- 1Alan Levin Department of Mechanical and Nuclear Engineering, Carl R. Ice College of Engineering, Kansas State University, Manhattan, KS, United States
- 2Strategic Energy Analysis Center, National Renewable Energy Laboratory (DOE), Golden, CO, United States
Introduction: There is a global goal to reduce greenhouse gas emissions by 43% by 2023. Nuclear microreactors, a subset of small modular reactors, offer a potential solution due to their compact size, transportability, and carbon-neutral power generation capabilities.
Methods: This study explores the feasibility of using heat from nuclear microreactors for bioconversion and agricultural processes, including transforming biomass into energy carriers and products such as syngas, bio-oil, and pasteurized milk. Operating requirements for gasification, pyrolysis, hydrothermal carbonization, hydrothermal liquefaction, hydrothermal gasification, ethanol production, anaerobic digestion, and pasteurization were obtained through a literature review. A Brayton cycle model based on the eVinciTM microreactor was developed to assess the feasibility of powering these processes using nuclear microreactor heat.
Results and Discussion: Exergetic efficiency values for high-temperature processes ranged from 72% to 100%, whereas lower-temperature processes ranged from 2% to 53%. These efficiencies depend on the available source temperature for each microreactor design. There were trade-offs between producing net power and using process heat, particularly for high-temperature processes. Three heat exchanger locations were considered: before the turbine (600
1 Introduction
Since the introduction of the Kyoto Protocol in 1997 (United Nations Climate Change, 1997) and leading up to the United Nations Framework Convention on Climate Change in 2022 (COP 27, 2022), international efforts, including the development of policies such as the Paris Agreement in 2015, have been aimed at limiting the increase of the global average temperature to 1.5°C (Paris Agreement, 2015). Thus far, only 4.5% of countries worldwide have achieved carbon neutrality, and most plan to do so by 2050–2070 (Chen et al., 2022; Zou et al., 2021). Per the findings of the International Energy Agency (IEA), it is considered critical to discontinue the expansion of extracting and using additional crude oil, coal, combustion, and natural gas by 2021 to achieve global carbon neutrality by 2050 (Chenic et al., 2022; Hanssen et al., 2020). Nuclear microreactors are an emerging carbon-neutral technology that can produce both heat and electricity on a smaller scale than a typical nuclear power plant (Zohuri, 2020). According to the Nuclear Energy Agency, small modular reactors (SMRs) have been securing the attention of policymakers as a suitable technology to address issues outlined in the Paris Agreement (Vaya Soler et al., 2021). Bioconversion and agricultural processes could benefit from the future integration of SMRs and further contribute to achieving global climate goals. Biofuels from bioconversion processes are a clean, reliable renewable energy source that helps stabilize energy grids and reduce reliance on fossil fuels in the economy (Graham et al., 2022). The objective of this brief research report is to serve as a guide for feasible bioconversion methods using the process heat of nuclear microreactor designs currently in development; that is, to analyze the tradeoffs present when concurrent processes operate using microreactor heat. Additionally, the report provides a brief literature review of bioconversion and agricultural processes, focusing on the respective required operating conditions and parameters needed to interface with microreactors. Research into integrating nuclear microreactors with bioconversion and agricultural processes represents a promising pathway toward achieving global climate goals by enhancing energy efficiency and reducing carbon emissions.
2 Nuclear microreactors
Nuclear microreactors are a subset of SMRs, which are advanced nuclear reactors that produce electricity up to 300 MWe per module or individual reactor unit (Peakman et al., 2018). Microreactors, however, typically have a power output below 20 MWe but can range from 1 to 50 MWe (Black et al., 2023); Table 1 lists the specifications for several microreactor concepts along with their design features, power production, process heat availability, and operational conditions. Nuclear microreactors, in general, are at a technology readiness level (TRL) of 4 to 5 (Testoni et al., 2021). This status is attributed to confirmed conceptual designs and validation of related technologies, including heat pipes and TRISO fuel. Microreactors are envisioned to be manufactured in a facility and shipped to their end use location or remain as transportable, mobile units (Antonello et al., 2023; Huning et al., 2023; Sugawara, 2024); subsequently, microreactor safety is an active research topic (Antonello et al., 2023; Huning et al., 2023; Sugawara, 2024; Moe, 2019). Antonello et al. (2023) presented a safety analysis of a 5 MWt, heat-pipe-cooled nuclear battery designed at MIT for autonomous operation and noted potential safety concerns related to using yttrium hydride as the moderator, risks associated with the loss of the working fluid (i.e., sodium) from the heat pipes, and quantification of necessary reaction time. Huning et al. (2023) presented a preliminary safety analysis for a 1 MWt microreactor utilizing TRISO fuel.
There are several nuclear reactor design technologies that enable wider service areas to different energy end-uses at varying capacity levels. For instance, high-temperature gas reactors operate at 750°C–950°C which allows it to be a great application for supplying industrial process heat. By using helium as its cooling gas, these reactors are able to obtain high thermal efficiency. High-temperature gas reactors are a mature technology originally proposed in 1945, which have been deployed commercially globally at the megawatt scale. Second, light-water reactors, also known as boiling water reactors and pressurized-water reactors, utilize water as the reactor’s moderated coolant. These reactors typically operate at approximately 320°C and of the available power generating reactor technologies, light-water reactors are the only type of reactors operating in the United States at industrial scale (NEA No. 7629: High-Temperature Gas-Cooled Reactors and Industrial Heat Applications, 2022). Third, liquid metal fast reactors use a more mature uranium or plutonium-based fuel that enables greater thermal efficiencies up to around 40%. For the reactor coolant, instead of water, liquid metals such as mercury, or molten salt mixtures of sodium or potassium have been used (Khodarev, 1978). Similarly to liquid metal fast reactors, molten salt reactors operate at similar temperature ranges >600°C, and use molten salts as primary coolants. Both of these reactor designs also boast safer operation than traditional light-water reactors due to their near atmospheric operating pressure, the chemically inert properties of molten salts, and the lack of irradiation damage to mechanical systems of the reactor (Status of Molten Salt Reactor Technology, Technical Reports Series No. 489, 2023). Finally, heat pipe reactors are small, compact reactors that are characterized by their passive heat transfer capability through the use of capillary forces. Heat pipe reactors usually operate in a temperature range from 650°C–1,240°C. Its design differentiates from other reactor technologies and allows it to be more easily transportable and more readily deployable, making it attractive for SMR applications (Yan et al., 2020).
In addition to being carbon neutral, the small size and relative ease of deployment make microreactors excellent candidates for supplying power to military installations, remote areas, mining sites, and critical infrastructure, such as hospitals (Zhang et al., 2024). Microreactors are valuable for use in remote or critical areas because they are not limited by the need for continuous refueling, unlike diesel generators or small gas turbines. Depending on the design, microreactors can run between 3 and 20 years before refueling is required (Ultra Safe Nuclear, 2019; X-Energy, 2024). They can function independently within an electric grid or contribute to a microgrid by generating electricity and process heat.
Currently, a significant drawback of installing nuclear microreactors is their rate of return on investment, which is driven by high expected initial capital costs (Kalinichenko et al., 2024). Another challenge is the availability of nuclear fuel for microreactors, such as TRISO, which faces supply chain limitations due to complex production processes and limited infrastructure (Terrani, 2022). To improve this return on investment, research is being conducted to maximize the utility of the process heat created by these microreactors (Guillen, 2023). One example, and a focus of this brief research report, is the use of microreactor process heat for bioconversion methods such as gasification, pyrolysis, hydrothermal carbonization (HTC), hydrothermal liquefaction (HTL), and hydrothermal gasification (HTG). These bioconversion methods transform renewable biomass or organic materials into useful energy carriers or other products—most notably, biofuels. Another focus of this research report is the application of microreactor process heat for various agricultural processes, including ethanol production, anaerobic digestion (AD) systems, and the pasteurization of milk.
As outlined in Table 1, a variety of microreactor design technologies are available, such as high-temperature gas reactors, light-water reactors, liquid metal fast reactors, molten salt reactors, and heat pipe reactors. Because these microreactor designs operate based on distinct technologies, they lead to variations in the available process heat temperatures and therefore suitable applications. Note that the microreactor designs present in Table 1 are in varying stages of development and licensure, and that the table is not an exhaustive list of all current microreactor concepts globally. As time passes, the information surrounding each design will likely become more readily available.
3 Bioconversion and agricultural processes
Biomass contributed approximately 1.3% to the total U.S. utility-scale electricity generation and made up 5.9% of electricity generation from renewable sources in 2022 (EIA, 2023). Electrical generation from all renewable energy sources globally is forecasted to increase from 29.5% in 2022 to 42% in 2028 (IEA, 2023). Nuclear microreactors could be leveraged for their process heat to facilitate bioconversion methods, and can also benefit agricultural processes. The processes described in this section are gasification, pyrolysis, HTC, HTL, HTG, ethanol production, AD systems, and pasteurization. The bioconversion processes discussed use a wide variety of biomass feedstocks. These feedstocks include lignocellulosic biomass, municipal solid waste, algae, sugar and starch crops, oily biomass, and animal waste, among others. The following bioconversion and agricultural processes have been reviewed in the literature in greater detail (Gollakota et al., 2018; Meegoda et al., 2018; Onuki et al., 2008; Pereira et al., 2012). This section briefly describes each process while highlighting operating conditions; operating conditions are summarized in Supplementary Table S5 in the Supplementary Material.
3.1 Gasification
Gasification is a thermochemical process in which carbon-based fuels in sub-stoichiometric conditions are transformed into a combustible gas known as syngas (i.e., producer gas, product gas, synthetic gas, or synthesis gas), along with byproducts tar and char (Rand and Dell, 2009; Zhang et al., 2019). This syngas primarily comprises of CO, H2, CH4, CO2, water vapor, smaller amounts of H2S, COS, and other trace contaminants (NETL, 2022); however, the composition of the syngas greatly depends on the feedstock used. Gasifiers can be classified into several types, including fixed bed, fluidized bed, and entrained flow gasifiers, each having distinct operational traits and syngas production profiles. Ideally in gasification, the moisture in the biomass feedstock is below 30%. If not, the gasification efficiency significantly decreases due to some energy being spent toward vaporization, thereby decreasing the gasification temperature. The gasification temperature is preferably high (600°C–1,200°C) because at higher temperatures, less tar and char are produced, thereby yielding more syngas. The carbonaceous biomass is treated and can be pressurized or unpressurized with air as a working fluid (De Filippis et al., 2015). Pressurized gasifiers can be useful when coupled with a turbine for concurrent electrical generation; however, they are more complex and bring high operational costs (Speidel et al., 2015).
3.2 Pyrolysis
Pyrolysis is a similar thermochemical process to gasification but differs due to the lack of a gasifying agent and lower process temperatures (Pecchi and Baratieri, 2019). The biomass feedstock is thermally degraded in an inert environment, resulting in the production of bio-oil, biochar, and syngas (Yung et al., 2016). Bio-oil derived from pyrolysis is typically a dark, viscous liquid fuel made up of oxygenated organic compounds and water (United States Department of Agriculture (USDA), 2017). The proportions of these products greatly depend on the feedstock used and the operating parameters. Like gasification, the feedstock needs a low moisture content to avoid preliminary drying, below 30%. There are three types of pyrolysis: slow pyrolysis, fast pyrolysis, and flash pyrolysis. Each has unique process temperature and residence times. Slow pyrolysis operates from 300°C to 550°C, with a residence time of 5–30 min and a heating value of 10°C/min. Fast pyrolysis operates from 500°C to 600°C, with a residence time of 0.5–2 s and a heating value of 10°C–1,000°C/s. Flash pyrolysis operates from 900°C to 1,300°C, with a residence time of less than 0.5 s and a heating value greater than 1,000°C/s (Sakthivel et al., 2024). Bio-oil production is maximized at process temperatures of 500°C and a heating rate of 1,000°C/s, where bio-oil yields can reach 60–70 wt% from a typical biomass feedstock (USDA, 2021).
3.3 Hydrothermal carbonization
Unlike gasification and pyrolysis, HTC requires significantly lower process temperatures, ranging from 180°C to 350°C (Berge et al., 2011). During HTC, the goal is the combined dehydration and decarboxylation of the biomass feedstock to achieve a higher calorific value (Funke and Ziegler, 2010). Along with a gas fraction and an aqueous liquid fraction, this results in the end product being a lignite-like char called hydrochar. HTC is conducted in pressurized water. Because the process is wet, this negates the need for feedstocks to reach a certain moisture level, thereby enabling a larger variety of viable feedstocks. The pressure required for HTC is determined by the saturation pressure of water at the process temperature (i.e., autogenous pressure), typically 2–10 MPa (Pecchi and Baratieri, 2019). Common feedstocks for HTC are rich in cellulose and include bagasse, straw, corn, and stover (Reza et al., 2014).
3.4 Hydrothermal liquefaction
Like HTC, HTL is a wet process, thereby enabling the treatment of wet biomass. Rather than the production of a hydrochar, HTL produces bio-oil, with aqueous phase products, gas phase products, and solid residues as byproducts (Xu and Li, 2021). The process uses slightly more elevated temperatures (i.e., 250°C–375°C (Sharma et al., 2022)). HTL is also run at autogenous pressures, usually ranging from 5 to 20 MPa; these pressures are higher due to the increased operating temperatures associated with the process (Gollakota et al., 2018). In the HTL process, biomass macromolecules undergo initial hydrolysis and/or degradation, resulting in the formation of smaller molecules. A significant portion of these newly formed molecules are characterized by instability and reactivity, leading to their combination into larger molecules. Throughout this transformation, a considerable amount of oxygen in the biomass is eliminated through dehydration or decarboxylation (Toor et al., 2011). As with all of the bioconversion methods mentioned, the chemical attributes of the manufactured bio-oil exhibit a strong reliance on the composition of the feedstock used (Tian et al., 2020). A conceptual biorefinery design for HTL was put forth by Snowden-Swan et al. as they researched ways to maximize the use of wet feedstocks (Snowden-Swan et al., 2017).
3.5 Hydrothermal gasification
HTG, also referred to as supercritical water gasification, is akin to both HTC and HTL because it takes place in a wet environment; however, HTG is a bioconversion method that seeks to produce fuel gas/syngas instead of solid or liquid fuel. The process involves the hydrolysis of biomass in supercritical water followed by further gasification of the produced aqueous oligomers (He et al., 2014). The reaction time is short, making it one of the most efficient technologies for wet biomass gasification. The operating temperatures and pressures associated with this process are 350°C–700°C and 21–30 MPa (GRTgaz, 2023; Sakthivel et al., 2024). Similar to other processes, the composition of the syngas is heavily dependent on the feedstock. Moreover, according to the Le Chatelier principle, hydrogen formation is preferred at high temperatures, whereas methane formation is more suited to higher pressures (Kruse, 2008). This flexibility in product output could be a significant factor for manufacturers.
3.6 Fermentation for ethanol production
Ethanol production is a key bioconversion process with substantial implications for renewable energy and biofuels. Ethanol is typically produced through the fermentation of sugars derived from biomass, such as sugarcane, corn, or lignocellulosic materials (Cardona and Sánchez, 2007). The efficiency of this process is influenced by factors such as feedstock composition, fermentation conditions, and the choice of microorganisms, such as yeast (Abreu-Cavalheiro and Monteiro, 2013). Compared to the previously mentioned techniques, the fermentation process for maximum ethanol production requires moderate temperatures, typically between 30°C and 35°C; however, during the pretreatment steps before fermentation, the highest operational temperatures can be found, reaching as high as 240°C. These temperatures are needed when hydrolyzing holocellulose using dilute acids (Zabed et al., 2017). Based on research done by the National Renewable Energy Lab (NREL), a process design for the conversion of lignocellulosic biomass into ethanol was described by Humbird et al. (2011).
3.7 Anaerobic digestion
AD is a biological process where anaerobic consortia, including methanogenic archaea, convert organic waste into carbon dioxide and methane (i.e., biogas) (Chen et al., 2008). Anaerobic treatment offers a means to diminish pollution from agricultural and industrial activities while simultaneously mitigating fossil fuels. The efficiency of AD is influenced by the composition of the organic waste, process temperature, retention time, and the microbial community involved (Liao et al., 2006). The microbial community driving AD prefers mesophilic conditions, exhibiting accelerated growth ranging from 25°C to 40°C, but when temperatures exceed 47°C, these methanogens die (Tang et al., 2022). In the absence of these methanogens, alternate microbial communities assume control of methane production in the thermophilic state (40°C–55°C), where the rate of methane production is lower. The overall gas pressure in a typical AD system is kept slightly higher than atmospheric pressure, with an overpressure of up to 0.02 bar (Chynoweth, 1987).
3.8 Pasteurization
Pasteurization is a key agricultural process, particularly in the dairy industry. Conventional pasteurization processes rely on continuous heat transfer to eliminate harmful pathogenic organisms in liquids like milk and slightly extend product shelf life (Swart et al., 2003). The most common means of heating comes from the use of plate heat exchangers (HTXs) due to their low cost, flexibility, high thermal efficiency, and ease of maintenance. There are two common techniques: batch pasteurization and continuous flow pasteurization. In batch pasteurization, milk in a large vat or tank is heated to at least 63°C for a minimum of 30 min. Continuous flow pasteurization methods include high-temperature, short-time pasteurization, which heats milk to a minimum of 72°C for 15 s, and ultrahigh temperature pasteurization, employing temperatures ranging from 135°C to 150°C for 4–15 s (Virginia Department of Health, 2016).
4 Methods
4.1 Brayton cycle model
To understand how these bioconversion and agricultural processes could be integrated with nuclear microreactor heat, a Brayton cycle model was developed. The model presented is based on published information about the Westinghouse eVinciTM microreactor (Westinghouse, 2024). The eVinciTM microreactor can produce 5 MWe with a 13-MWth design. The eVinciTM microreactor uses heat pipe cooling technology, with the power conversion system being an open-air Brayton cycle with an approximate efficiency of 36% (Lee et al., 2023). To realize this 36% cycle efficiency, a regenerator is incorporated into the Brayton cycle model (Figure 1). An additional, second HTX has been added to the cycle to accommodate the bioconversion/agricultural processes; the dotted boxes in Figure 1 indicate the potential positions for the HTX. The primary equations needed to build this model in Engineering Equation Solver (EES) are included in the Supplementary Material (Supplementary Equations S1–S14).
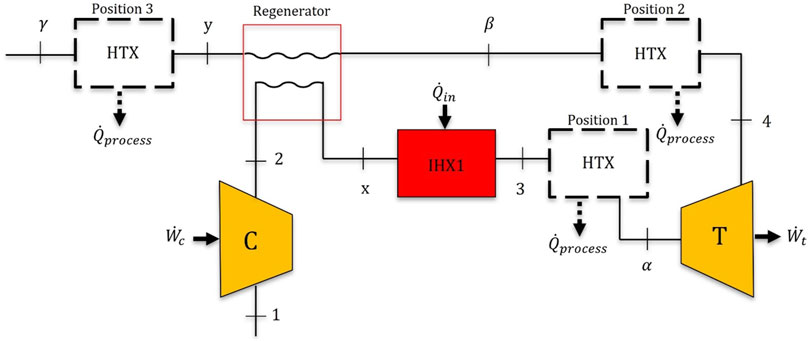
Figure 1. Representative regenerative Brayton cycle diagram including an additional HTX shown in three possible positions for supplying heat to the concurrent processes, depicted by the dotted boxes.
The placement of the HTX is flexible, depending on the requirements of a given process. For processes requiring high temperatures, placing the HTX immediately before the turbine at position 1 might be optimal because this is where the highest temperatures are available, yet that decreases the net power the cycle can produce. For processes that require lower temperatures, the HTX can be positioned between the turbine and the regenerator or after the regenerator. Assumptions for the Brayton cycle model include using an air standard analysis, state 1 having ambient conditions of 1 atm and a temperature of 20°C, no pressure drop through the HTXs, a turbine isentropic efficiency of 92% (Drbal et al., 2012), a compressor isentropic efficiency of 85% (Drbal et al., 2012), and a regenerator effectiveness of 90% (Xiao et al., 2017). Corresponding to the eVinciTM Brayton cycle,
4.2 Exergetic efficiency
To assess the feasibility of coupling the bioconversion and agricultural methods with nuclear microreactors, exergetic (second law) efficiencies are computed using Equation 1, and power and heat trade-offs are calculated for different processes. Exergetic efficiency is useful when matching an end use to a source, and it is given by:
where
5 Results and discussion
5.1 Exergetic efficiency results
Table 2 shows the exergetic efficiencies at position 1 (i.e., before the turbine) for different microreactor designs, coupled with the different bioconversion and agricultural process; N/A indicates an exergetic efficiency greater than 100%, which is impossible. These results indicate that some high-temperature processes, such as gasification and pyrolysis, are well-matched to the source temperatures. Although the exergetic efficiencies are high, there are significant trade-offs when considering the power generated in the cycle. Larger amounts of heat are required for the bioconversion processes, thereby diminishing the power produced by the turbine. For microreactor designs with lower reported process heat temperatures, processes such as HTC, HTL, and ethanol production are well-suited. Low-temperature processes, such as pasteurization and AD, have the lowest exergetic efficiency percentages and are better suited for using lower-grade waste heat (e.g., position 2 or 3 in Figure 1). It is also noteworthy that these exergetic efficiency values have been calculated for the case in which only a singular process is being integrated into the microreactor; it might be possible to run more than one process. Another consideration is that these exergetic efficiency results have been calculated at the peak process temperatures provided by each microreactor. The next section of results investigates the differences in process heat at different locations in the Brayton cycle model.
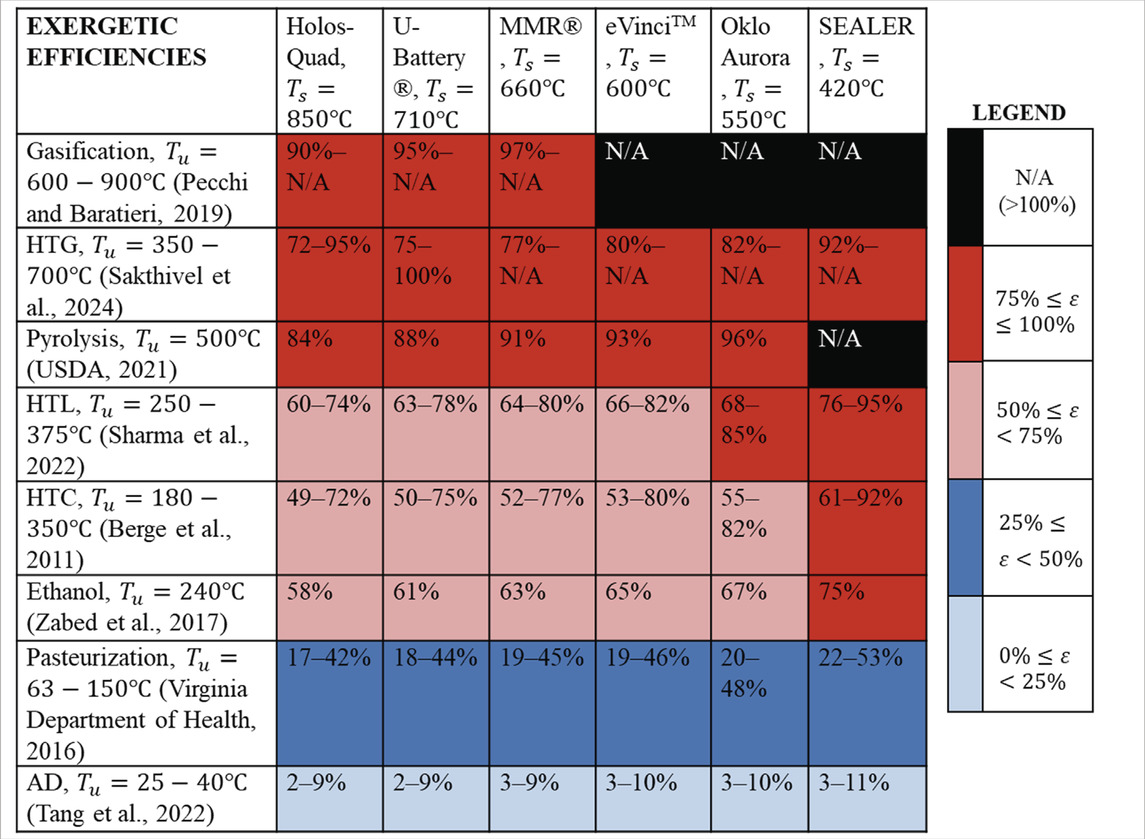
Table 2. Exergetic efficiency values for different microreactor designs at position 1 (i.e., before the turbine) when coupled with bioconversion and agricultural processes;
5.2 Trade-offs between process heat utilization and power production
Results indicate that there are heat and power trade-offs when meeting the temperature requirements of the bioconversion and agricultural processes. The model in EES calculated the net cycle work and maximum rate of heat transfer from the HTX when placed at three different potential locations (Figure 2). The numerical results from these calculations are available in the Supplementary Material. The process temperatures used are the average temperature values for each process (Section 3; Table 2); they are also presented in the Supplementary Material. As Figure 2 demonstrates, different processes are omitted for different HTX positions due to their incompatibility (e.g., negative amounts of

Figure 2. Power and maximum process heat trade-off plots when HTX is placed at three different locations: (A) position 1, between the turbine and IHX1; (B) position 2, between the turbine and regenerator; and (C) position 3, after the regenerator. Acronyms: HTC (hydrothermal carbonization), HTL (hydrothermal liquefaction), HTG (hydrothermal gasification), AD (anaerobic digestion), Past. (pasteurization).
In Figure 2A, where the HTX is placed ahead of the turbine and has access to the highest temperatures in the cycle (i.e., position 1 at 873K), all the processes are viable besides gasification and pyrolysis because, according to the model, these will bring the inlet turbine temperature too low to result in a positive
For position 2, (i.e., between the turbine and regenerator; Figure 2B), the available process temperatures in the Brayton cycle are lower than position 1, near 643 K. In this position, pyrolysis and HTG are eliminated because their process temperature requirements are greater than 643 K. Ethanol production, HTC, and HTL are still viable and strike a balance between running a concurrent process while also having sizable net power.
Finally, in position 3 (i.e., after the regenerator), depicted in Figure 2C, the lowest process temperatures are available at 465 K. At this process temperature, only AD and pasteurization are viable; however, because position 3 is when HTX is after the regenerator,
A practical way to interpret these results is to convert the process heat from the microreactor into quantitative end products. By utilizing specific energy requirements from the current literature for each process (Garkoti et al., 2024; Food and Agriculture Organization of the United Nations, 2004; Morris and Ahmed, 1992; Lucian and Fiori, 2017; Zhang et al., 2017; Nakagawa et al., 2007), a maximum amount of deliverable product can be determined. For example, using
The findings of this brief research report have some limitations. Since the model’s results were based on the current specifications of the eVinciTM microreactor design, future insights into the actual eVinciTM system design could potentially affect these results. Additionally, based on the process heat temperature from the eVinciTM design, certain concurrent processes were deemed unviable. However, with an alternative microreactor design that offers higher available process temperatures, some of these processes may become feasible (Stauff et al., 2023). In a report to assess the role of nuclear power plant technologies for supporting negative emissions technology, Stauff et al. (2023) identified drying of biomass, regeneration for carbon capture systems, and separation of syngas into its components as some potential users of nuclear waste heat. Additionally, some of the nuclear power plants assessed, such as Very High Temperature Reactors (e.g., 22 MWt, 10 MWe HolosGen), could provide the necessary heat for high-temperature processes, such as gasification. They also identified tradeoffs between heat and power. Also, for the bioconversion and agricultural processes, the average process temperature from the literature review was used. If these calculations were performed using the minimum and maximum temperatures within this range, the results of this work would be affected.
6 Conclusion
Addressing the pressing issue of global warming requires a multifaceted approach where the use of nuclear microreactors might play a significant role. In this study, we investigated the feasibility of using nuclear microreactors for concurrent bioconversion and agricultural processes.
Exergetic efficiency results of 72%–100% showed high compatibility between high-temperature processes (i.e., gasification, HTG, and pyrolysis) at position 1 before the turbine. In contrast, lower temperature processes (i.e., AD and pasteurization) with exergetic efficiencies of 2%–53% could result in some of the microreactor heat being used less efficiently from an exergetic viewpoint. A Brayton cycle model with a regenerator was developed to assess the feasibility of powering these processes using nuclear microreactor heat. From this model, power and heat trade-off analyses were studied to provide insights into the feasibility of using excess heat for different processes. Results indicated that high-temperature techniques, such as gasification, requiring a minimum of 600
Future work on this topic could include the integration of multiple processes, where trade-offs could be considered between running two or more concurrent systems. Additionally, further work could include incorporating different microreactor designs. The future adoption of nuclear microreactors supports worldwide decarbonization efforts, providing a potential pathway to achieving these global climate goals. This work acts as a guide to show potential uses for microreactor heat, maximizing their potential.
Data availability statement
The original contributions presented in the study are included in the article/Supplementary Material, further inquiries can be directed to the corresponding author.
Author contributions
JP: Conceptualization, Formal Analysis, Methodology, Writing–original draft. CS: Conceptualization, Investigation, Writing–review and editing. MD: Conceptualization, Funding acquisition, Supervision, Writing–review and editing.
Funding
The author(s) declare that financial support was received for the research, authorship, and/or publication of this article. This work was supported by the Department of Energy Nuclear Energy University Programs under grant no. DE-NE0009152 and the National Science Foundation under grant no. 1828571.
Acknowledgments
This work was authored in part by the National Renewable Energy Laboratory, operated by Alliance for Sustainable Energy, LLC, for the U.S. Department of Energy (DOE) under Contract No. DE-AC36-08GO28308.
Conflict of interest
The authors declare that the research was conducted in the absence of any commercial or financial relationships that could be construed as a potential conflict of interest.
Publisher’s note
All claims expressed in this article are solely those of the authors and do not necessarily represent those of their affiliated organizations, or those of the publisher, the editors and the reviewers. Any product that may be evaluated in this article, or claim that may be made by its manufacturer, is not guaranteed or endorsed by the publisher.
Author disclaimer
The views expressed in the article do not necessarily represent the views of the DOE or the U.S. Government. The U.S. Government retains and the publisher, by accepting the article for publication, acknowledges that the U.S. Government retains a nonexclusive, paid-up, irrevocable, worldwide license to publish or reproduce the published form of this work, or allow others to do so, for U.S. Government purposes.
Supplementary material
The Supplementary Material for this article can be found online at: https://www.frontiersin.org/articles/10.3389/fenrg.2024.1476974/full#supplementary-material
References
Abreu-Cavalheiro, A., and Monteiro, G. (2013). Solving ethanol production problems with genetically modified yeast strains. Braz. J. Microbiol. 44, 665–671. doi:10.1590/s1517-83822013000300001
Antonello, F., Buongiorno, J., and Zio, E. (2023). Insights in the safety analysis of an early microreactor design. Nucl. Eng. Des. 404, 112203. doi:10.1016/J.NUCENGDES.2023.112203
Berge, N. D., Ro, K. S., Mao, J., Flora, J. R. V., Chappell, M. A., and Bae, S. (2011). Hydrothermal carbonization of municipal waste streams. Environ. Sci. and Technol. 45 (13), 5696–5703. doi:10.1021/es2004528
Black, G., Shropshire, D., Araújo, K., and van Heek, A. (2023). Prospects for nuclear microreactors: a review of the technology, economics, and regulatory considerations. Nucl. Technol. 209 (Suppl. 1), S1–S20. doi:10.1080/00295450.2022.2118626
Boissevain, B. L., Zemke, P. E., and Wood, B. D. (2013). Improving energy utilization in anaerobic digester power systems. Biol. Eng. Trans. 6 (1), 43–56. doi:10.13031/2013.42632
Cardona, C. A., and Sánchez, Ó. J. (2007). Fuel ethanol production: process design trends and integration opportunities. Bioresour. Technol. 98 (12), 2415–2457. doi:10.1016/j.biortech.2007.01.002
Chen, L., Msigwa, G., Yang, M., Osman, A. I., Fawzy, S., Rooney, D. W., et al. (2022). Strategies to achieve a carbon neutral society: a review. Environ. Chem. Lett. 20 (4), 2277–2310. doi:10.1007/s10311-022-01435-8
Chen, Y., Cheng, J. J., and Creamer, K. S. (2008). Inhibition of anaerobic digestion process: a review. Bioresour. Technol. 99 (10), 4044–4064. doi:10.1016/j.biortech.2007.01.057
Chenic, A. Ș., Cretu, A. I., Burlacu, A., Moroianu, N., Vîrjan, D., Huru, D., et al. (2022). Logical analysis on the strategy for a sustainable transition of the world to green energy—2050. Smart cities and villages coupled to renewable energy sources with low carbon footprint. Sustainability 14 (14), 8622. doi:10.3390/su14148622
De Filippis, P., Scarsella, M., de Caprariis, B., and Uccellari, R. (2015). Biomass gasification plant and syngas clean-up system. Energy Procedia 75, 240–245. doi:10.1016/j.egypro.2015.07.318
Drbal, L., Westra, K., and Boston, P. (2012). Power plant engineering. Springer Science and Business Media.
EIA (2024). eVinci Microreactor. Available at: https://www.Eia.Gov/Energyexplained/Electricity/Electricity-in-the-Us.Php (Accessed June 30, 2023).
Food and Agriculture Organization of the United Nations (2004). Energy requirements in milk processing.
Funke, A., and Ziegler, F. (2010). Hydrothermal carbonization of biomass: a summary and discussion of chemical mechanisms for process engineering. Biofuels, Bioprod. Biorefining 4 (2), 160–177. doi:10.1002/bbb.198
Garkoti, P., Ni, J.-Q., and Thengane, S. K. (2024). Energy management for maintaining anaerobic digestion temperature in biogas plants. Renew. Sustain. Energy Rev. 199, 114430. doi:10.1016/j.rser.2024.114430
Gollakota, A. R. K., Kishore, N., and Gu, S. (2018). A review on hydrothermal liquefaction of biomass. Renew. Sustain. Energy Rev. 81, 1378–1392. doi:10.1016/j.rser.2017.05.178
Graham, N. T., Gakkhar, N., Singh, A. D., Evans, M., Stelmach, T., Durga, S., et al. (2022). Integrated analysis of increased bioenergy futures in India. Energy Policy 168, 113125. doi:10.1016/j.enpol.2022.113125
GRTgaz (2023). Carbon%20dioxide. Available at: https://www.Grtgaz.Com/En/Ourenergies/Wet-Waste/Hydrothermal-Gasification-5-Points#:∼:Text=How%20does%20Hydrothermal%20Gasification%20work,CO2%20.
Guillen, D. P. (2023). Review of passive heat removal strategies for nuclear microreactor systems. Nucl. Technol. 209 (Suppl. 1), S21–S40. doi:10.1080/00295450.2022.2055701
Hanssen, S. V., Daioglou, V., Steinmann, Z. J. N., Doelman, J. C., Van Vuuren, D. P., and Huijbregts, M. A. J. (2020). The climate change mitigation potential of bioenergy with carbon capture and storage. Nat. Clim. Change 10 (11), 1023–1029. doi:10.1038/s41558-020-0885-y
He, C., Chen, C.-L., Giannis, A., Yang, Y., and Wang, J.-Y. (2014). Hydrothermal gasification of sewage sludge and model compounds for renewable hydrogen production: a review. Renew. Sustain. Energy Rev. 39, 1127–1142. doi:10.1016/j.rser.2014.07.141
HolosGen (2017). Holos quad - holos. Available at: https://www.Holosgen.Com/Holos-Quad/.
Huning, A. J., Shropshire, D. E., and Kurt, E. (2023). Risk-informed opportunities and challenges for microreactors. React. Syst. Des. Analysis, 689–698. doi:10.13182/psa23-40924
Humbird, D., Davis, R., Tao, L., Kinchin, C., Hsu, D., Andy, A., et al. (2011). Process design and economics for biochemical conversion of lignocellulosic biomass to ethanol: dilute-acid pretreatment and enzymatic hydrolysis of corn stover. No. NREL/TP-5100-47764. Golden, CO, United States: National Renewable Energy Lab (NREL).
IEA (2023). Status of molten salt reactor technology. Tech. Rep. Ser. No. 489, 315. Available at: https://www-pub.iaea.org/MTCD/Publications/PDF/STI-DOC-010-489_web.pdf.
Kalinichenko, D., Wodrich, L., Lee, A. J. H., Kozlowski, T., and Brooks, C. S. (2024). Analysis of nuclear microreactor efficacy with hydrogen production methods. Prog. Nucl. Energy 168, 104994. doi:10.1016/j.pnucene.2023.104994
Khodarev, E. (1978). Liquid metal fast breeder reactors. IAEA Bull. 20 (6), 29–38. Available at: https://www.iaea.org/publications/magazines/bulletin/20-6/liquid-metal-fast-breeder-reactors
Kruse, A. (2008). Supercritical water gasification. Biofuels, Bioprod. Biorefining Innovation a Sustain. Econ. 2 (5), 415–437. doi:10.1002/bbb.93
Lee, S. W., Lee, Y., Kim, N., and Jo, H. (2023). Design of heat pipe cooled microreactor based on cycle analysis and evaluation of applicability for remote regions. Energy Convers. Manag. 288, 117126. doi:10.1016/j.enconman.2023.117126
Liao, B.-Q., Kraemer, J. T., and Bagley, D. M. (2006). Anaerobic membrane bioreactors: applications and research directions. Crit. Rev. Environ. Sci. Technol. 36 (6), 489–530. doi:10.1080/10643380600678146
Lucian, M., and Fiori, L. (2017). Hydrothermal carbonization of waste biomass: process design, modeling, energy efficiency and cost analysis. Energies 10 (2), 211. doi:10.3390/en10020211
Meegoda, J. N., Li, B., Patel, K., and Wang, L. B. (2018). A review of the processes, parameters, and optimization of anaerobic digestion. Int. J. Environ. Res. Public Health 15 (10), 2224. doi:10.3390/ijerph15102224
Moe, W. L. (2019). INL/EXT-19-55257-Rev. 000: key regulatory issues in nuclear microreactor transport and siting. Available at: http://www.inl.gov.
Moran, M. J., Shapiro, H. N., Boettner, D. D., and Bailey, M. B. (2010). Fundamentals of engineering thermodynamics. John Wiley and Sons.
Nakagawa, H., Namba, A., Sharma, A., and Miura, K. (2007). Production of fuel gas through the hydrothermal gasification of wastewater using highly active carbon-base catalyst. J. Chem. Eng. Jpn. 40 (13), 1210–1215. doi:10.1252/jcej.07we155
NETL (2022). NEA No. 7629: high-temperature gas-cooled reactors and industrial heat applications. Available at: https://www.Netl.Doe.Gov/Research/Coal/Energy-Systems/Gasification/Gasifipedia/Syngas-Composition.
Onuki, S., Koziel, J. A., van Leeuwen, J. H., Jenks, W. S., Grewell, D., and Cai, L. (2008). Ethanol production, purification, and analysis techniques: a review. Providence, 1. doi:10.13031/2013.25186
Paris Agreement (2015). in Report of the Conference of the Parties to the United Nations Framework Convention on Climate Change (21st Session, 2015: Paris), Paris, December 4, 2017, 2.
Pattiya, A., Sukkasi, S., and Goodwin, V. (2012). Fast pyrolysis of sugarcane and cassava residues in a free-fall reactor. Energy 44 (1), 1067–1077. doi:10.1016/j.energy.2012.04.035
Peakman, A., Hodgson, Z., and Merk, B. (2018). Advanced micro-reactor concepts. Prog. Nucl. Energy 107, 61–70. doi:10.1016/j.pnucene.2018.02.025
Pecchi, M., and Baratieri, M. (2019). Coupling anaerobic digestion with gasification, pyrolysis or hydrothermal carbonization: a review. Renew. Sustain. Energy Rev. 105, 462–475. doi:10.1016/j.rser.2019.02.003
Pereira, E. G., Da Silva, J. N., De Oliveira, J. L., and Machado, C. S. (2012). Sustainable energy: a review of gasification technologies. Renew. Sustain. Energy Rev. 16 (7), 4753–4762. doi:10.1016/j.rser.2012.04.023
Rand, D. A. J., and Dell, R. M. (2009). FUELS – HYDROGEN PRODUCTION | coal gasification. In J. Garche Eds Encyclopedia of electrochemical power sources, 276–292. Elsevier.
Reza, M. T., Andert, J., Wirth, B., Busch, D., Pielert, J., Lynam, J. G., et al. (2014). Hydrothermal carbonization of biomass for energy and crop production. Appl. Bioenergy 1 (1), 11–29. doi:10.2478/apbi-2014-0001
Sakthivel, R., Abbhijith, H., Harshini, G. V., Vardhan, M. S., and Shadangi, K. P. (2024). Biofuels: classification, conversion technologies, optimization techniques and applications. Biorefineries Prod. Fuels Platf. Chem., 1–30. doi:10.1002/9781119724872.ch1
Sharma, I., Rackemann, D., Ramirez, J., Cronin, D. J., Moghaddam, L., Beltramini, J. N., et al. (2022). Exploring the potential for biomethane production by the hybrid anaerobic digestion and hydrothermal gasification process: a review. J. Clean. Prod. 362, 132507. doi:10.1016/j.jclepro.2022.132507
Speidel, M., Kraaij, G., and Wörner, A. (2015). A new process concept for highly efficient conversion of sewage sludge by combined fermentation and gasification and power generation in a hybrid system consisting of a SOFC and a gas turbine. Energy Convers. Manag. 98, 259–267. doi:10.1016/j.enconman.2015.03.101
Stauff, N., Lee, C. H., and Filippone, C. (2022). Core design of the holos-quad microreactor. Argonne, IL (United States): Argonne National Lab. ANL.
Stauff, N. E., Mann, W. N., Moisseytsev, A., Durvasulu, V., Mantripragada, H., and Fout, T. (2023). Assessment of nuclear energy to support negative emission technologies. Argonne, IL (United States): Argonne National Laboratory ANL.
Sugawara, S. (2024). Towards “extended” safety goals (Conceptual exploration of safety goals for microreactors). Mech. Eng. J. 11 (2), 23–00375. doi:10.1299/mej.23-00375
Snowden-Swan, L. J., Yunhua, Z., Mark, D. B., Timothy, E. S., Susanne, B. J., Andrew, J. S., et al. (2017). Conceptual biorefinery design and research targeted for 2022: hydrothermal liquefacation processing of wet waste to fuels. No. PNNL-27186. Richland, WA, United States: Northwest National Lab (PNNL).
Swart, G. J., Blignaut, C. M., and Jooste, P. J. (2003). PASTEURIZATION | other pasteurization processes. In B. Caballero Eds Encyclopedia of food sciences and nutrition Second Edition, 4401–4406. Academic Press.
Tang, J., Pu, Y., Zeng, T., Hu, Y., Huang, J., Pan, S., et al. (2022). Enhanced methane production coupled with livestock wastewater treatment using anaerobic membrane bioreactor: performance and membrane filtration properties. Bioresour. Technol. 345, 126470. doi:10.1016/j.biortech.2021.126470
Terrani, K. (2022). “Building the Gen IV fuel supply chain,” in Nuclear engineering international magazine.
Testoni, R., Bersano, A., and Segantin, S. (2021). Review of nuclear microreactors: status, potentialities and challenges. Prog. Nucl. Energy 138, 103822. doi:10.1016/j.pnucene.2021.103822
Tian, Y., Wang, F., Djandja, J. O., Zhang, S.-L., Xu, Y.-P., and Duan, P.-G. (2020). Hydrothermal liquefaction of crop straws: effect of feedstock composition. Fuel 265, 116946. doi:10.1016/j.fuel.2019.116946
Toor, S. S., Rosendahl, L., and Rudolf, A. (2011). Hydrothermal liquefaction of biomass: a review of subcritical water technologies. Energy 36 (5), 2328–2342. doi:10.1016/j.energy.2011.03.013
U-Battery (2019). u-battery.com. Available at: https://www.u-Battery.Com/Cdn/Uploads/Supporting-Files/U-Battery_brochure_Feb21.Pdf.
United Nations Climate Change (1997). unfccc.int. Available at: https://Unfccc.Int/Kyoto_protocol
USDA (2021). Eastern regional research center. Available at: https://www.Ars.Usda.Gov/Northeast-Area/Wyndmoor-Pa/Eastern-Regional-Research-Center/Docs/Biomass-Pyrolysis-Research-1/What-Is-Pyrolysis/ (Accessed September 10, 2021).
United States Department of Agriculture (USDA) (2017). Bio-oil. Agriculture research service. Available at: https://www.ars.usda.gov/northeast-area/wyndmoor-pa/eastern-regional-research-center/docs/biomass-pyrolysis-research-1/bio-oil/.
Ultra Safe Nuclear Corporation (2019). Project description for the micro modular reactorTM project at Chalk River. Available at: https://www.Usnc.Com/Assets/Media-Kit/01%20CRP-LIC-01-001%20Rev%202%20Project%20Description.Pdf?V=41e03bfaa5 (Accessed March 11, 2020).
U.S. Nuclear Regulatory Commission (USNRC) (2020). Aurora-Oklo Application. Available at: https://www.nrc.gov/reactors/new-reactors/large-lwr/col/aurora-oklo.html.
Vaya Soler, A., Berthelemy, M., Verma, A., Bilbao y Leon, S., Kwong, G., Sozoniuk, V., et al. (2021). Small modular reactors: challenges and opportunities.
Virginia Department of Health (2016). vdh.Virginia.gov. Available at: https://www.Vdh.Virginia.Gov/Environmental-Health/Food-Safety-in-Virginia/Milk-Safety/Pasteurization/#:∼:Text=Batch%20pasteurization%20involves%20heating%20every,%C2%B0F%20for%2015%20s.
Westinghouse (2024). eVinci Microreactor. Available at: https://www.westinghousenuclear.com/energy-systems/evinci-microreactor.
World Nuclear Association (2024). Small nuclear power reactors. Available at: https://www.World-Nuclear.Org/Information-Library/Nuclear-Fuel-Cycle/Nuclear-Power-Reactors/Small-Nuclear-Power-Reactors.Aspx (Accessed February, 2024).
X-Energy: Xe-Mobile. (2024). Available at: Https://X-Energy.Com/Reactors/Xe-Mobile.
Xiao, G., Yang, T., Liu, H., Ni, D., Ferrari, M. L., Li, M., et al. (2017). Recuperators for micro gas turbines: a review. Appl. Energy 197, 83–99. doi:10.1016/j.apenergy.2017.03.095
Xu, Y.-H., and Li, M.-F. (2021). Hydrothermal liquefaction of lignocellulose for value-added products: mechanism, parameter and production application. Bioresour. Technol. 342, 126035. doi:10.1016/j.biortech.2021.126035
Yan, B. H., Wang, C., and Li, L. G. (2020). The technology of micro heat pipe cooled reactor: a review. Ann. Nucl. Energy 135, 106948. doi:10.1016/j.anucene.2019.106948
Yung, M. M., Stanton, A. R., Iisa, K., French, R. J., Orton, K. A., and Magrini, K. A. (2016). Multiscale evaluation of catalytic upgrading of biomass pyrolysis vapors on Ni-and Ga-modified ZSM-5. Energy and Fuels 30 (11), 9471–9479. doi:10.1021/acs.energyfuels.6b01866
Zabed, H., Sahu, J. N., Suely, A., Boyce, A. N., and Faruq, G. (2017). Bioethanol production from renewable sources: current perspectives and technological progress. Renew. Sustain. Energy Rev. 71, 475–501. doi:10.1016/j.rser.2016.12.076
Zhang, B., Wu, J., Deng, Z., Yang, C., Cui, C., and Ding, Y. (2017). A comparison of energy consumption in hydrothermal liquefaction and pyrolysis of microalgae. Trends Renew. Energy 3 (1), 76–85. doi:10.17737/tre.2017.3.1.0013
Zhang, Y., Cui, Y., Chen, P., Liu, S., Zhou, N., Ding, K., et al. (2019). Chapter 14 - gasification technologies and their energy potentials. In M. J. Taherzadeh, K. Bolton, J. Wong, and A. Pandey Eds Sustainable resource recovery and zero waste approaches, 193–206. Elsevier.
Zhang, Z., Wang, C., Guo, K., Qiu, S., Su, G. H., and Tian, W. (2024). “Microreactors,” in Nuclear power reactor designs (Elsevier), 309–347.
Keywords: microreactor, carbon-neutral energy, sustainable energy, biofuels, eVinciTM, waste heat recovery
Citation: Pakkebier J, Skangos C and Derby MM (2024) Feasibility of using nuclear microreactor process heat for bioconversion and agricultural processes. Front. Energy Res. 12:1476974. doi: 10.3389/fenrg.2024.1476974
Received: 06 August 2024; Accepted: 30 October 2024;
Published: 04 December 2024.
Edited by:
Pedro Haro, Universidad de Sevilla, SpainReviewed by:
Luis M. Gandía, Public University of Navarre, SpainVeera Gnaneswar Gude, Purdue University, United States
Copyright © 2024 Pakkebier, Skangos and Derby. This is an open-access article distributed under the terms of the Creative Commons Attribution License (CC BY). The use, distribution or reproduction in other forums is permitted, provided the original author(s) and the copyright owner(s) are credited and that the original publication in this journal is cited, in accordance with accepted academic practice. No use, distribution or reproduction is permitted which does not comply with these terms.
*Correspondence: Melanie M. Derby, ZGVyYnltQGtzdS5lZHU=