- 1Al Bilad Bank Scholarly Chair for Food Security in Saudi Arabia, The Deanship of Scientific Research, The Vice Presidency for Graduate Studies and Scientific Research, King Faisal University, Al Ahsa, Saudi Arabia
- 2Biological Sciences Department, College of Science, King Faisal University, Al Ahsa, Saudi Arabia
- 3Botany and Microbiology Department, Faculty of Science, Helwan University, Cairo, Egypt
- 4Biology Department, College of Science, Imam Abdulrahman Bin Faisal University, Ad-Dammam, Saudi Arabia
- 5Chemistry Department, College of Science, King Faisal University, Al Ahsa, Saudi Arabia
- 6Physics Department, College of Science, King Faisal University, Al Ahsa, Saudi Arabia
Background: Chemical plastics cause global environmental pollution and can take hundreds of years to be naturally removed from the environment; therefore, eco-friendly alternatives are sought. In that regard, marine algae are considered a promising source for bioplastics. However, macroscopic algae from the Arabian Gulf, despite being produced in massive quantities every year, have never been exploited for this purpose. Moreover, most of the available studies have been primarily based on the extraction of specific components of algae to prepare algal bioplastics, which is laborious and costly and does not allow the use of all biological products of algae. Therefore, the present study aimed at generating biodegradable bioplastic from the whole biomass of a marine green macroscopic alga from the Arabian Gulf, Saudi Arabia, using a simplified method.
Materials and methods: The identity of this green alga was investigated using both morphological characteristics and molecular analysis. Different treatments from the literature were initially tried to yield a bioplastic blend, but did not work. The successful method included drying the green macroalgal biomass and grinding it until it becomes a fine powder, followed by sieving. The powder was placed in 100 ml water with other reagents and then autoclaved. The resulting mixture was further treated with glycerin. Several reagents were tested, but successful treatment was achieved with the combination of the ground seeds of Plantago ovata and the chemical plasticizer polyethylene glycol (PEG; Mw = 3,350). The algal biocomposite was effective in forming a tensile polymer whose properties were further enhanced by adding glycerin 1 day after making the blend. Spectrophotometric, thermal, and mechanical analyses of the blend were conducted, including Fourier transform infrared (FTIR) spectroscopy, dynamic mechanical analysis (DMA) for the mechanical properties, and thermogravimetric analysis (TGA) for thermal stability. The biodegradability of the blend was also examined in sandy soil for 3 months.
Results: The green alga was identified as macroscopic green alga Ulva sp., which was confirmed by both morphological and molecular analyses. The combination of a plant-based plasticizer and algal biomass formed a polymer with excellent tensile properties and thermal stability. FTIR confirmed the formation of a starch-based blend whose functional groups, O–H, C–H, C=O, and C–O, indicate the formation of a starch bioplastic derived from both starch and cellulose in the green alga and in P. ovata. Biodegradability was proven as the blend lost nearly 40% of its biomass after the soil burial test.
Discussion: Ulva sp. is a marine alga that is widespread in marine habitats. This particular alga is highly rich in carbohydrates including cellulose, hemicelluloses, starch, and ulvan, among other carbohydrates that constitute the major part of its dry weight. This alga and the plant plasticizer both contain starch as reserve food material. Both natural polysaccharides are excellent precursors for the formation of bioplastics and are completely biodegradable by soil microorganisms. PEG is also biodegradable by bacterial action. Therefore, the whole blend is not only biodegradable but also has suitable tensile strength and thermal stability.
Conclusion: The present study describes an eco-friendly novel method that is mostly based on using the whole algal biomass in addition to a natural plant material as a plasticizer, thereby providing a sustainable blend for the manufacturing of bioplastics for use in a number of applications, including agriculture, as it is biodegradable and can be utilized for composting and fertilizing plants.
1. Introduction
Plastics are classified according to their origin into fossil-based or bio-based, or according to their affinity to decomposition into non-biodegradable or biodegradable (Devadas et al., 2021; Zanchetta et al., 2021). Due to global pollution with chemical plastics and their slow or non-biodegradability, eco-friendly alternatives are actively sought (Devadas et al., 2021; Zanchetta et al., 2021). In that regard, algal-based bioplastics represent plausible alternatives to chemical plastics. Algae are photosynthetic organisms that synthesize their organic matter, hence called primary producers. They are of ubiquitous distribution and occupy diverse habitats, including marine niches. Marine algae are currently being exploited in different industries (El Semary, 2020; El Semary, 2021), the most recent application of which is bioplastic production (Abdul Khalil et al., 2017; El Semary, 2021). (Gai et al., 2013; Ling et al., 2016; Bin Yusoff, 2017; Youning et al., 2018; Abdo and Ali, 2019; Amin et al., 2019; Ong et al., 2019; Filiciotto and Rothenberg, 2021 and Nikiema and Asiedu, 2022) Algae and plants usually contain starch and cellulose as the starting materials for bioplastic formation, which are completely biodegradable (Abdul Khalil et al., 2017; Devadas et al., 2021; Zanchetta et al., 2021). Macroalgae can be used in the formation of bioplastics mostly through using their derivatives (Devadas et al., 2021; Zanchetta et al., 2021). Indeed, algae are a source of a variety of raw materials that can be used to produce bioplastics such as hydrocolloids) Porse and Rudolph, 2017; Lim et al., 2021). Generally, plastics can be derived from various starting materials of different chemical compositions and can be mixed with other materials to fit a particular requirement (Lim et al., 2021). For example, Roja et al. (2019) extracted polyhydroxyalkanoates (PHAs) from marine microscopic algae and cyanobacteria and showed that this biomaterial can be a promising alternative to chemical plastics. There are several reports on the use of polysaccharides, which are colloidal in nature, for the generation of biofilms (Basiak et al., 2017; Ili Balqis et al., 2017; Nur Hanani and Aelma Husna, 2018). Although algae are rich in precursor materials for bioplastics, they need the addition of strengthening agents, plasticizers, or fillers in order to give a high degree of flexibility and durability to the produced bioplastic. For example, Sudhakar et al. (2021) used the red seaweed Kappaphycus alvarezii for the manufacture of a bioplastic film using polyethylene glycol (PEG) as a plasticizer. Jang et al. (2013) used the brown macroalga Laminaria japonica and the green macroalga Enteromorpha crinite to synthesize polypropylene biocomposites. E. crinite was stable at high temperatures and provided more reinforcement and better physical characteristics to the biocomposites compared to L. japonica. The highest thermal stability was obtained when green alga was pretreated with sulfuric acid. Sulfuric acid-treated green alga/polypropylene biocomposites showed improved thermal and mechanical properties. Chiellini et al. (2008) used the green alga Ulva armoricana for the formation of plastic composites with a hydrophilic, eco-compatible polyvinyl alcohol (PVA) polymer. They further added starch to the blend, which was successfully processed in the presence of glycerol. The composite showed improved film-forming properties and mechanical characteristics. The degradation and rapid mineralization rate was 80% in the soil, which occurred in 100 days. Otsuki et al. (2004) modified polyethylene by adding maleic anhydride for better interaction because there was no affinity between Chlorella sp. and polyethylene. This modification greatly enhanced the tensile strength and thermal plasticity of the composite, which was easily shaped and heat-pressurized. Therefore, blending the algal-based plastic with other materials can improve the physical and chemical properties of the bioplastic produced. In this regard, natural fibers are excellent candidates as they have the advantages of being abundant, light, biodegradable, economical, and renewable and are of low abrasive nature and have good mechanical properties (Sreekumar et al., 2008; Wang et al., 2011). The major constituents of natural fibers are cellulose fibers (helically wound cellulose microfibrils) bound together by an amorphous lignin matrix. Lignin keeps the water in the fibers, which acts as a stiffener that provides resilience against forces (Komuraiah et al., 2014). The hemicellulose found in natural fibers is believed to be a compatibilizer between cellulose and lignin (Hansen and Björkman, 1998). Recently, algal biocomposites have been used in many aspects of civil engineering (Rossignolo et al., 2022). As algal-based bioplastics are in demand as alternatives to chemical plastics, the current study therefore aimed to supply the first report on algal bioplastics from the Arabian Gulf whose algae have never before been exploited for this purpose. To achieve this, a novel method was developed for the formulation of an algal/plant-based bioplastic blend that is eco-friendly, economical, and biodegradable. In this method, the whole algal biomass, not a specific derivative, was used to maximize the use of all bio-assets and to minimize and economize the steps for preparation. We also examined the chemical and mechanical properties of the blend and its biodegradability potential to prove its suitability as a bioplastic.
2. Materials and methods
2.1. Algal collection and sampling
The macroalgal biomass was collected from the Al Uquair region, Al Ahsa, the Eastern Region in Saudi Arabia, in March 2022. A preliminary identification of the algal sample was conducted using identification keys. Based on the morphological characteristics, the green alga was initially identified as Ulva sp. The thallus was leaf-like, lobed with ruffled edges.
2.2. Molecular characterization and phylogenetic inference
2.2.1. DNA extraction of bacterial colonies
DNA was extracted from the algal biomass. The procedures for the DNA extraction are detailed in El Semary et al. (2022). Briefly, the extraction involved boiling at 95°C for 5 min, followed by placing in an ice bath for 15 min and centrifugation at 14,000 rpm for 5 min. The pellet was then suspended in 200 µl of Tris–EDTA buffer at pH 8.0 in a clean Eppendorf tube and stored at −20°C.
2.2.2. PCR amplification of DNA from the algal sample and phylogenetic inference
The partial 23S rRNA gene was amplified from the algal sample. The 23S rDNA genetic loci were p23SrV_f1 (5′-GGA CAG AAAGAC CCT ATG AA-3′) and p23SrV_r1 (5′-TCA GCCTGT TAT CCC TAG AG-3′), according to Sherwood and Presting (2007).
The main PCR steps were as follows: initial denaturation at 94°C for 2 min; 35 amplification cycles, with each cycle including denaturation at 94°C for 20 s, annealing at 55°C for 30 s, and extension at 72°C for 10 s; and a final extension step at 72°C for 10 min.
The amplicon was run on a gel and was purified using a PCR product purification kit (Qiagen, Germantown, MD, USA) and sent for sequencing to Macrogen (Seoul, South Korea). The retrieved sequence was subjected to Blastn search in GenBank, and the best matches and closely related sequences were used for tree reconstruction for the phylogenetic inference of the algal taxon.
2.3. Fabrication of bioplastics using whole algal biomass
The macroalgal sample was collected from Al Uquair, the Eastern Region of Saudi Arabia, in April 2022. The collection site latitude and longitude coordinates are 25°41′32.0" N, 50°09′33.5" E; 25°46′48.9" N, 50°10′18.7" E; and 25°43′59.0" N, 50°13′23.8" E. On the same collection day, the fresh biomass of the alga was thoroughly washed several times using distilled water and soaked for an hour in distilled water to get rid of any contaminants. Any clinging foreign mass was carefully removed using a brush to remove attached sediments and epiphytes and the biomass inspected with a magnifying lens for purity and cleanliness. The thallus was then used for verification of the morphological identity using taxonomic keys. The fresh biomass was cut into portions and air-dried at room temperature (RT) until use. Of the air-dried biomass of seaweeds, 3 g was placed in 100 ml of distilled water together with 3 g of PEG (Mw = 3,350) and 3 g of ground Plantago ovata seed biomass as a plasticizer after sieving. The whole mixture was thoroughly homogenized using a mortar and pestle and then autoclaved at 121°C for 15 min, after which the whole mixture was once again thoroughly homogenized. These components were thoroughly mixed. Subsequently, the blend was poured into a glass Petri plate to form a film. After the first day, 50% (v/v) glycerin was added drop by drop into the mixture to increase flexibility and to maintain the moisture content.
2.4. Characterization of the bioplastic film
2.4.1. FTIR spectroscopy
The spectra of the sample in the form of a casted film were recorded using a Fourier transform infrared (FTIR) spectrometer (Thermo Scientific, Waltham, MA, USA). The spectrum was acquired at 2 cm−1 resolution.
2.4.2. Measurements of the mechanical properties at different temperatures
The mechanical properties were characterized with a Q200 TA dynamic mechanical analyzer (DMA) testing machine (Physics Department, College of Science, King Faisal University, KSA). The biofilm was cut into sections with approximate dimensions of ~0.5 cm width, 8 cm length, and 0.03 cm thickness. The samples were stretched with a gauge length of 2.2 cm at a speed of 1 mm/min. The system was equilibrated at different temperatures and kept in isothermal isolation for a 4-min period for each temperature before ramping the force measured in the range 1–15 N (AlNaim et al., 2017).
2.4.3. Thermogravimetric analysis of the algal blend
The TA Q50 thermogravimetric analysis (TGA) instrument was used to measure the weight loss of the algal biomass sample as a function of temperature. The experiments were performed at two heating rates, 10°C and 20°C/min. For each experiment, approximately 12 mg of the algal biomass sample was placed in a platinum pan. Pure nitrogen (purity, 99.99%), with a flow rate of 60 ml min−1, was used as a carrier gas during all experiments to extinguish the mass transfer effect to a minimum level. Each macroalgal sample was heated from RT ~21°C to 600°C. The weight loss relative to the temperature increment was automatically recorded, and the thermogram (TG) and the derivative thermogram (DTG) were then plotted.
2.4.4. Soil burial test
The soil burial test was conducted to examine the biodegradability of the bioplastic film. Sieved sandy soil was used. Approximately 120 g of soil was placed in a clean plastic container. The sample was buried and left for 60 days at RT. The initial weight (W0) and the final weight (W1) were recorded and used to calculate the percentage of weight loss: weight loss by percentage = [(W0 − W1)/W0] × 100.
3. Results
3.1. Characterization of the macroscopic green alga
Molecular characterization using universal algal primers was successful in amplifying the partial 23S rDNA genetic locus from the green alga. The Blastn search using the retrieved sequence was best matched to Ulva sp., with a percentage similarity of 95% and sequence coverage of 93%.
Basic Local Alignment Search Tool (BLAST) computes a pairwise alignment between a query and the database sequences searched. For the purpose of sequence tree presentation, an implicit alignment between the database sequences was constructed based on the alignment of those (database) sequences to the query. Phylogenetic inference and tree reconstruction were performed using the neighbor-joining method, which showed robust cladding of the algal sequence with other Ulva closely related sequences (Figure 1).
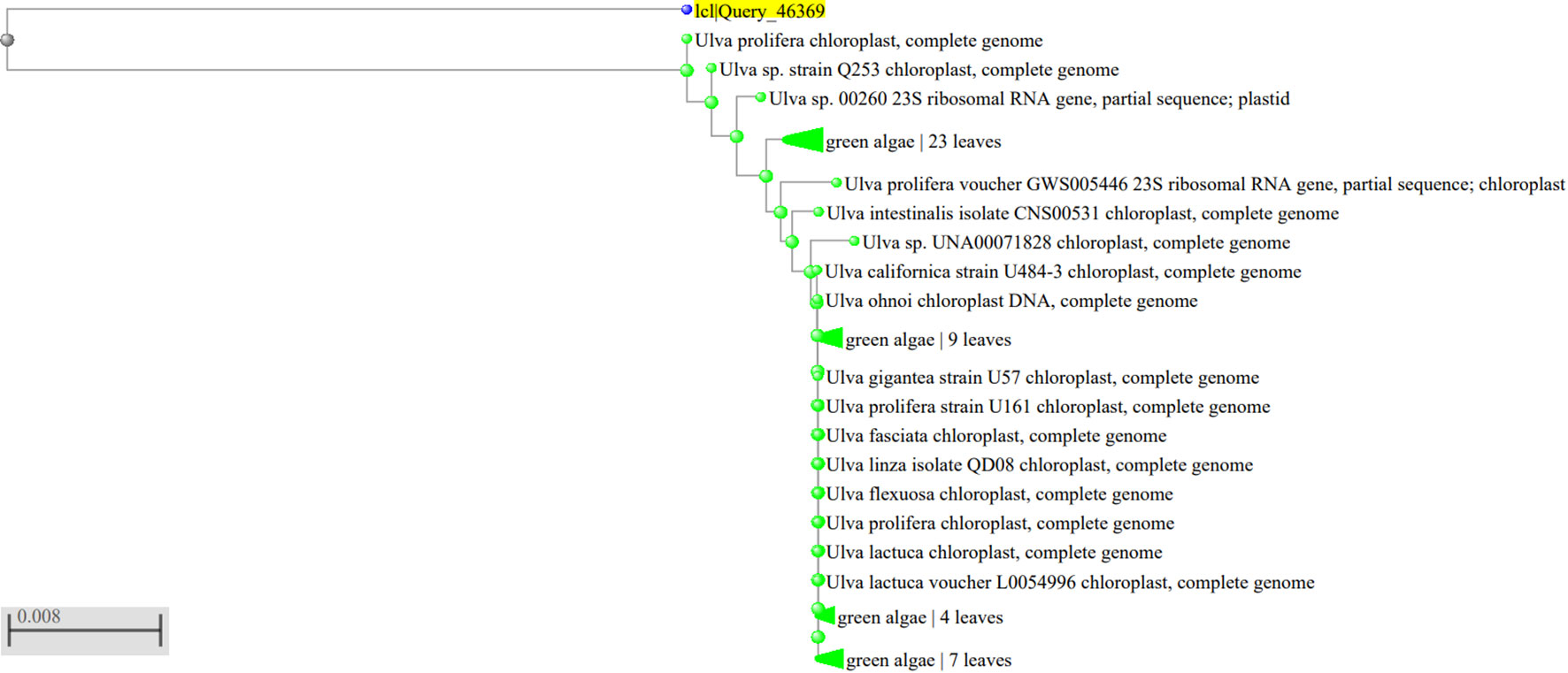
Figure 1 Neighbor-joining phylogenetic tree of green alga. The yellow highlighted sequence represents the green alga under investigation, while green circles highlight the closely related sequences.
3.2. Fabrication of the algal bioplastic
Despite numerous attempts to fabricate a bioplastic material using several methods from the literature, we were not able to produce one that worked. However, the use of ground P. ovata mixed with PEG and the biomass of the green alga resulted in a homogenous, flexible bioplastic film (Figure 2).
3.3. Fourier transform infrared
The FTIR spectra of the green alga–Plantago bioplastic blend are shown in Figure 3. In the spectra, the bands were closely related to those observed for starch (Amin et al., 2019). In addition, the cellulose banding pattern was represented, and an overlap between starch and cellulose at 2,883 cm−1 was observed, which might be due to both being polysaccharides. The broadband at 3,273 cm−1 was the O–H stretching. This signal can result from the stretching vibrations of carboxylic, phenolic, and alcoholic compounds, which indicates an increase in the number of hydrogen bonds of the plastics components and/or the electrostatic interactions. The peak at 2,983 corresponded to the C–H stretching, where the band at 2,800–3,000 cm−1 was related to =C–H and C–H stretching vibrations due to the lipid and carbohydrate contents in the alga (Youning et al.,2018). The bands from 704.27 to 1,014.48 cm−1 corresponded to the C–O bond stretching. The absorption bands of the C–H and C–O–H bending were shown at wave numbers 2,932.52 and 1,152.92 cm−1, respectively. Moreover, they can be attributed in part to the N–H stretching resulting from protein. The intensity of C–H and C–O–H at wave numbers 2,931 and 1,154 cm-1 indicates a possible electrostatic interaction inside the bioplastic blend resulting in a homogenous blend Filiciotto and Rothenberg (2021). Bands appearing at frequencies of 1,709–1,495 cm−1 were attributed to the C=O stretching vibration due to the free carboxyl groups present in lipids and some polysaccharides Chen et al. (2018). Lastly, C–O–C stretching was observed within 960–1,102 cm−1 (17).

Figure 3 Fourier transform infrared (FTIR) spectra of the green alga–Plantago blend with polyethylene glycol and glycerin.
3.4. Mechanical properties and thermal stability over a range of temperatures
Elongation at break is the ratio of the changes in length to the original length of the samples multiplied by 100 to obtain the percentage, as described in the formula: (ΔL/L) * 100. It is proportional to the acting force. On the other hand, the Young’s modulus evaluates the elasticity of rigid materials. It is equal to the stress divided by the strain and is measured as the slope of the strain vs. stress curves to show the withstanding changes in length (i.e., elongation), as shown in Table 1. The values of the Young’s modulus at different temperatures after 3 weeks of preparation were all high, with one at 40°C being the highest, reflecting its elasticity but, at the same time, also its comparatively less resistance to be deformed, whereas the lowest was found at 35°C, which reflects its reasonable elasticity, but with higher resistance to be deformed. Tensile strength tests (force per cross-sectional area required for breakage) of the samples were conducted to simulate quantitative damage illustrated by the strain vs. stress curves. Tensile strength reflects the maximum stress a material can handle and defines the limit between the plasticity zone and the rupture zone. The tensile toughness (strength) can be expressed as work per volume of tissue required for breakage. The highest was recorded at 35°C, reflecting resistance to breakage. The rest of the temperatures tested also showed very good tensile strength values (Table 1 and Figure 4).

Table 1 Mechanical properties of the bioplastic sample in different conditions associated with the Young’s modulus, toughness, and elongation.
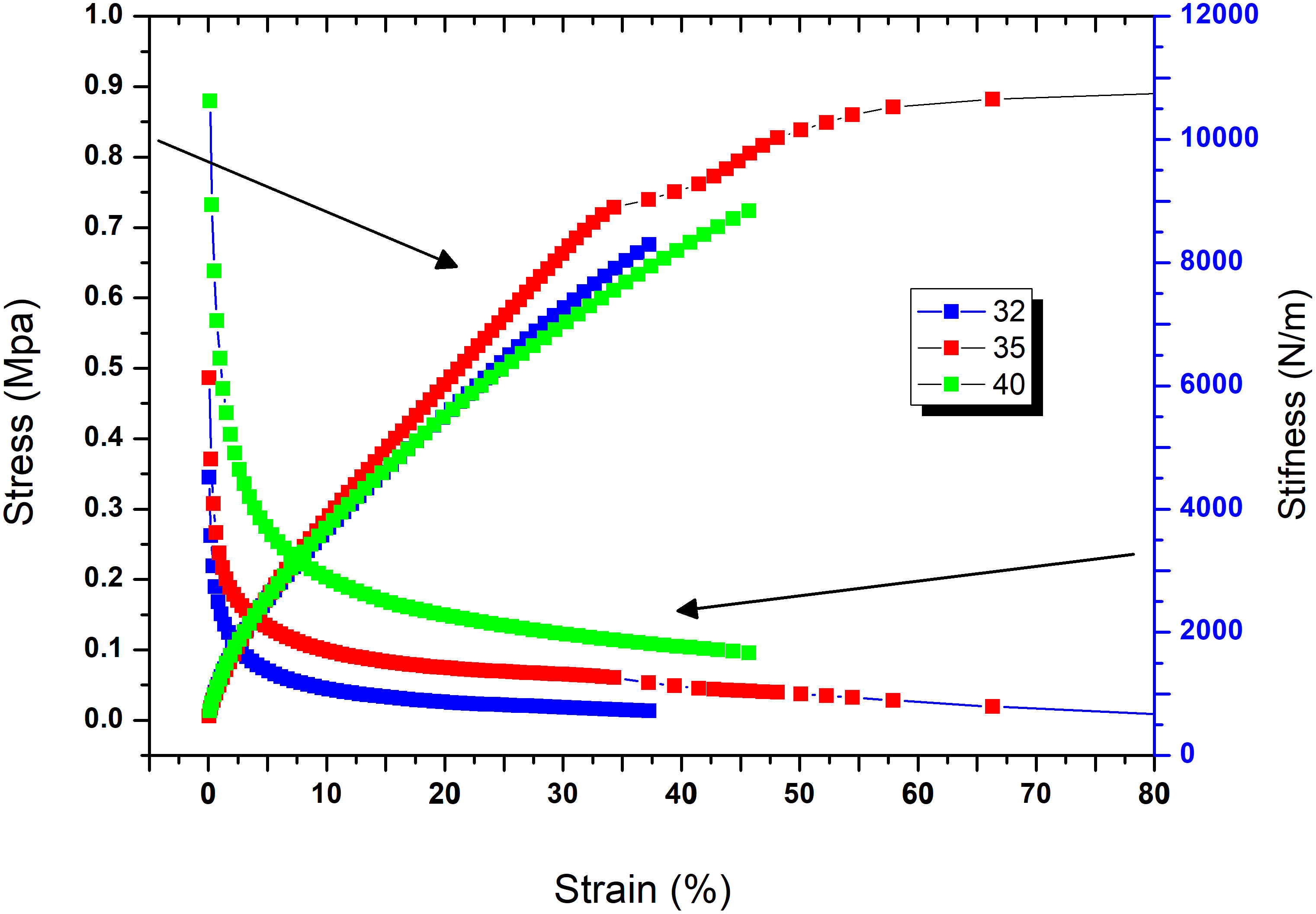
Figure 4 Strain vs. stress and stiffness for the 3-week samples at different temperatures (32°C, 35°C, and 40°C).
3.5. Thermogravimetric analysis
The association between temperature and the weight loss of the samples is shown at different temperatures at a rate of 10°C/min (Figure 5). However, the DTG graph effectively differentiated the thermal decomposition and clearly identified the individual steps of mass variation by locating the position of the peaks of first derivative, as shown in Figure 6. For this analysis, the temperature for each run was up to 650°C. However, the graphs were only drawn up to 500°C since the weight of the samples became stable after this temperature and no major loss was observed. Based on the results, the thermal degradation of the bioplastic blend takes place in a three-step reaction.
3.6. Soil burial test
The weight loss percentage of the bioplastic film was 40% in sandy soil.
4. Discussion
Algal-based bioplastics represent an eco-friendly and sustainable source of biodegradable plastics that can be plausible alternatives to chemical plastics (Zanchetta et al., 2021). Moreover, algae do not compete with the food production for human consumption and are also photosynthetic, thereby reducing carbon dioxide and mitigating global warming. Algae only have minimal growth requirements and can tolerate harsh environmental conditions (Zhang et al., 2019). In addition, algal-based bioplastics are favored over plant-based ones derived from cassava starch as the latter suffers from poor water resistance and mechanical issues (Machud et al., 2013). Algal bio-blends are based primarily on the combination of algal biomass and other components in order to enhance the physical and chemical properties of the bioplastic produced. For example, Chiellini et al. (2008) blended polyvinyl alcohol as a polyol plasticizer and starch with the alga U. armoricana to synthesize bioplastics. The starch reduced the amount of polyvinyl alcohol needed by approximately 40% while maintaining cohesion, the film-forming properties, and mechanical characteristics. A number of algal combinations investigated initially were all unsuccessful. Reflecting on the methods previously tried but did not work, it was discovered that the method developed by Surya et al. (2021) did give a cast, but was completely fragile and easily broken. Another method reported by Sudhakar et al. (2021) was utilized, but resulted in a hard crackable blend. Using sago as a plasticiser, in accordance with Bin Yusoff (2017), was also investigated, but with no success. In addition, we tried several materials such as sesame seeds, zinc oxide, carob seeds, and flax seeds, among other chemical and natural materials, but none of them worked, most likely due to differences in the algal types and their metabolites. In the present study, the green alga identity was revealed to be Ulva sp., which was confirmed using both morphological keys and molecular analysis, as well as phylogenetic inference. The phylogenetic tree showed the co-cladding of our algal sample with closely related Ulva spp. The identified Ulva sp. has a cell wall composed of cellulose, hemicelluloses, and ulvan polysaccharides as matrix. Cellulose is a water-insoluble polymer composed of glucose molecules. It has distinct hydrophilic and hydrophobic properties due to the presence of both equatorial hydroxyl groups and axial hydrogen atoms, which confer stability through the coplanar orientation of the individual glucopyranose rings (Zanchetta et al., 2021 and references therein). Cellulose is also the major load-bearing component of the cell wall of Ulva sp. The wall also contains different types of hemicelluloses, including xyloglucans, xylans, mannans, glucuronan, and β-glucans, which were found in the ulvan polysaccharide matrix (Marquese, 2017; Zanchetta et al., 2021 and references therein). Ulvan, which contributes 9%–36% of the wall components, is an anionic sulfated polysaccharide that mostly contains xylose and rhamnose 3-sulfate linked to uronic acids (Lim et al., 2021). Ulvan has a film-forming property, a characteristic that is extremely important in bioplastic production, in addition to cellulose, which makes Ulva sp. a plausible candidate for the formation of a filler or for reinforcement (Lakshmi et al., 2020). According to Moral et al. (2019), the cell wall of Ulva sp. is composed of 40.7% dry weight cellulose and 7.1% hemicelluloses in addition to lignin. These polysaccharides possess highly plausible characteristics for bioplastic formation with regard to their load bearing and film-forming capacities (Hansen and Björkman, 1998; Wang et al., 2011; Komuraiah et al., 2014). Regarding the total carbohydrate content of Ulva sp., Rasyid (2017) showed that carbohydrates constitute about 58% of the total dry weight of the alga, followed by 28.4% of dietary fibers and 13% protein. These different constituents of fibers, together with the load-bearing long-chain polysaccharides, favorably contribute to both elasticity and elongation, as well as resistance to breakage (tensile strength) (Hansen and Björkman, 1998; Wang et al., 2011; Komuraiah et al., 2014). In the present study, the algal biomass was combined with ground P. ovata seeds. These seeds are a source of psyllium, a type of dietary fiber derived from the seed husks. Psyllium is an indigestible soluble fiber that can be fermented into butyrate (https://medlineplus.gov/druginfo/natural/866.html, accessed 14 May 2022). It can be used as a laxative and is also utilized in folk medicine due to its mucilage-producing ability in aqueous solutions, which has been exploited in the pharmaceutical, cosmetic, and food industries. It is also used in herbal medicine to treat bladder problems, high blood pressure, and skin irritations. P. ovata seeds also contain many bioactive compounds such as flavonoids, alkaloids, terpenoids, phenolic acid derivatives, glycosides, fatty acids, and polysaccharides. Polysaccharides are considered as the most abundant constituent, accounting for more than 85% of dry weight. The polysaccharide fraction consists mainly of xylose (80%) and arabinose (14%). The husks of the seeds contain monosaccharides, such as xylose (68.94%), arabinose (15.97%), rhamnose (9.89%), galactose (2.63%), and mannose (2.26%). On the other hand, extraction using an alkaline solution (2 M NaOH) yielded some monosaccharides, including xylose (74.8%), arabinose (23.2%), galactose (1.2%), and rhamnose (0.8%) (Saghir et al., 2008) (33). Furthermore, Plantago seeds contain other components, including 17.4% protein, 6.7% fat, 24.6% total dietary fiber, 19.6% insoluble fiber, and 5.0% soluble fiber, as well as combustion heat of 4.75 kcal/g. Plantago seeds also produce 35.8% albumin, 23.9% globulin, and 11.7% prolamin. The oil derived from Plantago seeds has a high percentage of linoleic (40.6%) and oleic acids (39.1%) and a modest amount of linolenic acid (6.9%). Other constituents included casein, starch, corn oil, cellulose, sucrose, mineral mix, and a mix of vitamins (Romero-Baranzini et al., 2006). The gelling property of psyllium renders it suitable for drug delivery systems and absorption. Psyllium has also been reported to have cholesterol-lowering and wound-healing properties (Masood and Miraftab, 2010) Recently, Jérémy et al. (2021) have characterized and identified the natural polysaccharides extracted from psyllium as promising binders that could be substitutes to the classical organic binders from the petrochemical industry.
In a similar manner, Machud et al. (2013) utilized the red alga Eucheuma cottonii as the raw material for plastic production, in which the red alga was mixed separately with the latex of Artocarpus altilis and Calostropis gigantea as substitutes of glycerol as plasticizer due to the increased concentration of glycerol reducing the thickness, tensile strength, and density of the bioplastic. The authors found that the latex of these tropical plants did not affect the characteristics of the bioplastic produced, but instead increased the ductility, tensile strength, or energy absorption of the red alga-derived bioplastic. Based on the results, the mixture of the latex of tropical plants with algae to synthesize bioplastics that could be customized to suit different applications was recommended. Similarly, Lim et al. (2021) mixed ulvan with other polymers to improve the mechanical properties of films. However, our protocol used the whole algal biomass, not just an extracted fraction like ulvan, thereby benefiting from the whole biomass and saving time in the extraction and recovery procedures and the resources needed for the extraction of specific components. Furthermore, we used a natural plasticizer and filler (P. ovata) that is full of nutrients and fibers and can be easily biodegraded by microbial decomposers. Our formulation is completely biodegradable; even the PEG used is biodegradable by bacterial species such as Kocuria kristinae, Dermacoccus nishinomiyaensis, Pseudomonas stutzeri, and Acinetobacter haemolyticus. The values of the mechanical properties, such as the Young’s modulus, were all high at the different measuring temperatures; the highest value at 40°C reflected its elasticity, recording at the same time a high elongation percentage. However, at 40°C, the toughness (tensile strength) was relatively low; thus, the bioplastic film exhibited less resistance to be deformed. The lowest Young’s modulus was recorded at 35°C, reflecting resistance to be deformed, with reasonable elasticity and flexibility. Tensile strength reflects the maximum stress a material can handle and defines the limit between the plasticity zone and the rupture zone, i.e., it defines the resistance of a material to breakage. The highest was recorded at 35°C, reflecting resistance to breakage compared to the rest of the temperatures tested (Table 1 and Figure 4). Nonetheless, all samples showed good resistance to breakage by high forces, indicating their good durability and suitability for different applications and activities.
Comparing our results to those in the literature, we found that the Young’s modulus of the bioplastic film made from κ-carrageenan (Sudhakar et al., 2021) ranged between 1.29 and 5.82 MPa, whereas that in the present study ranged between 42.83 ± 1.9 and 46.62 ± 2.4 MPa. With regard to tensile strength, Sudhakar et al. (2021) reported values between 93.2 and 140.6 kgf/cm2, whereas our results showed a lowest value of 148.7 and a maximum value of 573.6 at a temperature of 35°C. Our results were much higher in terms of tensile strength (resistance to breakage) and Young’s modulus (an indicator of elasticity or flexibility) compared to those reported by Sudhakar et al. (2021) (as well as those of the references cited within). For example, Hassan et al. (2008) showed that the tensile strength of algal fillers using Ulva sp. was 22 MPa, whereas that of a biocomposite of Eklonia sp. with wood polypropylene was 11.113 MPa (Echeverria et al., 2017). Maximum tensile strength of 42.9 MPa was reported by Jang et al. (2013) using the green alga E. crinite. Our tensile strength values at different temperatures and even after 3 weeks of preparation surpassed all of the previously reported values, thereby emphasizing the suitability of the bioplastic produced. The elongation at break of the present bioplastic film ranged between 27% and 46%, which was mostly due to increasing the number and quantity of plasticizers, including the natural plasticizer (P. ovata), PEG, and glycerin. In addition, the presence of ulvan as a matrix contributed to the elongation ability. Indeed, the semi-refined carrageenan (70%) and ulvan polysaccharide along with glycerol gave an elongation at break range of 7.98%–9.24% (Ramu Ganesan et al., 2018). Concomitantly, Ili Balqis et al. (2017) showed an increase in the elongation at break of up to 16% when increasing the concentration of the PEG plasticizer. Moreover, Sudhakar et al. (2021) reported a range of elongation at break between 6.1% and 7.1% when using PEG 3000 as a plasticizer with the red alga K. alvarezii.
In this study, at all measuring temperatures, our results showed that the produced film achieved values well above 40 MPa for the Young’s modulus and high tensile strength values. Moreover, the strain vs. stress curves and the stiffness for the 3-week samples at different measuring temperatures showed the same curve patterns with only minor numerical differences, thereby indicating flexibility (indicated by the Young’s modulus) and durability (indicated by the tensile strength). Given that the other studies and our study used PEG, the differences in the results might be attributed to the combined effect of using an alga of high carbohydrate content and the ulvan matrix together with a unique type of plant plasticizer/filler (P. ovata), as used in the present study. TGA was used to analyze the thermal behavior of the macroalga at a temperature range between RT and 500°C with three different heating rates (10°C, 20°C, and 30°C/min) under nitrogen atmosphere. Based on the TGA results, the kinetic parameters were then determined according to the Coat–Redfern method. According to Nordin et al. (2018), starch as food packaging has the advantages of biodegradability, availability, and cost-effectiveness. Its mechanical and thermal resistance can be further improved using microcellulose fibers. The authors reported that the tensile strength and the elongation at break of the films increased with the addition of microcellulose fibers. These properties can be further enhanced with regard to the odor and color of the resulting bioplastic, adding bleach to enhance the color and activated carbon to remove the odor (Ling et al., 2016). In our research, this was verified as the green alga is cellulosic and contains starch, and P. ovata and their blend in the presence of PEG 3350 and glycerol resulted in a homogenous film with good interfacial interactions, as verified by the FTIR analysis, and excellent mechanical properties with thermal stability, as indicated by the uniform pattern under different temperatures. In the TGA of our blend, the first step of weight loss started from 70°C until ~130°C, which was explained by the evaporation of the moisture content in the samples losing around 50% of the sample weight (White et al., 2011) or some light volatile matters (Gai et al., 2013). The second stage, however, took place from~180°C to temperatures up to 250°C. At this stage, considerable major weight loss was observed resulting from the main degradation process. This loss was attributed to the decomposition and/or depolymerization of the algal organic constituents, such as carbohydrates, protein, and lipids. The mass loss of algae between 180°C and 270°C was attributed to the decomposition of carbohydrate, while the degradation of proteins and starch took place between 320°C and 450°C (Vega et al., 1996; Carpio et al., 2019).
Moreover, it was noticed that the increase in the heating rate has moved the decomposition of volatiles to the marginally higher temperature, based on the thermogram. In the literature, a similar scheme has been reported (Idris et al., 2010), and this lateral displacement (backwards and forwards) was primarily due to limitations in the heat transfer at higher heating rates inside the bulk of samples. At the higher heating rate, the reaction time became shorter and, hence, a higher temperature was required for the evolution of volatiles from the biomass samples, whereas at a low heating rate, a longer residence time and greater instantaneous energy were available for the volatiles evolved from the biomass (Waheed et al., 2015). In line with our findings, Ong et al. (2019) reported a low calorific value for algae and excellent mechanical and thermal properties and suggested their use for the production of biopolymers. The authors also performed TGA of the algal biomass in this study, where three species of seaweed used as a feedstock were exposed to different heating rates of 10°C, 20°C, and 30°C/min. The DTG values of Caulerpa lentillifera, Gracilaria coronopifolia, and Chaetomorpha linum indicated that the thermal degradation of the three algal samples happened gradually in steps. The sandy soil was less inhabited by microorganisms, but with the presence of the biofilm with nutritive components and a reasonable moisture content, the decomposers appeared to have acted efficiently with regard to the biodegradation of the bioplastic, resulting in 40% loss of the initial weight (Marichelvam et al., 2019).
In summary, to the best of our knowledge, this is the first study investigating bioplastic formation from a macroscopic green alga from the Arabian Gulf using P. ovata as a plasticizer and filler. Our study used the whole biomass of the algae, which did not extract carbohydrates or any other components like most of the previous studies did, thereby saving energy, labor, equipment, chemicals, and time, making our method cost-effective in terms of cutting costs needed for laborious steps. It also used all the biological products of the alga, which, in terms of biodegradability and using this bioplastic blend for soil biocompost, will add to the mineral, vitamin, growth-promoting chemicals, and antioxidants, among others, coming from the algal biomass and plant materials. We selected the plant plasticizer after numerous unsuccessful attempts with various materials using different methods and also several trials using our own materials. With regard to economic aspect, marine algae grow in masses along the Arabian Gulf coast; therefore, they are free for use and are produced in tonnes along the coast of the Eastern Province. Moreover, the method presented here was tested on other algal types and was found to work well. Furthermore, there is no need for instruments, except for an autoclave, which is of low cost (approximately 0.25 Saudi riyal/run) and can be compensated for by its use on larger algal quantities for mass preparations. The algal biomass or the blend was air-dried. All plant materials and the limited number of chemicals used cost about 2.95 Saudi riyals at the time of the experiments. Nonetheless, it should be noted that this is a rough estimation of the costs, and prices may vary from one country to another and from time to time. However, one important economic aspect is that there is no recycling or treatment cost for the used bioplastic, unlike chemical plastics. According to Nikiema and Aziedu (2022), the cost for treating the used chemical plastic is divided into many technologies on several levels, including mechanical recycling, chemical recycling (pyrolysis and gasification), and incineration. These all cost hundreds of thousands to millions, covering infrastructure, transport, and energy, among others. With regard to the chemical production of plastic, the cost of infrastructure is huge. Moreover, it is neither eco-friendly nor sustainable as fossil fuel is on the verge of complete depletion. Comparing that to the zero cost of recycling or processing of the present bioplastic, the blend presented here showed real cost-effectiveness. Future directions of this research include evaluating more and more algae for their potential in bioplastic formation. As the bioplastic is biodegradable and biocompostable, it will also serve as a biofertilizer for plants and for soil conditioning, saving costs on bio-fertilizers. Moreover, the blend can be useful in the production of small plant pots that can be inserted into soil and left to biodegrade or placing plantlets into soil within their biocompostable material, with no harmful wastes.
5. Conclusions
The macroscopic green alga Ulva sp. from the Arabian Gulf is suitable for the production of bioplastics given its high carbohydrate and fiber contents. The method provided here is simple, cost-effective, and eco-friendly. It exploits the whole algal biomass and the produced blend is biodegradable; therefore, it can be used as a biocompost and a biofertilizer for plants given its high nutritional value. This study provides an economical application for this unexploited, valuable marine biological resource and opens the door for the exploitation of local algae.
Data availability statement
The original contributions presented in the study are included in the article. Further inquiries can be directed to the corresponding author.
Author contributions
NE was responsible for idea of the research and its conceptualization. She was also responsible for designing experiments, supervising isolation and characterization of algae, coming up with the successful bioplastic recipe and formulation, supplying resources, interpretation of data, the original writing up and the twice rewriting of the revised manuscript after responding to reviewers comments and questions.In addition, she was responsible for applying for the chair fund. MA was responsible for conducting experiments on algal isolation and culturing, testing the different methods for bioplastics KA was responsible for supervising FTIR chemical analysis as well as provision of resources and lab. AA was responsible for mechanical and thermal properties measurements and interpretation. All authors contributed to the article and approved the submitted version.
Funding
This research was funded by the Al Bilad Bank Scholarly Chair for Food Security in Saudi Arabia, the Deanship of Scientific Research, the Vice Presidency for Graduate Studies and Scientific Research, King Faisal University, and Al Ahsa, Saudi Arabia, under Chair grant no. 17.
Acknowledgments
The authors express their deepest gratitude to Al Bilad Bank Scholarly Chair for Food Security in Saudi Arabia, The Deanship of Scientific Research, The Vice Presidency for Graduate Studies and Scientific Research, King Faisal University, and Al Ahsa, Saudi Arabia, grant chair number 17. The authors are grateful for Dr Muneera Aldayel for supplying the primers for the PCR and Mrs Al Anoud AlHumaiday for her help with the FTIR analysis. The research was conducted completely within the Premises of King Faisal University Al Ahsa and all the facilities were provided by College of Science, King Faisal University. The molecular analysis was conducted at Dr Khaled AlHudaib lab and the sequencing was conducted in Macrogen, South Korea.
Conflict of interest
The authors declare that the research was conducted in the absence of any commercial or financial relationships that could be construed as a potential conflict of interest.
Publisher’s note
All claims expressed in this article are solely those of the authors and do not necessarily represent those of their affiliated organizations, or those of the publisher, the editors and the reviewers. Any product that may be evaluated in this article, or claim that may be made by its manufacturer, is not guaranteed or endorsed by the publisher.
References
Abdo S., Ali G. (2019). Analysis of polyhydroxybutrate and bioplastic production from microalgae. Bull. Natl. Res. Centre 43, 1–4. doi: 10.1186/s42269-019-0135-5
Abdul Khalil H. P. S., Saurabh C. K., Tye Y. Y., Lai T. K., Easa A. M., Rosamah E., et al. (2017). Seaweed based sustainable films and composites for food and pharmaceutical applications: a review. Renewable Sustain. Energy Rev. 77, 353–362. doi: 10.1016/j.rser.2017.04.025
Al Naim A., Alnaim N., Ibrahim S. S., Metwally S. M. (2017). Effect of gamma irradiation on the mechanical properties of PVC/ZnO polymer nanocomposite. J. Radiat. Res. Appl. Sci., 1–7. doi: 10.1016/j.jrras.2017.03.004
Amin R., Chowdhury M., Kowser A. (2019). Characterization and performance analysis of composite bioplastics synthesized using titanium dioxide nanoparticles with corn starch. Heliyon 5, e02009. doi: 10.1016/j.heliyon.2019.e02009
Basiak E., Lenart A., Debeaufort F. (2017). Effect of starch type on the physico-chemical properties of edible films. Int. J. Biol. Macromol 98, 348–356. doi: 10.1016/j.ijbiomac.2017.01.122
Bin Yusoff Z. (2017). Biodegradable plastics from sago starch. J. Mechanical Eng. Department Politeknik Kuching Sarawak 1, 46–53.
Carpio R. B., Zhang Y., Kuo C. T., Chen W. T., Schideman L. C., Leon R. L. (2019). Characterization and thermal decomposition of demineralized wastewater algae biomass. Algal Res. 38, 1–12. doi: 10.1016/j.algal.2018.101399
Chen Y., Zhao W., Wang H., Meng X., Zhang L. (2018). A novel polyamine-type starch/glycidyl methacrylate copolymer for adsorption of Pb(II), Cu(II), Cd(II) and Cr(III) ions from aqueous solutions. R. Soc. Open Sci. 5 (6), 180281. doi: 10.1098/rsos.180281
Chiellini E., Cinelli P., Ilieva V., Martera M. (2008). Biodegradable thermoplastic composites based on polyvinyl alcohol and algae. Biomacromolecules 9 (3), 1007–1013. doi: 10.1021/bm701041e
Devadas V. V., Khoo K. S., Chia W. Y., Chew K. W., Munawaroh H. S. H., Lam M. K., et al. (2021). Algae biopolymer towards sustainable circular economy. Bioresour. Technol., 124703. doi: 10.1016/j.biortech.2021.124702
Echeverria C., Pahlevani F., Gaikwad V., Sahajwalla V. (2017). The effect of microstructure, filler load and surface adhesion of marine biofillers, in the performance of hybrid wood-polypropylene particulate bio-composite. J. Cleaner Prod. . 154, 284–294. doi: 10.1016/j.jclepro.2017.04.020
El Semary N. (2020). “Algae and fishes: Benefits and hazards,” in The handbook of environmental chemistry (Berlin, Heidelberg: Springer).
El Semary N. (2021). “Seaweeds for sustainable development,” in Sustainable solutions for environmental pollution. Ed. El-Gendy N. S. (Wilely USA: Scrivener publishing company).
El Semary N., Al Naim H., Aldayel M. F. (2022). A novel application of laser in biocontrol of plant pathogenic bacteria. 12(10), 4933. doi: 10.3390/app12104933
Filiciotto L., Rothenberg G. (2021). Biodegradable plastics: standards, policies, and impacts. Chem. Sus Chem., 14–56. doi: 10.1002/cssc.202002044
Gai C., Zhang Y., Chen W. T., Zhang P., Dong Y. (2013). Thermogravimetric and kinetic analysis of thermal decomposition characteristics of low-lipid microalgae. Bioresour. Technol. 150, 139–148. doi: 10.1016/j.biortech.2013.09.137
Hansen C. M., Björkman A. (1998). The ultrastructure of wood from a solubility parameter ؛Point of view. Holzforschung 52, 335–344. doi: 10.1515/hfsg.1998.52.4.335
Hassan M. M., Mueller M., Wagners M. H. (2008). Exploratory study on seaweed as novel filler in polypropylene composite. J. Appl. Polym Sci. 109, 1242–1247. doi: 10.1002/app.28287
Idris S. S., Rahman N. A., Ismail K., Alias A. B., Rashid Z. A., Aris M. J. (2010). Investigation on thermochemical behaviour of low rank Malaysian coal, oil palm biomass and their blends during pyrolysis via thermogravimetric analysis (TGA). Bioresour. Technol. 101, 4584–4592. doi: 10.1016/j.biortech.2010.01.059
Ili Balqis A. M., Nor Khaizura M. A. R., Russly A. R., Nur Hanani Z. A. (2017). Effects of plasticizers on the physicochemical properties of kappacarrageenan films extracted from eucheuma cottonii. Int. J. Biol. Macromol 103, 721–732. doi: 10.1016/j.ijbiomac.2017.05.105
Jang Y. H., Han S., Sim N., Kim H.-I. I. (2013). Pretreatment effects of seaweed on the thermal and mechanical properties of seaweed/polypropylene biocomposites. Part A: Appl. Sci. Manuf. 47, 83–90. doi: 10.1016/j.compositesa.2012.11.016
Jérémy M., Bourret J., Geffroy P.-M., Chartier T., Bienia M., Chaleix V., et al. (2021). Impact of bio-based binders on rheological properties of aqueous alumina slurries for tape casting. J. Eur. Ceramic Soc. 41 (1), 5593–5601. doi: 10.1016/j.jeurceramsoc.2021.03.049
Komuraiah A., Kumar N. S., Prasad B. D. (2014). Chemical composition of natural fibers and its influence on their mechanical properties. Mech. Compos. Mater. 50, 359–376. doi: 10.1007/s11029-014-9422-2
Lakshmi D. S., Sankaranarayanan S., Gajaria T. K., Li G., Kujawski W., Kujawa J., Navia R., et al (2020). A short review on the valorization of green seaweeds and ulvan: Feedstock for chemicals and biomaterials. Biomolecules 10 (7), 991.
Lim C., Yusoff S., Ng C. G., Lim P. E., Ching. Y. C. (2021). Bioplastic made from seaweed polysaccharides with green production methods. J. Environ. Chem. Eng. 9 (5), 105895. doi: 10.1016/j.jece.2021.105895
Ling H. S., Lim J.-Y., Ong W.-T., Wong C.-L. (2016). Agar from Malaysian seaweed as potential material for synthesis of bioplastic film. J. Eng. Sci. Technol. 11, 1–15.
Machud M., Fahmi R., Abdullah R., Kokarkin C. (2013). Characteristics of red algae Bioplastics/Latex blends under tension. Int. J. Sci. Eng. 5 (2), 81–88. doi: 10.12777/ijse.5.2.81-88
Marichelvam M., Jawaid M., Asim M. (2019). Corn and rice starch-based bio-plastics as alternative packaging materials. Fibers 7 (4), 32. doi: 10.3390/fib7040032
Marquese M. M. (2017). From macroalgae to bioplastic seaweed hydrolysates for polyhydroxyalkanoate production by marine bacteria (Portugal: Técnico Lisboa University).
Masood R., Miraftab M. (2010). “Psyllium: Current and future applications,” in Woodhead publishing series in textiles, medical and healthcare textiles. Eds. Anand S. C., Kennedy J. F., Miraftab M., Rajendran S. (UK: Woodhead Publishing), 244–253. doi: 10.1533/9780857090348.244
Moral A., Aguado R., Castelló R., Tijero A., Ballesteros M. (2019). Potential use of green alga ulva sp. for papermaking. BioResources 14, 6851–6862. doi: 10.15376/biores.14.3.6851-6862
Nikiema J., Asiedu Z. (2022). A review of the cost and effectiveness of solutions to address plastic pollution. Environ. Sci. pollut. Res. 29, 24547–24573. doi: 10.1007/s11356-021-18038-5
Nordin N., Othman S. H., Kadir Basha R., Abdul Rashid S. (2018). Mechanical and thermal properties of starch films reinforced with microcellulose fibres. Food Res. 2 (6), 555–563. doi: 10.26656/fr.2017.2(6).110
Nur Hanani Z. A., Aelma Husna A. B. (2018). Effect of different types and concentrations of emulsifier on the characteristics of kappacarrageenan films. Int. J. Biol. Macromol 114, 710–716. doi: 10.1016/j.ijbiomac.2018.03.163
Ong M. Y., Syahira Abdul Latif N.-I., Leong H. Y., Salman B., Show P. L., Nomanbhay S. (2019). Characterization and analysis of Malaysian macroalgae biomass as potential feedstock for bio-oil production. 12 (18), 3509. doi: 10.3390/en12183509
Otsuki T., Zhang F., Kabeya H., Hirotsu T. (2004). Synthesis and tensile properties of a novel composite of Chlorella and polyethylene. J. Appl. Polymer Sci. 92, 812–816. doi: 10.1002/app.13650
Porse H., Rudolph B. (2017). The seaweed hydrocolloid industry: 2016 updates, requirements, and outlook. J. Appl. phycol 29, 2187–2200. doi: 10.1007/s10811-017-1144-0
Ramu Ganesan A., Shanmugam M., Bhat R. (2018). Producing novel edible films from semi refined carrageenan (SRC) and ulvan polysaccharides for potential food applications. The International Journal of Biological Macromolecules 112, 1164–1170. doi: 10.1016/j.ijbiomac.2018.02.089
Rasyid A. (2017). Evaluation of nutritional composition of the dried seaweed ulva lactuca from pameungpeuk waters, Indonesia. Trop. Life Sci. Res. 28 (2), 119–125. doi: 10.21315/tlsr2017.28.2.9
Roja K., Ruben Sudhakar D., Anto S., Mathimani T. (2019). Extraction and characterization of polyhydroxyalkanoates from marine green alga and cyanobacteria. Biocatalysis and Agricultural Biotechnology 22, 101358. doi: 10.1016/j.bcab.2019.101358
Romero-Baranzini A., Rodriguez O., Yanez-Farias G., Barron-Hoyos J., Rayas-Duarte P. (2006). Chemical, physicochemical, and nutritional evaluation of plantago (Plantago ovata forsk). Cereal Chem. 83 (4), 358–362. doi: 10.1094/CC-83-0358
Rossignolo J. A., Felicio A. J., Duran P., Bueno C., Eduardo J., Filho M., et al. (2022). Algae application in civil construction: A review with focus on the potential uses of the pelagic sargassum spp. biomass. J. Environ. Manage. 303, 114258. doi: 10.1016/j.jenvman.2021.114258
Saghir S., Iqbal M. S., Hussain M. A., Koschella A., Heinze T. (2008). Structure characterization and carboxymethylation of arabinoxylan isolated from ispaghula (Plantago ovata) seed husk. Carbohydr. polymers 74 (2), 309–317. doi: 10.1016/j.carbpol.2008.02.019
Sherwood A. R., Presting G. G. (2007). Universal primers amplify a 23s rDNA plastid marker in eukaryotic algae and cyanobacteria 1. J. Phycol. 43, 605–608. doi: 10.1111/j.1529-8817.2007.00341.x
Sreekumar P. A., Saiah R., Saiter J. M., Lebianc N., Joseph K., Uikrishanan G., et al. (2008). Dynamic mechanical properties of sisal fiber reinforced polyester composites fabricated by resin transfer molding. Soc. Plast. Eng. 30 (6), 768–774. doi: 10.1002/pc.20611
Sudhakar M. P., Magesh Peter D., Dharani G. (2021). Studies on the development and characterization of bioplastic film from the red seaweed (Kappaphycus alvarezii). Environ. Sci. pollut. Res. Int. 28 (26), 33899–33913. doi: 10.1007/s11356-020-10010-z
Surya I., Chong E. W. N., Abdul Khalil H. P. S., Funmilayo O. G., Abdullah C. K., Sri Aprilia N. A., et al. (2021). Augmentation of physico-mechanical, thermal and biodegradability performances of bio-precipitated material reinforced in Eucheuma cottonii biopolymer films. J. Mater. Res. Technol. 12, 1673–1688. doi: 10.1016/j.jmrt.2021.03.055
Vega D., Villar M. A., Failla M. D., Valles E. M.. (1996). Thermogravimetric analysis of starch-based biodegradable blends. Polymer Bull. 37, 229–235. doi: 10.1007/BF00294126
Waheed Q. M. K., Maqsood S., Nawaz R., Aqeel A. B. (2015). “Investigation of thermal behavior and kinetic analysis of Pakistani biomass: Rice husk, sugarcane bagasse and wheat straw using thermogravimetric analysis,” in Proceedings of the 2015 Power Generation System and Renewable Energy Technologies (PGSRET), Islamabad, Pakistan, 10–11 June. (IEEE) pp. 1–7. doi: 10.1109/PGSRET.2015.7312212
Wang G. E., Shi S. Q., Wang J., Cao S., Cheng H. (2011). Micro tension test method for measuring tensile properties of individual cellulosic fibers. Wood Fiber Sci. 43 (3), 1–11.
White J. E., Catallo W. J., Legendre B. L. (2011). Biomass pyrolysis kinetics: A comparative critical review with relevant agricultural residue case studies. J. Anal. Appl. Pyrolysis 91, 1–33. doi: 10.1016/j.jaap.2011.01.004
Youning C., Wei Z., Huan W., Xiaohua M., Linjie Z. (2018). A novel polyamine-type starch/glycidyl methacrylate copolymer for adsorption of PB(II), CU(II), CD(II) and CR(III) ions from aqueous solutions. R. Soc. Open Sci. 5, 180281. doi: 10.1098/rsos.180281
Zanchetta E., Damergi E., Patel B., Borgmeyer T., Pick H., Pulgarin A., et al. (2021). Algal cellulose, production and potential use in plastics: Challenges and opportunities. Algal Res. 56, 102288. doi: 10.1016/j.algal.2021.102288
Keywords: algae, bioplastics, FTIR, Plantago ovata, polyethylene glycol, plasticizer, Ulva
Citation: El Semary N, Alsuhail M, Al Amer K and AlNaim A (2022) Applications of algae for environmental sustainability: Novel bioplastic formulation method from marine green alga. Front. Mar. Sci. 9:1047284. doi: 10.3389/fmars.2022.1047284
Received: 17 September 2022; Accepted: 21 November 2022;
Published: 19 December 2022.
Edited by:
Gehan Ismail, Tanta University, EgyptReviewed by:
Misri Gozan, University of Indonesia, IndonesiaMathimani T., National Institute of Technology, Tiruchirappalli, India
Copyright © 2022 El Semary, Alsuhail, Al Amer and AlNaim. This is an open-access article distributed under the terms of the Creative Commons Attribution License (CC BY). The use, distribution or reproduction in other forums is permitted, provided the original author(s) and the copyright owner(s) are credited and that the original publication in this journal is cited, in accordance with accepted academic practice. No use, distribution or reproduction is permitted which does not comply with these terms.
*Correspondence: Nermin El Semary, bmVsc2VtYXJ5QGtmdS5lZHUuc2E=