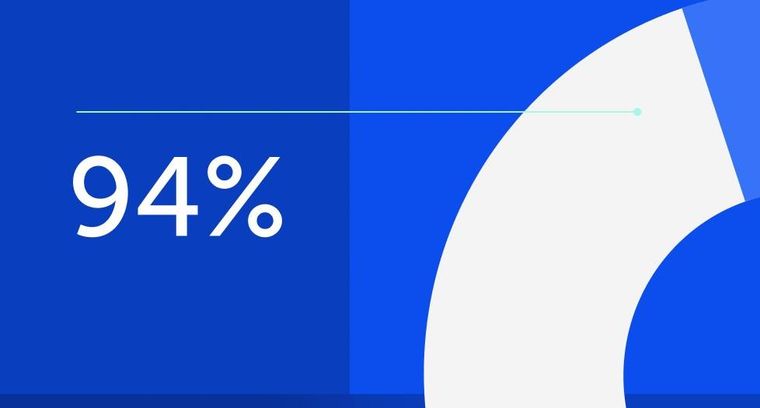
94% of researchers rate our articles as excellent or good
Learn more about the work of our research integrity team to safeguard the quality of each article we publish.
Find out more
ORIGINAL RESEARCH article
Front. Environ. Sci., 17 June 2024
Sec. Water and Wastewater Management
Volume 12 - 2024 | https://doi.org/10.3389/fenvs.2024.1422107
This article is part of the Research TopicWater and Wastewater Treatment and Management in the Textile IndustryView all 5 articles
The current study set out to assess and create long-term solutions for improving environmental performance concerning water use, wastewater production, and treatment at Syntan plant (glass-lined vessel unit) and application laboratory (small-scale leather retanning. Based on evaluations and analyses, best available techniques including water gauging, pressurized vessel washing, dedication of vessels to similar production, reuse techniques, developing commercial grade intermediate products from wash water, managing cooling water and developing reuse methods of reverse osmosis reject water were applied to reduce water consumption and effluent generation in process and non-process activities. Furthermore, the reduced effluent was subjected to treat using electrochemical processes, i.e., electrocoagulation and electro-Fenton, before it was drained to outside environment. As a result of the applications, 0%–100% change was measured in various process and non-process activities, whereas, 12.8%–100% reduction was measured in effluent. Soft cooling water consumption was reduced by 46.7%. The results of treated effluent parameters were compared and found the final removal efficiencies of total dissolved solids (51.4%), total suspended solids (99.2%), chemical oxygen demand (98.5%) and electric conductivity (67.7%). It is concluded that this study can be considered as a successful model to increased water efficiency in chemical industries, Furthermore, it could serve as a building block for the incorporation of cleaner and sustainable production approach into national agenda and to overcome stern issues of high-water and energy consumption and effluent management in different industries.
Globally, a range of chemicals is synthesized from putrescible animal skins using leather tanning, dyeing, smoothing and finishing processes. These chemicals, including basic chromium sulfate, synthetic tanning agents, pigments and adhesives, etc. are used to manufacture the end leather products (Novori and Ohkuma, 2001; Dixit et el. 2015; Navarro et al., 2020). Pigmented chemicals attained by the emulsification of TiO2, Carbon black, FeO2, Pb and Cr containing compounds, give aesthetic effects to leather which generates variety of shades and colors (Kaur et al., 2022). Polymer based chemicals commonly known as adhesives provide appropriate water resistance and compose leather pieces to produce required products. Synthetic tanning compounds are used to enhance the quality and texture of leather products. In addition, surfactants, oils, fat liquors, and acid dyes are produced to provide the necessary and aesthetically pleasing effects in the final leather manufacturing process (Wang et al., 2019).
The manufacturing of these compounds in any sector consumes enormous amount of water and generates considerable volumes of effluent (Saravanan et al., 2021). Consuming freshwater in large quantities has become a significant issue in chemical manufacturing industry, specifically in areas facing water crises (Zehnder et al., 2003; Jury and Vaux, 2007). Primarily, water consumption is segmented into process and non-process activities. Floor and vessel washing, spray drying, etc. are included in non-process activities while process water consumption involves the required quantity of water in manufacturing of abovementioned chemicals (Luo et al., 2015; Ali et al., 2020). These operations result in the production of harmful wastewater, posing a major environmental risk (Alyafei, 2018). The main constitutes of the untreated effluent are the extracts of chemical products such as synthetic tanning agents, adhesives and pigments as well as many other waste ingredients such as surfactants, oils, salts, acids, polymers, dyes, etc (Saravanan et al., 2021). When formaldehyde molecules are concentrated with phenols and amino precursors, a substance known as a “syntan” is created. This substance has the potential to release formaldehyde into wastewater, which is carcinogenic (Mohan et al., 2008; Luo et al., 2015). When these untreated pollutants are released into the environment, they gravitate toward aquatic bodies, where they bioaccumulate in living tissues and multiply through food chains, endangering natural ecosystems (Rabiet et al., 2009). Global efforts are being made to manage effluent discharge and reduce water consumption through the use of sustainable practices, such as best available techniques (BATs) in the chemical manufacturing industries (Ibáñez-Forés et al., 2013; Yılmaz et al., 2018).
The best ways can be devised and put into practice by first installing water flow gauges, then improving washing processes, reusing water, and altering process methods (Meals et al., 2010). Evaporative condenser cooling technology can save 50% of water in comparison to traditional water-cooling systems (HiuMing et al., 2015; Melander, 2017). Because of the increased level of concentration, this technology is expected to significantly minimize cooling water discharge. In recent literature, the adaptation to smart management practices and process altering methods in chemical manufacturing and cooling tower system has reduced water consumption to about 46%–100% in polyethylene terephthalate production resulting in high environmental performance and profitability (Alkaya and Demirer, 2015). In order to reduce wastewater generation, these sustainable techniques may be applied for the reduction of water consumption (Ali et al., 2020). Industries are having difficulty finding sustainable treatment methods for efficient management that comply with environmental regulations, as traditional treatment technologies are costly, energy-intensive, and land-intensive (Moussa et al., 2016).
According to a study of recent literature, electrochemical techniques are among the most economical and energy-efficient options for treating industrial wastewater (Garcia-Segura et al., 2020; Yang et al., 2021). Electrochemical processes include electrocoagulation and electro Fenton or the combination of both using iron electrode or iron catalyst or by adding hydrogen peroxide in one of the Fenton reagents (Ghanbari and Moradi, 2015). Because of the reliability, cost effectiveness and low energy demands of these techniques, they are considered as sustainable (Sahu and Chaudhari, 2013).
The chemical industry in developing nations faces severe challenges from excessive water use and inadequate effluent treatment. The majority of these businesses are found in cities that are already experiencing issues with water scarcity (Koop and Leeuwen, 2016; Chowdhary et al., 2019). Furthermore, the environment and general public health are seriously threatened by conventional effluent treatment methods since they do not meet the standards for the safe disposal of industrial wastewater. A cleaner approach was sought by the current study, which aims to 1) minimize water consumption and reduce effluent generation by applying the best techniques currently available, and 2) achieve efficiency of treatment technologies from syntan plant and application laboratory effluent using Fenton and electrocoagulation.
In this study, improving water efficiency was taken as a priority, further the reduced effluent was treated at selected industries; Syntan plant (glass-lined unit) and its commercial laboratory leather tanning in Lahore Pakistan. Before sustainable applications the effluent from this industry was discharged directly to Rohi industrial drain without any treatment. Further description of both units is as under.
Before putting any environmental management methods into action, the Syntan plant was equipped with four glass-lined containers of different capacities and categories (5 Tons (5A), 5 Tons (5B), 3 Tons (3A), and 3 Tons (3B)) as well as a neutralization vessel to monitor the current status. These containers supported the manufacture of compounds that were corrosive or reactive. Producing leather chemicals included making Formeco, super plasticizers, sulfated fat liquor, sugar reduced chromium, naphthalene dispersion agents, and synthetic tanning agents (syntan). Several commercial-grade products were produced with different liquid/powder, solid, and pH concentrations after these groups were further divided (Table 1).
The commercial laboratory serves as both a department for commercial activities and as a support system for the Syntan plant manufacture. In order to maintain the homogeneity of the control and experimental groups, wet blue skins are utilized in the majority of leather retention tests to test the qualities of resins. Table 2 lists the raw ingredients and conditions needed for the leather processing recipe (Ashraf et al., 2020).
An environmental performance evaluation was conducted in two stages in order to establish a baseline. In order to gather process-based numerical data on water consumption and wastewater generation, an initial survey was carried out during the first phase. Additionally, historical data from January to October of a chosen year’s monthly production and total water use were examined. Since monthly production was found to be roughly constant, averaging the data or using 1 month’s worth of data had little effect. However, water usage varied according to the production pattern used in the various Syntan plant vessels.
In November of the same year, a thorough evaluation was completed in the second phase to compute monthly production compared to water consumption and the typical production pattern, which was thought to be a reliable baseline before water-saving measures. Specific water usage and wastewater generation were calculated as m3/ton production for environmental performance indicators. Since water reduction and treatment were the study’s primary focus, only the following significant gaps were looked at: i) thorough vessel cleaning following manufacturing, as the primary source of effluent was unintentional chemical production; ii) the water-intensive cooling process; and iii) treating the Syntan plant’s decreased effluent and application lab.
A number of strategies, such as best available techniques (BATs), were used to reduce the amount of wastewater produced by the leather chemicals manufacturing sector and conserve water (Chung et al., 2013; Yukseler et al., 2017; Khan et al., 2019; Ali et al., 2020). The details of the BATs employed in this study are given as below.
➢ Water flow meters were installed at various locations where the measurement of non-process water consumption was needed.
➢ The implementation of engineering controls, such as pressurized vessel washing systems, is being considered. Additionally, vessels dedicated to comparable production types are being installed to minimize washing, and a new vessel is being installed to manage plant operations.
➢ Utilizing the initial wash of the vessel in the subsequent production run.
➢ The last wash was put to use again to recharge the spray dryer and keep the temperature stable.
➢ New commercial-grade chemicals are produced through chemical treatment and washing water with different solid and pH contents.
➢ Reduction of cooling water usage and associated liquid discharge through the application of engineering and management controls and alternatives.
➢ Reverse osmosis (RO) concentrates can be directly reused for domestic activities without any kind of treatment.
Effluent sampling was conducted at three Syntan plan and application laboratory locations, both prior to and during the application of the selected options (Figure 1). Location I represents the wastewater outflow from the Syntan plant, whereas, Location II depicts the wastewater leaving the application lab and combining with the wastewater from the Syntan plant at site III. In 500 mL amble bottles, 24 composite samples were collected during the first phase, 24 at location I, 24 at location II, and 24 at location III. Following applications in the Syntan unit, a composite sampling (24 at location III) was carried out in the second phase.
The quality assurance lab received all of the samples, and physicochemical characteristics like pH, total dissolved solids (TDS), total suspended solids (TSS), chemical oxygen demand (COD), electrical conductivity (EC), and color were measured. Wastewater was tested for pH, TDS, and electrical conductivity using a multimeter (model = HANNA HI 9811-5). To determine the TDS and COD concentrations, the APHA method 2005 was employed. Three distinct places were chosen to measure the wastewater flow, as shown in Figure 1. A Sensus DN 20 digital water flow meter was utilized for this purpose. The following formula was used to calculate the contaminants’ removal efficiency from the wastewater:
(Where, Co= Initial concentration and Ct = Final concentration).
To treat the wastewater from the Syntan facility, a lab and pilot scale treatment equipment were developed. Since the goal of the study is to minimize the amount of water used and wastewater produced by the Syntan plant, the reduced effluent from the Syntan and application lab was treated using two sustainable technologies: the Fenton process and electrocoagulation (EC).
A 1000 mL beaker put up simply on top of a magnetic stirring mechanism was the Fenton experiment’s lab-scale configuration (Figure 2). Four wastewater samples (F1, F2, F3, and F4), each containing 1,000 mL, were gathered from position III (Figure 1). Four beakers were filled with wastewater, and the pH was adjusted to 3–4 per the recommendations in the literature (Gökkuş and Oğuz, 2011). for Fenton oxidation. Various concentrations of FeSO4 and H2O2 were utilized to maximize effective treatment of the wastewater. FeSO4 and H2O2 in the ideal proportions (35% w/w) were added, and mixing was done both quickly and slowly afterward. Fenton oxidation is said to occur in two stages: i) oxidation and ii) coagulation. Hydrogen peroxide (H2O2) was introduced during the oxidation process, and it was quickly mixed for two to 3 minutes. The oxidized sample mentioned above was slowly combined for 20 min during the coagulation stage. After settling for 30 min, it was finally filtered to move on to the next step. The procedure helps remove electrolytes from the effluent, the EC system can perform better and achieve the necessary efficiency (Ghosh et al., 2008; Sim, 2015).
Figure 2. Representation of two-stage lab scale setup for treatment of Syntan and Application lab effluent.
After the Fenton method was used, a lab-scale EC plant measuring 0.2 L × 0.1 W × 0.27 H was created from Perspex material. In the reaction chamber, two anode and two cathode electrodes made of aluminum and iron, measuring 23 cm in height by 1 cm in diameter, were employed, respectively. Anode and cathode spacing was adjusted to 4 cm. To run the solar cell, a direct current (DC) power source was utilized (Yilmaz et al., 2018; Ali et al., 2021). Figure 2 displays the electrocoagulation unit’s schematic diagram. One liter of wastewater was added to the lab-scale EC unit to conduct the experiment. To equalize the effluent during treatment, this unit was equipped with a magnetic stirrer agitation device. The system was given a DC supply, which required three amps at first and dropped to half that after 3 minutes. Ten minutes were spent on the entire procedure, plus a further 10 minutes were allocated for the suspended coagulates to settle. After being cleaned, the samples were filtered and sent to a lab to have their water parameters examined.
The Syntan plant’s baseline month starting from October, the plant used 494.54 m3 of water per month for various processes, including the production of softened water through the reverse osmosis process (RO), cooling the heat transfer oil (HTO), and other household and cleaning uses (Table 3). Compared to other product manufacturing processes, the synthetic tanning agents (5.4%), naphthalene dispersing agents (4.1%), and super plasticizer (4%) had the highest overall water consumption percentage during the Syntan product manufacturing processes. Application lab operations accounted for 6.1% of the industry’s total water consumption, while washing accounts for a large portion of the industry’s water consumption (6.5%), both of which are sources of effluent formation. The primary sources of the industry’s effluent discharge, accounting for 224 m3/month along with RO concentrate of 108 m3/month, were vessel cleaning and cooling water, which contributed 28.3% and 17.4%, respectively (cooling of process and HTO). In terms of the study’s reduction of effluent and water use, these locations were the most significant. According to published reports, cooling water can account for up to 85% of the water used overall in the chemical industry (De Nicola et al., 2007; Alkaya and Demirer, 2015). A portion of the overall effluent, 7.2%, came from leather retention procedures, and 0.8% came from sulfated fat liquor in the form of acidic salt water, which was the outcome of other process formulations. Based on the finding, water efficiency measures that target the usage of cooling and washing water in vessels will lower the Syntan plant’s overall water demand. Water was utilized in the retanning studies in accordance with the application lab’s specifications. In order to prevent pollution of the environment, the study concentrated on effluent treatment.
In respect to the overall output of each product, Figure 3 depicts the current state of the plant’s vessel cleaning patterns over the course of a month. It is evident that several kinds of vessels were used to prepare the various materials. As the methodology indicated, the manufacturing plant could only accommodate four vessels; hence, there was limited chance for all sixteen items to be manufactured in sequence in four distinct vessels. It took a lot of water to clean every vessel after each manufacturing in this random production to avoid contamination in the next batch of created goods. On day one, all four vessels—5B, 3A, 3B, and 5A—were engaged with the fabrication of F-A, CTN, 245 and RC-GR. On the following day, however, 5B and 5A were busy producing other kinds of goods. A vessel’s blue color shows that it has been thoroughly cleaned before the next production that is required, however other vessels have no need for cleaning because of the daily production requirements (Figure 3). The fact that this activity plan calls for a lot of water for cleaning as well as a loss of product and production time highlights the deficiencies that this investigation found.
The primary reason for the industry’s high wastewater output is the total amount of washing water (140 m3/month) utilized in each vessel throughout a month following the application and installation of monitoring equipment (Figure 4). The primary cause of the high discharge was found during surveys to be the intensive vessel washing done without the use of sophisticated equipment or measuring devices. Vessel 5B was used to measure the maximum wash-water water because of its high production and variable cooling and heat-transfer requirements.
The Syntan facility produced an effluent that contained leftovers from a wide range of chemicals, including acrylic resins, fat liquors, formaldehyde condensates, and syntans based on phenol, naphthalene, formaldehyde, and melamine (Senthilvelan et al., 2018). Conversely, because of their superior filling tanning actions in the commercial lab, synthetic tanning chemicals were used in the leather processing. There was a major environmental risk since a significant amount of these artificial tannins were released as effluent after remaining unfixed in the tanning bath (Quadery et al., 2015). The initial pollution load at each sampling point is depicted in Figure 5, as is the ultimate pollution load at location III following the application of BATs. When compared to locations II and III, the high COD value (8,300 mg/L) at position I was examined. During comparison, the initial pollution load, site I (the Syntan unit) had the greatest TDS measurement (8,300 mg/L) compared to other locations, while location II (the application lab) had the highest COD value (7,800 mg/L). The syntan and application unit effluent outflow from Location III has a lower pollutant burden than the standalone effluent discharge. After each application, the analytical findings revealed that the initial pollution load was slightly higher than the TSS (1,670 mg/L), TDS (4,370 mg/L), COD (3,730 mg/L), and conductivity (1931 μS/cm) levels before the application. The removal of Syntan plant wastes from the main drain explained the low pollution levels after application; however, the cooling water concentration remained the sole source of the Syntan unit’s effluent discharge. Additionally, the diluting effect of the cooling water effluent in re-tanning wastewater had an impact on lowering the pollutant load at location III. Therefore, it was suggested that effluent treatment be applied in this case.
Given that vessel washing operations account for almost 28.3% of total water usage (Table 1; Figure 4), careful production planning was done to ensure that the products would fulfill consumer needs. The following month saw the implementation of sustainable management techniques, which were then seen in January of the following year. These included the installation of a pressurized washing system, a new production formation based on the similar nature of groups of chemicals in designated vessels, and a reduction in floor washing by replacing mopping. Furthermore, a new 6000 L vessel (G6) was installed for the highest output group (Figure 6). The idea behind designating specific production vessels was to reduce the amount of cleaning required of them so as not to compromise the quality of the subsequent batch of the same kind of product.
Figure 7 shows the Syntan plant’s revised production pattern that will be put into effect the following month and tracked during the application phase. This month’s measurement of the plant’s total production of 159.2 tons compared to the baseline month’s record of 161.9 tons (November) showed no discernible shift in the industry’s overall production. To minimize vessel washing, it is evident that every chemical group was produced according to a predetermined schedule for the entire month. Six vessels, meanwhile, was insufficient to meet the plant’s high demand for output. Production was conducted on a Formeco group vessel (5B); following batches did not require washing until production was suspended for a few days, which may have resulted in concentrated liquid patches left inside the vessel. The same vessels used in the production of synthetic tanning agents were employed to oversee the fabrication of each product type on different days. For example, the most popular product (245) was produced during the first 8 days of the month without the need to wash the vessels. Because product 806, which has a similar chemical makeup to that of 245 with the exception of pH and total solid content, was made in the same vessel, Table 1; Figure 7. So, in this way, there was no need for washing. Washing the vessel was required while switching to CTN manufacturing in order to prevent contamination. In a similar manner, DIS and CTN were created in order. For the entire month, only three times—on days 10, 18, and 29—was vessel washing necessary (Figure 7). Comparing this arrangement to baseline data, which showed more frequent vessel washing, showed a great accomplishment in reducing non-process water usage.
The study also focused on treating and reusing washing water from vessels (3A and 3B) to prevent effluent discharge. It also expanded the production facility and introduced three new commercial-grade products, which are named as sodium sulfate solution (Na2SO4), SFT-10 (Figure 3), and 272 powder. Washing water collected from the vessels after 806 items were produced was stored in a container and utilized again in the production of an identical batch of products with the same quality in the subsequent batch. The study also focused on treating and reusing washing water from vessels (3A and 3B) to prevent effluent discharge. It also expanded the production facility and introduced three new commercial-grade products, which are named as sodium sulfate solution (Na2SO4), SFT-10 (Figure 3), and 272 powder. After 806 products were manufactured, washing water that was obtained from the vessels was kept in a container and used again in the following batch of the same product’s creation with the same quality (Pervez et al., 2015).
It goes without saying that washing water contributes to effluent, but the production of acids and salts in effluent can also be attributed to the sulfonated fat liquor process. For this study, it was difficult to apply the recovery of these residues from wastewater. According to published reports, while making fat liquors, only sodium sulfate can be recovered (Cuq et al., 1998), therefore, it is necessary to describe the process of sulfated fat liquor production as presented by (Kiss et al., 2007; Leung et al., 2010). All sulfated fat liquors (SFT, SFT/10, and S-2106) are created when sulfuric acid and oil react. It is necessary to remove a specific amount of added sulfuric acid that remains unreacted during the procedure in order to stop the development of free sodium sulfate in fat liquor. As a normal procedure, the solution is treated with sodium sulfate to remove excess sulfuric acid. Consequently, the upper oily layer and the high TDS sodium sulfate solution separate into a water layer at the bottom, with the free acid joining the salt solution. Now that the acid salt solution has been separated, unreacted sulfuric acid (Na2SO4 + H2SO4 + H2O) and the originally supplied sodium sulfate are present (Arneth and Dötsch, 2006).
The following reaction can be used to transform excess acid in salt water into sodium sulfate (Na2SO4) by reacting it with caustic soda (NaOH);
A 2,000 kg batch of SFT and 281 kg of sulfuric acid were used in the experiment’s sulfonation process. Unreacted sulfuric acid had to be eliminated in order to produce the required product, so a 17% solution of sodium sulfate and water in 470 kg and 70 kg, respectively, was used for treatment. The finished mixture was gathered, weighing 540 kg (70 kg Na2SO4 + 400 kg water + 70 kg H2SO4). To fully convert 70 kg of H2SO4 into Na2SO4, 57.14 kg of sodium hydroxide (NaOH) were added. This resulted in the production of 101.43 kg of Na2SO4 (Table 4).
Following the collection of sodium sulfate solution, the industry was presented with two potential options to prevent the addition of liquid waste from the source. These are as follows:
Solution 1. After treatment, the sodium sulfate solution can be utilized in the following batch once its solid content and pH have been adjusted as needed by the process.
• Treated sodium sulfate solution (28.7%) = 244 kg
• Water = 226 kg
For the next batch of 2000 kg, the total solution is 470 kg (at 14.9% strength).
Solution 2. After adjusting the pH to the proper level, the gathered sodium sulfate solution can be spray dried to produce sodium sulfate powder. This sodium sulfate can be utilized as a powder in future batches of SFT and related products, or it can be used in other Syntan formulations.
Given that 19.9% of the industry’s total water usage came from cooling water, a thorough analysis was carried out to improve cooling system efficiency. The cooling of HTO was one of the industrial processes that utilized a single cooling tower to circulate 86 m3/month of water (Table 1). Figure 8 shows the cooling tower circulation. During production, cooling water was circulated in the vessel jacket and used for HTO heat exchange when the process required cold HTO to cool down. When new products were processed in the same vessel, cooling water from the previous batch had to be released from the jacket, which made these two potential sources of water waste before sustainable uses. Each discharge from vessels with a capacity of 3 Tons and 5 Tons, respectively, provided approximately 300 L and 500 L. The manufacturing of synthetic tanning agents and naphthalene dispersing agents also requires heat transfer oil to keep the process temperature between 160°C and 180°C. Prior to the subsequent production, the aforementioned 7.6 m3/month (Table 5) discharged from the vessel jacket was measured during the preceding arbitrary production.
Following the production plan, it is evident that the jacket discharge from the vessels was totally eliminated because they were exclusively used for cooling water during production, and the HTO was used to circulate water for the separate vessels containing synthetic tanning agents and dispersants based on naphthalene. Not only did the application save 7.6 m3/month of water, but it also prevented the same amount from ending up in the effluent.
Table 1 describes how 26 m3/month of cooling water was pumped to the heat transfer system before cooled air pumps took its place. According to published reports, air pumps can be utilized in place of water-based cooling systems (Arneth and Dötsch, 2006; Alkaya and Dermirer, 2015). The chemical sector can use more sophisticated techniques, including readily available air-cooled pumps, to reduce the amount of water in cooling operations (Warner 2006; Deziani et al., 2017). The greatest substitute, more ecologically friendly and energy-efficient than a water-cooling system, was an air-cooled pump (Ali et al., 2020). Two air-cooled pumps were built to cool down heat transfer oil based on literature, which reduces the industry’s overall water use by 8%. As a result, the cooling tower’s feed water flow was decreased from 86 m3/month to 52.8 m3/month.
Effluent came from cooling water blowdown, excluding all other applications. After establishing a water balance that showed insufficient effluent reduction, evaporation and drift losses were measured at 1 m3/month; this number has also been documented in literature (Alkaya and Dermirer, 2014). Since freshwater is the source of the feed water, it was observed that the cooling tower underwent three to four cycles of concentration. Table 6 provides a comparison of this condition with other investigations. Studies have indicated that using softened water can increase the cycle of concentration (Abbas et al., 2015), however, this study’s freshwater quality is suitable for cooling tower systems, as shown by previous research (Siddique et al., 2021).
The majority of the water used for process operations was reverse osmosis (RO) softened water, which made up 88.54 m3/month of the total. Of the effluent that was discharged down the drain, 55%, or 108 m3/month, is the RO contract percentage that is being tracked. After application, RO concentration was repurposed for usage in plantations and other domestic settings. Prior studies have indicated that RO concentrate with values ranging from 70% to 80% can be recycled directly for various industrial applications (Khan et al., 2019).
After 3 months of application in process and non-process activities, Figure 9 illustrates the overall reduction in effluent generation and specific water usage. There was a significant reduction in water consumption measured in cooling water delivered to HTO (100%), vessel washing (98%) and floor washing (90%), whereas, the effluent was significantly reduced in process (100%), vessel washing (100%), RO concentrate water (100%), and floor washing. Cooling water continued to be a source of effluent as blowdown, as described in the cooling water section. The industry’s total water consumption and discharge increased by 24%, with a 78.8% increase in wastewater generation.
Figure 9. Particular water usage and particular effluent release at the Syntan facility both before to and following application.
Following all sustainable applications, the Syntan and application lab’s reduced effluent was treated before being discharged into the outdoors. Because of the high concentration of electrolytes in this effluent, the Fenton technique was employed. A lab-scale system was designed specifically to process the reduced effluent. Figure 10 depicts the optimization of the Fenton process’s treatment efficiency for the samples (F1, F2, F3, and F4) collected at location III after applying water consumption. To achieve desirable results, the pH was raised to the acidic side (pH = 3) (Gökkuş and Oğuz, 2011). When compared to other samples, sample F1 had the greatest achieved TDS removal efficiency—nearly 50% (Figure 10A). This suggests that a small amount of Fenton reagent can significantly reduce TDS in re-tanning and cooling tower blow-down effluent. When the removal effectiveness of sample F3 with TSS (99%), COD (89.6%), and conductivity (48.3%) was compared to other samples, the results revealed that the dose of FeSO4 (1g) and H2O2 (2 mL) was the most successful Fenton process treatment (Figures 10B–D). In addition to other characteristics, the effluent color changed slightly during treatment, going from rose beige in F1 to dark orange in F2 and light orange in F3, F4, and so on. The mean value of before treatment and standard deviation of all samples has sown in Figure 11 which shows the less chances of differences between final results. Although, sample F3 was chosen due to higher COD and conductivity removal efficiency subjected to electrocoagulation treatment to lower the pollutant load in comparison to national emission quality standards (NEQS).
Figure 10. Outcomes of optimization using various Fenton process dosages in comparison to four effluent samples and parameter removal efficiencies. (A) The percentage elimination effectiveness of TDS at different FeSO4 and H2O2 dosages. (B) The percentage of TSS removed with varying FeSO4 and H2O2 dosages. (C) The percentage of COD that is removed efficiently when FeSO4 and H2O2 dosages are changed. (D) The percentage of electrical conductivity that is removed efficiently using different FeSO4 and H2O2 dosages. (E) Color removal using varying Fenton reagent dosages for all samples.
The results of sample F3 employing EC treatment following the Fenton process are shown in Table 7. 13.4%, 20%, 86%, and 37.6% of TDS, TSS, COD, and conductivity were removed with corresponding efficiency. TDS, TSS, COD, and conductivity were found to have ultimate removal efficiencies of 51.4%, 99.2%, 98.5%, and 67.7%, respectively. When combined, chemical and electrocoagulation can produce a COD elimination effectiveness of approximately 98%. Since all values were ultimately below the NEQS’s allowable limits, the study’s chosen parameters produced outstanding results. The treated wastewater can be further reused in a variety of industrial applications or can be decentralized utilizing reverse osmosis into the industry’s process activities, as evidenced by the colorless effluent that was produced as a result (Blandin et al., 2016).
Table 7. Results of Syntan’s physicochemical parameters and application lab effluent following lab-scale treatment Fenton technique and electrocoagulation.
The best ways to lower total water consumption (25.8%) and effluent generation (79.5%) were found in the Syntan plant study and the commercial application retanning laboratory. These techniques included process tweaks, engineering adjustments to the cooling system, and scheduled production in reactor vessels that were already available. Additionally, these applications help produce novel compounds of a commercial grade, like salts (Na2SO4) and powdered synthetic tannins, which have a positive economic impact on the business. Significant progress has been made in reducing the pollution load in wastewater discharge from the industry thanks to planned sustainable treatment options of the Fenton process (with optimal doses of FeSO4 and H2O2) and then applied electrocoagulation at lab-scale of reduced effluent from the retanning application lab and Syntan unit. Additionally, the study can be applied to decentralization options, where wastewater treated by reverse osmosis and ultrafiltration can be recycled in process activities, resulting in almost zero liquid discharge from the industry when implemented on a larger scale.
The raw data supporting the conclusions of this article will be made available by the authors, without undue reservation.
AA: Conceptualization, Data curation, Formal Analysis, Investigation, Methodology, Project administration, Resources, Writing–original draft, Writing–review and editing. IS: Conceptualization, Supervision, Writing–review and editing, Methodology, Project administration. SA: Methodology, Project administration, Resources, Writing–review and editing. MS: Formal Analysis, Investigation, Visualization, Writing–original draft. JY: Conceptualization, Formal Analysis, Funding acquisition, Writing–review and editing. MR: Investigation, Methodology, Validation, Writing–original draft. FS: Data curation, Formal Analysis, Methodology, Writing–original draft.
The author(s) declare that no financial support was received for the research, authorship, and/or publication of this article.
We appreciate the chance to operate in a state-of-the-art laboratory and production facility provided by Naveed, Manager, Research and Development Laboratory, SRC (Pvt) Ltd.
The authors declare that the research was conducted in the absence of any commercial or financial relationships that could be construed as a potential conflict of interest.
All claims expressed in this article are solely those of the authors and do not necessarily represent those of their affiliated organizations, or those of the publisher, the editors and the reviewers. Any product that may be evaluated in this article, or claim that may be made by its manufacturer, is not guaranteed or endorsed by the publisher.
Abbas, Z., Su, C., Tahira, F., Mapoma, H. W. T., and Aziz, S. Z. (2015). Quality and hydrochemistry of groundwater used for drinking in Lahore, Pakistan: analysis of source and distributed groundwater. Environ. Earth Sci. 74 (1), 4281–4294. doi:10.1007/s12665-015-4432-5
Ali, A., and Shaikh, I. A. (2021). Attaining water efficiency and reduction in chromium release through wastewater reuse in basic chromium sulfate production industry. Desalination Water Treat. 217, 243–252. doi:10.5004/dwt.2021.26910
Ali, A., Shaikh, I. A., Abbasi, N. A., Firdous, N., and Ashraf, M. (2020). Enhancing water efficiency and wastewater treatment using sustainable technologies: a laboratory and pilot study for adhesive and leather chemicals production. J. Water Process Eng. 36, 101308. doi:10.1016/j.jwpe.2020.101308
Alkaya, E., and Demirer, G. N. (2014). Sustainable textile production: a case study from a woven fabric manufacturing mill in Turkey. J. Clean. Prod. 65, 595–603. doi:10.1016/j.jclepro.2013.07.008
Alkaya, E., and Demirer, G. N. (2015). Reducing water and energy consumption in chemical industry by sustainable production approach: a pilot study for polyethylene terephthalate production. J. Clean. Prod. 99, 119–128. doi:10.1016/j.jclepro.2015.02.087
Alyafei, E. F. H. A. (2018) Sustainable design for offshore oil and gas platforms: a conceptual framework for topside facilities projects. Available at: http://hdl.handle.net/10399/3513.
Arneth, H., and Dötsch, S. (2006). Pumps for heat transfer applications. World Pumps 482, 22–27. doi:10.1016/s0262-1762(06)71143-9
Ashraf, M. N., Khan, S. M., Munir, S., and Saleem, R. (2020). Synthesis of formaldehyde free amino resin to produce green eco-labelled leather with improved retanning properties. J. Am. Leather Chem. As. 115 (4), 132–139. doi:10.34314/jalca.v115i4.3799
Blandin, G., Verliefde, A. R., Comas, J., Rodriguez-Roda, I., and Le-Clech, P. (2016). Efficiently combining water reuse and desalination through forward osmosis—reverse osmosis (FO-RO) hybrids: a critical review. Membranes 6 (3), 37. doi:10.3390/membranes6030037
Chowdhary, P., Bharagava, R. N., Mishra, S., and Khan, N. (2019) Role of industries in water scarcity and its adverse effects on environment and human health. Springer eBooks, 235–256. doi:10.1007/978-981-13-5889-0_12
Chung, J., Kim, J., Kim, Y., and Hwang, Y. W. (2013). Assessment and selection of best available technology (BAT) for wastewater facilities in the leather tanning and finishing industry. Resour. Conserv. Recycl 70, 32–37. doi:10.1016/j.resconrec.2012.10.005
Cuq, M. H., Benjelloun-Mlayah, B., and Delmas, M. (1998). Oil extracted from seal hides: characterization and use as leather fat liquor. J. Am. Oil Chem. Soc. 75 (8), 1015–1019. doi:10.1007/s11746-998-0280-8
De Nicola, E., Meriç, S., Gallo, M., Iaccarino, M., Rocca, C. D., Lofrano, G., et al. (2007). Vegetable and synthetic tannins induce hormesis/toxicity in sea urchin early development and in algal growth. Environ. Pollut. 146 (1), 46–54. doi:10.1016/j.envpol.2006.06.018
Deziani, M., Rahmani, K., Roudaki, S. M., and Kordloo, M. (2017). Feasibility study for reduce water evaporative loss in a power plant cooling tower by using air to Air heat exchanger with auxiliary Fan. Desalination 406, 119–124. doi:10.1016/j.desal.2015.12.007
Dixit, S. K., Yadav, A., Dwivedi, P. D., and Das, M. (2015). Toxic hazards of leather industry and technologies to combat threat: a review. J. Clean. Prod. 87, 39–49. doi:10.1016/j.jclepro.2014.10.017
Garcia-Segura, S., Qu, X., Alvarez, P. J. J., Chaplin, B. P., Chen, W., Crittenden, J. C., et al. (2020). Opportunities for nanotechnology to enhance electrochemical treatment of pollutants in potable water and industrial wastewater – a perspective. Nano 7 (8), 2178–2194. doi:10.1039/d0en00194e
Ghanbari, F., and Moradi, M. A. (2015). A comparative study of electrocoagulation, electrochemical Fenton, electro-Fenton and peroxi-coagulation for decolorization of real textile wastewater: electrical energy consumption and biodegradability improvement. J. Environ. Chem. Eng. 3 (1), 499–506. doi:10.1016/j.jece.2014.12.018
Ghosh, D., Solanki, H., and Purkait, M. K. (2008). Removal of Fe (II) from tap water by electrocoagulation technique. J. Hazard. Mat. 155 (1-2), 135–143. doi:10.1016/j.jhazmat.2007.11.042
Gökkuş, Ö., and Oğuz, M. (2011). Investigation of color and COD removal by Fenton reagent from aqueous solutions containing acid and reactive dyestuffs. Desalination Water Treat. 26 (1-3), 160–164. doi:10.5004/dwt.2011.2119
HiuMing, H. W., Zhang, J., Ngo, H. H., Guo, W., Hu, Z., Liang, S., et al. (2015). A review on the sustainability of constructed wetlands for wastewater treatment: design and operation. Bioresour. Technol. Rep. 175, 594–601. doi:10.1016/j.biortech.2014.10.068
Ibáñez-Forés, V., Bovea, M. D., and Azapagic, A. (2013). Assessing the sustainability of Best Available Techniques (BAT): methodology and application in the ceramic tiles industry. J. Clean. Prod. 51, 162–176. doi:10.1016/j.jclepro.2013.01.020
Jury, W. A., and Vaux, H. J. (2007). The emerging global water crisis: managing scarcity and conflict between water users. Adv. Agron., 1–76. doi:10.1016/s0065-2113(07)95001-4
Kaur, M., Sharma, S., and Sodhi, H. S. (2022). “An eco-friendly approach for the degradation of azo dyes and their effluents by Pleurotus Florida,” in Microbial consortium and biotransformation for pollution decontamination (Elsevier), 209–242.
Khan, I., Saeed, K., and Khan, I. (2019). Nanoparticles: properties, applications and toxicities. Arab. J. Chem. 12 (7), 908–931. doi:10.1016/j.arabjc.2017.05.011
Kiss, A. A., Dimian, A. C., and Rothenberg, G. (2007). Biodiesel by catalytic reactive distillation powered by metal oxides. Energy & Fuels 22 (1), 598–604. doi:10.1021/ef700265y
Koop, S., and Van Leeuwen, C. (2016). The challenges of water, waste and climate change in cities. Environ. Sustain 19 (2), 385–418. doi:10.1007/s10668-016-9760-4
Leung, D. Y., Wu, X., and Leung, M. (2010). A review on biodiesel production using catalyzed transesterification. Appl. Energy 87 (4), 1083–1095. doi:10.1016/j.apenergy.2009.10.006
Luo, X., Wang, J., Dooner, M., and Clarke, J. (2015). Overview of current development in electrical energy storage technologies and the application potential in power system operation. Appl. Energy 137, 511–536. doi:10.1016/j.apenergy.2014.09.081
Meals, D. W., Dressing, S. A., and Davenport, T. E. (2010). Lag time in water quality response to best management practices: a review. J. Environ. Qual. 39 (1), 85–96. doi:10.2134/jeq2009.0108
Melander, L. (2017). Achieving sustainable development by collaborating in green product innovation. Bus. Strategy. Environ. 26 (8), 1095–1109. doi:10.1002/bse.1970
Mohan, C. R., Saravanabhavan, S., Thanikaivelan, P., Rao, J. R., and Nair, B. U. (2008). Development of formaldehyde-free leathers in the perspective of retanning: part II. Combination of formaldehyde-free retanning syntans. Clean. Technol. Environ. Policy. 10 (3), 287–294. doi:10.1007/s10098-007-0113-8
Moussa, D. T., El-Naas, M., Nasser, M., and Al-Marri, M. (2016). A comprehensive review of electrocoagulation for water treatment: potentials and challenges. J. Environ. Manag. 30 (1), 18. doi:10.1016/j.jenvman.2016.10.032
Navarro, D., Wu, J., Lin, W., Fullana–i–Palmer, P., and Puig, R. (2020). Life cycle assessment and leather production. J. Leather Sci. Eng. 2 (1), 26. doi:10.1186/s42825-020-00035-y
Nisar, M. B., Shah, S. A. R., Tariq, M. O., and Waseem, M. (2020). Sustainable wastewater treatment and utilization: a conceptual innovative recycling solution system for water resource recovery. Sustainability 12 (24), 10350. doi:10.3390/su122410350
Noyori, R., and Ohkuma, T. (2001). Asymmetric catalysis by architectural and functional molecular engineering: practical chemo- and stereoselective hydrogenation of ketones. Angew. Chem. 40 (1), 40–73. doi:10.1002/1521-3773(20010105)40:1<40::aid-anie40>3.3.co;2-x
Pervez, M. K., Ahmed, F., Mahboob, S. J., Dewani, R., Nawaz, H. R., Zeeshan, M., et al. (2015). Synthesis of biological based anionic fatliquor and its application on leather. J. Am. Leather Chem. Assoc. 110 (10), 326–331.
Quadery, H., Uddin, M. T., Azad, A., Chowdhury, M. J., Deb, A. K., and Hassan, M. N. (2015). Fatliquor preparation from Karanja seed oil (Pongamia pinnata L.) and its application for leather processing. IOSR J. Appl. Chem. 8 (1), 54–58. doi:10.9790/5736-08115458
Rabiet, M., Brissaud, F., Seidel, J. L., Pistre, S., and Elbaz-Poulichet, F. (2009). Positive gadolinium anomalies in wastewater treatment plant effluents and aquatic environment in the Hérault watershed (South France). Chemosphere 75 (8), 1057–1064. doi:10.1016/j.chemosphere.2009.01.036
Sahu, O. P., and Chaudhari, P. K. (2013). Review on chemical treatment of industrial waste water. J. Appl. Sci. Environ. Manag. 17 (2), 241–257. doi:10.4314/jasem.v17i2.8
Saravanan, A., Kumar, P. S., Jeevanantham, S., Karishma, S., Tajsabreen, B., Yaashikaa, P., et al. (2021). Effective water/wastewater treatment methodologies for toxic pollutants removal: processes and applications towards sustainable development. Chemosphere 280, 130595. doi:10.1016/j.chemosphere.2021.130595
Senthilvelan, T., Kanagaraj, J., and Panda, R. C. (2018). Effective bioremoval of syntan using fungal laccase to reduce pollution from effluent. Int. J. Environ. Sci. Technol. 15 (7), 1429–1440. doi:10.1007/s13762-017-1495-8
Siddique, A., Shaikh, I. A., Ali, A., Islam, S., Tariq, A., and Ikram, K. (2021). Recycling of textile dyeing wash-off liquor using Fenton technology. Desalination Water Treat. 212, 244–253. doi:10.5004/dwt.2021.26592
Sim, J. (2015). Investigation of Microbial Electrochemical cell (MEC) as a sustainable alternative for synthesizing hydrogen peroxide (H2O2). Available at: https://uwspace.uwaterloo.ca/bitstream/10012/9156/3/Sim_Junyoung_Justin.pdf.
Wang, C., Ghadimi, P., Lim, M. K., and Tseng, M. (2019). A literature review of sustainable consumption and production: a comparative analysis in developed and developing economies. J. Clean. Prod. 206, 741–754. doi:10.1016/j.jclepro.2018.09.172
Werner, S. (2006). Heat-transfer pumps for processing synthetic oils. World Pumps 2006, 38–40. doi:10.1016/s0262-1762(07)70056-1
Yang, L., Hu, W., Chang, Z., Liu, T., Fang, D., Shao, P., et al. (2021). Electrochemical recovery and high value-added reutilization of heavy metal ions from wastewater: recent advances and future trends. Environ. Int. 152, 106512. doi:10.1016/j.envint.2021.106512
Yılmaz, S., Gerek, E. E., Yavuz, E., and Koparal, A. S. (2018). Treatment of vinegar industry wastewater by electrocoagulation with monopolar aluminum and iron electrodes and toxicity evaluation. Sci. Tech. 78 (12), 2542–2552. doi:10.2166/wst.2019.013
Yukseler, H., Uzal, N., Şahinkaya, E., Kitiş, M., Dilek, F. B., and Yetış, Ü. (2017). Analysis of the best available techniques for wastewaters from a denim manufacturing textile mill. J. Environ. Manag. 203, 1118–1125. doi:10.1016/j.jenvman.2017.03.041
Keywords: electrocoagulation, Fenton process, leather chemicals, reuse, water efficiency, wastewater treatment
Citation: Ali A, Shaikh IA, Ahmad SR, Shakoor MB, Yong JWH, Rizwan M and Samina F (2024) Application of effluent reduction methods and treatment using advanced oxidation process at leather chemicals and tanning industries. Front. Environ. Sci. 12:1422107. doi: 10.3389/fenvs.2024.1422107
Received: 24 April 2024; Accepted: 28 May 2024;
Published: 17 June 2024.
Edited by:
Miguel Angel Mueses, University of Cartagena, ColombiaReviewed by:
Anuradha Goswami, University of Alabama at Birmingham, United StatesCopyright © 2024 Ali, Shaikh, Ahmad, Shakoor, Yong, Rizwan and Samina. This is an open-access article distributed under the terms of the Creative Commons Attribution License (CC BY). The use, distribution or reproduction in other forums is permitted, provided the original author(s) and the copyright owner(s) are credited and that the original publication in this journal is cited, in accordance with accepted academic practice. No use, distribution or reproduction is permitted which does not comply with these terms.
*Correspondence: Azhar Ali, YXpoYXIuY2Vlc0BwdS5lZHUucGs=; Jean Wan Hong Yong, amVhbi55b25nQHNsdS5zZQ==
Disclaimer: All claims expressed in this article are solely those of the authors and do not necessarily represent those of their affiliated organizations, or those of the publisher, the editors and the reviewers. Any product that may be evaluated in this article or claim that may be made by its manufacturer is not guaranteed or endorsed by the publisher.
Research integrity at Frontiers
Learn more about the work of our research integrity team to safeguard the quality of each article we publish.