- 1Department of Industrial and Materials Science, Chalmers University of Technology, Gothenburg, Sweden
- 2Department of Social Sciences, Technology and Arts, Luleå University of Technology, Luleå, Sweden
- 3National Institute of Standards and Technology, Gaithersburg, MD, United States
- 4Morgan State University, Baltimore, MD, United States
- 5School of Engineering, The University of Tokyo, Tokyo, Japan
- 6Department of Management, Economics and Industrial Engineering, Politecnico di Milano, Milan, Italy
- 7Chalmers Industriteknik, Gothenburg, Sweden
- 8Department of Chemistry—Ångström Laboratory, Uppsala University, Uppsala, Sweden
- 9Global Industrial Development, Scania, Södertälje, Sweden
Advanced manufacturing research for sustainable battery life cycles is of utmost importance to reach net zero carbon emissions (European Commission, 2023a) as well as several of the United Nations Sustainable Development Goals (UNSDGs), for example: 30% reduction of CO2 emission, 10 million job opportunities and access to electricity for 600 million people (World Economic Forum, 2019). This editorial paper highlights international motivations for pursuing more sustainable manufacturing practices and discusses key research topics in battery manufacturing. Batteries will be central to our sustainable future as generation and storage become key components to on-demand energy supply. Four underlying themes are identified to address industrial needs in this field: 1. Digitalizing and automating production capabilities: data-driven solutions for production quality, smart maintenance, automation, and human factors, 2. Human-centric production: extended reality for operator support and skills development, 3. Circular battery life cycles: circular battery systems supported by service-based and other novel business models, 4. Future topics for battery value chains: increased industrial resilience and transparency with digital product passports, and next-generation battery chemistries. Challenges and opportunities along these themes are highlighted for transforming battery value chains through circularity and more sustainable production, with a particular emphasis on lithium-ion batteries (LIB). The paper concludes with directions for further research to advance a circular and sustainable battery value chain through utilizing the full potential of digitalization realising a cleaner, more energy-efficient society.
1 Introduction
As electrification of society booms, multifaceted aspects of industrial sustainability need to be considered. The implications for future battery value chains are massive, since production capacities are expected to multiply. The requirement for electric vehicle production is projected to create around 10 million jobs worldwide (Harsdorff et al., 2020). In addition, vehicle electrification is expected to reduce the CO2 emissions from the transportation sector by 30% globally by 2030 (World Economic Forum, 2019). With the pace predicted as of 2020, 30% of the worldwide passenger vehicle fleet will be electric vehicles (EVs) in 2032 (Rietmann et al., 2020). As a result, industrial developments around lithium-ion batteries (LIBs) are expanding. However, LIBs are accompanied with sustainability hurdles which need to be addressed, such as high environmental burden from raw material extractions, biodiversity loss, battery failure mechanisms, fire prevention strategies, and carcinogenic solvents and binders used during manufacturing (Wanger, 2011; Wang et al., 2019; Christensen et al., 2021).
For this paradigm shift to be beneficial for both society and the environment, battery production and battery life cycles need to build on sustainable solutions. Many countries and regions around the world are issuing laws, regulatory frameworks, and standards to support this sustainability transition. Notably, the European Green Deal (Lebedeva et al., 2016) which aims to reach climate neutrality by 2050, has been influential even outside Europe. One of the building blocks of the European Green Deal is its Circular Economy Action Plan. In March 2023, the Japanese government also announced the Growth-oriented, resource-autonomous circular economy strategy (METI, 2023) to accelerate the market development for a circular economy and gain international competitiveness through (i) developing regulations and rules, (ii) expanding policy support, and (iii) strengthening collaboration between industry, government, and academia. China has issued a series of laws for decarbonization and circular economy (Bleischwitz et al., 2022; Shang et al., 2022).
Focusing on batteries, the Global Battery Alliance (2024) and the European Battery Alliance (2024) launched in 2017 with workgroups on topics of importance for this transition including sustainable battery technology, clean energy, mobility, safety, and standardization. The U.S. also passed initiatives aimed at stimulating EV production, such as the Inflation Reduction Act of 2022 which incentivizes domestic supply chains and manufacturing through tax credits (United States Congress, 2022). Another important development in the European regulatory landscape is the Battery Regulation which also has international implications (Melin et al., 2021). In Japan according to the Automobile Recycling Law implemented in 2005, traction batteries must be dismantled for reuse or recycling; however, no regulations yet exist about how dismantled batteries should be processed.
The electrification of the transportation sector, combined with the growth of renewable energy and storage systems, have led to a rapid increase in the number of batteries produced and a continued expansion of the demand for batteries (McKinsey, 2023). The material composition of batteries and production methods employed are key factors in the sustainability of battery production and value chain overall. Future research must include sustainability impact assessments for the full range of systems across the product life cycle. Since this problem statement is multidisciplinary, this paper shines light on the challenges and opportunities for the manufacturing of batteries from a range of perspectives surrounding manufacturing production, supply chains, and business models. The focus is largely on LIBs given their predominance on the market, but the discussions will be broadly applicable to other types of batteries.
Building on a previous review of battery production challenges mostly at European and Swedish levels (Despeisse et al., 2023), this paper expands on key research topics organised in four themes shown in Figure 1 to address industrial needs in this field and to guide collaborative efforts at an international level. The first theme focuses on core topics under the umbrella of Industry 4.0 (Xu et al., 2018) with digitalization and automation to improve battery production performance, including cost, quality, resource efficiency, and reliability. The second theme focuses on human-centeredness to increase the social performance of production systems through competence development, improved workplace design, and supporting technologies such as collaborative robots and extended reality. The third theme focuses on circular battery life cycles to transition to more environmentally sustainable operations by maximising the value from battery life cycles and closing the loop of materials. Finally, the fourth theme covers other key research topics for future battery value chains, such as manufacturing resilience, digital product passports and the industrial implications of next-generation battery chemistries. Each section highlights unique manufacturing challenges related to research areas to be further explored and are of importance for the realization of sustainable battery production.
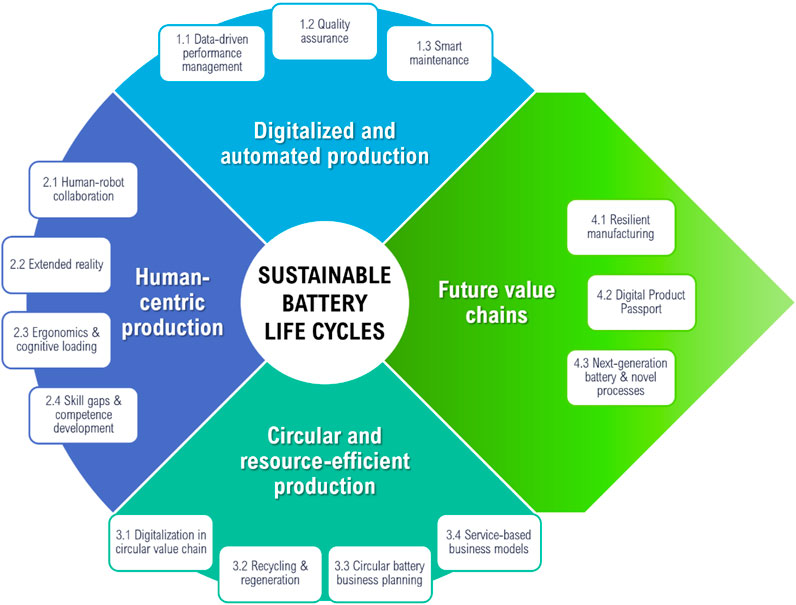
Figure 1. Manufacturing challenges and opportunities under four research themes for sustainable battery life cycles.
2 Digitalized and automated production capabilities
This section introduces challenges and opportunities for digitalizing and automating the production capabilities for battery manufacturing. While the first industrial revolutions (also called Industry 1.0 and 2.0) focused on mechanization and electrification, Industry 3.0 brought about the automation of industrial systems with progress in computer power and robotics enabled new levels of automation. With further advances in the digitalization of factories, the fourth industrial revolution (Industry 4.0) focused on increasing the connection and interactions between systems. While the transition to Industry 4.0 is still ongoing, the European Commission introduced the concept of Industry 5.0 which aims to place sustainability, human-centredness and resilience as central values of for industrial development (European Commission, Directorate-General for Research and Innovation et al., 2021). Figure 2 shows the industrial revolution timeline with key technologies and central industrial concepts enabling the transition between manufacturing paradigms.
The challenges associated with Industry 4.0 and 5.0 are closely tied to automated solutions heavily dependent on data access and transparency within production and across the value chain. Achieving resilient and sustainable battery production will increasingly rely on data-driven solutions for ensuring product quality, enabling production systems maintenance, and using digital product passports to manage information across the value chain. The combined effects of data-driven battery performance management coupled with smart maintenance practices and production improvements are envisioned to multiply the sustainability benefits contributing towards net-zero targets and other ambitious sustainability goals. In addition, other aspects of digitalized production, such as automation for physical and cognitive support, are further discussed in section 2 on human-centric production.
2.1 Data-driven performance management in battery manufacturing
Battery manufacturing has a significant impact on battery operation, quality, maintenance, and service life. Data about batteries (so-called battery data) can help identify how manufacturing affects the performance of battery components, such as pack consistency for LIB (Tian et al., 2020). Battery data has many different data sources at each life cycle stage, providing opportunities for data-driven quality and performance management in battery manufacturing. Digital battery passports (described in section 4.2) will be one mechanism in which battery data can be stored and made accessible across the life cycle. The collection of data on battery use can enable feedback loops into manufacturing production, thereby providing opportunities to improve production processes. For instance, data observations of poor-performing batteries can be correlated to production facilities and even equipment, offering insight into potential sources of flaws.
Battery data can be collected with different approaches like the battery management system, the battery health monitoring and analysis, and the secondary battery system. A battery management system is where key parameters such as voltage and temperature are monitored. It is essential for the EVs quick charging to control energy storage and transfer in batteries (Hannan et al., 2018). Battery health monitoring and analysis tracks battery operation (such as state of charge and state of health) using sensors and data acquisition systems. Collected data are then processed and analysed by algorithms to identify optimizing potential regarding battery lifetime, safety, reliability, efficiency, and cell balancing adjustments (Xing et al., 2011; Omariba et al., 2019). The secondary battery system prioritizes the measure of energy density performance for LIBs, nickel-metal hydride and nickel-cadmium batteries (Dutta et al., 2023).
Emerging studies focus on improving EV battery performance and health utilizing technologies like machine learning algorithms, decentralized data systems, and statistical models (Aenugu et al., 2020; Vidal et al., 2020; Yang et al., 2023). These data-driven approaches enable state-of-charge, state-of-health, and lifetime prediction and adoption of circular strategies of batteries. However, the main challenge is that the identification of patterns and trends is highly reliant on the quantity and quality of collected battery data (Wang L. et al., 2020). The lack of standardized tests and measurements hinders the collection of quality data and the application of data-driven approaches. Generalizability of data-driven approaches can be improved by addressing challenges posed by academia and industry and establishing standards for communication and comparison of results. Data-driven approaches also offer promise to trace problems with batteries back to manufacturing issues. Data-driven quality and performance management can help analyse root causes and develop preventive measures in battery manufacturing.
2.2 Quality assurance of battery production
The cost of the battery constitutes a large share of the total cost of an EV. This cost is though predicted to successively decrease (Nykvist and Nilsson, 2015; Mauler et al., 2021; Shahjalal et al., 2022). The quality of the battery is, in addition to cost, also related to performance, reliability and safety. Methods and strategies to reduce quality losses and identify quality problems are of vital importance for competitiveness and sustainability in modern EV battery production. Focusing on dimensional quality, examples show how variation in the gap between cells in a battery deteriorates the quality of laser welding of the busbars (Sun et al., 2021), how cell-to-cell variation affect the structural behavior of the battery pack (Arora et al., 2018), or how too much pressure in a module (partly) due geometrical deviations, might lead to thermal runways (Zhang et al., 2022).
Battery cells need to meet many different requirements, both material and process related, such as correct levels of moisture in electrode and separator material, but also accurate alignment between the anode and cathode surfaces to ensure that the active materials are in close contact over the entire surface area (Kwade et al., 2018). The dimensional tolerances are usually tight, and Kwade et al. (2018) mention that the tolerance of the thickness of the electrode can typically be around a few μm.
Many aspects of quality assurance can be applied to batteries. Strategies to minimize quality losses can be grouped into:
• Robust design, including simulation techniques
• Improvements in tolerancing
• Quality control measures during production
• Root cause analysis for problem identification
During design phases, robust solutions (i.e., design concepts that are insensitive to variation) should be sought out. Simulation tools can be used to evaluate the effects of different alignment strategies during module and pack assembly (Arora et al., 2018). Several existing computer-aided tolerancing tools can be used for this purpose (Söderberg et al., 2017; Schleich et al., 2018). Tolerancing is also an important activity to secure fulfilment of quality requirements without unnecessarily high costs. The effect of geometric tolerances at the assembly level can be simulated and evaluated using variation simulation and other variation management strategies (Schleich et al., 2018). For quality control in production, inspection is crucial, and also strategies to utilize inspection data to preemptively identify problems through trends analysis. Statistical process control, including multivariate quality control to monitor several dependent variables (Kornas et al., 2019) is an important tool. Also, digital twins for quality improvement can be useful (Söderberg et al., 2017). If quality problems remain, effective methods to identify the root causes of the problem must be applied. As with performance management for the production processes, these types of quality assurance are also dependent on known and good data. Metrology and standards are needed to facilitate appropriate data collection for use in validation of techniques and ultimately to create robust repeatable systems.
2.3 Smart maintenance
Battery manufacturing plants are complex systems characterized by substantial process diversity, large volumes of machinery and equipment, and time-variant process relations (Westermeier et al., 2014). This makes maintenance operations a crucial necessity to achieve high levels of operational performance and the ability to meet the growing demand for cells and packs. However, the specific academic research field of maintenance operations in battery production systems is severely lacking, where current state of the art consists mostly of analytical models of total manufacturing costs that treat maintenance as a negligible overhead cost (Duffner et al., 2021a). To stimulate growth and advancement in this research area, smart maintenance (Brundage et al., 2019; Bokrantz et al., 2020) is used as a theoretical and empirical foundation. The concept of smart maintenance (1) originates from practice and thus appeals to the logic and interest of working professionals, (2) is well-accepted and recognized in scholarly literature, and (3) has been empirically linked to higher maintenance performance and productivity (Bokrantz and Skoogh, 2023). This work outlines a series of opportunities and challenges for the four dimensions of smart maintenance (Bokrantz et al., 2020): data-driven decision-making, human capital resource, internal integration, and external integration.
Data-driven decision-making refers to the degree to which decisions are based on data. Improving maintenance decision-making using data is a major opportunity for battery manufacturers, owing to the highly digitalized greenfield factories that generate large volumes and variety of maintenance-related data. This can be used not only for predictive and prescriptive maintenance planning and scheduling but also to discover unknown process relations such as the influence of observable equipment parameters (e.g., vibration) on battery quality performance. However, such development is also challenging due to the newness of production equipment and the nature of scaling a new industry sector that lacks historical data and knowledge of past failures and behaviors of equipment.
Human capital resource is a unit capacity based on individual knowledge, skills, abilities, and other characteristics (KSAO) that are accessible for unit-relevant performance. Being a part of shaping the emerging battery sector is exciting and motivational to many individuals, and battery manufacturers can therefore attract maintenance talent from both local and global labor markets. Owing to the close link between maintenance and sustainability, talent recruitment can also help to increase the status of maintenance as a profession. Still, battery manufacturers face severe constraints in competence supply and need to put considerable emphasis on continuous up- and re-skilling initiatives.
Internal integration refers to the degree to which the maintenance function is a part of a unified, intra-organizational whole. As battery factories are being built from scratch, manufacturers have great opportunities to shape and form organizational designs where maintenance is closely connected to other functions such as production, quality, and purchasing. With fewer legacy constraints and embedded cultures, maintenance organizations can pursue more information sharing and joint decision-making with other actors. Large investments in IT infrastructure can also support the use of integrative mechanisms such as common data platforms and joint information systems. To be successful with internal integration, manufacturers need to overcome the challenges inherent to dealing with large and fast-scaling organizations where it is difficult to establish momentum in cross-functional initiatives. Maintenance needs to be included in the strategic procurement process at the earliest stage possible to prevent unexpected equipment issues during installation and ramp-up.
External integration is the degree to which the maintenance function is a part of a unified, inter-organizational whole. Learning about machinery and equipment in a new sector requires cross-company collaboration and an emphasis on knowledge-building and sharing from a larger population of the same or similar equipment. Establishing this type of external linkage is a major opportunity for maintenance organizations and is driven by a strong industrial interest in sharing and building maintenance excellence together. There are numerous challenges that originate from the global supply chains of battery production equipment, where maintenance organizations need to deal with geographically dispersed suppliers with variations in maturity, processes, languages and culture.
3 Human-centric production
Human-centric production aspects of the battery value chains include cognitive understanding and interactions of humans in the production environment. The human-centric approach aims at empowering humans both regarding understanding, learning, and gaining insights as well as for decision making. For a production to become/be human-centric, the surrounding resources need to share the right information/content to the human in a cognitive understandable manner as well as at the right time. Since the development of today is heavily centred on digitalizing production systems and data sources, a human-centric approach is needed to filter and present timely, accurate information. For example, learning environments in extended reality (XR) need to convey the data which helps the learner understand and learn skills, collaborative robots need to take heed and support the human. For this to be possible, additional skills are needed both to create human-centric production environments as well as operate and maintain them (Brundage et al., 2019).
3.1 Automation and human-robot collaboration
The advancement of information technology in the third industrial revolution significantly promoted the broad implementation of automation in the modern industry toward mass production (Xu et al., 2018; Leng et al., 2022). While battery components are still mass produced, shifting to mass customization at a product level stimulates transformation toward more flexible and agile automation to fulfil increasingly complex manufacturing tasks and the enlarging market of customized products. Among other automation technologies, robots have demonstrated superiority in conducting repetitive and unergonomic tasks quickly and precisely and have been widely adopted in modern production (Wang Y. et al., 2020). Nevertheless, further research is required to address challenges stemming from the lack of cognitive ability in robots.
More agile robotic solutions are desired to automate material handling processes in battery production involving variants of battery components and products (Sharma et al., 2019). Robotic automation can handle generic pick-and-place tasks and robotic inspection in battery production, especially in module and pace assembly (Kwade et al., 2018) and quality control (Sharma, 2024). However, conventional industrial robots are incompetent in dexterous robotic manipulation required for conducting complex operations in compact workplaces or handling flexible workpieces in components assembly (Sharma et al., 2019). Many variants of battery-powered products exist in current production. Meanwhile, the number of variants is expected to keep increasing with product customization. One of the customizable elements could be batteries for higher power or autonomy. A lack of standards for battery designs also leads to an increasingly varied battery structure and layout, exacerbating the challenge for robotic automation (Castelvecchi, 2021).
The numerous variants enable a higher level of customization but impede robotized battery assembly and disassembly that require agile robotic manipulation based on flexible and adaptive motion and path planning. The robotic control system needs to be adaptable to manipulating different objects (i.e., cells, modules, and other components of batteries) and assembly or disassembly operations in battery production. This adaptation requires advanced perception for a robotic control system for manipulating objects and tasks, where visual perception is critical when considering enriched information in visual inputs. To process visual inputs, computer vision techniques have been introduced to robotics and demonstrated their effectiveness in different production scenarios (Zhou et al., 2023). Particularly for battery production, computer vision techniques have been primarily explored, for example, for disassembly operations where battery cables were identified based on 3D point cloud instance segmentation (Brådland et al., 2022). With the recent successful adaptation of deep learning in computer vision, the potential arises to introduce additional computer vision techniques to enable more intelligent decision-making processes in robotized assembly and disassembly in battery production.
Besides full automation achieved solely by intelligent robots, the lack of agility and cognitive ability in robots stimulates research on human-robot collaboration toward human-centric automation (Wang L. et al., 2020) stressed in the recently proposed Industrial 5.0 (European Commission, Directorate-General for Research and Innovation et al., 2021). Human-robot collaboration is expected to enable the system to benefit from the symbiosis between robotic strengths in high accuracy and repeatability and humans’ superiority in agility and adaptability. In battery production, human-robot collaboration can promote the efficiency and agility of automation to address concerns in terms of labour cost, skilled operator shortage, operation ergonomics, and working environment safety (Kay et al., 2022). Nevertheless, guaranteeing the safety of human operators around robots remains a concern. Conventionally, protective equipment enclosing robots, such as physical barriers or laser curtains, is required in automated production for safety purposes (International Organization for Standardization, 2011a; International Organization for Standardization, 2011b). While in collaborative robot applications, new safety challenges exist as human operators and robots collaborate in closer proximity (Gerbers et al., 2018). Though numerous collision detectors have been proposed, their accuracy and robustness in actual production scenarios demand further improvement (Xiao et al., 2023). Besides passive reactions against potential collisions, computer vision techniques can enable active robotic motion and path planning to avoid collision based on human intention recognition and scene understanding, for example, hand gesture recognition, human action recognition, and indoor scene segmentation (Xiao et al., 2023). The active perception and understanding of human intentions, based on recognition of human gestures, eye movement, and haptics, can also improve human-robot interaction to promote the efficiency of human-robot collaboration in battery production, contributing to more intelligent decision-making processes and efficient and safe battery production.
3.2 Extended reality
Extended reality (XR) has been identified as one of the enabling technologies of Industry 4.0 and beyond (European Commission, Directorate-General for Research and Innovation and Müller, 2020) offering new immersive mediums of human-interaction with virtual, as well as physical, assets of production systems (Fast-Berglund et al., 2018). It is also a technology that could play a vital role in the current transformation of traditional OEM assembly manufacturing towards battery production and processing.
Ramp-up of battery production through green-field factories, along with its new processes and technologies, is being planned for globally, not the least within the EU. Markets that so far have limited previous experience and knowledge of battery production see an increasing need for decision support early on in the production planning and design phase (European Court of Auditors, 2023). By leveraging XR, it is possible to interact with early plans and designs to empower the decision-making process. Early digital assets, such as our factory-, machine- and product-designs can be visualized and interacted with on a higher immersive level (Jerald, 2016). Allowing for more stakeholders to partake in the interaction, knowledge exchange, and decision making prior to physical construction and commissioning (Gong, 2018). Engineers, suppliers, production staff, industry experts and management, from various locations of the globe, can jointly discuss, review, and validate factory layouts and processes on a 1:1 scale digital model. Thus, providing enhanced planning and designs early in the production life cycle.
XR can also support in the operational stage of battery production. It can be regarded as a cognitive support tool for addressing several issues regarding upskilling and reskilling for the operator which are crucial to accelerate the electrification trend (Mourtzis et al., 2022). Various benefits have been identified for XR to improve upskilling speed and quality during each stage of the training and cognitive assistance process. For example, the following benefits are seen in pre-training:
• Multiple stakeholders’ involvement: The multi-user XR platform enables multiple stakeholders involved for comprehensive understanding about the training challenges, opportunities for decision making on site or remotely (Gong et al., 2020).
• Flexibility: The setup of the XR training station could be a separate workstation near the training areas or non-disruptive individual workplace remotely (Gästrin and Winald, 2023).
During training:
• Customization of progress: The progress could be controlled by the operators and the repeatability could be especially beneficial from beginners through difficult sessions.
• Learning by doing: The experiential learning style is realized and pedagogically linked to Kolb’s model (Kolb et al., 2014). Positive reinforcement will bring the release of dopamine as an effective reward when applying gamification during training process (Koepp et al., 1998).
• Simulation of dangerous or crucial tasks: Simulation of the safety issues and failures in infrequent yet potentially dangerous working conditions, including handling of chemicals or high voltages, is essential for the training (Y. Chen et al., 2021).
And in post-training:
• Data-driven iteration of the training process: The evaluation system will be based on the real data during the training process for optimization of the program (Fabijan et al., 2017).
• Cost efficiency: The materials could be scaled up without much marginal costs and be used both as learning and examination tools (Hartzler et al., 2022).
Virtual reality (VR) can facilitate the virtual workstations and procedures and provide immersive experience and training for the operators in a non-disruptive and risk-free virtual environment while in a quick and easy setting (Krichenbauer et al., 2018; Strojny and Dużmańska-Misiarczyk, 2023). While Augmented reality (AR) can be used in the next step of the continuous training in the physical environment for better spatial cognition (Krichenbauer et al., 2018). A framework utilizing multiple XR technologies in sequence is suggested to accelerate the training and support of shopfloor technicians and operators, and thus ultimately accelerating the upskilling and ramp-up of battery manufacturing capabilities.
3.3 Ergonomics and cognitive loading
Battery manufacturing deals with process management which is about controlling flowing chemicals (flow production) in forming the battery cells, and discrete operations (discrete manufacturing) which are required as battery cells are combined into packs and placed in final products (Kwade et al., 2018). These processes are increasingly automated but also require human interventions for visual and manual checks.
When tasks require manual handling, i.e., picking, lifting, and carrying as well as screwing and running nuts, ergonomics analyses can help ensure that the physical loading is kept below safe threshold values so that no overload injuries occur (Berlin and Adams, 2017). The magnitude, duration and frequency of the strains are important factors. The ergonomics literature suggests thresholds for the strains as well as methods for analysing them. The analysis can be based on measurements and observations of the actual work, or computer manikin simulations of the planned work (Lämkull et al., 2005). The results are often communicated with a colour scale where green means safe, yellow means conditionally unsafe and needs further attention, and red means the task is unsafe and needs redesign.
In addition, cognitive loading in battery production relates to various operations and management tasks such as planning and quality control. While cognitive issues are important even in jobs regarded as simple, mental and cognitive conditions related to attention, concentration, adaption, learning, and planning become more pronounced in complex and extensive work tasks. Simpler jobs may increase in complexity particularly when combined in sequences which can vary due to the higher number of variants produced. A cognitively designed work leads to better product quality and worker wellbeing (Malmsköld et al., 2015; Wollter Bergman et al., 2021). It may also attract people to jobs, making them develop higher skills and stay longer on the jobs.
3.4 Skill gaps and competence development
The widespread societal transformation presents a major global challenge: the need to upskill and reskill the workforce for new or evolving job roles. One of the main hurdles for the battery industry today is to have the right-skilled workforce who can solve the challenges occurring when batteries are produced. When the industry is changing, workers may do new tasks. In this case, work tasks range from process industry to more traditional assembly (Kwade et al., 2018). For workers who are used to traditional tasks in automotive industry, a shift to battery production also leads to a higher demand of skills related to safety. Currently, industry is struggling to find the right-skilled people for battery-related jobs. This results mainly from two parallel phenomena: (1) the demographic change in European countries, the US, and China results in a shortage of available people in the working age (United Nations, 2022), and (2) among the people in working age, not enough candidates have the right skills to meet the battery industry’s demand (Rikala et al., 2024). With this background, the European Commission launched the Pact for Skills with the goal to upskill and reskill 800,000 workers for battery production by 2025. Several other upskilling and reskilling efforts have been undertaken such as the Deep Tech Talent Initiative (EIT Deep Tech Talent Initiative, 2024) and Automotive Skills Alliance (2024).
4 Circular battery life cycles
As batteries rely on scarce and valuable material flows, the transition towards circular systems is gaining momentum to create more sustainable and resilient battery production systems (Kennedy and Linnenluecke, 2022). A new standard ISO 59004 defines principles for a circular economy to help enable a global transition to a new economic model (International Organization for Standardization, 2024). A goal for this new model of circularity is to keep resources within the economy for as long as possible. The standard establishes three fundamental principles for pursuing this goal referred to as narrowing, slowing or closing the flow of materials. Narrowing implies rethinking the business models for products so as to keep resources in the economy longer. Slowing focuses on strategies to get the most use of products by extending their life to keep them in the in the economy longer. Closing refers to strategies for recovering products and materials after their use there by bringing them back into the economy in a circular manner. Applying these principles to circular battery design implies developing new strategies from innovative business models to practices enabling more longevity for battery lifecycles including secondary uses to standards to enable discovery and recovery of materials when the batteries are no longer useful. Key to enabling these strategies will be the flow of information from different phases of manufacturing to support the analytics, such as smart maintenance and automation as discussed above, as well as for developing market insights for prediction of future material availability. Applying principles of circularity to the battery design, material acquisition/sourcing, production, usage, and end-of-life management establishes the goal to retain and recover as much value as possible out of the used products: on one hand to keep in cycle the inner resources (Ali et al., 2021) and on the other hand to acquire autonomy from the suppliers (Baars et al., 2021).
In addition to vehicle batteries, attention has also been given to portable batteries through, for instance, the new EU regulations which require: 1) Performance and durability, 2) Removability and replaceability (design for disassembly), and 3) A take-back program and infrastructure (European Portable Battery Association, 2023). The EU programs will rely on digital solutions for the flow and management of information to enable the conservation and recovery of battery value through the introduction of a digital product passport as further discussed in section 4 (Future battery value chains).
4.1 Digitalization in circular LIB value chain
The LIB value chain comprises distinct stages, each playing a crucial role in achieving circularity. According to Oliveira et al. (2015), mining raw materials for LIBs has a notable environmental impact, leading to issues like water pollution and ecosystem destruction. Costa et al. (2021) suggest mitigating this impact by renewable energy in mining operations and recycling mining waste. Despite optimistic projections (Costa et al., 2021) about recycling LIBs, reducing reliance on natural resources by 50%, mining and exploration will remain essential due to the non-recyclability of all materials. Furthermore, the most carbon-intensive stages of the LIB life cycle—extraction, processing, and production—account for a significant portion of the total carbon footprint (Costa et al., 2021; Chen et al., 2022). Extracting lithium from brine deposits and mining cobalt are energy-intensive processes, contributing to emissions. Additionally, refining raw materials into battery-grade materials involves complex and energy-intensive procedures.
Design plays a pivotal role in circularity; batteries designed for easy disassembly and recycling are more likely to be recycled at the end of their life (Rönkkö et al., 2023). Albertsen et al. (2021) stress the importance of designing LIBs that facilitate repair, disassembly, and recycling, extending the significance of battery design to EV manufacturing, where it serves as a foundational element in technological development. Interestingly, there appears to be reluctance among EV manufacturers to share crucial information about the battery design and manufacturing with recycling firms, as evidenced by Yu et al. (2023).
The production of LIBs involves energy use for assembly and quality assurance, with cathode materials contributing significantly to emissions (Wang et al., 2017). Chen et al. (2022) project substantial emissions reductions in battery production by 2060, primarily through transitioning to greener electricity sources. Although there are ways to reduce the carbon footprint of LIBs, it is crucial to note that the technology is still in its early stages, requiring further research for more efficient and sustainable manufacturing processes. From a technological perspective, battery manufacturing is relatively mature, yet there is room for improvement (such as automation, digital twins, and artificial intelligence) to optimize processes and reduce costs (Wu et al., 2020).
The collection, pre-treatment and recycling of LIBs stand out as crucial activities to enable circular economy. According to Richter (2022), recycling end-of-life EV batteries could substantially meet global demand for cobalt, lithium, manganese, and nickel in 2040. However, waste management poses a major challenge due to the risk of fires and hazardous contamination, necessitating careful handling. Recycling methods, such as hydrometallurgy, direct physical recycling, and remanufacturing with recycled materials, can result in a 51.8% lower carbon footprint compared to battery production with raw materials (Chen et al., 2022). Reuse strategies, outlined by Albertsen et al. (2021), including intensified use, repair, repurposing, refurbishment, and remanufacturing, play a crucial role in extending the life of EV batteries and optimizing their life cycle value. Repurposing batteries in energy storage systems has also been identified as a viable market opportunity (Richter, 2022).
4.2 Battery recycling and regeneration processes
While LIBs were introduced to the market about 30 years ago, they are today considered state-of-the-art power sources for portable devices and EVs (Neumann et al., 2022). As batteries reach their end of use, they need to be handled with care to avoid negative ecological impacts as well as create opportunities for value recovery which is becoming increasingly important for components and materials with high economic value. Despite the rapid progress made with recycling technologies to recover different battery materials, LIBs are still poorly recycled with a large portion of spent batteries going to landfill without any material recovery. One of the challenges for battery recycling is the broad range of battery types (chemistries) cells, modules, packs and overall product designs. To overcome the challenge posed by this diversity and to enable large-scale, profitable battery material recovery, it is essential to consider in early product design the ability to disassemble and sort batteries, as well as to ensure compatibility in pre-treatment and recycling processes.
Among the different types of battery recycling processes the dominant methods used today include extractive metallurgical processes such as pyrometallurgy and hydrometallurgy (Blömeke et al., 2022; Neumann et al., 2022). The recovery rates for these established recycling techniques are already high; e.g., over 98% for lithium, over 95% for cobalt, and over 90% for graphite (Neumann et al., 2022). Pyrometallurgy requires high-temperatures and has a low recovery rate, and hydrometallurgy is a slower process which consumes more chemicals. Modern recycling processes usually combine multiple pre-treatment and recycling methods to achieve higher recovery of valuable metals, such as cobalt, lithium, manganese, and nickel. Thermal pre-treatment can improve the leaching yield and recover rates of these active materials (Petranikova et al., 2022). Substituting primary/virgin material with secondary materials in new battery chemistries can alleviate the resource extraction stress caused by the rapid increase in demand for rare and scarce minerals, but recovered materials remain a low contributor of the total production input to produce batteries (Baars et al., 2021). Some of the main challenges in LIB recycling include resource intensity (process efficiency for recovery lithium in particular), safety concerns due to the high reactivity of metallic lithium and consequently the necessary process developments for LIB pre-treatment.
Novel recycling processes are constantly being explored to improve recycling efficiency (energy and chemicals consumption), reduce costs, and further increase recovery and purity rates. For example, direct recycling or regeneration methods based on defect-targeted healing can reduce the necessary energy and resulting emissions compared to hydrometallurgical and pyrometallurgical methods (Xu C. et al., 2020). Different regeneration processes have different advantages and disadvantages (Zhao et al., 2020). They present promising avenues to reduce the environmental impact of recycling while generating significant economic benefits to create an incentive for their adoption. However, as some of these processes are still in early stage of development, they are not yet deployed at industrial scale. In addition, new battery chemistries (i.e., as discussed later in section 4.3) will require new recycling techniques; for example, lithium sulfur batteries are considered promising options for the future (Neumann et al., 2022), but no recycling process for such batteries exist as of today since they are yet to reach the market.
While there is a strong focus on developing such recycling solutions both in academia and industry, recycling is a lowest-priority circular strategy and thus should be considered when no other valuable or practicable applications for the remaining battery performance exist. Given the impact of battery production, the most desirable circular strategy is to use batteries for as long as possible until performance degrades below a certain acceptable threshold which is typically around 70%–80% of initial capacity. At that point, the battery can be repurposed for other applications with lower requirements such as stationary energy storage. Beyond repurposing, other circular strategies can be considered such as battery regeneration and refurbishing.
4.3 Circular battery business planning
Circular battery business practices are being developing around the world and include end-of-first-life activities (such as remanufacturing, refurbishment, repurposing, recycling) and battery leasing in China, Japan, Europe (e.g., Germany and Norway), and the United States (Jiao, 2017; Tao et al., 2022; Gonzalez-Salazar et al., 2023). Battery repurposing in a “second life” application is an important circularity strategy that offers promising business solutions to mitigate supply chain risks related to LIBs, reduces the environmental impact of manufacturing new LIBs, and creates additional economic value (Rajaeifar et al., 2022). Repurposing of EV LIB cells for a second-life application can help limit and extend the useable service time of many critical minerals such as cobalt and lithium. This method of reuse is supported by the fact that EV LIBs are often capable of storing 70%–80% of their original capacity at the end of their first life (Martinez-Laserna et al., 2018). The used LIBs are often suitable for refurbishment for second life deployment as stationary energy storage systems for the electrical grid, communication towers, and renewable energy generation sources (wind and solar farms). There are several international examples of second life implementation in the LIB lifecycles. For example, 4R Energy in Japan collects spent EV LIBs from an automobile OEM, car dealers, and dismantlers. The company inspects, grades, disassembles and reassembles, and sells spent LIBs to (i) the OEM as refurbished LIBs for spare parts, (ii) other users as repurposed LIBs for energy storage systems and other applications (e.g., automatic guided vehicles), and (iii) recycling companies as non-resalable LIBs to be processed as recycled materials (Tao et al., 2022). Another example is Eco Stor in Norway where the company collects spent LIBs from EVs and sells them as stationary energy storage systems. Spent batteries are dismantled and sorted to ensure sufficient remaining battery capacity for repurposing (Wrålsen and O’Born, 2023). Similar activities are taking place in the U.S., an example being a collaborative project co-led by state, university, and private industry stakeholders (Nissan and Seven State Power), which aims for Nissan to repurpose its used EV batteries for use in energy storage systems at their headquarters in Franklin, TN, U.S.
Such opportunities for circular businesses can be expected to expand in the future. When attempting to design sustainable circular battery businesses from both economic and environmental perspectives, the following items need to be considered:
• A vision and goals to be achieved in the business. These should be consistent with circular economy principles.
• External circumstances surrounding the business that influence the feasibility, economic profitability, and environmental impacts of the business. Typical examples are regulations, consumer behaviours and preferences, and economic and social situations in the country/region of interest. For example, the European battery regulations are setting mandatory minimum levels of recycled content of 6% for lithium and nickel, 16% for cobalt by 2031 for industrial batteries with a capacity greater than two kWh (European Commission, 2023b).
• Temporal changes and future uncertainties, such as technological development of LIBs. The cost, performance, and degradation rate of LIBs has been and will be improved, while the market share of LIB types will change in the future (Rajaeifar et al., 2022).
• Appropriate combinations of life cycle options and business options. Matching demand and supply of spent LIBs is key to making the business feasible (Takata et al., 2019; Tao et al., 2022). Possible life cycle options include remanufacturing, refurbishment, direct reuse, repurposing, and recycling. On the other hand, business options include battery sales, battery leasing (Gonzalez-Salazar et al., 2023), and battery swapping (Hu et al., 2023).
• Reduction of environmental loads and economic costs of LIB manufacturing. Full life cycle assessments focused on changes in battery manufacturing should be performed to verify significant reductions and justify the investment in new manufacturing. For example, even with highly efficient production processes, input electricity and heat will result in excess heat that is traditionally cooled away. By integrating industrial symbiosis strategies, excess heat from the production could be transferred and used in food production processes (e.g. fish farms, green houses etc.) or for district heating purposes (Mathur et al., 2019), thereby magnifying the reduction in environmental and economic benefits.
Research on sustainable circular battery business planning has been progressing by taking a qualitative approach (e.g., Jiao, 2017; Bajolle et al., 2022) and a quantitative approach (e.g., Takata et al., 2019; Huster et al., 2022; Gonzalez-Salazar et al., 2023). Furthermore, a scenario analysis approach by combining narrative stories and quantitative simulations is often taken to explore possible business plans considering future change and uncertainties (e.g., Tao et al., 2022; Schulz-Mönninghoff and Evans, 2023).
4.4 Service-based business models
Research on battery production requires a life cycle perspective which benefits from the increasing digitalization of industry. Exploring the business models that can better support battery production and commercialization is a task of urgent nature. By embedding circular economy principles in the value proposition of battery systems, industry can explore alternatives, such as the use, results or performance of batteries, over the offering of retention of ownership. One such model is servitization. Servitization is a business model trend which was introduced in the 1970s (Vandermerwe and Rada, 1988). Conceptually, servitization is when the manufacturer retains ownership of assets, focusing on access to assets with business models in the form of a leasing or sharing platform (Ahuja et al., 2020). By shifting towards servitization and adopting service-based business models, the concept of value delivery is decoupled from tangible assets and material resource consumption. Such decoupling of the tangible asset is known as dematerialization. Other potential benefits of servitization include product life cycle extension, competitive advantage, strengthened customer relationships, and more responsible consumption (Kamal et al., 2020).
Despite ongoing research regarding the commercialization of batteries with a life cycle perspective, few vehicle OEMs are providing public information about activities related to the commercialization of circular strategies, such as intensifying use, repair, refurbish, remanufacturing (Albertsen et al., 2021). Recent research proposes that this production paradigm could benefit from a lens where circular business models are considered the go-to alternative, with particular focus in embedding sustainability in battery value chains. It is worth noting that adopting circular business models does not necessarily lead to sustainable business models, a paradox that must be considered and avoided in this context (Blum et al., 2020). Servitization applied to batteries needs to be further explored. It can be expected that with complex value chains, barriers and challenges will require the orchestration of both internal and external resources to succeed. Some influencing factors (such as market forces, regulations, financial incentives, supporting infrastructure or lack thereof, etc.) could be viewed simultaneously as drivers and challenges for circular business models (Jacobs et al., 2022). Available literature has mainly adopted a perspective on batteries restricted to EV batteries: the take-back and servitization models where three archetypes are thoroughly described (Chirumalla et al., 2024). Although end-of-life vehicle take-back is essential for automotive battery recovery (Sopha et al., 2022), this approach shifts the value capture opportunities to the end-of-life and does not take advantage of benefits that could be developed at the design and use phase (Rocha et al., 2019). Servitization could reduce the initial cost of EVs and increase the number of returned EV batteries. Such cost structure combined with governmental incentives can encourage manufacturers to engage in product end-of-life and battery end-of-use management more proactively.
Several servitization models explore different value opportunities within batteries (Chirumalla et al., 2024). Among them is the case of exchangeable battery services, whereby the EV users do not own the battery (Mak et al., 2013). Instead, the batteries are commercialized as a leased product or component, based on a service contract (charged based on usage or distance driven). Battery swapping is another alternative which could provide fast-refuelling service for EVs (Ahmad et al., 2020). In this sense, the many structures for battery-as-a-service business models hold promising potential to avoid long recharging time during long-distance travels. Such business models exist in the Chinese market, where the number of swapping stations grew rapidly, and the expectation is that they will also increase their appearance in the European market. To enable swapping the EV batteries must be designed for swapping. Despite the benefits of servitization, a trend is emerging for larger EVs to go for cell-to-pack or cell-to-body design driven by minimizing cost and weight and maximizing energy density, hindering access for serviceability to handle the cell failures.
5 Future battery value chains
The transition to sustainable battery value networks is crucial to address environmental and social concerns across battery life cycles. In the future, batteries will be an even larger feature of our global energy systems, enabling capture of energy for on-the-spot and immediate consumption. Recovery of these batteries and their materials is necessary to sustain future production at the levels that will be needed worldwide. Digitization of information throughout the battery life cycle will enable better management of the resources by enabling traceability of materials and use phase performance including addressing remaining capacity. The insights gained through life cycle data collection can support more resilient outcomes both through the recovery of materials and insights useful to improve performance and evaluate flows across the global supply chain. The concept of a digital product passport is being pursued as a means of managing and sharing the data across partners. A digital battery passport will enable traceability of battery materials and components, manage complex information flows enabling circular strategies, and be instrumental in addressing disruptions resulting from global events and rapid technological advances (Jensen et al., 2023; King et al., 2023). This section presents research topics on the rise to support the development of future battery value chains.
5.1 Resilient manufacturing
LIB production depends on key materials that are sourced from several different geographical regions around the world (European Commission, Joint Research Centre et al., 2018). The process of value creation in LIB production spans from extracting and refining raw materials, to crafting cell components, modules, and assembling battery packs. This culminates in the assembly of the finished product, followed by its useful life, servicing, and ultimately, end-of-life management. This intricate value chain encompasses a sprawling global business network, making them vulnerable to risks. Examples include critical raw material supply shortage (Xu P. et al., 2020), geo-political issues, global supplier dependencies, recycling issues (Harper et al., 2019), the COVID-19 pandemic which brought vulnerabilities to international EV-LIB trade (Hu et al., 2021), and more. If LIB supply chains are to deal with such risks and contribute positively to sustainability, they need to be resilient (Marchese et al., 2018) in terms of increased transparency and flexibility or reduced dependencies in the supply chain.
Resilience is defined as the ability to prepare for anticipated hazards, adapt to changing conditions, to withstand and limit negative impacts due to events, and to return to intended functions/services within a specified time after a disruptive event (VanGeem, 2018). Manufacturing resilience is further defined as the ability of manufacturing companies and their supply chains to anticipate, cope, and learn from disruptions caused by risks so that they can revert to normal or better states of operation (Chari et al., 2023). Risk assessment, which is an important aspect of building resilient supply chains, thus becomes relevant especially from a supply chain perspective, as dependencies exist on both, the upstream and downstream stages (Yan et al., 2020). Building capabilities for suitable resilience and response strategies to deal with risks in LIB production while maintaining the triple bottom line of sustainability will be the next step in building resilient supply chains.
However, LIB value networks require collaborations between partners but this in turn increases dependencies and hence the vulnerability of value chains. Digitalization offers key opportunities and advantages to build the resilience of the LIB value network (Fu and Chien, 2019) by helping them respond faster to disruptive events, improve cooperation between value chain partners (Veile et al., 2022), and increase data transparency and full product transaction traceability (Krima et al., 2019; Zhao et al., 2019). The use of IoT, big data and decentralized data systems technologies (Hastig and Sodhi, 2020; Antônio Rufino Júnior et al., 2022; Tavana et al., 2023) can provide capabilities that further enhance the potential for the tracking and monitoring of the value-creation processes.
Specifically, IoT and big data can support data collection and analysis for battery management and optimizing performance to design sustainable and circular supply chains (Tavana et al., 2023). By agreeing on key events in the battery life cycle, the value chain (from raw material extraction to final product) may be monitored to support timely decisions. In cell manufacturing, tracking individual components’ origin and movement will allow manufacturers to pinpoint the source of any errors and promptly take corrective measures. Decentralized data systems (such as blockchain) can revolutionize how partners collaborate and exchange information and is seen as a vital tool in eliminating forced or child labour (Hastig and Sodhi, 2020). Such systems can also help detect if mines produce more than the expected amounts (which may indicate mineral mixing) and verify responsible purchasing and production practices, among other benefits. Process tacking and monitoring facilitates preventive maintenance, and with the appropriate analysis can reduce resource consumption and related expenses and improve the overall sustainability of the production system. Notably, recent advancements in digital product passports and digital battery passports offer promising solutions for sustainable and circular value chains (Berger et al., 2022). New methods to ensure the security of critical raw material supply (Blagoeva et al., 2020) across the value chain, including upstream and downstream activities, need to be developed.
As discussed in section 3, implementing circular economy strategies such as reuse, remanufacture and recycle (Alcalde-Calonge et al., 2022) can further improve supply chain resilience (Chari et al., 2022; Kurz et al., 2022). Due to the complexity involved in manually disassembling spent EV batteries, human-robot disassembly collaborations have emerged as a promising alternative (G. Yuan et al., 2023). By using real-time dismantling information and fault information data, these collaborative systems will improve operational efficiency, the system’s ability to respond to disruptions and quickly resume disassembly operations.
5.2 Digital product passports
For the effective growth of a circular value chain in the EV battery industry, reliable information is vital to verify that the product aligns with the principles of ethical sourcing and supply chain traceability (Adisorn et al., 2021; Berger et al., 2022). Presently, gaps exist in the data available within the EV battery landscape, posing challenges to achieving the circular economy model (Jackson et al., 2014; University of Cambridge Institute for Sustainability Leadership CISL and the Wuppertal Institute, 2022). One concept that has emerged as a potential enabler of a circular economy for batteries is the digital product passport. As described by the European Commission, the digital product passport concept relies on unique identifiers and decentralized ledger systems to provide extensive data throughout a product’s life cycle to fill the information voids and ensure transparency and verifiability of the information (European Commission, 2022). As such, a digital product passport is a structured collection of data related to a particular product with a predefined scope and agreed upon data ownership and access rights. The intended scope of the digital product passport includes information related to sustainability and circularity factors, as well as value retention for re-use, remanufacturing, and recycling (CIRPASS, 2023). Emphasizing material traceability and transparency is a critical step to mitigating waste and pollution and facilitating circularity in the battery sector (Geissdoerfer et al., 2017).
In Europe, the Ecodesign for Sustainable Product Regulation (ESPR) prescribes the gradual rollout of the digital product passport starting in 2027. Given efforts to decarbonize the transportation sector through increased adoption of EVs, the battery industry has become a priority (European Commission, 2018). Digital battery passports have thus become a use case for digital product passports in Europe (The Battery Pass consortium, 2023). Similarly, in 2018, China’s Ministry of Industry and Information Technology (MIIT) issued the Interim Regulations on Traceability Management of the Recycling and Utilization of New Energy Vehicle Power Batteries. This regulation aims to establish a comprehensive system for gathering information and overseeing the entire life cycle of EV batteries to determine recycling effectiveness (Cheng et al., 2021; Li et al., 2021; Xu et al., 2021). In the U.S., interest is increasing in advanced battery supply chain traceability and transparency. For example, the Inflation Reduction Act of 2022 aims to drive domestic EV and battery production by providing tax credits to consumers that purchase EVs that meet specific material and component requirements (United States Congress, 2022).
While global efforts and interest in digital battery passports continue to increase, the concept faces several challenges in development and implementation. From a high-level perspective, major challenges can be grouped into key areas:
• Estimating cost and benefits: Agreements as to who funds digital battery passports and who benefits are lacking. The business case for a digital battery passport is needed to articulate benefits and beneficiaries, costs, and funding models along with analysis of different options. Key to creating acceptance of digital battery passport, especially by manufacturers, is the need to develop business models around sharing better product circularity data (Adisorn et al., 2021).
• Balancing transparency and safeguarding sensitive information: Apprehensions exist regarding how to provide transparency without compromising intellectual property, business sensitive information, and consumer privacy and security, particularly in decentralized implementations of the digital product passport (Walden et al., 2021; Westerlund, 2023). This necessitates consensus on data governance to provide selective role-based data access to authorized end users.
• Authenticity and verification of data: Challenges emerge from stakeholder uncertainties about accountability and trustworthiness of data input to the digital battery passport (Berger et al., 2023). Methods used to collect data for the passport are yet to be determined, as are verification systems to validate the authenticity of data inputs (Adisorn et al., 2021; Jensen et al., 2023).
• Data infrastructure: The immense magnitude and complexity of data to be collected and systematically made available to approved parties requires extensive supporting data infrastructure. Decentralized architecture systems have been proposed as a means for data collection and storage, yet many hurdles must be overcome, including interoperability between data systems, data preservation upon exit of a stakeholder, and specifications for uniform dynamic data collection such as during battery use (Berg et al., 2022; Jansen et al., 2023). These specifications are extraordinarily broad in scope ranging from definitions for material declarations, to agreement on events or actions of interest, to messaging protocols for sharing the information. Many of these topics are actively being pursued within ISO and IEC.
• Lack of uniformity in battery technology and recovery options: Little to no conformity exists amongst batteries with respect to material content, product design, disassembly and recovery processes, performance standards for secondary market products, methods for estimating remaining useful life, and related criteria for assessing the capabilities for secondary uses (Torres et al., 2004; Merdan et al., 2010; Wegener et al., 2015; Beghi et al., 2023). The means to capture the necessary information in a digital battery passport to enable highest-value recovery processes in this diverse and disparate recovery ecosystem, where products pass through multiple life cycles, is yet to be determined.
Overcoming these challenges will necessitate collaboration and global consensus on issues such as data needs for circularity, data governance and verifiability, and unification and standardization to create acceptance and garner participation in digital battery passport systems. Metrics need to be defined for sustainability and circularity assessment across product life cycles and could be utilized to prioritize data inputs to digital battery passports. Standards are necessary to support uniform and interoperable data systems, harmonize data inputs and accessibility, and to develop methods for third-party verification of data authenticity. A commercial ecosystem needs to be developed that supports the equitable distribution of digital battery passport costs and benefits, and simultaneously business models should be innovated in support of the digitalization of circularity.
5.3 Process and production for next-generation battery chemistries
Next-generation batteries constitute a diverse flora of different batteries that challenge the LIB technology in proving either higher energy density or specific energy, being more sustainable and less costly, or have better safety and toxicity characteristics. These include dual-ion batteries, Na- and K-ion batteries, organic and bio-based batteries, Al-batteries, divalent chemistries (Ca, Mg, Zn), sulfur-based and oxygen-based cathodes, and solid-state batteries. In turn, all of these comprise many different subcategories, which thus together comprise thousands of different possible cell chemistries. Commonly, neither of these can yet show the total performance metrics that render them seriously competitive with the Li-ion technology, and some are still at very low technology readiness levels (TRL), and thereby need more research efforts. The most mature examples to date are Na-ion batteries, which generally display considerably lower resource scarcity than Li-ion batteries (Wickerts et al., 2024), and solid-state batteries based on Li-metal (Amici et al., 2022), which rather appear as less sustainable solutions (Mandade et al., 2023).
From a production point of view, there are no major changes involved when transferring from traditional Li-ion to Na-ion batteries; they involve the same type of processing steps performed in the same order (Duffner et al., 2021a) as they use a liquid electrolyte. Solid-state batteries, which use solid electrodes and solid electrolyte, involve profound changes, partly due to the handling of a metallic (Li-metal) negative electrode instead of a carbon porous electrode, and partly due to that the solid electrolyte cannot easily infiltrate the porous cathode. The latter problem needs to be solved differently, taking into account the properties of the solid-state electrolyte, which is commonly a Li-conducting ceramic sulfide or oxide, a Li-salt dissolved in a polymer, or a hybrid between these three categories (Sångeland et al., 2019).
Handling the production of solid-state batteries based on solid polymer electrolytes is the most straightforward way of transferring the process of LIBs to solid-state batteries, since less critical steps need changes. It could be argued that the comparatively easy production of polymer-based solid-state batteries is the cause for their successful implementation in different types of commercial vehicles, compared to the ceramic-based solid-state batteries (Song et al., 2023). The main differences as compared to LIB production are the implementation of the Li-metal anode, that the solid polymer electrolyte material need to be mixed in with the cathode slurry to fill the pores of the positive electrode, and that the polymer electrolyte need to be applied as a specific layer during coating instead of through filling. If solvent-based coating (tape casting, slot die or doctor blade casting, or screen printing) is to be used for the electrolyte casting, the solvent needs to be compatible with other cell components, not least the cathode binder. In order to avoid any such problems, and to also avoid drying of the solvent, extrusion of the polymer electrolyte can alternatively be used, which saves production time and cost (Schnell et al., 2018). As for all solid-state batteries, formation cycling is generally not necessary after production, which is likewise beneficial.
However, the handling of the Li-metal electrode is contributing to several additional steps that need consideration (Duffner et al., 2021b). Lithium is a very adhesive metal, and the processing implicates special challenges for roll-to-roll processes which requires a delicate balance between the pressure and tension to avoid tear or stretch for the application to meet needs of all the dimensional characteristics. Different types of handling tools could be employed; for example, laser for slitting instead of roll-knife slitting. Furthermore, lithium has to be processed in a dry atmosphere or under inert argon atmosphere. Otherwise, lithium will oxidize or form other surface layers that will seriously affect cell performance and ageing. To assure quality of the lithium metal electrode, the lithium metal electrode can be produced directly through extrusion in the battery production line. A so called ‘anode-less’ design, where the metal anode is formed in situ in the battery during charging, would clearly simplify the production of solid-state batteries (Tan et al., 2020), but has so far shown stability issues due to side-reaction and the limited Li content in the cells (Bertoli et al., 2023).
As for solid-state batteries based on solid polymer electrolytes, ceramic materials also need to be mixed with active materials, binders and conductive additives to produce ceramic-based solid-state battery cathodes by slot-die coating onto the Al current collector. Depending on the properties of the active material, which are fundamentally different for sulfidic and oxide solid-state batteries, different handling steps are necessary (Duffner et al., 2021a). The sulfidic materials are highly sensitive to air and often require an inert gas environment. However, they are mechanically ductile and can therefore use a straight-forward pressing step in the cathode formation. The oxides are chemically more inert (although still requiring dry room conditions) but brittle and need a high-temperature sintering step to assure good contacts between the cell components. This is energy and time-consuming, and alternatives such as spray-coating are therefore being studied. All types of processes are significantly more demanding as compared to conventional LIB cathodes.
The production of solid-state batteries also causes limitations in the different cell formats. In short, due to the adhesive properties of Li-metal and the brittleness of the solid electrolyte, pouch cells are needed (Janek and Zeier, 2023). However, solid-state batteries facilitate the use of bipolar configurations, with the single cells connected in series (Jung et al., 2019). Such configuration can be used to increase the cell voltage and to reduce the amounts of current collectors in the cell stack, thereby raising energy density further.
5.4 Example of novel processes: sustainable electrode manufacturing
The key to developing sustainable battery production lies in knowing how to create eco-friendly systems from raw material preparation to electrode manufacturing and cell assembly. At present, the high cost and high energy consumption of conventional battery manufacturing has a significant environmental impact, especially the slurry-based electrode manufacturing process which causes 20% of total manufacturing cost, 47% of total energy consumption and another 29% of total energy is consumed by the dry room facility (Li et al., 2020; Liu et al., 2021). This is because of the use of toxic and expensive organic solvent N-methyl-2-pyrrolidone (NMP) which needs to be recovered during electrode manufacturing processing (Kwade et al., 2018; Liu et al., 2021). Replacing NMP with water has attracted significant attention worldwide. This could decrease manufacturing energy by 43% and lower the cradle-to-gate life cycle impacts up to 88% over conventional battery manufacturing (Yuan et al., 2021). Ultimately, dry coating from dry electrode powder to the film would eliminate the use of any solvents, which is beneficial for the current LIB production, as well as important for future solid-state battery manufacturing (Duffner et al., 2021b). This advanced technology offers significant savings in manufacturing costs and reduced CO2 emissions.
Several advanced dry coating technologies have been proposed and investigated for the electrode formation. A few examples include dry pressing coating technology, dry spray coating technology and electrostatic coating methods (Ryu et al., 2023). The application of the dry coating technology in LIB manufacturing was implemented by the Maxwell Technologies Inc. by directly calendaring the mixed active materials, binder and conductive additive. A free-standing film can be obtained and then laminated on the surface of the current collector (Liu et al., 2021). In the process, a binder fibrillation, in which polytetrafluoroethylene (PTFE) forms long fibres, is important to hold the active materials and conductive materials together. Using a similar method, Meng et al. realized the formation LNMO electrodes at high loadings (3.0 mAh cm-2) and demonstrated the performance improvement of long-term cycling in the high voltage (4.7 V) for LIB application (Yao et al., 2023). Such a dry coating method can readily fabricate roll-to-roll electrode with controllable thickness and uniform film.
Recently, the electrostatic coating technology for electrode manufacturing has drawn significant attention from both academia and industry in battery manufacturing field. In a fabrication process, the premixed dry particles are charged via a spraying gun, followed by deposit on the ground current collector. The formed dry powder film is controlled by the charging voltage, carrier gas pressure, and the distance between the spray gun and the current collector. Several works have successfully dementated the use of electrostatic coating method to prepare a uniform and controllable electrode (Ludwig et al., 2016). Ludvig et al. used the dry powder electrostatic painting process prepared the lithium cobalt oxide-based electrode. A fast hot rolling process thermally activates the thermoplastic polymer to bind the active material in only a few seconds. The bonding test of the dry deposited particles onto the current collector shows that the bonding strength is greater than a slurry coated electrode. This simply electrostatic coating process also makes it easier to control the microstructure of the deposited electrode. Such dry spraying deposition is a versatile method because it can be widely used for all common active materials particles for LIB. Both roll-to-roll dry coating (binder fibrillation) and electrostatic coating has the potential for practical upscaling of electrodes manufacturing. For the electrochemical performance, a dry coating method could achieve higher active materials loading compared to conventional wet-coated electrodes and result in improved high-rate performance owing to uniform distribution of binder on the active particles.
6 Conclusion
The ongoing shift towards a more environmentally friendly society, also known as societal green transformation, is heavily reliant on electrification needs to build on resilient and sustainable solutions. For the green transformation to include future mobility and electrification using batteries, which is on an exponential growth curve, the battery value chain needs to be sustainable. We identified key issues to achieve this, organized around four themes:
(1) Digitalizing and automating production capabilities: this theme includes (1.1) data-driven performance management, (1.2) quality assurance and (1.3) smart maintenance in battery manufacturing;
(2) Human-centric production: (2.1) automation and human-robot collaboration, (2.2) extended reality, (2.3) ergonomics and human factors, and (2.4) skill gaps and competence development;
(3) Circular battery production systems: (3.1) navigating circularity and possibilities for digitalization in the LIB value chain, (3.2) battery recycling and regeneration processes, (3.3) circular battery business planning, and (3.4) service-based business models;
(4) Future battery value chains: (4.1) resilient manufacturing, (4.2) digital product passports, and (4.3) process and production for next-generation battery chemistries, and an example with electrode manufacturing.
The main suggestions for future research to address challenges for sustainable battery production (and their relations to the themes and challenges presented in the introduction, see Figure 1) include:
• Data-driven approaches for quality monitoring of batteries and digital passports for management and maintenance of batteries throughout the value chain of battery lifetimes (1.1, 1.2, 1.3, 3.1, 4.2).
• Quality assurance methods for tolerancing, root cause analysis, robust design and production (1.2, 4.3).
• Environmentally friendly materials and processes throughout the battery value chain that enable reuse/recycling and simultaneously maximise performance during the lifetime of batteries (1.1, 3.1, 3.2, 3.3, 3.4). Specific emphasis on addressing materials scarcity, toxicity of solvents, and recyclability is needed (3.1).
• Robust and automated processes for battery production and recycling empowering humans as decision makers for improved safety and productivity (2.1, 2.3, 3.1).
• Upskilling and reskilling of the workforce (2.2, 2.3, 2.4). Since several factories and recycling facilities are not built yet, training materials and VR/AR supported learning environments are essential to speed up the green transformation and enable more workers to join on aiding the transition process.
• Safety when working with materials and battery related technologies as exposure to flammable materials, electricity and automation is frequent during production (2.1, 2.4, 3.2). In addition, the quality criteria in this sector are very rigorous (e.g., utilizing clean rooms and tough tolerances on manufacturing) because of safety and high-performance requirements.
• Robust business planning, innovative business models and resilient manufacturing value chains (3.3, 3.4, 4.1). Battery production is a high-value activity and as of today also incorporates scarce materials. New business models and infrastructures for leasing, mobility as a service and closed-loop material cycles need to be developed.
• Improved end-of-use and end-of-life treatment methods (3.1, 3.2, 3.3, 3.4). Since LIBs are already common today, the circularity aspects of these batteries are already of high importance. Closing the loop and improving the recyclability of spent batteries and their path to secondary use is critical.
• Digital product passport (4.2). The digital product passport concept is under development in several parts of the world today. To bring this idea to fruition, a system of standards and deployment platform utilizing e.g. decentralized data system technologies to track and make good use of the resources will be needed.
• Digital battery passport (4.2). For digital product passports to be aptly applied to batteries research is needed to identify key aspects of the battery materials and life cycle that need to be tracked and traced, what use cases to prioritize, which stakeholders will benefit from access to which data, and how the information can be securely shared amongst stakeholders.
• Design guidelines for development of new batteries (4.3). As the production of batteries ramps up and circularity is pursued as a means of maximizing resource use, attention will need to be given to guidelines for design and recovery of the new batteries. Guidelines, performance indicators, and metrics are needed to assess the quality of new designs to meet the needs for changing business models and recovery and circularity goals. Research is need to address both divergent form factors that will be available and the vastly different chemistries that are emerging.
• Sustainability assessment. Care must be given to assure that the end result of this changing landscape is more sustainable in the long run. The new systems must respond to a growing number of priorities and evaluation of the outcomes before, during and after physical implementation will be essential for success. Significant work will be needed to model the new systems and evaluate their environment, social, and governance qualities prior to deployment.
Author contributions
BJ: Conceptualization, Formal Analysis, Funding acquisition, Investigation, Project administration, Supervision, Visualization, Writing–original draft, Writing–review and editing, Data curation, Methodology, Resources, Validation. MD: Conceptualization, Formal Analysis, Funding acquisition, Investigation, Methodology, Project administration, Resources, Supervision, Writing–original draft, Writing–review and editing, Data curation, Validation, Visualization. JB: Funding acquisition, Investigation, Writing–original draft, Writing–review and editing. GB: Conceptualization, Formal Analysis, Investigation, Writing–original draft, Writing–review and editing. HC: Formal Analysis, Investigation, Methodology, Writing–original draft, Writing–review and editing, Data curation, Validation. AC: Formal Analysis, Investigation, Methodology, Validation, Writing–original draft, Writing–review and editing. QF: Conceptualization, Formal Analysis, Investigation, Writing–original draft, Writing–review and editing, Methodology, Validation. CG: Formal Analysis, Investigation, Writing–original draft, Writing–review and editing, Conceptualization, Methodology. AS: Conceptualization, Formal Analysis, Investigation, Resources, Validation, Writing–original draft, Writing–review and editing, Methodology, Supervision. HS: Writing–original draft, Writing–review and editing, Conceptualization, Formal Analysis, Investigation. HW: Formal Analysis, Investigation, Validation, Writing–original draft, Writing–review and editing. KW: Formal Analysis, Investigation, Validation, Writing–original draft, Writing–review and editing, Conceptualization, Funding acquisition, Resources. LN: Writing–original draft, Writing–review and editing, Funding acquisition, Methodology, Project administration, Resources. JS: Conceptualization, Formal Analysis, Investigation, Validation, Writing–original draft, Writing–review and editing, Methodology. RO: Investigation, Writing–original draft, Writing–review and editing, Formal Analysis, Validation. KS: Formal Analysis, Investigation, Validation, Writing–original draft, Writing–review and editing, Conceptualization. LE: Conceptualization, Formal Analysis, Investigation, Validation, Writing–original draft, Writing–review and editing. KM: Investigation, Writing–original draft, Writing–review and editing, Conceptualization, Methodology, Resources. JN: Data curation, Formal Analysis, Investigation, Methodology, Validation, Writing–original draft, Writing–review and editing. YK: Data curation, Formal Analysis, Investigation, Validation, Writing–original draft, Writing–review and editing, Conceptualization, Funding acquisition, Methodology, Project administration, Resources. YU: Data curation, Formal Analysis, Investigation, Validation, Writing–original draft, Writing–review and editing. FA: Writing–review and editing, Conceptualization, Methodology, Data curation, Formal Analysis, Investigation, Validation, Writing–original draft. MP: Data curation, Formal Analysis, Investigation, Validation, Writing–original draft, Writing–review and editing. HP: Data curation, Formal Analysis, Investigation, Validation, Writing–original draft, Writing–review and editing, Conceptualization, Methodology. SC: Data curation, Formal Analysis, Investigation, Validation, Writing–original draft, Writing–review and editing. KE: Data curation, Formal Analysis, Investigation, Validation, Writing–original draft, Writing–review and editing, Funding acquisition, Resources. DB: Data curation, Formal Analysis, Investigation, Validation, Writing–original draft, Writing–review and editing. MG: Data curation, Investigation, Validation, Writing–original draft, Writing–review and editing, Formal Analysis. HR: Conceptualization, Writing–original draft, Writing–review and editing, Data curation, Formal Analysis, Investigation, Validation. LA: Data curation, Formal Analysis, Funding acquisition, Investigation, Resources, Validation, Writing–original draft, Writing–review and editing. AO: Conceptualization, Data curation, Funding acquisition, Investigation, Methodology, Project administration, Resources, Supervision, Validation, Writing–original draft, Writing–review and editing. JS: Conceptualization, Funding acquisition, Methodology, Project administration, Resources, Supervision, Writing–original draft, Writing–review and editing.
Funding
The author(s) declare that financial support was received for the research, authorship, and/or publication of this article.
Acknowledgments
This work was supported by Västra Götaland Regionen Regionutvecklingsnämnden under grant no. RUN 2022-00294 (PreMAXBATT), by Swedish innovation agency Vinnova and the strategic innovation programme Produktion2030 under grants no. 2022-02467 (MATTER), 2022-01279 (EWASS) and 2023-00868 (VIVACE), Scientific Research (21H01234 and 23H03676) of the Japan Society for the Promotion of Science (JSPS) and the Environment Research and Technology Development Fund (JPMEERF20223R04) of the Environmental Restoration and Conservation Agency provided by the Ministry of Environment of Japan, by the Horizon Europe project DaCapo under grant no. 101091780, by the MICS (Made in Italy–Circular and Sustainable) Extended Partnership and received funding from the European Union Next-Generation EU (Piano Nazionale di Ripresa E Resilienza (PNRR) – Missione 4 Componente 2, Investimento 1.3 – D.D. 1551.11-10-2022, PE00000004), by The HumanTech Project financed by the Italian Ministry of University and Research (MUR) for the 2023-2027 period as part of the ministerial initiative “Departments of Excellence” (L. 232/2016). The European Research Council (ERC) (Grant 771777 “FUN POLYSTORE”). Digital Europe Programme (DIGITAL), project number 101083432, Acronym: CIRPASS. The work was carried out within Chalmers’ Production Area of Advance. The support is gratefully acknowledged. This manuscript reflects only the authors’ views and opinions, neither the European Union nor the European Commission can be considered responsible for them. We’d like to acknowledge support of the NIST Circular Economy Program as well as our appreciation for the generous review by Jamie Weaver.
Conflict of interest
The authors declare that the research was conducted in the absence of any commercial or financial relationships that could be construed as a potential conflict of interest.
The author(s) declared that they were an editorial board member of Frontiers, at the time of submission. This had no impact on the peer review process and the final decision.
Publisher’s note
All claims expressed in this article are solely those of the authors and do not necessarily represent those of their affiliated organizations, or those of the publisher, the editors and the reviewers. Any product that may be evaluated in this article, or claim that may be made by its manufacturer, is not guaranteed or endorsed by the publisher.
Author disclaimer
These opinions, recommendations, findings, and conclusions do not necessarily reflect the views or policies of NIST or the United States Government. Trade names and commercial products are identified in this paper to specify the experimental procedures in adequate detail. This identification does not imply recommendation or endorsement by the authors or by the National Institute of Standards and Technology, nor does it imply that the products identified are necessarily the best available for the purpose. Contributions of the National Institute of Standards and Technology are not subject to copyright.
References
Adisorn, T., Tholen, L., and Götz, T. (2021). Towards a digital product passport fit for contributing to a circular economy. Energies 14 (8), 2289. doi:10.3390/en14082289
Aenugu, I. R., Bere, G., Ochoa, J. J., Kim, T., Lee, C., and Park, J. (2020). “Battery data management and analytics platform using blockchain technology,” in 2020 IEEE Transportation Electrification Conference and Expo (ITEC), Chicago, IL, USA, 23-26 June 2020 (IEEE), 153–157.
Ahmad, F., Saad Alam, M., Saad Alsaidan, I., and Shariff, S. M. (2020). Battery swapping station for electric vehicles: opportunities and challenges. IET Smart Grid 3 (3), 280–286. doi:10.1049/iet-stg.2019.0059
Ahuja, J., Dawson, L., and Lee, R. (2020). A circular economy for electric vehicle batteries: driving the change. J. Prop. Plan. Environ. Law 12 (3), 235–250. doi:10.1108/JPPEL-02-2020-0011
Albertsen, L., Richter, J. L., Peck, P., Dalhammar, C., and Plepys, A. (2021). Circular business models for electric vehicle lithium-ion batteries: an analysis of current practices of vehicle manufacturers and policies in the EU. Resour. Conservation Recycl. 172, 105658. doi:10.1016/j.resconrec.2021.105658
Alcalde-Calonge, A., Sáez-Martínez, F. J., and Ruiz-Palomino, P. (2022). Evolution of research on circular economy and related trends and topics. A thirteen-year review. Ecol. Inf. 70, 101716. doi:10.1016/j.ecoinf.2022.101716
Ali, H., Khan, H. A., and Pecht, M. G. (2021). Circular economy of Li batteries: technologies and trends. J. Energy Storage 40, 102690. doi:10.1016/j.est.2021.102690
Amici, J., Asinari, P., Ayerbe, E., Barboux, P., Bayle-Guillemaud, P., Behm, R. J., et al. (2022). A roadmap for transforming research to invent the batteries of the future designed within the European large scale research initiative BATTERY 2030+. Adv. Energy Mater. 12 (17). doi:10.1002/aenm.202102785
Antônio Rufino Júnior, C., Sanseverino, E. R., Gallo, P., Koch, D., Schweiger, H.-G., and Zanin, H. (2022). Blockchain review for battery supply chain monitoring and battery trading. Renew. Sustain. Energy Rev. 157, 112078. doi:10.1016/j.rser.2022.112078
Arora, S., Kapoor, A., and Shen, W. (2018). Application of robust design methodology to battery packs for electric vehicles: identification of critical technical requirements for modular architecture. Batteries 4 (3), 30. doi:10.3390/batteries4030030
Automotive Skills Alliance (2024). Automotive skills alliance. Available at: https://automotive-skills-alliance.eu/.
Baars, J., Domenech, T., Bleischwitz, R., Melin, H. E., and Heidrich, O. (2021). Circular economy strategies for electric vehicle batteries reduce reliance on raw materials. Nat. Sustain. 4 (1), 71–79. doi:10.1038/s41893-020-00607-0
Bajolle, H., Lagadic, M., and Louvet, N. (2022). The future of lithium-ion batteries: exploring expert conceptions, market trends, and price scenarios. Energy Res. Soc. Sci. 93, 102850. doi:10.1016/j.erss.2022.102850
Beghi, M., Braghin, F., and Roveda, L. (2023). Enhancing disassembly practices for electric vehicle battery packs: a narrative comprehensive review. Designs 7 (5), 109. doi:10.3390/designs7050109
Berg, H., Kulinna, R., Guth-Orlowski, S., Stöcker, C., Thiermann, R., and Porepp, N. (2022). Overcoming information asymmetry in the plastics value chain with digital product passports. Wuppertal Paper no. 197.
Berger, K., Baumgartner, R. J., Weinzerl, M., Bachler, J., and Schöggl, J.-P. (2023). Factors of digital product passport adoption to enable circular information flows along the battery value chain. Procedia CIRP 116, 528–533. doi:10.1016/j.procir.2023.02.089
Berger, K., Schöggl, J.-P., and Baumgartner, R. J. (2022). Digital battery passports to enable circular and sustainable value chains: Conceptualization and use cases. J. Clean. Prod. 353, 131492. doi:10.1016/j.jclepro.2022.131492
Berlin, C., and Adams, C. (2017). Designing work systems to support optimal human performance. London United Kingdom: Ubiquity Press. Available at: http://www.jstor.org/stable/j.ctv3t5qtf.
Bertoli, L., Bloch, S., Andersson, E., Magagnin, L., Brandell, D., and Mindemark, J. (2023). Combination of solid polymer electrolytes and lithiophilic zinc for improved plating/stripping efficiency in anode-free lithium metal solid-state batteries. Electrochimica Acta 464, 142874. doi:10.1016/j.electacta.2023.142874
Blagoeva, D., Marmier, A., Alves Dias, P., and C Pavel, C. (2020). A new methodology to assess the EU resilience to materials supply along the value chain: case of lithium for lithium-ion batteries in electric vehicles. Material Sci. Eng. Int. J. 4 (3), 73–81. doi:10.15406/mseij.2020.04.00130
Bleischwitz, R., Yang, M., Huang, B., Xu, X., Zhou, J., McDowall, W., et al. (2022). The circular economy in China: achievements, challenges and potential implications for decarbonisation. Resour. Conservation Recycl. 183, 106350. doi:10.1016/j.resconrec.2022.106350
Blömeke, S., Scheller, C., Cerdas, F., Thies, C., Hachenberger, R., Gonter, M., et al. (2022). Material and energy flow analysis for environmental and economic impact assessment of industrial recycling routes for lithium-ion traction batteries. J. Clean. Prod. 377, 134344. doi:10.1016/j.jclepro.2022.134344
Blum, N. U., Haupt, M., and Bening, C. R. (2020). Why “Circular” doesn’t always mean “Sustainable.”. Resour. Conservation Recycl. 162, 105042. doi:10.1016/j.resconrec.2020.105042
Bokrantz, J., and Skoogh, A. (2023). Adoption patterns and performance implications of Smart Maintenance. Int. J. Prod. Econ. 256, 108746. doi:10.1016/j.ijpe.2022.108746
Bokrantz, J., Skoogh, A., Berlin, C., Wuest, T., and Stahre, J. (2020). Smart Maintenance: a research agenda for industrial maintenance management. Int. J. Prod. Econ. 224, 107547. doi:10.1016/j.ijpe.2019.107547
Brådland, H., Choux, M., and Cenkeramaddi, L. R. (2022). Point cloud instance segmentation for automatic electric vehicle battery disassembly, 247–258. doi:10.1007/978-3-031-10525-8_20
Brundage, M. P., Sexton, T., Hodkiewicz, M., Morris, K., Arinez, J., Ameri, F., et al. (2019). “Where do we start? Guidance for technology implementation in maintenance management for manufacturing,” in Volume 1: additive manufacturing; manufacturing equipment and systems; bio and sustainable manufacturing. doi:10.1115/MSEC2019-2921
Castelvecchi, D. (2021). Electric cars and batteries: how will the world produce enough? Nature 596 (7872), 336–339. doi:10.1038/d41586-021-02222-1
Chari, A., Niedenzu, D., Despeisse, M., Machado, C. G., Azevedo, J. D., Boavida-Dias, R., et al. (2022). Dynamic capabilities for circular manufacturing supply chains—exploring the role of Industry 4.0 and resilience. Bus. Strategy Environ. 31 (5), 2500–2517. doi:10.1002/bse.3040
Chari, A., Stahre, J., Bärring, M., Despeisse, M., Li, D., Friis, M., et al. (2023). Analysing the antecedents to digital platform implementation for resilient and sustainable manufacturing supply chains - an IDEF0 modelling approach. J. Clean. Prod. 429, 139598. doi:10.1016/j.jclepro.2023.139598
Chen, Q., Lai, X., Gu, H., Tang, X., Gao, F., Han, X., et al. (2022). Investigating carbon footprint and carbon reduction potential using a cradle-to-cradle LCA approach on lithium-ion batteries for electric vehicles in China. J. Clean. Prod. 369, 133342. doi:10.1016/j.jclepro.2022.133342
Chen, Y., Kang, Y., Zhao, Y., Wang, L., Liu, J., Li, Y., et al. (2021). A review of lithium-ion battery safety concerns: the issues, strategies, and testing standards. J. Energy Chem. 59, 83–99. doi:10.1016/j.jechem.2020.10.017
Cheng, Y., Hao, H., Tao, S., and Zhou, Y. (2021). Traceability management strategy of the EV power battery based on the blockchain. Sci. Program. 2021, 1–17. doi:10.1155/2021/5601833
Chirumalla, K., Kulkov, I., Parida, V., Dahlquist, E., Johansson, G., and Stefan, I. (2024). Enabling battery circularity: unlocking circular business model archetypes and collaboration forms in the electric vehicle battery ecosystem. Technol. Forecast. Soc. Change 199, 123044. doi:10.1016/j.techfore.2023.123044
Christensen, P. A., Anderson, P. A., Harper, G. D. J., Lambert, S. M., Mrozik, W., Rajaeifar, M. A., et al. (2021). Risk management over the life cycle of lithium-ion batteries in electric vehicles. Renew. Sustain. Energy Rev. 148, 111240. doi:10.1016/j.rser.2021.111240
CIRPASS (2023). DPP in a nutshell. Available at: https://cirpassproject.eu/dpp-in-a-nutshell/.
Costa, C. M., Barbosa, J. C., Gonçalves, R., Castro, H., Campo, F. J., and Lanceros-Méndez, S. (2021). Recycling and environmental issues of lithium-ion batteries: advances, challenges and opportunities. Energy Storage Mater. 37, 433–465. doi:10.1016/j.ensm.2021.02.032
Despeisse, M., Johansson, B., Bokrantz, J., Braun, G., Chari, A., Chen, X., et al. (2023). Battery production systems: state of the art and future developments, 521–535. doi:10.1007/978-3-031-43688-8_36
Duffner, F., Kronemeyer, N., Tübke, J., Leker, J., Winter, M., and Schmuch, R. (2021a). Post-lithium-ion battery cell production and its compatibility with lithium-ion cell production infrastructure. Nat. Energy 6 (2), 123–134. doi:10.1038/s41560-020-00748-8
Duffner, F., Mauler, L., Wentker, M., Leker, J., and Winter, M. (2021b). Large-scale automotive battery cell manufacturing: analyzing strategic and operational effects on manufacturing costs. Int. J. Prod. Econ. 232, 107982. doi:10.1016/j.ijpe.2020.107982
Dutta, A., Mitra, S., Basak, M., and Banerjee, T. (2023). A comprehensive review on batteries and supercapacitors: development and challenges since their inception. Energy Storage 5 (1). doi:10.1002/est2.339
EIT Deep Tech Talent Initiative (2024). EIT deep Tech talent initiative. Available at: https://www.eitdeeptechtalent.eu/.
European Battery Alliance (2024). European battery alliance. Available at: https://www.eba250.com/.
European Commission (2018). Annex to the communication from the commission to the European parliament, the council, the European economic and social committee and the committee of the regions.
European Commission (2022). Proposal for a regulation of the European parliament and of the council - establishing a framework for setting Ecodesign requirements for sustainable products and repealing directive 2009/125/EC.
European Commission (2023a). Proposal for a regulation on establishing a framework of measures for strengthening Europe’s net-zero technology products manufacturing ecosystem ('Net Zero Industry Act’). Available at: https://single-market-economy.ec.europa.eu/publications/net-zero-industry-act_en.
European Commission (2023b). Regulation (EU) 2023/1542 of the European Parliament and of the Council of 12 July 2023 concerning batteries and waste batteries. Available at: http://data.europa.eu/eli/reg/2023/1542/oj.
European Commission, Directorate-General for Research and Innovation Müller, J. (2020). Enabling Technologies for Industry 5.0: results of a workshop with Europe’s technology leaders. Luxembourg: Publications Office of the European Union.
European Commission, Directorate-General for Research and Innovation Breque, M., De Nul, L., and Petridis, A. (2021). Industry 5.0: towards a sustainable, human-centric and resilient European industry. Luxembourg: Publications Office of the European Union.
European Court of Auditors (2023). Special report 15/2023: the EU’s industrial policy on batteries – new strategic impetus needed. doi:10.2865/580370
European Portable Battery Association (EPBA) (2023). EU batteries regulation. Available at: https://www.epbaeurope.net/policy/eu-directive/eu-batteries-regulation.
Fabijan, A., Dmitriev, P., Olsson, H. H., and Bosch, J. (2017). “The evolution of continuous experimentation in software product development: from data to a data-driven organization at scale,” in 2017 IEEE/ACM 39th International Conference on Software Engineering (ICSE), Buenos Aires, Argentina, 20-28 May 2017 (IEEE), 770–780.
Fast-Berglund, Å., Gong, L., and Li, D. (2018). Testing and validating Extended Reality (xR) technologies in manufacturing. Procedia Manuf. 25, 31–38. doi:10.1016/j.promfg.2018.06.054
Fu, W., and Chien, C.-F. (2019). UNISON data-driven intermittent demand forecast framework to empower supply chain resilience and an empirical study in electronics distribution. Comput. Industrial Eng. 135, 940–949. doi:10.1016/j.cie.2019.07.002
Gästrin, J., and Winald, A. (2023). Operator training in virtual reality. Chalmers Reproservice, Gothenburg, Sweden: Chalmers University of Technology.
Geissdoerfer, M., Savaget, P., Bocken, N. M. P., and Hultink, E. J. (2017). The Circular Economy – a new sustainability paradigm? J. Clean. Prod. 143, 757–768. doi:10.1016/j.jclepro.2016.12.048
Gerbers, R., Wegener, K., Dietrich, F., and Dröder, K. (2018). Safe, flexible and productive human-robot-collaboration for disassembly of lithium-ion batteries, 99–126. doi:10.1007/978-3-319-70572-9_6
Global Battery Alliance (2024). Global battery alliance. Available at: https://www.globalbattery.org/.
Gong, L. (2018). Virtual reality technology for factory layout planning. Chalmers Reproservice, Gothenburg, Sweden: Chalmers University of Technology.
Gong, L., Söderlund, H., Bogojevic, L., Chen, X., Berce, A., Fast-Berglund, Å., et al. (2020). Interaction design for multi-user virtual reality systems: an automotive case study. Procedia CIRP 93, 1259–1264. doi:10.1016/j.procir.2020.04.036
Gonzalez-Salazar, M., Kormazos, G., and Jienwatcharamongkhol, V. (2023). Assessing the economic and environmental impacts of battery leasing and selling models for electric vehicle fleets: a study on customer and company implications. J. Clean. Prod. 422, 138356. doi:10.1016/j.jclepro.2023.138356
Hannan, M. A., Hoque, M. M., Hussain, A., Yusof, Y., and Ker, P. J. (2018). State-of-the-Art and energy management system of lithium-ion batteries in electric vehicle applications: issues and recommendations. IEEE Access 6, 19362–19378. doi:10.1109/ACCESS.2018.2817655
Harper, G., Sommerville, R., Kendrick, E., Driscoll, L., Slater, P., Stolkin, R., et al. (2019). Recycling lithium-ion batteries from electric vehicles. Nature 575 (7781), 75–86. doi:10.1038/s41586-019-1682-5
Harsdorff, M., Montt, G. E., Rius, A., Bonnet, A., and Luu, T. (2020). Jobs in green and healthy transport: making the green shift. Geneva, Switzerland: ILO.
Hartzler, B., Hinde, J., Lang, S., Correia, N., Yermash, J., Yap, K., et al. (2022). Virtual training is more cost-effective than in-person training for preparing staff to implement contingency management. J. Technol. Behav. Sci. 8 (3), 255–264. doi:10.1007/s41347-022-00283-1
Hastig, G. M., and Sodhi, M. S. (2020). Blockchain for supply chain traceability: business requirements and critical success factors. Prod. Operations Manag. 29 (4), 935–954. doi:10.1111/poms.13147
Hu, X., Wang, C., Zhu, X., Yao, C., and Ghadimi, P. (2021). Trade structure and risk transmission in the international automotive Li-ion batteries trade. Resour. Conservation Recycl. 170, 105591. doi:10.1016/j.resconrec.2021.105591
Hu, X., Yang, Z., Sun, J., and Zhang, Y. (2023). Optimal pricing strategy for electric vehicle battery swapping: pay-per-swap or subscription? Transp. Res. Part E Logist. Transp. Rev. 171, 103030. doi:10.1016/j.tre.2023.103030
Huster, S., Glöser-Chahoud, S., Rosenberg, S., and Schultmann, F. (2022). A simulation model for assessing the potential of remanufacturing electric vehicle batteries as spare parts. J. Clean. Prod. 363, 132225. doi:10.1016/j.jclepro.2022.132225
International Organization for Standardization (2011a). ISO 10218-1:2011 Robots and robotic devices — safety requirements for industrial robots — Part 1: robots. Available at: https://www.iso.org/standard/51330.html.
International Organization for Standardization (2011b). ISO 10218-2:2011 Robots and robotic devices — safety requirements for industrial robots — Part 2: robot systems and integration. Available at: https://www.iso.org/standard/41571.html.
International Organization for Standardization (2024). ISO 59004 Circular economy — vocabulary, principles and guidance for implementation. Available at: https://www.iso.org/standard/80648.html.
Jackson, M., Lederwasch, A., and Giurco, D. (2014). Transitions in theory and practice: managing metals in the circular economy. Resources 3 (3), 516–543. doi:10.3390/resources3030516
Jacobs, C., Soulliere, K., Sawyer-Beaulieu, S., Sabzwari, A., and Tam, E. (2022). Challenges to the circular economy: recovering wastes from simple versus complex products. Sustainability 14 (5), 2576. doi:10.3390/su14052576
Janek, J., and Zeier, W. G. (2023). Challenges in speeding up solid-state battery development. Nat. Energy 8 (3), 230–240. doi:10.1038/s41560-023-01208-9
Jansen, M., Meisen, T., Plociennik, C., Berg, H., Pomp, A., and Windholz, W. (2023). Stop guessing in the dark: identified requirements for digital product passport systems. Systems 11 (3), 123. doi:10.3390/systems11030123
Jensen, S. F., Kristensen, J. H., Adamsen, S., Christensen, A., and Waehrens, B. V. (2023). Digital product passports for a circular economy: data needs for product life cycle decision-making. Sustain. Prod. Consum. 37, 242–255. doi:10.1016/j.spc.2023.02.021
Jerald, J. (2016). The VR book – human-centered design for virtual reality. New York City, United States: Association for Computing Machinery and Morgan and Claypool. doi:10.1145/2792790
Jiao, N. (2017). “Business model for second-life electric vehicle battery systems,” (Cambridge: University of Cambridge).
Jung, K., Shin, H., Park, M., and Lee, J. (2019). Solid-state lithium batteries: bipolar design, fabrication, and electrochemistry. ChemElectroChem 6 (15), 3842–3859. doi:10.1002/celc.201900736
Kamal, M. M., Sivarajah, U., Bigdeli, A. Z., Missi, F., and Koliousis, Y. (2020). Servitization implementation in the manufacturing organisations: classification of strategies, definitions, benefits and challenges. Int. J. Inf. Manag. 55, 102206. doi:10.1016/j.ijinfomgt.2020.102206
Kay, I., Farhad, S., Mahajan, A., Esmaeeli, R., and Hashemi, S. R. (2022). Robotic disassembly of electric vehicles’ battery modules for recycling. Energies 15 (13), 4856. doi:10.3390/en15134856
Kennedy, S., and Linnenluecke, M. K. (2022). Circular economy and resilience: a research agenda. Bus. Strategy Environ. 31 (6), 2754–2765. doi:10.1002/bse.3004
King, M. R. N., Timms, P. D., and Mountney, S. (2023). A proposed universal definition of a Digital Product Passport Ecosystem (DPPE): worldviews, discrete capabilities, stakeholder requirements and concerns. J. Clean. Prod. 384, 135538. doi:10.1016/j.jclepro.2022.135538
Koepp, M. J., Gunn, R. N., Lawrence, A. D., Cunningham, V. J., Dagher, A., Jones, T., et al. (1998). Evidence for striatal dopamine release during a video game. Nature 393 (6682), 266–268. doi:10.1038/30498
Kolb, D. A., Boyatzis, R. E., and Mainemelis, C. (2014). “Experiential learning theory: previous research and new directions,” in Perspectives on thinking, learning, and cognitive styles (New York, United States: Routledge), 227–248. doi:10.4324/9781410605986-9
Kornas, T., Knak, E., Daub, R., Bührer, U., Lienemann, C., Heimes, H., et al. (2019). A multivariate KPI-based method for quality assurance in lithium-ion-battery production. Procedia CIRP 81, 75–80. doi:10.1016/j.procir.2019.03.014
Krichenbauer, M., Yamamoto, G., Taketom, T., Sandor, C., and Kato, H. (2018). Augmented reality versus virtual reality for 3D object manipulation. IEEE Trans. Vis. Comput. Graph. 24 (2), 1038–1048. doi:10.1109/TVCG.2017.2658570
Krima, S., Hedberg, T., and Barnard-Feeney, A. (2019). Securing the digital threat for smart manufacturing. doi:10.6028/NIST.AMS.300-6
Kurz, L., Forster, S., Wörner, R., and Reichert, F. (2022). Environmental impacts of specific recyclates in European battery regulatory-compliant lithium-ion cell manufacturing. Sustainability 15 (1), 103. doi:10.3390/su15010103
Kwade, A., Haselrieder, W., Leithoff, R., Modlinger, A., Dietrich, F., and Droeder, K. (2018). Current status and challenges for automotive battery production technologies. Nat. Energy 3 (4), 290–300. doi:10.1038/s41560-018-0130-3
Lämkull, D., Hanson, L., and Örtengren, R. (2005). Digital human models’ appearance impact on observers’ ergonomic assessment. SAE Technical Papers. doi:10.4271/2005-01-2722
Lebedeva, N., Di Persio, F., and Boon-Brett, L. (2016). Lithium ion battery value chain and related opportunities for Europe. Luxembourg: Publications Office of the European Union. doi:10.2760/6060
Leng, J., Sha, W., Wang, B., Zheng, P., Zhuang, C., Liu, Q., et al. (2022). Industry 5.0: prospect and retrospect. J. Manuf. Syst. 65, 279–295. doi:10.1016/j.jmsy.2022.09.017
Li, J., Lu, Y., Yang, T., Ge, D., Wood, D. L., and Li, Z. (2020). Water-based electrode manufacturing and direct recycling of lithium-ion battery electrodes—a green and sustainable manufacturing system. IScience 23 (5), 101081. doi:10.1016/j.isci.2020.101081
Li, W., Yang, M., Long, R., Mamaril, K., and Chi, Y. (2021). Treatment of electric vehicle battery waste in China: a review of existing policies. J. Environ. Eng. Landsc. Manag. 29 (2), 111–122. doi:10.3846/jeelm.2021.14220
Liu, Y., Zhang, R., Wang, J., and Wang, Y. (2021). Current and future lithium-ion battery manufacturing. IScience 24 (4), 102332. doi:10.1016/j.isci.2021.102332
Ludwig, B., Zheng, Z., Shou, W., Wang, Y., and Pan, H. (2016). Solvent-free manufacturing of electrodes for lithium-ion batteries. Sci. Rep. 6 (1), 23150. doi:10.1038/srep23150
Mak, H.-Y., Rong, Y., and Shen, Z.-J. M. (2013). Infrastructure planning for electric vehicles with battery swapping. Manag. Sci. 59 (7), 1557–1575. doi:10.1287/mnsc.1120.1672
Malmsköld, L., Örtengren, R., and Svensson, L. (2015). Improved quality output through computer-based training: an automotive assembly field study. Hum. Factors Ergonomics Manuf. Serv. Industries 25 (3), 304–318. doi:10.1002/hfm.20540
Mandade, P., Weil, M., Baumann, M., and Wei, Z. (2023). Environmental life cycle assessment of emerging solid-state batteries: a review. Chem. Eng. J. Adv. 13, 100439. doi:10.1016/j.ceja.2022.100439
Marchese, D., Reynolds, E., Bates, M. E., Morgan, H., Clark, S. S., and Linkov, I. (2018). Resilience and sustainability: similarities and differences in environmental management applications. Sci. Total Environ. 613–614, 1275–1283. doi:10.1016/j.scitotenv.2017.09.086
Martinez-Laserna, E., Gandiaga, I., Sarasketa-Zabala, E., Badeda, J., Stroe, D.-I., Swierczynski, M., et al. (2018). Battery second life: hype, hope or reality? A critical review of the state of the art. Renew. Sustain. Energy Rev. 93, 701–718. doi:10.1016/j.rser.2018.04.035
Mathur, N., Deng, S., Singh, S., Yih, Y., and Sutherland, J. W. (2019). Evaluating the environmental benefits of implementing Industrial Symbiosis to used electric vehicle batteries. Procedia CIRP 80, 661–666. doi:10.1016/j.procir.2019.01.074
Mauler, L., Duffner, F., Zeier, W. G., and Leker, J. (2021). Battery cost forecasting: a review of methods and results with an outlook to 2050. Energy and Environ. Sci. 14 (9), 4712–4739. doi:10.1039/D1EE01530C
McKinsey (2023). Battery 2030: resilient, sustainable, and circular. Available at: https://www.mckinsey.com/industries/automotive-and-assembly/our-insights/battery-2030-resilient-sustainable-and-circular.
Melin, H. E., Rajaeifar, M. A., Ku, A. Y., Kendall, A., Harper, G., and Heidrich, O. (2021). Global implications of the EU battery regulation. Science 373 (6553), 384–387. doi:10.1126/science.abh1416
Merdan, M., Lepuschitz, W., Meurer, T., and Vincze, M. (2010). “Towards ontology-based automated disassembly systems,” in IECON 2010 - 36th Annual Conference on IEEE Industrial Electronics Society, Glendale, AZ, USA, 07-10 November 2010 (IEEE), 1392–1397.
METI (2023). Growth-oriented, resource-autonomous circular economy. Available at: https://www.meti.go.jp/english/press/2022/1003_006.html.
Mourtzis, D., Angelopoulos, J., and Panopoulos, N. (2022). Operator 5.0: a survey on enabling technologies and a framework for digital manufacturing based on extended reality. J. Mach. Eng. 22 (1), 43–69. doi:10.36897/jme/147160
Neumann, J., Petranikova, M., Meeus, M., Gamarra, J. D., Younesi, R., Winter, M., et al. (2022). Recycling of lithium-ion batteries—current state of the art, circular economy, and next generation recycling. Adv. Energy Mater. 12 (17). doi:10.1002/aenm.202102917
Nykvist, B., and Nilsson, M. (2015). Rapidly falling costs of battery packs for electric vehicles. Nat. Clim. Change 5 (4), 329–332. doi:10.1038/nclimate2564
Oliveira, L., Messagie, M., Rangaraju, S., Sanfelix, J., Hernandez Rivas, M., and Van Mierlo, J. (2015). Key issues of lithium-ion batteries – from resource depletion to environmental performance indicators. J. Clean. Prod. 108, 354–362. doi:10.1016/j.jclepro.2015.06.021
Omariba, Z. B., Zhang, L., and Sun, D. (2019). Review of battery cell balancing methodologies for optimizing battery pack performance in electric vehicles. IEEE Access 7, 129335–129352. doi:10.1109/ACCESS.2019.2940090
Petranikova, M., Naharro, P. L., Vieceli, N., Lombardo, G., and Ebin, B. (2022). Recovery of critical metals from EV batteries via thermal treatment and leaching with sulphuric acid at ambient temperature. Waste Manag. 140, 164–172. doi:10.1016/j.wasman.2021.11.030
Rajaeifar, M. A., Ghadimi, P., Raugei, M., Wu, Y., and Heidrich, O. (2022). Challenges and recent developments in supply and value chains of electric vehicle batteries: a sustainability perspective. Resour. Conservation Recycl. 180, 106144. doi:10.1016/j.resconrec.2021.106144
Richter, J. L. (2022). A circular economy approach is needed for electric vehicles. Nat. Electron. 5 (1), 5–7. doi:10.1038/s41928-021-00711-9
Rietmann, N., Hügler, B., and Lieven, T. (2020). Forecasting the trajectory of electric vehicle sales and the consequences for worldwide CO2 emissions. J. Clean. Prod. 261, 121038. doi:10.1016/j.jclepro.2020.121038
Rikala, P., Braun, G., Järvinen, M., Stahre, J., and Hämäläinen, R. (2024). Understanding and measuring skill gaps in Industry 4.0 — a review. Technol. Forecast. Soc. Change 201, 123206. doi:10.1016/j.techfore.2024.123206
Rocha, C. S., Antunes, P., and Partidário, P. (2019). Design for sustainability models: a multiperspective review. J. Clean. Prod. 234, 1428–1445. doi:10.1016/j.jclepro.2019.06.108
Rönkkö, P., Majava, J., Hyvärinen, T., Oksanen, I., Tervonen, P., and Lassi, U. (2023). The circular economy of electric vehicle batteries: a Finnish case study. Environ. Syst. Decis. 44, 100–113. doi:10.1007/s10669-023-09916-z
Ryu, M., Hong, Y.-K., Lee, S.-Y., and Park, J. H. (2023). Ultrahigh loading dry-process for solvent-free lithium-ion battery electrode fabrication. Nat. Commun. 14 (1), 1316. doi:10.1038/s41467-023-37009-7
Sångeland, C., Mindemark, J., Younesi, R., and Brandell, D. (2019). Probing the interfacial chemistry of solid-state lithium batteries. Solid State Ionics 343, 115068. doi:10.1016/j.ssi.2019.115068
Schleich, B., Wärmefjord, K., Söderberg, R., and Wartzack, S. (2018). Geometrical variations management 4.0: towards next generation geometry assurance. Procedia CIRP 75, 3–10. doi:10.1016/j.procir.2018.04.078
Schnell, J., Günther, T., Knoche, T., Vieider, C., Köhler, L., Just, A., et al. (2018). All-solid-state lithium-ion and lithium metal batteries – paving the way to large-scale production. J. Power Sources 382, 160–175. doi:10.1016/j.jpowsour.2018.02.062
Schulz-Mönninghoff, M., and Evans, S. (2023). Key tasks for ensuring economic viability of circular projects: learnings from a real-world project on repurposing electric vehicle batteries. Sustain. Prod. Consum. 35, 559–575. doi:10.1016/j.spc.2022.11.025
Shahjalal, M., Roy, P. K., Shams, T., Fly, A., Chowdhury, J. I., Ahmed, M. R., et al. (2022). A review on second-life of Li-ion batteries: prospects, challenges, and issues. Energy 241, 122881. doi:10.1016/j.energy.2021.122881
Shang, Y., Song, M., and Zhao, X. (2022). The development of China’s Circular Economy: from the perspective of environmental regulation. Waste Manag. 149, 186–198. doi:10.1016/j.wasman.2022.05.027
Sharma, A., Zanotti, P., and Musunur, L. P. (2019). Enabling the electric future of mobility: robotic automation for electric vehicle battery assembly. IEEE Access 7, 170961–170991. doi:10.1109/ACCESS.2019.2953712
Sharma, A. (2024). Making electric vehicle batteries safer through better inspection using artificial intelligence and cobots. Int. J. Prod. Res. 62 (4), 1277–1296. doi:10.1080/00207543.2023.2180308
Söderberg, R., Wärmefjord, K., Carlson, J. S., and Lindkvist, L. (2017). Toward a Digital Twin for real-time geometry assurance in individualized production. CIRP Ann. 66 (1), 137–140. doi:10.1016/j.cirp.2017.04.038
Song, Z., Chen, F., Martinez-Ibañez, M., Feng, W., Forsyth, M., Zhou, Z., et al. (2023). A reflection on polymer electrolytes for solid-state lithium metal batteries. Nat. Commun. 14 (1), 4884. doi:10.1038/s41467-023-40609-y
Sopha, B. M., Purnamasari, D. M., and Ma’mun, S. (2022). Barriers and enablers of circular economy implementation for electric-vehicle batteries: from systematic literature review to conceptual framework. Sustainability 14 (10), 6359. doi:10.3390/su14106359
Strojny, P., and Dużmańska-Misiarczyk, N. (2023). Measuring the effectiveness of virtual training: a systematic review. Comput. Educ. X Real. 2, 100006. doi:10.1016/j.cexr.2022.100006
Sun, T., Franciosa, P., and Ceglarek, D. (2021). Effect of focal position offset on joint integrity of AA1050 battery busbar assembly during remote laser welding. J. Mater. Res. Technol. 14, 2715–2726. doi:10.1016/j.jmrt.2021.08.002
Takata, S., Suemasu, K., and Asai, K. (2019). Life cycle simulation system as an evaluation platform for multitiered circular manufacturing systems. CIRP Ann. 68 (1), 21–24. doi:10.1016/j.cirp.2019.04.081
Tan, D. H. S., Banerjee, A., Chen, Z., and Meng, Y. S. (2020). From nanoscale interface characterization to sustainable energy storage using all-solid-state batteries. Nat. Nanotechnol. 15 (3), 170–180. doi:10.1038/s41565-020-0657-x
Tao, F., Kishita, Y., Scheller, C., Blömeke, S., and Umeda, Y. (2022). Designing a sustainable circulation system of second-life traction batteries: a scenario-based simulation approach. Procedia CIRP 105, 733–738. doi:10.1016/j.procir.2022.02.122
Tavana, M., Sohrabi, M., Rezaei, H., Sorooshian, S., and Mina, H. (2023). A sustainable circular supply chain network design model for electric vehicle battery production using internet of things and big data. Expert Syst. 41, e13395. doi:10.1111/exsy.13395
The Battery Pass consortium (2023). Battery passport content guidance: achieving compliance with the EU battery regulation and increasing sustainability and circularity.
Tian, J., Wang, Y., Liu, C., and Chen, Z. (2020). Consistency evaluation and cluster analysis for lithium-ion battery pack in electric vehicles. Energy 194, 116944. doi:10.1016/j.energy.2020.116944
Torres, F., Gil, P., Puente, S. T., Pomares, J., and Aracil, R. (2004). Automatic PC disassembly for component recovery. Int. J. Adv. Manuf. Technol. 23 (1–2), 39–46. doi:10.1007/s00170-003-1590-5
United Nations (2022). World population prospects. Available at: https://population.un.org/wpp/.
United States Congress (2022). Inflation reduction Act, H.R. 5376. Available at: https://www.congress.gov/bill/117th-congress/house-bill/5376.
University of Cambridge Institute for Sustainability Leadership (CISL) and the Wuppertal Institute (2022). Digital Product Passport: the ticket to achieving a climate neutral and circular European economy?
Vandermerwe, S., and Rada, J. (1988). Servitization of business: adding value by adding services. Eur. Manag. J. 6 (4), 314–324. doi:10.1016/0263-2373(88)90033-3
VanGeem, M. G. (2018). Defining resilience. Adv. Civ. Eng. Mater. 7 (1), 308–315. doi:10.1520/ACEM20170136
Veile, J. W., Schmidt, M.-C., and Voigt, K.-I. (2022). Toward a new era of cooperation: how industrial digital platforms transform business models in Industry 4.0. J. Bus. Res. 143, 387–405. doi:10.1016/j.jbusres.2021.11.062
Vidal, C., Malysz, P., Kollmeyer, P., and Emadi, A. (2020). Machine learning applied to electrified vehicle battery state of charge and state of health estimation: state-of-the-art. IEEE Access 8, 52796–52814. doi:10.1109/ACCESS.2020.2980961
Walden, J., Steinbrecher, A., and Marinkovic, M. (2021). Digital product passports as enabler of the circular economy. Chemie-Ingenieur-Technik 93 (11), 1717–1727. doi:10.1002/cite.202100121
Wang, C., Chen, B., Yu, Y., Wang, Y., and Zhang, W. (2017). Carbon footprint analysis of lithium ion secondary battery industry: two case studies from China. J. Clean. Prod. 163, 241–251. doi:10.1016/j.jclepro.2016.02.057
Wang, L., Liu, S., Liu, H., and Wang, X. V. (2020a). Overview of human-robot collaboration in manufacturing, 15–58. doi:10.1007/978-3-030-46212-3_2
Wang, Q., Mao, B., Stoliarov, S. I., and Sun, J. (2019). A review of lithium ion battery failure mechanisms and fire prevention strategies. Prog. Energy Combust. Sci. 73, 95–131. doi:10.1016/j.pecs.2019.03.002
Wang, Y., Tian, J., Sun, Z., Wang, L., Xu, R., Li, M., et al. (2020b). A comprehensive review of battery modeling and state estimation approaches for advanced battery management systems. Renew. Sustain. Energy Rev. 131, 110015. doi:10.1016/j.rser.2020.110015
Wanger, T. C. (2011). The Lithium future-resources, recycling, and the environment. Conserv. Lett. 4 (3), 202–206. doi:10.1111/j.1755-263X.2011.00166.x
Wegener, K., Chen, W. H., Dietrich, F., Dröder, K., and Kara, S. (2015). Robot assisted disassembly for the recycling of electric vehicle batteries. Procedia CIRP 29, 716–721. doi:10.1016/j.procir.2015.02.051
Westerlund, L. (2023). Enabling a circular economy with digital product passports: information requirements and data collection practices. Universitetsservice, Stockholm, Sweden: KTH.
Westermeier, M., Reinhart, G., and Steber, M. (2014). Complexity management for the start-up in lithium-ion cell production. Procedia CIRP 20, 13–19. doi:10.1016/j.procir.2014.05.026
Wickerts, S., Arvidsson, R., Nordelöf, A., Svanström, M., and Johansson, P. (2024). Prospective life cycle assessment of sodium-ion batteries made from abundant elements. J. Industrial Ecol. 28 (1), 116–129. doi:10.1111/jiec.13452
Wollter Bergman, M., Berlin, C., Chafi, M. B., Falck, A.-C., and Örtengren, R. (2021). Cognitive ergonomics of assembly work from a job demands–resources perspective: three qualitative case studies. Int. J. Environ. Res. Public Health 18 (23), 12282. doi:10.3390/ijerph182312282
World Economic Forum (2019). A vision for a sustainable battery value chain in 2030. Available at: https://www3.weforum.org/docs/WEF_A_Vision_for_a_Sustainable_Battery_Value_Chain_in_2030_Report.pdf.
Wrålsen, B., and O’Born, R. (2023). Use of life cycle assessment to evaluate circular economy business models in the case of Li-ion battery remanufacturing. Int. J. Life Cycle Assess. 28 (5), 554–565. doi:10.1007/s11367-023-02154-0
Wu, B., Widanage, W. D., Yang, S., and Liu, X. (2020). Battery digital twins: perspectives on the fusion of models, data and artificial intelligence for smart battery management systems. Energy AI 1, 100016. doi:10.1016/j.egyai.2020.100016
Xiao, J., Jiang, C., and Wang, B. (2023). A review on dynamic recycling of electric vehicle battery: disassembly and echelon utilization. Batteries 9 (1), 57. doi:10.3390/batteries9010057
Xing, Y., Ma, E. W. M., Tsui, K. L., and Pecht, M. (2011). Battery management systems in electric and hybrid vehicles. Energies 4 (11), 1840–1857. doi:10.3390/en4111840
Xu, C., Dai, Q., Gaines, L., Hu, M., Tukker, A., and Steubing, B. (2020a). Future material demand for automotive lithium-based batteries. Commun. Mater. 1 (1), 99. doi:10.1038/s43246-020-00095-x
Xu, L.Da, Xu, E. L., and Li, L. (2018). Industry 4.0: state of the art and future trends. Int. J. Prod. Res. 56 (8), 2941–2962. doi:10.1080/00207543.2018.1444806
Xu, P., Dai, Q., Gao, H., Liu, H., Zhang, M., Li, M., et al. (2020b). Efficient direct recycling of lithium-ion battery cathodes by targeted healing. Joule 4 (12), 2609–2626. doi:10.1016/j.joule.2020.10.008
Xu, Z., Wu, S., Xu, S., Wang, P., Jiang, X., Cheng, M., et al. (2021). “Study on the life cycle traceability management of NEV traction battery based on industrial internet identifier resolve system,” in 2021 IEEE International Conference on Power Electronics, Computer Applications (ICPECA), Shenyang, China, 22-24 January 2021 (IEEE), 26–31.
Yan, W., Cao, H., Zhang, Y., Ning, P., Song, Q., Yang, J., et al. (2020). Rethinking Chinese supply resilience of critical metals in lithium-ion batteries. J. Clean. Prod. 256, 120719. doi:10.1016/j.jclepro.2020.120719
Yang, K., Zhang, L., Zhang, Z., Yu, H., Wang, W., Ouyang, M., et al. (2023). Battery state of health estimate strategies: from data analysis to end-cloud collaborative framework. Batteries 9 (7), 351. doi:10.3390/batteries9070351
Yao, W., Chouchane, M., Li, W., Bai, S., Liu, Z., Li, L., et al. (2023). A 5 V-class cobalt-free battery cathode with high loading enabled by dry coating. Energy and Environ. Sci. 16 (4), 1620–1630. doi:10.1039/D2EE03840D
Yu, W., Guo, Y., Xu, S., Yang, Y., Zhao, Y., and Zhang, J. (2023). Comprehensive recycling of lithium-ion batteries: fundamentals, pretreatment, and perspectives. Energy Storage Mater. 54, 172–220. doi:10.1016/j.ensm.2022.10.033
Yuan, C., Cao, H., Shen, K., Deng, Y., Zeng, D., Dong, Y., et al. (2021). Water-based manufacturing of lithium ion battery for life cycle impact mitigation. CIRP Ann. 70 (1), 25–28. doi:10.1016/j.cirp.2021.04.038
Yuan, G., Liu, X., Zhang, C., Pham, D. T., and Li, Z. (2023). A new heuristic algorithm based on multi-criteria resilience assessment of human–robot collaboration disassembly for supporting spent lithium-ion battery recycling. Eng. Appl. Artif. Intell. 126, 106878. doi:10.1016/j.engappai.2023.106878
Zhang, H., Wang, L., and He, X. (2022). Trends in a study on thermal runaway mechanism of lithium-ion battery with LiNi x Mn y Co 1- x - y O 2 cathode materials. Battery Energy 1 (1). doi:10.1002/bte2.20210011
Zhao, G., Liu, S., Lopez, C., Lu, H., Elgueta, S., Chen, H., et al. (2019). Blockchain technology in agri-food value chain management: a synthesis of applications, challenges and future research directions. Comput. Industry 109, 83–99. doi:10.1016/j.compind.2019.04.002
Zhao, Y., Yuan, X., Jiang, L., Wen, J., Wang, H., Guan, R., et al. (2020). Regeneration and reutilization of cathode materials from spent lithium-ion batteries. Chem. Eng. J. 383, 123089. doi:10.1016/j.cej.2019.123089
Keywords: battery production, digitalization, industry 5.0, electrification, human centeredness, sustainable value chain management, sustainable production, life cycle engineering
Citation: Johansson B, Despeisse M, Bokrantz J, Braun G, Cao H, Chari A, Fang Q, González Chávez CA, Skoogh A, Söderlund H, Wang H, Wärmefjord K, Nyborg L, Sun J, Örtengren R, Schumacher KA, Espinal L, Morris KC, Nunley J Jr., Kishita Y, Umeda Y, Acerbi F, Pinzone M, Persson H, Charpentier S, Edström K, Brandell D, Gopalakrishnan M, Rahnama H, Abrahamsson L, Rönnbäck AÖ and Stahre J (2024) Challenges and opportunities to advance manufacturing research for sustainable battery life cycles. Front. Manuf. Technol. 4:1360076. doi: 10.3389/fmtec.2024.1360076
Received: 22 December 2023; Accepted: 05 June 2024;
Published: 20 August 2024.
Edited by:
Duck Young Kim, Pohang University of Science and Technology, Republic of KoreaReviewed by:
Franz Dietrich, Technical University of Berlin, GermanyJian Zhang, Shantou University, China
Copyright © 2024 Johansson, Despeisse, Bokrantz, Braun, Cao, Chari, Fang, González Chávez, Skoogh, Söderlund, Wang, Wärmefjord, Nyborg, Sun, Örtengren, Schumacher, Espinal, Morris, Nunley, Kishita, Umeda, Acerbi, Pinzone, Persson, Charpentier, Edström, Brandell, Gopalakrishnan, Rahnama, Abrahamsson, Rönnbäck and Stahre. This is an open-access article distributed under the terms of the Creative Commons Attribution License (CC BY). The use, distribution or reproduction in other forums is permitted, provided the original author(s) and the copyright owner(s) are credited and that the original publication in this journal is cited, in accordance with accepted academic practice. No use, distribution or reproduction is permitted which does not comply with these terms.
*Correspondence: Björn Johansson, Ympvcm4uam9oYW5zc29uQGNoYWxtZXJzLnNl