- Faculty of Sustainable Design Engineering, University of Prince Edward Island, Charlottetown, PE, Canada
In the face of environmental challenges (e.g., dramatically increasing greenhouse gas emissions and climate change), it is utmost of importance to sustainable energy systems. Biomass consisting of agricultural and forest waste, municipal solid waste, and aquatics, has been identified as alternative and promising fuel sources. Thermochemical conversion approaches like pyrolysis can turn various types of biomass into three valuable product streams, namely, bio-oil, biochar, and syngas. To date, past review articles have considered the major operating parameters of kinetics, chemistry, and the application of pyrolysis products. However, ash content is one of the key biomass components that lacks investigation on its influence during biomass pyrolysis with respect to products yield and properties. This review article examines: i) the ash content and composition in different types of biomass; ii) effects of ash content on catalytic pathway and biomass thermal degradation; iii) ash related problems in the thermal degradation of biomass; and iv) available deashing techniques for biomass. The review aims to provide new understandings and insights regarding the effects of ash content and composition on biomass pyrolysis.
1 Introduction
Given the environmental impact of fossil fuels such as oil, coal, and natural gas, there is a need to develop alternative energy sources which fulfil the world’s growing energy needs. Alternative energy sources should be economical and sustainable, biomass is a promising renewable energy source. Compared to other types of sustainable energy (e.g., solar and wind), biomass is a carbon-rich energy source. Among the different types of biomass, lignocellulose including agricultural and forestry residue and energy crop has been extensively utilized as a raw materials to produce biofuels and biochemicals via different conversion technologies (M. Guo et al., 2015; Manikandan et al., 2023; Braghiroli and Passarini, 2020). Monir et al. (2022) applied a mixture of empty fruit bunches of palm oil, coconut shell, and forest waste to produce syngas along with bioethanol through a hybrid gasification and syngas fermentation. Valizadeh et al. (2022) and Li et al. (2021) turned woody sawdust and rice husk, respectively, into bio-oil (a substitute to petroleum crude oil) by pyrolysis. The main advantages of using lignocellulosic biomass as a fuel source include its abundance, carbon neutrality, and economical processing. Aside from lignocellulosic biomass, algae that belongs to the third generation of biofuels offers benefits of high biomass productivity, fast growth rate, an ability to be cultivated in wastewater or brine water, high lipid yield, and presences of valuable biochemicals (e.g., β-carotene, lutein, and astaxanthin) (Adeniyi et al., 2018). As suggested by da Rosa et al. (2023), there is a parallel drawn between algae in both energy and food markets. Algae biorefineries are used in food, chemical and energy markets.
To date, different types of biomass conversion technologies have been developed ranging from biological methods, chemical, to thermochemical methods. A summary of the main categories of biomass conversion are shown in Figure 1. Thermochemical techniques like pyrolysis could be a more effective approach for biomass processing (W. Li et al., 2017). This could be related to the inherent benefits of pyrolysis such as its ability to use a variety of feedstock; minimize environmental effects; and the co-production of bio-oil, biochar, and syngas (Osman et al., 2023). In contrast, a prolonged reaction time is needed in the biological conversion methods. For example, mesophilic anaerobic digestion typically requires 25–30 days to convert organic waste into biogas and digestate. During biological conversion, it is also significant to properly control the culture medium (e.g., pH, temperature, and the existence of inhibitory chemicals) over the entire reaction to avoid microorganism inactivity and reaction failure. Another limitation is the requirement for an additional treatment before fermentation, such as enzymatic hydrolysis or saccharification to break down big carbohydrate’s molecules into fermentable simple sugars (Awasthi et al., 2023).
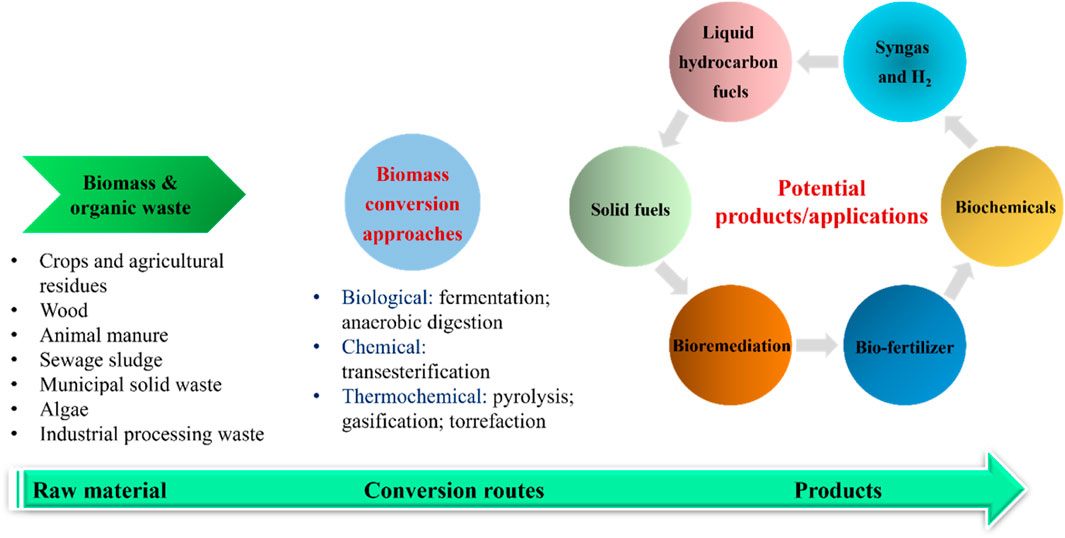
FIGURE 1. Summary of biomass conversion methods to produce value-added bioproducts and applications.
Pyrolysis is a thermochemical conversion process in an inert condition with or without the presence of a catalyst. As illustrated in Figure 1, in a typical biomass pyrolysis, biomass is initially pre-treated by size reduction, washing, and drying, and then loaded to a pyrolysis reactor (e.g., auger reactor and fluidized bed reactor). During the reaction, pyrolysis vapor is released from the volatiles fraction of biomass upon thermal degradation, followed by condensation to separate bio-oil and gaseous products (Gahane et al., 2022). Bio-oil (also called pyrolysis oil) can be used as a cleaner fuel source in boilers to replace petroleum crude oil and can also be further upgraded to hydrocarbon fuels to reduce the consumption of petroleum crude oil. Another application of bio-oil is the recovery of a wide spectrum of chemicals like phenolics, alcohols, and acids (Hu and Gholizadeh, 2020).
Due to the complexity in biomass composition and the multiphase reactions involved in the pyrolysis process, a full understanding of the associated chemical reaction pathways is challenging. Previous studies have used characteristic biomass compounds like cellulose (Hu et al., 2022; Fliri et al., 2023; Shao et al., 2023), hemicellulose (D. Chen et al., 2022; Hu et al., 2024), lignin (Folgueras et al., 2023; Genuino et al., 2023; Pienihäkkinen et al., 2023), lipid (Bartoli et al., 2021; Bartolucci et al., 2023), protein, and their monomers like glucose, xylose, phenol (Lago et al., 2022; Cruz-Reina et al., 2023), and amino acids in either individual, binary, or tertiary systems to study the underlying reaction mechanism. Past review papers have been previously reported by (Osatiashtiani et al., 2022; Al-Balushi et al., 2023; Sierra et al., 2023; Silos-Llamas et al., 2023; Xing et al., 2023). Past studies have examined the effects of reaction parameters on biomass pyrolysis with respect to products distribution and properties (Kan et al., 2016), catalyst usage (Grams et al., 2023), bio-oil upgrading (Fermoso et al., 2017), and the applications of biochar (Ghodake et al., 2021) and gaseous products (X. J. Lee et al., 2020).
Aside from organics (e.g., cellulose, hemicellulose, and lignin), biomass also contains a certain amount of inorganics. Past studies have discussed the catalytic effects of ash fraction on biomass pyrolysis by affecting the bio-oil and biochar yield and products properties. In other studies, it was found that the presence of ash in bio-oil helped reduce NOx emissions upon combustion and lower the number of O-containing functional groups in bio-oil (Kim et al., 2021; Wang et al., 2021). Moreover, ash fraction present in biomass often leads to slagging, fouling, bed agglomeration, and corrosion problems during the biomass thermal degradation including pyrolysis. Most previous studies focused on the ash-related properties in biomass combustion (Vassilev et al., 2014; L; Wang et al., 2012; Nunes et al., 2016; Niu et al., 2016) and potential applications of biomass ash in concrete manufacturing and agriculture (Pode, 2016; Silva et al., 2019; Olatoyan et al., 2023). However, to the best of our knowledge, past literature has not examined the influence of ash content and composition on biomass pyrolysis in terms of products yield and properties.
Therefore, in this review article, i) the ash content and composition in different types of biomass including agricultural waste, forestry waste, municipal solid waste, and aquatic biomass, will be examined; ii) the effects of ash content on catalytic pathway and biomass thermal degradation will be reported; iii) ash related problems including slagging, sintering, fouling, bed agglomeration, and corrosion, will also be reviewed; and iv) lastly, deashing techniques covering biological processes, acid leaching, and additives addition, will be investigated.
2 Ash content and composition in different types of biomass
To evaluate the ash’s effect on biomass pyrolysis, it is important to understand the content and main composition of ash fraction of commonly used types of biomass in pyrolysis. This is helpful for selecting the appropriate type of biomass for pyrolysis and deciding on whether a deashing pre-treatment is needed. In general, the ash fraction present in different sources, ranging from agriculture, forestry, to municipal, exhibits variations in the content and chemical composition. These differences occur due to geographical location, local ecosystem, cultivation conditions, as well as the surrounding environment.
Ash usually contains alkali and alkaline earth metals (AAEMs), heavy metals, non-metals, and other elements. Their composition and reactivity affect the thermal degradation pathway of biomass. The alkali salts present in the ash fraction of biomass could either act as catalysts or inhibit the thermal degradation of major biomass biomolecules (Changi et al., 2015). The minerals present in the ash could be bound onto an organic matrix of the biomass by substituting with acidic H atoms in the carboxylic acid or phenolic groups and then subsequently form salts (Nik-Azar et al., 1997).
In general, ash is composed of both major and minor mineral elements. Major mineral elements include titanium (Ti), phosphorus (P), aluminium (Al), potassium (K), iron (Fe), calcium (Ca), magnesium (Mg), and silicon (Si), while minor mineral elements include nickel (Ni), molybdenum (Mo), mercury (Hg), copper (Cu), chromium (Cr), cadmium (Cd), barium (Ba), vanadium (V), and zinc (Zn). In comparison, the existence of major mineral elements results in ash fouling and corrosion towards process equipment. By comparison, the particle emission is primarily caused by minor mineral elements.
Biomass can be classified into i) high ash-containing biomass (ash wt% > 10 wt%), ii) medium ash-containing biomass (ash wt% = 5–10 wt%), and iii) low ash-containing biomass (ash wt% < 5 wt%) (Stella Mary et al., 2016). In the following sections, the ash content and composition of the commonly used types of biomass in pyrolysis, including agricultural waste, forestry waste, municipal solid waste, and aquatic biomass, will be discussed.
2.1 Agricultural waste
Agricultural waste is usually the result of harvesting on the farms and slaughterhouses. Examples of agricultural waste include rice husk, corn straw, sugarcane bagasse, hazelnut glume, and pistachio shell. Slaughterhouse waste is another stream of agricultural waste and includes the animal waste generated from the slaughtering process. Other examples of slaughterhouse waste are feathers, hatchery waste, blood, bedding material, shell, and animal litter (Muduli et al., 2018).
In a detailed study by Melikoglu et al. (2023), the ash content in orange filter cake, pomegranate filter cake, corn stalk, sugarcane bagasse, olive pomace, hazelnut glume, hazelnut shell, poplar branch, walnut shell, and pistachio shell was measured. The results are summarized in Table 1. It can be observed that all tested agricultural waste had either a medium or a low level of ash content, based on the category of ash content. Bagasse, hazelnut shell, walnut shell, pistachio shell, orange filter cake, pomegranate filter cake and poplar branch were found to be lower in ash content than other agricultural waste. Olive pomace, hazelnut glume and corn stalk fell into the medium ash content group.
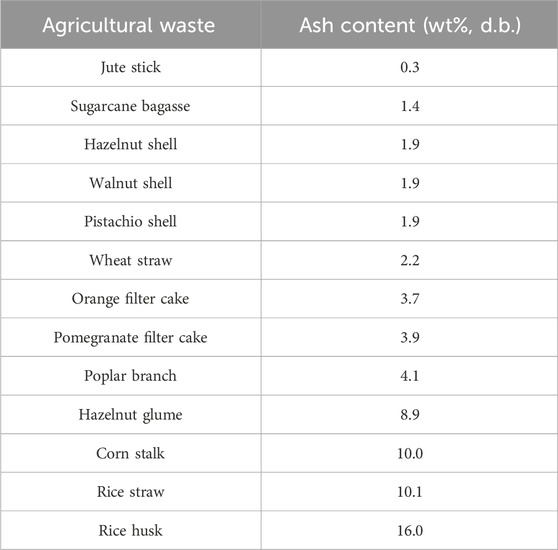
TABLE 1. Summary of ash content in different forms of agricultural waste (Islam et al., 2021; Melikoglu et al., 2023).
Islam et al. (2021) showed that the ash content of rice husk, rice straw, jute stick, and wheat straw was determined to be 16 wt%, 10.19 wt%, 0.3 wt%, 2.21 wt%, respectively. Rice husk was found to contain the highest amount of ash (i.e., 16 wt%). Such a high ash content could lead to a series of industrial machinery problems such as fouling, sintering, slag deposition, and agglomeration, and a detailed explanation is provided in Section 4. Therefore, ash removal from rich husk might be necessary prior to pyrolysis or other thermochemical conversion methods.
In addition to the total ash content, the detailed chemical composition of ash fraction present in the biomass is another critical factor affecting the subsequent biomass thermal degradation by pyrolysis. The ash composition of various types of agricultural waste has been explored in other previous studies. A summary of the ash composition of different agricultural waste is provided in Table 2. As shown in Table 2, corn straw contained the highest ash content (7.7 wt%) compared to other agricultural waste. The most dominant species in the ash fraction of corn straw were SiO2, CaO, and K2O. This also occurs for other agricultural waste such as Miscanthus grass, sweet sorghum grass, and barley straw.
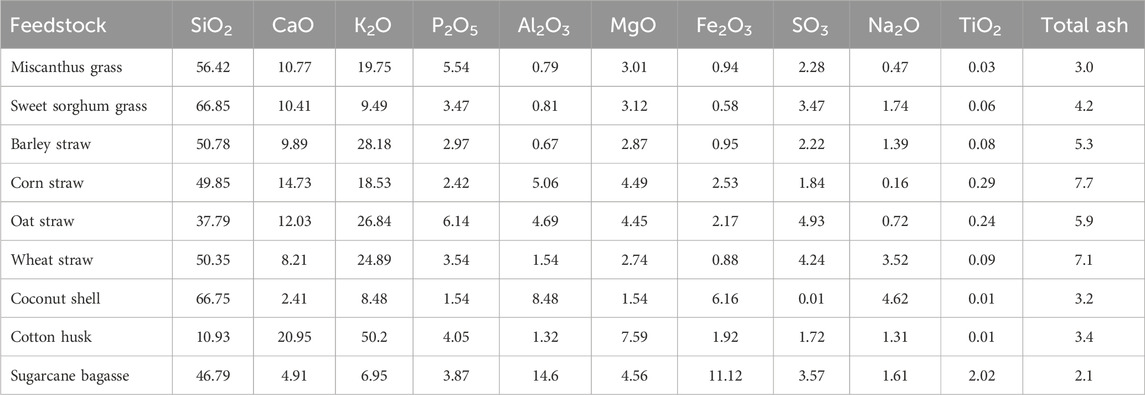
TABLE 2. Summary of ash composition in agricultural waste (wt%, d.b.) (Vassilev et al., 2010).
In the following section, the effect of such chemical species on biomass degradation and product distribution is discussed. In recent studies, the ash fraction derived from agricultural waste has been valorized into value-added bioproducts. Shen (2017) discussed the potential of using silica derived from rice husk for soil remediation, pollutant removal, and fabrication of silicon materials.
2.2 Forestry waste
Forestry waste is derived generally from deforestation and wildfires, including soft and hard stems, branches, foliage, barks, chips, lumps, pellets, sawdust, and other various wood species (Vassilev et al., 2010). Compared to agricultural waste, woody biomass is a more common feedstock used in pyrolysis for fuel generation. The ash content in forestry waste is usually much lower than that present in agricultural waste. Tables 3, 4 shows the ash content and composition identified in forestry residue.
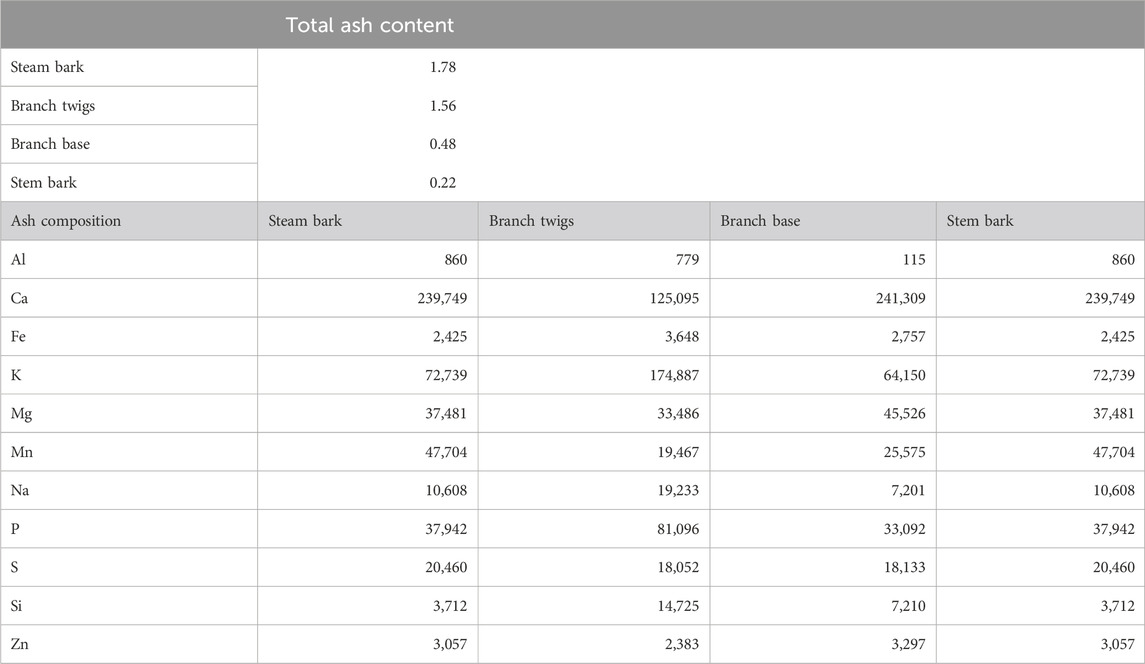
TABLE 3. Total ash content (wt%, dry basis) and ash composition (mg/kg, dry basis) of woody biomass (Dibdiakova et al., 2015).
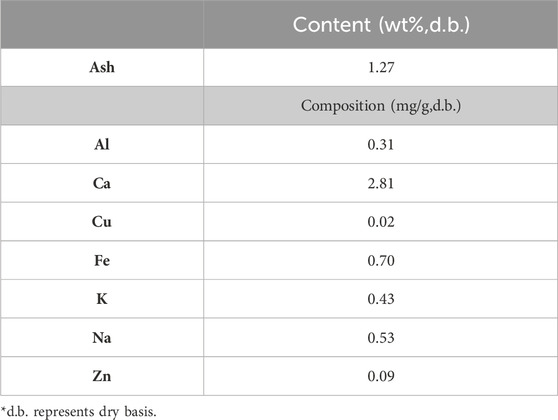
TABLE 4. Ash composition derived from forest residue biomass (Bosch et al., 2022).
Table 3 indicates that the dominant species in the ash fraction of woody biomass (i.e., Pinus Sylvestris) are Ca, K, Mg, Mn, P, and Si. In particular, the content of K, Na, and P in the twigs were observed to be considerably higher than those in the steam wood, bark, and branch. Stem bark contained the highest amount of ash content (1.78 wt%). This result could lead to unwanted ash melting and slagging when using twigs in the boiler or furnace (Dibdiakova et al., 2015).
The ash content and composition derived from forest residue has also been studied by Bosch et al. (2022). The forest residue was derived from a local wood processing facility and was a mixture of sapwood, bark, tops, and branches. The results are shown in Table 4. An amount of 1.27 wt% of ash content was found. This ash fraction primarily was composed of Al, Ca, Cu, Fe, K, Na, and Zn. Compared to Table 3, the differences in ash composition between two forest residues could be caused by the differences in the type of wood, soil quality used to grow the wood, as well as the wood cultivation conditions.
2.3 Municipal solid waste
Generally, municipal solid waste (MSW) comes from three major sources, namely, construction, industrial, and commercial sources. Examples of MSW include paper waste, paper scraps, boxes, broken glassware, light bulbs, ash, leather elements, textiles, toxic substances (e.g., paints, batteries), and hazardous solid waste (e.g., sanitary napkins and used syringes) (Islam et al., 2021). The inappropriate treatment of MSW like incineration and a landfill results in a substantial amount of greenhouse gas emissions (Chen et al., 2022; Nair et al., 2023).
Recent studies have used pyrolysis to treat MSW and valorise this organic waste into value-added bioproducts like bio-oil and biochar. Previously, Sotoudehnia et al. (2020) turned waste corrugated cardboard into biochar and bio-oil by pyrolysis at 350°C–450°C with a feed rate of 0.5 kg/h. Lim et al. (2022) co-pyrolyzed plastics and food mixtures for producing bio-oil under flue gas conditions. The content of ash in different types of MSW has been previously measured by Islam et al. (2021), as shown in Table 5. It can be found that the ash content was in the range of 0.23–3.28 wt%. Among the investigated feedstocks, tire waste was observed to contain the highest ash content of 3.28 wt%.
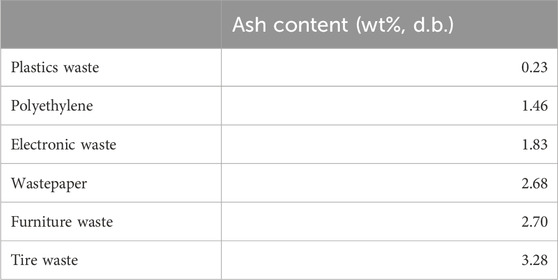
TABLE 5. Ash content in various municipal waste (Islam et al., 2021).
Table 6 shows the chemical composition of MSW’s ash fraction. It was found that alkali metals are formed with metal oxides where Al2O3 was found to be present in the largest quantity. When compared to agricultural waste (Table 1) and woody biomass (Table 3), a higher ash content can be found in the MSW (i.e., 27 wt%). Specifically, MSW contains a significantly higher content of ash that of woody biomass. An ash content of 1.27 wt% is present in forest residue derived from a mixture of sapwood, bark, tops, and branches (Table 4).
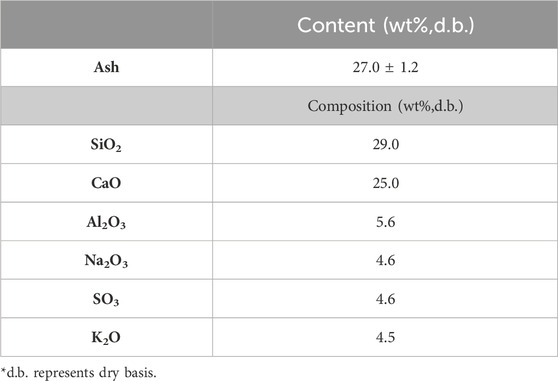
TABLE 6. Composition of municipal solid waste (Márquez et al., 2023).
2.4 Aquatic biomass
Researchers have found that aquatic plants can be an excellent resource for renewable energy production, due to comparatively high productivity compared land-grown plants, and land which is not required in the cultivation stage and hence without competition between food and fuel production (Miranda et al., 2017).
It was found that water hyacinth has a growing rate at 100 dry tonnes/(ha∙year) while switchgrass (i.e., one type of energy crop) only produces about 25 dry tonnes/(ha∙year) (Wullschleger et al., 2010). Together with a tailorable biosynthesis pathway, algae could be another promising feedstock for producing biofuels and biochemicals by pyrolysis (Banerjee et al., 2020; X; Wang et al., 2022). The ash content and composition of different algae species are summarized in Tables 7, 8 respectively. As indicated in Table 7, the different species resulted in a variation in the ash content. The ash fraction in the algae strains ranged from 5.4 wt% to 17.0 wt%. The highest ash content of 17 wt% was observed in the Phaeodactylum tricornutum.
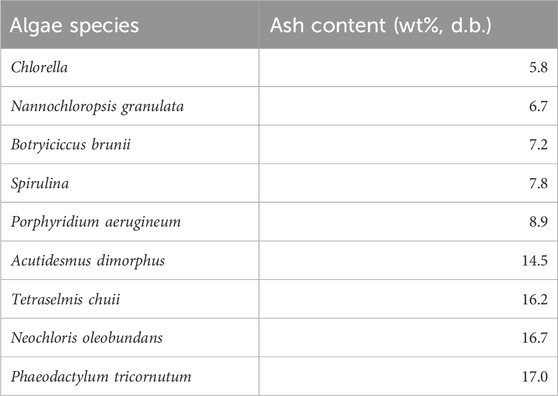
TABLE 7. Total ash content of algae (Tibbetts et al., 2015).
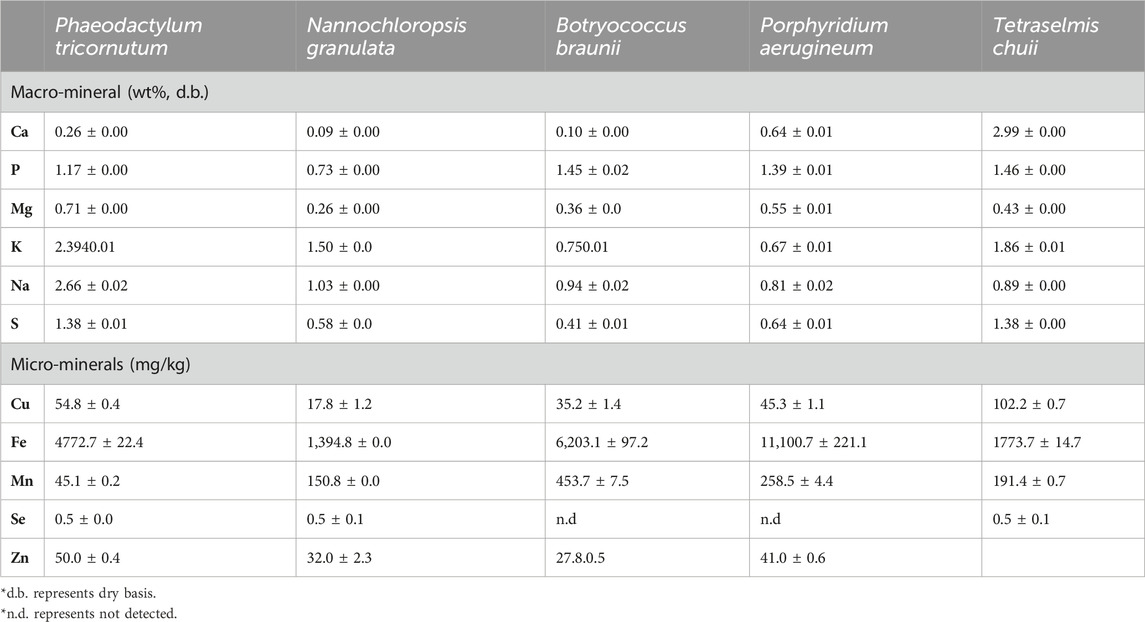
TABLE 8. Ash composition of different algae species (Tibbetts et al., 2015).
Tibbetts et al. (2015) examined the micro and micromineral content of various algae species. Results showed that Ca varied in the range of 0.26–2.99 wt% and P was found to lie in the range of 0.73–1.46 wt%. It can be observed that Na content was found to be one of the highest amongst other macronutrients with a range of 0.81%–2.66%. S varied between 0.41 and 1.38 wt%. The presence of such nutrients in the algae is primarily due to the fact that nutrients are one of the key elements in the algae cultivation stage, and thus the nutrients will be uptake by algae.
Overall, it can be observed that forestry residue contains the lowest ash content when compared with agricultural waste, municipal solid waste, and aquatic biomass, as illustrated in Table 9 To reduce the operational challenges associated with high ash content, woody biomass can be a more suitable feedstock than other types in thermal degradation treatment. In the following sections, the influences of ash content and particular ash composition on catalytic pathways and biomass thermal degradation during pyrolysis treatment are reviewed.
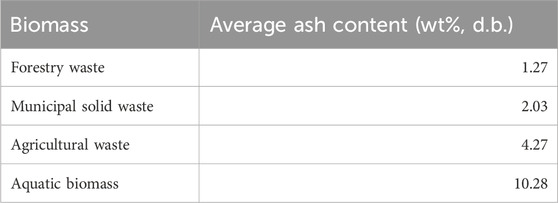
TABLE 9. Average value of ash content of four types of biomass (average value based on past literature).
3 Effects of ash content on catalytic pathway and biomass thermal degradation
Ash has shown significant effects on various thermochemical conversion methods including pyrolysis, in terms of the reaction pathways and products distribution and properties. From past literature, ash content/composition primarily affects pyrolysis with respect to i) the reaction rate; ii) bio-oil yield and properties; iii) composition of biochar; and iv) the total biomass conversion (Antal, 1983; Scott et al., 2001; Wright et al., 2010; Bridgwater, 2012; Mayer et al., 2012; Carpenter et al., 2014).
3.1 General description of ash fraction
As earlier mentioned in Section 2, ash usually contains alkali and alkaline earth metals (AAEMs), heavy metals, non-metals, and other elements. This section will discuss the general impact of ash fraction on biomass thermal degradation and pyrolysis products yield and properties by categorizing the ash fraction into alkali metals, alkaline earth metals, heavy metals, non-metals, and other elements.
3.1.1 Alkali metals
consist of Li, Na, K, Rb, Cs, and Fr, which have their outermost electron in an s-orbital. They are highly reactive at standard temperature and pressure (STP) and exist as shiny and soft. Among them, K and Na are considered the most critical species in the ash fraction of biomass, causing unwanted reactions. Upon biomass thermal degradation, these alkali metals are evaporated and then form aerosols such as KOH, KCl, K2SO4, NaCl, and Na2SO4 in the gas phase. The resulting aerosols could lead to the formation of ash agglomeration and slag (Mlonka-Medrala et al., 2020). The detailed effects of K and Na on biomass thermal degradation and bio-oil production are discussed below.
⁃ K: In a thermal degradation study of lignin, K induced a catalytic effect. Past literature also suggests that K is responsible for a high biochar yield but a low yield of tar. Tar is typically the heavy fraction of bio-oil. Lastly, several studies have observed that K hinders the depolymerization process of main biomass components (Scott et al., 2001; Patwardhan et al., 2010; Mohan et al., 2006; Mourant et al., 2011; Thy et al., 2013; Carpenter et al., 2014).
⁃ Na: It is known for high biochar production even with a smaller Na concentration (i.e., down to a few ppm) in the raw material, along with a lower yield and quality of bio-oil. This observation could result from the Na-induced secondary cracking of pyrolysis vapor and thus exhibits an adverse impact on bio-oil formation (Patwardhan et al., 2010; Bridgwater, 2012; Radlein and Quignard, 2013; Thy et al., 2013; Carpenter et al., 2014).
3.1.2 Alkaline earth metals
Include Be, Mg, Ca, Sr, Ba, and Ra, which lies in the group 2 of the periodic table. They are less reactive at STP compared to alkali metals and exist as shiny and slivery-white. For alkaline earth metals detected in the biomass ash, Ca and Mg have been reported to be the primarily reactive elements (Mlonka-Medrala et al., 2020; Yu et al., 2021).
⁃ Ca and Mg: One previous study has reported that the catalytic effect of Ca and Mg on thermal degradation of lignin is minor. In particular, they led to a lower tar and higher biochar yield (Patwardhan et al., 2010; Radlein and Quignard, 2013; Thy et al., 2013; Carpenter et al., 2014). In particular, Yip et al. (2010) observed that Ca and two alkali metals (i.e., K and Na) were retained in the biochar product and all demonstrated catalytic activity during biomass thermal degradation. The order of catalytic performance was K>Na>Ca.
3.1.3 Heavy metals
Are characterized by relatively high densities, atomic weights, or atomic numbers. Some heavy metals identified in the ash fraction of biomass are listed below. Fe is one of the heavy metals identified in the biomass ash and exists in the form of Fe2O3 (Mlonka-Medrala et al., 2020). Pb is another type of heavy metal that could be present in the biomass since it can be incorporated into biomass during the growth period. Past literature found that Demol Timber and sewage sludge contained a Pb content of 6,300 mg/kg and 150 mg/kg, respectively (Nzihou and Stanmore, 2013).
⁃ Fe: It has shown to increase the rate of reaction of cellulosic degradation (Radlein and Quignard, 2013; Thy et al., 2013; Carpenter et al., 2014), which in turn causes an increase in the biomass conversion and the bio-oil yield.
⁃ Pb: A possible catalytic influence of Pb has been reported by several researchers. In the thermal degradation of cellulose and lignin, its presence leads to the demineralization of cellulose and lignin (Obernberger and Biedermann, 2002; Thy et al., 2013; Carpenter et al., 2014).
3.1.4 Non-metal elements
Elements that mostly do not exhibit metallic properties, such as H, He, and N. They have a low density, high electronegativity, and act as poor conductors for heat and electricity, unlike metals. For the category of non-metal elements, Capablo et al. (2009) summarized the content of non-metal elements like Cl and S for waste generated from agricultural, forestry, and municipal, e.g., Cl and S for mash from beer brewery, empty fruit bunch, and shea waste. Olive waste was 0.01 wt% and 0.22 wt%, 0.35 wt., % and 0.13 wt%, 0.07 wt% and 0.24 wt%, and 0.24 wt% and 0.13 wt%. Although their contents are low, the presence of such elements has demonstrated a significant impact on biomass thermal degradation. In addition, Blasing et al. (2013) observed that P is another trace element that belongs to non-metal existing in various biomass including willow, poplar, oak, pine seed shells, hazel nut shells, and almond shells.
⁃ S: typically causes catalyst deactivation. During pyrolysis, the deoxygenation reaction (i.e., one of the common chemical reactions occurring in the biomass depolymerization) is inhibited due to the formation of
⁃ Cl: The presence of Cl leads to an increase in the yield of levoglucosan (i.e., a six-carbon ring structure that is often produced from pyrolysis of cellulose); however, it could lead to the catalyst poisoning and deactivation like S element (Atadana, 2010; Shimada et al., 2008; He et al., 2010; Mohan et al., 2006; Thy et al., 2013; Bridgwater, 2012).
⁃ P: Along with the positive catalytic effect on biochar yield, it has also been found that phosphoric acid (H3PO4) promotes the coke deposition, which not only poses a threat to catalyst deactivation but also causes fouling and corrosion the process machinery (Ruddy et al., 2014).
3.1.5 Other elements
Si is a metalloid and does not belong to either metal or non-metal. As shown in Table 2, SiO2 is the most dominant species found in the ash fraction of agricultural waste. Armesto et al. (2002) also found that the main trace element in the ash fraction of rice husk was SiO2, C, K, and P, and similar results were previously reported by Fernandes et al. (2016). This chemical species has shown to have negative effects on bio-oil yield but catalyses the char formation (Bulushev and Ross, 2011; Carrier et al., 2013; Carpenter et al., 2014).
3.2 Effects of ash on products yield and properties and catalyst used in pyrolysis
In this section, the effects of ash fraction on pyrolysis products distribution and properties, and the performance of the catalyst in pyrolysis are discussed. In an experimental study conducted by Yildiz et al. (2015), the authors stated that the ash fraction affected pyrolysis process by four pathways. The catalytic thermal cracking of primary pyrolysis vapours is triggered, which leads to a significant increase in the production of gaseous products and biochar but negatively affects the bio-oil yield and properties. It reduces the molecular size of the molecules in the vapor phase owing to the promoted cracking of the pyrolysis vapor. Thirdly, those molecules with reduced size could enter and block the catalyst’s pores or channels, and consequently reduce the catalytic activity. Also, catalyst poisoning takes places due to the interaction with ash particles. An overview of the effects of ash fraction on catalysis used in the pyrolysis and products distribution and properties is displayed in Figure 2.
3.2.1 Lowering catalytic performance
Recently, catalysts have been applied either in-situ or downstream for the pyrolysis process to facilitate biomass degradation or the formation of target pyrolysis products, respectively (He et al., 2010; Dayton et al., 2015; Al-Salem et al., 2017). Past literature has suggested that the ash fraction demonstrates a negative impact on the in-situ catalytic pyrolysis. Specifically, the deposit of ash either on the surface of the catalyst or the inside of the catalyst’s porous structure leads to the catalyst deactivation since it could position the active sites of the catalysts and subsequently deactivate them (Bridgwater, 2012; Einvall et al., 2007). In particular, the presence of S and Cl elements in the ash fraction of biomass results in catalyst deactivation, as earlier mentioned in Section 3.1. Furthermore, other researchers have mentioned the ash fraction of biomass could lead to a reduction in the surface area of the catalyst (Lee et al., 2010; Song and Guo, 2012; Batista et al., 2018).
3.2.2 Products distribution and properties
In general, for pyrolysis at moderate temperatures (i.e., 400°C–600°C), the metallic species are retained in the porous structure of char particles, which can then catalyse the thermal degradation of biopolymer (Nzihou et al., 2019). Mullen and Boateng (2013) showed that above 90% of K and Na that originally present in biomass were transferred to biochar fraction during pyrolysis reaction at 550°C. Wang et al. (2021) found that ash could reduce the surface area of the biomass particles by depositing on the surface of biomass particles at a prolonged reaction time. This might limit the heat and mass transfer within the biomass particle (Naterer, 2021) and subsequently affects the biomass conversion rate and products distribution and properties. As illustrated in Figure 3, during the process of biomass thermal degradation, pyrolysis vapor is continuously released from the biomass, followed by an appropriate condensation stage. The pyrolysis vapor is consequently separated into bio-oil (condensable fraction) and gases (non-condensable fraction). Therefore, it is critical to avoid the cracking of pyrolysis vapor inside the pyrolysis reactor if high-quality yield of bio-oil is the major objective. However, alkali and alkaline earth metals (AAEMs) have been reported to be responsible for catalytic cracking and thermolysis reactions which usually take place in the pyrolysis vapour. This intensely affects the products distribution and bio-oil properties (DeGroot and Shafizadeh, 1984; Mohan et al., 2006; Shimada et al., 2008; Patwardhan et al., 2010; Eom et al., 2012; Tan et al., 2013). Patwardhan et al. (2010) observed that even an ash content of 0.5 wt% led to a variation in the yield of levoglucosan. Specifically, the authors investigated the effect of ash composition on levoglucosan yield. The influence was followed in the order of: K+ > Na+> Ca2+> Mg2+. Among the studied ash elements, K+ was found to show the strongest impact on pyrolysis of cellulose and levoglucosan yield. Richardson et al. (2015) compared different types of metallic elements (e.g., Ce, Mn, Fe, Co, Ni, Cu, and Zn) on pyrolysis product distribution obtained from eucalyptus wood at 500 °C. The results are shown in Figure 4. It was observed that all the metallic elements led to a reduced yield of bio-oil compared to metallic elements-free biomass, while no significant difference was observed among seven metallic elements with respect to bio-oil yield.
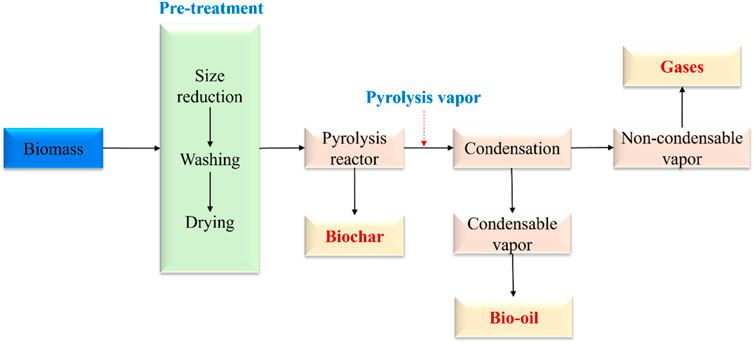
FIGURE 3. Flowchart describing biomass pyrolysis (Gahane et al., 2022).
Patwardhan et al. (2010a) and Ronsse et al. (2012), reported a lower yield of levoglucosan was found in the presence of ash. Yildiz et al. (2015) observed that the presence of ash resulted in a decrease in the yield of biochar and bio-oil by ∼ 2 wt% for each product, whereas the non-condensable gas yields increased by 4 wt%. This decrease in the bio-oil yield could be attributed to vapour cracking caused by ash. Also, it was found that ash promoted the production of H2 and CH4 for both non-catalytic and catalytic pyrolysis. This trend indicated that the ash fraction of biomass facilitates the gasification of pyrolysis vapor to form H2 and CH4. Another study by Gómez et al. (2018) reported, the phase separation of bio-oil when conducting pyrolysis at higher temperatures (i.e., 510°C–550°C). This phenomenon could be caused by the existence of K present in ash. This promoted cleavage of the glycosidic bond of cellulose via depolymerization and fragmentation, leading to the formation of low molecular weight and water-soluble molecules such acetone, acetic acid, formic acid, and hydroxy acetaldehyde. These molecules are also the commonly identified chemicals in the bio-oil. This leads to the phase separation of bio-oil. The researchers also stated that K could lead to an increased formation of phenolics compounds in bio-oil but decreasing concentration of furfurals in bio-oil (Nowakowski and Jones, 2008). K could trigger a different decomposition pathway of cellulose by decreasing anhydro sugars and furans but promoting phenols, as evidenced by GC-MS analysis. In an experimental study performed by Kim et al. (2021), it was observed that bio-oil yield decreased significantly from 45.7 wt% to 29.9 wt% as the amount of ash content increased. The study also concluded that the concentration of phenolic monomers increased from 2.8 mg/g to 20.2 mg/g in the bio-oil.
Unlike the yield of bio-oil, the influence of ash on the yield of biochar is contradictory. Yildiz et al. (2015) observed a reduction in the biochar yield. However, Shimada et al. (2008) reported an improvement in the yield of biochar, which could be due to the promoted effect of alkaline earth metals of ash, especially those existing in the form of chlorides such as MgCl2 and CaCl2. Wang et al. (2021) concluded that biochar yield decreased because of ash melting at higher pyrolysis temperatures. Further research is still needed to clearly elucidate the effects of ash on biochar yield and properties during the pyrolysis treatment. A table summarizing the major influences of ash fraction on pyrolysis of biomass is displayed in Table 10.
4 Ash related problems
Ash related problems are one of the main issues leading to the undesirable downtime of plant, as they cause instability within the operation (Sommersacher et al., 2013; Niu et al., 2019). In terms of the ash composition, the presence of K in biomass has been reported to be main cause of the ash related problems. Upon thermal degradation, K and other inorganics (e.g., P, Cl, Fe, Ca, and S) present in biomass can be released into the vapor phase and subsequently condensed and deposited on the surface of process equipment to form solid ash. Another problematic ash composition is Cl of biomass. Biomass with a high concentration of Cl could result in the formation of hydroxides and carbonates at around 800°C in the thermal conversion. This phenomenon could be attributed to the reaction between HCl and high volatile metals in the biomass at higher temperatures (Abioye et al., 2024).
The following figure illustrates the main stages involved in the ash formation and transformation during biomass thermal degradation. As indicated in Figure 5, upon thermal degradation, the volatile fraction containing metallic compounds is first released by devolatilization, and then the solid char particles are formed. A fraction of the alkali and alkaline-earth metals and volatile trace elements are diffused out of the char particles. Among them, some metallic elements like K and Na, particularly K, result in a series of ash-associated problems through nucleation, condensation, and reaction such as slagging, sintering, fouling, beg agglomeration, and corrosion (Niu et al., 2016).
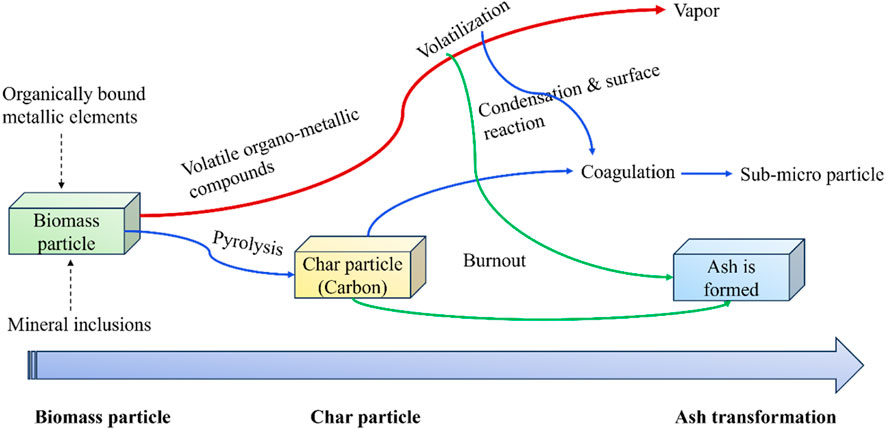
FIGURE 5. Schematic diagram to describe the main stages of ash formation upon biomass thermal degradation (Niu et al., 2016).
Past articles have limited their discussion about the ash effects on thermal degradation of biomass in a furnace or boiler for generating heat, i.e., formation mechanisms of bottom ash and fly ash, the associated challenges of bottom ash and fly ash, and the possible solution to reduce or limit bottom ash and fly ash (Tan et al., 2013; Vassilev and Vassileva, 2016; Kleinhans et al., 2018; Abioye et al., 2024). In the following sections, the formation mechanisms of each ash related challenge include slagging, sintering, fouling, corrosion, and beg agglomeration. It should be highlighted that past literature lacks discussion regarding how ash-associated problems affect the pyrolysis product yield and distribution, which could be one of the future research directions in this field.
4.1 Slagging and sintering
At operating temperatures above 1,000°C, the ash fraction of biomass turns into molten ash which is then lumped or aggregated together. The phenomena of the formation of molten ash lumps are called slagging (Bryers, 1986; Rong et al., 2017). Slagging is also related to sintering, which forms molten ash and, has glassy properties during cooling (Bryers, 1986). In a typical furnace or boiler, slag could appear on the wall of furnace and superheater, which is primarily caused by the high Cl and K content. Specifically, the presence of a high concentration of Cl in the biomass could trigger the release of K from the biomass, and then results in the formation of KCl. The resulting KCl can further condense and deposit on the surface of processing equipment by a series of mechanisms like diffusion, electrophoresis, thermophoresis, inertial impaction, and gravity. The KCl can also bond slag and later with the tube behaving like an adhesive. A schematic diagram of the slagging formation is depicted in Figure 6 (Zhu et al., 2014). Possible strategies can be applied to reduce slagging is adding additives like kaolin (Davidsson et al., 2008) and biomass pretreatment via water washing and acid pickling (Werkelin et al., 2010).
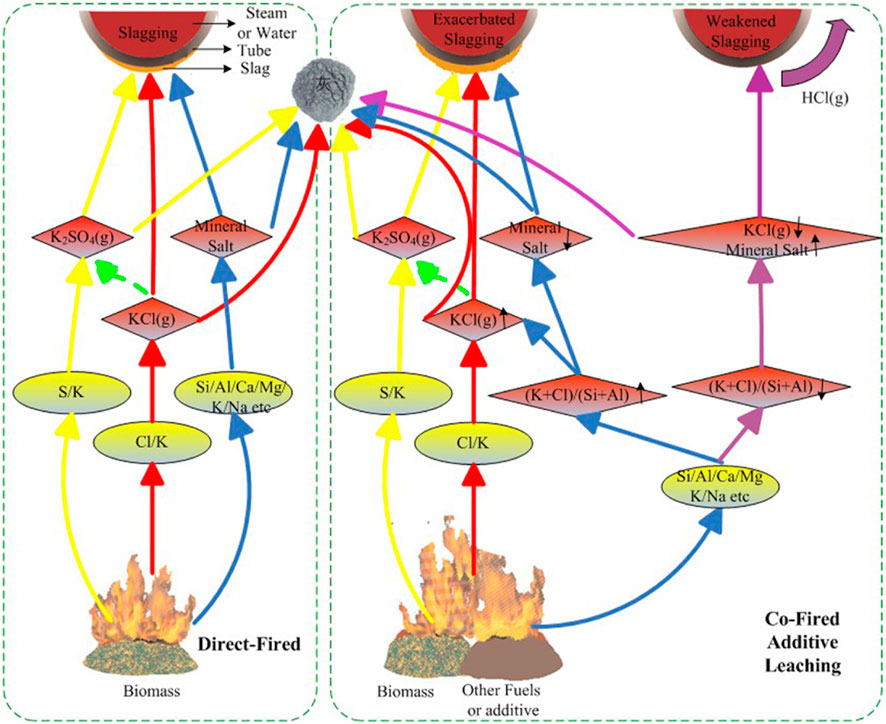
FIGURE 6. Schematic diagram illustrating the slagging formation in a biomass fired furnace/boiler (Zhu et al., 2014) (Licence: CC BY 3.0 DEED).
4.2 Fouling
Fouling refers to the deposition of non-melting ash. A portion of ash composition has a melting point that is higher than the temperature at which fouling begins. This, the portion of ash would turn into molten ash to cause slagging and sintering (Shao et al., 2012; Rong et al., 2017). Fouling could occur when ash is deposited in the convection section of the boiler, which consists of the superheater, reheater tube, economizer, and air heater. With proper removal of ash deposit, it might lead to a decrease in the furnace heat absorption but an increase in the temperature of flue gas in the boiler. This further causes issues relating to the deposit formation (Zhang, 2013). Míguez et al. (2021) reported that the ash fouling/deposition occurred in four steps: i) solid bed freed of inorganic materials; ii) the formation of aerosol; iii) the free inorganic compounds tend to travel to the surface of the process equipment; and iv) finally, the ash is deposited and accumulated on the surface.
4.3 Bed agglomeration
The fundamental chemistry in agglomeration is the formation of alkali silicate eutectics. The eutectic system is defined as a homogenous mixture that has a melting point lower than those of the components of the system. This occurs from the reaction between SiO2 in the bed materials (silica sand is a very common bed material used in the fluidized bed reactor) or ash (as earlier mentioned, SiO2 can be identified in the ash fraction of certain type of biomass) with alkali metal oxides like K2O or Na2O. The associated chemical reaction is K2O+ nSiO2 → K2O ∙ nSiO2 (where, n varies from 1 to 4) (Morris et al., 2018). The temperature at which agglomeration occurs depends on the amount of biomass ash, but typically, the temperature should be higher than 800°C (T.M. Nussbaumer, 2001; T; Nussbaumer et al., 2008). The images describing the agglomeration of bed particles during thermal degradation of high alkali biomass are shown in Figure 7 (Kittivech and Fukuda, 2020).
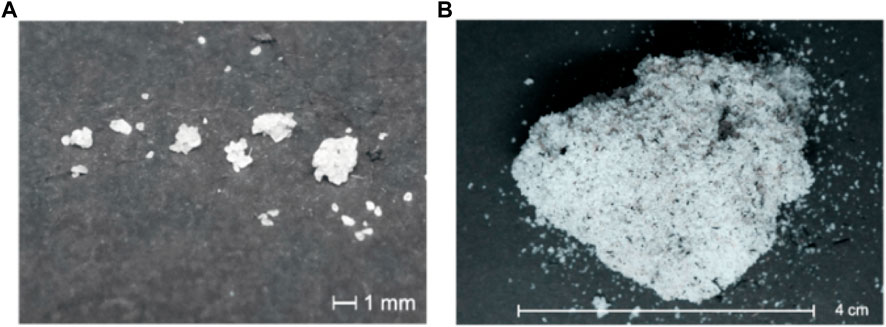
FIGURE 7. Images of bed agglomeration due to thermal degradation of high alkali biomass: (A) small agglomerate of bed particles (500–200 μm); (B) big agglomerate of large bed particles (4 cm) (Kittivech and Fukuda, 2020) (Licence: CC BY 4.0 DEED).
In recent years, the mechanisms for forming bed agglomeration caused by biomass ash include coating-triggered agglomeration and melt-triggered agglomeration. For the first coating-triggered agglomeration mechanism, Ohman et al. (2000) found that ash is initially deposited on the bed particles and a coating is created. This could result from: i) the small ash particles that attach to the bed particles, ii) the alkali elements present in ash can condense, and iii) the interaction between these alkali elements and the surface of bed particles. Afterwards, the sintering occurs at this coating and further homogenizes and strengths the coating. Finally, the severity of the agglomeration process is primarily determined by the temperature-driven adhesive force, which is controlled by the melting of this coating. Figure 8 describes this coating-triggered agglomeration mechanism for two different ash scenarios.
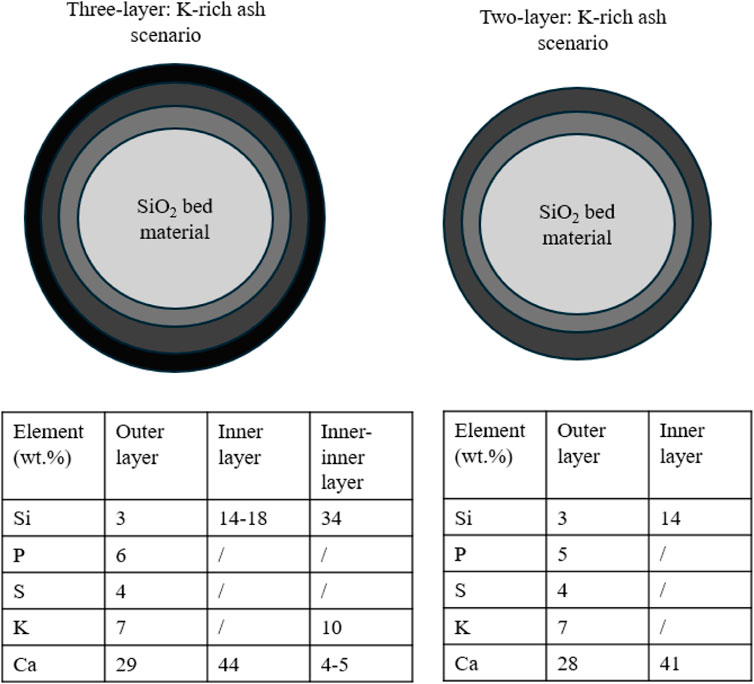
FIGURE 8. Coating-triggered mechanism for agglomeration (Morris et al., 2018).
For the second melt-triggered agglomeration mechanism, Olofsson et al. (2002) reported the temperature of some localized hot spot is above 1,000°C, which is higher than the operating temperature of ∼670°C–870°C. This results in the formation of an alkali silicate melt phase that could be originally obtained from both biomass ash and bed particle. The largest agglomerate (i.e., size of 50–60 mm) was exhibited as a glass-like form, suggesting prolonged exposure to a high temperature.
4.4 Corrosion
Corrosion refers to the phenomena of accelerated decomposition, in which ash particles containing compounds such as K2CO3, K2SO4, SiO2, KCl, NaCl and CaSO4 settle on the surface of process equipment (Konist, 2023; G; Song et al., 2018; Sanusi et al., 2022; Obot, 2021; H; Chen et al., 2017). Generally, the deposit of alkali chloride onto the superheater tubes results in corrosion towards a boiler when burning biomass and other organic waste. In addition to the corrosion issue, it can also reduce the final steam temperature and hence the boiler efficiency (Enestam et al., 2013). To limit the corrosion challenge associated with the alkali chlorides, particularly at high temperatures, Cr has been added to the Fe- and Ni-based alloys, during which protective oxide layers containing Cr2O3 can significantly limit the corrosion caused by alkali chlorides. These protective oxide layers can be broken down due to the interaction with gaseous KCl and NaCl to form K2CrO4 and Na2CrO4 (Li et al., 2007). Chemical corrosion can occur if the ash fraction encounters moisture. Galvanic corrosion can be observed when metal alloys react with ash. Furthermore, the phenomena of erosion-corrosion are found when ash damages the oxide layers on the surface of process machinery (Míguez et al., 2021; Abioye et al., 2024).
5 Deashing techniques
High ash containing biomass demonstrates several challenges when applying it as a biofuel owing to the increase in the capital and operating costs (Hess et al., 2019). Biological approaches, leaching, and adding additives have been identified as the most effective deashing treatment methods. The selection of an appropriate deashing strategy is dependent on the composition and yield of biomass ash, the type of biomass, environment and other factors (L. Wang et al., 2012; Boström et al., 2012). In general, the major factors that are taken into consideration for selecting the deashing methods include the fouling index, alkali index, slagging index and alkali ratio (Abioye et al., 2024). Different de-ashing strategies have been widely developed and adopted for coal, and have the potential to be used for biomass, as summarized in Table 11 (Dhawan and Sharma, 2019).

TABLE 11. Summary of deashing strategies that can be applied to biomass (Dhawan and Sharma, 2019).
5.1 Biological processes
Biological processes have been frequently used to remove ash from biomass. Amongst those techniques, bioleaching has been the most successful and most regularly used one. This is due to the lower utilization of chemicals and other resources (Krebs et al., 1997; Wu and Ting, 2006). In bioleaching, conversion takes place at a microbial level, to convert solid compounds into soluble chemicals, easing the following extraction and recovery stages (Krebs et al., 1997). The microorganisms involved in bioleaching are responsible for the formation of organic and inorganic acids, such as H2SO4, citric acid and gluconic acid (Krebs et al., 1997). Aspergillus niger is the most widely used microorganism (Bosshard et al., 1996; Q; Wang et al., 2009).
5.2 Leaching
For the detaching of intrinsic inorganic species, such as alkali, Cl and S from biomass, leaching is widely used (Tonn et al., 2012; Niu et al., 2016). Water and acid leaching are the most popular solvents used in the leaching as 90% of alkali metals and all alkali chlorides are water and acid soluble (Wei et al., 2019). This method is commonly used, especially when ash deposition/fouling is a problem in the process (Q. Guo et al., 2020).
According to Gudka et al. (2016), woody biomass wood can be leached using water as the leaching agent. It was seen that hot water washing led to an increase in the ash melting temperatures, i.e., an increase from 820°C to 1,400°C. The variations in the concentration of ash composition were detected. For example, Mg dropped from around 5 wt% to 60 wt%, but Na increased from 10 wt% to 90 wt% and S increased from 0 wt% to 90 wt%. Another study performed by Carrillo et al. (2014) on sorghum biomass showed that water leaching resulted in the declination of ash content of around 20% and while lignin increased up to 53%. A 0.5 M nitric acid was utilized by Feng et al. (2014) to remove ash from woody biomass (i.e., white pine bark, white spruce bark, and white birch bark) at room temperature for 8 h under stirring and a biomass/acid ratio of 1:20 (g/mL). The results indicated that acid leaching was effective in removing K from all studied biomass and a reduction in the Ca concentration was observed in the white spruce and white birch bark.
Javed (2020) applied CH3COOH, HCl, and H2SO4 to pretreat wheat straw to remove the ash fraction. It was found that acid leaching pre-treatment showed a significant impact on the thermal degradation properties of pre-treated what straw and an increase in the energy content and C content of pre-treated what straw. Jiang et al. (2013) also found that the physicochemical properties and pyrolysis characteristics of biomass can be largely dependent on the deashing pre-treatment towards biomass. Specifically, after deashing pre-treatment, the functional groups present at the surface of biomass were removed, and the emission peak of some volatile fraction of pre-treated biomass was shifted. The authors reported that alkali and alkaline earth metals demonstrated a catalytic effect on biomass pyrolysis. Hess et al. (2019) conducted a techno-economic analysis for ash removal from high ash containing microalgae. The results found that an increase in the ash content from 0 wt% to 70 wt% led to a doubling increase in the downstream capital cost.
5.3 Additives
Additives are usually added to the biomass ash with an aim of enhancing the melting temperature of ash. It is known that the additives have an impact on ash chemistry and hence the physical properties such as the melting point (Konist, 2023; L; Wang et al., 2014; Míguez et al., 2021). Some types of additives are aluminium silicate based, S-based, and P-based (G. Wang et al., 2022).
Additives are usually the best solution to deal with ash related problems as they have been shown to improve ash fusion characteristics and sequester the species, which cause problems during biomass thermal conversion (Roberts et al., 2019). Miccio et al. (2019) added fireclay and quartzite to the olive husk. The results showed that no bed agglomeration was occurred when using fireclay as the additive even at a prolonged reaction time. Another study performed by Batir et al. (2019), using kaolin as an additive, was able to sequester the formation of KCl and KOH. Two species could lead to problems in the thermal conversion of biomass, owing to the interaction with kaolin to form potassium alumina silicates. To date, kaolin has been found to be the most effective additive to remove ash from biomass, particularly KCl. The active chemical present in kaolin is kaolinite, Al2Si2O5(OH)4. It is thermally decomposed at 450°C–600°C to form meta-kaolinite (a mixture of alumina and silica and is shown as the amorphous structure) and water is also released. The resulting meta-kaolinite can react with the K species present in biomass ash to form potassium aluminium silicates possessing a high melting temperature. The associated chemical reactions are shown below, Eqs 1–9 (Abioye et al., 2024):
6 Conclusion
This review article discussed the ash content and composition identified in the most common types of biomass in pyrolysis including agricultural and forestry waste, municipal solid waste, and aquatic biomass. The effects of ash content and composition on the biomass pyrolysis with respect to the catalytic performance in the catalytic pyrolysis process and products yield and properties were reviewed. Besides, various technical challenges (e.g., slagging, sintering, fouling, bed agglomeration, and corrosion) caused by the ash fraction in the thermal conversion of biomass were reviewed, along with a description of the possible deashing methods of biological processes, leaching using water or acid, and additives addition. Overall, this review has offered new insights and understanding of the influence of ash content and composition on biomass pyrolysis, laying a useful groundwork for future research in this field.
Author contributions
LP: Writing–original draft. YH: Writing–review and editing. GN: Writing–review and editing.
Funding
The author(s) declare that financial support was received for the research, authorship, and/or publication of this article. Natural Sciences and Engineering Research Council of Canada (NSERC).
Acknowledgments
The authors are grateful for the financial support of Natural Sciences and Engineering Research Council of Canada (NSERC), i.e., RGPIN-2022-03203, Development of next-generation technologies to produce clean and renewable transportation fuels.
Conflict of interest
The authors declare that the research was conducted in the absence of any commercial or financial relationships that could be construed as a potential conflict of interest.
Publisher’s note
All claims expressed in this article are solely those of the authors and do not necessarily represent those of their affiliated organizations, or those of the publisher, the editors and the reviewers. Any product that may be evaluated in this article, or claim that may be made by its manufacturer, is not guaranteed or endorsed by the publisher.
References
Abioye, K. J., Harun, N. Y., Sufian, S., Yusuf, M., Jagaba, A. H., Ekeoma, B. C., et al. (2024a). A review of biomass ash related problems: mechanism, solution, and outlook. J. Energy Inst. 112, 101490. doi:10.1016/j.joei.2023.101490
Adeniyi, O. M., Azimov, U., and Burluka, A. (2018). Algae biofuel: current status and future applications. Renew. Sustain. Energy Rev. 90, 316–335. doi:10.1016/j.rser.2018.03.067
Al-Balushi, F. A., Burra, K. G., Chai, Y., and Wang, M. (2023). Co-pyrolysis of waste tyre and pine bark: study of reaction kinetics and mechanisms. Biomass Bioenergy 168, 106654. doi:10.1016/j.biombioe.2022.106654
Al-Salem, S. M., Antelava, A., Constantinou, A., Manos, G., and Dutta, A. (2017). A review on thermal and catalytic pyrolysis of plastic solid waste (PSW). J. Environ. Manag. 197, 177–198. doi:10.1016/j.jenvman.2017.03.084
Antal, M. J. (1983). Effects of reactor severity on the gas-phase pyrolysis of cellulose- and kraft lignin-derived volatile matter. Ind. Eng. Chem. Prod. Res. Dev. 22, 366–375. doi:10.1021/i300010a039
Armesto, L., Bahillo, A., Veijonen, K., Cabanillas, A., and Otero, J. (2002). Combustion behaviour of rice husk in a bubbling fluidised bed. Biomass Bioenergy 23, 171–179. doi:10.1016/S0961-9534(02)00046-6
Atadana, (2010). “Catalytic pyrolysis of cellulose, hemicellulose and lignin model compounds,” (Virginia: Virginia Polytechnic Institute and State University). MSc thesis.
Awasthi, M. K., Sar, T., Gowd, S. C., Rajendran, K., Kumar, V., Sarsaiya, S., et al. (2023). A comprehensive review on thermochemical, and biochemical conversion methods of lignocellulosic biomass into valuable end product. Fuel 342, 127790. doi:10.1016/j.fuel.2023.127790
Banerjee, S., Banerjee, S., Ghosh, A. K., and Das, D. (2020). Maneuvering the genetic and metabolic pathway for improving biofuel production in algae: present status and future prospective. Renew. Sustain. Energy Rev. 133, 110155. doi:10.1016/j.rser.2020.110155
Bartoli, M., Asomaning, J., Xia, L., Chae, M., and Bressler, D. C. (2021). Desulphurization of drop-in fuel produced through lipid pyrolysis using brown grease and biosolids feedstocks. Biomass Bioenergy 154, 106233. doi:10.1016/j.biombioe.2021.106233
Bartolucci, L., Cordiner, S., Mele, P., and Mulone, V. (2023). Defatted spent coffee grounds fast pyrolysis polygeneration system: lipid extraction effect on energy yield and products characteristics. Biomass Bioenergy 179, 106974. doi:10.1016/j.biombioe.2023.106974
Batir, O., Selçuk, N., and Kulah, G. (2019). Effect of kaolin addition on alkali capture capability during combustion of olive residue. Combust. Sci. Technol. 191 (1), 43–53. doi:10.1080/00102202.2018.1452376
Batista, E. M. C. C., Shultz, J., Matos, T. T. S., Fornari, M. R., Ferreira, T. M., Szpoganicz, B., et al. (2018). Effect of surface and porosity of biochar on water holding capacity aiming indirectly at preservation of the Amazon biome. Sci. Rep. 8 (1), 10677. doi:10.1038/s41598-018-28794-z
Blasing, M., Zini, M., and Muller, M. (2013). Influence of feedstock on the release of potassium, sodium, chlorine, sulfur, and phosphorus species during gasification of wood and biomass shells. Energy fuels. 27, 1439–1445. doi:10.1021/ef302093r
Bosch, D., Back, J. O., Gurtner, D., Giberti, S., Hofmann, A., and Bockreis, A. (2022). Alternative feedstock for the production of activated carbon with ZnCl2: forestry residue biomass and waste wood. Carbon Resour. Convers. 5 (4), 299–309. doi:10.1016/j.crcon.2022.09.001
Bosshard, P. P., Bachofen, R., and Brandl, H. (1996). Metal leaching of fly ash from municipal waste incineration by Aspergillus niger. Environ. Sci. Technol. 30 (10), 3066–3070. doi:10.1021/es960151v
Boström, D., Skoglund, N., Grimm, A., Boman, C., Öhman, M., Broström, M., et al. (2012). Ash transformation chemistry during combustion of biomass. Energy and Fuels 26 (1), 85–93. doi:10.1021/ef201205b
Braghiroli, F. L., and Passarini, L. (2020). Valorization of biomass residues from forest operations and wood manufacturing presents a wide range of sustainable and innovative possibilities. Curr. For. Rep. 6 (2), 172–183. doi:10.1007/s40725-020-00112-9
Bridgwater, A. V. (2012). Review of fast pyrolysis of biomass and product upgrading. Biomass Bioenergy 38, 68–94. doi:10.1016/j.biombioe.2011.01.048
Bryers, R. W. (1986). Influence of segregated mineral matter in coal on slagging. Washington, D.C.: ACS Publication, 353–374. doi:10.1021/bk-1986-0301.ch025
Bulatov, I., and Klemeš, J. (2009). Towards cleaner technologies: emissions reduction, energy and waste minimisation, industrial implementation. Clean Technol. Environ. Policy 11 (1), 1–6. doi:10.1007/s10098-008-0177-0
Bulushev, D. A., and Ross, J. R. H. (2011). Catalysis for conversion of biomass to fuels via pyrolysis and gasification: a review. Catal. Today 171 (1), 1–13. doi:10.1016/j.cattod.2011.02.005
Capablo, J., Jensen, P. A., Pedersen, K. H., Hjuler, K., Nikolaisen, L., Backman, R., et al. (2009). Ash properties of alternative biomass. Energy fuels. 23, 1965–1976. doi:10.1021/ef8008426
Carpenter, D., Westover, T. L., Czernik, S., and Jablonski, W. (2014). Biomass feedstocks for renewable fuel production: a review of the impacts of feedstock and pretreatment on the yield and product distribution of fast pyrolysis bio-oils and vapors. Green Chem. 16 (2), 384–406. doi:10.1039/C3GC41631C
Carrier, M., Joubert, J.-E., Danje, S., Hugo, T., Görgens, J., Knoetze, J., et al. (2013). Impact of the lignocellulosic material on fast pyrolysis yields and product quality. Bioresour. Technol. 150, 129–138. doi:10.1016/j.biortech.2013.09.134
Carrillo, M. A., Staggenborg, S. A., and Pineda, J. A. (2014). Washing sorghum biomass with water to improve its quality for combustion. Fuel 116, 427–431. doi:10.1016/j.fuel.2013.08.028
Changi, S. M., Faeth, J. L., Mo, N., and Savage, P. E. (2015). Hydrothermal reactions of biomolecules relevant for microalgae liquefaction. Industrial Eng. Chem. Res. 54 (47), 11733–11758. doi:10.1021/acs.iecr.5b02771
Chen, D., Cen, K., Zhuang, X., Gan, Z., Zhou, J., Zhang, Y., et al. (2022). Insight into biomass pyrolysis mechanism based on cellulose, hemicellulose, and lignin: evolution of volatiles and kinetics, elucidation of reaction pathways, and characterization of gas, biochar and bio-oil. Combust. Flame 242, 112142. doi:10.1016/j.combustflame.2022.112142
Chen, H., Namioka, T., and Yoshikawa, K. (2011). Characteristics of tar, NOx precursors and their absorption performance with different scrubbing solvents during the pyrolysis of sewage sludge. Appl. Energy 88 (12), 5032–5041. doi:10.1016/j.apenergy.2011.07.007
Chen, H., Pan, P., Wang, Y., and Zhao, Q. (2017). Field study on the corrosion and ash deposition of low-temperature heating surface in a large-scale coal-fired power plant. Fuel 208, 149–159. doi:10.1016/j.fuel.2017.06.120
Cruz-Reina, L. J., Flórez-Rojas, J. S., López, G. D., Herrera-Orozco, I., Carazzone, C., and Sierra, R. (2023). Obtention of fatty acids and phenolic compounds from Colombian cashew (Anacardium occidentale) nut shells using pyrolysis: towards a sustainable biodiesel production. Heliyon 9 (8), e18632. doi:10.1016/j.heliyon.2023.e18632
da Rosa, M. D. H., Alves, C. J., dos Santos, F. N., de Souza, A. O., Zavareze, E. d. R., Pinto, E., et al. (2023). Macroalgae and microalgae biomass as feedstock for products applied to bioenergy and food industry: a brief review. Energies 16, 1820. doi:10.3390/en16041820
Davidsson, K. O., Amand, L. E., Steenari, B. M., Elled, A. L., Eskilsson, D., and Leckner, B. (2008). Countermeasures against alkali-related problems during combustion of biomass in a circulating fluidized bed boiler. Chem. Eng. Sci. 63, 5314–5329. doi:10.1016/j.ces.2008.07.012
Dayton, D. C., Carpenter, J. R., Kataria, A., Peters, J. E., Barbee, D., Mante, O. D., et al. (2015). Design and operation of a pilot-scale catalytic biomass pyrolysis unit. Green Chem. 17 (9), 4680–4689. doi:10.1039/C5GC01023C
DeGroot, W. F., and Shafizadeh, F. (1984). The influence of exchangeable cations on the carbonization of biomass. J. Anal. Appl. Pyrolysis 6 (3), 217–232. doi:10.1016/0165-2370(84)80019-4
Dhawan, H., and Sharma, D. K. (2019). Advances in the chemical leaching (inorgano-leaching), bio-leaching and desulphurisation of coals. Int. J. Coal Sci. Technol. 6, 169–183. doi:10.1007/s40789-019-0253-6
Dibdiakova, J., Wang, L., and Li, H. (2015). Characterization of ashes from Pinus Sylvestris forest biomass. Energy Procedia 75, 186–191. doi:10.1016/j.egypro.2015.07.289
Einvall, J., Albertazzi, S., Hulteberg, C., Malik, A., Basile, F., Larsson, A.-C., et al. (2007). Investigation of reforming catalyst deactivation by exposure to fly ash from biomass gasification in laboratory scale. Energy and Fuels 21 (5), 2481–2488. doi:10.1021/ef060633k
Enestam, S., Bankiewicz, D., Tuiremo, J., Makela, K., and Hupa, M. (2013). Are NaCl and KCl equally corrosive on superheater materials of steam boiler? Fuel 104, 294–306. doi:10.1016/j.fuel.2012.07.020
Eom, I.-Y., Kim, J.-Y., Kim, T.-S., Lee, S.-M., Choi, D., Choi, I.-G., et al. (2012). Effect of essential inorganic metals on primary thermal degradation of lignocellulosic biomass. Bioresour. Technol. 104, 687–694. doi:10.1016/j.biortech.2011.10.035
Feng, S., Yuan, Z., Leitch, M., and Xu, C. C. (2014). Hydrothermal liquefaction of barks into bio-crude – effects of species and ash content/composition. Fuel 116, 214–220. doi:10.1016/j.fuel.2013.07.096
Fermoso, J., Pizarro, P., Coronado, J. M., and Serrano, D. P. (2017). Advanced biofuels production by upgrading of pyrolysis bio-oil. WIREs Energy Environ. 6, 4. doi:10.1002/wene.245
Fernandes, I., Calheiro, D., Kieling, A. G., Moraes, C. A. M., Rocha, T. L. A., Brehm, F. A., et al. (2016). Characterization of rice husk ash produced using different biomass combustion techniques for energy. Fuel 165, 351–359. doi:10.1016/j.fuel.2015.10.086
Fliri, L., Guizani, C., Miranda-Valdez, I. Y., Pitkänen, L., and Hummel, M. (2023). Reinvestigating the concurring reactions in early-stage cellulose pyrolysis by solution state NMR spectroscopy. J. Anal. Appl. Pyrolysis 175, 106153. doi:10.1016/j.jaap.2023.106153
Folgueras, M. B., Gómez-Martín, J. M., and Diez, M. A. (2023). How height-related variations in hybrid poplars affect composition and pyrolytic behaviour: the key role of lignin maturity during woody-biomass pyrolysis. J. Anal. Appl. Pyrolysis 169, 105861. doi:10.1016/j.jaap.2023.105861
Gahane, D., Biswal, D., and Mandavgane, S. A. (2022). Life cycle assessment of biomass pyrolysis. Bioenergy Res. 15 (3), 1387–1406. doi:10.1007/s12155-022-10390-9
Genuino, H. C., Contucci, L., Velasco, J. O., Sridharan, B., Wilbers, E., Akin, O., et al. (2023). Pyrolysis of lignoboost lignin in ZnCl2-KCl-NaCl molten salt media: insights into process-pyrolysis oil yield and composition relations. J. Anal. Appl. Pyrolysis 172, 106005. doi:10.1016/j.jaap.2023.106005
Ghodake, G. S., Shinde, S. K., Kadam, A. A., Saratale, R. G., Saratale, G. D., Kumar, M., et al. (2021). Review on biomass feedstocks, pyrolysis mechanism and physicochemical properties of biochar: state-of-the-art framework to speed up vision of circular bioeconomy. J. Clean. Prod. 297, 126645. doi:10.1016/j.jclepro.2021.126645
Gómez, N., Banks, S. W., Nowakowski, D. J., Rosas, J. G., Cara, J., and Sanchez, M. E. (2018). Effect of temperature on product performance of a high ash biomass during fast pyrolysis and its bio-oil storage evaluation. Fuel Processing Technology 172, 97–105.
Grams, J., Jankowska, A., and Goscianska, J. (2023). Advances in design of heterogeneous catalysts for pyrolysis of lignocellulosic biomass and bio-oil upgrading. Microporous Mesoporous Mater. 362, 112761. doi:10.1016/j.micromeso.2023.112761
Gudka, B., Jones, J. M., Lea-Langton, A. R., Williams, A., and Saddawi, A. (2016). A review of the mitigation of deposition and emission problems during biomass combustion through washing pre-treatment. J. Energy Inst. 89 (2), 159–171. doi:10.1016/j.joei.2015.02.007
Gunawardena, A. D., and Fernando, S. D. (2013). “Methods and applications of deoxygenation for the conversion of biomass to petrochemical products,” in Biomass now - cultivation and utilization (London, United Kingdom: IntechOpen). doi:10.5772/53983
Guo, M., Song, W., and Buhain, J. (2015). Bioenergy and biofuels: history, status, and perspective. Renew. Sustain. Energy Rev. 42, 712–725. doi:10.1016/j.rser.2014.10.013
Guo, Q., Cheng, Z., Chen, G., Yan, B., Hou, L., and Ronsse, F. (2020). Optimal strategy for clean and efficient biomass combustion based on ash deposition tendency and kinetic analysis. J. Clean. Prod. 271, 122529. doi:10.1016/j.jclepro.2020.122529
He, M., Xiao, B., Liu, S., Hu, Z., Guo, X., Luo, S., et al. (2010). Syngas production from pyrolysis of municipal solid waste (MSW) with dolomite as downstream catalysts. J. Anal. Appl. Pyrolysis 87 (2), 181–187. doi:10.1016/j.jaap.2009.11.005
Hess, D., Wendt, L. M., Wahlen, B. D., Aston, J. E., Hu, H., and Quinn, J. C. (2019). Techno-economic analysis of ash removal in biomass harvested from algal turf scrubbers. Biomass Bioenergy 123, 149–158. doi:10.1016/j.biombioe.2019.02.010
Hu, B., Zhang, W., Zhang, B., Wang, X., Yang, Y., Ma, S., et al. (2022). Role of glycosidic bond in initial cellulose pyrolysis: investigation by machine learning simulation. Appl. Energy Combust. Sci. 9, 100055. doi:10.1016/j.jaecs.2021.100055
Hu, B., Zhang, W. M., Guo, X. W., Liu, J., Yang, X., and Lu, Q. (2024). Experimental and computational study on xylan pyrolysis: the pyrolysis mechanism of main branched monosaccharides. Fuel Process. Technol. 253, 107989. doi:10.1016/j.fuproc.2023.107989
Hu, X., and Gholizadeh, M. (2020). Progress of the applications of bio-oil. Renew. Sustain. Energy Rev. 134, 110124. doi:10.1016/j.rser.2020.110124
Islam, M. K., Khatun, M. S., Arefin, M. A., Islam, M. R., and Hassan, M. (2021). Waste to energy: an experimental study of utilizing the agricultural residue, MSW, and e-waste available in Bangladesh for pyrolysis conversion. Heliyon 7 (12), e08530. doi:10.1016/j.heliyon.2021.e08530
Javed, M. A. (2020). Acid treatment effecting the physiochemical structure and thermal degradation of biomass. Renew. Energy 159, 444–450. doi:10.1016/j.renene.2020.06.011
Jiang, L., Hu, S., Sun, L., Su, S., Xu, K., He, L., et al. (2013). Influence of different demineralization treatments on physicochemical structure and thermal degradation of biomass. Bioresour. Technol. 146, 254–260. doi:10.1016/j.biortech.2013.07.063
Kan, T., Strezov, V., and Evans, T. J. (2016). Lignocellulosic biomass pyrolysis: a review of product properties and effects of pyrolysis parameters. Renew. Sustain. Energy Rev. 57, 1126–1140. doi:10.1016/j.rser.2015.12.185
Kim, H., Sriram, S., Fang, T., Kelley, S., and Park, S. (2021a). An eco-friendly approach for blending of fast-pyrolysis bio-oil in petroleum-derived fuel by controlling ash content of loblolly pine. Renew. Energy 179, 2063–2070. doi:10.1016/j.renene.2021.08.033
Kittivech, T., and Fukuda, S. (2019). Investigating agglomeration tendency of Co-gasification between high alkali biomass and woody biomass in a bubbling fluidized bed system. Energies 13, 56. doi:10.3390/en13010056
Kleinhans, U., Wieland, C., Frandsen, F., and Spliethoff, H. (2018). Ash formation and deposition in coal and biomass fired combustion systems: progress and challenges in the field of ash particle sticking and rebound behavior. Prog. Energy Combust. Sci. 68, 65–168. doi:10.1016/j.pecs.2018.02.001
Konist, A. (2023). Investigation of fouling and corrosion of low-temperature reheater in a CFBC boiler. Fuel 338, 127373. doi:10.1016/j.fuel.2022.127373
Krebs, W., Brombacher, C., Bosshard, P. P., Bachofen, R., and Brandl, H. (1997). Microbial recovery of metals from solids. FEMS Microbiol. Rev. 20 (3–4), 605–617. doi:10.1111/j.1574-6976.1997.tb00341.x
Lago, A., Sanz, M., Gordón, J. M., Fermoso, J., Pizarro, P., Serrano, D. P., et al. (2022). Enhanced production of aromatic hydrocarbons and phenols by catalytic co-pyrolysis of fruit and garden pruning wastes. J. Environ. Chem. Eng. 10 (3), 107738. doi:10.1016/j.jece.2022.107738
Lee, J. W., Kidder, M., Evans, B. R., Paik, S., Buchanan III, A. C., Garten, C. T., et al. (2010). Characterization of biochars produced from cornstovers for soil amendment. Environ. Sci. Technol. 44 (20), 7970–7974. doi:10.1021/es101337x
Lee, X. J., Ong, H. C., Gan, Y. Y., Chen, W.-H., and Mahlia, T. M. I. (2020). State of art review on conventional and advanced pyrolysis of macroalgae and microalgae for biochar, bio-oil and bio-syngas production. Energy Convers. Manag. 210, 112707. doi:10.1016/j.enconman.2020.112707
Li, P., Shi, X., Wang, X., Song, J., Fang, S., Bai, J., et al. (2021). Bio-oil from biomass fast pyrolysis: yields, related properties and energy consumption analysis of the pyrolysis system. J. Clean. Prod. 328, 129613. doi:10.1016/j.jclepro.2021.129613
Li, W., Dang, Q., Brown, R. C., Laird, D., and Wright, M. M. (2017). The impacts of biomass properties on pyrolysis yields, economic and environmental performance of the pyrolysis-bioenergy-biochar platform to carbon negative energy. Bioresour. Technol. 241, 959–968. doi:10.1016/j.biortech.2017.06.049
Li, Y. S., Niu, Y., and Spiegel, M. (2007). High temperature interaction of Al/Si-modified Fe-Cr alloys with KCl. Corros. Sci. 49, 1799–1815. doi:10.1016/j.corsci.2006.10.019
Lim, H. Y., Tang, S. H., Chai, Y. H., Yusup, S., and Lim, M. T. (2022). Co-pyrolysis of plastics and food waste mixture under flue gas condition for bio-oil production. Sustain. Energy Technol. Assessments 54, 102826. doi:10.1016/j.seta.2022.102826
Manikandan, S., Vickram, S., Sirohi, R., Subbaiya, R., Krishnan, R. Y., Karmegam, N., et al. (2023). Critical review of biochemical pathways to transformation of waste and biomass into bioenergy. Bioresour. Technol. 372, 128679. doi:10.1016/j.biortech.2023.128679
Márquez, A., Patlaka, E., Sfakiotakis, S., Ortiz, I., and Sanchez-Hervas, J. M. (2023). Pyrolysis of municipal solid waste: a kinetic study through multi-step reaction models. Waste Management 172, 171–181.
Mayer, Z. A., Apfelbacher, A., and Hornung, A. (2012). A comparative study on the pyrolysis of metal- and ash-enriched wood and the combustion properties of the gained char. J. Anal. Appl. Pyrolysis 96, 196–202. doi:10.1016/j.jaap.2012.04.007
Melikoglu, M., Ozdemir, M., and Ates, M. (2023). Pyrolysis kinetics, physicochemical characteristics and thermal decomposition behavior of agricultural wastes using thermogravimetric analysis. Energy Nexus 11, 100231. doi:10.1016/j.nexus.2023.100231
Miccio, F., Murri, A. N., Medri, V., and Landi, E. (2019). Utilization of fireclay for preventing fluidized-bed agglomeration during biomass thermochemical processing. Industrial Eng. Chem. Res. 58 (51), 23498–23507. doi:10.1021/acs.iecr.9b06253
Míguez, J. L., Porteiro, J., Behrendt, F., Blanco, D., Patiño, D., and Dieguez-Alonso, A. (2021). Review of the use of additives to mitigate operational problems associated with the combustion of biomass with high content in ash-forming species. Renew. Sustain. Energy Rev. 141, 110502. doi:10.1016/j.rser.2020.110502
Miranda, A. F., Ramkumar, N., Andriotis, C., Höltkemeier, T., Yasmin, A., Rochfort, S., et al. (2017). Applications of microalgal biofilms for wastewater treatment and bioenergy production. Biotechnol. Biofuels 10 (1), 120. doi:10.1186/s13068-017-0798-9
Mlonka-Medrala, A., Magdziarz, A., Gajek, M., Nowinska, K., and Nowak, W. (2020). Alkali metals association in biomass and their impact on ash melting behaviour. Fuel 261, 116421. doi:10.1016/j.fuel.2019.116421
Mohan, D., Pittman, C. U., and Steele, P. H. (2006). Pyrolysis of wood/biomass for bio-oil: a critical review. Energy and Fuels 20 (3), 848–889. doi:10.1021/ef0502397
Monir, M. U., Aziz, A. A., and Yousuf, A. (2022). Integrated technique to produce sustainable bioethanol from lignocellulosic biomass. Mater. Lett. X 13, 100127. doi:10.1016/j.mlblux.2022.100127
Morris, J. D., Daood, S. S., Chilton, S., and Nimmo, W. (2018). Mechanisms and mitigation of agglomeration during fluidized bed combustion of biomass: a review. Fuel 230, 452–473. doi:10.1016/j.fuel.2018.04.098
Mourant, D., Wang, Z., He, M., Wang, X. S., Garcia-Perez, M., Ling, K., et al. (2011). Mallee wood fast pyrolysis: effects of alkali and alkaline earth metallic species on the yield and composition of bio-oil. Fuel 90 (9), 2915–2922. doi:10.1016/j.fuel.2011.04.033
Muduli, S., Champati, A., Popalghat, H. K., Patel, P., and Sneha, K. R. (2018). Poultry waste management: an approach for sustainable development. Int. J. Adv. Sci. Res. 8.
Mullen, C. A., and Boateng, A. A. (2013). Accumulation of inorganic impurities on HZSM-5 zeolites during catalytic fast pyrolysis of switchgrass. Industrial Eng. Chem. Res. 52, 17156–17161. doi:10.1021/ie4030209
Nair, R. R., Kißling, P. A., Marchanka, A., Lecinski, J., Turcios, A. E., Shamsuyeva, M., et al. (2023). Biochar synthesis from mineral and ash-rich waste biomass, part 2: characterization of biochar and co-pyrolysis mechanism for carbon sequestration. Sustain. Environ. Res. 33 (1), 14. doi:10.1186/s42834-023-00176-9
Nik-Azar, M., Hajaligol, M., Sohrabi, M., and Dabir, B. (1997). Mineral matter effects in rapid pyrolysis of beech wood. Fuel Process. Technol. 51, 7–17. doi:10.1016/s0378-3820(96)01074-0
Niu, Y., Lv, Y., Zhang, X., Wang, D., Li, P., and Hui, S. (2019). Effects of water leaching (simulated rainfall) and additives (KOH, KCl, and SiO2) on the ash fusion characteristics of corn straw. Appl. Therm. Eng. 154, 485–492. doi:10.1016/j.applthermaleng.2019.03.124
Niu, Y., Tan, H., and Hui, S. (2016a). Ash-related issues during biomass combustion: alkali-induced slagging, silicate melt-induced slagging (ash fusion), agglomeration, corrosion, ash utilization, and related countermeasures. Prog. Energy Combust. Sci. 52, 1–61. doi:10.1016/j.pecs.2015.09.003
Nowakowski, D. J., and Jones, J. M. (2008). Uncatalysed and potassium-catalysed pyrolysis of the cell-wall constituents of biomass and their model compounds. J. Anal. Appl. Pyrolysis 83 (1), 12–25. doi:10.1016/j.jaap.2008.05.007
Nunes, L. J. R., Matias, J. C. O., and Catalão, J. P. S. (2016). Biomass combustion systems: a review on the physical and chemical properties of the ashes. Renew. Sustain. Energy Rev. 53, 235–242. doi:10.1016/j.rser.2015.08.053
Nussbaumer, T., Czasch, C., Klippel, N., Johansson, L., and Tullin, C. (2008). Particulate emissions from biomass combustion in IEA countries. Available at: https://task32.ieabioenergy.com/wp-content/uploads/sites/24/2017/03/Nussbaumer_et_al_wp_2_Report_PM10_Jan_2008.pdf (Accessed at January 28, 2024).
Nussbaumer, T. M. (2001). Aerosols from biomass combustion: international seminar at 27 June 2001 in Zurich (Switzerland). Available at: https://task32.ieabioenergy.com/wp-content/uploads/sites/24/2017/03/aerosols.pdf (Accessed on January 25, 2024).
Nzihou, A., and Stanmore, B. (2013). The fate of heavy metals during combustion and gasification of contaminated biomass – a brief review. J. Hazard. Mater. 256-257, 56–66. doi:10.1016/j.jhazmat.2013.02.050
Nzihou, A., Stanmore, B., Lyczko, N., and Minh, D. P. (2019). The catalytic effect of inherent and adsorbed metals on the fast/flash pyrolysis of biomass: a review. Energy 170, 326–337. doi:10.1016/j.energy.2018.12.174
Obernberger, I., and Biedermann, F. (2002). “Fractionated heavy metal separation in biomass combustion plants—possibilities, technological approach, experiences,” in Impact of mineral impurities in solid fuel combustion (Netherlands: Kluwer Academic Publishers), 595–608. doi:10.1007/0-306-46920-0_44
Obot, I. B. (2021). Under-deposit corrosion on steel pipeline surfaces: mechanism, mitigation and current challenges. J. Bio- Tribo-Corrosion 7 (2), 49. doi:10.1007/s40735-021-00485-9
Ohman, M., Nordin, A., Skrifvars, B. J., Backman, R., and Hupa, M. (2000). Bed agglomeration characteristics during fluidized bed combustion of biomass fuels. Energy and Fuels 14, 169–178. doi:10.1021/ef990107b
Olatoyan, O. J., Kareem, M. A., Adebanjo, A. U., Olawale, S. O. A., and Alao, K. T. (2023). Potential use of biomass ash as a sustainable alternative for fly ash in concrete production: a review. Hybrid. Adv. 4, 100076. doi:10.1016/j.hybadv.2023.100076
Olofsson, G., Ye, Z., Bjerle, I., and Andersson, A. (2002). Bed agglomeration problems in fluidized-bed biomass combustion. Industrial Eng. Chem. Res. 41, 2888–2894. doi:10.1021/ie010274a
Osatiashtiani, A., Zhang, J., Stefanidis, S. D., Zhang, X., and Bridgwater, A. V. (2022). The mechanism for catalytic fast pyrolysis of levoglucosan, furfural and furan over HZSM-5: an experimental and theoretical investigation. Fuel 328, 125279. doi:10.1016/j.fuel.2022.125279
Osman, A. I., Farghali, M., Ihara, I., Elgarahy, A. M., Ayyad, A., Mehta, N., et al. (2023). Materials, fuels, upgrading, economy, and life cycle assessment of the pyrolysis of algal and lignocellulosic biomass: a review. Environ. Chem. Lett. 21 (Issue 3), 1419–1476. doi:10.1007/s10311-023-01573-7
Patwardhan, P. R., Satrio, J. A., Brown, R. C., and Shanks, B. H. (2010a). Influence of inorganic salts on the primary pyrolysis products of cellulose. Bioresour. Technol. 101 (12), 4646–4655. doi:10.1016/j.biortech.2010.01.112
Pienihäkkinen, E., Stamatopoulos, I., Krassa, P., Svensson, I., Ohra-aho, T., Lindfors, C., et al. (2023). Production of pyrolytic lignin for the phenolic resin synthesis via fast pyrolysis. J. Anal. Appl. Pyrolysis 176, 106239. doi:10.1016/j.jaap.2023.106239
Pode, R. (2016). Potential applications of rice husk ash waste from rice husk biomass power plant. Renew. Sustain. Energy Rev. 53, 1468–1485. doi:10.1016/j.rser.2015.09.051
Radlein, D., and Quignard, A. (2013). A short historical review of fast pyrolysis of biomass. Oil Gas Sci. Technol. – Revue d’IFP Energies Nouvelles 68 (4), 765–783. doi:10.2516/ogst/2013162
Richardson, Y., Tanoh, S. T., Julbe, A., and Blin, J. (2015). Improving the kinetics of the CO 2 gasification of char through the catalyst/biomass integration concept. Fuel 154, 217–221. doi:10.1016/j.fuel.2015.03.059
Roberts, L. J., Mason, P. E., Jones, J. M., Gale, W. F., Williams, A., Hunt, A., et al. (2019). The impact of aluminosilicate-based additives upon the sintering and melting behaviour of biomass ash. Biomass Bioenergy 127, 105284. doi:10.1016/j.biombioe.2019.105284
Rong, H., Wang, T., Zhou, M., Wang, H., Hou, H., and Xue, Y. (2017). Combustion characteristics and slagging during Co-combustion of rice husk and sewage sludge blends. Energies 10 (4), 438. doi:10.3390/en10040438
Ronsse, F., Bai, X., Prins, W., and Brown, R. C. (2012). Secondary reactions of levoglucosan and char in the fast pyrolysis of cellulose. Environ. Prog. Sustain. Energy 31 (2), 256–260. doi:10.1002/ep.11633
Ruddy, D. A., Schaidle, J. A., Ferrell III, J. R., Wang, J., Moens, L., and Hensley, J. E. (2014). Recent advances in heterogeneous catalysts for bio-oil upgrading via “ex situ catalytic fast pyrolysis”: catalyst development through the study of model compounds. Green Chem. 16 (2), 454–490. doi:10.1039/C3GC41354C
Sanusi, T., Sumner, J., and Simms, N. J. (2022). A comparative evaluation of waste wood and herbaceous biomass fireside corrosion behaviours. Fuel 324, 124070. doi:10.1016/j.fuel.2022.124070
Scott, D. S., Paterson, L., Piskorz, J., and Radlein, D. (2001). Pretreatment of poplar wood for fast pyrolysis: rate of cation removal. J. Anal. Appl. Pyrolysis 57 (2), 169–176. doi:10.1016/S0165-2370(00)00108-X
Shao, Y., Li, C., Fan, M., Gao, G., Inkoua, S., Zhang, L., et al. (2023). Sequential pyrolysis for understanding specific influence of cellulose- and lignin-derived volatiles on properties of counterpart char. Green Chem. Eng. doi:10.1016/j.gce.2023.04.004
Shao, Y., Wang, J., Preto, F., Zhu, J., and Xu, C. (2012). Ash deposition in biomass combustion or co-firing for power/heat generation. Energies 5 (12), 5171–5189. doi:10.3390/en5125171
Shen, Y. (2017). Rice husk silica derived nanomaterials for sustainable applications. Renew. Sustain. Energy Rev. 80, 453–466. doi:10.1016/j.rser.2017.05.115
Shimada, N., Kawamoto, H., and Saka, S. (2008). Different action of alkali/alkaline earth metal chlorides on cellulose pyrolysis. J. Anal. Appl. Pyrolysis 81 (1), 80–87. doi:10.1016/j.jaap.2007.09.005
Sierra, I., Ayastuy, J. L., Gutiérrez-Ortiz, M. A., and Iriarte-Velasco, U. (2023). A study on the impact of the reaction mechanism of the thermochemical activation of bone char (by pyrolysis and carbonization). J. Anal. Appl. Pyrolysis 171, 105973. doi:10.1016/j.jaap.2023.105973
Silos-Llamas, A. K., Sudibyo, H., Hernández-Montoya, V., Meredith, W., and Durán-Jiménez, G. (2023). Fast pyrolysis of agricultural residues: reaction mechanisms and effects of feedstock properties and microwave operating conditions on the yield and product composition. J. Anal. Appl. Pyrolysis 175, 106217. doi:10.1016/j.jaap.2023.106217
Silva, F. C., Cruz, N. C., Tarelho, L. A. C., and Rodrigues, S. M. (2019). Use of biomass ash-based materials as soil fertilisers: critical review of the existing regulatory framework. J. Clean. Prod. 214, 112–124. doi:10.1016/j.jclepro.2018.12.268
Sommersacher, P., Brunner, T., Obernberger, I., Kienzl, N., and Kanzian, W. (2013). Application of novel and advanced fuel characterization tools for the combustion related characterization of different wood/kaolin and straw/kaolin mixtures. Energy and Fuels 27 (9), 5192–5206. doi:10.1021/ef400400n
Song, G., Qi, X., Yang, S., and Yang, Z. (2018). Investigation of ash deposition and corrosion during circulating fluidized bed combustion of high-sodium, high-chlorine Xinjiang lignite. Fuel 214, 207–214. doi:10.1016/j.fuel.2017.11.011
Song, W., and Guo, M. (2012). Quality variations of poultry litter biochar generated at different pyrolysis temperatures. J. Anal. Appl. Pyrolysis 94, 138–145. doi:10.1016/j.jaap.2011.11.018
Sotoudehnia, F., Baba Rabiu, A., Alayat, A., and McDonald, A. G. (2020). Characterization of bio-oil and biochar from pyrolysis of waste corrugated cardboard. J. Anal. Appl. Pyrolysis 145, 104722. doi:10.1016/j.jaap.2019.104722
Stella Mary, G., Sugumaran, P., Niveditha, S., Ramalakshmi, B., Ravichandran, P., and Seshadri, S. (2016). Production, characterization and evaluation of biochar from pod (Pisum sativum), leaf (Brassica oleracea) and peel (Citrus sinensis) wastes. Int. J. Recycl. Org. Waste Agric. 5 (1), 43–53. doi:10.1007/s40093-016-0116-8
Tan, S., Zhang, Z., Sun, J., and Wang, Q. (2013). Recent progress of catalytic pyrolysis of biomass by HZSM-5. Chin. J. Catal. 34 (4), 641–650. doi:10.1016/S1872-2067(12)60531-2
Thy, P., Yu, C., Jenkins, B. M., and Lesher, C. E. (2013). Inorganic composition and environmental impact of biomass feedstock. Energy and Fuels 27 (7), 3969–3987. doi:10.1021/ef400660u
Tibbetts, S. M., Milley, J. E., and Lall, S. P. (2015). Chemical composition and nutritional properties of freshwater and marine microalgal biomass cultured in photobioreactors. J. Appl. Phycol. 27 (3), 1109–1119. doi:10.1007/s10811-014-0428-x
Tonn, B., Thumm, U., Lewandowski, I., and Claupein, W. (2012). Leaching of biomass from semi-natural grasslands – effects on chemical composition and ash high-temperature behaviour. Biomass Bioenergy 36, 390–403. doi:10.1016/j.biombioe.2011.11.014
Valizadeh, S., Oh, D., Jae, J., Pyo, S., Jang, H., Yim, H., et al. (2022). Effect of torrefaction and fractional condensation on the quality of bio-oil from biomass pyrolysis for fuel applications. Fuel 312, 122959. doi:10.1016/j.fuel.2021.122959
Vassilev, S. V., Baxter, D., Andersen, L. K., and Vassileva, C. G. (2010). An overview of the chemical composition of biomass. Fuel 89 (5), 913–933. doi:10.1016/j.fuel.2009.10.022
Vassilev, S. V., Baxter, D., and Vassileva, C. G. (2014). An overview of the behaviour of biomass during combustion: Part II. Ash fusion and ash formation mechanisms of biomass types. Fuel 117, 152–183. doi:10.1016/j.fuel.2013.09.024
Vassilev, S. V., and Vassileva, C. G. (2016). Composition, properties and challenges of algae biomass for biofuel application: an overview. Fuel 181, 1–33. doi:10.1016/j.fuel.2016.04.106
Wang, G., Poulsen, J. N. F., Poulsen, S. N. F., Jensen, P. A., and Frandsen, F. J. (2022). Influence of kaolin and coal fly ash addition on biomass ash deposition in an entrained flow reactor. Fuel 313, 123041. doi:10.1016/j.fuel.2021.123041
Wang, L., Hustad, J. E., and Grønli, M. (2012). Sintering characteristics and mineral transformation behaviors of corn cob ashes. Energy and Fuels 26 (9), 5905–5916. doi:10.1021/ef300215x
Wang, L., Hustad, J. E., Skreiberg, Ø., Skjevrak, G., and Grønli, M. (2012). A critical review on additives to reduce ash related operation problems in biomass combustion applications. Energy Procedia 20, 20–29. doi:10.1016/j.egypro.2012.03.004
Wang, L., Skreiberg, Ø., and Becidan, M. (2014). Investigation of additives for preventing ash fouling and sintering during barley straw combustion. Appl. Therm. Eng. 70 (2), 1262–1269. doi:10.1016/j.applthermaleng.2014.05.075
Wang, Q., Yang, J., Wang, Q., and Wu, T. (2009). Effects of water-washing pretreatment on bioleaching of heavy metals from municipal solid waste incinerator fly ash. J. Hazard. Mater. 162 (2–3), 812–818. doi:10.1016/j.jhazmat.2008.05.125
Wang, X., Zhai, M., Guo, H., Panahi, A., Dong, P., and Levendis, Y. A. (2021). High-temperature pyrolysis of biomass pellets: the effect of ash melting on the structure of the char residue. Fuel 285, 119084. doi:10.1016/j.fuel.2020.119084
Wei, Y., Tang, J., Xie, J., and Shen, C. (2019). Molten alkali carbonates pyrolysis of digestate for phenolic productions. J. Clean. Prod. 225, 143–151. doi:10.1016/j.jclepro.2019.03.234
Werkelin, J., Skrifvars, B., Zevenhoven, M., Holmbom, B., and Hupa, M. (2010). Chemical forms of ash-forming elements in woody biomass fuels. Fuel 89, 481–493. doi:10.1016/j.fuel.2009.09.005
Wright, M. M., Daugaard, D. E., Satrio, J. A., Brown, R. C., and Hsu, D. D. (2010). Techno-economic analysis of biomass fast pyrolysis to transportation fuels. Fuel 89, S2–S10. doi:10.1016/j.fuel.2010.07.029
Wu, H.-Y., and Ting, Y.-P. (2006). Metal extraction from municipal solid waste (MSW) incinerator fly ash—chemical leaching and fungal bioleaching. Enzyme Microb. Technol. 38 (6), 839–847. doi:10.1016/j.enzmictec.2005.08.012
Wullschleger, S. D., Davis, E. B., Borsuk, M. E., Gunderson, C. A., and Lynd, L. R. (2010). Biomass production in switchgrass across the United States: database description and determinants of yield. Agron. J. 102 (4), 1158–1168. doi:10.2134/agronj2010.0087
Xing, Z., Chen, C., and Jiang, X. (2023). A molecular investigation on the mechanism of co-pyrolysis of ammonia and biodiesel surrogates. Energy Convers. Manag. 289, 117164. doi:10.1016/j.enconman.2023.117164
Yildiz, G., Ronsse, F., Venderbosch, R., Duren, R. van, Kersten, S. R. A., and Prins, W. (2015). Effect of biomass ash in catalytic fast pyrolysis of pine wood. Appl. Catal. B Environ. 168–169, 203–211. doi:10.1016/j.apcatb.2014.12.044
Yip, K., Tian, F., Hayashi, J., and Wu, H. (2010). Effect of alkali and alkaline earth metallic species on biochar reactivity and syngas compositions during steam gasification. Energy fuels. 24, 173–181. doi:10.1021/ef900534n
Yu, J., Guo, Q., Gong, Y., Ding, L., Wang, J., and Yu, G. (2021). A review of the effects of alkali and alkaline earth metal species on biomass gasification. Fuel Process. Technol. 214, 106723. doi:10.1016/j.fuproc.2021.106723
Zhang, D. (2013). “Chapter 6 – ash fouling, deposition and slagging in ultra-supercritical coal power plants,” in Ultra-supercritical coal power plants (Sawston, Cambridge: Woodhead Publishing), 133–183.
Zhang, Y., Kajitani, S., Ashizawa, M., and Oki, Y. (2010). Tar destruction and coke formation during rapid pyrolysis and gasification of biomass in a drop-tube furnace. Fuel 89 (2), 302–309. doi:10.1016/j.fuel.2009.08.045
Zhu, Y., Niu, Y., Tan, H., and Wang, X. (2014). Short review on the origin and countermeasure of biomass slagging in grate furnace. Front. Energy Res. 2. doi:10.3389/fenrg.2014.00007
Glossary
Keywords: pyrolysis, products yield, products properties, biomass, ash
Citation: Puri L, Hu Y and Naterer G (2024) Critical review of the role of ash content and composition in biomass pyrolysis. Front. Fuels. 2:1378361. doi: 10.3389/ffuel.2024.1378361
Received: 29 January 2024; Accepted: 28 February 2024;
Published: 08 March 2024.
Edited by:
Abul Kalam Hossain, Aston University, United KingdomReviewed by:
Justin Thomas, Czech Technical University in Prague, CzechiaVikas Sharma, University of Brighton, United Kingdom
Copyright © 2024 Puri, Hu and Naterer. This is an open-access article distributed under the terms of the Creative Commons Attribution License (CC BY). The use, distribution or reproduction in other forums is permitted, provided the original author(s) and the copyright owner(s) are credited and that the original publication in this journal is cited, in accordance with accepted academic practice. No use, distribution or reproduction is permitted which does not comply with these terms.
*Correspondence: Greg Naterer, Z25hdGVyZXJAdXBlaS5jYQ==; Yulin Hu, eXVsaW5odUB1cGVpLmNh