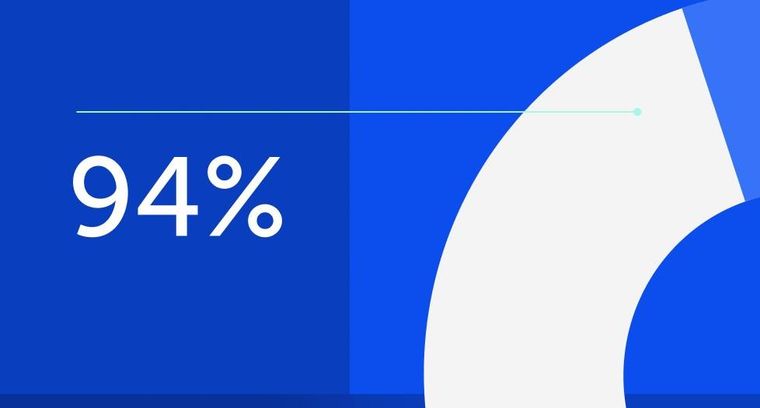
94% of researchers rate our articles as excellent or good
Learn more about the work of our research integrity team to safeguard the quality of each article we publish.
Find out more
REVIEW article
Front. Geochem., 30 April 2024
Sec. Mineral Geochemistry
Volume 2 - 2024 | https://doi.org/10.3389/fgeoc.2024.1378996
This article is part of the Research TopicCelebrating 1 Year of Frontiers in GeochemistryView all 4 articles
The global need for lithium (Li) is increasing due to its use in batteries which are used to make electric vehicles, wind turbines and fuel cells to facilitate the world’s ‘green transition’ to low carbon economies. The mining of Li, like that of other Earth materials, produces large volumes of waste such as tailings and processing chemicals. A growing body of research is addressing the resource potential and environmental impacts of wastes from mining of Li-bearing granites and pegmatites that produce around 40% of the world’s Li. The wastes are dominated by SiO2 and Al2O3, with lesser Na2O, K2O and Fe2O3, that are hosted in quartz, feldspar and micas. They can contain around 1 wt% Li2O that is found in residual spodumene, lepidolite and zinnwaldite, and trace (<1 wt%) amounts of Rb, Cs, U and Be. Some exploitation of the Li from granite-pegmatite tailings is occurring on a commercial scale. There is also good potential for the waste quartz, feldspar and mica to be used in ceramics and building materials, and for the Rb, Cs and Be to be used for photovoltaic cells, alloys and other applications. Spodumene-bearing wastes can contain potentially toxic and/or radioactive U, Th and Tl, but the concentrations are generally low. Overall, Li-bearing granite-pegmatite mine wastes have good potential to be reused, remined and recycled. More research is required to characterize their geochemistry and mineralogy in detail to improve recovery and to understand how processing and weathering may affect environmental risk.
The mining industry produces huge volumes of waste because the economic commodities form only a small proportion of the materials extracted (Hudson-Edwards, 2016). A variety of solid wastes are produced, including coal and mineral fuels, sediment, overburden soil, mill tailings, processing chemicals and metallurgical slag (Hudson-Edwards et al., 2011). In 2022 the global amount of mine wastes was estimated to be around 268 billion tonnes, and this has been projected to increase to around 379 billion tonnes by 2030 (Research and Markets, 2024). The main reason for this is that most high-grade deposits have already mined, leading industry to exploit larger deposits with lower grades (Hudson-Edwards et al., 2011). A secondary reason is that there is increasing demand for Critical Raw Materials (CRMs), Earth materials with high economic and/or strategic importance for which there is no adequate substitute and a high supply risk (EC European Commission, 2014). CRMs are essential components for modern technologies such as batteries, photovoltaics, wind turbines, electronics, fuel cells, mobile phones, computers and other products, many of which are required to provide renewable energy as the world aims to reduce its reliance on fossil fuels.
Lithium (Li) is regarded by many countries as a CRM because it is a major component of Li-ion batteries that power electric vehicles and other electrical devices, and because it is currently mined in only a few countries. The World Bank Group predicted that the production of lithium could increase by 500% by 2050 to meet demand (World Bank Group, 2020). Around 60% of lithium is produced from salar brines, and the rest is extracted from ‘hard rock’ Li-bearing granites and pegmatites (Tadesse et al., 2019). Little is known about the salar Li mine wastes except that they are salts rich in all cations in the brines except Li (Vera et al., 2023). By contrast, wastes from Li-bearing granite and pegmatite mining are better studied and some are being exploited for Li and other commodities.
Knowledge of the geochemistry and mineralogy of wastes is essential for evaluating their potential for reuse, remining and recycling, in designing and optimising schemes to extract their economic components and in understanding and managing their environmental impacts (Brough et al., 2013; Jamieson et al., 2015). In this review the generation of Li-bearing granite-pegmatite wastes are outlined, and their geochemistry, mineralogy, resource potential and environmental impacts are described, and themes for future research are presented.
Li-bearing granites and pegmatites occur in every continent of the world except, to our knowledge, in Antarctica. The largest deposits are found in Australia, China and Brazil (Shaw, 2016). The parent magmas form at the post-collisional stage of orogenesis (Bradley et al., 2017), and the Li-bearing granites crystallise from these. Coarse-grained Li-bearing pegmatites are thought to form by crystallisation of highly fractionated melts that are derived from the granitic magmas (London, 2018; Li et al., 2023), or anatexis of sedimentary rocks (Shaw et al., 2016; Müller et al., 2017) or Li-rich clays and borates (Simmons and Webber, 2008).
These rocks contain a variety of Li-bearing minerals that are summarised in Table 1. Lepidolite and zinnwaldite are the most common minerals in Li-granites, whereas spodumene and petalite are the main minerals found in pegmatites (Gourcerol et al., 2019). The other minerals shown in Table 1 occur in lesser amounts, mainly in pegmatites.
Table 1. Lithium-bearing minerals in Li-bearing granite-pegmatite ores and mine wastes. Adapted from Brown (2016) and Aylmore et al. (2018).
Despite their global occurrence, in 2022 Li-bearing granites and pegmatites were mined only in Australia (accounting for most of the production), China, Zimbabwe, Portugal and Canada (USGS, 2023). Spodumene was also recovered from tailings produced by AMG’s tantalum Mibra Mine in Brazil (AMGLithium, 2024). In 2022, considerable exploration and development of Li-bearing granites and pegmatites was taking place globally (Australia, Austria, Brazil, Canada, China, Congo (Kinshasa), Czechia, Ethiopia, Finland, Germany, Ghana, Kazakhstan, Mali, Namibia, Nigeria, Peru, Portugal, Russia, Serbia, Spain, Thailand, Zimbabwe; (USGS, 2023), and so many more mines may be operational in the future.
Spodumene is the main Li-bearing mineral that is processed by industry due to its abundance and high Li content (Table 1) (Tadesse et al., 2019). It is concentrated using heavy media separation, froth flotation and/or magnetic separation processes (Amarante et al., 1999) To extract Li, spodumene concentrates undergo calcination at temperatures between 850°C and 1,100°C (Salakjani et al., 2016; Karrech et al., 2021b; Pickles and Marzoughi, 2022). This process causes the original monoclinic α-spodumene to transform to tetragonal β-spodumene that has a 30% larger structure and lower bulk density than the α-spodumene (Paris et al., 2023). These new properties allow the β-spodumene to be easily leached, often in concentrated sulfuric acid (H2SO4), resulting in the production of soluble Li2SO4 which is used to make Li hydroxide and Li carbonate (Salakjani et al., 2019). Digestion of the β-spodumene with HF and Ca(OH)2 is also used to extract the Li (Rosales et al., 2014). The wastes produced from these processes are known as delithiated β-spodumene (DβS) tailings (Karrech et al., 2021b; Karrech et al., 2021a).
Zinnwaldite can also be concentrated by flotation (Samková, 2009) and because it contains relatively high amounts of Fe (Table 2), by magnetic separation (Botula et al., 2005; Tadesse et al., 2019). The resulting concentrate can be calcined with CaCO3 and leached with water. A very high quality (>99% pure) Li2CO3 concentrate can then be produced (Jandová et al., 2010). Lepidolite can also be concentrated using flotation, but it can be difficult to separate from muscovite due to their similar compositions (Tadesse et al., 2019). As with spodumene, lepidolite concentrates can also be digested in hot H2SO4 to recover Li. The resultant solutions can also contain K, Al, Rb and Cs, making separation and purification of the Li challenging (Li et al., 2019). Research is ongoing to attempt to crystallise the contaminating cations as mixed alums to provide a higher purity Li solution (Vieceli et al., 2018).
The major and trace element geochemical compositions of a range of wastes from lithium (spodumene), Sn-W and kaolinite mining are summarised in Table 2. All wastes have high concentrations of SiO2 (50.7–81.5 wt%) and Al2O3 (8.29–27.0 wt%) and moderate concentrations of Na2O (0.4–6.7 wt%), K2O (0.6–13.2 wt%) and Fe2O3 (0.1–8.39 wt%). Variable but low (<1 wt%) concentrations of CaO, MgO, TiO2, P2O5, BeO, Rb2O and SO3 have also been reported. Lithium oxide (Li2O) concentrations range from 0.02 to 1.3 wt%. Concentrations of potentially toxic metal (loids) such as As, Cd, Cu, Pb and Zn are generally not reported for Li-bearing granite-pegmatite wastes, but when they are, they tend to be very low (Lemougna et al., 2019a). Concentrations of U, Th and Tl are discussed in the Environmental Impacts section of this paper.
Lithium-bearing granite-pegmatite wastes are normally white in colour (Figure 1A) and fine-grained, with heterogeneous grain sizes and angular shapes (Figure 1B). The major (>5 vol%) and minor (<5 vol%) minerals in the wastes are summarised in Table 3. Quartz, plagioclase, K-feldspar and muscovite are the major minerals present and account for the high to moderate concentrations of SiO2, Al2O3, Na2O and K2O in the wastes (Table 2). Minerals such as Nb-Ta oxides (Table 3) account for the minor amounts of Nb2O5 and Ta2O5 present (Table 2).
Figure 1. (A) Lithium-bearing wastes in former kaolinite mine pit, Cornwall, United Kingdom (B) scanning electron microscope (SEM) photomicrograph of quartz feldspar sand (QFS) from spodumene tailings waste. Q: quartz, (A) albite, M: microcline. Numbered stars show point that were analysed to determine mineral composition. Reprinted from Minerals Engineering, 141, Lemougna, P.N. et al., Spodumene tailings for porcelain and structural materials: Effect of temperature (1,050°C–1,200°C) on the sintering and properties, 105,843, Copyright (2019), with permission from Elsevier.
Table 3. Resource potential and environmental risk of minerals in Li-bearing granite-pegmatite mine wastes.
Most of the mineralogical determination of Li-bearing granite-pegmatite wastes is done using X-ray diffraction (e.g., (Lemougna et al., 2019b; Karrech et al., 2021a). While this method can identify minerals, it does not give information on their trace element compositions. Roy et al. (2023) sampled spodumene from the raw ore, concentrator feed and tailings from density separation and spodumene flotation at the Whabouchi mine project in Québec, Canada. They conducted extensive mineralogical analysis using automated mineralogical analysis with a QEMSCAN™ instrument, scanning electron microscopy (SEM) with energy dispersive spectrometers (EDS) and electron probe micro analysis (EPMA) for major and trace element chemical analysis, respectively. They showed that the processing reduced the amount of spodumene from ore to tailings but did not alter mineral compositions. Many of the minerals were shown to have trace impurities. The spodumene, for example, contained trace amounts of Fe, Mn and Nb whereas the petalite did not. Nb-Ta oxides ranged in composition from columbite-rich ((Fe,Mn)(Nb>>Ta)O6) to pure tantalite ((Fe,Mn)TaO6), and contained trace Ti, Sn and U. Such data are useful in evaluating the resource potential and environmental impact of the wastes.
The Li concentrations in the granite-pegmatite wastes (Table 2) have been considered high enough for researchers and industry to find optimal methods for their reprocessing. Froth flotation has been successfully shown to concentrate the spodumene (Yusupov et al., 2015; Tian et al., 2018), lepidolite (He et al., 2013; Sousa et al., 2018) and zinnwaldite (Samková, 2009; Jandová et al., 2010; Siame and Pascoe, 2011) from these wastes to upgrade their Li content (Table 3). Flotation can be followed by magnetic separation to further increase the amount of Li in the concentrate to around 4.5–6.0 wt% Li2O (Siame and Pascoe, 2011; Yusupov et al., 2015; Tian et al., 2018). The remaining feldspars and quartz can also be separated by flotation and used for other products (Sousa et al., 2018; Tian et al., 2018)(see next section). These combined actions can use of the majority of the wastes produced from the primary mining (e.g., 70%; Tian et al. (2018)).
The resultant Li waste concentrate can be processed using similar methods to those used for primary Li ores. This can involve roasting with additives such as limestone, gypsum and sodium sulfate (Siame and Pascoe, 2011). This process is followed by leaching with H2SO4 or other acids (e.g., HF) at moderate to high temperatures to recover the Li and make it into saleable products such as Li2CO3 and Li(OH) (Jandová et al., 2010).
The resource potential of the quartz, feldspar and mica components of Li-bearing granite-pegmatite wastes have been evaluated by several researchers. Two types of wastes have been studied: DβS tailings (Karrech et al., 2021b; Karrech et al., 2021a) and quartz and feldspar rich tailings from spodumene tailings, known as quartz feldspar sand (QFS) (Lemougna et al., 2019a; Lemougna et al., 2019b; Lemougna et al., 2020). DβS has been characterised as a silt loam with variably shaped and sharp-edged grains (Karrech et al., 2021a). It requires addition of granulated blast furnace slag to make construction and geotechnical materials. When such mixtures are made, often with other wastes such as fly ash, the addition of DβS has been shown to increase workability and setting time, and to reduce shrinkage (Karrech et al., 2021b; Karrech et al., 2021a).
QFS has been evaluated as a raw material for ceramic production. Lemougna et al. (2019a), Lemougna et al. (2019b) and Lemougna et al. (2020) carried out experiments using QFS from Keliber Oy in Finland to evaluate its suitability for porcelain and construction materials. The QFS comprised quartz, albite, microcline and minor muscovite (Table 3). QFS was combined with kaolinite (Lemougna et al., 2019b), ladle slag (Lemougna et al., 2019a) and glass wool waste (Lemougna et al., 2020) and analysed to determine optimal mixtures for porcelain, brick and construction materials, respectively. Grinding of some of the components, sintering temperatures, secondary mineral formation and addition of fluxes such as sodium hydroxide and carbonate were the major factors affecting the density and strength of the final products. It was concluded that QFS had significant potential to be used as a resource.
Lithium lies in Group 1 of the Periodic Table can be substituted in minerals by other elements in this group. One of these is Rb, which is known to occur in spodumene, lepidolite and zinnwaldite (Kunasz, 2006). Rb2O concentrations between 0.17 and 0.40 wt% have been reported in lepidolite- and zinnwaldite-bearing wastes from Sn-W and kaolinite mining (Table 1). The Rb can be recovered from these minerals when processing for Li (Buttermann and Reese Jr, 2003). Jandová et al. (2010), for example, recovered Rb by roasting zinnwaldite concentrates containing 1.21wt% Li and 0.84wt% Rb with CaCO3 and leaching the produced calcine with water. The concentrate was prepared from zinnwaldite wastes containing 0.21wt% Li and 0.20wt% Rb that were generated through the processing of Sn-W ores. Notable concentrations of Rb2O have been documented in spodumene tailings (Melentiev et al., 2022; Roy et al., 2023) (Table 2), and Rb is also known to occur in muscovite, which is present in all Li-bearing granite-pegmatite mine wastes documented in Table 2. As a result, many authors have suggested that these wastes may be suitable exploration targets for Rb that could be used in photovoltaic cells and other applications (Siame and Pascoe, 2011; Iqbal, 2015; Melentiev et al., 2022; Bian et al., 2023).
Trace concentrations of Cs (0.11 wt%) have been found in zinnwaldite-bearing wastes from the dressing of Sn-W ores (Jandová et al., 2010). Samková (2009) demonstrated that the zinnwaldite from such wastes could be effectively separated using flotation with an amine-based cationic collector at laboratory scale.
The mineral beryl has been found in spodumene tailings (Table 3) and has been proposed to be a source of Be for alloys (Browning et al., 1964; Melentiev et al., 2022). Browning et al. (1964) showed that it could be recovered using an HF activator and an oleic acid collector.
The potential environmental impacts of the minerals and their included elements are summarised in Table 3. Kinetic leach testing of spodumene-bearing tailings from the Whabouchi mine project in Québec, Canada, produced waters with mg to sub-mg/L amounts of U (Roy et al., 2023). These were attributed to the weathering of primary uraninite and U-rich zircon in the tailings in the presence of a Ca-bearing fluid. Phases with uranophane (Ca(UO2)2SiO3(OH)2⋅5H2O) compositions and U-Ca-phosphates were found in filling voids and fractures in spodumene tailings, and were proposed to precipitate from these fluids. Overall, however, the U concentrations in these wastes (2.97–5.28 mg/kg) are well below Canadian Soil Guideline Values of 23–300 mg/kg (CCME, 2024).
Other potentially ecotoxic elements have been found Li-bearing granite-pegmatite tailings. Melentiev et al. (2022) detected Tl (1.51–5.49 mg/kg) in spodumene tailings from the Zabaikalsk mining and processing plant in Russia. Thallium (1.2–2.8 mg/kg) was also found in the Whabouchi tailings, in addition to minor amounts of Th (1.2–2.8 mg/kg) (Roy et al., 2022).
Sulfur contents of Li-bearing granite/pegmatite wastes are not always reported, but those available are low (Table 2), suggesting that the wastes will not generate acid. This is confirmed by paste pH and leaching tests that yield waters with pH values between eight and nine (e.g., Chen and Goulet, 2022; Roy et al., 2022).
The evolution of spodumene flotation and analcime-containing tailings from the former Quebec Lithium Corporation site in La Corne, Quebec, Canada during 55 years of storage was evaluated by (Roy et al., 2022). Textural analysis and sequential extraction data suggested that the tailings had not been significantly weathered nor formed secondary minerals. Despite this, elevated concentrations of Li, Al, K, Rb and Be were found in the chemical extractant solutions derived from the analcime tailings. These were suggested to result from the acid roasting and pressured alkaline leaching that the materials had experienced, which would have made them more susceptible to breakdown. High (mg/L-level) concentrations of Li in the tailings porewaters may have been due to this process, but their environmental impacts were unknown. Chen and Goulet (2022) compared metal concentrations from static and kinetic leach tests on wastes from three unnamed proposed spodumene Li mines in Quebec to Canadian and USA groundwater and aquatic life water quality guidelines. They found that some of the As, Cu and Li concentrations were above the guideline values. Based on their analysis, they recommended that the As and Cu data should be used in environmental risk assessment models and that Li toxicity testing should be conducted to optimise mine waste management.
The published studies of Roy et al. (2022), Roy et al. (2023) and Chen and Goulet (2022) are, to the author’s knowledge, the few that have evaluated the long-term stability and potential impacts of Li granite-pegmatite mine wastes and related these to potential environmental impacts. Given the potential increase in hard-rock Li mining that may occur in the 2020s and 2030s, more research is needed, especially as high concentrations of Li have been found in other mining-affected areas (e.g., 13 mg/L Li in mine drainage; Aral and Veccio-Sadus (2008)).
Mine wastes generated from Li-bearing granite and pegmatite extraction and processing have high contents of SiO2 and Al2O3, and moderate contents of Na2O, K2O and Fe2O3, which are hosted in quartz, feldspar and micas. They also contain 0.02 to 1.3 wt% Li2O that is found in residual spodumene, lepidolite and zinnwaldite. A growing body of research has shown that there is significant potential for the wastes to be reused, remined and recycled to recover Li, quartz-feldspar sand, Rb, Cs and Be for a variety of applications. Overall the wastes are not toxic nor acid-generating, but some contain U and Th that may generate radioactivity.
Although bulk geochemical and mineralogical data for the Li-bearing granite/pegmatite wastes are documented in the literature, they are insufficient for understanding the effects of processing and weathering on the potential mobility of elements from the wastes, and for understanding how the presence of mineral impurities may affect the quality and stability of reuse, recycling or remining products (Table 3). Detailed mineral chemical and textural evidence such as that presented in Roy et al. (2022) and Roy et al. (2023) is required for these wastes to enable their full resource and environmental risk potentials to be evaluated. This information can be combined with geochemical data and leaching tests to understand the geochemical behaviour of the wastes and their products (Parbhakar-Fox et al., 2013; Jamieson et al., 2015), and in turn potentially increase the market value and demand for the latter.
KH-E: Writing–original draft, Writing–review and editing.
The author(s) declare financial support was received for the research, authorship, and/or publication of this article. This review is supported by the UK’s Natural Environment Research Council funded Lithium for Future Technology (LiFT) project (NE/V007009/1).
KHE thanks members of the LiFT research team for support.
The author declares that the research was conducted in the absence of any commercial or financial relationships that could be construed as a potential conflict of interest.
The author(s) declared that they were an editorial board member of Frontiers, at the time of submission. This had no impact on the peer review process and the final decision.
All claims expressed in this article are solely those of the authors and do not necessarily represent those of their affiliated organizations, or those of the publisher, the editors and the reviewers. Any product that may be evaluated in this article, or claim that may be made by its manufacturer, is not guaranteed or endorsed by the publisher.
Amarante, M. M., De Sousa, A. B., and Leite, M. M. (1999). Processing a spodumene ore to obtain lithium concentrates for addition to glass and ceramic bodies. Miner. Eng. 12, 433–436. doi:10.1016/s0892-6875(99)00023-0
AMGLITHIUM (2024). AMGLIthium. Available at: https://amglithium.com/ (Accessed January 28, 2024).
Aral, H., and Vecchio-Sadus, A. (2008). Toxicity of lithium to humans and the environment-A literature review. Ecotoxicol. Environ. Saf. 70, 349–356. doi:10.1016/j.ecoenv.2008.02.026
Aylmore, M. G., Merigot, K., Quadir, Z., Rickard, W. D. A., Evans, N. J., Mcdonald, B. J., et al. (2018). Applications of advanced analytical and mass spectrometry techniques to the characterisation of micaceous lithium-bearing ores. Miner. Eng. 116, 182–195. doi:10.1016/j.mineng.2017.08.004
Bian, Z., Zhang, H., Ye, J., and Ning, Z. (2023). Flotation behavior of oleate and dodecylamine as mixed collector for recovery of lithium and rubidium from low-grade spodumene tailings: experiment, characterization and DFT calculation. Appl. Surf. Sci. 638, 158117. doi:10.1016/j.apsusc.2023.158117
Botula, J., Rucký, P., and Řepka, V. (2005). Extraction of zinnwaldite from mining and processing wastes.
Bradley, D. C., Mccauley, A. D., and Stillings, L. L. (2017). “Mineral-deposit model for lithium-cesium-tantalum pegmatites,” in Mineral deposit models for resource assessment (USBS).
Brough, C. P., Warrender, R., Bowell, R. J., Barnes, A., and Parbhakar-Fox, A. (2013). The process mineralogy of mine wastes. Miner. Eng. 52, 125–135. doi:10.1016/j.mineng.2013.05.003
Browning, J. S., Bennett, P. E., and Mcvay, T. L. (1964). Continuous flotation of beryl from spodumene mill tailings. Kings Mountain, N.C. Washington: Foote Mineral Company.
Buttermann, W. C., and Reese, R. G. (2003). Mineral commodity profiles rubidium. Open File Report 03-045. U.S. Geological Survey.
Ccme, C. C. O. M. O. T. E. (2024). Canadian environmental quality guidelines (CEQGs). Available at: https://ccme.ca/en/current-activities/canadian-environmental-quality-guidelines (Accessed January 9, 2024).
Chen, R., and Goulet, R. R. (2022). “Identifying potential contaminants of concern in lithium mine waste to limit environmental impacts,” in 12th ICARD International Conference on Acid Rock Drainage, Virtual Australia, September 21, 2022.
EC (EUROPEAN COMMISSION (2014). EU commission, 2014. Report on critical raw materials for the EU. Report of the ad-hoc working Group on defining critical raw materials.
Gourcerol, B., Gloaguen, E., Melleton, J., Tuduri, J., and Galiegue, X. (2019). Re-assessing the European lithium resource potential - a review of hard-rock resources and metallogeny. Ore Geol. Rev. 109, 494–519. doi:10.1016/j.oregeorev.2019.04.015
He, G. C., Feng, J. N., Mao, M. X., and Wu, Y. P. (2013). Application of combined collectors in flotation of lepidolite. Adv. Mater. Res. 734-737, 921–924. doi:10.4028/www.scientific.net/amr.734-737.921
Huang, Z., Zhang, S., Cheng, C., Wang, H., Liu, R., Hu, Y., et al. (2020). Recycling lepidolite from tantalum−niobium mine tailings by a combined magnetic−flotation process using a novel Gemini surfactant: from tailings dams to the “bling” raw material of lithium. ACS Sustain. Chem. Eng. 8, 18206–18214. doi:10.1021/acssuschemeng.0c06609
Hudson-Edwards, K. A. (2016). Tackling mine wastes. Science 352, 288–290. doi:10.1126/science.aaf3354
Hudson-Edwards, K. A., Jamieson, H. E., and Lottermoser, B. G. (2011). Mine wastes: past, present, future. Elements 7, 375–380. doi:10.2113/gselements.7.6.375
Iqbal, Z. (2015). Recovery of lithium from kaolin mining waste material (Birmingham, UK: University of Birmingham). PhD.
Jamieson, H. E., Walker, S. R., and Parsons, M. B. (2015). Mineralogical characterization of mine waste. Appl. Geochem. 57, 85–105. doi:10.1016/j.apgeochem.2014.12.014
Jandová, J., Dvořák, P., and Vu, H. N. (2010). Processing of zinnwaldite waste to obtain Li2CO3. Hydrometallurgy 103, 12–18. doi:10.1016/j.hydromet.2010.02.010
Karrech, A., Dong, M., Skut, J., Elchalakani, M., and Shahin, M. A. (2021a). Management and valorisation of delithiated β-spodumene and its processing stream. Case Stud. Constr. Mater. 15, e00671. doi:10.1016/j.cscm.2021.e00671
Karrech, A., Dong, M., Skut, J., Elchalakani, M., and Shahin, M. (2021b). Delithiated β−spodumene as a geopolymer precursor. Constr. Build. Mater. 309, 124974. doi:10.1016/j.conbuildmat.2021.124974
Kunasz, I. (2006). “Lithium resources,” in Industrial minerals and rocks Editors J. E. KOGEL, N. C. TRIVEDI, J. M. BARKER, and S. T. KRUKOWSKI 7 (Littleton, Colorado, USA: Society for Mining, Metallurgy and Exploration Inc).
Lemougna, P. N., Yliniemi, J., Ismailov, A., Levanen, E., Tanskanen, P., Kinnunen, P., et al. (2019a). Recycling lithium mine tailings in the production of low temperature (700–900 °C) ceramics: Effect of ladle slag and sodium compounds on the processing and final properties. Constr. Build. Mater. 221, 332–344. doi:10.1016/j.conbuildmat.2019.06.078
Lemougna, P. N., Yliniemi, J., Ismailov, A., Levanen, E., Tanskanen, P., Kinnunen, P., et al. (2019b). Spodumene tailings for porcelain and structural materials: Effect of temperature (1050–1200 °C) on the sintering and properties. Miner. Eng. 141, 105843. doi:10.1016/j.mineng.2019.105843
Lemougna, P. N., Yliniemi, J., Nguyen, H., Adesanya, E., Tanskanen, P., Kinnunen, P., et al. (2020). Utilisation of glass wool waste and mine tailings in high performance building ceramics. J. Build. Eng. 31, 101383. doi:10.1016/j.jobe.2020.101383
Li, B., Zhao, L., Lu, A.-H., Luo, J.-B., Kong, H., and Lai, J.-Q. (2024). Mineralogical constraints on pegmatite genesis and rare metal mineralization in the Mufushan batholith, South China. Ore Geol. Rev. 164, 105856. doi:10.1016/j.oregeorev.2023.105856
Li, H., Eksteen, J., and Kuang, G. (2019). Recovery of lithium from mineral resources: state-of-the-art and perspectives – a review. Hydrometallurgy 189, 105129. doi:10.1016/j.hydromet.2019.105129
London, D. (2018). Ore-forming processes within granitic pegmatites. Ore Geol. Rev. 101, 349–383. doi:10.1016/j.oregeorev.2018.04.020
Melentiev, G. B., Yurgenson, G. A., and Delitzyn, L. M. (2022). Prospects and priorities for the reconstruction and development of lithium mining production on the basis of domestic raw materials. Эволюция биосферы и техногенез. Материалы Всероссийской конференции с международным участием 962, 012055. doi:10.57245/978_5_9293_3064_3_2022_1_218
Müller, A., Romer, R. L., and Pedersen, R.-B. (2017). The Sveconorwegian pegmatite province – thousands of pegmatites without parental granites. Can. Mineralogist 55, 283–315. doi:10.3749/canmin.1600075
Parbhakar-Fox, A., Lottermoser, B., and Bradshaw, D. (2013). Evaluating waste rock mineralogy and microtexture during kinetic testing for improved acid rock drainage prediction. Miner. Eng. 52, 111–124. doi:10.1016/j.mineng.2013.04.022
Paris, J., Mohammadi-Jam, S., Li, R., Liang, J., Oh, H. J., Kökkiliç, O., et al. (2023). “Preliminary investigation into lithium extraction by phosphoric acid leaching of spodumene,” in Sustainable minerals (United Kingdom: Falmouth).
Pickles, C. A., and Marzoughi, O. (2022). Thermodynamic modelling of spodumene decrepitation. Mineral Process. Extr. Metallurgy 131, 130–144. doi:10.1080/25726641.2020.1827675
Rosales, G. D., Ruiz, M. D. C., and Rodriguez, M. H. (2014). Novel process for the extraction of lithium from β-spodumene by leaching with HF. Hydrometallurgy 147-148, 1–6. doi:10.1016/j.hydromet.2014.04.009
Roy, T., Plante, B., Benzaazoua, M., and Demers, I. (2023). Geochemistry and mineralogy of a spodumene-pegmatite lithium ore at various mineral beneficiation stages. Miner. Eng. 202, 108312. doi:10.1016/j.mineng.2023.108312
Roy, T., Plante, B., Benzaazoua, M., Demers, I., Coudert, L., and Turcotte, S. (2022). Geochemistry of decades-old spodumene mine tailings under a humid continental climate. Appl. Geochem. 146, 105481. doi:10.1016/j.apgeochem.2022.105481
Salakjani, N. K., Singh, P., and Nikoloski, A. N. (2016). Mineralogical transformations of spodumene concentrate from Greenbushes, Western Australia. Part 1: conventional heating. Miner. Eng. 98, 71–79. doi:10.1016/j.mineng.2016.07.018
Salakjani, N. K., Singh, P., and Nikoloski, A. N. (2019). Production of lithium - a literature review. Part 2. Extraction from spodumene. Mineral Process. Extr. Metallurgy Rev. 42, 268–283. doi:10.1080/08827508.2019.1700984
Samková, R. (2009). Recovering lithium mica from the waste after mining Sn-W ores through the use of flotation. Geosci. Eng. LV, 33–37.
Shaw, R. A., Goodenough, K. M., Roberts, N. M. W., Horstwood, M. S. A., Chenery, S. R., and Gunn, A. G. (2016). Petrogenesis of rare-metal pegmatites in high-grade metamorphic terranes: a case study from the Lewisian Gneiss Complex of north-west Scotland. Precambrian Res. 281, 338–362. doi:10.1016/j.precamres.2016.06.008
Siame, E., and Pascoe, R. D. (2011). Extraction of lithium from micaceous waste from China clay production. Miner. Eng. 24, 1595–1602. doi:10.1016/j.mineng.2011.08.013
Simmons, W. B. S., and Webber, K. L. (2008). Pegmatite genesis: state of the art. Eur. J. Mineralogy 20, 421–438. doi:10.1127/0935-1221/2008/0020-1833
Sousa, R., Ramos, V., Guedes, A., Noronha, F., Botelho de Sousa, A., Machado Leite, M., et al. (2018). The Alvarrões-Gonçalo Li project: an example of sustainable lithium mining. Adv. Geosciences 45, 1–5. doi:10.5194/adgeo-45-1-2018
Tadesse, B., Makuei, F., Albijanic, B., and Dyer, L. (2019). The beneficiation of lithium minerals from hard rock ores: a review. Miner. Eng. 131, 170–184. doi:10.1016/j.mineng.2018.11.023
Tian, J., Xu, L., Wu, H., Fang, S., Deng, W., Peng, T., et al. (2018). A novel approach for flotation recovery of spodumene, mica and feldspar from a lithium pegmatite ore. J. Clean. Prod. 174, 625–633. doi:10.1016/j.jclepro.2017.10.331
Vera, M. L., Torres, W. R., Galli, C. I., Chagnes, A., and Flexer, V. (2023). Environmental impact of direct lithium extraction from brines. Nat. Rev. Earth Environ. 4, 149–165. doi:10.1038/s43017-022-00387-5
Vieceli, N., Nogueira, C. A., Pereira, M. F. C., Durão, F. O., Guimarães, C., and Margarido, F. (2018). Optimization of an innovative approach involving mechanical activation and acid digestion for the extraction of lithium from lepidolite. Int. J. Minerals, Metallurgy Mater. 25, 11–19. doi:10.1007/s12613-018-1541-7
WORLD BANK GROUP (2020). Minerals for climate action: the mineral intensity of the clean energy transition. Washington, D.C., United States: WORLD BANK GROUP.
Yusupov, T. S., Isupov, V. P., Vladimirov, A. G., Zagorsky, V. E., Kirillova, E. A., Shumskaya, L. G., et al. (2015). Analysis of material composition and dissociation potential of minerals in mine waste to assess productivity of lithium concentrates. J. Min. Sci. 51, 1242–1247. doi:10.1134/s106273911506054x
Keywords: lithium, mine waste, granite, pegmatite, spodumene, lepidolite, quartz feldspar sand
Citation: Hudson-Edwards KA (2024) Geochemistry and mineralogy of wastes from lithium-bearing granite-pegmatite mining: resource potential and environmental risks. Front. Geochem. 2:1378996. doi: 10.3389/fgeoc.2024.1378996
Received: 30 January 2024; Accepted: 05 April 2024;
Published: 30 April 2024.
Edited by:
Jon Telling, Newcastle University, United KingdomReviewed by:
Nikolaos Koukouzas, Centre for Research and Technology Hellas (CERTH), GreeceCopyright © 2024 Hudson-Edwards. This is an open-access article distributed under the terms of the Creative Commons Attribution License (CC BY). The use, distribution or reproduction in other forums is permitted, provided the original author(s) and the copyright owner(s) are credited and that the original publication in this journal is cited, in accordance with accepted academic practice. No use, distribution or reproduction is permitted which does not comply with these terms.
*Correspondence: Karen A. Hudson-Edwards, ay5odWRzb24tZWR3YXJkc0BleGV0ZXIuYWMudWs=
Disclaimer: All claims expressed in this article are solely those of the authors and do not necessarily represent those of their affiliated organizations, or those of the publisher, the editors and the reviewers. Any product that may be evaluated in this article or claim that may be made by its manufacturer is not guaranteed or endorsed by the publisher.
Research integrity at Frontiers
Learn more about the work of our research integrity team to safeguard the quality of each article we publish.