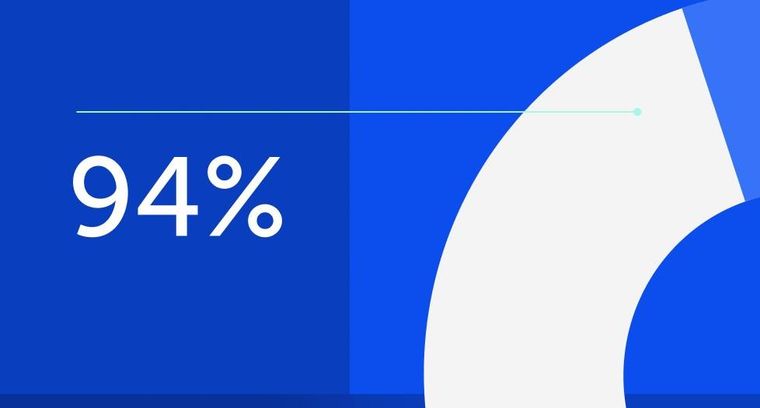
94% of researchers rate our articles as excellent or good
Learn more about the work of our research integrity team to safeguard the quality of each article we publish.
Find out more
ORIGINAL RESEARCH article
Front. Energy Res., 05 June 2024
Sec. Sustainable Energy Systems
Volume 12 - 2024 | https://doi.org/10.3389/fenrg.2024.1415901
This article is part of the Research TopicUrban Multi-energy System Networks with High Proportion of Renewable EnergyView all 7 articles
Environmental hazards linked with scrap tires have been a great concern for the Saudi government. The Kingdom of Saudi Arabia has a Vision 2030 project with an aim to produce 50% of its energy through renewable energy resources. The tire market in the country reached 22.2 million units in 2022 and is expected to increase up to 24.9 million in 2028 with a growth rate of 2.11%. This study used a vacuum pyrolyzer for transforming scrap tires into tire-derived oil (TDO), along with other products such as synthesis gas (syngas) and carbon black. It provides a feasible way of transforming scrap tires into synthetic fuel via vacuum pyrolysis (a thermochemical approach). Vacuum pyrolysis of scrap tires at temperature 350–400oC yields 45%–55% derived oil, 10%–15% steel wires, 30%–35% carbon black, and 10%–15% non-condensable gases. The heating value of the obtained tire-derived oil is 32–37 MJ/kg, which is somehow less than that of diesel, which has an energy value of 44–46 MJ/kg. Such products are expected to be obtained after the successful adaptation of advanced techniques such as thermochemical approaches and can successfully be used as an alternative to fossil fuels. Based on the scrap tire produced in the country, if Saudi Arabia can process 22.2 million units of tires (trucks and passenger cars) annually through vacuum pyrolysis, it can earn approximately $47.40 million annually (or $2.14 per tire) through tire pyrolysis. Utilization of carbon black (recovered from scrap tire pyrolysis) in manufacturing tires can save approximately 2.5 tons of CO2 production compared to per ton production of new (virgin) carbon black. This study suggested pyrolysis to be a viable recycling and waste tire management technique, and it can be an independent profitable operation in Saudi Arabia and helps in meeting the Saudi Vision 2030.
Energy is the foremost necessity of the 21st century as it is essential for improving any country’s standards by discovering and managing the increase in energy demands. Renewable and alternative energy assets are gaining significant attention in the world as a source of oxygenated fuels due to economic and environmental concern, as well as their supportive behavior toward waste-to-energy conversion (Jahirul et al., 2014; Wang et al., 2016). Disposing waste in landfills is costly and deteriorates the environment. Saudi Arabia has a population of around 29 million that annually generates nearly 53 million tons of total waste, with an estimated rate of approximately 1.5–1.8 kg/person/day. Various techniques have been adopted worldwide to utilize the produced waste for energy generation either through biochemical, physiochemical, and thermochemical processes. The increase in living standards has increased the number of vehicles, which ultimately led to a higher production of scrap tires. As these scrap tires are very difficult to decompose, they are a severe threat to human and environmental health. The scrap tires promote pest and insect invasion, and they are a cause of high fire that results in an emittance of harmful constituents, leading to air, land, and underground water contamination (Daniel Martinez et al., 2013). Tires are manufactured using a non-biodegradable material such as styrene butadiene rubber, which raises concern in developed nations regarding environmental deterioration.
The structure of the tire is very complicated, due to which its recycling is challenging. The tires comprise rubber, carbon black, steel, and textile overlay (47, 22, 25, and 5.5%, respectively) (Martínez et al., 2013). From the entire global transportation system, approximately 1.5 billion automobile scrap tires have been produced on an annual basis (Khan et al., 2021). It has been predicted that every individual in a developed nation has discarded one automobile tire annually, due to which the scrap tire waste increased to 2,500 million units by 2022 (Martínez, 2021). Similarly, an upswing in the lifestyle of a Saudi inhabitant contributes to an increase in the automobile industry of the country, which hikes the tire market as well. The tire market in the country has increased by 11% from 2016 to 2021 and produced 21.8 million units on an annual basis, and the tire production rate is expected to go higher up to 24.7 million units by 2027 (IMARC, 2022; Smith, 2017). Out of this huge scrap tire generation, only 20% of the tires undergo recycling, whereas the remaining 80% are discarded at the disposal sites (Parthasarathy et al., 2016). However, approximately up to 18% of the initial new tire weight is decreased when it becomes scrap (Rubber Manufacturers Association, 2009). Sorting out waste management and its treatment is a massive task for the government sector with every passing day as the target has been set to treat 106 million tons of waste by 2035 (Salman, 2020). The composition of passenger and truck tires is shown in Table 1.
Table 1. Composition of tires (Office of Permitting, 1999).
Based on the tire composition, the waste tire-handling techniques comprised utilization in kilns, energy generation plants, co-incineration with other waste materials, foundation making, and road development. Most of the industrial processes that involve combustion are dependent on non-renewable energy sources such as coal. The oil obtained from the pyrolysis of scrap tires has a higher heating value of 37–45 MJ/kg, which is significantly higher than that of local available coal; hence, the obtained oil can easily be utilized in industrial and residential power plants (Fiksel et al., 2011). Waste tires can directly be used in combustion, but it causes environmental pollution. To effectively convert scrap tires to energy, various investigations have been conducted to date that comprised volarization/gasification, pyrolysis, and hydrothermal liquification (Dai et al., 2001). However, the interest is on treating the scrap tire through pyrolysis due to the number of products derived from the process. Pyrolysis processes can be used to produce biofuels from various wastes such as biomass, coal, plastic, and scrap tires. Pyrolysis is a mechanism for breaking long-chain hydrocarbons into small chains in the absence of oxygen and under high temperature to obtain bio-oil, char, and combustible gase mixture, along with steel recovery (Uddin et al., 2018). The chemical composition and properties of the other materials that are commonly considered for pyrolysis, along with scrap tires, are shown in Figure 1. The difference in the composition of these materials is based on the moisture content in the feed material, carbon, volatile, and ash contents, whereas the handling procedures for the scrap tires are shown in Figure 2.
Figure 1. Ultimate and proximate analyses compared to other wastes used for pyrolysis (Menares et al., 2020).
During the pyrolysis process, cracking of tires at a temperature between 300 and 700°C produces oil that can be directly utilized in an internal combustion engine or for heating purposes in the industrial sector with minimum exhaust pollution (Ilkılıç and Aydın, 2011). Due to the absence of a market representing tire-derived oil (TDO), it can be directly used in internal combustion engines after upgradation. Various researchers concluded that pyrolysis oil provides a feasible solution as an alternative to diesel oil due to its higher quality and similar energy values (Aydin and Ilkiliç, 2012a). The oil produced from pyrolysis comprised hydrocarbons and olefins, along with carbon black and activated carbons. Operating conditions such as reactor type, temperature, and feed stock type directly affect the char/carbon black physical properties (Zhang et al., 2021). The tire-derived oil ranges between 35% and 60%, char as carbon black ranges between 30% and 50%, steel wire ranges between 10% and 15%, and non-condensable gases ranges between 5% and 15%, depending on the operating temperature of the pyrolyzer (Khan et al., 2016). Zhang et al. investigated vacuum pyrolysis of tire granules in the presence of Na2CO3 and NaOH at a temperature between 450 and 600oC. The maximum oil percentage of 50% by wt, 36.6% char yield, and 13.7% gas yield was obtained at a temperature of 480oC, concluding that the addition of NaOH facilitates the pyrolysis process (Zhang et al., 2008). Roy et al. carried out passenger car tire vacuum pyrolysis at a pressure lower than 10 kPa between a temperature of 480 and 550oC. The processes yielded 56% oil by wt, 10% gas, and 33% carbon black (Roy et al., 1999). Berrueco et al. used a fixed-bed pyrolyzer to process scrap tires in a 4-h operation using N2 as a carrier flow at a temperature of 400°C–700°C with a heating rate of 12 °C/min. An increase in gas by 2 wt% and liquid by 13 wt% was observed as the temperature increased from 400°C to 700°C (Berrueco et al., 2005). Aydin et al. concluded approximate results yielding oil by 40 wt% from scrap tire pyrolysis conducted at 500°C under continuous nitrogen flow. The investigation also concluded that an increase in temperature causes a decrease in solid production, along with an increase in gas yield. Meanwhile, a negligible effect on product yield was observed due to inert gas flow during the processes (Aydın and İlkılıç, 2012b). Similarly, pyrolysis of a 750-g truck tire between a temperature of 375°C and 575°C reported an increase in oil yield from 47 to 55 wt%. Smaller particle size and lower residence time were optimum for increasing the liquid yield (Islam et al., 2011).
This study investigated a way, keeping in view of the Saudi Vision, of producing 50% of its energy through renewable/waste resources. This study involves preparing a technoeconomic feasible approach of transforming Saudi Arabian scrap tires (truck and passenger cars) into TDO and carbon black and synthesis gas (syngas) via vacuum pyrolysis in a moving bed batch-type reactor. Currently, Saudi Arabia exports approximately 65% of its total waste tire, while the rest is dumped at landfill sites. The 35% dump share contributes toward serious environmental threats in the country. Keeping in view of Saudi Vision 2030, adaptation of this scrap tire conversion technique can generate energy through waste, save energy, and decrease products cost through sustainable recycling, which will create jobs in the country. Hence, the assessment of scrap tire pyrolysis can be useful for the commercialization of thermochemical techniques, as well as for calculating the production cost of biofuels and chemicals in Saudi Arabia.
Waste can be converted into sustainable fuel via biochemical, physiochemical, and thermochemical processes, as shown in Figure 3. The solid fuels can easily be transformed into bio-oil (diesel equivalent depending on the material to be pyrolyzed) and synthesis gas through thermochemical approaches (Fytili and Zabaniotou, 2008). The biochemical and physiochemical processes have several challenges, like material preparation, optimum temperature, pH ranges, and other operational parameters, for which skilled labor and challenging processes are required for the successful operation of the unit. On the other hand, the pyrolysis technique is a thermochemical process that ensures the system performance quite efficiently and solves the problems of waste handling by energy generation in a reliable manner. The benefit of this technique is the prospect of changing the solid fuel into a bio-oil and clean synthetic gas that retains 70%–80% of the chemical energy (Higman and Van der Burgt, 2008).
Pyrolysis is a thermochemical approach that breaks the material when subjected to high temperatures between 300 and 700oC in the absence of oxygen or under the flow of nitrogen gas as a fluidizing medium to produce volatiles in the form of non-condensable and condensable hydrocarbons (Pradhan and Singh, 2011). Pyrolysis is an attractive approach of obtaining valuable products from waste tire processing without causing any serious degradation to the environment. The obtained products such as syngas and tire-derived oil and solids can be easily optimized based on their usage. Efficient processing of tires through this technique is greatly affected by the temperature. Lower temperature produces higher oil yield, whereas higher temperature favors higher syngas production (Altayeb, 2015). The oil obtained from tire pyrolysis is brown–black and has odor due to the sulfur content in the tire. The tire-derived oil is processed to minimize the sulfur contents and remove moisture via distillation processes. Similarly, pyrolytic reactor conditions like thermal profile, residence time, and reactor under pressure directly affect the oil composition. Previous tire pyrolysis study results are shown in Table 2.
The syngas that is obtained from the pyrolysis process is composed of carbon monoxide, methane, and hydrogen, having a calorific value os 8–12 MJ/Nm3. The synthesis gas obtained through vapor condensation comprised paraffins, olefins, and aromatic hydrocarbons that can be used directly to power the internal combustion engines after upgradation. The synthesis gas obtained from the pyrolytic process comprised C1–C4 hydrocarbons with higher energy values and can easily be served as a fuel without any intense value addition. The tire pyrolytic char is in the form of carbon black that can be reused in the production of new tires and road making, depending on the chemical composition (structure, size, and surface area) (Rowhani A. and Rainey T., 2016). The product yield obtained from the tire pyrolysis process is shown in Figure 4.
The pyrolyzer used for this study is batch-type and had a capacity of processing 5 tons of input feed material (scrap tires) per day and comprised pre-processing, processing, and post-processing units. The pre-processing unit comprised a shredder for tire size reduction, which increases heat transfer during the pyrolysis process. After size reduction, various other tire components such as beads, steel wires, and fabrics are removed. The size of the waste tire should be reduced to 1–10 mm because the particle size has a significant effect on the pyrolysis product quality. The first stage of the shredder decreases the size up to 2 inches. Then, the granulator further decreases the size of the tire up to 10 mm or less, and steel and fiber are separated from the rubber using a magnetic effect or belt conveyors (Reschner, 2008). The processing unit comprised a vacuum-based rotary type pyrolysis reactor, which is equipped with a continuous feeding system, stirrer, and gas outlet system, along with a carbon black removal system. This reactor is capable of efficiently converting the scrap tires into TDO, gas, and carbon black. The proposed schematics of the pyrolysis system are shown in Figure 5 (Papuga et al., 2023).
Figure 5. Block diagram of the fixed-bed pyrolysis reactor: (A) cylinder with nitrogen gas, (B) gas mass flow meter, (C) pyrolysis reactor, (D) thermal insulation, (E) steam condensation system, (F) separation system vessel for the condensate, (G) discharge of non-condensable gases in the gas washing system, and (H) control box (I) PC (a/) reducing valve, and (c/) electric heater connection wiring.
In this processing unit (reactor), the tires are heated in the absence of oxygen by the application of an indirect heat source. The continuous flow of inert nitrogen gas into the pyrolysis reactor is intended to expel oxygen gas in the reactor and oxygen entering through the condenser pipe during the pyrolysis process. The lesser the oxygen gas in the reactor, the higher the quality of the pyrolysis product. The presence of oxygen in the reactor during the process adds water quantity in the tire derived oil. The post-processing unit comprised a separation system for the condensate and a gas washing system, along with gas–carbon black separation and tire-derived oil collection after condensation. During the process, small amounts of nitrogen are blown to carry out the pyrolysis processes efficiently. The products such as oil are collected by the condensing process, whereas the char/carbon black and synthetic gas are collected using the cyclone separator. The oil yield obtained from the reactor is directly dependent on the condensation process. The condensation systems should be enough to recover maximum condensate from the flowing gas. The product yield is calculated by using Eqs 1, 2, 3 (Khalaf et al., 2021) (Do et al., 2014).
The main factor that is considered for checking the suitability of the pyrolysis process is the volatile matter (VM) contents and moisture contents in the feed material. Higher VM (66.31%) and lower moisture (2.3%) in the scrap tires yield high quality and quantity of tire-derived pyrolysis oil, and hence, this feed stock is proven to be suitable for its transformation through pyrolysis processes.
The type of rubber used for tire manufacturing is described by the thermal degradation curve. The peak temperatures are used for characterizing the derivative thermogravimetric (DTG) curves of the scrap tire used in pyrolysis. When the tire is heated at 10 °C/min, the peak temperature for natural rubber (NR) ranges between 360 and 390oC, whereas the peak temperature for synthetic rubber is 420–480oC (styrene–butadiene rubber, 430–458oC, and butadiene rubber, 468–480oC) (Seidelt et al., 2006). During the pyrolysis processes, the maximum material degradation/transformation occurs between 280 and 440oC; at this temperature range, approximately 70% of the feed material weight is lost. This temperature range is referred to as the active pyrolysis stage, whereas the remaining feed material degradation (which is carried out slowly compared to the active stage) is completed in the passive pyrolysis stage. The thermogravimetric (TG) and DTG analysis showed that a temperature of 350–450oC is most optimum for scrap tire pyrolysis. The TG/DTG curve for scrap tires is shown in Figure 6.
Figure 6. Scrap tire thermogravimetric (TG) and derivative thermogravimetric (DTG) curves (Hossain et al., 2023).
For technoeconomic analysis, the previously reported physical properties of the obtained scrap tire pyrolysis oil are considered, and its comparison with diesel fuel is shown in Table 3, whereas the output products with carbon conversion efficiency above 80% are shown in Figure 7.
For the adaptation of a tire pyrolysis technique at a commercial level, a viable analysis is needed based on technical and economic aspects relevant to each other. To determine the effective feasibility of the pyrolysis process via the product cost of production and profit earning, energy balance and economic analysis need to be performed (Abdallah et al., 2020b).
To determine the product yield, some technical analyses need to be considered, comprising the suitable thermal profile range between 450 and 650oC under oxygen-free conditions. The obtained oil has significant features over unprocessed tires, which provides its higher volumetric energy density. The presence of oxygen favors oxygenated compounds that yield lower-energy value crude oil. Catalytic treatment can be deployed to reduce the oxygenated compounds in crude oil. For system optimization and economic analysis, yield assessment and conversion rate are the most significant features to be considered. The product yield can easily be altered by the pyrolyzer internal thermal profile, and it could be estimated using Eq. 4, whereas the tire conversion efficiency can be estimated by using Eq. 5.
Previous research concluded that efficient pyrolysis of 1,000-kg waste tire yields 500 kg of pyrolytic oil, 30 kg of carbon black, 100 kg of steel, and 100 kg of gases (Islam and Nahian, 2016b; Rowhani A. and Rainey T. J., 2016). However, the maximum oil product reported from tire pyrolysis was 63% (Murugan et al., 2008). It was also reported that catalytic tire pyrolysis can increase the oil product yield up to 80% (Swanson et al., 2010). The calorific value (HHV) of tire-derived oil ranged between 39 and 46 MJ/kg with a density of 840–900 kg/m3 (Pilusa et al., 2014), whereas the HHV of the syngas was calculated up to 8.9 MJ/kg (Mrad and El-Samra, 2020), while the HHV for carbon black was 29 MJ/kg (Ourak et al., 2021). Similarly, Abdullah et al. reported the pyrolysis of 5 ton scrap tires that produced 45% tire-derived oil, 34% carbon black, 11% scrap steel wires, and 10% pyro-gas (Abdallah et al., 2020c). The previously reported results are considered for calculating the feasibility of the scrap tire pyrolysis project in Saudi Arabia.
Three aspects need to be considered while carrying out the economic analysis of the tire pyrolysis project. The first parameter is the pyrolysis product market value (sold for gaining profit). Second, it recycles auto tires, one of the most abundant waste products in the world. Globally, 2.3 billion tires were produced in 2021 (Deinma et al., 2020). The third parameter that needs to be considered is energy efficiency. Most pyrolysis plants are self-sufficient in energy use. Byproducts of the pyrolysis process are reused to fire furnaces and generate electricity. It abided by the law of the conservation of energy, which states that the input energy is equal to the output energy. Previously reported higher heating values are used for the energy balance calculations. The energy balance for 1 ton of tire pyrolysis is shown in Table 4.
The energy required for the pyrolysis process of 5 tons of scrap tire is calculated in Table 5.
The economic analysis of this tire pyrolysis process is based on the annual cost method. This method comprised fixed and variable costs for the complete pyrolysis process.
Several assumptions need to be considered while calculating the annual fixed cost of the pyrolysis unit. The following assumptions are shown in Table 6.
For calculating the initial cost of the pyrolysis unit, a capacity of 5 tons/day/pyrolysis plant is considered. The initial cost comprised equipment, mounting, accessories, and civil work, as shown in Table 7. The complete calculations are performed by Lefilter Corp., Ltd.
This includes parametric costs that are responsible for the pyrolysis plant to be in operation. Variable costs include repair and maintenance cost, labor cost, scrap tire purchasing, and transportation cost and electricity cost for the pyrolysis unit. The variable cost of the pyrolysis unit with respect to various assumptions is shown in Table 8. Table 9 presents the fixed and variable costs per annum and per ton of biomass used by the pyrolysis unit.
The revenue generated from scrap tire pyrolysis is determined based on the study by Abdullah et al. The investigation concluded that after efficient tire pyrolysis, the product comprised 45% tire-derived crude oil, 35% carbon black, 10% non-condensable gases, and 10% scrap steel wires (Abdallah et al., 2020c). This means that on every 1-ton scrap tire pyrolysis, the obtained product weighed 0.450, 0.350, 0.10, and 0.10 tons (TDO, carbon black, syngas, and scrap steel, respectively). The selling price in the international market for these pyrolysis products is $400 per ton of tire-derived oil, $50 per ton of carbon black, and $180 per ton of scrap steel wires. However, pyro-gas (non-condensable gas) can be used in the system for meeting the extra heating requirements during the pyrolysis process. The total revenue generation per batch of 1-ton scrap pyrolysis is shown in Table 10.
Table 10 shows that by adopting the scrap tire pyrolysis technique, an income of $1,190.0 per 5-ton batch processing would be obtained.
The daily expenditures for the processing of a 5-ton tire pyrolysis plant are shown in Table 11.
The daily profit ratio for processing 1-ton scrap tire pyrolysis is calculated as shown below.
Daily expenditures for processing 1-ton tire pyrolysis = $166.93.
Daily revenue generated from 1-ton tire pyrolysis = $238.0.
Daily profit gained per ton = $71.07.
Annually profit (after processing 22.2 million tires) = $47.40 million.
Currently, the total available scrap tire in Saudi Arabia on an annual basis is approximately 22.2 million units (Market Research Report, 2023). If the average weight of the scrap tire used for this investigation is assumed to be 27.25 kg, then, the total scrap tire waste generated annually in Saudi Arabia is 0.67 million tons. In other words, it was estimated that the cost for processing each tire is approximately $4.49, whereas the income generation from pyrolysis of each tire is approximately $6.63. The net profit gained from each tire pyrolysis is approximately $2.14. If the pyrolysis industry is set up in Saudi Arabia, the adopter can earn approximately up to $47.40 million annually by managing waste tires, thus reducing the landfilling dumping site cost and slowing down the process of environmental degradation, which is due to direct combustion.
Break-even analysis reveals the point at which enough units have been sold out to cover all the costs. The break-even point for the scrap tire pyrolysis plant is calculated to be 0.71 years or 259 days of operation (Figure 8). The break-even point (BEP = X) in terms of cost and revenue was found as follows:
where X is the operating time in years and TFC is the total fixed cost invested in the beginning of the project.
V is the total cost (fixed + variable) per annum of the pyrolysis unit.
p is the gross revenue generated per year through the pyrolysis unit.
To calculate the project profitability, the net present value (NPV) was calculated using the cash flow method. A positive NPV reflects the success story of the project, whereas a negative NPV corresponds to project failure. For the scrap tire pyrolysis project, the initial cost at the start for purchasing the equipment with a capacity of 5 tons was $96,000. The annual cash flow of this machine was determined to be $95,964. The scrap value of the machine at the end of the 10th year (final year life of the equipment) of the equipment life was 10% of the initial invested value ($96,000). Similarly, the return rate (discount rate) was 10%. Considering all these factors, the NPV of this project appears positive (+$497,358.62), with a total return of (+inflow) $969,240. This NPV represents that the assumptions made for determining the gross income and cost stand valid. Similarly, the internal rate of return (IRR) of the project is calculated as the rate at which the NPV of the project becomes zero. The IRR for this project was found to be 99.87%.
To recover energy from waste products, waste tires processed through the pyrolysis technique show high potential to produce byproducts that can serve as an alternative. The internal thermal profile of the reactor significantly affects the physical and chemical properties of the products, and the solid, liquid, and gaseous phase yields are dependent on the process temperature. In addition to that, the feed stock size, conversion rate, composition of the feed stock, process time, catalyst, and medium are other significant parameters that directly alter the pyrolysis yield and heating values.
The products obtained from scrap tire pyrolysis yield approximately 41% pyrolytic oil, 38% carbon black, 12% gas, and 8.9% steel scrap. The pyro-oil obtained from the tire pyrolysis process has higher heating values of 46 MJ/kg that burn readily as an alternative in diesel engines and furnaces. The TDO can be converted into light olefins and aromatics that can support the petrochemical industry. Similarly, the gases obtained can be used as fuel for meeting the heating requirements of the industry even for the pyrolysis process. The carbon black was composed of 90% carbon, which has higher quality than required by the steel and ink industries, and the pyrolytic oil was composed of 66% gasoline and 33% other oils, with sufficient quality to be used as an additive for fuels or as fuel for engines and furnaces. The obtained carbon black can even be used for pollutant removal, as well as for manufacturing new tires from the recovered carbon black, thus ultimately reducing 2.5 tons of CO2 that can be produced more on manufacturing new carbon black. Thus, the environmental benefits of the pyrolysis process of scrap tires include avoiding the disposal of tires directly into landfills and wasteland, thus avoiding the contamination of soil, water, and air due to the emission of chemical contaminants formed during the decomposition of the scrap tires. In addition, there is no need for the extraction of raw materials to produce steel, fuel, and carbon black produced in the scrap tire pyrolysis plant.
Recapitulating, recycling, or utilization of scrap tires would reduce the impact on the environment, including human and soil health. The adaptation of the pyrolysis technique would enhance the life span of landfills. In addition to that, if Saudi Arabia can adopt this technique, it will earn a net amount of $47.4 million annually through tire pyrolysis. The net profit gained from each tire pyrolysis process is approximately $2.14. This work showed that tire pyrolysis is an innovative and ecofriendly process, offering a clean production that is economically viable and can be used as a solution for the disposal of used tires in Saudi Arabia.
The raw data supporting the conclusion of this article will be made available by the authors, without undue reservation.
SA: conceptualization, formal analysis, funding acquisition, investigation, project administration, supervision, validation, visualization, and writing–review and editing. MO: investigation, methodology, validation, visualization, and writing–original draft.
The author(s) declare financial support was received for the research, authorship, and/or publication of this article. This article was made possible by the funding from Qassim University, Qassim, Saudi Arabia (Project no. QU-IF-1-3-1).
The authors acknowledge the Ministry of Education and Qassim University in Saudi Arabia. The authors also acknowledge the supervision of the Research Deanship of Qassim University.
The authors declare that the research was conducted in the absence of any commercial or financial relationships that could be construed as a potential conflict of interest.
All claims expressed in this article are solely those of the authors and do not necessarily represent those of their affiliated organizations, or those of the publisher, the editors, and the reviewers. Any product that may be evaluated in this article, or claim that may be made by its manufacturer, is not guaranteed or endorsed by the publisher.
Abdallah, R., Juaidi, A., Assad, M., Salameh, T., and Manzano-Agugliaro, F. (2020a). Energy recovery from waste tires using pyrolysis: Palestine as case of study. Energies 13, 1817–1913. doi:10.3390/en13071817
Abdallah, R., Juaidi, A., Assad, M., Salameh, T., and Manzano-Agugliaro, F. (2020b). Energy recovery from waste tires using pyrolysis: Palestine as case of study. Energies 13, 1817. doi:10.3390/en13071817
Abdallah, R., Juaidi, A., Assad, M., Salameh, T., and Manzano-Agugliaro, F. (2020c). Energy recovery from waste tires using pyrolysis: Palestine as case of study. Energies 13, 1817. doi:10.3390/en13071817
Acosta, , Tavera, C., Gauthier-Maradei, P., and Nabarlatz, D. (2015). Production of oil and char by intermediate pyrolysis of scrap tyres: influence on yield and product characteristics. Int. J. Chem. React. Eng. 13 (2), 189–200. doi:10.1515/ijcre-2014-0137
Altayeb, R. K. (2015). Liquid fuel production from pyrolysis of waste tires: process simulation, exergetic analysis, and life cycle assessment. Thesis.
Aydin, H., and Ilkiliç, C. (2012a). Optimization of fuel production from waste vehicle tires by pyrolysis and resembling to diesel fuel by various desulfurization methods. Fuel 102, 605–612. doi:10.1016/j.fuel.2012.06.067
Aydın, H., and İlkılıç, C. (2012b). Optimization of fuel production from waste vehicle tires by pyrolysis and resembling to diesel fuel by various desulfurization methods. Fuel 102, 605–612. doi:10.1016/j.fuel.2012.06.067
Berrueco, C., Esperanza, E., Mastral, F. J., Ceamanos, J., and GarcíaBacaicoa, P. (2005). Pyrolysis of waste tyres in an atmospheric static-bed batch reactor: analysis of the gases obtained. J. Anal. Appl. Pyrol. 74, 245–253. doi:10.1016/j.jaap.2004.10.007
Cunliffe, A. M., and Williams, P. T. (1998). Composition of oils derived from the batch pyrolysis of tyres. J. Anal. Appl. Pyrolysis 44, 131–152. doi:10.1016/S0165-2370(97)00085-5
Dai, X., Yin, X., Wu, C., Zhang, W., and Chen, Y. (2001). Pyrolysis of waste tires in a circulating fluidized-bed reactor. Energy 26, 385–399. doi:10.1016/s0360-5442(01)00003-2
Daniel Martinez, J., Murillo, R., Garcia, T., and Veses, A. (2013). Demonstration of the waste tire pyrolysis process on pilot scale in a continuous auger reactor. J. Hazard. Mater. 267, 637–645. doi:10.1016/j.jhazmat.2013.07.077
Deinma, T. D., Agboola, O., and Ayeni, A. O. (2020). Pyrolysis of waste tyre for high-quality fuel products. A Rev., doi:10.3934/energy.2020.5.869
Do, T. X., Lim, Y.-I., and Yeo, H. (2014). Techno-economic analysis of biooil production process from palm empty fruit bunches. Energy Convers. Manag. 80, 525–534. doi:10.1016/j.enconman.2014.01.024
Fiksel, J., Bakshi, B. R., Baral, A., Guerra, E., and DeQuervain, B. (2011). Comparative life cycle assessment of beneficial applications for scrap tires. Clean. Technol. Environ. Policy 13, 19–35. doi:10.1007/s10098-010-0289-1
Fytili, D., and Zabaniotou, A. (2008). Utilization of sewage sludge in EU application of old and new methods: a review. Renew. Sust. Energy Rev. 12, 116–140. doi:10.1016/j.rser.2006.05.014
Haseeb, Y., Yew, H. T., Muhammad, A. J., and Gulzar, M. (2021). Potential of tire pyrolysis oil as an alternate fuel for diesel engines: a review. J. Energy Inst. 96, 205–221. doi:10.1016/j.joei.2021.03.002
Higman, C., and Van der Burgt, M. (2008). Gasification. Amsterdam, Netherlands: GPP-Elsevier. ISBN-13: 978-0-7506-8528-3.
Hossain, M. S., Islam, M. R., Rahman, M. S., Kader, M. A., and Haniu, H. (2017). Biofuel from Co-pyrolysis of solid tire waste and rice husk. Energy Proc. 110, 453–458. doi:10.1016/j.egypro.2017.03.168
Hossain, M. S., Shozib, I. A., Das., B. K., Hossain., M. S., Das., A., Islam, M. R., et al. (2023). Characterization, performance assessment, techno-economic potential, and process optimization of scrap tire pyrolysis in Bangladesh. J. Clean. Prod. 421, 138522. doi:10.1016/j.jclepro.2023.138522
Ilkılıç, C., and Aydın, H. (2011). Fuel production from waste vehicle tires by catalytic pyrolysis and its application in a diesel engine. Fuel Process. Technol. 92, 1129–1135. doi:10.1016/j.fuproc.2011.01.009
IMARC 2022 Saudi Arabia tire market: industry trends, share, size, growth, opportunity and forecast 2022-2027. Available at: https://www.imarcgroup.com/saudi-arabia-tire-market.11-10-2022.
Islam, M. N., and Nahian, M. R. (2016a). Improvement of waste tire pyrolysis oil and performance test with diesel in CI engine. J. Renew. Energy 2016, 1–8. doi:10.1155/2016/5137247
Islam, M. N., and Nahian, M. R. (2016b). Improvement of waste tire pyrolysis oil and performance test with diesel in CI engine. J. Renew. Energy 2016, 1–8. doi:10.1155/2016/5137247
Islam, M. R., Haniu, H., and Beg, M. R. A. (2008). Liquid fuels and chemicals from pyrolysis of motorcycle tire waste: product yields, compositions and related properties. Fuel 87, 3112–3122. doi:10.1016/j.fuel.2008.04.036
Islam, M. R., Joardder, M. U. H., Kader, M. A., and Sarker, M. R. I. (2011). “Valorization of solid tire wastes available in Bangladesh by thermal treatment,” in Presented at the 2nd International Conference On Solid Waste Management in Developing Countries, Khulna, Bangladesh, February 2011.
Jahirul, M. I., Koh, W., Brown, R. J., Senadeera, W., Hara, I., and Moghaddam, L. (2014). Biodiesel production from non-edible beauty leaf (Calophyllum inophyllum) oil: process optimization using response surface methodology (RSM). Energies 7, 5317–5331. doi:10.3390/en7085317
Juma, , et al. (2006). Pyrolysis and combustion of scrap tire. Petroleum Coal 48 (1), 15–26. doi:10.1002/pat.811
Khalaf, , Abudi, Z., and Dhaher, S. (2021). Bio oil production by thermal and catalytic pyrolysis of waste tires. J. Ecol. Eng. 22 (8), 189–199. doi:10.12911/22998993/140258
Khan, M. Z. H., Ikram Hossain, M., Kumar Halder, P., Rafiul Hasan, M., and Rashid Al-Mamun, M. (2016). Fuel properties of pyrolytic tyre oil and its blends with diesel fuel e towards waste management. Int. J. Environ. Waste Manag. 18 (4), 335e348. doi:10.1504/IJEWM.2016.10002722
Khan, S. R., Masood, A., Zeeshan, M., and Qaisar, S. (2021). The influence of dual-catalyst bed system of zeolitic and metal oxide catalysts on the production of valuable hydrocarbons during co-pyrolysis of rice straw and waste tire. Biomass Convers. Biorefinery 13, 12935–12946. doi:10.1007/s13399-021-02052-1
Market Research Report (2023). Saudi Arabia tire market: industry trends, share, size, growth, opportunity and forecast 2023-2028. Market Research Report Format: Report ID: SR112023A2182.
Martínez, J. D. (2021). An overview of the end-of-life tires status in some Latin American countries: proposing pyrolysis for a circular economy. Renew. Sustain Energy Rev. 144, 111032. doi:10.1016/j.rser.2021.111032
Martínez, J. D., Puy, N., Murillo, R., García, T., Navarro, M. V., and Mastral, A. M. (2013). Waste tyre pyrolysis—a review. Renew. Sustain. Energy Rev. 23, 179–213. doi:10.1016/j.rser.2013.02.038
Menares, T., Herrera, J., Romero, R., Osorio, P., and Arteaga-Perez, L. E. (2020). Waste tires pyrolysis kinetics and reaction mechanisms explained by TGA and Py-GC/MS under kinetically-controlled regime. Waste Manag. 102, 21–29. doi:10.1016/j.wasman.2019.10.027
Mohan, R. K., Sarojini, J., Rajak, U., Verma, T. N., and Agbulut, U., (2023). Alternative fuel production from waste plastics and their usability in light duty diesel engine: combustion, energy, and environmental analysis. Energy 265, 126140. doi:10.1016/j.energy.2022.126140
Mrad, M., and El-Samra, R. (2020). Waste tire management: Lebanon case study. J. Waste Manag. Dispos. 3, 101.
Murugan, S., Ramaswamy, M. C., and Nagarajan, G. (2008). The use of tyre pyrolysis oil in diesel engines. Waste Manag. 28, 2743–2749. doi:10.1016/j.wasman.2008.03.007
Office of Permitting (1999). Waste tire recycling program, tnrcc information. Wheaton, MD, United States: Office of Permitting.
Ourak, M., Gallego, M. M., Burnens, G., Largeau, J. F., Kordoghli, S., Zagrouba, F., et al. (2021). Experimental study of pyrolytic oils from used tires: impact of secondary reactions on liquid composition. Waste Biomass Valorization 12, 4663–4678. doi:10.1007/s12649-020-01313-w
Papuga, , Djurdjevic, M., Tomović, G., and Vecchio Ciprioti, S. (2023). Pyrolysis of tyre waste in a fixed-bed reactor. Symmetry 15, 2146. doi:10.3390/sym15122146
Parthasarathy, P., Choi, H. S., Park, H. C., Hwang, J. G., Yoo, H. S., Lee, B.-K., et al. (2016). Influence of process conditions on product yield of waste tyre pyrolysis—a review. Korean J. Chem. Eng. 33, 2268–2286. doi:10.1007/s11814-016-0126-2
Pilusa, J., Shukla, M., and Muzenda, E. (2014). Economic assessment of waste tyres pyrolysis Technology: a case study for gauteng province, South Africa. Int. J. Res. Chem. Metall. Civ. Eng. 1, 41–49. doi:10.15242/IJRCMCE.E1113542
Pradhan, D., and Singh, R. K. (2011). Thermal pyrolysis of bicycle waste tyre using batch reactor. Int. J. Chem. Eng. Appl. 2, 332–336. doi:10.7763/ijcea.2011.v2.129
Razzaq, G. H. A., and Majeed, N. S. (2021). Pyrolysis of scrap tire by utilizing zeolite as catalyst. Mater. Proc. 45, 4606–4611. doi:10.1016/j.matpr.2020.12.1232
Reschner, K. (2008). Scrap tire recycling: a summary of prevalent disposal and recycling methods, 1–16.
Rowhani, A., and Rainey, T. (2016a). Scrap tyre management pathways and their use as a fuel-A review. Energies 9, 888. doi:10.3390/en9110888
Rowhani, A., and Rainey, T. J. (2016b). Scrap tyre management pathways and their use as a fuel - a review. Energies 9, 888. doi:10.3390/en9110888
Roy, C., Challa, A., and Darmstad, H. (1999). The vacuum pyrolysis of used tires. J. Anal. Appl. pyrolysis 51 (1–2), 201–221. doi:10.1016/s0165-2370(99)00017-0
Rubber Manufacturers Association (2009). Scrap tire markets in the United States. Washington, DC, United States: Rubber Manufacturers Association.
Salman, Z. (2020). Solid waste management in saudiarabia. Available at: https://www.ecomena.org/solid-waste-management-in-saudi-arabia/.
Seidelt, S., Müller-Hagedorn, M., and Bockhorn, H. (2006). Description of tire pyrolysis by thermal degradation behaviour of main components. J. Anal. Appl. Pyrolysis 75, 11–18. doi:10.1016/J.JAAP.2005.03.002
Smith, S. 2017 Saudi Arabia tire market forecast and opportunities, 2021. Jan11, 2017. Available at: https://www.prnewswire.com/news-releases/saudi-arabia-tire-market-forecast--opportunities-2021-300389463.html.
Swanson, R. M., Satrio, J. A., Brown, R. C., and Hsu, D. D. (2010). Techno-economic analysis of biomass-to-liquids production based on gasification. Energy 89, S11–S19. doi:10.1016/j.fuel.2010.07.027
Uddin, M. N., Techato, K., Taweekun, J., Rahman, M. M., Rasul, M. G., Mahlia, T. M. I., et al. (2018). An overview of recent developments in biomass pyrolysis technologies. Energies 11, 3115. doi:10.3390/en11113115
Wang, W.-C., Bai, C.-J., Lin, C.-T., and Prakash, S. (2016). Alternative fuel produced from thermal pyrolysis of waste tires and its use in a DI diesel engine. Appl. Therm. Eng. 93, 330–338. doi:10.1016/j.applthermaleng.2015.09.056
Zhang, G., Chen, F., Zhang, Y., Zhao, L., Chen, J., Cao, L., et al. (2021). Properties and utilization of waste tire pyrolysis oil: a mini review. Fuel Process Technol. 211, 106582. doi:10.1016/j.fuproc.2020.106582
Keywords: scrap tire, pyrolysis, vacuum pyrolyzer, tire derived oil, carbon black, non-condensable gases
Citation: Yahya SA and Omar MM (2024) Technoeconomic analysis: the potential and opportunities of transforming Saudi Arabian scrap tires into synthetic fuel via vacuum pyrolysis. Front. Energy Res. 12:1415901. doi: 10.3389/fenrg.2024.1415901
Received: 11 April 2024; Accepted: 03 May 2024;
Published: 05 June 2024.
Edited by:
Wenke Zhao, Harbin Institute of Technology, ChinaReviewed by:
Liangliang Fan, Nanchang University, ChinaCopyright © 2024 Yahya and Omar. This is an open-access article distributed under the terms of the Creative Commons Attribution License (CC BY). The use, distribution or reproduction in other forums is permitted, provided the original author(s) and the copyright owner(s) are credited and that the original publication in this journal is cited, in accordance with accepted academic practice. No use, distribution or reproduction is permitted which does not comply with these terms.
*Correspondence: Sulaiman Al Yahya, c3loeWFAcWVjLmVkdS5zYQ==; Muhammad Mubashar Omar, bXViYXNoYXIub21hckB1YWYuZWR1LnBr
Disclaimer: All claims expressed in this article are solely those of the authors and do not necessarily represent those of their affiliated organizations, or those of the publisher, the editors and the reviewers. Any product that may be evaluated in this article or claim that may be made by its manufacturer is not guaranteed or endorsed by the publisher.
Research integrity at Frontiers
Learn more about the work of our research integrity team to safeguard the quality of each article we publish.