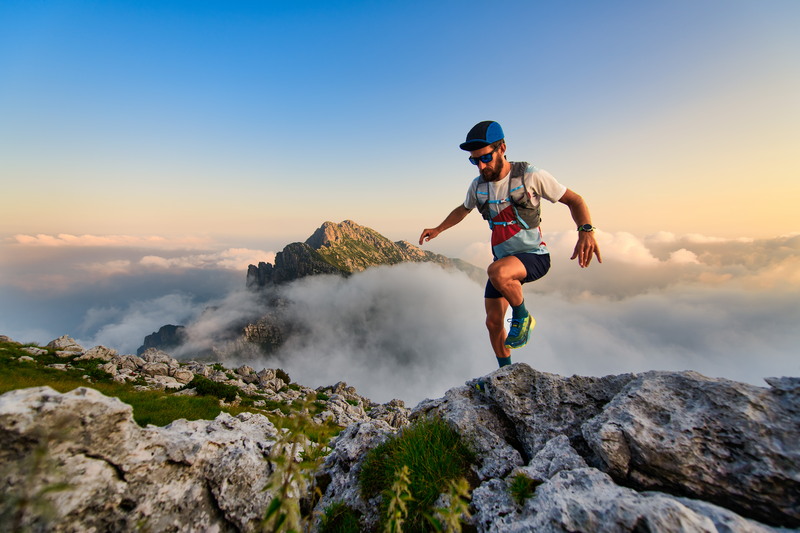
95% of researchers rate our articles as excellent or good
Learn more about the work of our research integrity team to safeguard the quality of each article we publish.
Find out more
PERSPECTIVE article
Front. Energy Res. , 20 March 2024
Sec. Nuclear Energy
Volume 12 - 2024 | https://doi.org/10.3389/fenrg.2024.1359688
This article is part of the Research Topic Shaping the Future of Nuclear Assets with Digital Twins View all 7 articles
Digital twins (DT) are synchronized clones that mirror their physical counterparts at all times, enabling real-time monitoring, analysis, decision-making, and planning for optimized operations. Digital twins can transcend traditional two-dimensional interfaces by incorporating VR/AR/MR (XR) technology, providing immersive, intuitive, and interactive representations of systems, assets, and processes. Furthermore, real-time data from sensors, simulations, and other sources can be integrated into the XR-enabled digital twins, leading to better and more intuitive understanding and to more efficiently monitor, analyze, and maintain complex systems such as nuclear assets. Immersive, interactive, multi-player XR capabilities embedded in DTs will allow spatially accurate and more realistic representation, leading to improved risk assessment, optimized and predictive maintenance scheduling, enhanced situational awareness, and more effective communication among interdisciplinary teams. By combining the strengths of XR and digital twins, nuclear facilities can achieve heightened safety, operational efficiency, and decision-making accuracy. Marrying XR technology with digital twins is also likely to extend the utilization of digital twins to optimize those aspects of the design and operation of nuclear assets that involve human beings–specifically in human factors engineering. Training can also be significantly enhanced if DTs are linked with XR technology. These systems may also be used to assess human performance through human factors engineering for the safety analysis of nuclear assets. A specific example is assessing human performance in semi-autonomous nuclear assets or operating multiple nuclear assets. After briefly reviewing digital twins of nuclear systems from the perspective of XR technology, this paper summarises our work in the nuclear energy space on VR/AR/MR and how these can be integrated into the newly evolving DTs of nuclear assets. The paper also describes the potential use of such systems in optimizing the design and operations of nuclear systems. As XR technology advances, its symbiotic relationship with digital twins can significantly reshape the landscape of nuclear operations and asset management.
Significant advances over the past 20 years in computing and digital technology have resulted in the emergence of artificial intelligence (AI) and virtual reality (VR) as two of the most promising and groundbreaking enabling technologies. While AI and Machine Learning (ML) are slowly gaining traction in the nuclear sector for various applications, the widespread integration of VR technology, which has been around in a fairly mature form for longer than the AI, is yet to be realized.
This paper aims to shed light on the untapped potential of integrating VR technology with digital twins for nuclear asset management. VR is not presently utilized in DTs of NPP. Instead, we propose it as an integrable technology to DTs, introducing an additional layer to human vision and perception. This paper presents a perspective (derived through various studies) that anticipates a reduction in cost and time when used to include direct human involvement in designing and evaluating semi-autonomous DT components. Furthermore, VR is highlighted as a significant enhancer of human perception that has the potential for intuitive visualization of real-time data of DTs, surpassing traditional 2D screens. By exploring the possibilities and benefits, this paper aims to inspire and motivate researchers to delve deeper into the realm of VR technologies, fostering innovation and advancements in nuclear science and technology in the context of digital twins.
The term digital twin refers to any virtual representation of a physical system, such as a turbine, a chemical plant, or an automobile. Yadav et al. (2021) noted that the term digital twin can have different definitions based on context and industries. Generally, the terms digital twins or digital twin system refer to a digital representation of a currently existing or under-design physical counterpart. When the physical system is already in existence, there is a link between the physical system and its digital twin. This connection facilitates the continuous data exchange between the two systems. The digital twin is expected to be in the same state as that of the physical system at all times. If the prediction by the digital twin deviates from the actual state of the physical system at any time, the data from the physical system is used to correct and bring the digital twin in conformity with the current state of the physical system. Among other goals, digital twins are expected to be used to predict the future state for operational management and planning. DTs are to be used for monitoring, diagnostics and prognostics, and to optimize asset performance and utilization. By combining sensory data with past experience (through AI) and human expertise, DTs can be used to improve performance and productivity.
As technology advances, it is crucial to explore the use of other emerging and enabling technologies that can be integrated in digital twins. While continuously advancing computing and AI/ML are likely to impact the evolution of digital twins in many ways, VR (and its variations) is in a unique position to help integrate humans and introduce realistic human-machine-interface in the digital twin. This is likely to address ergonomics, evaluation of human factors, and human interactions with machines through realistic digital interfaces. Introduction of VR in digital twins will allow to more realistically capture and simulate the important role that humans play in the operation of any physical system. The subsequent sections will delve into different types of VR technologies and some of their applications in academia and in the nuclear industry. This will be followed by a discussion on the prospects of integration of VR in digital twins.
Virtual Reality (VR) comprises of technologies that enable immersive human interaction with digitally created entities. VR refers to technology and devices in which the user is completely immersed in the digital world, with no interactions with the physical surroundings. The user in VR may interact with the digital content. While current VR technologies primarily focus on stereoscopic vision for complete 3-D immersion, ongoing advancements aim to enhance immersion by targeting additional senses such as haptic, taste, and olfactory, mimicking even more realistic real-world experiences. VR hardware over the last few decades has evolved from the early million-dollar CAVE systems to few-hundred-dollars head-mounted displays (HMDs), to even few-dollars cardboard boxes in which regular smart phones can be used to experience 3-D immersion. Software for application development has also evolved from early developments being done in OPEN-GL to modern game development platforms (Early VR technologies, like the CAVE, and their use in the nuclear field are discussed in Rizwan-uddin et al. (2003). Head-mounted displays (HMDs) are the most recent technological developments in VR. Discussion in this article is limited to HMDs.)
Extensions of VR have led to augmented (AR) and mixed reality (MR). Augmented reality (AR) entails experiencing the physical and the digital (virtual) worlds simultaneously, through inputs such as vision. It is, for example, achieved by seeing the physical world through the transparent part of the HMD’s screen, while simultaneously having access to digital contents on another part of the HMD. The digital content can even be overlaid on the physical objects. In general, there is none to very limited interactivity in AR between the user and the digital content. Currently the most advanced of these technologies is called mixed reality (MR). MR is AR with interactive digital content. Feeding AR devices with sensory inputs and data from the physical system allows interactivity between the digital content and the physical world. Most XR devices are now incorporating some MR capabilities, for example, in the form of depth sensors or interactive digital/virtual drop-down menu (Note that the definition of VR, AR, MR and other similar terms such as extended reality (XR, a term sometimes used to collectively refer to AR, MR and VR) are continuously evolving.)
Research and development in virtual technology for nuclear applications can be traced back to the early 2000s in Karancevic and Rizwan-uddin (2003) and Andritsos et al. (2004). That was pre-HMD period. Earlier developments included walk-through models of nuclear power plants and 3-D models of other assets that could be visualized in VR hardware. Later developments included several interactive capabilities such as “displaying” the radiation field in 2-D and 3-D and virtual interactive models of modern control rooms. As in academia, nuclear industry has also taken only limited advantage of advances in the VR technology (Pitkänen, 2020). Outsourcing the development of the VR models and early VR hardware had both been expensive. However, decreasing cost of VR hardware and increasing awareness and familiarity of the new workforce with this technology are making VR more appealing to the nuclear industry. There is recognition that the VR technology can be effectively used for education and training, as well as in dose minimisation efforts at nuclear power plants (NPPs). There is potential for VR to transform safety protocols, training methods, and operation and maintenance practices within the nuclear sector. State of specific aspects of VR and its use in the nuclear sector–both, industrial and academic–are reviewed in the following subsections.
Minimising the dose that workers receive when working in radiation environment is critical. Minimising the amount of time spent around radiation and avoiding the high radiation areas whenever possible will help in dose minimisation. Familiarity with the work environment, familiarity with the radiation field in the work area, and excessive practice of the task to be completed can significantly reduce the amount of time workers spend in radiation environments and thus the total dose they receive. Ideally, a facility that is an identical twin of the workspace, but without the radiation, can be used for training the workforce. Radiation-related situational awareness can be communicated in this physical twin by marking high and low radiation areas. This is however an expensive preposition. On the other hand, VR technology excels in communicating spatial awareness and 3-D visualization, and is inexpensive. Any VR experience in the virtual equivalent of a physical space is likely to be remembered and impact actions and behavior when the user is later operating in the corresponding physical space. Employing VR to train for work in such a harmful environment offers a much simpler and more cost effective approach. Not only the worker can become familiar with the space in which work needs to be performed, even the radiation levels in different parts of the virtual 3-D facility can be shown. By developing a virtual replica of the workspace, workers can be trained in a safe and radiation-free environment, and develop situational and radiation awareness before setting foot in the hazardous physical workspace.
Hanifah et al. (2017) reported the culmination of efforts that resulted in a virtual dose minimization game that can be played on smart phones. The game was initially developed for computers and immersive devices. The game is played in a 3-D virtual model of the TRIGA Mark II1 nuclear reactor, which was located at the University of Illinois campus in Urbana (Yoshinori et al., 2014). This virtual model has gone through several upgrades. This model is a fairly accurate and to-scale representation of the TRIGA facility. The facility had several levels, with the reactor bay near the center. Stairs led to the top of the bay. The neutron beam lines were in the large open area at the lowest level. The virtual, 3D, interactive model of the TRIGA research reactor was created using the Unity-3D game engine. It allows users to explore the facility. This virtual facility was selected for the dose minimization game as it is a multi-level building with several floors and many rooms, making the game challenging and engaging. For the dose minimization game, this model is used as a facility with varying levels of radiation due to multiple (virtual) radiation sources of different strengths, stored in different locations in the multi-level building, leading to a realistic radiation field. Additionally, virtual objects are placed in the building, which are to be collected by the player. In this scavenger hunt game, the player is to navigate through the reactor building and collect the desired objects while receiving minimal radiation dose. This game built upon capabilities developed earlier that included the capability to display the radiation level in the 3-D virtual model of a facility by coloring the floor. The display of the radiation level can be turned on or off. Virtual dosimeter developed earlier, is also integrated in this dose minimisation game. Player simply picks up the dosimeter and starts performing the assigned tasks. Based on the radiation level, location of the player and time spent, a counter at the bottom of the screen shows the dose received. Dosimeter feature can also have a beeping sound similar to that of a Geiger counter. At the end of the game, the dose received (in mSv), the time duration over which the radiation map was viewed, and a score based on these two factors, are displayed. Player can thus learn about three important concepts in radiation protection: time, distance, and shielding. The radiation field in these models is provided as an input. It can be pre-calculated using radiation transport codes such as MCNP, or a simplified version of the field can be on the fly calculated using simple point kernel type method (Rizwan-uddin, 2018; Hagita et al., 2020).
The virtual model of the reactor facility was used in a study to assess the feasibility of using 3-D models to train personnel for operations in an alien environment (Kriz et al., 2010) through prior training in the virtual 3-D model of the facility.
Nuclear decommissioning poses significant challenges due to potential exposure to high radiation levels. VR has been shown to be effective in training workers for decommissioning scenarios, addressing the critical need to prepare them for handling radioactive materials during decontamination and decommissioning. A VR training system was proposed by Jeong et al. (2014) to enhance safety during nuclear power plant decommissioning, emphasizing a framework for system development and the inclusion of multiplayer capabilities. While the study demonstrated improved worker familiarity with the environment, data were lacking. A subsequent study (Jeong et al., 2016) provided extensive results, focusing on ergonomic assessment in a radiation environment. The study assessed optimal postures for descending in various scenarios, acknowledging limitations in evaluating postures due to the restricted motion control using mouse and keyboard controls. Despite the limitations, these studies offer a foundation for the future use of VR in nuclear power plant operations, as well as decontamination and decommissioning. Another study by Sato et al. (2020) also discusses the use of VR and 3D imaging technique for visualization of radioactive substances during decommissioning training.
VR provides a cost effective method of “hands on” training with equipment. It can also be used to conduct virtual experiments in a virtual lab to better communicate physics concepts (Rizwan-uddin, 2020; Ilie, 2021). It can be used to supplement physical labs in academia, and equipment training in industry. The Virtual Education and Research Laboratory (VERL) at the University of Illinois at Urbana-Champaign has developed 3-D and VR models, including labs for radiation shielding experiment, half-life measurement experiment, and calorimetry experiment. These virtual labs offer hands-on experience, integrating cutting-edge virtual technologies into education (Xi et al., 2009; Haddish et al., 2013; Satoh et al., 2015). Some of these are briefly described below.
One of the first developed for nuclear applications, the player in this virtual lab can measure the attenuation coefficients of four different materials. This VR lab aims to provide a highly realistic environment, emphasizing lifelike graphics, detailed 3-D models, textures, and realistic lighting to enhance immersion. While the physics is simple, the focus is on crafting an intricately detailed setting. The model is shown in Figures 1A, B. The goal of this lab is to make users feel present in the lab environment when doing the experiments. Users can manipulate shielding blocks made of different materials, place multiple blocks between the radiation source and the detector, thus effectively changing the thickness of the shielding, and operate the radiation measurement equipment. The student clicks on the shielding blocks placed on the table, which moves them next to a scale, allowing the student to measure their thickness. Next, clicking on the block moves it to the space between the radiation source and the detector. Counts can then be measured by setting the time interval and clicking on the counter button. The process is repeated for different numbers of shielding blocks, thus gathering data for different thicknesses. The entire process can then be repeated for blocks made of different materials. The physics model is based on the attenuation model (e-μΔ x), where Δ x is the thickness of the shielding material. The data displayed is realistic and can be used to estimate the attenuation coefficient of the shielding material. The virtual model has gone through several upgrades over the years. Figure 1A shows the virtual lab. Figure 1B shows two of the shielding blocks placed in between the radiation source (on the left) and the detector (on the right). Other shielding blocks (C, D and E) are placed on the table. Collimator blocks can also be seen.
Figure 1. Pictures showing (A) Side by side comparison of the virtual and physical labs (B) Virtual model of the shielding lab, and (C,D) show VR calorimetry lab.
The virtual calorimetry lab is designed to measure the specific heat of metals. This laboratory has virtual instruments (like scale and hotplate) and virtual monitors. Virtual instruments in the model are interactive, and can be moved and/or operated by the player. For example, the specimens in the experiment can be moved. When a specimen is placed on the scale, the virtual scale displays its weight in its digital window. The virtual hotplate can (virtually) heat the objects placed on it (Figure 1C). Clicking the knob on the hotplate turns it on/off. Thermocouples can be connected to objects. The temperature is displayed on the computer monitor in real time. Step-by-step instructions are displayed through GUI. Steps include measuring the mass of the metal specimens, heating the water to 100°C (when the temperature reaches 100 C, bubbles are generated in the beaker), heating the specimen to 100°C by placing it in the boiling water, measuring and pouring water at room temperature (20°C) in the calorimeter, placing the specimen in the calorimeter, attaching the thermocouples, and observing and noting down the temperature change on the virtual computer screen. A simple physics model based on conservation of thermal energy is coded to evaluate the temperature of the water and the metal specimen as a function of time.
A recent improvement is the introduction of improved haptic feedback with new controllers. Through the Virtual Grasp API,2 users can hold two objects, like beakers and metal specimens (at any angle, to facilitate the pouring action), in two different hands as shown in Figure 1C, mimicking real lab setups. The sensation of different weights can be replicated using strong or gentle haptic vibrations. Another improvement made in this lab is by making the lab setup more realistic. For example, a single click in the older version connected a wire (such as a thermocouple) to its intended location. The user in the new version can “grab” the tip of the wire and then “insert” it at the desired port or object where it needs to be connected (Figure 1D).
3-D model of the TRIGA reactor facility described in Section 4.1 (Stefano and Rizwan-uddin, 2006) was used to develop the TRIGA reactor lab. A virtual control room, very similar to the actual control room, was developed to conduct reactor experiments. The development process of the virtual reactor consists of three major parts: 3D modeling; event scripting; and user interactions. Specifically, the buttons and knobs in the virtual control room were made interactive, and a reactor physics model was added to determine the reactor behavior in response to specific operator actions. Point reactor kinetics (one delayed neutron precursor) with simplified thermal (fuel temperature) feedback model is implemented to determine the real time reactor response to operator actions. Measured differential rod worth tables from the original reactor are used to determine the amount of reactivity that is inserted for each rod at each rod position. Reactivity and power levels are displayed on the panel. This virtual model of the reactor allows users to explore the facility, and virtually operate the reactor from the control room.
Figure 2A shows the reactor control room in the virtual model. Reactor bay can be seen through the glass panel in front of the control desk in Figure 2B shows a zoomed-in view of the control panel. Figure 2C shows additional parts of the control panel. The buttons and knobs of the control panel in the model are interactive, and can be operated by the player or operator. The power key, the switch labeled FIRE and the knob labeled TR SELECT in the left side of Figure 2C; and switches labeled AIR, MAGNET, UP, DOWN, ACKNOWLEDGE, and SCRAM in the right side of Figure 2C can be manipulated (clicked on) by the operator. For example, a supervisor must turn the (virtual) power key to the ON position before any other action can be carried out. Clicking on the Fire button fully raises the transient rod, which is one of the control rods.
Figure 2. Virtual models of UIUC TRIGA reactor. (A) A view of the control room. (B) A close-up control panel view. (C) Further close-up views of the right and left sides of the control panel shown in (B).
Several other features reported earlier—such as displaying the radiation level by coloring the floors, virtual dosimeter, in-game step-by-step instructions, and remote security cameras—have also been implemented in this reactor model. Virtual and interactive research reactor model is fairly realistic. It can be used to supplement reactor lab experience for students as well as reactor operators. If used judiciously, it offers a cost effective approach to enhance reactor operations experience.
Key contribution in another study (Kiryukhin et al., 2020), focused on replicating a graphite-uranium subcritical (GUS) assembly experiment, is in visualizing neutron flux in 3-D (in VR) using pre-calculated data.
The need to develop virtual models of NPP control rooms first arose when there was a desire to assess conversion of analog control rooms in currently operating NPPs to digital control rooms, and to develop fully digital control rooms for advanced NPP designs. Issues surrounding human factors, personnel interactions, line of sight, and situational awareness, could potentially be researched and addressed using 3D virtual models of NPP control rooms. However, VR’s limitations, including resolution issues, susceptibility to motion sickness, discomfort, limited field of view, and restricted haptic feedback, have so far hindered its widespread adoption as an alternative for control room training.
Simulators for nuclear power plant control room (NPP-CR), to be used for design and training, can include multiple components such as control consoles, simulation software, safety systems, communication setups, and more. Transforming these elements into VR requires integration across domains, including 3-D designers, software developers, and CR operators. Bergroth et al. (2018) report the use of VR in control room assessment. Experienced NPP operators participated in this study, which was centered around operator response in an emergency scenario. The crew had to follow procedural instructions in VR. The crew identified (through questionnaires on monitoring, operation, and procedural adherence) VR’s limitations, such as resolution challenges, communication, and lack of tactile feedback during operation. The study suggested that with improvements, Virtual Reality Control Rooms (VR CR) can offer realistic early-stage design and ergonomic evaluation (Gatto et al., 2013; Lee and Cha, 2019), facilitating flexible design changes and cost savings (Qin et al., 2020) through multiple validations before physical modification. This study provides a blueprint for VR development in control room training, addressing both human and technical factors.
Another study (Pitkänen, 2020) briefly outlines the tools used to construct the VR CR model. A notable aspect in this study is the introduction of small VR simulator applications, offering fundamental VR training before participants enter more complex environments like a control room simulator. These applications, covering fire safety evacuation and valve operation training, proved highly beneficial for participants unfamiliar with VR, helping them become acquainted with the technology, evident in comprehensive participant ratings expressing satisfaction with the virtual CR experience.
Digital twins of various assets in the NPPs and of entire nuclear power plants promise a framework in which a digital and time-synchronized replica of the asset is available to the operators. These DTs can be used for operational and planning purposes.
DTs have so far been in general described as uber-simulators, available on (2D) computer screens. DTs on their own do not have any three-dimensional equivalence with the actual equipment or plant they represent. This lack of 3-dimensionality in DTs restricts embedding of humans in the loop in a realistic fashion. Thus, assessments and studies that involve humans cannot be realistically carried out on classical DTs. Thus, integrating DTs and VR is likely to improve DTs in three significant ways. First, a VR/AR/MR (XR) model of the equipment or the facility will allow a much more realistic training environment for the workforce, enhancing the safety and ergonomic considerations of NPPs and their assets. The immersive visualizations facilitated by VR will offer a considerable advantage in the real-time monitoring of nuclear assets. Second, it will provide situational awareness (around the equipment) to the plant operators as they take advantage of the DT to improve operational efficiency through the control and management of nuclear assets. XR will enhance decision-making capabilities by overlaying critical data directly in front of equipment operators. And third, VR+DT systems will allow human factor studies to be conducted on DT providing valuable feedback in the design and manufacturing stages of NPP’s lifecycle by employing human operators in the virtual framework of the digital twin.
There have been limited integration or even discussion of integration of DTs and VR thus far in any industry. One recent study (Coupry et al., 2021) reviewed literature on DTs of building information modeling (BIM) and XR devices to improve maintenance procedures in smart buildings. This is a fairly exhaustive review with a large bibliography and extensive review of both, DT and XR technologies. From varying definitions of “digital model,” “digital shadow,” and “digital twin,” to ever rapidly evolving XR technologies, authors have extensively discussed the background as well as potential use of XR with DTs. This review goes beyond just the application of these technologies to building maintenance. Demonstrations of the use of the XR technology to nuclear applications discussed in the previous sections are similar to what is being implemented in other industries. Thus, integration of XR in DT of nuclear systems can also benefit from similar efforts in other industries, such as building maintenance.
There are two areas specific to nuclear that may benefit from the integration of XR in DTs more than in some other industries. First is the assessment of human performance, and the second is the facilitation of semi-autonomous control and operations of nuclear assets. During the design phase of semi-autonomous digital twin (DT) systems, evaluating their interaction with humans is crucial. Gathering direct data on human interaction becomes essential for conducting risk and ergonomic assessments throughout the design process of these semi-autonomous systems. Traditionally, gathering such data should involve iterative changes to the physical components based on their interaction with humans, incurring both cost and time; virtual generation of this data facilitated through VR can be cost-effective and faster. Furthermore, XR devices have the potential to enhance semi-autonomous control and operations in the nuclear asset management of DTs. They can offer operators an immersive interface, projecting 3D representations and real-time data overlays directly onto physical components. When integrated with IoT sensors, XR can facilitate emergency responses and foster collaborative decision-making, potentially improving overall plant efficiency and ensuring a safer and more responsive nuclear power plant operation.
Kuts et al. (2019) described the synchronized control of industrial robotic cell through a combination of its digital twin and VR. This is of relevance to the nuclear industry as with better VR controls, it will be feasible to manage nuclear assets in 3-D in real-time using robotics, networking, and low-latency IoT devices, offering increased precision and safety. Overseeing of semi-autonomous assets using DTs, especially those assets that employ machine learning (ML) and artificial intelligence (AI) for safety and maintenance decisions, may be facilitated by improved training on a combination of DT and XR.
Integration of VR with DT can play a pivotal role in nuclear asset management, evident by ongoing technological advancements aligning with the sector’s specific needs. This integration of VR and digital twins is expected to create a symbiotic relationship covering the entire lifecycle of nuclear asset management, including human factor studies. Despite limited studies, increased research engagement is expected to expedite its implementation. This paper provides insights into potential VR and DT applications, urging further exploration. It also advocates for additional research to enhance the reliability of VR-DT systems and position them as a cost-effective alternative in nuclear asset management.
The raw data supporting the conclusion of this article will be made available by the authors, without undue reservation.
SR: Conceptualization, Formal Analysis, Writing–original draft. SS: Investigation, Validation, Writing–review and editing. R-u: Investigation, Supervision, Validation, Writing–review and editing.
The authors declare that no financial support was received for the research, authorship, and/or publication of this article.
We would like to acknowledge the large number of undergraduate students in NPRE and other departments at the University of Illinois at Urbana Champaign who, over the last 20 years, have contributed to the work reviewed here.
The authors declare that the research was conducted in the absence of any commercial or financial relationships that could be construed as a potential conflict of interest.
All claims expressed in this article are solely those of the authors and do not necessarily represent those of their affiliated organizations, or those of the publisher, the editors and the reviewers. Any product that may be evaluated in this article, or claim that may be made by its manufacturer, is not guaranteed or endorsed by the publisher.
1https://distributedmuseum.illinois.edu/exhibit/triga-mark-ii-nuclear-reactor/
2https://www.virtualgrasp.com/
Andritsos, D., Griffith, J., Karancevic, N., Jevremovic, T., Stubbins, J., and and Rizwan-uddin, (2004). INIE collaboration between UIUC and Purdue on virtual reactor development. Trans. Am. Nucl. Soc. 91, 992–993.
Bergroth, J. D., Koskinen, H. M. K., and Laarni, J. O. (2018). Use of immersive 3-D virtual reality environments in control room validations. Nucl. Technol. 202, 278–289. doi:10.1080/00295450.2017.1420335
Coupry, C., Noblecourt, S., Richard, P., Baudry, D., and Bigaud, D. (2021). BIM-based digital twin and XR devices to improve maintenance procedures in smart buildings: a literature review. Appl. Sci. 11, 6810. doi:10.3390/app11156810
Gatto, L. B. S., Mól, A. C. A., Luquetti dos Santos, I. J., Jorge, C. A. F., and Legey, A. P. (2013). Virtual simulation of a nuclear power plant’s control room as a tool for ergonomic evaluation. Prog. Nucl. Energy 64, 8–15. doi:10.1016/j.pnucene.2012.11.006
Haddish, I., Rizwan-uddin, , and Li, Y. (2013). “Fully interactive virtual labs for training and education,” in Proc. Conference on Nuclear Training and Education CONTE 2013 (Jacksonville, FL: American Nuclear Society).
Hagita, K., Kodama, Y., and Takada, M. (2020). Simplified virtual reality training system for radiation shielding and measurement in nuclear engineering. Prog. Nucl. Energy 118, 103127. doi:10.1016/j.pnucene.2019.103127
Hanifah, Z., Mattingly, G., Riewski, E., Tan, Q., Chun, D., and and Rizwan-uddin, (2017). “Recent developments in virtual dose minimization game for education, training and outreach,” in ETrap 2017, Valencia, Spain, 30 May 2017 - 2nd June 2017.
Ilie, R. (2021). Developing virtual reality labs for EM courses, VRIllinois. Available at: https://vr.illinois.edu/2021/04/21/developing-virtual-reality-labs-for-em-courses/ (Accessed December 17, 2023).
Jeong, K., Choi, B., Moon, J., Hyun, D., Lee, J., Kim, I., et al. (2014). The scenario-based system of workers training to prevent accidents during decommissioning of nuclear facilities. Ann. Nucl. Energy 71, 475–479. doi:10.1016/j.anucene.2014.04.033
Jeong, K., Choi, B., Moon, J., Hyun, D., Lee, J., Kim, I., et al. (2016). An evaluation on the scenarios of work trajectory during installation of dismantling equipment for decommissioning of nuclear facilities. Ann. Nucl. Energy 91, 25–35. doi:10.1016/j.anucene.2016.01.002
Karancevic, N., and and Rizwan-uddin, (2003). Virtual systems for understanding and advancement of nuclear power. Trans. Am. Nucl. Soc. 88.
Kiryukhin, P., Shcherbakov, A., Romanenko, V., Pugachev, P., Khomyakov, D., Tikhomirov, G., et al. (2020). Development of a virtual analogue of uranium-graphite subcritical assembly and visualization of the neutron flux distribution in virtual reality. Procedia Comput. Sci. 169, 192–197. doi:10.1016/j.procs.2020.02.135
Kriz, Z., Wu, H., Aaron, M. C., Rytych, C., Conley, L., Prochaska, R., et al. (2010). An assessment of a game-like 3-D model for training at NPPs. Trans. Am. Nucl. Soc. 102, 65–66.
Kuts, V., Otto, T., Tähemaa, T., and Bondarenko, Y. (2019). Digital twin based synchronised control and simulation of the industrial robotic cell using virtual reality. J. Mach. Eng. 19, 128–144. doi:10.5604/01.3001.0013.0464
Lee, H., and Cha, W. C. (2019). Virtual reality-based ergonomic modeling and evaluation framework for nuclear power plant operation and control. Sustainability 11, 2630. doi:10.3390/su11092630
Pitkänen, V. (2020). “Utilization of virtual reality in loviisa nuclear power plant,”. Master’s Thesis (Finland: LUTPub).
Qin, S., Wang, Q., and Chen, X. (2020). Application of virtual reality technology in nuclear device design and research. Fusion Eng. Des. 161, 111906. doi:10.1016/j.fusengdes.2020.111906
Rizwan-uddin, (2018). Virtual reality for education, training and dose reduction. Nucl. Plant J. 36, 30–33. Online/Virtual.
Rizwan-uddin, (2020). “Role and status of VR/AR/MR in digital twins in the nuclear industry,” in Presentation at the Workshop on Digital Twin Applications for Advanced Nuclear Technologies (INL/ORNL) Virtual/online.
Rizwan-uddin, , Karancevic, N., and Tikves, S. (2003). “Virtual reality: at the service of GEN-IV, and V,” in Proc. Int Congress Advances in Nuclear Power Plants, Cordoba, Spain, May 4 2003 - May 7 2003.
Sato, Y., Minemoto, K., Nemoto, M., and Torii, T. (2020). Construction of virtual reality system for radiation working environment reproduced by gamma-ray imagers combined with slam technologies. Nucl. Instrum. Methods Phys. Res. Sect. A Accel. Spectrom. Detect. Assoc. Equip. 976, 164286. doi:10.1016/j.nima.2020.164286
Satoh, Y., Zhu, X., Li, Y., Kuprianczyk, C. A., and and Rizwan-uddin, (2015). “Virtual research reactor with interactive control room for reactor operator training,” in Proc. 9th International Topical Meeting on Nuclear Plant Instrumentation, Control, and Human-Machine Interface Technologies 2015, February 22–26, 2015, (Charlotte: American Nuclear Society), 1589–1596.
Stefano, M., and and Rizwan-uddin, (2006). “A virtual control room with an embedded, interactive nuclear reactor simulator,” in Proc. 5th International Topical Meeting on Nuclear Plant Instrumentation Controls, and Human Machine Interface Technology 2015, Albuquerque, USA, 675–679.
Xi, C., Wu, H., Joher, A., Kirsch, L., Luo, C., Khasawneh, M., et al. (2009). “3-D virtual reality for education, training and improved human performance in nuclear applications,” in Proc. 6th American Nuclear Society International Topical Meeting on Nuclear Plant Instrumentation, Control, and Human-Machine Interface Technologies 2009, Knoxville, Tennessee, April 5-9, 2009 (LaGrange Park, IL: American Nuclear Society), 2347–2356.
Yadav, V., Zhang, H., Chwasz, C. P., Gribok, A. V., Ritter, C., Lybeck, N. J., et al. (2021). “The state of technology of application of digital twins,”. Tech. rep. (Washington, DC: U.S. Nuclear Regulatory Commission).
Keywords: virtual reality, augmented reality, mixed reality, human factors, digital twins, nuclear environments, real-time monitoring, asset management
Citation: Roy S, Singh S and Rizwan-uddin (2024) XR and digital twins, and their role in human factor studies. Front. Energy Res. 12:1359688. doi: 10.3389/fenrg.2024.1359688
Received: 21 December 2023; Accepted: 04 March 2024;
Published: 20 March 2024.
Edited by:
Prashant K. Jain, Oak Ridge National Laboratory (DOE), United StatesReviewed by:
Roberto Alonso González-Lezcano, CEU San Pablo University, SpainCopyright © 2024 Roy, Singh and Rizwan-uddin. This is an open-access article distributed under the terms of the Creative Commons Attribution License (CC BY). The use, distribution or reproduction in other forums is permitted, provided the original author(s) and the copyright owner(s) are credited and that the original publication in this journal is cited, in accordance with accepted academic practice. No use, distribution or reproduction is permitted which does not comply with these terms.
*Correspondence: Samrendra Roy, cm95c2FtQGlsbGlub2lzLmVkdQ==
Disclaimer: All claims expressed in this article are solely those of the authors and do not necessarily represent those of their affiliated organizations, or those of the publisher, the editors and the reviewers. Any product that may be evaluated in this article or claim that may be made by its manufacturer is not guaranteed or endorsed by the publisher.
Research integrity at Frontiers
Learn more about the work of our research integrity team to safeguard the quality of each article we publish.