- 1State Grid Sichuan Electric Power Research Institute, State Grid Sichuan Electric Power Company, Chengdu, Sichuan, China
- 2Power Internet of Things Key Laboratory of Sichuan Province, State Grid Sichuan Electric Power Company, Chengdu, Sichuan, China
- 3School of Electrical and Automation, Wuhan University, Wuhan, Hubei, China
- 4State Grid Sichuan Electric Power Company, Chengdu, Sichuan, China
The flexibility of power systems needs to be enhanced to address the volatility of renewable energy sources, and industrial loads on the demand side have significant potential to improve this flexibility. As a typical high-energy-consuming industrial load, electrolytic aluminum has advantages such as large individual capacity and strong power controllability. However, its participation in various types of grid interaction faces challenges such as unclear power control methods, impacts on normal production, and associated cost burdens. To address these issues, this paper analyzes the production process characteristics of electrolytic aluminum loads and establishes a power control model for these loads. It examines the effects of power regulation on normal production, explores the mechanisms behind regulation costs, and proposes a method for calculating these costs. Considering production safety constraints and power regulation constraints during grid interaction, the paper proposes a control strategy for electrolytic aluminum loads that incorporates process flow and regulation costs. In the case study, the above power control strategy is verified based on the production data of an electrolytic aluminum load. The results show that the above strategy can take into account the response requirements of the power grid and the safety requirements of the load production. A feasible scheme is proposed for the electrolytic aluminum industrial load to participate in the interactive control of the power grid.
1 Introduction
The intensification of the greenhouse effect has drawn widespread global attention (Huang et al., 2021). Integrating renewable energy and developing low-carbon technologies can effectively reduce carbon emissions, making low-carbon green development the mainstream direction for the international community. Developing new power systems with a high proportion of renewable energy is one of the effective ways to achieve low-carbon green development in the future. Developing new power systems with a high proportion of renewable energy is one of the effective ways to achieve low-carbon green development in the future. Artificial intelligence-related technologies have been applied to smart grids to address the challenges brought by the large-scale integration of renewable energy into power systems (Cheng and Yu, 2019). The volatility and instability of new energy sources can affect the quality and frequency stability of the power system (Poncelet et al., 2016; Shu et al., 2017), posing new demands on the system’s ability to adapt to renewable energy. The ability of a power system to rapidly adjust itself based on power demand changes is known as the system’s flexibility. Enhancing this flexibility can be approached from the power generation side, the grid side, and the demand side (Cheng et al., 2022; Cheng et al., 2020). studies the bidding problem in the electricity market based on evolutionary game theory. However, improving flexibility on the power generation and grid sides faces challenges such as high equipment retrofit costs, environmental pollution, and stringent technical and safety requirements (Ren et al., 2021; Lin et al., 2017). On the demand side, reducing user load to balance supply and demand in the grid offers significant potential for enhancing system flexibility. Demand response, a method of demand-side management, can effectively improve power system flexibility. Reference (Cheng et al., 2021) investigates the decision-making problem in demand response management from the perspective of evolutionary game dynamics. Liu et al. (2015) analyzes the power characteristics of residential and commercial loads to integrate them into demand response. However, residential and commercial loads often have small individual capacities, high installation costs for power control terminals, and relatively low overall load response rates. In contrast, high-energy-consuming industrial loads on the demand side have large individual capacities and faster power response speeds (Ding et al., 2014), showing a strong willingness to participate in grid interactions and holding significant potential to enhance the flexibility of the power system (Shoreh et al., 2016). However, high-energy-consuming industrial loads face challenges in participating in grid demand response, such as unclear power control characteristics, potential impacts on normal production, and a lack of incentive mechanisms to enhance response benefits. As a result, the current level of participation of high-energy-consuming industrial loads in demand response is relatively low. In response to the above issues, the problem of power control for high-energy-consuming industrial loads has been widely studied. Paulus and Borggrefe (2011) identifies the regulation potential of high-energy-consuming industrial loads from the technical perspective of power adjustment based on industrial load production processes. Fan et al. (2024) proposes a method for assessing demand response potential based on the power characteristics of industrial loads. Regarding research on power control for different types of industrial loads, Tu et al. (2018) analyzes the power characteristics of steelmaking loads and proposes a power regulation method using the voltage-impedance coordination of electric arc furnaces. Liu et al. (2022) considers the power characteristics of magnesium electrolytic loads and suggests a method for integrating magnesium electrolytic loads into demand-side management. Jiang et al. (2022) addresses the power control characteristics of various loads such as steel and polysilicon and proposes a method for smoothing out renewable energy fluctuations. The electrolytic aluminum industry load is a typical high-energy-consuming industrial load with significant power regulation potential. Its process involves complex physical and chemical reactions, where power regulation can affect product quality and even production safety. Liao et al. (2018) points out that the electrolytic aluminum load has a large adjustable capacity, and brief power adjustments have little impact on normal production, indicating significant potential for power regulation. Based on the power characteristics of electrolytic aluminum loads, Liu et al. (2019) proposes a power control model for electrolytic aluminum participation in auxiliary services. However, research on the interaction of electrolytic aluminum with other types of grid interactions is relatively scarce. To address this issue, this paper uses electrolytic aluminum loads, a typical high-energy-consuming industrial load, as an example to propose a power control method for integrating electrolytic aluminum loads into multiple types of grid interactions, which can effectively enhance grid regulation flexibility. The main contributions of the paper are as follows:
1) Based on the power characteristics of electrolytic aluminum loads, a power control model for electrolytic aluminum industrial loads is established, and key production parameters and their control boundaries are identified.
2) The relationship between power regulation and anode effects is analyzed, and a method for calculating the power regulation costs associated with anode effects under continuous power regulation is proposed.
3) Considering the time scales of multiple types of grid interactions, a power control strategy is proposed based on the production safety requirements of electrolytic aluminum industrial loads and the needs for power regulation, taking into account the process flow and regulation costs.
The rest is organized as fellows: The second section introduces the process flow of electrolytic aluminum loads and the power control model. The third section discusses the impact of power regulation on the production of electrolytic aluminum loads and the associated regulation costs. The fourth section presents the control methods for integrating electrolytic aluminum industrial loads into multiple types of grid interactions. The fifth section provides a simulation analysis of electrolytic aluminum load interactions with the grid under different scenarios. The final section contains conclusions and a summary.
2 Analysis of the process flow and power characteristics of the electrolytic aluminum industry loads
This section mainly introduces the process flow and power regulation characteristics of electrolytic aluminum industrial loads, analyzes the feasibility of power regulation for these loads, and establishes a power regulation model for electrolytic aluminum industrial loads.
2.1 Analysis of the process flow for electrolytic aluminum industrial loads
Electrolytic aluminum industrial loads are typical high-energy-consuming industrial loads, and their process flow involves complex physical-chemical reactions. The process flow includes: electrolytic refining, anode assembly, casting, and auxiliary melting. The electrolytic refining process is the core production stage of the electrolytic aluminum industry, accounting for over 90% of the total energy consumption of the entire process. The anode assembly stage involves cleaning, crushing, and assembling new anodes. The casting stage processes aluminum through electrolytic heating. The auxiliary smelting stage provides oxygen and transports raw materials for the three aforementioned stages. Given the high energy consumption of the electrolytic refining stage and the complex power regulation characteristics of other process stages, the analysis of the power regulation potential in the electrolytic aluminum industry focuses solely on the electrolytic refining stage.
In the electrolytic refining process, the modern electrolytic aluminum industry generally uses alumina as the solute and molten cryolite as the solvent. Under high-temperature conditions, electrolytic cells facilitate the electrochemical reaction between the electrodes to produce aluminum. The primary equipment used is the electrolytic cell. In the cryolite-alumina molten salt electrolysis method, a direct current of several hundred kiloamperes is typically passed through, creating an electrochemical reaction between the electrodes. The product at the cathode is molten aluminum, while the product at the anode is carbon dioxide gas. Schematic diagram of the production process for electrolytic refining is illustrated in Figure 1.
In electrolytic refining process, thermal balance is crucial for aluminum production. The process requires maintaining the electrolytic cell within a high-temperature range, which is controlled by adjusting the direct current supplied. Prolonged power adjustments can affect the state of the molten cryolite in the cell, and during the start of production, it's important to prevent cryolite from solidifying to avoid “freezing of the cell,” which can significantly impact production safety and economic benefits. However, the electrolytic cell has a large thermal inertia, allowing it to maintain suitable refining temperatures for a longer period even when power decreases. Therefore, short-term power adjustments have minimal impact on thermal balance. Interruptions in the cell lasting from a few minutes to 3 h might affect aluminum production, but they will not cause cryolite to solidify. Thus, short-term power adjustments have little effect on production, indicating the feasibility of power control in electrolytic aluminum industrial loads.
In electrolytic refining process, the direct current passing through the electrolytic cell is collected into the DC bus after being rectified by multiple sets of rectifier bridges. The topology of the electrolytic refining process is shown in Figure 2.
In electrolytic refining process, the load tap-changing transformer, rectifier transformer, and saturation reactor convert AC into DC through the rectifier bridge. The saturation reactor, which is connected in series, mainly eliminates the anode effect during the electrolytic process. When the anode effect causes an increase in the DC side voltage, the saturation reactor mitigates this by increasing the voltage drop through changes in its inductance. The normal voltage drop across the saturation reactor is around 20 V, with a maximum designed value of 60 V, which can offset the 30–40 V DC voltage variation caused by the anode effect. In the electrolytic aluminum industry load, the electrolytic refining process is divided into different series, each of which is independent. Within these series, all electrolytic cells are connected in series, while the rectification part involves parallel rectification of all rectifier units. All electrolytic cells can be equated to a series resistance and a series back electromotive force. There is a linear relationship between the DC voltage and the DC current of the electrolytic cell, which can be expressed as Equation 1:
Where EAL,i represents the equivalent back electromotive force of series i, RAL,i represents the equivalent resistance of series i, UB,i is the DC side voltage of series i, and Id,i is the DC side current of series i. The equivalent back electromotive force and equivalent resistance of the series are parameters to be identified, which can be determined through parameter identification of the DC voltage and DC current. Therefore, the equivalent circuit diagram of the electrolytic cells within a series can be represented as shown in Figure 3.
Where UAH,i represents the high-voltage side voltage of series i, UAL,i represents the low-voltage side voltage of series i, and USR,i is the voltage drop across the saturation reactor of series i. The power characteristics of electrolytic refining can be expressed as shown in Equations 2, 3 (Jiang et al., 2014).
Where PAL,i represents the active power consumed by the electrolytic refining series i, and kAL,i is the tap ratio of the on-load tap changer for series i. From the above power characteristics, it is evident that the power of the electrolytic refining process can be adjusted by regulating the tap ratio of the on-load tap changer and controlling the voltage drop across the saturation reactor. However, the participation of electrolytic aluminum industry loads in multi-type grid interactions requires consideration of different time scales. Adjusting the ratio of an on-load tap-changing transformer typically takes several seconds, while adjusting the taps of a multi-tap transformer may take tens of seconds. In such cases, it cannot meet the grid frequency regulation requirements at the second scale. If the method of changing the voltage drop of a saturated reactor is adopted, power regulation can be completed within tens of milliseconds. To meet the time scale requirements for multi-type grid interactions, this paper considers regulating the voltage drop of the saturated reactor to achieve power regulation of the electrolytic aluminum industry load. For a series of electrolytic cells, the regulation of the saturation reactor is divided into individual and total adjustments. Individual adjustment refers to controlling a single saturation reactor, which has limited power regulation capability. Usually, power regulation in the electrolytic refining process is achieved through total adjustment, where instructions are issued to simultaneously adjust the voltage drops of all saturation reactors. The voltage drop of the saturation reactor has regulatory constraints; excessive voltage drop may cause the saturation reactor to lose its effect of eliminating anode effects, while insufficient voltage drop affects power regulation. The constraints on the voltage drop regulation of the saturation reactor are shown in Equation 4:
Where USR,imin,USR,imax represent the minimum and maximum voltage drops of the saturation reactor required for production safety in the electrolytic refining process. It is assumed that, within the same series of electrolytic refining processes, all saturation reactors have the same voltage drop value when regulating power.
In summary, the power regulation of the electrolytic refining process for electrolytic aluminum industry loads is feasible. The power consumed by different series in the electrolytic refining process of electrolytic aluminum can be expressed as shown in Equation 5:
Where
Where
It is important to note that changes in the temperature of the electrolytic cell have a significant impact on the electrolytic aluminum production process. The production of electrolytic aluminum requires high-temperature and high-current density conditions, so variations in the electrolytic cell temperature can affect both the yield and quality of the electrolytic aluminum. When the temperature of the electrolytic cell exceeds the rated temperature, the increase in temperature will lead to a rise in the conductivity of the electrolyte and the rate of the electrolytic reaction. However, if the temperature is too high, it can cause the formation of bubbles and crusts on the surface of the aluminum metal. Additionally, variations in the electrolytic cell temperature can also affect the physical and chemical properties of the electrolyte, such as solubility, viscosity, density, and other characteristics, leading to changes in the electrolyte’s properties and impacting current efficiency, which in turn affects the yield and quality of the electrolytic aluminum. Moreover, changes in the electrolytic cell temperature can also influence the lifespan of the refractory materials and equipment of the electrolytic cell. Excessive temperature can accelerate the wear and corrosion of the equipment, thereby shortening its service life. Therefore, when participating in power regulation for the electrolytic refining process, the temperature within the electrolytic cell needs to be considered. The energy conversion within the electrolytic cell during the electrolytic refining process mainly involves the conversion of electrical energy to thermal energy, potential energy, and energy losses. Here, it is assumed that electrical energy conversion to useful energy and energy losses are constant, meaning that the temperature changes within the electrolytic cell are only influenced by the active power regulation of the electrolytic refining process. When the active power in the electrolytic refining process changes, the temperature variation in the electrolytic cell can be expressed as shown in Equation 7:
Where
Where
3 Calculation method for load power regulation costs in the aluminum electrolysis industrial loads
The process flow in electrolytic aluminum industry involves numerous complex physical and chemical reactions, and power regulation can affect the production order. It is necessary to calculate the cost of power regulation to quantify its impact on normal production. Different production states in the electrolytic refining stage vary, and by quantifying the cost of power regulation for different series, decisions can be made regarding the sequence of series participating in power regulation, which helps to minimize the impact of power regulation on normal production.
When regulating power during the electrolytic refining stage, it is important to consider the anode effects and loss costs due to temperature changes. Since short-term power regulation has minimal impact on the electrolytic cell’s temperature, temperature-related loss costs are not considered here. The anode effect significantly impacts normal production in the electrolytic aluminum industry, and its control costs need to be considered. Typically, losses from the anode effect are categorized into four areas: electrical energy loss, raw material loss, atmospheric pollution loss, and the cost of extinguishing the anode effect. The anode effect increases cell voltage, thereby raising energy consumption. The increased voltage typically converts electrical energy into heat during production, causing a rapid rise in temperature between the cell electrodes and spreading around the anode, leading to substantial raw material volatilization. Additionally, the anode effect produces gases harmful to the atmospheric ozone layer, which adds to atmospheric pollution costs. Extinguishing the anode effect requires additional raw materials. Regulation costs in aluminum electrolysis loads can be expressed as Equations 9–13:
Where
Where
In summary, the cost associated with power regulation in the electrolytic refining process can be expressed as Equation 15:
Where
Where
4 Strategies for the electrolytic aluminum industry load to participate in multiple types of power grid interactions
When electrolytic aluminum industry load participates in multiple types of power grid interactions, it is necessary to consider the impact of power regulation on its normal production. Based on the cost of power regulation, a load power regulation plan should be developed to minimize the costs incurred due to power regulation.
The main method for power regulation of the electrolytic aluminum industry load is through saturation reactors. Saturation reactors can adjust their own voltage drop within a very short time, allowing the electrolytic aluminum industry load to meet the power grid’s interaction control requirements across different time scales. Types of grid interactions generally include frequency regulation and demand response. In different types of grid interactions, the time scale of period t varies. Typically, power users participating in multiple types of grid interactions must meet power regulation capacity requirements. For grid interaction control with shorter time scales, such as aiding the grid in accommodating renewable energy, the power regulation requirements are specifically represented as shown in Equations 17–19:
Where
For grid interaction control with longer time scales, such as participating in demand response, load power curve collection is conducted over a specific time period t. During the specified time period, it is necessary to meet the capacity response requirements, as specifically represented in Equation 20.
Where
When electrolytic aluminum industry load participates in different types of grid interactions, it prioritizes the impact of its power regulation on normal production. Its strategies for participating in various types of grid interaction control are as shown in Equation 21.
5 Example and result
5.1 Description of the example
To verify the effectiveness of the electrolytic aluminum load’s participation in different types of grid interaction control strategies, considering process flow and regulation costs, this section sets up scenarios where an electrolytic aluminum industrial load participates in grid fast power regulation, demand response, and other activities. The relevant production data for the electrolytic aluminum load is shown below.
Assuming the electrolytic aluminum industrial load has 3 production series in its electrolytic refining stage, with the number of electrolytic cells being 320, 310, and 335 respectively. The cells are of the same type, with a direct current (DC) current of 445 kA under normal operating conditions and a saturation reactor voltage drop of 20 V. The series equivalent resistances calculated from production data are 2.8764, 2.7865, and 3.0112 mΩ, and the series equivalent electromotive forces are 496.44, 425.28, and 531.9 V, respectively. The load baseline is its rated power during normal operation, as it needs to maintain a stable DC current. The control range for the saturation reactor voltage drop is 0–70 V. The cost of anode effects for different series is 9,500, 8,700, and 10,500 yuan. The anode effect occurrence probability coefficients b1 are 1/6,400, 1/6,200, and 1/7,000, and b2 coefficients are 1/4,000, 1/3,700, and 1/4,500. The temperature limits in the electrolytic cells are 970 and 950°C. The existing power control strategy for electrolytic aluminum industry loads distributes the power that needs to be regulated equally across different electrolytic refining series.
5.2 Electrolytic aluminum industrial load participating in grid fast power regulation scenarios
When the electrolytic aluminum industrial load participates in grid fast power regulation scenarios, the time scale for power regulation requirements is generally not slower than the second level. Assuming the grid issues a power regulation instruction with a total duration of 40 s, the power regulation instruction is shown in Figure 4.
Based on the above power regulation strategy, the power regulation states of different series in the electrolytic refining stage of the electrolytic aluminum industrial load and the changes in the saturation reactor voltage drop are shown in Figures 5, 6.
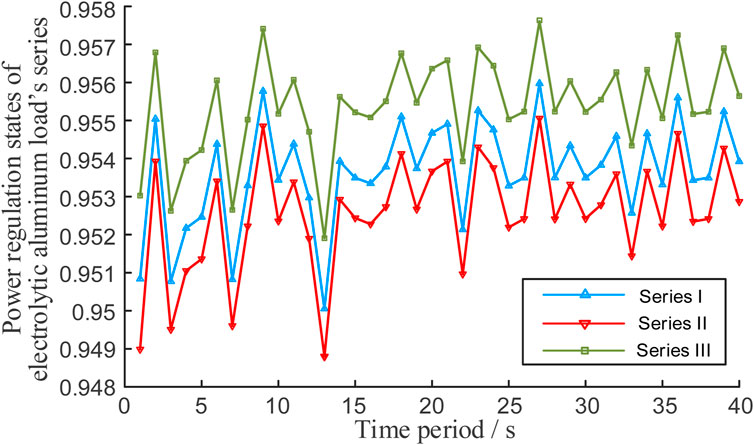
Figure 5. Power regulation states of different series in the electrolytic refining stage during fast power regulation.
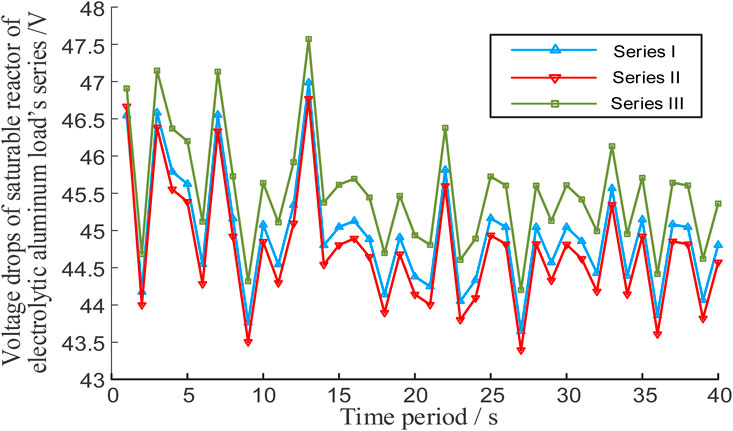
Figure 6. Changes in saturation reactor voltage drop for different series in the electrolytic refining stage during fast power regulation.
In the above power regulation scenario, the overall cost incurred by the electrolytic aluminum industrial load participating in power regulation amounts to 180,950 yuan. During the interaction of the electrolytic aluminum industrial load with the grid, the overall power in the electrolytic refining stage can follow changes in the power regulation instruction. Throughout the entire power regulation process, the voltage drop of the saturation reactors in different series remains within the normal operating range, and the voltage drop changes in different series are similar. This indicates that the above power regulation strategy ensures normal production of the electrolytic aluminum load while minimizing the cost incurred from power regulation. As shown in Figure 5, each stage’s power regulation capacity accounts for about 5% of the rated capacity. Short-term regulation has a minimal impact on the normal production of the electrolytic aluminum industrial load, so the effect of temperature changes is not considered at this time.
5.3 Electrolytic aluminum industrial load participating in grid demand response power regulation scenarios
When the electrolytic aluminum industrial load participates in grid demand response power regulation, the typical time scale for power regulation requirements is 15 min. Assuming a total response duration of 5 h, the response demands for different hours are: 246,000, 254,000, 255,250, 268,000, and 264,000 kWh. The anode effect caused by power regulation over a longer time scale has a greater impact on the normal production of the electrolytic aluminum load, leading to increased costs of 142,500, 130,500, and 157,500 yuan. Assuming the temperature of the electrolytic refining stage is maintained at 960°C, the power regulation states of different series, voltage drop changes in saturation reactors, and the temperature changes of the electrolytic cell are shown in Figures 7–9, with the power regulation effects detailed in Table 1.
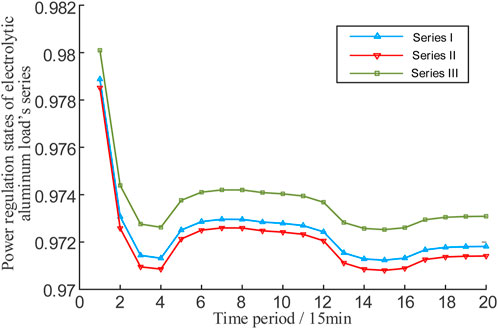
Figure 7. Power regulation states of different series in electrolytic refining during demand response.
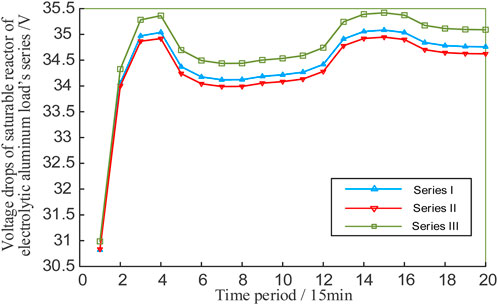
Figure 8. Voltage drop changes of different series of saturation reactors in electrolytic refining during demand response.
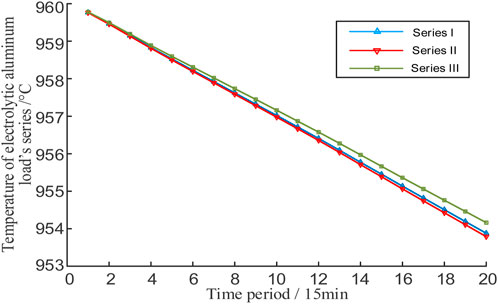
Figure 9. Temperature change states of different series of electrolytic cells in electrolytic refining during demand response.
The power regulation cost incurred by the electrolytic aluminum industrial load participating in the above-mentioned demand response scenario is 453,470 yuan. Based on the calculation results, it can be seen that the electrolytic aluminum industrial load’s participation in demand response can meet the power regulation capacity requirements. During the power regulation period, the voltage drop across the saturation reactors consistently meets the normal operational requirements. The temperature of the electrolytic cells decreased by only about 6°C throughout the entire response process, which has almost no impact on the normal production order of the electrolytic aluminum industry, validating the effectiveness of the proposed power regulation strategy.
If the conventional power regulation strategy is used, where the capacity response demand is evenly distributed across different electrolytic refining series, the electrolytic aluminum industry load would still meet the power regulation capacity requirements. During the power regulation period, the voltage drop across the saturated reactor would also meet normal operating requirements. However, the power regulation cost in this case would be 453,787 yuan. This result demonstrates that the aforementioned power regulation strategy, while meeting production safety requirements, reduces the power regulation costs for the electrolytic aluminum industry load’s participation in grid interactions compared to the conventional power regulation method.
6 Conclusion
This paper addresses the issue of electrolytic aluminum industry loads participating in multi-type grid interactions, which can affect normal production processes. It proposes a control strategy for electrolytic aluminum load participation in multi-type grid interactions, taking into account the production process and regulation costs. Based on the characteristics of the electrolytic aluminum production process, key power regulation parameters of critical production equipment are analyzed, and a power regulation model for electrolytic aluminum industry loads is proposed, along with the regulation boundaries of key production parameters. The mechanism of anode effect generation during the electrolysis process is studied, and a method for calculating the cost of power regulation resulting from the anode effect is introduced, considering the dynamic nature of continuous power regulation. The strategy integrates production safety constraints of the electrolytic aluminum load and the power regulation capacity constraints for grid interactions, considering the time scale requirements of different types of interactions. A power regulation strategy is proposed, factoring in both the production process and the costs of power regulation. Finally, the proposed power regulation strategy is validated through simulations under different grid interaction scenarios. The simulation results show that the strategy effectively meets grid regulation needs while minimizing the impact of power regulation on normal electrolytic aluminum production. This provides a feasible and effective solution for the participation of electrolytic aluminum industry loads in multi-type grid interactions. In future research, the strategy will be further refined by considering the specific characteristics of the electrolytic aluminum production process for participation in multi-type grid interactions.
Data availability statement
The original contributions presented in the study are included in the article/supplementary material, further inquiries can be directed to the corresponding author.
Author contributions
XW: Funding acquisition, Project administration, Writing–review and editing. BC: Conceptualization, Data curation, Investigation, Methodology, Writing–review and editing. HX: Formal Analysis, Methodology, Validation, Writing–original draft. XY: Visualization, Writing–review and editing. JB: Software, Writing–review and editing.
Funding
The author(s) declare that financial support was received for the research, authorship, and/or publication of this article. This work is supported by the State Grid Corporation of China’s technology project: Research and application of flexible load participation in grid regulation and safety control technology (521997230019).
Conflict of interest
Author XY was employed by State Grid Sichuan Electric Power Company.
The remaining authors declare that the research was conducted in the absence of any commercial or financial relationships that could be construed as a potential conflict of interest.
The authors declare that this study received funding from State Grid Sichuan Electric Power Company. The funder had the following involvement in the study: they provided the study design.
Publisher’s note
All claims expressed in this article are solely those of the authors and do not necessarily represent those of their affiliated organizations, or those of the publisher, the editors and the reviewers. Any product that may be evaluated in this article, or claim that may be made by its manufacturer, is not guaranteed or endorsed by the publisher.
References
Cheng, L., Chen, Y., and Liu, G. (2022). 2PnS-EG: a general two-population n-strategy evolutionary game for strategic long-term bidding in a deregulatedmarket under different market clearing mechanisms. Int. J. Electrial Power and Energy Syst. 142, 108182. doi:10.1016/j.ijepes.2022.108182
Cheng, L., Liu, G., Huang, H., Wang, X., Chen, Y., Zhang, J., et al. (2020). Equilibrium analysis of general N-population multi-strategy games for generation-side long-term bidding: an evolutionary game perspective. J. Clean. Prod. 276, 124123. doi:10.1016/j.jclepro.2020.124123
Cheng, L., Yin, L., Wang, J., Shen, T., Chen, Y., Liu, G., et al. (2021). Behavioral decision-making in power demand-side response management: a multi-population evolutionary game dynamics perspective. Int. J. Electrial Power and Energy Syst. 129, 106743. doi:10.1016/j.ijepes.2020.106743
Cheng, L., and Yu, T. (2019). A new generation of AI: a review and perspective on machine learning technologies applied to smart energy and electric power systems. Int. J. Energy Res. 43 (6), 1928–1973. doi:10.1002/er.4333
Ding, Y., Min, S., Ho, H., and Xiao, H. (2014). A demand response energy management scheme for industrial facilities in smart grid. IEEE Trans. Industrial Inf. 10 (4), 2257–2269. doi:10.1109/tii.2014.2330995
Fan, Y., Jiang, T., Huang, Q., and Ju, P. (2024). Portrait-based assessment on demand response potential of industrial parks. Automation Electr. Power Syst. 48 (1), 41–49.
Huang, Y., Ding, T., Li, Y., LiI, L., Chi, F., Wang, K., et al. (2021). Decarbonization technologies and inspirations for the development of novel power systems in the context of carbon neutrality. Proc. CSEE 41 (zk), 28–51.
Jiang, H., Lin, J., Song, Y., Gao, W., Xu, Y., Shu, B., et al. (2014). “Demand side frequency control scheme in an isolated wind power system for industrial aluminum smelting production,” in 2014 IEEE PES General Meeting/Conference and Exposition, National Harbor, MD, USA, 1–1.
Jiang, X., Xu, J., Liao, S., and Sun, Y. (2022). Coordinated control scheme of multi-type loads for wind power fluctuation in industrial parks considering the difference in response willingness of industrial users. Eng. J. Wuhan Univ. 55 (09), 876–885.
Liao, S., Xu, J., Sun, Y., and Bao, Y. (2018). Local utilization of wind electricity in isolated power systems by employing coordinated control scheme of industrial energy-intensive load. Appl. Energy 217 (1), 14–24. doi:10.1016/j.apenergy.2018.02.103
Lin, L., Zou, L., Zhou, P., and Tian, X. (2017). Multi-angle economic analysis on deep peak regulation of thermal power units with large-scale wind power integration. Automation Electr. Power Syst. 41 (7), 21–27.
Liu, C., Sun, A., Wang, Y., He, H., Zhang, H., and Ning, L. (2022). Day-ahead and intra-day joint economic dispatching method of electric power system considering combined peak-shaving of fused magnesium load and energy storage. Electr. Power Autom. Equip. 42 (2).
Liu, J., Zeng, K., Wang, C., Le, L., Zhang, M., and Ai, X. (2019). “Unit commitment considering electrolytic aluminum load for ancillary service,” in 2019 4th International Conference on Intelligent Green Building and Smart Grid(IGBSG), Hubei, China, 6-9 September 2019, 608–611. doi:10.1109/igbsg.2019.8886327
Liu, M., Quilumba, F. L., and Lee, W. J. (2015). A collaborative design of aggregated residential appliances and renewable energy for demand response participation. IEEE Trans. Industry Appl. 51 (5), 3561–3569. doi:10.1109/tia.2015.2427286
Paulus, M., and Borggrefe, F. (2011). The potential of demand-side management in energy-intensive industries for electricity markets in Germany. Appl. Energy 88 (2), 432–441. doi:10.1016/j.apenergy.2010.03.017
Poncelet, K., Hoschle, H., Delarue, E., Virag, A., and Drhaeseleer, W. (2016). Selecting representative days for capturing the implications of integrating intermittent renewables in generation expansion planning problems. IEEE Trans. Power Syst. 32 (3), 1936–1948. doi:10.1109/tpwrs.2016.2596803
Ren, J., Xue, C., and Ma, X. (2021). Two-stage model of peak regulation ancillary service market with source-load interaction. Automation Electr. Power Syst. 45 (18), 94–102.
Shoreh, M. H., Siano, P., Shafie-Khah, M., and Loia, V. (2016). A survey of industrial applications of demand Response. Electr. Power Syst. Res. 141, 31–49. doi:10.1016/j.epsr.2016.07.008
Shu, Y., Zhang, Z., Guo, J., and Zhang, Z. (2017). Study on key factors and solution of renewable energy accommodation. Proc. CSEE 37 (1), 1–8.
Keywords: industrial load, grid interaction control, load power flexibility control, control strategy, electrolytic aluminum load
Citation: Wang X, Chen B, Xie H, Ye X and Bai J (2025) Participation of electrolytic aluminum loads in grid interaction control strategies considering process flow and regulation costs. Front. Energy Res. 12:1493558. doi: 10.3389/fenrg.2024.1493558
Received: 09 September 2024; Accepted: 29 November 2024;
Published: 06 January 2025.
Edited by:
Pengfei Zhao, Chinese Academy of Sciences (CAS), ChinaReviewed by:
Lefeng Cheng, Guangzhou University, ChinaXiandong Xu, Tianjin University, China
Yingjun Wu, Hohai University, China
Copyright © 2025 Wang, Chen, Xie, Ye and Bai. This is an open-access article distributed under the terms of the Creative Commons Attribution License (CC BY). The use, distribution or reproduction in other forums is permitted, provided the original author(s) and the copyright owner(s) are credited and that the original publication in this journal is cited, in accordance with accepted academic practice. No use, distribution or reproduction is permitted which does not comply with these terms.
*Correspondence: Haocong Xie, MTc1Mjk1OTMwMkBxcS5jb20=