- 1Wolfson School of Mechanical, Electrical and Manufacturing Engineering, Loughborough University, Loughborough, United Kingdom
- 2Tiyeni Malawi, Mzuzu, Malawi
This paper describes an innovative method to provide a micro-electric tractor which has been developed as part of an initiative that aims to provide socially inclusive and affordable green energy solutions to smallholders in sub-Saharan Africa. It utilizes a 15.0-kW solar array and battery system to power micro-electric tractors for an agricultural practice called deep bed farming in Malawi. Deep bed farming increases smallholder crop yield by about two and half times, which increases revenue by up to 12 times. The extra revenue can then be used to perpetually purchase domestic energy from the solar array, creating a self-sustaining model for decentralized energy access. However, the requirement for land preparation is onerous, and mechanization is needed to help overcome barriers to entry. This paper describes the technical requirements of a solar base station and micro-tractor for use with the deep bed farming technique. The paper covers the 5.9 kWp modular solar design and a 10.0-kWh rated micro-tractor. Testing was undertaken at an isolated grid in Loughborough as a precursor for large-scale testing in Malawi.
1 Introduction
According to the International Energy Agency (IEA), over 800 million people have no reliable access to electricity, primarily in Sub-Saharan Africa and rural regions of developing Asia (IEA, 2023). However, despite many existing initiatives, energy poverty eradication is a demanding challenge and requires novel strategies to meet the ambitious targets (Hakiri et al., 2016; Longe, 2020; Bacar et al., 2022). Obstacles include high capital costs (Buchana and Ustun, 2015), difficulties with energy demand forecasts (Asiegbu et al., 2023), environmental factors (Kolokotsa and Santamouris, 2014), theft, and damage (Wabukala et al., 2023).
The roll-out of grid or micro-grid connections to rural communities is often limited by the expendable income of a community being too low to purchase sufficient energy to be attractive to an infrastructure investor.
In Malawi, the majority of the rural populations are subsistence farmers arranged in smallholding households. The average annual production of maize per adult in smallholder households is 175.0 kg, which falls short of the minimum subsistence requirement of 200.0 kg. They obtain no external monetary income, and seasonal external work is largely paid in-kind with maize. A culture that would be capable of supporting a self-funding and profitable electrical grid/micro-grid infrastructure does not exist (Eales et al., 2020a).
Malawi is a small country with an estimated land area of 11.8 million hectares, of which Lake Malawi occupies one-fifth of the total. In Malawi, lands with slopes of less than 6.0% account for approximately 63.0% of the total land area, and lands with moderately/strongly sloping terrains with slopes of 6.0–30.0% account for 31.5% (Guiying et al., 2017). Out of 9.4 million hectares of land, approximately 5.3 million ha, or 56.0 percent, was cultivated in 2010. Most of the suitable lands have already been developed for cultivation, and agriculturally available land expansions are limited (Guiying et al., 2017). Malawi has a subtropical climate with distinct rainy and dry seasons: the rainy season spans from November to the following April, delivering 90.0%–95.0% of the annual precipitation, while the mean surface temperature is between 22.0 and 23.0°C (World Bank Group, 2024). Agriculture is pivotal to Malawi’s economy, accounting for over a quarter of its GDP and significantly influencing employment and export earnings. The sector is dominated by maize and tobacco, and as quoted in different publications, maize accounts for over 40.0% of export revenues (Trade, 2024).
There have been some published works looking at micro-grids in Africa and their success or otherwise, including in Malawi (Ikejemba et al., 2017; Eales et al., 2020b; Eales et al., 2022). The conclusions of most of the published works are that these fail due to lack of management following installation and equipment, which is left to deteriorate (Ikejemba et al., 2017). There needs to be sufficient revenue generation for ensuring ongoing management. The costs of hardware for a micro-grid solar and battery installation are approximately US$9.0k–US$10.0k per kW (Eales et al., 2022), while operational costs for ongoing management are quoted as US$3.8k per year. Implementation of solar micro-grids would cost approximately US$210.00 per person and average operational expenses of US$17.00 per person per year (Eales et al., 2020b).
Across large areas of Malawi, a heavily compacted layer of rock-hard earth is found a few inches under the topsoil. This is largely the result of long-term use of manual tilling hoes, human and animal footfall, and occasionally heavy machinery. Plant roots generally cannot penetrate through this hard layer, nor can air or water, which is necessary for the healthy living soils that support good agriculture (Mvula, 2021). The UNDP-quoted figures for soil loss from 2014 estimated that the average national soil loss rate in Malawi was 29.0 tons per hectare per year. However, these are old statistics with no new national statistics available (Vargas and Omuto, 2024). Statistics on the soil loss explains why Malawi is one of the world’s poorest countries, and why hunger is so common.
To generate wealth to pay for electrification, it is advisable to also address agricultural issues, which would help generate rural income to fund electricity. Previous work into joint agriculture/electrification projects has focused on cold storage (Yan et al., 2023) and crop shading (Aroca-Delgado et al., 2018).
Published work on use of mechanical power devices for agriculture in Sub-Saharan Africa includes (Mrema et al., 2018)
• Tractors using traditional two-axle, four-wheel tractors (4 W T).
• Specially designed for the developing world, four-wheel low horsepower tractors such as the Kabanyolo and Tinkabi.
• The power tiller or two-wheel tractor (2 W T), initially developed for irrigated areas in Asia.
• Crawler tractors for land clearing.
• Motorized pumps and other water-lifting devices.
• Motorized harvesting, postharvest handling, and on-farm processing equipment.
• Grain milling equipment.
Some work has been announced on electrification of tractors, but these are likely to be several orders of magnitude more expensive than a Malawian household could afford (Dezeen, 2023).
Deep bed farming (DBF) is an innovative agricultural methodology that has been developed by Tiyeni. DBF reconceptualizes the traditional Malawian agricultural cycle, and the methodology has received approval from the Malawian Ministry of Agriculture. DBF demonstrates a significant increase in yield.
The steps involved with this process are as follows (Tiyeni, 2023):
• Break up the hardpan: breaking up the hardpan delivers immediate benefits, allowing roots, water, and air to penetrate into the soil, curbing soil erosion.
• Create contour ridges and deep beds: these are designed to minimize water runoff, to maximize water retention, and to prevent the development of a new hard compacted layer under the ground, allowing roots, water, and air to penetrate downward on a long-term basis. Marker ridges are created along the contour lines of the terrain, at intervals down the slope. The ridge is then stabilized by planting it with Vetiver, a non-invasive but deep-rooted grass that stabilizes the ridge. Between the spaced marker ridges, deep beds of soil are created, raised above the level of the surrounding terrain. These deep beds are a meter wide, enough for planting two rows of maize or three rows of smaller crops.
• Planting: the deep beds are planted with crops. Maize, the staple crop of Malawi, is typically inter-planted with beans, pumpkin, kale, soya, groundnuts, and other local crops. These nitrogen-fixing “green manure crops” enhance soil fertility and create shade, which keeps the soil cooler and damper, reducing evaporation. They also help dissipate the force of big raindrops, protecting the soils from direct rain impacts.
• Harvesting
• Maintenance and preparation: following years
DBF is not just about creating and maintaining the deep bed but also includes a change in other agricultural practices such as soil health and fertility improvement through manure and compost application, residue incorporation, mulching, green manure cover crops, agroforestry, and crop rotation with legumes. This is to encourage farmers to reduce fertilizer use.
DBF requires a substantial increase in the amount of land prepared in the first year before an increase in yield. This creates a barrier to entry, especially for those households with a deficiency in family labor (child-, female-, and elder population-dominant households).
This paper presents a novel solution to these challenges. It proposes a solar-powered electric walk-behind tractor (AfTrak) designed for the preparation and maintenance of fields for the Tiyeni DBF concept, shown in Figure 1. The unit also provides access to zero carbon solar-powered electricity that is reliable year-round. Malawi has only 25.0% variance in solar generation across the year (Madhlopa, 2006). AfTrak directly addresses United Nations Sustainable Development Goal 7, SDG7, i.e., access to affordable and clean energy, on two key fronts:
1. Deep bed farming has been shown to increase smallholder revenue by up to 12 times, potentially generating a self-sustaining model.
2. Direct domestic energy provision, for low-power applications such as lighting, phone charging, and clean, electric, cooking.
This energy could offset high-carbon processes such as charcoal generation, open fire cooking, and lighting.
This paper is novel because it describes and details a new agricultural device, AfTrak, that is capable of both DBF ground preparation and electricity provision. The remainder of the paper is organized as follows: Section 2 highlights the specifications, Section 3 describes the materials involved, Section 4 describes the methods, and Section 5 and Section 6 detail the results and discussions respectively.
2 Specifications
The AfTrak system needs to enable faster and less arduous deep bed preparation. It must especially benefit those members of the communities who live in households with reduced resources to conduct manual labor, such as elderly, disabled, child, or female-led households, while at the same time providing a source of affordable electricity to the local community. The requirements for the AfTrak system are split into four parts.
• Performance of the base station (solar charging and energy storage).
• Performance of the Aftrak unit (the solar micro-electric tractor unit).
• Environmental and agricultural impact.
• Socio-economic benefits and community engagement.
This paper focuses primarily on the first two requirements regarding technical performance. Table 1 shows the requirements for the AfTrak unit and the performance requirements for the base station.
3 Materials
3.1 Hardware design: base station
The AfTrak unit requires to be charged from a base station to ensure sufficient energy to enable land preparation. The solar mounting array is designed to be modular with two panels fitting on each solar mounting frame. The AfTrak unit is designed to fit under the solar mounting frame and has a container for up to 5.0 kWh of batteries that is shielded from the weather by the solar panel.
The frame is a flat pack in format and was designed to be easily assembled in the country using a hammer and rivet gun as shown in Figure 2. This minimizes the space needed for shipping. The frame is mostly made from a folding and tab design. Tabs are aligned to fit into slots and are then hammered to complete and make a rigid joint. The final frame with the AfTrak unit is shown in Figure 3. The frame is designed so that the AfTrak unit sits underneath the frame and charges through Anderson connectors obtained from the power electronics and energy storage unit.
Each solar mounting frame has space for 5.0 kWh of batteries along with the solar energy maximum power point tracking (MPPT) controller and grid-connected inverter. There are two possible ways this could be set up:
Setup 1: With a single connector so that each set of PV panels is either charging the base station batteries or the AfTrak unit and Anderson connectors are used to switch from one to the other. The base station batteries are not used to charge the AfTrak unit but to provide energy for other applications.
Setup 2: As a fully controllable system where the PV channels charge the base station batteries and then either the AfTrak unit can be charged from the solar panels or from the base station batteries (additional converter needed along with protection and isolators).
Table 2 shows the cost of the material for the prototype system that was built based on Setup 1.
3.2 Hardware design: AfTrak unit
The AfTrak unit is a micro-electric tractor. It has four motor drives that are required to drive the wheels (one per rear wheel), drive a linear motor to lower an actuator, and run a trenching chain to cut through the hard pan soil. The motor drives sit in the base of the unit. Four 12.0-V VARTA batteries sit on the base unit to provide weight to help with breaking up the hard pan. There is a cover over the batteries and a small inverter to produce AC power for customers. The base support unit houses all the cabling and power electronics in a compartment and at the same time provides a stand for the batteries to sit in. It needs to carry around 400.0 kg in weight to provide sufficient weight to enable DBF. Figure 4 shows the concept product and the location of the key component parts.
The main assembly is welded together and then the unit turned upside down to install the motors (lynch motor to run the chain, linear actuator to lower the chain into the ground, and brushless DC motors to drive the two rear wheels), the power electronic drives (for the lynch motor and wheels), and the wiring harnesses. The chain is fitted and the guard plate added.
The batteries are located in a top assembly which bolts to the base assembly, as shown in Figure 5. These have a small distribution circuit with connections to a 1,200.0 VA inverter to provide local 240.0 V and universal serial bus (USB) level power for phone charging through a waterproof plug socket on the side of the unit.
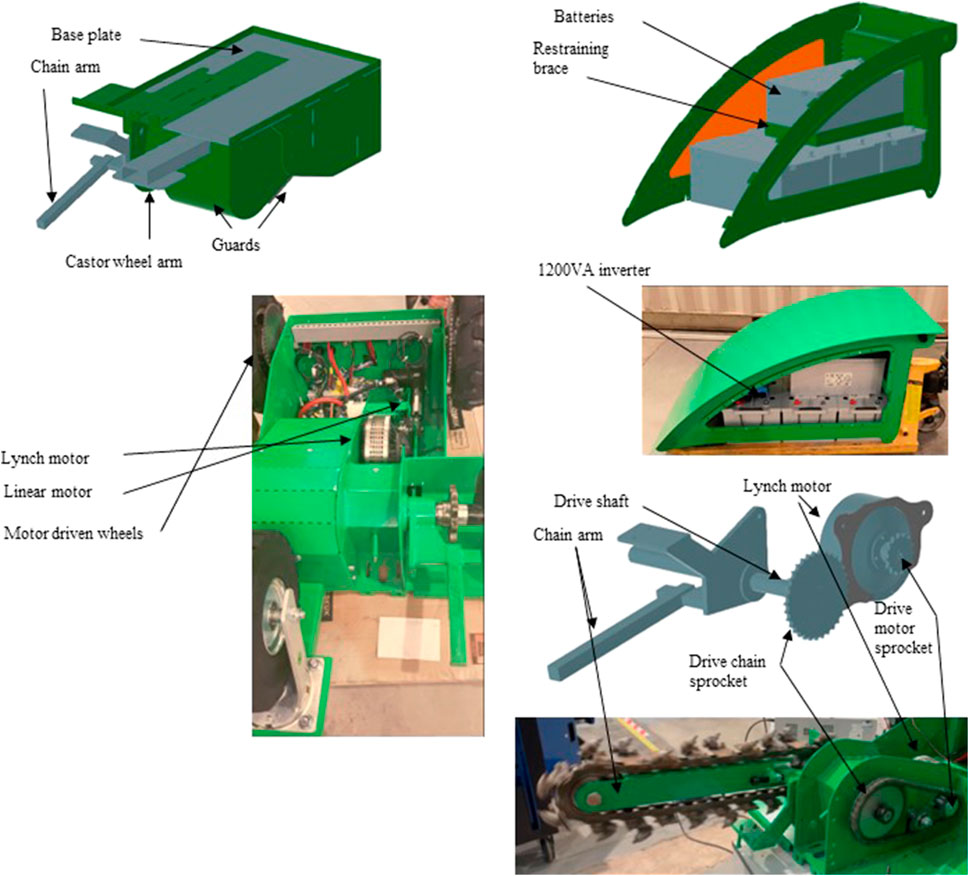
Figure 5. Base support drawing and underside drive mounting, top assembly, and battery installation.
The handle has been designed to be rugged so that it can carry cabling between the main body of the AfTrak unit and the controller, through the channels in the design. The user handles are designed to be intuitive to use with a push button throttle and two leavers to raise and lower the chain and to control its speed. A brake is fitted on the handle similar to that in a bike, which can disable the drive functionality.
There are three main motor assemblies. The most important of these is the lynch motor which drives the DBF chain. Figure 5 shows the mechanical assembly drawing of the lynch motor and the completed hardware assembly. The lynch motor and wheel motors are fed from the 48.0-V battery system. The linear motor (which operates to raise and lower the chain arm) is 24.0 V, and the supply for this is tapped from the midpoint of the series battery string. This creates a small imbalance in the power draw. However, this is deemed insignificant in terms of the total energy.
Table 3 shows the cost of the material for the prototype system that was built. Moving toward production, the AfTrak Unit will include bespoke printed circuit board (PCB) controllers and utilize the cost reductions in part procurement and manufacturing associated with bulk supply chains. This will significantly reduce the overall cost per unit of the system, as well as producing a supply chain for replacement parts and maintenance.
Costs are above the target at this point; however, there will be savings from the manufacturing scale. All costs are based on prices from April 2023.
4 Methods
To test the system and ensure it worked in line with design calculations, a dawn–dusk test was set up at Loughborough University, as shown in Figure 6. The AfTrak system setup included:
Primary solar array:
• Consists of 12 panels with 425.0-W modules each.
• Connected to the main MTTP Multi RS Solar 48/6000.
Secondary solar array:
• Two 425.0-W panels mounted on the prototype modular frame.
• This design is tailored for easy assembly in African locations.
• Connected to its own modular MPPT.
Battery pack:
• Base station pack made up of eight 12.0 V VARTA 210.0 amp-hour batteries in 2P4S.
• Powers an inverter which delivers up to 5.0 kW of AC load.
Ground station:
• Receives up to 5.0 kW of AC load from the inverter.
• Supports connected devices.
AfTrak unit:
• Connects to the base station battery system via a detachable Anderson charging connector.
• Allows for energy transfer from the ground station for recharging.
• Capable of supplying AC power to remote locations.
The setup was designed to operate close to one-third of a full-scale 15.0 kWp system. A 15.0 kWp system was chosen as this is the peak power of solar panels needed to meet a goal of 60 kWh of daily energy supplied as specified by the Milken–Motsepe prize for green energy for their size of micro-grid (Milken-Motsepe prize, 2024).
The measurement system for the test setup is shown in Figure 7. This consisted of commercial AC meters, Fdit, Intelligent Mini Power meter plug (accuracy not given), a Victron Cerbo GX (accuracy not given), and a Victron DC SmartShunt (±0.01 A and ±0.01 V on data sheet) to monitor the power use. The solar radiation was measured using a Kipp & Zonen CMP11 thermopile pyranometer (sensitivity 5.0–32.0 μV/W/m2 from data sheet) and Campbell Scientific CR800 logger.
A set of loads as shown in Table 4 were switched on and off during the day on the different devices, and the energy figures on each instrument were captured at the start, middle, and end of the day.
5 Results
The calculated energy from the solar radiation in conjunction with the solar panel area and energy generation reported by the Victron Cerbo GX is shown in Figure 8; the latter is divided into two parts, the small solar module frame with two panels and a more standard solar array with 12 panels to understand the impact of the frame design on generation. It should be noted that
• All measurements have been taken from an unobstructed location.
• The S29 (South—29.0° tilt) is from a standard “plane-translation” model with the measured global horizontal measurements and Sun position calculation as inputs.
• The timestamps are in GMT (i.e., no adjustment to British Summer Time for daylight saving).
• The timestamps for the averaged data at lower time resolution are for the beginning-of-period.
The 1 hour shift between calculated energy and measured in time is due to GMT/BST reporting.
The generation as recorded on the two MPPT units over the day was as follows:
• RS 48/6000 MPPT: 29.4 kWh (5,100.0 kWp).
• Modular MPPT: 4.98 kWh (850.0 kWp).
• The total generation over the course of the day was 34.38 kWh.
Generated PV energy has exceeded the expected targets for the array. This is due to several factors including slightly longer days at the test location latitude than in the target market, and generally clear sky. The team has optimized the installation using optimal tilt and angle for maximum irradiance; these values can be optimized at any global location, and instructions and a link to a suitable phone app will aid within the country setup. Negative impactors include a high panel temperature (higher than peak seasonal generation in Malawi).
In order to assess the performance of the new modular solar frame, the results were normalized using the total installed capacity, allowing for direct comparison.
The data show that the modular frame consistently generates more energy than the stock frame and over the course of 24 h generated 102.0% as the array.
These improvements have been attributed to two key factors:
• Shadowing: the increased height of the frame stops low level shadowing from grass and insects.
• MPPT optimization, using smaller cheap and modular MPPTs allows the units to optimize production for each module rather than attempting to find an optimal point across several panels.
The modular frame design was shown to provide good parking location and a charging station for the AfTrak units, protecting the tractor somewhat from continual thermal radiation, which will extend the units’ lifespan.
The steel framework was demonstrated to be sturdy and will likely hold up to storms, but this will need verifying in the country.
The AfTrak tractor units were successful in charging from the base station array, making use of the solar generation and additional input from the base station batteries. It has been extrapolated that a full charge after ploughing will take 1–3 h dependent on solar radiation.
The charge connector is designed to disconnect the tooling when on charge to prevent accidental operation. This functionality was tested and validated. The system has been tested as an isolated grid. However, our choice of power electronics means that micro-grid operation is possible if required at any stage.
A range of loads were tested through the test period and connected to both the base station and tractor unit; these are shown in Table 4. Two significant base loads were present from an EV charger and water heater, which when combined pushed the continuous load to 4.5 kW with additional 500.0 W of instantaneous power from smaller loads leaving a peak inverter load of 5.0 kW. A total consumption of 34.2 kWh was demonstrated throughout the day. The recorded data during the day are shown in Table 5.
The AfTrak unit used 3.0 kWh of load throughout the day on providing power for devices and running the deep bed farming trenching. This was then recharged using the solar panels toward the end of the day. The battery pack on the base station ended at 2.08 kWh lower charge than it started while the AfTrak battery unit was 0.02 kWh lower. This accounts for inefficiencies within the system.
Although difficult to deconvolve, manufacturing equipment’s efficiency has been stated as
• Victron Inverter at 30.0°C: 96.0%
• Lead acid round trip at 30.0°C: 85.0%
• Victron MPPT at 30.0°C: 96.0%–98.0%
Efficiency of system = output power/input power = 34.2/(34.2 + 2.08 + 0.02) = 94.2%
A total system efficiency of 94.2% is a reasonable figure considering that a significant amount of energy is directly consumed by the load and not charging the batteries. In a scenario where the batteries are used as short-term storage, an 80.0% efficiency is expected as energy loss occurs at both charging and discharging.
The DBF’s main requirement, from a labor standpoint, is the depth of soil penetration during the tilling process. The AfTrak unit has been demonstrated to be able to successfully mechanize the process of DBF by operating a 400.0-mm-deep cut, while de-compacting the soil to a small particle size, allowing for greater crop root penetration than by use of traditional hand tools, as shown in Figure 9.
The AfTrak tractor is equipped with a smart current monitoring shunt displaying power data live over Bluetooth. During soil preparation, a peak current of 152.99 A was recorded. This will vary with soil conditions but is expected to drop in dryer soils.
The AfTrak digging technique has been measured turning at 400.0 mm for a battery life equivalent to 50.0 m2 over 2 h of operation per unit. Combined with the solar base station, each AfTrak unit should be capable of at least two operations per day, resulting in 100.0 m2 per unit per day when used with two cycles and 150.0 m2 when three cycles are used. The average farm area in Malawi is 0.47 ha (FAO, 2024). To prepare half the land for DBF would require around 2 weeks of an AfTrak unit in year 1, and this is process is significantly faster than use of a pickaxe.
6 Discussion
This work is aimed at helping communities in Sub-Saharan Africa to adopt DBF as an agricultural practice to increase crop yield, help with water retention, and reduce soil erosion. This paper has described a micro-electric tractor that has been designed to both undertake DBF and also provide communities with a source of static and mobile micro-grid power.
The work has entailed developing a new base station structure to house the AfTrak unit and provide housing for batteries and the power electronics needed for charging and micro-grid applications. Both the base station and AfTrak unit worked with a variety of loads, and the AfTrak unit has the capability to cut through a hard pan to 40.0 cm.
The AfTrak system is designed to have very little running cost and to be maintained by the community. This results in extremely low running costs for the AfTrak system. The costs of the demonstration system from Tables 2 and 3 are base unit: £9,086.00 or USD$ 11,377.26 (just over 1/3 size) and AfTrak: £7,409.84 or USD$ 9,275.64 (each). The hardware costs for a 5.9 kWp solar array and single 10.0 kWh micro-tractor unit are approximately US$ 20,000.00 combined. This is cheaper than currently quoted typical micro-grid prices of US$ 9.0k–US$ 10.0k per kW but does not include labor, installation, and land costs. Some of the costs of a typical micro-grid include laying cables to houses. This has not been included within the costing as the micro-tractor is portable. We anticipate villages having multiple micro-tractors per base station with sizes being scalable.
Using solar modeling, the amount of energy that could be generated by the base station per year is around 10.0 MWh. This is equivalent to a capital cost of US$ 0.06/kWh. For a full-scale base station this reduces to US$ 0.02/kWh with one tractor and US$ 0.03/kWh with three tractors. The current price of electricity in Malawi is listed as 173.70 K/kWh (Mhone, 2023) equivalent to around US$ 0.10/kWh.
This estimation of the capital cost per unit was based on a quoted 30-year lifespan of the panels. It is expected that the AfTrak units will have a lifespan of at least 10 years, but given that they only need to convert each field once to DBF, they can be retired after this point and used solely as energy vectors.
This work is not complete as detailed testing in Malawi needs to be performed. In addition, technical improvements have been identified. In particular, the original wheel drive, while fine on flat hard ground, did not have enough torque for seamless operation while undertaking trenching. The motor drives had to be replaced, and additional gearing was needed to meet the high torque requirements. It is also necessary to undertake large-scale testing in Malawi within the community to understand more deeply their social and technical requirements and improve the design based on this.
Data availability statement
The raw data supporting the conclusion of this article will be made available by the authors, without undue reservation.
Author contributions
TW: conceptualization, formal analysis, investigation, methodology, software, and writing–review and editing. JW: conceptualization, formal analysis, funding acquisition, software, supervision, validation, visualization, and writing–original draft. LP: methodology, resources, visualization, and writing–review and editing. CA: formal analysis, investigation, visualization, and writing–review and editing. IC: investigation, validation, and writing–review and editing. FG: investigation, validation, and writing–review and editing. TB: formal analysis, investigation, and writing–review and editing. DS: formal analysis, data curation, project administration, software, and writing–original draft.
Funding
The author(s) declare that financial support was received for the research, authorship, and/or publication of this article. This work was supported by Innovate UK project 10039354 AfTrak and the Milken–Motsepe prize.
Acknowledgments
The project was managed by the Consortium for Battery Innovation and the VARTA® batteries used in the project were donated by Clarios.
Conflict of interest
The authors declare that the research was conducted in the absence of any commercial or financial relationships that could be construed as a potential conflict of interest.
Publisher’s note
All claims expressed in this article are solely those of the authors and do not necessarily represent those of their affiliated organizations, or those of the publisher, the editors, and the reviewers. Any product that may be evaluated in this article, or claim that may be made by its manufacturer, is not guaranteed or endorsed by the publisher.
References
Aroca-Delgado, R., Pérez-Alonso, J., Callejón-Ferre, Á. J., and Velázquez-Martí, B. (2018). Compatibility between crops and solar panels: an overview from shading systems. Sustainability 10, 743. doi:10.3390/su10030743
Asiegbu, A., Almaktoof, A., and Khalat, A. (2023). “Energy access assessment report focusing on energy poverty and energy demand for Rwanda,” in 2023 IEEE 3rd International Maghreb Meeting of the Conference on Sciences and Techniques of Automatic Control and Computer Engineering (MI-STA), Benghazi, Libya, May, 2023, 820–882.
Bacar, B., Almaktoof, A., Khalat, A. M., and Elmezughi, M. K. (2022). “Smart metering and energy access programs: an approach to energy poverty reduction in sub-Saharan Africa,” in 2022 IEEE 2nd International Maghreb Meeting of the Conference on Sciences and Techniques of Automatic Control and Computer Engineering (MI-STA), Sabratha, Libya, May, 2022, 127–132.
Buchana, P., and Ustun, T. S. (2015). “The role of microgrids and renewable energy in addressing Sub-Saharan Africa's current and future energy needs,” in IREC2015 The Sixth International Renewable Energy Congress, Sousse, Tunisia, March, 2015, 1–6.
Dezeen (2023). AMO and Volkswagen propose electric tractor design for sub-Saharan Africa. Available at: https://www.dezeen.com/2020/03/02/amo-volkswagen-electric-tractor-africa/ (Accessed November 17, 2023).
Eales, A., Alsop, A., Frame, D., Strachan, S., and Galloway, S. (2020a). Assessing the market for solar photovoltaic (PV) microgrids in Malawi. Hapres, J. Sustain. energy.
Eales, A., Alsop, A., Frame, D., Strachan, S., and Galloway, S. (2020b). Assessing the market for solar photovoltaic (PV) microgrids in Malawi. Hapres J. Sustain. Res. 2 (1), e200008.
Eales, A., Banda, E., Taulo, G., Coley, W., and Frame, D. (2022). Deploying solar microgrids in Malawi: lessons learned and implications for the Malawian microgrid ecosystem. Available at: https://ease.eee.strath.ac.uk/wp-content/uploads/2022/11/Deploying-Solar-Microgrids-in-Malawi-Technical-Report.pdf (Accessed November 17, 2023).
FAO (2024). Family farming knowledge platform. Available at: https://www.fao.org/family-farming/data-sources/dataportrait/farm-size/en/ (Accessed February 09, 2024).
Guiying, L., Messina, J. L., Peter, B. G., and Snapp, S. S. (2017). Mapping land suitability for agriculture in Malawi. Land Degrad. Dev. 28 (7), 2001–2016. doi:10.1002/ldr.2723
Hakiri, J., Moyo, A., and Prasad, G. (2016). “Assessing the role of solar home systems in poverty alleviation: case study of Rukungiri district in Western Uganda (November 2015),” in 2016 International Conference on the Domestic Use of Energy (DUE), Cape Town, South Africa, November, 2015, 1–9.
IEA (2023). SDG7: data and projections. Available at: https://www.iea.org/reports/sdg7-data-and-projections (Accessed November 17, 2023).
Ikejemba, E. C. X., Mpuan, P. B., Schuur, P. C., and Van Hillegersberg, J. (2017). The empirical reality and sustainable management failures of renewable energy projects in Sub-Saharan Africa (part 1 of 2). Renew. Energy 102 (Part A), 234–240. ISSN 0960-1481. doi:10.1016/j.renene.2016.10.037
Kolokotsa, D., and Santamouris, M. (2014). “Energy poverty in Europe: challenges for energy efficiency,” in IISA 2014, The 5th International Conference on Information, Intelligence, Systems and Applications, Chania, Greece, 229–234.
Longe, O. M. (2020). “A review of energy and gender poverty nexus in South Africa,” in 2020 IEEE PES/IAS PowerAfrica, Nairobi, Kenya, August, 2020, 1–5.
Madhlopa, A. (2006). Solar radiation climate in Malawi. Sol. Energy 80 (8), 1055–1057. ISSN 0038-092X. doi:10.1016/j.solener.2005.08.007
Mhone, C. (2023). Review of ESCOM electricity tariffs. Available at: https://mera.mw/2023/11/09/review-of-escom-electricity-tariffs/ (Accessed February 09, 2024).
Milken-Motsepe prize (2024). Milken-Motsepe prize for green energy. Available at: https://milkenmotsepeprize.org/green-energy/ (Accessed April 21, 2024).
Mrema, G. C., Kienzle, J., and Mpagalile, J. (2018). Current status and future prospects of agricultural mechanization in sub-saharan Africa (SSA). Ama, Agric. Mech. Asia, Afr. Lat. Am. 49 (2), 13–30.
Mvula, A. (2021) The social-ecological sustainability of the Tiyeni deep-bed conservation agriculture system in Malawi. Phd thesis. Worcester, England: University of Worcester.
Tiyeni (2023). Deep bed farming. Available at: https://www.tiyeni.org/deep-bed-farming (Accessed November 17, 2023).
Trade (2024). Malawi – country commercial guide. Available at: https://www.trade.gov/country-commercial-guides/malawi-agricultural-sector (Accessed April 21, 2024).
Vargas, R., and Omuto, C. (2024). Soil loss assessment in Malawi. Available at: https://info.undp.org/docs/pdc/Documents/H21/Soil%20Loss%20Report-Final%20copy%20November%2018,%202016.pdf (Accessed April 20, 2024).
Wabukala, B. M., Mukisa, N., Watundu, S., Bergland, O., Rudaheranwa, N., and Adaramola, M. S. (2023). Impact of household electricity theft and unaffordability on electricity security: a case of Uganda. Energy Policy 173, 113411. ISSN 0301-4215. doi:10.1016/j.enpol.2022.113411
World Bank Group (2024). Climate change knowledge portal. Available at: https://climateknowledgeportal.worldbank.org/country/malawi/climate-data-historical#:∼:text=Malawi%20has%20two%20main%20seasons,30%C2%B0%2D%2035%C2%B0C (Accessed April 21, 2024).
Keywords: agricultural engineering, agricultural machinery, batteries, micro-grids, solar power generation
Citation: Williams T, Wilson J, Partington L, Andrews C, Chavula I, Gondwe F, Betts T and Strickland D (2024) Micro-electric tractors for deep bed farming and sustainable micro-grid electricity. Front. Energy Res. 12:1384568. doi: 10.3389/fenrg.2024.1384568
Received: 09 February 2024; Accepted: 08 May 2024;
Published: 06 June 2024.
Edited by:
Haonan Zhang, North China Electric Power University, ChinaReviewed by:
Godwin Norense Osarumwense Asemota, University of Rwanda, RwandaNitin Kumar Saxena, University of Denver, United States
Copyright © 2024 Williams, Wilson, Partington, Andrews, Chavula, Gondwe, Betts and Strickland. This is an open-access article distributed under the terms of the Creative Commons Attribution License (CC BY). The use, distribution or reproduction in other forums is permitted, provided the original author(s) and the copyright owner(s) are credited and that the original publication in this journal is cited, in accordance with accepted academic practice. No use, distribution or reproduction is permitted which does not comply with these terms.
*Correspondence: Dani Strickland, ZC5zdHJpY2tsYW5kQGxib3JvLmFjLnVr