- 1State Grid Sichuan Electric Power Research Institute, Chengdu, China
- 2Power Internet of Things Key Laboratory of Sichuan Province, Chengdu, China
- 3School of Electrical Engineering and Information, Southwest Petroleum University, Chengdu, China
Battery pack provides the backup power supply for DC system of power substations. In the event of an AC power outage or other accidents, it is an important guarantee for the reliable operation of power substation. To prevent possible failures, batteries usually require careful maintenance. Common methods are online monitoring, condition assessments, and health management. Among these, model-based techniques are widely used for battery monitoring and prognostics optimization. Data-driven methods are a good alternative solution when no mathematical models are available. As substations develop towards intelligent and unmanned modes, this paper proposes an online battery monitoring and management system based on the “cloud-network-edge-end” Internet of Things (IoT) architecture. Firstly, advanced battery monitoring system based on IoT architecture is reviewed in depth. It provides basis for later designing. Secondly, the battery online monitoring and management system is designed considering functional requirements and data link. Designing functions include ledger management, basic battery information display, real-time display of battery monitoring data, and the visualization of battery alarm information. It can implement online monitoring and intelligent maintenance management for battery operating status. Finally, the designed and developed system is applied in a 110 kV offshore substation, mainly providing battery maintenance suggestions and fault alarm prompts. Typical results of ledger information management, key parameter monitoring and alarm prompt are presented. This verifies the effectiveness and convenience of IoT-based system for the monitoring and management of batteries.
1 Introduction
Battery pack provides the backup power supply for DC systems of power substations. It mainly provides power for DC loads used for protection, control, automatic devices, and emergency lighting. Therefore, its reliability is extremely important. If an accident occurs in a substation, however, the battery cannot supply power, then the entire power system may encounter equipment shutdowns, power supply paralysis, or other major operational accidents. Entire station voltage loss incidents caused by battery failures have occasionally happened. This has had serious impacts on the safety of the power grid (Li et al., 2013). Therefore, it is important to estimate battery usage and health status.
Batteries normally operate in floating charge state. Long-term floating charge will cause electrochemical substances to lose water, crystallize, and form salt. This will result in reduced capacity and shortened life. Therefore, batteries need to be maintained over time. Main maintenance methods are regular nuclear capacity discharges, regular internal resistance tests, regular terminal voltage measurements, and online monitoring (Pradhan and Chakraborty, 2022). Among these, the nuclear capacity discharge cycle is generally 1–2 years. Voltage measurements for a single battery should be conducted once a month, and battery internal resistance testing should be conducted at least once a year. It is often the case that one or several batteries fail first and lead to a decline in the overall performance of battery pack. It is difficult to detect the lagging batteries in time through maintenance with long interval period. In addition, problems such as high maintenance costs, cumbersome processes, and low maintenance efficiency have become increasingly prominent. Thus it is urgent to investigate effective online monitoring and maintenance methods.
Power fading, capacity, and internal resistance are the parameters that help to assess battery aging levels (Pradhan and Chakraborty, 2022). Some battery management systems have been developed for monitoring the health of batteries. They mainly monitor battery cell voltage, floating charge current, internal resistance, and ambient temperature. And they conduct comprehensive analyses, provide diagnoses, and issue fault warnings. According to differences in the monitoring algorithms, these systems are mainly divided into two categories at present. One type is based on modeling and the other is driven by data.
The model-based system establishes electrochemical and equivalent circuit models by analyzing the deterioration mechanism in batteries (Hu et al., 2020). Particle filter and derived algorithms are usually combined to estimate the model parameters. However, it has limitations in adaptability for complex environments, model deviations and error accumulations, high data demands, and slow real-time response speeds (Semeraro et al., 2022). Data-driven monitoring systems rely on artificial intelligence technology to analyze and process data in real time (Samanta et al., 2021). The focus is on improving the efficiency and accuracy of battery monitoring. Various artificial intelligence technologies can be combined to cope with the complexity and variability of battery management, including machine learning, deep learning, and data mining technologies (Deng et al., 2020).
Many online monitoring systems have been developed. However, most of them have the following problems: 1) high maintenance costs, cumbersome processes and low maintenance efficiency (Zhou et al., 2017); 2) insufficient data analysis and alarm prompts (Thomas et al., 2021); 3) limited remote control capabilities (Kim et al., 2012). In recent years, remote control and communication technologies have been developing rapidly. With the proposal of digital and intelligent construction for power grids, battery maintenance has tended to use remote control monitoring systems. This requires the monitoring system to have strong remote control, online monitoring, and massive data processing capabilities. Since the Internet of Things (IoT) technology has outstanding advantages for massive data integration and intelligent processing, the application of IoT technology to intelligent monitoring has become a research hotspot.
Figure 1 shows a typical monitoring system diagram under the IoT framework. It is composed of four parts, a data collector, an IoT gateway, a database, and a comprehensive analysis platform, with an integrated application and display platform. Data is collected from sensors and uploaded to a database and comprehensive analysis platform through an IoT gateway using GPRS, LoRa, ZigBee, or other communication technologies. After calculation and processing, the analysis results are presented to the integrated application and display platform to achieve remote monitoring.
Monitoring systems based on the IoT architecture have advantages in remote control, data interconnection, and intelligent processing. This is very important for improving the efficiency for battery monitoring, operation, and maintenance. It also helps in overcoming the remote control shortcomings of traditional battery monitoring systems. Researchers have explored and conducted some research on battery monitoring systems based on IoT architecture. Abd proposed the application of IoT technology to electric vehicle power battery monitoring to achieve direct monitoring of vehicle battery performance (Abd Wahab et al., 2018). Friansa proposed a BMS-IoT battery monitoring system, which improved the efficiency of data transmission and processing (Friansa et al., 2017). In general, battery monitoring system collects a large amount of data, which can be uploaded to the cloud server. The related data-driven and model-based research can expand upon the breadth and depth of battery status analysis (Wu et al., 2021).
In view of the various problems existing in battery monitoring system, this paper first summarizes the importance of battery monitoring and the application of IoT technology to monitoring systems in part 2. Then, a battery online monitoring management system is designed in part 3 based on sensing layer, transmission layer and application layer. Finally, the system is verified through practical application in part 4, establishing online monitoring for the battery operating status.
2 Battery monitoring system based on the internet of things architecture
2.1 Battery monitoring system based on the “cloud-network-end” internet of things architecture
The term “Internet of Things” first originated in 1999. It is the concept that objects are connected to the internet (in accordance with agreed upon transmission protocols) via embedded information sensing devices, thereby allowing intelligent management of real-world objects. As an important part of modern information technology, the IoT has many functions, such as real-time monitoring, remote control, intelligent decision-making, and data sharing. Currently the IoT is widely used in many fields, such as monitoring and measurement, industrial automation, smart cities, intelligent transportation, and IoT agriculture.
The architecture of the IoT can be divided into three layers, perception layer, network layer and application layer (Zhu and Hu, 2022), as shown in Figure 2. As the bottom layer of the IoT, the perception layer has the function of acquiring and processing object information. The network layer uses private networks, the internet, or carrier networks to transmit object information obtained by perception layer. The application layer mainly deploys application services based on perceptual information, including information processing and human-computer interaction.
When applied to the field of battery monitoring, IoT technology has certain advantages. It can implement real-time network connections and data exchanges among equipment and parallel computing between the edge and the cloud. It can implement efficient monitoring of the battery status, environmental parameters, and other information. It can also improve the real-time, precision, and intelligence of the monitoring system, provide users with more comprehensive and accurate monitoring services, and promote the efficiency of decision optimization and resource management. In research conducted by Zhang and Qian (2023), a cloud monitoring system is proposed for lithium battery packs based on GPRS, which implements the real-time monitoring of battery data through a cloud platform and reduces remote monitoring maintenance costs. In general, the application of IoT technology in the field of battery monitoring has been a research hotspot in recent years.
Therefore, battery monitoring systems based on “cloud-network-end” IoT architecture have advantages including real-time monitoring, big data analysis, high-speed communication, remote control, and cost effectiveness. The overall performance of the monitoring system and user experience can be improved (Liu et al., 2022). Figure 3 shows a battery monitoring system based on the “cloud-network-end” Internet of Things architecture.
“End” is the IoT terminal layer. It can realize intelligent perception, information collection and automatic control of the battery. IoT terminals mainly include batteries, information sensors, RFIDs and two-dimensional codes, and other terminal devices. In addition, the IoT terminal layer also has a variety of communication technologies such as commonly used LoRa and WIFI technologies. It uses an IoT gateway to transmit basic battery and monitoring information.
“Network” refers to the network transmission layer. It uses wireless or wired communication technology for battery information transmission and processing. Widely covered operator communication networks, rapidly developing internet and user private networks are the foundation of IoT deployments. These widely used networks can implement the transmission and delivery of data information, which guarantees large-scale IoT coverage.
“Cloud” is the remote integrated management layer. It can monitor battery information and mainly handles information processing and human-computer interactions. Remote integrated management is the main development goal of IoT technology. By combining IoT-related technologies with battery monitoring needs, intelligent applications can be deployed, including the monitoring and management of energy storage power stations, electric vehicle power batteries, and substation backup power supplies.
2.2 Battery monitoring systems based on “cloud-network-edge-end” internet of things architecture
The battery monitoring system of “cloud-network-end” Internet of Things architecture improves the remote control, online monitoring, and mass data processing capabilities of the monitoring system to a certain extent. However, it also has many deficiencies and limitations such as network dependence, data transmission security, and processing delays. Therefore, advanced battery monitoring systems have been mainly developed in the fields of network and information security, data analysis and processing, distributed systems, and parallel computing, along with energy-saving technology and green computing. A NB-IoT-ZigBee technology lithium-ion battery pack monitoring system has been proposed to solve the problems of high cost, high loss and low coverage of monitoring. In research conducted by Friansa et al. (2017), a BMS-IoT battery monitoring system was proposed to improve data analysis and processing effects. To improve data transmission security and optimize system performance, Islam et al. (2024) proposed an IoT battery monitoring system combining a narrowband Internet of Things (NB-IoT) with edge technology.
Compared with other monitoring systems, battery monitoring systems based on the “cloud-network-edge-end” IoT architecture have better data processing and response abilities. These systems have enhanced security and privacy protection, enhanced system stability and reliability, and reduced network bandwidth requirements. This can significantly improve the overall performance and user experience (Kim et al., 2015). These systems have become the mainstream currently.
The system is roughly divided into a front-end monitoring layer, a data transmission layer, an edge computing layer, and an IoT terminal layer. The typical structure is shown in Figure 4. An edge computing layer is added to the original “cloud-network-end” IoT architecture. The IoT terminal layer transmits the perceived battery information to the edge computing layer through an access network. The data information ensures the security of the data transmission through a 4G/5G private network or other communication technologies. In the edge computing layer, the battery data information is preliminarily processed through edge computing. Parallel computing is implemented for edge computing and cloud computing. This improves the data analysis abilities and data processing speeds. The network transmission layer uploads the processed data to the cloud server using high-speed communication technology. The remote integrated management includes a cloud server and a remote-control interface. The cloud server performs big data analysis on the battery information from the IoT terminal and feeds the analysis results back to the remote-control interface, which establishes the integrated management and monitoring of the battery.
The battery monitoring system of “cloud-network-edge-end” IoT architecture involves cloud computing and edge computing. In data processing tasks, it is often necessary to divide the tasks between cloud computing and edge computing in order to reduce the data processing delay. Specific strategies for task partitioning can be implemented by key factors and criteria such as real-time requirements, resource constraints, network bandwidth costs, security and privacy requirements, and application characteristics (Chen et al., 2022).
3 Design of the battery online monitoring and management system
Battery monitoring systems based on the “cloud-network-end” IoT architecture have advantages in information perception, identification, transmission, and computing to improve the overall system performance. However, there are still challenges in battery monitoring data analysis and processing, and data transmission delays. The “cloud-network-edge-end” IoT architecture adopts edge technology. Edge computing analyzes the operating state of the battery near the source of the data, which can significantly improve the data processing rate and reduce the network energy consumption. In research conducted by Pascual, edge end monitoring is integrated with the cloud, which solves the problem of the high complexity of the data computations and the low data transmission rate. In research conducted by Sodhro, edge and IoT technology are used to effectively allocate computing resources and improve energy efficiency (Sodhro et al., 2019). In research conducted by Gotz, edge computing is combined with cloud computing to conduct a joint analysis of the battery operating status (Gotz et al., 2023), which improved the monitoring accuracy.
Based on the analysis above, the battery online monitoring and management system designed in this paper also adopts the “cloud-network-edge-end” Internet of Things architecture. Consequently, the overall functionality and data links are then addressed.
3.1 System functional requirement
Battery management system ensures the health of the battery by performing key processes such as charge and discharge management, temperature management, operating condition assessment, fault diagnosis, and maintenance decisions. The above processes can ensure that the battery is charged and discharged within a safe range. It can also ensure that the battery is operating within a safe range and predict the future health of the battery. It usually monitors the operating status of the battery, detects abnormal conditions, issues warnings in time, and makes maintenance decisions to prevent serious damage or safety issues (Xiong et al., 2018).
The designed system should have the following functional requirements. This can ensure that users understand the status and performance of battery in real time. It also improves the reliability and energy efficiency of the system.
3.1.1 Ledger management
The battery ledger management function records the entire life cycle of the battery. The ledger management function can input the battery’s basic information. It can be convenient for users to query, manage, and track battery procurement and supply chain information. At the same time, it can also manage the battery’s test records and maintenance records, helping users to track the functional status and health status of the battery. Furthermore, users can find the faults and problems of the battery in time and carry out appropriate maintenance or replacement.
3.1.2 Battery basic information display
The system provides a battery information display interface in which users can browse the basic information of each battery, so that users can clearly understand the overall status of the battery pack. At the same time, the interface should include the battery model, manufacturer, capacity, voltage, and other basic information and can show the production date, remaining capacity, and other additional information. In this way, users can have a comprehensive understanding of the characteristics of the battery.
3.1.3 Real-time display of battery monitoring data
The battery monitoring data is displayed in real time, which can show users the operating status of battery. The real-time monitoring and display of important parameters such as battery voltage, current, internal resistance, and temperature are implemented. The changes in each parameter are displayed in the form of charts, so that users can have an intuitive understanding of a battery’s operating status. The data display interface can intuitively reflect the change rules of each parameter of the battery pack during operation. Through graphics and real-time curves, users can clearly see the changing trends in the various battery indicators and thus determine the running status of the battery.
3.1.4 Visualization of battery alarm information
Battery alarm information can be visualized in text boxes. Various parameters of the battery are monitored online. When they reach or exceed the preset critical value, the system issues a real-time alarm, and the alarm information box immediately displays the relevant information including the platform, equipment, alarm time, alarm content, and alarm level. Through this function, users can comprehend the battery alarm situation more intuitively and handle faults or problems in a timely manner.
3.1.5 Measurement accuracy of the characteristic parameters
The characteristic parameters that reflect the battery state can be divided into temperature parameters, voltage parameters, SOC parameters, current parameters, capacity parameters, and internal resistance parameters (Hu et al., 2019). The system designed in this paper mainly measures and monitors voltage, current and internal resistance.
Voltage monitoring is used to describe the electrochemical and physical properties of the battery, which evaluates the performance of the battery under different conditions. Current monitoring is used to judge thermal stability in case high current leads to serious capacity loss. A 100% increase in internal resistance is usually considered the end of battery life (EOL), so internal resistance monitoring is used to assess the performance status and health of the battery (Waag et al., 2013).
Accurate measurement is the basis for the precise evaluation of the battery status. The measurement accuracy for parameters needs to meet certain standards. In standard DL/T 2226–2021, the accuracy requirements for voltage, current, and internal resistance measurements are those listed in Table 1.
The measurement system is a technical system used to acquire, record and process data. The basic components include sensor, signal processing and data acquisition. As the battery monitoring system designed in this paper is mainly applied for offshore platforms, the measurement accuracy meets above requirements and even better. They are 0.3% for battery pack voltage, 0.15% for single battery voltage, 1% for current, 5% for resistance, and 1°C for temperature.
It needs to mention that due to the importance of energy production and complex environment for offshore platforms, the reliability of the entire offshore power system is required to be high, and the battery is the key to ensure uninterrupted power supply (Itiki et al., 2019). Therefore, the quality of the collected battery data must meet the measurement accuracy, so that the health state of the battery can be accurately judged. To meet the accuracy requirements, the entire edge measurement system becomes a complex, accurate and expensive system.
3.1.6 Continuous monitoring of batteries
In the process of battery monitoring, it is important to ensure continuous monitoring of the battery. The monitoring system of Internet of Things relies on the network for data transmission and big data analysis. When the monitoring system network is down, measures need to be taken to ensure continuous monitoring during such events. Currently, battery monitoring systems respond to network outages through a variety of technologies and strategies to ensure that battery status can be continuously and effectively monitored and timely notified under any circumstances. Specific methods include local data storage and caching, off-line mode, real-time alarms and notifications, automatic reconnection and recovery mechanism, alternate communication path. Their detailed functions are listed in Table 2.
3.2 Overall system architecture
The overall diagram of the system designed in this paper is shown in Figure 5.
The system is mainly divided into data acquisition layer, edge computing layer, data transmission layer, data judgment layer and uses front-end management layer. The specific functional information of each module is described as follows.
3.2.1 Data collecting layer
This module is designed to collect the operating status data of the target battery such as voltage, current and internal resistance. It is mainly composed of different measurement subsystems. A subsystem usually includes sensing, data acquisition and signal processing. Sensors here includes voltage sensor, current sensor, temperature sensor and so on.
The voltage sensor directly contacts the positive and negative electrodes of the battery through the probe or fixture, and collected data is sent to processing unit by wireless. The current sensor is a current transducer and is sleeved onto wires in a non-invasive manner. The internal resistance is calculated through specific device. Similarly, the data is transmitted to the receiving device by wireless.
Once the sensors and monitoring devices are installed, data can be transmitted via wireless to the data processing unit. It can be said that the whole monitoring is non-invasive.
3.2.2 Edge computing layer
This module implements real-time processing and analysis of the data, filters and compresses the data, and sends important data to the central server. The edge computing layer provides a short delay communication mechanism for the monitoring system, enabling the monitoring system to respond quickly to emergencies and warnings. In addition, the edge computing layer can also process and encrypt the data locally, reduce the risk of data transmission in the network, ensure the security of the monitoring data, and improve the reliability and fault tolerance of the system.
3.2.3 Data transmission layer
This module mainly uses the data concentrator to transmit collected monitoring data from the sender to the receiver and verifies the receipt of the data by using a confirmation mechanism. In addition, the data transmission layer provides flow control and quality of service options to dynamically adjust the transmission rate to avoid packet accumulation or packet loss during data transmission. It meets the specific requirements of the monitoring system for data transmission.
In the process of data transmission, it is often necessary to prevent data leakage, ensure data integrity, protect privacy and compliance. Therefore, using data encryption methods can achieve the above effect. Common data encryption algorithms include Advanced Encryption Standard (AES), Rivest-Shamir-Adleman (RSA) (Han, 2022), Transport Layer Security (TLS)/Secure Sockets Layer (SSL) encryption (Tiago, 2020), and MD5 Message-Digest Algorithm (MD5) (Reddy et al., 2024). The specific methods are shown in Table 3.
The data encryption method used in this battery monitoring system is MD5 Message-Digest Algorithm. Security measures are also needed to protect sensitive battery data. Common security measures include: 1) Identity authentication and access control; 2) Secure transmission protocol; 3) Security audit and monitoring; 4) Data anonymization and desensitization.
3.2.4 Data judgment layer
This module mainly assesses the battery operation data to determine whether the terminal voltage, internal resistance, and charge/discharge current are normal or not.
First, the battery voltage seems to be normal when the battery is in floating state. Once the battery needs to carry a DC load, the battery terminal voltage may drop rapidly. In this situation, the battery cannot meet the DC load power supply requirements.
Secondly, with an increase in discharge times, the electrolyte inside the battery will be gradually consumed. The activity of the chemical substances on the plate will decrease, and the internal resistance will increase. The worse the battery condition, the faster the internal resistance increases. Therefore, the internal resistance can be used as an indicator of battery degradation. By monitoring the internal resistance of the battery, its status can be judged. If the internal resistance exceeds 25% of the reference value, the battery capacity should be unqualified. If it exceeds 50%, the battery needs to be replaced immediately (Wang et al., 2022).
Finally, an increase in battery charging and discharging current will cause the battery temperature to rise, thereby accelerating the decay of the battery life. However, it will also affect the structure of the positive and negative electrode materials to a certain extent, accelerate the consumption of the electrolyte solution on the positive and negative plates, and thus accelerate the attenuation of the battery capacity.
Therefore, Qt Creator software is used for programming. The monitoring data, including the battery voltage, charge/discharge current and internal resistance, are obtained from the cloud server. Distributed computing and parallel computing are then implemented to complete the assessment of the battery operation status data.
Reducing data processing latency is crucial for battery monitoring systems. It can improve the timeliness, accuracy, and effectiveness of monitoring. It can also ensure the safe operation of equipment and systems, extend the service life of batteries, and improve utilization efficiency. In terms of minimizing data processing delays and maintaining real-time monitoring, there are the following specific strategies: distributed computing and parallel processing, streaming processing, cache and prefetch technology, optimization algorithm (Ju et al., 2019; Oliveira et al., 2022), as shown in Table 4.
The system designed mainly adopts distributed computing, parallel processing, optimization algorithm to reduce the data processing delay.
3.2.5 Front-end management layer
This module is used to display the battery operation status data obtained by the data judgment layer on the front-end interface. Operation and maintenance personnel can interact with the front-end management layer to view the battery running status information in real time. When a battery device fails, the front-end management layer will issue an alarm notification in a timely manner. Operation and maintenance personnel can obtain the fault information and take corresponding measures. At the same time, they can also view the operation status information of any monitored battery in the module.
3.3 Data link
Data link is the transmission path of the battery-related data in the entire battery monitoring and management system, as shown in Figure 6.
It can be seen from Figure 6 that the data transmission path is from the IoT “terminal” to the “edge” end and then to the “cloud” end. The IoT “terminal” is connected to the monitored battery to obtain battery-related data, including monitoring data, basic battery information, and video monitoring. The “edge” end performs edge computing on the battery monitoring data and processes the video monitoring information, including: 1) processing of the battery voltage, current and internal resistance data, 2) uploading the diagnostic results to the IoT platform, and 3) uploading the video monitoring information to the video networking platform. The “cloud” end presents the operating status data information on the front-end interface to achieve the human-computer interaction.
In general, data link shows the transmission path of data in each system. The data transmission process often involves the compatibility and integration of monitoring system and equipment. The following are some common measures and steps: 1) to develop a unified standardized format, interface specifications; 2) Adopt common data format; 3) Follow industry standards and open standards; 4) Develop a complete monitoring system product chain (Qiu et al., 2022). The data transmission path here can be divided into two parts as follows:
1) The battery video monitoring information from the IoT “terminal” is first uploaded to the “edge” end of the visual networking platform for processing and then uploaded to the “cloud” end of the battery online monitoring management system. Finally, the video information is displayed on the battery online management page. The video monitoring information is the monitoring video of the on-site battery in the room.
2) The battery monitoring information of the IoT “terminal” is first uploaded to the IoT platform at the “edge” end. Edge computing is performed, and the results are uploaded to the IoT platform and alarm center. Then, the battery operating status is analyzed by cloud computing at the “cloud” end. Edge computing and cloud computing can jointly analyze the battery operating status, thereby improving the accurate monitoring of the battery operating status. Finally, the operating status information and alarm information are uploaded to the online monitoring and management system for display.
4 Application verification
In this paper, the battery monitoring system is installed in a 110 kV substation of offshore platform. Rated voltage of battery pack is required to be 400 V. 32 batteries are used in serial and each has an initial voltage of 14 V.
It is first necessary to enter the basic information and establish the overall management of all the battery equipment, so that management personnel can query information and track the basic information. Figure 7A is the designed interface and Figure 7B is the actual system interface. A difference is that the system is presented in Chinese in field application.
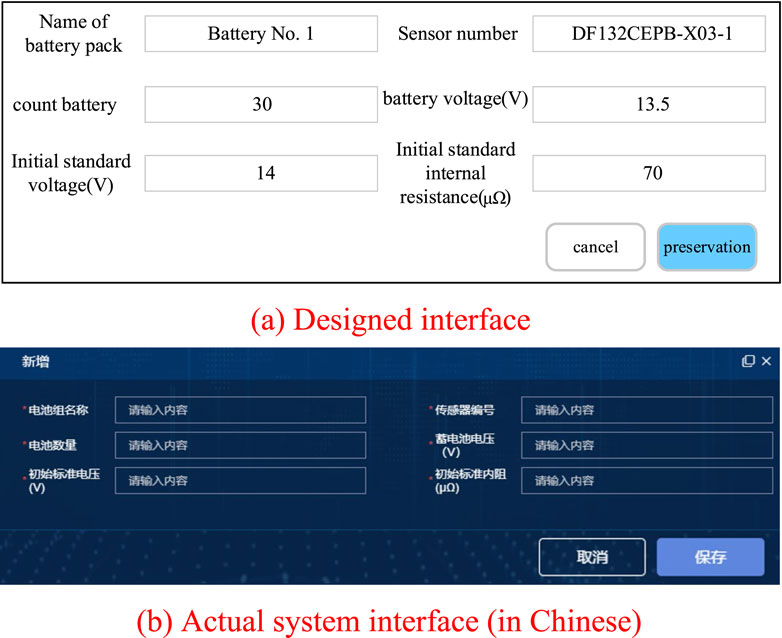
Figure 7. Battery account information. (A) Designed interface. (B) Actual system interface (in Chinese).
In other words, the designed online monitoring and management system have a ledger management function. The entered information includes battery pack name, sensor number, number of batteries, battery voltage, initial standard voltage, and initial standard internal resistance.
The overall management of all the battery equipment can be established after the battery pack ledger is entered. Then the system interface can intuitively and comprehensively display the basic information of the battery. Figure 8 shows a typical example. It shows the basic information (manufacturer, type, capacity, rated voltage, quantity, etc.) of the battery in the DC power supply system of an offshore oil and gas field.
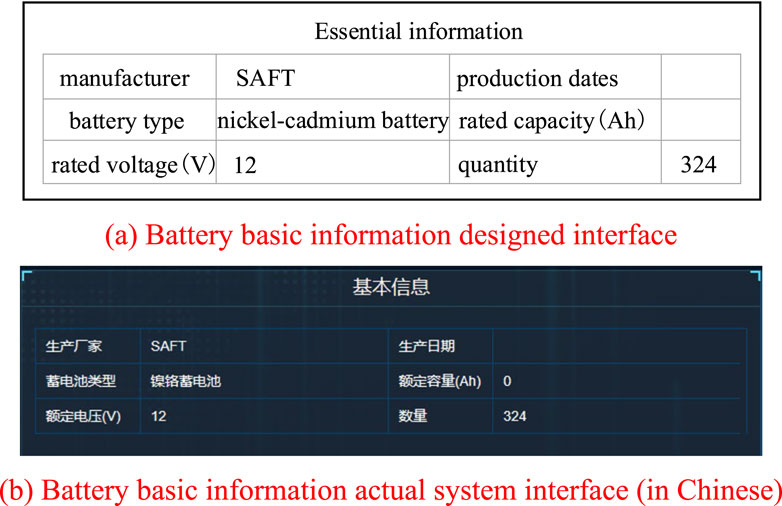
Figure 8. Basic battery information. (A) Battery basic information designed interface. (B) Battery basic information actual system interface (in Chinese).
After completing the entry of the monitoring battery ledger information, the battery operation status data can be obtained from the data acquisition layer. The data here includes the voltage of a single battery, the initial standard voltage, the internal resistance, the initial standard internal resistance, the total battery voltage, and the charging current of the entire battery.
Figure 9 shows the designed and actual interface of battery monitoring data. The data of the battery pack includes cell number, cell voltage, initial standard voltage, cell internal resistance, and initial standard internal resistance. When abnormal information is detected, the system will record the specific time when the battery failure occurred and the specific alarm content and display them on the front-end interface.
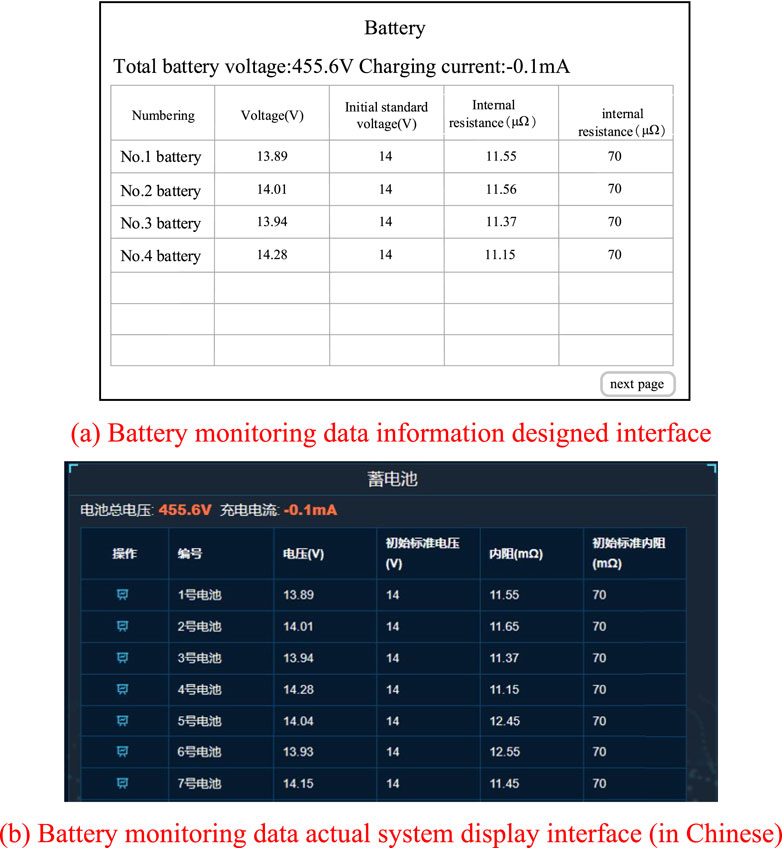
Figure 9. Battery monitoring data. (A) Battery monitoring data information designed interface. (B) Battery monitoring data actual system display interface (in Chinese).
The 455.6 V here is the total voltage of the battery pack. It has 32 batteries in serial and each has a voltage near 14 V. Voltages for No. 1 to No. 7 battery are shown here. It needs to click on next page bottom to see more results.
Figure 10 shows the designed and actual interface of battery alarm information.
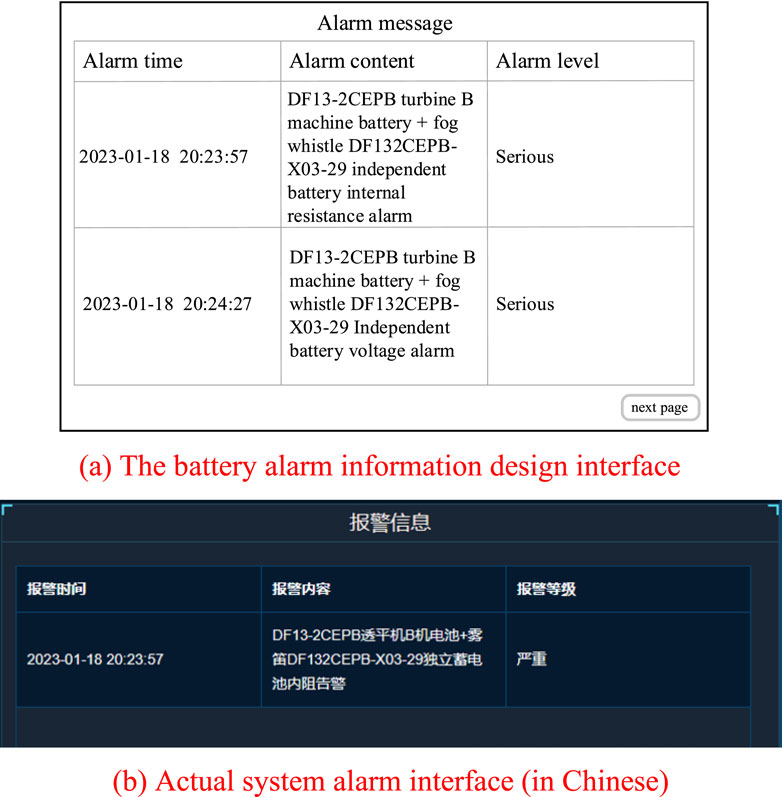
Figure 10. Battery alarm information. (A) The battery alarm information design interface. (B) Actual system alarm interface (in Chinese).
The alarm information is from an offshore oil and gas field. It shows that the internal resistance alarm, voltage alarm and alarm level of the DF13-2CEPB platform turbine B have serious problems. The operation and maintenance personnel urgently need to address these issues.
In summary, the features of this system are the applications of the Internet of Things technology, edge computing, data-driven technology, and high-speed communication technology. The system has many advantages such as online monitoring, remote control, big data analysis, high-speed communication, and fault diagnosis. At the same time, the system implements functions such as battery ledger management, basic information display, real-time display of monitoring data, and visualization of battery alarm information. The system has been applied to the battery monitoring of a DC power supply system in a 110 kV substation. It has proven to provide convenient services to the operation and maintenance personnel and ensures the reliability of the DC power supply system.
5 Conclusion
With the advancement of the digital and intelligent construction of power grid, the management and maintenance of substation batteries is trending towards the use of remote-control monitoring systems. At present, remote control and communication technologies are developing rapidly, and battery management and maintenance urgently needs to improve in efficiency, with reduced costs. This paper summarizes and analyzes the relevant Internet of Things architecture, data transmission, edge computing, and cloud computing technologies. Conclusions are drawn as follows:
(1) An online battery monitoring management system based on the “cloud-network-edge-end” Internet of Things architecture is proposed. The designed system has functions including ledger management, battery basic information display, real-time display of battery monitoring data, and visualization of battery alarm information.
(2) The module functions of the system are verified by practical application. It establishes online monitoring and management for batteries, improving the maintenance management optimization and fault warning for the DC power supply system. It provides a guarantee for the stable operation of the DC system in the substation.
(3) Battery monitoring and management is a comprehensive concept. There are still many challenges to overcome in online monitoring. High-quality data need to be transmitted to ensure the accuracy and reliability. The interfaces and data formats also need to be standardized to break down data barriers. Artificial intelligence technology and big data analysis may be good choices to improve the fault diagnosis functions, life predictions, state evaluations, and maintenance decisions. Important premise is to collect sufficient and comprehensive data.
(4) Based on practical operating experience, artificial intelligence and big data analytics are planned to use in data cleaning, trending analysis and association analysis. Data cleaning is used to improve data quality by removing unexpected noises. Trending and association analysis are expected to find issues with higher sensitivity. This will help to improve the accuracy of diagnosis, assessment, and prediction.
Data availability statement
The original contributions presented in the study are included in the article/supplementary material, further inquiries can be directed to the corresponding author.
Author contributions
KC: Writing–original draft, Writing–review and editing. LL: Writing–original draft, Writing–review and editing. WL: Writing–original draft, Writing–review and editing. PL: Writing–original draft, Writing–review and editing. LZ: Writing–original draft, Writing–review and editing.
Funding
The author(s) declare that financial support was received for the research, authorship, and/or publication of this article. This work is supported by the Science and Technology Project of State Grid Sichuan Electric Power Company (No. 521997220024).
Conflict of interest
The authors declare that the research was conducted in the absence of any commercial or financial relationships that could be construed as a potential conflict of interest.
The authors declare that this study received funding from State Grid Sichuan Electric Power Company. The funder had the following involvement in the study: study design, analysis of data, the writing of this article, and the decision to submit it for publication.
Publisher’s note
All claims expressed in this article are solely those of the authors and do not necessarily represent those of their affiliated organizations, or those of the publisher, the editors and the reviewers. Any product that may be evaluated in this article, or claim that may be made by its manufacturer, is not guaranteed or endorsed by the publisher.
References
Abd Wahab, M. H., Anuar, N. I., Ambar, R., Baharum, A., Shanta, S., Sulaiman, M. S., et al. (2018). IoT-based battery monitoring system for electric vehicle. Int. J. Eng. and Technol. (IJET). 7 (4.31), 505–510. doi:10.14419/ijet.v7i4.31.25472
Chen, H., Qin, W., and Wang, L. (2022). Task partitioning and offloading in IoT cloud-edge collaborative computing framework: a survey. J. Cloud Comput. 11 (1), 86. doi:10.1186/s13677-022-00365-8
Deng, Z., Hu, X., Lin, X., Che, Y., Xu, L., and Guo, W. (2020). Data-driven state of charge estimation for lithium-ion battery packs based on Gaussian process regression. Energy 205, 118000. doi:10.1016/j.energy.2020.118000
Friansa, K., Haq, I. N., Santi, B. M., Kurniadi, D., Leksono, E., and Yuliarto, B. (2017). Development of battery monitoring system in smart microgrid based on internet of things (IoT). Procedia Eng. 170, 482–487. doi:10.1016/j.proeng.2017.03.077
Gotz, J. D., dos Reis Mendes, J. P., Galvão, J. R., Viana, E. R., Corrêa, F. C., and Borsato, M. (2023). “An online application of edge-cloud computing for lithium-ion battery with SOC estimation,” in 2023 IEEE Vehicle Power and Propulsion Conference (VPPC), 1–6.
Han, P. (2022). Network information security data protection based on data encryption technology. Wirel. Personal. Commun. 126 (3), 2719–2729. doi:10.1007/s11277-022-09838-0
Hu, X., Feng, F., Liu, K., Zhang, L., Xie, J., and Liu, B. (2019). State estimation for advanced battery management: key challenges and future trends. Renew. Sustain. Energy Rev. 114, 109334. doi:10.1016/j.rser.2019.109334
Hu, X., Xu, L., Lin, X., and Pecht, M. (2020). Battery lifetime prognostics. Joule 4 (2), 310–346. doi:10.1016/j.joule.2019.11.018
Islam, M. M., Hasan, M. K., Islam, S., Balfaqih, M., Alzahrani, A. I., Alalwan, N., et al. (2024). Enabling pandemic-resilient healthcare: narrowband Internet of Things and edge intelligence for real-time monitoring. CAAI Trans. Intell. Technol., 1–18. doi:10.1049/cit2.12314
Itiki, R., Di Santo, S. G., Itiki, C., Manjrekar, M., and Chowdhury, B. H. (2019). A comprehensive review and proposed architecture for offshore power system. Int. J. Electr. Power and Energy Syst. 111, 79–92. doi:10.1016/j.ijepes.2019.04.008
Ju, Q., Sun, G., Li, H., and Zhang, Y. (2019). Collaborative in-network processing for internet of battery-less things. IEEE Internet Things J. 6 (3), 5184–5195. doi:10.1109/JIOT.2019.2899022
Kim, T., Qiao, W., and Qu, L. (2012). Power electronics-enabled self-X multicell batteries: a design toward smart batteries. IEEE Trans. Power Electron. 27 (11), 4723–4733. doi:10.1109/TPEL.2012.2183618
Kim, T., Wang, Y., Fang, H., Sahinoglu, Z., Wada, T., Hara, S., et al. (2015). Model-based condition monitoring for lithium-ion batteries. J. Power Sources 295, 16–27. doi:10.1016/j.jpowsour.2015.03.184
Li, P. Y., Pan, Y. T., and Ma, Y. Q. (2013). Remote monitoring technologies of performances of battery charger in digitalized transformer substation. Adv. Mater. Res. 662, 731–735. doi:10.4028/www.scientific.net/amr.662.731
Liu, W., Placke, T., and Chau, K. (2022). Overview of batteries and battery management for electric vehicles. Energy Rep. 8, 4058–4084. doi:10.1016/j.egyr.2022.03.016
Oliveira, E., Rocha, A. R., Mattsos, M., and Delicato, F. C. (2022). Latency and energy-awareness in data stream processing for edge based IoT systems. J. Grid Comput. 20 (3), 27. doi:10.1007/s10723-022-09611-4
Pradhan, S. K., and Chakraborty, B. (2022). Battery management strategies: an essential review for battery state of health monitoring techniques. J. energy storage 51, 104427. doi:10.1016/j.est.2022.104427
Qiu, Q., Wang, D., Du, X., Yu, S., Liu, S., and Zhao, B. (2022). Security standards and measures for massive IoT in the 5G era. Mob. Netw. Appl. 27 (1), 392–403. doi:10.1007/s11036-021-01841-2
Reddy, M. I., Rao, P. V., Kumar, T. S., and K, S. R. (2024). Encryption with access policy and cloud data selection for secure and energy-efficient cloud computing. Multimedia Tools Appl. 83 (6), 15649–15675. doi:10.1007/s11042-023-16082-6
Samanta, A., Chowdhuri, S., and Williamson, S. (2021). Machine learning-based data-driven fault detection/diagnosis of lithium-ion battery: a critical review. Electronics 10 (11), 1309. doi:10.3390/electronics10111309
Semeraro, C., Caggiano, M., Olabi, A. G., and Dassisti, M. (2022). Battery monitoring and prognostics optimization techniques: challenges and opportunities. Energy 255, 124538. doi:10.1016/j.energy.2022.124538
Sodhro, A. H., Pirbhulal, S., and De Albuquerque, V. H. (2019). Artificial intelligence-driven mechanism for edge computing-based industrial applications. IEEE Trans. Industrial Inf. 15 (7), 4235–4243. doi:10.1109/TII.2019.2902878
Thomas, J., Crasta, H., Kausthubha, K., and Rao, A. (2021). Battery monitoring system using machine learning. J. Energy Storage 40, 102741. doi:10.1016/j.est.2021.102741
Tiago, M. (2020). From pre-quantum to post-quantum IoT security: a survey on quantum-resistant cryptosystems for the internet of things. IEEE Internet Things J. 7 (7), 6457–6480. doi:10.1109/JIOT.2019.2958788
Waag, W., Käbitz, S., and Sauer, D. U. (2013). Experimental investigation of the lithium-ion battery impedance characteristic at various conditions and aging states and its influence on the application. Appl. energy 102, 885–897. doi:10.1016/j.apenergy.2012.09.030
Wang, Y., Kim, S., Chen, Y., Zhang, H., and Park, S. J. (2022). An SMPS-based lithium-ion battery test system for internal resistance measurement. IEEE Trans. Transp. Electrification 9 (1), 934–944. doi:10.1109/TTE.2022.3178981
Wu, J., Liu, X., Meng, J., Lin, M., Hernandez, P. J., and Lee, Y. (2021). Cloud-to-edge based state of health estimation method for Lithium-ion battery in distributed energy storage system. J. Energy Storage 47, 102974. doi:10.1016/j.est.2021.102974
Xiong, R., Li, L., and Tian, J. (2018). Towards a smarter battery management system: a critical review on battery state of health monitoring methods. J. Power Sources 405, 18–29. doi:10.1016/j.jpowsour.2018.10.019
Zhang, R., and Qian, F. (2023). Design of lithium battery monitoring system based on GPRS short message communication. E3S Web Conf. 406, 02044. doi:10.1051/e3sconf/202340602044
Zhou, S., Li, D. J., and Han, Y. (2017). Advances in battery manufacturing, service, and management systems (Wiley). doi:10.1002/9781119060741
Keywords: battery, online monitoring, internet of things, cloud-network-edge-end, fault diagnosis
Citation: Chen K, Luo L, Lei W, Lv P and Zhang L (2024) Design and implementation of online battery monitoring and management system based on the internet of things. Front. Energy Res. 12:1454398. doi: 10.3389/fenrg.2024.1454398
Received: 25 June 2024; Accepted: 23 August 2024;
Published: 04 September 2024.
Edited by:
Jinpeng Tian, Hong Kong Polytechnic University, Hong Kong SAR, ChinaReviewed by:
Jianfeng Liang, Xi’an University of Technology, ChinaXutao Han, Xi’an Jiaotong University, China
Anju S. Pillai, Amrita Vishwa Vidyapeetham University, India
Copyright © 2024 Chen, Luo, Lei, Lv and Zhang. This is an open-access article distributed under the terms of the Creative Commons Attribution License (CC BY). The use, distribution or reproduction in other forums is permitted, provided the original author(s) and the copyright owner(s) are credited and that the original publication in this journal is cited, in accordance with accepted academic practice. No use, distribution or reproduction is permitted which does not comply with these terms.
*Correspondence: Liang Zhang, bGlhbmd6aGFuZ3N3cHVAZ21haWwuY29t