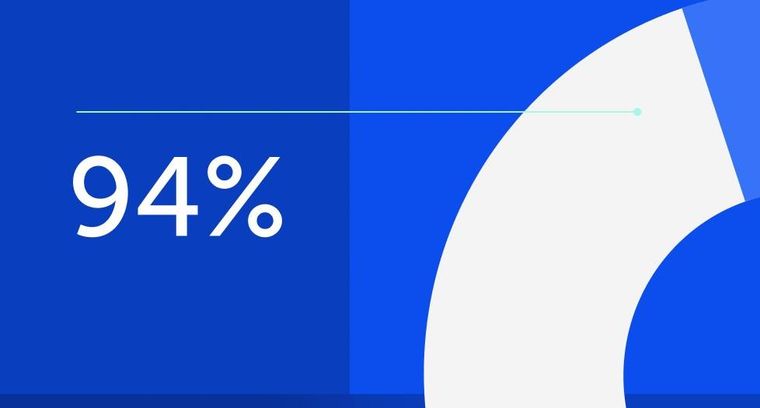
94% of researchers rate our articles as excellent or good
Learn more about the work of our research integrity team to safeguard the quality of each article we publish.
Find out more
EDITORIAL article
Front. Manuf. Technol.
Sec. Precision Engineering
Volume 5 - 2025 | doi: 10.3389/fmtec.2025.1608699
This article is part of the Research TopicAdvances of Finite Element Methods in the Precision Manufacturing ProcessesView all 5 articles
The final, formatted version of the article will be published soon.
Select one of your emails
You have multiple emails registered with Frontiers:
Notify me on publication
Please enter your email address:
If you already have an account, please login
You don't have a Frontiers account ? You can register here
Manufacturing encompasses various physical phenomena, including processes for burr creation, plastic deformation, frictional contact, and thermo-mechanical coupling, among others. Undoubtedly, the most prevalent method for simulating manufacturing processes (A.S. Wifi and E.A. Orady,1985) is the finite element method (FEM). The FEM, which has been continuously developing, can replicate experimental techniques to analyze manufacturing processes, especially when a vast array of intricate characteristics are involved, such as process parameters, non-linearity, complex workpiece materials and geometries, composite/multi-layered materials, shape memory alloys, and tool types. Therefore, "Advances of FEM in Precision Machining Processes" provides a concise analysis of the FEM's application to manufacturing processes (Fritz Klocke et al.,2002;R. Quiza et al.,2012 ). Current experimental data can be utilized to design and calibrate a finite element study. The difficulty in obtaining information near the cutting tool, which cannot be easily measured through experiments (many of which are laborious and expensive), such as strain, strain rate, the cutting force, and temperature, has driven researchers to gain a more profound understanding of the metal cutting mechanism via FEM. Furthermore, the material constitutive law regarding flow stresses, the type of friction present at the tool-chip interface, and fracture control are all highly significant to the FEM analysis of machining issues (Quiza et al.,2012). The constitutive models applied in manufacturing processes and the following FE simulations to comprehend the characteristics (surface roughness, residual stresses, micro-hardness, plastic deformation, phase transitions, elastic recovery effect, ball indentation, and thermal behavior, etc.) are gaining increasing In this subject, the authors study focused on the modeling, internal structure examination, and 116 automation of a cassava grinding machine. For the design, the single-cylinder grinder was selected 117 because of its advantages, particularly simplicity and versatility. The automation of the grinder was 118 implemented using a GRAFCET model and an advanced human-machine interface (HMI), adding an 119 extra safety feature for the machine and enabling the operator to oversee the operation through an 120 easy graphical interface. This automation facilitates continuous operation with minimal human 121 involvement, thus enhancing the efficiency and safety of the cassava grinding process. 122This Research Topic on Advances of Finite Element Methods in the Precision Manufacturing 123Processes marks the recent advances and insights in the field of structural mechanics and the growing 124 interest in academic and applied research. We hope that the topic is interesting with the rapid 125 development of manufacturing approaches, and methods, for new potential applications in the fields 126 of additive manufacturing, metallic powder bed AM processes, optimization of manufacturing
Keywords: manufacturing, FE modeling, machining, rolling, Welding, Sheet metal, Laser peening, Additive manufactuirng
Received: 09 Apr 2025; Accepted: 21 Apr 2025.
Copyright: © 2025 Pany, Desai and Rossi. This is an open-access article distributed under the terms of the Creative Commons Attribution License (CC BY). The use, distribution or reproduction in other forums is permitted, provided the original author(s) or licensor are credited and that the original publication in this journal is cited, in accordance with accepted academic practice. No use, distribution or reproduction is permitted which does not comply with these terms.
* Correspondence: Chitaranjan Pany, Vikram Sarabhai Space Centre, Thiruvananthapuram, India
Disclaimer: All claims expressed in this article are solely those of the authors and do not necessarily represent those of their affiliated organizations, or those of the publisher, the editors and the reviewers. Any product that may be evaluated in this article or claim that may be made by its manufacturer is not guaranteed or endorsed by the publisher.
Supplementary Material
Research integrity at Frontiers
Learn more about the work of our research integrity team to safeguard the quality of each article we publish.