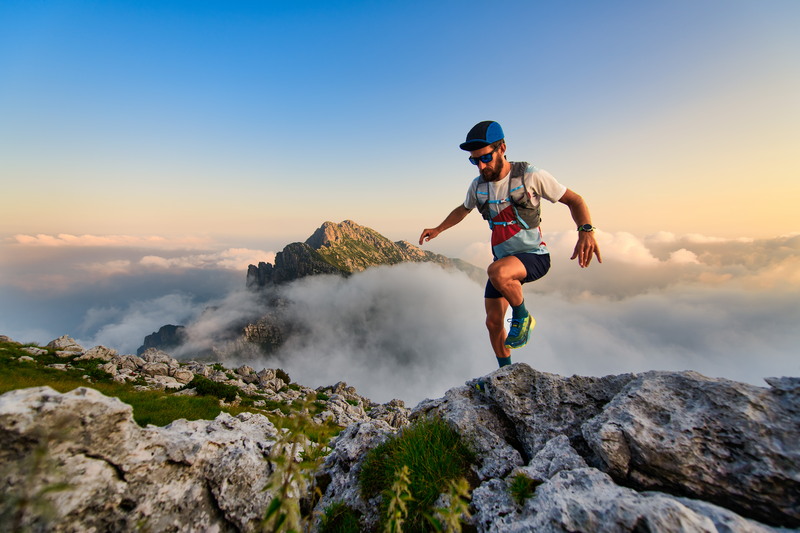
95% of researchers rate our articles as excellent or good
Learn more about the work of our research integrity team to safeguard the quality of each article we publish.
Find out more
EDITORIAL article
Front. Manuf. Technol. , 23 September 2022
Sec. Sustainable Life Cycle Engineering and Manufacturing
Volume 2 - 2022 | https://doi.org/10.3389/fmtec.2022.1008987
This article is part of the Research Topic Life Cycle Engineering in the Era of Industry 4.0 View all 5 articles
Editorial on the Research Topic
Life cycle engineering in the era of Industry 4.0
In today’s sustainability debate, industries are working to modernise their life cycle engineering strategies. Identifying a sustainable competitive edge in the era of Industry 4.0 is the most critical problem. Consequently, researchers and industry experts worldwide have optimised product life cycle by integrating machine learning, modern computing technologies, information management, and other multifaceted technologies, viz., semantic interoperability. Nevertheless, there are gaps between life cycle engineering and evolving Industry 4.0 technologies. Therefore, it is crucial to optimise the product life cycle via. digitalisation, innovation, resilience, and sustainability. This will allow for more value throughout the whole product’s life cycle design and resource planning to environmentally friendly production, unrestricted operational availability, and full recycling or reusability. In light of this, this Research Topic aims to assemble articles highlighting innovations in life cycle engineering motivated by Industry 4.0.
Three research articles and one review article are among the papers on this Research Topic that have been published. A sound maintenance plan is crucial for optimising life cycle engineering. The research work by Alamri and Mo used the failure mode and consequences analysis to build novel preventive maintenance (PM) schedule for a complex system. Their methodology mainly relies on mean-time-to-failure (MTTF) information derived from Industry 4.0 system feedback data. If new MTTF data becomes available, the technique makes it simple to change the PM schedule. The case study findings show that over 90% system reliability has been reached while ensuring that related costs are kept to a minimum. The technical, environmental, and economic effects of maintenance choices throughout the product life cycle are considered in this approach.
Information management has pushed digital manufacturing to discover more effective ways to link and share data throughout different system stages. One of the cornerstones of Industry 4.0 is the horizontal and vertical integration of intelligent and self-adaptive systems. To develop an intelligent manufacturing system, Pereira et al. tackled the problem of semantic interoperability. This study provided a conceptual framework based on semantic technologies to address semantic integration and interoperability issues. The architecture put forth is called MANUMATE, and it comprises two processes–ontology specialisation and information application, along with three artefacts–reference ontologies, requirements, and application ontologies. For beverage industry product life cycle optimisation, the system has been validated.
West et al. explored the research question in the smart factory environment through an integrative literature review: “What are the effects on product lifecycle management (PLM) when bundling assets with diverse operational lifespans in digitally enabled product-service systems?”. In addition, this study introduces the concept of nested lifecycles, which examines subsystems with different lifespans that must be handled holistically by other actors with different perspectives. Nested lifecycles take a systems perspective on asset management. Additionally, by enabling the nested lifecycles to be precisely recognised and handled, this study offers a framework for determining methods for lifespan management. The concept of nested lifecycles provides a fresh perspective to the asset management and PLM research community from a theoretical standpoint. From a managerial standpoint, the proposed paradigm will assist managers in understanding why and where collaboration between various actors may provide challenges because of their disparate perspectives and backgrounds.
Finally, to increase sustainability, Sarswatula et al. focused particularly on energy concerns in life cycle engineering. This study suggested the use of statistics and machine learning in the production of metal, electrical, food, and plastic to achieve sustainability at the industrial level. Herein, energy consumption prediction models are created utilising machine learning methods like the random forest regressor, the extreme gradient boost regressor, etc. The machine learning models could help compare the energy usage of factories and locate areas for energy efficiency improvement.
The papers gathered in this Research Topic can be seen as a “taster” for what is to come because the field of digital transformation of the engineering life cycle is constantly growing. More intriguing outcomes are expected in the future. Many thanks to all of the researchers that contributed to this Research Topic.
AJ drafted the editorial. SK and ST proofread it.
The authors declare that the research was conducted in the absence of any commercial or financial relationships that could be construed as a potential conflict of interest.
All claims expressed in this article are solely those of the authors and do not necessarily represent those of their affiliated organizations, or those of the publisher, the editors and the reviewers. Any product that may be evaluated in this article, or claim that may be made by its manufacturer, is not guaranteed or endorsed by the publisher.
Keywords: life cycle engineering, machine learning, Industry 4.0, maintenance, sustainability
Citation: Jain AK, Kumar S and Tayal S (2022) Editorial: Life cycle engineering in the era of Industry 4.0. Front. Manuf. Technol. 2:1008987. doi: 10.3389/fmtec.2022.1008987
Received: 01 August 2022; Accepted: 16 August 2022;
Published: 23 September 2022.
Edited and reviewed by:
Björn Johansson, Chalmers University of Technology, SwedenCopyright © 2022 Jain, Kumar and Tayal. This is an open-access article distributed under the terms of the Creative Commons Attribution License (CC BY). The use, distribution or reproduction in other forums is permitted, provided the original author(s) and the copyright owner(s) are credited and that the original publication in this journal is cited, in accordance with accepted academic practice. No use, distribution or reproduction is permitted which does not comply with these terms.
*Correspondence: Amit Kumar Jain, YW1pdGt1bWFyLmphaW5AZ2N1LmFjLnVr
Disclaimer: All claims expressed in this article are solely those of the authors and do not necessarily represent those of their affiliated organizations, or those of the publisher, the editors and the reviewers. Any product that may be evaluated in this article or claim that may be made by its manufacturer is not guaranteed or endorsed by the publisher.
Research integrity at Frontiers
Learn more about the work of our research integrity team to safeguard the quality of each article we publish.