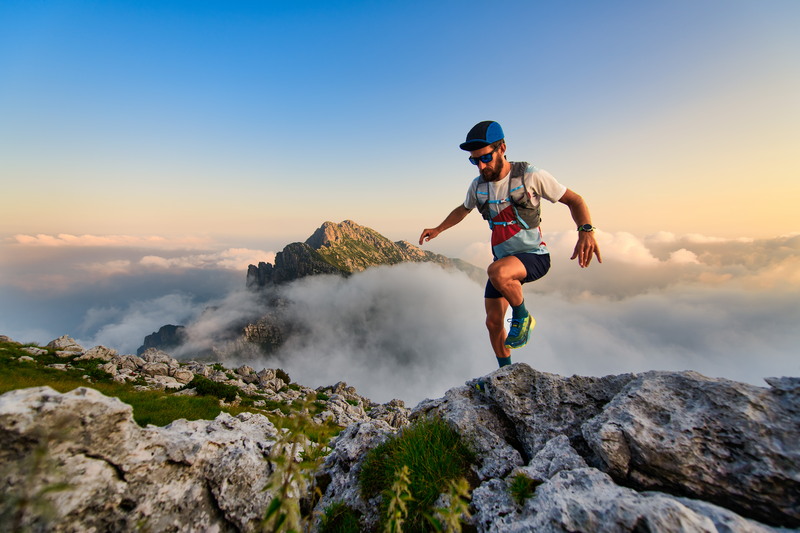
95% of researchers rate our articles as excellent or good
Learn more about the work of our research integrity team to safeguard the quality of each article we publish.
Find out more
MINI REVIEW article
Front. Mater. , 30 September 2014
Sec. Smart Materials
Volume 1 - 2014 | https://doi.org/10.3389/fmats.2014.00017
Cellulose electro-active paper (EAPap) is an attractive material of electro-active polymers family due to its smart characteristics. EAPap is thin cellulose film coated with metal electrodes on both sides. Its large displacement output, low actuation voltage, and low power consumption can be used for biomimetic sensors/actuators and electromechanical system. Because cellulose EAPap is ultra-light weight, easy to manufacture, inexpensive, biocompatible, and biodegradable, it has been employed for many applications such as bending actuator, vibration sensor, artificial muscle, flexible speaker, and can be advantageous in areas such as micro-insect robots, micro-flying objects, micro-electromechanical systems, biosensors, and flexible displays.
In last few decades, electro-active polymers (EAPs) have received significant attention due to their ability to fabricate large displacement actuators. Cellulose is an endless source of raw materials for environmentally friendly and biocompatible products, and its offshoot are used for optical films, coatings, laminates, pharmaceuticals, and textiles. The shear piezoelectricity in polymers of biological origin such as cellulose and collagen was reported very early in 1950; Fukada experimentally demonstrated the piezoelectric coefficients of wood and verified that oriented cellulose crystallites are responsible for the observed piezoelectricity (Fukada, 2000). The piezoelectric effect exhibited by cellulose film depends on various factors, type of wood, environmental conditions, and orientation of samples. Regardless of these early studies, the prospects of cellulose as an ultra light weight material for electromechanical transduction applications have not been fully explored. The early investigation on EAPap actuator characterized by chemically treated paper with thin electrodes on its both sides shows reasonable performance (Kim and Seo, 2002). When 2 MVm−1 of excitation electric field was applied to the paper actuator, more than 3 mm tip displacement was observed from the 30 mm long paper film. However, the actuation frequency was low and force output of the EAPap actuator was also small. The force and frequency bandwidth was improved by variation in thickness in the EAPap material at the cost of low actuation voltage and large bending displacement (Yun et al., 2007). In order to enhance the performance of EAPap actuator, conducting polymer coating on EAPap was suggested, which was previously gold electrodes coated (Deshpande et al., 2005). The electrode thickness plays a key role in the performance of actuator. Other techniques employed to achieve smart actuators were use of a single-walled carbon nanotube/polyaniline coated cellulose electro-active paper (EAPap) hybrid actuator and by mixing multi-walled carbon nanotubes and cellulose (Yun et al., 2006; Yun and Kim, 2007). Carbon nanotubes-mixed cellulose-EAPap actuator exhibited the highest mechanical power output. The investigation on in-plain strain under electric fields reveals that high Young’s modulus of EAPap is promising for its use as artificial muscle. The electrical power consumption was <8 mW/cm2, which is beyond the safety limit of microwave power in air, which direct to the possibility for achieving microwave driven EAPap actuators (Kim et al., 2007).
The potential of cellulose EAPap for smart application is promising. Addition of poly(ethylene oxide)-poly(ethylene glycol) (PEO-PEG), conductive polymer, and carbon nanotubes coatings improved the displacement output and force output of EAPap actuators (Mahadeva et al., 2009a). Cellulose EAPap can be characterized as biosensor since it is biodegradable, biocompatible, capable of broad chemical modification, and hydrophilic (Kim et al., 2008d). The direct piezoelectric effect extends its possibility to be used as self powered vibration and strain sensor for structural health monitoring, energy scavenging transducers, flexible speaker in acoustic applications, and beam vibration control.
Kim et al. (2006b) reported the discovery of cellulose as a smart material that can be used for biomimetic sensor/actuator devices and micro-electromechanical systems. This smart cellulose was termed as EAPap. Considering the cellulose structure and processing of cellulose-based EAPap, its actuation mechanism is combination of ion migration and dipolar orientation. Figure 1 depicts the concept of EAPap bending actuator. Cellulose EAPap is a film of regenerated cellulose and morphologically, regenerated cellulose consists of ordered and disordered regions. The ordered domains are composed of crystalline and amorphous sections, and water molecules attached to hydroxyl groups can be found in large disordered regions. During the fabrication process, sodium ions were injected in the fiber. When electric field was applied, these ions migrate to anode, selective ionic, and water transport across the polymer, which direct to bending of actuator. Consequently, the large ordered region is responsible for the dipolar orientation, leading to permanent polarization, which results into piezoelectric behavior.
Figure 1. Concept of EAPap bending actuator: (A) EAPap actuator, (B) cellulose microfibril, and (C) water molecules bonded with hydroxyls. Adapted with permission from Kim et al. (2006b).
The evaluation of electromechanical coupling is very essential to utilize EAPap for broader applications. To compute piezoelectricity of EAPap, piezoelectric charge constants of EAPap were investigated using quasi-static direct piezoelectricity. Induced charge on the surface of electrode was measured for different specimens when the mechanical stretching was applied to the EAPap. Piezoelectric charge constant of 45° sample has the largest value, which shows the same pattern observed in the electromechanical behavior test. In-plane piezoelectric charge constants of EAPap are very similar to commercial piezoelectric polymer films PVDF (Kim et al., 2008b). XRD patterns showed that samples fabricated by electrospinning and stretching method enhanced crystallinity of cellulose film, which improves piezoelectricity of EAPap (Yun et al., 2008b). Wet drawing method with different stretching conditions during the fabrication process of cellulose film reveals that EAPap is sensitive to drawing ratio and material orientation (Yang et al., 2009). Another effective way to enhance the piezoelectricity of EAPap is using electrically aligned cellulose film. The application of external electric fields induces formation of nanofibers in the cellulose, resulting in an increase in the crystallinity index (CI) values (Yun et al., 2009). Theoretical model for electromechanical actuation behavior of CBC-EAPap shows good correlation with the experiment results, which can be helpful to predict and understand the electromechanical behavior of EAPap devices such as artificial muscle, biomimetic pump, and other potential applications (Jang et al., 2009).
Mechanical properties of EAPap are heavily dependent on the humidity and temperature conditions. The elastic strength and stiffness gradually decreases with the increase of both humidity and temperature. The measured value of Young’s modulus of EAPap ranges from 4 to 9 GPa, which is relatively on the higher side as compared to other EAP materials. Layered and oriented cellulose-EAPap is a complex anisotropic material in term of elastic and plastic deformation, creep. It is also dependent on temperature and humidity (Kim et al., 2008a). EAPap creeps at elevated temperature, the elastic behavior varies inversely with temperature and with the bias angle tested. However, the overall viscous behavior of the EAPap tested was relatively complex (Kim et al., 2008c; Lee et al., 2009a). Hydrothermal behavior of EAPap showed that the creep resistance varied by changing the orientation of EAPap samples (Kim et al., 2009).
Cellulose-EAPap actuation mechanism, which is combination of piezoelectric effect and ion migration effect associated with constituent of cellulose materials and their material properties, demonstrates its potential for many applications. Due to exciting actuation phenomenon, EAPap can be used for sensors and actuating devices. Kim et al. (2006a) studied a micro-patterning technique regarded as micro transfer printing, a gold (Au) electrode pattern for a surface acoustic wave (SAW) MEMS device on cellulose EAPap. Cellulose-based EAPap shows potential as biosensor since it is eco-friendly, sustainable, biocompatible, good mechanical strength and stiffness, and hydrophilic nature. However, some challenges needed to be addressed in terms of consistency, material robustness, and niche application progress (Kim et al., 2008d).
Electro-active paper performance and material characterization shows promise for light weight smart and hybrid actuators, which make use of converse piezoelectric effect (Yun et al., 2008a; Mahadeva et al., 2009b). More recently, a remotely powered and controlled actuator made by using a dipole rectenna array along with modulated microwaves was investigated. Modulated microwave power transmission is very valuable technology for remotely driven actuators, biomimetic robots, and remote sensing units (Yang et al., 2013). EAPap also shows fair quality results when tested as vibration sensor and for beam vibration control (Lee et al., 2009b; Kim et al., 2010a,b). Acoustic characterization of cellulose EAPap for flexible film type speaker suggests that piezoelectricity of EAPap can be used in acoustic applications (Kim et al., 2011). The reasonable piezoelectric coupling coefficient and ability to withstand high vibration amplitude due to flexible nature can help to develop EAPap energy harvesting wireless sensor nodes. Cellulose film coated with different size metal electrode was excited under different acceleration input to examine its possibility for flexible energy harvesting transducer (Abas et al., 2014a,b). The tests on EAPap demonstrate the feasibility of cellulose EAPap for haptic applications (Yun et al., 2010). Cellulose–silica/gold one-dimensional nano-composite was prepared by sol-gel cross linking process, and was investigated for electronic applications due its optical, electrical, and mechanical properties (Kim et al., 2014). Figure 2 shows cellulose paper applications.
Figure 2. Cellulose paper applications: (A) micro-flying object; (B) micro-insect robots; (C) biodegradable MEMS; (D) thin flexible EAPap speaker film after electrode formation. Adapted with permission from Kim et al. (2006b, 2011).
A review of cellulose EAPap is presented from its discovery to real world technology applications. Cellulose paper has been investigated as a smart material and can be used as biomimetic actuators and sensors. Its smart characteristics and actuation mechanism makes it suitable for many applications including micro robotics, MEMS devices, flexible speaker, micro pumps, remotely controlled actuators, and a possible application as self powered wireless sensor node. There is a lot of potential in cellulose EAPap for a smart material. Nevertheless, some issues exist in terms of consistency, material robustness, environmental effects, and future applications development.
The authors declare that the research was conducted in the absence of any commercial or financial relationships that could be construed as a potential conflict of interest.
This research was supported by the Basic Science Research Program, through the National Research Foundation of Korea (NRF), funded by the Ministry of Education, Science and Technology (NRF-2011-0021720).
Abas, Z., Kim, H. S., Zhai, L., Kim, J., and Kim, J. H. (2014a). Electrode effects of a cellulose-based electro-active paper energy harvester. Smart Mater. Struct. 23, 074003. doi: 10.1088/0964-1726/23/7/074003
Abas, Z., Kim, H. S., Zhai, L., Kim, J., and Kim, J. H. (2014b). Possibility of cellulose-based electro-active paper energy scavenging transducer. J. Nanosci. Nanotechnol. 14, 7458–7462. doi:10.1166/jnn.2014.9566
Deshpande, S. D., Kim, J., and Yun, S. R. (2005). Studies on conducting polymer electroactive paper actuators: effect of humidity and electrode thickness. Smart Mater. Struct. 14, 876–880. doi:10.1088/0964-1726/14/4/048
Fukada, E. (2000). History and recent progress in piezoelectric polymers. IEEE Trans. Ultrason. Ferroelectr. Freq. Control 47, 1277–1290. doi:10.1109/58.883516
Jang, S. D., Kim, J. H., and Kim, J. (2009). Modeling of electromechanical behavior of chitosan-blended cellulose electroactive paper (EAPap). J. Appl. Phys. 105, 103510–103516. doi:10.1063/1.3129699
Kim, G. H., Ramesh, S., Kim, J. H., Jung, D., and Kim, H. S. (2014). Cellulose-silica/gold nanomaterials for electronic applications. J. Nanosci. Nanotechnol. 14, 7495–7501. doi:10.1166/jnn.2014.9551
Kim, H. S., Kim, J., Jung, W., Ampofo, J., Craft, W., and Sankar, J. (2008a). Mechanical properties of cellulose electro-active paper under different environmental conditions. Smart Mater. Struct. 17, 015029. doi:10.1088/0964-1726/17/01/015029
Kim, H. S., Li, Y., and Kim, J. (2008b). Electro-mechanical behavior and direct piezoelectricity of cellulose electro-active paper. Sens. Actuat. A Phys. 147, 304–309. doi:10.1016/j.sna.2008.05.003
Kim, J., Ampofo, J., Craft, W., and Kim, H. S. (2008c). Modeling elastic, viscous and creep characteristics of cellulose electro-active paper. Mech. Mater. 40, 1001–1011. doi:10.1016/j.mechmat.2008.07.001
Kim, J., Yun, S., and Lee, S. K. (2008d). Cellulose smart material: possibility and challenges. J. Intell. Mater. Syst. Struct. 19, 417–422. doi:10.1177/1045389X07083140
Kim, H. S., Yang, C., and Kim, J. (2009). Hygrothermal behavior of electro-active paper actuator. J. Mech. Sci. Technol. 23, 2285–2290. doi:10.1007/s12206-009-0352-1
Kim, J., Bae, S. H., and Lim, H. G. (2006a). Micro transfer printing on cellulose electro-active paper. Smart Mater. Struct. 15, 889–892. doi:10.1088/0964-1726/15/3/026
Kim, J., Yun, S., and Ounaies, Z. (2006b). Discovery of cellulose as a smart material. Macromolecules 39, 4202–4206. doi:10.1088/0957-4484/25/9/092001
Kim, J., Jung, W., and Kim, H. S. (2007). In-plane strain of electro-active paper under electric fields. Sens. Actuat. A Phys. 140, 225–231. doi:10.1016/j.sna.2007.06.041
Kim, J., Lee, H., and Kim, H. S. (2010a). Beam vibration control using cellulose-based electro-active paper sensor. Int. J. Precis. Eng. Manuf. 11, 823–827. doi:10.1007/s12541-010-0099-8
Kim, J., Lee, H., Kim, H. S., and Kim, J. (2010b). Vibration sensor characteristics of piezoelectric electro-active paper. J. Intell. Mater. Syst. Struct. 21, 1123–1130. doi:10.1177/1045389X10376679
Kim, J., and Seo, Y. B. (2002). Electro-active paper actuators. Smart Mater. Struct. 11, 355–360. doi:10.1088/0964-1726/11/3/305
Kim, J., Yun, G. Y., Kim, J. H., Lee, J., and Kim, J. H. (2011). Piezoelectric electro-active paper (EAPap) speaker. J. Mech. Sci. Technol. 25, 2763–2768. doi:10.1007/s12206-011-0718-z
Lee, S., Kim, J. H., Kang, K., Kim, J., Kim, H. S., and Yang, C. (2009a). Characterization of micro-scale creep deformation of an electro-active paper actuator. Smart Mater. Struct. 18, 095008. doi:10.1088/0964-1726/18/9/095008
Lee, S. W., Kim, J. H., Kim, J., and Kim, H. S. (2009b). Characterization and sensor application of cellulose electro-active paper (EAPap). Chin. Sci. Bull. 54, 2703–2707. doi:10.1007/s11434-009-0219-y
Mahadeva, S. K., Kim, J., Kang, K. S., Kim, H. S., and Park, J. M. (2009a). Effect of Poly(ethylene oxide)-Poly(ethylene glycol) addition on actuation behavior of cellulose Electroactive Paper. J. Appl. Polym. Sci. 114, 847–852. doi:10.1002/app.30450
Mahadeva, S. K., Yun, S., and Kim, J. (2009b). Dry electroactive paper actuator based on cellulose/poly(ethylene oxide)-poly(ethylene glycol) microcomposite. J. Intell. Mater. Syst. Struct. 20, 1141–1146. doi:10.1177/1045389X09103222
Yang, C., Kim, J. H., Kim, J. H., Kim, J., and Kim, H. S. (2009). Piezoelectricity of wet drawn cellulose electro-active paper. Sens. Actuat. A Phys. 154, 117–122. doi:10.1016/j.sna.2009.07.016
Yang, S. Y., Mahadeva, S. K., and Kim, J. (2013). Remotely powered and controlled EAPap actuator by amplitude modulated microwaves. Smart Mater. Struct. 22, 017001. doi:10.1088/0964-1726/22/1/017001
Yun, G. Y., Kim, H. S., and Kim, J. (2008a). Blocked force measurement of an electro-active paper actuator using a cantilevered force transducer. Smart Mater. Struct. 17, 025021. doi:10.1088/0964-1726/17/2/025021
Yun, G. Y., Kim, H. S., Kim, J., Kim, K., and Yang, C. (2008b). Effect of aligned cellulose film to the performance of electro-active paper actuator. Sens. Actuat. A Phys. 141, 530–535. doi:10.1016/j.sna.2007.10.014
Yun, G. Y., Kim, J., Kim, J. H., and Kim, S. Y. (2010). Fabrication and testing of cellulose EAPap actuators for haptic application. Sens. Actuat. A Phys. 164, 68–73. doi:10.1016/j.sna.2010.09.005
Yun, S., Jang, S., Yun, G. Y., and Kim, J. (2009). Electrically aligned cellulose film for electro-active paper and its piezoelectricity. Smart Mater. Struct. 18, 117001. doi:10.1088/0964-1726/18/11/117001
Yun, S., and Kim, J. (2007). A bending electro-active paper actuator made by mixing multi-walled carbon nanotubes and cellulose. Smart Mater. Struct. 16, 1471–1476. doi:10.1088/0964-1726/16/4/062
Yun, S., Kim, J., and Song, C. (2007). Performance of Electro-active paper actuators with thickness variation. Sens. Actuat. A Phys. 133, 225–230. doi:10.1016/j.sna.2006.03.007
Keywords: cellulose, electro-active paper, actuator, piezoelectrics, smart material
Citation: Abas Z, Kim HS, Kim J and Kim J-H (2014) Cellulose electro-active paper: from discovery to technology applications. Front. Mater. 1:17. doi: 10.3389/fmats.2014.00017
Received: 18 July 2014; Accepted: 15 September 2014;
Published online: 30 September 2014.
Edited by:
Ilkwon Oh, Korea Advanced Institute of Science and Technology, South KoreaReviewed by:
Ravi Kumar Cheedarala, Ulsan National Institute of Science and Technology, South KoreaCopyright: © 2014 Abas, Kim, Kim and Kim. This is an open-access article distributed under the terms of the Creative Commons Attribution License (CC BY). The use, distribution or reproduction in other forums is permitted, provided the original author(s) or licensor are credited and that the original publication in this journal is cited, in accordance with accepted academic practice. No use, distribution or reproduction is permitted which does not comply with these terms.
*Correspondence: Heung Soo Kim, Department of Mechanical, Robotics and Energy Engineering, Dongguk University, 30 Pil-Dong 1-ga, Jung-Gu, Seoul 100-715, South Korea e-mail:aGV1bmdzb29AZGd1LmVkdQ==
Disclaimer: All claims expressed in this article are solely those of the authors and do not necessarily represent those of their affiliated organizations, or those of the publisher, the editors and the reviewers. Any product that may be evaluated in this article or claim that may be made by its manufacturer is not guaranteed or endorsed by the publisher.
Research integrity at Frontiers
Learn more about the work of our research integrity team to safeguard the quality of each article we publish.