- 1School of Marine Sciences, Darling Marine Center, University of Maine, Walpole, ME, United States
- 2Aquaculture Research Institute, Darling Marine Center, University of Maine, Walpole, ME, United States
- 3Department of Naval Architecture and Ocean Engineering, United States Naval Academy, Annapolis, MD, United States
- 4Kelson Marine Co., Scarborough, ME, United States
Aquaculture of seaweeds, particularly in emerging farming regions such as North America, Europe, and South America, is steadily increasing. The growth of the sector has been supported by public and private R&D investment with the long-term goal of reducing farm-gate production costs. Reducing expenses would potentially allow growers to target high volume, low value markets, such as hydrocolloids, animal feeds, food thickening agents, biofuels, and carbon dioxide removal (CDR), as well as the higher value, “whole foods” markets. Regardless of the eventual fate of farmed seaweed, nursery production must increase in parallel with ocean cultivation to support the raw materials needs of the expanding industry. We quantified S. latissima (hereafter kelp) nursery production costs and identified potential barriers to cost-effective scaling using a techno-economic model (TEM). Semi-structured interviews with nursery operators in the U.S. and Europe were supplemented by an extensive literature review to parameterize the TEM. Reducing the sporophyte grow-out duration, increasing labor capacity, de-risking energy efficient flow-through systems, and optimizing tank and PVC “spool” size emerged as the most important research priorities based on our analysis. We point towards expanded gametophyte culture, and an associated policy framework to protect wild kelp population structure from monocultures, as necessary elements to support these potential improvements. The results of this work, as well as the open-source nursery TEM, are relevant to seaweed aquaculture producers, policy makers, and researchers, and can be used to guide future decision making regarding the cost-benefit of best available nursery technology.
Introduction
Seaweed aquaculture is increasingly proposed as a component of numerous climate change solutions. Whether as a biofuel, fertilizer, animal feed, or protein, seaweed has immense potential as a source for low carbon food, raw materials, and energy for a growing population (Duarte et al., 2017; Kim et al., 2017; Augyte et al., 2021; Duarte et al., 2021; Roque et al., 2021). Nations around the world have mobilized significant public and private funding to explore these opportunities for sustainable growth. For example, in the United States (US), the Department of Energy’s Macroalgae Research Inspiring Novel Energy Resources (MARINER) program has focused on developing a seaweed industry capable of producing two quads of bioenergy (equivalent to 344 million barrels of oil) by 2050 (ARPA-E, 2017). In the European Union, the Blue Growth Strategy initiative has also recognized seaweed aquaculture as a potential means of generating economic activity while providing food and fuels with minimal greenhouse gas emissions (European Commission, 2012). Research is underway to explore a variety of seaweed end-uses, including organic fertilizers and aquaculture feeds, in numerous South American nations (Buschmann et al., 2008; Alemañ et al., 2019). The National Academy of Sciences, Engineering, and Medicine (NASEM) recently profiled the potential of farmed seaweeds as a scalable carbon dioxide removal (CDR) technology. NASEM has recommended that a ~USD $45 million per year research program would be required to reduce scientific uncertainty, develop verification standards, and facilitate scaling (NASEM, 2021). Regardless of the eventual fate of farmed seaweed biomass, recent expanded interest in the crop determines that global production will need to substantially increase to meet future demand.
The majority of globally farmed seaweed originates in East or Southeast Asia, regions that have long production histories. The sector is dominated by kelp species (of the order Laminariales), and the red seaweeds Kappaphychus and Eucheuma spp (FAO, 2020) destined for use as cosmetics, food thickening agents, fertilizers, pharmaceuticals, and consumer food products (Kim et al., 2017; Augyte et al., 2021). China, Indonesia, Japan, and the Republic of Korea alone generated nearly 95% of the 31.5 million tons (wet mass) harvested in 2018 (FAO, 2020). Despite the ambitious goals of research and commercialization programs in North America, Europe, and South America, the three continents currently produce a small fraction, <0.01%, of the world’s farmed seaweeds (Alemañ et al., 2019; FAO, 2020; Piconi et al., 2020; North Sea Farmers, 2021). High volume and mature domestic markets for macroalgae-based raw materials exist to supply the phycocolloid industries in both the US and Europe, however domestic producers are hampered by their comparatively small scale (Hafting et al., 2015). This, coupled with the difficulty of competing with imported products from Asian commodity seaweed markets, has resulted in kelp growers in emerging regions primarily targeting smaller “whole foods’’ markets, relying on value-added processing, such as drying, milling, or blanching, to generate profit (van den Burg et al., 2016; Grebe et al., 2019; McKinley Research Group, 2021; St-Gelais et al., 2022).
Recent commercial success by farmers outside of the Pacific Rim targeting the “whole foods” market reflects substantial public and private investments in research and development (Redmond et al., 2014; Yarish et al., 2017; North Sea Farmers, 2021). Yet the cost structures of these farms remain fundamentally misaligned with the raw material needs of many “high volume, low value” applications, i.e., the biofuel, animal feed, nutraceutical, and Carbon Dioxide Removal (CDR) sectors (Thomas, 2018; Hasselström et al., 2020). A primary goal of the MARINER program is to reduce farmed seaweed production costs to < $80 per dry ton (ARPA-E, 2017), a price point identified as a prerequisite for a competitive kelp biofuel supply chain. Current and historic production cost estimates for kelp grown in North America, Europe, and South America range from $2,000 - $24,000 ton1 (dry mass; Figure 1). Identifying methods to substantially expand the market, while reducing farmers’ overhead and operating expenses, is a top priority for effective scaling of this emerging industry.
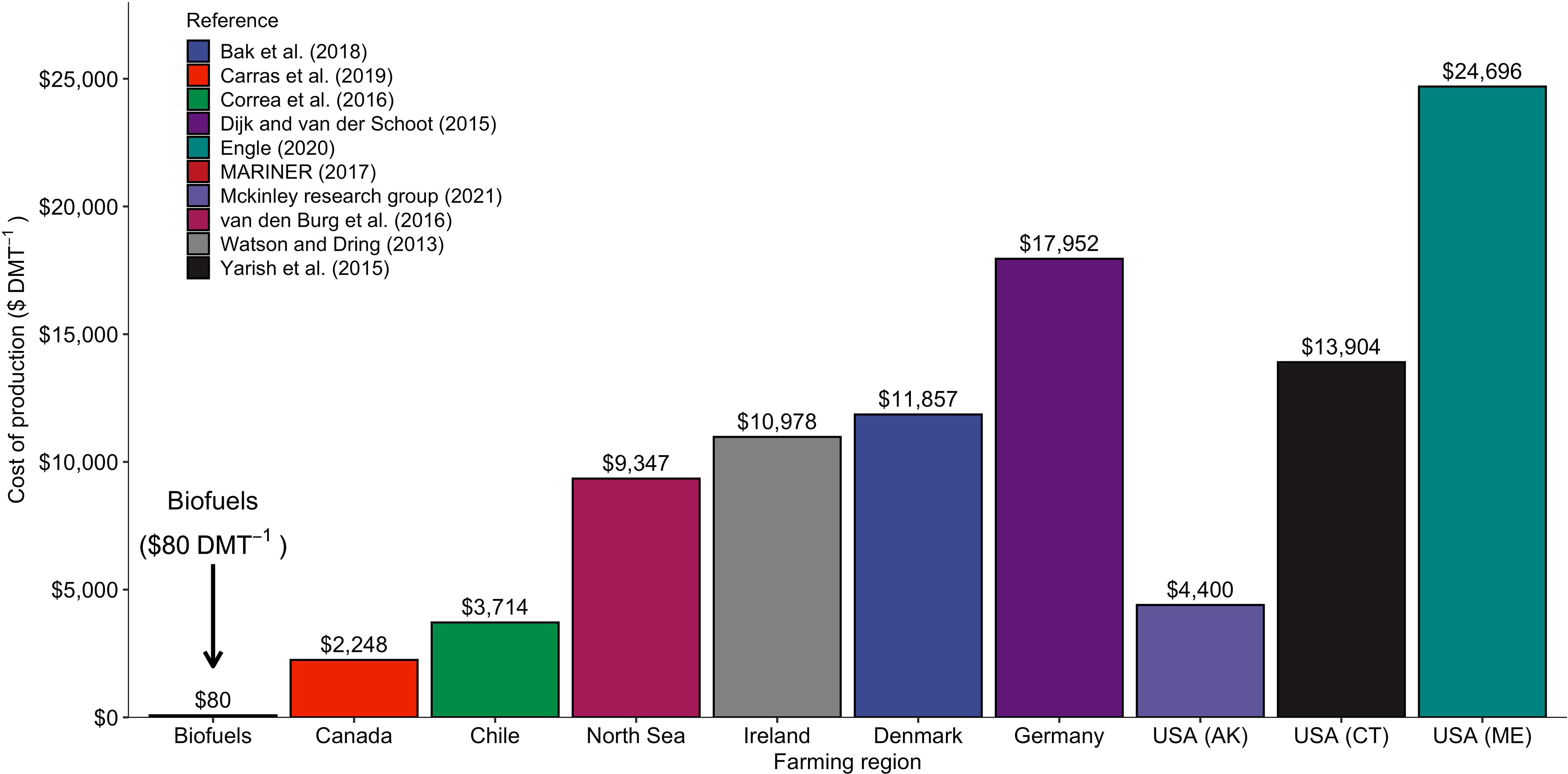
Figure 1 Production costs ($ dry metric ton (DMT)-1) estimated from the literature for kelp produced in emerging farming regions around the world. The farm-gate price required for a profitable biofuels sector ($80 DMT-1) is shown for comparison (ARPA-E, 2017).
The nursery stage is a critical component of any seaweed aquaculture operation and sourcing juveniles can make up a significant portion of expenses. Bringing the production of juvenile sporophytes into a controlled laboratory setting has made “seed” available to both small cottage operations (such as those in North America and Europe), and large industrial scale farms (such as those in Asia) at a price point compatible with their respective sectors (Forbord et al., 2012; Su et al., 2017). Manipulation of the life cycle and selective breeding programs of many commercially important species, such as kelps, have allowed growers in Asia to genetically select for increased yield and temperature tolerance (Hu et al., 2021). Many nurseries in Asia also rely on large, flow-through systems that utilize ambient light and energy efficient pumps, thereby keeping production costs low at large scales (Su et al., 2017). The combination of selective breeding and efficient nurseries has, in part, allowed the region to dominate global production (van den Burg et al., 2021). Such selective breeding programs in North America, South America, and Europe are in early development stages (Umanzor et al., 2021), but are complicated by concerns of maintaining genetic structure in wild kelps, and avoiding introgression from farmed to wild populations (Valero et al., 2017; Evankow et al., 2019; Grebe et al., 2019). In an effort to break this bottleneck, the majority of research & development (R&D) efforts of large scale seaweed production in North America, South America, and Europe have included developing novel farming platforms and techniques (Bak et al., 2018; Bak et al., 2020) in parallel with effective nursery methods (Kerrison et al., 2018; Forbord et al., 2020).
Nurseries require a laboratory grade facility, a consistent supply of filtered and sometimes sterilized seawater, centralized pumps and plumbing, grow-lights, blowers for aeration, nutrients, and skilled labor (Edwards and Watson, 2015). Nurseries usually supply 1 - 2 mm diameter twine (made of natural or synthetic fibers) wrapped around PVC pipes (hereafter referred to as “spools”; Figure S1A) and seeded with juvenile sporophytes. Once mature, juvenile sporophytes are transferred to coastal grow-out ocean sites and the twine is wrapped around a larger grow-line (Figure S1B) (Flavin et al., 2013; Grebe et al., 2019; St-Gelais et al., 2022). Nursery production costs, and thus the price assumed by a farmer or vertically integrated business, can vary considerably. The few values reported in the literature suggest costs can range between $0.12 - $1.38 m-1 of seeded twine, and are dependent on production method, species, and geography (van den Burg et al., 2016; Camus and Buschmann, 2017; Camus et al., 2019). Small variations in price, when multiplied over potentially hundreds of thousands of meters of grow-line, can substantially impact a farmer’s bottom line. Furthermore, given that a small number of nurseries often support dozens of growers (McKinley Research Group, 2021), reducing production costs can have implications for the success of a regional industry. The recent expansion of the farmed seaweed sector in North America, Europe, and South America, coupled with substantial investment in kelp CDR, biofuel, food, and animal feed programs, determines that kelp seed production must cost-effectively increase to keep pace.
The three primary goals of this study were to: (1) quantify the impacts of scale on nursery production costs, (2) determine the most pressing bottlenecks limiting the expansion of the nursery industry in emerging farming regions, and (3) create an R&D roadmap to support the development of cost-effective nursery production methods. To ground assumptions in best practices relevant to the study regions, we conducted semi-structured interviews with nursery operators and an extensive literature review. These data were then used to develop a nursery techno-economic model (TEM). We explored the effects of scale, labor practices, energy requirements, and parameter variability on production costs. To demonstrate the utility of this framework, we then used the seaweed aquaculture industry in Maine, USA, as a case study of the ways in which future sectoral growth and process improvement may impact the cost structure of kelp nurseries. We address both near and short-term strategies to substantially reduce production costs and draw conclusions useful to seaweed aquaculture industry members, researchers, and policy makers.
Methods
Data Collection
The TEM was designed strictly following commercially established processes in North America and Europe (Forbord et al., 2012; Flavin et al., 2013; Redmond et al., 2014; Forbord, 2018; Alver, 2019). In an effort to constrain the design space, the facility was assumed to be located in Maine, USA, and exclusively produce 1 - 2 mm sugar kelp (S. latissima) sporophytes settled on twine-wrapped PVC spools. Maine was chosen as the study region given that at the time of writing, the state had the largest kelp aquaculture industry in the U.S. (Piconi et al., 2020). Sugar kelp, encompassing both S. latissima and S. angustissima, (hereafter kelp) was selected as the study species given that it comprises ~80% of the total annual U.S. harvest volume (FAO, 2020; ME DMR, 2021).
Data used to parameterize the model were sourced primarily from semi-structured interviews with seven industry professionals currently operating some of the largest kelp nurseries in North America and Europe. Participants were asked to describe their production process, the size of their facility, the layout and quantity of grow-tanks, energy and labor requirements, and the annual output (m of seeded twine) of their businesses. The interview script can be found in the Supplementary Material. To fill in information gaps and validate assumptions from semi-structured interviews, we conducted an extensive literature review and contacted equipment suppliers directly.
Production Scale
To investigate the effects of scale, we assumed that the baseline facility would produce enough seeded twine to supply the Maine seaweed aquaculture industry. Maine seaweed farmers harvested ~227,000 kg wet weight (WW) of various macroalgae species (mainly kelps) in 2020 (ME DMR, 2021). Based on a recent industry benchmarking study, farms typically yield 4.01 kg WW per m of grow-line (Engle et al., 2020). While this estimate is likely conservative, it is the most up to date industry wide value available. These figures suggest that Maine farmers deployed ~56,600 m of grow-line in the fall of 2019. A ratio of 1.8:1 of seeded twine to grow-line was then assumed based on an industry average (Engle et al., 2020). Therefore, the baseline nursery would need to annually produce 101,880 m of seeded twine. All components of the TEM were then designed to scale with the length of seeded twine required (m) as the base unit. Increases or decreases in the quantity of seeded twine produced resulted in parallel increases or decreases in the number of outplanted spools, tanks, grow-lights, etc.
Basis of the Nursery Techno-Economic Model
The basis of the nursery TEM assumed a 30-year design life, during which values (i.e., costs and volume of seeded twine) were aggregated annually. We primarily used cost of production (COP) to evaluate the performance of the TEM. COP is defined as the sum of all costs incurred by the nursery within a period of time divided by the quantity of seeded twine (m) produced during that same period of time. COP ($ m-1) was thus calculated as:
where n was the number of years used in the analysis (30), FC was fixed costs, OE was operating expenses, and M was the quantity (m) of twine produced. FC included interest, depreciation, insurance, and permits. OE included energy, labor, consumables, and maintenance.
FC were primarily driven by upfront construction and investment costs, and depreciation. We assumed a 50:50 split between owner debt and equity for all equipment, land, and facility investments. All equipment was depreciated using a straight-line schedule based on the useful lifespan of the item with no salvage value (Table 1). The remaining investment (50%) was financed using a 30-year term loan with a 5% interest rate and annual repayment schedule. Annual permitting, accounting, and legal fees were assumed to cost $7,228. We also assumed an additional one-time payment of $3,038 for construction permits, accounting, and legal fees.
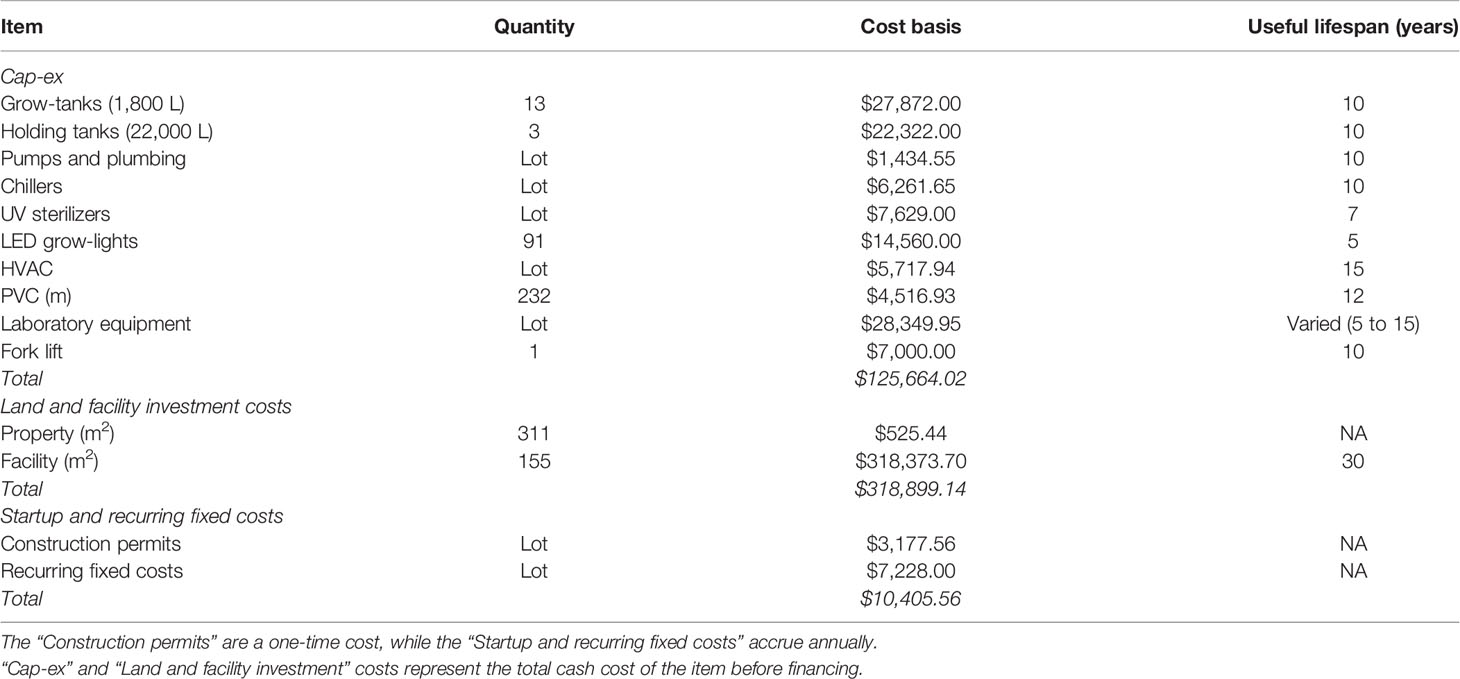
Table 1 Summary of fixed costs (FC) included in the baseline techno-economic model (101,880 m of twine produced annually).
OE consisted mainly of energy, labor, and consumables. Daily energy requirements (kWh day-1) were calculated based on the quantity and volume of tanks, chilling/pumping requirements, HVAC, grow-lights, UV sterilization, and laboratory equipment (Table 2). The average price for grid electricity in Maine of $0.16 kWh-1 was assumed (Maine Public Utilities Commission, 2021). Detailed energy calculations within the TEM are available in the Supplementary Material. Labor expenses were estimated (average, n=7) from semi-structured interviews. For every 44,148 m of seeded twine produced annually, the facility would require one full time employee (8 hr day-1; $25 hour-1). The facility also required a manager with a $60,000 annual salary prorated over the production period ($1,154 week-1). Seawater was delivered as needed via truck at a price of $0.013 L-1. Lastly, twine, nutrients, and disposable laboratory supplies were assumed to be consumable items replaced annually. The corresponding values are provided in Table 2.
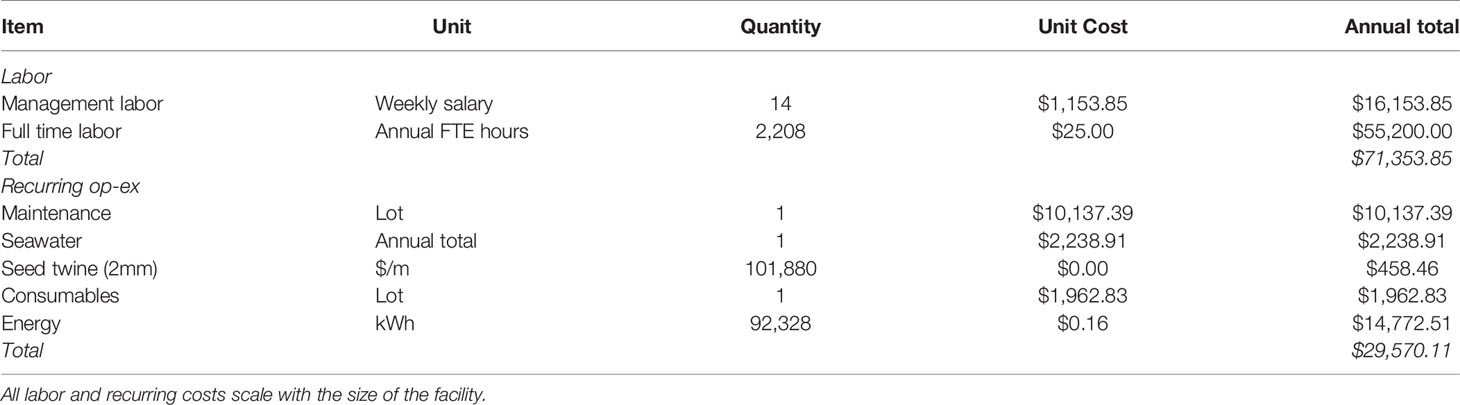
Table 2 Summary of operating expenses included in the baseline techno-economic model (101,880 m of twine produced annually).
Analyses
To quantify the effects of production scale on model performance, we first tracked the impacts of increasing the annual quantity of seeded twine (m) produced by the nursery on COP ($ m-1). Over the last 6 years (2014 - 2020) the total kelp harvest from Maine has increased by over 3,000% (ME DMR, 2021). While this growth is expected to slow, production is still predicted to expand by an order of magnitude over the next decade. A recent (2020) market analysis of the farmed seaweed industry in Maine projected a “high”, “low”, and “best estimate” for the 2035 harvest with values of 2,705,000, 698,000, and 1,388,000 kg WW, respectively. Using the same average yield (4.01 kg WW m-1) from the 2020 benchmarking analysis, and the same conversion from grow-line to seeded twine (1.8), these estimates indicate that the industry will require approximately 1,214,200, 313,300, and 623,000 m of seeded twine by 2035 according to the high, low, and best estimate market growth projections, respectively. Therefore, COP was calculated based on the requirements of the 2020 Maine industry (101,880 m), 2035 high (1,214,200 m), 2035 low (313,300 m), and 2035 best estimate (623,000 m) volume scenarios.
We then aggregated expenses for the 2020 baseline nursery (101,880 m of twine) by major line items to provide a categorical cost breakdown. A sensitivity analysis was then performed using six of the most important parameters within the baseline model: (1) duration of the sporophyte grow-out period (days), (2) labor requirements (m twine per FTE employee), (3) electricity costs ($ kWh-1), (4) interest rate (%), (5) product loss (% total-1), and (6) facility construction costs ($ m-2). The baseline values for each of the six parameters were increased and decreased in +/- 10% increments, to limits of +/- 40%, to obtain a COP range. Each parameter was changed individually so as to quantify its relative influence on model performance.
To account for parameter uncertainty and potential randomness, we ran a stochastic Monte Carlo analysis (Engle, 2010). Four key variables were assumed to be triangularly distributed and a minimum, maximum, and “most likely” (the assumption used within the baseline model) value for each parameter was selected based on variability within semi-structured interviews and the literature. The random number generator in Microsoft Excel was used to select a value within the probability distribution for each variable and calculate a corresponding COP. 1,000 iterations of this analysis were performed and the mean +/- standard deviation, maximum, and minimum COP were recorded.
To explore the effects of altering the physical components and design of the nursery facility on production costs, COP was calculated over a range of tank and PVC spool sizes (Gonzalez-Romero et al., 2014). Separate analyses were carried out for the effect of either PVC spool or tank size on production costs. To maintain the ratio of tank length to width, and PVC spool height to diameter, used in the baseline TEM, a scaling factor (% increase) was applied to the length and width of the grow-tanks (i.e., tank volume), or the height and diameter of PVC spools (i.e., capacity of spools). In increments of 10%, the scaling factor was increased from 0 - 100% of the baseline assumption and all other parameters were held constant. In an effort to accurately capture cost tradeoffs, we accounted for the increase in tank size, and thus water volume and pumping, required to house larger spools, and PVC materials costs. We performed this analysis separately for the 2020 baseline (101,880 m twine), 2035 high (1,214,200 m), 2035 low (313,300 m), and 2035 best estimate (623,000 m) scenarios.
Results
Semi-Structured Interview Results: Production Process and Facility Design
Semi-structured interview participants stated that the nursery process typically begins with the collection of fertile mature sporophytes in the late summer or early fall from wild kelp populations. The kelp is brought back to the facility, wiped clean, and treated with disinfectant. The reproductive sorus tissue located in the midsection of the blade is excised, wrapped in paper towels, and then left to desiccate in dark, cool (10°C) conditions. After 24h, the sorus tissue is rehydrated within beakers containing filtered and sterilized seawater to induce the release of microscopic zoospores (spores). Spore density is estimated using a hemocytometer and the solution is diluted to a concentration of 1,000 - 5,000 spores mL-1. The spore solution is then poured into tanks containing sterilized or filtered seawater, half strength Pavrasoli’s Enriched Solution (PES), and sterilized PVC spools wrapped with 2 mm twine. The tanks are left in dark conditions for 24 hours and the water is minimally aerated to allow spores to settle onto the twine.
After spore settlement, the tanks are drained and replenished with filtered seawater containing half strength PES. The tanks are then aerated and temperature controlled (10°C). Overhead LED lights are programmed on a 12:12 light:dark schedule for the remainder of the grow-out process. The pH within tanks is managed using hospital grade CO2 as needed. Approximately two weeks after settlement, juvenile spores enter the reproductive gametophyte stage, cross-fertilize, and grow into microscopic sporophytes. Germanium dioxide (GeO2) is added during the first two weeks of the culture cycle to prevent diatom growth (Shea and Chopin, 2007). The spools leave the nursery and are transported to an open ocean site approximately 46 days after spore settlement, when sporophytes are 1 - 2 mm in length.
The facility was assumed to be built on undeveloped land ~40 km from the coast. Property prices were sourced from 10 listings, and an average price of $1.69 m-2 was used. The facility was assumed to be 155.5 m2, with a construction price of $2,048 m-2, which included HVAC and lighting (RSMeans, 2013). At this size, there would be ample room for a 22,000 L seawater settling tank affixed to the exterior of the building, a 22,000 L insulated and chilled holding tank within the building, 7 pairs of 1,800 L (2.5 x 1.2 x 0.6 m) grow-tanks (13 total), pumps, grow-tank chillers, laboratory space, and a wastewater tank buried outside the facility. As a means of creating redundancy for biosecurity purposes, each pair of tanks was equipped with its own pump, chiller, UV sterilization system, and 75W LED grow-lights. The PVC spools were 0.07 m (~3”) in diameter and 0.6 m (~24”) in length, with a total capacity of 132 m of twine per spool. Due to contamination or poor growth, 5% of spools would be unusable each year.
Fresh seawater was collected weekly from the coast, trucked to the facility, and transferred into the outdoor settling tank. Before entering the settling tank, the water was manually filtered down to 100 μm. As water flowed into the indoor insulated and chilled holding tank, it was UV sterilized and pumped through a progressively finer set of mechanical filters, ranging from 100 to 2 μm. As seawater was pumped from the holding tank into the grow-tanks, it was ultimately filtered down to 0.2 μm. The facility was equipped with a central pump and plumbing system to supply the grow-tanks. The grow-tanks were replenished with new seawater weekly and the water within tanks was maintained at 10°C. Wastewater was pumped into the “discard” tank buried outside the facility, treated with disinfectant, and then emptied. Treated wastewater can either be discharged back to sea or to a municipal wastewater facility. There are likely costs or fees associated with permitting or discharge rates for either method. These costs are not accounted for in the model.
Model Analysis
The baseline nursery (supplying the entire 2020 Maine kelp industry) produced seeded twine at a price point of $1.39 m-1, or $173.9 spool-1, in line with the prices that kelp farmers can expect to pay for sugar kelp twine in the Gulf of Maine: $1.80 - $1.98 m-1 (Piconi et al., 2020). Out of the three projected growth scenarios for the 2035 Maine kelp industry, COP was lowest, $0.86 m-1, for the nursery supplying the “2035 high growth scenario” industry with ~1,214 km of seeded twine annually. COP declined as production scale increased across the range of facility sizes, a product of economies of scale (Figure 2). However, the cost curve leveled off between the second largest and largest nurseries, indicating that there are limits to the benefits of increased scale at the upper end of the range used in this analysis. Labor made up the majority of costs within the baseline model, at $0.74 m-1 of twine, followed by energy, operating expenses, and interest each at $0.15 m-1 (Figure 3). A breakdown of energy expenditures shows that seawater chilling and sterilizing made up the largest portion at just over $0.04 m-1.
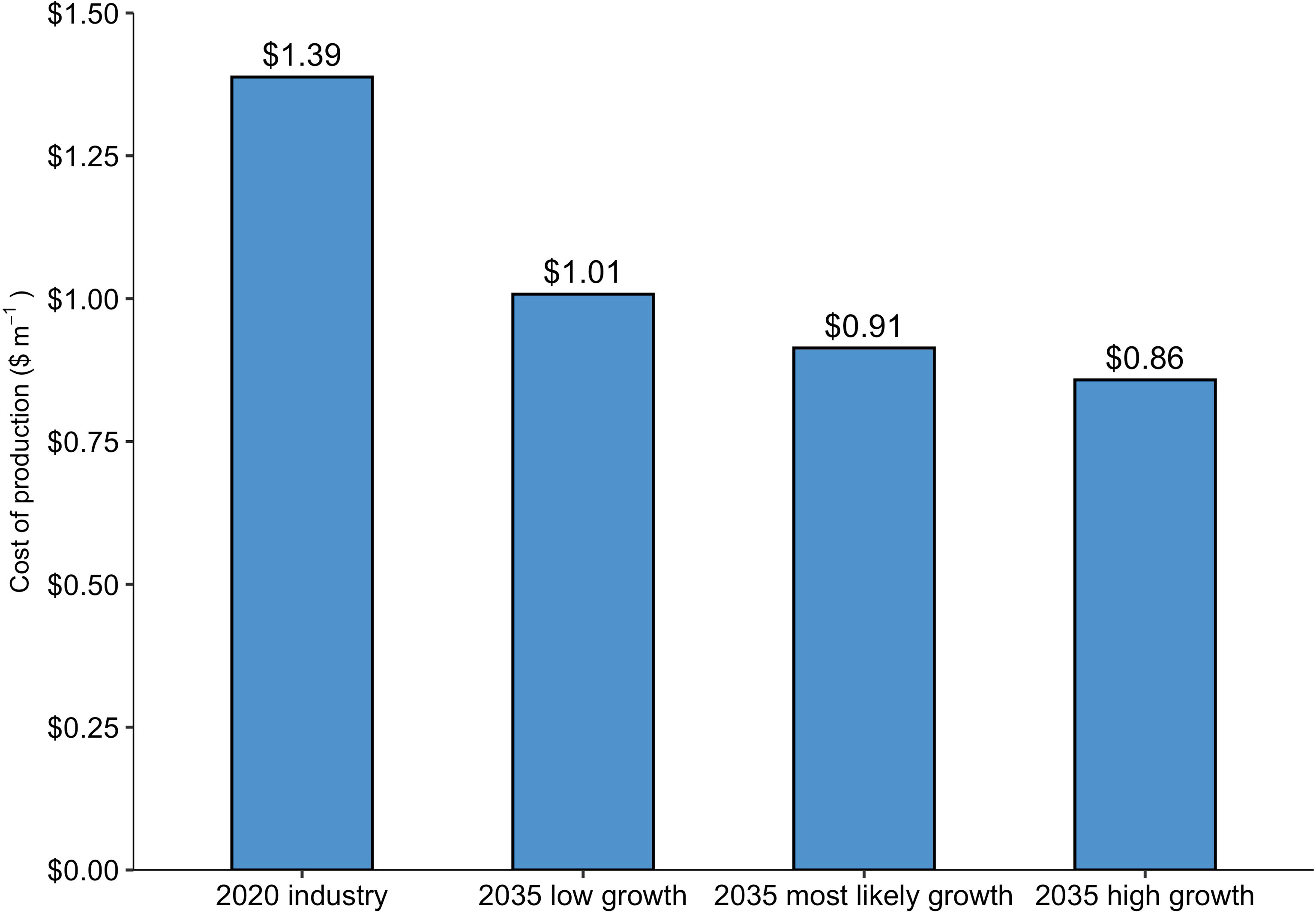
Figure 2 Production costs ($ m twine-1; COP) as a function of production scale (m of twine). The “2020 industry” represents a quantity of 101,880 m of twine produced. Based on the projected growth of the Maine kelp industry, the “2035 low growth”, “2035 most likely growth”, and the “2035 high growth” scenarios correspond to quantities of 313,300, 623,000, and 1,214,200 m of twine, respectively.
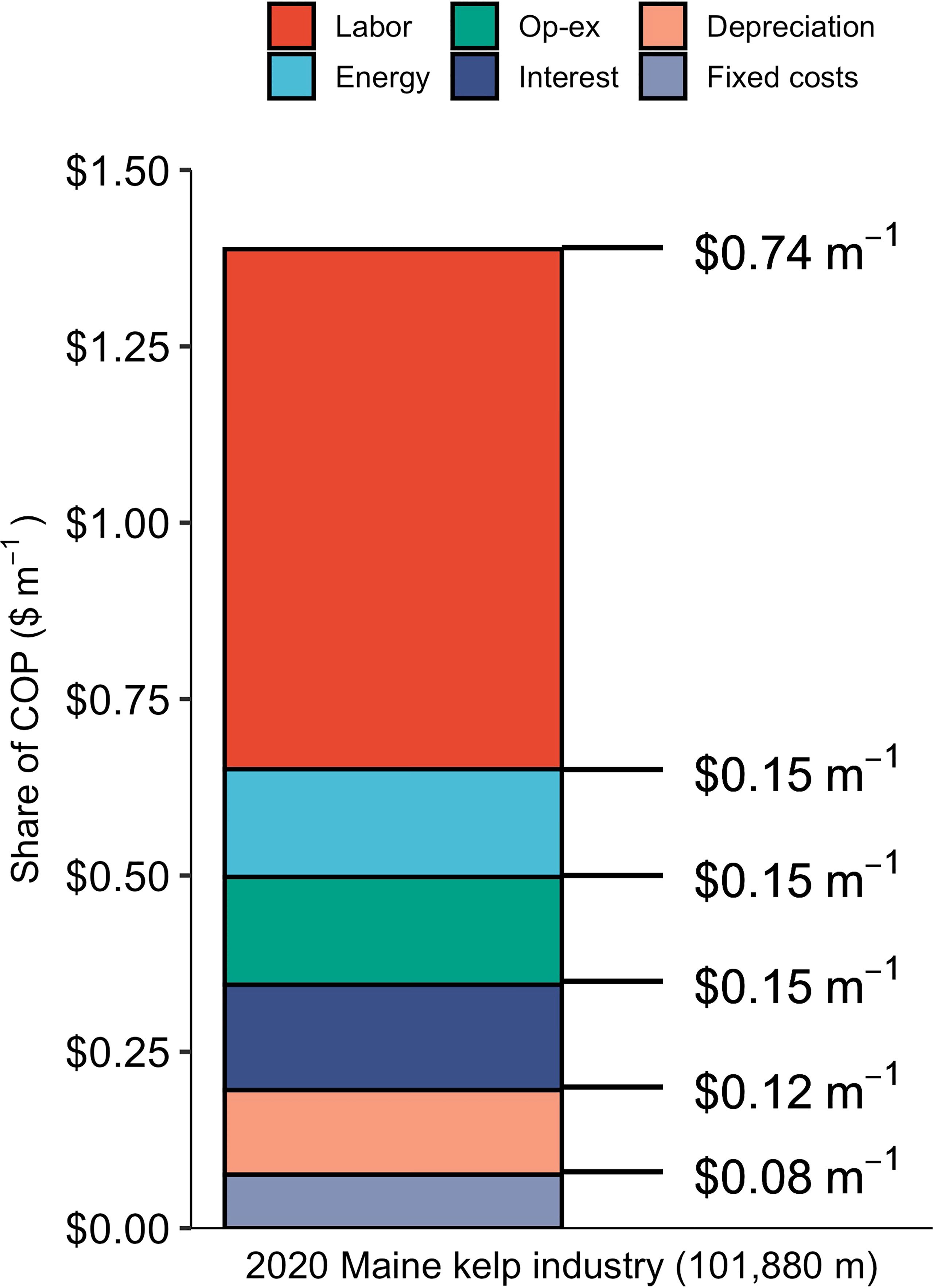
Figure 3 Breakdown of costs ($ m-1) by major line items over a 30 year period for the baseline nursery producing 101,880 m of seeded twine, annually.
The results of the sensitivity analysis were overwhelmingly driven by the number of days required for settled spores to grow into juvenile sporophytes ready for outplanting. A 40% reduction in grow-out (29 vs 44 days) reduced COP from $1.39 to $1.08 m-1, a 22% decline (Figure 4). Labor requirements were the second most important component of production costs (Figure 3). Increases or decreases in labor capacity resulted in a stepwise function, as the number of FTE employees required within the facility was rounded up to the nearest whole number based on production scale (1 FTE per 44,148 m of twine) within the TEM. Nonetheless, increasing the capacity of a single FTE employee to annually produce 65 km of twine, up from ~44 km, decreased production costs from $1.39 to $1.20 m-1 (Figure 4).
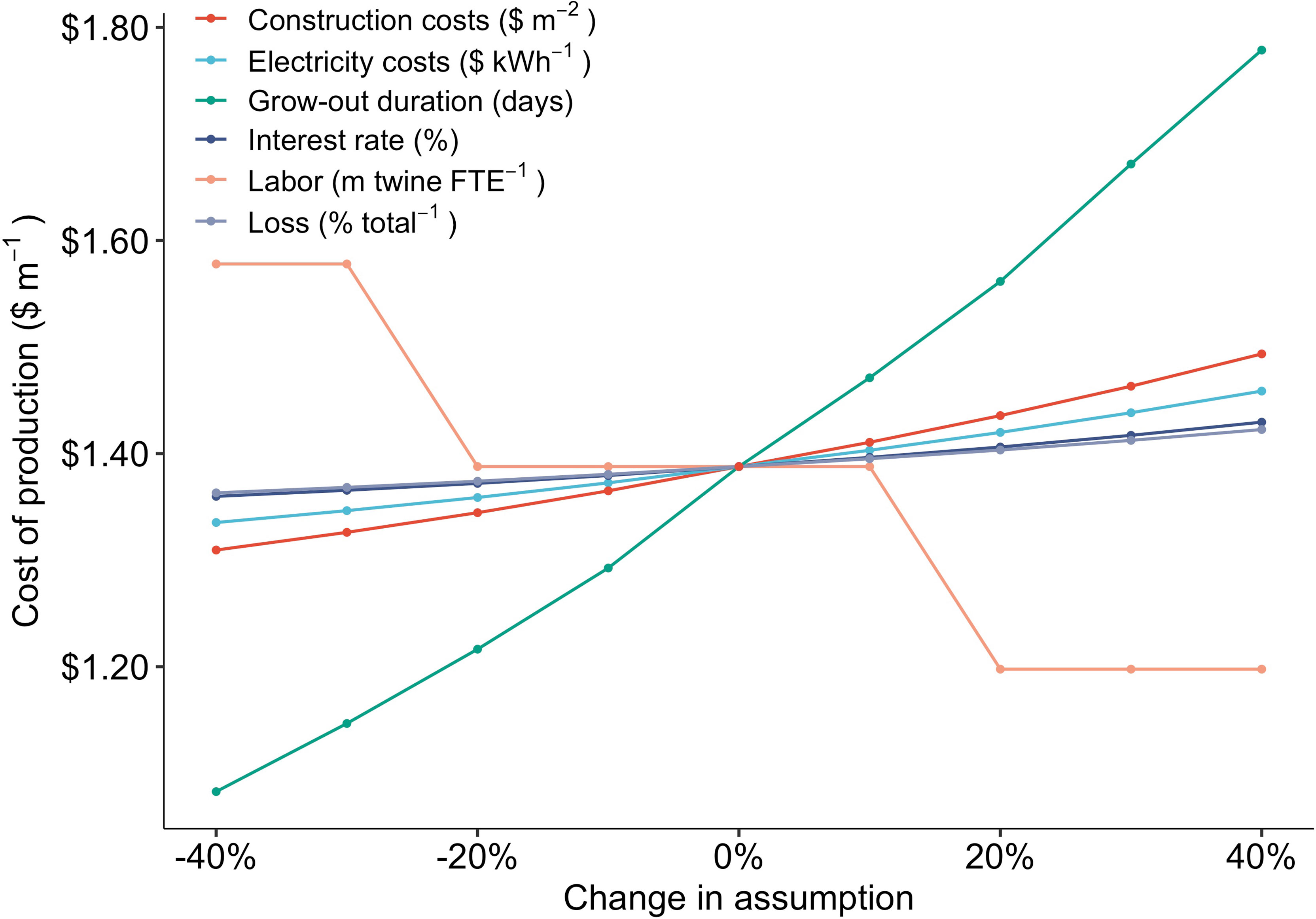
Figure 4 Change in production costs ($ m-1) as a result of proportional (%) changes in six key model assumptions: construction costs ($ m-2), electricity costs ($ kWh-1), sporophyte grow out duration (days), interest rate on loans (%), the facility labor requirements (m twine per FTE employee), and the annual twine loss (% total-1).
During semi-structured interviews and literature reviews, we identified a substantial range for four assumptions used in the Monte Carlo analysis: (1) the number of days required for sporophyte grow-out, (2) km of seeded twine produced annually per FTE employee, (3) energy costs in the state of Maine ($ kWh-1), and (4) facility construction costs ($ m-2). Over 1,000 iterations of the simulation, COP was distributed about a mean of $1.50 +/- $0.23 m-1 with a tail that extended towards $2.40 m-1 (Figure 5). Across all values, COP ranged from $1.00 - $2.37, representing the “best” and “worst case” scenarios, respectively (Table 3).
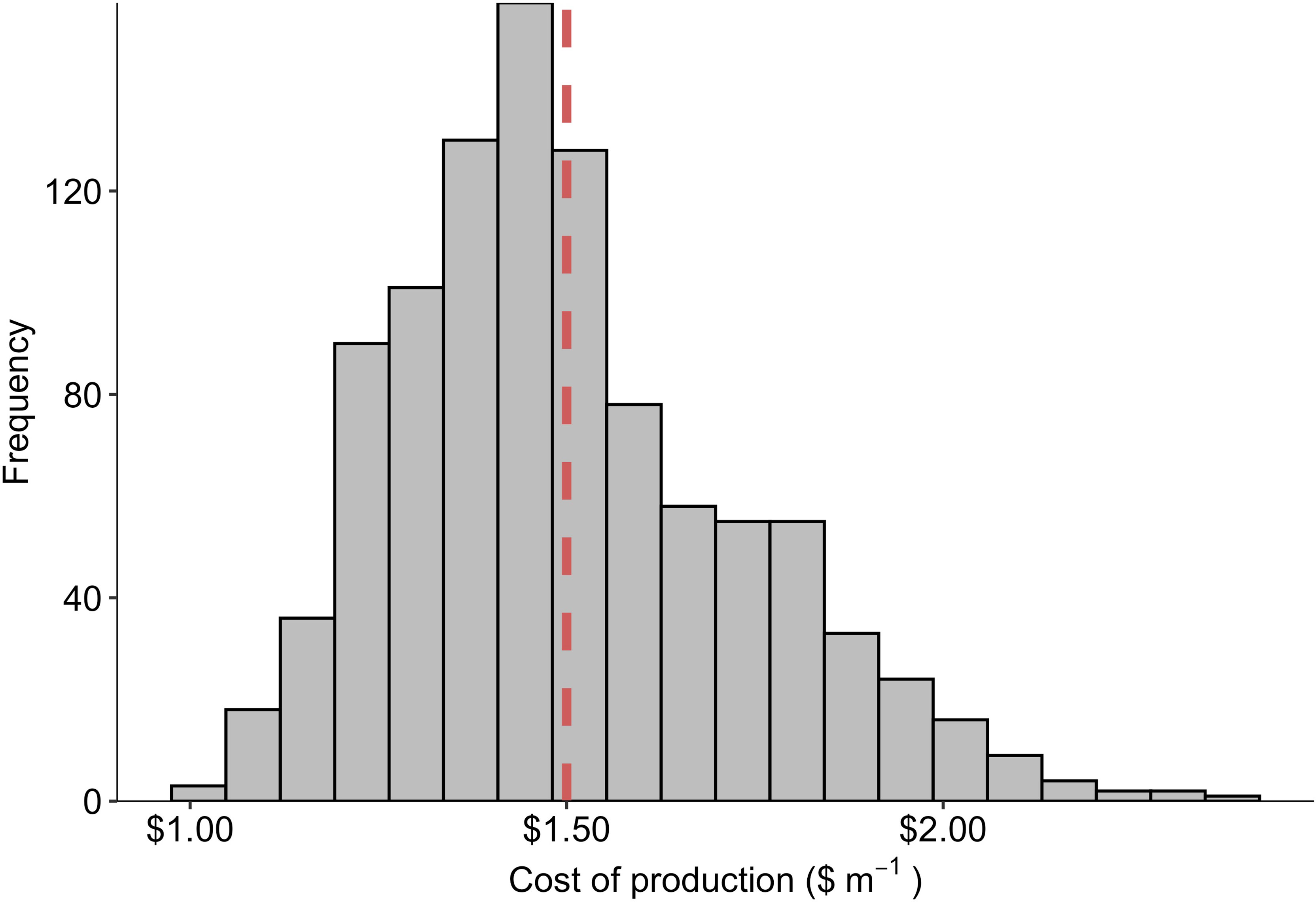
Figure 5 Frequency histogram of production costs ($ m-1) derived from 1,000 iterations of a Monte Carlo simulation in which the grow-out duration (days), labor requirements (m of twine per FTE employee), energy costs ($ kWh-1), and facility construction costs ($ m-2) were simultaneously modeled as potentially random variables with triangular probability distributions. The dashed vertical line depicts the average (n = 1,000) cost of production value over all simulations: $1.50 m-1.
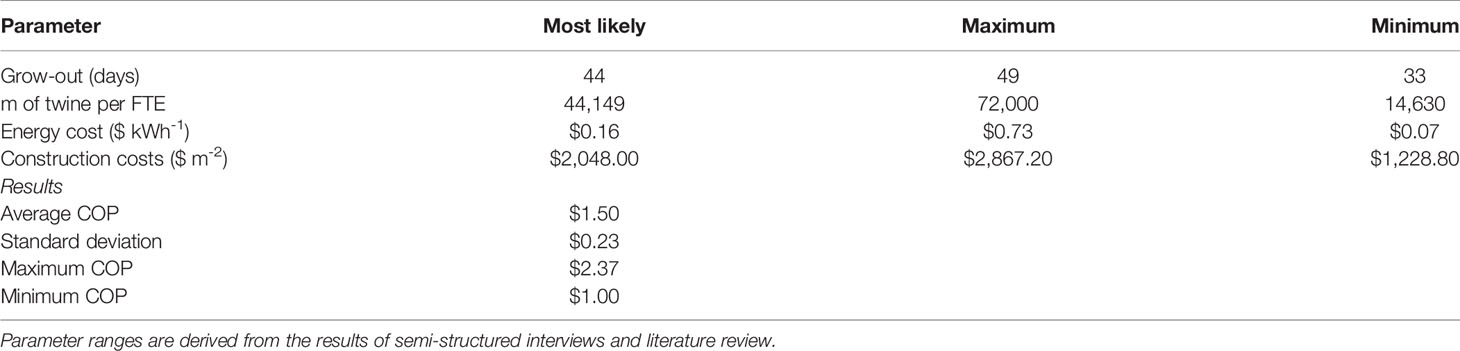
Table 3 Results of a Monte Carlo analysis (1,000 iterations) in which the grow-out duration (days), labor requirements (m of twine per FTE employee), energy costs ($ kWh-1), and facility construction costs ($ m-2) were all modeled as triangularly distributed random variables.
Increasing the PVC spool capacity (m of twine per spool) had a stronger impact on production costs compared to altering the size of the grow-tanks. The effect was most pronounced for the “2035 high growth scenario” nursery in which a 100% increase in the size of the PVC spools resulted in a 25% decrease in COP (Figure 6). Increasing the size of the PVC spools reduced COP within the three other nursery scenarios, but the impact was less significant. Increasing the size of the grow-tanks resulted in a less consistent reduction in COP. For the baseline nursery, a 100% increase in tank volume had no impact on COP. Between a 0 - 60% increase in tank size, COP declined for the baseline nursery. However, between tank size increases of 70 - 100%, COP increased to $1.39 m-1 (Figure 6). In the other three scaling scenarios, a 100% increase in the size of the tanks reduced COP by 5 - 8% (Figure 6).
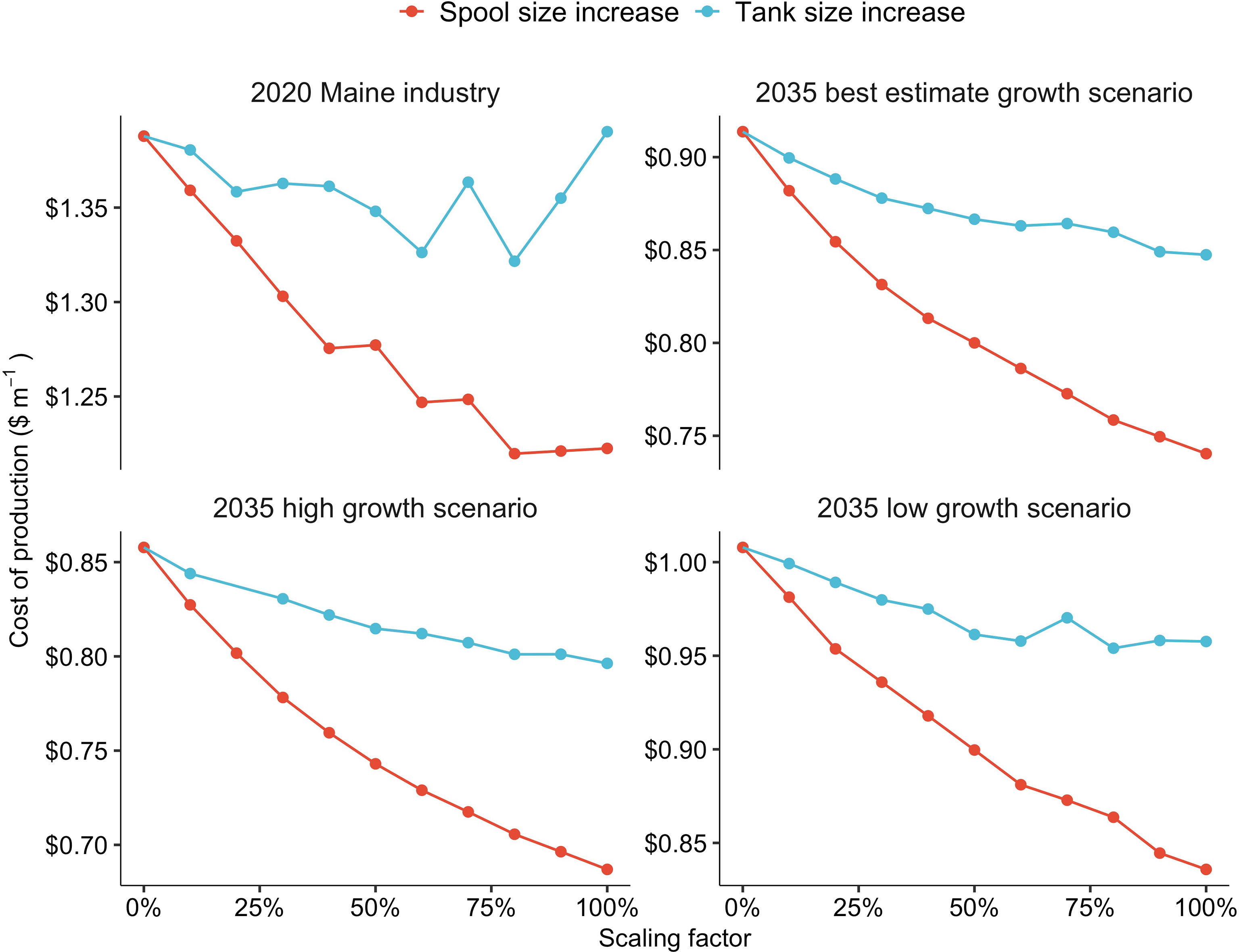
Figure 6 The effects of increases in either spool (red) or tank (blue) size on production costs ($ m-1) within a kelp nursery producing 101,880 m (2020 Maine industry), 623,000 m (2035 best estimate growth scenario), 1,214,200 m (2035 high growth scenario), or 313,300 m (2035 low growth scenario) of seeded twine, annually. The scaling factor represents a % increase in both the diameter and height of the PVC spools, as well as a % increase in both the length and width of the grow-tanks.
An optimization analysis was then conducted in an effort to synthesize the cumulative effects of process improvement, materials cost reductions, increased energy efficiency, and scaling on production costs within the baseline nursery. For each of seven key parameters for which an observed range was identified through interviews or literature reviews, the assumption was changed to either the maximum or minimum value that decreased COP. After each parameter change, the decrease in COP was recorded. Lastly, an “optimized” COP was calculated by summing the changes. The baseline assumptions for grow-out duration, labor capacity, energy costs, spool size, facility costs, product loss, and annual production scale were altered (Table 4). Increasing the scale of the facility resulted in the largest decrease in COP (-$0.36), followed by a reduction in the grow-out duration (-$0.23) and an increase in spool size (-$0.13) (Figure 7). Combining all potential improvements resulted in a 75% reduction in COP ($0.35 vs. $1.39 m-1; Figure 7 and Table 4).
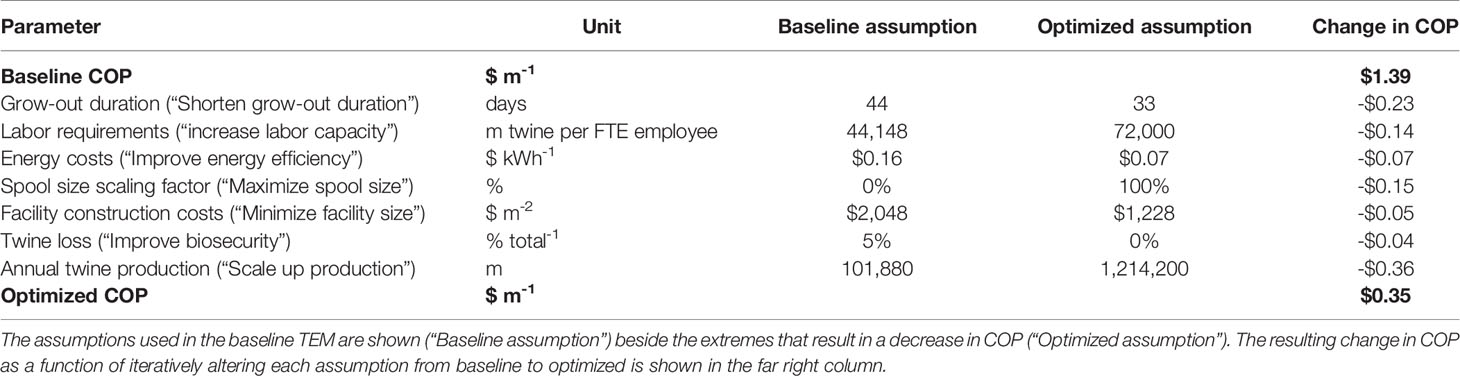
Table 4 Values used in the optimization analysis with ranges derived from semi-structured interviews and literature review.
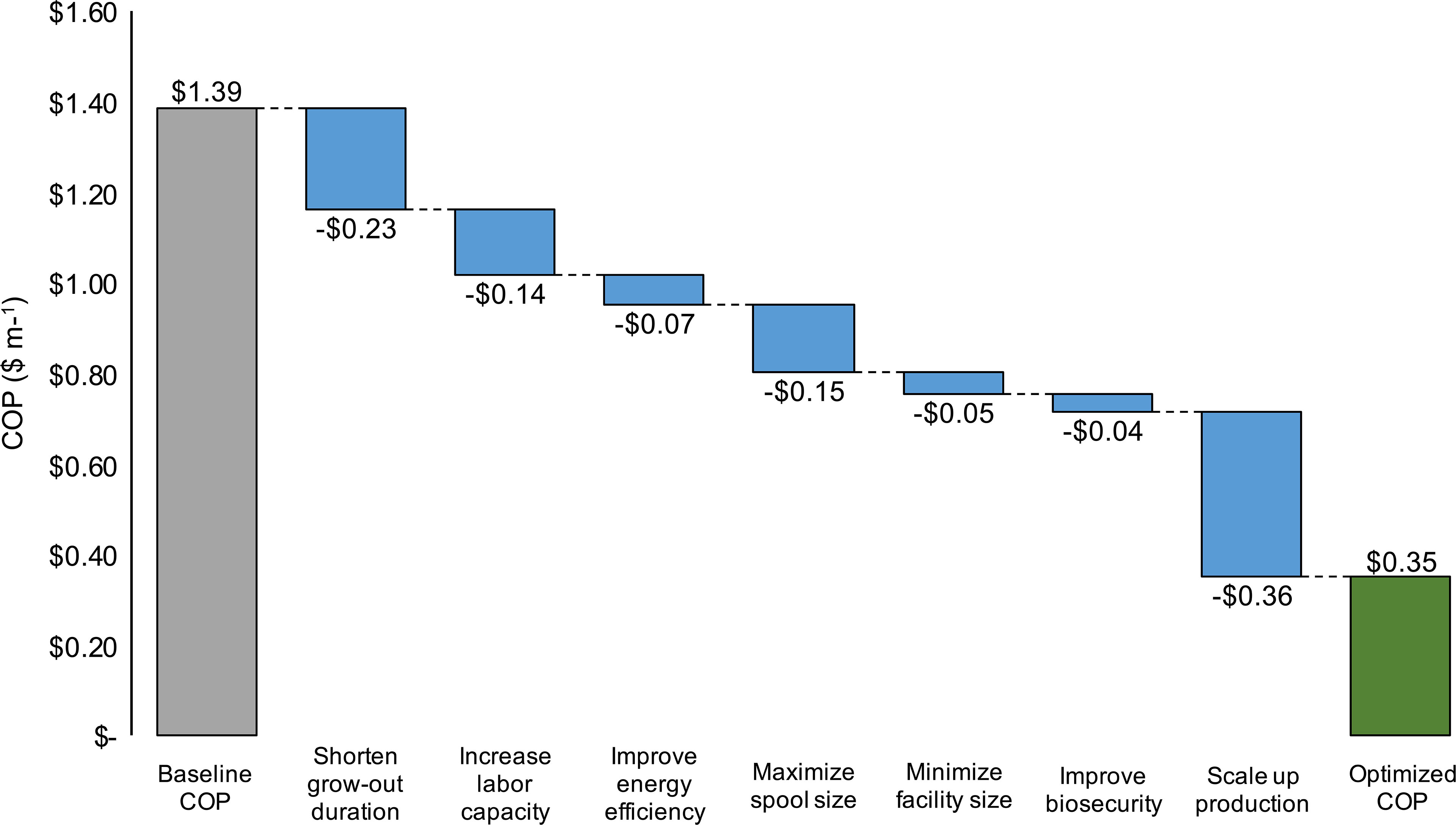
Figure 7 Hypothetical decreases in baseline production costs ($ m-1; COP) as a result of a shortened grow-out duration (days), increase in labor capacity (m of twine per FTE employee), reduction in grid electricity costs ($ kWh-1), 100% increase in spool size, reduction in facility construction costs ($ m-2), reduction in product loss (% total-1), and increase in scale (>1,200 km of twine). The “Optimized COP” value depicts the sum of all process improvements.
Discussion
Given recent commercial interest in expanding kelp aquaculture in North America, Europe, and South America (European Commission, 2012; Buschmann et al., 2014; ARPA-E, 2017; NASEM, 2021), nursery production will need to significantly increase in parallel with open-ocean cultivation to meet raw materials needs. Using the expanding farmed kelp industry in the Gulf of Maine as a case study on potential barriers to future growth, we identified significant economies of scale, strong influences of the duration of sporophyte grow-out on production costs, a linear relationship between nursery size and labor requirements, and numerous avenues for potential process improvements. Based on these results, we propose a potential R&D roadmap to substantially reduce both nursery costs and energy usage (Figure 7).
The number of days that spools are held within grow-tanks was one of the primary determinants of nursery production costs in the TEM. Shifting from the average (n = 7) value obtained through interviews (44 days) to the minimum (33 days) reduced COP by $0.25 m-1, an 18% decrease from the baseline (Figure 7). Increasing sporophyte growth rates on twine wrapped spools will require optimization of light intensity, flow-rates, nutrient media, and temperature (Rößner et al., 2014; Chu et al., 2019). While these sensitivities were not captured in the TEM, reducing the duration of grow-out does represent one of the most critical research priorities to reduce costs. Camus and Buschmann (2017) investigated a combination of culture parameters and observed a 15 day reduction (60 to 45 days) for juvenile M. pyrifera grow-out lengths, demonstrating that further improvement may be possible through optimization (Camus and Buschmann, 2017). However, producers may be able to achieve more substantial reductions in the nursery timeline, and thus costs, by moving away from holding kelps on twine wrapped PVC spools within tanks over the entire kelp lifecycle. Specifically, culture of free-floating sporophytes or inoculating spools with fertile gametophytes may bring down costs based on space and grow-out length requirements (Kerrison et al., 2018; Greene et al., 2020). However, caution must be taken when evaluating the potential cost-benefit of these approaches as, despite the fact that protocols have existed for some time (Westermeier et al., 2006), they have not been demonstrated as commercially viable means of production (Alver et al., 2019).
Development of effective gametophyte or free-floating sporophyte culture protocols could have positive knock-on effects beyond reducing materials and investment costs within nurseries. These methods could also alleviate downstream operational costs for farmers. However, field trials have yielded varied success with respect to growth and holdfast retention at open-ocean sites (Kerrison et al., 2018; Forbord et al., 2020; Boderskov et al., 2021) and thus direct seeding of sporophytes and gametophytes have not been widely adopted (Alver, 2019). Given the importance of reducing the sporophyte grow-out length, however, our analysis calls for comparing the cost-benefit of potentially reduced yields in the field vs. a shortened (and thus potentially less expensive) nursery period and any associated on-farm benefits as a result of gametophyte or direct seeding sporophyte culture. While Forbord et al. (2020) observed that gametophytes settled on twine produced ~50% lower yields compared to spores, the authors noticed little difference in yield between gametophyte seeded spools held in the nursery for 21 vs. 14 days (Forbord et al., 2020). Based on this optimistic 14 day timeline, three full grow-out cycles could be completed within the same time frame used in our baseline analysis. If the grow-out duration is reduced to 14 days within the TEM, COP falls from $1.39 to $0.79 m-1. The on-farm labor associated with twine seeding makes up a large portion of operational costs (Hasselström et al., 2020), and moving away from twine with direct seeding of grow-lines at sea may have additional benefits. A holistic TEM that incorporates accurate nursery costs for the alternative methods discussed above, as well as associated farming expenses and biomass yield, would be a powerful decision making tool.
Successful gametophyte culture also unlocks the potential for selective breeding, a critical element of increased on-farm yields as well as consistent settlement and growth within nurseries. Selective breeding programs have allowed seaweed sectors in Asia to rapidly increase yields and expand production (FAO, 2020; Goecke et al., 2020). This work is ongoing in emerging farming regions (Augyte et al., 2020; Wade et al., 2020; Umanzor et al., 2021), but remains in developmental stages. The economic importance of leveraging kelp breeding technologies, as evidenced by TEM outputs, underscores the need to accurately map distinct wild kelp populations (Mao et al., 2020) to prevent potential genetic contamination from monocultures (Campbell et al., 2019; Grebe et al., 2019; Visch et al., 2020). Policy measures must not only support the responsible rollout of these breeding programs, but also remain conducive to progress. For example, the state of Alaska currently requires nursery operators to source 50 parental blades at the start of each production season (ADFG, 2020), eliminating the possibility of maintaining stocks of optimized gametophyte cultures to be used year over year. Regulations such as Alaska’s are necessary to protect wild kelp population structure while the science progresses to a point to allow for legislation to facilitate safe breeding programs. An important area of research to this end would be development of sterile strains to eliminate chances for farmed-to-wild gene flow. This is a topic of active interest (Loureiro et al., 2015; Grebe et al., 2019).
Labor had the second most influence on COP within the TEM, making up nearly half the cost required to produce each meter of seeded twine. A 40% increase in labor capacity resulted in a 14% reduction in costs (Figures 3 and 4). Semi-structured interview participants discussed that collecting broodstock, wrapping PVC spools in twine, rotating spools, monitoring water quality, and cleaning equipment were some of the most labor intensive tasks. The difference between the annual cost of labor vs. depreciation within the baseline model ($71,353 vs. $11,605 year-1, respectively; Tables 1 and 2) suggests that there is significant room for increased automation despite the associated increase in cap-ex. As nurseries increase in scale, developing automated water quality monitoring systems, spooling machines, and PVC rotating devices should be a concerted effort on the part of both researchers and industry alike. Transitioning to gametophyte or free-floating sporophyte culture could also potentially alleviate labor requirements within facilities, a function of reduced grow-out periods, tank space, and equipment needs (Kerrison et al., 2018). Transitioning to gametophyte culture (and culture of selected strains) would also allow the nursery sector to shift from reliance on collection of wild sorus tissue, which has been identified as an area of risk to the industry and also an impediment to increased sustainability (Grebe et al., 2019). It should be noted that doing so would require some level of year-round nursery operations as gametophyte cultures would be required to be maintained at all times. Thus, this transition (not accounted for in this model) may actually increase labor costs to an undetermined extent and these tradeoffs should be included within future assessments.
Energy costs contributed ~11% to the cost structure of the baseline nursery. Reducing energy costs (a proxy for energy efficiency) to the minimum price in the state of Maine ($0.07 kWh-1) led to a $0.07 reduction in COP within the TEM (Figure 7). This highlights the need to both develop energy efficient systems to reduce expenses, and source electricity from renewables to limit GHG emissions. In addition to identifying locations with low consumer power prices, the TEM results also point towards refining the operations of larger, flow-through systems. Interview participants described that smaller tanks coupled with weekly water drawdowns and sterilizations were necessary for biosecurity purposes and reducing product loss. However, at the largest scale (~1,200 km of twine) tested in our analysis, the facility would require nearly 68 pairs of 1,800 L tanks each equipped with a 1/10 hp chiller, submersible pump, UV sterilizer, and LED grow-lights. Su et al. (2017) describe the nursery protocols within an S. japonica facility located in northern China. In this facility, racks of twine are cultured within 6,500 L (10 × 1.3 × 0.5 m) flow-through tanks supplied with ambient light through a greenhouse roof (Su et al., 2017). While the example from Su et al. (2017) represents a different model of energy efficiency and biosecurity, the current protocols used in many nurseries outside of the Pacific Rim may pose a potential energy bottleneck as facilities increase scale. Similarly, if seaweed aquaculture is to play a role in climate mitigation through CDR, reducing nursery GHG emissions will be critical to minimize the overall C output and maximize available credits (Froehlich et al., 2019). The “2035 high growth” scenario nursery consumed 436,028 kWh of electricity per year, equivalent to 168 tCO2eq. Improving energy efficiency with biosecure flow-through systems would have the combined benefits of reduced electricity costs, GHG emissions, and product loss. However, pursuing flowthrough systems would require the facility to utilize coastal real estate, which may impact property value and tax liability. A blended approach between Su et al. (2017) and the model used in this TEM would likely be optimal.
Spool size had a clear impact on costs within the TEM, and increasing the twine capacity of the PVC pipes led to a reduction in costs within all scenarios. A 100% increase in the size of the spools within the “2035 high growth” scenario nursery resulted in a 50% decrease in both the number of grow-tanks and the size of the facility needed to supply the same quantity of seeded twine (1,214 km) annually. It must be noted, however, that there are likely unforeseen tradeoffs between increasing spool size and production costs not captured within our TEM. An increase in the height or diameter of the PVC might lead to increased shading within tanks, prolonging grow-out or increasing light requirements. Similarly, the relationship between aeration and tank volume is likely nonlinear, and would require more research to optimize. Lastly, larger spools may prove more difficult to handle, further increasing labor requirements. In an analysis of potentially optimized offshore kelp production, Greene et al. (2020) examined the use of 1 m diameter x 1 m tall PVC spools. While the Greene et al. (2020) value represents a hypothetical extreme, the results of our analysis determine that nursery operators should work closely with farmers to maximize spool size without sacrificing handleability on the water or ease of transportation. Multiple interview participants mentioned that this was an immediate priority.
Increasing the scale of the facility from 101 to 1,214 km of twine produced annually, after prescribing the above mentioned process improvements (Table 4), resulted in a $0.36 reduction in COP. If nurseries are able to increase production volume, per unit costs will likely come down even without process alterations (Figure 2). However, limits to the benefits of increased scale were observed at the end of the tested range, and underscore the importance of parallel process improvements. We observed a 27% decrease in COP between the baseline and “2035 low growth” scenarios, but only a 6% decrease in costs between the “2035 most likely” and “2035 high growth” scenarios. Linearly increasing labor expenses, energy usage, op-ex, and investment costs across this range point towards the need to make changes to the nursery process to facilitate scaling. Combining all improvements outlined in Figure 7 resulted in a 75% reduction in costs per m of twine produced. Increasing labor capacity through automation or reducing the time spools are held in tanks through gametophyte culture would not only help new facilities, but also increase the capacity of existing operations to produce more seed with established infrastructure and personnel. Similarly, these alterations can potentially reduce energy usage and bolster the ability of farmed kelps to contribute to low GHG supply chains. The baseline nursery emitted 0.35 kg CO2eq for every m of twine produced. After making the process improvements within the optimization analysis (Table 4), this value fell to 0.06 kg CO2eq per m of twine produced, an 83% improvement in energy efficiency. While there are likely unaccounted for energy tradeoffs within the TEM, our analysis demonstrates that the incentives to reduce costs as nurseries scale up production are aligned with the necessary changes to reduce energy usage.
Despite providing insight into potential nursery improvements, the TEM has some obvious limitations. Given the geographic distance between interview participants (i.e., Norway and Alaska) generalizing across all facilities is difficult. Site specific differences will lead to variation in production costs if the TEM were to be applied to different regions. For example, Camus et al. (2019) reported that twine for a hypothetically optimized M. pyrifera farm in Chile would cost a grower 0.12 m-1, and only make up 14% of annual operating expenses (Camus et al., 2019). Conversely, in an analysis of large-scale S. latissima production in the North Sea, van den Burg et al. (2016) assumed a twine cost of 1.38 m-1, making up 38% of annualized expenses (van den Burg et al., 2016). Sensitivity and Monte Carlo analyses aid in uncovering sources of uncertainty, but caution must be taken when drawing conclusions that may be impacted by site specific factors. Furthermore, the model does not account for materials cost reductions or “learning rates” (i.e., the fractional reduction in costs with each doubling of capacity) with both scale and time (Rubin et al., 2015). The addition of equipment scaling factors can lead to more accurate estimates of investment costs as production volume increases (van Dijk and van der Schoot, 2015). Similarly, over a period of 30 years (the TEM design life) there will be inevitable process improvements that come from “learning by doing” (Kavlak et al., 2018). While these types of factors are difficult to estimate, they will almost certainly play a key role in the development of nursery protocols as the kelp aquaculture industry expands.
Conclusion
If the seaweed aquaculture sector is to continue to grow, nursery production will need to significantly expand in parallel with open-ocean farming. Using a techno-economic modeling (TEM) approach, we identified both near and long-term challenges to cost-effectively increasing seeded twine output within kelp nurseries. Based on our analysis, four key research priorities emerged: (1) reducing the period of time that spools are held within tanks (potentially through expansion of gametophyte culture), (2) increasing automation to increase labor capacity, (3) de-risking biosecure, flow-through systems to reduce both energy usage and product loss, and (4) optimizing tank and spool size in collaboration with farmers to minimize facility size. Developing effective nursery protocols can have positive impacts beyond the production of affordable “seed” for farmers. Selective breeding programs that leverage optimized gametophyte cultures could potentially reduce not only facility, materials, and energy costs for nursery operators (three of the most important parameters within our TEM), but also improve yields for farmers. However, R&D and policy must work to optimize these experimental methods and support their continued sustainable expansion. Lastly, nursery models, such as the TEM developed here, must ultimately be linked with ocean grow-out models to evaluate the cost-benefit of future best practices, and potential unforeseen cost tradeoffs.
Data Availability Statement
The raw data supporting the conclusions of this article will be made available by the authors, without undue reservation.
Author Contributions
All authors contributed to the conceptualization of the work. SC and AS developed the semi-structured interview script and outreach plan. SC conducted semi-structured interviews and model analyses with guidance from all co-authors. SC wrote the initial draft of the manuscript. AS, DB, DF, and TD provided manuscript edits and comments on model analyses. SC led figure and table production. All authors contributed to the article and approved the submitted version.
Funding
This study received funding from Conscience Bay Research, LLC. The funder was not involved in the study design, collection, analysis, interpretation of data, the writing of this article or the decision to submit it for publication. All authors declare no other competing interests.
Conflict of Interest
TD is employed by Kelson Marine, LLC.
The remaining authors declare that the research was conducted in the absence of any commercial or financial relationships that could be construed as a potential conflict of interest.
Publisher’s Note
All claims expressed in this article are solely those of the authors and do not necessarily represent those of their affiliated organizations, or those of the publisher, the editors and the reviewers. Any product that may be evaluated in this article, or claim that may be made by its manufacturer, is not guaranteed or endorsed by the publisher.
Acknowledgments
We would like to acknowledge the nursery producers who kindly provided expertise and their time to make this research possible.
Supplementary Material
The Supplementary Material for this article can be found online at: https://www.frontiersin.org/articles/10.3389/fmars.2022.894461/full#supplementary-material
References
ADFG. (2020). Applying for Aquatic Stock Acquisition and Transport Permit (Juneau, AK: Alaska Department of Fish and Game). Available at: https://www.adfg.alaska.gov/index.cfm?adfg=aquaticfarming.acquistions.
Alemañ A. E., Robledo D., Hayashi L. (2019). Development of Seaweed Cultivation in Latin America: Current Trends and Future Prospects. Phycologia 58 (5), 462–471. doi: 10.1080/00318884.2019.1640996
Alver M. (2019). D5.1 Industrial Production Line for Seedlings (Trondheim, Norway: SINTEF). Available at: https://sintef.brage.unit.no/sintef-xmlui/bitstream/handle/11250/2582466/302002488-00006%2BD5.1%2BIndustrial%2Bproduction%2Bline%2Bfor%2Bseedlings.pdf?sequence=1&isAllowed=y.
ARPA-E (2017). Macroalgae Research Inspiring Novel Energy Resources (MARINER) Program Overview (Washington DC: Department of Energy). Available at: https://arpa-e.energy.gov/sites/default/files/documents/files/MARINER_ProgramOverview_FINAL.pdf.
Augyte S., Kim J. K., Yarish C. (2021). Seaweed Aquaculture From Historic Trends to Current Innovation. J. World Aquacul. Soc. 52 (5), 1004–1008. doi: 10.1111/jwas.12854
Augyte S., Wikfors G. H., Pitchford S., Marty-Rivera M., Umanzor S., Lindell S., et al. (2020). The Application of Flow Cytometry for Kelp Meiospore Isolation. Algal. Res. 46, 101810. doi: 10.1016/j.algal.2020.101810
Bak U. G., Gregersen Ó., Infante J. (2020). Technical Challenges for Offshore Cultivation of Kelp Species: Lessons Learned and Future Directions. Botanica Mar. 63 (4), 341–353. doi: 10.1515/bot-2019-0005
Bak U. G., Mols-Mortensen A., Gregersen O. (2018). Production Method and Cost of Commercial-Scale Offshore Cultivation of Kelp in the Faroe Islands Using Multiple Partial Harvesting. Algal. Res. 33, 36–47. doi: 10.1016/j.algal.2018.05.001
Boderskov T., Nielsen M. M., Rasmussen M. B., Balsby T. J. S., Macleod A., Holdt S. L., et al. (2021). Effects of Seeding Method, Timing and Site Selection on the Production and Quality of Sugar Kelp, Saccharina Latissima: A Danish Case Study. Algal. Res. 53, 102160. doi: 10.1016/j.algal.2020.102160
Buschmann A. H., Gonzalez M., del C. H., Varela D. (2008). Seaweed Future Cultivation in Chile: Perspectives and Challenges. Int. J. Environ. Pollut. 33 (4), 432. doi: 10.1504/IJEP.2008.020571
Buschmann A. H., Prescott S., Potin P., Faugeron S., Vásquez J. A., Camus C., et al. (2014). “The Status of Kelp Exploitation and Marine Agronomy, With Emphasis on Macrocystis Pyrifera, in Chile,” in Advances in Botanical Research, vol. Vol. 71. (London, UK: Elsevier), 161–188. doi: 10.1016/B978-0-12-408062-1.00006-8
Campbell I., Macleod A., Sahlmann C., Neves L., Funderud J., Øverland M., et al. (2019). The Environmental Risks Associated With the Development of Seaweed Farming in Europe—Prioritizing Key Knowledge Gaps. Front. Mar. Sci. 6. doi: 10.3389/fmars.2019.00107
Camus C., Buschmann A. H. (2017). Macrocystis Pyrifera Aquafarming: Production Optimization of Rope-Seeded Juvenile Sporophytes. Aquaculture 468, 107–114. doi: 10.1016/j.aquaculture.2016.10.010
Camus C., Infante J., Buschmann A. H. (2019). Revisiting the Economic Profitability of Giant Kelp Macrocystis Pyrifera (Ochrophyta) Cultivation in Chile. Aquaculture 502, 80–86. doi: 10.1016/j.aquaculture.2018.12.030
Chu Y., Liu Y., Li J., Gong Q. (2019). Effects of Elevated pCO 2 and Nutrient Enrichment on the Growth, Photosynthesis, and Biochemical Compositions of the Brown Alga Saccharina Japonica (Laminariaceae, Phaeophyta). PeerJ 7, e8040. doi: 10.7717/peerj.8040
Duarte C. M., Bruhn A., Krause-Jensen D. (2021). A Seaweed Aquaculture Imperative to Meet Global Sustainability Targets. Nat. Sustain 5, 185–93. doi: 10.1038/s41893-021-00773-9
Duarte C. M., Wu J., Xiao X., Bruhn A., Krause-Jensen D. (2017). Can Seaweed Farming Play a Role in Climate Change Mitigation and Adaptation? Front. Mar. Sci. 4. doi: 10.3389/fmars.2017.00100
Edwards M., Watson L. (2015). Aquaculture Explained: Cultivating Laminaria Digitata Ireland North: Dublin . doi: 10.13140/RG.2.1.2153.3283
Engle C. (2010). Aquaculture Economics and Financing: Management and Analysis (Halowell, ME: John Wiley & Sons).
Engle C., van Senten J., Schwartz M., Brayden C., Belle S. (2020). Benchmarks for Mussel, Oyster, Scallop, and Seaweed Culture in Maine [Benchmarking Study] (Maine Aquaculture Association). Available at: https://maineaqua.org/benchmarking/.
European Commission (2012) Communication From the Commission to the European Parliament, the Council, the European Economic and Social Committee and the Committee of the Regions. Available at: https://eur-lex.europa.eu/LexUriServ/LexUriServ.do?uri=COM:2012:0494:FIN:EN:PDF.
Evankow A., Christie H., Hancke K., Brysting A. K., Junge C., Fredriksen S., et al. (2019). Genetic Heterogeneity of Two Bioeconomically Important Kelp Species Along the Norwegian Coast. Conserv. Genet. 20 (3), 615–628. doi: 10.1007/s10592-019-01162-8
FAO (2020). The State of World Fisheries and Aquaculture 2020 (Rome, Italy: FAO). doi: 10.4060/ca9229en
Flavin K., Flavin N., Flahive B. (2013). Kelp Farming Manual: A Guide to the Processes, Techniques, and Equipment for Farming Kelp in New England Waters [Manual] (Portland, ME: LLC). Available at: https://static1.squarespace.com/static/52f23e95e4b0a96c7b53ad7c/t/52f78b0de4b0374e6a0a4da8/1391954701750/OceanApproved_KelpManualLowRez.pdf.
Forbord S. (2018). Protocols for Macroalgae Research. 1st ed. Eds. Charrier B., Wichard T., Reddy C. R. K. (Boca Raton, FL: CRC Press). doi: 10.1201/b21460
Forbord S., Skjermo J., Arff J., Handå A., Reitan K. I., Bjerregaard R., et al. (2012). Development of Saccharina Latissima (Phaeophyceae) Kelp Hatcheries With Year-Round Production of Zoospores and Juvenile Sporophytes on Culture Ropes for Kelp Aquaculture. J. Appl. Phycol. 24 (3), 393–399. doi: 10.1007/s10811-011-9784-y
Forbord S., Steinhovden K. B., Solvang T., Handå A., Skjermo J. (2020). Effect of Seeding Methods and Hatchery Periods on Sea Cultivation of Saccharina Latissima (Phaeophyceae): A Norwegian Case Study. J. Appl. Phycol. 32 (4), 2201–2212. doi: 10.1007/s10811-019-01936-0
Froehlich H. E., Afflerbach J. C., Frazier M., Halpern B. S. (2019). Blue Growth Potential to Mitigate Climate Change Through Seaweed Offsetting. Curr. Biol. 29 (18), 3087–3093.e3. doi: 10.1016/j.cub.2019.07.041
Goecke F., Klemetsdal G., Ergon Å. (2020). Cultivar Development of Kelps for Commercial Cultivation—Past Lessons and Future Prospects. Front. Mar. Sci. 8. doi: 10.3389/fmars.2020.00110
Gonzalez-Romero M. A., Hernandez-Llamas A., Ruiz-Velazco J. M. J., Plascencia-Cuevas T. N., Nieto-Navarro J. T. (2014). Stochastic Bio-Economic Optimization of Pond Size for Intensive Commercial Production of Whiteleg Shrimp Litopenaeus Vannamei. Aquaculture 433, 496–503. doi: 10.1016/j.aquaculture.2014.07.010
Grebe G. S., Byron C. J., Gelais A., Kotowicz D. M., Olson T. K. (2019). An Ecosystem Approach to Kelp Aquaculture in the Americas and Europe. Aquacul. Rep. 15, 100215. doi: 10.1016/j.aqrep.2019.100215
Greene J. M., Gulden J., Wood G., Huesemann M., Quinn J. C. (2020). Techno-Economic Analysis and Global Warming Potential of a Novel Offshore Macroalgae Biorefinery. Algal. Res. 51, 102032. doi: 10.1016/j.algal.2020.102032
Hafting J. T., Craigie J. S., Stengel D. B., Loureiro R. R., Buschmann A. H., Yarish C., et al. (2015). Prospects and Challenges for Industrial Production of Seaweed Bioactives. J. Phycol. 51 (5), 821–837. doi: 10.1111/jpy.12326
Hasselström L., Thomas J.-B., Nordström J., Cervin G., Nylund G. M., Pavia H., et al. (2020). Socioeconomic Prospects of a Seaweed Bioeconomy in Sweden. Sci. Rep. 10 (1), 1610. doi: 10.1038/s41598-020-58389-6
Hu Z., Shan T., Zhang J., Zhang Q., Critchley A. T., Choi H., et al. (2021). Kelp Aquaculture in China: A Retrospective and Future Prospects. Rev. Aquacul. 13 (3), 1324–1351. doi: 10.1111/raq.12524
Kavlak G., McNerney J., Trancik J. E. (2018). Evaluating the Causes of Cost Reduction in Photovoltaic Modules. Energy Policy 123, 700–710. doi: 10.1016/j.enpol.2018.08.015
Kerrison P. D., Stanley M. S., Hughes A. D. (2018). Textile Substrate Seeding of Saccharina Latissima Sporophytes Using a Binder: An Effective Method for the Aquaculture of Kelp. Algal. Res. 33, 352–357. doi: 10.1016/j.algal.2018.06.005
Kim J. K., Yarish C., Hwang E. K., Park M., Kim Y. (2017). Seaweed Aquaculture: Cultivation Technologies, Challenges and its Ecosystem Services. ALGAE 32 (1), 1–13. doi: 10.4490/algae.2017.32.3.3
Loureiro R., Gachon C. M. M., Rebours C. (2015). Seaweed Cultivation: Potential and Challenges of Crop Domestication at an Unprecedented Pace. New Phytol. 206 (2), 489–492. doi: 10.1111/nph.13278
Maine Public Utilities Commission (2021) Residential Electric Rates. Available at: https://www.maine.gov/mpuc/regulated-utilities/electricity/delivery-rates.
Mao X., Augyte S., Huang M., Hare M. P., Bailey D., Umanzor S., et al. (2020). Population Genetics of Sugar Kelp Throughout the Northeastern United States Using Genome-Wide Markers. Front. Mar. Sci. 7. doi: 10.3389/fmars.2020.00694
McKinley Research Group (2021). Alaska Seaweed Market Assessment (Anchorage, AK: McKinley Research Group). Available at: https://www.afdf.org/wp-content/uploads/Alaska-Seaweed-Market-Assessment-2021-08-FINAL.pdf.
ME DMR (2021) DMR Open Data. MaineDMR Aquaculture - AQ Leases. Available at: https://dmr-maine.opendata.arcgis.com/.
NASEM (2021). A Research Strategy for Ocean-Based Carbon Dioxide Removal and Sequestration (Washington DC: National Academies Press), 26278. doi: 10.17226/26278
North Sea Farmers (2021). “Market Potential Report for Cultivated Seaweeds in Existing Seaweed Food Markets,” in MountainView Research Netherlands: The Hague, 59. Available at: https://www.northseafarmers.org/news/2021/Seaweed-market-study_210302.pdf.
Piconi P., Veidenheimer R., Chase B. (2020). Edible Seaweed Market Analysis (Rockland, ME: Island Institute), 56. Available at: https://www.islandinstitute.org/edible-seaweed-market-analysis/.
Redmond S., Green L., Yarish C., Kim J., Neefus C. (2014). New England Seaweed Culture Handbook (University of Connecticut Sea Grant). Available at: http://digitalcommons.uconn.edu/seagrant_weedcult/1?utm_source=digitalcommons.uconn.edu%2Fseagrant_weedcult%2F1&utm_medium=PDF&utm_campaign=PDFCoverPages.
Rößner Y., Krost P., Schulz C. (2014). Increasing Seaweed Crop Yields Through Organic Fertilisation at the Nursery Stage. J. Appl. Phycol. 26 (2), 753–762. doi: 10.1007/s10811-014-0269-7
Roque B. M., Venegas M., Kinley R. D., de Nys R., Duarte T. L., Yang X., et al. (2021). Red Seaweed (Asparagopsis Taxiformis) Supplementation Reduces Enteric Methane by Over 80 Percent in Beef Steers. PloS One 16 (3), e0247820. doi: 10.1371/journal.pone.0247820
Rubin E. S., Azevedo I. M. L., Jaramillo P., Yeh S. (2015). A Review of Learning Rates for Electricity Supply Technologies. Energy Policy 86, 198–218. doi: 10.1016/j.enpol.2015.06.011
Shea R., Chopin T. (2007). Effects of Germanium Dioxide, an Inhibitor of Diatom Growth, on the Microscopic Laboratory Cultivation Stage of the Kelp, Laminaria Saccharina. J. Appl. Phycol. 19 (1), 27–32. doi: 10.1007/s10811-006-9107-x
St-Gelais A. T., Fredriksson D. W., Dewhurst T., Miller-Hope Z. S., Costa-Pierce B. A., Johndrow K. (2022). Engineering A Low-Cost Kelp Aquaculture System for Community-Scale Seaweed Farming at Nearshore Exposed Sites via User-Focused Design Process. Frontiers in Sustainable Food Systems. Front Mar Sci 6, 848035. doi: 10.3389/fsufs.2022.848035
Su L., Pang S. J., Shan T. F., Li X. (2017). Large-Scale Hatchery of the Kelp Saccharina Japonica: A Case Study Experience at Lvshun in Northern China. J. Appl. Phycol. 29 (6), 3003–3013. doi: 10.1007/s10811-017-1154-y
Thomas J. B. (2018). Insights on the Sustainability of a Swedish Seaweed Industry (Stockholm, Sweden: Doctoral, KTH Royal Institute of Technology). Available at: http://kth.diva-portal.org/smash/get/diva2:1215011/FULLTEXT01.pdf.
Umanzor S., Li Y., Bailey D., Augyte S., Huang M., Marty-Rivera M., et al. (2021). Comparative Analysis of Morphometric Traits of Farmed Sugar Kelp and Skinny Kelp, Saccharina Spp., Strains From the Northwest Atlantic. J. World Aquacul. Soc. 52 (5), 1059–1068. doi: 10.1111/jwas.12783
Valero M., Guillemin M.-L., Destombe C., Jacquemin B., Gachon C. M. M., Badis Y., et al. (2017). Perspectives on Domestication Research for Sustainable Seaweed Aquaculture. Perspect. Phycol. 4 (1), 33–46. doi: 10.1127/pip/2017/0066
van den Burg S., Selnes T., Alves L., Giesbers E., Daniel A. (2021). Prospects for Upgrading by the European Kelp Sector. J. Appl. Phycol. 33 (1), 557–566. doi: 10.1007/s10811-020-02320-z
van den Burg S., van Duijn A. P., Bartelings H., van Krimpen M. M., Poelman M. (2016). The Economic Feasibility of Seaweed Production in the North Sea. Aquacul. Econom. Manage. 20 (3), 235–252. doi: 10.1080/13657305.2016.1177859
van Dijk W., van der Schoot J. R. (2015). An Economic Model for Offshore Cultivation of Macroalgae (Wageningen, Netherlands: Wageningen UR), Public Output No. 215G; p. 21. Available at: https://edepot.wur.nl/424022.
Visch W., Kononets M., Hall P. O. J., Nylund G. M., Pavia H. (2020). Environmental Impact of Kelp (Saccharina Latissima) Aquaculture. Mar. Pollut. Bull. 155, 110962. doi: 10.1016/j.marpolbul.2020.110962
Wade R., Augyte S., Harden M., Nuzhdin S., Yarish C., Alberto F. (2020). Macroalgal Germplasm Banking for Conservation, Food Security, and Industry. PloS Biol. 18 (2), e3000641. doi: 10.1371/journal.pbio.3000641
Westermeier R., Patino D., Piel M. I., Maier I., Mueller D. G. (2006). A New Approach to Kelp Mariculture in Chile: Production of Free-Floating Sporophyte Seedlings From Gametophyte Cultures of Lessonia Trabeculata and Macrocystis Pyrifera. Aquacul. Res. 37 (2), 164–171. doi: 10.1111/j.1365-2109.2005.01414.x
Yarish C., Kim J., Lindell S., Kits-Powell H. (2017). Developing an Environmentally and Economically Sustainable Sugar Kelp Aquaculture Industry in Southern New England: From Seed to Market [Project Report] (Stamford, Connecticut: University of Connecticut). Available at: https://opencommons.uconn.edu/marine_sci/4?utm_source=opencommons.uconn.edu/marine_sci/4&utm_medium=PDF&utm_campaign=PDFCoverPages.
Keywords: kelp aquaculture, nurseries, techno-economics, bottlenecks, S. latissima
Citation: Coleman S, Gelais ATS, Fredriksson DW, Dewhurst T and Brady DC (2022) Identifying Scaling Pathways and Research Priorities for Kelp Aquaculture Nurseries Using a Techno-Economic Modeling Approach. Front. Mar. Sci. 9:894461. doi: 10.3389/fmars.2022.894461
Received: 11 March 2022; Accepted: 25 April 2022;
Published: 24 May 2022.
Edited by:
Michael Phillips, WorldFish, MalaysiaReviewed by:
Simona Augyte, Ocean Era, Inc., United StatesAlejandro H. Buschmann, University of Los Lagos, Chile
Copyright © 2022 Coleman, Gelais, Fredriksson, Dewhurst and Brady. This is an open-access article distributed under the terms of the Creative Commons Attribution License (CC BY). The use, distribution or reproduction in other forums is permitted, provided the original author(s) and the copyright owner(s) are credited and that the original publication in this journal is cited, in accordance with accepted academic practice. No use, distribution or reproduction is permitted which does not comply with these terms.
*Correspondence: Struan Coleman, c3RydWFuLmNvbGVtYW5AbWFpbmUuZWR1