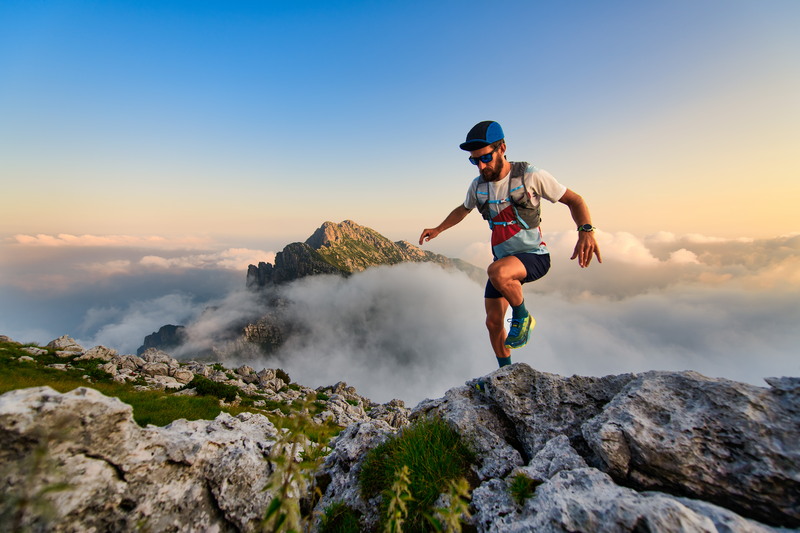
94% of researchers rate our articles as excellent or good
Learn more about the work of our research integrity team to safeguard the quality of each article we publish.
Find out more
ORIGINAL RESEARCH article
Front. Mater. , 05 January 2015
Sec. Smart Materials
Volume 1 - 2014 | https://doi.org/10.3389/fmats.2014.00034
In order to enhance adjustable mechanical properties of a specific magnetorheological elastomer (MRE), this study presents a new exterior structure of MRE by punching circular honeycomb holes on the MRE samples. Seven silicone rubber MRE samples with the same component are fabricated and then punched holes with different numbers and diameters. The influence of different porosities on the mechanical properties of MRE under various magnetic fields is experimentally investigated by using a rheometer with electromagnetic suite. It is shown from experimental investigation that the porosity of MRE samples has a significant impact on the performance of MRE; the shear storage modulus (MR effect), and the loss factor is greatly increased. It is also observed that all the field-induced mechanical properties of the samples attain their respective maximum performance when the porosity increases to a critical value. The experimental results presented in this work directly indicate that high performances of the field-dependent mechanical and rheological properties can be achieved by means of external alternative structures such as honeycomb holes.
Magnetorheological elastomer (MRE) is a relatively new branch of magnetorheological (MR) material family, whose rheological, mechanical, and magnetic properties can be varied continuously, rapidly, and reversibly under applied magnetic field (Jolly et al., 1996; Gong et al., 2005). MRE mainly consists of soft magnetic particles in a rubber-like non-magnetic matrix material. The outstanding field-control characteristic means that MRE has wide application prospects in smart isolator (Opie and Yim, 2011; Li et al., 2012, 2013), adaptive absorber (Deng et al., 2006), and controllable actuator (Böse et al., 2012). Simultaneously, it is well known that the compromise between mechanical properties and MR effects of existing MRE materials limits their engineering applications in which suitable quasi-static and dynamic mechanics performances are coordinately demanded. In order to develop high-performance MRE, many researchers and investigators improved formula, raw material selection, as well as manufacturing process (Hu et al., 2005; Böse, 2007; Chen et al., 2007; Li et al., 2008; Ge et al., 2013). However, a few academics have studied the approaches of altering exterior structure of MRE to improve the mechanical performance of MRE. In the literature, York et al. (2007) designed MR fluid-elastomer (MRF-E) composite through encapsulating MR fluids into an elastomer to achieve both the stiffness and damping capability controlled by an external magnetic field. Zhang et al. (2008) fabricated the patterned MREs with pre-designed lattice and body centered cubic (BCC) structures. Zhang et al. (2010) prepared a type of hybrid MRE, in which MRFs and magnetorheological gels (MRGs) were injected into the punched holes, to improve mechanical performance. Ju et al. (2012) fabricated isotropic porous MRE by using the decomposition reaction of filled NH4HCO3 to generate the porous structure. They showed that both MR effect and damping property of the porous MRE reached a higher level than that of the MRE without pores.
To this end, generally, circular cell honeycomb solids provide an alternative exterior structure with the potential for improved mechanical properties, which have small solid volume fractions or relative densities. Furthermore, the reasonable place to start this study is to investigate the influence of circular honeycomb structure in the field-dependent performance without changing the formula and process of the original MRE. Consequently, a technical novelty of this work is to propose a new silicone rubber MRE with circular honeycomb holes. In order to validate high performances of the proposed MRE, several MRE samples with different porosities are tested under shear mode in an increasing magnetic field. The dynamic magnetic-controllable mechanical properties of MRE such as shear storage modulus, MR effect, and loss factor are confirmed by calculation and analysis of experimental results. It is reasonably addressed that this study can propose an effective approach to improve the mechanical properties of MRE by changing external alternative structures without modification of MRE formula.
Magnetorheological elastomer specimens were composed by magnetic particles in an elastic matrix. To prepare MREs, a two-component room temperature vulcanizing (RTV) silicone rubber (Type: SC-2110, Beijing Sanchen Industrial New Material Co. Ltd., China) was selected as the base elastomer materials, while a silicone oil with a kinetic viscosity of 500 cSt was mixed within the specimen to change the ductility of the rubber base. The filler particles dispersed in the matrix were carbonyl iron particles (Type: JCF2-2, Jilin Jien Nickel Industry Co. Ltd., China) with the size distribution d50 = 5 ~ 8 μm. In all specimens, the mass fraction of the carbonyl iron particles, silicone rubber, and silicone oil was 70, 20, and 10%, respectively. A flow chart of MRE samples preparation was shown in Figure 1. The fabrication procedure of MREs was as follows: firstly, the iron particles were mixed into the silicone rubber in a beaker and then stirred for about 10 min at room temperature. Secondly, after all ingredients were evenly mixed, the resulting material was put in a vacuum drying oven to remove air bubbles and then packed into an aluminum mold. Finally, the mixture was cured for 24 h at room temperature in a self-developed permanent magnet device with the magnetic field of 600 mT.
In this study, seven anisotropic MRE samples with the uniform size of 20 mm in diameter and 1 mm in thickness were cut from the prepared MRE specimens. Different numbers and sizes of holes were punched regularly in the MRE samples by using the punch with a suitable drill, as shown in Table 1. Moreover, the holes positioned parallel to the direction of the chain-like structure in the MREs. Figure 2 is the photograph of samples used in this experimental study.
Dynamic mechanical properties of MRE specimens were measured by using an advanced commercial rheometer (MCR 301, Anton Paar Co., Austria). The rheometer and its operating principle were shown in Figure 3. A parallel-plate rotor and a Magneto Rheological Device (MRD 170, Anton Paar Co., Austria) were installed in the rheometer. The diameter of the plate was 20 mm and the parallel-plate gap was fixed at 1 mm. The testing magnetic field perpendicular to the direction of the shear flow was generated by adjusting the current value supplied to the electromagnetic coil, and testing temperatures were controlled by a water bath. A sample was placed between the rotating disk and the base without slip effect. When the rotating disk rotated, the sample worked in oscillation shear mode, in which the direction of the oscillation was represented by green arrow. This system applied a desired oscillatory strain amplitude and frequency to the sample and measured the amplitude and phase of the output force, from which the shear storage modulus and loss modulus were calculated. In the experiment, the MRE sample was sandwiched between rotating disk and base in parallel, in which the particle chains were distributed along the thickness direction. MRE samples were tested under shear mode at room temperature controlled by a water circulator. The shear oscillation frequency and shear strain amplitude were set as a constant 10 Hz and 1%, respectively. To avoid the sliding effect between the sample and the parallel plate, a constant normal force of 10 N was applied during the tests. As shown in Figure 4, the shear stress appears to be a linear relationship with the increasing shear strain amplitudes ranging from 0.1 to 10% at 10 Hz during the previous dynamic strain sweep experiments without magnetic field, in which demonstrated that there is no sliding effect in the rheometer testing system. In addition, each sample was measured for three times at the same condition with the magnetic flux density changing from 0 to 1.2 T.
The shear storage modulus G′ for the punched MRE samples with different numbers of holes (different porosities) is shown in Figure 5. As can be seen from the experimental data, the field-dependent storage modulus G′ of each samples exhibit an increasing trend with increasing magnetic flux density, which was because the interaction among iron particles filled in the matrix resulted in an increase in mechanical stiffness. As shown in Figure 6, the zero-field storage modulus of non-porous MRE sample is larger than that of porous MRE samples. This is due to the integrity of sample. However, the modulus of the samples firstly increases with increasing porosity up to 9.00% (Sample MRE-N9-D2) and then modulus decreases with increasing porosity. A linear fitting results for the initial storage modulus and Gaussian fitting for the maximum modulus at magnetic saturation are presented in Figure 6. It can be easily seen that the field-induced storage modulus is reached a maximum of 1.3 MPa when the porosity is 9.00%. With the increase of porosity, the shear storage modulus at magnetic saturation showed greater than that of non-porous MRE, as the chain-like structures of iron particles highly reduced. The MR effect is a critical parameter for evaluating MRE performance, and is defined as follow:
where is the shear storage at magnetic saturation, G0 is the initial modulus. Figure 7 shows the relation between the MR effects and different porosities, in which the red curve has been given with a feasible Gaussian peak fitting. Obviously, the MR effects for the prepared samples reached a maximum of 300% when the porosity of MRE samples was 13.00% (Sample MRE-N13-D2). Due to a lower initial modulus, the MR effect of MRE-N13-D2 was higher than that of MRE-N9-D2, which had the largest magnetic modulus. As a result, it is obvious that MR effects can be dramatically improved by punching circular honeycomb holes.
The damping property of MRE with circular honeycomb holes is also investigated. The loss factor is an important factor of damping capability expressed as follows:
where G″ is the loss modulus. And to be clear, in the measurement of viscoelastic material, the loss modulus represents the level of dissipating energy by the viscous portion while the loss factor is the ratio of loss modulus to storage modulus. Figures 8 and 9 show the loss modulus and loss factor of MRE samples with different porosities under different magnetic flux densities. It can be seen that both the loss modulus and the loss factor of punched MRE samples are higher than that of un-punched MRE sample to a variable extent. Furthermore, the two damping parameters have showed firstly increasing and then decreasing trend with the increasing porosity. It is seen from Figure 10 that the sample MRE-N13-D2 with a porosity of 13% and the sample MRE-N17-D2 with a porosity of 17% are reached to the best damping capacity. Due to the exterior structural changes after punching holes on the MRE samples, the damping property of MRE improved under various magnetic fields.
In this work, a series of MREs with different numbers of two-dimensional circular honeycomb holes were developed based on the ordinary silicon rubber MREs. The influence of circular honeycomb holes or porosities on the mechanical properties of MRE under different magnetic fields was experimentally investigated. The dynamic mechanical properties including storage modulus, MR effect, loss modulus, and loss factor have been significantly improved by punching holes on the MRE samples, which adopted various exterior structure of MRE samples. It has been also observed that the field-induced mechanical performance increases first and then decreases with the increasing porosity. The shear storage modulus, MR effect, loss modulus, and loss factor reached a maximum when the porosity of MRE samples were 9.00, 13.00, 13.00, and 17.00%, respectively. The experimental results presented in this work indicate that high-performance properties of MRE can be achieved without changing its preparation in the specific formula. In addition, this work can be a useful guideline to choose optimal number of porosity, which can produce maximum performances of mechanical and rheological properties of MRE under the same magnetic field.
The authors declare that the research was conducted in the absence of any commercial or financial relationships that could be construed as a potential conflict of interest.
This work was financially supported by the National Natural Science Foundation of China (Grant No. 61203098), the National Science and Technology Support Program (2012BAF06B00F).
Böse, H. (2007). Viscoelastic properties of silicone-based magnetorheological elastomers. Int. J. Mod. Phys. B 21, 4790–4797. doi: 10.1142/S0217979207045670
Böse, H., Rabindranath, R., and Ehrlich, J. (2012). Soft magnetorheological elastomers as new actuators for valves. J. Intell. Mater. Syst. Struct. 23, 989–994. doi:10.1177/1045389X11433498
Chen, L., Gong, X. L., Jiang, W. Q., Yao, J. J., Deng, H. X., and Li, W. H. (2007). Investigation on magnetorheological elastomers based on natural rubber. J. Sci. Mater. 42, 5483–5489. doi:10.1007/s10853-006-0975-x
Deng, H. X., Gong, X. L., and Wang, L. H. (2006). Development of an adaptive tuned vibration absorber with magnetorheological elastomer. Smart Mater. Struct. 15, N111–N116. doi:10.1088/0964-1726/15/5/N02
Ge, L., Gong, X., Fan, Y., and Xuan, S. (2013). Preparation and mechanical properties of the magnetorheological elastomer based on natural rubber/rosin glycerin hybrid matrix. Smart Mater. Struct. 22, 115029. doi:10.1088/0964-1726/22/11/115029
Gong, X. L., Zhang, X. Z., and Zhang, P. Q. (2005). Fabrication and characterization of isotropic magnetorheological elastomers. Polym. Test. 24, 669–676. doi:10.1016/j.polymertesting.2005.03.015
Hu, Y., Wang, Y. L., Gong, X. L., Gong, X. Q., Zhang, X. Z., Jiang, W. Q., et al. (2005). New magnetorheological elastomers based on polyurethane/Si-rubber hybrid. Polym. Test. 24, 324–329. doi:10.1016/j.polymertesting.2004.11.003
Jolly, M. R., Carlson, J. D., and Muñoz, B. C. (1996). A model of the behaviour of magnetorheological materials. Smart Mater. Struct. 5, 607–614. doi:10.1088/0964-1726/5/5/009
Pubmed Abstract | Pubmed Full Text | CrossRef Full Text | Google Scholar
Ju, B. X., Yu, M., Fu, J., Yang, Q., Liu, X. Q., and Zheng, X. (2012). A novel porous magnetorheological elastomer: preparation and evaluation. Smart Mater. Struct. 21, 035001. doi:10.1088/0964-1726/21/3/035001
Li, J. F., Gong, X. L., Xu, Z. B., and Jiang, W. Q. (2008). The effect of pre-structure process on magnetorheological elastomer performance. Int. J. Mater. Res. 99, 1358–1364. doi:10.3139/146.101775
Li, W. H., Zhang, X. Z., and Du, H. P. (2012). Development and simulation evaluation of a magnetorheological elastomer isolator for seat vibration control. J. Intell. Mater. Syst. Struct. 23, 1041–1048. doi:10.1177/1045389x11435431
Li, Y., Li, J., Li, W., and Samali, B. (2013). Development and characterization of a magnetorheological elastomer based adaptive seismic isolator. Smart Mater. Struct. 22, 035005. doi:10.1088/0964-1726/22/3/035005
Opie, S., and Yim, W. (2011). Design and control of a real-time variable modulus vibration isolator. J. Intell. Mater. Syst. Struct. 22, 113–125. doi:10.1177/1045389X10389204
York, D., Wang, X., and Gordaninejad, F. (2007). A new MR fluid-elastomer vibration isolator. J. Intell. Mater. Syst. Struct. 18, 1221–1225. doi:10.1177/1045389X07083622
Zhang, W., Gong, X. L., Xuan, S. H., and Xu, Y. G. (2010). High-performance hybrid magnetorheological materials: preparation and mechanical properties. Ind. Eng. Chem. Res. 49, 12471–12476. doi:10.1021/ie101904f
Keywords: magnetorheological elastomer, mechanical property, rheological property, honeycomb holes, ordinary silicon rubber
Citation: Yu M, Xing Z, Zheng X, Fu J and Choi S-B (2015) Experimental investigation on the field-dependent properties of magnetorheological elastomer with circular honeycomb holes. Front. Mater. 1:34. doi: 10.3389/fmats.2014.00034
Received: 02 September 2014; Accepted: 11 December 2014;
Published online: 05 January 2015.
Edited by:
Weihua Li, University of Wollongong, AustraliaReviewed by:
X. M. Zhang, Tohoku University, JapanCopyright: © 2015 Yu, Xing, Zheng, Fu and Choi. This is an open-access article distributed under the terms of the Creative Commons Attribution License (CC BY). The use, distribution or reproduction in other forums is permitted, provided the original author(s) or licensor are credited and that the original publication in this journal is cited, in accordance with accepted academic practice. No use, distribution or reproduction is permitted which does not comply with these terms.
*Correspondence: Miao Yu, College of Optoelectronic Engineering, Chongqing University, Chongqing, 400044, China e-mail:eXVtaWFvQGNxdS5lZHUuY24=
Disclaimer: All claims expressed in this article are solely those of the authors and do not necessarily represent those of their affiliated organizations, or those of the publisher, the editors and the reviewers. Any product that may be evaluated in this article or claim that may be made by its manufacturer is not guaranteed or endorsed by the publisher.
Research integrity at Frontiers
Learn more about the work of our research integrity team to safeguard the quality of each article we publish.