- Laboratory for Manufacturing Systems and Automation, Department of Mechanical Engineering and Aeronautics, University of Patras, Rio Patras, Greece
The shift of traditional mass-producing industries towards mass customisation practices is nowadays evident. However, if not implemented properly, mass customisation can lead to disturbances in material flow and severe reduction in productivity. Moreover, manufacturing enterprises often face the challenge of manufacturing highly customized products in small lot sizes. One solution to adapt to the ever-changing demands, which increases resource flexibility, lies in the digitization of the manufacturing systems. Furthermore, the distributed manufacturing environment and the ever-increasing product variety and complexity result in reduced time-to market, ubiquitous data access and sharing and adaptability and responsiveness to changes. These requirements can be achieved through smart manufacturing tools and especially Wireless Sensor Networks (WSN). Thus, the aim of this position paper is to summarize the design and development of solutions based on cutting-edge technologies such as Cloud Computing, Artificial Intelligence (AI), Internet of Things (IoT), Simulation, 5G, and so on. Concretely, the first part discusses the development of a Cloud-based production planning and control system for discrete manufacturing environments. The proposed approach takes into consideration capacity constraints, lot sizing and priority control in a “bucket-less” manufacturing environment. Then, an open and interoperable Internet of Things platform is discussed, which is enhanced by innovative tools and methods that transform them into Cyber-Physical Systems (CPS), supporting smart customized shopping, through gathering customers’ requirements, adaptive production, and logistics of vending machines replenishment and Internet of Things and Wireless Sensor Networks for Smart Manufacturing. To that end, all the proposed methodologies are validated using data derived from Computer Numerical Control (CNC) machine building industry, from European Metal-cutting and mold-making SMEs, from white goods industry and SMEs that produces solar panels.
1 Introduction
In the realm of the Industry 4.0, the manufacturing landscape is undergoing a series of changes. Modern market demand has been transitioned towards the mass personalization of products and services (Mourtzis, 2016; ElMaraghy et al., 2021), including Product-Service Systems (PSS) (Angelopoulos and Mourtzis, 2022). Therefore, demand is driven by quality, quantity and variety of products and services. Furthermore, as it became obvious in the last couple of years, modern manufacturing, and production systems, although they are capable of coping with the volatile customer demand, they suffer from resiliency (Ameri et al., 2022). In other words, taking into consideration of the analogue of the spring/damper system, manufacturing systems can be realized as the spring/damper couple, and the external excitations are the system disturbances (Makkonen, 1999). Due to the insufficient damping effect, external excitations cannot be dampened adequately (in a short time horizon), and by extension self-excited vibrations occur, thus leading the system to its limits/failure. However, engineers are equipped with several digital technologies as well as new techniques (e.g., Artificial Intelligence-AI, Extended Reality-XR), which facilitates the improvement of business models, productivity and revenue rates as well as to ensure high competitiveness (Papakostas and Ramasubramanian, 2022). In this research work the current advances in the topic of scheduling to CMfg focusing on Industry 4.0 implementations are presented and discussed in an attempt to build an adequate theoretical background. In continuation, insightful feedback will be parsed from the practical implementation in real-life modern industrial use cases (Mourtzis et al., 2022a). The contribution of this research work extends to the provision of recommendations on bridging CMfg to Scheduling (Mourtzis, 2020a) and DT (Stavropoulos and Mourtzis, 2022).
Many promising and innovative technologies, such as cloud manufacturing (CMfg) and Digital Twin (DT), have risen to prominence as a result of Industry 4.0, while existing technologies, such as scheduling, have thrived as well (Mourtzis et al., 2020a). Complex hybrid logical and terminal constraints, non-stationary process execution, and complex interrelationships between process design dynamics, power utilization, and system configurations all emerge as unique scheduling issues in Industry 4.0 and CMfg (Ivanov et al., 2018). Key technologies of industry 4.0, particularly cloud manufacturing, enable flexible production, particularly with CPS and highly customized assemblies, and on-demand manufacturing services (Ivanov et al., 2018; Dolgui et al., 2020). As a result of the flexible use of services rather than fixed allocations of machines and operations, process design and job scheduling are integrated in digital manufacturing. Furthermore, services are formed dynamically based on available machines and operations. The services can be built using almost any combination of machines and operations. The emergence of cloud computing is considered as the primary enabler for cloud manufacturing to replace traditional manufacturing methods (Xu, 2012). Companies are reshaping their business models in order to maintain high product quality and integrate customization into their production models as the demand for customized products grows (Zhang et al., 2019). To that end, the current literature contains innovations and techniques based on cloud technologies (Doukas et al., 2014; Mourtzis & Vlachou, 2016; Mourtzis & Vlachou, 2018). The increased demand for customized products has prompted original equipment manufacturers (OEMs) to decentralize, according to Mourtzis et al. (2012a). The authors have also proposed a methodology for identifying efficient supply chains in decentralized production environments in this publication. Effective scheduling, as a fundamental issue in manufacturing, can reduce the time it takes to complete specific tasks, increase resource efficiency, and thus maximize profits. Manufacturing paradigms shift as a result of new technology and manufacturing requirements, and scheduling modes shift accordingly. This paper also emphasizes the importance of scheduling in the design, control, and operation of MFG systems, as well as the main issues that engineers face. The following is a summary of the issues: The generation of requirements, the processing complexity, the scheduling criteria, and the scheduling environment are all factors to consider. As a result, research efforts have centered on developing innovative solutions for integrating existing scheduling techniques with recent technological advancements and changes in the global market schema. There are more than 30 advanced production paradigms, according to the International Society of Production Engineering (Esmaeilian et al., 2016), including the Toyota production system, computer integrated manufacturing system, flexible manufacturing system, lean production, agile manufacturing, reconfigurable manufacturing system, cloud manufacturing, network manufacturing, and intelligent manufacturing. The transformation of production modes causes changes in scheduling modes, as shown in Figure 1 (Jiang et al., 2021).
As shown in Figure 1, production scheduling has evolved through a series of paradigms, first gaining prominence in the early 20th century with the use of the Gantt chart (1916). However, it took another 40 years for Johnson (1954) to publish his paper, which was the first in the field to introduce the mode of two-machine flow shop scheduling. It is commonly regarded as the starting point for scheduling research (Pinedo, 2016) and the starting point of the classic scheduling theory (Potts and Strusevich, 2009). Scheduling can be realized as the series of actions undertaken by engineers in order to distribute and allocate the available resources (including materials, machines, and human operators), in a predefined time horizon, aiming towards the optimization of a single or multiple objectives (Pinedo, 2016; Stecca, 2014). However, due to the increased volatility of market demand (see Mass Customization and Mass Personalization paradigms), manufacturing and production has transitioned to models producing a wider variety of products in smaller quantities. On the other hand, considering the recent advances in digital technologies under the framework of Industry 4.0 (e.g., ICT and Data Analytics), engineers are capable of designing, developing, and implementing new scheduling approaches, which consider external system disturbances, and their effect on the (manufacturing) system behavior, and thus adapt the system’s parameters in order to continuously satisfy the company’s objectives. The above-mentioned approaches fall under the term Adaptive Scheduling. Since then, scheduling has grown into its own discipline within Operations Research (OR). Due to the rapid advancement of information technology in the 1980s, distributed and decentralized scheduling emerged; in 2010, cloud manufacturing, a service-oriented manufacturing mode, gained traction. Scheduling was modeled as a mathematical combination optimisation problem that needed to be solved using exact algorithms, such as dynamic programming and integer programming, from the 1950s to the 1970s. It was later classified as NP-hardness specific questions (Garey et al., 1976). The Palmer method (Palmer 1965), CDS method (Campbell et al., 1970), RA method (Dannenbring 1977), and NEH method (Nawaz et al., 1983) are examples of approximate methods (e.g., constructive and iterative heuristics) that have been used to find near-optimal solutions. Over 100 heuristic approaches had been proposed by 1977 (Panwalkar and Iskander 1977). A variety of metaheuristic algorithms, Artificial Intelligence (AI) methods, and simulation methods/applications have been used in scheduling, as shown in Table 1. Some scheduling issues, such as flexible manufacturing system scheduling and distributed multi-factory scheduling, have arisen as a result of the shift in manufacturing paradigm.
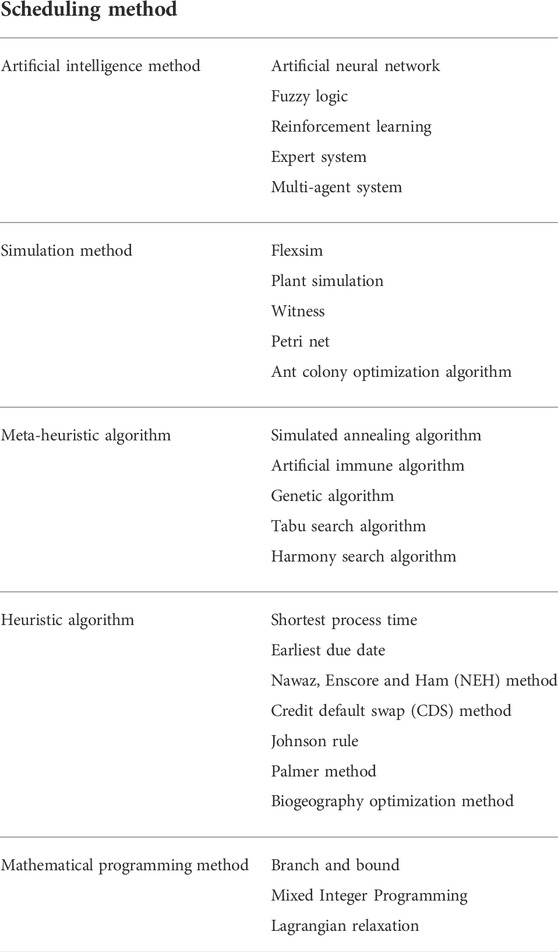
TABLE 1. Production scheduling approaches (adapted from Jiang et al., 2021; Fera et al., 2013).
As a result of the widespread use of personal computers in manufacturing facilities since the 1980s, scheduling has advanced rapidly. In scheduling modeling, incorporating machine reliability into an energy-efficient production plan is a common practice (Hermann J.W., 2006). Furthermore, Mourtzis (2020b) has presented a comprehensive review of the current state of the art and new trends, as well as major historical milestones in the development of simulation engineering for manufacturing systems and recent business approaches and studies in key industrial areas. This study summarizes the fundamentals of cloud manufacturing scheduling, as well as common work on cloud manufacturing service composition and related scheduling issues, as well as research challenges, techniques, and methodologies. Rossit et al. (2019) present Smart Scheduling, a new decision-making scheme that employs an effective screening process to produce flexible and efficient manufacturing schedules while taking advantage of the advantages of both centralized and decentralized production systems. Rolón and Martínez (2012) also present an adaptive decision-making system that supports distributed execution control and emergent scheduling. Finally, in terms of Supervisory Control and Data Acquisition (SCADA) in manufacturing systems, SCADA is a technology that allows one or more remote installations to collect data while sending limited control instructions to those installations (Boyer, 2004). Mourtzis et al. (2019) proposed a methodology for deriving main scheduling decisions for the exploitation of machine data in near-real-time machine condition monitoring to that end. Moving on to supply chain simulation, a model was implemented in the form of an Internet-enabled software framework, offering a set of features such as virtual organization, scheduling, and monitoring to promote cooperation and flexible planning and monitoring across extended manufacturing enterprises (Mourtzis, 2011). Finally, Mourtzis et al. (2021b) present an integrated production and maintenance scheduling method, that is, supported by AR technology and real-time machine monitoring (2021b). Modern production systems must take advantage of as much data from the shop floor as possible in order to respond quickly to any disruption. The developed system is based on a mobile device that collects and uses sensor data for Condition Based Maintenance (CBM). The proposed system is implemented as a mobile application, taking advantage of mobile devices’ increased mobility and accessibility, making it easier for shop-floor operators to perform CBM operations using AR instructions. The system receives all necessary data from sensors in order to monitor the machine’s status, remaining operating time between failures, and proper connections. It also has the capability of detecting available time slots on the current machine schedule in order to plan the maintenance task schedule. Furthermore, the operator’s ability to improve his performance is aided by the connection to the Cloud AR instructions database. Furthermore, the machine schedule is constantly updated by sending feedback based on the duration of the maintenance task, resulting in a significant reduction in system response time. Finally, factory personnel can perform maintenance operations using AR instructions, reducing the need for specialized Original Equipment Manufacturing (OEM) maintenance support.
2 State of the art
2.1 Classification of scheduling problems
Scheduling can be classified as cloud manufacturing scheduling (CMS), decentralized scheduling, distributed scheduling, and centralized scheduling in an object-oriented system, as shown in Figure 2. The most traditional scheduling method is centralized scheduling, which always involves single-factory scheduling. Next, decentralized scheduling results from the decentralized architecture of production systems and distributed scheduling is the result of distributed production environments and the use of multi-agent systems (MAS), which includes distributed flow shop and job shop scheduling, among other things (Mourtzis et al., 2022b).
The goal of centralized and distributed scheduling is to efficiently allocate resources to tasks in order to achieve one or more objectives at the same time while working within processing and resource constraints. CMS, on the other hand, aims to match and select the best service for the job. Exact algorithms, simulation methods, AI methods, metaheuristic algorithms, and heuristic algorithms are examples of centralized scheduling methods. Meanwhile, methods like hierarchical task networks and semantic based matching are used in CMS to solve task decomposition and task-service matching. Finally, metaheuristic algorithms and AI methods are used to solve service composition optimization and cloud manufacturing resource scheduling problems.
2.1.1 Centralized scheduling
The most traditional scheduling problem, centralized scheduling, has been the subject of research for more than half a century, and related studies have yielded promising results. Johnson’s rule was used to solve the two-machine flow shop scheduling problem with the shortest makespan. The simulation method was first applied to dynamic job shop scheduling in 1957 (Jackson 1957). Reiter (1966) was the first to propose the concept of batch scheduling and Graham et al. (1979) summarized prior research and used the triple α|β|γ| to present a scheduling problem. According to the literature, centralized scheduling problems can be classified based on a variety of factors, including the operating environment, system goals, and resource constraints.
2.1.1.1 Operating environment perspectives
The assembly flow shop model and its methods were studied by Komaki et al. (2019). Next, the literature on non-permutation flow-shop scheduling problems was examined by Rossit et al. (2018) and the deterministic job shop scheduling problem was studied by Jain and Meeran (1999) from the perspectives of problem representation, solution method, and benchmark.
2.1.1.2 Objectives and constraints
Behnamian (2016) rearranged the findings of the relevant literature on fuzzy shop scheduling problems, while Akbar and Irohara (2018) focused on sustainable manufacturing scheduling. In terms of methodology, Amjad et al. (2018) performed a statistical analysis of the literature on flexible job shop scheduling using genetic algorithms, Muhamad and Deris (2013) summarized existing literature on artificial immune systems in job shop scheduling; and Çaliş and Bulkan (2015) summarized AI methods in shop scheduling.
2.1.2 Cloud manufacturing scheduling
Cloud technologies have become a requirement for modern manufacturing systems as a result of the fourth industrial revolution, which was followed by the introduction of digitalization and automation in the industrial domain. Cloud Manufacturing (CMfg) is defined by Li et al. (2010) as an advanced manufacturing paradigm that improves resource utilization and efficiency while responding to a wide range of customer needs. The CM is defined as a computer and service-oriented manufacturing model that was created using enterprise information technologies and existing advanced manufacturing models with the help of the Internet of Things, Cloud computing, advanced computing technologies, virtualization, and service-oriented technologies. Kuman et al. support the same definition (2016).
Li et al. (2010) were the first to coin the term “cloud manufacturing.” They define CMfg as an advanced manufacturing paradigm capable of increasing resource utilization while responding quickly to a variety of customer needs. Cloud computing’s emergence could be viewed as a major enabler for the replacement of traditional manufacturing methods from CMfg (Xu X., 2012). Companies are undoubtedly reshaping their business models to meet the growing demand for customized products as well as the demand for high-quality products, but customers are also expressing an increased desire to participate in the production of goods (Zhang et al., 2019). As a result, there is a growing need for new approaches to the pursuit of improved manufacturing techniques. It can be deduced from previous published works by Rauschecker et al. (2011); Wang and Xu (2013); and Lu and Xu (2019) that with the adoption of CMfg, customers effectively become part of the design and production phases, with their specialized requirements taken into account. However, CMfg adoption is not without its challenges.
Another important aspect of CMfg is the problem of local pickup and delivery (LPDP). A long list of contributions can be found in the published literature suggesting optimization algorithms to address the issue. Chen et al. (2013) contributes to the body of knowledge by proposing a Dispatching System based on data mining. The proposed system provides a simulation platform for strategic decision making and analysis, and the results obtained from historical data can be combined with an optimization algorithm to improve the LDPD’s outcome. Machine Learning (ML) is a subset of the Artificial Intelligence domain (AI), which has benefited from technological advancements over the last few decades. In fact, ML can be a strategic solution for integrating advanced manufacturing processes. Sharp et al. (2018) conducted a thorough investigation into the use of ML in the field of smart manufacturing in their comprehensive review. Last but not least, Kusiak, (2018) presents a comprehensive vision of smart manufacturing. In Cloud Manufacturing, task composition refers to the selection of appropriate services from the CM platform and their combination to complete the task. The primary goal is to achieve the expected results (Wu et al., 2013). With various performance measures, the composition problem is one of the most important functional issues in CM, and several researchers have discussed it. Tao et al. (2013) developed a parallel intelligent algorithm that took into account time, cost, energy, reliability, maintainability, trust, and function similarity. Price, time, availability, and reputation were used as performance measures by Zhou and Yao (2017), who then aggregated them using weights for each measure before combining the modified artificial bee colony and cuckoo search algorithms for the problem at hand. Furthermore, Ahn et al. (2019) consider a task guided acyclic graph and propose graph-based algorithms for calculating the cost, time, quality, and reliability of a task with multiple composition patterns. Furthermore, they use the Kano model to model the problem of task composition by introducing cost and execution time as performance attributes, as well as quality and reliability as basic attributes.
2.1.3 Decentralized scheduling
Production systems are expected to respond as quickly as possible to products’ short life cycles and changing market demand in the context of globalization. However, centralized production systems are unable to meet such demands, necessitating the development of a decentralized architecture (Toptal and Sabuncuoglu 2010). Decentralized scheduling was eventually developed, with the holonic manufacturing system, agent-based manufacturing system, fractal manufacturing system, and bionic manufacturing system serving as the foundation. Production systems have become more decentralized, reconfigurable, self-organizing, and adaptive thanks to new technologies (Wang et al., 2017). Decentralized scheduling, as opposed to centralized scheduling, is better suited to dynamic production systems with frequent disruptions and rescheduling. Each resource or task in the production system can be thought as an agent, an intelligent decision-making entity that acts like a human and communicates with each other to formulate a scheduling plan based on the internal state and the external environment. To avoid chaos, this process necessitates collaboration among the systems. As a result, an agent will frequently make a near-optimal decision for itself to achieve a larger goal. The interactive negotiation process is used to make decisions between agents to solve the decentralized scheduling problem. Although it cannot always guarantee an optimal scheduling scheme, it does improve scheduling flexibility significantly.
2.1.4 Distributed scheduling
Science and technology advances, particularly in information technology, provide the foundation for the management of distributed production systems. The manufacturing model has shifted from single factory to multi-factory coproduction (distributed manufacturing). Distributed manufacturing can take advantage of the resources of multiple factories, allocate resources more efficiently, and improve product quality while lowering production and transportation costs and reducing management risks. Distributed scheduling is more difficult than centralized scheduling because the decisions to be made in the process are interrelated (e.g., specifying the appropriate factory for each job and arranging the job processing sequence for each factory). Distributed scheduling is classified as an NP-hard problem in theory, but in practice, a good schedule scheme can significantly reduce the production cycle or costs. Next, exact algorithms, heuristic algorithms, and metaheuristic algorithms are the most common distributed scheduling methods (Chan and Chung, 2013).
2.2 Advances in scheduling methodologies
Chryssolouris (2013) defined Manufacturing Systems as “the combination of humans, machinery, and equipment that are bound by a common material and information flow.” Scheduling is critical for the design, control, and operation of manufacturing systems, as evidenced by the preceding. The main scheduling challenges that engineers face are listed as follow: 1) requirement generation, 2) processing complexity, 3) scheduling criteria, and 4) scheduling environment. As a result of recent technological advancements and changes in the global market schema, research efforts have focused on developing innovative solutions for improving existing scheduling techniques. To that end, scheduling is a complex problem that lends itself to extensive research. The provision of an energy-efficient production plan by incorporating machine reliability is a common practice in scheduling modeling.
Production scheduling allows a manufacturing system to allocate resources efficiently and at a low cost. However, for production scheduling, pure mathematical methods are commonly used, which are not understandable or practical for different domain engineers. Furthermore, heterogeneous information during production scheduling can lead to ambiguity in communication or a delay in information. Furthermore, the lack of a unified expression of production information limits the interaction and reuse of production data. To help with production scheduling, a model-based systems engineering (MBSE) approach based on the satisfiability modulo theory (SMT) has been proposed by Chen et al. (2022). The authors evaluated their approach in package production line case study. During the COVID-19 pandemic, the scheduling goal was to maintain high production efficiency, reduce working time and worker costs while increasing working distances. The outcome of the case study was that the multiple architectural view modeling language KARMA enables a unified description of modeling production scheduling and optimization of scheduling schemes (Figure 3).
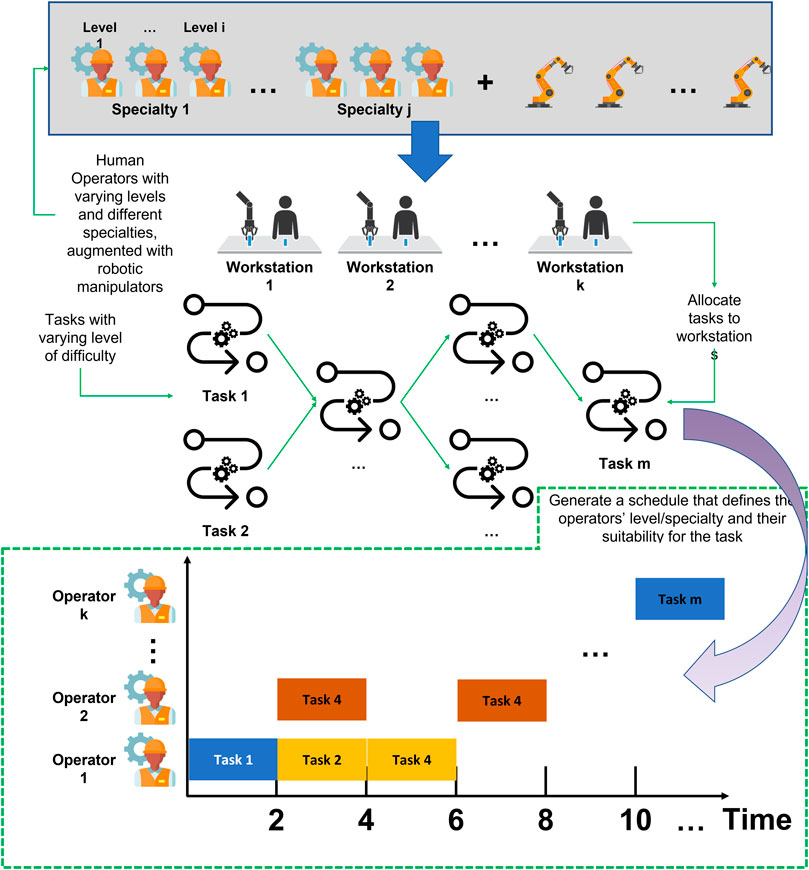
FIGURE 3. Problem statement of production scheduling (Chen et al., 2022).
As a result, Chen et al. (2019) developed a mathematical programming model based on the ant-colony optimization method with the goal of minimizing both tardiness and energy costs. Mourtzis (2020) also presents a comprehensive review of the state-of-the-art and new trends in simulation engineering for manufacturing systems, as well as major historical milestones in the development of simulation engineering for manufacturing systems and recent approaches to business and study in key industrial areas. Furthermore, Yongkui et al. (2019) discuss the current state of the art and research challenges in cloud manufacturing scheduling. This research summarizes the fundamentals of cloud manufacturing scheduling, as well as typical work on service composition and scheduling in cloud manufacturing, as well as related scheduling issues and research challenges, techniques, and methodologies. Additionally, Rossit et al., 2019 present a new decision-making schema called Smart Scheduling that uses an efficient screening procedure with the goal of yielding flexible and efficient production schedules that take advantage of the features of both centralized and decentralized manufacturing systems.
Maintenance activities are a constant feature of manufacturing systems. Maintenance, on the other hand, can create uncertainty because the occurrence of a malfunction cannot always be predicted or even avoided. Furthermore, maintenance activities could be classified as multi-mode due to the increased complexity of modern manufacturing equipment. Moradi and Shadrokh (2019) present a heuristic algorithm that they designed and developed for selecting maintenance activities in the production schedule, taking into account the effect of entities on system reliability as well as their importance value. A product-service system (CARM2-PSS) is also proposed, which includes a Cloud-based platform for condition-based preventive maintenance, as well as a shop-floor monitoring service and an Augmented Reality (AR) application (Mourtzis et al., 2017a and 2017b). Next, machines play an important role in custom IoT manufacturing environments. Xu et al. (2019) conducted a study to fill the gaps in the literature for new algorithms that take advantage of such technologies. The authors proposed a system in which workers with stochastic workloads arrive at a computer at random and their workload (enabled by IoT) is revealed when they arrive.
Although this technology is not new to the market, a methodology for deriving scheduling decisions is introduced by Mourtzis et al. (2016) for the exploitation of machine information in near real-time machine condition monitoring. Similarly, in a batch order-based manufacturing environment, an attempt is made to translate five generic key performance indicators (KPIs) into a continuous real-time cost function. Microelectronics and hard metal composite manufacturers were given the task of controlling and optimizing resource utilization, production efficiency, product-process quality, environmental impact, and inventory. Thus, Psarommatis et al. (2022) aim to make decision-making easier by converting data from operations management into dynamic financial cost models. The process of converting engineering data from the physical level and operations management level into financial metrics establishes a common language among engineers, managers, and financial departments of a company, all of whom have their own priorities but share the same goal of increasing profitability. Additionally, defects are unavoidable during manufacturing processes, and scholars have invested a great deal of time and effort into improving defect prevention. Zero Defect Manufacturing (ZDM) (Psarommatis et al., 2020a) aims to eliminate manufacturing flaws. Furthermore, technological advancements have made it possible to repair defective products (Mourtzis et al., 2021a). This necessitates more frequent rescheduling of productions in order to account for the actions required to repair defective parts. To that end, Psarommatis et al. (2020a) research focuses on ZDM detection and repair strategies. The authors use a newly developed hybrid Decision Support System (DSS) that detects defects using data-driven and knowledge-based approaches before automating the necessary decision-making processes. To describe the production domain and enrich the available data with contextual information, the system uses an ontology based on the MASON ontology.
As far as the supply chain (SC) simulation is concerned, Makris et al. (2011) present an extended presentation of supply chain control logic in simulation. Furthermore, according to Mourtzis (2011), modern manufacturing companies must collaborate with their business partners throughout the development, production, distribution, and after-sales service processes. In addition, a model in the form of an Internet-enabled technology system has been introduced, which offers a variety of features such as digital organization, scheduling, and monitoring to promote collaboration and flexible planning and monitoring through extended manufacturing companies.
Regarding the Design and Planning of manufacturing networks, existing systems also fail to address the numerous issues of manufacturing network management in a systematic comprehensive way as they apply to data and context not directly related to manufacturing (e.g., long-term strategic planning vs. short-term operational scheduling) as presented by Si et al. (2011).
2.3 Adaptive or dynamic scheduling
In literature the term “Scheduling in manufacturing/production” is considered as the preparation of a good quality optimized baseline schedule, that is, constructible and easy to maintain (i.e., Predictive Scheduling). Even this is correct; however, in industrial world, real-time events severely disrupt schedule integrity. Schedules can quickly become neither optimized nor realistic if the responsible project management team does not act dynamically to mitigate the impact of these events. Accordingly, for the successful implementation of project planning, the presence and implementation of a predefined Adaptive or Dynamic Scheduling strategy to mitigate real-time event disruptions is a necessity. Adaptive or Dynamic Scheduling is the process of absorbing the effect of real-time events, analyzing the current status of schedule, and automatically modifying the schedule with optimized measures in order to mitigate disruptions and ensure resiliency (Mourtzis et al., 2021c).
Any of the above-mentioned real-time events could have a significant impact on the efficiency or even the correctness of a predefined schedule, necessitating a complete rescheduling of the project in some cases. Dynamic Scheduling (DS) specifies the strategy for generating the initial baseline as well as the strategy for responding to real-time events (Fahmy et al., 2014). The three main DS categories (or strategies) are presented in Figure 4.
There are some prerequisites to enable adaptive scheduling. They must have the ability to, first, choose alternative resources for various operations, and, second, allow variable throughput time components based on shop floor conditions. As a result, the adaptive scheduling requires the following inputs: 1) expected shop floor conditions at the time of planned production, 2) resource capabilities, and 3) throughput time components of the various operations. The operations of the production orders are assigned to the available resources in the first step of scheduling. Here, the capabilities of the resources are matched to the product requirements. When multiple resources are available to meet the demands, the selection is made based on predefined criteria (e.g., shortest operation time, cheapest processing). The utilized throughput time components are chosen based on the expected shop floor conditions at the time of production. In this way, when compared to planning with static master data, the scheduling results are much more in line with the actual situation on the shop floor (Reinhart and Geiger, 2011).
3 Applied innovations of scheduling in cloud manufacturing
Engineers have seized the opportunity to improve existing scheduling techniques and invent new ones as a result of the introduction of digitalization. However, research has progressed from theoretical discussions to the practical implementation of the proposed solutions, with early adopters providing feedback. Through several real-life use cases, the following paragraphs will attempt to reflect the impact of scheduling innovations in modern manufacturing systems. Many promising and innovative technologies, such as cloud manufacturing (CMfg) and digital twin (DT), have risen to prominence as a result of Industry 4.0, while existing technologies, such as scheduling, have thrived as well (Mourtzis et al., 2021b). Complex hybrid logical and terminal constraints, nonstationary process execution, and complex interrelationships between process design dynamics, power utilization, and system configurations all emerge as scheduling issues in Industry 4.0 and cloud manufacturing (Ivanov et al., 2018). Industry 4.0 key technologies, particularly CMFg, enable flexible production, particularly with CPS and highly customized assemblies, to deliver manufacturing services on demand (Dolgui et al., 2020). Data generation in ever-increasing volume, variety, and speed, also known as Big Data, is one of the most important outcomes of the emergence of IoT. The modern mass customization range is built on the analysis of this data, which means meeting the needs of individualized consumer markets. The analysis of this data is necessary for the improvement of knowledge repositories and decision-making (Renu et al., 2013). Shukla et al. (2019) also discuss next-generation smart manufacturing and service systems that use big data analytics.
Tao et al. (2018) also present a conceptual framework and typical application scenarios that address the role of big data in supporting smart manufacturing. Aside from the positive outcomes of IoT paradigms and Industry 4.0 examples, the complexity is a significant challenge. Many methods for quantifying complexity have been developed, based on heuristics, statistics, and probabilities (ElMaraghy et al., 2012 and Mourtzis et al., 2013a). Mourtzis et al. (2019) aim to fill in the gaps in the literature on complexity quantification methods. To that end, Figure 5 presents the Industry 4.0 model, which is based on Information Theory and quantitatively assesses the complexity and capacity of Industry 4.0 systems.
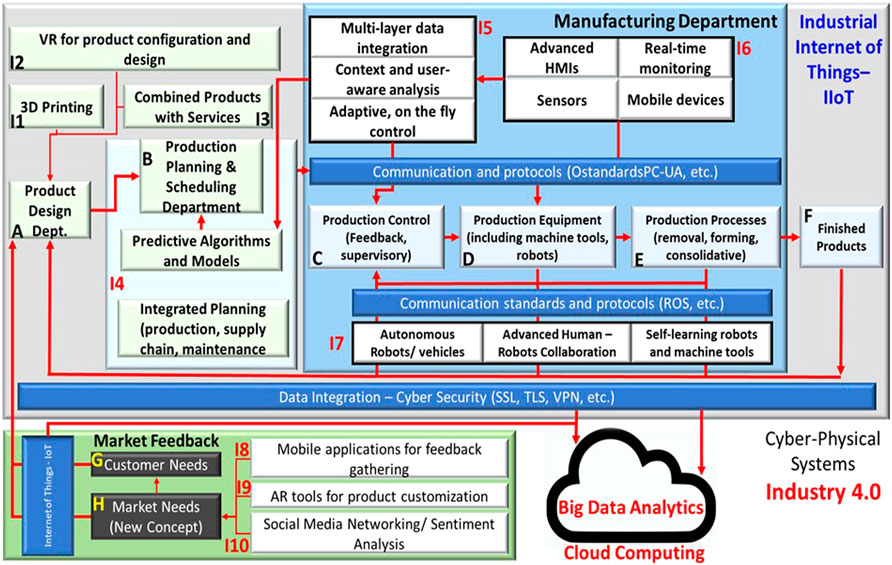
FIGURE 5. Cyber physical systems in Industry 4.0 model adapted from Mourtzis et al. (2019).
3.1 Decision making applications for smart scheduling
Decentralized decision-making and real-time reaction to unexpected developments, which occur frequently in both manufacturing and consumer environments, are two important factors that affect a production chain’s flexibility in meeting demand. Papakostas et al. (2012) present an agent-based approach to real-time and hierarchical manufacturing decision-making problems. The global market landscape has changed in recent decades, and hierarchical mass production appears to be unable to meet the changing demand demands imposed by globalization. Mourtzis et al. (2012b) examine the performance and viability of centralized and decentralized production networks under heavy production conditions in order to contribute to this shift. To assess the quality of automotive production networks under highly diversified consumer demand, discrete-event simulation models (DES) have been developed. Thus, multiple conflicting user-defined parameters were used in the evaluation, including lead time, final product price, versatility, annual production volume, and environmental impact due to product transportation. Mourtzis et al. (2013b) presented the mass customization paradigm in conjunction with efficient manufacturing configurations. Figure 6 shows the architecture tool for designing and planning centralized and decentralized production networks. The proposed approach is validated through a real life case acquired from the CNC machine building industry.
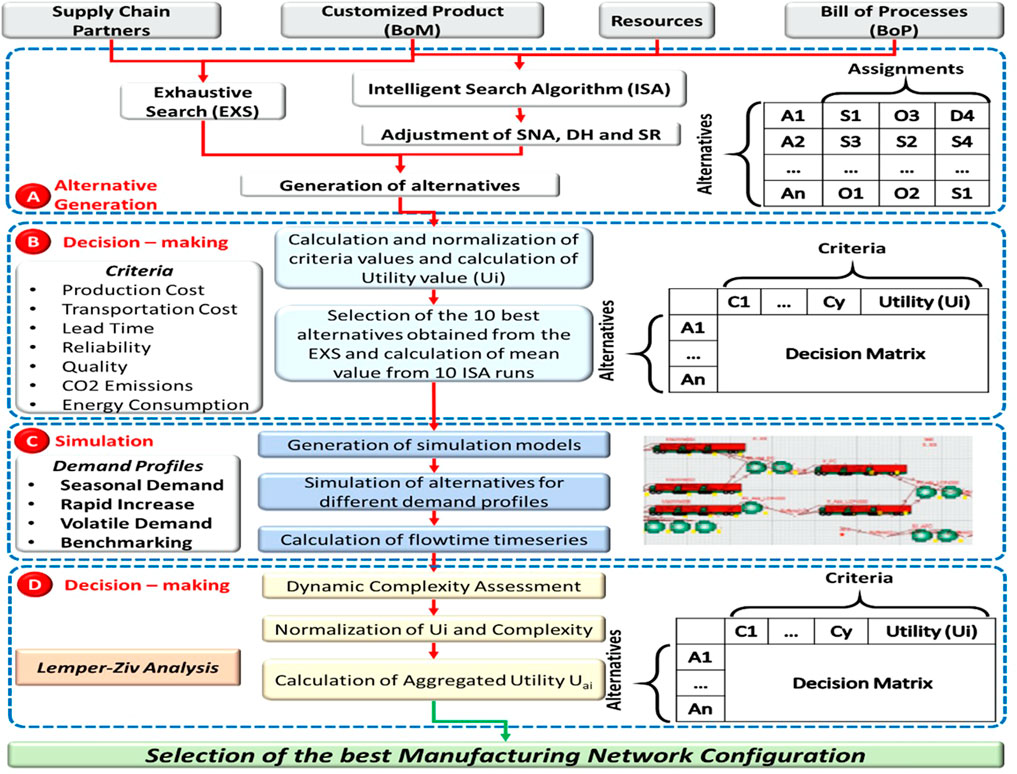
FIGURE 6. Workflow of the proposed design and operation method (Mourtzis et al., 2013a).
As regards the validation of the proposed framework, Decentralised Manufacturing Network (DMN) has a clear advantage over Centralised Manufacturing Network (CMN) based on utility values obtained from computer experiments for the Exhaustive Search (EXS) and Intelligent Search Algorithm (ISA). DMN has a clear advantage over CMN based on utility values obtained from computer experiments for the EXS and ISA (Mourtzis et al., 2013b; Figure 7). Table 2 shows the calculated criteria values for the DMN and CMN. Table 1 shows the calculated criteria values for the DMN and CMN.
The ISA results for the DMN case are 2.4 percent worse than the EXS results, but they take 15,295 times less time to compute. When compared to the EXS results, the ISA results are of high quality, ranking in the top 1% of the highest utility value solutions. As a result, ISA has a clear advantage over the EXS. In most cases, DMN values are superior to CMN because DMN allows for the formation of alternatives where suppliers can perform assembly tasks, reducing total transportation distance and thus lowering costs, CO2 emissions, and energy requirements (Mourtzis et al., 2013a).
Two approaches are used in the decision-making process: an exhaustive search and a smart search algorithm. Multiple conflicting user-defined parameters, such as lead time, cost of production, versatility, annual volume of production, and environmental impact, are used to evaluate alternative production and transportation schemes. The smart search method’s performance is investigated using statistical design of experiments (SDoE). Also included is an intelligent algorithm calibration technique. Mourtzis et al. (2015a) examine the performance of decentralized manufacturing networks using the Tabu Search and Simulated metaheuristic methods in conjunction with the Artificial Intelligence method in order to contribute to the globalization paradigm. The decision support system (DSS) enables the development and evaluation of alternative production network configurations based on a set of conflicting user-defined cost, time, performance, and environmental impact criteria. The proposed solution is explored through a probabilistic framework to guide the decision-maker in selecting the values of the variable control parameters to achieve high-quality network designs for manufacturing.
The overall performance of manufacturing systems is influenced by product complexity, particularly in highly personalized markets. Production scheduling is an important part of the decision-making process when dealing with the challenge of high flexibility. As a result, Mourtzis et al. (2015b) proposed a knowledge-rich short-term job-shop scheduling mechanism that could be integrated into a mobile app. The proposed approach is validated through a real-life case acquired from European Metal-cutting and mold-making SMEs (Figure 8). The operating principle focuses on short-term scheduling of machine shop resources using an intelligent algorithm that generates and compares alternate resource allocations to tasks. The adaptive calculation procedure results in the need for a new order in order to evaluate alternative schedules and make a quick decision. It also allows for the presentation of the derivative schedule on mobile devices. Mourtzis and colleagues present the method’s overall workflow (Mourtzis et al., 2016b). Furthermore, a collection of mobile apps designed to aid consumer integration during the service design phase and subsequent network design is presented.
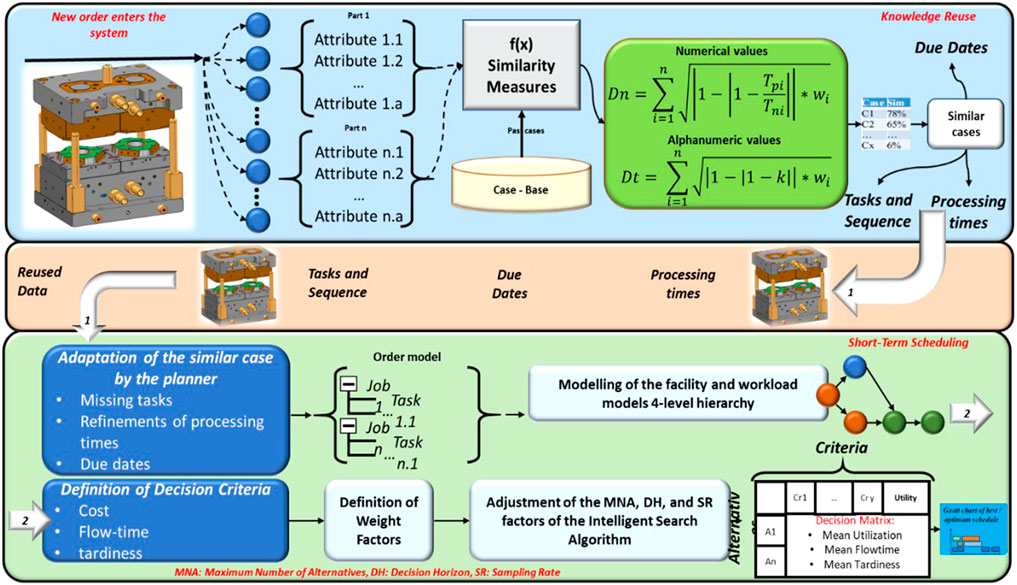
FIGURE 8. Workflow of the knowledge-enriched short-term scheduling (KES) method. The method consists of two mechanisms, namely: (1) The knowledge extraction and reuse mechanism and (2) the short-term scheduling mechanism (Mourtzis et al., 2016a).
Real data from a high precision mold making machine shop is used in the case study. The mold-shop is best suited to the engineer-to-order (ETO) business model, which involves designing and manufacturing custom molds and dies based on specific customer requirements. This mold-injection molds are one-of-a-kind, first-time-right products that vary greatly in terms of quality requirements, tolerances, and, most importantly, functionality. Mold-making is clearly a highly specialized and knowledge-based industry. The shop floor consists of eight job shops, each with 14 work-centers and a total of 40 individual resources (Figure 8). On the one hand, there are high-precision CNC machines capable of milling, drilling, turning, electro-discharge wire cutting, sinking, grinding, tapping, roughing, polishing, and hardening operations and on the other human operators that perform manually operations of design, fitting, assembly, measuring, and polishing. The processing times, tasks, sequences, and resources used for the manufacturing of thirty (30) molds are included in the historical dataset. The information was gathered over the course of about 3 years. According to the analysis of historical data, five orders (moulds) are executed simultaneously in the shopfloor on average. As a result, four orders are currently being processed, and a new order enters the system eight calendar days later. The schedules for these orders have already been created and are in the process of being carried out. In order to accommodate the new order, the system must be rescheduled. The identification number for the new mold order is “13.23.” Table 3 lists the basic characteristics of “13.23,” as well as the various components and tasks required for this mold.
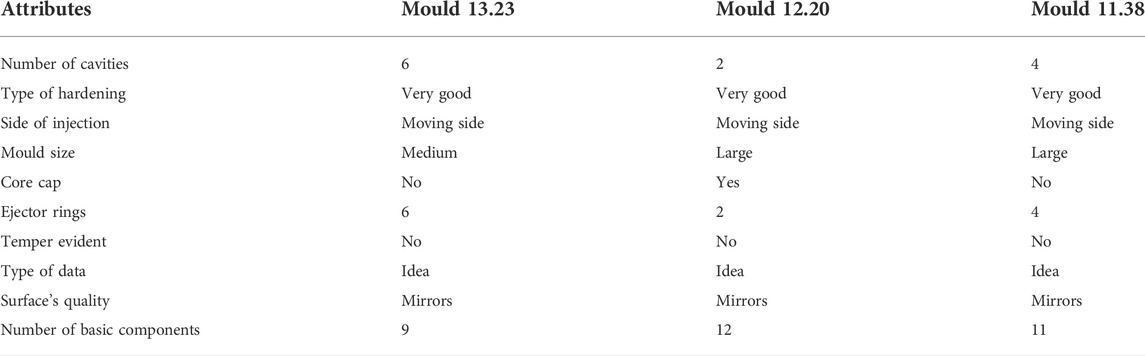
TABLE 3. Attributes of the compared mould cases (Mourtzis et al., 2016a).
The past case is the complete dataset of a previously completed mold-making order, which includes the mold specifications/attributes, scheduling parameters used, the schedule followed (policy, sequencing, etc.), and documented processing times and task sequencing. The new order is compared to all 30 documented past cases in the case study. For pairwise comparison of cases, Case Base Reasoning (CBR) considers 10 attributes: Number of cavities, type of hardening, injection side, mould size, core cap, ejector rings, tamper evident, type of data, surface quality, and number of basic components, with the following weight factors: 0.15, 0.05, 0.1, 0.1, 0.1, 0.1, 0.1, 0.1, 0.1, 0.1, 0.1, 0.1, 0.1, 0.1, 0.1, 0.1. The number of basic components that must be manufactured has a direct impact on the required number of manufacturing processes, so the attribute “number of basic components” has a high weight value, because the more required processes, the longer the production flowtime. The shape of the stacks is another important factor, that is, taken into account. Thus, there are two options, moulds with cylindrical or rectangular stacks. The attribute “length” is ignored during similarity because the mould “13.23” has cylindrical stacks. The results of a similarity calculation show that the moulds “13.23” and “12.20” have an 83 percent similarity index. The planner then adapts the latter’s process plan to prepare the dataset for the former’s scheduling. The next most similar mold “11.38,” which is 75% similar to “13.23.” The similarity mechanism is then used in a second step to estimate the due date of the new mould case. The pairwise comparison of previous and new cases yields a ranked list of the most similar cases based on the defined attribute weights. The estimated lead time for the new case is then calculated by multiplying the manufacturing lead time of the previous case by the similarity index. Thus, based on the database of the company, Table 4 shows the actual processing times for each mold. Furthermore, the average set-up time required to perform a task is 30 min, according to data retrieved from the mold-making industry and analyzed. In order to reduce the complexity of the model, the setup time is factored into the processing times (Mourtzis et al., 2016a).
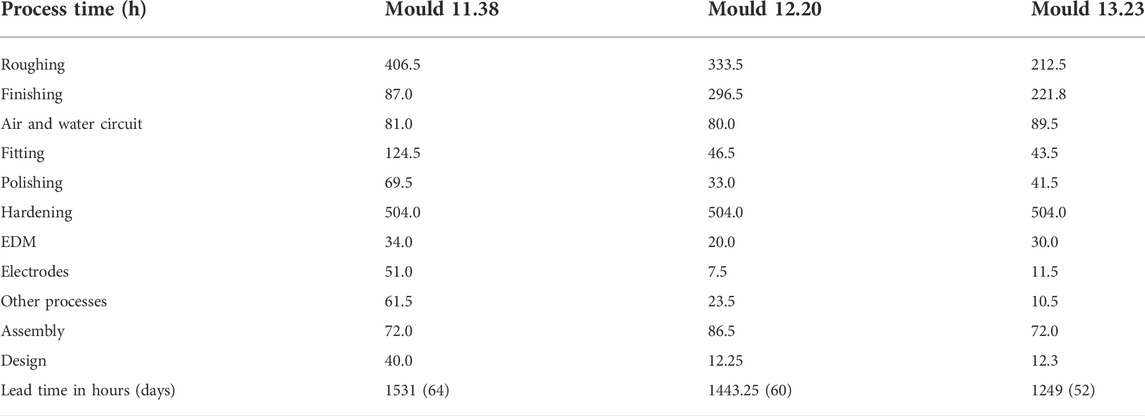
TABLE 4. Lead time estimation produced by the case based reasoning (CBR) mechanism (Mourtzis et al., 2016a).
Then, the similarity index is calculated and two stored cases “12.20” and “11.38” are the most similar to the new case “13.23.” Following that, the case is adapted in order to determine the manufacturing lead time. The similarity measure between “12.20” and “13.23” is multiplied by the lead time of the case “13.23” mold, and the result is divided by 10. Lead time13.23 = 1209.6708 h is the resulting value for the lead time estimation. When this lead time is converted to calendar days, keeping in mind the working shifts of each resource per day, the order’s due date is calculated to be 51 days. It should be noted that this estimate differed by only 3.15 percent from actual historical values, demonstrating the accuracy of the lead time estimation method. It is also worth noting that using a larger pool of previous cases improves the method’s accuracy. The scheduling algorithm generates and evaluates scheduling alternatives and their respective performance indicators once the new case has been fully adapted (Mourtzis et al., 2016a).
3.2 Cloud-based scheduling approaches
Another method for dealing with manufacturing shop-floor disruptions and the growing number of product variants is to use adaptive and flexible process planning methods. Mourtzis et al. (2016b) describe a two-service cloud-based software platform, that is, system-oriented. The first system uses a genetic algorithm to generate non-linear process plans. The second service uses sensors, operator inputs, and device schedules to collect data from machine tools. An information fusion technology processes monitoring data in order to feed the process planning system with the status, requirements, and availability time periods of machine tools (Figure 9). The proposed work is validated in a white-goods industry.
In order to demonstrate the functionalities for monitoring distributed manufacturing resources and performing remote device control, as well as performing distributed and adaptive process planning, the developed platform is implemented and validated in a pilot case involving three different machine tools on three different shop floors. After the data acquisition is set up, the sensor board collects data from the sensors and sends it to the cloud via the microcontroller (Mourtzis et al., 2016d; Figure 10). The data is then processed using an information fusion technique that combines the Analytical Hierarchy Process (AHP) and Dempster–Shafer (DS) theories of evidence. The DS theory of evidence is directly applied on the spindle and axes statuses at the low stage of fusion. The masses for both “Available” and “Busy” statuses for the two sources are 0.5 and 0.9, respectively, at this stage. The AHP is used because the higher stage of fusion includes three heterogeneous sources that provide information (i.e., sensory system, operator, and machine schedule). The weights of each source are 0.4917, 0.3770, and 0.1313, respectively, for sensory system, operator, and schedule. Precision, synchronization, flexibility, error probability, and prediction capability are some of the criteria used in the AHP. During the operation of the system, the monitoring service provides all of the required information to the adaptive planning system regarding the availability of the machine tools and their capabilities.
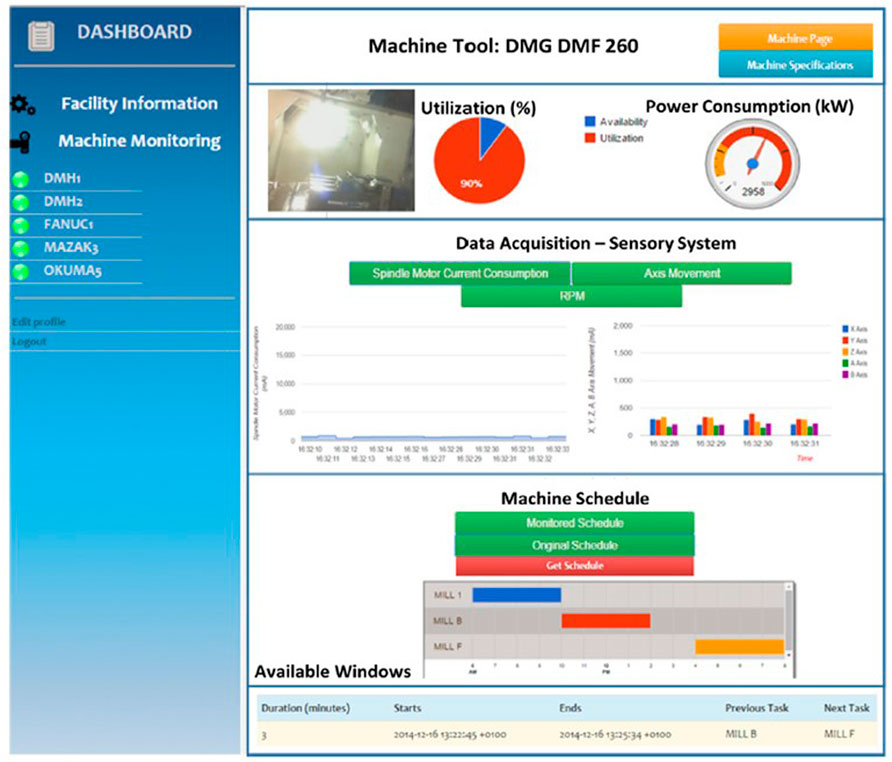
FIGURE 10. Visualization of the monitoring service graphical user interface for the DMG DMF 260 milling machine.
In order to meet the demands of mass personalization market demand, companies need to change their supply chains (Mourtzis, 2022). A new supply chain is required to respond to the dramatic changes imposed by changing market conditions. But in a world where natural disasters and pandemic crises are becoming more common, such new supply chains must also take environmental factors into account. Some researchers have recently demonstrated how Industry 4.0 technologies can aid this transformation (Ivanov et al., 2018). Under the Industry 4.0 concept, manufacturers face the challenge of producing highly customized goods in small batches. One way to respond to ever-changing demands and improve resource flexibility is to digitize production processes. The integration of Internet of Things (IoT) technologies in Automated Customized Shopping to create a sustainable environment of connected distribution and selling points is the solution to these challenges. Yang et al. (2019) present a review of IoT technologies and systems, which are the drivers and pillars of smart manufacturing data-driven developments.
The Fourth Industrial Revolution has elevated the importance of efficient and adaptable manufacturing as a research priority. Complex production lines are required to meet the demand for personalized products. Due to increased complexity, manufacturing process planning, and scheduling seeks to identify near-optimal solutions to ensure quick and precise decision making. Therefore, Mourtzis et al. (2020a) aim to contribute to the field of adaptive scheduling by proposing an algorithm that allows machines, workers, and the production manager to collaborate in near real-time. An SME that manufactures solar panels will present a framework for self-adaptive scheduling in a real-world manufacturing case (Figure 11). The proposed framework for self-adaptive scheduling in a real-world manufacturing case is derived from an SME that produces solar panels.
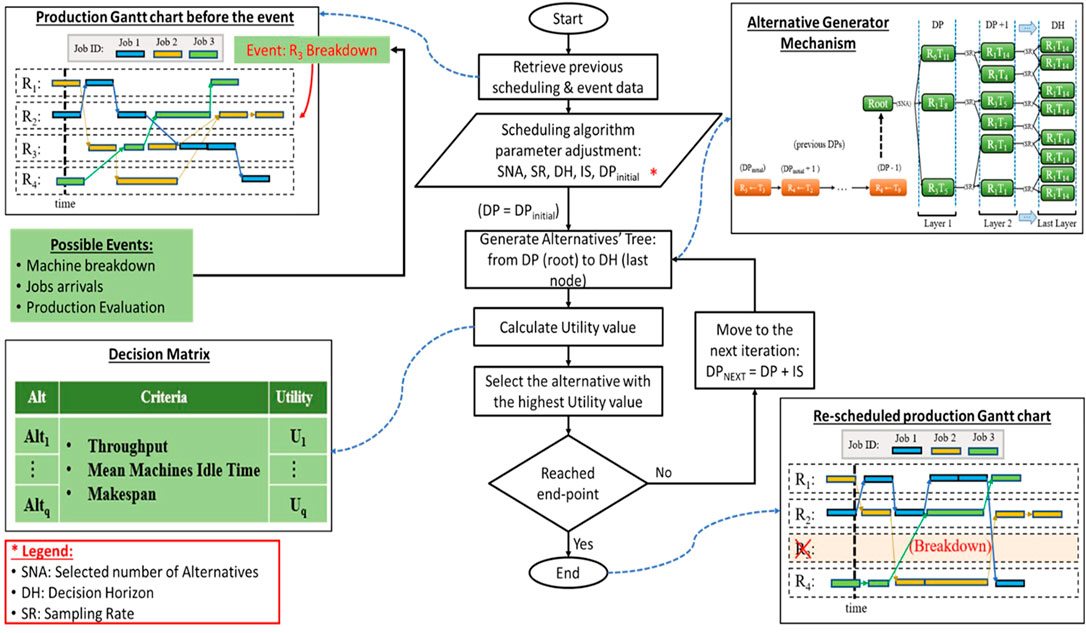
FIGURE 11. Architecture of the proposed decision-making adaptive scheduling framework (adapted from Mourtzis et al., 2020a).
Data from a SME production line for solar panel heaters was used to validate the proposed algorithm. Its goal is to mass-produce a single heater model, which will change when a newer model is designed and put into production. This Cellular System is made up of multiple cells. The jacket, caps, flanges, and sleeves of the final product are all made by different cells. Semi-final assembly, final assembly, and quality control stations are also available. Expected and unexpected events can occur during the operation of a manufacturing cell, necessitating immediate rescheduling. One scenario involved an upcoming scheduled maintenance operation, which necessitated the creation of a new adapted schedule in order to reduce production latency. For the proposed solution, the parameters of the algorithm were adjusted as follows: Selected Number of Alternative (SNA) at 20% of the maximum SNA provided; Sampling Rate (SR) at 30% of the selected SNA and Decision Horizon (DH) at 2. Furthermore, the different weight coefficients for calculating utility values were set to 0.25, 0.5, and 0.75, respectively. The results were compared to the results obtained from the SME’s production system current scheduling method. The comparison, as shown in Figure 12, revealed that the proposed methodology provided 15% higher utility, resulting in 15% better resource scheduling based on the previously discussed criteria after the event had occurred and in significantly less computational time.
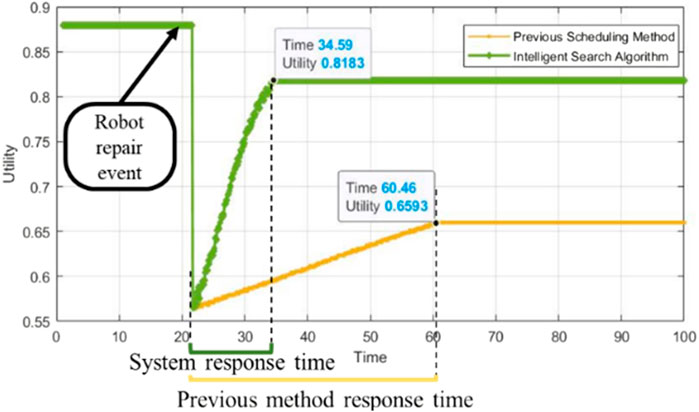
FIGURE 12. Comparison graph between previous production scheduling method and the intelligent search algorithm (ISA) (Mourtzis et al., 2020a).
According to the proposed findings, increasing DH may have a negative impact on the utility as well as the convergence of the solution. Furthermore, a sufficient parameterization of the SNA and SR is at approximately 30% and 40%, respectively.
Finally, due to the massive growth in available data, shop floor decision making has become more complex than ever before. Critical judgment and decision-making have become critical requirements of modern manufacturing problems as market demands for product quality and delivery times have increased. Human decision-making has become insufficient, and manufacturers are struggling to meet their objectives. The IoT and CPS, which are cornerstones of Industry 4.0 smart factories, can help with efficient decision making. Thus, one of the most important issues that engineers must address is production scheduling. The decision support tools of the Industry 4.0 era help to schedule production effectively while taking into account more data and constraints than ever before. To that end, Mourtzis et al. (2020b) study proposes a production scheduling method that checks resource and task status using historical and near-real-time data, providing insight to production engineers and enabling better decision making. A case study in the structural steelwork industry validates the findings.
3.3 Scheduling in cloud manufacturing
Based on the above-mentioned, order/task submission, preliminary order/task processing, scheduling, result delivery, and service assessment are the five phases of the entire scheduling process in cloud manufacturing.
Submission of orders/tasks: The entire scheduling process begins with the submission of orders/tasks from customers. Tasks can be classified into design tasks, manufacturing tasks, test tasks, and so on, depending on their functional requirements, or they can be combined (Liu et al., 2017).
Preliminary order/task processing: After orders/tasks are submitted to a cloud platform, they must first be processed, which includes classification, description, analysis, decomposition, and other functions. Following the preliminary processing, the requirements for each task, including functional and non-functional requirements, are clarified. The former refers to the function that must be carried out in order to complete the task (for example, a part or a product with a specific function). The realization of the function necessitates the invocation and execution of specific types of services. The latter usually refers to a set of criteria (e.g., time, cost, and quality) as well as the constraints that come with them (Liu et al., 2017).
Scheduling: The scheduling management module, with the help of the scheduling supporting module, service management module, and monitoring management module, schedules tasks after preliminary order processing. The core scheduling module is in charge of creating optimal schedules and overseeing task execution. The scheduling supporting module is in charge of maintaining scheduling metrics, rules, methods, and algorithms, as well as assisting the scheduling management module (e.g., assisting the scheduling management module in determining scheduling methods). The service management module job is to manage service-related activities like service classification, search and matching, composition, and assessment that are required for scheduling. The monitoring managing module is critical for monitoring the status of resources and orders on factory floors (Li et al., 2015) and provides real-time status information (e.g., machine availability), that is, required for achieving optimal scheduling (Mourtzis et al., 2016a).
Result delivery: After a task is completed, associated resources are released, and the ultimate execution results (e.g., parts, components, or end-products) are delivered to consumers via logistics or the Internet (Liu et al., 2017).
Service assessment: Consumers can evaluate the services they have used after they receive the execution results (Feng and Huang 2018). The evaluation results reflect their overall level of satisfaction with the results, and they can also serve as a useful reference for future customers when choosing services (Cui et al., 2016).
There have been several papers published recently that focus on the scheduling process (Table 5).
4 Challenges and trends
4.1 Opportunities and challenges of I4.0 to production scheduling
Customer demands, which are characterized by personalization, call for a more rapid and accurate market response from manufacturing enterprises today, against the backdrop of globalization and fierce market competition. Enterprises are expected to establish a more efficient supply chain and improve their operational efficiency through horizontal integration or inter-organizational collaboration (such as cloud network synergy, human-equipment synergy, and equipment synergy) to meet this requirement (Mourtzis et al., 2022a). As a result of the socialization of global production and life, the impact of global climate, and the recognition of the concept of environmental protection and sustainable development, environmental protection (emission reduction, resource conservation, recycling and reuse) has become another focus for manufacturing enterprises (Sachs et al., 2021). As a result, in light of the current manufacturing industry development and reform, scheduling will face the following challenges as a key tool for optimizing production operations:
Sustainable Manufacturing Scheduling (Jena et al., 2020).
Mass customized manufacturing scheduling (Wan et al., 2021).
Inter-and intra-organizational collaboration scheduling (Frazzon et al., 2020).
While Cyber Physical System (CPS) and adaptive manufacturing may be the most influential I4.0 factors for operational scheduling (Monostori et al., 2016), scheduling is also influenced by other layers of organizational decision-making. As a result, in order to fully assess the potential impact of I4.0 on scheduling, the concepts, methods, and technologies of I4.0 that affect other layers of organizational decision-making, such as Internet of Things (IoT), horizontal and vertical integration, big data, and cloud computing, have to be considered (Meissner and Aurich 2019). Table 6 lists the general opportunities in the scheduling field, as well as the most significant challenges associated with each of these opportunities. The table also includes a list of critical research and operational fields that are relevant to each challenge. It has to be also noted that big data and cloud technologies (i.e., cloud computing, cloud manufacturing) appear to be mostly regarded as potential solutions to some of the identified challenges in the scheduling field, rather than posing new challenges (Zhong et al., 2017).
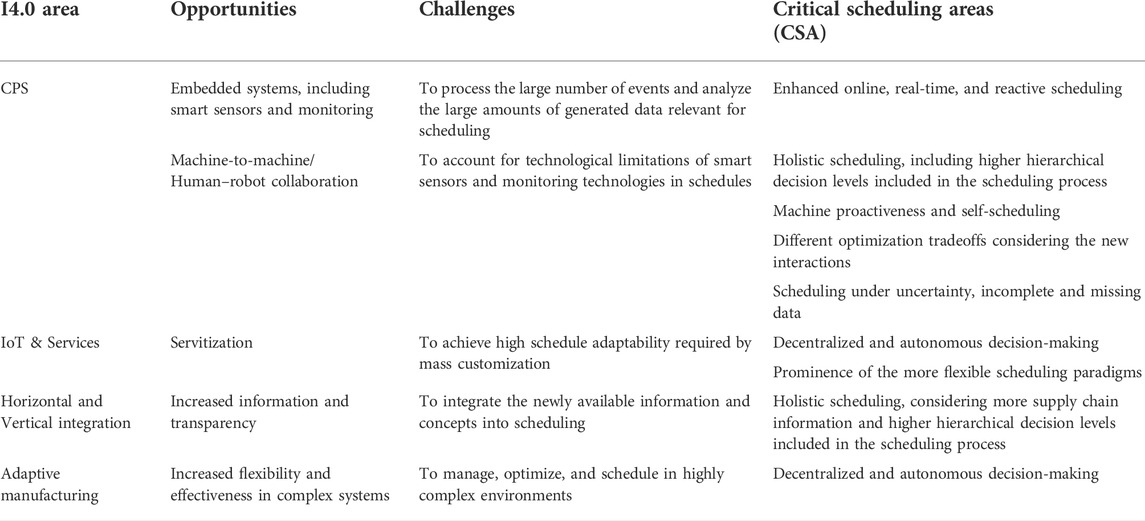
TABLE 6. Opportunities and challenges in scheduling stemming from the implementation of I4.0 (Parente et al., 2020).
4.2 Development trends
According to literature, researchers have begun to use advanced information and communication technology (such as IoT, cloud computing, CPS, big data, edge computing, and AI) to address the challenges that the manufacturing system has faced in Industry 4.0. Therefore, the implementation of these technologies will have significant impact on the production system, potentially leading to changes in production scheduling modes.
Adaptive and self-organized scheduling (Dolgui et al., 2019; Mourtzis, 2020a)
Big data driven scheduling (Kong et al., 2020)
Collaborative scheduling
o Supply-chain collaborative scheduling (Dolgui et al., 2020)
o Cloud-edge collaborative scheduling (Ma et el., 2020)
o Human-machine collaborative scheduling (Zhou et al., 2019)
Digital Twins-based scheduling (Zhang et al., 2019; Wang and Wu, 2020)
4.3 Disadvantages of production scheduling in manufacturing
Within manufacturing operations, production scheduling is one of the most critical operations. There is a lack of planning and execution in the overall production process without adequate production scheduling. Production scheduling is used by many operations and production facilities in order to determine when products will be manufactured. However, there are a few drawbacks with regards to the utilization of production scheduling in manufacturing that must be considered before the tool/software is implemented. The main drawbacks of the identified production scheduling techniques that require improvement are as follows (King et al., 2021):
Complexity: A common disadvantage for smaller manufacturing industries. Because of the numerous variables associated with production scheduling and production scheduling software, a significant amount of time is required to fully understand the operation. When it comes to production scheduling, it is critical to keep track of the production crews, which can result in a lot of work for the person in charge of production scheduling. Additionally, the usage of the scheduling software, there are many details that have to be addressed.
Cost: The cost of implementation is another potential issue with production scheduling. The manufacturing industries may need to purchase software and other resources to aid in the implementation of a production scheduling system. Next, they will also need to pay for training so that the software can be used. This may necessitate devoting an employee to the training, which is costly. Thus, managers and engineers should consider whether the additional cost is justified before implementing production scheduling.
Lack of flexibility: Several factors in the manufacturing process can significantly alter the outcome. The businesses may not be able to adapt quickly enough to avoid problems if they are on a production schedule. It can be difficult to stop the process and start working elsewhere once materials have arrived and the staff is ready to work.
Skewness: The difficulty in scheduling processes is the final potential issue with production scheduling. For instance, if an unexpected machine breakdown occurs for a specific timeslot, the entire production schedule is disrupted.
While there are some drawbacks to production scheduling, it is a requirement for all manufacturing operations. To stay ahead of the competition, industrial and manufacturing companies should have an adequate and advantageous production system.
4.4 Industry 4.0 adoption level
Industry 4.0 is currently recognized as a key factor in the competitiveness of businesses currently and in the future. The readiness and implementation of various technologies, however, varies from enterprise to enterprise. An Industry 4.0 index has been developed based on the performed factor analysis and allows businesses to assess their current Industry 4.0 maturity (Honti et al., 2020). Enterprises can quickly determine their own level of Industry 4.0 technology readiness thanks to the VPi4 index (Pech and Vrchota, 2022) and its methodology. The index is a tool that managers can use to set strategic goals and create plans that address the issues raised by the Fourth Industrial Revolution. It can also be a factor in choosing priorities for the future development of an enterprise when deciding on investment plans. The managers can also contribute to the choice of projects that should be carried out in order to maximize synergies.
Summarizing, adoption of Industry 4.0 technologies and use cases varies significantly by continent and by industry sectors. According to IoT Analytics and Industry 4.0 and Smart Manufacturing Adoption Report the following can be summarized regarding the international level of Industry 4.0 adoption (Wopata, 2020):
Less than 30% of manufacturers report widespread adoption of Industry 4.0
Regional variations: North American manufacturers have adopted Industry 4.0 technologies the most (36%), while the adoption percentage of European Manufacturers is 27% and Asian with a focus on Chinese manufacturers is 20%.
Leading manufacturers in Industry 4.0 adoption are: Siemens, General Electric (GE), and Boeing.
a) Siemens
i) Visionary Industry 4.0 Strategy
ii) New digital business models
iii) Extensive Industry 4.0 implementations in own smart factories
b) GE
i) Digital Twin Approach
ii) Great Digital Products
iii) High usage of Industry 4.0 implementations in own smart factories
c) Boeing
i) Implementation of Digital Twins in a large scale
ii) Pillar technologies of Industry 4.0 such as Augmented Reality, Simulation and 3D Printing
For many years, the automotive industry has been driven by competition to innovate. Due to that, automotive Original Equipment Manufacturers (OEMs) have embraced new technologies like robotics and management techniques to increase operational efficiency and gain a competitive edge
5 Discussion and outlook
5.1 Adaptive shop-floor scheduling framework
Short-term scheduling is one of the most common manufacturing decision-making issues. In modern shop floors, increasing product variety creates even more uncertainty and turbulence, making scheduling a difficult problem. The integration of scheduling and monitoring systems will allow for adaptive decision-making, which will improve shop-floor awareness and information flow. A typical case study in Industry 4.0 manufacturing facilities is the Data Monitoring Systems in Shopfloors. The monitoring system’s data is used to identify potential machine-tool breakdowns and create feasible and adaptable schedules. The data from the monitoring system can be used in two ways. In the first case, the scheduling tool and algorithm can request monitoring data from the monitoring system. The second method is that the monitoring system informs the scheduling tool and algorithm about shopfloor turbulences. The monitoring system checks the progress of running tasks and retrieves information about their status. Each scheduled task can have one of the following status: Completed, in progress, or pending. In order to produce feasible and accurate schedules, the aforementioned data are used as input to the scheduling algorithm. According to Mourtzis and Vlachou (2018), Adaptive scheduling is defined as the ability to re-generate alternative and feasible schedules based on the current shop-floor situation. Re-scheduling is done whenever a change is required, as determined by the monitoring system’s feedback. Furthermore, re-scheduling can be done in two ways based on the information gathered by the monitoring system:
When the status of a machine tool is detected to be down, as well as when it returns from down or set up mode
When the monitored processing time exceeds the scheduled time, the makespan is greatly influenced
More specifically, and as shown in Figure 13, the status of the machine tools is investigated first. The running tasks are monitored if the status of the machine tools is not detected as down or if the machine tools do not return from down or setup mode. The status of each task, as well as the task duration, is monitored. The time required to complete a task based on the generated schedule is referred to as task duration. If a monitored task duration is longer than the scheduled task duration provided by the scheduling tool, the system looks into two possibilities:
The machine tool next task is checked by the system. The overall schedule is shifted forward if the end time of the monitored task is greater than the start time of the next task in the machine tool
The post-condition of each task is also checked by the system. If the end time of a task is greater than the start time of the post condition, the overall schedule is shifted forward
underWhen rescheduling is required in any of the situations, the monitoring system calculates the pending tasks as well as the availability of each machine tool. As a result, when rescheduling is necessary, the monitoring system provides the scheduling algorithm with the machine tools, as well as their availability and pending and ongoing tasks. To generate feasible scheduling alternatives, the scheduling algorithm is used, which consists of a multi-criteria decision-making algorithm. As presented in the workflow of Figure 13, the determination of the alternatives is the first step in the procedure. The next step is to identify the attributes, which are the criteria used to rank the options. Following the definition of the criteria, the consequences must be defined. The values of the attributes at the time the decisions are made in order to evaluate the alternatives are the consequences. The proposed algorithm takes into account the following main criteria: flowtime (6), tardiness (7), cost (8), and quality (9). Finally, in comparison to other approaches, the proposed scheduling algorithm is chosen because it has the ability to adapt to new orders and perform quick rescheduling with high-quality solutions (Mourtzis et al., 2013a) as presented in Table 7.

TABLE 7. Time required for scheduling within a week based on the adaptive scheduling and the traditional approach.
5.2 Industry 4.0 and beyond
There have been several responses and discussions in the research community since the European Commission published its Policy Brief on “Industry 5.0—Towards a Sustainable, Human-Centric, and Resilient European Industry” (Breque et al., 2021). The report acknowledges the ability of industry to achieve societal goals beyond employment and growth to become a resilient provider of prosperity. This is done by requiring production to respect the limits of our planet and putting industrial worker wellbeing at the center of the production process.
While Industry 5.0 is more value-driven toward practical applications of readily accessible enabling technologies in industry, Industry 4.0 is more technology focused (Xu et al., 2021). Three interconnected pillars are considered the core values of Industry 5.0: 1) human centricity, 2) sustainability, and 3) resilience. It has to be emphasized that:
“Industry 5.0 complements the existing Industry 4.0 paradigm by having research and innovation drive the transition to a Sustainable, Human-centric & Resilient European industry”
Additionally, to strike a balance between economic growth and the eradication of social issues in society, the Japan Cabinet (CAO, 2016) has proposed the term Society 5.0 (Deguchi et al., 2020). In Society 5.0, people, things, and systems are all connected in cyberspace and optimal results obtained by AI exceeding the capabilities of humans are fed back to physical space. This process brings new value to industry and society in ways not previously possible as presented in Figure 14.
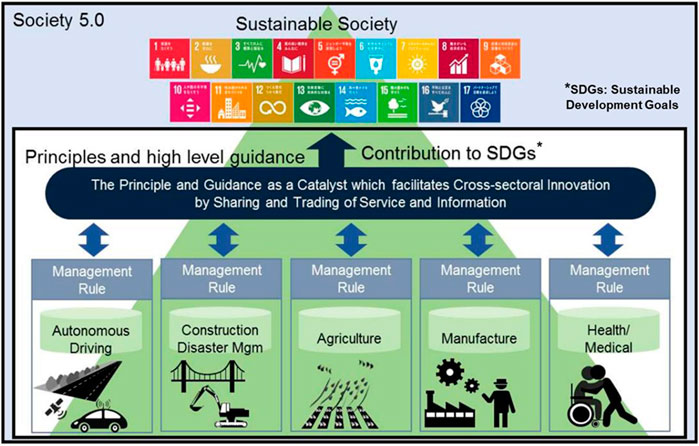
FIGURE 14. Society 5.0 as an ecosystem (Okamoto, 2019).
Thus, both Industry 5.0 and Society 5.0, recognize the power of industry to achieve societal goals beyond jobs and growth, to become a “resilient provider” of prosperity by making production respect the boundaries of our planet and placing the wellbeing of the industry worker at the center of the production process (Mourtzis et al., 2022b).
5.3 Adaptive bio-inspired transformation of manufacturing
Optimization as a general topic, has an increased added value, as it enables engineers to improve manufacturing and production systems. Up until the last decade, optimization has been limited to two approaches, in particular 1) deterministic, and 2) meta-heuristic. Although the above-mentioned techniques have provided adequate results, there is still fertile ground for further improvement. In Figure 15, Manufacturing is opposed to Biology, in an attempt to identify the possible aspects that could be affected by bio-inspired engineering. Essentially, the content of Figure 15 could facilitate engineers towards the design and development of frameworks for the integration of bio-inspired approaches/algorithms in modern manufacturing (Byrne et al., 2018.)
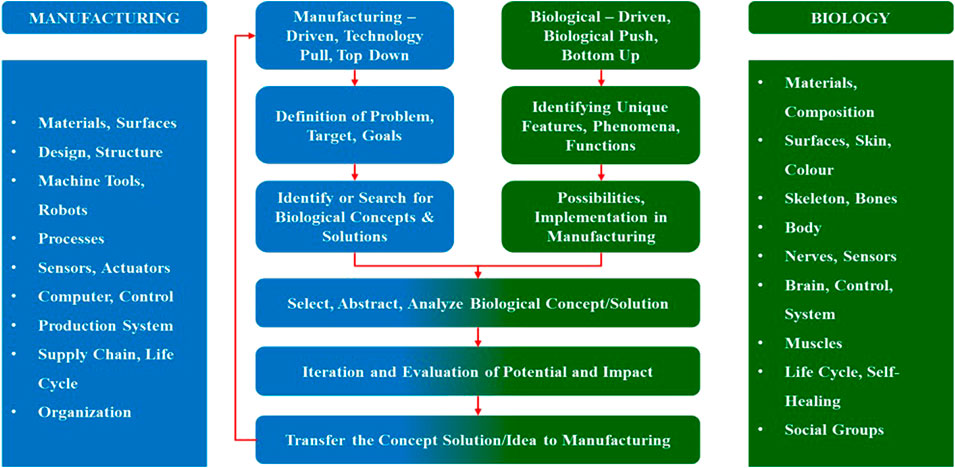
FIGURE 15. The bi-directional systematic approach for the identification of potential impact of biological transformation of manufacturing.
Undeniably, during the last decades manufacturing as well as Information and Communication Technologies (ICT) have undergone tremendous changes, especially when taking into consideration the advances in the computational power and the hardware/network capabilities. As it is commonly concluded, AI is not a revolutionary technological field, however, given the above-mentioned technological advances, it resurfaced during the last 5 years and under the framework of Industry 4.0. AI approaches, and especially optimization is based on the setup of a proper mathematical model, that efficiently describes the physical model. Consequently, in order to optimize certain parameters the implementation of suitable fitness functions is necessary, in order to explicitly define the optimization goals, criteria, as well as the limitations. On the contrary, physical systems, and nature’s optimization models, operate under an entirely different model, which could be described by the term “Open Adaptation.” Essentially, Open Adaptation does not require the strict setup of the above-mentioned parameters, thus entailing an advanced level of intelligence versus the evolutionary intelligence of modern computational systems. By extension engineers will have to further work on the comprehensive understanding of the natural optimization systems, in order to successfully reverse engineer its properties, the models’ structures, and the operating principles, before proceeding with application in modern production and manufacturing systems.
Considering the statements made in the previous paragraph of this Section, one can conclude, that natural systems are very complex systems, having undergone centuries of development, adaptation, and optimization. Delving deeper into the structure of the natural systems, a possible approach for the successful decoding of these systems, would the creation of parallels. More specifically, engineers could focus on depicting natural systems as engineering systems or interpreting natural processes in engineering/system processes. For example, immune systems logic, could facilitate in the design and development of crisis management strategies. Concretely, robustness and resilience of systems, which has been largely researched through the last 2 years, could imitate the principles of immune systems in order to detect volatile behaviors, detect and recover from external disturbances and therefore to reschedule the operation of the production network, in order to minimize undesired effects. Similarly, nature uses collective systems, which can be realized as smaller communities (e.g., insects). Such social insect societies and their operating principles are useful for the development of scheduling approaches, e.g., job-shop scheduling, and their contribution could extend to planning and layout of entire manufacturing networks.
Ultimately, nature could be considered as a black box, which engineers have not yet fully decoded. However, as it is apparent, there are several underlying opportunities if lessons are to be learnt from nature and its models/mechanisms. However, some key points for consideration and future research need to be discussed. Firstly, so far, engineering was based on heavily structured systems, systems that in various cases are not adaptable/flexible to changes, centralized, and all aspects are over-defined, thus minimizing the degrees of freedom. On the contrary, natural systems operate in an abstract way. Therefore, Ueda has proposed a new concept for manufacturing systems, the Biological Manufacturing Systems (BMS) (Ueda, 1992; Ueda et al., 2000). Among the key features/benefits of the BMS is the ability for real-time scheduling, reducing the need for global control of the production network, the ability of disengage production for the need for line setup by integrating modular and mobile elements.
According to Ueda, BMS do not require global control, thus control is passed to the lower levels of the production. Consequently, the implementation of suitable frameworks that provide with decision-making tools/functionalities to the lower production levels is required, while the upper production levels receive adequate insights regarding the facility and network operations. Thus holonic approaches have emerged, realizing individual entities of the production as holons/agents, distributed within the production network, capable of co-operating with other holons, but autonomous as well (Mourtzis et al., 2021c).
Currently, due to the vast amount of data produced at a daily basis from manufacturing facilities, and the increased complexity of the digital/virtual models employed for describing physical production networks, increased computational resources are required. Therefore, given the continuously connected device networks complex calculations can be performed more easily. Ephemeral computing can be realized as a paradigm that enables the execution of complex computational tasks by exploiting heterogeneous computational resources associated with a limited time (Mostaghim, 2010).
6 Conclusion
In this research work the latest advances and the trends in adaptive scheduling in the Cloud Manufacturing scheme have been investigated. It can be stressed out that the Industry 4.0 as well as the upcoming Industry 5.0 are the key enablers, and the industrial domain has to take advantage of the constantly evolving technologies and techniques in order to 1) remain competitive in the challenging global landscape, 2) become even more resilient, 3) integrate humans at a greater scale (human centricity). The current status of Industry 4.0 implementation (at a global scale) indicates that although there is adequate technological background/support, industries have to pick up the pace in order to reach a common level of technological integration. By extension, this will enable modern manufacturing and production systems and networks to start working on the human-centric aspect of the systems, and consequently to embrace such technologies. In order to do so, research focus has been set on the topics of Smart Manufacturing, Cloud Manufacturing, and Scheduling. The latter, as examined in the previous paragraphs is a multi-faceted problem that requires special attention from the research community. Industrial scheduling, and by extension Planning and Control, despite being very old engineering challenges, can be facilitated by the new technologies introduced under the Industry 4.0 framework, and more specifically, by Big Data Sets, as well as the constantly increasing computational power. On the hand, Quantum Computing, which is still in its infancy will further facilitate the processing of even bigger data sets, in shorter times, thus engineers will be able to model physical systems in a more natural (close to natural) way.
By and large, Industry is constantly getting modernized with the integration of cutting-edge technologies. During the last decade, digital technologies have been advanced considerable, thus unveiling new opportunities for the optimization of the modelling, design and operation of manufacturing systems and networks. In the current era of digitalization, researchers are putting effort on developing solutions based on Artificial Intelligence algorithms. Indeed, AI can be considered as a mainstream topic that will elevate the Smart Manufacturing paradigm.
Author contributions
DM conceived the idea, is responsible for the conceptualization of the project and the writing of the paper, conducted the research for similar works.
Conflict of interest
The author declares that the research was conducted in the absence of any commercial or financial relationships that could be construed as a potential conflict of interest.
Publisher’s note
All claims expressed in this article are solely those of the authors and do not necessarily represent those of their affiliated organizations, or those of the publisher, the editors and the reviewers. Any product that may be evaluated in this article, or claim that may be made by its manufacturer, is not guaranteed or endorsed by the publisher.
References
Akbar, M., and Irohara, T. (2018). Scheduling for sustainable manufacturing: A review. J. Clean. Prod. 205, 866–883. doi:10.1016/j.jclepro.2018.09.100
Ahn, G., Park, Y.-J., and Hur, S. (2019). Performance computation methods for composition of tasks With multiple patterns in cloud manufacturing. Internat. J. Production Res. 57 2, 517–530. doi:10.1080/00207543.2018.1451664
Ameri, F., Sormaz, D., Psarommatis, F., and Kiritsis, D. (2022). Industrial ontologies for interoperability in agile and resilient manufacturing. Int. J. Prod. Res. 60 (2), 420–441. doi:10.1080/00207543.2021.1987553
Amjad, M. K., Butt, S. I., Kousar, R., Ahmad, R., Agna, M. H., Faping, Z., et al. (2018). Recent research trends in genetic algorithm based flexible job shop scheduling problems. Mathematical Problems in Engineering, Editor T. Hanne 2018, 9270802. doi:10.1155/2018/9270802
Angelopoulos, J., and Mourtzis, D. (2022). An intelligent product service system for adaptive maintenance of engineered-to-order manufacturing equipment assisted by augmented reality. Appl. Sci. 12 (11), 5349. doi:10.3390/app12115349
Behnamian, J. (2016). Survey on fuzzy shop scheduling. Fuzzy Optim. Decis. Mak. 15 (3), 331–366. doi:10.1007/s10700-015-9225-5
Boyer, S. (2004). SCADA: Supervisory control and data acquisition. 3rd ed. Research Triangle Park, North Carolina: ISA-The Instrumentation, Systems and Automation Society.
Breque, M., De Nul, L., and Petridis, A. (2021). Industry 5.0: Towards a sustainable, human-centric and resilient European industry. Luxembourg, LU: European Commission, Directorate-General for Research and Innovation.
Byrne, G., Dimitrov, D., Monostori, L., Teti, R., van Houten, F., Wertheim, R., et al. (2018). Biologicalisation: Biological transformation in manufacturing. CIRP J. Manuf. Sci. Technol. 21, 1–32. doi:10.1016/j.cirpj.2018.03.003
Calis, B., and Bulkan, S. (2015). A research survey: Review of AI solution strategies of job shop scheduling problem. J. Intell. Manuf. 26 (5), 961–973. doi:10.1007/s10845-013-0837-8
Campbell, H. S., Dudek, R. A., and Smith, M. L. (1970). A heuristic algorithm for the n job, m machine sequencing problem. Management Sci. 16 (10), B630–B637. Available at: http://www.jstor.org/stable/2628231
Cao, Y., Wang, S., Kang, L., and Gao, Y. (2016). A TQCS-based service selection and scheduling strategy in cloud manufacturing. Int. J. Adv. Manuf. Technol. 82 (1), 235–251. doi:10.1007/s00170-015-7350-5
Chan, H. K., and Chung, S. H. (2013). Optimisation approaches for distributed scheduling problems. Int. J. Prod. Res. 51 (9), 2571–2577. doi:10.1080/00207543.2012.755345
Chen, J., Wang, G., Lu, J., Zheng, X., and Kiritsis, D. (2022). Model-based system engineering supporting production scheduling based on satisfiability modulo theory. J. Industrial Inf. Integration 27, 100329. doi:10.1016/j.jii.2022.100329
Chen, L., Wang, J., and Xu, X. (2019). An energy-efficient single machine scheduling problem with machine reliability constraints. Comput. Industrial Eng. 137, 106072. doi:10.1016/j.cie.2019.106072
Chen, W., Song, J., Shi, L., Pi, L., and Sun, P. (2013). Data mining-based dispatching system for solving the local pickup and delivery problem. Ann. Oper. Res. 203, 351–370. doi:10.1007/s10479-012-1118-1
Cheng, Z., Zhan, D., Zhao, X., and Wan, H. (2014). Multitask oriented virtual resource integration and optimal scheduling in cloud manufacturing. J. Appl. Math. 2014, 1–9. Article ID 369350. doi:10.1155/2014/369350
Chryssolouris, G. (2013). Manufacturing systems: Theory and practice Berlin/Heidelberg, Germany: Springer Science & Business Media
Cui, J., Ren, L., and Zhang, L. (2016). “Cloud manufacturing service selection model based on adaptive variable evaluation metrics,” in Theory, methodology, tools and applications for modeling and simulation of complex systems (Singapore: Springer), 13–19. doi:10.1007/978-981-10-2669-0_2
Dannenbring, D. G. (1977). An evaluation of flow shop sequencing heuristics. Manag. Sci. 23 (11), 1174–1182. doi:10.1287/mnsc.23.11.1174
Deguchi, A., Hirai, C., Matsuoka, H., Nakano, T., Oshima, K., Tai, M., et al. (2020). What is society 5.0. Society 5, 1–23. doi:10.1007/978-981-15-2989-4_1
Dolgui, A., Ivanov, D., Potryasaev, S., Sokolov, B., Ivanova, M., Werner, F., et al. (2020). Blockchain-oriented dynamic modelling of smart contract design and execution in the supply chain. Int. J. Prod. Res. 58 (7), 2184–2199. doi:10.1080/00207543.2019.1627439
Dolgui, A., Ivanov, D., Sethi, S. P., and Sokolov, B. (2019). Scheduling in production, supply chain and industry 4.0 systems by optimal control: Fundamentals, state-of-the-art and applications. Int. J. Prod. Res. 57 (2), 411–432. doi:10.1080/00207543.2018.1442948
Doukas, M., Psarommatis, F., and Mourtzis, D. (2014). Planning of manufacturing networks using an intelligent probabilistic approach for mass customised products. Int. J. Adv. Manuf. Technol. 74 (1747)–1758. doi:10.1007/s00170-014-6121-z
ElMaraghy, H., Monostori, L., Schuh, G., and ElMaraghy, W. (2021). Evolution and future of manufacturing systems. CIRP Ann. 70 (2), 635–658. doi:10.1016/j.cirp.2021.05.008
ElMaraghy, W., ElMaraghy, H., Tomiyama, T., and Monostori, L. (2012). Complexity in engineering design and manufacturing. CIRP Ann. 61 (2), 793–814. doi:10.1016/j.cirp.2012.05.001
Esmaeilian, B., Behdad, S., and Wang, B. (2016). The evolution and future of manufacturing: A review. J. Manuf. Syst. 39, 79–100. doi:10.1016/j.jmsy.2016.03.001
Feng, Y., and Huang, B. (2018). A hierarchical and configurable reputation evaluation model for cloud manufacturing services based on collaborative filtering. Int. J. Adv. Manuf. Technol. 94 (9), 3327–3343. doi:10.1007/s00170-017-0662-x
Fera, M., Fruggiero, F., Lambiase, A., Martino, G., and Nenni, M. E. (2013). “Production scheduling approaches for operations management,” in Operations management (United States: InTech). doi:10.5772/55431
Frazzon, E. M., Agostino, Í. R. S., Broda, E., and Freitag, M. (2020). Manufacturing networks in the era of digital production and operations: A socio-cyber-physical perspective. Annu. Rev. control 49, 288–294. doi:10.1016/j.arcontrol.2020.04.008
Garey, M. R., Johnson, D. S., and Sethi, R. (1976). The complexity of flowshop and jobshop scheduling. Math. OR. 1 (2), 117–129. doi:10.1287/moor.1.2.117
Graham, R. L., Lawler, E. L., Lenstra, J. K., and Rinnooy Kan, A. H. G. (1979). Optimization and approximation in deterministic sequencing and scheduling: a survey. Annals of Discrete Mathematics, Editor P. L. Hammer, E. .L. Johnson, and B. H. Korte Elsevier 5, 287–326. doi:10.1016/S0167-5060(08)70356-X
Honti, G., Czvetkó, T., and Abonyi, J. (2020). Data describing the regional Industry 4.0 readiness index. Data Brief 33, 106464. doi:10.1016/j.dib.2020.106464
Ivanov, D., Dolgui, Al., Suresh, S., and Sokolov, B. (2018). Scheduling in production, supply chain and industry 4.0 systems by optimal control: Fundamentals, state-of-the-art and applications. Int. J. Prod. Res. 57 (2), 411–432. doi:10.1080/00207543.2018.1442948
Jackson, R. (1957). Simulation research on job shop production. Naval Res. Logist. Quart. 4 (4), 287–295. doi:10.1002/nav.3800040404
Jain, A. S., and Meeran, S. (1999). Deterministic job-shop scheduling: Past, present and future. Eur. J. operational Res. 113 (2), 390–434. doi:10.1016/S0377-2217(98)00113-1
Jena, M. C., Mishra, S. K., and Moharana, H. S. (2020). Application of Industry 4.0 to enhance sustainable manufacturing. Environ. Prog. Sustain. Energy 39 (1), 13360. doi:10.1002/ep.13360
Jian, C. F., and Wang, Y. (2014). Batch task scheduling-oriented optimization modelling and simulation in cloud manufacturing. Int. J. Simul. model. 13 (1), 93–101. doi:10.2507/IJSIMM13(1)CO2
Jiang, Z., Yuan, S., Ma, J., and Wang, Q. (2021). The evolution of production scheduling from Industry 3.0 through Industry 4.0. Int. J. Prod. Res. 60, 3534–3554. doi:10.1080/00207543.2021.1925772
Johnson, S. M. (1954). Optimal two and three stage production schedules with setup times included. Nav. Res. Logist. 1 (1), 61–68. doi:10.1002/nav.3800010110
King, L. P., Jacob, M., and Velykoivanenko, O. (2021). Production scheduling – the good, the bad, and the ugly. White Paper, Phenix. Available at: https://phenixps.com/wp-content/uploads/2021/10/Production-Scheduling-the-good-the-bad-and-the-ugly-White-Paper.pdf (Accessed on 25/05/2022)
Komaki, G. M., Sheikh, Shaya, and Malakooti., Behnam (2019). Flow shop scheduling problems with assembly operations: A review and new trends. Int. J. Prod. Res. 57 (10), 2926–2955. doi:10.1080/00207543.2018.1550269
Kong, W., Qiao, F., and Wu, Q. (2020). Real-manufacturing-oriented big data analysis and data value evaluation with domain knowledge. Comput. Stat. 35 (2), 515–538. doi:10.1007/s00180-019-00919-6
Kusiak, A. (2018). Smart manufacturing. Int. J. Prod. Res. 56 (1-2), 508–517. doi:10.1080/00207543.2017.1351644
Laili, Y., Zhang, L., and Tao, F. (2011). Energy adaptive immune genetic algorithm for collaborative design task scheduling in cloud manufacturing system. IEEE International Conference on Industrial Engineering and Engineering Management, 06-09 Dec. 2011, Singapore, 1912–1916. IEEE, doi:10.1109/IEEM.2011.6118248
Lartigau, J., Xu, X., and Zhan, D. (2014). Artificial bee colony optimized scheduling framework based on resource service availability in cloud manufacturing. International Conference on Service Sciences, 22-23 May 2014, Wuxi, China. IEEE, 181–186. doi:10.1109/ICSS.2014.16
Li, B. H., Zhang, L., Wang, S. L., Tao, F., Cao, J. W., Jiang, X. D., et al. (2010). Cloud manufacturing: A new service- oriented networked manufacturing model. Comput. Integr. Manuf. Syst. 16 (1), 1–7.
Li, F., Zhang, L., Liu, Y., Laili, Y., and Tao, F. (2017). A clustering network-based approach to service composition in cloud manufacturing. Int. J. Comput. Integr. Manuf. 30 (12), 1331–1342. doi:10.1080/0951192X.2017.1314015
Li, J. S., Wang, A. M., Tang, C. T., and Lu, Z. B. (2012). Distributed coordination scheduling technology based on dynamic manu- facturing ability service. [In Chinese. Comput. Integr. Manuf. Syst. 18 (7), 1563–1574. doi:10.14743/apem2019.3.331
Li, X., Song, J., and Huang, B. (2016). A scientific workflow management system architecture and its scheduling based on cloud service platform for manufacturing big data analytics. Int. J. Adv. Manuf. Technol. 84 (1–4), 119–131. doi:10.1007/s00170-015-7804-9
Li, Z., Zhang, W., Wang, Z., and Wang, Z. (2015). Service monitoring of production and processing in cloud manufacturing. Comput. Integr. Manuf. Syst. 21 (7), 1953–1962. doi:10.13196/j.cims.2015.07.030
Lin, Y. K., and Chong, C. S. (2017). Fast GA-based project scheduling for computing resources allocation in a cloud manufacturing system. J. Intell. Manuf. 28 (5), 1189–1201. doi:10.1007/s10845-015-1074-0
Liu, Y., and Xu, X. (2017). Industry 4.0 and cloud manufacturing: A comparative analysis. J. Manuf. Sci. Eng. 139 (3). doi:10.1115/1.4034667
Lu, J., Hu, Q., Dong, Q., and Tang, H. (2017). Cloud manufacturing-oriented mixed-model hybrid shop-scheduling problem. China Mech. Eng. 28 (2), 191–198. doi:10.3969/j.issn.1004-132X.2017.02.011
Lu, Y., and Xu, X. (2019). Cloud-based manufacturing equipment and big data analytics to enable on-demand manufacturing services. Robot. Comput. Integr. Manuf. 57, 92–102. doi:10.1016/j.rcim.2018.11.006
Ma, J., Luo, G., Lu, D., and Guo, Y., 2014. Research on manufacturing resource cloud integration meta modeling and cloud-agent service scheduling. China Mech. Eng., 25(7), p.917. doi:10.3969/j.issn.1004-132X.2014.07.013
Ma, J., Zhou, H., Liu, C., Mingcheng, E., Jiang, Z., Wang, Q., et al. (2020). Study on edge-cloud collaborative production scheduling based on enterprises with multi-factory. IEEE Access 8, 30069–30080. doi:10.1109/ACCESS.2020.2972914
Makkonen, P. (1999). On multi body systems simulation in product design Trita-MMK. Available at: http://urn.kb.se/resolve?urn=urn:nbn:se:kth:diva-2800
Makris, S., Zoupas, P., and Chryssolouris, G. (2011). Supply chain control logic for enabling adaptability under uncertainty. Int. J. Prod. Res. 60 (1), 121–137. doi:10.1080/00207543.2010.508940
Meissner, H., and Aurich, J. C. (2019). Implications of cyber-physical production systems on integrated process planning and scheduling. Procedia Manuf. 28, 167–173. doi:10.1016/j.promfg.2018.12.027
Monostori, L., Kádár, B., Bauernhansl, T., Kondoh, S., Kumara, S., Reinhart, G., et al. (2016). Cyber-physical systems in manufacturing. Cirp Ann. 65 (2), 621–641. doi:10.1016/j.cirp.2016.06.005
Moradi, H., and Shadrokh, S. (2019). A robust reliability-based scheduling for the maintenance activities during planned shutdown under uncertainty of activity duration. Comput. Chem. Eng. 130, 106562. doi:10.1016/j.compchemeng.2019.106562
Mostaghim, S. (2010). “Parallel multi-objective optimization using self-organized heterogeneous resources,” in Parallel and distributed computational intelligence (Berlin, Heidelberg: Springer), 165–179. doi:10.1007/978-3-642-10675-0_8
Mourtzis, D., and Vlachou, E. (2016). Cloud-based cyber-physical systems and quality of services. TQM J. 28 (5), 704–733. doi:10.1108/TQM-10-2015-0133
Mourtzis, D. (2020a). “Adaptive scheduling in the era of cloud manufacturing,” in Scheduling in industry 4.0 and cloud manufacturing (Cham: Springer), 61–85. doi:10.1007/978-3-030-43177-8_4
Mourtzis, D., Angelopoulos, J., and Panopoulos, N. (2021a). Equipment design optimization based on digital twin under the framework of zero-defect manufacturing. Procedia Comput. Sci. 180, 525–533. doi:10.1016/j.procs.2021.01.271
Mourtzis, D., Angelopoulos, J., and Panopoulos, N. (2022b). Manufacturing personnel task allocation taking into consideration skills and remote guidance based on augmented reality and intelligent decision making. Int. J. Comput. Integr. Manuf., 1–16. doi:10.1080/0951192X.2022.2078513
Mourtzis, D., Angelopoulos, J., and Panopoulos, N. (2022). Operator 5.0: A survey on enabling technologies and a framework for digital manufacturing based on extended reality. J. Mach. Eng., 22, 43–69. doi:10.36897/jme/147160
Mourtzis, D., Angelopoulos, J., and Panopoulos, N., 2021c. Robust engineering for the design of resilient manufacturing systems. Appl. Sci., 11(7), p.3067. doi:10.3390/app11073067
Mourtzis, D., Angelopoulos, J., and Zogopoulos, V. (2021b). Integrated and adaptive AR maintenance and shop-floor rescheduling. Comput. Industry 125, 103383. doi:10.1016/j.compind.2020.103383
Mourtzis, D. (2016). Challenges and future perspectives for the life cycle of manufacturing networks in the mass customisation era. Logist. Res. 9 (2). doi:10.1007/s12159-015-0129-0
Mourtzis, D., Doukas, M., and Psarommatis, F. (2012a). A multi-criteria evaluation of centralized and decentralized production networks in a highly customer-driven environment. CIRP Ann. 61 (1), 427–430. doi:10.1016/j.cirp.2012.03.035
Mourtzis, D., Doukas, M., and Psarommatis, F. (2015b). A toolbox for the design, planning and operation of manufacturing networks in a mass customisation environment. J. Manuf. Syst. 36, 274–286. doi:10.1016/j.jmsy.2014.06.004
Mourtzis, D., Doukas, M., and Psarommatis, F. (2013a). Design and operation of manufacturing networks for mass customisation. CIRP Ann. 62 (1), 467–470. doi:10.1016/j.cirp.2013.03.126
Mourtzis, D., Doukas, M., and Psarommatis, F. (2012b). Design and planning of decentralised production networks under high product variety demand. Procedia CIRP 3, 293–298. doi:10.1016/j.procir.2012.07.051
Mourtzis, D., Doukas, M., and Psarommatis, F. (2015a). Design of manufacturing networks for mass customisation using an intelligent search method. Int. J. Comput. Integr. Manuf. 28 (7), 679–700. doi:10.1080/0951192X.2014.900867
Mourtzis, D., Doukas, M., Psarommatis, F., and Panopoulos, N. (2013b). “Design of multi-stage manufacturing networks for personalized products using metaheuristics,” in Advances in sustainable and competitive manufacturing systems, lecture notes in mechanical engineering. Editor A. Azevedo (Springer), Berlin/Heidelberg, Germany, 1263–1276. doi:10.1007/978-3-319-00557-7_103
Mourtzis, D., Doukas, M., and Vlachou, E. (2016a). A mobile application for knowledge-enriched short-term scheduling of complex products. Logist. Res. 9 (3). doi:10.1007/s12159-015-0130-7
Mourtzis, D., Gargallis, A., Angelopoulos, J., and Panopoulos, N. (2020b). “An adaptive scheduling method based on cloud technology: A structural steelwork industry case study,” in Proceedings of 5th International Conference on the Industry 4.0 Model for Advanced Manufacturing (Cham: Springer), 1–14. doi:10.1007/978-3-030-46212-3_1
Mourtzis, D. (2011). Internet-based collaboration in the manufacturing supply chain. CIRP J. Manuf. Sci. Technol. 4 (3), 296–304. doi:10.1016/j.cirpj.2011.06.005
Mourtzis, D., Panopoulos, N., and Angelopoulos, J. (2022). “Production management guided by industrial internet of things and adaptive scheduling in smart factories,” in Design and operation of production networks for mass personalization in the era of cloud technology (Elsevier), Amsterdam, Netherlands, 117–152. doi:10.1016/B978-0-12-823657-4.00014-2
Mourtzis, D., Siatras, V., Synodinos, G., Angelopoulos, J., and Panopoulos, N. (2020a). A framework for adaptive scheduling in cellular manufacturing systems. Procedia CIRP 93, 989–994. doi:10.1016/j.procir.2020.04.040
Mourtzis, D. (2020b). Simulation in the design and operation of manufacturing systems: State of the art and new trends. Int. J. Prod. Res. 58 (7), 1927–1949. doi:10.1080/00207543.2019.1636321
Mourtzis, D. (2022). “The mass personalization of global networks,” in Design and operation of production networks for mass personalization in the era of cloud technology (Elsevier), Amsterdam, Netherlands, 79–116. doi:10.1016/B978-0-12-823657-4.00006-3
Mourtzis, D., Vlachou, A., and Zogopoulos, V. (2017a). Cloud-based augmented reality remote maintenance through shop-floor monitoring: A product-service system Approach. J. Manuf. Sci. Eng. 139. doi:10.1115/1.4035721
Mourtzis, D., and Vlachou, E. (2018). A cloud-based cyber-physical system for adaptive shop-floor scheduling and condition-based maintenance. J. Manuf. Syst. 47, 179–198. doi:10.1016/j.jmsy.2018.05.008
Mourtzis, D., Vlachou, E., Doukas, M., Kanakis, N., Xanthopoulos, N., and Koutoupes, A. (2015c). “Cloud-based adaptive shop-floor scheduling considering machine tool availability,” in ASME International Mechanical Engineering Congress and Exposition, November 13–19, 2015 57588, (American Society of Mechanical Engineers (ASME)), Houston, Texas, V015T19A017. doi:10.1115/IMECE2015-53025
Mourtzis, D., Vlachou, E., Giannoulis, C., Siganakis, E., and Zogopoulos, V. (2016b). Applications for frugal product customization and design of manufacturing networks. Procedia CIRP 52, 228–233. doi:10.1016/j.procir.2016.07.055
Mourtzis, D., Vlachou, E., Milas, N., and Xanthopoulos, N. (2016d). A cloud-based approach for maintenance of machine tools and equipment based on shop-floor monitoring. Procedia Cirp 41, 655–660. doi:10.1016/j.procir.2015.12.069
Mourtzis, D., Vlachou, E., Zogopoulos, V., and Fotini, X. (2017b). “Integrated production and maintenance scheduling through machine monitoring and augmented reality: An industry 4.0 approach,” in Advances in production management systems. The path to intelligent, collaborative and sustainable manufacturing. APMS 2017. IFIP advances in information and communication technology. Editors H. Lödding, R. Riedel, K. D. Thoben, G. von Cieminski, and D. Kiritsis (Cham: Springer), 513. doi:10.1007/978-3-319-66923-6.42
Mourtzis, M., Fotia, S., Boli, N., and Vlachou, E. (2019). Modelling and quantification of industry 4.0 manufacturing complexity based on information theory: A robotics case study. Int. J. Prod. Res. 57, 6908–6921. doi:10.1080/00207543.2019.1571686
Muhamad, A. S., and Deris, S. (2013). An artificial immune system for solving production scheduling problems: A review. Artif. Intell. Rev. 39 (2), 97–108. doi:10.1007/s10462-011-9259-1
Nawaz, M., Enscore, E. E., and Ham, I. (1983). A heuristic algorithm for the m-machine, n-job flow-shop sequencing problem. Omega 11 (1), 91–95. doi:10.1016/0305-0483(83)90088-9
Palmer, D. S. (1965). Sequencing jobs through a multi-stage process in the minimum total time—A quick method of obtaining a near optimum. J. Operational Res. Soc. 16 (1), 101–107. doi:10.1057/jors.1965.8
Panwalkar, S. S., and Iskander, W. (1977). A survey of scheduling rules. Operations Res. 25 (1), 45–61. doi:10.1287/opre.25.1.45
Papakostas, N., Mourtzis, D., Michalos, G., Makris, S., and Chryssolouris, G. (2012). An agent-based methodology for manufacturing decision making: A textile case study. Int. J. Comput. Integr. Manuf. 25 (6), 509–526. doi:10.1080/0951192X.2011.637963
Papakostas, N., and Ramasubramanian, A. K. (2022). “Chapter 6-Digital technologies as a solution to complexity caused by mass personalization,” in Design and operation of production networks for mass personalization in the era of cloud technology. Editor D. Mourtzis (Elsevier, 153–180. doi:10.1016/B978-0-12-823657-4.00009-9
Parente, M., Figueira, G., Amorim, P., and Marques, A. (2020). Production scheduling in the context of industry 4.0: Review and trends. Int. J. Prod. Res. 58 (17), 5401–5431. doi:10.1080/00207543.2020.1718794
Pech, M., and Jaroslav, V. Index of industry 4.0. 2022, Encyclopedia, Available at: https://encyclopedia.pub/entry/1574 (accessed June 22, 2022).
Potts, C. N., and Strusevich, V. A. (2009). Fifty years of scheduling: A survey of milestones. J. Operational Res. Soc. 60 (1), S41–S68. doi:10.1057/jors.2009.2
Psarommatis, F., Danishvar, M., Mousavi, A., and Kiritsis, D. (2022). Cost-based decision support system: A dynamic cost estimation of key performance indicators in manufacturing. IEEE Trans. Eng. Manag., 99 1–13. doi:10.1109/TEM.2021.3133619
Psarommatis, F., May, G., Dreyfus, P. A., and Kiritsis, D. (2020a). Zero defect manufacturing: State-of-the-art review, shortcomings and future directions in research. Int. J. Prod. Res. 58 (1), 1–17. doi:10.1080/00207543.2019.1605228
Rauschecker, U., Meier, M., Muckenhirn, R., Yip, A., Jagadee-san, A., and Corney, J. (2011). Cloud-based manufacturing-as-a-service environment for customized products. Florence, Italy: IIMC, International Information Management Corporation.
Reinhart, G., and Geiger, F. (2011). Adaptive scheduling by means of product-specific emergence data, 2011 IEEE International Conference on Industrial Engineering and Engineering Management. 06-09 December 2011, Singapore, IEEE, 347–351. doi:10.1109/IEEM.2011.6117936
Reiter, S. (1966). A system for managing job-shop production. J. Busines. 39 3, 371–393. Available at: http://www.jstor.org/stable/2351855
Renu, R. S., Mocko, G., and Koneru, A. (2013). Use of big data and knowledge discovery to create data backbones for decision support systems. Procedia Comput. Sci. 20, 446–453. doi:10.1016/j.procs.2013.09.301
Rolón, M., and Martínez, E. (2012). Agent learning in autonomic manufacturing execution systems for enterprise networking. Computers Indust. Eng. 63 (4), 901–925. doi:10.1016/j.cie.2012.06.004
Rossit, D. A., Tohmé, F., and Frutos, M. (2019). Industry 4.0: Smart scheduling. Int. J. Prod. Res. 57 (12), 3802–3813. doi:10.1080/00207543.2018.1504248
Rossit, D. A., Tohmé, F., and Frutos, M. (2018). The non-permutation flow-shop scheduling problem: A literature review. Omega 77, 143–153. doi:10.1016/j.omega.2017.05.010
Sachs, J., Kroll, C., Lafortune, G., Fuller, G., and Woelm, F. (2021). Sustainable development report 2021. Cambridge University Press. Cambridge, United Kingdom
Sharp, M., Ak, Ar., and Hedberg, T. (2018). A survey of the advancing use and development of machine learning in smart manufacturing. J. Manuf. Syst. 48 (Part C), 170–179. doi:10.1016/j.jmsy.2018.02.004
Shukla, N., Tiwari, M. K., and Beydoun, G. (2019). Next generation smart manufacturing and service systems using big data analytics. Comput. Industrial Eng. 128, 905–910. doi:10.1016/j.cie.2018.12.026
Si, X. S., Wang, W., Hu, C. H., and Zhou, D. H. (2011). Remaining useful life estimation – a review on the statistical data-driven approaches. Eur. J. Operational Res. 213 (1), 1–14. doi:10.1016/j.ejor.2010.11.018
Stavropoulos, P., and Mourtzis, D. (2022). “Chapter 10-Digital twins in industry 4.0,” in Design and operation of production networks for mass personalization in the era of cloud technology. Editor D. Mourtzis (Elsevier, 277–316. doi:10.1016/B978-0-12-823657-4.00010-5
Stecca, G. 2014. Scheduling, CIRP encyclopedia of production engineering. L. Laperrière, and G. Reinhart (eds). in: The international academy for production engineering, Springer, Berlin, Heidelberg. doi:10.1007/978-3-642-20617-7_6571
Tai, L., Hu, R., Zhao, H., and Chen, C. (2013). Multi-objective dynamic scheduling of manufacturing resource to cloud manufacturing services. Zhongguo Jixie Gongcheng/China Mechanical Eng. 24, 1616–1622. doi:10.3969/j.issn.1004-132X.2013.12.012
Tao, F., LaiLi, Y., Xu, L., and Zhang, L. (2013). FC-PACO-RM: A parallel method for service composition optimal-selection in cloud manufacturing system. IEEE Trans. Ind. Inf. 9 (4), 2023–2033. doi:10.1109/TII.2012.2232936
Tao, F., Qi, Q., Liu, A., and Kusiak, A. (2018). Data-driven smart manufacturing. J. Manuf. Syst. 48 (Part C), 157–169. doi:10.1016/j.jmsy.2018.01.006
Toptal, A., and Sabuncuoglu, I. (2010). Distributed scheduling: A review of concepts and applications. Int. J. Prod. Res. 48 (18), 5235–5262. doi:10.1080/00207540903121065
Ueda, K. (1992). “A concept for bionic manufacturing systems based on DNA-type information,” in Human Aspects in Computer Integrated Manufacturing Proceedings of the IFIP TC5/WG 5.3 Eight International PROLAMAT Conference, Man in CIM, Tokyo, Japan, 24–26 June 1992 (Elsevier), 853–863.
Ueda, K., Hatono, I., Fujii, N., and Vaario, J. (2000). Reinforcement learning approaches to biological manufacturing systems. CIRP Ann. 49 (1), 343–346. doi:10.1016/S0007-8506(07)62960-6
Wan, J., Li, X., Dai, H. N., Kusiak, A., Martínez-García, M., and Li, D. (2013). Artificial-intelligence-driven customized manufacturing factory: Key technologies, applications, and challenges in Proceedings of the IEEE 109 (4), 377–398. doi:10.1109/JPROC.2020.3034808
Wang, X. V., and Xu, X. W. (2013). An interoperable solution for Cloud manufacturing. Robot. Comput. Integr. Manuf. 29 (4), 232–247. doi:10.1016/j.rcim.2013.01.005
Wang, Y., and Wu, Z. (2020). Model construction of planning and scheduling system based on digital twin. Int. J. Adv. Manuf. Technol. 109 (7), 2189–2203. doi:10.1007/s00170-020-05779-9
Wang, Z., Zhang, J. H., and Qi, Y. Q. (2017). Job shop scheduling method with idle time in cloud manufacturing. Control Decis. 32 (5), 811–816. doi:10.13195/j.kzyjc.2016.0447
Wang, Z., Zhang, J., and Si, J. (2014). “Application of particle swarm optimization with stochastic inertia weight strategy to resources scheduling and assignment problem in cloud manufacturing environment,” in Proceedings of the 33rd Chinese Control Conference, 28-30 July 2014, Nanjing, China, 7567–7572. doi:10.1109/ChiCC.2014.6896260
Wopata, M. (2020). Industry 4.0 adoption 2020 – Who is ahead? IoT analytics, market insiights for the internet of things. Available at: https://iot-analytics.com/industry-4-0-adoption-2020-who-is-ahead/ (Accessed June 22, 2022).
Wu, D., Greer, M. J., Rosen, D. W., and Schaefer, D. (2013). “Cloud manufacturing: Drivers, current status, and future trends,” in International Manufacturing Science and Engineering Conference Collocated with the 41st North American Manufacturing Research Conference, June 10–14, 2013 (Madison, WI. doi:10.1115/MSEC2013-1106
Xiao, Y. Y., Li, B. H., Zhuang, C. H., Chai, X. D., and Lin, T. Y. (2015). Distributed supply chain scheduling oriented to multi-variety customization. Comput. Integr. Manuf. Syst. 21 (3), 800–812. doi:10.1016/j.ijpe.2008.10.008
Xu, J., Tran, H. M., Gautam, N., and Bukkapatnam, S. (2019). Joint production and maintenance operations in smart custom-manufacturing systems. IISE Trans. 51 (4), 406–421. doi:10.1080/24725854.2018.1511938
Xu, X. (2012). From cloud computing to cloud manufacturing. Robotics Computer-Integrated Manuf. 28 (1), 75–86. doi:10.1016/j.rcim.2011.07.002
Xu, X., Lu, Y., Vogel-Heuser, B., and Wang, L. (2021). Industry 4.0 and industry 5.0—inception, conception and perception. J. Manuf. Syst. 61, 530–535. doi:10.1016/j.jmsy.2021.10.006
Yang, H., Kumara, S., Bukkapatnam, S., and Tsung, F. (2019). The internet of things for smart manufacturing: A review. IISE Trans. 51 (11), 1190–1216. doi:10.1080/24725854.2018.1555383
Yongkui, L., Lihui, W., Xi, W., Xun, X., and Lin, Z. (2019). Scheduling in cloud manufacturing: State-of-the-art and research challenges. Int. J. Prod. Res. 57, 4854–4879. doi:10.1080/00207543.2018.1449978
Yuan, M., Deng, K., Chaovalitwongse, W. A., and Cheng, S. (2017). Multi-objective optimal scheduling of reconfigurable assembly line for cloud manufacturing. Optim. Methods Softw. 32 (3), 581–593. doi:10.1080/10556788.2016.1230210
Zhang, S., and Wong, T. N. (2017). Flexible job-shop scheduling/rescheduling in dynamic environment: A hybrid MAS/ACO approach. Int. J. Prod. Res. 55 (11), 3173–3196. doi:10.1080/00207543.2016.1267414
Zhang, Z., Wang, X., Zhu, X., Cao, Q., and Tao, F. (2019). Cloud manufacturing paradigm with ubiquitous robotic system for product customization. Robotics Computer-Integrated Manuf. 60, 12–22. doi:10.1016/j.rcim.2019.05.015
Zhong, R. Y., Xu, C., Chen, C., and Huang, G. Q. (2017). Big data analytics for physical internet-based intelligent manufacturing shop floors. Int. J. Product. Res. 55 9, 2610–2621. doi:10.1080/00207543.2015.1086037
Zhou, J., and Yao, X. (2017). A hybrid approach combining modified artificial bee colony and cuckoo search algorithms for multi-objective cloud manufacturing service composition. Int. J. Prod. Res. 55 (16), 4765–4784. doi:10.1080/00207543.2017.1292064
Zhou, J., Zhou, Y., Wang, B., and Zang, J. (2019). Human–cyber–physical systems (HCPSs) in the context of new-generation intelligent manufacturing. Engineering 5 (4), 624–636. doi:10.1016/j.eng.2019.07.015
Keywords: artificial Intelligence, adaptive Scheduling, industry 4.0, manufacturing, cyber physical systems
Citation: Mourtzis D (2022) Advances in Adaptive Scheduling in Industry 4.0. Front. Manuf. Technol. 2:937889. doi: 10.3389/fmtec.2022.937889
Received: 06 May 2022; Accepted: 28 June 2022;
Published: 19 July 2022.
Edited by:
Dimitris Kiritsis, Swiss Federal Institute of Technology Lausanne, SwitzerlandReviewed by:
Flavio Tonelli, University of Genoa, ItalyFrancesco Gabriele Galizia, University of Bologna, Italy
Tianyuan Liu, Donghua University, China
Copyright © 2022 Mourtzis. This is an open-access article distributed under the terms of the Creative Commons Attribution License (CC BY). The use, distribution or reproduction in other forums is permitted, provided the original author(s) and the copyright owner(s) are credited and that the original publication in this journal is cited, in accordance with accepted academic practice. No use, distribution or reproduction is permitted which does not comply with these terms.
*Correspondence: Dimitris Mourtzis, bW91cnR6aXNAbG1zLm1lY2gudXBhdHJhcy5ncg==