- 1Beijing Institute of Smart Energy, Beijing, China
- 2Institute for Advanced Materials and Technology, University of Science and Technology Beijing, Beijing, China
Thermal storage ceramics using metals as phase change materials (PCMs) have both high thermal conductivity and high heat storage density. However, in the process of use is very easy to occur in the metal phase change material leakage, will seriously affect the service life of the thermal storage ceramics. In this study, ceramic composite phase change heat storage materials with Al-12Si alloy as phase change material were prepared. Firstly, Al-12Si was pretreated by sol-gel method and high temperature heat treatment to obtain the pretreated Al-12Si alloy powder with dense alumina shell layer. After that, the pretreated Al-12Si alloy powder was mixed and pressed with alumina, silicon dioxide, magnesium oxide, and mullite respectively, and sintered at 1,100°C, 1,200°C, or 1,300°C. The experimental results show that the metal phase change materials and the four ceramic materials show good chemical compatibility, and pretreated Al-12Si essentially retains its initial shape and is uniformly dispersed in the heat storage material. Among all the samples, the pre-treated Al-12Si/mullite ceramic thermal storage materials with a sintering temperature of 1,200°C showed the best thermal storage performance. The thermal conductivity of the samples was up to 17.94 W/(m·K). The latent heat storage value was 139.51 J/g before thermal cycling, 138.27 J/g after 100 thermal cycling, which was only decreased by 0.89%, and there was almost no alloy leakage. This study has successfully realized that the ceramic thermal storage material possesses high thermal conductivity, high thermal storage density and excellent thermal cycling performance at the same time, and provides a new method for the production and preparation of Al-12Si/ceramic heat storage materials, which has great potential for application in heat storage systems.
1 Introduction
Energy is the basis for human survival and development, and the energy crisis is a serious problem facing the world in the twenty-first century (Ramachandran et al., 2023). Thermal energy storage (TES) can effectively support the application scenarios of “zero-carbon heating” and “zero-carbon building,” provide scientific solutions for realizing the goals of carbon peaking and carbon neutrality (Zhang et al., 2024). It has a wide range of application prospects in the rapid economic development and energy shortage, and has received extensive attention from scholars at home and abroad.
Thermal storage material is the core and key of TES systems, which not only needs to have good thermal storage capacity and thermal conductivity, but also should have enough strength and cyclic stability to ensure its long service life (Ali et al., 2024). In recent years, sensible heat storage (SHS) materials such as concrete (Boquera et al., 2021), magnesium oxide (Yan et al., 2018), alumina (Khare et al., 2013), cordierite and mullite (Cheng et al., 2018), as well as latent heat storage (LHS), phase change materials (PCMs) such as nitrate (Takahashi et al., 1988), carbonate (Lu et al., 2019) and chloride (Zhao et al., 2014) have been widely used in TES systems. In order to improve the heat storage capacity of SHS materials and prepare stable LHS materials, composite heat storage materials consisting of SHS materials with high sensible heat storage capacity and PCMs with high latent heat storage capacity have been prepared. These composite heat storage materials can realize the perfect combination of high heat storage density, high thermal conductivity and high mechanical properties. Among these heat storage materials, ceramic materials with good mechanical properties and cyclic stability are usually used to provide the supporting skeleton and sensible heat storage. Li et al. (2019) successfully prepared an inorganic salt-based composite phase change material suitable for medium and high temperature heat storage with stable shape by using NaLiCO3, which has a melting temperature of about 500°C, as a PCM and MgO as a SHS material for the ceramic skeleton. Jiang et al. (2018) successfully prepared Na2SO4-NaCl/Al2O3 and Na2SO4-NaCl/mullite composites through the use of cold press sintering method. These new composites exhibit excellent thermal stability, not only avoiding the cracking phenomenon, but also performing well in weight loss, which is only 0.50% and 0.74%, respectively. Even more noteworthy is the reduction of latent heat by only 1% and 2%. However, the low thermal conductivity of molten salts and ceramic materials seriously hinders the heat transfer performance of thermal storage materials (Jiang et al., 2018; Jiang et al., 2020; Sun et al., 2020; Ma et al., 2021). The commonly used solution is to add graphite, silicon carbide, or other materials with high thermal conductivity to the thermal storage ceramics (Jiang et al., 2020). Li et al. (2016) investigated the thermal properties of thermal storage ceramics with NaNO3 as the PCM and found that a 20 wt% addition of silicon carbide could increase the thermal conductivity of this composite from 0.70 W/(m·K) at 300°C to 3.25 W/(m·K). Xiao et al. (2013) used sodium nitrate, potassium nitrate and their mixtures as the base materials, and, EG as an additive to improve the thermal conductivity. The apparent thermal conductivities of the nitrates/10 wt% EG mixture PCMs are increased by about 30%–40%, compared to those of pure nitrates. Ge et al. (2014) improved the thermal conductivity of thermal storage ceramics with Li2CO3-Li2CO3 as the PCM and MgO as the backbone material by adding graphite, and they increased the thermal conductivity of the thermal storage ceramics from about 3 W/(m·K) to about 5 W/(m·K). However, the oxidation of such materials at high temperatures makes the thermal cycle life of heat storage ceramics seriously degraded (Li et al., 2020), which has limited their wide application.
If metallic PCMs with high latent heat and high thermal conductivity are composited with ceramic materials, the goal of improving the thermal conductivity and thermal storage value of the thermal storage materials can be achieved at the same time. The high latent heat of Al-Si alloys 490–520 J/g (Farkas and Birchenall, 1985) makes them a popular research topic in the field of heat storage. In addition, due to the high thermal conductivity of Al-Si alloys (Nomura et al., 2018), adding them to thermal storage ceramics can effectively improve the thermal conductivity. Therefore, Al-Si alloys should be considered as important candidate PCMs for thermal storage ceramics to provide latent heat and high thermal conductivity. However, the corrosive and oxidizing nature of molten alloys (Kawaguchi et al., 2020) can shorten their service life, and molten metal leakage that occurs during use can seriously affect the thermal cycling stability of heat storage ceramics. In previously reported studies, these problems were solved by encapsulating Al-Si alloys with ceramic materials into capsules (He et al., 2015a; Katiyar and Saha, 2022), whose outer shell separates the molten alloys from the environment, preventing them from leaking and resisting corrosion. Therefore, first encapsulating Al-Si alloys and then using them as PCMs in thermal storage ceramics is a feasible way to achieve high thermal storage capacity and high thermal conductivity at the same time.
Based on the above discussion, if thermal storage ceramics with Al-Si alloys as PCMs without any leakage of molten alloy are successfully prepared, thermal storage materials with high thermal conductivity, high thermal storage and good thermal cycling performance will be obtained.
In this study, Al-12Si alloy powder was selected as the PCM, and alumina, silicon dioxide, magnesium oxide and mullite were used as the ceramic matrix materials. The novelty of this study lies in the fact that the Al-12Si alloy was firstly pretreated with cladding by two steps: sol-gel method and heat treatment. The metallic PCM is transformed into a core-shell structure of Al-12Si/Al2O3 to prevent the leakage of the liquid Al-12Si alloy during thermal storage use. Further, the pretreated Al-12Si alloy is mixed with the ceramic matrix material and cold-pressed sintered, so that the Al-12Si alloy phase change material can be stabilized and immobilized in the thermal storage material. The effects of different ceramic matrix materials and different sintering temperatures on the thermal performance, thermal conductivity and thermal cycle stability of Al-12Si/ceramic composite thermal storage materials were investigated. The results show that these thermal storage ceramics have excellent physical and thermal properties, especially high thermal conductivity and latent heat value with good thermal stability.
2 Materials and methods
2.1 Raw materials
Al-12Si eutectic alloy possesses high latent heat value (560 J/g), high thermal conductivity [160 W/(m·K)], small volume expansion (63.9 × 10−6) and small subcooling. Therefore, in this study, Al-12Si (particle size range: 40–60 μm) was used as the PCM, provided by Array Additive Technology Co. The melting point and latent heat of phase transition of the alloy were measured to be 582.0°C and 512.6 J/g, respectively, as shown in Figure 1.
In this study, magnesium oxide, silicon dioxide, alumina and mullite with particle size ≤75 μm were used as ceramic base materials. The chemical compositions of Magnesium oxide, Silicon dioxide, Alumina and Mullite are listed in Table 1.
2.2 Sample preparation
2.2.1 Pretreatment of Al-12Si alloy
The Al-12Si powder was kept in water at a constant temperature of 80°C for 1 h to roughen the surface and generate a small amount of boehmite (AlOOH) precursor. Then immersed in aluminum sol (the solid content was about 20%, in which the particle size of Al2O3 was 50–70 nm), and continued to be stirred for 3 h, after which it was cleaned with anhydrous ethanol and filtered. At this point, a core-shell structure Al-Si alloy powder with Al-Si alloy as the core and boehmite and alumina as the shell was obtained. Finally, the alloy powder placed in a muffle furnace for the high temperature treatment at 1,200°C for 2 h to complete the pretreatment of the Al-12Si. It can get the core-shell structure pretreated Al-Si alloy powder with Al-Si alloy as the core and dense alumina as the shell. According to Takahiro’s work, boehmite shell layer was first formed on the surface of the alloy powder during the pretreatment process, and then transformed into an alumina shell layer by polycondensation and oxidation reaction in the high temperature treatment (Kawaguchi et al., 2020). The microscopic morphology and elemental distribution of Al-12Si alloy powder before and after pretreatment are shown in Figure 2. The surface of pretreated Al-12Si alloy powder showed uniformly distributed Al2O3 films and chains, and this homogeneous alumina shell layer will effectively prevent leakage of the Al-12Si alloy during the phase change thermal storage process.
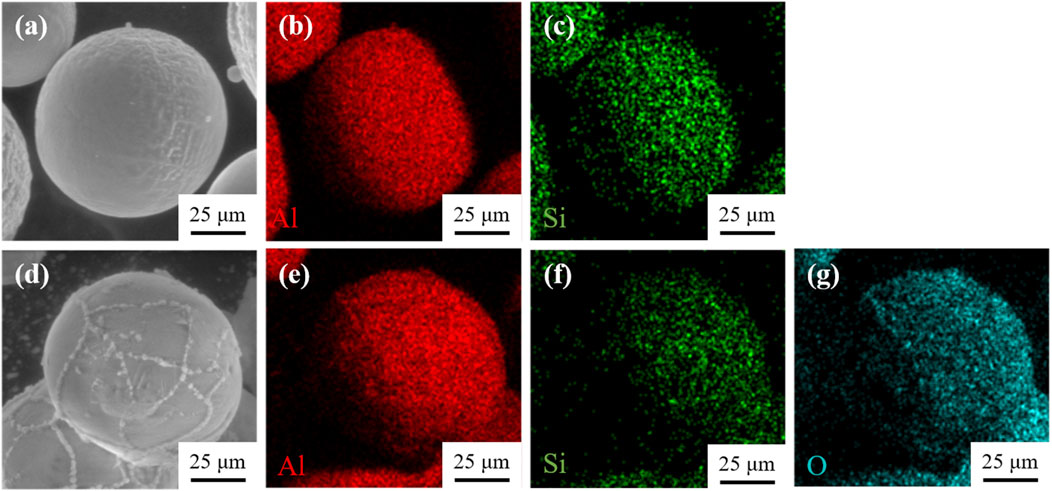
Figure 2. (A–C) Micro-morphology and elemental distribution of Al-12Si before pretreatment; (D–G) Micro-morphology and elemental distribution of pre-treated Al-12Si.
2.2.2 Preparation of ceramic heat storage materials
Magnesium oxide, Silicon dioxide, Alumina and Mullite powders were mixed homogeneously with Pre-treated Al-12Si alloy powders in a ratio of 1:1 by mass respectively as shown in Table 2, in addition to an additional 2 wt% of water was added to the mixtures to ensure press molding stability. The mixture was pressed into a cylindrical steel film of Φ20 mm under an isometric pressure of 120 MPa and held for 30 s. The produced billets were dried in an oven at 110°C for 1 h and then sintered under air atmosphere at 1,100°C, 1,200°C or 1,300°C for 2 h, with a temperature increase rate of 10°C/min, followed by furnace cooling.
2.3 Characteristics
2.3.1 Phase analysis and microstructure of the samples
The surface micromorphology of the samples was observed using scanning electron microscopy (SEM; GeminiSEM 300). Prior to the observation, the surfaces of the samples were coated by graphite to increase the conductivity. The phase composition of the samples was determined using X-ray diffraction (XRD; SmartLab), the scanning angle is 10°–90°. The samples used in these tests were disks with a diameter of 20 mm and a thickness of 6–7 mm while the surfaces of the samples were ground to flatten them.
2.3.2 Properties of the samples
In this section, density, compressive strength, thermal conductivity, enthalpy of phase transition and phase transition temperature are the arithmetic mean of the results of three tests.
The bulk density of the samples was measured at ambient temperature using water as the medium according to Archimedes’ principle. The compressive strength of the samples at room temperature was tested using a microcomputer controlled electronic universal testing machine [CMT5250 (UTC2014-056)]. The range of testing accuracy was ±0.5%. The samples used in the experiments were cylinders with a diameter of 20 mm and a thickness of 30–40 mm.
Thermal conductivity values were measured at room temperature by Thermal Constant Analysis Instrument (Hot Disk, TPS2200), the samples were cylinders with a diameter of 20 mm and a thickness range of 5–10 mm, and the accuracy of the test ranged from ±0.5%.
The enthalpy and temperature of phase change of the samples were measured using the TG-DSC simultaneous thermal analyzer (STA449F5, NETZSCH) in an air atmosphere. The temperature increase rate during the test was 10°C/min, the test temperature range was 50°C–800°C, the samples were 8–12 mg of sample powder, and the test accuracy range was ±0.3%.
3 Results and analyses
3.1 Compatibility analysis
Figure 3 shows the XRD patterns of different samples before and after mixed sintering. As shown in Figure 3A, no new crystalline phase is generated in pre-treated Al-12Si/alumina ceramic thermal storage materials compared to pre-treated Al-12Si and alumina. The pre-treated Al-12Si/silicon dioxide ceramic thermal storage materials also have no new crystalline phase generation compared to pre-treated Al-12Si and silicon dioxide as shown in Figure 3B. As shown in Figure 3C, compared with pre-treated Al-12Si and magnesium oxide, pre-treated Al-12Si/magnesium oxide ceramic thermal storage materials showed new crystalline phases MgAl2O4, which formed from the solid solution of MgO and Al2O3, other than that no other new crystalline phase is generated. As shown in Figure 3D, no new crystalline phase was also generated in pre-treated Al-12Si/mullite ceramic thermal storage materials compared to pre-treated Al-12Si with mullite.
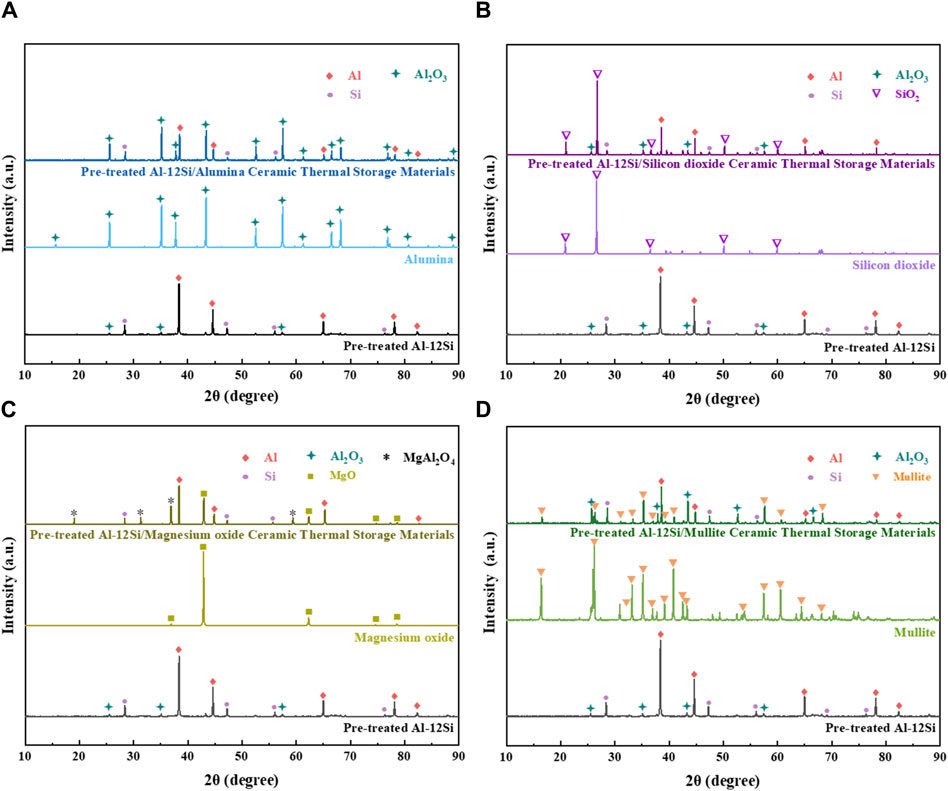
Figure 3. XRD patterns of (A) Pre-treated Al-12Si/alumina ceramic thermal storage material; (B) Pre-treated Al-12Si/silicon dioxide ceramic thermal storage material; (C) Pre-treated Al-12Si/magnesium oxide ceramic thermal storage material; (D) Pre-treated Al-12Si/mullite ceramic thermal storage material before and after mixed sintering.
It can be observed from the SEM images shown in Figure 4 that almost all of the Pretreated Al-12Si alloy particles in the thermal storage ceramic samples remain spherical and identical to the original morphology, which means that the Al-12Si alloy particles were successfully encapsulated by the alumina shells during the heat treatment of the samples. This encapsulation is important because the Al-12Si alloy particles can undergo a phase transition within the shell without severe oxidation, thus ensuring a longer service life of the Al-12Si alloy as well as a higher latent heat storage density and thermal conductivity of the thermal storage ceramics (Alehosseini and Jafari, 2020). It was also observed that the Pre-treated Al-12Si alloy particles were very well dispersed in the samples.
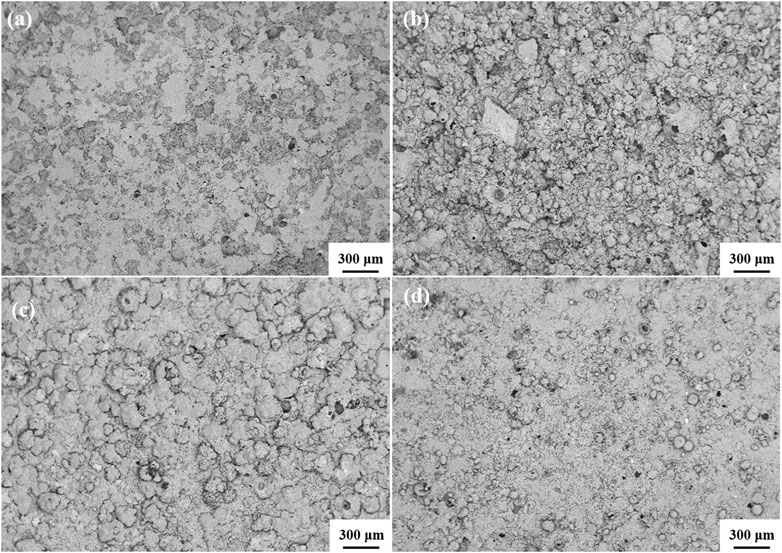
Figure 4. SEM micrographs of (A) Pre-treated Al-12Si/alumina ceramic thermal storage material; (B) Pre-treated Al-12Si/silicon dioxide ceramic thermal storage material; (C) Pre-treated Al-12Si/magnesium oxide ceramic thermal storage material; (D) Pre-treated Al-12Si/mullite ceramic thermal storage material.
From the above, it can be seen that Pre-treated Al-12Si and the four ceramic powders are simple physical combinations during the mixing and sintering process, and they all possess good chemical compatibility and can be fully mixed. Therefore, we further discussed the effect of different sintering temperatures on the microstructure and properties of four pre-treated Al-12Si/ceramic thermal storage material samples.
3.2 Effect of sintering temperatures on the microstructure and properties of ceramic thermal storage material samples
3.2.1 XRD and SEM analysis of samples prepared at different sintering temperatures
Figures 5, 6 show the XRD patterns and SEM micrographs of the ceramic heat storage samples sintered at different temperatures for 2 h, respectively. As shown in Figure 5, the crystalline phases of each sample remain consistent and almost unchanged at different sintering temperatures. However, the intensity of the peaks of Al2O3 in Figures 5A, B, D, and the peak of MgAl2O4 in Figure 5C increased slightly with the sintering temperature. This is mainly due to the greater oxidation of aluminium at higher sintering temperatures, leading to an increase in the content of Al2O3, which also increases the formation of solid solution MgAl2O4 in the pretreated Al-12Si/magnesium oxide ceramic heat storage material. The occurrence of this phenomenon is simultaneously supported by the decrease in the strength of the aluminium peak, which implies that the depletion of aluminium is caused by the oxidation of aluminium in the particles of the Pre-treated Al-12Si alloy. Silicon is a relatively stable material compared to aluminium, so the silicon peaks remain almost unchanged as the sintering temperature increases (Ciriminna et al., 2011). Figure 6 shows that the pre-treated Al-12Si/magnesium oxide ceramic thermal storage materials showed localized liquid phase coalescence at elevated sintering temperatures, suggesting that a small amount of leakage of Al-12Si occurred as the sintering temperature increased. However, this phenomenon did not appear in the rest of the ceramic thermal storage samples, indicating that the pre-treated of Al-12Si alloy particles was successful, and the sintering of the mixed ceramic substrate was also an effective way to prevent leakage. However, the formation of solid solution MgAl2O4 is continuously depleting the dense Al2O3 film on the surface layer of Pre-treated Al-12Si, which leads to a slight Al-12Si leakage in pre-treated Al-12Si/magnesium oxide ceramic thermal storage materials.
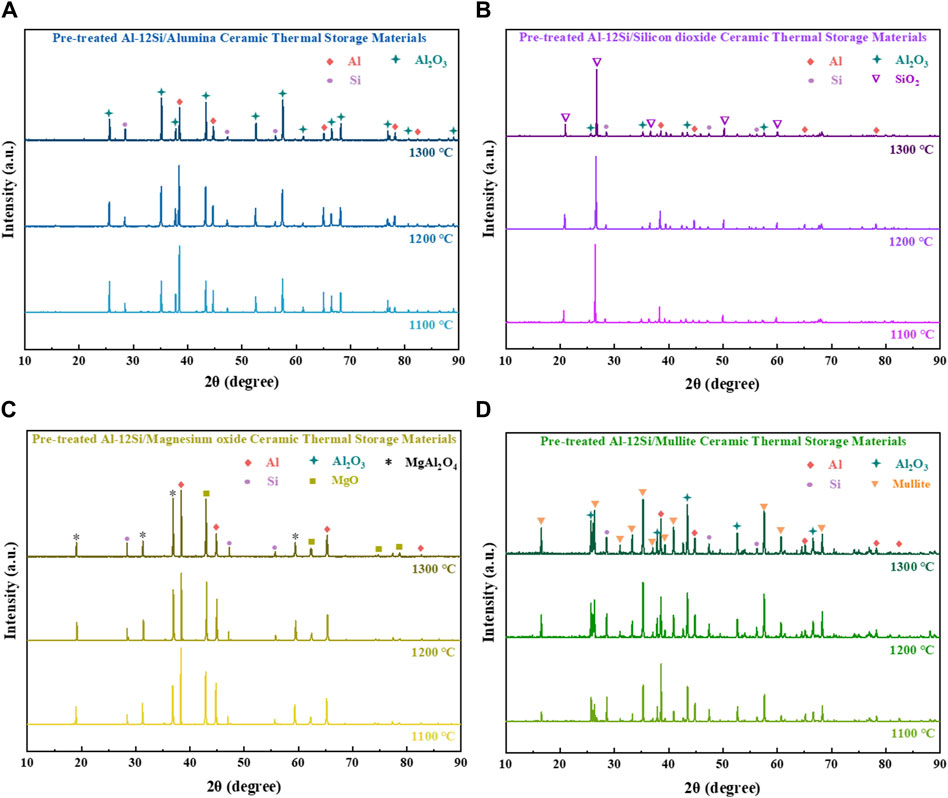
Figure 5. XRD patterns of (A) Pre-treated Al-12Si/alumina ceramic thermal storage material; (B) Pre-treated Al-12Si/silicon dioxide ceramic thermal storage material; (C) Pre-treated Al-12Si/magnesium oxide ceramic thermal storage material; (D) Pre-treated Al-12Si/mullite ceramic thermal storage material with different sintering temperatures.
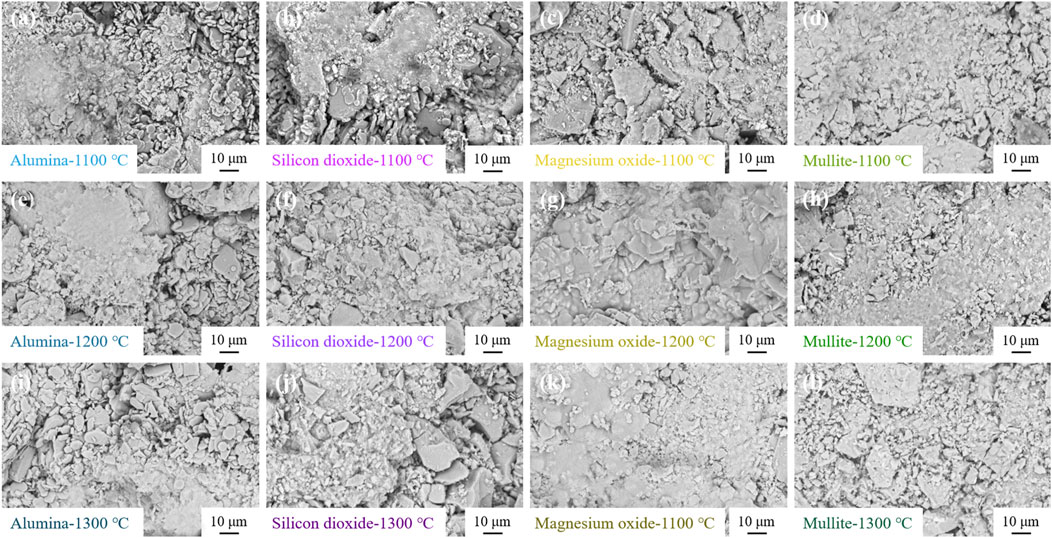
Figure 6. SEM micrographs of (A,E,I) Pre-treated Al-12Si/alumina ceramic thermal storage material; (B,F,J) Pre-treated Al-12Si/silicon dioxide ceramic thermal storage material; (C,G,K) Pre-treated Al-12Si/magnesium oxide ceramic thermal storage material; (D,H,I) Pre-treated Al-12Si/mullite ceramic thermal storage material with different sintering temperatures.
3.2.2 Physical and mechanical properties of samples prepared at different sintering temperatures
Figure 7A shows the compressive strength of different ceramic heat storage material samples prepared at 1,100°C, 1,200°C and 1,300°C. The compressive strength of the four types of ceramic heat storage materials increases and then decreases as the sintering temperature increases, and the compressive strength of the samples prepared at 1,300°C shows very little change compared to that of the samples prepared at 1,200°C, which indicates that the samples prepared at these two temperatures have similar properties. This conclusion is supported by the densities of the different ceramic heat storage material samples shown in Figure 7B, where the densities of the samples prepared at these two temperatures are approximately equal. This may be due to the fact that Pre-treated Al-12Si and ceramic matrix have similar properties at high temperatures. Due to the slight leakage of Al-12Si, the effect of metal melt flow and cooling agglomeration makes pre-treated Al-12Si/magnesium oxide ceramic thermal storage materials have the highest compressive strength of 28.59 MPa and density of 2.37 g/cm3 at a sintering temperature of 1,200°C.
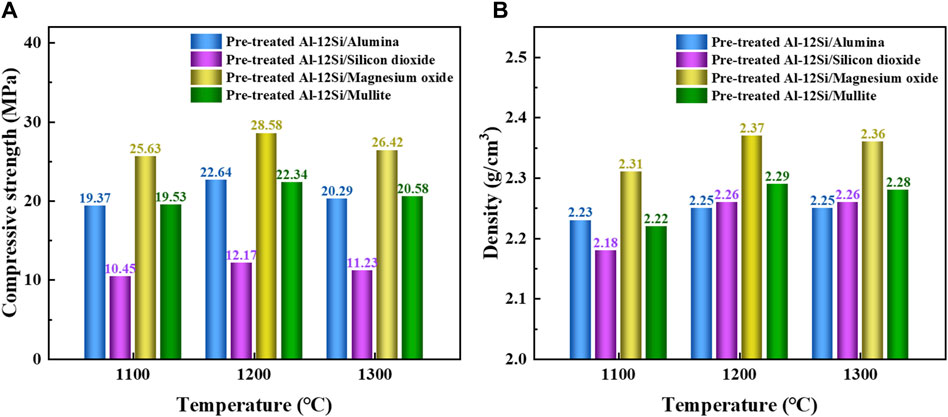
Figure 7. (A) Compressive strength and (B) Density of different ceramic thermal storage material samples with different sintering temperatures.
The thermal conductivity of the thermal storage material is also very important in practical industrial application scenarios. The higher the thermal conductivity, the faster the process of storing/releasing heat, the higher the energy storage efficiency of the energy storage system, and the lower the heat loss and thermal diffusion in the process. As can be seen from Table 3, the thermal conductivity of the ceramic thermal storage materials with different matrices shows a tendency of first increasing and then decreasing with the increase of sintering temperature of the samples, all of which have higher thermal conductivity under the sintering temperature of 1,200°C. In particular, pre-treated Al-12Si/mullite ceramic thermal storage materials prepared at a sintering temperature of 1,200°C have a thermal conductivity of up to 17.94 W/(m·K), which is about 7–17 times higher than that of ordinary thermal storage ceramics (Lu et al., 2020; Shi et al., 2022). This is due to the fact that the specimens prepared at 1,200°C are better sintered and have a lower porosity than the specimens prepared at 1,100°C. The samples prepared at 1,200°C consume less aluminium and have a higher Al-12Si alloy content during the heating process compared to the samples prepared at 1,300°C. When the sintering temperature is higher than 1,200°C, even though the thermal conductivity of the samples decreases, it is still much higher than that of the molten salt-based thermal storage ceramics whose thermal conductivity is improved by adding graphite (Yu et al., 2019; Yu and Tao, 2022), for example,. This suggests that even though the sintering temperature is much higher than the melting point of the Al-12Si alloy particles, the Al-12Si alloy particles may still be present in the initial form, and has successfully increased the thermal conductivity of the samples.
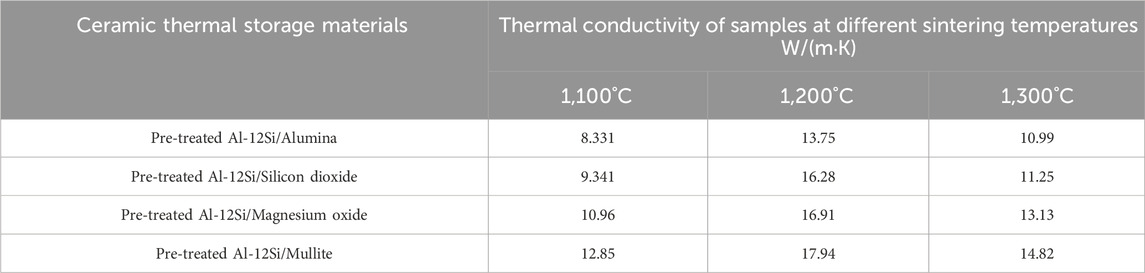
Table 3. Thermal conductivity of different ceramic thermal storage material samples with different sintering temperatures.
From Figure 8, it can be seen that the latent heat values of the ceramic thermal storage materials with different matrices show a decreasing trend with increasing sintering temperature, mainly due to the fact that, with increasing sintering temperature, the amount of aluminium oxidation in the Al-12Si alloy particles increases. Among them, the latent heat value of pre-treated Al-12Si/magnesium oxide ceramic thermal storage materials decreases rapidly with increasing sintering temperature, which is mainly attributed to the leakage loss of Al-12Si alloy particles. With the exception of Al-12Si/magnesium oxide ceramic thermal storage materials, the latent heat values of the three ceramic heat storage material samples were all above 140 J/g, which is much higher than many reported values for heat storage ceramics (Jiang et al., 2019).
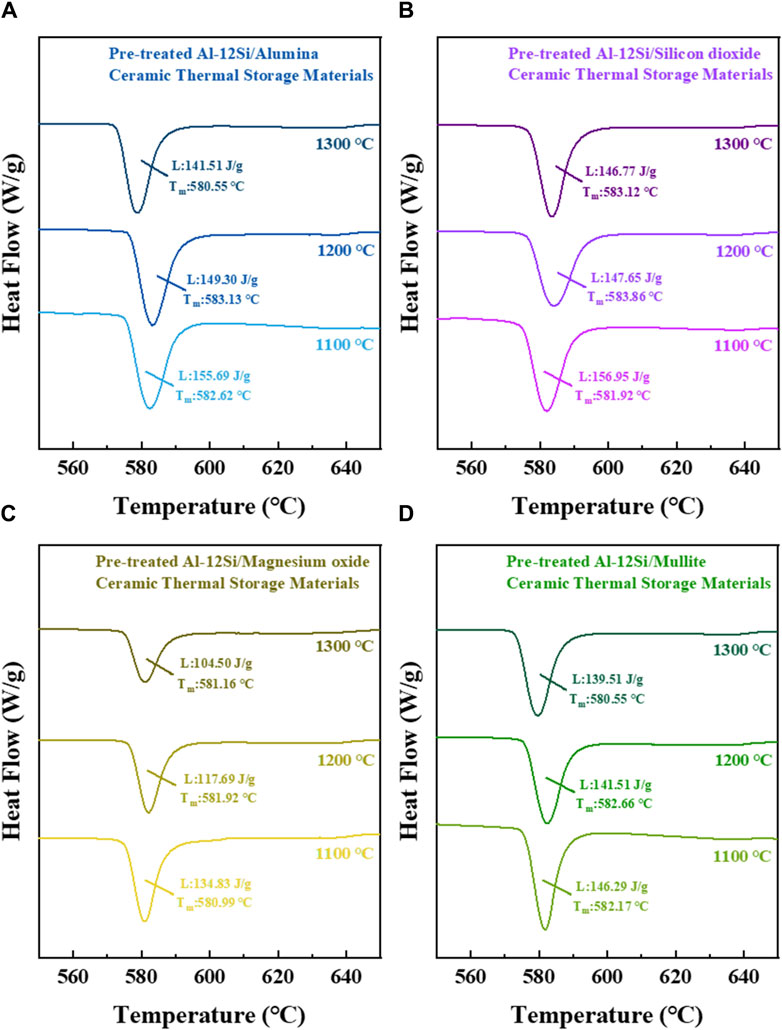
Figure 8. DSC analysis of (A) Pre-treated Al-12Si/alumina ceramic thermal storage material; (B) Pre-treated Al-12Si/silicon dioxide ceramic thermal storage material; (C) Pre-treated Al-12Si/magnesium oxide ceramic thermal storage material; (D) Pre-treated Al-12Si/mullite ceramic thermal storage material with different sintering temperatures.
From the above results and discussion, it can be seen that higher sintering temperatures are beneficial to the mechanical properties and thermal conductivity of the samples, but are not conducive to maintaining the high latent heat of the Al-12Si alloy. Therefore, the application of Al-12Si alloy as a phase change material in thermal storage ceramics requires a balance between mechanical properties, thermal conductivity and thermal storage properties.
Thermal cycling test of heat storage ceramics is also very important as it can simply predict their service life. The less the properties of the thermal storage material decay during the thermal cycling test, the better its thermal cycling stability and the longer its service life. This study focuses on the variation of latent heat value of thermal storage materials with different ceramic matrixes prepared at different sintering temperatures after 100 thermal cycles, and the test results are shown in Table 4. After 100 thermal cycles, the latent heat value of the Pre-treated Al-12Si/Magnesium oxide Ceramic Thermal Storage Materials decreased severely after the thermal cycle test, and serious leakage loss of Al-12Si alloy particles occurred. The latent heat value of the remaining three ceramic thermal storage materials prepared at 1,100°C decreased seriously, mainly due to the more serious leakage loss of Al-12Si alloy. The latent heat values of the samples with sintering temperatures of 1,200°C and 1,300°C decreased slightly. Especially, there is almost no significant change in the samples prepared at 1,300°C sintering temperature, which indicates that increasing the sintering temperature is helpful to avoid the leakage of the Al-12Si alloy phase change material. According to the literature (He et al., 2015b; Zou et al., 2019), the presence of pores in Al-12Si alloys after heat treatment at 1,200°C allowed the formation of aluminium oxide by the contact of oxygen with the aluminium liquid. In addition, these pores provide enough space for the melt expansion of Al-12Si alloy particles. Therefore, if the sintering temperature is not high enough (e.g., 1,100°C), the pores within the alloy are not sufficient due to limited aluminium oxidation, resulting in the Al-12Si alloy being more susceptible to leakage during thermal cycling tests. As the sintering temperature increases, more aluminium is consumed, resulting in more internal pores in the alloy and a thicker external aluminium oxide shell layer. This means that at sintering temperatures of 1,200°C and 1,300°C, the pores provide sufficient expansion space while the outer alumina layer effectively prevents the flow of the alloy, so that there is no significant leakage loss of the alloy after thermal cycling tests.
The results provided in this study contribute to the preparation and application of metallic phase change thermal storage ceramics Table 5. Summarized the thermal performance of various materials commonly used as well as the samples with potential thermal behavior in this study.
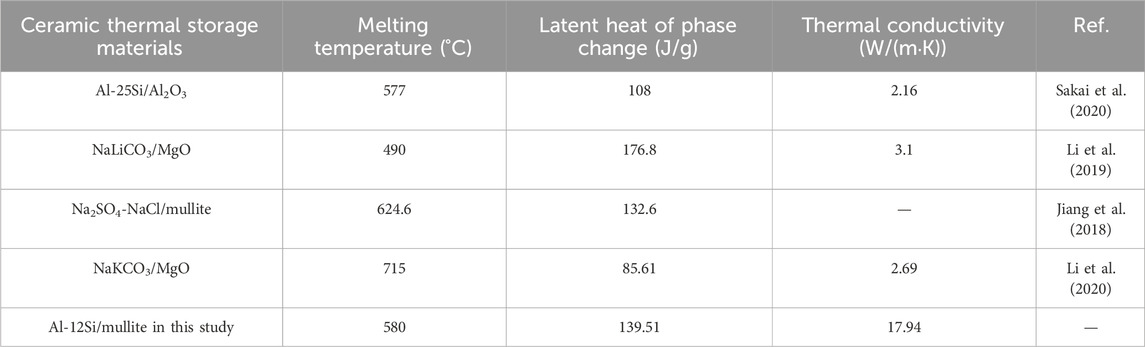
Table 5. Comparison of the samples in this study with commonly used phase change thermal storage ceramics.
We demonstrate the possibility of preparing thermal storage ceramic materials with both high latent heat value and high thermal conductivity. At the same time, it is also feasible to achieve cycling stability via examining their cycling durability for long-term use.
4 Conclusion
In this study, using Al-12Si as the phase change material and four kinds of alumina, silicon dioxide, magnesium oxide, and mullite as the ceramic matrix materials. Firstly, the Al-12Si alloy particles were pretreated, and the pre-treated Al-12Si phase change material with the Al-12Si/Al2O3 core-shell structure was prepared, which effectively prevents leakage loss of Al-12Si phase change material during use. The four pretreated Al-12Si/ceramic composite heat storage materials were prepared by mixing, pressing and sintering with ceramic matrix materials. It further immobilizes the metal PCM, prevents the loss of PCM, and improves the thermal cycle stability and industrial applicability of phase change heat storage materials. The results show that the chemical compatibility between the Al-12Si phase change materials and the four ceramic materials was good. At different sintering temperatures, each of the four ceramic composite heat storage materials shows similar microstructure, phase composition and physical properties. According to the performance test results, the pre-treated Al-12Si/mullite ceramic thermal storage materials have better properties than the remaining three ceramic thermal storage materials. In addition, at a sintering temperature of 1,200°C, pre-treated Al-12Si/mullite ceramic thermal storage materials exhibited the best performance due to higher density and lower oxidation. The thermal conductivity of the samples is up to 17.94 W/(m·K). The latent heat storage value of the samples was 139.51 J/g before thermal cycling and 138.27 J/g after 100 thermal cycles, which only decreased by 0.89%, with almost no leakage loss of Al-12Si alloy, showing excellent thermal cycle stability. In industrial production applications will show high latent heat density, high heat transfer efficiency and long service life. In this study, a kind of metal-based heat storage ceramics with simple preparation process, excellent performance and relatively low cost was successfully prepared, which provides technical support and theoretical basis for industrialized production and application.
Data availability statement
The original contributions presented in the study are included in the article/supplementary material, further inquiries can be directed to the corresponding author.
Author contributions
GZ: Conceptualization, Methodology, Writing–original draft, Writing–review and editing. DD: Investigation, Visualization, Writing–review and editing. JZ: Conceptualization, Methodology, Writing–original draft, Writing–review and editing. JH: Supervision, Writing–review and editing. ZD: Supervision, Writing–review and editing.
Funding
The author(s) declare that financial support was received for the research, authorship, and/or publication of this article. This study was funded by research and development project of State Grid Corporation of China under the grant number: 5419-202158300A-0-0-00, project Research on metallic composite phase change material and heat storage module design. The funder was not involved in the study design, collection, analysis, interpretation of data, the writing of this article, or the decision to submit it for publication.
Conflict of interest
The authors declare that the research was conducted in the absence of any commercial or financial relationships that could be construed as a potential conflict of interest.
Publisher’s note
All claims expressed in this article are solely those of the authors and do not necessarily represent those of their affiliated organizations, or those of the publisher, the editors and the reviewers. Any product that may be evaluated in this article, or claim that may be made by its manufacturer, is not guaranteed or endorsed by the publisher.
Abbreviations
PCMs, Phase change materials; TES, Thermal energy storage; SHS, Sensible heat storage; LHS, Latent heat storage; XRD, X-ray diffraction; SEM, Scanning electron microscopy.
References
Alehosseini, E., and Jafari, S. M. (2020). Nanoencapsulation of phase change materials (PCMs) and their applications in various fields for energy storage and management. Adv. Colloid Interfac. 283, 102226. doi:10.1016/j.cis.2020.102226
Ali, H. M., Rehman, T., Arıcı, M., Said, Z., Duraković, B., Mohammed, H. I., et al. (2024). Advances in thermal energy storage: fundamentals and applications. Prog. Energy Combust. 100, 101109. doi:10.1016/j.pecs.2023.101109
Boquera, L., Castro, J. R., Pisello, A. L., and Cabeza, L. F. (2021). Research progress and trends on the use of concrete as thermal energy storage material through bibliometric analysis. J. Energy Storage 38, 102562. doi:10.1016/j.est.2021.102562
Cheng, H., Ye, F., Wu, J., Shi, W., Leng, S., and Wu, S. (2018). In situ synthesis and mechanism of mullite-silicon carbide composite ceramics for solar thermal storage. Ceram. Int. 44 (15), 18541–18550. doi:10.1016/j.ceramint.2018.07.076
Ciriminna, R., Sciortino, M., Alonzo, G., Schrijver, A. D., and Pagliaro, M. (2011). From molecules to systems: sol−Gel microencapsulation in silica-based materials. Chem. Rev. 111 (2), 765–789. doi:10.1021/cr100161x
Farkas, D., and Birchenall, C. E. (1985). New eutectic alloys and their heats of transformation. Metall. Trans. A 16 (3), 323–328. doi:10.1007/BF02814330
Ge, Z., Ye, F., Cao, H., Leng, G., Qin, Y., and Ding, Y. (2014). Carbonate-salt-based composite materials for medium- and high-temperature thermal energy storage. Particuology 15, 77–81. doi:10.1016/j.partic.2013.09.002
He, F., Song, G., He, X., Sui, C., and Li, M. (2015a). Structural and phase change characteristics of inorganic microencapsulated core/shell Al–Si/Al2O3 micro-particles during thermal cycling. Ceram. Int. 41 (9), 10689–10696. doi:10.1016/j.ceramint.2015.05.001
He, F., Sui, C., He, X., and Li, M. (2015b). Comparison of structure and phase change characteristic of microencapsulated core/shell Al–Si alloy microparticles synthesized by two methods. J. Sol-Gel Sci. Techn. 76 (1), 1–10. doi:10.1007/s10971-015-3743-z
Jiang, F., Zhang, L., She, X., Li, C., Cang, D., Liu, X., et al. (2020). Skeleton materials for shape-stabilization of high temperature salts based phase change materials: a critical review. Renew. Sustain. Energy Rev. 119, 109539. doi:10.1016/j.rser.2019.109539
Jiang, Y., Sun, Y., Jacob, R. D., Bruno, F., and Li, S. (2018). Novel Na2SO4-NaCl-ceramic composites as high temperature phase change materials for solar thermal power plants (Part I). Sol. Energy Mat. Sol. C 178, 74–83. doi:10.1016/j.solmat.2017.12.034
Jiang, Y., Sun, Y., and Li, S. (2019). Performance of novel Na2SO4-NaCl-ceramic composites as high temperature phase change materials for solar power plants (Part II). Sol. Energy Mat. Sol. C 194, 285–294. doi:10.1016/j.solmat.2018.05.028
Katiyar, N., and Saha, S. K. (2022). Study of shrinkage effect of aluminium based binary alloys as phase change materials for latent heat thermal energy storage applications. J. Energy Storage 47, 103587. doi:10.1016/j.est.2021.103587
Kawaguchi, T., Sakai, H., Sheng, N., Kurniawan, A., and Nomura, T. (2020). Microencapsulation of Zn-Al alloy as a new phase change material for middle-high-temperature thermal energy storage applications. Appl. Energy 276, 115487. doi:10.1016/j.apenergy.2020.115487
Khare, S., Dell'Amico, M., Knight, C., and Mcgarry, S. (2013). Selection of materials for high temperature sensible energy storage. Sol. Energy Mat. Sol. C 115, 114–122. doi:10.1016/j.solmat.2013.03.009
Li, B., Tan, H., Liu, Y., Liu, Q., Zhang, G., Deng, Z., et al. (2020). Experimental investigations on the thermal stability of Na2CO3–K2CO3 eutectic salt/ceramic composites for high temperature energy storage. Renew. Energy 146, 2556–2565. doi:10.1016/j.renene.2019.08.027
Li, C., Li, Q., Cong, L., Jiang, F., Zhao, Y., Liu, C., et al. (2019). MgO based composite phase change materials for thermal energy storage: the effects of MgO particle density and size on microstructural characteristics as well as thermophysical and mechanical properties. Appl. Energy 250, 81–91. doi:10.1016/j.apenergy.2019.04.094
Li, R., Zhu, J., Zhou, W., Cheng, X., and Li, Y. (2016). Thermal properties of sodium nitrate-expanded vermiculite form-stable composite phase change materials. Mater. and Des. 104, 190–196. doi:10.1016/j.matdes.2016.05.039
Lu, Y., Zhang, G., Hao, J., Ren, Z., Deng, Z., Xu, G., et al. (2019). Fabrication and characterization of the novel shape-stabilized composite PCMs of Na2CO3-K2CO3/MgO/glass. Sol. Energy. 189, 228–234. doi:10.1016/j.solener.2019.07.064
Lu, Y., Zhang, G., Hao, J., Ren, Z., Deng, Z., Xu, G., et al. (2020). Study on the effect of glass on the properties of Na2CO3-K2CO3 eutectic salt/MgO composite as phase change thermal storage materials. Energy Sources, Part A Recovery, Util. Environ. Eff. 1–12. doi:10.1080/15567036.2020.1783033
Ma, Q., Zou, D., Wang, Y., and Lei, K. (2021). Preparation and properties of novel ceramic composites based on microencapsulated phase change materials (MEPCMs) with high thermal stability. Ceram. Int. 47 (17), 24240–24251. doi:10.1016/j.ceramint.2021.05.135
Nomura, T., Yoolerd, J., Sheng, N., Sakai, H., Hasegawa, Y., Haga, M., et al. (2018). Microencapsulation of eutectic and hyper-eutectic Al-Si alloy as phase change materials for high-temperature thermal energy storage. Sol. Energy Mat. Sol. C 187, 255–262. doi:10.1016/j.solmat.2018.08.001
Ramachandran, T., Sana, S. S., Kumar, K. D., Kumar, Y. A., Hegazy, H. H., and Kim, S. C. (2023). Asymmetric supercapacitors: unlocking the energy storage revolution. J. Energy Storage 73, 109096. doi:10.1016/j.est.2023.109096
Sakai, H., Sheng, N., Kurniawan, A., Akiyama, T., and Nomura, T. (2020). Fabrication of heat storage pellets composed of microencapsulated phase change material for high-temperature applications. Appl. Energy 265, 114673. doi:10.1016/j.apenergy.2020.114673
Shi, B., Zhao, X., Zhang, J., Jin, Y., Liu, D., Yan, S., et al. (2022). Preparation and performance characterization of steel slag-based thermal storage composites for waste recycling and thermal energy storage. Energy Sources, Part A Recovery, Util. Environ. Eff. 44 (3), 8221–8234. doi:10.1080/15567036.2022.2120933
Sun, G., Liu, Y., Dong, S., and Wang, J. (2020). Study on novel molten salt-ceramics composite as energy storage material. J. Energy Storage 28, 101237. doi:10.1016/j.est.2020.101237
Takahashi, Y., Sakamoto, R., and Kamimoto, M. (1988). Heat capacities and latent heats of LiNO3, NaNO3, and KNO3. Int. J. Thermophys. 9 (6), 1081–1090. doi:10.1007/BF01133275
Xiao, X., Zhang, P., and Li, M. (2013). Thermal characterization of nitrates and nitrates/expanded graphite mixture phase change materials for solar energy storage. Energy Convers. Manage. 73, 86–94. doi:10.1016/j.enconman.2013.04.007
Yan, W., Wu, G., Ma, S., Schafföner, S., Dai, Y., Chen, Z., et al. (2018). Energy efficient lightweight periclase-magnesium alumina spinel castables containing porous aggregates for the working lining of steel ladles. J. Eur. Ceram. Soc. 38 (12), 4276–4282. doi:10.1016/j.jeurceramsoc.2018.05.002
Yu, K., Jin, B., Liu, Y., and Li, L. (2019). Enhanced thermal conductivity of form-stable phase change materials using carbon nanofiber-expanded graphite hybrid structure. Mater. Res. Express 6 (12), 125503. doi:10.1088/2053-1591/ab52ae
Yu, X. K., and Tao, Y. B. (2022). Preparation and characterization of paraffin/expanded graphite composite phase change materials with high thermal conductivity. Int. J. Heat. Mass Tran. 198, 123433. doi:10.1016/j.ijheatmasstransfer.2022.123433
Zhang, J., Guo, Z., Zhu, Y., Zhang, H., Yan, M., Liu, D., et al. (2024). Preparation and characterization of novel low-cost sensible heat storage materials with steel slag. J. Energy Storage 76, 109643. doi:10.1016/j.est.2023.109643
Zhao, W., France, D. M., Yu, W., Kim, T., and Singh, D. (2014). Phase change material with graphite foam for applications in high-temperature latent heat storage systems of concentrated solar power plants. Renew. Energy 69, 134–146. doi:10.1016/j.renene.2014.03.031
Keywords: latent heat storage, ceramic composite materials, Al-12Si alloy, thermal energy storage, composite heat storage material
Citation: Zhang G, Duan D, Zhang J, Hao J and Deng Z (2024) Preparation and characterization of Al-12Si/ceramic composite phase change heat storage material. Front. Energy Res. 12:1455576. doi: 10.3389/fenrg.2024.1455576
Received: 27 June 2024; Accepted: 05 August 2024;
Published: 19 August 2024.
Edited by:
Chatchai Sirisamphanwong, Naresuan University, ThailandReviewed by:
Ganeshraja Ayyakannu Sundaram, Saveetha Dental College and Hospitals, IndiaTholkappiyan Ramachandran, United Arab Emirates University, United Arab Emirates
Aneesh A. Chand, University of the South Pacific, Fiji
Copyright © 2024 Zhang, Duan, Zhang, Hao and Deng. This is an open-access article distributed under the terms of the Creative Commons Attribution License (CC BY). The use, distribution or reproduction in other forums is permitted, provided the original author(s) and the copyright owner(s) are credited and that the original publication in this journal is cited, in accordance with accepted academic practice. No use, distribution or reproduction is permitted which does not comply with these terms.
*Correspondence: Jingcen Zhang, MTc4ODg4MDMyNTRAMTYzLmNvbQ==