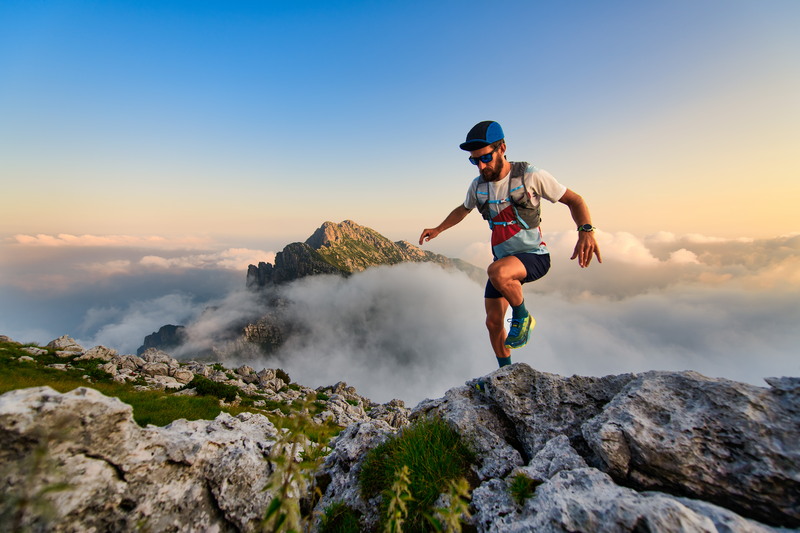
95% of researchers rate our articles as excellent or good
Learn more about the work of our research integrity team to safeguard the quality of each article we publish.
Find out more
PERSPECTIVE article
Front. Mar. Sci. , 24 August 2021
Sec. Ocean Observation
Volume 8 - 2021 | https://doi.org/10.3389/fmars.2021.669413
This article is part of the Research Topic Advancing Ocean Observing Technology and Industry - Science Partnerships for the Future of Ocean Science View all 12 articles
Governments are increasingly turning toward public–private partnerships to bring industry support to improving public assets or services. Here, we describe a unique public–private collaboration where a government entity has developed mechanisms to support public and private sector advancement and commercialization of monitoring technologies for marine renewable energy. These support mechanisms include access to a range of skilled personnel and test facilities that promote rapid innovation, prove reliability, and inspire creativity in technology development as innovations move from concept to practice. The ability to iteratively test hardware and software components, sensors, and systems can accelerate adoption of new methods and instrumentation designs. As a case study, we present the development of passive acoustic monitoring technologies customized for operation in energetic waves and currents. We discuss the value of testing different systems together, under the same conditions, as well as the progression through different test locations. The outcome is multiple, complementary monitoring technologies that are well suited to addressing an area of high environmental uncertainty and reducing barriers to responsible deployment of low-carbon energy conversion systems, creating solutions for the future.
Public–private partnerships (PPPs) are efficient mechanisms that bring industry needs and knowledge into public services. They are widely used to ensure quality at an optimal price, particularly for public infrastructure and services (Roehrich et al., 2014). This framework for quality and public responsibility also applies to research and development (e.g., Wilczak et al., 2015; Shaw et al., 2019 for wind energy forecasting).
The United States Department of Energy (DOE) Water Power Technologies Office (WPTO) is employing multiple approaches to research and development (R&D) that advance the marine renewable energy (MRE) industry. These include PPPs to develop monitoring technologies that can help to identify and mitigate impacts from MRE generation systems (Copping and Hemery, 2020). Providing academia and commercial entities access to testing sites, development facilities, and expertise enhances all stages of R&D across multiple scales, while bringing in new ideas and perspectives. Finding innovative ways to enable these partnerships is critical to their success, and WPTO has achieved this with the Triton Initiative, a PPP.
This perspective article discusses the Triton PPP, with a focus on distinct and complementary acoustic monitoring technologies. We highlight the value and effectiveness of the Triton program to accelerate deployment of MRE monitoring systems through collaborative, multi-scale testing procedures over a range of environmental conditions.
The Triton PPP supports R&D and advancement of technologies for MRE applications, including environmental monitoring capabilities necessary to progress the industry in a sustainable manner. Triton is spearheaded by the Pacific Northwest National Laboratory’s Marine and Coastal Research Laboratory (PNNL’s MCRL), which provides facilities and technical support for Triton projects focused on underwater noise, electromagnetic fields, marine organism interaction, benthic habitat mapping, and integrated sensor packages.
A key element of Triton is access to vessels and skilled personnel at marine testing locations that are permitted for a range of environmental monitoring system deployments. Testing locations include a quiescent site, tidally energetic area, deeper water site, and a site with consistent waves – all accessed from a single shore facility. This facilitates technology readiness level (TRL) advancement from proof-of-concept to commercialization by enabling baseline field-testing, design comparisons to existing technologies, benchmark improvements, and field demonstrations.
In 2016, WPTO released a Triton funding opportunity announcement to develop and/or advance environmental monitoring systems that could overcome limitations with existing technologies in energetic environments. This included electromagnetic field measurements, benthic habitat surveys, acoustic target detection, optical imaging, and passive acoustic monitoring of radiated noise from marine energy converters. For the latter, two technologies were selected – one from commercial business (Integral Consulting Inc.) and one from academia (University of Washington). Both project teams leveraged MCRL support and expertise, and benefited from broader collaboration that emerged under the PPP.
Many industrial activities associated with MRE installation, operation, and decommissioning generate anthropogenic sounds that overlap spatially, temporally, and in bandwidths pertinent to marine fauna (Copping and Hemery, 2020). Monitoring potential disturbances and the correlated vocal reactions by marine fauna will inform mitigation efforts of regulatory and stakeholder relevance. Radiated noise from MRE devices must also not exceed regulatory thresholds for acoustic harassment [National Marine Fisheries Service (NMFS), 2018]. While passive acoustic monitoring in the marine environment is common (Sousa-Lima et al., 2013), MRE monitoring requires accurate measurements in energetic currents (>1 m/s speed) and waves (>2 m height). Further, given the limited understanding of noise radiated by MRE systems, passive acoustic monitoring must be able to differentiate between MRE noise and other natural or anthropogenic sources, as well as comply with international standards [International Electrotechnical Commission (IEC), 2019] to increase transferability of data across sites and systems.
The Triton PPP facilitated collaborative testing that was conducted at several locations near MCRL, which is located at the mouth of Sequim Bay in Washington State, United States. The bay is a sheltered body adjacent to the Strait of Juan de Fuca and is roughly 3.2 km long and 1.6 km wide at the mouth. The maximum water depth in the bay is 35 m, with the bottom consisting primarily of mud. Sequim Bay is tidally influenced, with tidal ranges from 1.5 m (neap tide) to 2.5 m (spring tide) [National Oceanic and Atmospheric Administration (NOAA), 2021]. Acoustic testing was conducted in four areas: a relatively shallow, quiescent site near the middle of Sequim Bay (SB2; ∼25 m); the mouth of the Bay in the energetic tidal channel (MSL; ∼10 m); in deeper-water in Dungeness Bay (>50 m); and in Clallam Bay, an energetic location in the Strait that is subject to stronger waves (Figure 1).
Figure 1. Triton Initiative test sites: SB2, MSL, Dungeness Bay, and Clallam Bay, located along Washington State’s (United States) northern coast.
NoiseSpotter® is a passive acoustic monitoring device developed by Integral Consulting Inc. (Integral) to characterize, classify, and provide accurate location information, in near real-time, for underwater anthropogenic and natural sounds (Raghukumar et al., 2020). It consists of a compact array of particle motion sensors that measure acoustic pressure and three-dimensional particle velocities associated with the propagation of an acoustic wave, enabling triangulation of individual bearings and sound source localization with a single unit (Raghukumar et al., 2020). These sensors (GeoSpectrum Technologies Inc.) measure tri-axial particle motion and omnidirectional pressure at a frequency range of 50 Hz – 3 kHz, at a sample rate of 20 kHz, as well as earth-referenced orientation with an integrated inertial measurement unit (IMU).
At the beginning of the project, NoiseSpotter® was at TRL 4 (bench-scale prototype). Four advancements were required to achieve TRL 8 (field-tested commercial prototype):
• Develop continuous and synchronous data logging and real-time transmission
• Improve data quality, detection sensitivity, and location estimation by minimizing electronic, system, and flow-noise interferences
• Increase the power budget to achieve autonomous operation for at least 7 days
• Create a portable system with modular configuration capabilities to facilitate field operations for a wide range of environments.
These advancements were facilitated through a series of five field-tests, supported by the Triton PPP, conducted at SB2, MSL, and Dungeness Bay (Figure 1). Field-tests involved moored deployments of the NoiseSpotter® V1–V4 and controlled acoustic source-signal transmissions over a range of source-receiver separation distances. The original NoiseSpotter® V1 design was a linear particle motion sensor array on a mid-water column mooring with each sensor cabled to an off-the-shelf data logger and battery pack, housed in a surface buoy (Figure 2A). Testing at SB2 helped identify several issues, primarily stemming from the mid-water column design. Issues included system instability and acoustic contamination, cable-induced signal losses of 8 dB, and difficulties with field operations due to unwieldy cables. Data logger self-noise was observed at multiple frequencies, as well as high-amplitude sound at low frequencies (<200 Hz), indicative of flow-noise (Strasberg, 1979; Bassett et al., 2014).
Figure 2. (A–D) Photographs of Integral Consulting Inc.’s NoiseSpotter® design iterations from V1 through V4, respectively. (E,F) Schematic diagram of University of Washington’s DAISY design. (G) Schematic diagram of Oregon State University’s spar buoy drifting hydrophone. (H) Concurrent benchmarking of DAISYs and SBDH at SB2.
These issues were mitigated by redesigning NoiseSpotter® such that the sensors, data logger, and batteries were mounted on a stable bottom platform (Figures 2B–D), thereby reducing cable lengths from 15 m to <1 m. Further improvements were made by incorporating a custom, low-power, low-noise, high-capacity data logger, and custom flow-noise shields (Raghukumar et al., 2019). Particle motion sensors with flow-noise shields were vertically and horizontally separated on the bottom platform (Figures 2C,D) to facilitate accurate geolocation estimation. The data logger pressure housing was designed and fabricated with the support of MCRL under the Triton PPP.
Field-tests of the NoiseSpotter® V2–3 (TRL 5–6) at SB2, MSL, and Dungeness Bay demonstrated simplified deployment, zero cable-induced signal losses, no platform instability, little to no data logger self-noise, reduced power requirements (by ∼1 A), increased data storage (by ∼2 TB), and flow-noise reduction of ∼10 dB. The remaining issues for the NoiseSpotter® V3 design included mitigating potential acoustic reflectance from aluminum, time-consuming system mobilization, and insufficient power. NoiseSpotter® V4a,b (TRL 7, 8) was thus redesigned with modular, high-density polyethylene frames (Figure 2D; Raghukumar et al., 2020) to reduce acoustic reflectance potential and custom 258 Ahr rechargeable battery packs. NoiseSpotter® V4b includes onboard real-time data processing and telemetry of acoustic data metrics to a cloud server.
The Triton PPP undoubtedly accelerated development for the NoiseSpotter®. Three different, permitted test locations, and the collaborative environment facilitated by the PPP helped overcome design challenges ranging from data and power budgets, electronic and environmental acoustic interference, to difficulties with field operations. Integral is currently transitioning NoiseSpotter® from research-grade to a commercial acoustic monitoring device (United States Utility Patent No. 16/879,434; approved) and is a product available for lease with contracted services for operation and data analysis.
The Drifting Acoustic Instrumentation SYstem (DAISY) was developed by the University of Washington (UW). The DAISY’s primary sensor is a hydrophone sensitive to acoustic pressure. Unlike NoiseSpotter®, source localization requires multiple time-synchronized DAISYs to be deployed around an MRE device, but the resolvable frequency range is wider (1 Hz–200 kHz). As previously mentioned, relative motion between a hydrophone and surrounding water produces high-amplitude, low-frequency pressure and velocity fluctuations (advected and shed turbulence) that are indistinguishable from propagating sound (Strasberg, 1979; Bassett et al., 2014) and can mask radiated noise from MRE devices. Because of this, the DAISY is designed to drift with the prevailing metocean forcing, a suspension system decouples the hydrophone and logger from the surface expression with GPS tracking, and, when drifting in currents, a flow shield (inspired by Wilson et al., 2014) is employed to create a quiescent pocket around the hydrophone.
The DAISY V1 (TRL 5) was a modified version of a SWIFT buoy used to measure wave dissipation (Thomson, 2012). A rigid hull coupled a hydrophone (Loggerhead Instruments DSG) at 1 m depth to a surface expression for tracking. This approach was effective at minimizing flow-noise in unidirectional river currents (Polagye and Murphy, 2015), but resulted in significant flow-noise and self-noise in wavy environments. Further, the hydrophones could not be synchronized for source localization. The DAISY V1.5 (TRL 6), initially tested at the MSL and SB2 sites, replaced the rigid spar with a 2.5 m rubber cord, incorporated a flow shield, and changed the hydrophone to an OceanSonics icListen HF to allow multi-DAISY synchronization.
Ideally, technology development proceeds linearly through TRLs, but for DAISY development, it was necessary to take a few steps back to move forward. The OceanSonics hydrophone constituted >80% of the total system cost and, because it was designed for stand-alone deployment, the batteries, clock, and onboard processors were redundant with the DAISY’s. For these reasons, UW developed a custom data acquisition board for an HTI-99-UHF built around a low-cost microcontroller (BeagleBone Black). This required several iterations to minimize electrical self-noise, particularly at frequencies about 10 kHz, such that the DAISY regressed to TRL 4/5, before advancing to TRL 7 (Figure 2E) in recent testing at MSL and SB2. Similar iterations were also required to design and manufacture a flow shield with sufficient durability.
To support commercialization, UW partnered with MarineSitu Inc. to provide a commercial version of DAISY for purchase or lease, as well as contracted monitoring services and data processing. The primary goal of this partnership is to ensure that DAISY technology is made available to the greater marine industry, rather than remaining an academic research tool. As a UW spin-off company, MarineSitu’s technology translation is supported by CoMotion, UW’s commercialization office. MarineSitu is working with CoMotion to license the underlying technology and develop marketing materials for the DAISY.
One of the Triton PPP objectives was benchmarking performance of new systems against existing technologies. A spar buoy drifting hydrophone (SBDH), developed by Oregon State University (OSU), served as the benchmark system for acoustic measurements and characterization of MRE devices and background sound levels. The SBDH has been operated at several open ocean project sites off the Oregon coast (e.g., PacWave, Camp Rilea, and Charleston) and consists of a broadband hydrophone (10 Hz–20 kHz) mounted on a 3 m long, 10.15 cm diameter PVC spar buoy with lead ballast near the bottom for increased inertial moment (Figure 2G). A shock cord is soft-tethered to the spar buoy, followed by a static line of variable length depending on the project site. The static line is connected to a motion damping disc or heave plate, followed by the suspended hydrophone instrument. Unlike the NoiseSpotter® and DAISY, the SBDH does not support synchronized timing and cannot be used for source localization.
In addition to individual support offered to NoiseSpotter® and DAISY technology R&D, the Triton PPP facilitated co-located field-testing of the NoiseSpotter®, DAISY, and SBDH systems for unique benchmark comparisons in quiescent and high-energy environments (Figure 2H). Benchmark comparison testing consisted of three objectives:
1. Compare acoustic recordings in quiescent conditions in Sequim Bay with light currents and no wave action for system noise floor evaluations. The SBDH and three DAISYs were deployed in close proximity (<5 m) for these tests. The NoiseSpotter® was deployed on the seabed and DAISYs and SBDH drifted over it.
2. Compare acoustic recordings in more energetic current conditions at the MSL site (Figure 1). The NoiseSpotter® was deployed on the seabed and DAISYs drifted over it.
3. Compare acoustic recordings in more energetic wave conditions at the Clallam Bay site (Figure 1). The SBDH and three DAISYs were deployed in close proximity and at similar depths (12 m) for an evaluation of measured noise levels during higher energy conditions. In Clallam Bay tests, the DAISY suspension system consisted of a rubber cord and heave plate and did not include a flow shield (Figure 2F).
Results from these tests were encouraging. Benchmark comparisons between the DAISY and SBDH resulted in nearly identical response in the frequency bands of highest interest for MRE radiated noise (10 Hz–3 kHz) in waves and the quiescent environment. Quiescent testing also identified high frequency, broadband electrical noise in the prototype DAISY. Similarly, a comparison with a shielded broadband hydrophone on the NoiseSpotter® platform demonstrated that the drifting, shielded DAISY had a noise floor roughly 20 dB lower than a fixed, shielded hydrophone at frequencies <100 Hz. Beyond the technical outcomes from this testing, the experience of shared field operations with academic and industrial colleagues allowed all parties to pass on best practices and better understand the strengths and weaknesses of each system.
Under the Triton PPP, MRCL supported the project teams in multiple ways. All field-testing involving NoiseSpotter® and DAISY were conducted aboard MCRL vessels and their staff participated in deployment and recovery operations. MCRL consolidated all necessary permits and environmental reviews for field testing, reducing the administrative load on the technology teams and the compliance burden for federal and state resource managers. Acoustic sources employed during field-testing, and ancillary environmental data (e.g., conductivity-temperature-depth and current velocity) were collected by MCRL. NoiseSpotter® and DAISY development further benefited from technical expertise and capabilities at MCRL, with electrical engineering staff providing input on the design and fabrication of the custom data logger for the NoiseSpotter® as well as initial design of the custom hydrophone acquisition board for the prototype DAISYs.
The NoiseSpotter® and DAISY each started at different TRLs but benefited equally from government-supported facilities and expertise, while also gaining the opportunity to collaborate and improve their systems. Multiscale acoustic testing facilitated by the Triton PPP allowed for comparison of various technological approaches (e.g., moored versus drifting, near-surface versus near-bottom, and sound pressure versus pressure/particle motion) that have been developed to assess sound from MRE installations. Having technology-agnostic facilities enabled systematic testing of different technologies throughout the R&D process, with rapid turnarounds from in-water testing, to bench improvements, and back to in-water testing. Each of the technological solutions advanced under the Triton PPP have unique capabilities, while simultaneously accommodating specific engineering tradeoffs that include flow-noise suppression, deployment duration, sensitivity, frequency range, and cost. Testing of systems at a common facility allows for objective evaluation of each system’s capabilities and tradeoffs regarding their use in acoustic characterization of MRE installations. These tests served to build confidence in the technology design and approach used for measuring and characterizing MRE radiated noise.
Several factors contributed to the success of Triton; these practices are recommended for other technology development PPPs. First, MCRL played an independent, convening role for all project teams, allowing lessons learned from one test to transfer seamlessly to another. National laboratories are well positioned for this function, particularly when they are technology-agnostic. Second, WPTO encouraged teams to collaborate transparently and emphasized the overall success of the Triton PPP, rather than individual outcomes. This provided a strong incentive for teams to share knowledge and expertise. Similarly, as teams identified additional opportunities to work together outside of the original workplan, WPTO provided additional resources to MCRL to support these efforts – the combined benchmarking system test of the NoiseSpotter®, DAISY, and SBDH systems was one such activity. Third, while team members for the acoustic measurement projects had not worked extensively together before Triton, all were professionally acquainted and came into the project from a position of mutual respect. This demonstrates the benefits of informal, collaborative research communities.
The ability to access publicly funded facilities that employ consistent methods and testing procedures, enables sharing of knowledge and rapid innovation, benefiting all aspects of R&D. It is hoped that the success of Triton and related PPPs such as the European Marine Energy Centre Ltd., and DOE Testing Expertise and Access for Marine Energy Research (TEAMERTM) program provide blueprints for additional PPPs that advance technology development spanning the MRE and oceanographic industries. A critical factor is the availability of a range of testing sites with different conditions that are suitable for technologies at different stages of development, coupled with the opportunity to work with other researchers who are developing related technologies.
The original contributions presented in the study are included in the article; further inquiries can be directed to the corresponding author/s.
GH-K and GC conceived the idea of this Perspective article. GC, KR, BP, JH, JJ, GS, and FS designed and participated in the multiscale and co-testing case study. All authors wrote sections of the manuscript and contributed to manuscript revision, read, and approved the submitted version.
This material was based on work supported by the United States Department of Energy’s Office of Energy Efficiency and Renewable Energy (EERE) under the Water Power Technologies Office Award Numbers DE-EE0007822 (KR and GC) and DE-EE0007823 (BP). PNNL is managed by Battelle Memorial Institute under Contract No. DE-AC05-76RL01830 with the United States Department of Energy.
This material was prepared as an account of work sponsored by an agency of the United States Government. Neither the United States Government nor any agency thereof, nor any of their employees, makes any warranty, express or implied, or assumes any legal liability or responsibility for the accuracy, completeness, or usefulness of any information, apparatus, product, or process disclosed, or represents that its use would not infringe privately owned rights. Reference herein to any specific commercial product, process, or service by trade name, trademark, manufacturer, or otherwise does not necessarily constitute or imply its endorsement, recommendation, or favoring by the United States Government or any agency thereof. The views and opinions of authors expressed herein do not necessarily state or reflect those of the United States Government or any agency thereof.
GC, KR, and FS are employed by Integral Consulting Inc., and JJ is employed by MarineSitu Inc.
The remaining authors declare that the research was conducted in the absence of any commercial or financial relationships that could be construed as a potential conflict of interest.
All claims expressed in this article are solely those of the authors and do not necessarily represent those of their affiliated organizations, or those of the publisher, the editors and the reviewers. Any product that may be evaluated in this article, or claim that may be made by its manufacturer, is not guaranteed or endorsed by the publisher.
GC, KR, and FS wish to acknowledge Sean Griffin and Jesse Spence for their assistance with NoiseSpotter® technology development and testing; and Craig Jones, Sharon Kramer, and Jesse Roberts for project support. GH-K, GS, and JH wish to acknowledge the key contribution of the field team at the Marine and Coastal Research Laboratory, and Andrea Copping for working through ideas that led to this article. BP wishes to acknowledge the contributions of Corey Crisp, Jessica Noe, Paul Murphy, and Christopher Bassett of the University of Washington to the development of DAISY technology.
Bassett, C., Thomson, J., Dahl, P. H., and Polagye, B. (2014). Flow-noise and turbulence in two tidal channels. J. Acoust. Soc. Am. 135, 1764–1774. doi: 10.1121/1.4867360
Copping, A. E., and Hemery, L. G. (2020). OES-Environmental 2020. State of the Science Report (No. PNNL-29976). Richland, WA: Pacific Northwest National Laboratory (PNNL).
International Electrotechnical Commission (IEC) (2019). Technical Specification 62600-40: Marine energy-Wave, Tidal and Other Water Current Converters-Part 40: Acoustic characterization of marine energy converters. Geneva: International Electrotechnical Commission.
National Marine Fisheries Service (NMFS) (2018). 2018 Revisions to: Technical Guidance for Assessing the Effects of Anthropogenic Sound on Marine Mammal Hearing (Version 2.0): Underwater Thresholds for Onset of Permanent and Temporary Threshold Shifts. Silver Spring, MD: NOAA Technical Memorandum NMFS-OPR-59, 167.
National Oceanic and Atmospheric Administration (NOAA) (2021). https://tidesandcurrents.noaa.gov/stationhome.html?id=9444555 [accessed February 16, 2021].
Polagye, B., and Murphy, P. (2015). “Acoustic characterization of a hydrokinetic turbine,” in Proceedings of the 11th European Wave and Tidal Energy Conference, September 6–11, 2015, Nantes, France. Seattle, WA: University of Washington.
Raghukumar, K., Chang, G., Spada, F., and Jones, C. (2020). A vector sensor-based acoustic characterization system for marine renewable energy. J. Mar. Sci. Eng. 8:187. doi: 10.3390/jmse8030187
Raghukumar, K., Chang, G., Spada, F., Jones, C., Spence, J., Griffin, S., et al. (2019). “Performance characteristics of a vector sensor array in an energetic tidal channel,” in Proceedings of the Fifth Underwater Acoustics Conference and Exhibition, ed. J. S. Papadakis (Crete, Greece), 653–658.
Roehrich, J. K., Lewis, M. A., and George, G. (2014). Are public–private partnerships a healthy option? A systematic literature review. Soc. Sci. Med. 113, 110–119. doi: 10.1016/j.socscimed.2014.03.037
Shaw, W. J., Berg, L. K., Cline, J., Draxl, C., Djalalova, I., Grimit, E. P., et al. (2019). The second wind forecast improvement project (wfip2): general overview. Bull. Am. Meteorol. Soc. 100, 1687–1699. doi: 10.1175/BAMS-D-18-0036.1
Sousa-Lima, R. S., Norris, T. F., Oswald, J. N., and Fernandes, D. P. (2013). A review and inventory of fixed autonomous recorders for passive acoustic monitoring of marine mammals. Aquat. Mamm. 39, 205–210. doi: 10.1578/am.39.2.2013.205
Strasberg, M. (1979). Nonacoustic noise interference in measurements of infrasonic ambient noise. J. Acoust. Soc. Am. 66, 1487–1493. doi: 10.1121/1.383543
Thomson, J. (2012). Wave breaking dissipation observed with “SWIFT” drifters. J. Atmos. Ocean. Technol. 29, 1866–1882. doi: 10.1175/jtech-d-12-00018.1
Wilczak, J., Finley, C., Freedman, J., Cline, J., Bianco, L., Olson, J., et al. (2015). The wind forecast improvement project (WFIP): a public–private partnership addressing wind energy forecast needs. Bull. Am. Meteorol. Soc. 96, 1699–1718. doi: 10.1175/BAMS-D-14-00107.1
Wilson, B., Lepper, P. A., Carter, C., and Robinson, S. P. (2014). “Rethinking underwater sound-recording methods to work at tidal-stream and wave-energy sites,” in Marine Renewable Energy Technology and Environmental Interactions, eds M. A. Shields and A. I. L. Payne (Dordrecht: Springer), 111–126. doi: 10.1007/978-94-017-8002-5_9
Keywords: marine renewable energy, acoustics, underwater sound, public–private, commercialization, environmental monitoring, technology
Citation: Chang G, Harker-Klimeš G, Raghukumar K, Polagye B, Haxel J, Joslin J, Spada F and Staines G (2021) Clearing a Path to Commercialization of Marine Renewable Energy Technologies Through Public–Private Collaboration. Front. Mar. Sci. 8:669413. doi: 10.3389/fmars.2021.669413
Received: 18 February 2021; Accepted: 30 July 2021;
Published: 24 August 2021.
Edited by:
Wayne Homer Slade, Sequoia Scientific, Inc., United StatesReviewed by:
Ann Clarke, University of Southern Denmark, DenmarkCopyright © 2021 Chang, Harker-Klimeš, Raghukumar, Polagye, Haxel, Joslin, Spada and Staines. This is an open-access article distributed under the terms of the Creative Commons Attribution License (CC BY). The use, distribution or reproduction in other forums is permitted, provided the original author(s) and the copyright owner(s) are credited and that the original publication in this journal is cited, in accordance with accepted academic practice. No use, distribution or reproduction is permitted which does not comply with these terms.
*Correspondence: Grace Chang, Z2NoYW5nQGludGVncmFsLWNvcnAuY29t
Disclaimer: All claims expressed in this article are solely those of the authors and do not necessarily represent those of their affiliated organizations, or those of the publisher, the editors and the reviewers. Any product that may be evaluated in this article or claim that may be made by its manufacturer is not guaranteed or endorsed by the publisher.
Research integrity at Frontiers
Learn more about the work of our research integrity team to safeguard the quality of each article we publish.