- 1Engines and Energy Conversion Lab, Department of Mechanical Engineering, Colorado State University, Fort Collins, CO, United States
- 2Cooper Machinery Service, Houston, TX, United States
Impending and increasingly stringent emissions regulations regarding natural gas compressor engines drive the research behind blending hydrogen with natural gas to make these internal combustion engines and their combustion process more efficient. This investigation seeks to answer two fundamental questions: will blending hydrogen with natural gas reduce overall engine fuel consumption, and can greenhouse gas emissions be reduced by blending hydrogen with natural gas? A 4-cylinder Cooper–Bessemer GMV engine, housed at Colorado State University’s Powerhouse facility, was investigated for hydrogen–natural gas blending using multiple engine configurations. A lean-burn engine uses an active pre-combustion chamber as its ignition source, along with electronically activated high pressure fuel injection in the main combustion chamber. One configuration tested utilized high-pressure fuel injection and blending in hydrogen, up to 40% by volume, in both the main chamber and pre-combustion chamber fuel supplies. A second configuration, where the main combustion chamber fuel was solely natural gas and only the pre-combustion chamber received hydrogen-blended natural gas, was also tested. The final configuration to be tested used low pressure fuel injection with mechanically actuated valves in the main chamber with a traditional spark plug ignition source. All engine configurations saw reductions in methane emissions of up to 30% using blended natural gas and hydrogen. Carbon dioxide emissions were also shown to be reduced for the two configurations. A reduction in brake-specific fuel consumption of up to 2% was also seen for two configurations. These results support the hypothesis that blending hydrogen into natural gas can reduce engine total fuel consumption and reduce greenhouse gas emissions.
1 Introduction
More than 6000 integral natural gas (NG) compressors are located along The United States’ natural gas pipelines. These compressors are primarily powered by 2-stroke, slow speed (300 rpm) large bore (14–22”) natural gas engines. Many of these engines have been operating for over 50 years. Due to their heavy construction, slow speed, and low power density, they are very reliable and could potentially operate for another 50 years. Ensuing emissions regulations are the primary impediment to their continued use on pipelines. Low-cost retrofit technologies must be developed for these engines to reduce emissions and meet future emissions limits.
Since 1992, Colorado State University (CSU) has been actively engaged in research on large bore natural gas engines used for gas compression on interstate natural gas pipelines. Our focus has been on improving engine efficiency and reducing emissions through combustion improvements and exhaust after-treatment. CSU operates a highly instrumented Cooper–Bessemer GMV-4 large bore, 2-stroke cycle natural gas engine. This engine, in larger cylinder count configurations, is a very commonly used on natural gas pipelines.
It is anticipated that stranded hydrogen
This project focuses on hydrogen–natural gas fuel blending for methane reduction. If successful, there would be two major benefits.
• Reduction in fuel consumption. Methane
• Reduction in greenhouse gas (GHG) emissions. GHG regulations are anticipated in the future, and most operating companies are taking preemptive steps to reduce GHG emissions. Methane reduction from 2-stroke lean-burn (LB) natural gas engines will substantially reduce GHG emissions. Methane constitutes a significant portion of GHG emissions (GHG =
2 Materials and methods
This investigation was performed on a Cooper–Bessemer GMV-4TF natural gas engine. The engine is a slow speed (300 rpm) 2-stroke-cycle engine with a 14 in. (35.6 cm) bore and a 14.375 in. (36.5125 cm) stroke. Two engine fueling configurations were used in the testing: 1) electro-hydraulic high-pressure fuel injection (HPFI), and 2) low-pressure mechanical gas admission valves (MGAV). Each cylinder was fixed with an active pre-combustion chamber (PCC) for the HPFI configuration while the MGAV configuration used a spark plug in place of the PCC. The rated load for each configuration was 440 hp (330 bkW), with a brake mean effective pressure of 67.6 psi (466 kPa). Two
2.1 High-pressure fuel injection engine configuration
The engine was tuned so that brake-specific
2.2 Low-pressure mechanical gas admission valve engine configuration
The MGAV engine configuration utilized simulated piston-scavenged air flow into the MCC. Because engine testing was done in Fort Collins, CO at an elevation of 5,000 ft (1,525 m), both the intake and exhaust pressures were boosted to 1.1 bar (110 kPa) and 1.01 bar (101 kPa), respectively, to create sea-level atmospheric pressure conditions. The inlet air temperature was 107–109°F (41.6–42.7°C). The engine’s fuel injection pressure was set to 2.32 bar (232 kPa). These conditions led to brake-specific
3 HPFI results
3.1 MCC/PCC fuel blending
A
For this round of testing, the boost pressure was left constant at the nominal value of 1.34 bar (134 kPa). Spark timing was held constant, leaving the location of peak pressure (LoPP) uncontrolled. The power and torque outputs were held constant at 440 bhp and 7,700 lb-ft, respectively. Because the boost pressure and power and torque outputs were left constant,
3.1.1 Pressure traces, LoPP, and COVs of peak pressure
For each blend (data point) tested, 1000 individual combustion/scavenging cycles were recorded, and the average of those cycles were compared to a nominal point (solely natural gas) labeled “baseline #.” The results of the sweep can be seen in Figure 2A. Two baseline points were taken during testing: baseline 1 was taken before the
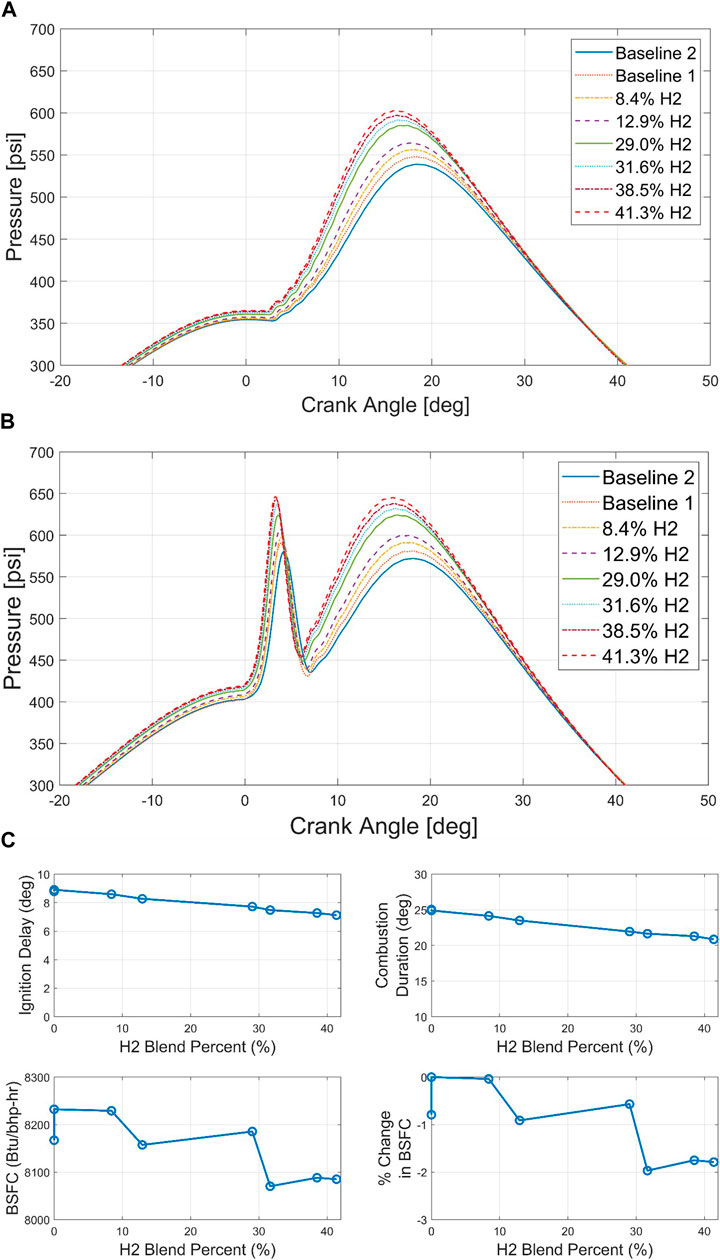
Figure 2. (A) MCC/PCC
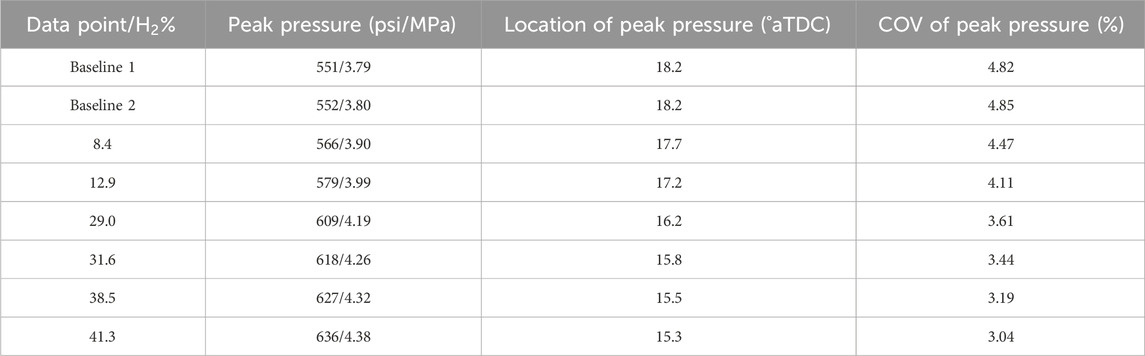
Table 2. MCC/PCC
The same peak pressure and LoPP trends can be seen for the PCC pressure traces in Figure 2B. As the percentage of
3.1.2 Ignition delay, combustion duration, and BSEC
Ignition delay, defined as the time in crank-angle degrees for 0%–10% of the mass of fuel to burn (also known as mass fraction burned—MFB), was 8.79° and 8.90° for baselines 1 and 2, respectively. Table 3 presents values for each
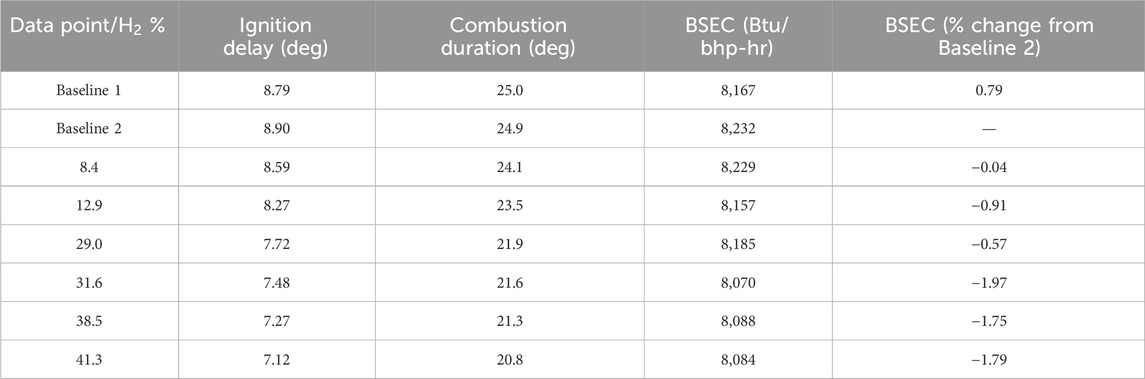
Table 3. MCC/PCC
For combustion duration, defined as the time for 10%–90% fuel MFB, baselines 1 and 2 were at 25.0° and 24.9°, respectively. Again, the shortest duration, 20.8°, came from the highest
3.1.3 Emissions
3.1.3.1 Total hydrocarbons and
Brake-specific total hydrocarbon (THC) emissions for baselines 1 and 2 were 7.26 and 7.52 g/bhp-hr, respectively. Although a decrease in THC emissions was seen for all fuel blends (Figure 3A), a maximum reduction of 28.7% (5.17 g/bhp-hr) in emissions came from the 31.6% fuel blend (Figure 3B). The decrease in emissions was still present but less pronounced at higher hydrogen percent blends. This maximum in percentage reduction (minimum in g/bhp-hr output) indicates that there is an ideal percentage of
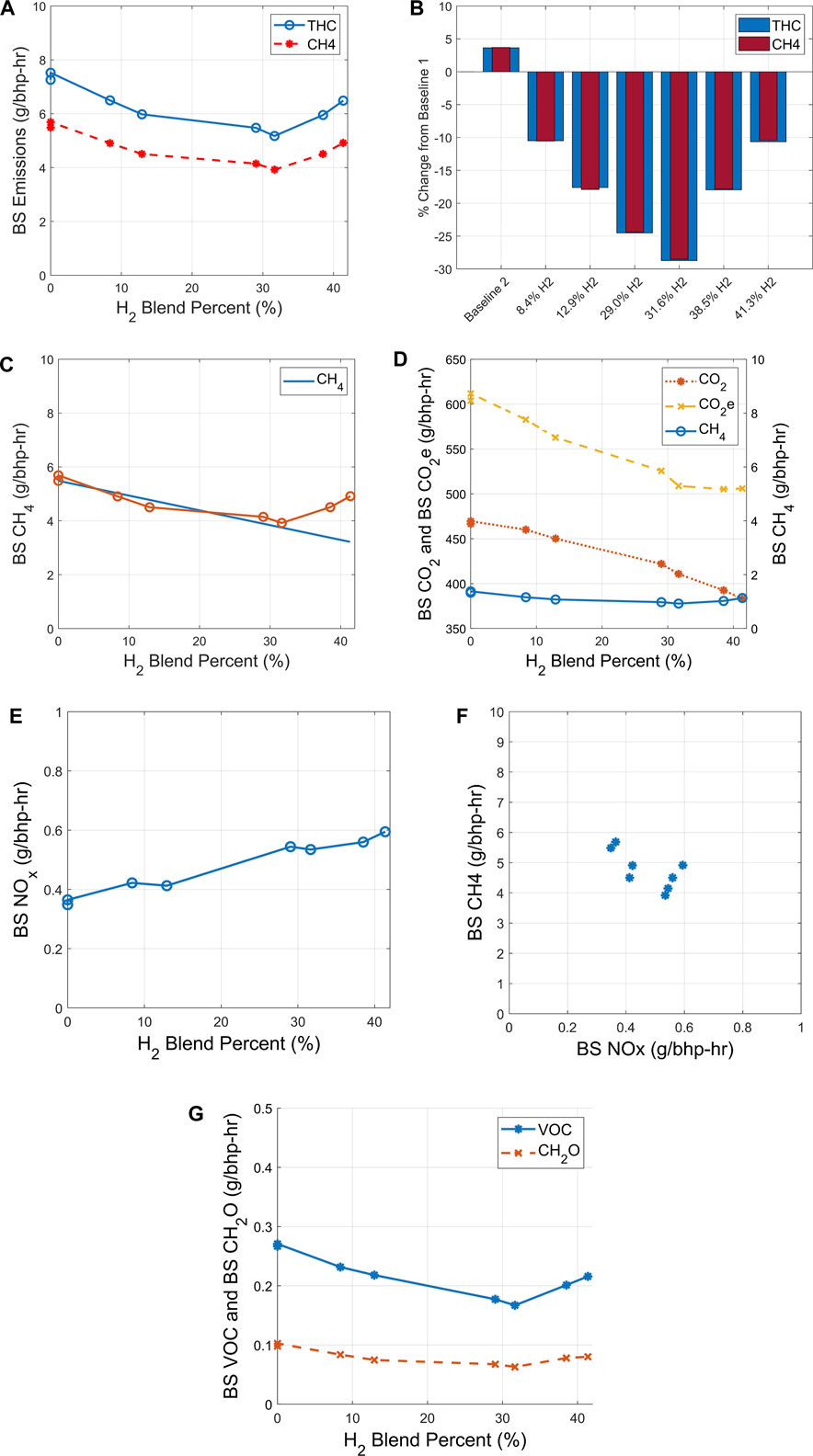
Figure 3. (A) MCC/PCC
Brake-specific methane emissions for each fuel blend, along with the percent change for the brake-specific methane emissions, can also be seen in Figure 3A and Table 3. As
While there was a decrease in methane emissions as the percentage of hydrogen increased, when accounting for the carbon in the natural gas being replaced by hydrogen, the combustion process is less impressive for methane reduction. Figure 3C depicts where the brake-specific methane emissions should be based solely on carbon in the natural gas being re-placed by hydrogen. The reduction seen in the testing follows the reduction based on carbon content very closely, up to and including the 31.6% 2 blend. From this percentage blend onward, the experimental reduction, while less than baselines 1 and 2, is higher than the emissions based on carbon content. This illustrates that while the addition of hydrogen increases flame growth and propagation rates (decreased ignition delay and combustion duration times), it does not improve the combustion efficiency of carbon-based molecules.
3.1.3.2 , , and
Carbon monoxide (CO), carbon dioxide
3.1.3.3
Baselines 1 and 2 produced 0.35 and 0.36 g/bhp-hr of
Figure 3F is a brake-specific
3.1.3.4 VOC’s and
Figure 3G depicts brake-specific VOC emissions as a function of
The brake-specific formaldehyde
3.2 PCC fuel blending
For this portion of the testing, the MCC fuel was set to solely natural gas, while the PCC fuel was blended with
PCC fuel-blending test combustion statistics (pressure traces, LoPPs, COVs of peak pressure, ignition delay, combustion duration, BSEC) and emission results for each
3.2.1 Emissions
3.2.1.1 Total hydrocarbons/
Figure 4A shows the brake-specific THC and
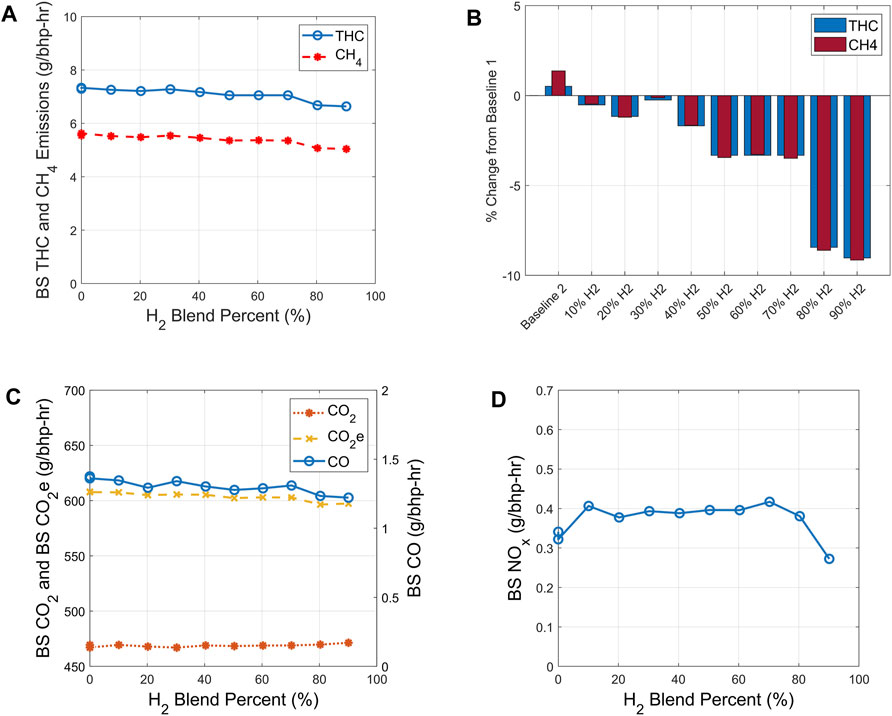
Figure 4. (A) PCC
3.2.1.2 , , and
As expected, due to the slight increased in combustion efficiency, CO and
3.2.1.3
Figure 4D shows brake-specific
3.2.1.4 VOC’s and
Both VOC and
4 MGAV results
4.1 Test plan
The test plan for the MGAV engine arrangement included a natural gas–hydrogen fuel blend sweep for fixed-spark (uncontrolled LoPP) configuration and a load sweep configuration for 0%
4.1.1 Pressure traces, LoPP, and COVs of peak pressure
Figure 5A shows the pressure trace for each
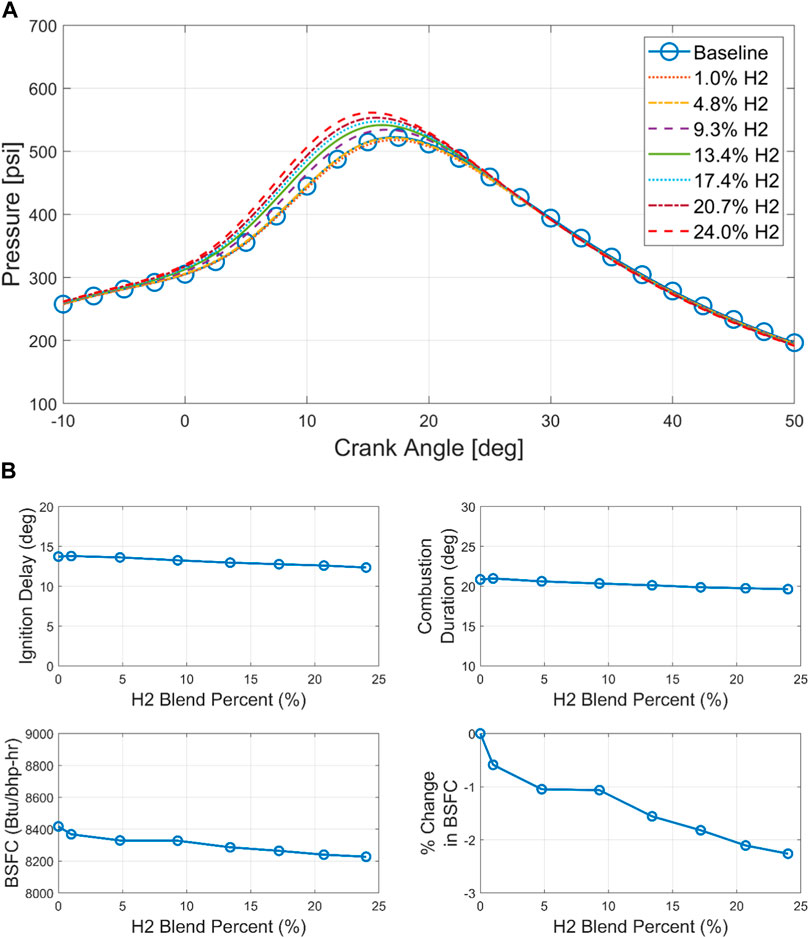
Figure 5. (A) MGAV

Table 4. MGAV
4.1.2 Ignition delay, combustion duration, and BSEC
As expected, ignition delay and combustion duration both decreased as
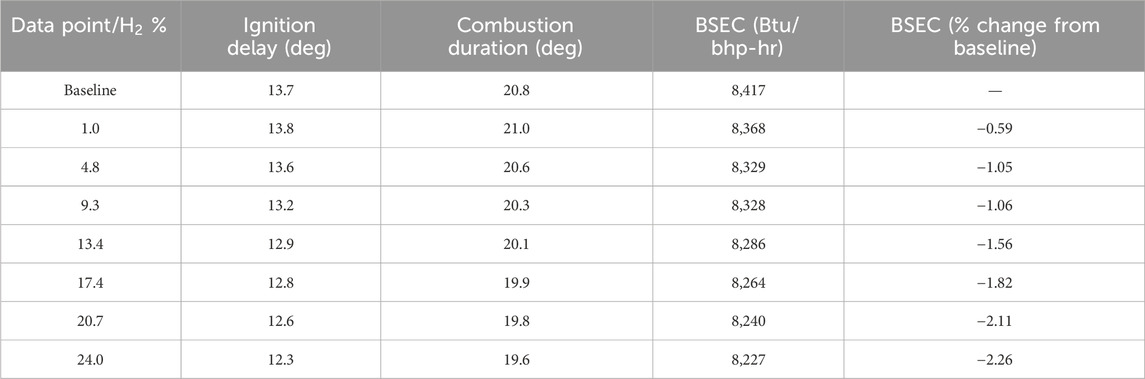
Table 5. MGAV
4.1.3 Emissions
4.1.3.1 Total hydrocarbons/
Figure 6A shows the brake-specific THC and
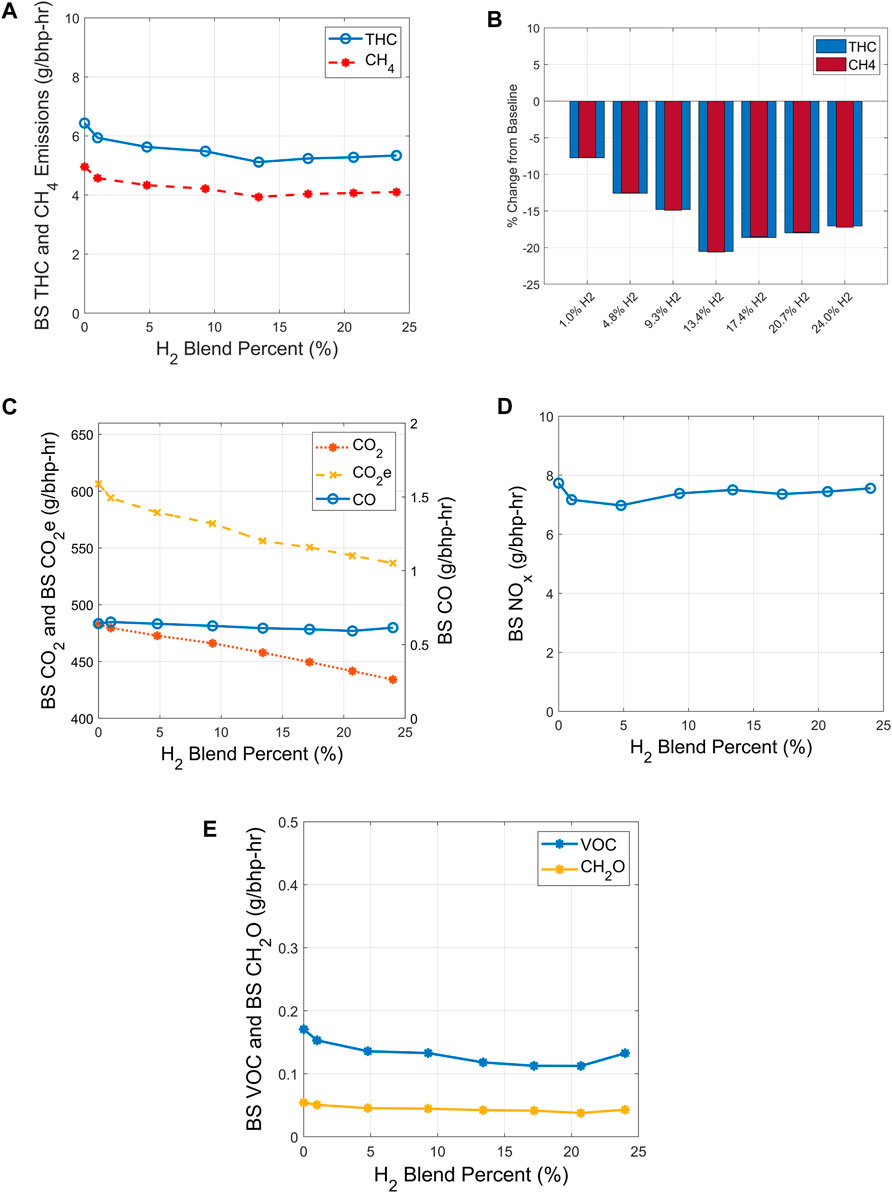
Figure 6. (A) MGAV
4.1.3.2 , , and
Because of the reduction in brake-specific
4.1.3.3
4.1.3.4 VOC’s and
Figure 6E shows the brake-specific VOC emissions versus
Figure 6E shows the brake-specific
5 Conclusion
When natural gas–hydrogen blended fuels were used with HPFI in both the MCC and PCC, coupled with load/power output kept constant, there was an increase in cylinder pressure—the higher the percentage of
Ignition-delay duration times, combustion duration times, and BSEC all saw decreases as the percentage of
THC and
Due to these experimental results, coupled with the previously cited research, it is expected that the addition of hydrogen to a natural gas fuel in large total volume percentages will result in a stronger, faster, and hotter combustion event producing a higher peak cylinder pressure, advanced LoPP, higher
When natural gas–hydrogen blends were used as the PCC fuel and the MCC used just natural gas, there was little change seen in the combustion statistics, even at the higher
The results of this experiment showed that the addition of
When using the blended fuels with the MGAV fueling configuration, the same trends were observed as the HPFI fueling configuration with both MCC and PCC fuels being blended. At 24.0%
The emissions exhibited similar behavior. THC and
The resulting engine emissions from the addition of
These testing results not only show that using
Although, in general, the trends in engine performance and emissions output as a function of
Data availability statement
The datasets presented in this article are not readily available because they are proprietary. Requests to access the datasets should be directed to aW5mb0BwcmNpLm9yZw==.
Author contributions
GV: conceptualization, data curation, formal analysis, investigation, methodology, visualization, writing–original draft, and writing–review and editing. RL: visualization and writing–original draft. MP: writing–review and editing. DO: writing–review and editing and writing–original draft.
Funding
The authors declare that financial support was received for the research, authorship, and/or publication of this article. This research was made possible through funding from the Pipeline Research Council International (PRCI).
Conflict of interest
Author MP was employed by the company Cooper Machinery Service.
The remaining authors declare that the research was conducted in the absence of any commercial or financial relationships that could be construed as a potential conflict of interest.
Publisher’s note
All claims expressed in this article are solely those of the authors and do not necessarily represent those of their affiliated organizations, or those of the publisher, the editors, and the reviewers. Any product that may be evaluated in this article, or claim that may be made by its manufacturer, is not guaranteed or endorsed by the publisher.
Supplementary material
The Supplementary Material for this article can be found online at: https://www.frontiersin.org/articles/10.3389/ffuel.2024.1404367/full#supplementary-material
References
Akansu, S., Kahraman, N., and Ceper, B. (2007). Experimental study on a spark ignition engine fuelled by methane–hydrogen mixtures. Int. J. Hydrogen Energy 32, 4279–4284. doi:10.1016/j.ijhydene.2007.05.034
de Vries, H., Mokhov, A. V., and Levinsky, H. B. (2017). The impact of natural gas/hydrogen mixtures on the performance of end-use equipment: interchangeability analysis for domestic appliances. Appl. Energy 208, 1007–1019. doi:10.1016/j.apenergy.2017.09.049
Du, Y., Yu, X., Wang, J., Wu, H., Dong, W., and Gu, J. (2016). Research on combustion and emission characteristics of a lean burn gasoline engine with hydrogen direct-injection. Int. J. Hydrogen Energy 41, 3240–3248. doi:10.1016/j.ijhydene.2015.12.025
Karim, G., Wierzba, I., and Al-Alousi, Y. (1996). enMethane-hydrogen mixtures as fuels. Int. J. Hydrogen Energy 21, 625–631. doi:10.1016/0360-3199(95)00134-4
Ma, F., and Wang, Y. (2008). Study on the extension of lean operation limit through hydrogen enrichment in a natural gas spark-ignition engine. Int. J. Hydrogen Energy 33, 1416–1424. doi:10.1016/j.ijhydene.2007.12.040
Ma, F., Wang, Y., Haiquan, L., Yong, L., Junjun, W., and Shangfen, D. (2008). enEffects of hydrogen addition on cycle-by-cycle variations in a lean burn natural gas spark-ignition engine. Int. J. Hydrogen Energy 33, 823–831. doi:10.1016/j.ijhydene.2007.10.043
Mariani, A., Prati, M. V., Unich, A., and Morrone, B. (2013). Combustion analysis of a spark ignition i. c. engine fuelled alternatively with natural gas and hydrogen-natural gas blends. Int. J. Hydrogen Energy 38, 1616–1623. doi:10.1016/j.ijhydene.2012.11.051
Pan, J., Lu, Y., Huang, M., Otchere, P., Chen, W., and Fan, B. (2019). Effect of different hydrogen blending ratios on combustion process of gasoline-fueled rotary engine. Environ. Prog. and Sustain. Energy 38, 13200. doi:10.1002/ep.13200
Park, J., Hwang, D. J., Park, J. S., Kim, J. S., Keel, S. I., Cho, H. C., et al. (2007). Hydrogen utilization as a fuel: hydrogen-blending effects in flame structure and NO emission behaviour of CH4–air flame. Int. J. Energy Res. 31, 472–485. doi:10.1002/er.1259
Vieira, G. D., Banji, T., Lorenzen, R., and Olsen, D. B. (2024). Methane abatement from LB NG 2-stroke cycle engines through in-cylinder modifications. Tech. Rep. PR179-21205-R01.
Wang, J., Chen, H., Liu, B., and Huang, Z. (2008). Study of cycle-by-cycle variations of a spark ignition engine fueled with natural gas–hydrogen blends. Int. J. Hydrogen Energy 33, 4876–4883. doi:10.1016/j.ijhydene.2008.06.062
Keywords: hydrogen, natural gas, methane reduction, internal combustion engines, fuel blending, large bore, two-stroke
Citation: Vieira G, Lorenzen R, Patterson M and Olsen D (2024) Methane emission reduction through hydrogen blending in a large bore 2-stroke lean-burn natural gas compressor engine. Front. Fuels. 2:1404367. doi: 10.3389/ffuel.2024.1404367
Received: 20 March 2024; Accepted: 11 November 2024;
Published: 09 December 2024.
Edited by:
Rakesh Kumar Maurya, Indian Institute of Technology Ropar, IndiaReviewed by:
Carlo Beatrice, Institute of Sciences and Technologies for Sustainable Energy and Mobility (CNR-STEMS), ItalyAngelo Onorati, Polytechnic University of Milan, Italy
Copyright © 2024 Vieira, Lorenzen, Patterson and Olsen. This is an open-access article distributed under the terms of the Creative Commons Attribution License (CC BY). The use, distribution or reproduction in other forums is permitted, provided the original author(s) and the copyright owner(s) are credited and that the original publication in this journal is cited, in accordance with accepted academic practice. No use, distribution or reproduction is permitted which does not comply with these terms.
*Correspondence: Greg Vieira, Z3JlZy52aWVpcmFAY29sb3N0YXRlLmVkdQ==