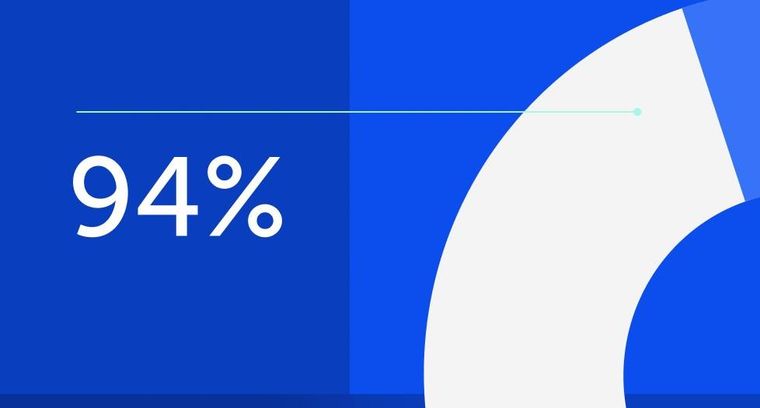
94% of researchers rate our articles as excellent or good
Learn more about the work of our research integrity team to safeguard the quality of each article we publish.
Find out more
EDITORIAL article
Front. Manuf. Technol., 03 January 2024
Sec. Material Forming and Removal
Volume 3 - 2023 | https://doi.org/10.3389/fmtec.2023.1352187
This article is part of the Research TopicRolling Bearing Optimization through Innovative Manufacturing ProcessesView all 4 articles
Editorial on the Research Topic
Rolling bearing optimization through innovative manufacturing processes
Addressing the imperative issues of resource conservation and the reduction of CO2 emissions is crucial in the global effort to mitigate climate change. The demand for solutions in this domain is steadily increasing, particularly in the field of conventional machinery executing rotational movements. As the transition to larger wind turbines and electric drives unfolds, new challenges emerge concerning the fatigue and durability of bearing materials. Effectively addressing these challenges necessitates the translation of innovative research findings into industrial applications. Currently, there is a heightened focus on pioneering procedures, both existing and in development, aimed at significantly enhancing the performance of bearings and lubrication systems. This emphasis on innovation is essential for fostering a sustainable and efficient future.
In recent years, a considerable body of research has been dedicated to enhancing bearings through the utilization of novel manufacturing processes. One notable example is the use of deep rolling processes to significantly extend the service life of bearings (Pape et al., 2020). This approach has been coupled with hard turning, taking into account the impact of induced residual stresses and improved surface roughness. Moreover, emerging manufacturing techniques, such as tailored forming, have demonstrated the ability to conserve valuable raw materials and reduce the weight of bearings (Coors et al., 2018). Surface modifications applied to bearing surfaces have been explored as a means to decrease frictional losses. The application of coatings on bearings is particularly noteworthy, as it serves to prevent damage to bearing surfaces in the event of conventional lubricant failure during operation. Furthermore, the integration of sensors has been investigated to enable more effective monitoring of bearing conditions (Pape et al., 2023). Notably, self-regenerative coatings like molybdenum oxide with a molybdenum reservoir exhibit intriguing properties in this context (Konopka et al., 2022). Ongoing research is also placing emphasis on developing additional optimized surfaces and surface textures for further advancements in bearing performance. Three exciting contributions have been submitted in the field of bearings.
Hwang and Poll presents a method to more accurately predict bearing life under complex operating conditions, such as oscillation, while considering surface residual stresses. In the standardized calculation method, material properties, such as fatigue limit stress, were taken into account by introducing the fatigue limit stress proposed by Ioannides and Harris. This standard calculation method provides a reasonable range for fatigue life, aligning well with experimental results under ideal test conditions, such as constant external load. However, complex operating conditions of bearings, such as fluctuating loads and oscillating movements, are not considered. Nevertheless, this is essential for the application of bearings in machinery, such as wind turbines. Hence, there is a need for a new analytical calculation model that can predict the fatigue life of bearings under these complex conditions. In the proposed approach, fatigue life is determined based on the Palmgren-Miner linear damage rule by evaluating subsurface stresses below the rolling contact using the S-N curve according to the fatigue criterion of Lundberg and Palmgren. Hwang and Poll work confirmed that the analytically determined fatigue life according to ISO 281 still remains close to the results of bearing life tests.
In another article, tapered roller bearings are optimized concerning lubrication. Liu et al. investigate the contact between the roller end and the rib of tapered roller bearings. This contact significantly influences the lubrication state and performance loss. To enhance the lubrication performance of the inner ring rib and the large roller end in tapered roller bearings used in railway wagons, a thermal elastohydrodynamic lubrication model was created based on the structural analysis of the inner rib and the large roller end. This considers spin-slide effects between the rib and the large roller end, using a Carreau rheological model in a tapered roller bearing. Under various conditions, variations in the friction coefficient were compared to the ratio of the curvature radii of the large roller end to the rib, and the film thickness and film temperature varied with the speed, while the effect of the load between the two rib structures was compared. The results showed that rotational movement has little influence on the lubrication at the contact point between the inner ring rib and the large roller end of the tapered roller bearing. There exists an optimal ratio of curvature radii between the large roller end and the spherical or conical rib; furthermore, the friction coefficient corresponding to this optimal ratio value is the lowest. With increasing inner ring speed, both the film thickness and temperature increase for the two rib structures. In contrast to the spherical rib, the difference between the minimum and central film thickness is nearly constant, and the conical rib shows a slight temperature increase. With increasing load, the difference between the minimum and central film thickness becomes larger, and the temperature in the contact zone gradually rises for both ribs. In contrast to the conical rib, due to the higher film temperature, the spherical rib exhibits a lower friction coefficient and a smaller minimum film thickness
Kelley et al. pursue an alternative approach to enhance lubrication conditions by using micro textures on bearing surfaces. Microtextures are employed to mitigate friction in start-stop cycles, under mixed lubrication conditions, and during sliding in a rolling element bearing, as well as at the contact between a roller and a bearing rib. The selection of the microstructure geometry is crucial, ensuring that individual depressions in the contact area between the ball or roller and the bearing surface act as reservoirs for the lubricant. Initial applications involving microstructured angular contact ball bearings under oscillating motion conditions demonstrated friction-reducing effects during reciprocating motion, where the microstructures functioned as lubricant reservoirs. This concept is extended to the sliding contact for tapered roller bearings, exploring whether the observed reductions in friction can be attributed to the microstructures acting as lubricant reservoirs or if there is a positive hydrodynamic effect due to the microstructures. Through a calculation approach and some illustrative bench test measurements, the behavior of microstructured tapered roller bearings is investigated. An examplarly micro dimple is shown in Figure 1. It is obvious, that small dimples help to increase the central film thickness.
FIGURE 1. Center-line film thickness and pressure in X and Y directions for 0.5 µm deep micro dimple and film thickness distribution, pressure-ciscosity coefficient of 15 GPa−1.
FP: Conceptualization, Writing–original draft, Writing–review and editing. JT: Writing–review and editing. OM: Writing–review and editing. XL: Writing–review and editing.
The author(s) declare that no financial support was received for the research, authorship, and/or publication of this article.
Author JT was employed by the company Thyssenkrupp Rothe Erde Germany GmbH. Author OM was employed by the company Ecoroll AG Werkzeugtechnik.
The remaining authors declare that the research was conducted in the absence of any commercial or financial relationships that could be construed as a potential conflict of interest.
All claims expressed in this article are solely those of the authors and do not necessarily represent those of their affiliated organizations, or those of the publisher, the editors and the reviewers. Any product that may be evaluated in this article, or claim that may be made by its manufacturer, is not guaranteed or endorsed by the publisher.
Coors, T., Pape, F., and Poll, G. (2018). Bearing fatigue life of a multi-material shaft with an integrated raceway. Bear. World J. 3, 23–30.
Konopka, D., Pape, F., and Poll, G. (2022). “Untersuchungen zur Funktionsfähigkeit von trockengeschmierten molybdänbasierten Axialzylinderrollenlagern,” in book: Reibung, Schmierung und Verschleiß Forschung und praktische Anwendungen, Proceedings, 63. Tribologie-Fachtagung (Publisher: Gesellschaft für Tribologie e.V) P2/1–P2/4.
Pape, F., Coors, T., and Poll, G. (2020). Studies on the influence of residual stresses on the fatigue life of rolling bearings in dependence on the production processes. Front. Mech. Eng. 6, 56. doi:10.3389/fmech.2020.00056
Pape, F., Konopka, D., Coors, T., Poll, G., Steppeler, T., Ottermann, R., et al. (2023). “Direct sensor integration on the raceway of roller bearings,” in book: 64. Tribologie-Fachtagung 2023 Reibung, Schmierung und Verschleiß Forschung und praktische Anwendung, Chapter P3 (Publisher: Gesellschaft für Tribologie e.V) P3/1–P3/9.
Keywords: rolling bearings, fatigue, manufacturing, tapered roller bearing, micro textured surface
Citation: Pape F, Terwey JT, Maiss O and Li X (2024) Editorial: Rolling bearing optimization through innovative manufacturing processes. Front. Manuf. Technol. 3:1352187. doi: 10.3389/fmtec.2023.1352187
Received: 07 December 2023; Accepted: 14 December 2023;
Published: 03 January 2024.
Edited and reviewed by:
Andrea Ghiotti, University of Padua, ItalyCopyright © 2024 Pape, Terwey, Maiss and Li. This is an open-access article distributed under the terms of the Creative Commons Attribution License (CC BY). The use, distribution or reproduction in other forums is permitted, provided the original author(s) and the copyright owner(s) are credited and that the original publication in this journal is cited, in accordance with accepted academic practice. No use, distribution or reproduction is permitted which does not comply with these terms.
*Correspondence: Florian Pape, cGFwZUBpbWt0LnVuaS1oYW5ub3Zlci5kZQ==
Disclaimer: All claims expressed in this article are solely those of the authors and do not necessarily represent those of their affiliated organizations, or those of the publisher, the editors and the reviewers. Any product that may be evaluated in this article or claim that may be made by its manufacturer is not guaranteed or endorsed by the publisher.
Research integrity at Frontiers
Learn more about the work of our research integrity team to safeguard the quality of each article we publish.