- 1Tianjin Key Laboratory of Dredging Engineering Enterprises, CCCC Tianjin Dredging Co., Ltd., Tianjin, China
- 2School of Artificial Inteligence, Shanghai Normal University Tianhua College, Shanghai, China
- 3Automotive Structure and Energy Storage Engineering Center, School of Mechanical Engineering, Shanghai Dianji University, Shanghai, China
Fuel cell vehicles are considered as the direct alternative to fuel vehicles due to their similar driving range and refueling time. The United Nations World Forum for Harmonization of Vehicle Regulations (UN/WP29) released the Global Technical Regulation on Hydrogen and Fuel Cell Vehicles (GTR13) in July 2013, which was the first international regulation in the field of fuel cell vehicles. There exist some differences between GTR13 and the existing safety technical specifications and standards in China. This paper studied the safety requirements of the GTR13 compressed hydrogen storage system, analyzed the current hydrogen storage safety standards for fuel cell vehicles in China, and integrated the advantages of GTR13 to propose relevant suggestions for future revision of hydrogen storage standards for fuel cell vehicle in China.
1 Introduction
The rapid development of China’s automotive industry has imposed an increasing impact on China’s energy, resources and environment. According to the statistics, 31% of environmental phenomena such as climate degradation and smog in the air in China are caused by the automotive industry. In addition, China’s current dependence on foreign crude oil has reached as high as 72% (Zhao et al., 2022). Under the pressure of environment and resources, the country has intensively implemented multiple policies to support the development of new energy vehicle. The prevalence of global decarbonization trends has promoted the large-scale development and utilization of renewable energy. However, renewable energy sources such as solar energy and wind energy are unstable and intermittent during generation, and thus these valuable electric energies are difficult to apply continuously and stably (Sun and Zhang, 2022). To tackle this issue, the employment of energy storage and conversion systems may greatly improve the utilization rate and stability of renewable energy, such as water electrolyzers to produce green hydrogen and fuel cells to produce electricity when needed (Li et al., 2022). Fuel cell vehicle is considered as the direct alternative to fuel vehicle because their range and refueling time are similar (Lin et al., 2021). Proton exchange membrane fuel cell vehicle is an efficient and environmentally friendly power generation device, and currently fuel cell vehicle mainly uses proton exchange membrane fuel cell (Yuan et al., 2020).
The fuel cell vehicle industries abroad have achieved remarkable results due to their early layouts. Japanese and Korean companies such as Toyota, Hyundai, and Honda have all achieved mass production of fuel cell vehicles and established their commercialization schedules. Toyota Motor Corporation of Japan commercialized the fuel cell vehicle Mirai in December 2014 (Figure 1A). Hyundai Motors of South Korea mass-produced the fuel cell vehicle ix35 in 2013 (Figure 1B). Honda Motor Corporation of Japan launched its first hydrogen oxygen fuel vehicle, the Clarity, in November 2015 (Figure 1C).
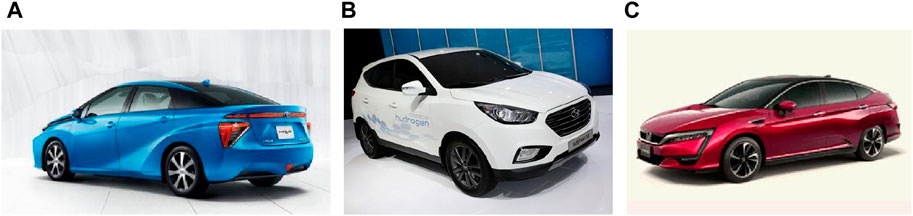
Figure 1. Mass production of fuel cell vehicles. (A) Mirai of Toyota; (B) ix35 of Hyundai; (C) Clarity of Honda.
In addition, the United States is also actively developing the fuel cell vehicle industry. In 2009, the Obama administration implemented an economic stimulus plan in the United States, and invested $300 million in advanced energy technologies, including proton exchange membrane fuel cell vehicles. In order to encourage the enterprises to use fuel cell vehicles, the United States issued fuel cell and hydrogen related policies in 10 states in 2016, including tax incentive, adjustment of electricity price and other measures.
China’s researches on the application of hydrogen energy and fuel cell vehicle technology can be traced back to the 1950s, including the National 863 Plan, the 10th Five Year Plan on major science and technology projects for electric vehicles, the 11th Five Year Plan on major projects for energy saving and new energy vehicles, the 12th Five Year Plan on major projects for key technologies and system integration of electric vehicles, the 13th Five Year Plan on national strategic emerging industry development plan, and the Made in China 2025 project. In March 2022, the National Development and Reform Commission and the National Energy Administration of China jointly issued the “Medium and Long Term Plan for the Development of Hydrogen Energy Industry (2021–2035),” which put forward specific requirements for the development of China’s hydrogen energy industry from the top-level design. In 2023, the sales volume of commercial hydrogen fuel vehicles was 5,362, a slight year-on-year increase of 2.4%. And the sales volume of the passenger hydrogen vehicles was 5,800, with a year-on-year increase of 72.3%.
In addition to the characteristics of clean combustion and emission, hydrogen is also easy to explode and has a wide combustion range. When the volume fraction of hydrogen in the air is between 4% and 75%, it will explode (Figure 2A) in the presence of open fire. Moreover, hydrogen can degrade metal materials, which is prone to hydrogen embrittlement (Figure 2B). How to ensure the safety of hydrogen storage container has become one of the problems to be solved in the application field of hydrogen energy technology, and has attracted extensive attention in the world.
In order to eliminate trade barriers in the fuel cell vehicle industry in various countries, the United Nations World Forum for Harmonization of Vehicle Regulations (UN/WP29) released the Global Technical Regulation on Hydrogen and Fuel Cell Vehicles (GTR13) (UN GTR, 2018) in July 2013. The main purpose is to ensure that hydrogen fuel cell vehicles can achieve the same level of safety as traditional fuel vehicles, and prevent injuries to drivers and passengers due to hydrogen explosions or combustion (Guo et al., 2020).
There are some differences between GTR13 and the existing safety technical specifications and standards in China. The technical content of GTR13 mainly includes the requirements and test methods of safety of fuel cell vehicle and hydrogen storage system. The safety requirements and testing methods for fuel cell vehicles in China (Figure 3) are specified in the national standard GB/T 24,549-2020 (Fuel cell electric vehicles—Safety requirements) (State Administration for Market Regulation, Standardization Administration, 2021), while the safety requirements and testing methods for hydrogen storage systems are specified in the national standard GB/T 35,544-2017 (Fully-wrapped carbon fiber reinforced cylinders with an aluminum liner for the on-board storage of compressed hydrogen as a fuel for land vehicles) (General Administration of Quality Supervision, 2018).
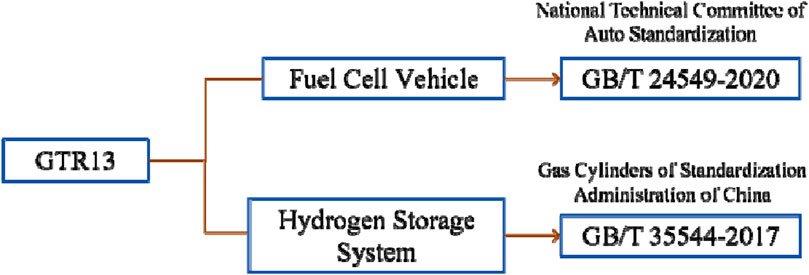
Figure 3. The technical specifications and standards of hydrogen storage safety requirements in GTR13 and China.
The implementation of GTR13 will have a significant impact on China’s development of safety technology in hydrogen storage system. Therefore, it is necessary to study the advantages of GTR13, and integrate with developed countries’ new energy vehicle industry standards, propose and construct a safety standard strategy for China’s fuel cell vehicle hydrogen storage system, so as to provide technical support for enterprises to break through foreign trade barriers as soon as possible.
Aligning China’s standards more closely with GTR13, the risk assessment and control for hydrogen storage and use could be strengthened, so as to improve the safety of hydrogen storage system. At the same time, GTR13 has covered the latest technologies and best practices in the global hydrogen energy field. Aligning with GTR13, Chinese enterprises and scientific research institutions could better integrate into the global innovation network, promote technical exchanges and cooperation, and promote the development of China’s hydrogen energy technology.
2 Summary of GTR13
The safety requirements of GTR13 for hydrogen fuel cell vehicles aim to minimize the risk of fire, explosion, or leakage from fuel cell systems in vehicle fuel and hydrogen storage system, so as to protect the safety of vehicle drivers and passengers.
2.1 Performance test requirements
GTR13 provides performance requirements and type test requirements for compressed hydrogen storage system, fuel system and electrical safety. The compressed hydrogen storage system of fuel cell vehicles must perform the verification test items in Table 1 to ensure that newly developed fuel cell vehicles could meet safety requirements.
2.2 Hydrogen storage system safety requirements in GTR13
The compressed hydrogen storage system mentioned in GTR13 includes hydrogen storage container, thermally-activated pressure relief device (TPRD), check valve, shut-off valve, and piping and fittings between the above components (if any), fuelling receptacle, venting system, warning system and electric safety system. Hydrogen has typically been stored at a NWP of 35 MPa or 70 MPa, with maximum fuelling pressures of 125 percent of NWP (43.8 MPa or 87.5 MPa respectively). The service life of the compressed hydrogen storage system shall have a service life of 15 years or less.
Hydrogen storage container: The hydrogen storage container stores the compressed hydrogen gas. NWP of the hydrogen storage container is 35 MPa or 70 MPa. The working temperature is −40–85°C (80 per cent NWP at −40°C, 125 per cent NWP at 85°C). The volume is no more than 450L. And the service life is 15 years or less.
TPRD: TPRD is designed to vent the entire contents of the hydrogen storage container rapidly. The TPRD shall meet the following performance qualification requirements including pressure cycling test, accelerated life test, temperature cycling test, salt corrosion resistance test, vehicle environment test, stress corrosion cracking test, drop and vibration test, leak test, bench top activation test and flow rate test.
Check valve, shut-off valve, and piping and fittings (if any): The check valve prevents back-flow of hydrogen into the fuelling line. The shut-off valve prevents the out-flow of stored hydrogen when the vehicle is not operating or when a fault is detected. The valve units shall meet the following performance qualification requirements including hydrostatic strength test, leak test, extreme temperature pressure cycling test, salt corrosion resistance test, vehicle environment test, atmospheric exposure test, electrical tests, vibration test, stress corrosion cracking test and pre-cooled hydrogen exposure test.
Fuelling receptacle: Fuelling receptacle is the equipment to which a fuelling station nozzle attaches to the vehicle and through which fuel is transferred to the vehicle. The fuelling receptacle shall prevent reverse flow to the atmosphere. A label shall be affixed close to the fuelling receptacle showing the fuel type, NWP, date of removal from service of containers.
Venting system: The hydrogen venting of the TPRD shall be protected with a cover. The hydrogen emitted from the venting system shall not exceed 4% by volume fraction in 3 s, and shall not exceed 8% at any time. The most important safety requirement is to control the hydrogen leakage rate. According to the GTR13, the hydrogen leakage rate of the venting system during crash test should be less than 118NL/h. And the hydrogen concentration in the passenger compartment and the luggage compartment is kept at a low level, generally required to be less than 4% by volume fraction.
Warning system: Dangerous situations can occur if unintended leakage of hydrogen reaches flammable concentrations. A warning system is to alert the driver when hydrogen leakage may result in danger. Protection against the occurrence of hydrogen in air in the enclosed or semi-enclosed spaces within the vehicle that contain unprotected ignition sources is important. Any single failure downstream of the main hydrogen shut off valve shall not result in any level of hydrogen concentration in air anywhere in the passenger compartment. Warning system shall be working when hydrogen concentrations in air of 2 percent ± 1.0 percent or greater by volume fraction is detected. If the hydrogen concentration exceeds 3 percent ± 1.0 percent by volume in air in the enclosed or semi-enclosed spaces of the vehicle, the main shutoff valve shall be closed to isolate the storage system.
Electric safety system: The voltage of fuel cell vehicle can reach as high as 300–600V. A failure of a high voltage may cause an electric shock on a human body. The electric safety system shall provide safe anti-electrocution measures to ensure the personal safety. The electric safety system requirements are divided into in-use and post-crash requirements. The specific test items are shown in Table 2.
3 Safety standards for hydrogen storage systems for fuel cell vehicles in China
The fuel cell vehicles mostly use high pressure hydrogen storage containers. A typical high pressure hydrogen storage system consists of a hydrogen storage container, TPRD, check valve, shut-off valve, and piping and fittings between the above components (Figure 4). At the initial state, the shut-off valve is closed. Its core and body form a seal, and the gas cannot flow to the outlet. When the temperature around the hydrogen storage container is too high, the TPRD pressure relief device is activated, the internal safety valve is opened, and the hydrogen is released at a low speed, effectively avoiding the hydrogen storage container from cracking or even explosion due to exceeding the pressure limit.
Hydrogen storage container could be divided into four common types according to the different materials: all metal container (Type I in Figure 5A), metal liner composite hoop wrap container (Type II in Figure 5B), metal liner composite full wrap container (Type III in Figure 5C), and plastic liner composite full wrap container (Type IV in Figure 5D). Type Ⅰ and Ⅱ hydrogen storage containers are not suitable for fuel cell vehicles due to their large weight-volume ratio. Type Ⅳ hydrogen storage containers are easy to leak hydrogen outward from the non-metallic liner under high pressure. And it is difficult to guarantee the connection strength between the valve units made of metal and the non-metallic liner. Therefore, China has not yet allowed the application of type IV hydrogen storage containers in fuel cell vehicles.
China’s fuel cell vehicles use metal liner composite full wrap containers (Type III). The quality of the hydrogen storage cylinder is in line with GB/T 35,544-2017 (Fully-wrapped carbon fiber reinforced cylinders with an aluminum liner for the on-board storage of compressed hydrogen as a fuel for land vehicles). The liner is made from aluminum alloy 6,061, and the outside of the hydrogen storage cylinder is fully wound with carbon fiber material. The main safety risks of the high pressure hydrogen storage system mainly include hydrogen leakage caused by the loss of functions of the key hydrogen storage container such as TPRD, check valve and shut-off valve, and leakage of the connecting piping joints.
At present, the standardization committee engaged in the research and formulation of standards and regulations for fuel cell electric vehicles in China is the electric vehicle sub committee of the National Technical Committee of Auto Standardization (TC114/SC27). Under the electric vehicle sub committee, a fuel cell electric vehicle working group has been established. At present, four standards related to the safety of hydrogen storage system listed in Table 3 have been completed, including GB/T 24548-2009 (Fuel cell electric vehicles—Terminology) (General Administration of Quality Supervision, 2017), GB/T 24549–2020, GB/T 26779-2021 (Hydrogen fuel cell electric vehicle refueling receptacle) (State Administration for Market Regulation, Standardization Administration, 2022), GB/T 26,990-2011 (Fuel cell electric vehicles—Onboard hydrogen system—Specifications) (General Administration of Quality Supervision, 2022).
In addition, the National Technical Committee on Gas Cylinders of Standardization Administration of China was officially established in 2011, which was under the approval of the National Standardization Administration. And its number is SAC/TC31/SC8, which is responsible for the standardization of compressed natural gas cylinders for vehicles, high pressure hydrogen cylinders for vehicles and other composite gas cylinders. Sub Technical Committee TC31/SC8 for high pressure fuel gas cylinders for vehicles (subordinate to China Standardization Committee on Boilers and Pressure Vessels), whose competent department is the State Administration for Market Regulation. And its main relevant standard is GB/T 35544-2017.
To sum up, the safety regulations of main test items in China are as follows.
(1) Hydrogen storage container
Hydrogen storage containers are aluminum liner composite full wrap cylinders (Type III) that meet the standard requirements of GB/T 35,544-2017, which should be the stereotypical products that have passed the type test inspection by the National Gas Cylinder Quality Supervision and Inspection Center.
(2) TPRD
TPRD meets the standard requirements of GB/T 35544-2017, and uses fusible alloy stopper or other suitable structural type. Its action temperature shall be (110 ± 5)°C, and the relief port shall not be directed toward the bottle.
(3) Check valve, shut-off valve, and piping and fittings
Test method for check valve, shut-off valve, and piping and fittings lack national standards to support them. Currently, the testing of these parts is based on the GB/T 35544–2017 standard, which is accompanied by hydrogen containers for the verification of partial product experiments.
(4) Fuelling receptacle
The fuelling receptacle meets the requirements of GB/T 26779–2021 standard. Fuel is filled through the fuelling receptacle, which is equipped with a dust cover to prevent dust, soil, liquid and pollutants from entering. The maximum fuelling pressure is displayed next to the dust cover and there are measures to eliminate static electricity. The fuelling receptacle meets the requirements for gas tightness based on a certain level of strength and shall not fail under loads of 670 N from any direction.
(5) Venting system
The large-scale commercialization of PEMFCs requires higher power and current densities. However, at high operating current densities, the massive accumulation of liquid water will lead to flooding and impede the hydrogen gas diffusion, resulting in rapid degradation of cell performance and the large quantity of hydrogen gas emitted from the PEMFC without reactions/consumption (Yan et al., 2023). Accordingly, improving the water management ability is imperative for avoiding the leakage of hydrogen gas as well.
The venting system meets the requirements of GB/T 24549–2020 standard. Ventilation and deflation are necessary for the breakdown or accident of the vehicle. The direction of the airflow shall be away from people, power sources, and other ignition sources inside the vehicle. The venting devices shall be installed as high as possible inside the vehicle. Hydrogen shall not be directly discharged to the passenger compartment and the luggage compartment. In order to ensure that hydrogen does not leak, the piping for hydrogen must be made of metal with a high melting temperature.
(6) Warning system
The warning system meets the requirements of 24,549–2020 standard. When the hydrogen concentration in the vehicle reaches a certain value, it can be signaled through sound alarm, emergency display, cutting off the hydrogen source or cutting off the power supply. When the warning system detects that the hydrogen concentration in the vehicle reaches 2% in volume fraction, the vehicle occupants are reminded of the possible safety risks by means of sound alarm device or emergency display. And when the system detects that the hydrogen concentration in the vehicle reaches 3% in volume fraction, the system shall take the initiative to cut off the hydrogen source or directly turn off the power supply of the system. When the hydrogen leakage detection sensors break down, such as signal interruption, disconnection, short circuit, etc., it should be able to send a fault warning signal to the driver.
(7) Electric safety system
The electrical safety meets the requirements of GB 18384-2020 (Electric vehicle safety requirements) (State Administration for Market Regulation, Standardization Administration, 2023). At present, the fuel cell vehicle electric safety standard puts forward safety requirements and experimental methods for direct electric shock protection, indirect contact protection and functional safety protection. Physical isolation of the human body from electrically charged parts is realized through insulating materials, enclosures or shields. Under the maximum working voltage, the insulation resistance of DC circuit shall be not less than 100 Ω/V, and the insulation resistance of AC circuit shall be not less than 500 Ω/V.
4 Technical recommendations on the safety of hydrogen storage systems for fuel cell vehicles in China
Hydrogen has certain safety risks, so strengthening safety of hydrogen storage standards could reduce the frequency and severity of potential accidents. By adopting safer hydrogen storage technology, the safety risks of fuel cell vehicles could be effectively reduced. This would help to eliminate the doubts about the safety of fuel cell vehicles and provide a more reliable basis for their large-scale applications.
In order to ensure the popularization of fuel cell vehicles as soon as possible, in terms of clarifying the requirements in terms of safety, with reference to GTR13, China should do a good job in researching the contents of the relevant hydrogen storage safety standards, and formulate and revise the relevant standards in a timely manner, and it is recommended to do a good job in the implementation of the following contents:
The national standard GB/T 35,544–2017 has been released and implemented, which stipulates the technical requirements of metal liner composite full wrap container of 70 MPa and below. The safety technical indexes of GB/T 35,544–2017 are not lower than GTR13, which could meet the demand of the development of fuel cell vehicles in China.
The national standard GB/T 35,544–2017 has stipulated the test methods and qualified indicators of TPRD. And the safety technical indexes of TPRD in GB/T 35,544–2017 are not lower than GTR13, which could meet the demand of the development of fuel cell vehicles in China.
In the absence of a national standard to support valve units, reference can be made according to GTR13, where valve units are tested with hydrogen containers for the verification of partial product experiments, which are carried out using hydrogen gas. All tests are conducted at room temperature of 20°C unless it is specified. Tests include leakage test, hydrostatic strength test, atmospheric exposure test, stress corrosion cracking test (for copper-based materials), pre-cooled hydrogen exposure test, vibration test, automotive environmental test, salt spray corrosion resistance test, extreme temperature and pressure cycling test, and electrical test (only for automatic shut-off valves).
The type and technical requirements of the hydrogen fuelling receptacle shall meet the requirements of GB/T 26,779–2021 standard, and pass the inspection of National Motor Vehicle Product Quality Supervision and Inspection Center. The safety technical indexes of GB/T 26,779-2021 are not lower than GTR13, which could meet the demand of the development of fuel cell vehicles in China.
The venting system shall meet the standard requirements of GB/T 24,549-2020. In accord with GTR13, the vehicle leakage alarm after collision of hydrogen shall be considered. The safety requirements after the crash test are mainly to control the hydrogen leakage rate, which shall not exceed 118 NL/h. And the hydrogen concentration in the passenger compartment and luggage compartment shall not exceed 4% in volume fraction.
The warning system shall meet the requirements of GB/T 24,549-2020. In accord with GB/T 26,990-2011 and GTR13, the hydrogen leakage detection standard shall be considered. When the system detects that the hydrogen concentration in the vehicle reaches 2% by volume, the vehicle occupants will be reminded of the possible safety risks by means of sound alarm device or emergency display, and the alarm light will show yellow; when the system detects that the hydrogen concentration in the vehicle reaches 3% by volume, the system should take the initiative to cut off the gas source, or directly turn off the system power, and the alarm light will show red.
The electric safety system shall meet the requirements of the standard GB/T 24,549-2020. Referring to the standard GB 18384-2020 and the content of GTR13, the fuel cell power system is tested for online insulation to improve safety.
Regarding the discrepancies between China’s current standards and those outlined in GTR13, the testing methodologies and performance requirements of the hydrogen storage system shall meet the safety performance as shown in Table 4.
5 Research outlook
The safety standards should be developed under the collaboration between three parties, including academia, industry, and national authority. Then a hydrogen storage safety standard setting committee could be established. The resources and expertise of all parties are integrated to promote the implementation of hydrogen storage safety standards. This would help to improve the safety performance of hydrogen storage system, promote the sustainable development of hydrogen storage technology, and create a good environment and conditions for the development of hydrogen storage industry.
The specifications about the safety of hydrogen storage in GTR13 and Chinese standards are compared and analyzed, including hydrogen storage container, TPRD, check valve, shut-off valve, piping and fittings, fuelling receptacle, venting system and warning system. China has been preparing to manufacture the type IV hydrogen cylinder standard nowadays. So it is very important to learn from foreign advanced experience, The purpose of this article is provide relevant instructs for manufacture, inspection and test, to formulate China’s vehicle-mounted hydrogen storage containers, and improves the conversion and application of standards.
After the implementation of GTR13, the development of hydrogen storage system for fuel cell vehicles in China will face greater challenges. This paper collects, translates and organizes the GTR13 standard about the safety of the hydrogen storage system. Then China’s hydrogen storage safety standards for fuel cell vehicles are analyzed. By comparing with the GTR13 standard, the shortcomings of China’s hydrogen storage standards for fuel cell vehicles are summed up. Drawing on the advantages of GTR13, relevant suggestions are proposed for the revision of hydrogen storage safety standards for fuel cell vehicles in China.
GTR13 requires the hydrogen storage system and the vehicle as the test object, but there is a lack of corresponding standards in China. Compared with GB/T 35,544-2017, which stipulates the test items of individual valves, the test object of GTR13 is the whole system. TPRD, check valves, shut-off valves, pipelines and fittings are tested together with the hydrogen storage container. Compared with GB/T 24,549-2020, GTR13 also stipulates the hydrogen leakage index requirements for the vehicle. Interpretation of the GTR13 provides technical support for China’s enterprises to break through the trade barriers of fuel cell vehicles as soon as possible.
The implementation of GTR13 has greatly influenced the development of fuel cell vehicles and compressed hydrogen storage systems in China. The management mode and standards in China are difficult to meet the requirements of GTR13. In China, hydrogen storage container, compressed hydrogen storage system, and standard setting are managed by different administrative departments. Hydrogen storage container is managed by the State Administration for Market Regulation, compressed hydrogen storage system is managed by General Administration of Quality Supervision, Inspection and Quarantine, while standard setting is managed by the Standardization Administration.
In order to align with GTR13, it is recommended to carry out further researches in the following two aspects. First of all, attention should be paid to the specific impact of GTR13 on the development of hydrogen fuel cell vehicles and compressed hydrogen storage systems. The safety test method of compressed hydrogen storage system should be studied, so as to realize the transition from the current component based test method to system based test method. Then the corresponding specifications and standards could be established. Secondly, the ability of hydrogen safety test should be improved. Devices that could meet the safety performance test of 70 MPa compressed hydrogen storage system should be developed. The sequence test of compressed hydrogen storage system should also be carried out.
Moreover, establishing international cooperation projects, attracting international experts to participate in the formulation and research of China’s hydrogen storage safety standards could also help China to fill the existing gap in hydrogen storage safety standards, and promote the development of China’s hydrogen storage safety standards, so as to improve the effectiveness of domestic safety technical standards for hydrogen storage in fuel cell vehicles, and provide reliable technical support for the rapid development of hydrogen energy industry in the future.
Author contributions
SZ: Writing–review and editing. CD: Writing–review and editing. XH: Writing–original draft, Writing–review and editing. YT: Visualization, Writing–review and editing.
Funding
The author(s) declare that no financial support was received for the research, authorship, and/or publication of this article.
Conflict of interest
SZ was employed by Tianjin Key Laboratory of Dredging Engineering Enterprises, CCCC Tianjin Dredging Co., Ltd.
The remaining authors declare that the research was conducted in the absence of any commercial or financial relationships that could be construed as a potential conflict of interest.
Publisher’s note
All claims expressed in this article are solely those of the authors and do not necessarily represent those of their affiliated organizations, or those of the publisher, the editors and the reviewers. Any product that may be evaluated in this article, or claim that may be made by its manufacturer, is not guaranteed or endorsed by the publisher.
References
General Administration of Quality Supervision (2017). Inspection and quarantine of the people’s Republic of China. GB/T 24548-2009 fuel cell electric vehicles - Terminology. Available at: https://www.doc88.com/p-1196366204744.html.
General Administration of Quality Supervision (2022). Inspection and Quarantine of the People’s Republic of China. GB/T 26990-2011 Fuel cell electric vehicles - Onboard hydrogen system - specifications. Available at: https://www.doc88.com/p-97339666639702.html.
General Administration of Quality Supervision (2018). Inspection and Quarantine of the People’s Republic of China. GB/T 35544-2017 Fully-wrapped carbon fiber reinforced cylinders with an aluminum liner for the on-board storage of compressed hydrogen as a fuel for land vehicles. Available at: https://www.doc88.com/p-38939428039628.html.
Guo, S., Liu, D., Sun, F., Xue, H., and Gao, Z. (2020). Interpretation of type test contents of hydrogen storage tank in GTR13. Low Temp. Specialty Gases 38 (3), 50–54. doi:10.3969/j.issn.1007-7804.2020.03.013
Li, J., Gao, C., Lu, X., and Hoseyni, A. (2022). A combined energy system consisting of fuel cell, water electrolyzer and solar technologies to produce hydrogen fuel and electricity. Energy Sources, Part A Recovery, Util. Environ. Eff. 44 (1), 1173–1188. doi:10.1080/15567036.2022.2055680
Lin, X., Liu, Y., Shao, J., Zhao, X., and Xu, Q. (2021). Emission reduction benefit analysis of hydrogen fuel cell vehicle replacing fuel vehicle. Sci-tech Innovation Prod. (9), 77–81. doi:10.3969/j.issn.1674-9146.2021.09.077
State Administration for Market Regulation, Standardization Administration (2023). GB/T 18384-2020 Electric vehicle safety requirements. Available at: https://www.doc88.com/p-67461203001290.html.
State Administration for Market Regulation, Standardization Administration (2021). GB/T 24549-2020 Fuel cell electric vehicles — safety requirements. Available at: https://www.doc88.com/p-70487649833717.html.
State Administration for Market Regulation, Standardization Administration (2022). GB/T 26779-2021 Hydrogen fuel cell electric vehicle refueling receptacle. Available at: https://www.doc88.com/p-11161997994997.html.
Sun, C., and Zhang, H. (2022). Review of the development of first-generation redox flow batteries: iron-chromium system. ChemSusChem 15 (1), e202101798. doi:10.1002/cssc.202101798
UN GTR. (2018). 13 Global technical regulation concerning the hydrogen and fuel cell vehicles. Available at: http://www.unece.org/trans/main/wp29/wp29wgs/wp29gen/wp29glob_registry.html, 2018 .
Yan, S., Yang, M., Sun, C., and Xu, S. (2023). Liquid water characteristics in the compressed gradient porosity gas diffusion layer of proton exchange membrane fuel cells using the Lattice Boltzmann method. Energies 16 (16), 6010. doi:10.3390/en16166010
Yuan, H., Dai, H., Wei, X., and Ming, P. (2020). Model-based observers for internal states estimation and control of proton exchange membrane fuel cell system: a review. J. Power Sources 468, 228376. doi:10.1016/j.jpowsour.2020.228376
Keywords: fuel cell vehicle, compressed hydrogen storage, safety technical specification, GTR13, UN/WP29
Citation: Zhu S, Ding C, Hu X and Tian Y (2024) Analysis of safety technical standards for hydrogen storage in fuel cell vehicles. Front. Energy Res. 12:1376739. doi: 10.3389/fenrg.2024.1376739
Received: 26 January 2024; Accepted: 20 June 2024;
Published: 22 July 2024.
Edited by:
Jianxin Zou, Shanghai Jiao Tong University, ChinaCopyright © 2024 Zhu, Ding, Hu and Tian. This is an open-access article distributed under the terms of the Creative Commons Attribution License (CC BY). The use, distribution or reproduction in other forums is permitted, provided the original author(s) and the copyright owner(s) are credited and that the original publication in this journal is cited, in accordance with accepted academic practice. No use, distribution or reproduction is permitted which does not comply with these terms.
*Correspondence: Xing Hu, hux@sdju.edu.cn