- 1Exploration and Development Research Institute, Shengli Oilfield, Dongying, China
- 2National Key Laboratory of Deep Oil and Gas, China University of Petroleum (East China), Qingdao, China
- 3School of Petroleum Engineering, China University of Petroleum (East China), Qingdao, China
During the steam flooding of extra heavy oil, expansion of steam chamber is difficult and erosion channels appear, which is different from conventional heavy oil. The thermochemical composite system composed of steam, foam and viscosity reducer can effectively improve the development effect of extra heavy oil reservoirs. However, during the thermochemical composite flooding, the rheological characteristics of extra heavy oil and the influence of erosion channels on oil displacement mechanism are not yet researched. Taking the extra heavy oil reservoir in Block X of the Chunfeng Oilfield as an example, experimental research on the rheological properties and thermochemical composite flooding of extra heavy oil model with erosion channel is conducted. Firstly, the influence of thermochemical composite system on the rheological properties of extra heavy oil is evaluated. Then, a one-dimensional (1D) sand-pack model with erosion channel is used to conduct thermochemical composite flooding experiments, comparing the recovery of steam flooding, foam assisted steam flooding, viscosity reducer assisted steam flooding, and composite flooding (foam and viscosity reducer assisted steam flooding). Finally, a two-dimensional (2D) sand-pack model with erosion channel is used to conduct thermochemical composite flooding experiments, comparing the recovery of viscosity reducer assisted flooding and composite flooding. The results show that viscosity reducer reduces the viscosity of extra heavy oil greatly, and the extra heavy oil is not sensitive to the change of temperature after viscosity reduction. When the concentration of viscosity reducer is 0.4% or more, good viscosity reduction effect can be achieved at different oil-water ratio. In the 1D sand-pack model experiments, compared to steam flooding, foam assisted steam flooding, viscosity reducer assisted steam flooding, and composite flooding, the recovery increased by 4.38%, 17.38%, and 30.46%, respectively. In the 2D sand-pack model experiments, compared to steam flooding, the viscosity reducer assisted steam flooding and composite flooding increase the oil recovery by 12.49% and 16.61%, respectively. The thermochemical composite flooding of extra heavy oil is dominated by erosion, supplemented by displacement. There is a synergistic effect between chemicals in the process of composite flooding. At the same time, the purpose of “enhanced erosion and expanded sweep” is achieved.
1 Introduction
Heavy oil resources of China account for more than 20% of the total oil resources, and the annual output of heavy oil accounts for about 8% of China’s annual oil output (Sun et al., 2022). In order to meet the national demand for oil and gas resources, the development of extra heavy oil has attracted more attention (Liu and Dong, 2022). The Liaohe Oilfield has preliminarily revealed the production mechanism of steam flooding for extra heavy oil, emphasizing “erosion as the main mechanism and displacement as secondary” in field practice (Hu, 2020). Erosion refers to the high-temperature and high-pressure steam reducing the boiling point temperature of the reservoir liquid. When the temperature equals or exceeds the system’s boiling point temperature, the mixture will boil, causing the crude oil to be stripped through distillation action, transferring oil from dead pores to connected pores, thereby increasing the chances of oil displacement. In recent years, the thermochemical composite flooding technology to improve the development effect of extra heavy oil reservoir has become a research hotspot (Lyu et al., 2018; Liu YG. et al., 2020; Sun et al., 2023; Zhang et al., 2023). Compared with conventional heavy oil, extra heavy oil almost does not flow under formation conditions, but the erosion channel is easily formed between injection and production wells developed by steam flooding, and the synergistic mechanism of erosion and displacement is unclear in the process of field application. Therefore, it is urgently necessary to conduct experiments on the thermochemical composite flooding under conditions of non-piston erosion channels and to study the oil displacement mechanism in order to achieve efficient development of extra heavy oil.
Under the action of thermochemical agent, heavy oil can form emulsions, and there is a significant difference in rheological properties between heavy oil and emulsions (Alade et al., 2019a; Ahuja et al., 2021; Al-Anssari et al., 2021; Strelets and Ilyin, 2021; Zhu et al., 2021; Yadykova and Ilyin, 2022; Li et al., 2024). Jing conducted research on the relationship between startup stress and apparent viscosity. The study examined the effects of oil-water ratio, surfactant concentration, startup temperature, and constant shear rate on the maximum startup stress, leading to the establishment of a new startup pressure model (Jing et al., 2020). Zhang conducted experiments on the rheological characteristics of unstable heavy oil-water dispersion mixtures. The study systematically considered factors such as oil volume fraction, shear rate, and temperature, and investigated phase transition phenomena and stability in oil-water mixtures (Zhang et al., 2019). Li conducted a study using ultrasonic dispersion to prepare emulsions and observed their microstructural characteristics using optical microscopy and a nanometer particle size analyzer. The research aimed to investigate the influence of different surfactant concentrations, oil-water ratio, and dynamic conditions on the emulsion type and microstructural features. The rheological properties of water-in-oil (O/W) and oil-in-water (W/O) emulsions are also studied through experiments (Li et al., 2020; Ramírez-González and Quinones-Cisneros, 2020). Extra heavy oil, with higher viscosity, can reach 10,000 mPas under surface conditions. The changes in rheological properties before and after emulsification are more pronounced for extra heavy oil. Research on the rheological properties of extra heavy oil serves as the foundation for subsequent studies.
Some scholars have conducted a series of studies on the seepage characteristics of heavy oil thermochemical composite flooding. Numerous studies have shown that chemical agents assisted steam flooding can effectively reduce interfacial tension, leading to the emulsification of heavy oil into an emulsion, thus reducing the viscosity of heavy oil (Mohammadzadeh et al., 2019; Ahmadi and Chen, 2020; Huang and Babadagli, 2020; Wang et al., 2020; Pratama and Babadagli, 2022). Furthermore, chemicals have the capability to alter the wettability of rocks, making them more hydrophilic and enhancing the efficiency of steam flooding (Xi et al., 2019; Bruns and Babadagli, 2020; Tian et al., 2020; Zhai et al., 2022). Through the synergistic action of heat and chemicals, the development efficiency of heavy oil steam flooding is significantly improved (Li et al., 2019; Liu H. et al., 2020; Zhai et al., 2023). Through the seepage experiment of high temperature composite foam, Qi shows that when the liquid phase velocity is very low, the pressure difference almost does not change with the increase of gas phase velocity. However, with the increase of liquid phase velocity, the plugging pressure difference increases linearly with the increase of gas phase velocity (Qi et al., 2009). Alade uses the in-situ steam generation technology with the injection of thermochemical fluids to investigate the influence of different temperatures on recovery. The results indicate that at the injection temperatures of 100°C, 50 °C and 30°C, the pressures generated at the entrance of the core increase to 1,600, 1,200, and 280 psi, respectively, with recovery of 83%, 66%, and 54% (Alade et al., 2019b; Mahmoud et al., 2019; Alade et al., 2020; Alade et al., 2023). However, the predecessors mainly discussed the thermochemical composite flooding mechanism under the condition of forming high permeability layer in the process of thermal recovery of heavy oil. For extra heavy oil, the mobility difference is even greater, and the slender erosion channel is very easy to appear in the process of steam flooding. The erosion channel is filled with heavy oil with water and oil saturation lower than the residual oil saturation. The conventional thermochemical composite flooding mechanism cannot reflect the existence of erosion channel of extra heavy oil.
Therefore, taking the extra heavy oil reservoir in Block X of Chunfeng Oilfield as an example, the experiment of thermochemical composite flooding mechanism of extra heavy oil is carried out under the condition of erosion channel. At first, rheological experiments on the thermochemical composite system of heavy oil are conducted using a rheometer, considering the influence of temperature, shear rate, viscosity reducer concentration, and the oil-water ratio. Then, 1D displacement experiments are conducted to study the oil displacement mechanism of thermochemical composite flooding for extra heavy oil in the presence of erosion channels. Finally, 2D displacement experiments are conducted to investigate the oil displacement mechanism of thermochemical composite flooding for extra heavy oil in the presence of high-permeability zone. This study innovatively proposes an erosion channel sand-pack model, providing guidance for improving the development efficiency of thermochemical composite flooding for extra heavy oil. These findings provide valuable insights into the rheological behavior and displacement mechanisms of extra heavy oil under thermochemical conditions.
2 Experiment approach
2.1 Experimental materials
The extra heavy oil used for the experiment is extracted from Block X of the Chunfeng Oilfield. The viscosity of liquids is measured using rheometers (MCR302). At the reservoir temperature of 40°C, the viscosity of the crude oil is 28,768 mPas, with a density of 0.957 g cm-3, a gum content of 18.3%, and an asphaltene content of 12.2%. To ensure the accuracy and repeatability of the rheological testing experiment, the oil sample is pretreated. At first, the crude oil is degassed and dehydrated using a dehydrator. Then the oil sample is heated at a constant temperature of 40 °C for 4 h to achieve a relatively uniform state of internal molecules. Finally, the oil sample is cooled to room temperature to obtain the base oil sample for rheological testing.
The water used for the experiment is deionized water, prepared with standard saline solution with a mineralization degree of 13,000 mg L-1. The concentrations of Cl− and Mg2+are 7,551 mg L-1 and 332 mg L-1, respectively.
The viscosity reducer and foaming agent are provided by Sinopec Shengli Oilfield. The chemical agents are hydrophilic surfactants. The preparation process of crude oil emulsion is as follows: Firstly, a viscosity reducer solution is prepared by adding a viscosity reducer into water and stirring. Then, this viscosity reducer solution is added to the crude oil and stirred inside an emulsifier. Once the crude oil and viscosity reducer are thoroughly mixed, a stable emulsion is formed. The relationship curve between oil-water interfacial tension and viscosity reducer concentration is measured using an interfacial tension meter (TX-500C), as shown in Figure 1.
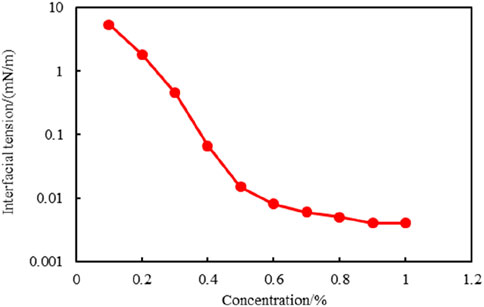
Figure 1. Relationship curve between oil-water interfacial tension and viscosity reducer concentration.
2.2 Oil and chemical agent property experiment
The high-temperature and high-pressure rheometer (MCR302) is used to obtain the rheological properties of extra heavy oil and emulsion and study the influence of viscosity reducer on the rheological properties of extra heavy oil. The experimental scheme is shown in Table 1.
The specific steps are as follows: At first, the air compressor is turned on. When the air compressor pressure reaches 5 MPa, the compressor valve is closed. Then, the rheometer is opened to initialize the instrument, and the rotor is installed for normal force adjustment. Finally, the sample is loaded to be tested. Viscosity-temperature curve test: The shear rate is 7.34 s-1, and temperature ranges from 0°C to 200°C, with measurements taken at 10°C intervals. Constant temperature variable shear test: The shear rate ranges from 0 to 100 s-1. The viscosity of heavy oil is tested at temperatures of 40°C, 100°C, 150°C, and 200°C. Each measurement is sampled separately, and the steps - are repeated.
2.3 Oil displacement experiments in 1D sand-pack model
2.3.1 Experimental equipment
As shown in Figure 2, the experimental equipment mainly includes: ISCO plunger pump, steam generator, foam generator, backpressure pump, intermediate container, sand-pack model with erosion channels, pressure sensor, etc. In order to reflect the formation of erosion channels during steam flooding of extra heavy oil, a sand-pack model with channels is used (Figure 3). The sand-pack model uses quartz sand mixed with extra heavy oil to fill the sand-pack model and quartz sand saturated formation water to fill the erosion channel in the center. The 40–70 mesh quartz sand are selected for the experiment and filled the sand-pack model, resulting in a permeability of 4,000 × 10−3 μm2. The size of the model is Φ2.5 cm × 30 cm. The diameter of the erosion channel is 1.0 cm–1.5 cm and the length is 30 cm. Foaming agent and nitrogen can produce foam through foam generator. The half-life of the foam is 2 h at 25°C. The half-life decreases with the increase of temperature, and it basically fails when the temperature exceeds 120°C.
2.3.2 Experimental procedure
The formation water is injected into the sand-pack model at an injection rate of 0.5 mL min-1, and the porosity is calculated. Different injection rates are used for displacement, and the water permeability is calculated using Darcy’s law. The temperature of the oven is raised to 100 °C and maintained for 1 h. The pretreated crude oil is injected into the intermediate container at the rate of 1.0 mL min-1 until no further water production is observed. Finally, the temperature of the oven is lowered to the reservoir temperature of 40°C. The oil displacement experiment is carried out. The steam temperature is maintained at 200°C, the steam quality is 0.5, and the injection rate is 1.0 mL min-1. The pressure of backpressure pump is kept below 0.5 MPa. The displacement is stopped when the water cut reaches over 98%.
2.3.3 Experimental scheme
Steam flooding: The steam injection volume is 3.6 PV, and displacement is stopped when the water cut reaches 98%. Foam assisted steam flooding: After the injection of 1.0 PV of steam, 0.4% concentration of foaming agent and 0.5 PV of N2 are injected when the temperature, then the subsequent steam flooding is conducted. Viscosity reducer assisted steam flooding: After the injection of 1.0 PV of steam, 0.4 PV of viscosity reducer is injected, then the subsequent steam flooding is conducted. Composite (foam and viscosity reducer assisted steam) flooding: After the injection of 1.0 PV of steam, 0.4% concentration of foaming agent and 0.5 PV of N2 are injected, followed by steam flooding. After injecting 0.5 PV of steam, 0.4% of the viscosity reducer is injected, followed by subsequent steam flooding. Compared different thermochemical composite flooding with steam flooding, the enhanced oil recovery (EOR) of thermochemical flooding is analyzed.
2.4 Oil displacement experiments in 2D sand-pack model
2.4.1 Experimental equipment
As shown in Figure 4A, the experimental equipment mainly includes: ISCO pump, steam generator, gas flow meter, gas cylinder, intermediate container, sand-pack model, pressure gauge, thermometer, etc. The 2D sand-pack model is made of stainless steel and consists of a chamber, a top cover, rubber sealing gaskets, simulated wells, and sampling valves. The chamber size is 35 cm × 35 cm × 3 cm, and it is filled with quartz sand of different mesh sizes to simulate a porous medium environment. Rubber sealing gaskets with a diameter of 0.3 cm are used to seal the groove between the top cover and the chamber. To ensure a good seal, organic glass adhesive is applied around the sealing gasket. The model is equipped with 10 sampling ports on the back and 25 inlet and outlet ports on the side, all equipped with valves. During the experiment, the liquid is taken out from the sampling port to obtain the oil saturation at this sampling port, and then the oil saturation distribution of the entire model can be obtained through interpolation. The top cover is securely fastened to the model body using 26 long screws.
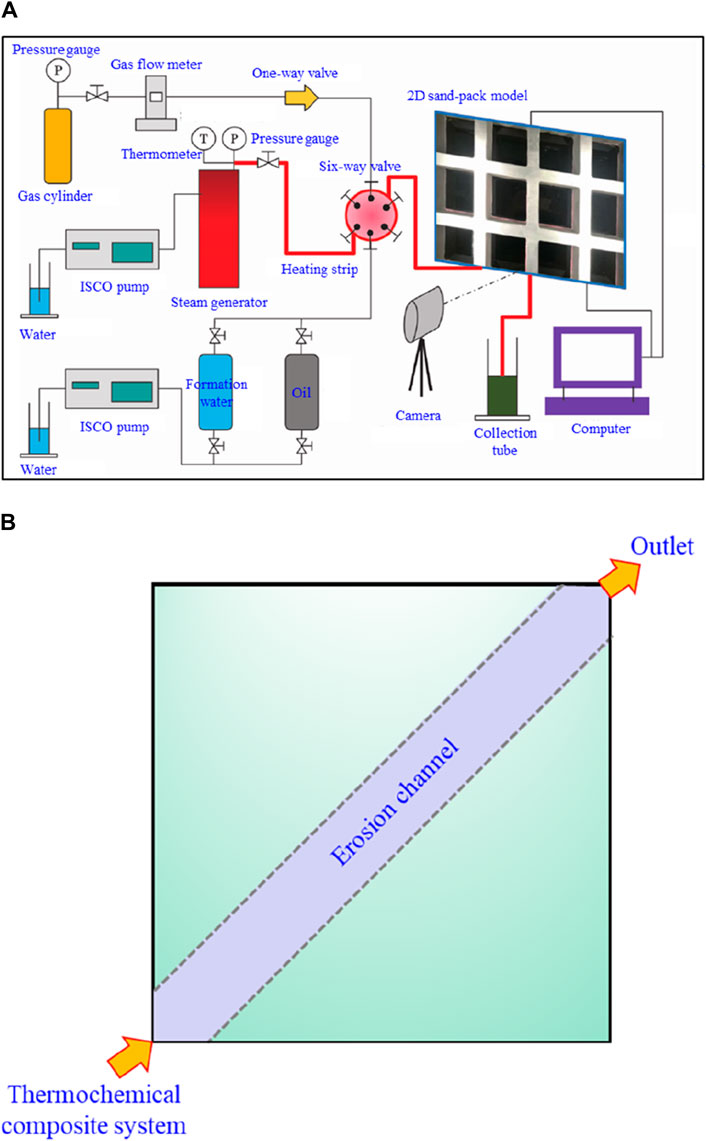
Figure 4. The experimental setup and layout of the 2D sand-pack model. (A) Experimental setup. (B) The layout of the 2D sand-pack model.
2.4.2 Sand filling method
In the 2D sand-pack model experiments, a strip of high-permeability zone is used to simulate the erosion channels. Quartz sand with different mesh sizes are used to fill the 2D sand-pack model. The layout of the 2D sand-pack model is shown in Figure 4B. The central diagonal strip is the high-permeability zone, filled with 30–50 mesh quartz sand. The parallel width of the zone is 6.7cm, and the zone is distributed along the diagonal of the model, with a permeability of 5,500 × 10−3 μm2. The two triangular areas on both sides are the low-permeability zones, filled with 50–90 mesh quartz sand. The diagonal side length of the zones is 43cm, and the permeability of the zones is 2,200 × 10−3 μm2. The porosity of the model is calculated using the weighing method, and the permeability of the 2D model is equivalent to the permeability determined using the quartz sand with same mesh size in the sand-pack model under the same sand filling conditions.
2.4.3 Experimental procedure
The sand-pack model is connected to the vacuum system, and the valve is closed after reaching a negative pressure of 0.1 MPa. The valve connected to the simulated formation water is opened to saturate the model, followed by injecting formation water until the model is completely saturated. Simulated oil is alternately injected into the sand-pack model at different injection points on the side of the model until the model is fully saturated with simulated oil, maintaining the connate water saturation at around 15%. Steam is injected into the 2D model at a rate of 3.0 mL min-1 at a temperature of 200 °C and a steam quality of 0.5. After that, 0.3 PV chemical enhancing system is injected for displacement. Finally, subsequent steam flooding is conducted until the water cut reaches 98%. Two sets of experiments are conducted, one involving the enhancement of viscosity reducer assisted steam flooding and the other involving the enhancement of composite flooding.
3 Results and discussion
3.1 The influence of thermochemical composite system on the rheological properties of extra heavy oil
In the viscosity temperature curve test of extra heavy oil, the test temperature range is 40°C–200°C, and the shear rate is 7.34 s-1. The viscosity-temperature curve of extra heavy oil is shown in Figure 5. Within the temperature range of 40°C–100°C, as the temperature increases, the viscosity of extra heavy oil significantly decreases. After the temperature exceeds 100°C, as the temperature increases, the viscosity of extra heavy oil decreases slowly.
In the rheological properties test of extra heavy oil emulsion, the viscosity reducer with a concentration of 0.4% is used. The crude oil and viscosity reducer are thoroughly mixed in an oil-water ratio of 3:7 to obtain an emulsion. Firstly, a viscosity reducer solution is prepared by adding a viscosity reducer into water and stirring. Then, this viscosity reducer solution is added to the crude oil and stirred inside an emulsifier. Once the crude oil and viscosity reducer are thoroughly mixed, a stable emulsion is formed. A rheometer is used to test the viscosity-temperature relationship of the emulsion, and the results are shown in Figure 6. The temperature of the test ranges from 40°C to 200°C, with a shear rate of 7.34 s-1.
Figure 6 shows the viscosity of the emulsion forms an almost horizontal straight line on a logarithmic scale and shows minimal variation with temperature. This indicates that temperature has a relatively small influence on the viscosity of the emulsion. In the process of heavy oil development, the addition of viscosity reducers is a common method to reduce the viscosity of heavy oil and improve oil recovery.
The mechanism of adding viscosity reducer during steam injection is that while steam heating reduces the viscosity of crude oil, the viscosity reducer can effectively reduce the interfacial tension between oil and water, form oil-in-water emulsion and greatly reduce the viscosity of crude oil. The injection of viscosity reducer can also change the wettability of rock and improve the relative permeability of oil phase. In order to study the rheological properties of the emulsion after the addition of viscosity reducer, the viscosity of the emulsion with shear is tested by rheometer (Figure 7). The test temperature is 40°C, 100°C, 150°C and 200°C. The shear rate is in the range of 0–100 s-1. Figure 7 shows that in logarithmic coordinates, the viscosity of extra heavy oil emulsions at different temperatures decreases with the increase of shear rate. The variation curves of viscosity with shear rate at different temperatures almost coincide, so it can be concluded that the rheological property of emulsion is less affected by temperature and more affected by shear rate.
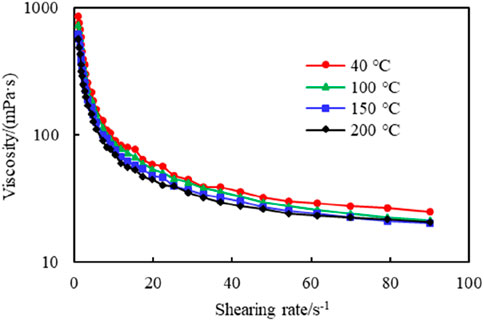
Figure 7. Curves of viscosity of extra heavy oil emulsion with shear rate at different temperatures.
The viscosity-temperature curve of the emulsion is tested by rheometer (Figure 8), in which the ratio of oil to water is 3:7, the test temperature range is 40°C–200°C and the shear rate is 7.34 s-1. As can be seen from Figure 8, when the concentration of viscosity reducer is 0.2%, the viscosity of the emulsion decreases with the increase of temperature. When the Viscosity reducer concentration is 0.4% or more, after the viscosity reducer is mixed with extra heavy oil, the viscosity almost does not change with temperature. When the concentration of viscosity reducer is high, the viscosity is less affected by temperature. The variation of emulsion viscosity with shear rate is measured by rheometer (Figure 9). The ratio of oil to water is 3:7, the test temperature is 100°C, and the shear rate is in the range of 0–100 s. Figure 9 shows that the viscosity of the emulsion decreases with the increase of shear rate under different viscosity reducer concentration schemes. When the concentration of viscosity reducer is 0.2%, the viscosity of the emulsion is higher than the concentration of 0.4% and 0.6% at different shear rates. When the concentration of viscosity reducer is more than 0.4%, the variation curve of viscosity with shear rate almost coincides.
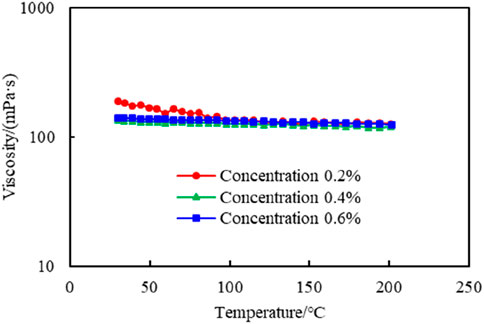
Figure 8. Viscosity-temperature curves of emulsions with different viscosity reducer concentrations.
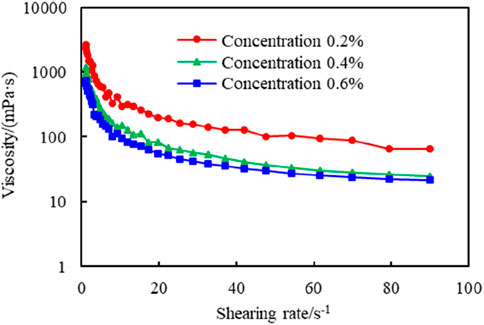
Figure 9. Curves of emulsion viscosity with shear rate with different viscosity reducer concentration.
To sum up, the crude oil can be fully emulsified when the viscosity reducer with a concentration of 0.4% or more is mixed with extra heavy oil. For the properties of the emulsion itself, its viscosity is almost not affected by temperature, but only decreases with the increase of shear rate. Therefore, in the actual injection process, it is necessary to keep the minimum concentration of viscosity reducer at 0.4%, so that the extra heavy oil is fully emulsified and the crude oil viscosity is reduced to the maximum.
The emulsion is obtained by fully mixing 0.4% viscosity reducer with extra heavy oil at 5:5, 3:7 and 1:9 oil-water ratio, respectively. The viscosity-temperature curves of emulsions with different oil-water ratio are tested by rheometer (Figure 10). The test temperature range is 40°C–200°C and the shear rate is 7.34 s-1. As can be seen from Figure 10, the viscosity-temperature curves of emulsions with different oil-water ratio almost coincide, and the viscosity of mixtures with different oil-water ratio varies little with temperature, indicating that viscosity reducers with different oil-water ratio can fully emulsify extra heavy oil. The effect of temperature on the viscosity of emulsion under different oil-water ratio is relatively small. The change of emulsion viscosity with shear is tested by rheometer (Figure 11). The concentration of viscosity reducer is 0.4%, the test temperature is 100°C, and the shear rate is in the range of 0–100 s-1. It can be seen from Figure 11 that the variation curves of emulsion viscosity with shear rate obtained by different oil-water ratio schemes almost coincide, and the viscosity decreases with the increase of shear rate. As a result, it can be concluded that different oil-water ratio has little effect on the viscosity reduction effect of viscosity reducer. To sum up, the viscosity reduction effect of viscosity reducer on crude oil is greatly affected by concentration and less affected by oil-water ratio.
3.2 Oil displacement experiment of thermochemical composite flooding of extra heavy oil in 1D sand-pack model
The recovery contrast curve of foam assisted steam flooding and steam flooding is shown in Figure 12A, and the water cut contrast curve is shown in Figure 12B. As can be seen from Figure 12A, the recovery of foam assisted steam flooding is higher than that of steam flooding, and the final oil recovery is 48.57%, which is 4.38% higher than that of steam flooding. As can be seen from Figure 12B, after foam injection, the water cut decreases from 94.44% to 79.41%, and the water cut decreases by 15.0%. The injection of foam can plug the steam channeling channel, expand the area of steam, further expand the steam heat to the depth of the formation, and heat the oil in the area not swept by the steam, which further improve the utilization efficiency of heat energy and improve the oil recovery in the steam flooding.
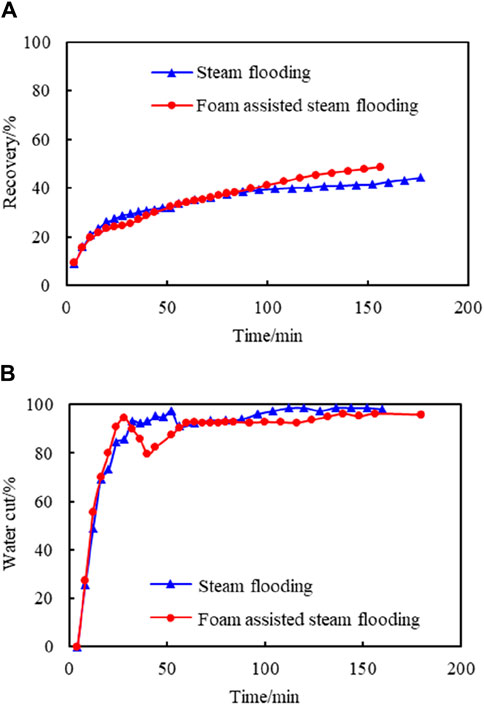
Figure 12. Comparison curve of foam assisted steam flooding and steam flooding. (A) Recovery. (B) Water cut
The recovery comparison curve of viscosity reducer assisted steam flooding and steam flooding is shown in Figure 13A, and the water cut contrast curve is shown in Figure 13B. As can be seen from Figures 13A, B, the final recovery of viscosity reducer assisted steam flooding is 61.57%, which is 17.38% higher than that of steam flooding. After viscosity reducer injection, the water cut decreases from 92.44% to 63.76%, and the oil production rate increases rapidly in this process. It can be seen that the viscosity of extra heavy oil is high, and even after steam heating, it still has high residual oil saturation. After viscosity reducer is injected, it can effectively reduce the oil-water interfacial tension, strengthen erosion, and drive out more crude oil. Reduce residual oil saturation and greatly improve oil recovery.
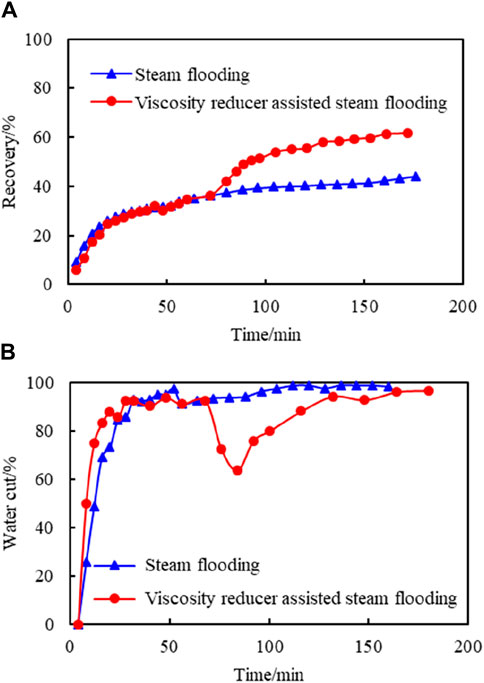
Figure 13. Comparison curve of viscosity reducer assisted steam flooding and steam flooding. (A) Recovery (B) Water cut.
The contrast curves of recovery degree and water cut between composite flooding and steam flooding are shown in Figures 14A, B, respectively. As can be seen from Table 2, the oil recovery after foam injection increases by 3.96% compared with the steam flooding, and the oil recovery after viscosity reducer injection increases by 30.46% compared with the steam flooding. The EOR of composite flooding is 8.7% higher than the sum of EOR of single foam flooding and single viscosity reducer flooding, indicating that foam and viscosity reducer have synergistic effect. The injection of foam blocks the non-piston erosion channel to a certain extent, so that steam can further expand the crude oil in the unaffected area to the depth of the formation. It expands the swept area of steam, and viscosity reducer can also can emulsify oil and reduce its viscosity, and greatly improve oil recovery.
3.3 Oil displacement experiment of thermochemical composite flooding of extra heavy oil in 2D sand-pack model
The dynamic curve of viscosity reducer assisted steam flooding for reservoir development is shown in Figure 15. During the steam flooding process, the water cut rapidly increases, and the steam flooding recovery is 32.76%. During the viscosity reducer flooding, the water cut rapidly decreases, and the water cut decline funnel is deep and narrow. After the water cut decreases to 33.33%, it quickly increases again. The recovery of subsequent steam flooding after viscosity reducer flooding is 45.25%, which is 12.49% higher than steam flooding alone.
Figure 16 shows the dynamic curve of composite flooding for reservoir development. The steam flooding recovery is 35.55%. During the composite flooding, the water cut decline funnel is shallow and wide with fluctuating features. After the water cut decreases to 61.67%, it slowly increases again. The recovery after composite flooding is 52.16%, which is 16.61% higher than steam flooding alone. The viscosity of the viscosity reducer solution is similar to water, and most of the viscosity reducers still flow along the erosion channels during displacement. The low interfacial tension promotes the emulsification of heavy oil, improving the oil phase permeability.
Table 3 shows the recovery of viscosity reducer assisted steam flooding and composite flooding after steam flooding and at the end of displacement. It can be seen that composite flooding improves oil recovery and is more effective than viscosity reducer assisted steam flooding, resulting in higher oil recovery.
Figure 17 shows the distribution of remaining oil during viscosity reducer assisted steam flooding. During the steam flooding, the injected simulated formation water flows along the central high-permeability zone. After 40 min of injection, steam breakthrough occurs at the outlet of model, resulting in lower sweep efficiency. After 120 min of steam injection, viscosity reducer is injected. Due to the high viscosity ratio between oil and water, the viscosity reducer solution tends to experience viscous fingering. Following the viscosity reducer injection, steam continues to be injected, leading to a slight increase in the steam sweep area, and the saturation of remaining oil outside the high-permeability zone begins to decrease.
Figure 18 shows the distribution of remaining oil flooding by a composite system of steam, foam, and viscosity reducer. Similar to viscosity reducer assisted steam flooding, during the steam flooding, the injected simulated formation water flows along the central high-permeability zone. After 60 min of injection, steam breakthrough occurs at the outlet of the model. After 100 min of steam injection, foam is injected along with the viscosity reducer, and the foam can plug the high-permeability zone. Continuing to inject steam, there is a relatively noticeable expansion in the steam sweep area, with a greater decrease in the remaining oil saturation outside the high-permeability zone.
3.4 Discussion
This study conducted experiments on the rheological properties of extra heavy oil and 1D and 2D sand-pack model displacement, and obtained recovery under different displacement methods. The mechanism of different displacement methods was analyzed.
However, during the sand-pack model displacement experiment, there are various errors. There are errors in the measurement of oil and water remaining in the pipeline, as well as errors in the displacement pump, intermediate container, etc., combined with reading errors, resulting in certain errors in the final calculation results. Through experimental design, we have minimized the impact of the amount of oil and water in the pipeline on the calculation results. At the same time, due to significant differences between laboratory and reservoirs, heat can spread throughout the sand-pack model during the transfer process, resulting in a slightly higher recovery than the actual oil field.
Besides, there are still some problems in the experiments: the strength of foam at high temperature (150°C, 200°C) decreases, and the plugging performance is poor. It is necessary to develop a foaming agent with better performance to improve the plugging strength of foam at high temperature. The 2D model cannot consider the effects of steam overlap and gravity, and a thicker 3D model is needed to study the influence of steam overlap and gravity on oil recovery in the future. In addition, with the addition of chemical agents such as foam and viscosity reducer in the displacement process, the cost of development is also increasing. Later, the economic net present value needs to be calculated to determine the profit of each displacement method.
4 Conclusion
In this study, rheological tests and oil displacement experiments are conducted to investigate the rheological properties and seepage characteristics of extra heavy oil under thermochemical conditions. The following conclusions are obtained:
(1) Steam heating effectively reduces the viscosity of the crude oil while the addition of viscosity reducer reduced the oil-water interfacial tension, enabling the formation of water-in-oil emulsions and significantly lowering the oil viscosity. Mixing the heavy oil with viscosity reducer at concentrations of 0.4% or higher results in thorough emulsification of the crude oil. The rheological properties of the emulsions are minimally influenced by temperature but are significantly influenced by shear rate.
(2) During the 1D thermochemical composite flooding, the primary oil recovery mechanism is erosion, with displacement playing a secondary role. The foam increases the sweep efficiency through plugging, while the viscosity reducer greatly reduces the viscosity of oil through emulsification. Compared with steam flooding, foam assisted steam flooding improves oil recovery by 4.38%, viscosity reducer assisted steam flooding improves oil recovery by 17.38%, and composite flooding improves oil recovery by 30.46%. The composite system of steam, foam, and viscosity reducer exhibits a synergistic effect, enhancing both erosion and displacement, resulting in a significant increase in recovery.
(3) In 2D sand-pack displacement experiments, viscosity reducer assisted steam flooding and composite flooding increases recovery by 12.49% and 16.61%, respectively. The addition of foam increases the sweep efficiency of steam. However, due to weak plugging strength of the foam, the recovery of composite flooding only increases 4.12% compared to viscosity reducer assisted steam flooding.
The above conclusions provide valuable insights into the rheological behavior and oil displacement mechanism of extra heavy oil under thermochemical conditions.
Data availability statement
The original contributions presented in the study are included in the article/Supplementary material, further inquiries can be directed to the corresponding author.
Author contributions
QC: Writing–original draft, Data curation. HZ: Writing–review and editing, Methodology. JY: Writing–original draft, Conceptualization. ZX: Writing–original draft, Investigation. TW: Writing–review and editing, Supervision. SZ: Writing–review and editing, Formal Analysis. RL: Writing–review and editing, Validation.
Funding
The author(s) declare that financial support was received for the research, authorship, and/or publication of this article. This work was supported by the National Natural Science Foundation of China (grant number U20B6003) and the Foundation of SINOPEC (grant number P21077-4).
Conflict of interest
The authors declare that the research was conducted in the absence of any commercial or financial relationships that could be construed as a potential conflict of interest.
Publisher’s note
All claims expressed in this article are solely those of the authors and do not necessarily represent those of their affiliated organizations, or those of the publisher, the editors and the reviewers. Any product that may be evaluated in this article, or claim that may be made by its manufacturer, is not guaranteed or endorsed by the publisher.
References
Ahmadi, M., and Chen, Z. Challenges and future of chemical assisted heavy oil recovery processes. Adv. colloid interface Sci., 2020, 275: 102081, doi:10.1016/j.cis.2019.102081
Ahuja, A., Lee, R., and Joshi, Y. M. Advances and challenges in the high-pressure rheology of complex fluids. Adv. Colloid Interface Sci., 2021, 294: 102472, doi:10.1016/j.cis.2021.102472
Alade, O. S., Al Shehri, D. A., and Mahmoud, M. Investigation into the effect of silica nanoparticles on the rheological characteristics of water-in-heavy oil emulsions. Petroleum Sci., 2019a, 16: 1374–1386. doi:10.1007/s12182-019-0330-x
Alade, O. S., Hamdy, M., Mahmoud, M., Al Shehri, D. A., Mokheimer, E., Patil, S., et al. A preliminary assessment of thermochemical fluid for heavy oil recovery. J. Petroleum Sci. Eng., 2020, 186: 106702, doi:10.1016/j.petrol.2019.106702
Alade, O. S., Mahmoud, M., Hassan, A., Al-Shehri, D., Al-Nakhli, A., and Bataweel, M. Evaluation of kinetics and energetics of thermochemical fluids for enhanced recovery of heavy oil and liquid condensate. Energy and Fuels, 2019b, 33(6): 5538–5543. doi:10.1021/acs.energyfuels.9b00681
Alade, O. S., Ogunlaja, A. S., Mohamed, A. H., Mahmoud, M., Al Shehri, D., Al-Nakhli, A., et al. Prospects of co-injecting ionic liquid and thermochemical fluid for recovery of extra-heavy oil. Fuel, 2023, 331: 125947, doi:10.1016/j.fuel.2022.125947
Al-Anssari, S., Ali, M., Alajmi, M., Akhondzadeh, H., Khaksar Manshad, A., Kalantariasl, A., et al. Synergistic effect of nanoparticles and polymers on the rheological properties of injection fluids: implications for enhanced oil recovery. Energy and Fuels, 2021, 35(7): 6125–6135. doi:10.1021/acs.energyfuels.1c00105
Bruns, F., and Babadagli, T. Initial screening of new generation chemicals using sandpack flooding tests for recovery improvement of gravity driven steam applications. J. Petroleum Sci. Eng., 2020, 194: 107462. doi:10.1016/j.petrol.2020.107462
Hu, C. H. Research progress and development direction of steam flooding technology for medium and deep heavy oil reservoirs. Special Oil Gas Reservoirs, 2020, 27(6): 54–59. doi:10.3969/j.issn.1006-6535.2020.06.007
Huang, J., and Babadagli, T. Efficiency improvement of heavy-oil recovery by steam-assisted gravity drainage injection using new generation chemicals. Energy and Fuels, 2020, 34(4): 4433–4447. doi:10.1021/acs.energyfuels.0c00208
Jing, J., Wang, S., Ling, A., Yuan, L., Zhang, M., and Yin, R. Rheological behavior of heavy crude oil and its emulsions. Petroleum Sci. Technol., 2020, 38(5): 440–446. doi:10.1080/10916466.2020.1727502
Li, S., Li, Z., Xu, Z., Ban, X., and Lu, T. Study of rheological properties and micro-mechanism of heavy oil emulsion prepared via ultrasonic dispersion. Energy and Fuels, 2020, 34(12): 15843–15854. doi:10.1021/acs.energyfuels.0c02486
Li, Y. B., Zhang, Y. Q., Luo, C., Gao, H., Li, K., Xiao, Z. R., et al. The experimental and numerical investigation of in situ re-energization mechanism of urea-assisted steam drive in superficial heavy oil reservoir. Fuel, 2019, 249: 188–197. doi:10.1016/j.fuel.2019.03.086
Li, Z., Huang, X., Xu, X., Bai, Y., and Zou, C. Unstable coalescence mechanism and influencing factors of heterogeneous oil droplets. Molecules, 2024, 29(7): 1582, doi:10.3390/molecules29071582
Liu, H., Wang, Y., Zheng, A., Sun, X., Dong, X., Li, D., et al. Experimental investigation on improving steam sweep efficiency by novel particles in heavy oil reservoirs. J. Petroleum Sci. Eng., 2020b, 193: 107429, doi:10.1016/j.petrol.2020.107429
Liu, H. Q., and Dong, X. H. (2022). Current status and future trends of hybrid thermal EOR processes in heavy oil reservoirs. Petroleum Sci. Bull. 02, 174–184.
Liu, Y. G., Song, H. Z., Zou, J., Zhou, F., and Sun, Y. Research and application of low temperature thermochemistry mechanism on offshore heavy oil. J. Petrochem. Univ., 2020a, 33(3): 27. doi:10.3969/j.issn.1006-396X.2020.03.005
Lyu, X., Liu, H., Pang, Z., and Sun, Z. Visualized study of thermochemistry assisted steam flooding to improve oil recovery in heavy oil reservoir with glass micromodels. Fuel, 2018, 218: 118–126. doi:10.1016/j.fuel.2018.01.007
Mahmoud, M., Alade, O. S., Hamdy, M., Patil, S., and Mokheimer, E. M. In situ steam and nitrogen gas generation by thermochemical fluid Injection: a new approach for heavy oil recovery. Energy Convers. Manag., 2019, 202: 112203, doi:10.1016/j.enconman.2019.112203
Mohammadzadeh, O., Sedaghat, M. H., Kord, S., Zendehboudi, S., and Giesy, J. P. Pore-level visual analysis of heavy oil recovery using chemical-assisted waterflooding process–Use of a new chemical agent. Fuel, 2019, 239: 202–218. doi:10.1016/j.fuel.2018.10.104
Pratama, R. A., and Babadagli, T. A review of the mechanics of heavy-oil recovery by steam injection with chemical additives. J. Petroleum Sci. Eng., 2022, 208: 109717, doi:10.1016/j.petrol.2021.109717
Qi, N., Li, J. F., and Wen, Q. Foam flowing mechanisms of steam-foam flooding for heavy oil reservoirs. J. Liaoning Petrochem. Univ., 2009, 29(4): 34–38.
Ramírez-González, P. V., and Quinones-Cisneros, S. E. Rheological behavior of heavy and extra-heavy crude oils at high pressure. Energy and Fuels, 2020, 34(2): 1268–1275. doi:10.1021/acs.energyfuels.9b02867
Strelets, L. A., and Ilyin, S. O. Effect of enhanced oil recovery on the composition and rheological properties of heavy crude oil. J. Petroleum Sci. Eng., 2021, 203: 108641, doi:10.1016/j.petrol.2021.108641
Sun, H. Q., Liu, H. Q., and Wang, H. T. Development technology and direction of thermal recovery of heavy oil in China. Acta Pet. Sin., 2022, 43(11): 1664–1674. doi:10.7623/syxb202211013
Sun, Q., Zhang, N., Liu, W., Li, B., Li, S., Bhusal, A., et al. Insights into enhanced oil recovery by thermochemical fluid flooding for ultra-heavy reservoirs: an experimental study. Fuel, 2023, 331: 125651, doi:10.1016/j.fuel.2022.125651
Tian, Y., Ju, B., Lü, G., Liu, N., Dong, Y., and Ma, S. The comprehensive model for solvent assisted steam flooding in thin heavy oil reservoirs considering asphaltene deposition. J. Petroleum Sci. Eng., 2020, 185: 106676, doi:10.1016/j.petrol.2019.106676
Wang, Y., Liu, H., Zhang, Q., Chen, Z., Wang, J., Dong, X., et al. Pore-scale experimental study on EOR mechanisms of combining thermal and chemical flooding in heavy oil reservoirs. J. Petroleum Sci. Eng., 2020, 185: 106649, doi:10.1016/j.petrol.2019.106649
Xi, C. F., Qi, Z. Y., Zhang, Y. J., Liu, T., Shen, D., Mu, H., et al. CO2 assisted steam flooding in late steam flooding in heavy oil reservoirs. Petroleum Explor. Dev., 2019, 46(6): 1242–1250. doi:10.1016/s1876-3804(19)60277-6
Yadykova, A. Y., and Ilyin, S. O. Compatibility and rheology of bio-oil blends with light and heavy crude oils. Fuel, 2022, 314: 122761, doi:10.1016/j.fuel.2021.122761
Zhai, M., Du, Q., Wu, G., Sun, J., and Sha, Y. Potential of a new water-soluble agent for enhancing heavy oil recovery: a pore-scale investigation. J. Petroleum Sci. Eng., 2022, 208: 109646, doi:10.1016/j.petrol.2021.109646
Zhai, M., Zhou, K., Sun, Z., Wu, D., Du, Q., and Hou, J. Synergistic mechanism of enhanced heavy oil recovery by compound flooding using 3D visualization model. Fuel, 2023, 353: 129214, doi:10.1016/j.fuel.2023.129214
Zhang, J., Chen, X. P., and Xu, J. Rheological characteristics of unstable heavy crude oil-water dispersed mixtures. J. Petroleum Sci. Eng., 2019, 182: 106299, doi:10.1016/j.petrol.2019.106299
Zhang, N., Liu, W., Zou, X., Wang, S., Sun, Q., Li, B., et al. Experimental study on thermochemical composite system huff-n-puff process in ultra-heavy oil production. Fuel, 2023, 332: 126014, doi:10.1016/j.fuel.2022.126014
Keywords: extra heavy oil, thermochemical composite flooding, physical experiments, erosion channels, chemical agents
Citation: Cao Q, Zheng H, Yu J, Xiong Z, Wei T, Zhu S and Liu R (2024) Experimental study on thermochemical composite flooding mechanism of extra heavy oil reservoirs with erosion channels. Front. Energy Res. 12:1357508. doi: 10.3389/fenrg.2024.1357508
Received: 22 February 2024; Accepted: 10 June 2024;
Published: 27 June 2024.
Edited by:
Dr. Muhammad Farooq, University of Engineering and Technology, PakistanReviewed by:
Imran Zahid, Government College University, PakistanZhihua Zhao, Henan University of Technology, China
Copyright © 2024 Cao, Zheng, Yu, Xiong, Wei, Zhu and Liu. This is an open-access article distributed under the terms of the Creative Commons Attribution License (CC BY). The use, distribution or reproduction in other forums is permitted, provided the original author(s) and the copyright owner(s) are credited and that the original publication in this journal is cited, in accordance with accepted academic practice. No use, distribution or reproduction is permitted which does not comply with these terms.
*Correspondence: Haoyu Zheng, emhlbmdoYW95dV91cGNAMTYzLmNvbQ==