When we focused on the environmental effect, it is clear that the length of median cracks observed in water was longer than that in heptane. On the other hand, length of the lateral cracks in water was nearly the same with that in heptane.
Figure 4. Crack length as a function of scratch speed when scratched with 200 gf applied normal load (A) in water and (B) in heptane.
Figures 5A,B show the average crack length as a function of normal load when scratch speed was very slow (70 μm s−1). In both environments and in both types of cracks, crack length increased with the applied normal load. The crack initiation load of median crack was lower than that of lateral crack, and the crack formation tendency was found to depend on the environment. When scratched in heptanes, both median and lateral cracks were formed together in many cases. On the other hand, when scratched in water, low normal load gave the median crack and high normal load gave the lateral crack. In contrast to the formation of cracks, when crack was once formed, its length did not depend strongly on the environment in the case of slow scratch speed.
Figure 5. Crack length as a function of applied normal load when scratched at 70 μm s−1 (A) in water and (B) in heptane.
When we focus on the effect of scratch speed, it is clear that the crack length decreased with the scratch speed. According to Bandyopadhyay et al., width of the scratch groove depends on the scratch speed when normal load is as high as 5 N (510 gf) but does not depend on the speed when normal load is 2 N (204 gf). As most of our present study was carried out less than 2 N, deformation at scratch process should be elastic deformation and plastic flow together with densification, and they should not contain the time-dependent deformation such as viscous flow. Therefore, maximum stress should not depend on the scratch speed, and thus the scratch speed dependence cannot be explained by the crack propagation at KIC. This means that we must pay attention for the SCG (Wiederhorn, 1967). SCG at regions I and II are the stress-assisted bond-breaking reaction of glass with water. That at region III is the intrinsic SCG free from water. Soda-lime glass is known to show both types of SCG. Scratch speed dependence of the crack length can be explained by the SCG as follows. Low scratch speed gives long loading duration, and so crack can grow up in this duration. On the other hand, high scratch speed gives short loading duration, and so enough time for crack growth cannot be achieved. Therefore, slower scratch speed gives longer crack length.
When we compare Figure 4A with Figure 4B, it is clear that the length of median crack scratched in water is longer than that in heptane, but the length of lateral crack in water is nearly the same with that in heptane when it is formed. This can be explained when we assume that origin of these two cracks positioned at different sites. The origin of cracking in median crack would be at the contact point of glass surface with indenter. Therefore, the origin would be surrounded by water or heptane, and so the stress corrosion will give the environmental effect. Scratching in water will give regions I and II SCG for median crack, which can occur even at relatively low stress field. In contrast with this, scratching in heptane can give only region III SCG, which is difficult to occur at low stress field. By the way, the origin of cracking in lateral crack would be at the interior of glass. Stress between plastically deformed region and elastic region will make the crack. Therefore, as the origin is not surrounded by water or heptane, only region III SCGC can occur and gives no environmental effects.
Increasing the normal load increases the crack length as shown in Figure 5. This should be due to the increase of stress field at crack tip with the applied normal load. In the case of scratching in water, median crack is diminished at high stress field, and only lateral crack is formed. Further study should be required to clarify this phenomenon. In addition, we must note that although the crack formation tendencies of median and lateral cracks are different to each other, if both of the cracks are formed at the same condition, length of the two cracks are similar to each other. This suggests that the stress field around the groove is almost concentric with the groove as the center.
In the practical use of scratch process in industry, application of high normal stress is not favored for precision machining because it forms both median and lateral cracks. For scribing and breaking process, low load and low scratch speed process is favored because it forms median crack free from lateral one. Therefore, chipping at the edge would be diminished in this condition. However, as the scribing tool used in industry is much sharper than Knoop indenter, more study should be required for actual application. On the other hand, in the case of grinding process, low load and high speed is favored because it forms lateral crack free from median one. This will improve the surface strength of the grinded glass because of the few existence of deep crack. In addition, grinding environment free from water is found to be effective to prevent the formation of median crack.
Morphology of the scratch-induced cracks in a commercial soda-lime-silica glass was investigated by the scanning electron microscopy for the specimen broken across the scratch groove formed by a Knoop indenter in water and in heptane. Increase of the scratch load increases the length of median and lateral cracks. Length of median crack in water is longer than that in heptanes, while that lateral crack does not show environmental effect. Increase of the scratch speed decreases the crack length.
JM planned the study, developed the experimental procedure, and made the discussion from the data. DG developed the experimental procedure, carried out the experiments, and made the discussion from the data. SY developed the experimental procedure and made the discussion from the data.
The authors declare that the research was conducted in the absence of any commercial or financial relationships that could be construed as a potential conflict of interest.
The reviewer EM and handling editor declared their shared affiliation, and the handling editor states that the process nevertheless met the standards of a fair and objective review.
Bandyopadhyay, P., Dey, A., and Mukhopadhyay, A. K. (2012). Novel combined scratch and nanoindentation experiments on soda-lime-silica glass. Int. J. Appl. Glass Sci. 3, 163–179. doi:10.1111/j.2041-1294.2011.00073.x
Bulusara, V. H., and Chandrasekar, S. (1997). Direct observation of contact damage around scratches in brittle solids. Proc. SPIE 3060, 76–88. doi:10.1117/12.277067
Gross, T. M. (2012). Scratch damage in ion-exchanged alkali aluminosilicate glass: crack evolution and the dependence of lateral cracking threshold on contact geometry. Ceram. Trans. 230, 113–122. doi:10.1002/9781118433010.ch8
Gu, W., and Yao, Z. (2011). Evaluation of surface cracking in micron and sub-micron scale scratch tests for optical glass BK7. J. Mech. Sci. Technol. 25, 1167–1174. doi:10.1007/s12206-011-0306-2
Le Houérou, V., Sangleboeuf, J.-C., Dériano, S., Rouxel, T., and Duisit, G. (2003). Surface damage of soda-lime-silica glasses: indentation scratch behavior. J. Non Cryst. Solids 316, 54–63. doi:10.1016/S0022-3093(02)01937-3
Li, K., Shapiro, Y., and Li, J. C. M. (1998). Scratch test of soda-lime glass. Acta Mater. 46, 5569–5578. doi:10.1016/S1359-6454(98)00163-3
Schneider, J., Schula, S., and Weinhold, W. P. (2012). Characterisation of the scratch resistance of annealed and tempered architectural glass. Thin Solid Films 520, 4190–4198. doi:10.1016/j.tsf.2011.04.104
Surdyka, N. D., Pantano, C. G., and Kim, S. H. (2014). Environmental effects on initiation and propagation of surface defects on silicate glasses: scratch and fracture toughness study. Appl. Physics A 116, 519–528. doi:10.1007/s00339-014-8552-7
Wiederhorn, S. M. (1967). Influence of water vapor on crack propagation in soda-lime glass. J. Am. Ceram. Soc. 50, 407–414. doi:10.1111/j.1151-2916.1967.tb15145.x
Yoshida, S., Hayashi, T., Fukuhara, T., Soeda, K., Matsuoka, J., and Soga, N. (2005). Scratch test for evaluation of surface damage in glass. Fract. Mech. Ceram. 14, 101–111. doi:10.1007/978-0-387-28920-5_9
Yoshida, S., Hidaka, A., and Matsuoka, J. (2004). Crack initiation behavior of sodium aluminosilicate glasses. J. Non Cryst. Solids 344, 37–43. doi:10.1016/j.jnoncrysol.2004.07.019
Keywords: soda-lime-silica glass, scratch, cracking, lateral crack, median crack, stress corrosion
Citation: Matsuoka J, Guo D and Yoshida S (2017) Cross-section Morphology of the Scratch-Induced Cracks in Soda-Lime-Silica Glass. Front. Mater. 4:8. doi: 10.3389/fmats.2017.00008
Received: 30 November 2016; Accepted: 09 March 2017;
Published: 24 March 2017
Edited by:
Lothar Wondraczek, University of Jena, GermanyReviewed by:
Timothy Michael Gross, Corning Incorporated, USACopyright: © 2017 Matsuoka, Guo and Yoshida. This is an open-access article distributed under the terms of the Creative Commons Attribution License (CC BY). The use, distribution or reproduction in other forums is permitted, provided the original author(s) or licensor are credited and that the original publication in this journal is cited, in accordance with accepted academic practice. No use, distribution or reproduction is permitted which does not comply with these terms.
*Correspondence: Jun Matsuoka, bWF0c3Vva2EuakBtYXQudXNwLmFjLmpw
Disclaimer: All claims expressed in this article are solely those of the authors and do not necessarily represent those of their affiliated organizations, or those of the publisher, the editors and the reviewers. Any product that may be evaluated in this article or claim that may be made by its manufacturer is not guaranteed or endorsed by the publisher.
Research integrity at Frontiers
Learn more about the work of our research integrity team to safeguard the quality of each article we publish.