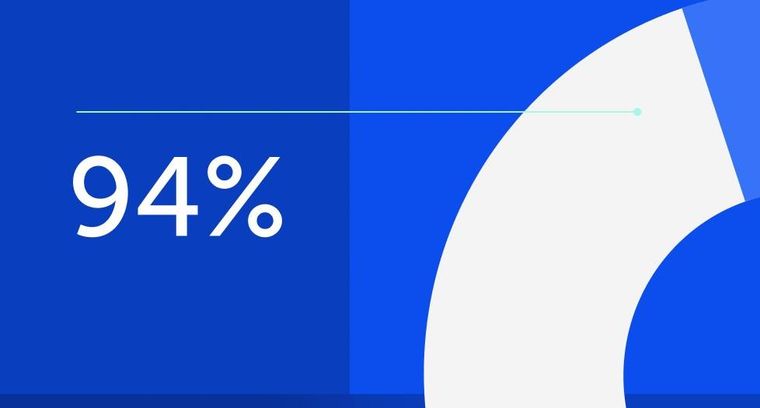
94% of researchers rate our articles as excellent or good
Learn more about the work of our research integrity team to safeguard the quality of each article we publish.
Find out more
ORIGINAL RESEARCH article
Front. Environ. Sci., 11 May 2023
Sec. Toxicology, Pollution and the Environment
Volume 11 - 2023 | https://doi.org/10.3389/fenvs.2023.1183945
This article is part of the Research TopicMine Environmental GovernanceView all 7 articles
The mining industry provides essential mineral resources for human society’s development. However, this industry generates a large quantity of waste material while rapidly extracting valuable elements from ore, such as processed tailings. The existence of mined voids will cause surface subsidence, and the surface stockpiling of tailings and waste rocks occupy a large amount of land and the risk of Tailings Storage Facility (TSF) failure. This paper proposes tailings backfill technology to mitigate surface subsidence and provides an alternative disposal method for tailings generated during ore extraction. Tailings backfill technology prepares the slurry by adding a certain amount of cementitious material into the tailings and transporting it to the underground goaf through a pipeline. The backfill slurry could then gradually build up its strength during the hydration of. Cementitious material. A case study of a lead-zinc mine in the Inner Mongolia Autonomous Region of China using tailings backfill technology was introduced in detail to solve the problems of grassland collapse caused by mine excavation and environmental damage due to tailings disposal. Spread test and rheological test were carried out to study the flow characteristics of filling slurry and the uniaxial compressive strength (UCS) of backfill was tested as well. The result illustrates that the spread of the filling slurry with a solid content between 72% and 76% and cement-tailings ratio between 1:4 and 1:8 is greater than 14 cm, and the UCS of backfill is above 1 MPa. The research shows that the tailings backfill technology recycles tailings waste while mitigating surface grassland subsidence and land occupation of waste disposal. Tailings backfill technology can significantly reduce tailings discharge or even achieve no discharge. A leaching test for heavy metal element classification of the backfill sample was carried out. The results show that the heavy metal detection indicators meet the environmental protection standard requirements and will not cause secondary environmental pollution. Therefore, tailings backfill technology can realize green and efficient management of mine waste and has great application and promotion prospects.
The mining industry provides fundamental mineral resources for the development of human society. However, this industry generates a large quantity of waste material during the rapid extraction of valuable elements from ore. Processed tailings are one of the major solid wastes generated during mineral extraction. (Jehring and Bareither, 2016; Gorakhki and Bareither, 2017; Sun et al., 2018). Traditionally, the tailings material is usually discharged to a storage area commonly known as Tailings Storage Facility (TSF). The conventional way of stockpiling tailings materials in surface storage facilities may damage the mine site geotechnical stability and the local environment and cause economic problems. TSF has substantial security risks, and some significant tailings dam failures that occurred recently have resulted in disastrous environmental and human tragedies (Rico et al., 2008; Wei et al., 2013; Concha Larrauri and Lall, 2018; Piciullo et al., 2022). In 2019, the Brumadinho dam failure happened in Mina Córrego do Feijão, Minas Gerais, Brazil had released around 10 million cubic meters of mine tailings, and 270 people were killed (Rotta et al., 2020; Cheng et al., 2021; Grebby et al., 2021). Enormous damage to the environment, local ecosystems, and communities were caused, and the economic impact (social and environmental) of a major tailings dam failure can be between $750 million and $56 billion (Clarkson and Williams, 2020; Thompson et al., 2020; Vergilio et al., 2020).
There are nearly 10,000 TSFs in China, covering an area of about 36,600 square kilometers, of which one-third of the TSFs have high environmental risks (Wei et al., 2019; Li Q et al., 2020). Inner Mongolia has the largest grassland ecosystem in China and is rich in mineral resources. Open-pit mining of mineral resources causes irreversible damage to the surface of the grassland, leaving eternal scars, while underground mining forms a large number of goaves, causing surface collapse and other problems. In recent years, with the increasing awareness of sustainable development, China has strengthened its environmental protection standards, promulgated a number of laws and regulations for environmental pollution control, and forced enterprises to increase investment in environmental protection and change the development model by levying environmental taxes and other means (Wang et al., 2019; Liu et al., 2021; Li et al., 2022; Ma et al., 2022).
Backfill technology was initially used to fill mined voids to control the movement of the surrounding rock during mining activity. During the past few decades, the use of cemented tailings backfill is constantly increasing, as it uses mine processed tailings as the raw material of mine backfilling. In this case, the cemented tailings backfill technology utilizes mine tailings previously stockpiled in TSFs for underground mine geotechnical stability control, which provides an alternative disposal method for mine processed tailings and mitigates the environmental and economic issues caused by tailings surface disposal (Sheshpari, 2015; Yin et al., 2020).
Taking a Lead-Zinc mine in Inner Mongolia as an example, this paper introduces the use of tailings backfill technology to solve the problems of surface subsidence due to mining activity, including the following contents: (1) investigation and three-dimensional modeling of underground goaf and surface subsidence area, (2) tailings backfill test, (3) tailings backfill process. The key technical point of tailings filling goaves is to maximize the solid content of the filling slurry, reduce the water dehydration of filling slurry in the goaves, and prevent secondary pollution caused by the backfill body under the condition of filling slurry is transportable by the pipe. By using tailings to fill the underground goaves, the surface subsidence is not only controlled, but also the amount of tailings discharged to the TSF is significantly reduced, the stock of tailings piles is reduced, and the damage to the environment caused by mining mineral resources is reduced, thus achieving a harmonious coexistence of economic development and environmental protection.
The study Lead-Zinc mine belongs to Shangdong Gold Group A’erhada Minerals Co., Ltd., with a capacity of 900 thousand tons per year, which lies in East Ujumuqin steppe of Xilin Gol League in the middle part of the Inner Mongolia Autonomous region in the North of China as shown in Figure 1. The altitude of the study area is between 922 m and 1,045 m, with an average annual temperature of 2.5°C, the lowest temperature of −37.4°C, and the highest temperature of 38°C. The average annual precipitation is 242.9 mm, and the maximum precipitation is 457.3 mm.
FIGURE 1. Location of the study Area (Map downloaded from Ministry of Natural Resources of the People’s Republic of China).
This study was conducted in three steps. First, the underground goaves and surface subsidence area were investigated, and the three-dimensional models were established to calculate the volume of goaf and collapse. Second, the parameters such as particle size of the classified coarse tailings are tested and the solid content and cement-tailings ratio of filling slurry was determined through carrying out the flow characteristics of filling slurry test, backfill strength test, and leaching detection of heavy metal elements test. Third, udergroud goaves and collapse pits were filled.
The open stope method mined ore body with a vertical height between 808 m and 928 m of A’erhada Lead-Zinc mine. About 1.95 million tons of ore have been mined, and about 600 thousand cubic meters of goaves have left, distributed in an area of 420 thousand square meters with a length of 2,100 m from east to west and a width of 200 m from north to south. With the extension of time, the rock at the top of the goaves gradually collapsed due to oxidation and other reasons, which connected with the surrounding fracture zone and caused surface subsidence. According to the investigation, there are six collapse pits with a total area of 25,057 m2 in the mining area.
By using 3D laser scanner (Long et al., 2018; Janus and Ostrogórski, 2022) and manual field investigation, the goaves between 808 m level and 928 m level were investigated and classified. Table 1 shows the survey results of the goaves, and Figure 2 shows the morphology of the goaves under the mine.
A three-dimensional laser scanner was used to scan and model the goaf shape and calculate the volume of the goaf. Between the 808 m level and 928 m level, the volume of the goaves at the 768 m level is about 128,657 m3, that of the goaves at the 808 m level is about 13,455 m3, that of the goaves at the 848 m level is about 24,889 m3 and that of the goaves at 888 m level is about 24,636 m3. Figure 3 shows the process of scanning and modeling the goaf using a 3D laser scanner.
The backfill slurry was prepared by the mixture of tailings and a certain amount of cement, and it is piped to the underground goaves from the filling station on the surface. Then backfill body is generated from the filling slurry through dehydration and hydration reaction of cement. The backfill body fills the goaf and supports the overlying rock to prevent it from collapsing to solve the problem of surface collapse.
Tailings backfill system mainly includes tailings slurry settling system, cement supplying system, stirring and transporting system, and automatic control system. The backfill process of A’erhada Lead-Zinc mine is shown in Figure 4. The tailings slurry pumped from the mineral processing plant first flows into the cyclone at the top of the tailings silo in the filling station. After cyclone classification, the bottom coarse tailings slurry flows into the tailings silo for secondary concentration, and the overflow fine tailings slurry is pumped to the TSF. Through using wind or water, the settled tailings in the tailings silo are precipitated into a high concentration of tailing pulp, which is then self-flowing to the mixer. Meanwhile, the cement is transported to the mixer through the screw feeder, and the evenly mixed filling slurry is self-flowing to the underground goaves through the pipeline.
One of the key links of tailings backfill technology is to ensure the filling slurry transporting stably from the surface to the underground goaves. The flow characteristics of the filling slurry are related to the solid content and cement-tailings ratio of the filling slurry. The flow characteristics of filling slurry are usually studied by carrying out the rheological parameters tests.
The experimental materials included classified coarse tailings, cement, and water, which the classified coarse tailings and cement were taken from the A’erhada Lead-Zinc mine and the water was laboratory tap water. The density of classified coarse tailings is 2.97 g/cm3, and the density of cement is 3.05 g/cm3. The particle size distribution curve of classified coarse tailings is shown in Figure 5. The tailings with particle sizes less than 37 μm and 74 μm accounted for 12.58% and 21.05%, respectively.
The spread test of filling slurry adopts a metal frustum with a top diameter of 36 mm, a bottom diameter of 60 mm and a height of 60 mm (Chen et al., 2020; Li W et al., 2020), as shown in Figure 6.
R/S SST rheometer was used to test the rheological parameters of filling slurry (Yang et al., 2019; Cheng et al., 2020; Kou et al., 2020), as shown in Figure 7.
The filling slurry with solid content (Cw) of 72%, 74%, 76%, and 78% was used to carry out the spread test and rheological parameters test, and the filling slurry of each solid content had three cement-tailings ratios of 1:4, 1:8 and 1:12.
Take filling slurry with the cement-tailings ratio of 1:4 as an example, the spread test is as shown in the Figure 8 and Figure 9 shows the results of the spread test. With the increase of solid content, the spread of filling slurry generally decreases, indicating that solid content is the main factor affecting the spread. Within the experimental solid content range, the spread of filling slurry with a solid content of 72% is the largest, and spreads of different cement-tailings ratios are all greater than 22 cm. When the solid contents of the filling slurry are 74% and 76%, the spreads are about 18 cm and 14 cm, respectively. When the solid content is 78%, the filling slurry is difficult to flow, and the spread is only about 10 cm. The cement-tailings ratio seems to have a small influence on the spread diameter, with the decrease of the cement-tailings ratio the spread diameter showing a decreasing trend.
According to the spread test results, the solid content of the filling slurry should be below 78%. Generally, the filling slurry is identified as Bingham fluid, and the rheological equation is shown below. Shear stress (
Where
Table 2 shows the rheological parameters test results. Similar to the spread test results, the yield stress is mainly affected by the solid content of the filling slurry, and the cement-tailings ratio influences it little. With the increase of solid content, the yield stress of filling slurry increased too. The viscosity coefficient of filling slurry has no constant change features with the increase or decrease of solid content and cement-tailings ratio.
According to rheological parameters and the Buckingham formula, the frictional resistance of filling slurry flowing in the pipe can be calculated using Equation 2 (Gopala et al., 2011; Chen et al., 2016; Yang et al., 2020).
Where
To ensure the filling slurry transporting stably from the surface to the underground goaves by pipe, the pressure difference between the inlet and outlet of the pipe should be more significant than the head loss caused by friction resistance.
The backfill in the goaf can not only control the movement of top rock to prevent surface subsidence but also serves as the supporting platform or pillar of adjacent ore mining, which requires the backfill to reach a certain strength. Backfill strength is mainly related to the solid content and cement-tailings ratio of filling slurry, and curing age also influences the strength of backfill.
The filling slurry was mixed evenly using the JJ-5 planetary mixer and then poured into the cube test block with a size of 70.7 mm*70.7 mm*70.7 mm. After the filling slurry turned into the solid backfill, the test blocks were placed in the standard curing room for 7 d and 28 d, and uniaxial compressive strengths (UCS) of the test blocks with different curing ages were tested. Table 3 shows the strength test results. The UCS increases with the increase of solid content, cement-tailings ratio, and curing age. In the solid content range of 72%–76%, the UCS of test blocks cured 7d with cement-tailings ratio 1:4, 1:8, and 1:12 are in the ranges of 1.71 MPa–2.80 MPa, 0.59 MPa–0.90 MPa, and 0.31 MPa–0.40 MPa, respectively. Moreover, the UCS of test blocks cured 28 d with cement-tailings ratios 1:4, 1:8, and 1:12 are in the ranges of 4.71 MPa–5.92 MPa, 1.32 MPa–1.69 MPa, and 0.70 MPa–0.88 MPa, respectively. According to the exposed backfill area when adjacent ore mining, the UCS of backfill cured 28d should be no less than 1.0 MPa.
In order to prevent the backfill in the goaves from causing pollution to the groundwater, the cemented backfill test blocks that had been cured for 28 days were broken and all the samples passed through the screen with a diameter of 3 mm. Then, the horizontal vibration method is used to carry out the leaching detection test of heavy metal elements. Figure 10 shows the process of the leaching detection test. The leaching detection test results were as Table 4 shown. According to the leaching detection test results, all the detection indexes are up to the discharge standard (GB25466-2010), which means using tailings backfilling the goaves won't cause pollution to the groundwater.
According to the experimental results, the solid content range of filling slurry is 72%–76%, and the cement-tailings ratio range is 1:4–1:8. According to the tailings production and the volume of goaves, the calculated filling capacity is 110 m3/h and the pipe used is with an outside diameter of 133 mm and 10 mm wall thickness. Figure 11 shows the fill station and goaf backfilling.
FIGURE 11. Fill station and goaf backfilling: (A) fill station (B) filling pipe (C) goaf backfilling.
Between the 808 m level and 928 m level, the total volume of the goaves is about 191,637 m3. By the end of 2022, about 80% of the goaves had been filled.
About 800,000 tons of tailings are produced in A’erhada Lead-Zinc mine every year, and 70% of them are used to backfill the underground voids, which reduces the area of the TSF indirectly. The waste rock stockpiled on the surface is also used to backfill the collapse, accumulating 120,000 m³ waste rock filled into the collapse. Figure 12 shows the comparison of surface collapse before and after backfilling.
FIGURE 12. Comparison of surface collapse before and after backfilled: (A) before (B) after 4 Discussion.
Backfill technology was developed to control the movement of the surrounding rock during mining. With the increasingly high requirement for environmental protection, backfill technology is gradually developed to exert other functions such as disposal of non-hazardous solid waste (tailings, waste rock and slag) and underground goaf filled as this study introduced (Yilmaz et al., 2018; Yin et al., 2018). When using the backfill technology, attentions should be paid to whether it will cause secondary pollution.
According to the standard for pollution control on the non-hazardous industrial solid waste storage and landfill (GB 18599-2020), only class I non-hazardous industrial solid waste can be directly used to backfill the underground goaf or open pit and it is required to be filled into mined-out areas in the original mining area. When using class II non-hazardous industrial solid waste to backfill, the impact of backfill on groundwater, surface water and soil needs to be assessed.
Backfill technology was developed to control the movement of the surrounding rock during mining. With the increasingly high requirement for environmental protection, backfill technology is gradually developed to exert other functions such as disposal of non-hazardous solid waste (tailings, waste rock and slag) and underground goaf filled as this study introduced (Yilmaz et al., 2018; Yin et al., 2018). When using the backfill technology, attentions should be paid to whether it will cause secondary pollution. According to the standard for pollution control on the non-hazardous industrial solid waste storage and landfill (GB 18599-2020), only class I non-hazardous industrial solid waste can be directly used to backfill the underground goaf or open pit and it is required to be filled into mined-out areas in the original mining area. When using class A B II non-hazardous industrial solid waste to backfill, the impact of backfill on groundwater, surface water and soil needs to be assessed.
This paper take A’erhada Lead-Zinc mine as an example introducing the use of tailings backfill technology to solve surface subsidence problems in detail. Through investigating the underground goaves and surface subsidence area and establishing the three-dimensional models of goaves, the volumes of goaves and the area of collapse pits were calculated. According to the results of the flow characteristics of filling slurry test and backfill strength test, the solid content range of filling slurry is 72%–76%, and the cement-tailings ratio range is 1:4–1:8. Leaching test of backfill samples shows that the heavy metal detection indicators meet the environmental protection standard requirements and will not cause secondary environmental pollution. Filling slurry was prepared in the fill station, which self-flowed into the goaves through a 133 mm outside diameter, 10 mm thick pipe. By the end of 2022, about 153,310 m3 had been filled. Also, the waste rock stockpiled on the surface was used to fill the collapse pits. By using tailings to fill the underground goaves and waste rock to fill the collapse pits, grassland collapse is remediated and lands occupied by the TSF and waste rock are reduced.
The original contributions presented in the study are included in the article/Supplementary Material, further inquiries can be directed to the corresponding author.
XC: conceptualization and drafting the manuscript; LG: supervision and validation; YAZ: investigation and modeling; WX: methodology and data analysis; YUZ: manuscript check. All authors listed have made a substantial, direct, and intellectual contribution to the work and approved it for publication. All authors contributed to the article and approved the submitted version.
This research was funded by the National Key R & D Program of China, grant number 2022YFE0129200, and funded by the National Natural Science Foundation of China, grant number 52274122.
Authors XC, LG, WX, and YUZ were employed by BGRIMM Technology Group. Author YAZ was employed by XilinGol Shangdong Gold Group A’erhada Minerals Co., Ltd.
All claims expressed in this article are solely those of the authors and do not necessarily represent those of their affiliated organizations, or those of the publisher, the editors and the reviewers. Any product that may be evaluated in this article, or claim that may be made by its manufacturer, is not guaranteed or endorsed by the publisher.
Chen, Q., Zhang, Q., Wang, X., Xiao, C., and Hu, Q. (2016). A hydraulic gradient model of paste-like crude tailings backfill slurry transported by a pipeline system. Environ. Earth Sci. 75, 1099–9. doi:10.1007/s12665-016-5895-8
Chen, X., Yang, X., Guo, L., Xu, W., and Wei, X. (2020). Risk factors for subsequential carbapenem-resistant Klebsiella pneumoniae clinical infection among rectal carriers with carbapenem-resistant Klebsiella pneumoniae. Chin. J. Eng. 42, 1299–1305. doi:10.2147/IDR.S247101
Cheng, D., Cui, Y., Li, Z., and Iqbal, J. (2021). Watch out for the tailings pond, a sharp edge hanging over our heads: Lessons learned and perceptions from the brumadinho tailings dam failure disaster. Remote Sens. 13, 1775. doi:10.3390/rs13091775
Cheng, H., Wu, S., Li, H., and Zhang, X. (2020). Influence of time and temperature on rheology and flow performance of cemented paste backfill. Constr. Build. Mater. 231, 117117. doi:10.1016/j.conbuildmat.2019.117117
Clarkson, L., and Williams, D. (2020). Critical review of tailings dam monitoring best practice. Int. J. Min. Reclam. Environ. 34, 119–148. doi:10.1080/17480930.2019.1625172
Concha Larrauri, P., and Lall, U. (2018). Tailings dams failures: Updated statistical model for discharge volume and runout. Environments 5, 28. doi:10.3390/environments5020028
Gopala, V. R., à Nijeholt, J.-A. L., Bakker, P., and Haverkate, B. (2011). Development and validation of a cfd model predicting the backfill process of a nuclear waste gallery. Nucl. Eng. Des. 241, 2508–2518. doi:10.1016/j.nucengdes.2011.04.021
Gorakhki, M. H., and Bareither, C. A. (2017). Sustainable reuse of mine tailings and waste rock as water-balance covers. Minerals 7, 128. doi:10.3390/min7070128
Grebby, S., Sowter, A., Gluyas, J., Toll, D., Gee, D., Athab, A., et al. (2021). Advanced analysis of satellite data reveals ground deformation precursors to the brumadinho tailings dam collapse. Commun. Earth Environ. 2, 2. doi:10.1038/s43247-020-00079-2
Janus, J., and Ostrogórski, P. (2022). Underground mine tunnel modelling using laser scan data in relation to manual geometry measurements. Energies 15, 2537. doi:10.3390/en15072537
Jehring, M. M., and Bareither, C. A. (2016). Tailings composition effects on shear strength behavior of co-mixed mine waste rock and tailings. Acta Geotech. 11, 1147–1166. doi:10.1007/s11440-015-0429-1
Kou, Y., Jiang, H., Ren, L., Yilmaz, E., and Li, Y. (2020). Rheological properties of cemented paste backfill with alkali-activated slag. Minerals 10, 288. doi:10.3390/min10030288
Li, Q., Chen, Z., Zhang, B., Li, B., Lu, K., Lu, L., et al. (2020). Detection of tailings dams using high-resolution satellite imagery and a single shot multibox detector in the jing–jin–ji region, China. Remote Sens. 12, 2626. doi:10.3390/rs12162626
Li, S., Yu, L., Jiang, W., Yu, H., and Wang, X. (2022). The recent progress China has made in green mine construction, part i: Mining groundwater pollution and sustainable mining. Int. J. Environ. Res. Public Health 19, 5673. doi:10.3390/ijerph19095673
Li, W., Guo, L., Liu, G., Pan, A., and Zhang, T. (2020). Analytical and experimental investigation of the relationship between spread and yield stress in the mini-cone test for cemented tailings backfill. Constr. Build. Mater. 260, 119770. doi:10.1016/j.conbuildmat.2020.119770
Liu, L., Fang, Z., Wang, M., Qi, C., Zhao, Y., and Huan, C. (2020). Experimental and numerical study on rheological properties of ice-containing cement paste backfill slurry. Powder Technol. 370, 206–214. doi:10.1016/j.powtec.2020.05.024
Liu, Y., Wang, A., and Wu, Y. (2021). Environmental regulation and green innovation: Evidence from China's new environmental protection law. J. Clean. Prod. 297, 126698. doi:10.1016/j.jclepro.2021.126698
Long, N. Q., Buczek, M. M., Hien, L. P., Szlapińska, S. A., Nam, B. X., Nghia, N. V., et al. (2018). Accuracy assessment of mine walls' surface models derived from terrestrial laser scanning. Int. J. Coal Sci. Technol. 5, 328–338. doi:10.1007/s40789-018-0218-1
Ma, S., Li, L., Ke, H., and Zheng, Y. (2022). Environmental protection, industrial structure and urbanization: Spatiotemporal evidence from beijing–tianjin–hebei, China. Sustainability 14, 795. doi:10.3390/su14020795
Piciullo, L., Storrøsten, E. B., Liu, Z., Nadim, F., and Lacasse, S. (2022). A new look at the statistics of tailings dam failures. Eng. Geol. 303, 106657. doi:10.1016/j.enggeo.2022.106657
Rico, M., Benito, G., and Diez-Herrero, A. (2008). Floods from tailings dam failures. J. Hazard. Mater. 154, 79–87. doi:10.1016/j.jhazmat.2007.09.110
Rotta, L. H. S., Alcântara, E., Park, E., Negri, R. G., Lin, Y. N., Bernardo, N., et al. (2020). The 2019 brumadinho tailings dam collapse: Possible cause and impacts of the worst human and environmental disaster in Brazil. Int. J. Appl. Earth Obs. Geoinf. 90, 102119. doi:10.1016/j.jag.2020.102119
Sheshpari, M. (2015). A review of underground mine backfilling methods with emphasis on cemented paste backfill. Electron. J. Geotech. Eng. 20, 5183–5208.
Sun, W., Wang, H., and Hou, K. (2018). Control of waste rock-tailings paste backfill for active mining subsidence areas. J. Clean. Prod. 171, 567–579. doi:10.1016/j.jclepro.2017.09.253
Thompson, F., de Oliveira, B. C., Cordeiro, M. C., Masi, B. P., Rangel, T. P., Paz, P., et al. (2020). Severe impacts of the brumadinho dam failure (minas gerais, Brazil) on the water quality of the paraopeba river. Sci. Total Environ. 705, 135914. doi:10.1016/j.scitotenv.2019.135914
Vergilio, C. d. S., Lacerda, D., Oliveira, B. C. V. d., Sartori, E., Campos, G. M., Pereira, A. L. d. S., et al. (2020). Metal concentrations and biological effects from one of the largest mining disasters in the world (brumadinho, minas gerais, Brazil). Sci. Rep. 10, 5936. doi:10.1038/s41598-020-62700-w
Wang, G., Xu, Y., and Ren, H. (2019). Intelligent and ecological coal mining as well as clean utilization technology in China: Review and prospects. Int. J. Min. Sci. Technol. 29, 161–169. doi:10.1016/j.ijmst.2018.06.005
Wei, Z., Chen, Y., Yin, G., Yang, Y., and Shu, W. (2019). An alternative upstream method for the zhelamuqing tailings impoundment construction of a copper mine in China. Geomech. Eng. 19, 383–392.
Wei, Z., Yin, G., Wang, J.-G., Wan, L., and Li, G. (2013). Design, construction and management of tailings storage facilities for surface disposal in China: Case studies of failures. Waste Manage Res. 31, 106–112. doi:10.1177/0734242X12462281
Yang, L., Wang, H., Li, H., and Zhou, X. (2019). Effect of high mixing intensity on rheological properties of cemented paste backfill. Minerals 9, 240. doi:10.3390/min9040240
Yang, X., Xiao, B., Gao, Q., and He, J. (2020). Determining the pressure drop of cemented gobi sand and tailings paste backfill in a pipe flow. Constr. Build. Mater. 255, 119371. doi:10.1016/j.conbuildmat.2020.119371
Yilmaz, T., Ercikdi, B., and Deveci, H. (2018). Utilisation of construction and demolition waste as cemented paste backfill material for underground mine openings. J. Environ. Manage. 222, 250–259. doi:10.1016/j.jenvman.2018.05.075
Yin, S., Shao, Y., Wu, A., Wang, H., Liu, X., and Wang, Y. (2020). A systematic review of paste technology in metal mines for cleaner production in China. J. Clean. Prod. 247, 119590. doi:10.1016/j.jclepro.2019.119590
Yin, S., Shao, Y., Wu, A., Wang, Y., and Chen, X. (2018). Expansion and strength properties of cemented backfill using sulphidic mill tailings. Constr. Build. Mater. 165, 138–148. doi:10.1016/j.conbuildmat.2018.01.005
Keywords: remediation of subsidence, mine backfill, tailings, grassland ecological protection, filling slurry
Citation: Chen X, Guo L, Zhou Y, Xu W and Zhao Y (2023) Remediation of grassland subsidence and reduction of land occupation with tailings backfill technology: a case study of lead-zinc mine in Inner Mongolia, China. Front. Environ. Sci. 11:1183945. doi: 10.3389/fenvs.2023.1183945
Received: 10 March 2023; Accepted: 02 May 2023;
Published: 11 May 2023.
Edited by:
Ling Xia, Wuhan University of Technology, ChinaReviewed by:
J. Viridiana Garcia Meza, Autonomous University of San Luis Potosí, MexicoCopyright © 2023 Chen, Guo, Zhou, Xu and Zhao. This is an open-access article distributed under the terms of the Creative Commons Attribution License (CC BY). The use, distribution or reproduction in other forums is permitted, provided the original author(s) and the copyright owner(s) are credited and that the original publication in this journal is cited, in accordance with accepted academic practice. No use, distribution or reproduction is permitted which does not comply with these terms.
*Correspondence: Lijie Guo, Z3VvbGlqaWVAYmdyaW1tLmNvbQ==
Disclaimer: All claims expressed in this article are solely those of the authors and do not necessarily represent those of their affiliated organizations, or those of the publisher, the editors and the reviewers. Any product that may be evaluated in this article or claim that may be made by its manufacturer is not guaranteed or endorsed by the publisher.
Research integrity at Frontiers
Learn more about the work of our research integrity team to safeguard the quality of each article we publish.