- 1Department of Mechanical Engineering, University of Sheffield, Sheffield, United Kingdom
- 2Energy Institute, University of Sheffield, Sheffield, United Kingdom
- 3Management School, University of Sheffield, Sheffield, United Kingdom
The aviation industry, driven by evolving societal needs, faces rising demand post-Covid and increasing pressure to align with emission reduction targets, prompting the development of drop-in sustainable aviation fuels (SAF). Their compatibility with existing aircraft and infrastructure will help to implement these fuels with the urgency the global climate crisis requires. This review delves into the benefits and challenges of various feedstocks, addressing complexities in estimating feedstock availability by location. Identified research gaps include enhancing feedstock availability, yield, and diversity, investigating compositions, and implementing sustainable agricultural practices. A summary of ASTM-certified conversion processes and technical specifications is outlined, prompting further research into conversion efficiency, catalyst selectivity, blending limits, aromatic compounds, combustion instability, and numerical modeling. A summary of recent life cycle assessments (LCA) highlighted gaps in cradle-to-cradle assessments, location-specific analyses, temporal considerations, and broader environmental impact categories. Recommendations stress obtaining primary data for enhanced LCA accuracy, conducting more specialized and general LCA studies and combining LCA, techno-economic analysis, fuel requirements, and socio-political assessments in multi-criteria decision analysis. This paper underlines the pressing need for comprehensive research to inform SAF production alternatives in the context of global climate crisis mitigation.
1 Introduction
Despite challenges such as periodic disruptions due to global health crises, the demand for air travel continues to rise, increasing post-Covid by 73% from 2021 to 2022 (Statista Res. Dep., 2023). In 2021, our global anthropogenic greenhouse gas (GHG) emissions amounted to 54.59 billion tons CO2eq, an increase of 12.7 times pre-industrial levels (Ritchie et al., 2020), with aviation accounting for around 3.5% of effective anthropogenic radiative forcing (Ritchie, 2024). Many countries and regions have set ambitious targets to reduce carbon emissions and combat climate change. For example, in their 2022 Jet Zero Strategy, the United Kingdom government committed to achieving net zero domestic aviation and zero emission airport operations in England by 2040 and complete net zero air travel by 2050 (Dep. for Transport, 2023). Moreover, the aviation industry’s dependence on conventional fossil fuels poses risks related to energy security and price volatility (Mayer, 2022).
Sustainable aviation fuels (SAF) are designed to reduce the carbon footprint of aviation since they are produced from sustainable feedstocks, such as biomass and waste oils (Teoh et al., 2022). Developing SAF from a variety of feedstocks, including renewable and non-petroleum sources, enhances energy security and resilience by creating a more diverse and sustainable fuel supply chain (Martinez-Valencia et al., 2021). The main benefits of SAF, compared with electric or hydrogen powered aircraft, are their compatibility with existing infrastructure, requiring no modifications to existing aircraft and presenting a near-term solution for reducing aviation emissions (Bauen et al., 2020).
The sustainable production of SAF depends on the availability and diversity of feedstocks. Prominent challenges involve sourcing sufficient feedstocks that do not compete with food crops and ensuring a diverse and sustainable supply chain (O’Malley et al., 2021). Moreover, the overall GHG emissions reduction potential of SAF is subject to the entire lifecycle of the fuel, including feedstock production, processing, and distribution. Therefore, ensuring a net reduction in emissions compared to conventional fuels is crucial (Seber et al., 2022). Furthermore, the cost of producing SAF is often higher than traditional jet fuels, therefore achieving economic viability and cost competitiveness is a significant challenge (Shahriar and Khanal, 2022). Achieving the necessary production volumes of SAF is also a challenge due to the large investment requirements and availability of feedstocks (Dietrich et al., 2024).
The key novelty of this review paper is the in-depth discussion of the potential future direction of SAF research, based on the current research gaps. The majority of previous reviews provide a summary of the technologies under consideration with only a brief discussion of the recent discoveries, research gaps, and recommended directions for future research (Bauen et al., 2020; Cabrera and de Sousa, 2022; Vardon et al., 2022; Peters et al., 2023; Chen et al., 2024). Therefore, this review paper aims to provide a thorough examination of the prominent research gaps and how they can be addressed.
Many reviews of SAF conversion technologies and applications of LCA on SAF discuss a range of feedstocks, although far from comprehensive (Bauen et al., 2020; Cabrera and de Sousa, 2022; Vardon et al., 2022; Peters et al., 2023; Chen et al., 2024). There is a lack of reviews which compare the full range of recognized feedstocks to ascertain the level of development of technical and LCA research into different feedstocks. Therefore, this review aims to account for a wider range of feedstocks for comparison. One of the primary novelties of this review paper lies in the inclusion of an in-depth discussion of the available feedstocks from various categories and the main benefits and challenges of each.
Reviews of SAF conversion technologies predominantly focus on gasification and Fischer-Tropsch synthesis (GFT), hydroprocessed esters and fatty acids (HEFA), hydroprocessed fermented sugars (HFS), and alcohol-to-jet (ATJ) conversion processes (Bauen et al., 2020; Ng et al., 2021; Cabrera and de Sousa, 2022; Afonso et al., 2023; Detsios et al., 2023b; Peters et al., 2023), with some also considering other less developed pathways. There is a lack of reviews which compare all technologically significant SAF production pathways, developed and emerging. Therefore, this review aims to provide an original comparison of the technological significance and development of LCA research across all significant biobased SAF production pathways, giving a comprehensive overview of the current scope of comparative research, as well as highlighting research gaps. Non-biobased SAF feedstocks and production processes fall outside of the scope of this review.
The following sections are outlined as follows. Section 2 reviews the main benefits and challenges of various feedstock groups, some of the prominent research gaps, and addresses the availability of certain feedstock groups by location. Section 3 outlines the certified SAF conversion processes and emerging technologies, as well as their recent technical developments. Section 4 summarizes the technical specifications for SAF and reviews a range of recent developments and research gaps. Section 5 reviews various prominent LCA on SAF conversion processes and some crucial areas for further LCA research. Section 6 suggests areas for future research relating to feedstocks, conversion processes, achieving the technical specifications, LCA, and other comparative assessment methods.
2 Biobased feedstocks
2.1 Categorization
Under the CORSIA framework (Carbon Offsetting and Reduction Scheme for International Aviation), there are five categories of feedstocks for fuel production: primary products, co-products, by-products, residues, and wastes. The feedstocks currently recognized by CORSIA are summarized in Table 1, along with their respective generations, product categories, and main composition.
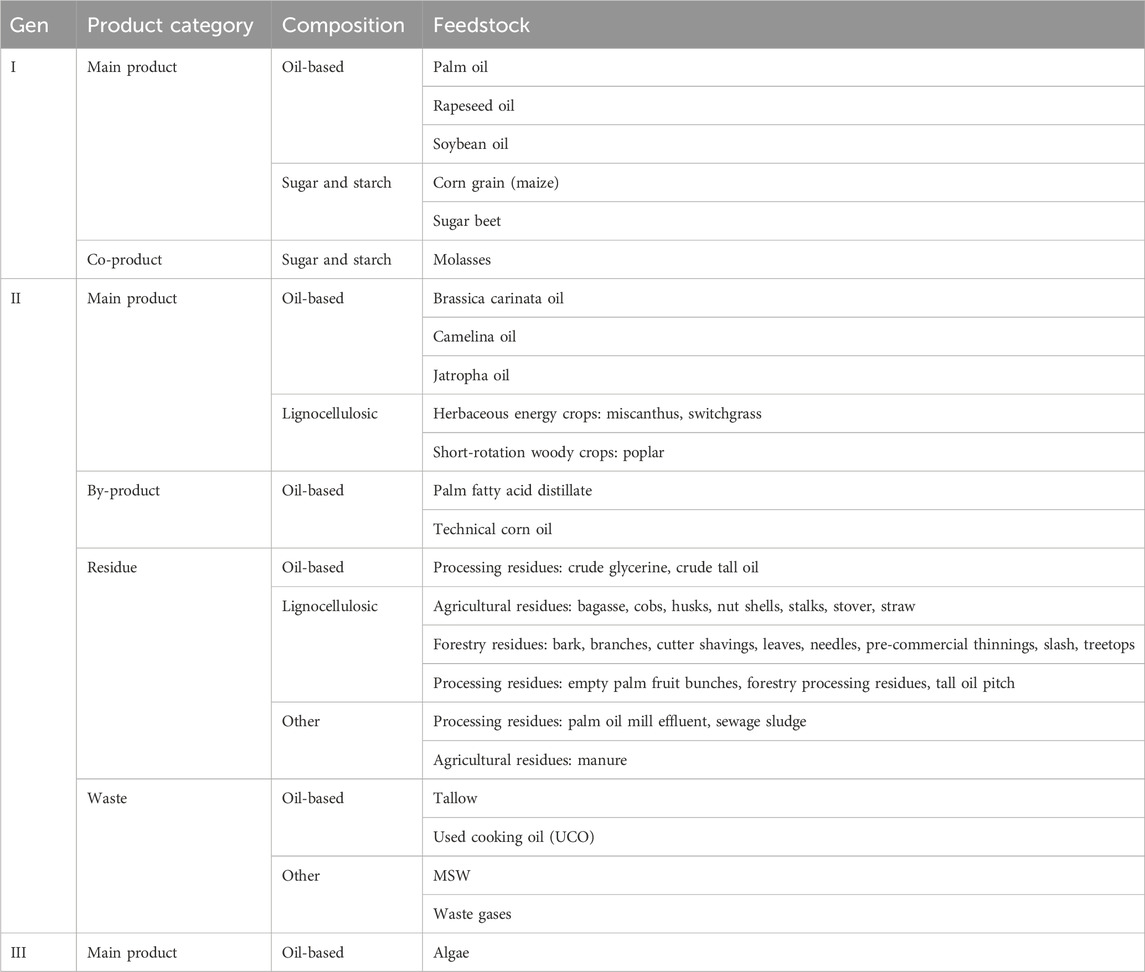
Table 1. Feedstocks currently recognized in the CORSIA framework to produce SAF, with the exception of algae (ICAO, 2021).
2.2 Benefits and challenges
2.2.1 First-generation feedstocks
First-generation feedstocks come from traditional food crops and vegetable oils. Alternative feedstocks not recognized by CORSIA include sugar cane, wheat, and barley. The benefits of using first-generation feedstocks are that the infrastructure for planting, harvesting, and processing is already in place as these crops are already well-established. However, these feedstocks raise significant concerns about competition with food production, land use change, deforestation, use of pesticides, fertilizers, and irrigation, and social issues such as increased food prices (Walls and Rios-Solis, 2020).
2.2.2 Second-generation feedstocks
Second-generation feedstocks are obtained from non-food biomass. These include energy crops grown specifically for energy creation purposes as well as a wide range of wastes. Alternative feedstocks not recognized by CORSIA include hazel (Walls and Rios-Solis, 2020).
Energy crops have a large oil and lipid content per unit mass. Jatropha can be grown in inhospitable places on marginal land. Camelina is fast growing and can be grown in rotation with wheat. However, large investment is required for energy crops and scale-up may not be possible while farmers are hesitant to invest without a well-established industry in place (Ng et al., 2021).
Agricultural residues are not in direct competition with food; however, straw is currently used as animal fodder. They also have the same characteristics across suppliers, are unlikely to be contaminated, and are easier to process than feedstocks such as municipal solid waste (MSW). However, they have a high ash, chlorine, and alkali metal content, as well as being seasonal so requiring more storage space. Moreover, straw is more expensive to transport due to its low volumetric density (E4tech (United Kingdom) Ltd., 2017; Ng et al., 2021).
Forestry residues have less competition with other industries so are widely available for fuel production. However, it may not be economically viable or sustainable to transport them long distances to processing plants. Waste wood from construction is produced consistently and currently has a negative price. However, it may lead to processing issues if low grade wood is used and incur costs to separate wood from other wastes in construction (E4tech (United Kingdom) Ltd., 2017; Ng et al., 2021).
MSW feedstocks come from household waste and can include a wide range of different products such as grass clipping, furniture, food scraps, clothes, newspapers, and packaging. The use of MSW reduces landfill dumping, lowering the emission of CO2, methane, and other gasses from anaerobic decomposition (Kandaramath Hari et al., 2015; Cabrera and de Sousa, 2022). However, it is constituted from highly contaminated materials such as ash, nitrogen, and heavy metals, and has a high moisture content, leading to it requiring more pre-treatment and separation processes. This also leads to a higher formation of coke and tar during the gasification process (Kolosz et al., 2020; Ng et al., 2021).
Used cooking oil is an already commercialized feedstock for fuel production and has a low cost. However, the oil is usually upgraded as part of other technologies, such as biodiesel production, which may decrease its availability in SAF production (Ben Hassen Trabelsi et al., 2018; Ng et al., 2021).
Generating SAF from waste plastic may become another future production pathway as feasibility studies on its use in diesel production have yielded promising efficiency and emissions results (Mariappan et al., 2021; Cabrera and de Sousa, 2022).
The advantage of second-generation feedstocks is that they aim to address concerns associated with first-generation feedstocks by using non-food sources, reducing competition with food production, and utilizing waste or by-products, as well as having low raw material costs. However, there is limited infrastructure to harvest and process these feedstocks as they have so far been considered mainly as waste products and therefore currently have high processing costs (Walls and Rios-Solis, 2020).
2.2.3 Third-generation feedstocks
Third-generation feedstocks are often publicized for their potential high oil yields and the ability to grow in non-arable land, minimizing competition with food crops. In particular, algae can be cultivated in various environments, including ponds, bioreactors, or even wastewater, offering flexibility in production (Walls and Rios-Solis, 2020). Their growth in wastewater can even be used in water treatment plants, further enhancing their environmental and economic advantages (Singh and Olsen, 2011). They also have faster growth rates, as little as 3.5 h to double their mass (Chisti, 2007), and require less land than first or second-generation feedstocks (Cabrera and de Sousa, 2022). The main limitation of third-generation feedstocks is that the technology is predominantly still in the development stage and few large-scale applications have been demonstrated, leading to high cultivation costs. Fourth-generation feedstocks are also being considered. These refer to engineered algal and cyanobacterial biomass which has improved productivity (Walls and Rios-Solis, 2020).
2.3 Further research
Understanding the composition and variability of different feedstocks is essential for consistent and reliable production. Further research is needed to address challenges related to variations in feedstock quality, impurities, and their impact on the production processes.
Further research is needed to improve the yield and productivity of energy crops. This includes optimizing agricultural practices, crop diversification, and genetic modifications to enhance crop performance and oil or starch content. Vogel and Jung investigated the genetic modification of switchgrass and other herbaceous species in order to achieve a higher yield for animal feed and fuel production. They highlighted that further research is required to ascertain the importance of genetically modified crops as stakeholders are unlikely to invest in new technologies unless their importance is proven. Further study of the most important genes for modification is also needed in order to achieve the required quality parameters. Moreover, better testing and characterization methods are required for accurate results (Vogel and Jung, 2001).
Developing and promoting sustainable agricultural practices for energy crop cultivation is vital for sustainable biofuel production. This includes strategies for minimizing environmental impact such as implementing cover crops and no-till practices, reducing water and nutrient use, and avoiding land-use change that could lead to deforestation or biodiversity loss. Das et al. studied the effects of soil microbes on plant productivity and health. Since microbes convert nutrients in the soil into a useable form for plants and help to inhibit pathogens, there is interest in engineering microbial inoculants, biofertilizers, and biopesticides to reduce reliance on chemical soil additives (Das et al., 2022). Further research is required in this area to reach the implementation stage.
2.4 Availability by location
The availability of different feedstocks for SAF production varies by location due to a combination of geographical, climatic, agricultural, and economic factors. Certain biomass feedstocks are better suited to specific climate and soil conditions, as well as having certain water requirements. The existing agricultural and industrial infrastructure provides established markets for certain feedstocks, aided by government subsidies and incentives. Competition for land between food production, energy crops, and other land uses has a large impact on the choice of feedstocks as some regions prioritize food production over other land uses.
O’Malley et al. estimated the amount of EU waste feedstocks available for SAF production once other uses have been accounted for, based on 2030 predictions, as shown in Figure 1. The availability from agricultural residues and cover crops was found to be significantly higher than any other sector. However, the maximum SAF production capacity was higher for waste fats, oils, and greases (FOGs), meaning that these production pathways must have significantly higher conversion efficiencies. The total amount of available feedstocks was estimated to be 124.4 Mt, producing 3.4 Mt of SAF which is equal to 5.5% of the 2030 jet fuel demand (O’Malley et al., 2021). Therefore, further research is required to investigate how the supply of sustainable feedstocks for SAF production can be increased and how to improve the conversion efficiency of production processes in order to increase our total SAF production capacity.
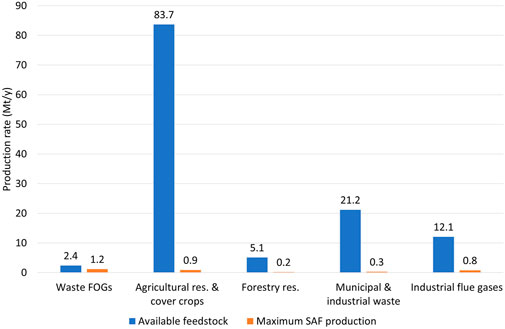
Figure 1. 2030 estimates of availability of EU feedstocks from wastes for SAF production (Mt/y) and maximum potential SAF production (Mt/y) (O’Malley et al., 2021).
The United States Department of Agriculture (USDA) assessed the production quantities of major oilseeds, protein meals, and vegetable oils in the main producing countries, including Brazil, China, United States, Argentina, India, Indonesia, Malaysia, and the EU for the agricultural year 2022–2023 (USDA, 2023). Oilseeds are most commonly produced in Brazil and the United States (see Figure 2A), protein meals are mostly produced in China (see Figure 2B), and vegetable oils are commonly produced in Indonesia (see Figure 2C). Brazil, the United States, China, and Argentina dominate the overall first-generation feedstock production (see Figure 2D), but only a small fraction of these crops can be used for fuel production.
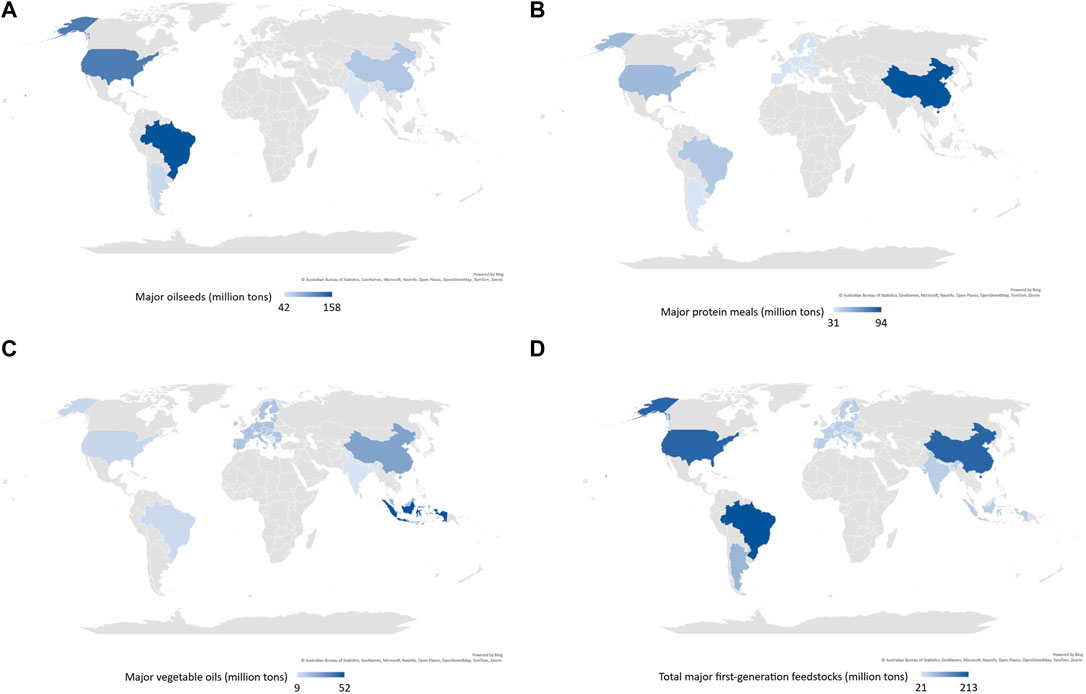
Figure 2. Production quantities of various first-generation feedstocks by the main producing countries around the world, based on data from the 2022/23 agricultural year (USDA, 2023); (A) major oilseeds including copra, cottonseed, palm kernel, peanut, rapeseed, soybean, and sunflower seed, (B) major protein meals including copra, cottonseed, fish, palm kernel, peanut, rapeseed, soybean, and sunflower meal, (C) major vegetable oils including coconut, cottonseed, olive, palm, palm kernel, peanut, rapeseed, soybean, and sunflower seed, (D) total major first-generation feedstocks.
Second-generation feedstocks are derived from a broader range of non-food crops, lignocellulosic materials, and agricultural residues. These sources are more diverse compared to the first-generation feedstocks. The variability in feedstock types and origins makes it challenging to establish uniform measurement and reporting methods of feedstock availabilities. For second and third-generation feedstocks, the lack of widespread commercialization makes it difficult to obtain accurate and comprehensive data on production quantities. Moreover, the economic viability of these feedstocks is still being established. As these technologies evolve and become more economically competitive, the production quantities may change, and more standardized reporting mechanisms may be developed. Additionally, since many feedstocks are used for multiple uses, such as biodiesel production or animal feed, it is difficult to quantify how much of these are available for SAF production. Further research should focus on methods to quantify the availability of various feedstocks depending on their demand from various sectors, climate conditions affecting crop yields, and locational variability.
3 Conversion technology status
3.1 Certified conversion processes
The production technology depends on the chosen feedstock. Production technologies are certified by ASTM International. As of July 2023, there are 11 approved pathways for SAF production, encompassing variations of four key technologies: GFT, HEFA, HFS, ATJ, as shown in Table 2 (Dep. for Transport, 2023; ICAO, 2023). Figure 3 shows the key technologies and their respective feedstocks, as outlined in Table 2, and some prominent emerging technologies. The level of technological maturity of each conversion process is given by a Technology Readiness Level (TRL), with basic ideas defined as one and a proven system in operation defined as 9 (EASA, 2023). The TRL generally varies within each technology, depending on the feedstock used and the producer. Some of the most successful results in conversion technology research are presented in Table 3, showing the feedstocks used, reactor conditions, and the results of the studies.
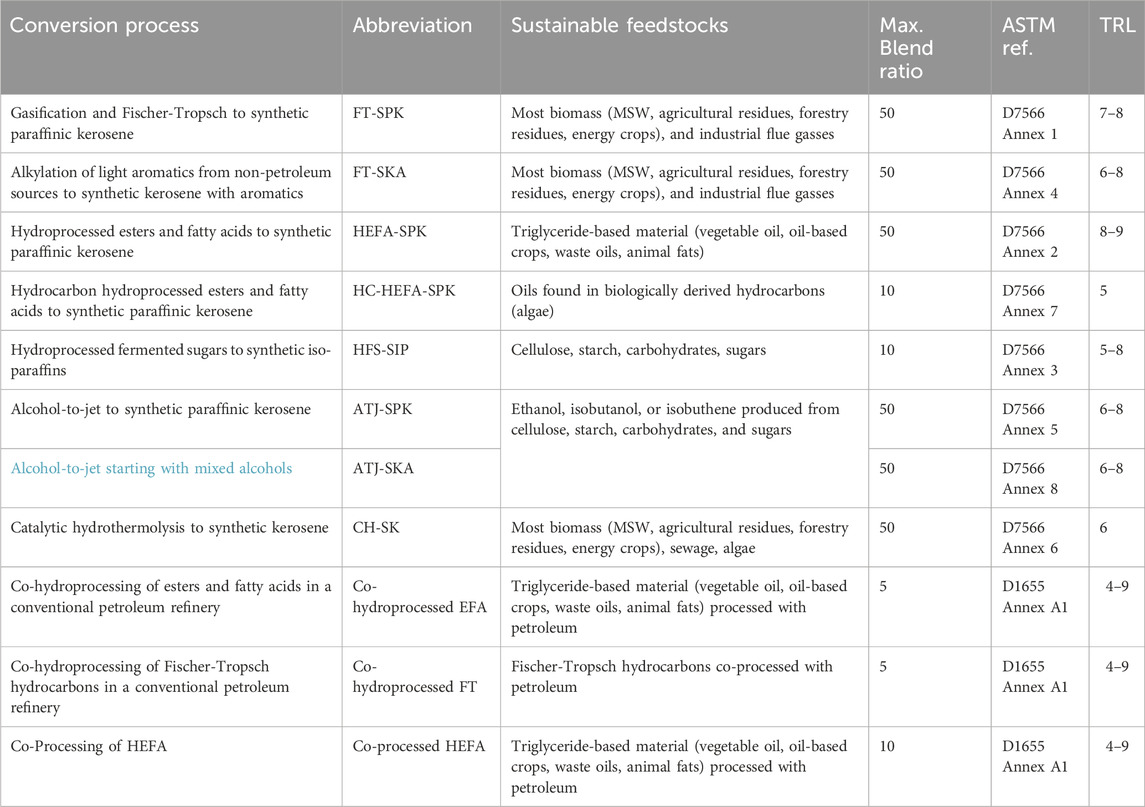
Table 2. Summary of certified SAF production technologies (Detsios et al., 2023b; EASA, 2023; ICAO, 2023; Okolie et al., 2023).
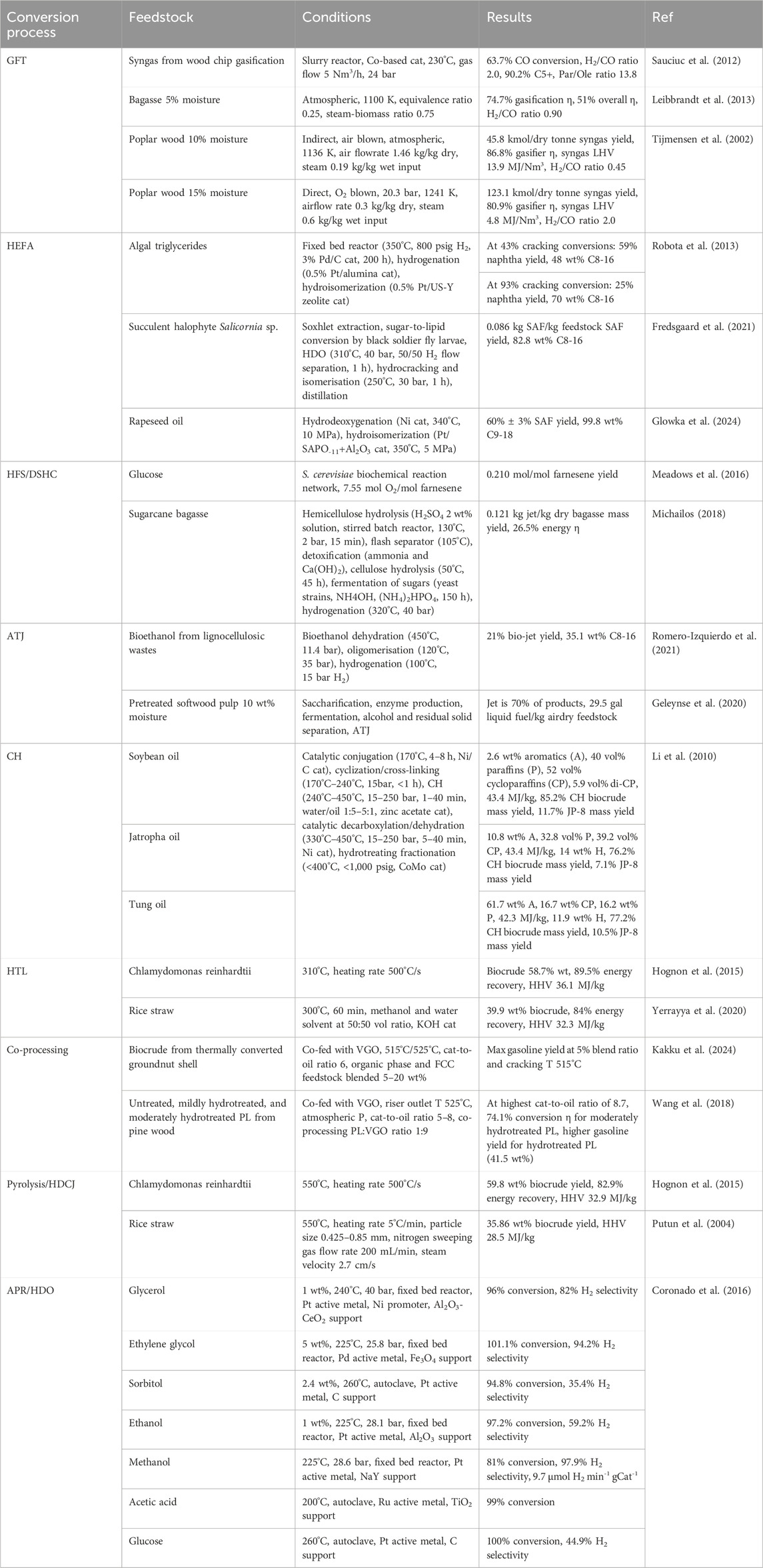
Table 3. Summary of SAF conversion technology developments and their prominent findings; including discussion of vacuum gasoline oil (VGO), fluid catalytic cracking (FCC), pyrolysis liquid (PL), catalysts (cat), and efficiency (𝜂).
3.1.1 Fischer-Tropsch (FT-SPK/SKA)
The FT synthetic paraffinic kerosene (FT-SPK) production process converts any carbon-based feedstock into SAF. Usually, lignocellulosic biomass and MSW are used. The certified process uses gasification as the biomass conversion process, however other methods could be used, such as pyrolysis and liquefaction. First, the feedstock is pretreated by sorting, sizing, and drying. Then, gasification is carried out to convert the biomass into syngas containing mostly CO and H2, at temperatures of 1,000°C–1,600°C (Bauen et al., 2020; Ng et al., 2021; Cabrera and de Sousa, 2022). The syngas produced in the gasification step is often not in the optimal ratio for FT synthesis, so the water-gas shift reaction is used to adjust the ratio of H2 to CO by reacting the gasses with water vapor (Bauen et al., 2020).
To avoid catalyst poisoning, the syngas must be cleaned to remove solids, tars, nitrogen, and sulfur (Boerrigter et al., 2002). This remains a major limitation of this technology and requires more research to achieve the required cleaning standard and to reduce costs (Santos and Alencar, 2020; Ng et al., 2021). These pretreatment processes somewhat reduce the total GHG savings (E4tech (UK) Ltd., 2017).
FT synthesis is a thermochemical reaction with a cobalt or iron catalyst in which the syngas is converted into a liquid and gas mixture (Cabrera and de Sousa, 2022). Research is underway to find a catalyst with a selectivity which is more appropriate for SAF production (Bauen et al., 2020). The CO and H2 molecules are chemically transformed into liquid hydrocarbons through a series of polymerization and chain growth reactions, producing hydrocarbons with a range of chain lengths from light gasses to waxes (Ng et al., 2021). The products are then refined via hydrocracking and isomerization, before being distilled (Cabrera and de Sousa, 2022). Light gasses can be used to generate heat and power or refined into LPG, naphtha and kerosene can be used for gasoline and jet fuel, distillate can be refined into diesel, and waxes can be hydrocracked into diesel (Ng and Sadhukhan, 2011). The fuels are free of sulfur and contain a minimal amount of aromatics, reducing pollution (Tijmensen et al., 2002). Generally, 5–6 tons of biomass feedstock can yield 1 ton of liquid (Ng et al., 2021).
The individual processes have been demonstrated on a commercial scale, however the whole process of FT-SPK production has not. Some of the main limitations of this technology include economic viability, catalyst selectivity, and overall efficiency (IRENA, 2016; Bauen et al., 2020).
The FT synthetic kerosene with aromatics (FT-SKA) production process uses the same FT synthesis process but introduces alkylation of light aromatics such as benzene. This means that the fuel produced has an aromatic content, increasing its compatibility with traditional engines regarding fuel leakages. Due to its aromatic content, FT-SKA has more potential to increase its blending percentage in the future, although currently limited to 50% (Roland Berger, 2020; Cabrera and de Sousa, 2022).
3.1.2 Recent developments
Additive manufacturing allows for the fabrication of highly optimized equipment. Metzger et al. used additive manufacturing to design and investigate FT synthesis, including heating, cooling, and sensing. The reactor showed excellent temperature control and product yield. This was achieved by reducing the diameter of the channels for catalyst and heating and cooling fluids, giving better control of heat release. This led to no hot spot formation or catalyst deactivation (Metzger et al., 2023). Further research in this area includes improving heat and mass transfer, fabrication time, and temperature control during the reduction and removal of used catalysts. The use of additive manufacturing will also help with scale-up of production processes (Metzger et al., 2023).
Yang et al. investigated direct electrochemical FT synthesis under ambient conditions using a copper electrode coated with a p-block element, with the aim of creating milder reaction conditions. It was found that when the Sn or In coating was optimized, a series of C2H6 and C3-7 hydrocarbons were produced via surface chain-growth reactions (Yang et al., 2024). Further research is needed to develop and optimize catalysts for FT synthesis to enhance efficiency, selectivity, and overall performance in converting syngas into liquid hydrocarbons. Catalyst deactivation and regeneration processes are also areas of interest.
Elangovan et al. demonstrated a combination of technologies using anaerobic digester gas to produce liquid hydrocarbons, almost doubling the production output compared to conventional FT synthesis. Solid oxide electrolysis was employed to process the bio-CO2, while a low energy plasma reformer processed the bio-CH4. The resultant syngas was then fed into a FT reactor to produce liquid fuel (Elangovan et al., 2023).
3.1.3 Hydro-processed esters and fatty acids ((HC-)HEFA-SPK)
HEFA synthetic paraffinic kerosene (HEFA-SPK), also known as hydrotreated renewable jet (HRJ), is the most mature pathway certified by ASTM International and is the only alternative fuel in commercial use (Bauen et al., 2020). It was previously known as hydrotreated vegetable oils (HVO), but its name was updated to account for the wider range of feedstocks now available for its production (Cabrera and de Sousa, 2022).
The HEFA production process uses feedstocks from vegetable oils, animal fats, waste cooking oil, pyrolysis oil, and algae oil which undergo hydro-processing. It involves extracting the fatty acids from the biomass, isomerization to rearrange the molecules, and hydrocracking to reduce the carbon chain lengths of the molecules to ensure the fuel meets the specifications (Ng et al., 2021).
First, the oil is extracted from the biomass by crushing or solvent extraction. Then, catalytic hydrogenation takes place to remove the double bonds from the unsaturated fatty acids (glycerides) in the oil, producing triglycerides. The catalysts require precious metals such as nickel, palladium, or platinum, at temperatures ranging from 80°C to 220°C and pressures from 0.7 bar to 4 bar (Ng et al., 2021). Next, thermal hydrolysis is used to break down the triglyceride into glycerol and free fatty acids (Alenezi et al., 2010). Hydrogen is added to convert the glycerol into propane, making it more stable (Bauen et al., 2020).
Hydrodeoxygenation (HDO) or decarboxylation (DCO) is used to remove the oxygen in the fatty acids, producing straight chain paraffins such as octadecane (C18H38) and heptadecane (C17H36), respectively. HDO requires a large amount of high-pressure hydrogen and temperatures of 300°C–600°C with a catalyst such as sulfide NiMo and CoMo supported on alumina, generating water as a by-product (Huber et al., 2006). In DCO, CO2 is generated but lower pressures are required and therefore less hydrogen (Ng et al., 2021).
Hydroisomerization converts the straight chain paraffins into branched chain paraffins, ensuring that the products meet the specifications for flash point, freeze point, and cloud point. Hydrocracking is carried out to crack and saturate the hydrocarbons to form synthetic kerosene with carbon chain length from C9 to C15 (Wang, 2016). Finally, the products are distilled and separated.
Around 1.2 tons of oil are needed to produce 1 ton of fuel (Ng et al., 2021). The energy conversion efficiency of oils and fats into HEFA-SPK stands at around 76%, making it the most efficient SAF production route (Bauen et al., 2020). Moreover, these fuels have shown reduced NOx emissions due to their lower combustion temperatures (Roland Berger, 2020). This production pathway is currently the most economically viable as the production process can be integrated into a traditional oil refinery with minor additions (Cabrera and de Sousa, 2022).
One of the main limitations of this SAF production pathway is the feedstock availability. Used cooking oil and tallow are limited resources, and land use and sustainability concerns restrict the use of virgin vegetable oil. Exploration of alternative crops, including camelina and brassica carinata is underway (Bauen et al., 2020).
The hydrocarbon HEFA synthetic paraffinic kerosene (HC-HEFA-SPK) production process is very similar to the HEFA process, except that it describes the hydroprocessing of bio-derived hydrocarbons obtained from oils found in a specific alga, Botryococcus braunii (Green Car Congress, 2020).
3.1.4 Recent developments
With a TRL of 8-9, HEFA is shown to be the most developed SAF production pathway. Tanzil et al. compared the minimum fuel selling price (MFSP) and fuel yield of HEFA with five other production pathways based on lignocellulosic feedstocks. It was found that HEFA achieved the best economic performance due to its high fuel yield. Lignocellulosic feedstocks led to a lower fuel yield, and therefore higher cost, due to their higher oxygen content. New techniques are required to remove oxygen from the biomass feedstock in the form of H2O rather than CO2 or CO which decreases the carbon conversion efficiency into SAF. Further research is required to maximize the carbon conversion efficiencies of production pathways since only technologies that fully exploit the carbon contained in the feedstock are likely to be economically competitive with fossil-based fuels (Tanzil et al., 2021a).
Glowka et al. demonstrated the use of a novel, highly selective, Pt/(SAPO-11+Al2O3) hydroisomerization catalyst on the conversion of rapeseed oil via the HEFA process, achieving an average yield of the SAF fraction of 60%. The properties of a 50% blend of this SAF with Jet A-1 was compared to 100% Jet A-1, revealing that the bio-blend had a preferable crystallization temperature, 50% lower aromatic content, and higher calorific value which subsequently led to a reduction in fuel consumption and slightly lower CO2 and NOx emissions. Further research is required to apply the use of this novel catalyst to other feedstocks in the HEFA process (Glowka et al., 2024).
3.1.5 Hydroprocessed fermented sugars (HFS-SIP)
The HFS synthetic iso-paraffins (HFS-SIP) production process is a biological conversion process also known as direct sugars to hydrocarbons (DSHC) or advanced fermentation. First, the biomass feedstock is pretreated to separate the sugars from the lignin. Then, the sugars are converted into farnesene (C15H24) via enzymatic hydrolysis and fermentation (Ng et al., 2021) by which genetically modified yeasts consume the sugars and excrete long-chain liquid alkenes (Bauen et al., 2020). Using the S. cerevisiae strain, the farnesene yield can reach 16.8% at a rate of 16.9 g/ltr/d (Ng et al., 2021). Aerobic fermentation can be done using air at atmospheric pressure, assisted by heterotrophic algae, yeast, or bacteria (Davis et al., 2013). The solids and liquids are separated and the farnesene is recovered (Ng et al., 2021). Then, hydroprocessing is carried out to convert the farnesene into its alkane, farnesane. This is distilled to obtain aviation fuel. Currently, the primary feedstock for this production pathway is sugarcane, but other sugar-based feedstocks can be used. The main limitation of this technology is its high operational costs (Cabrera and de Sousa, 2022; Goh et al., 2022).
Alternative uncertified methods using genetically modified microorganisms to transform sugars into lipids or hydrocarbons are in development. These include heterotrophic algae or yeast which convert sugars to lipids within their cells (Bauen et al., 2020). These can be extracted by rupturing the cells with solvents, before being cleaned and upgraded. This process also co-produces a protein animal feed (E4tech (UK) Ltd., 2017). Alternatively, bacteria which consume sugars and excrete short-chain gaseous alkenes like isobutene are being developed (Bauen et al., 2020). These can then be oligomerized and hydrotreated.
3.1.6 Recent developments
Detsios et al. investigated a combination of anaerobic and aerobic fermentation processes of crushed bark to produce biofuels. Initially, an anaerobic syngas fermentation step took place to produce acetate, followed by aerobic fermentation of acetate into triglycerides, then purification and hydrotreatment to produce biofuels. The bacteria demonstrated tolerance towards syngas contaminants which minimized the gas cleaning requirements. The low pressure and temperature requirements further reduced costs and energy consumption. Moreover, the anaerobic fermentation step had limited by-products, reducing the probability of catalyst deactivation. Carbon utilization and energetic fuel efficiency were measured, achieving comparative values with other technologies using similar feedstocks. Further research should focus on techno-economic analysis and LCA of multiple technologies for comparison (Detsios et al., 2023a).
Few recent studies could be found concerning technological developments in the HFS-SIP conversion process. Meadows et al. investigated the S. cerevisiae yeast strain with the aim of adapting its chemically inefficient biosynthesis pathways to promote higher yield of farnesene. The production scale of farnesene is limited by the yield and productivity of the conversion process so various metabolic reactions were used to rewire the core conversion reaction. This resulted in reduced CO2 emissions from the yeast and improved redox reactions. Using the same quantity of sugar feedstock, the modified yeasts produced 25% more farnesene and required 75% less oxygen. This demonstrated that modifying the yeast metabolism is an effective way to achieve large-scale farnesene production with lower feedstock costs, CO2 emissions, and O2 consumption (Meadows et al., 2016).
3.1.7 Alcohol-to-jet (ATJ-SPK/SKA)
The ATJ synthetic paraffinic kerosene (ATJ-SPK) and ATJ synthetic kerosene with aromatics (ATJ-SKA) production pathways turn alcohol into SAF. The ATJ-SKA production process creates a fuel containing aromatics which can potentially be substituted 100% for traditional fuels. Different alcohols can be used (e.g., ethanol, methanol, isobutanol), providing flexibility in the production process as a range of feedstocks can be used, such as sugar and starch crops, lignocellulosic biomass, and wastes. Moreover, alcohol can easily be transported and stored, meaning that the alcohol production plant does not have to be collocated with the SAF production plant. The main limitation of this production method is its selectivity (Bauen et al., 2020).
Alcohol can be produced via biochemical conversion processes such as fermentation of sugary or starchy crops or through thermochemical methods such as gasification or pyrolysis of lignocellulosic feedstocks. Microbial synthesis has also been explored as an alcohol production method (Lan and Liao, 2013).
The two main pathways for ATJ production are methanol-to-olefins (MTO) followed by the Mobil olefin-to-gasoline/distillate (MOGD) or alcohol processing through dehydration, oligomerization, and hydrogenation (Ng et al., 2021).
In the methanol feedstock route, a fluidized bed reactor at 482°C and 1 bar is used to generate methane, C2-C4 paraffins, C2-C4 olefins, and C5-C11 gasoline. An olefin fractionation unit is used to obtain light gasses, gasoline, and olefins. Gasoline is then separated as the main product while the light gasses are recycled in the MTO unit to increase the yield. Olefins are then sent to a fixed bed reactor at 400°C and 1 bar to produce light gasses, gasoline, and distillate. The fractionation unit allows the separation of C11-C13 kerosene (Baliban et al., 2013).
In the alternative alcohol processing route, alcohols are dehydrated to form alkenes at 288°C–343°C, pressure no more than 14 bar, and acidic catalysts. Then the alkenes are combined into long-chain hydrocarbons via oligomerization at 100°C using a Nafion or Amberlyst catalyst. Some of these molecules are recycled to generate a higher yield of C12-C16 olefins. Finally, the olefins are saturated via hydrogenation using hydrogen and a PtO2 catalyst, producing kerosene, and the products are distilled (Harvey and Quintana, 2010; Ng et al., 2021).
3.1.8 Recent developments
Geleynse et al. investigated the integration of the ATJ process into a conventional kraft pulp mill. The established feedstock handling processes and supply chain infrastructure provided economic benefits. A relative reduction in energy use compared to pulp production was achieved due to the integration of the energy recovery system of the pulp mill with the biomass treatment systems (Geleynse et al., 2020).
Romero-Izquierdo et al. modeled and simulated the ATJ process using bioethanol from lignocellulosic wastes, based on a conventional case and an intensified case. The aim of the intensified case was to reduce costs and environmental impacts by intensifying the process and integrating energy recovery. In the intensified case, the energy consumption was reduced by 5.31%, reducing the total annual cost by 4.83% and the CO2 emissions by 4.99% (Romero-Izquierdo et al., 2021).
3.1.9 Catalytic hydrothermolysis (CH-SK)
Catalytic hydrothermolysis synthetic kerosene (CH-SK) is also known as catalytic hydrothermolysis jet fuel (CHJ). It is a very similar process to hydrothermal liquefaction (HTL) but with the addition of a catalyst to increase the yield (Bauen et al., 2020).
In HTL, water is heated at high pressures to near and supercritical temperatures which allows it to act as a catalyst and depolymerize the biomass feedstock, producing bio-crude oil. Then, the oil is hydrotreated to saturate residual olefins and remove oxygenates. The oil has a higher molecular weight distribution than pyrolysis oil, making it more appropriate for diesel production. However, hydrocracking can be done to produce SAF which has been demonstrated at laboratory-scale (Bauen et al., 2020; Cabrera and de Sousa, 2022). Conversely, in CH-SK, a catalyst is incorporated to modify the reaction pathways and improve the efficiency and yield (Cabrera and de Sousa, 2022).
Catalytic hydrothermolysis (CH) and HTL can take wet feedstocks such as sewage, manure, and algae, as well as lignocellulosic biomass. The oils produced have a lower water and oxygen content, higher calorific value, and better stability in comparison with pyrolysis oils and therefore will require less upgrading and be cheaper to transport. The main limitation of this technology is the high pressures and corrosive conditions in operation (Bauen et al., 2020).
3.1.10 Recent developments
Harisanka and Vinu demonstrated that extensive research has been conducted into the possible feedstocks, optimal operating conditions, and product compositions for HTL (Harisanka and Vinu, 2023). HTL is a popular conversion process for converting MSW as it has shown to be successful in dealing with a wide range of feedstock compositions. Hydrogen donor solvents such as methanol, ethanol, tetralin, and glycerol are under investigation due to their ability to facilitate hydrogen donation to the fuel products, increasing their HHV, without the need for a high-pressure hydrogen stream (Mahesh et al., 2021; Harisanka and Vinu, 2023). HTL using a range of biogenic and non-biogenic wastes has provided a wide range of yields from 15–80 wt% and product HHV of around 30–40 MJ/kg (Harisanka and Vinu, 2023).
Wang et al. simulated CH of corn stalks to optimize the process for SAF production. The conventional process involved the direct combustion of the lignin by-product. Two alternative uses of lignin were proposed; including gasification to obtain hydrogen and depolymerization in ethanol to obtain hydrocarbon fuel. Although the alternative use of lignin increased the complexity of the process, production costs were reduced by gasification while carbon dioxide emission were reduced by depolymerization (Wang et al., 2023).
Cronin et al. conducted tier α and β testing on samples of wet-waste HTL biocrude to predict required properties for certification. A range of feedstocks were used such as food waste, sewage sludge, and fats, oils, and greases (FOGs). Undistilled and distilled fuel samples were analyzed. The upgraded fuels showed physical and chemical properties which fell within the required range for certification (Cronin et al., 2022). The main limitation to SAF produced via HTL is the high nitrogen content of 9,600–13,400 ppm compared to <10 ppm for Jet A, increasing the NOx emissions during combustion. Therefore, further research should focus on hydrodenitrogenation of the product to reduce the nitrogen content (Cronin et al., 2022).
3.1.11 Co-processing
In the co-processing production pathway, biocrude oil is blended with crude oil in a petroleum refinery at up to 5% concentration. One of the main advantages of this is that the infrastructure for manufacturing is already in place, reducing capital investment and resource usage. Moreover, the high capacities of oil refineries allow for a higher product output. However, the sustainability of this pathway is questionable as 95% of the fuel produced still originates from crude oil (Tanzil et al., 2021b; Cabrera and de Sousa, 2022).
3.1.12 Recent developments
Tanzil et al. investigated co-processing of Virent’s BioForming (an example of aqueous phase reforming), ATJ, HFS, fast pyrolysis, GFT, and integrated carbonization GFT (ICGFT). Sharing infrastructures contributed to a 3%–14% reduction in MFSP. Co-processing of intermediate products reduced the MFSP by 10%–19%. Repurposing idle or shutdown petroleum refineries reduced the MFSP by 16%–34%. ICGFT was found to be the best form of co-processing in terms of maximum fuel yield (Tanzil et al., 2021b).
Kakku et al. investigated co-processing of bio-oil generated from thermal conversion of groundnut shells. The organic phase and fluid catalytic cracking (FCC) feedstock weight ratios were varied from 5%–20%, demonstrating minimal changes in dry gas, light cycle oil, and heavy cycle oil yields and a significant increase in LPG and gasoline yields, with bottoms being reduced (Kakku et al., 2024).
Biomass conversion typically produces heavier bio-oils compared to the fossil-based oils fed into the FCC in a petroleum refinery. Therefore, catalysts are expected to degrade faster due to heavy metal depositions (Han et al., 2021). Gerards et al. investigated the use of Ni and V impregnated zeolite catalysts for co-processing of bio-oil in order to reduce catalyst poisoning. The heavy metal additions on the catalyst proved to increase the lifetime of the catalyst and reduce coke formation (Gerards et al., 2020).
3.2 Emerging technologies
There are a number of emerging technologies for SAF production still under research and development, including pyrolysis and upgrading, aqueous phase reforming, and aerobic fermentation.
3.2.1 Pyrolysis and upgrading
Pyrolysis and upgrading, also known as pyrolysis-to-jet or hydrotreated depolymerized cellulosic jet (HDCJ), is a thermochemical conversion process which can be used to transform lignocellulosic biomass and solid waste into bio-crude oil which can be upgraded to SAF. A range of feedstocks can be used, including low quality and wet feedstocks, although the ideal feedstock is dry lignocellulosic biomass (Bauen et al., 2020; E4tech (UK) Ltd., 2017).
Pyrolysis is a process in which dry biomass undergoes controlled thermal decomposition at a moderate temperature, in the absence of oxygen, producing bio-oil, gas, and char (Wang et al., 2015; Ng et al., 2021). The addition of a catalyst increases the production of liquid oil, while the gas product can be used to heat the system. The oil is then upgraded either by blending with fossil vacuum gas oil at 10%–20% in a refinery fluid catalytic cracker or by subjecting it to hydro-deoxygenation where hydrogen is added at high pressure to remove oxygen. These processes produce a mixture of light, medium, and heavy products which are distilled and separated into diesel, jet fuel, and gasoline (E4tech (UK) Ltd., 2017).
The main limitations of this technology are the oil’s high water and oxygen contents, high acidity, high viscosity, and chemical instability (IRENA, 2016). Therefore, transportation of this oil may require specialist infrastructure as it is difficult to store and handle. Pyrolysis oil is already being used for heating but its use as a SAF is only at demonstration stage (Bauen et al., 2020; E4tech (UK) Ltd., 2017). Research into materials and catalysts for upgrading the fuel is ongoing (Shell, 2024).
3.2.2 Recent developments
De Sousa et al. analyzed liquid bio-hydrocarbons obtained from vegetable oils using a NbOPO4 catalyst in the pyrolysis process, producing bio-gasoline, SAF, and biodiesel. The fuels were characterized via infrared and mass spectroscopy and gas chromatography. They demonstrated that an 83% conversion rate to SAF was possible. The SAF produced showed a freezing point which adhered to the required standard (de Sousa et al., 2024).
Suriapparao et al. investigated microwave co-pyrolysis of rice straw and sugarcane bagasse with polypropylene and polystyrene, followed by catalytic upgradation using a HZSM-5 catalyst. Yield, composition, and fuel properties from individual feedstocks and equal composition mixtures before and after catalytic upgradation were evaluated. The bio-oil yield from polypropylene (82 wt%) and polystyrene (98 wt%) were high compared to rice straw (26 wt%) and bagasse (29 wt%). After catalytic upgradation, higher selectivity to unsaturated aliphatics and aromatics was demonstrated. The properties of upgraded bio-oil from biomass-polypropylene mixtures were similar to light fuel oil with a high calorific value, low viscosity, optimum density, and high flash point, as well as a low oxygen content (<5%) compared to upgraded (14%–18%) or non-upgraded (20%–24%) bio-oil from a single feedstock (Suriapparao et al., 2020).
Rjeily et al. analyzed the effects of temperature and steam-to-carbon ratio on the products from pyrolysis-catalytic reforming of biomass into syngas. Hydrogen yield was increased by increasing the temperature and steam-to-carbon ratio. Complete conversion of pinewood was achieved at 600°C with a steam-to-carbon ratio of four using a nickel catalyst. Pyrolysis bio-oil underwent steam reforming at 700°C and a steam-to-carbon ratio of 15 with a nickel catalyst supported by lanthana-alumina, resulting in yields of 95% and 93% for hydrogen and carbon monoxide respectively (Rjeily et al., 2021).
Since pyrolysis oil is generally corrosive, immiscible with hydrocarbons, and only partly volatile, it is usually unsuitable for co-processing in a petroleum refinery or for use as a fuel. French et al. investigated mild hydroprocessing, leaving 7 wt% oxygen, to reduce hydrotreatment costs and make the fuel’s properties more suitable for co-processing. The mildly hydrotreated pyrolysis oil was generated in a semibatch laboratory reactor at 360°C, 2,500 psig hydrogen, with a hydrogen flow of 0.22 sl/g-oil/h and 10 wt% nickel-molybdenum/Al2O3 catalyst. The oil showed low acidity, good miscibility with hydrocarbons, and high volatility (French et al., 2010).
3.2.3 Aqueous phase reforming (APR)
Aqueous phase reforming (APR), also known as hydro-deoxygenated synthetic kerosene (HDO-SK), catalytically converts an aqueous solution of oxygenates (sugars, sugar alcohols, and polyols) into hydrogen, CO2, alkanes, acids, ketones, and aromatics in a high-temperature reforming process. Sugars are converted into hydrocarbons via biochemical conversion (Davis et al., 2015). The carbon chains are then lengthened via condensation reactions, before undergoing hydroprocessing, isomerization, and distillation (Bauen et al., 2020; E4tech (UK) Ltd., 2017; Ng et al., 2021). This process can use wet biomass as a feedstock, removing dewatering costs. It can also be used to produce biochemicals, leading to higher value products and more investment. The main limitations of this technology are its low selectivity and deactivation, caused by coking reducing the catalyst lifetime (Bauen et al., 2020).
3.2.4 Recent developments
Kalekar and Vaidya investigated APR of microalgae and sewage sludge using Pt/Al2O3 and Pt/Al2O3-CeO2 catalysts, producing H2, CH4, CO2, and CO. The optimal reaction conditions were identified by varying process parameters such as reforming temperature, batch time, and catalyst loading. The Pt/Al2O3 catalyst resulted in higher H2 yields for reforming of glycerol and glucose, and a lower conversion for alanine. The highest H2 yield was produced via glycerol conversion using the Pt/Al2O3 catalyst. Humic acid in sewage sludge showed the lowest conversion to H2 (Kalekar and Vaidya, 2022). Further research includes investigating other catalysts and their respective process variables to increase the H2 yield further.
4 Technical specifications
4.1 International standards
The international standards for aviation fuel specifications are particularly stringent. The most commonly used fuels in commercial aviation are Jet A and Jet A-1, while JP-8 is used in military aviation and Jet B is much less common (Ng et al., 2021). Alternative fuels must meet the requirements set out in the ASTM D7566 standards while being blended at a minimum of 50% by volume with conventional jet fuel (ICAO, 2023). Establishing consistent criteria for the certification of various SAF pathways is crucial for industry-wide adoption and acceptance by aviation authorities. Table 4 summarizes the technical specifications of Jet A, Jet A-1, JP-8, and Jet B.
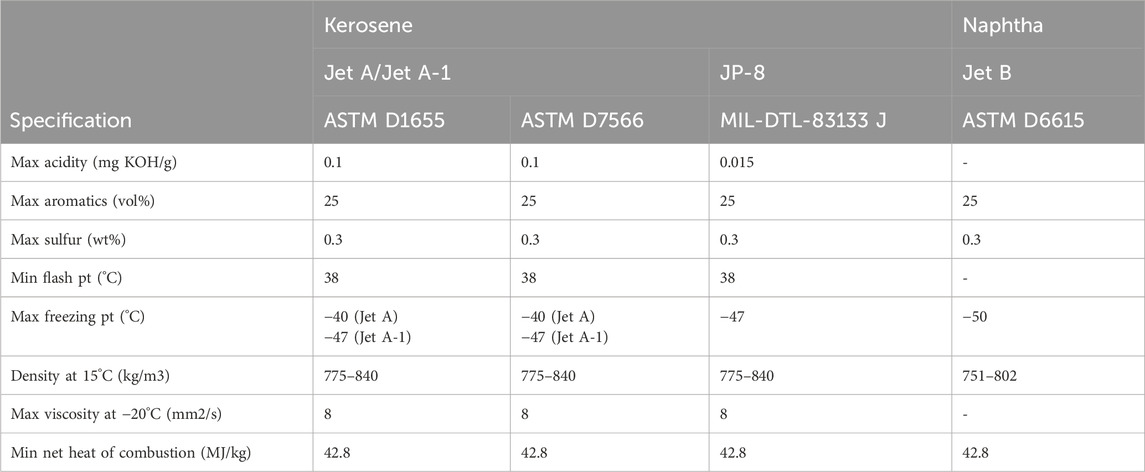
Table 4. Summary of conventional jet fuels and their specifications (Ng et al., 2021).
4.2 Testing
Understanding and controlling the composition and properties of bio-jet fuel is essential for meeting aviation fuel standards. Lab, component, engine, and flight tests are done to ensure the fuel meets the technical and safety requirements. In the lab, SAF are developed that have similar properties to conventional aviation fuels. The fuel serves multiple functions within both the aircraft and engine, functioning as a lubricant, cooling fluid, hydraulic fluid, and used for combustion. Ground tests assess performance across various power settings, comparing it to conventional fuel. They measure engine start time, ignition stability, and fuel behavior during acceleration and deceleration. Material compatibility checks ensure there are no adverse effects on aircraft components. Additional tests focus on fuel control, pumping, and gauging. Emission testing compares exhaust emissions between SAF and conventional jet fuel. In-the-air tests include endurance testing and standard tests to simulate unusual flight conditions (The Bus. Av. Coal., 2020). Table 5 presents typical engine tests using SAF or SAF blends, showing the testing organization, test conditions, and results. In general, SAF blends have been shown to present no adverse effects on engine performance and better emission results than fossil-based jet fuel.
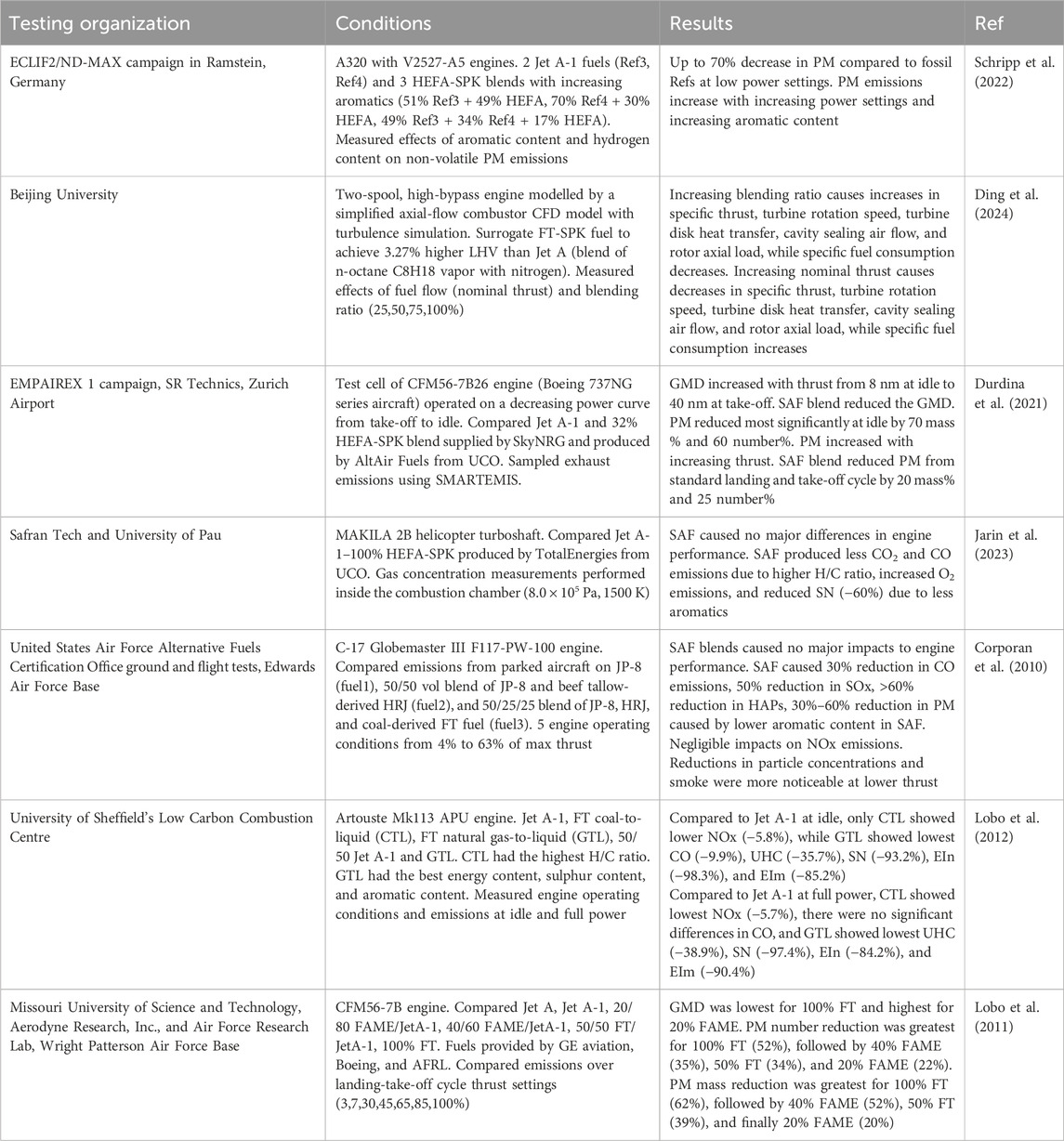
Table 5. Examples of engine tests carried out using SAF or SAF blends, including discussion of particulate matter (PM), lower heating value (LHV), geometric mean diameter (GMD), hazardous air pollutants (HAPs), unburnt hydrocarbons (UHC), PM number (EIn), PM mass-based emissions indices (EIm), and smoke number (SN).
4.3 Recent developments
Aromatic compounds, such as benzene, are generally found in fossil-based fuels and lead to the formation of pollutants such as NOx and particulate matter, leading to the formation of contrails, as well as reducing the energy density and thermal stability of the fuel. However, they also facilitate polymer seal swelling which reduces the risk of fuel leaks. Vardon et al. found that SAF often contain a much lower concentration of aromatics, if any, and therefore demonstrated an increased energy density, lower fuel consumption, and lower contrail emissions (Vardon et al., 2022). The Business Aviation Coalition found that SAF also show a reduction in SOx and CO emissions (The Bus. Av. Coal., 2020). Undavalli et al. highlighted that further experimental and numerical research is needed on the aromatic species and concentrations to balance emissions and improve engine compatibility (Undavalli et al., 2023).
The need for some aromatic content to enable seal swelling, as well as other chemical and physical properties, limits the amount of SAF that can be blended with conventional jet fuel. Yang et al. demonstrated a lignin-based jet fuel blend component to complement SAF by increasing their swelling potential and thereby support the potential use of 100% SAF (Yang et al., 2022). Yang et al. investigated the relation between distillation cut points and potential blend ratio, finding that there is competition between SAF yield and engine compatibility. Fractional distillation was used to cut the product that failed to meet specifications. The computational results predicted that a completely un-cut SAF product could be blended at 8%v with conventional jet fuel to meet the specification, while an 18% SAF yield (82% cut) could be substituted 100% for conventional fuel. To achieve a 50% blend limit with Jet A-1, the SAF yield was found to be 22%. The limiting properties to achieve a higher blend ratio were flash point, density, and freeze point (Yang et al., 2023). Therefore, further research is required to investigate how the chemical and physical properties of the fuel can be improved to increase its blending limit.
Lin et al. experimentally investigated spray penetration, angle, and volume of SAF under varying ambient temperatures, ambient pressures, and injection pressures. The results showed that as the temperature increased, penetration, spray angle, and spray volume decreased, reaching stability fastest at a high temperature (Lin et al., 2023). Liu et al. simulated atomization features of SAF and found that as pressure increased, more stable combustion was achieved (Liu et al., 2023).
Lean fuel combustion can lead to increased fuel efficiency as excess air allows for more complete combustion which often reduces fuel consumption, as well as reducing NOx and CO emissions. However, this can lead to lean blowoff where combustion is unstable due to excess air. Stachler et al. demonstrated that lean blowoff scales with evaporative, mixing, and chemical time scales (Stachler et al., 2020). Further research is required on combustion instability and its impact on noise and vibration, influencing the engine lifetime. Undavalli et al., 2023 emphasised that current research has shown a negligible difference compared to conventional jet fuel, however too little is known for it to be appropriately accounted for (Undavalli et al., 2023).
Modeling is vital to aid development by reducing experimental costs and time through optimization. Further investigation is needed using experimental and numerical models to predict the combustion behavior of SAF under varying conditions (Undavalli et al., 2023).
5 Life cycle assessment
5.1 Overview
SAF can be sourced from a diverse range of feedstocks, each contributing to carbon savings compared to traditional fossil fuels in distinct ways. The carbon emissions released by the combustion of biomass-derived biofuels are offset by the carbon which has been sequestered by the organic matter during its growth. This contrasts with fossil fuels which release carbon that would otherwise have been locked into the ground. Carbon savings are achieved when converting fossil wastes, such as MSW or industrial waste gasses, into fuels proves more efficient than traditional disposal methods.
An LCA is a comprehensive methodology used to evaluate the environmental impacts of a product, process, or service throughout its entire life cycle. It is a systematic approach that considers all stages of a product’s life, including raw material acquisition, manufacturing, transportation, usage, and end-of-life. By considering the entire life cycle of a product, LCA helps to avoid the problem of shifting burdens, where improvements in one stage of the life cycle may lead to increased impacts in another. There are generally four stages to an LCA: goal and scope, inventory, impact assessment, and improvement assessment (DEAT, 2004). In general, it is difficult to compare LCA results of different technologies and feedstocks as inconsistent assumptions and boundaries are made across different studies (Ng et al., 2021).
Process LCA, input-output LCA, and hybrid LCA are different approaches to conducting LCA, each with its own characteristics and applications. Process LCA focuses on specific processes in detail and is often applied to analyze the environmental impact of specific manufacturing processes, relying on detailed data. Input-output LCA uses averaged data for the sector to provide a broader picture of the environmental effects. Hybrid LCA considers both direct and indirect impacts by integrating input-output analysis with specific process data, offering a broader perspective of implications of changes in demand or technology across an entire sector, while also considering the specific scenario under investigation (Acquaye et al., 2012). Careful consideration of the system boundaries is required when planning or comparing LCA.
Environmental impact categories are usually chosen to align with a given standard. The PEF (or EN15804+A2) and CML standards are used worldwide, except North America. TRACI is only used in North America. ReCiPe is another standard which is not described here as it is not commonly used in product LCA (Ecochain, 2023; 2024; OneClickLCA, 2023). The impact categories common to all standards are listed below:
- Global warming potential–total fossil, biogenic, and land use (GWP)
- Ozone depletion potential (ODP)
- Acidification potential (AP)
- Freshwater eutrophication potential (FEP)
- Marine eutrophication potential (MEP)
- Terrestrial eutrophication potential (TEP)
- Photochemical ozone creation potential (POCP)
- Abiotic resource depletion potential (ADP)
Some other impact categories which are not common to all standards include direct or indirect land use change (D/ILUC), human toxicity potential (HTP), freshwater, marine, and terrestrial ecotoxicity potential (F/M/TETP), photochemical oxidation potential (POP), non-renewable and total cumulative energy demand (CEDnr/t), and water depletion potential (WDP).
5.2 Recent LCA on SAF conversion processes
Table 6 summarizes some recent LCA of SAF conversion processes, highlighting the location of the study, and the feedstocks and impact categories considered. The literature review methodology included searching on Google Scholar, PubMed, Scopus, and ResearchGate for papers published in the past 10 years by relevance to keywords such as ‘LCA’, ‘SAF’, and the various names of each conversion process.
Figure 4 presents a visualization of the availability of EU feedstocks from wastes for various SAF conversion processes compared to their TRL and the extent of LCA for each technology, color coded by a traffic-light system with green being the most extensive LCA and red being the least extensive. It can be seen that although HEFA is one of the most technologically ready processes and has some of the most LCA, the feedstock availability from wastes is significantly lower than for all the other conversion processes, partially due to it being in competition with biodiesel production. With the addition of oil-based energy crops, this availability will increase. Therefore, to achieve large-scale SAF production using HEFA, it is crucial to develop the production capacity of second-generation oil-based energy crops such as brassica carinata, camelina, and jatropha, as well as investigating their environmental, economic, and socio-political impacts. Although some LCA have focused on assessing some second-generation feedstocks such as jatropha and brassica carinata (Field, 2022; Zhang et al., 2024), limited research has been carried out to ascertain the potential production capacity of second-generation feedstocks in the UK, EU, or globally. Figure 4 also highlights that further LCA is recommended for aerobic fermentation, APR, and CHJ.
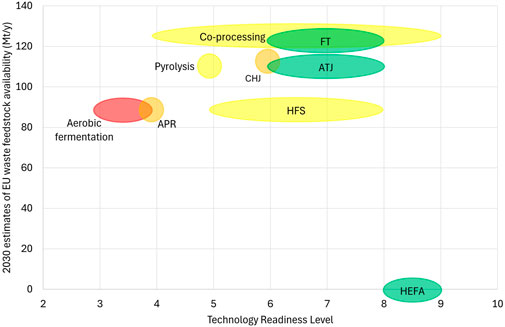
Figure 4. Visualization of the availability of EU waste feedstocks for various certified and emerging conversion processes in relation to their technology readiness level and extent of LCA, represented by traffic light coloring with green being the most extensive LCA, yellow being the second-most extensive, orange being the second-least extensive, and red being the least extensive LCA (O’Malley et al., 2021).
Vardon et al. reviewed the life cycle emissions of the HEFA, ethanol-to-jet, isobutanol-to-jet, and FT pathways, each with a variety of feedstocks (Vardon et al., 2022). The core LCA data included emissions from feedstock cultivation and collection, feedstock transportation, feedstock-to-fuel conversion, and fuel transportation. Induced land use change (ILUC) calculated by CORSIA were also evaluated. The results found that the minimum life cycle emissions came from the FT process with miscanthus as a feedstock at −22.5 gCO2eq/MJ and the isobutanol-to-jet process using miscanthus at −10.7 gCO2eq/MJ. The negative life cycle emissions for the use of miscanthus as a feedstock is due to its ability to increase soil organic carbon during cultivation. The maximum emissions came from the HEFA process using palm oil at 99.1 gCO2eq/MJ and the ATJ process using corn grain at 90.8 gCO2eq/MJ, proving to be higher than the life cycle emissions of fossil-based jet fuel at 89 gCO2eq/MJ. The HEFA process has the largest range of life cycle emissions across the feedstocks presented, from 13.9 gCO2eq/MJ for waste oils to 99.1 gCO2eq/MJ for palm oil.
Rogachuk and Okolie investigated the decomposition of waste tires via thermochemical processes to produce SAF (Rogachuck and Okolie, 2024). They compared fast pyrolysis with catalytic hydroprocessing and GFT processes. It was assumed that the feedstock was primarily synthetic rubber and hydrogen was obtained from natural gas, while the energy source was not specified. Pyrolysis showed approximately half the GWP at 34.3 kgCO2eq/kg SAF compared to GFT at 58.6 kgCO2eq/kg SAF, with the pyrolysis step being the most impactful in the production pathway. However it had higher potential environmental impacts in most other categories, except in terrestrial ecotoxicity where they were similar. Assuming a specific energy of SAF to be approximately 43 MJ/kg (Chuck and Donnelly, 2014), the GWP of FT-SPK determined by Rogachuk and Okolie equates to around 1.4 kgCO2eq/MJ which is within the range of GWP determined by Vardon et al. Therefore, these two studies present comparable results.
Oehmichen et al. assessed the impacts of SAF production technologies individually and as multi-blends with Jet A-1, namely, ATJ using maize, HEFA using tallow oil, and SIP using sugarcane (Oehmichen et al., 2022). Two case studies were proposed for multi-blend fuels; case A considering ATJ and HEFA fuels mixed with fossil Jet A-1, and case B considering SIP fuel blended with Jet A-1. For ATJ, the results were divided into a product-based assessment based on the lower heating value. The by-products of the HEFA process were used internally and therefore not considered further. For the SIP process, surplus electricity was assumed to replace emission factors for the same type of fossil-based power. The results showed that HEFA had the lowest overall impact of 3.1 gCO2eq/MJ. This was dominated by the biomass supply process as ATJ and SIP required arable land and water for feedstock production while HEFA used waste tallow oil and therefore required no land for production, with agriculture causing similar impacts for TAP. For FDP and MEPinf, the ATJ process was the highest due to its demand for hydrogen, heat, and electricity, as well as fertilizer production and fossil fuels used in agricultural machinery which was also common to SIP. Similarly, FEP was caused by use of fertilizers and combustion of fossil fuels in machinery. The highest overall impact was given by ATJ at 35.8 gCO2eq/MJ. A sensitivity analysis was carried out on the ATJ process using heat from a wood chip boiler and electricity from PV panels which showed a reduction in GHG emissions by 43%. For the multi-blend cases, GHG emissions were shown to reduce by a maximum of 35% compared to fossil Jet A-1. Case B had higher GHG emissions due to the low blending rate of SIP and HEFA, meaning a higher proportion of Jet A-1 was used.
Zhang et al. conducted an LCA of soybean-based and jatropha-based HEFA, as well as modeling the impacts of ILUC from soil carbon sequestration (Zhang et al., 2024). The LCA included crop cultivation, transportation, fuel production, and fuel usage stages. Two methods of producing jatropha-based SAF were modeled; with pathway one including the oil residue being used for fertilizer or power generation and pathway two including the oil residue being detoxified and used for animal feed. Two methods of producing soybean-based SAF were modeled, with pathway one including a certain amount of straw being returned to the field and pathway two including no straw being returned to the field. The LCA results showed that, for jatropha-based SAF, using the oil residue as animal feed was more beneficial since the life cycle GHG emissions of pathway one was found to be −36.1 gCO2eq/MJ and pathway two was found to be −59.4 gCO2eq/MJ. For soybean-based SAF, returning straw to the field was more beneficial since the life cycle GHG emissions for pathway one was 2.9 gCO2eq/MJ and pathway two was 66.1 gCO2eq/MJ. When soil carbon sequestration was included in the calculation, the emission reduction potential of jatropha-based SAF compared with fossil aviation fuel increased from 84% to 141% for pathway 1, and from 111% to 167% for pathway 2. The emission reduction potential of soybean-based SAF compared with fossil aviation fuel increased from 43% to 97% for pathway 1, however for pathway two it decreased from 43% to 26%. Soil carbon sequestration was higher for jatropha than for soybean due to less soil tillage being required for jatropha cultivation.
For HEFA technologies, a very wide range of GWP are presented across the works of Oehmichen et al., Vardon et al., and Zhang et al., ranging from −59.4 to 99.1 gCO2eq/MJ. However, the GWP results from Zhang et al. seem to be generally much lower than those from Vardon et al., highlighting the importance of assumptions and different feedstocks considered across various LCA studies. Similarly, a very wide range of GWP are described across the works of Oehmichen et al. and Vardon et al. for the ATJ process, ranging from −10.7 to 90.8 gCO2eq/MJ.
Chen et al. quantified the life cycle carbon intensity (CI) of SAF produced via CH from a variety of oil-based feedstocks (Chen et al., 2024). The LCA included feedstock production and transportation, preprocessing, hydrothermal cleanup (HCU), CH, hydrotreatment and fractionation, fuel transport, and end use. The base-case scenario used natural gas for heating, the US electricity mix, and hydrogen created from steam methane reforming. The sensitivity scenario used renewable natural gas (RNG) from landfill gas, wind power, and green hydrogen. Three feedstock groups were considered; a clean feedstock based on carinata oil (assumed to also be representative of vegetable oils like soy, camelina, canola, and corn), a moderately contaminated feedstock (yellow grease), and a heavily contaminated feedstock (brown grease) either fully dried or with reduced dewatering with no final evaporator. The results showed that the core CI values of oilseed derived SAF, neglecting ILUC, ranged from 28.2 to 46.1 gCO2eq/MJ. Corn oil and yellow grease had lower CI impacts of 15.9 and 18.4 gCO2eq/MJ respectively, while brown grease had a CI of 22.9 gCO2eq/MJ. Corn oil had the lowest CI with an 82% reduction from the fossil fuel baseline. Farming processes significantly contributed to the CI, especially from fertilizer usage causing N2O emissions. When ILUC values were included for oilseed crops, the total CI of soy oil and canola oil increased to 52.7 and 65.2 gCO2eq/MJ which pushed them above the target threshold of a 50% reduction in CI compared to fossil-based aviation fuels. Carinata and camelina oils had negative ILUC values which decreased their CI to 12.8 and 32.7 gCO2eq/MJ respectively. The greases had a larger share in pre-processing CI due to their higher water contents but had lower HCU and CH CI due to their higher yields. The greases also had a higher heating demand in the pre-processing stage, but this was compensated for since they produced more gasses in the HCU and CH which can be used for heating. Brown grease had the highest transportation CI due to its high water content. The LCA results were comparable with those from HEFA production. The proposed improvements to reduce the CI included using renewable energy and removing the final evaporator from the brown grease process, which reduced the overall CI by 65.7%. Using green hydrogen for hydrotreating reduced the overall CI by 36.6%.
Tzanetis et al. assessed HTL using forestry residues in Sweden, investigating changes in catalyst type, reaction temperature, and the catalyst-biomass mass ratio (Tzanetis et al., 2017). LCA were conducted on two system models; FE340 using an iron catalyst at a temperature of 340°C and W300 using a water catalyst at a temperature of 300°C. An economic allocation method was utilised, biogenic carbon was considered to be carbon neutral, and the potential environmental impacts of the catalysts were not considered due to lack of data. For the FE340 and W300 processes, the GWP were calculated to be 13.1 kgCO2eq/GJ and 13.2 kgCO2eq/GJ respectively. For FE340, the upgrading step showed the highest contribution at 34%, followed by raw material acquisition at 25%, transport at 20%, oil production at 14%, and finally product transportation at 7%. For W300, oil production had the lowest contribution at 2% due to no consumption of natural gas. For both cases, bio-jet fuel could lead to a reduction in GHG emissions of 85% compared to fossil-based fuel. When the European electricity mix was considered, the GWP increased to 21.1 and 21.9 kgCO2eq/GJ for FE340 and W300 respectively. Since lots of steam was produced, this could be used for heating another process, further reducing the GWP by 1.5 and 13.8 kgCO2eq/GJ for FE340 and W300 respectively.
De Souza Deuber et al. examined various scenarios of HTL based on the sugarcane industry in Brazil (De Souza Deuber et al., 2023). Three standalone plants were considered; converting sugarcane bagasse with a water catalyst (SA-H2O-SCB), converting sugarcane bagasse with an ethanol catalyst (SA-EtOH-SCB), and converting straw with a water catalyst (SA-H2O-STW). Two integrated plants were considered; converting straw with a water catalyst (INT-H2O-SCB&STW) and converting bagasse and straw with ethanol (INT-EtOH-SCB&STW). The LCA included biomass production, conversion, fuel distribution, and fuel use. The environmental impacts of the various products were divided based on energy allocation. The SA-EtOH-SCB scenario showed the least GHG emission savings of around 73% compared to fossil-based jet, while INT-H2O-SCB&STW showed the greatest GHG savings at around 82%. Overall, HTL performed better than fossil fuels in GWP, POCP, TEP, and fossil resource scarcity, but worse in FEP, land use, and mineral resource scarcity. The ethanol solvent contributed 47% of the total emissions for SA-EtOH-SCB, proving that water is the less impactful liquefaction solvent. For the standalone cases, HTL conversion was the most significant contributor (74%–83%). Hydrogen production through steam methane reforming (SMR) was a large contributor (13%–29% of the total impact), as was natural gas usage (9%–20%) and electricity (13%–23%). The straw feedstock had higher impacts than bagasse since harvesting was considered, while no production emissions were assumed for bagasse. For the integrated scenarios, biomass production had the most significant impact (63%–64%) since the larger production scale meant more emissions originated from agriculture. Fuel distribution had the second largest contribution (17%–19%) due to an assumed average transport distance of 1,500 km by road. No impacts related to background emissions from electricity or natural gas were considered since the energy demand was supplied by the CHP system and biomethane was produced internally. The GWP results for the HTL process from Tzanetis et al. and De Souza Deuber et al. are in a similar range from 13.1 to 18.3 gCO2eq/MJ, therefore showing comparability between these studies.
Tanzil et al. investigated co-processing of SAF in a midsize petroleum refinery (PR) (Tanzil et al., 2021b). The analysis was iterated over five lignocellulosic SAF technologies: Virent’s BioForming (VB), ATJ, DSHC, FP, GFT, and integrated carbonization-GFT (ICGFT), using corn stover as the feedstock. The amount of bio-oil produced from each conversion process determined the co-processing ratio; with DSHC co-processed at a ratio of 6%, GFT at 7%, VB and ATJ at 10%, and FP at 15%, while ICGFT was not specified. A range of scenarios were proposed across various integration strategies. Out of the 21 proposed scenarios, 17 showed GHG savings ranging from 7% to 92%. The lowest total GHG emissions were produced via one of the ATJ scenarios at 6.1 gCO2eq/MJ, representing a 93% saving compared to fossil-based aviation fuel with 87 gCO2eq/MJ. The second lowest emissions were produced from two of the ICGFT scenarios at 6.9 gCO2eq/MJ, representing a 92% emissions saving. Overall, the ICGFT scenarios had the highest yields, contributing to economic and environmental benefits. The highest emissions came from two of the VB scenarios at 119.8 gCO2eq/MJ, representing an increase in emissions of 38%. The second highest emissions came from two of the DSHC scenarios at 111.5 gCO2eq/MJ, representing an increase in emissions of 28%.
Peters et al. investigated the uses of bio-oil produced from pyrolysis of hybrid short-rotation poplar in Spain (Peters et al., 2015). Four scenarios were proposed, namely, cogeneration (CG) in a district heating plant, co-combustion in a coal-fired power plant (CC), and upgrading via hydrotreating either in a decentralized biorefinery (BR-d) or in an integrated biorefinery (BR-i). For BR-d, all pyrolysis gasses and a portion of the biochar was burned on site for heat generation, while the additional char was substituted for coal in a coal-fired power plant. For BR-i, all pyrolysis gasses were processed in the steam reformer of the refinery, reducing the natural gas requirement, while all the biochar was burned to produce heat for the pyrolysis reactor. The LCA system boundaries included feedstock production, production of utilities, and all steps up to the end user. An avoided burden approach was used, where all products replaced equivalent conventional fossil-based products. Hence, most of the LCA results are negative, showing a decrease in potential environmental impacts compared to fossil-based alternatives. CG shows the highest benefit for ODP, CEDnr, and CEDt. CC shows the highest benefits in terms of GWP, ADP, EP, and AP, predominantly due to the comparative effects of emissions from existing coal-fired power plants. BR-i showed the worst results in every impact category except for ODP. The impacts from EP and AP are related to the electricity requirements since coal-fired power stations still play a significant role in the Spanish energy mix. BR-d and BR-i showed the worst results for EP and AP since the production of biofuels requires more electricity than fossil fuel production. The pyrolysis step contributes a significant share of the overall environmental impact for each of the scenarios, and within this, electricity usage and direct emissions from the combustor are the major factors. The agricultural step is shown to be a favorable contributor in CED and GWP due to the CO2 fixed during plant growth, but contributed negatively toward AP, EP, ADP, and ODP. Direct emissions from CG and CC combustion are major contributors to GWP, as are electricity and natural gas consumption in the biorefineries. The choice of substitution played a key role in the LCA results. The GWP results from Peters et al. contrast greatly with those from Rogachuk and Okolie since the former found pyrolysis to have a marginally negative GWP and the latter found a GWP of 34.3 kgCO2eq/kg SAF.
Pipitone et al. investigated hydrogenation of vegetable oils to produce SAF (Pipitone et al., 2023). Two scenarios were proposed, namely, HEFA with hydrotreatment using hydrogen derived from fossil sources and an advanced case using in-situ hydrogen produced via APR of the glycerol by-product. The LCA was conducted with gate-to-gate system boundaries limited to the biorefinery. An attributional method was used to separate the GWP of the products based on mass and energy contents. Materials and energy for construction were not considered, the European energy mix was used, natural gas was used for thermal energy, and the cooling thermal power was converted to electricity. Hydrogen was mainly responsible for the GWP at 90% and 80% for the conventional and advanced scenarios respectively. For the advanced case, the amount of external hydrogen required decreased by 63% compared to the conventional case, and electricity consumption decreased by 43%, but the heating demand increased by 37%. Before impact allocation was conducted, the GWP of the conventional and advanced biorefineries were 54 gCO2eq/MJ and 23 gCO2eq/MJ respectively. After mass-based allocation was conducted, the GWP for the advanced case reduced to 8.2 gCO2eq/MJ. After energy-based allocation, the GWP of the advanced case was 11.7 gCO2eq/MJ, 54% lower than the conventional case.
5.3 Summary of LCA research gaps
Aerobic fermentation is the only SAF production pathway for which no LCA could be found. Abel et al. carried out an LCA of aerobic microbial systems but did not consider their applications to SAF production (Abel et al., 2022).
Although it has economic benefits such as reduced capital costs, the sustainability of co-processing requires further investigation as the majority of this fuel type still originates from crude oil, maintaining high carbon emissions on combustion.
Most SAF conversion processes have been subjected to LCA in some form, however the detail and fullness of the analysis generally varies, making it difficult to compare results across different LCA. Many studies present cradle-to-grave LCA, however some gate-to-gate and cradle-to-gate studies were also found. There is a lack of cradle-to-cradle LCA to simulate a circular economy involving SAF production. Defining appropriate system boundaries and allocation methods for multi-output processes in the SAF supply chain can be challenging. Consensus on methodological choices is necessary for consistent and comparable assessments.
GWP is a common impact category in all LCA, however there is a lack of published comparisons between the results of different environmental impact categories on SAF production, specifically concerning potential local impacts such as eutrophication potential.
Consideration of temporal and spatial variability in LCA models is crucial. Biofuel production systems may vary over time and across different geographical locations, influencing the environmental performance. Dynamic modeling approaches need further development. Many LCA focus on SAF production in the United States due to the established infrastructure and supply chain of energy crops. Other studies look at locations in which a specific feedstock supply chain is already well-established, such as sugarcane production in Brazil. There is a lack of LCA specifically targeting UK SAF production, focusing on feedstocks available in this country or, if it is necessary to import feedstocks, which imports have the lowest environmental impacts and costs.
There is a need for primary data from industry and modeling to conduct LCA on other feedstocks. Due to the complexity of the supply chain, availability of comprehensive and accurate data for all stages of the life cycle of SAF, including feedstock production, conversion processes, distribution, and end-use, is a significant challenge. Data gaps can affect the accuracy and completeness of LCA results. Moreover, improved methods for uncertainty and sensitivity analysis are needed to enhance the robustness of LCA results. Understanding the uncertainties associated with data inputs and model parameters is crucial for decision-makers.
Rapid advancements in SAF conversion technologies may outpace the development of corresponding LCA methodologies and databases. Continuous updates and improvements to LCA models are necessary to keep up with evolving technologies.
6 Recommendations for future research
6.1 Feedstocks
Further research into feedstock production should focus on increasing the availability, yield, and productivity of feedstocks to help achieve scale-up and reach the necessary production volumes. Moreover, increasing the diversity of SAF feedstocks requires further attention in order to increase supply chain resilience and reduce risks associated with a sudden reduction in the supply of a particular feedstock. The composition of different feedstocks needs further research as limited investment opportunities necessitate prioritization of the most applicable feedstock options. Furthermore, development and implementation strategies of sustainable agricultural practices are necessary to minimize emissions throughout the whole supply chain.
6.2 Conversion processes
The economic viability and cost competitiveness of SAF production processes is a major factor that requires further attention. Further research is required to improve the conversion efficiency of each conversion process in order to reduce costs and increase the yield. Improving the catalyst selectivity and efficiency is a common requirement for many conversion processes, as well as preventing catalyst deactivation. Modeling and additive manufacturing of all conversion processes requires further attention to improve heat and mass transfer, fabrication time, and temperature control. Further research is needed regarding the FT process to avoid catalyst poisoning via syngas cleaning. This will help to achieve the required cleaning standard and reduce costs. The CH process requires further attention to reduce the nitrogen content of the product. A limitation of APR is its low selectivity and catalyst deactivation caused by coking.
6.3 Technical specifications
Additional research is needed to ensure engine compatibility, focusing on both experimental and numerical exploration of the chemical and physical properties of the fuel is crucial for extending its blending limit. Additionally, examining ways to optimize the aromatic species and concentrations is necessary to reduce emissions and improve engine compatibility. Further investigation into combustion instability and its repercussions on noise, vibration, and engine lifespan is necessary. Although existing research indicates a minimal difference compared to conventional jet fuel, insufficient knowledge exists for accurate incorporation. Extensive investigation, utilizing both experimental and numerical models, is essential to predict the combustion behavior of SAF across diverse conditions.
6.4 LCA
Further research should focus on conducting cradle-to-cradle LCA of various SAF production pathways using different feedstocks and technologies with the aim of simulating a circular economy. For example, gaseous products from many SAF conversion processes can be used for heating or power generation in the conversion plant, reducing costs and emissions. Further research into the effectiveness, efficiency, and costs and emissions impacts should be conducted to ascertain the applicability of gas re-use. Moreover, solid biochar by-products from processes such as pyrolysis can be used as soil additives to increase crop yields. A very low application of biochar fertilizers has been shown to increase crop productivity by 10% compared with conventional fertilizers and 186% compared with no fertilizer use, as well as increasing crop productivity by 15% on soil that is not responsive to conventional fertilizer (Melo et al., 2022). Further research in this area should focus on specializing the properties and functionalities of biochar fertilizers for specific applications to further increase their economic and environmental benefits. There is also a need to assess whether biochar fertilizers create changes in the rhizosphere electron transfer properties, leading to higher efficiency nutrient use and therefore higher crop productivity. Further research is also needed to ascertain whether continual use of biochar can allow for reductions in chemical fertilizer usage, particularly when combined with other sustainable agricultural practices such as cover crops. If proven technically, environmentally, and economically beneficial, the use of biochar soil additives could help to achieve a circular economy in SAF production, reducing costs and environmental impacts.
Although many LCA have focused on SAF production in the United States or the production of a specific feedstock in its native country, prioritizing locally sourced feedstocks helps to reduce emissions. Consequently, there is a need for LCA focusing on United Kingdom feedstocks and infrastructure. Due to the varying resources available in different areas, location-specific data and analysis is necessary for accurate LCA, taking into account local climates, energy sources, agricultural practices, water availability, and feedstock availabilities. Since the United Kingdom is an island and has limited land availability, it may be more beneficial to invest in low-land-requirement SAF production pathways such as the use of MSW in GFT and algae in HC-HEFA. A UK-based LCA would help to ascertain to what extent this is true. The environmental impact of transporting feedstocks to the production facility, as well as distributing the final SAF product, can vary based on location. Accounting for transportation distances, modes of transport, and associated emissions provides a more accurate assessment of life cycle emissions and helps to assess the viability of different SAF production pathways in various locations. Moreover, understanding the local infrastructure helps to optimize the entire supply chain as design and investment decisions can be tailored to a specific location. Different regions may have specific policies, regulations, and incentives related to SAF production. Furthermore, a location-specific LCA ensures compliance with local environmental standards and regulations, providing insights into areas where improvements can be made to meet or exceed sustainability targets, while also helping to inform further policy and regulation development.
Temporal LCA requires further attention in the context of SAF production in order to account for future technological advancements, considering changes in energy efficiency, resource use, and emissions. It is important to consider the ability to retrofit more advanced technologies, or to be able to adjust processes, after a production plant has been built in order to keep up to date with new research that aims to reduce environmental impacts and costs. Moreover, the GWP of a process may vary over time due to changes in the energy mix. These must be accurately accounted for to ensure that SAF remain a beneficial option. Additionally, the adaptive potential of conversion processes is highly important as the availability of feedstocks may change over time due to requirements for other uses and varying climate conditions. The ability of a temporal LCA to respond to future uncertainties in consumer behavior, policies, and regulations is also highly valued.
Explicit comparisons of different environmental impact categories are required to provide a holistic understanding of the effects of different SAF production pathways across a range of categories which are not necessarily related. For example, the use of chemical fertilizers may increase the risk of eutrophication, affecting local communities, which does not directly contribute to the GWP. Moreover, assessing multiple impact categories allows for the identification of trade-offs and synergies. Improving performance in one category might have adverse effects in another. A comprehensive comparison helps balance environmental considerations and avoid unintended consequences, which currently has not been widely examined.
Additionally, further research is required to obtain primary data from industry, pilot production plants, and models in order to fill data gaps. Many LCA must incorporate data estimation or substitutions since data gaps exist. Obtaining primary data on various production pathways will help to reduce uncertainties in LCA results and provide more accurate information for stakeholder investment and policy development. Meanwhile, where data gaps cannot be avoided, improved methods for uncertainty and sensitivity analysis are required.
As the technological development of SAF conversion processes and feedstock production methods continues, further LCA is required to compare the most up-to-date processes in order for stakeholders to make informed decisions. Current methodologies, resource usage, and emissions must be considered in order to provide an accurate assessment of the environmental impacts of various technologies. While doing this, it is important to conduct a variety of scopes of LCA, with some being specialized to one production pathway, giving an in-depth analysis, and others providing a broader comparison of many different production pathways. One technology may become favorable over time due to technological or methodological developments, affecting stakeholder decisions. Moreover, it is important for developing technologies to keep up to date with current policies and regulations on emissions, ecosystem impact, and safety.
6.5 Other comparative analyses
Combining LCA with Techno-Economic Analysis (TEA), physical and chemical property requirements, and socio-political studies is important to achieve a more comprehensive and integrated approach to sustainability assessments of various production pathways, allowing for a more informed decision-making. It also helps to identify trade-offs and barriers across a wide range of applicable sectors, helping to address challenges during the design and development stages.
This can be done via multi-criteria decision analysis (MCDA) which aims to help decision-makers make more informed and objective decisions that align with multiple requirements. To the best of our knowledge, only four MCDA studies on SAF conversion processes have been published (Xu et al., 2019; Ahmad et al., 2021; Chai and Zhou, 2022; Okolie et al., 2023). Future research should focus on considering a broader range of SAF production pathways in one MCDA to obtain a comprehensive view of the current technology status. Further research should also include location specific data, such as where certain feedstocks are grown and location requirements for technologies, to ascertain which are better suited for different countries or areas. In terms of the methodology, investigations into different weighting distributions and scoring methods would be highly beneficial as they have mainly focused on qualitative stakeholder-based methods. Other methods such as entropy weighting and calculation-based scoring should be employed to reduce the subjectivity of the method. Further research should also focus on comparative analyses with other MCDA methods in order to demonstrate the reliability or uncertainty in the results.
7 Conclusion
The development of SAF is crucial for mitigating the environmental impact of the aviation industry, aligning with emission reduction targets, and addressing the urgency of the global climate crisis, as well as enhancing energy security by minimizing dependence on conventional fossil fuels. This review investigated the benefits and challenges of various CORSIA recognized feedstocks for SAF production and emphasized the difficulties in estimating feedstock availabilities by location. Some of the main research gaps in relation to feedstock production were described, such as increasing the availability, yield, and diversity of feedstocks, investigating their compositions, and implementing sustainable agricultural practices. The conversion processes certified by ASTM were summarized, along with their primary feedstocks, blending ratios, TRL, and recent developments in their fields. The most prominent emerging technologies were also illustrated, along with their recent developments. The main research gaps and areas for further research include improving the economic viability, conversion efficiency, catalyst selectivity, and modeling capacity, as well as preventing catalyst deactivation. The technical specifications for engine compatibility and safety were outlined. Further research is required to investigate blending limits, aromatic species and concentrations, combustion instability, and numerical modeling. Some prominent LCA were summarized, including the data source, software and methodology, location, feedstocks considered, and impact categories. Some of the main research gaps in relation to the type and scope of LCA include conducting cradle-to-cradle LCA to demonstrate a more circular economy, carrying out location-specific LCA particularly in the UK and EU, and conducting temporal LCA to help predict future trends, as well as considering more environmental impact categories especially related to localized effects. It is highly recommended that focus is put on obtaining more primary data from industry, pilot production plants, and models in order to fill data gaps which currently limit the accuracy and scope of LCA for some production pathways. As technologies continue to be developed, more LCA must be carried out, with some specializing on a particular in-depth process, and others focusing on the general picture of SAF production to compare alternatives. Future work should also address combining LCA, TEA, fuel requirements, and socio-political assessments in a MCDA as this is a highly under-developed area of research regarding SAF production.
Author contributions
EB: Writing–original draft, Writing–review and editing. SK: Writing–review and editing. RY: Writing–review and editing.
Funding
The authors declare that financial support was received for the research, authorship, and publication of this article. The authors would like to acknowledge EPSRC for the funding support of the research project (Grant Ref: EP/W524360/1) and Supergen (EP/Y016300/1).
Acknowledgments
For the purpose of open access, the author has applied a Creative Commons Attribution (CC BY) license to any Author-Accepted Manuscript version arising.
Conflict of interest
The authors declare that the research was conducted in the absence of any commercial or financial relationships that could be construed as a potential conflict of interest.
Publisher’s note
All claims expressed in this article are solely those of the authors and do not necessarily represent those of their affiliated organizations, or those of the publisher, the editors and the reviewers. Any product that may be evaluated in this article, or claim that may be made by its manufacturer, is not guaranteed or endorsed by the publisher.
References
Abel, A. J., Adams, J. D., and Clark, D. S. (2022). A comparative life cycle analysis of electromicrobial production systems. Energy and Environ. Sci. 15 (7), 3062–3085. doi:10.1039/d2ee00569g
Acquaye, A. A., Sherwen, T., Genovese, A., Kuylenstierna, J., Lenny Koh, S. C., and Mcqueen-Mason, S. (2012). Biofuels and their potential to aid the UK towards achieving emissions reduction policy targets. Renew. Sustain. Energy Rev. 16 (7), 5414–5422. doi:10.1016/j.rser.2012.04.046
Afonso, F., Sohst, M., Diogo, C. M. A., Rodrigues, S. S., Ferreira, A., Ribeiro, I., et al. (2023). Strategies towards a more sustainable aviation: a systematic review. Prog. Aerosp. Sci. 137, 100878. doi:10.1016/j.paerosci.2022.100878
Ahmad, S., Ouenniche, J., Kolosz, B. W., Greening, P., Andresen, J. M., Maroto-Valer, M. M., et al. (2021). A stakeholders’ participatory approach to multi-criteria assessment of sustainable aviation fuels production pathways. Int. J. Prod. Econ. 238 (108156), 108156. doi:10.1016/j.ijpe.2021.108156
Alenezi, R., Baig, M., Wang, J., Santos, R., and Leeke, G. A. (2010). Continuous flow hydrolysis of sunflower oil for biodiesel. Energy Sources, Part A Recovery, Util. Environ. Eff. 32 (5), 460–468. doi:10.1080/15567030802612341
Baliban, R. C., Elia, J. A., Floudas, C. A., Xiao, X., Zhang, Z., Li, J., et al. (2013). Thermochemical conversion of duckweed biomass to gasoline, diesel, and jet fuel: process synthesis and global optimization. Industrial Eng. Chem. Res. 52 (33), 11436–11450. doi:10.1021/ie3034703
Bauen, A., Bitossi, N., German, L., Harris, A., and Leow, K. (2020). Sustainable aviation fuels. Johns. Matthey Technol. Rev. 64 (3), 263–278. doi:10.1595/205651320x15816756012040
Ben Hassen Trabelsi, A. B. H., Zaafouri, K., Baghdadi, W., Naoui, S., and Ouerghi, A. (2018). Second generation biofuels production from waste cooking oil via pyrolysis process. Renew. Energy 126, 888–896. doi:10.1016/j.renene.2018.04.002
Boerrigter, H., Den Uil, H., and Calis, H. (2002). “Green diesel from biomass via fischer-tropsch synthesis: new insights in gas cleaning and process design,” in Pyrolysis and gasification of biomass and waste, expert meeting.
Cabrera, E., and de Sousa, J. M. M. (2022). Use of sustainable fuels in aviation—a review. Energies 15 (7), 2440. doi:10.3390/en15072440
Chai, N., and Zhou, W. (2022). A novel hybrid MCDM approach for selecting sustainable alternative aviation fuels in supply chain management. Fuel 327, 125180. doi:10.1016/j.fuel.2022.125180
Chen, P. H., Lee, U., Liu, X., Cai, H., and Wang, M. (2024). Life-cycle analysis of sustainable aviation fuel production through catalytic hydrothermolysis. Biofuels, Bioprod. Biorefining 18 (1), 42–54. doi:10.1002/bbb.2574
Chisti, Y. (2007). Biodiesel from microalgae. Biotechnol. Adv. 25 (3), 294–306. doi:10.1016/j.biotechadv.2007.02.001
Chuck, C. J., and Donnelly, J. (2014). The compatibility of potential bioderived fuels with Jet A-1 aviation kerosene. Appl. Energy 118, 83–91. doi:10.1016/j.apenergy.2013.12.019
Coronado, I., Stekrova, M., Reinikainen, M., Simell, P., Lefferts, L., and Lehtonen, J. (2016). A review of catalytic aqueous-phase reforming of oxygenated hydrocarbons derived from biorefinery water fractions. Int. J. Hydrogen Energy 41 (26), 11003–11032. doi:10.1016/j.ijhydene.2016.05.032
Corporan, E., Dewitt, M. J., Klingshirn, C. D., and Anneken, D. (2010). Alternative fuels tests on a C-17 aircraft: emissions characteristics. AFRL-RZ-WP-TR-2011-2004. Fuels and Energy Branch, University of Dayton Research Institute: Air Force Research Laboratory, United States Air Force.
Cronin, D. J., Subramaniam, S., Brady, C., Cooper, A., Yang, Z., Heyne, J., et al. (2022). Sustainable aviation fuel from hydrothermal liquefaction of wet wastes. Energies 15 (4), 1306. doi:10.3390/en15041306
Das, P. P., Singh, K. R., Nagpure, G., Mansoori, A., Singh, R. P., Ghazi, I. A., et al. (2022). Plant-soil-microbes: a tripartite interaction for nutrient acquisition and better plant growth for sustainable agricultural practices. Environ. Res. 214 (113821), 113821. doi:10.1016/j.envres.2022.113821
Davis, R., Biddy, M., Tan, E., Tao, L., and Jones, S. (2013). Biological conversion of sugars to hydrocarbons technology pathway. National Renewable Energy Laboratory (NREL): U.S. Department of Energy, Bioenergy Technologies Office.
Davis, R., Tao, L., Scarlata, C., Tan, E. C. D., Ross, J., Lukas, J., et al. (2015). Process design and economics for the conversion of lignocellulosic biomass to hydrocarbons: dilute-acid and enzymatic deconstruction of biomass to sugars and catalytic conversion of sugars to hydrocarbons. National Renewable Energy Laboratory (NREL): U.S. Department of Energy Office of Energy Efficiency & Renewable Energy.
DEPARTMENT FOR TRANSPORT (2023). Pathway to net zero aviation: developing the UK sustainable aviation fuel mandate. London, United Kingdom: Department for Transport.
de Sousa, F. P., Dos Reis, G. P., and Pasa, V. M. D. (2024). Catalytic pyrolysis of vegetable oils over NbOPO4 for SAF and green diesel production. J. Anal. Appl. Pyrolysis 177 (106314), 106314. doi:10.1016/j.jaap.2023.106314
de Souza Deuber, R., Bressanin, J. M., Fernandes, D. S., Guimarães, H. R., Chagas, M. F., Bonomi, A., et al. (2023). Production of sustainable aviation fuels from lignocellulosic residues in Brazil through hydrothermal liquefaction: techno-economic and environmental assessments. Energies 16 (6), 2723. doi:10.3390/en16062723
Detsios, N., Maragoudaki, L., Atsonios, K., Grammelis, P., and Orfanoudakis, N. G. (2023a). Design considerations of an integrated thermochemical/biochemical route for aviation and maritime biofuel production. Biomass Convers. Biorefinery. doi:10.1007/s13399-023-03754-4
Detsios, N., Theodoraki, S., Maragoudaki, L., Atsonios, K., Grammelis, P., and Orfanoudakis, N. G. (2023b). Recent advances on alternative aviation fuels/pathways: a critical review. Energies 16 (4), 1904. doi:10.3390/en16041904
Dietrich, R., Adelung, S., Habermeyer, F., Maier, S., Philippi, P., Raab, M., et al. (2024). Technical, economic and ecological assessment of European sustainable aviation fuels (SAF) production. CEAS Aeronautical J. 15 (2), 161–174. doi:10.1007/s13272-024-00714-0
Ding, S., Ma, Q., Qiu, T., Gan, C., and Wang, X. (2024). An engine-level safety assessment approach of sustainable aviation fuel based on a multi-fidelity aerodynamic model. Sustainability 16 (9), 3814. doi:10.3390/su16093814
Durdina, L., Brem, B. T., Elser, M., Schönenberger, D., Siegerist, F., and Anet, J. G. (2021). Reduction of nonvolatile particulate matter emissions of a commercial turbofan engine at the ground level from the use of a sustainable aviation fuel blend. Environ. Sci. Technol. 55 (21), 14576–14585. doi:10.1021/acs.est.1c04744
EASA (2023). What are sustainable aviation fuels? Available at: https://www.easa.europa.eu/eco/eaer/topics/sustainable-aviation-fuels/what-are-sustainable-aviation-fuels (February 07, 2024).
ECOCHAIN (2023). The revised EPD standard ‘EN15804 +A2’: what’s going to change? Available at: https://ecochain.com/blog/en15804-consequences/ (January 18, 2024).
ECOCHAIN (2024). Impact categories (LCA) – overview. Available at: https://ecochain.com/blog/impact-categories-lca/ (January 18, 2024).
Elangovan, S., Hartvigsen, J., Hollist, M., and Elwell, J. (2023). (Invited) utilization of bio-CO2 and bio-methane for fuel production: integration solid oxide electrolyzer, low energy plasma reformer with fischer-tropsch synthesis. ECS Trans. 112 (5), 91–101. doi:10.1149/11205.0091ecst
Field, J. (2022). Modeling the yield, biogenic emissions, and soil carbon sequestration outcomes of Brassica carinata grown in the southeastern US as a winter cash crop and sustainable aviation fuel feedstock. Wiley.
Fredsgaard, M., Hulkko, L. S. S., Chaturvedi, T., and Thomsen, M. H. (2021). Process simulation and techno-economic assessment of Salicornia sp. based jet fuel refinery through Hermetia illucens sugars-to-lipids conversion and HEFA route. Biomass Bioenergy 150, 106142. doi:10.1016/j.biombioe.2021.106142
French, R. J., Hrdlicka, J., and Baldwin, R. (2010). Mild hydrotreating of biomass pyrolysis oils to produce a suitable refinery feedstock. Environ. Prog. Sustain. Energy 29 (2), 142–150. doi:10.1002/ep.10419
Geleynse, S., Jiang, Z., Brandt, K., Garcia-Perez, M., Wolcott, M., and Zhang, X. (2020). Pulp mill integration with alcohol-to-jet conversion technology. Fuel Process. Technol. 201, 106338. doi:10.1016/j.fuproc.2020.106338
Gerards, R. T. J., Fernandes, A., Graça, I., and Ribeiro, M. F. (2020). Towards understanding of phenolic compounds impact on Ni- and V-USY zeolites during bio-oils co-processing in FCC units. Fuel 260, 116372. doi:10.1016/j.fuel.2019.116372
Glowka, M., Wójcik, J., Boberski, P., Białecki, T., Gawron, B., Skolniak, M., et al. (2024). Sustainable aviation fuel – comprehensive study on highly selective isomerization route towards HEFA based bioadditives. Renew. Energy 220, 119696. doi:10.1016/j.renene.2023.119696
Goh, B. H. H., Chong, C. T., Ong, H. C., Seljak, T., Katrašnik, T., Józsa, V., et al. (2022). Recent advancements in catalytic conversion pathways for synthetic jet fuel produced from bioresources. Energy Convers. Manag. 251, 114974. doi:10.1016/j.enconman.2021.114974
GREEN CAR CONGRESS (2020). ASTM approves 7th annex to D7566 sustainable jet fuel specification: HC-HEFA. Available at: https://www.greencarcongress.com/2020/05/20200514-ihi.html (January 18, 2024).
Han, X., Wang, H., Zeng, Y., and Liu, J. (2021). Advancing the application of bio-oils by co-processing with petroleum intermediates: a review. Energy Convers. Manag. X 10, 100069. doi:10.1016/j.ecmx.2020.100069
Harisankar, S., and Vinu, R. (2023). Comprehensive evaluation of municipal solid wastes and mixed feedstocks for commercial hydrothermal liquefaction in bio-refineries. Fuel 339, 127236. doi:10.1016/j.fuel.2022.127236
Harvey, B. G., and Quintana, R. L. (2010). Synthesis of renewable jet and diesel fuels from 2-ethyl-1-hexene. Energy and Environ. Sci. 3 (3), 352–357. doi:10.1039/b924004g
Hognon, C., Delrue, F., Texier, J., Grateau, M., Thiery, S., Miller, H., et al. (2015). Comparison of pyrolysis and hydrothermal liquefaction of Chlamydomonas reinhardtii. Growth studies on the recovered hydrothermal aqueous phase. Biomass Bioenergy 73, 23–31. doi:10.1016/j.biombioe.2014.11.025
Huber, G. W., Iborra, S., and Corma, A. (2006). Synthesis of transportation fuels from biomass: chemistry, catalysts, and engineering. Chem. Rev. 106 (9), 4044–4098. doi:10.1021/cr068360d
ICAO (2021). SAF feedstocks. Available at: https://www.icao.int/environmental-protection/Pages/SAF_Feedstocks.aspx (January 06, 2024).
ICAO (2023). Conversion processes. Available at: https://www.icao.int/environmental-protection/GFAAF/Pages/Conversion-processes.aspx (January 08, 2024).
Jarin, J., Champion-Réaud, J., Lambert, P., Mendes, C., Jeuland, N., May-Carle, J., et al. (2023). GAS concentration maps within a turbomachine combustor fueled with jet-a1 or sustainable aviation fuel (SAF),” in ASME Turbomachinery Technical Conference and Exposition, Boston, MA, June 26–30, 2023.
Kakku, S., Naidu, S., Chakinala, A. G., Joshi, J., Thota, C., Maity, P., et al. (2024). Co-processing of organic fraction from groundnut shell biocrude with VGO in FCC unit to produce petrochemical products. Renew. Energy 224, 120182. doi:10.1016/j.renene.2024.120182
Kalekar, V. N., and Vaidya, P. D. (2022). Hydrogen production by aqueous-phase reforming of model compounds of wet biomass over platinum catalysts. Industrial Eng. Chem. Res. 61 (28), 10004–10013. doi:10.1021/acs.iecr.2c01131
Kandaramath Hari, T., Yaakob, Z., and Binitha, N. N. (2015). Aviation biofuel from renewable resources: routes, opportunities and challenges. Renew. Sustain. Energy Rev. 42, 1234–1244. doi:10.1016/j.rser.2014.10.095
Kolosz, B. W., Luo, Y., Xu, B., Maroto-Valer, M. M., and Andresen, J. M. (2020). Life cycle environmental analysis of ‘drop in’ alternative aviation fuels: a review. Sustain. Energy and Fuels 4 (7), 3229–3263. doi:10.1039/c9se00788a
Lan, E. I., and Liao, J. C. (2013). Microbial synthesis of n-butanol, isobutanol, and other higher alcohols from diverse resources. Bioresour. Technol. 135, 339–349. doi:10.1016/j.biortech.2012.09.104
Leibbrandt, N. H., Aboyade, A. O., Knoetze, J. H., and Görgens, J. F. (2013). Process efficiency of biofuel production via gasification and Fischer–Tropsch synthesis. Fuel 109, 484–492. doi:10.1016/j.fuel.2013.03.013
Li, L., Coppola, E., Rine, J., Miller, J. L., and Walker, D. (2010). Catalytic hydrothermal conversion of triglycerides to non-ester biofuels. Energy and Fuels 24 (2), 1305–1315. doi:10.1021/ef901163a
Lin, J., Nurazaq, W. A., and Wang, W. (2023). The properties of sustainable aviation fuel I: spray characteristics. Energy 283 (129125), 129125. doi:10.1016/j.energy.2023.129125
Liu, Y., Ding, Q., Xiong, W., and Yan, Q. (2023). Numerical investigation on atomization characteristics of sustainable aviation biofuel. AIP Adv. 13 (10). doi:10.1063/5.0148811
Lobo, P., Hagen, D. E., and Whitefield, P. D. (2011). Comparison of PM emissions from a commercial jet engine burning conventional, biomass, and fischer–tropsch fuels. Environ. Sci. Technol. 45 (24), 10744–10749. doi:10.1021/es201902e
Lobo, P., Rye, L., Williams, P. I., Christie, S., Uryga-Bugajska, I., Wilson, C. W., et al. (2012). Impact of alternative fuels on emissions characteristics of a gas turbine engine – Part 1: gaseous and particulate matter emissions. Environ. Sci. Technol. 46 (19), 10805–10811. doi:10.1021/es301898u
Mahesh, D., Ahmad, S., Kumar, R., Chakravarthy, S. R., and Vinu, R. (2021). Hydrothermal liquefaction of municipal solid wastes for high quality bio-crude production using glycerol as co-solvent. Bioresour. Technol. 339, 125537. doi:10.1016/j.biortech.2021.125537
Mariappan, M., Panithasan, M. S., and Venkadesan, G. (2021). Pyrolysis plastic oil production and optimisation followed by maximum possible replacement of diesel with bio-oil/methanol blends in a CRDI engine. J. Clean. Prod. 312, 127687. doi:10.1016/j.jclepro.2021.127687
Martinez-Valencia, L., Garcia-Perez, M., and Wolcott, M. P. (2021). Supply chain configuration of sustainable aviation fuel: review, challenges, and pathways for including environmental and social benefits. Renew. Sustain. Energy Rev. 152, 111680. doi:10.1016/j.rser.2021.111680
Mayer, A. (2022). Fossil fuel dependence and energy insecurity. Energy, Sustain. Soc. 12 (27), 27. doi:10.1186/s13705-022-00353-5
Meadows, A. L., Hawkins, K. M., Tsegaye, Y., Antipov, E., Kim, Y., Raetz, L., et al. (2016). Rewriting yeast central carbon metabolism for industrial isoprenoid production. Nature 537 (7622), 694–697. doi:10.1038/nature19769
Melo, L. C. A., Lehmann, J., Carneiro, J. S. D. S., and Camps-Arbestain, M. (2022). Biochar-based fertilizer effects on crop productivity: a meta-analysis. Plant Soil 472 (1-2), 45–58. doi:10.1007/s11104-021-05276-2
Metzger, D. F., Klahn, C., and Dittmeyer, R. (2023). Downsizing sustainable aviation fuel production with additive manufacturing—an experimental study on a 3D printed reactor for fischer-tropsch synthesis. Energies 16 (19), 6798. doi:10.3390/en16196798
Michailos, S. (2018). Process design, economic evaluation and life cycle assessment of jet fuel production from sugar cane residue. Environ. Prog. Sustain. Energy 37 (3), 1227–1235. doi:10.1002/ep.12840
Ng, K. S., Farooq, D., and Yang, A. (2021). Global biorenewable development strategies for sustainable aviation fuel production. Renew. Sustain. Energy Rev. 150, 111502. doi:10.1016/j.rser.2021.111502
Ng, K. S., and Sadhukhan, J. (2011). Techno-economic performance analysis of bio-oil based Fischer-Tropsch and CHP synthesis platform. Biomass Bioenergy 35 (7), 3218–3234. doi:10.1016/j.biombioe.2011.04.037
Oehmichen, K., Majer, S., Müller-Langer, F., and Thrän, D. (2022). Comprehensive LCA of biobased sustainable aviation fuels and JET A-1 multiblend. Appl. Sci. 12 (7), 3372. doi:10.3390/app12073372
Okolie, J. A., Awotoye, D., Tabat, M. E., Okoye, P. U., Epelle, E. I., Ogbaga, C. C., et al. (2023). Multi-criteria decision analysis for the evaluation and screening of sustainable aviation fuel production pathways. iScience 26, 106944. doi:10.1016/j.isci.2023.106944
O’Malley, J., Pavlenko, N., and Searle, S. (2021). Estimating sustainable aviation fuel feedstock availability to meet growing European Union demand. Int. Counc. Clean Transp.
ONECLICKLCA (2023). Impact assessment categories. CML, TRACI and PEF. Available at: https://oneclicklca.zendesk.com/hc/en-us/articles/360015036980-Impact-Assessment-Categories-CML-TRACI-and-PEF (January 18, 2024).
Peters, J. F., Iribarren, D., and Dufour, J. (2015). Life cycle assessment of pyrolysis oil applications. Biomass Convers. Biorefinery 5, 1–19. doi:10.1007/s13399-014-0120-z
Peters, M. A., Alves, C. T., and Onwudili, J. A. (2023). A review of current and emerging production technologies for biomass-derived sustainable aviation fuels. Energies 16 (6100), 6100. doi:10.3390/en16166100
Pipitone, G., Zoppi, G., Pirone, R., and Bensaid, S. (2023). Sustainable aviation fuel production using in-situ hydrogen supply via aqueous phase reforming: a techno-economic and life-cycle greenhouse gas emissions assessment. J. Clean. Prod. 418, 138141. doi:10.1016/j.jclepro.2023.138141
Putun, A. E., Apaydin, E., and Putun, E. (2004). Rice straw as a bio-oil source via pyrolysis and steam pyrolysis. Energy 29, 2171–2180. doi:10.1016/j.energy.2004.03.020
Ritchie, H. (2024). Climate change and flying: what share of global CO2 emissions come from aviation? Available at: https://ourworldindata.org/co2-emissions-from-aviation (January 06, 2024).
Ritchie, H., Rosado, P., and Roser, M. (2020). Greenhouse gas emissions. Available at: https://ourworldindata.org/greenhouse-gas-emissions (January 06, 2024).
Rjeily, M. A., Gennequin, C., Pron, H., Abi-Aad, E., and Randrianalisoa, J. H. (2021). Pyrolysis-catalytic upgrading of bio-oil and pyrolysis-catalytic steam reforming of biogas: a review. Environ. Chem. Lett. 19 (4), 2825–2872. doi:10.1007/s10311-021-01190-2
Robota, H. J., Alger, J. C., and Shafer, L. (2013). Converting algal triglycerides to diesel and HEFA jet fuel fractions. Energy and Fuels 27 (2), 985–996. doi:10.1021/ef301977b
Rogachuk, B. E., and Okolie, J. A. (2024). Comparative assessment of pyrolysis and Gasification-Fischer Tropsch for sustainable aviation fuel production from waste tires. Energy Convers. Manag. 302, 118110. doi:10.1016/j.enconman.2024.118110
Romero-Izquierdo, A. G., Gómez-Castro, F. I., Gutiérrez-Antonio, C., Hernández, S., and Errico, M. (2021). Intensification of the alcohol-to-jet process to produce renewable aviation fuel. Chem. Eng. Process. Process Intensif. 160 (108270), 108270. doi:10.1016/j.cep.2020.108270
Santos, R. G. D., and Alencar, A. C. (2020). Biomass-derived syngas production via gasification process and its catalytic conversion into fuels by Fischer Tropsch synthesis: a review. Int. J. Hydrogen Energy 45 (36), 18114–18132. doi:10.1016/j.ijhydene.2019.07.133
Sauciuc, A., Abosteif, Z., Weber, G., Potetz, A., Rauch, R., Hofbauer, H., et al. (2012). Influence of operating conditions on the performance of biomass-based Fischer–Tropsch synthesis. Biomass Convers. Biorefinery 2 (3), 253–263. doi:10.1007/s13399-012-0060-4
Schripp, T., Anderson, B. E., Bauder, U., Rauch, B., Corbin, J. C., Smallwood, G. J., et al. (2022). Aircraft engine particulate matter emissions from sustainable aviation fuels: results from ground-based measurements during the NASA/DLR campaign ECLIF2/ND-MAX. Fuel 325, 124764. doi:10.1016/j.fuel.2022.124764
Seber, G., Escobar, N., Valin, H., and Malina, R. (2022). Uncertainty in life cycle greenhouse gas emissions of sustainable aviation fuels from vegetable oils. Renew. Sustain. Energy Rev. 170, 112945. doi:10.1016/j.rser.2022.112945
Shahriar, M. F., and Khanal, A. (2022). The current techno-economic, environmental, policy status and perspectives of sustainable aviation fuel (SAF). Fuel 325, 124905. doi:10.1016/j.fuel.2022.124905
SHELL (2024). BIOMASS TO FUELS: IH2 COMMERCIAL PROCESS OPTIMISATION. Available at: https://www.shell.com.cn/en_cn/business-customers/catalysts-technologies/licensed-technologies/benefits-of-biofuels/ih2-technology/process-optimisation.html# (January 18, 2024).
Singh, A., and Olsen, S. I. (2011). A critical review of biochemical conversion, sustainability and life cycle assessment of algal biofuels. Appl. Energy 88 (10), 3548–3555. doi:10.1016/j.apenergy.2010.12.012
Stachler, R., Heyne, J., Stouffer, S., and Miller, J. (2020). Lean blowoff in a toroidal jet-stirred reactor: implications for alternative fuel approval and potential mechanisms for autoignition and extinction. Energy and Fuels 34 (5), 6306–6316. doi:10.1021/acs.energyfuels.9b01644
STATISTA RESEARCH DEPARTMENT (2023). Global air traffic - scheduled passengers 2004-2022. Available at: https://www.statista.com/statistics/564717/airline-industry-passenger-traffic-globally/ (January 06, 2024).
Suriapparao, D. V., Vinu, R., Shukla, A., and Haldar, S. (2020). Effective deoxygenation for the production of liquid biofuels via microwave assisted co-pyrolysis of agro residues and waste plastics combined with catalytic upgradation. Bioresour. Technol. 302, 122775. doi:10.1016/j.biortech.2020.122775
Tanzil, A. H., Brandt, K., Wolcott, M., Zhang, X., and Garcia-Perez, M. (2021a). Strategic assessment of sustainable aviation fuel production technologies: yield improvement and cost reduction opportunities. Biomass Bioenergy 145, 105942. doi:10.1016/j.biombioe.2020.105942
Tanzil, A. H., Brandt, K., Zhang, X., Wolcott, M., Stockle, C., and Garcia-Perez, M. (2021b). Production of sustainable aviation fuels in petroleum refineries: evaluation of new bio-refinery concepts. Front. Energy Res. 9, 735661. doi:10.3389/fenrg.2021.735661
Teoh, R., Schumann, U., Voigt, C., Schripp, T., Shapiro, M., Engberg, Z., et al. (2022). Targeted use of sustainable aviation fuel to maximize climate benefits. Environ. Sci. Technol. 56 (23), 17246–17255. doi:10.1021/acs.est.2c05781
THE BUSINESS AVIATION COALITION FOR SUSTAINABLE AVIATION FUEL (2020). Fuelling the future sustainable aviation fuel guide. Bus. Aviat. Coalition Sustain. Aviat. Fuel.
Tijmensen, M. J. A., Faaij, P. C., Hamelinck, C. N., and van Hardeveld, M. R. M. (2002). Exploration of the possibilities for production of Fischer Tropsch liquids and power via biomass gasification. Biomass Bioenergy 23, 129–152. doi:10.1016/s0961-9534(02)00037-5
Tzanetis, K. F., Posada, J. A., and Ramirez, A. (2017). Analysis of biomass hydrothermal liquefaction and biocrude-oil upgrading for renewable jet fuel production: the impact of reaction conditions on production costs and GHG emissions performance. Renew. Energy 113, 1388–1398. doi:10.1016/j.renene.2017.06.104
UK production capacity outlook to 2030 (2024). Department for transport in partnership with TRL, temple and scarlett research.
Undavalli, V., Olatunde, O. B. G., Boylu, R., Wei, C., Haeker, J., Hamilton, J., et al. (2023). Recent advancements in sustainable aviation fuels. Prog. Aerosp. Sci. 136, 100876. doi:10.1016/j.paerosci.2022.100876
Vardon, D. R., Sherbacow, B. J., Guan, K., Heyne, J. S., and Abdullah, Z. (2022). Realizing ''net-zero-carbon'' sustainable aviation fuel. Joule 6, 16–21. doi:10.1016/j.joule.2021.12.013
Vogel, K. P., and Jung, H. G. (2001). Genetic modification of herbaceous plants for feed and fuel. Crit. Rev. Plant Sci. 20 (1), 15–49. doi:10.1016/s0735-2689(01)80011-3
Walls, L. E., and Rios-Solis, L. (2020). Sustainable production of microbial isoprenoid derived advanced biojet fuels using different generation feedstocks: a review. Front. Bioeng. Biotechnol. 8, 599560. doi:10.3389/fbioe.2020.599560
Wang, C., Venderbosch, R., and Fang, Y. (2018). Co-processing of crude and hydrotreated pyrolysis liquids and VGO in a pilot scale FCC riser setup. Fuel Process. Technol. 181, 157–165. doi:10.1016/j.fuproc.2018.09.023
Wang, J., Bi, P., Zhang, Y., Xue, H., Jiang, P., Wu, X., et al. (2015). Preparation of jet fuel range hydrocarbons by catalytic transformation of bio-oil derived from fast pyrolysis of straw stalk. Energy 86, 488–499. doi:10.1016/j.energy.2015.04.053
Wang, W. (2016). Techno-economic analysis of a bio-refinery process for producing Hydro-processed Renewable Jet fuel from Jatropha. Renew. Energy 95, 63–73. doi:10.1016/j.renene.2016.03.107
Wang, W., Zhong, Z., Liu, Q., Xiang, Z., Yang, Y., Pan, X., et al. (2023). Process simulation and environmental impact assessment of different cases in hydrothermal catalytic bio-jet fuel production. Biomass Convers. Biorefinery. doi:10.1007/s13399-023-04403-6
Xu, B., Kolosz, B. W., Andresen, J. M., Ouenniche, J., Greening, P., Chang, T. S., et al. (2019). Performance evaluation of alternative jet fuels using a hybrid MCDA method. Energy Procedia 158, 1110–1115. doi:10.1016/j.egypro.2019.01.275
Yang, J. H., Hwang, S. Y., Maeng, J. Y., Park, G. E., Yang, S. Y., Rhee, C. K., et al. (2024). Opening direct electrochemical fischer–tropsch synthesis path by interfacial engineering of Cu electrode with P-block elements. ACS Appl. Mater. Interfaces 16, 3368–3387. doi:10.1021/acsami.3c15596
Yang, Z., Boehm, R. C., Bell, D. C., and Heyne, J. S. (2023). Maximizing Sustainable aviation fuel usage through optimization of distillation cut points and blending. Fuel 353, 129136. doi:10.1016/j.fuel.2023.129136
Yang, Z., Xu, Z., Feng, M., Cort, J. R., Gieleciak, R., Heyne, J., et al. (2022). Lignin-based jet fuel and its blending effect with conventional jet fuel. Fuel 321, 124040. doi:10.1016/j.fuel.2022.124040
Yerrayya, A., Shree Vishnu, A. K., Shreyas, S., Chakravarthy, S. R., and Vinu, R. (2020). Hydrothermal liquefaction of rice straw using methanol as Co-solvent. Energies 13 (10), 2618. doi:10.3390/en13102618
Keywords: SAF, LCA, feedstocks, conversion processes, technical specifications
Citation: Borrill E, Koh SCL and Yuan R (2024) Review of technological developments and LCA applications on biobased SAF conversion processes. Front. Fuels. 2:1397962. doi: 10.3389/ffuel.2024.1397962
Received: 08 March 2024; Accepted: 13 June 2024;
Published: 12 July 2024.
Edited by:
Abul Kalam Hossain, Aston University, United KingdomReviewed by:
Ravikrishnan Vinu, Indian Institute of Technology Madras, IndiaVikas Sharma, University of Brighton, United Kingdom
Copyright © 2024 Borrill, Koh and Yuan. This is an open-access article distributed under the terms of the Creative Commons Attribution License (CC BY). The use, distribution or reproduction in other forums is permitted, provided the original author(s) and the copyright owner(s) are credited and that the original publication in this journal is cited, in accordance with accepted academic practice. No use, distribution or reproduction is permitted which does not comply with these terms.
*Correspondence: Eleanor Borrill, ZWxib3JyaWxsMUBzaGVmZmllbGQuYWMudWs=