- 1Department of Mechanical Engineering, Iowa State University, Ames, IA, United States
- 2Bioeconomy Institute, Iowa State University, Ames, IA, United States
- 3Department of Chemical and Biological Engineering, Iowa State University, Ames, IA, United States
Sugars are precursors to the majority of the world’s biofuels. Most of these come from sugar and starch crops, such as sugarcane and corn grain. Lignocellulosic sugars, although more challenging to extract from biomass, represent a large, untapped, opportunity. In response to the increasing attention to renewable energy, fuels, and chemicals, we review and compare two strategies for extracting sugars from lignocellulosic biomass: biochemical and thermochemical processing. Biochemical processing based on enzymatic hydrolysis has high sugar yield but is relatively slow. Thermochemical processing, which includes fast pyrolysis and solvent liquefaction, offers increased throughput and operability at the expense of low sugar yields.
1 The need for sugars
Transferring society’s dependence from petroleum to biomass resources for the production of liquid transportation fuels and commodity chemicals can improve the sustainability of energy and chemical industries by reducing pollution and managing greenhouse gas (GHG) emissions. Biofuels can play a key role in meeting the growing demands for renewable energy and help alleviate global climate change (Smith, 2016; IPCC, 2018). In addition to fuels, biomass can be converted into chemical building blocks, replacing some of the most commonly used petroleum-based chemicals (Werpy et al., 2004). The constituents of biomass include carbohydrates, lipids, protein, and lignin, all of which, in principle, can be converted into renewable fuels and chemicals. However, most of the current supply and much of the projected supply of these bio-based products are anticipated to come from carbohydrates, which is the focus of this review.
2 Fuels and chemicals
2.1 Fuels
Transportation constitutes approximately 27% of the total GHG emissions in the world, thus representing one of the largest opportunities to displace fossil fuels (Sources of Greenhouse Gas Emissions, 2020). The current transportation sector is based on spark-ignition engines, which require high-octane fuels like gasoline, and compression-ignition engines, which require high-cetane fuels like diesel. Ethanol, with an octane number of 113, is attractive for replacing gasoline, while methyl esters, with a cetane number approximately 55, can replace diesel fuel. Ethanol is readily produced by fermenting carbohydrates, while methyl esters (familiarly known as biodiesel) are the product of transesterification of plant lipids and animal fats (Brown and Brown, 2014). The potential energy supply from carbohydrates is far in excess of the energy that could be produced from plant lipids and animal fats. Accordingly, much of the future supply of biofuels is premised on fermenting sugars from various kinds of carbohydrates into either ethanol for use in spark-ignition engines or lipids and terpenes for compression-ignition engines and jet engines.
Sugar and starch crops such as sugarcane and corn are the source of carbohydrates to produce so-called first-generation (1G) ethanol, which accounts for most of the growth in the biofuels industry to date. Today, essentially all gasoline in the United States of America (USA) is blended with 10% ethanol (EIA, 2016). Other countries of the world have also established policies to encourage production of biofuels. In 2008, the worldwide ethanol production was 66.77 billion liters (Gupta and Verma, 2015), which subsequently increased to 106.6 billion liters in 2022 with Brazil and USA contributing to over 80% of the total ethanol production (Renewable Fuels Association, 2023).
Ethanol has several advantages as transportation fuel. From an environmental perspective, ethanol is biodegradable and less toxic than gasoline. An analysis by the Renewable Fuels Association showed that ethanol blended with gasoline resulted in a cumulative CO2 savings of 1.212 billion metric tons to date (Unnasch et al., 2023). From a performance perspective, blends of ethanol and gasoline have octane ratings higher than gasoline (Anderson et al., 2012). Ethanol has disadvantages as a fuel that periodically raises concerns in the press. Consumers notice lower fuel economy (distance driven per volume of fuel) for ethanol–gasoline blends, especially as the blend ratio increases, arising from the lower volumetric energy density of ethanol than of gasoline. Although this is not an energy efficiency issue, it is an inconvenience, requiring more frequent refueling. Gasoline–ethanol blends can phase-separate when contaminated with water, which prevents their distribution in exiting gasoline pipelines (Furey and Perry, 1991; Whims, 2002; Wallner et al., 2009). However, these problems are relatively modest when compared to the challenges of transforming the large and diverse global resource of carbohydrates into fermentable sugars.
Sugarcane contains sucrose, a disaccharide, which both microorganisms and animals (such as humans) can metabolize. Starch is the carbohydrate in corn and other grains, a storage polysaccharide, which is readily hydrolyzed to monosaccharide glucose through the action of acids, enzymes, and microorganisms found in the digestive system of many animals. As many critics to biofuels point out, first-generation ethanol is produced from feedstocks that are an important part of the human food chain.
In response to concerns about worldwide food insecurity and indirect land use change, as well as on the potential for increased rural economic growth, biofuel policies around the world incentivize the use of non-food crops for the production of biofuels. Of special interest are plants classified as lignocellulosic biomass, such as wood, grasses, and crop residues. Lignocellulosic biomass, which are rich sources of the structural carbohydrates, cellulose and hemicellulose, include a wide range of waste and dedicated energy crops that are high yielding, abundant, and of relatively low cost. Like storage carbohydrates, structural carbohydrates can be hydrolyzed to fermentable sugars and metabolized, although only a relatively few organisms have evolved to directly utilize them as sources of energy and carbon. Further challenges include releasing polysaccharides from the lignocellulosic structure, hydrolyzing the polysaccharides to simple sugars, removing fermentation inhibitors from the substrate, and efficiently fermenting both hexoses (six-carbon sugars) and pentoses (five-carbon sugars) produced from the polysaccharides. Overcoming these technical challenges is not enough; the resulting process for the production of cellulosic ethanol must be carbon-efficient, cost-effective, and environmentally sustainable.
Structural carbohydrates can be converted into liquid fuels other than ethanol such as hydrocarbons for diesel and jet fuels or completely new fuel molecules such as 2,5-dimethylfuran (Chidambaram and Bell, 2010; Climent et al., 2014; Braun and Antonietti, 2017; Eagan et al., 2017). Microbial fermentation can transform biomass-derived sugars into a variety of biofuels such as ethanol, butanol, isobutanol, and acetone (Tao and Aden, 2009). Conventionally, butanol is produced commercially through ABE (acetone, butanol, and ethanol) fermentation of molasses using anaerobic bacteria. Clostridium acetobutylicum, genetically modified Saccharomyces cerevisiae, and Escherichia coli strains are the basis for producing butanol from sugars (Mohagheghi et al., 2002; Zhang et al., 2008). Genetically engineered E. coli can also convert sugars into structurally tailored fatty acids suitable for biodiesel production (Steen et al., 2010). Various recent reports show that engineered oleaginous yeasts with cost-efficient bioconversion processes and lipid extraction mechanisms can effectively convert simple sugars into drop-in transportation fuels (Kruger et al., 2018; Xu, P. et al., 2016).
Hydrocarbons can be produced from sugars (Davis et al., 2013; Climent et al., 2014). This area has deservedly received much attention, but their biological production often involves complex metabolic pathways. Instead of trying to adapt microorganisms to the production of conventional fuel molecules, many researchers advocate adapting fuel infrastructure to molecules that are more readily produced biologically (Shanks and Keeling, 2017).
2.2 Chemicals
Sugars can be converted into bio-based products other than biofuels. Chemicals typically have higher price points than fuels, which allows small, specialized companies to compete with much larger producers. Lignocellulosic sugars can be used to manufacture commodity chemical suitable for the production of polymers, pharmaceuticals, reagents, and solvents (Mika et al., 2018). Researchers have demonstrated that sugars can be transformed into high-value chemical precursors that are not easily produced from petroleum. For instance, the chiral structure of levoglucosan, an anhydrosugar from thermal deconstruction of cellulose, is useful in creating unique molecules for the pharmaceutical and plastic industries (Itabaiana Junior et al., 2020). Production of levoglucosan and other carbohydrates from petroleum is very inefficient, involving many low-yielding synthesis steps. Recently, researchers have established highly selective levoglucosan production methods at a purity of up to 95% from completely renewable biomass sources in a small number of steps (Chen et al., 2016; Rover et al., 2019). Levoglucosenone, which is doubly dehydrated glucose, also has chiral characteristics that make it an attractive building block for pharmaceutical products (Comba et al., 2018). Levoglucosenone can be converted into 1,6-hexanediol, a nylon precursor, and dihydrolevoglucosenone (cyrene), a bio-based solvent that can replace many toxic polar aprotic solvents (Cao et al., 2015; Kudo et al., 2017).
Sugar-based furanic dehydration products also have the potential as chemical building blocks. One of the most interesting molecules is 5-hydroxymethylfurfural (5-HMF), typically produced by a triple dehydration of fructose or isomerization of glucose to fructose and subsequent dehydration. It can be used to produce a range of useful molecules such as furandicarboxylic acid, levulinic acid, and dimethylfuran via catalytic routes (van Putten et al., 2013). These products, among others, can be used as platform chemicals for making solvents, polymers, fuel additives, and plastics (Werpy et al., 2004; Dutta et al., 2012; Delidovich et al., 2016; Galbis et al., 2016). Similarly, furfural, a dehydrated furanic compound derived from xylose, can be transformed into commodity chemicals such as furan, tetrahydrofuran (THF), furfuryl alcohol, tetrahydrofurfuryl alcohol, maleic acid, and methyl furan, among others, all of which are highly useful as polymer precursors, industrial solvents, and fuels (Mariscal et al., 2016). Polyols such as glycerol, and propylene and ethylene glycol are precursor chemicals for manufacturing fuel alkanes or aromatic hydrocarbons. These polyols can be generated from sorbitol, the result of glucose hydrogenation (Kunkes et al., 2008). Simple sugars can also be readily fermented into carboxylic acids such as lactic acid and succinic acid, which have applications in the food, pharmaceutical, and adhesive industries (Luterbacher et al., 2014).
Carbohydrate-derived chemicals are attractive precursors for the manufacture of new kinds of fine and commodity chemicals due to their unique properties and, in some cases, reduced environmental impact. Figure 1 illustrates a selection of the many pathways from sugars to bio-based fuels and chemicals.
3 Sugars from lignocellulosic biomass
The two most abundant biopolymers in the world are cellulose (Heinze et al., 2018) and hemicellulose (Rao et al., 2023), usually occurring together as lignocellulose, a biocomposite of these two polysaccharides along with lignin. Lignocellulose evolved as recalcitrant structural material found in the roots, stems, leaves, and seed casings of terrestrial plants. Lignocellulose is water-insoluble and resists microbial and insect-based attacks. Although this recalcitrance is a key to plant survival, it becomes a significant hurdle in efforts to release fermentable sugars from the polysaccharides in lignocellulose (Himmel et al., 2007; Zhao et al., 2012; Lindstrom et al., 2019b).
This recalcitrance is chiefly responsible for the continued dominance of 1G ethanol production from grains, sugarcane, and sugar beets despite government policies around the world being intended to promote second-generation (2G) refineries (Bertrand et al., 2012). By contrast, converting starch to fermentable sugars using enzymes or heat does not pose a significant technical or economic challenge (Kelsall et al., 2003; Bertrand et al., 2012; Brown and Brown, 2014).
Monosaccharides and disaccharides from sugar and starch crops are edible carbohydrate, which has led to the so-called “food vs. fuel” debate (Wallington et al., 2012). The basic premise is simple: using crops to produce fuels reduces the world food supply causing scarcity, increase in prices, and even deforestation in the tropics (Wallington et al., 2012). This debate gained credibility in 2008 when the price of food spiked, at a time when biofuel production increased in the USA and the European Union (EU). The World Bank and others linked these two events, appearing to validate this concern. The World Bank’s report blamed biofuel production for increasing food prices, leading to riots and financial hardship in developing nations (Mitchell, 2008). As more data become available and the initial trends failed to hold, the World Bank reviewed the 2008 event 2 years later and changed their opinion on the cause of the spike in food prices. With more time and data, they determined that the commodity price boom was mostly the result of energy prices and financial investors—not due to biofuel production (Baffes and Haniotis, 2010). The nonpartisan Congressional Budget Office agreed (Congressional Budget Office, 2009). Hoping to end the debate, the Renewable Fuels Association commissioned an analysis in 2016 when crop prices were falling and biofuel production was at record levels. Despite finding no link between food prices and biofuels (Informa Economics, 2016), the reputation of 1G biofuels was damaged in the eyes of many environmental groups and parts of the public. In principle, cellulosic biofuels circumvent this concern although one might argue that depolymerizing cellulose into glucose has transformed a structural polysaccharide into food. At the heart of this debate is deciding what level of human intervention in the environment is acceptable to provide society with basic needs beyond food.
Beyond policy or society pressures, utilizing lignocellulosic biomass instead of food crops has the potential for higher efficiency. On a land area basis, corn produces less carbohydrate than many lignocellulosic crops. Crop yields matter to both farmers and biorefineries. Transporting crops over large distances is often very expensive due to their low volumetric density, so crop yields in the surrounding areas can influence the size of a planned biorefinery (Jacobson et al., 2014). The 2016 Billion-Ton Report details the untapped potential of lignocellulosic biomass (U.S. Department of Energy, 2016). Note that sugar comprises the majority of lignocellulosic biomass (Williams et al., 2016). The amount of sugar that can actually be extracted from structural carbohydrate depends upon the biochemical or thermochemical process employed, which is explored in detail in this review.
4 Policies
Over 60 countries have put in place policies to encourage adoption of biofuels (Lane, 2019). International associations of nations have also set out goals to reduce carbon emissions that impact biofuels adoption. This section summarizes some of the most impactful policies around the world.
4.1 The United States
Two major pieces of legislation influencing biofuels' adoption emerged in the USA at the turn of the 21st century. The US Energy Policy Act of 2005 established the Renewable Fuel Standard (RFS). The standard was subsequently replaced and expanded upon by the Energy Independence and Security Act of 2007. Soon afterward, California established the Low-Carbon Fuel Standard (LCFS). Although it only applies to fuel use in California, by virtue of its large economic impact on the United States, California’s LCFS has influenced other states to adopt similar fuel policies.
The updated RFS (RFS2) created a target of 36 billion gallons (136 billion liters) of renewable fuels in the USA by 2022 (Figure 2A) (Renewable Identification Number, 2023). Of this amount, approximately 15 gallons (57 billion liters) could be 1G ethanol, whereas the remaining 21 billion gallons (79 billion liters) was mandated to be other kinds of biofuels, such as 2G ethanol, also commonly known as cellulosic ethanol (Perlack et al., 2005). The RFS is enforced through the use of renewable volume obligations (RVOs), which requires fuel producers to blend renewable fuels or purchase renewable identification numbers (RINs) from a producer who has blended more than the obligated volume (McPhail et al., 2011). The original plan called for an aggressive expansion of cellulosic biofuel production, beginning in 2010 (Energy Independence and Security Act of 2007, 2007; Regulation of Fuels and Fuel Additives, 2011).
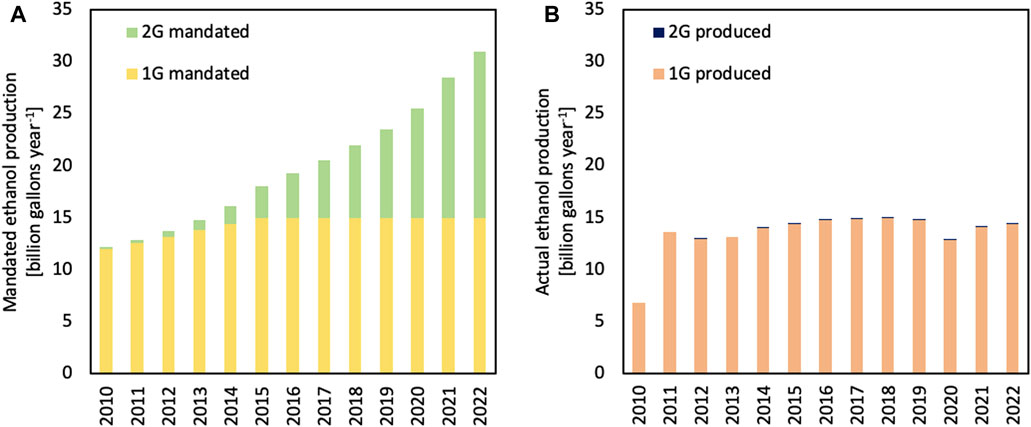
FIGURE 2. Biofuel mandates in the USA (A) have been met only for first-generation (1G) biofuels, while volumes of second-generation (2G) biofuels are less than 5% of the volumes envisioned by 2022. Actual ethanol production in the USA is shown in (B). Figures are based on Renewable Identification Number data, which excludes exported 1G ethanol, from the USA EPA.
As illustrated in Figure 2B, while 1G biofuels targets were met much faster than mandated, production of 2G biofuels is still less than 5% of mandated volumes. This failure would be even more glaring if the US Environmental Protection Agency (EPA) had not ruled that methane from the anaerobic digestion of organic wastes such as manure and wastewater solids, known as renewable natural gas (RNG), could be counted as 2G biofuels. The actual volumes of cellulosic ethanol are currently less than 15 million gallons (57 million liters) per year.
While some commercial-scale cellulosic ethanol plants were built in the USA, none remain operating today. This failure of the cellulosic fuel industry has several causes (Kramer, 2022). In part, the difficulties of deconstructing lignocellulosic biomass were not fully acknowledged, especially when scaling up technology identified in the laboratory. However, there were also market forces and policy failures at work. When the price of petroleum surged in 2008 to $146 per barrel, a 140% increase in 2 years, the future of advanced biofuels looked bright. However, the next year, the price dropped to $35 per barrel, destroying the market price of fuel ethanol along with the business model of the cellulosic ethanol industry. Finally, the volatility of RIN prices, often politically influenced, added to the risk of making long-term investments in new technology (Brown, 2019, 2018).
The (Clean Air Act of 1970) allows California to ask the EPA for a waiver to regulate transportation emissions more strictly than federal standards. This exemption was included because California established an air quality agency known as the California Air Resource Board (CARB) prior to the federal government’s standards. The unique climate and geography of California encouraged stricter emission standards than the Clean Air Act to reach air quality improvement. This waiver ultimately allowed California to explore innovations such as the LCFS to improve air quality in the state. The California LCFS works by assigning carbon intensity scores to every fuel based upon the life cycle analysis of GHGs using the California (CA) Greenhouse gases, Regulated Emissions, and Energy use in Transportation (GREET) model (California Air Resources Board, 2023). The total California fuel pool carbon intensity is set, and credits are earned for having lower scores and must be purchased for fuels that exceed the limit.
More recent policy developments include the Inflation Reduction Act of 2022, touted as the most significant of government commitments to low-carbon biofuels since the establishment of the Renewable Fuel Standard. This act includes the Higher Blend Infrastructure Incentive Program, which sets aside $500 million in government funding to expand infrastructure for biofuels production and distribution (Inflation Reduction Act of 2022, 2022). The act also extends the $1/gallon biomass-based diesel blender’s tax credit until 31 December 2024 and the $0.50/gallon alternative fuels tax credit through 2025 (Inflation Reduction Act of 2022, 2022). While expired at the end of 2021, the second-generation biofuel income tax credit was extended through 2024 (Inflation Reduction Act of 2022, 2022). Additionally, a new sustainable aviation fuel (SAF) credit was established (Inflation Reduction Act of 2022, 2022). A new Clean Fuel Production Credit will take effect in 2025 to incentivize fuels with low life-cycle greenhouse gas emissions (Inflation Reduction Act of 2022, 2022).
4.2 Brazil
Until 2006, Brazil was the largest ethanol producer worldwide (International Energy Statistics, 2017). Unlike the USA, which started its major biofuels program in 2005, Brazil launched the National Alcohol Program in 1975 in response to the 1973 oil crisis (Sewalk, 2014). This program was highly successful, leading to a rapid expansion of the Brazilian ethanol industry. Ethanol blending reached the target level of 20% in only a few years (Hira and de Oliveira, 2009). Today, standard gasoline blend in Brazil contains 27% ethanol with the option of using hydrous ethanol in specifically designed vehicles (Barros, 2018). With the passage of the Paris Agreement, Brazil introduced a new biofuels program called RenovaBio that took effect in 2020 (Barros, 2021). The new program was introduced to accelerate the transition to renewable fuels to meet the Brazilian carbon reduction commitment (Barros, 2018). Unlike the National Alcohol Program, the government does not guarantee a selling price for ethanol. RenovaBio will use tradable decarbonization credits to reach mandated carbon intensity reduction targets. Second-generation ethanol plants would utilize the vast quantities of bagasse from production of sugarcane ethanol, further reducing the carbon intensity of ethanol production in Brazil.
4.3 The European Union
The Renewable Energy Directive (RED) establishes the overall policies for renewable energy production and promotion within the EU. According to this directive, the EU had to supply at least 42.5% of its total energy requirements from renewable sources by 2030 (Directive (EU) 2023/1791 of the European Parliament and of the Council of 13 September 2023 on energy efficiency and amending Regulation (EU) 2023/955 (recast), 2023). In this directive, biofuels have been identified as instrumental in meeting the goals for renewable transportation fuel production in Europe. Furthermore, the RED also set sustainability criteria for biofuel production and consumption. The major criteria require biofuel production to achieve at least a 50% reduction in GHG emissions for biofuel operations that started production before 5 October 2015 and a 60% reduction for those that started after the same date. The RED ensures that high biodiversity areas (e.g., wetlands and forests) are not used for biofuel feedstock production. This directive encourages the biofuels industry to use dedicated energy crops and agricultural residues as feedstock (Directive (EU) 2023/1791 of the European Parliament and of the Council of 13 September 2023 on energy efficiency and amending Regulation (EU) 2023/955 (recast), 2023).
4.4 China and India
The world’s two most populous nations are aggressively developing wind and solar energy but have less ambitious goals for biofuels. For this reason, their renewable transportation fuels policies are only briefly outlined.
In 2017, China established a goal of 10% ethanol in their gasoline transportation fuel supply by 2020. At that time, domestic biorefineries were producing approximately 1 billion gallons (3.8 billion liters) of ethanol annually (Li et al., 2017), a fifth of the amount required to blend with all gasoline (UPDATE 1-China’s Tianjin to use gasoline with ethanol in most vehicles, 2018). Few biorefineries have been proposed and even fewer approved to meet this demand through domestic production alone. Faced with these constraints, China has decided to suspend the program rather than purchase ethanol from the USA or Brazil to achieve its goal (Gu et al., 2020).
Under the National Policy on Biofuels established in 2008, India set an ambitious goal of blending 20% biofuels in gasoline and diesel by 2017 (Aradhey, 2017). India missed this target, managing to blend only 3.3% in 2016 (Aradhey, 2017). This low blend rate resulted from limited supply because domestic biofuels' production was restricted to non-food feedstocks (Aradhey, 2017). Currently, the main ethanol feedstock is waste sugarcane molasses; however, the policy intended for the production goals to be met with 2G ethanol (Aradhey, 2017). India has amended its National Biofuels Policy to target 20% blend by 2025 and to permit additional feedstocks for fuel production, which include food sources (Das and Rosmann, 2023). In 2022, the average national blend rate in India was 11.5%; however, it is still expected that India will struggle to meet its 20% blend target by 2025 (Das and Rosmann, 2023).
4.5 Association of Southeast Asian Nations
While currently heavily dependent on fossil fuel, the 10 developing countries in the Pacific known as the Association of Southeast Asian nations (ASEAN) are strategically capable to produce advanced biofuels from their abundant lignocellulosic feedstocks, particularly palm biomass residues. The first ASEAN country to sign the government policy to promote the biofuels industry was Thailand in 2000, targeting 1.9% biofuel contribution to the total energy consumption by 2011 (Bloyd, 2017). The current Alternative Energy Development Plan (AEDP) in Thailand set a guideline of 20%–25% renewables target from ethanol and biodiesel by the year 2036 (Bloyd, 2017). Indonesia’s National Energy Policy in 2006 targeted energy diversification that led to a subsequent Biofuel Program with blending mandates of B35 as of 2023 (Rahmanulloh, 2022). Indonesia is a significant producer of biofuels at 9.3 billion liters in the year 2022 (Biofuel production by country/region and fuel type, 2016–2022, 2022). The other member states with blending mandates of bioethanol and biodiesel are Malaysia, Thailand, Vietnam, and the Philippines (Chanthawong and Dhakal, 2016).
4.6 The Paris Agreement
In December 2015, the United Nations Framework Convention on Climate Change (UNFCCC) met in Paris where it reached a landmark consensus on fighting climate change, establishing accelerated actions and investments to encourage a low-carbon future (Savaresi, 2016). The central aim of the Paris Agreement was to strengthen efforts to keep the rise in global temperature below 2°C from pre-industrial levels with ambitions to further reduce this rise to only 1.5°C. As of 2023, every country recognized by the United Nations has signed the agreement, although not all countries have ratified it (United Nations Treaty Collection, 2023).
Furthermore, this agreement has set a goal of strengthening the ability of countries to deal with the impacts of climate change. To achieve these ambitious goals, it is becoming increasingly important to develop 2G ethanol.
5 Deconstruction methods
In this review, we discuss three major pathways for biomass deconstruction to produce precursor sugars for advanced biofuels production. Biochemical deconstruction employs enzymatic hydrolysis to break down plant polysaccharides into fermentable sugars. Thermal deconstruction, which uses thermal energy to convert lignocellulosic biomass into monosaccharides, includes fast pyrolysis and solvent liquefaction. Challenges to sugar production via the three described routes are separately described.
Enzymatic hydrolysis utilizes a system of enzymes known as cellulases to facilitate the multistep depolymerization of cellulose in the presence of water to produce monosaccharides (Brown and Brown, 2014). In this process, insoluble cellulose is first broken down at the interface of solid and liquid by the action of endoglucanase and cellobiohydrolase to produce cellodextrins and cellobiose (Yang et al., 2011). Cellodextrins are further hydrolyzed to cellobiose by these two enzymes, while cellobiose is subsequently hydrolyzed to glucose by β-glucosidase (Dien and Bothast, 2003). The enzyme system can also include hemicellulases to hydrolyze hemicellulose although this polysaccharide is often partially or fully solubilized during pretreatments intended to improve the accessibility of enzymes to the interior of the lignocellulosic structure (Dien and Bothast, 2003).
Fast pyrolysis is the rapid thermal deconstruction of biomass in the absence or near absence of oxygen and at temperatures in the range of 400°C–600°C to produce liquid, gas, and char (Polin et al., 2019; Polin et al., 2019; Venderbosch, 2019). The predominant carbohydrate products in bio-oil are anhydrosugars that include anhydrohexoses, anhydropentoses, and di-anhydrosugars, which are formed from thermal cracking rather the hydrolysis of glycosidic bonds (Patwardhan et al., 2011a; 2009). However, the presence of xylose among the products of pyrolysis suggests that sufficient moisture is present to support partial hydrolysis of hemicellulose. Importantly, these anhydrosugars and monosaccharides have vapor pressures high enough at pyrolysis temperatures to allow them to vaporize and escape the pyrolyzer along with other volatile products. Microorganisms have evolved in burnt environments that can metabolize anhydrosugars (Layton et al., 2011; Linger et al., 2016). Furthermore, anhydrosugars such as levoglucosan and cellobiosan can be acid hydrolyzed into glucose and cellobiose, respectively, which are readily fermented by S. cerevisiae. On the other hand, S. cerevisiae is unable to convert xylose (Jansen et al., 2017) although other kinds of wild-type yeast and genetically modified microorganisms can be employed for this purpose (Seike et al., 2019).
Solvent liquefaction uses a solvent to aid in thermal deconstruction of biomass, converting cellulose and hemicellulose into carbohydrates dissolved in the solvent. This process occurs at moderate temperatures and high pressures (105°C–350°C, up to 20 MPa), depending upon the solvent system and kind of biomass (Ghosh and Haverly, 2019). Solvent liquefaction is sometimes facilitated with a homogeneous catalyst. The carbohydrate products include anhydrosugars, mono- and oligosaccharides, or alkylated sugars, depending on the type of solvent system implemented.
6 Lignocellulosic feedstock logistics
6.1 Milling and comminution
The first step in producing sugars from lignocellulosic biomass is comminution (particle size reduction). Comminution increases the surface-area-to-volume ratio of the feedstock, reducing heat and mass transfer barriers to deconstruction. For example, the rates of conversion and yields of liquid products from pyrolysis and solvent liquefaction often require very small particles to overcome heat and mass transport limitations (Gaston et al., 2011). On the other hand, enzymatic hydrolysis is typically kinetically limited by slow enzyme reaction rates and can therefore accept larger particles as long as the structure has been opened up to make the biomass more accessible to the enzymes (Cullis et al., 2004).
The cost of comminution, which typically involves one or more milling operations, can be significant. Modest size reduction may only require energy input of 90 kWh ton−1, while reducing biomass to fine powder can consume 600 kWh ton−1 (Schell and Harwood, 1994; Oyedeji et al., 2020). The desired particle size dictates the kind of milling equipment employed and affects power demand for comminution. Himmel et al. (1985) found that energy requirement increases exponentially as the milled particle size decreases, with electricity costs increasing accordingly (Mayer-Laigle et al., 2018). Finer milling increases equipment wear, which is exacerbated if the feedstock contains abrasive ash (Tolan, 2002). Additionally, predicting the costs of milling is difficult because of the great variability in biomass composition and process requirements (Kenney et al., 2013; Man, 2022).
6.2 Solid handling
Solid biomass poses significant handling issues compared to liquid and gaseous feedstocks. Whereas pumps and compressors can efficiently and reliably move liquids and gases around a biorefinery, biomass has relatively poor and unpredictable flow properties resulting in handling and conveyance equipment that is sometimes unreliable and difficult to fully automate. The 1G ethanol industry could adopt technologies developed over several decades by the food industry to handle grains and seeds, which have flow properties vastly superior to fibrous biomass. The 2G ethanol industry is still developing feedstock logistics for chipped and baled biomass.
Many industries successfully handle friable solid materials like coal and minerals, which are readily crushed to desired sizes of roughly spherical particles with manageable flow properties. Lignocellulose, on the other hand, consists of flexible plant fibers that cannot be readily crushed into small particles. Instead, these fibers must be subjected to repeated cutting operations to achieve the desired size comminution. This milling process is energy intensive and produces elongated particles of roughly cylindrical shape (Ciesielski et al., 2015). These cylindrical particles readily cling together and cause the well-known phenomenon of bridging in vertical containers or packing in bends and even vertical runs of pipes (Mattsson, 1990; Stasiak et al., 2019). Material handling becomes much easier post-deconstruction once the majority of the biomass has been solubilized or converted to liquid.
7 Biochemical deconstruction
7.1 Enzymatic hydrolysis
Enzymatic hydrolysis requires several kinds of enzymes to break glycosidic bonds in cellulose and hemicellulose. These enzymes work by diffusing into the biomass, binding to the polysaccharides, and breaking glycosidic bonds at specific locations. Given the different enzyme mechanisms, this process ultimately requires a cocktail of enzymes to liberate monosaccharides from the polysaccharides.
Enzymatic depolymerization of cellulose requires a consortium of three classes of cellulases: endoglucanase, exoglucanase (specifically cellobiohydrolase), and β-glucosidase (Figure 3) (Selinger et al., 1996). Endoglucanase targets amorphous regions of cellulose fibrils, attacking mid-chain bonds to break the cellulose into shorter cellodextrin chains (Lambertz et al., 2014). This step creates new reducing and nonreducing ends upon which cellobiohydrolase liberates some glucose units but primarily breaks cellulose down into cellobiose or longer oligosaccharides (Lambertz et al., 2014). Finally, β-glucosidase catalyzes end-chain hydrolysis of glycosidic bonds, extracting glucose from cellobiose and cellodextrin (Lambertz et al., 2014).
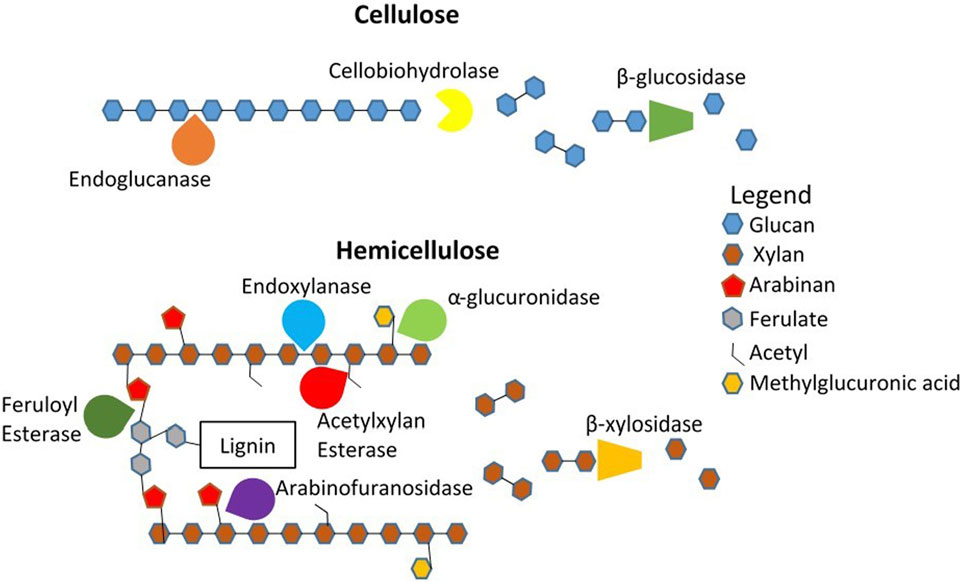
FIGURE 3. Typical enzymatic activity in saccharification of cellulose and hemicellulose entails many enzymes acting on specific locations. Figure based on Selinger et al. (1996).
The mechanism by which enzymes break glycosidic bonds is complex and highly selective. This complexity results in the enzymes being extremely sensitive to environmental conditions and structural perturbations in the enzymes. Even minor changes in geometry (less than 2 Å) to the active sites of these enzymes can result in a major reduction in hydrolysis performance (Yan et al., 2011). The mechanism of breaking glycosidic bonds varies among different kinds of enzymes. The endoglucanase protein is formed with its active site located in a large cleft that allows it to bind to cellulose at midchain positions (Brás et al., 2011). Once bound to an exposed cellulose chain, amino acids at the active site bend the cellulose chain to change the conformation of the glucan unit, thereby priming the glycosidic bond for hydrolysis (Petersen et al., 2009). Hydrolysis is carried out by opposing acid and base moieties. In the case of endoglucanase isolated from Clostridium thermocellum, these moieties are composed of glutamic acid and aspartate (Petersen et al., 2009). The glutamic acid initiates hydrolysis by protonating the oxygen on one side of the bond (Petersen et al., 2009). The aspartate then coordinates a nucleophilic attack by water on the carbon at the other end of the bond deprotonating the water molecule in the process (Petersen et al., 2009). By utilizing many small steps, endoglucanase reduces the activation energy of hydrolysis to 36 kcal mol−1 (Petersen et al., 2009). Once the glycosidic bond is severed, the endoglucanase protein unbinds from the surface, and the process repeats. Endoglucanase alone is not useful in producing monomeric sugar. Brás et al. (2011) found endoglucanase had reduced activity on cellopentaose, producing only cellotriose and cellobiose with no activity on shorter chains, indicating endoglucanase is incapable of producing glucose (Brás et al., 2011). The production of monomers and dimers from cellulose therefore requires a different enzymatic mechanism.
The active site of cellobiohydrolase, for example, isolated from Trichoderma reesei, contains one aspartic acid and two glutamic acid moieties. Through a series of hydrogen bonding interactions between enzyme and polymer, the reducing end of the cellulose chain is extracted from the cellulose fiber bundle and drawn into the enzyme (Knott et al., 2014a). The geometry of the enzyme causes the cellulose chain to twist, straining the glycosidic bond in the proximity of the enzyme’s active site (Knott et al., 2014a). With the glycosidic bond primed, a concerted acid and base attack on opposing sides of the glycosidic bond is carried out by glutamic acid and its conjugate base glutamate breaking the glycosidic bond, liberating a cellobiose molecule from the end of the polymer chain (Knott et al., 2014b). This coordinated action reduces the activation energy for glycosidic bond fragmentation from 54.4 kcal mol−1 to only 15.5 kcal mol−1, allowing the reaction to proceed at appreciable rates at modest temperatures (Mayes and Broadbelt, 2012; Knott et al., 2014b). The cellobiohydrolase enzyme moves along the cellulose chain at 3.5 nm s−1, releasing additional cellobiose molecules as it proceeds (Igarashi et al., 2009). Cellobiohydrolase, like many enzymes, have high turnover number, defined as the maximum number of chemical conversions of substrate molecules per second that a single enzyme will execute for a given enzyme concentration. However, because cellobiohydrolase can only bond with the end of a long polymer chain (Cozier, 2015), the overall rate at which it can depolymerize cellulose decreases with the increasing degree of polymerization. Consider that cellulose polymers in corn stover, for example, contain on average 2,500 glucan monomer units (Hallac and Ragauskas, 2011), then enzymatic hydrolysis by cellobiohydrolase alone would be unacceptably slow for a commercial process.
While the combination of endoglucanase and cellobiohydrolase can consume cellulose, the resulting solution of cellobiose requires a final hydrolysis step to yield glucose. Unlike the other enzymes, which bind to solid cellulose, β-glucosidase’s activity occurs in solution, which changes its kinetic behavior (Andric et al., 2010). Most β-glucosidases utilize the same active site mechanism as cellobiohydrolase with a concerted acid and base attack (Cairns and Esen, 2010). The active site is similar to that of cellobiohydrolase, but the binding domain can be quite varied. Some enzymes mimic the tunnel structure of cellobiohydrolase or cleft of endoglucanase, while others simply contain a surface depression or crater referred to as a catalytic pocket (Sørensen et al., 2013). As with most catalysts, the stabilization of the transition state speeds up the reaction rates in both directions. Endoglucanase and cellobiohydrolase prevent the reverse reaction by only binding to the cellulose chains longer than four units or by processing down the cellulose chain, respectively. In the case of β-glucosidase, the products and reactants compete to bind at the active site. This competition greatly inhibits the rate and final concentration of glucose achieved by enzymatic hydrolysis. The inhibition can be very strong with β-glucosidase from Daldinia eschscholzii being inhibited at only 0.79 mM glucose (Karnchanatat et al., 2007), while β-glucosidase isolated from Aspergillus terreus is inhibited at 13.6 mM (Kitamura et al., 1991). Due to the abundance of β-glucosidases in nature, the search for enzymes that stay productive at high glucose concentrations is ongoing (Cairns and Esen, 2010).
7.2 Pretreatment
The structure of plant cell walls and the presence of hemicellulose and lignin impede the diffusion of cellulases to cellulose fibers. As a result, enzymatic hydrolysis of unmodified lignocellulosic biomass liberates little sugar even after days or weeks of treatment (Hatakka, 1983; Rohrbach and Luterbacher, 2021). The rate and yield of enzymatic hydrolysis can be greatly increased by removing lignin and hemicellulose, which is the goal of biomass pretreatments that are frequently employed prior to enzymatic hydrolysis. Cellulases can bind to cellulose at greater rates when the normal crystalline cellulose structure is broken up into amorphous regions where cellulose is more susceptible to attack (Ciesielski et al., 2019). Success in enzymatic hydrolysis of lignocellulosic biomass requires pretreatments that both increase accessibility of enzymes to polysaccharides and transform crystalline cellulose into amorphous cellulose.
Effective pretreatments can be characterized as physiochemical, altering both the physical structure and chemical composition of the biomass. A wide range of pretreatments have been developed, ranging from soaking biomass in hot compressed water (Ko et al., 2015) to irradiation with electron beams (Bak, 2014). One way to classify pretreatments is whether they primarily target lignin or hemicellulose for removal to improve the accessibility of cellulases to cellulose.
Lignin can be modified or removed from the lignocellulosic matrix by a variety of pretreatments (Talebnia et al., 2010). Because lignin forms a protective sheath around cellulose, its removal or displacement allows cellulase to diffuse more easily to cellulose fibers. Furthermore, removal of lignin prevents the non-productive binding of enzymes to the lignin surface, increasing the effectiveness of enzymes (Kim et al., 2016).
Other pretreatments target hemicellulose in biomass, often with the goal of hydrolyzing this polysaccharide to monosaccharides, mainly xylose, along with smaller amounts of other monosaccharides. Pretreatments that are focused on hydrolyzing hemicellulose employ dilute acid or processes that generate an acidic environment via deacetylation of hemicellulose (Talebnia et al., 2010). These treatments are effective in opening the cellulose fibers as hemicellulose crosslinks cellulose and lignin. During these pretreatments, lignin detaches and migrates to the biomass surface forming distinct droplets (Donohoe et al., 2008). This reduced the surface-area-to-volume ratio of these lignin droplets compared to unmodified lignin strands mitigates, although does not eliminate, non-productive binding to enzymes. This effect can be further mitigated through the addition of nonionic surfactants (Qi et al., 2010). Examples of common pretreatment methods and their efficacy in delignifying biomass and increasing polysaccharide digestibility are summarized in Table 1.
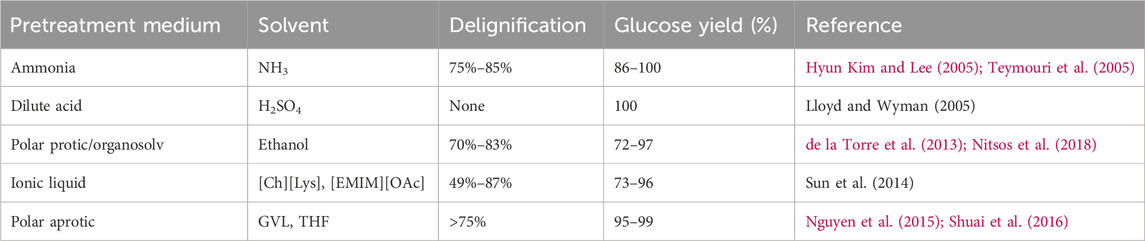
TABLE 1. Delignification and sugar recovery from enzymatic hydrolysis of lignocellulosic biomass for various pretreatment processes.
7.2.1 Ammonia
Ammonia infusion into biomass is a relatively low-cost pretreatment that is effective in removing lignin. The two most common ammonia-based pretreatments are ammonia recycle percolation (ARP) and ammonia fiber explosion (AFEX).
In ARP, ammonia interacts directly with lignin and solubilizes it. Hyun Kim and Lee (2005) reported 75%–85% removal of lignin along with 50%–60% removal of hemicellulose while retaining 92% of cellulose (Hyun Kim and Lee, 2005). This significant delignification not only opened up the structure of the biomass but also allowed the use of relatively low enzyme loadings since enzyme deactivation by lignin was substantially reduced (Hyun Kim and Lee, 2005).
AFEX exploits the fact that ammonia can be easily liquefied at moderate pressure, allowing it to readily diffuse into the biomass. When system pressure is subsequently reduced, the infused liquid ammonia instantly boils. The rapid expansion of the volatilized ammonia causes the biomass to explode, breaking the biomass into fibers. Furthermore, lignin tends to condense into droplets on the surface of the fibers and cellulose crystallinity is reduced (Mosier et al., 2005). The pretreated biomass is susceptible to enzymatic hydrolysis at modest enzyme loadings. Teymouri et al. (2005) demonstrated that ammonia pretreatment of corn stover for 5 minutes at 90°C yields almost 100% glucose and 80% xylose upon enzymatic hydrolysis. The advantage of using ammonia over other chemicals is that it is easily recovered and recycled (Kim et al., 2016). However, amide-containing by-products such as acetamide, phenolic amides, pyrazines, and imidazole are formed (Zhao et al., 2020).
7.2.2 Solvent-based pretreatments
Organic solvents are a well-known media for effective pretreatment of biomass. Solvent-based pretreatment typically implements either of the two types of solvents: polar protic or polar aprotic solvents. Each of these solvent-based pretreatment technologies is discussed below.
Biomass pretreatment using primarily polar protic solvents such as primary alcohols and formic acid is a well-established technology known as the organosolv process. Originally developed for the paper pulping industry to generate clean cellulose (Johansson et al., 1987), it was adopted as a pretreatment technique for enzymatic hydrolysis (Nitsos et al., 2018). In the organosolv process, ethanol is commonly used to solubilize the lignin and remove it from the biomass at moderate temperatures (Zhao et al., 2009). The use of ethanol as a solvent can make the pretreatment process more sustainable and more cost-effective (Silveira et al., 2015). Although not a protic solvent, acetone is also used widely for the organosolv process (Huijgen et al., 2010). An acid catalyst is often added to break apart the hemicellulose and liberate the lignin (Zhao et al., 2009). The organic solvent can be diluted with water causing the relatively unmodified lignin to precipitate from the solution, thereby facilitating its recovery (Nitsos et al., 2018). Because ethanol, methanol, and acetone can be obtained from biomass conversion technologies, these are considered green solvents. The organosolv process has the added benefit of producing a relatively pure lignin as a by-product (Sun et al., 2016).
The high rates of lignin removal make the organosolv process an attractive pretreatment for woody biomass, which is more resistance to enzymatic hydrolysis due to its high lignin content (Zhao et al., 2009). de la Torre et al. (2013) reached 87% lignin removal from wheat straw after 30 min using ethanol as the solvent. Nitsos et al. (2018) could achieve cellulose conversion yields of 72%–97% from softwood biomass. However, due to the high temperatures used, much of the hemicellulose and some of the cellulose are converted into biological inhibitors (Nitsos et al., 2018). Similar to ammonia pretreatment, organic solvents can be recovered and recycled.
Enzymatic hydrolysis of biomass polysaccharides can be significantly enhanced through thermochemical pretreatment with polar aprotic solvents. This type of pretreatment uses mild acid-catalyzed reaction conditions and water as the co-solvent for promoting solubilization and hydrolysis of hemicellulose, recovering xylose as a water-soluble product. Lignin is highly soluble in most polar aprotic solvents (Sameni et al., 2016). As a result, biomass so pretreated is rendered into a largely delignified, cellulose-rich feedstock (Nguyen et al., 2015). These compositional changes contribute to the opening of the polymeric matrix of biomass, and thus the biomass becomes substantially more susceptible to enzymatic hydrolysis (Nguyen et al., 2015; Shuai et al., 2016).
Nguyen et al. (2015) have demonstrated enhanced production of glucose, xylose, and arabinose from enzymatic hydrolysis of corn stover after pretreatment in a mixture of THF and water at 150°C with sulfuric acid serving as a catalyst. Significantly, the overall sugar yields as a result of this pretreatment reached approximately 95% even at the lowest enzyme loading of 2 mg g−1 (glucan basis) after 14 days, whereas the yield from corn stover that had been pretreated with dilute acid, a commercial benchmark for cellulosic ethanol production, was only approximately 70% under the same enzymatic hydrolysis conditions. The high sugar recovery at such a low enzyme loading was probably the result of substantial lignin removal, a conclusion supported by compositional analysis, fractal kinetic modeling, and scanning electron microscopy images (Nguyen et al., 2015).
Shuai et al. (2016) describe a mild pretreatment using biomass-derived polar aprotic solvent, γ-valerolactone (GVL), for the production of concentrated sugar solutions from hardwood biomass. This process, using 80% GVL and 20% water as co-solvents with 75 mM sulfuric acid at 120°C, could achieve 80% delignification while retaining 96%–99% of the original cellulose in the pretreated biomass. The pretreated substrate upon enzymatic hydrolysis yielded 99% and 100% of the total glucose and xylose, respectively, which was recovered at 99.5% using a liquid carbon dioxide extraction method. This GVL pretreatment process attains a threefold higher enzyme digestibility than other organic solvents, such as THF and ethanol, and 20-fold higher than pure water as the solvent.
Alkaline pretreatment uses a base, such as sodium hydroxide, to cleave lignin–carbohydrate linkages. It also solubilizes hemicellulose by saponifying ester bonds in acetyl and uronic acid moieties (Whistler, 1993). Alkaline treatments have been used for many years by the pulp and paper industry to extract lignin from wood while leaving the cellulose fibers nearly unaltered. A strong base will partially solubilize lignin in addition to hemicellulose. Weaker bases, such as calcium hydroxide, are less effective, resulting in lower lignin removal rates (Kim et al., 2016). Using sodium hydroxide at 160°C, Karp et al. (2015) could achieve 80% cellulose and xylan conversion from switchgrass. They could remove up to 70% of the lignin while retaining most of the polysaccharides, even when low concentrations of sodium hydroxide were used (Karp et al., 2015). Since alkaline pretreatment does not break glycosidic bonds in hemicellulose, enzymatic hydrolysis must include xylanases as well as cellulases to recover pentose sugars (Chen et al., 2013).
Dilute acid pretreatments generally use mineral acids, often sulfuric acid due to its low cost. The goal is to preferentially hydrolyze hemicellulose, which is more accessible to acid molecules than the tightly bundled microfibrils of cellulose (de Oliveira Santos et al., 2018). This method has the advantage of selectively removing xylose while making the cellulose fibers more accessible to cellulase during subsequent enzymatic hydrolysis (Taherzadeh and Karimi, 2007). Hsu et al. (2010) converted 89% of the hemicellulose in rice straw to xylose after dilute acid pretreatment with sulfuric acid at 160°C and 180°C, eliminating hemicellulases from the enzyme cocktail employed for subsequent enzymatic hydrolysis. Lloyd and Wyman (2005) reported cellulose conversion of near 100% after enzymatic hydrolysis of dilute acid–pretreated corn stover with a 5-minute pretreatment at 180°C and pH of 1.25.
Dilute acid pretreatments can have the unintended consequence of converting some of the released sugars into fermentation inhibitors, such as furfural and hydroxymethylfurfural (Rasmussen et al., 2014). Additionally, enzymes can bind to residual lignin, increasing enzyme loadings for effective hydrolysis of cellulose. While non-productive binding of enzymes to lignin can occur with all kinds of treatments, it can be particularly problematic with dilute acid pretreatments, with the extent depending upon the severity of the dilute acid pretreatment (Kellock et al., 2019). Despite this prominent disadvantage, the relatively low cost of dilute acid pretreatment has made it the standard pretreatment for enhancing enzymatic hydrolysis (Humbird et al., 2011).
Using only hot water, it is possible to liberate acetyl groups from hemicellulose, which further react with water to form acetic acid. This produced acid can hydrolyze hemicellulose in a manner similar to dilute acid pretreatment, which is described as autohydrolysis. Because autohydrolysis depends upon the presence of acetyl groups in biomass, this simple and inexpensive pretreatment is restricted to biomass with high acetyl content such as hardwoods (Singh et al., 2015).
By pretreating hardwoods with hot compressed water, Ko et al. (2015) could achieve cellulose conversion yields of 70%, although this required high enzyme loadings. Unfortunately, lignin in the pretreated biomass bound and deactivated the enzymes, with the result that low enzyme loadings were ineffective in converting cellulose to sugars (Ko et al., 2015).
If the hot, liquid water in the biomass is rapidly depressurized, the resulting steam explosion will, like AFEX, shatter the biomass into fibers (Taherzadeh and Karimi, 2007). However, steam explosion, unlike AFEX, promotes conversion of acetyl groups into acetic acid. As in autohydrolysis, the acid hydrolyzes hemicellulose, further opening the structure of the biomass to enzymatic hydrolysis. Unfortunately, the elevated temperature promotes degradation of the sugars into enzyme inhibitors.
Ionic liquids (ILs) have drawn increasing attention as a pretreatment for enzymatic saccharification due to their high polysaccharide solubilization capability (van Osch et al., 2017) and tunable physiochemical properties (Hayes et al., 2015; van Osch et al., 2017). Ionic liquids consist of an organic cation and an inorganic or organic anion that promote disruption of cellulose crystallinity and, therefore, significantly increase sugar yields during enzymatic hydrolysis, even at temperatures below 100°C (Zhao et al., 2010; Tadesse and Luque, 2011).
In a typical pretreatment, cellulose is substantially dissolved in IL followed by the addition of an anti-solvent such as water to precipitate the cellulose, which can be enzymatically hydrolyzed in the absence of hemicellulose and lignin (Zhao et al., 2010). During IL pretreatment, a part of the hemicellulose and lignin are depolymerized and dissolved, which can end up in the regenerated biomass (Arora et al., 2010). Most ILs are inhibitory toward enzymatic activity, so their thorough removal is required prior to enzymatic hydrolysis.
Ionic liquid pretreatment can significantly delignify biomass (greater than 80% removal) (Sun et al., 2014; Verdía et al., 2014), which increases accessibility of enzymes to cellulose in pretreated biomass. Additionally, this ability is tunable. For example, imidazolium acetate-based ILs have greater delignification efficiency (86%) and can produce up to 96% of glucose yields by enzymatic hydrolysis post-treatment (Sun et al., 2014).
7.3 Systems for converting lignocellulosic biomass into fermentation products
Like most biochemical processes, enzymatic hydrolysis and fermentation exhibit product inhibition, which complicates the design of biochemical systems to produce bio-based products. For example, cellobiose inhibits the activity of endoglucanase and cellobiohydrolase and glucose inhibits β-glucosidase (Dien and Bothast, 2003; Grata, 2020). The desire for both high reaction rates and high product yields has resulted in several distinct approaches to designing bioprocesses that incorporate enzymatic hydrolysis: separate hydrolysis and fermentation (SHF), simultaneous saccharification and fermentation (SSF), consolidated bioprocessing (CBP), and one-pot bioprocessing. These designs grapple with the trade-off between systems of complex mechanical design and those involving complex bioconversions (Figure 4). Those involving complex mechanical design consist of many unit operations that come at high capital costs and require sophisticated control systems. Conversely, systems involving complex bioconversions are potentially less expensive to build and easier to operate but require long and costly investment in research and development ahead of commercialization.
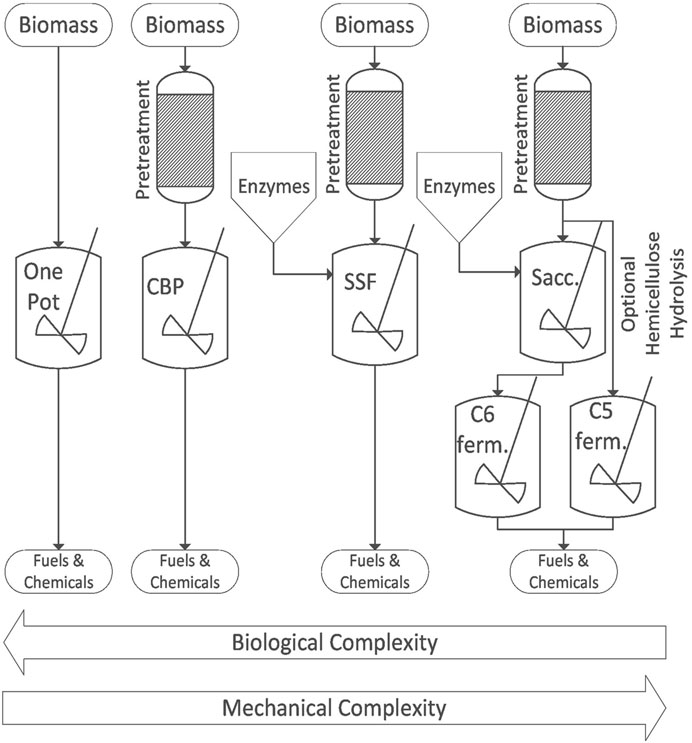
FIGURE 4. The biological and mechanical complexity of biochemical deconstruction processes are inversely correlated.
7.3.1 Separate hydrolysis and fermentation
This approach separates pretreatment, enzyme production, hydrolysis, and fermentation into separate unit operations. Biomass is pretreated to solubilize hemicellulose and improve subsequent cellulose hydrolysis. The solubilized hemicellulose can be separated from the cellulose/lignin pulp for separate saccharification and fermentation or processed together. Sufficient water is added to the cellulose–lignin pulp to form a pumpable slurry, which is transferred into a saccharification tank along with enzymes that are either purchased or produced in a separate enzyme production facility (Humbird et al., 2011). After hydrolysis is complete, the resulting sugar solution(s) are pumped into fermentation tank(s) where appropriate yeasts or bacteria are introduced to metabolize the sugars to desired products. If the sugars from cellulose and hemicellulose are separately fermented, the processes can be optimized but at the cost of mechanical complexity (Brethauer and Studer, 2015).
7.3.2 Simultaneous saccharification and fermentation
Mechanical complexity can be significantly decreased by combining saccharification and fermentation in the same reactor. Pretreated biomass is combined with both enzymes and fermentation microorganisms to simultaneously produce and consume sugars (Brethauer and Studer, 2015). Not only does SSF simplify the process but the suppression of sugar concentration in the reactor also mitigates enzyme inhibition (Wright et al., 1988).
In typical SSF processes, the biomass, enzymes, and yeast are mixed together at the beginning of the process. Adding these components incrementally allows for a more consistent sugar level, the process that is known as fed-batch SSF. Fed-batch SSF improves yeast activity and product yields by overcoming substrate inhibition and increasing solids loading, which exacerbates mass transfer limitations (Hemansi and Saini, 2023). Nguyen et al. (2017) achieved an ethanol yield of 90.5% from pretreated corn stover using fed-batch SSF at a solids loading of 20 wt%. Cellulosic emulsions have also been applied to SSF to increase mass transfer between enzymes and cellulose fibers (Hoffman et al., 2021).
Another challenge is the incompatibility of temperature and pH for hydrolysis and fermentation steps (Afedzi and Parakulsuksatid, 2023). Attempting to optimize temperature for saccharification and fermentation processes has proven to show lower fermentation yields (Sarkar et al., 2012). Thermotolerant bacteria and yeasts are being explored for their ability to withstand the optimal temperatures of both fermentation and hydrolysis (Choudhary et al., 2016; de Barros et al., 2017; Wu et al., 2021; Ndubuisi et al., 2023; Panda and Maiti, 2024). A co-culture of high temperature-resistant Saccharomyces cerevisiae and xylose-utilizing S. cerevisiae could convert corn stover to 59.8 g L−1 ethanol at 42°C (Zhu et al., 2020). A new approach shows cyclic temperature shifting with a thermotolerant yeast species to improve ethanol production from rice straw by up to 5.1-fold (Panda and Maiti, 2024).
Although mechanically simpler than SHF, SSF still requires purchase or separate manufacturing of enzymes. The capital and operating costs of SSF can be reduced if enzymes are produced on-site while also reducing the overall environmental impact (Nogueira et al., 2022).
7.3.3 Consolidated bioprocessing
The goal of CBP is to accomplish enzyme production, enzymatic hydrolysis, and fermentation using a single microorganism. The fact that this microorganism must produce a variety of enzymes and metabolize both pentose and hexose sugars into the desired product makes it the most complex bioconversion proposed for processing lignocellulosic biomass (Brethauer and Studer, 2015). The consolidation of these operations into a single reactor greatly reduces the capital and operating costs of a biorefinery (Dempfle et al., 2021). The difficulty of CBP lies in developing a microorganism with the desired metabolic pathways that is sufficiently robust to survive and produce high titers of the desired products under potentially harsh operating conditions (Lynd et al., 2016). Thus, thermophilic microorganisms have historically been the preferred microorganisms for CBP (Govil et al., 2022). The thermophile C. thermocellum converts pretreated empty fruit bunch from oil palm into glucose, acetic acid, and ethanol without the addition of external enzymes (Triwahyuni et al., 2022). Other naturally cellulolytic microorganisms have been explored, but they lack the ability to produce target compounds in desired quantities (Singh et al., 2018; Dutta and Suresh Kumar, 2023). Thus, research has pivoted toward either using a microbial consortium (Shahab et al., 2018) or genetic engineering non-cellulolytic microorganisms known to produce commercially relevant compounds (Yan and Fong, 2017; Banner et al., 2021). The non-conventional yeast Yarrowia lipolytica was genetically engineered to enhance cellulolytic function and achieved a 50% conversion rate of pretreated corn stover (Xu et al., 2018). Many studies emphasize the potential of yeast S. cerevisiae as a CBP candidate due to its heightened fermentation properties and ability to undergo genetic manipulation (Banner et al., 2021; Minnaar et al., 2024). Adding an enzyme cocktail of laccase, cellulase, and xylase to aid in lignin depolymerization enhanced ethanol production of S. cerevisiae (Rajak and Banerjee, 2020). Industrial scale implementation of CBP requires advanced research to identify robust microorganisms and widen the product range. Currently, no single microorganism has been identified nor engineered to enzymatically deconstruct lignocellulose, hydrolyze to sugars, and ferment to desired products (Minnaar et al., 2024).
7.3.4 One-pot integrated processing
A simple example of one-pot processing is the anaerobic digestion of mixed streams of lignocellulosic biomass and manure (Neshat et al., 2017). Raw feedstock without pretreatment is added into a reactor where enzymes released from a consortium of bacteria and fungi hydrolyze polysaccharides, fats, and proteins into simple sugars, fatty acids, and amino acids, respectively. Acetogens convert these intermediate products into carboxylic acids, which are subsequently converted by methanogens into methane, all within the same reactor. Even the separation of gaseous products from the reactants and solid products occurs in the same reactor. It might be argued that nature perfected this one-pot integrated process, but it is a useful model for envisioning engineered systems developed along the same principle of all reactions occurring in a single vessel.
Attempting to mimic the natural bioreactor process used by bovine animals has led to the development of co-treatment. This process, developed by the BioEnergy Science Center at the Oak Ridge National Laboratory, does not employ chemical pretreatment. Instead, biomass is deconstructed by continual or periodic milling, during or after partial enzymatic digestion (Paye et al., 2016; Balch et al., 2017). The combination of enzymes and milling creates a synergistic effect that achieves sugar yields from switchgrass up to 88% (Balch et al., 2017). As co-treatment is a relatively new technology, further development is required to improve microorganism survivability and optimize the in situ milling process. Eliminating toxic chemicals and harsh processing conditions makes co-treatment with CBP a very promising approach to liberate sugars from biomass (Lynd et al., 2017).
The Joint BioEnergy Institute at the Sandia National Laboratories has recently developed another approach to a single-pot process, made possible through the discovery of biocompatible ionic liquids such as cholinium lysinate ([Ch][Lys]) that readily solubilize cellulose (Liszka et al., 2016; Xu, F. et al., 2016). Because these so-called “bionic liquids” are non-toxic to enzymes and microorganisms, the solubilized carbohydrate does not have to be recovered from the solvent to perform enzymatic hydrolysis and fermentation. Its current manifestation still requires separate addition of enzymes although the microorganisms developed for CBP, in principle, could be used in this one-pot integrated process to truly combine all the steps required to convert lignocellulosic biomass in a single reactor.
7.4 Industrial considerations
7.4.1 Enzyme cocktail
To assure fast and efficient conversion of polysaccharides in biomass to fermentable sugars, enzyme cocktails must be tailored to the specific biomass feedstock. In addition to cellulases, hemicellulases can be added if the substrate includes significant hemicellulose (Dien and Bothast, 2003). Due to the variety and quantity of enzymes that must be produced, enzyme cocktails are expensive and represent a large operating cost for sugar production.
7.4.2 Enzyme production and recycling
To reduce enzyme costs, on-site manufacture and recycling have been contemplated for commercial operations. Onsite enzyme production eliminates transportation costs and offers cost savings through integration with other processes in the plant (Humbird et al., 2011). Recycling has proven difficult to accomplish as processes used to concentrate the enzymes can also destroy them. One of the most promising methods recycles the solid residue from saccharification, which contains significant amounts of enzymes adsorbed onto the solid residue (Humbird et al., 2011).
7.5 Process flow
The flow of materials through a biorefinery based on dilute acid pretreatment and enzymatic hydrolysis is illustrated in Figure 5. The high selectivity of enzymes results in most of the carbohydrate being converted to monosaccharides, while lignin is essentially unconverted and removed as lignin cake. In practice, this lignin stream often contains substantial carbohydrates not effectively separated or saccharified in the process.
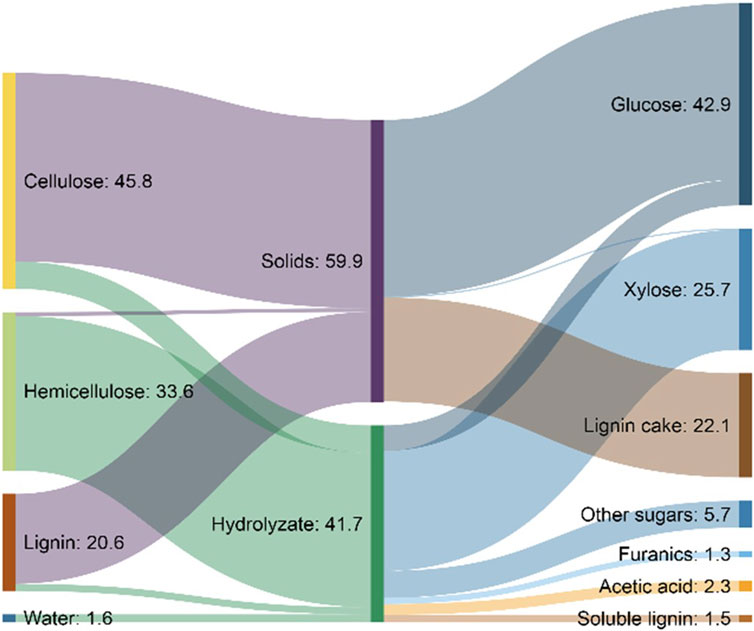
FIGURE 5. Theoretical mass flows in a 2,000-ton-per-day ethanol biorefinery using dilute acid pretreatment of corn stover as modeled by the National Renewable Energy Laboratory (NREL) (Humbird et al., 2011).
7.6 Challenges to sugars via enzymatic hydrolysis
Enzymatic hydrolysis is a highly selective process for deconstructing polysaccharides, achieving over 90% yields of glucose and xylose at low temperatures. Nevertheless, it is yet to become an economically viable technology. As evident from Figure 6, the mass loading of enzymes with respect to the carbohydrate substrate correlates positively with the increased rate of enzymatic hydrolysis. This trend holds for well-established dilute acid pretreatment (Figure 6A) as well as more recently developed organic solvent-based pretreatments (Figure 6B). Regardless of the pretreatment, enzymatic hydrolysis takes several hours to a few days to achieve sugar yields surpassing 70% (Nguyen et al., 2015).
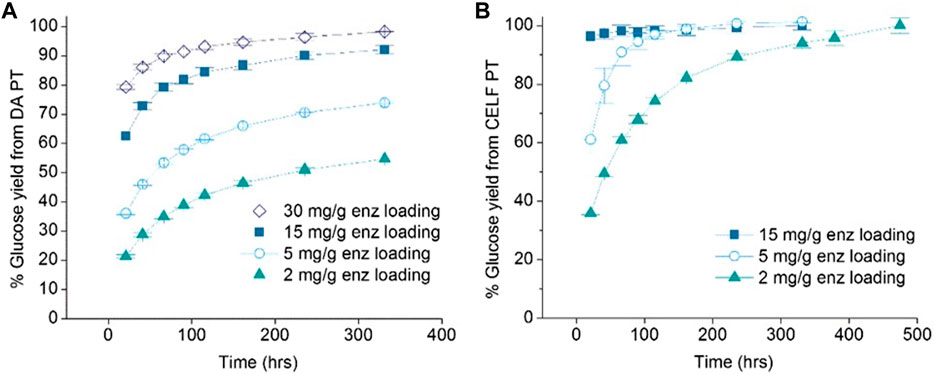
FIGURE 6. Glucose release with reaction time for (A) dilute acid-pretreated corn stover using enzyme and (B) THF/water/acid-pretreated corn stover using enzyme. Reprinted with permission from Nguyen et al. (2015). DAPT, dilute acid pretreatment; CELF PT, so-called solvent-enhanced lignocellulosic fractionation pretreatment.
The catalytic activity of cellulases can suffer from product inhibition, a common phenomenon in bioconversion processes. The xylo-oligomers, furans, and phenolic compounds generated during pretreatment also negatively impact enzyme activity (Qing et al., 2010; Kim et al., 2011). Furthermore, biochemical processing requires substrate-specific enzymes, sterilization of reaction vessels and piping, and complicated separations to recover enzymes (Brown and Brown, 2014).
8 Thermochemical deconstruction
Thermochemical deconstruction of biomass includes fast pyrolysis and solvent liquefaction (Brown and Zhang, 2019). These processes were developed to deconstruct biomass into liquids known as bio-oil or biocrude. As traditionally produced, these liquids contain furans and other light oxygenates derived from polysaccharides but very little sugar. In recent years, biomass pretreatments and processing conditions have been identified that generate significant quantities of mono- and disaccharides (Ghosh and Haverly, 2019; Venderbosch, 2019). Although the yields are typically lower than that achieved through enzymatic hydrolysis, the processes are fast and simple and have the potential to produce inexpensive sugars from lignocellulosic biomass.
8.1 Fast pyrolysis
Fast pyrolysis is the thermal decomposition of organic matter in the absence of significant oxidation at moderate temperatures (400°C–600°C) producing primarily liquid products (bio-oil) as well as solid (biochar) and non-condensable gases (NCG) (Radlein and Quignard, 2013; Pecha et al., 2019; Venderbosch, 2019). As the name implies, the feedstock must be rapidly heated. Under ideal circumstances, fast pyrolysis of biomass can yield up to 75 wt% bio-oil, where 60 wt% is organic compounds with the balance comprising water (Bridgwater, 2012). Biochar and NCG can be combusted for process heat although there is increasing interest in using biochar for other applications such as for use as a soil amendment and carbon sequestration (Brewer et al., 2009; Woolf et al., 2010; Brown et al., 2015; Smith, 2016).
8.1.1 Bio-oil
Bio-oil is the liquid product from pyrolysis of biomass. Most of this liquid is condensed from vapors released during pyrolysis (Lindstrom et al., 2019b; Tiarks et al., 2019). Organic vapors must be rapidly removed from the pyrolyzer and cooled to prevent secondary decomposition reactions, reducing the yield of bio-oil such as in the decomposition of volatilized sugars (Shin et al., 2001; Evans and Nimlos, 2002; Zhang et al., 2012; Haverly et al., 2015). The liquid from pyrolysis of lignocellulosic biomass includes hundreds of compounds (Chaala et al., 2004; Patwardhan et al., 2011b; 2011a; 2009), which complicates its analysis and the separation of products (Carpenter et al., 2014). It is well known that phenolic compounds derived from lignin are chiefly responsible for the high viscosity (Bridgwater, 2003) of bio-oil, while phenolic compounds and carboxylic acids both contribute to its high corrosivity (Bridgwater, 2003; Keiser et al., 2014; Haverly et al., 2015). Less well known, bio-oil can also contain significant quantities of sugar, depending on how the biomass is prepared and processed.
Most sugars have vanishingly small vapor pressures (Oja and Suuberg, 1999; Westerhof et al., 2011), and their discovery in bio-oil was somewhat surprising, encouraging the idea that thermal ejection was responsible for their presence. However, studies on sugars and anhydrosugars, a class of carbohydrates that lack one or more water molecules when compared to standard carbohydrates, which are found in bio-oil, revealed that they had significant vapor pressures at pyrolysis temperatures (Oja and Suuberg, 1999). Heating these carbohydrates as pure compounds revealed that they can be readily volatilized (Bai et al., 2013). Table 2 depicts the most common sugar products from biomass fast pyrolysis. Sugar yield depends upon the type of polysaccharide, reaction conditions, and whether secondary reactions that degrade sugars proceed to a significant extent.
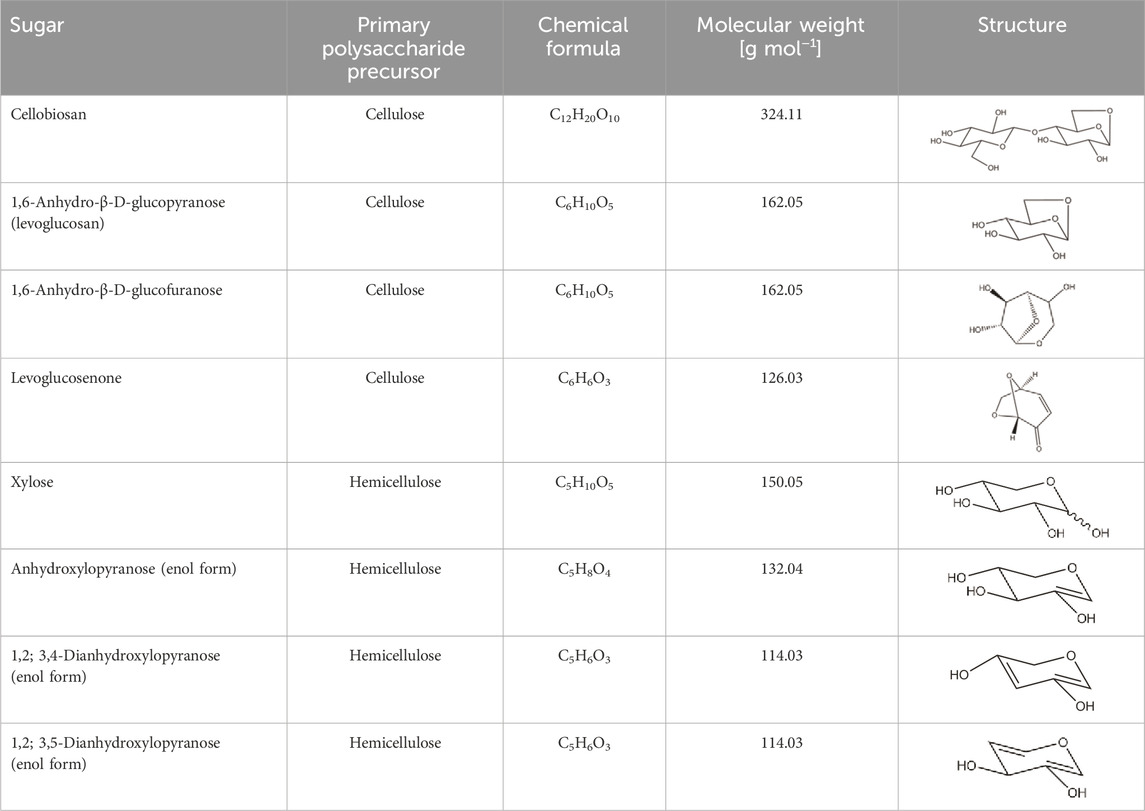
TABLE 2. Major sugars products from biomass fast pyrolysis organized by descending molecular weight and the most likely polysaccharide precursor: cellulose (Patwardhan et al., 2009) or hemicellulose (Patwardhan et al., 2011a).
The yields of these sugars are also highly dependent on the presence of naturally occurring alkali and alkaline earth metals (AAEMs) in the biomass, which catalyze pyranose and furanose ring fragmentation in polysaccharides (Patwardhan et al., 2010; Kuzhiyil et al., 2012; Zhou et al., 2016). Secondary interactions with biochar, which contains AAEM, catalyze secondary reactions of levoglucosan decomposition and degrade pyrolytic vapors, leading to decreased sugar yields during pyrolysis (Plouffe et al., 2022). Biomass pretreatment to remove or passivate AAEM is therefore required to obtain high sugar yields from biomass.
8.1.2 Biomass pretreatment to enhance pyrolytic sugar production
During biomass pyrolysis, AAEM cations interact with polar moieties and functional groups in carbohydrates, leading to greatly reduced sugar yields compared to pure polysaccharides (Mayes et al., 2015). Sugar yields comparable to pure polysaccharides can be achieved for lignocellulose by either liquid extraction of soluble AAEMs or passivating the catalytic activity of AAEMs in situ prior to pyrolysis (Golova and Krylova, 1960; Kilzer and Broido, 1965; Broido, 1966; Patwardhan et al., 2010; Kuzhiyil et al., 2012; Bai et al., 2014; Dalluge et al., 2014; Wang et al., 2014; Oudenhoven et al., 2016a; 2016b). Regardless of the pretreatment method, AAEMs must be dealt with thoroughly as each metal atom is estimated to catalyze up to 1,000 fragmentations of pyranose or furanose rings (Zhou et al., 2016).
Both AAEM extraction and passivation improve sugar yields from fast pyrolysis of lignocellulosic biomass, but the application of these pretreatments differs substantially. Extraction involves using water to wash the AAEMs from the biomass. Inclusion of acids, such as carboxylic acid produced during pyrolysis, improves the extraction (Oudenhoven et al., 2016b). This technique increases sugar yields compared to no pretreatment (Oudenhoven et al., 2016b) but has significant drawbacks. Washing requires substantial water usage, which in turn is expensive to dry prior to pyrolysis and to treat prior to discharge (Oudenhoven et al., 2016b). For these economic reasons, this review focuses primarily on passivation.
Passivation predominantly uses mineral acids to convert AAEM cations in biomass into thermally stable salts (Kuzhiyil et al., 2012). When using acids, AAEMs likely bind to the conjugate base, forming inorganic salts. For example, if sulfuric acid is used, the conjugate base would be sulfate or hydrogen sulfate (bisulfate), which bonds with AAEMs forming salts such as calcium sulfate and sodium hydrogen sulfate (Kuzhiyil et al., 2012). AAEMs are less catalytically active when bonded as thermally stable salts. Although the protons released into the biomass in this manner do not appear to catalyze pyranose and furanose ring fragmentation, excessive acid can diminish sugar yields. Accordingly, there appears to be an optimal acid pretreatment level to passivate AAEMs (Figure 7) (Kuzhiyil et al., 2012).
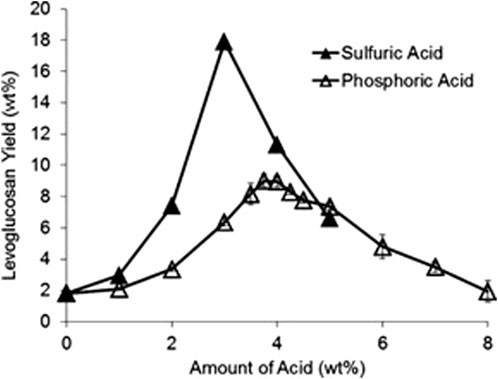
FIGURE 7. Levoglucosan yield from corn stover pyrolysis can be improved by judicious acid pretreatment reproduced from Kuzhiyil et al. (2012) with permission from Wiley Online Library.
Optimal infusion of mineral acid into lignocellulosic biomass can effectively passivate all catalytic activity of AAEMs, achieving sugar yields in (batch) micro-pyrolyzers equal to those from pyrolysis of pure polysaccharides, up to approximately 60 wt% (Patwardhan et al., 2010; Kuzhiyil et al., 2012; Wang et al., 2014). Enhancements from pretreating biomass are typically the greatest for biomass containing high AAEM content (Kuzhiyil et al., 2012; Dalluge et al., 2014). Continuous pyrolysis of pretreated biomass has also demonstrated enhanced sugar yields although to date they have only reached approximately 30 wt% monosaccharides on a polysaccharide basis (Kuzhiyil et al., 2012; Dalluge et al., 2014; Kim et al., 2014; David et al., 2018; 2017). Possible explanations for this discrepancy are subsequently discussed.
Kuzhiyil et al. (2012) developed a stoichiometric relationship between the AAEM content of biomass and amount of acid required for AAEM passivation. Polyprotic acids, such as sulfuric acid, can donate multiple protons, thereby generating more negative electric charges in the form of polyanionic conjugate bases, enhancing the AAEM passivation potential. Conversely, monoprotic acids, such as hydrochloric acid, can produce only monoanionic conjugate bases and are therefore less efficient on a molar basis. In addition to the number of protons available to donate, low acid dissociation constants (pKa) are very important. The conjugate base—not the proton—inhibits the AAEMs, so a stronger acid leads to more available conjugate base anions for a given amount of acid. In moderation, the proton itself appears unimportant and does not catalyze sugar destruction but is not wholly desirable because excessive acid addition produces lower sugar yields (Kuzhiyil et al., 2012). Theoretically, other chemicals could be used as long as they release appropriate anions and the corresponding cation does not catalytically degrade carbohydrates during pyrolysis. Additionally, these salts must be thermally stable. Kuzhiyil et al. (2012) claim that the greater thermal stability of potassium hydrogen sulfate compared to potassium dihydrogen phosphate explains the superior performance of sulfuric over phosphoric acid. This same explanation applies to carboxylic acids as they are not thermally stable and have higher dissociation constants and therefore yield less sugar (Kuzhiyil et al., 2012).
Maintaining the optimal level of acid pretreatment is essential to maximizing sugar yields, as illustrated in Figure 7. Adding too little or too much acid drastically reduces sugar yield, so pretreatment levels must be carefully monitored. Aside from this issue, acid pretreatment has another large operational challenge: agglomeration.
8.1.3 Overcoming pretreatment-caused agglomeration
Pyrolysis of biomass without pretreatment usually yields a fine char, which can be elutriated and captured in a gas cyclone. Acid-pretreated biomass, on the other hand, results in large masses of agglomerated char and bed material. Agglomerates are not necessarily an impediment to proper reactor operation. For example, auger pyrolyzers readily grind agglomerated char as it is formed (Dalluge et al., 2014). On the other hand, agglomeration of char in a fluidized bed pyrolyzer forces operation at reduced biomass feed rates to maintain stable bed operation, which in turn reduces rates of sugar production. Understanding the mechanism by which agglomerates form is important to advancing the production of pyrolytic sugars.
The fact that biomass from which AAEM has been substantially extracted by water washing demonstrates that agglomeration arises from the loss of AAEM rather than the addition of protons to the biomass. The surface of agglomerated char from pyrolysis of washed biomass (Oudenhoven et al., 2016a) and acid-pretreated biomass (Rollag et al., 2020) suggests the formation of a melt phase prior to dehydration to char. This melt incorporates particles of bed media (sand), creating large agglomerates (Oudenhoven et al., 2016a). Rollag et al. (2020) have recently discovered that AAEM catalyzes depolymerization of both polysaccharides and lignin. It appears that AAEM increases the rate at which lignin depolymerizes and devolatilizes (Rollag et al., 2020) without substantially altering the final product's composition (Dalluge et al., 2017).
Tiarks et al. (2019) used optical and laser visualization techniques to explore the pyrolysis of lignocellulosic biomass and its components, which helps understand agglomeration of lignin. Upon pyrolysis on a heated metal strip, technical lignin powder produced large agglomerates, which was not observed for pyrolysis of wood powders. However, by mixing the lignin powder with nonreactive inorganic filler, simulating the dispersion strands of lignin polymers among the polysaccharides in biomass, agglomeration was eliminated. This suggests that char agglomeration occurs if dispersed strands of lignin have time to melt and coalesce before they can depolymerize into volatile molecules.
Since most biomass naturally contain sufficient AAEMs to catalyze lignin depolymerization, devolatilization proceeds more quickly than melt diffusion, with the result that lignin dehydrates in place to produce fine char particles that retain the cell wall structure. Removal or passivation of AAEMs slows depolymerization and devolatilization, giving time for melted lignin to diffuse to particle surfaces where it acts as an adhesive to bind together both pyrolyzing biomass particles and bed media. Untreated corn stover rind before and after pyrolysis have largely intact plant cell wall structures (Rollag et al., 2020). On the other hand, acid pretreated corn stover rind pyrolyzed for the same time duration has clearly melted (Rollag et al., 2020). Removing the catalytic activity of the AAEM promotes the melting and diffusion of lignin to the biomass surface, where it serves as an adhesive to bind particles together and subsequently dehydrate into agglomerated char (Rollag et al., 2020). Small additions of calcium hydroxide to a fluidized bed pyrolyzer has been shown to reduce although not eliminate char agglomeration of lignin (Zhou et al., 2015), and of course the addition of this alkaline earth metal when pyrolyzing whole biomass would be detrimental to sugar yields.
After discovering the role of AAEMs in depolymerizing lignin, Rollag et al. (2020) sought a biomass pretreatment that both passivated AAEMs and selectively catalyzed lignin depolymerization. Ferrous sulfate proved particularly effective, although magnesium sulfate was also successful (Rollag et al., 2020). The sulfate anion passivates AAEMs in the biomass, while the ferrous cation catalyzes lignin depolymerization without interfering with sugar yields. This new pretreatment intensifies volumetric sugar productivity (g L−1 h−1) by simultaneously increasing sugar yields and maintaining high biomass throughput. Rollag et al. (2020) also showed that the pyrolyzer could run autothermally, which further intensifies the process.
Adding small amounts of oxygen to a pyrolyzer in the form of air at low equivalence ratios, typically anathema for pyrolysis, can greatly increase biomass throughput for a reactor of given dimensions. Polin, Carr, et al. (2019) and Polin, Peterson, et al. (2019) increased the biomass throughput for an 8.9-cm-diameter reactor by threefold to fourfold through autothermal operation. Furthermore, intensification increases with reactor size, scaling linearly with reactor diameter (Brown, 2020). These methods may also reduce agglomeration by oxidizing char agglomerates (Kim et al., 2014). While the addition of oxygen to a pyrolyzer releases CO and CO2, life cycle analyses of pyrolysis and autothermal pyrolysis demonstrate net carbon removal (Ganguly et al., 2022). Ganguly et al. (2022) demonstrated that for a 250-ton-per-day autothermal pyrolysis facility–processing corn stover, red oak, or yellow pine, the amount of carbon removed from the atmosphere was greater than the amount of carbon emitted. This is primarily due to the products of biochar and phenolic oil (for bio-asphalt application) that sequester biogenic carbon (Ganguly et al., 2022).
Pyrolysis has the potential to dramatically increase volumetric sugar productivity compared to enzymatic hydrolysis (Rollag et al., 2020). Under conventional (non-oxidative) pyrolysis of untreated corn stover, volumetric sugar productivity was 62 g L−1 h−1 compared to only 5.4 g L−1 h−1 for enzymatic hydrolysis of corn stover. However, the combination of ferrous sulfate pretreatment, which increased sugar yields on a biomass basis from less than 1% to over 12%, and autothermal pyrolysis, which increased biomass throughput by a factor of 2.5, increased volumetric sugar productivity to 2041 g L−1 h−1 (Rollag et al., 2020). An optimum reactor temperature of 450°C maximizes sugar production from autothermal pyrolysis of ferrous sulfate–pretreated corn stover (Peterson et al., 2023).
8.1.4 Process flow
Figure 8 demonstrates that fast pyrolysis of untreated biomass yields less bio-oil while producing more gas and char than pretreated biomass. Furthermore, the concentration of sugar in bio-oil is higher when pyrolyzing pretreated biomass.
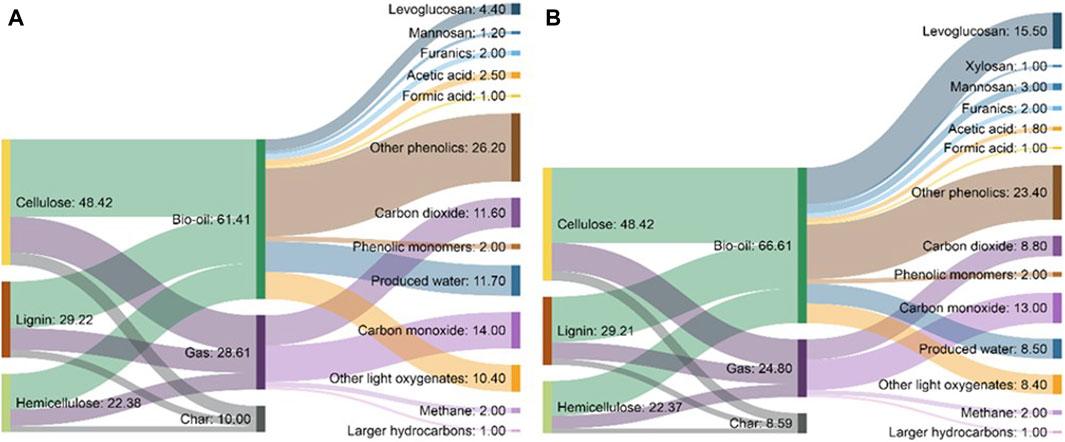
FIGURE 8. Sankey diagrams demonstrate the differences in product yields from fast pyrolysis of unmodified (A) and acid-pretreated (B) pine. Figure produced using the pine composition and product yields from Oudenhoven et al. (2016b) and Williams et al. (2017), respectively, assuming proportional fractions of the biopolymers generate each product stream.
8.2 Challenges to sugars via fast pyrolysis
Using pyrolysis to produce sugars from lignocellulosic biomass has three primary challenges: sugar yield limitations, sugar separation from bio-oil, and utilization of anhydrosugars in fermentation processes (Brown, 2021).
8.2.1 Sugar yield limitations
Fast pyrolysis rapidly converts polysaccharides into monosaccharides and, to a lesser extent, disaccharides; however, the elevated temperature of pyrolysis also promotes secondary reactions that degrade sugar monomers. For example, fast pyrolysis of cellulose even under ideal laboratory conditions rarely yields more than 60 wt% sugar, which stoichiometrically should be 100 wt% (Patwardhan et al., 2009). Competition among three condensed phase reactions may prevent higher yields than presently achieved: cracking (the primary depolymerization reaction), end-chain levoglucosan production, and degradation reactions (Lindstrom et al., 2019a). Cracking reactions convert polysaccharides to anhydro-oligosaccharides that are subsequently cracked into smaller anhydro-oligosaccharides (Radlein et al., 1987; Mayes and Broadbelt, 2012; Vinu and Broadbelt, 2012; Gong et al., 2014; Burnham et al., 2015; Lindstrom et al., 2019a). Levoglucosan can form directly from anhydro-oligosaccharides and readily volatilizes (Mayes and Broadbelt, 2012; Vinu and Broadbelt, 2012; Burnham et al., 2015; Lindstrom et al., 2019a). Secondary reactions limit sugar production by decomposing levoglucosan (Lindstrom et al., 2019a).
As discussed earlier, AAEMs promote pyranose and furanose ring fragmentation. The ion-dipole forces between the AAEM atoms and carbohydrates alter the reaction rates (Mayes et al., 2015), leading to reduced sugar yields. It is worth reiterating that preventing these reactions, by extracting or passivating the AAEM, only increases sugar yields to the levels observed for pure polysaccharides, which is much below the expected stoichiometric yields. Although some authors have claimed higher yields (Maduskar et al., 2018), these results have not been reliability reproduced by others.
The maximum sugar yield achieved in continuous pyrolysis systems is almost 50% lower than that achieved in microscale benchtop reactors even when using the same pretreated biomass for the experiments (Kuzhiyil et al., 2012; Dalluge et al., 2014). The lower yields from continuous pyrolysis are not fully understood but may be due to longer vapor residence times during which secondary reactions can decompose sugars. Indeed, Ronsse et al. (2012) demonstrated that alkali-rich char catalyzes vapor-phase decomposition of levoglucosan at pyrolysis temperatures.
8.2.2 Sugar separation from bio-oil
The conventional approach to recovering condensable products of pyrolysis involves the rapid cooling of pyrolysis vapors in a spray of non-polar liquid (Venderbosch, 2019). This yields an emulsion of lignin-derived phenolic compounds in an aqueous phase in which most of the carbohydrate-derived compounds are dissolved. Although the phenolic compounds (often referred to as “pyrolytic lignin”) in this bio-oil can be precipitated by adding water, separating sugar from the aqueous phase is more challenging. Even the volatile components cannot be separated by distillation because bio-oil is extremely reactive. To combat these problems, condensable products of pyrolysis are increasingly being recovered in stages by exploiting differences in vapor pressure for the various components, as illustrated in Figure 9. High-boiling-point anhydrosugars such as levoglucosan and sugars such as xylose will condense at the highest temperatures, followed by phenolic compounds such as guaiacol and o-creosol, and ultimately lighter compounds such as furfural and acetic acids, as the temperature is lowered.
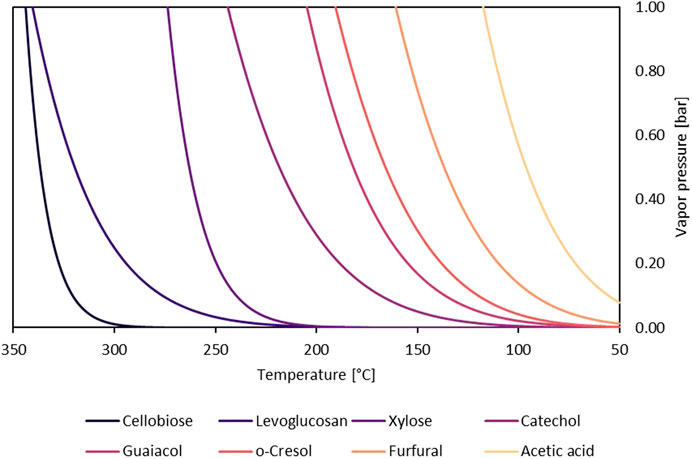
FIGURE 9. Vapor pressures show significant differences among common bio-oil components. Temperatures are displayed in the reverse order to illustrate chemicals condensing as the bio-oil vapors are cooled. Pressures calculated using the Antoine equation with constants from Oja and Suuberg (1999) and the National Institute of Standards and Technology (NIST) (NIST Chemistry WebBook, 2023). Cellobiose was used in lieu of cellobiosan as the Antoine constants were unavailable.
One scheme for selective recovery of the components of bio-oil is illustrated in Figure 10 (Pollard et al., 2012). Products of pyrolysis entrained in the gas flow leaving the pyrolysis reactor pass through gas cyclones for the removal of particulate matter (biochar), and then through a temperature-controlled condenser that cools the gas stream to 102°C, which is low enough to condense sugars, anhydrosugars, and most of the phenolic compounds in the stream. This so-called stage fraction 1 (SF 1) could, in principle, be operated at higher temperatures to encourage phenolic compounds to be collected downstream of SF 1, but success in this separation depends upon the relative vapor pressures of the sugars and phenolic compounds and the thermal stability of the sugars at higher quench temperatures (Dalluge et al., 2019). High-boiling-point aerosols produced during this cooling process must be separately recovered in a temperature-controlled electrostatic precipitator (ESP), designated as SF 2. The composition of liquids recovered from SF 1 and 2 have similar composition (Pollard et al., 2012), thus they are often combined and referred to as the “heavy ends” of bio-oil. A relatively simple water extraction can separate the water-insoluble phenolic compounds from the water-soluble sugars (Stanford et al., 2018). The sugar-rich aqueous solution (syrup) contains a small number of phenolic compounds that are well-known fermentation inhibitors (Rover et al., 2014) that must be removed before the syrup can be used as substrate in bioconversions. Filtration with resin columns has proved effective in this respect (Stanford et al., 2018). Stage fractions operating at progressively lower boiling points can collect other fractions of bio-oil.
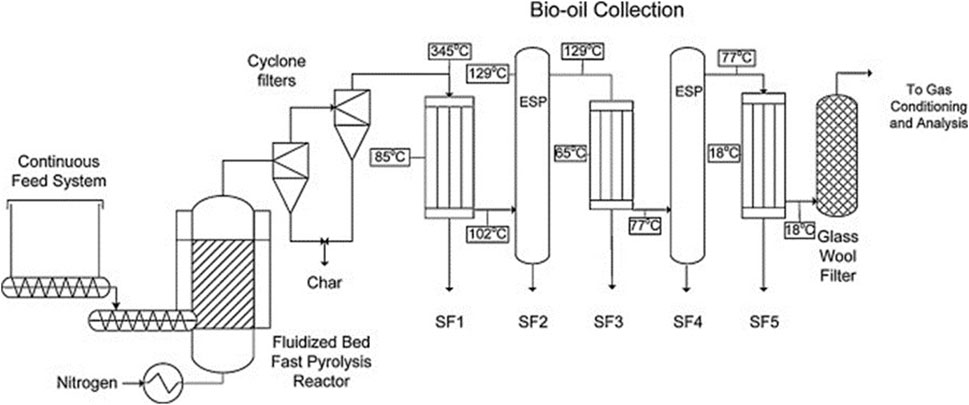
FIGURE 10. Pairs of condensers to quench pyrolysis vapors according to boiling points and electrostatic precipitators (ESPs) to collect aerosols can be used to produce stage fractions (SFs) of bio-oil. Figure reprinted with permission from Elsevier, Inc. (Pollard et al., 2012).
8.3 Bioconversion of anhydrosugars
Most sugar bioconversion pathways require fully hydrated carbohydrates rather than anhydrosugars. Acid hydrolysis readily converts anhydrosugars into their fully hydrated forms that can be fermented into biochemical products such as ethanol (Shafizadeh et al., 1979; Helle et al., 2007; Bennett et al., 2009). The kinetics of levoglucosan hydrolysis have been well captured by Helle et al. (2007). Levoglucosan, and presumably other anhydro-monosaccharides, are hydrated into their fully hydrated counterparts, namely, glucose. Cellobiosan is either first hydrolyzed to cellobiose followed by hydrolytic breaking of the glycosidic bond between the two monomeric units to liberate glucose or the glycosidic bond is first hydrolyzed to release glycose and levoglucosan followed by hydration of the levoglucosan to glucose.
Acid hydrolysis must be followed by acid neutralization and sugar purification to produce a sugar-rich syrup suitable for fermentation. As soluble salts inhibit fermentation (Casey et al., 2013), an effect neutralization strategy is used to make a metal hydroxide [e.g., Ca(OH)2] react with the mineral acid to create water-insoluble precipitates (Chan and Duff, 2010; Lian et al., 2010). However, separation of these precipitates in a biorefinery would be challenging due to polymerization of phenolics during acid hydrolysis (Stanford et al., 2018). To overcome this challenge, Ghosh et al. (2023) developed an acid hydrolysis process upon which the neutralization of the sulfuric acid catalyst would be compatible with downstream sugar purification and fermentation. Using 150 mM sulfuric acid at 115°C during a 3-hour reaction, glucose production was maximized within acceptable ranges of acid concentration and temperature for sustainable and economic biorefining (Ghosh et al., 2023).
Although not commercially developed at this time, some wild microorganisms can utilize anhydrosugars as sources of energy and carbon (Bacik and Jarboe, 2016). Levoglucosan and cellobiosan, in particular, are thermally generated in forest fires (Vicente et al., 2013), which explains the evolutionary pressure for the emergence of anhydrosugar-utilizing microorganisms. Some microorganisms directly metabolize levoglucosan and cellobiosan (Kitamura et al., 1991; Yasui et al., 1991; Lian et al., 2016), while others require exogenous sources of β-glucosidase to utilize cellobiosan (Linger et al., 2016). Considering the hundreds of years that microorganisms have been bred to utilize fully hydrated sugars in commercial processes, hydrolyzing anhydrosugars from pyrolysis followed by fermentation of glucose with commercially available yeasts and bacteria might be the most expedient path forward in the near term. However, engineering new microorganisms that can directly exploit anhydrosugars would eliminate the unit operations of acid hydrolysis and neutralization, reducing capital and operating costs of a biorefinery based on production of pyrolytic sugars.
9 Solvent liquefaction
Solvent liquefaction is another promising route for thermochemical production of cellulosic sugars. Solvent liquefaction is broadly defined as the conversion of biomass or other carbonaceous feedstocks in the presence of a solvent into primarily liquid or solubilized compounds, gas, and solids (Behrendt et al., 2008; Kandiyoti et al., 2017; Ghosh and Haverly, 2019). There are several advantages of this process for production of cellulosic sugars. In some manifestations, solvent liquefaction can process wet feedstock, thus omitting the energy-intensive drying of biomass prior to thermochemical reaction (Haverly et al., 2019). Polar solvents are capable of selectively catalyzing the depolymerization and hydrolysis reactions that govern sugar production. Liquefaction is conducted at relatively modest temperatures (105°C–350°C) when compared to pyrolysis. Product distribution can be tuned by selecting different solvent media and reaction conditions, which provides high flexibility to the process. The reactants and products are diluted in the solvent medium, which helps suppress secondary degradation of the sugars. Lastly, solubilized sugar can be directly delivered to the fermentation unit.
9.1 Processing solvents for saccharification
Solvents facilitate heat and mass transfer, while some solvents also influence solvation and reaction energetics. Both aqueous and organic solvents have been used for solvent liquefaction. Relevant organic solvents can be divided into three major categories: polar protic, polar aprotic, and ionic liquids.
Polar solvents have one or more electric dipoles. Solvents possessing a hydrogen atom attached to an oxygen (hydroxyl group) or a nitrogen (amine group) atom are known as polar protic solvents (Shuai and Luterbacher, 2016). Solvents that lack a hydrogen atom attached to an electronegative atom are called polar aprotic solvents. Polar protic solvents can accept a hydrogen bond due to the presence of a lone pair of electrons and can donate a hydrogen atom or participate in hydrogen bonding due to the presence of an acidic proton. By contrast, polar aprotic solvents can accept a hydrogen bond through lone pair electrons but are incapable of donating any acidic protons or forming hydrogen bonding (Reichardt and Welton, 2010). Alcohols and carboxylic acids are strongly polar protic solvents, whereas ketones, ethers, cyclic ethers, lactones, and esters are examples of polar aprotic solvents. By contrast, nonpolar solvents (such as benzene) are rarely used in solvent liquefaction due to their dissimilarity to biomass. Figure 11 demonstrates the similarity of various solvents to biopolymers and common biomass solvent liquefaction products with Hansen solubility parameter (HSP or δTotal) (Hansen, 2007), which divides intermolecular forces into dispersion (δD), polar (δP), and hydrogen bonding (δH) interactions. These parameters correlate with biomass deconstruction yields and rates (Ghosh et al., 2016; Castellví Barnés et al., 2017).
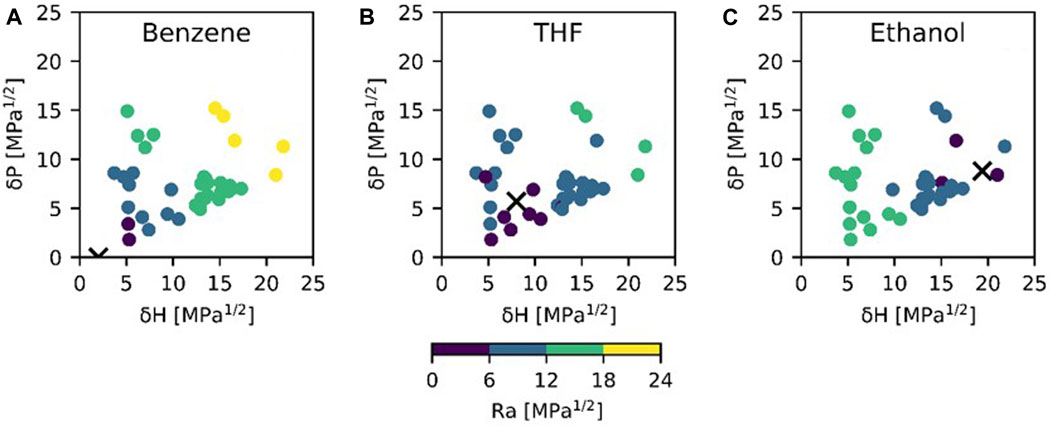
FIGURE 11. Lower relative energy distance (RED, Ra) illustrates a greater potential for solvation between biomass deconstruction products (color-filled circles) and various solvents (X): nonpolar benzene (A), polar aprotic THF (B), and polar protic ethanol (C). Figures produced in Python (Hunter, 2007; Pérez and Granger, 2007) using values from Hansen (2007).
Temperature and pressure complicate the interaction between solvent and solute. Temperature increases molecular motion and pressure compresses the solvents. Both factors alter molecular contact and therefore the interaction. HSP effectively captures these changes for gases, liquids, and supercritical fluids in terms of cohesive energy divided by molar volume (Williams et al., 2004; Hansen, 2007). Equations 1–3 (and by extension Eq. 4) each contains a cubic expansion coefficient (α) [K−1] and isothermal compressibility term (β) [MPa−1] (Williams et al., 2004; Hansen, 2007). Accordingly, each component varies with both temperature and pressure.
Ionic liquids are a special class of solvents consisting of organic salts in liquid form. The ions in IL are poorly coordinated, contributing to their liquid state below 100°C and sometimes even at room temperature (Pinkert et al., 2009). Important advantages of ionic liquids include excellent solvation capability at low temperatures, low volatility, non-flammability, and high thermal stability, which make them suitable for biomass liquefaction (Zhu et al., 2006). However, ionic liquids are very expensive and thus demand high recovery efficiency (Mai et al., 2014).
Applications of various types of solvents in biomass deconstruction targeted toward production of solubilized carbohydrates are summarized in Table 3.
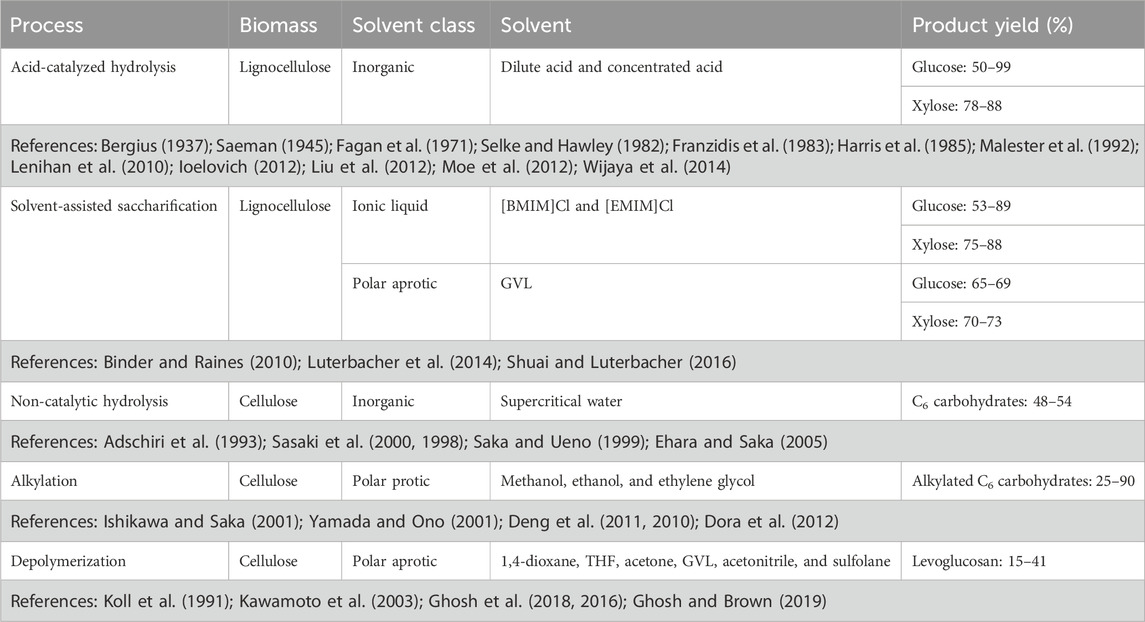
TABLE 3. Major applications of different solvents in lignocellulosic sugar production, adapted from Ghosh (2018).
9.2 Processing of saccharides in inorganic solvents
9.2.1 Dilute and concentrated acid
Hydrolysis of cotton linen in concentrated sulfuric acid is one of the earliest examples of biomass liquefaction in an aqueous solvent to produce sugars (Braconnot, 1819). Later, dilute sulfuric acid was used to produce fermentable sugars from lignocellulosic biomass. Dilute acid hydrolysis can achieve 50%–83% yields of sugar, whereas concentrated acid produces 78%–99% yields of sugar (Bergius, 1937; Saeman, 1945; Fagan et al., 1971; Selke and Hawley, 1982; Franzidis et al., 1983; Harris et al., 1985; Malester et al., 1992; Lenihan et al., 2010; Ioelovich, 2012; Liu et al., 2012; Moe et al., 2012; Wijaya et al., 2014). Concentrated acid is typically operated at low temperatures for its strong catalytic effect promotes depolymerization of biomass polysaccharides selectively over sugar dehydration reactions. However, the use of acid for saccharification of biomass has not been highly industrialized due to the hazards of handling mineral acids, complicated recovery issues, and corrosive effects on reactors (Wright and Power, 1986; Taherzadeh and Karimi, 2007).
9.2.2 Subcritical and supercritical water
Cellulose hydrolysis has been studied extensively in supercritical water in the absence of any catalysts (Adschiri et al., 1993; Saka and Ueno, 1999; Sasaki et al., 2000; Ehara and Saka, 2005; Cantero et al., 2015). The high solubilization capability of supercritical water allows it to easily hydrolyze cellulose to glucose and other oligosaccharides, achieving up to 48%–54% yields (Adschiri et al., 1993; Saka and Ueno, 1999; Sasaki et al., 2000). Nevertheless, hot, pressurized water is highly corrosive requiring expensive corrosion-resistant materials of construction. Since cellulose decomposition occurs quickly in supercritical water, maximum sugar yields require precise control over reaction time (0.05–10 s) (Sasaki et al., 2000). On the other hand, using subcritical water (usually between 200°C and 300°C) encourages dehydration products of glucose, namely, 5-HMF, due to the increased catalytic activity of water caused by autodissociation into hydronium and hydroxide ions (American Society of Mechanical Engineers, 1993; Sasaki et al., 1998; Ehara and Saka, 2005; Bandura and Lvov, 2006). Furthermore, numerous studies show that 5-HMF and furfural, produced from acid-catalyzed dehydration of monosaccharides in water, can condense into undesirable water-insoluble polymeric material known as humins (Van Zandvoort et al., 2013; Tsilomelekis et al., 2016).
9.2.3 Polar protic solvents
The use of polar protic solvents for production of cellulosic sugars is a comparatively less explored pathway. Ishikawa and Saka (2001) demonstrated the deconstruction of cellulose using supercritical methanol to produce methylated glucosides as the major products. Other alcohols, such as ethanol and ethylene glycol, can also be used for producing alkylated cellulosic sugars (Yamada and Ono, 2001; Deng et al., 2011). Interestingly, alcoholysis of cellulose in the presence of strong acid catalyst can produce methyl and ethyl glucosides at yields of 57%–63% when compared to only 5%–10% in pure water (Deng et al., 2011; 2010; Dora et al., 2012). Furthermore, a remarkably high yield of 99.5% of n-decyl pentosides was observed when wheat bran hemicellulose was treated in n-decanol at 100°C while using sulfuric acid catalyst (Marinkovic and Estrine, 2010). However, these alkylated sugars are not particularly attractive for fermentation applications due to additional upgrading steps to utilize them. These sugars are more attractive as precursors for production of cosmetics, detergents, emulsifiers, and nonionic surfactants (Marinkovic and Estrine, 2010; Villandier and Corma, 2010).
9.2.4 Polar aprotic solvents
Polar aprotic solvents do not directly participate in biomass conversion reactions but influence the energetics and thermodynamics of reaction equilibria. These solvents have unique properties that make them attractive alternatives to pure water for hydrolysis and depolymerization of polysaccharides and are therefore receiving increased attention.
Compared to water, several polar aprotic solvents, such as GVL, 1,4-dioxane, and THF, reduce the apparent activation energy of acid-catalyzed hydrolysis of cellobiose, the structural unit of cellulose. At the same time, they increase activation energies for secondary reactions of the monosaccharides (Mellmer et al., 2014). In fact, increasing the ratio of GVL to water for cellobiose acid hydrolysis facilitates higher reaction rates, with a particularly sharp increase above 80 wt% GVL in the solvent mixture.
The favorable reaction energetics in polar aprotic solvents makes them highly selective for the production of sugars from cellulosic biomass. In the absence of water, polar aprotic solvents such as 1,4-dioxane, sulfolane, and acetone readily deconstruct cellulose, yielding levoglucosan as the major carbohydrate product (Koll et al., 1991; Kawamoto et al., 2003; GuiRong et al., 2008). Furthermore, the type of polar aprotic solvent also governs the yield and distribution of solubilized carbohydrates from cellulose with and without catalysts (Ghosh et al., 2018; 2016). Ghosh et al. (2016) showed that the yield of levoglucosan correlates linearly with the Hansen polar solubility parameter of the solvent, indicating a higher degree of polar interaction between the solvent and cellulose polymer. This effect reduces the activation energy of cellulose depolymerization in solvents of higher polarity (Ghosh et al., 2016).
Luterbacher et al. (2014) obtained 69%–73% yield of C5 and C6 sugars in a semi-continuous reactor system using corn stover and maple wood in a solution of GVL, water, and dilute sulfuric acid at approximately 157°C–217°C. In this work, the solvent flowed through a fixed bed reactor pre-loaded with biomass as shown in Figure 12. The sugar was subsequently separated from the solvent mixture using liquid carbon dioxide (CO2) or sodium chloride (NaCl) solution. The system operated at relatively modest pressures compared to hydrothermal liquefaction due to the relatively low vapor pressure of GVL.
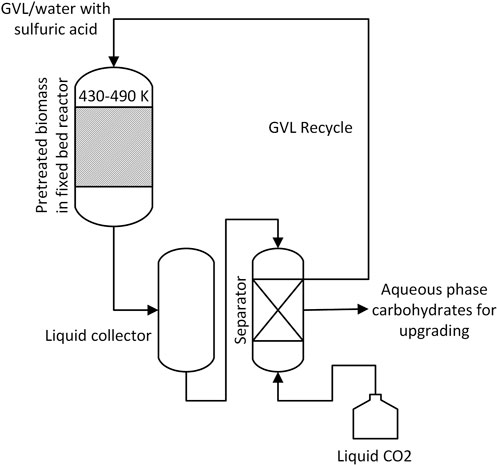
FIGURE 12. Non-enzymatic sugar production from lignocellulosic biomass using a semi-continuous reactor system of GVL/water/acid and liquid CO2/NaCl extraction for GVL recovery. Figure based on Luterbacher et al. (2014).
Similarly, Bai et al. (2014) have produced a mixture of glucose, levoglucosan, and xylose at a total yield of 19.8 wt% (on a biomass, not sugar, basis) by liquefaction of acid-infused switchgrass in 1,4-dioxane and water at 300°C. Taking this process further, Questell-Santiago et al. (2018) added formaldehyde to the system to react with C5 and C6 monosaccharide products, protecting them from decomposing into furanic compounds. This stabilization strategy overturns the typical kinetic limits of polysaccharide depolymerization and produces high yields of C6 (over 70%) and C5 (over 90%) sugars at approximately 5 wt% concentrations.
9.2.5 Ionic liquids
Ionic liquids have been explored widely for converting cellulose and whole biomass at low temperatures to fermentable sugars. Chlorine- and acetate-based imidazolium ILs are known to be highly effective in decrystallizing and dissolving cellulose (Wasserscheid and Keim, 2000; Swatloski et al., 2002; Pinkert et al., 2009). These basic anions can easily disrupt the extensive network of hydrogen bonding in cellulose and thus require only a small amount of thermal energy to break down the crystalline matrix. Moreover, ILs such as 1-ethyl-3-methylimidazolium, promote cellulose hydrolysis to glucose (Li and Zhao, 2007). Rinaldi et al. (2008) reported that ILs are also capable of effectively depolymerizing cellulose in the presence of solid catalyst.
Binder and Raines (2010) demonstrated high yields of glucose from corn stover using a chloride-based IL with gradual introduction of water into the system during hydrolysis. More recently, the Joint BioEnergy Institute (JBEI) group at Sandia National Laboratories has developed a lysinate based on biocompatible ionic liquid or “bionic liquids” for saccharification of whole biomass (Liszka et al., 2016; Xu, F. et al., 2016). Among the bionic liquids, cholinium lysinate ([Ch][Lys]) has the potential for one-pot conversion of biomass.
9.3 Process flow
The Sankey diagram in Figure 13 illustrates a typical mass flow in a two-stage solvent liquefaction process for lignocellulosic sugar production. The biomass is subjected to pretreatment to separate lignin from cellulose and hemicellulose using a GVL–water–acid catalyst mixture at moderate temperatures. Subsequently, the pretreated biomass, mostly containing cellulose and some hemicellulose, is further deconstructed to soluble carbohydrates and their degradation products. The liquor at the end of two-stage liquefaction contains primarily C5 and C6 sugars, carboxylic acids, and furanics, while the solids are mostly insoluble lignin and some humins derived from polymerization of sugar and furanic products. These solids can be combusted for process heat and stationary power. After GVL separation, the sugars are further separated for fermentation in the aqueous phase while the furanic compounds and GVL stream can also undergo processing.
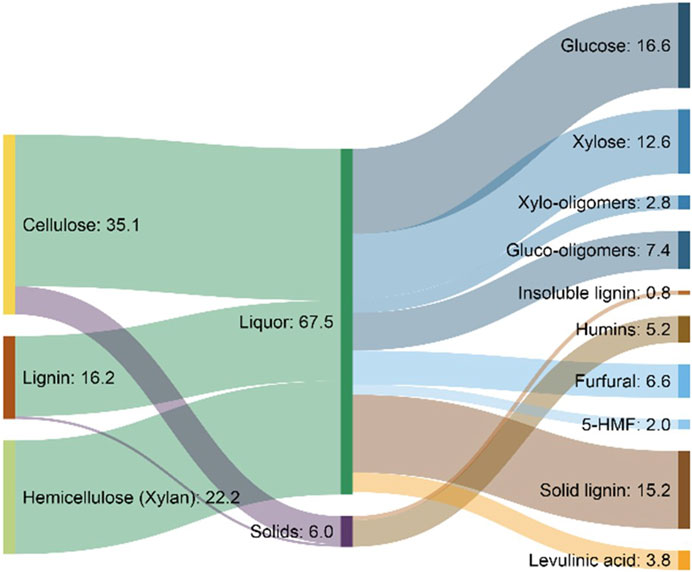
FIGURE 13. Sankey diagram prepared for the two-stage liquefaction process using GVL/water and sulfuric acid catalyst for corn stover using mass flow data from Luterbacher et al. (2014).
9.4 Current challenges of solvent liquefaction
9.4.1 High-pressure feed system
Feeding solid biomass into high-pressure reactors is a significant challenge for scaling up of solvent liquefaction technologies, especially at high mass loadings. Higher feedstock-to-solvent ratios allow for a smaller reactor with the same throughput, reduced solvent use, and higher product concentrations. These effects in turn can lower capital and operating costs. Loading of wood chips in solvents greater than 10–12 wt% can clog pumping systems (Thigpen and Berry, 1982). This can be partially mitigated by wet milling and other pretreatments to reduce biomass particle size, thus increasing bulk density of the feedstock, but can be expensive (Elliott et al., 1989; Ghosh and Haverly, 2019).
Extruder systems have been explored for high-pressure biomass feeding at pilot scale reactors (White et al., 1987; Haverly et al., 2018). Despite stable performance at high pressures and temperatures, successful operation requires uniform feedstock size and careful attention to the feedstock-to-solvent ratio. Progressive cavity, piston, and plunger pumps have also been employed to feed biomass slurries into high pressure reactors (Elliott et al., 2015; 1989; Zöhrer et al., 2014; Mørup et al., 2015; Zhang et al., 2015). Generally, these pumps have limited scalability and can be very expensive. Furthermore, both piston and plunger pumps deliver pulsed or discontinuous flow, and pulseless flow requires operating at least two pumps in tandem, which further increases the capital cost.
9.4.2 Solvent recovery and recycle
The high cost of solvent is one of the greatest challenges to the commercialization of solvent liquefaction biorefineries. A 1,000-ton-per-day hydrothermal liquefaction plant operating at 75% solvent (water) recovery and recycle would require approximately $3.9 M in make-up solvent annually (Ghosh and Haverly, 2019). Wastewater treatment adds $19.8 M to the annual operating costs. Of course, solvent recovery costs are even higher for more costlier organic solvents.
Despite the significant economic challenges, solvent recovery and recycle studies are scarce. Separation of polar solvents, such as GVL, could be complicated and expensive due to the high miscibility of the solvent with the aqueous phase where sugars are recovered. For example, a separation subsystem of compressed liquid CO2 extraction units for recovering and recycling GVL is necessary for economic feasibility of cellulosic ethanol production (Han et al., 2015). Unremoved products in a recycled solvent stream or other impurities may adversely impact the reaction chemistry. Furthermore, purification of recycle streams by distillation or flash separation may reduce sugar quality due to degradation during rapid heating. In some cases, it may be environmentally or economically attractive to employ a product of the liquefaction process, a goal of some of the earliest work in biomass liquefaction (Thigpen and Berry, 1982) and more recently a process explored by Chevron (Haverly et al., 2018).
9.4.3 Pretreatment and liquefaction cost
When employed, pretreatment and solvent liquefaction can be the largest components of the total cost for solvent liquefaction. Techno-economic analysis of GVL- and THF-based cellulosic ethanol production shows that biomass pretreatment and liquefaction could be 37.9% of the total capital cost and 31.7% of the total installed equipment cost, respectively (Han et al., 2015; Li et al., 2018). The liquefaction cost contribution is mainly due to the use of high solvent-to-biomass ratios and suboptimal solvent liquefaction performance, whereas pretreatment cost drivers are the large amounts of solvent required and long reaction times. Pretreatment and liquefaction processes deserve further development to understand how they can contribute to reducing the cost of sugars from solvent liquefaction.
9.4.4 Solvent-to-biomass-slurry ratio
Organic solvents contribute to process economics either from the costs of recovering or replacing them. The effect of the biomass-to-solvent ratio on economic feasibility of biomass conversion for sugar production is shown in Figure 14 for GVL-based solvent liquefaction (Han et al., 2015). By increasing biomass feeding capacity per unit volume of solvent used, the capital and operating costs can be lowered significantly and the heating requirements for large volumes of solvent, solvent replacement, and recycling costs can also be reduced. Additionally, the sugar produced per unit volume of solvent processed increases, thereby improving the economics of solvent liquefaction.
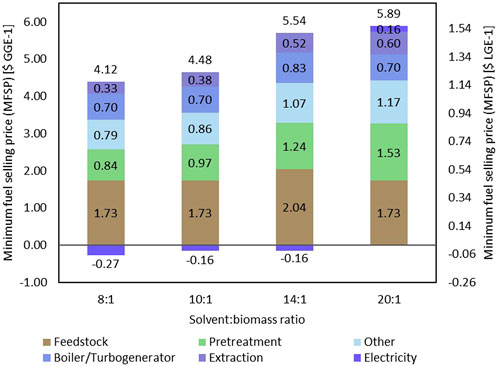
FIGURE 14. Solvent-to-biomass ratio significantly influences minimum fuel selling price of bioethanol in US dollars per gallon of gasoline equivalent (GGE) and liters of gasoline equivalent (LGE). Figure produced using data from Han et al. (2015).
9.4.5 Lower yields than biochemical processing
Solvent liquefaction has the potential to reach approximately 70% of theoretical sugar yields from biomass polysaccharides (Luterbacher et al., 2014). This combination of relatively high sugar yields without expensive enzymes and high conversion rates makes solvent liquefaction attractive for biomass processing. Nevertheless, the process is currently not economically competitive with biochemical processing (Han et al., 2015; Li et al., 2018), reflecting the fact that these systems require corrosion-resistant materials of construction, pressure vessels and piping, heat transfer equipment for thermal management, and solvent recovery or replacement. Accurate yields of bio-oil from solvent liquefaction should be generated using laboratory-scale systems that mimic the high heat transfer rates of continuous systems (Lindstrom et al., 2020).
10 Comparative process economics of cellulosic sugar production
Process economics are of paramount importance for producing fuels and chemicals. Unfortunately for this discussion, the economics are highly speculative. Only enzymatic hydrolysis has been commercialized, and all data associated with these projects are highly guarded. Despite these caveats, the potential economics and technical feasibility of each process are considered through techno-economic analyses (TEA). Techno-economic analyses consider the design, operation, and processes of a technology and systematically assesses the economic performance. The typical TEA follow the general methodology of process designing, process modeling, equipment sizing, capital cost and operating cost estimation, and cash flow analysis. Many TEA employ sensitivity analyses to determine the effect of the most significant parameters on economic viability. Assumptions such as plant life, working capital, and internal rate of return can vary between studies but are typically based on published studies or heuristics. TEA are useful tools for evaluating technology on a specific case basis and for determining where potential improvements can be implemented to mitigate risk and reduce cost.
10.1 Enzymatic hydrolysis
The economics of enzymatic hydrolysis is driven primarily by the cost of pretreatment and enzymes. These costs are intertwined as the method of pretreatment greatly affects the enzyme loading required for conversion of cellulose to glucose.
The National Renewable Energy Laboratory (NREL) modeled the likely economics of a dilute acid enzymatic hydrolysis plant processing 2,000 metric tons per day of biomass (Humbird et al., 2011). The plant design was not built to produce sugars but rather ferment the sugars to ethanol using SSF. Since the added cost of fermentation is minimal compared to the costs of producing the sugars, economics can still be derived from their analyses. They found that the second largest expense after feedstock costs was enzymes, even when manufactured on-site. Due to the dilute nature of enzymatic hydrolysis and the lack of lignin utilization beyond boiler fuel, the two largest equipment costs are the boiler with generator and wastewater treatment at $66 million and $49 million, respectively. The economics of enzymatic hydrolysis has been sufficiently promising in the last decade to encourage the construction of commercial plants. Unfortunately, the recent fate of these plants—either closure or operation substantially below design capacity—suggests biochemical deconstruction is not economically viable in the current era of low petroleum prices (Lane, 2017; Eller, 2019; 2018).
10.2 Fast pyrolysis
Pyrolysis is attractive to be deployed at distributed scales to mirror the distributed nature of biomass. The economics of producing sugars via fast pyrolysis is poorly understood compared to enzymatic hydrolysis and solvent liquefaction. Most research into fast pyrolysis have focused on production of drop-in hydrocarbon fuels rather than the oxygenated fuels typically produced from sugars. Few techno-economic studies have investigated fast pyrolysis sugar production.
The Zhang et al. (2013) model of a 2,000-metric-ton-per-day fast pyrolysis facility explores the economics of fuels from pyrolytic sugars. Unlike the theoretical NREL enzymatic hydrolysis plant often used as a base case (Humbird et al., 2011), this facility uses red oak as a feedstock and produce cellulosic ethanol as well as gasoline and diesel from the phenolic component of bio-oil. These added processing steps bring the total cost of the project to $326 million. They found that the facility had a positive internal rate of return for sugar prices between $0.40 and 0.87 per kilogram when compared to NREL sugar price of $0.315 per kilogram (Humbird et al., 2011). With an annual operating cost of $111 million, the two largest costs were feedstock and depreciation at $54 million and $16 million, respectively. Recent developments enhancing volumetric sugar productivity via fast pyrolysis would undoubtedly reduce the sugar costs estimated in this analysis.
Ganguly et al. (2022) modeled both fast pyrolysis and autothermal pyrolysis at a scale of 250 metric tons per day. The pyrolysis reaction section of the plant represents 25% of the equipment costs for the pyrolysis plant, but only 10% of the equipment costs for the autothermal pyrolysis plant. This is due to the ability of a smaller autothermal reactor achieving the same throughput as a larger pyrolyzer. Additionally, equipment such as heat exchangers and other ancillary equipment are not required to operate an autothermal pyrolyzer. Fixing the internal rate of return (IRR) at 10% and solving for minimum sugar selling prices (MSSPs) showed profitable pyrolysis and autothermal pyrolysis plants for lignin-rich feedstocks. Phenolic oil sold as bio-asphalt and biochar as soil amendment led to positive net present values (NPVs) for these plants. Only autothermal pyrolysis of corn stover without pretreatment showed profitability, as large amounts of pretreatment to passivate the AAEM drove up the MSSP to positive values.
10.3 Solvent liquefaction
The economics of solvent liquefaction can vary greatly based on solvent choice, solvent recycling, and solvent-to-biomass ratio, in addition to feedstock costs. The loss of solvent and the cost of recycling solvents contribute significantly to the economics of solvent liquefaction. For example, Klein-Marcuschamer et al. (2013) showed that if the IL price was considered $50 kg−1, the cost of the raw material contributed up to 73% of the ethanol price as opposed to 52% in case of the IL price being $2.5 kg−1. Thus, most raw material costs were associated with purchasing fresh IL to supplement for the loss of IL solvent. A highly quantitative recovery of the solvent (nearly 100%) or inexpensive solvent (for solvent replacement) is necessary when the solvent cost is often similar to or higher than the renewable chemical being produced. In this context, lower boiling point solvents, such as methanol, ethanol, THF, and acetone, may be the better option for lignocellulosic sugar production due to their high recovery and recyclability potentials, as well as significant lower costs. However, these solvents generally incur increased reactor costs due to higher pressures required to prevent the solvents from boiling. It is worth noting that solvent liquefaction economics for cellulosic ethanol production can be improved further by considering biomass-derived solvents such as GVL and biocompatible ILs such as cholinium lysinate if the cost of solvent recovery is low. Biocompatible ILs can prevent cost-intensive pretreatment by omitting IL separation post-pretreatment and lower the amount of water required to regenerate pretreated biomass prior to the enzymatic hydrolysis (Xu, F. et al., 2016). Solvents are also desired to have high thermochemical stability during and after multiple processing cycles to reflect in a lower minimum ethanol selling price (MESP).
Systems with solvent-to-biomass ratios of 10:1 and solvent recycle rates of 99.6% are expected to have MESP ranging from $3 to $5 gallon−1 ($0.79–$1.30 L−1) (Shuai and Luterbacher, 2016). GVL- and THF-based non-enzymatic saccharification processes can result in significantly lower MESPs, which are comparable to the common base case scenario of cellulosic ethanol from dilute acid pretreatment in combination with enzymatic hydrolysis (Figure 15) (Li et al., 2018).
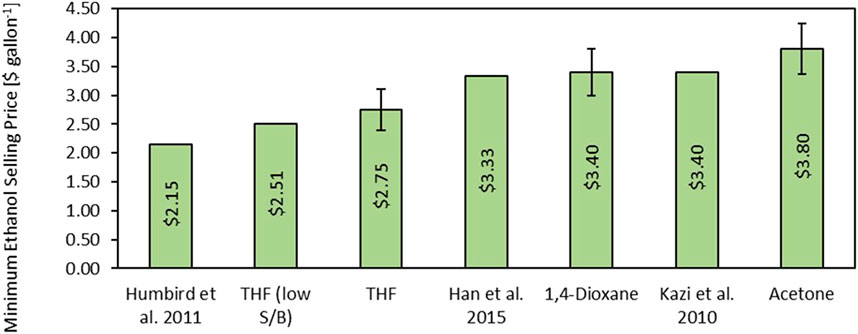
FIGURE 15. MESP scenarios for cellulosic ethanol produced via solvent liquefaction for three different solvents (THF, acetone, and 1,4-dioxane) (Li et al., 2018) are cost-competitive with enzymatic cellulosic ethanol production processes (Kazi et al., 2010; Humbird et al., 2011; Han et al., 2015). Low S/B signifies the lower solvent-to-biomass ratio. Figure produced from data compiled in Li et al. (2018).
11 Conclusion
The choice of conversion technology for the production of biofuel precursor sugars is highly dependent on feedstock type, energy policy, yields, and process economics. Biochemical deconstruction has several advantages. Chief among these is the ability to achieve very high yields of sugars from lignocellulosic biomass. The mild operating conditions and high selectivity of enzymes allow near-quantitative sugar recovery from saccharification (Loow et al., 2016). Production of cellulosic sugars via biochemical deconstruction is closer to commercialization than thermochemical processing (Valdivia et al., 2016). This advantage arises from commonalities with well-developed 1G fermentation technology (Kelsall et al., 2003) and significant private and public investment in 2G fermentation technologies over the last several decades.
Thermochemical processes operate at higher temperatures than biochemical processes giving them the advantage of higher reaction rates even if operated without catalysts. As a result, thermochemical processes can achieve remarkably high volumetric sugar productivity compared to biochemical processing, even considering the lower selectivity of thermochemical processing. Continuously operated fast pyrolysis only requires seconds to produce up to 60 wt% sugar on a polysaccharide basis (although to date continuous processes have only achieved approximately half this sugar yield). In minutes to hours, solvent liquefaction at the laboratory scale has similarly achieved sugar yields reaching 60 wt%. On the other hand, enzymatic hydrolysis can release over 90% of available sugar, provided the reaction is allowed to proceed over many hours.
Ultimately, the economic prospects of cellulosic sugar, whether through biochemical or thermochemical means, will be determined by the price of petroleum and other fossil fuels. Currently, fossil fuels in the market are plentiful and inexpensive, suggesting there is still opportunity to improve cellulosic sugar technologies for the day that consumer demand and public policy favor their commercial deployment.
Author contributions
JB: Formal Analysis, Investigation, Visualization, Writing–original draft. JL: Formal Analysis, Investigation, Visualization, Writing–original draft. AG: Formal Analysis, Investigation, Visualization, Writing–original draft. SR: Formal Analysis, Investigation, Visualization, Writing–original draft. RB: Conceptualization, Writing–review and editing.
Funding
The authors declare that financial support was received for the research, authorship, and/or publication of this article. The authors appreciate the support of the Gary and Donna Hoover Endowment at Iowa State University. Additional support came from the Department of Energy under Award Number DE-EE0007888-7-4. It was prepared as an account of work sponsored by an agency of the United States Government. Neither the United States Government nor any agency thereof, nor any of their employees, make any warranty, express or implied, or assume any legal liability or responsibility for the accuracy, completeness, or usefulness of any information, apparatus, product, or process disclosed, or represent that the use of these would not infringe privately owned rights. Any reference herein to any specific commercial product, process, or service by trade name, trademark, manufacturer, or otherwise does not necessarily constitute or imply its endorsement, recommendation, or favoring by the United States Government or any agency thereof.
Acknowledgments
Chad A. Peterson and Robert Mills assisted in the conception and preparation of original graphics in this paper.
Conflict of interest
The authors declare that the research was conducted in the absence of any commercial or financial relationships that could be construed as a potential conflict of interest.
Publisher’s note
All claims expressed in this article are solely those of the authors and do not necessarily represent those of their affiliated organizations, or those of the publisher, the editors, and the reviewers. Any product that may be evaluated in this article, or claim that may be made by its manufacturer, is not guaranteed or endorsed by the publisher.
Author disclaimer
The views and opinions of authors expressed herein do not necessarily state or reflect those of the United States Government or any agency thereof.
References
Adschiri, T., Hirose, S., Malaluan, R., and Arai, K. (1993). Noncatalytic conversion of cellulose in supercritical and subcritical water. J. Chem. Eng. Jpn. 26, 676–680. doi:10.1252/jcej.26.676
Afedzi, A. E. K., and Parakulsuksatid, P. (2023). Recent advances in process modifications of simultaneous saccharification and fermentation (SSF) of lignocellulosic biomass for bioethanol production. Biocatal. Agric. Biotechnol. 54, 102961. doi:10.1016/j.bcab.2023.102961
American Society of Mechanical Engineers (1993). ASME steam Tables: thermodynamic and transport properties of steam.
Anderson, J. E., Dicicco, D. M., Ginder, J. M., Kramer, U., Leone, T. G., Raney-Pablo, H. E., et al. (2012). High octane number ethanol-gasoline blends: quantifying the potential benefits in the United States. Fuel 97, 585–594. doi:10.1016/j.fuel.2012.03.017
Andric, P., Meyer, A. S., Jensen, P. A., and Dam-Johansen, K. (2010). Reactor design for minimizing product inhibition during enzymatic lignocellulose hydrolysis: I. Significance and mechanism of cellobiose and glucose inhibition on cellulolytic enzymes. Biotechnol. Adv. 28, 308–324. doi:10.1016/j.biotechadv.2010.01.003
Arora, R., Manisseri, C., Li, C., Ong, M. D., Scheller, H. V., Vogel, K., et al. (2010). Monitoring and analyzing process streams towards understanding ionic liquid pretreatment of switchgrass (Panicum virgatum L.). Bioenergy Res. 3, 134–145. doi:10.1007/s12155-010-9087-1
Bacik, J. P., and Jarboe, L. R. (2016). Bioconversion of anhydrosugars: emerging concepts and strategies. IUBMB Life 68, 700–708. doi:10.1002/iub.1533
Bai, X., Brown, R. C., Fu, J., Shanks, B. H., and Kieffer, M. (2014). The influence of alkali and alkaline earth metals and the role of acid pretreatments in production of sugars from switchgrass based on solvent liquefaction. Energy Fuels 28, 1111–1120. doi:10.1021/ef4022015
Bai, X., Johnston, P., and Brown, R. C. (2013). An experimental study of the competing processes of evaporation and polymerization of levoglucosan in cellulose pyrolysis. J. Anal. Appl. Pyrolysis 99, 130–136. doi:10.1016/j.jaap.2012.10.012
Bak, J. S. (2014). Electron beam irradiation enhances the digestibility and fermentation yield of water-soaked lignocellulosic biomass. Biotechnol. Rep. 4, 30–33. doi:10.1016/j.btre.2014.07.006
Balch, M. L., Holwerda, E. K., Davis, M. F., Sykes, R. W., Happs, R. M., Kumar, R., et al. (2017). Lignocellulose fermentation and residual solids characterization for senescent switchgrass fermentation by: Clostridium thermocellum in the presence and absence of continuous in situ ball-milling. Energy Environ. Sci. 10, 1252–1261. doi:10.1039/c6ee03748h
Bandura, A. V., and Lvov, S. N. (2006). The ionization constant of water over wide ranges of temperature and density. J. Phys. Chem. Ref. Data 35, 15–30. doi:10.1063/1.1928231
Banner, A., Toogood, H. S., and Scrutton, N. S. (2021). Consolidated bioprocessing: synthetic biology routes to fuels and fine chemicals. Microorganisms 9, 1079. doi:10.3390/microorganisms9051079
Behrendt, F., Neubauer, Y., Oevermann, M., Wilmes, B., and Zobel, N. (2008). Direct liquefaction of biomass. Chem. Eng. Technol. 31, 667–677. doi:10.1002/ceat.200800077
Bennett, N. M., Helle, S. S., and Duff, S. J. B. (2009). Extraction and hydrolysis of levoglucosan from pyrolysis oil. Bioresour. Technol. 100, 6059–6063. doi:10.1016/j.biortech.2009.06.067
Bergius, F. (1937). Conversion of wood to carbohydrates. Industrial Eng. Chem. 29, 247–253. doi:10.1021/ie50327a002
Bertrand, E., Vandenberghe, L. P. S., and Soccol, C. R. (2012). “First generation bioethanol,” in Green energy and technology (Springer International Publishing), 175–212. doi:10.1007/978-1-4471-2372-9
Binder, J. B., and Raines, R. T. (2010). Fermentable sugars by chemical hydrolysis of biomass. Proc. Natl. Acad. Sci. U. S. A. 107, 4516–4521. doi:10.1073/pnas.0912073107
Biofuel production by country (2016). Biofuel production by country/region and fuel type. 2016-2022 [WWW Document], 2022. . IEA. URL Available at: https://www.iea.org/data-and-statistics/charts/biofuel-production-by-country-region-and-fuel-type-2016-2022.
Braconnot, H. (1819). Memoir on the conversion of wood particles in rubber, in sugar, and in a special natural acid, by means of sulfuric acid; conversion of the same woody substance in ulmin by potash (Translated from French). Ann. Chi. Phys. 12, 172–195.
Brás, J. L. A., Cartmell, A., Luísa, A., Carvalho, M., Verzé, G., Bayer, E. A., et al. (2011). Structural insights into a unique cellulase fold and mechanism of cellulose hydrolysis. Proc. Natl. Acad. Sci. 108, 5237–5242. doi:10.1073/pnas.1015006108
Braun, M., and Antonietti, M. (2017). A continuous flow process for the production of 2,5-dimethylfuran from fructose using (non-noble metal based) heterogeneous catalysis. Green Chem. 19, 3813–3819. doi:10.1039/c7gc01055a
Brethauer, S., and Studer, M. H. (2015). Biochemical conversion processes of lignocellulosic biomass to fuels and chemicals - a review. Chim. (Aarau) 69, 572–581. doi:10.2533/chimia.2015.572
Brewer, C. E., Schmidt-Rohr, K., Satrio, J. A., and Brown, R. C. (2009). Characterization of biochar from fast pyrolysis and gasification systems. Environ. Prog. Sustain Energy 28, 386–396. doi:10.1002/ep.10378
Bridgwater, A. V. (2003). Renewable fuels and chemicals by thermal processing of biomass. Chem. Eng. J. 91, 87–102. doi:10.1016/s1385-8947(02)00142-0
Bridgwater, A. V. (2012). Review of fast pyrolysis of biomass and product upgrading. Biomass Bioenergy 38, 68–94. doi:10.1016/j.biombioe.2011.01.048
Broido, A. (1966). Thermogravimetric and differential thermal analysis of potassium bicarbonate contaminated cellulose. Pyrodynamics 4, 243–251.
Brown, R. C. (2020). Process intensification through directly coupled autothermal operation of chemical reactors. Joule 4, 2268–2289. doi:10.1016/j.joule.2020.09.006
Brown, R. C. (2021). Heterodoxy in fast pyrolysis of biomass. Energy Fuels. doi:10.1021/acs.energyfuels.0c03512
Brown, R. C., and Brown, T. R. (2014). Biorenewable resources. 2nd ed. Ames, IA: John Wiley & Sons. doi:10.1002/9781118524985
Brown, R. C., del Campo, B., Boateng, A. A., Garcia-Perez, M., and Masek, O. (2015). “Fundamentals of biochar production,” in Biochar for environmental management: science, technology, and implementation. Editors J. Lehmann,, and S. Joseph (London, U. K.: Taylor & Francis Group), 39–61.
Brown, R. C., and Zhang, X. (2019). “Introduction to thermochemical processing of biomass into fuels, chemicals, and power,” in Thermochemical processing of biomass: conversion into fuels, chemicals and power. Editor R. C. Brown (John Wiley & Sons, Ltd), 1–16. doi:10.1002/9781119990840.ch1
Brown, T. R. (2018). Price uncertainty, policy, and the economic feasibility of cellulosic biorefineries. Biofuels, Bioprod. Biorefining 12, 485–496. doi:10.1002/bbb.1865
Brown, T. R. (2019). Why the cellulosic biofuels mandate fell short: a markets and policy perspective. Biofuels, Bioprod. Biorefining 13, 889–898. doi:10.1002/bbb.1987
Burnham, A. K., Zhou, X., and Broadbelt, L. J. (2015). Critical review of the global chemical kinetics of cellulose thermal decomposition. Energy Fuels 29, 2906–2918. doi:10.1021/acs.energyfuels.5b00350
Cairns, J. R. K., and Esen, A. (2010). β-Glucosidases. Cell. Mol. Life Sci. 67, 3389–3405. doi:10.1007/s00018-010-0399-2
California Air Resources Board (2023). LCA models and documentation. Available at: https://ww2.arb.ca.gov/resources/documents/lcfs-life-cycle-analysis-models-and-documentation (Accessed November 19, 2023) [abstract].
Cantero, D. A., Bermejo, M. D., and Cocero, M. J. (2015). Governing chemistry of cellulose hydrolysis in supercritical water. ChemSusChem 8, 1026–1033. doi:10.1002/cssc.201403385
Cao, F., Schwartz, T. J., McClelland, D. J., Krishna, S. H., Dumesic, J. A., and Huber, G. W. (2015). Dehydration of cellulose to levoglucosenone using polar aprotic solvents. Energy Environ. Sci. 8, 1808–1815. doi:10.1039/c5ee00353a
Carpenter, D., Westover, T. L., Czernik, S., and Jablonski, W. (2014). Biomass feedstocks for renewable fuel production: a review of the impacts of feedstock and pretreatment on the yield and product distribution of fast pyrolysis bio-oils and vapors. Green Chem. 16, 384–406. doi:10.1039/c3gc41631c
Casey, E., Mosier, N. S., Adamec, J., Stockdale, Z., Ho, N., and Sedlak, M. (2013). Effect of salts on the Co-fermentation of glucose and xylose by a genetically engineered strain of Saccharomyces cerevisiae. Biotechnol. Biofuels 6, 83. doi:10.1186/1754-6834-6-83
Castellví Barnés, M., Oltvoort, J., Kersten, S. R. A., and Lange, J. P. (2017). Wood liquefaction: role of solvent. Ind. Eng. Chem. Res. 56, 635–644. doi:10.1021/acs.iecr.6b04086
Chaala, A., Ba, T., Garcia-Perez, M., and Roy, C. (2004). Colloidal properties of bio-oils obtained by vacuum pyrolysis of softwood bark: aging and thermal stability. Energy Fuels 18, 1535–1542. doi:10.1021/ef030156v
Chan, J. K. S., and Duff, S. J. B. (2010). Methods for mitigation of bio-oil extract toxicity. Bioresour. Technol. 101, 3755–3759. doi:10.1016/j.biortech.2009.12.054
Chanthawong, A., and Dhakal, S. (2016). Liquid biofuels development in southeast asian countries: an analysis of market, policies and challenges. Waste Biomass Valorization 7, 157–173. doi:10.1007/s12649-015-9433-9
Chen, L., Zhao, J., Pradhan, S., Brinson, B. E., Scuseria, G. E., Zhang, Z. C., et al. (2016). Ring-locking enables selective anhydrosugar synthesis from carbohydrate pyrolysis. Green Chem. 18, 5438–5447. doi:10.1039/c6gc01600f
Chen, Y., Stevens, M. A., Zhu, Y., Holmes, J., and Xu, H. (2013). Understanding of alkaline pretreatment parameters for corn stover enzymatic saccharification. Biotechnol. Biofuels 6, 8. doi:10.1186/1754-6834-6-8
Chidambaram, M., and Bell, A. T. (2010). A two-step approach for the catalytic conversion of glucose to 2,5-dimethylfuran in ionic liquids. Green Chem. 12, 1253–1262. doi:10.1039/c004343e
Choudhary, J., Singh, S., and Nain, L. (2016). Thermotolerant fermenting yeasts for simultaneous saccharification fermentation of lignocellulosic biomass. Electron. J. Biotechnol. 21, 82–92. doi:10.1016/j.ejbt.2016.02.007
Ciesielski, P. N., Crowley, M. F., Nimlos, M. R., Sanders, A. W., Wiggins, G. M., Robichaud, D., et al. (2015). Biomass particle models with realistic morphology and resolved microstructure for simulations of intraparticle transport phenomena. Energy Fuels 29, 242–254. doi:10.1021/ef502204v
Ciesielski, P. N., Wagner, R., Bharadwaj, V. S., Killgore, J., Mittal, A., Beckham, G. T., et al. (2019). Nanomechanics of cellulose deformation reveal molecular defects that facilitate natural deconstruction. Proc. Natl. Acad. Sci. U. S. A. 116, 9825–9830. doi:10.1073/pnas.1900161116
Climent, M. J., Corma, A., and Iborra, S. (2014). Conversion of biomass platform molecules into fuel additives and liquid hydrocarbon fuels. Green Chem. 16, 516. doi:10.1039/c3gc41492b
Comba, M. B., Tsai, Y. H., Sarotti, A. M., Mangione, M. I., Suárez, A. G., and Spanevello, R. A. (2018). Levoglucosenone and its new applications: valorization of cellulose residues. Eur. J. Org. Chem. 2018, 590–604. doi:10.1002/ejoc.201701227
Congressional Budget Office (2009). The impact of ethanol use on food prices and greenhouse-gas emissions.
Cozier, M. (2015). The Bioenergy debate. Biofuels, Bioprod. Biorefining 9, 341–343. doi:10.1002/BBB.1574
Cullis, I. F., Saddler, J. N., and Mansfield, S. D. (2004). Effect of initial moisture content and chip size on the bioconversion efficiency of softwood lignocellulosics. Biotechnol. Bioeng. 85, 413–421. doi:10.1002/bit.10905
Dalluge, D. L., Daugaard, T., Johnston, P., Kuzhiyil, N., Wright, M. M., and Brown, R. C. (2014). Continuous production of sugars from pyrolysis of acid-infused lignocellulosic biomass. Green Chem. 16, 4144–4155. doi:10.1039/c4gc00602j
Dalluge, D. L., Kim, K. H., and Brown, R. C. (2017). The influence of alkali and alkaline earth metals on char and volatile aromatics from fast pyrolysis of lignin. J. Anal. Appl. Pyrolysis 127, 385–393. doi:10.1016/j.jaap.2017.07.011
Dalluge, D. L., Whitmer, L. E., Polin, J. P., Choi, Y. S., Shanks, B. H., and Brown, R. C. (2019). Comparison of direct and indirect contact heat exchange to improve recovery of bio-oil. Appl. Energy 251, 113346. doi:10.1016/j.apenergy.2019.113346
David, G. F., Justo, O. R., Perez, V. H., and Garcia-Perez, M. (2018). Thermochemical conversion of sugarcane bagasse by fast pyrolysis: high yield of levoglucosan production. J. Anal. Appl. Pyrolysis 133, 246–253. doi:10.1016/j.jaap.2018.03.004
David, G. F., Perez, V. H., Rodriguez Justo, O., and Garcia-Perez, M. (2017). Effect of acid additives on sugarcane bagasse pyrolysis: production of high yields of sugars. Bioresour. Technol. 223, 74–83. doi:10.1016/j.biortech.2016.10.051
Davis, R., Biddy, M., Tan, E., Tao, L., and Jones, S. (2013). Biological conversion of sugars to hydrocarbons technology pathway.
de Barros, E. M., Carvalho, V. M., Rodrigues, T. H. S., Rocha, M. V. P., and Gonçalves, L. R. B. (2017). Comparison of strategies for the simultaneous saccharification and fermentation of cashew apple bagasse using a thermotolerant Kluyveromyces marxianus to enhance cellulosic ethanol production. Chem. Eng. J. 307, 939–947. doi:10.1016/j.cej.2016.09.006
de la Torre, M. J., Moral, A., Hernández, M. D., Cabeza, E., and Tijero, A. (2013). Organosolv lignin for biofuel. Ind. Crops Prod. 45, 58–63. doi:10.1016/j.indcrop.2012.12.002
Delidovich, I., Hausoul, P. J. C., Deng, L., Pfützenreuter, R., Rose, M., and Palkovits, R. (2016). Alternative monomers based on lignocellulose and their use for polymer production. Chem. Rev. 116, 1540–1599. doi:10.1021/acs.chemrev.5b00354
Dempfle, D., Krocher, O., and Studer, M.H.-P. (2021). Techno-economic assessment of bioethanol production from lignocellulose by consortium-based consolidated bioprocessing at industrial scale. N. Biotechnol. 65, 53–60. doi:10.1016/j.nbt.2021.07.005
Deng, W., Liu, M., Zhang, Q., Tan, X., and Wang, Y. (2010). Acid-catalysed direct transformation of cellulose into methyl glucosides in methanol at moderate temperatures. Chem. Commun. 46, 2668–2670. doi:10.1039/b925723c
Deng, W., Liu, M., Zhang, Q., and Wang, Y. (2011). Direct transformation of cellulose into methyl and ethyl glucosides in methanol and ethanol media catalyzed by heteropolyacids. Catal. Today 164, 461–466. doi:10.1016/j.cattod.2010.10.055
de Oliveira Santos, V. T., Siqueira, G., Milagres, A. M. F., and Ferraz, A. (2018). Role of hemicellulose removal during dilute acid pretreatment on the cellulose accessibility and enzymatic hydrolysis of compositionally diverse sugarcane hybrids. Ind. Crops Prod. 111, 722–730. doi:10.1016/j.indcrop.2017.11.053
Dien, B. S., and Bothast, R. J. (2003). “A primer for lignocellulosic biochemical conversion to fuel ethanol,” in The alcohol textbook (Nottingham, U.K.: Nottingham University Press), 73–94.
Directive (EU) 2023/1791 of the European Parliament and of the Council of 13 September 2023 on energy efficiency and amending Regulation (EU) 2023/955 (recast) (2023). Official Journal L231, 1–111.
Donohoe, B. S., Decker, S. R., Tucker, M. P., Himmel, M. E., and Vinzant, T. B. (2008). Visualizing lignin coalescence and migration through maize cell walls following thermochemical pretreatment. Biotechnol. Bioeng. 101, 913–925. doi:10.1002/bit.21959
Dora, S., Bhaskar, T., Singh, R., Naik, D. V., and Adhikari, D. K. (2012). Effective catalytic conversion of cellulose into high yields of methyl glucosides over sulfonated carbon based catalyst. Bioresour. Technol. 120, 318–321. doi:10.1016/j.biortech.2012.06.036
Dutta, S., De, S., and Saha, B. (2012). A brief summary of the synthesis of polyester building-block chemicals and biofuels from 5-hydroxymethylfurfural. Chempluschem 77, 259–272. doi:10.1002/cplu.201100035
Dutta, S., and Suresh Kumar, M. (2023). Potential use of thermophilic bacteria for second-generation bioethanol production using lignocellulosic feedstocks: a review. Biofuels 14, 851–864. doi:10.1080/17597269.2023.2184935
Eagan, N. M., Chada, J. P., Wittrig, A. M., Buchanan, J. S., Dumesic, J. A., and Huber, G. W. (2017). Hydrodeoxygenation of sorbitol to monofunctional fuel precursors over Co/TiO2. Joule 1, 178–199. doi:10.1016/j.joule.2017.07.004
Ehara, K., and Saka, S. (2005). Decomposition behavior of cellulose in supercritical water, subcritical water, and their combined treatments. J. Wood Sci. 51, 148–153. doi:10.1007/s10086-004-0626-2
Eller, D. (2018). “Low prices trade disputes sow fears of 80s style farm crisis,” in Des moines register.
Eller, D. (2019). Despite heavy lobbying, Iowa farmers, elected leaders say Trumps EPA reneges on renewable fuels promise. Des Moines Register.
Elliott, D. C., Baker, E. G., Sealock, L. J., Neuenschwander, G. G., and Butner, R. S. (1989). Low-temperature conversion of high-moisture biomass continuous reactor system results. Richland, WA.
Elliott, D. C., Biller, P., Ross, A. B., Schmidt, A. J., and Jones, S. B. (2015). Hydrothermal liquefaction of biomass: developments from batch to continuous process. Bioresour. Technol. 178, 147–156. doi:10.1016/j.biortech.2014.09.132
Energy Independence and Security Act of 2007 (2007). Energy independence and security act of 2007. United States Congress.
Fagan, R. D., Grethlein, H. E., Converse, A. O., and Porteous, A. (1971). Kinetics of the acid hydrolysis of cellulose found in paper refuse. Environ. Sci. Technol. 5, 545–547. doi:10.1021/es60053a006
Franzidis, J.-P., Porteous, A., and Anderson, J. (1983). The acid hydrolysis of cellulose in refuse in a continuous reactor. Conservation Recycl. 5, 215–225. doi:10.1016/0361-3658(82)90050-9
Fuels Association, Renewable. 2023. Annual Ethanol Production [WWW Document]. URL https://ethanolrfa.org/markets-and-statistics/annual-ethanol-production.
Furey, R. L., and Perry, K. L. (1991). Composition and reactivity of fuel vapor emissions from gasoline-oxygenate blends.
Galbis, J. A., García-Martín, M. D. G., De Paz, M. V., and Galbis, E. (2016). Synthetic polymers from sugar-based monomers. Chem. Rev. 116, 1600–1636. doi:10.1021/acs.chemrev.5b00242
Ganguly, A., Brown, R. C., and Wright, M. M. (2022). Techno-economic and greenhouse gas emission assessment of carbon negative pyrolysis technology. Green Chem. 24, 9290–9302. doi:10.1039/d2gc03172h
Gaston, K. R., Jarvis, M. W., Pepiot, P., Smith, K. M., Frederick, W. J., and Nimlos, M. R. (2011). Biomass pyrolysis and gasification of varying particle sizes in a fluidized-bed reactor. Energy Fuels 25, 3747–3757. doi:10.1021/ef200257k
Ghosh, A. (2018). Production of solubilized carbohydrates from lignocellulosic biomass using solvent liquefaction (Dissertation). Ames: Iowa State University.
Ghosh, A., Bai, X., and Brown, R. C. (2018). Solubilized carbohydrate production by acid-catalyzed depolymerization of cellulose in polar aprotic solvents. ChemistrySelect 3, 4777–4785. doi:10.1002/slct.201800764
Ghosh, A., Brown, J. L., Smith, R. G., and Brown, R. C. (2023). Hydrolysis of anhydrosugars derived from pyrolysis of lignocellulosic biomass for integration in a biorefinery. Sustain Energy Fuels 7, 3361–3374. doi:10.1039/d3se00240c
Ghosh, A., and Brown, R. C. (2019). Factors influencing cellulosic sugar production during acid-catalyzed solvent liquefaction in 1,4-dioxane. ACS Sustain Chem. Eng. 7, 18076–18084. doi:10.1021/acssuschemeng.9b05108
Ghosh, A., Brown, R. C., and Bai, X. (2016). Production of solubilized carbohydrate from cellulose using non-catalytic, supercritical depolymerization in polar aprotic solvents. Green Chem. 18, 1023–1031. doi:10.1039/c5gc02071a
Ghosh, A., and Haverly, M. R. (2019). “Solvent liquefaction,” in Thermochemical processing of biomass: conversion into fuels, chemicals and power. Editor R. C. Brown (Wiley & Sons), 257–306.
Golova, O. P., and Krylova, R. G. (1960). Thermal depolarization of cellulose. Dokl. Akad. Nauk. SSSR 135, 1391–1394.
Gong, X., Yu, Y., Gao, X., Qiao, Y., Xu, M., and Wu, H. (2014). Formation of anhydro-sugars in the primary volatiles and solid residues from cellulose fast pyrolysis in a wire-mesh reactor. Energy Fuels 28, 5204–5211. doi:10.1021/ef501112q
Govil, T., Narayanan, A. S., Salem, D. R., and Sani, R. (2022). “Progress in consolidated bioprocessing of lignocellulosic biomass for biofuels and biochemicals,” in Microbial biotechnology for renewable and sustainable energy (Springer), 35–54.
Grata, K. (2020). Determining cellulolytic activity of microorganisms. Chem. Didact. Ecol. Metrol. 25, 133–143. doi:10.2478/cdem-2020-0010
Gu, H., Xu, M., and Singh, S. (2020). EXCLUSIVE-China suspends national rollout of ethanol mandate. [WWW Document]. Reuters. URL Available at: https://www.reuters.com/article/china-ethanol-policy/exclusive-china-suspends-national-rollout-of-ethanol-mandate-sources-idUKL4N29D1EE.
GuiRong, B., Saka, S., and Wang, H. (2008). Cellulose decomposition behavior in hot-compressed aprotic solvents. Sci. China B Chem. 51, 479–486. doi:10.1007/s11426-008-0052-1
Gupta, A., and Verma, J. P. (2015). Sustainable bio-ethanol production from agro-residues: a review. Renew. Sustain. Energy Rev. 41, 550–567. doi:10.1016/j.rser.2014.08.032
Hallac, B. B., and Ragauskas, A. J. (2011). Analyzing cellulose degree of polymerization and its relevancy to cellulosic ethanol. Biofuels, Bioprod. Biorefining 5, 215–225. doi:10.1002/bbb.269
Han, J., Luterbacher, J. S., Alonso, D. M., Dumesic, J. A., and Maravelias, C. T. (2015). A lignocellulosic ethanol strategy via nonenzymatic sugar production: process synthesis and analysis. Bioresour. Technol. 182, 258–266. doi:10.1016/j.biortech.2015.01.135
Hansen, C. M. (2007). Hansen solubility parameters: a user’s handbook. 2nd ed. Boca Raton, LA: CRC Press.
Harris, J. F., Minor, J. L., Springer, E. L., Baker, A. J., Pettersen, R. C., Wegner, T. H., et al. (1985). Two-stage, dilute sulfuric acid hydrolysis of wood: an investigation of fundamentals.
Hatakka, A. I. (1983). Pretreatment of wheat straw by white-rot fungi for enzymic saccharification of cellulose. Eur. J. Appl. Microbiol. Biotechnol. 18, 350–357. doi:10.1007/bf00504744
Haverly, M. R., Ghosh, A., and Brown, R. C. (2019). The effect of moisture on hydrocarbon-based solvent liquefaction of pine, cellulose and lignin. J. Anal. Appl. Pyrolysis 146, 104758. doi:10.1016/j.jaap.2019.104758
Haverly, M. R., Schulz, T. C., Whitmer, L. E., Friend, A. J., Funkhouser, J. M., Smith, R. G., et al. (2018). Continuous solvent liquefaction of biomass in a hydrocarbon solvent. Fuel 211, 291–300. doi:10.1016/j.fuel.2017.09.072
Haverly, M. R., Whitmer, L. E., and Brown, R. C. (2015). Evaluation of polymer compatibility with bio-oil produced from thermochemical conversion of biomass. Energy Fuels 29, 7993–7997. doi:10.1021/acs.energyfuels.5b01943
Hayes, R., Warr, G. G., and Atkin, R. (2015). Structure and nanostructure in ionic liquids. Chem. Rev. 115, 6357–6426. doi:10.1021/cr500411q
Heinze, T., El Seoud, O. A., and Koschella, A. (2018). “Structure and properties of cellulose and its derivatives,” in Cellulose derivatives. Springer series on polymer and composite materials (Cham: Springer), 39–172. doi:10.1007/978-3-319-73168-1_2
Helle, S., Bennett, N. M., Lau, K., Matsui, J. H., and Duff, S. J. B. (2007). A kinetic model for production of glucose by hydrolysis of levoglucosan and cellobiosan from pyrolysis oil. Carbohydr. Res. 342, 2365–2370. doi:10.1016/j.carres.2007.07.016
Hemansi, , and Saini, J. K. (2023). Enhanced cellulosic ethanol production via fed-batch simultaneous saccharification and fermentation of sequential dilute acid-alkali pretreated sugarcane bagasse. Bioresour. Technol. 372, 128671. doi:10.1016/j.biortech.2023.128671
Himmel, M., Tucker, M., Baker, J., Rivard, C., Oh, K., and Grohmann, K. (1985). “Comminution of biomass: hammer and knife mills,” in Biotechnology and bioengineering symposium, 39–58.
Himmel, M. E., Ding, S.-Y., Johnson, D. K., Adney, W. S., Nimlos, M. R., Brady, J. W., et al. (1979). Biomass recalcitrance: engineering plants and enzymes for biofuels production. Science 315, 804–807. doi:10.1126/science.1137016
Hira, A., and de Oliveira, L. G. (2009). No substitute for oil? How Brazil developed its ethanol industry. Energy Policy 37, 2450–2456. doi:10.1016/j.enpol.2009.02.037
Hoffman, S. M., Alvarez, M., Alfassi, G., Rein, D. M., Garcia-Echauri, S., Cohen, Y., et al. (2021). Cellulosic biofuel production using emulsified simultaneous saccharification and fermentation (eSSF) with conventional and thermotolerant yeasts. Biotechnol. Biofuels 14, 157. doi:10.1186/s13068-021-02008-7
Hsu, T. C., Guo, G. L., Chen, W. H., and Hwang, W. S. (2010). Effect of dilute acid pretreatment of rice straw on structural properties and enzymatic hydrolysis. Bioresour. Technol. 101, 4907–4913. doi:10.1016/j.biortech.2009.10.009
Huijgen, W. J. J., Reith, J. H., and Den Uil, H. (2010). Pretreatment and fractionation of wheat straw by an acetone-based organosolv process. Ind. Eng. Chem. Res. 49, 10132–10140. doi:10.1021/ie101247w
Humbird, D., Davis, R., Tao, L., Kinchin, C., Hsu, D., Aden, A., et al. (2011). Process design and economics for biochemical conversion of lignocellulosic biomass to ethanol: dilute-acid pretreatment and enzymatic hydrolysis of corn stover. Golden, CO.
Hunter, J. D. (2007). Matplotlib: a 2D graphics environment. Comput. Sci. Eng. 9, 90–95. doi:10.1109/mcse.2007.55
Hyun Kim, T., and Lee, Y. Y. (2005). Pretreatment of corn stover by soaking in aqueous ammonia. Appl. Biochem. Biotechnol. 124, 1119–1132. doi:10.1385/abab:124:1-3:1119
Igarashi, K., Koivula, A., Wada, M., Kimura, S., Penttilä, M., and Samejima, M. (2009). High speed atomic force microscopy visualizes processive movement of Trichoderma reesei cellobiohydrolase I on crystalline cellulose. J. Biol. Chem. 284, 36186–36190. doi:10.1074/jbc.M109.034611
Informa Economics IEG (2016). The impact of ethanol industry expansion on food prices: a retrospective analysis. Washington D.C.
Ioelovich, M. (2012). Study of cellulose interaction with concentrated solutions of sulfuric acid. ISRN Chem. Eng. 2012, 1–7. doi:10.5402/2012/428974
IPCC (2018). “Global warming of 1.5°C an IPCC Special Report on the impacts of global warming of 1.5°C above pre-industrial levels and related global greenhouse gas emission pathways,” in The context of strengthening the global response to the threat of climate change, sustainable development, and efforts to eradicate poverty. Editors Masson-Delmotte, V., Zhai, P., Portner, H. O., Roberts, D., Skea, J., and Shukla, P. R.
Ishikawa, Y., and Saka, S. (2001). Chemical conversion of cellulose as treated in supercritical methanol. Cellulose 8, 189–195. doi:10.1023/a:1013170020469
Itabaiana Junior, I., Avelar Do Nascimento, M., De Souza, R. O. M. A., Dufour, A., and Wojcieszak, R. (2020). Levoglucosan: a promising platform molecule? Green Chem. 22, 5859–5880. doi:10.1039/d0gc01490g
Jacobson, J. J., Roni, M. S., Lamers, P., and Cafferty, K. G. (2014). Biomass feedstock supply system design and analysis.
Jansen, M. L. A., Bracher, J. M., Papapetridis, I., Verhoeven, M. D., de Bruijn, H., de Waal, P. P., et al. (2017). Saccharomyces cerevisiae strains for second-generation ethanol production: from academic exploration to industrial implementation. FEMS Yeast Res. 17, fox044. doi:10.1093/femsyr/fox044
Johansson, A., Aaltonen, O., and Ylinen, P. (1987). Organosolv pulping-methods and pulp properties. Biomass 13, 45–65. doi:10.1016/0144-4565(87)90071-0
Kandiyoti, R., Herod, A., Bartle, K., and Morgan, T. (2017). “Liquefaction: thermal breakdown in the liquid phase,” in Solid fuels and heavy hydrocarbon liquids (Elsevier Ltd.), 205–249.
Karnchanatat, A., Petsom, A., Sangvanich, P., Piaphukiew, J., Whalley, A. J. S., Reynolds, C. D., et al. (2007). Purification and biochemical characterization of an extracellular β-glucosidase from the wood-decaying fungus Daldinia eschscholzii (Ehrenb.:Fr.) Rehm. FEMS Microbiol. Lett. 270, 162–170. doi:10.1111/j.1574-6968.2007.00662.x
Karp, E. M., Resch, M. G., Donohoe, B. S., Ciesielski, P. N., O’Brien, M. H., Nill, J. E., et al. (2015). Alkaline pretreatment of switchgrass. ACS Sustain Chem. Eng. 3, 1479–1491. doi:10.1021/acssuschemeng.5b00201
Kawamoto, H., Hatanaka, W., and Saka, S. (2003). Thermochemical conversion of cellulose in polar solvent (sulfolane) into levoglucosan and other low molecular-weight substances. J. Anal. Appl. Pyrolysis 70, 303–313. doi:10.1016/s0165-2370(02)00160-2
Kazi, F. K., Fortman, J. A., Anex, R. P., Hsu, D. D., Aden, A., Dutta, A., et al. (2010). Techno-economic comparison of process technologies for biochemical ethanol production from corn stover. Fuel 89, S20–S28. doi:10.1016/j.fuel.2010.01.001
Keiser, J. R., Brady, M. P., Thomson, J. K., Connatser, R. M., Lewis, S. A., and Leonard, D. N. (2014). “Bio-oil properties and effects on containment materials,” in Corrosion 2014 (San Antonio).
Kellock, M., Maaheimo, H., Marjamaa, K., Rahikainen, J., Zhang, H., Holopainen-Mantila, U., et al. (2019). Effect of hydrothermal pretreatment severity on lignin inhibition in enzymatic hydrolysis. Bioresour. Technol. 280, 303–312. doi:10.1016/j.biortech.2019.02.051
Kelsall, , Dave, R., and Lyons, T. P. (2003). “Practical management of yeast: conversion of sugars to ethanol,” in The alcohol textbook. Editors K. A. Jacques, T. P. Lyons, and D. R. Kelsall (Nottingham: Nottingham University Press), 121–134.
Kenney, K. L., Smith, W. A., Gresham, G. L., and Westover, T. L. (2013). Understanding biomass feedstock variability. Biofuels 4, 111–127. doi:10.4155/bfs.12.83
Kilzer, F. J., and Broido, A. (1965). Speculations on the nature of cellulose pyrolysis. Pyrodynamics, 151–163.
Kim, J. S., Lee, Y. Y., and Kim, T. H. (2016). A review on alkaline pretreatment technology for bioconversion of lignocellulosic biomass. Bioresour. Technol. 199, 42–48. doi:10.1016/j.biortech.2015.08.085
Kim, K. H., Brown, R. C., and Bai, X. (2014). Partial oxidative pyrolysis of acid infused red oak using a fluidized bed reactor to produce sugar rich bio-oil. Fuel 130, 135–141. doi:10.1016/j.fuel.2014.04.044
Kim, Y., Ximenes, E., Mosier, N. S., and Ladisch, M. R. (2011). Soluble inhibitors/deactivators of cellulase enzymes from lignocellulosic biomass. Enzyme Microb. Technol. 48, 408–415. doi:10.1016/j.enzmictec.2011.01.007
Kitamura, Y., Abe, Y., and Yasui, T. (1991). Metabolism of levoglucosan(1,6-anhydro-.BETA.-D-glucopyranose) in microorganisms. Agric. Biol. Chem. 55, 515–521. doi:10.1271/bbb1961.55.515
Klein-Marcuschamer, D., Turner, C., Allen, M., Gray, P., Dietzgen, R. G., Gresshoff, P. M., et al. (2013). Technoeconomic analysis of renewable aviation fuel from microalgae, Pongamia pinnata, and sugarcane. Biofuels, Bioprod. Biorefining 7, 416–428. doi:10.1002/bbb.1404
Knott, B. C., Crowley, M. F., Himmel, M. E., Ståhlberg, J., and Beckham, G. T. (2014a). Carbohydrate-protein interactions that drive processive polysaccharide translocation in enzymes revealed from a computational study of cellobiohydrolase processivity. J. Am. Chem. Soc. 136, 8810–8819. doi:10.1021/ja504074g
Knott, B. C., Haddad Momeni, M., Crowley, M. F., MacKenzie, L. F., Götz, A. W., Sandgren, M., et al. (2014b). The mechanism of cellulose hydrolysis by a two-step, retaining cellobiohydrolase elucidated by structural and transition path sampling studies. J. Am. Chem. Soc. 136, 321–329. doi:10.1021/ja410291u
Ko, J. K., Kim, Y., Ximenes, E., and Ladisch, M. R. (2015). Effect of liquid hot water pretreatment severity on properties of hardwood lignin and enzymatic hydrolysis of cellulose. Biotechnol. Bioeng. 112, 252–262. doi:10.1002/bit.25349
Koll, P., Borchers, G., and Metzger, J. O. (1991). Thermal degradation of chitin and cellulose. J. Anal. Appl. Pyrolysis 19, 119–129. doi:10.1016/0165-2370(91)80038-a
Kramer, D. (2022). Whatever happened to cellulosic ethanol? Phys. Today 75, 22–24. doi:10.1063/PT.3.5036
Kruger, J. S., Cleveland, N. S., Yeap, R. Y., Dong, T., Ramirez, K. J., Nagle, N. J., et al. (2018). Recovery of fuel-precursor lipids from oleaginous yeast. ACS Sustain Chem. Eng. 6, 2921–2931. doi:10.1021/acssuschemeng.7b01874
Kudo, S., Goto, N., Sperry, J., Norinaga, K., and Hayashi, J. I. (2017). Production of levoglucosenone and dihydrolevoglucosenone by catalytic reforming of volatiles from cellulose pyrolysis using supported ionic liquid phase. ACS Sustain Chem. Eng. 5, 1132–1140. doi:10.1021/acssuschemeng.6b02463
Kunkes, E. L., Simonetti, D. A., West, R. M., Serrano-Ruiz, J. C., Gartner, C. A., and Dumesic, J. A. (2008). Catalytic conversion of biomass to monofunctional hydrocarbons and targeted liquid-fuel classes. Science 322, 417–421. doi:10.1126/science.1159210
Kuzhiyil, N., Dalluge, D., Bai, X., Kim, K. H., and Brown, R. C. (2012). Pyrolytic sugars from cellulosic biomass. ChemSusChem 5, 2228–2236. doi:10.1002/cssc.201200341
Lambertz, C., Garvey, M., Klinger, J., Heesel, D., Klose, H., Fischer, R., et al. (2014). Challenges and advances in the heterologous expression of cellulolytic enzymes: a review. Biotechnol. Biofuels 7, 135. doi:10.1186/s13068-014-0135-5
Lane, J. (2017). Depolymerizing that dang lignin: the Digest’s 2017 guide to biochemical. lignin deconstruction [WWW Document]. Digest (Wash D C).
Layton, D. S., Ajjarapu, A., Choi, D. W., and Jarboe, L. R. (2011). Engineering ethanologenic Escherichia coli for levoglucosan utilization. Bioresour. Technol. 102, 8318–8322. doi:10.1016/j.biortech.2011.06.011
Lenihan, P., Orozco, A., O’Neill, E., Ahmad, M. N. M., Rooney, D. W., and Walker, G. M. (2010). Dilute acid hydrolysis of lignocellulosic biomass. Chem. Eng. J. 156, 395–403. doi:10.1016/j.cej.2009.10.061
Li, C., and Zhao, Z. K. (2007). Efficient acid-catalyzed hydrolysis of cellulose in ionic liquid. Adv. Synth. Catal. 349, 1847–1850. doi:10.1002/adsc.200700259
Li, M., Zhang, W., Hayes, D., Arthur, R., Yang, Y., and Wang, X. (2017). China’s new nationwide E10 ethanol mandate and its global implications. Agric. Policy Rev.
Li, W., Ghosh, A., Bbosa, D., Brown, R., and Wright, M. M. (2018). Comparative techno-economic, uncertainty and life cycle analysis of lignocellulosic biomass solvent liquefaction and sugar fermentation to ethanol. ACS Sustain Chem. Eng. 6, 16515–16524. doi:10.1021/acssuschemeng.8b03622
Lian, J., Chen, S., Zhou, S., Wang, Z., O’Fallon, J., Li, C. Z., et al. (2010). Separation, hydrolysis and fermentation of pyrolytic sugars to produce ethanol and lipids. Bioresour. Technol. 101, 9688–9699. doi:10.1016/j.biortech.2010.07.071
Lian, J., Choi, J., Tan, Y. S., Howe, A., Wen, Z., and Jarboe, L. R. (2016). Identification of soil microbes capable of utilizing cellobiosan. PLoS One 11, e0149336. doi:10.1371/journal.pone.0149336
Lindstrom, J. K., Brown, J. L., Peterson, C. A., Ghosh, A., Rollag, S. A., Kouris, P. D., et al. (2020). A novel semi-batch autoclave reactor to overcome thermal dwell time in solvent liquefaction experiments. Chem. Eng. J. 417, 128074. doi:10.1016/j.cej.2020.128074
Lindstrom, J. K., Proano-Aviles, J., Johnston, P. A., Peterson, C. A., Stansell, J. S., and Brown, R. C. (2019a). Competing reactions limit levoglucosan yield during fast pyrolysis of cellulose. Green Chem. 21, 178–186. doi:10.1039/c8gc03461c
Lindstrom, J. K., Shaw, A., Zhang, X., and Brown, R. C. (2019b). “Condensed phase reactions during thermal deconstruction,” in Thermochemical processing of biomass: conversion into fuels, chemicals and power. Editor R. C. Brown (Wiley & Sons).
Linger, J. G., Hobdey, S. E., Franden, M. A., Fulk, E. M., and Beckham, G. T. (2016). Conversion of levoglucosan and cellobiosan by Pseudomonas putida KT2440. Metab. Eng. Commun. 3, 24–29. doi:10.1016/j.meteno.2016.01.005
Liszka, M. J., Kang, A., Konda, N. V. S. N. M., Tran, K., Gladden, J. M., Singh, S., et al. (2016). Switchable ionic liquids based on di-carboxylic acids for one-pot conversion of biomass to an advanced biofuel. Green Chem. 18, 4012–4021. doi:10.1039/c6gc00657d
Liu, Z.-S., Wu, X.-L., Kida, K., and Tang, Y.-Q. (2012). Corn stover saccharification with concentrated sulfuric acid: effects of saccharification conditions on sugar recovery and by-product generation. Bioresour. Technol. 119, 224–233. doi:10.1016/j.biortech.2012.05.107
Lloyd, T. A., and Wyman, C. E. (2005). Combined sugar yields for dilute sulfuric acid pretreatment of corn stover followed by enzymatic hydrolysis of the remaining solids. Bioresour. Technol. 96, 1967–1977. doi:10.1016/j.biortech.2005.01.011
Loow, Y.-L., Wu, T. Y., Jahim, J. M., Mohammad, A. W., and Teoh, W. H. (2016). Typical conversion of lignocellulosic biomass into reducing sugars using dilute acid hydrolysis and alkaline pretreatment. Cellulose 23, 1491–1520. doi:10.1007/s10570-016-0936-8
Luterbacher, J. S., Martin Alonso, D., and Dumesic, J. A. (2014). Targeted chemical upgrading of lignocellulosic biomass to platform molecules. Green Chem. 16, 4816–4838. doi:10.1039/c4gc01160k
Luterbacher, J. S., Rand, J. M., Alonso, D. M., Han, J., Youngquist, J. T., Maravelias, C. T., et al. (2014). Nonenzymatic sugar production from biomass using biomass-derived γ-valerolactone. Science 343, 277–280. doi:10.1126/science.1246748
Lynd, L. R., Guss, A. M., Himmel, M. E., Beri, D., Herring, C., Holwerda, E. K., et al. (2016). Advances in consolidated bioprocessing using Clostridium thermocellum and thermoanaerobacter saccharolyticum. Ind. Biotechnol. Microorg. 2, 365–394. doi:10.1002/9783527807796.ch10
Lynd, L. R., Liang, X., Biddy, M. J., Allee, A., Cai, H., Foust, T., et al. (2017). Cellulosic ethanol: status and innovation. Curr. Opin. Biotechnol. 45, 202–211. doi:10.1016/j.copbio.2017.03.008
Maduskar, S., Maliekkal, V., Neurock, M., and Dauenhauer, P. J. (2018). On the yield of levoglucosan from cellulose pyrolysis. ACS Sustain Chem. Eng. 6, 7017–7025. doi:10.1021/acssuschemeng.8b00853
Mai, N. L., Ahn, K., and Koo, Y.-M. (2014). Methods for recovery of ionic liquids - a review. Process Biochem. 49, 872–881. doi:10.1016/j.procbio.2014.01.016
Malester, I. A., Green, M., and Shelef, G. (1992). Kinetics of dilute acid hydrolysis of cellulose originating from municipal solid wastes. Industrial Eng. Chem. Res. 31, 1998–2003. doi:10.1021/ie00008a023
Man, Y. T. (2022). Why is the bond ball mill grindability test done the way it is done? Eur. J. Mineral Process. Environ. Prot. 2, 34–39.
Marinkovic, S., and Estrine, B. (2010). Direct conversion of wheat bran hemicelluloses into n-decyl-pentosides. Green Chem. 12, 1929–1932. doi:10.1039/c0gc00309c
Mariscal, R., Maireles-Torres, P., Ojeda, M., Sádaba, I., and López Granados, M. (2016). Furfural: a renewable and versatile platform molecule for the synthesis of chemicals and fuels. Energy Environ. Sci. 9, 1144–1189. doi:10.1039/c5ee02666k
Mattsson, J. E. (1990). Basic handling characteristics of wood fuels: angle of repose, friction against surfaces and tendency to bridge for different assortments. Scand J Res 5, 583–597. doi:10.1080/02827589009382641
Mayer-Laigle, C., Blanc, N., Rajaonarivony, R. K., and Rouau, X. (2018). Comminution of dry lignocellulosic biomass, a review: Part I. from fundamental mechanisms to milling behaviour. Bioengineering 5, 41. doi:10.3390/bioengineering5020041
Mayes, H. B., and Broadbelt, L. J. (2012). Unraveling the reactions that unravel cellulose. J. Phys. Chem. A 116, 7098–7106. doi:10.1021/jp300405x
Mayes, H. B., Nolte, M. W., Beckham, G. T., Shanks, B. H., and Broadbelt, L. J. (2015). The alpha-bet(a) of salty glucose pyrolysis: computational investigations reveal carbohydrate pyrolysis catalytic action by sodium ions. ACS Catal. 5, 192–202. doi:10.1021/cs501125n
McPhail, L., Westcott, P., and Lutman, H. (2011). The renewable identification number system and U.S. Biofuel Mandates.
Mellmer, M. A., Martin Alonso, D., Luterbacher, J. S., Gallo, J. M. R., and Dumesic, J. A. (2014). Effects of γ-valerolactone in hydrolysis of lignocellulosic biomass to monosaccharides. Green Chem. 16, 4659–4662. doi:10.1039/c4gc01768d
Mika, L. T., Cséfalvay, E., and Németh, Á. (2018). Catalytic conversion of carbohydrates to initial platform chemicals: chemistry and sustainability. Chem. Rev. 118, 505–613. doi:10.1021/acs.chemrev.7b00395
Minnaar, L. S., Kruger, F., Fortuin, J., Hoffmeester, L. J., and den Haan, R. (2024). Engineering Saccharomyces cerevisiae for application in integrated bioprocessing biorefineries. Curr. Opin. Biotechnol. 85, 103030. doi:10.1016/j.copbio.2023.103030
Moe, S. T., Janga, K. K., Hertzberg, T., Hägg, M. B., Øyaas, K., and Dyrset, N. (2012). “Saccharification of lignocellulosic biomass for biofuel and biorefinery applications - a renaissance for the concentrated acid hydrolysis?,” in Energy procedia (Elsevier Ltd), 50–58. doi:10.1016/j.egypro.2012.03.007
Mohagheghi, A., Evans, K., Chou, Y.-C., and Zhang, M. (2002). Cofermentation of glucose, xylose, and arabinose by genomic DNA-integrated xylose/arabinose fermenting strain of Zymomonas mobilis AX101. Appl. Biochem. Biotechnol. 98 (100), 885–898. doi:10.1385/abab:98-100:1-9:885
Mørup, A. J., Becker, J., Christensen, P. S., Houlberg, K., Lappa, E., Klemmer, M., et al. (2015). Construction and commissioning of a continuous reactor for hydrothermal liquefaction. Ind. Eng. Chem. Res. 54, 5935–5947. doi:10.1021/acs.iecr.5b00683
Mosier, N., Wyman, C., Dale, B., Elander, R., Lee, Y. Y., Holtzapple, M., et al. (2005). Features of promising technologies for pretreatment of lignocellulosic biomass. Bioresour. Technol. 96, 673–686. doi:10.1016/j.biortech.2004.06.025
Ndubuisi, I. A., Amadi, C. O., Nwagu, T. N., Murata, Y., and Ogbonna, J. C. (2023). Novel thermotolerant yeast suitable for industrial bioethanol production. Biofuels, 1–10. doi:10.1080/17597269.2023.2267850
Neshat, S. A., Mohammadi, M., Najafpour, G. D., and Lahijani, P. (2017). Anaerobic co-digestion of animal manures and lignocellulosic residues as a potent approach for sustainable biogas production. Renew. Sustain. Energy Rev. 79, 308–322. doi:10.1016/j.rser.2017.05.137
Nguyen, T. Y., Cai, C. M., Kumar, R., and Wyman, C. E. (2015). Co-Solvent pretreatment reduces costly enzyme requirements for high sugar and ethanol yields from lignocellulosic biomass. ChemSusChem 8, 1716–1725. doi:10.1002/cssc.201403045
Nguyen, T. Y., Cai, C. M., Kumar, R., and Wyman, C. E. (2017). Overcoming factors limiting high-solids fermentation of lignocellulosic biomass to ethanol. Proc. Natl. Acad. Sci. U. S. A. 114, 11673–11678. doi:10.1073/pnas.1704652114
Nitsos, C., Rova, U., and Christakopoulos, P. (2018). Organosolv fractionation of softwood biomass for biofuel and biorefinery applications. Energies (Basel) 11, 50. doi:10.3390/en11010050
Nogueira, G. P., Capaz, R. S., Franco, T. T., Dias, M. O. S., and Cavaliero, C. K. N. (2022). Enzymes as an environmental bottleneck in cellulosic ethanol production: does on-site production solve it? J. Clean. Prod. 369, 133314. doi:10.1016/j.jclepro.2022.133314
Oja, V., and Suuberg, E. M. (1999). Vapor pressures and enthalpies of sublimation of D-glucose, D-xylose, cellobiose, and levoglucosan. J. Chem. Eng. Data 44, 26–29. doi:10.1021/je980119b
Oudenhoven, S. R. G., Lievens, C., and Kersten, S. R. A. (2016a). Effect of temperature on the fast pyrolysis of organic-acid leached pinewood the potential of low temperature pyrolysis. Biomass Bioenergy 89, 78–90. doi:10.1016/j.biombioe.2015.12.019
Oudenhoven, S. R. G., van der Ham, A. G. J., van den Berg, H., Westerhof, R. J. M., and Kersten, S. R. A. (2016b). Using pyrolytic acid leaching as a pretreatment step in a biomass fast pyrolysis plant: process design and economic evaluation. Biomass Bioenergy 95, 388–404. doi:10.1016/j.biombioe.2016.07.003
Oyedeji, O., Gitman, P., Qu, J., and Webb, E. (2020). Understanding the impact of lignocellulosic biomass variability on size reduction process - a review. Oak Ridge.
Panda, S. K., and Maiti, S. K. (2024). Novel cyclic shifting of temperature strategy for simultaneous saccharification and fermentation for lignocellulosic bioethanol production. Bioresour. Technol. 391, 129975. doi:10.1016/j.biortech.2023.129975
Patwardhan, P. R., Brown, R. C., and Shanks, B. H. (2011a). Product distribution from the fast pyrolysis of hemicellulose. ChemSusChem 4, 636–643. doi:10.1002/cssc.201000425
Patwardhan, P. R., Brown, R. C., and Shanks, B. H. (2011b). Understanding the fast pyrolysis of lignin. ChemSusChem 4, 1629–1636. doi:10.1002/cssc.201100133
Patwardhan, P. R., Satrio, J. A., Brown, R. C., and Shanks, B. H. (2009). Product distribution from fast pyrolysis of glucose-based carbohydrates. J. Anal. Appl. Pyrolysis 86, 323–330. doi:10.1016/j.jaap.2009.08.007
Patwardhan, P. R., Satrio, J. A., Brown, R. C., and Shanks, B. H. (2010). Influence of inorganic salts on the primary pyrolysis products of cellulose. Bioresour. Technol. 101, 4646–4655. doi:10.1016/j.biortech.2010.01.112
Paye, J. M. D., Guseva, A., Hammer, S. K., Gjersing, E., Davis, M. F., Davison, B. H., et al. (2016). Biological lignocellulose solubilization: comparative evaluation of biocatalysts and enhancement via cotreatment. Biotechnol. Biofuels 9, 8. doi:10.1186/s13068-015-0412-y
Pecha, M. B., Arbelaez, J. I. M., Garcia-Perez, M., Chejne, F., and Ciesielski, P. N. (2019). Progress in understanding the four dominant intra-particle phenomena of lignocellulose pyrolysis: chemical reactions, heat transfer, mass transfer, and phase change. Green Chem. 21, 2868–2898. doi:10.1039/c9gc00585d
Pérez, F., and Granger, B. E. (2007). IPython: a system for interactive scientific computing. Comput. Sci. Eng. 9, 21–29. doi:10.1109/mcse.2007.53
Perlack, R. D., Wright, L. L., Turhollow, A. F., Graham, R. L., Stokes, B. J., and Erbach, D. C. (2005). Biomass as feedstock for a Bioenergy and bioproducts industry: the technical feasibility of a billion-ton annual supply. Oak Ridge, TN.
Petersen, L., Ardèvol, A., Rovira, C., and Reilly, P. J. (2009). Mechanism of cellulose hydrolysis by inverting GH8 endoglucanases: a QM/MM metadynamics study. J. Phys. Chem. B 113, 7331–7339. doi:10.1021/jp811470d
Peterson, C. A., Rollag, S. S., Lindstrom, J. K., and Brown, R. C. (2023). The effect of ferrous sulfate pretreatment on the optimal temperature for production of sugars during autothermal pyrolysis. J. Anal. Appl. Pyrolysis 171, 105966. doi:10.1016/j.jaap.2023.105966
Pinkert, A., Marsh, K. N., Pang, S., and Staiger, M. P. (2009). Ionic liquids and their interaction with cellulose. Chem. Rev. 109, 6712–6728. doi:10.1021/cr9001947
Plouffe, C., Peterson, C. A., Rollag, S. A., and Brown, R. C. (2022). The role of biochar in the degradation of sugars during fast pyrolysis of biomass. J. Anal. Appl. Pyrolysis 161, 105416. doi:10.1016/j.jaap.2021.105416
Polin, J. P., Carr, H. D., Whitmer, L. E., Smith, R. G., and Brown, R. C. (2019). Conventional and autothermal pyrolysis of corn stover: overcoming the processing challenges of high-ash agricultural residues. J. Anal. Appl. Pyrolysis 143, 104679. doi:10.1016/j.jaap.2019.104679
Polin, J. P., Peterson, C. A., Whitmer, L. E., Smith, R. G., and Brown, R. C. (2019). Process intensification of biomass fast pyrolysis through autothermal operation of a fluidized bed reactor. Appl. Energy 249, 276–285. doi:10.1016/j.apenergy.2019.04.154
Pollard, A. S., Rover, M. R., and Brown, R. C. (2012). Characterization of bio-oil recovered as stage fractions with unique chemical and physical properties. J. Anal. Appl. Pyrolysis 93, 129–138. doi:10.1016/j.jaap.2011.10.007
Qi, B., Chen, X., and Wan, Y. (2010). Pretreatment of wheat straw by nonionic surfactant-assisted dilute acid for enhancing enzymatic hydrolysis and ethanol production. Bioresour. Technol. 101, 4875–4883. doi:10.1016/j.biortech.2010.01.063
Qing, Q., Yang, B., and Wyman, C. E. (2010). Xylooligomers are strong inhibitors of cellulose hydrolysis by enzymes. Bioresour. Technol. 101, 9624–9630. doi:10.1016/j.biortech.2010.06.137
Questell-Santiago, Y. M., Zambrano-Varela, R., Talebi Amiri, M., and Luterbacher, J. S. (2018). Carbohydrate stabilization extends the kinetic limits of chemical polysaccharide depolymerization. Nat. Chem. 10, 1222–1228. doi:10.1038/s41557-018-0134-4
Radlein, D., and Quignard, A. (2013). A short historical review of fast pyrolysis of biomass. Oil Gas Sci. Technol. 68, 765–783. doi:10.2516/ogst/2013162
Radlein, D. S. T. A. G., Grinshpun, A., Piskorz, J., and Scott, D. S. (1987). On the presence of anhydro-oligosaccharides in the sirups from the fast pyrolysis of cellulose. J. Anal. Appl. Pyrolysis 12, 39–49. doi:10.1016/0165-2370(87)80013-x
Rajak, R. C., and Banerjee, R. (2020). An innovative approach of mixed enzymatic venture for 2G ethanol production from lignocellulosic feedstock. Energy Convers. Manag. 207, 112504. doi:10.1016/j.enconman.2020.112504
Rao, J., Lv, Z., Chen, G., and Peng, F. (2023). Hemicellulose: structure, chemical modification, and application. Prog. Polym. Sci. 140, 101675. doi:10.1016/j.progpolymsci.2023.101675
Rasmussen, H., Sørensen, H. R., and Meyer, A. S. (2014). Formation of degradation compounds from lignocellulosic biomass in the biorefinery: sugar reaction mechanisms. Carbohydr. Res. 385, 45–57. doi:10.1016/j.carres.2013.08.029
Regulation of Fuels and Fuel Additives (2011). Renewable Fuel Standards. 75 Fed. Reg., 76790–76830. (Dec. 9, 2010)
Reichardt, C., and Welton, T. (2010). Solvents and solvent effects in organic chemistry. 4th ed. Weinheim, Germany: Wiley VCH.
Renewable Identification Number (2023). Renewable identification number (RIN) data for renewable fuel standard program.
Rinaldi, R., Palkovits, R., and Schüth, F. (2008). Depolymerization of cellulose using solid catalysts in ionic liquids. Angew. Chem. 120, 8167–8170. doi:10.1002/ange.200802879
Rohrbach, J. C., and Luterbacher, J. S. (2021). Investigating the effects of substrate morphology and experimental conditions on the enzymatic hydrolysis of lignocellulosic biomass through modeling. Biotechnol. Biofuels 14, 103. doi:10.1186/s13068-021-01920-2
Rollag, S. A., Lindstrom, J. K., and Brown, R. C. (2020). Pretreatments for the continuous production of pyrolytic sugar from lignocellulosic biomass. Chem. Eng. J. 385, 123889. doi:10.1016/j.cej.2019.123889
Ronsse, F., Bai, X., Prins, W., and Brown, R. C. (2012). Secondary reactions of levoglucosan and char in the fast pyrolysis of cellulose. Environ. Prog. Sustain Energy 31, 256–260. doi:10.1002/ep.11633
Rover, M. R., Aui, A., Wright, M. M., Smith, R. G., and Brown, R. C. (2019). Production and purification of crystallized levoglucosan from pyrolysis of lignocellulosic biomass. Green Chem. 21, 5980–5989. doi:10.1039/c9gc02461a
Rover, M. R., Johnston, P. A., Jin, T., Smith, R. G., Brown, R. C., and Jarboe, L. (2014). Production of clean pyrolytic sugars for fermentation. ChemSusChem 7, 1662–1668. doi:10.1002/cssc.201301259
Saeman, J. F. (1945). Kinetics of wood saccharification hydrolysis of cellulose and decomposition of sugars in dilute acid at high temperature. Ind. Eng. Chem. 37, 43–52. doi:10.1021/ie50421a009
Saka, S., and Ueno, T. (1999). Chemical conversion of various celluloses to glucose and its derivatives in supercritical water. Cellulose 6, 177–191. doi:10.1023/a:1009232508644
Sameni, J., Krigstin, S., and Sain, M. (2016). Characterization of lignins isolated from industrial residues and their beneficial uses. Bioresources 11, 8435–8456. doi:10.15376/biores.11.4.8435-8456
Sarkar, N., Ghosh, S. K., Bannerjee, S., and Aikat, K. (2012). Bioethanol production from agricultural wastes: an overview. Renew. Energy 37, 19–27. doi:10.1016/j.renene.2011.06.045
Sasaki, M., Fang, Z., Fukushima, Y., Adschiri, T., and Arai, K. (2000). Dissolution and hydrolysis of cellulose in subcritical and supercritical water. Ind. Eng. Chem. Res. 39, 2883–2890. doi:10.1021/ie990690j
Sasaki, M., Kabyemela, B., Malaluan, R., Hirose, S., Takeda, N., Adschiri, T., et al. (1998). Cellulose hydrolysis in subcritical and supercritical water. J. Supercrit. Fluids 13, 261–268. doi:10.1016/s0896-8446(98)00060-6
Savaresi, A. (2016). The Paris Agreement: a new beginning? J. Energy Nat. Resour. Law 34, 16–26. doi:10.1080/02646811.2016.1133983
Schell, D. J., and Harwood, C. (1994). Milling of lignocellulosic biomass results of pilot-scale testing. Appl. Biochem. Biotechnol. 45, 46. doi:10.1007/BF02941795
Seike, T., Kobayashi, Y., Sahara, T., Ohgiya, S., Kamagata, Y., and Fujimori, K. E. (2019). Molecular evolutionary engineering of xylose isomerase to improve its catalytic activity and performance of micro-aerobic glucose/xylose co-fermentation in Saccharomyces cerevisiae. Biotechnol. Biofuels 12, 139. doi:10.1186/s13068-019-1474-z
Selinger, L. B., Forsberg, C. W., and Cheng, K.-J. (1996). The rumen: a unique source of enzymes for enhancing livestock production. Anaerobe 2, 263–284. doi:10.1006/anae.1996.0036
Selke, S. M., Hawley, M. C., Hardt, H., Lamport, D. T. A., Smith, G., and Smith, J. (1982). Chemicals from wood via HF. Ind. Eng. Chem. Prod. Res. Dev. 21, 11–16. doi:10.1021/i300005a003
Sewalk, S. (2014). Brazil’s energy policy and regulation. Fordham Environ. Law Rev. 25, 652–705. doi:10.2307/26195861
Shafizadeh, F., Furneaux, R. H., Cochran, T. G., Scholl, J. P., and Sakai, Y. (1979). Production of levoglucosan and glucose from pyrolysis of cellulosic materials. J. Appl. Polym. Sci. 23, 3525–3539. doi:10.1002/app.1979.070231209
Shahab, R. L., Luterbacher, J. S., Brethauer, S., and Studer, M. H. (2018). Consolidated bioprocessing of lignocellulosic biomass to lactic acid by a synthetic fungal-bacterial consortium. Biotechnol. Bioeng. 115, 1207–1215. doi:10.1002/bit.26541
Shanks, B. H., and Keeling, P. L. (2017). Bioprivileged molecules: creating value from biomass. Green Chem. 19, 3177–3185. doi:10.1039/c7gc00296c
Shin, E.-J., Nimlos, M. R., and Evans, R. J. (2001). Kinetic analysis of the gas-phase pyrolysis of carbohydrates. Fuel 80, 1697–1709. doi:10.1016/s0016-2361(01)00056-4
Shuai, L., and Luterbacher, J. (2016). Organic solvent effects in biomass conversion reactions. ChemSusChem 9, 133–155. doi:10.1002/cssc.201501148
Shuai, L., Questell-Santiago, Y. M., and Luterbacher, J. S. (2016). “A mild biomass pretreatment using γ-valerolactone for concentrated sugar production,” in Green chemistry, Vol. 18, 937–943. doi:10.1039/c5gc02489g
Silveira, M. H. L., Morais, A. R. C., Da Costa Lopes, A. M., Olekszyszen, D. N., Bogel-Łukasik, R., Andreaus, J., et al. (2015). Current pretreatment technologies for the development of cellulosic ethanol and biorefineries. ChemSusChem 8, 3366–3390. doi:10.1002/cssc.201500282
Singh, J., Suhag, M., and Dhaka, A. (2015). Augmented digestion of lignocellulose by steam explosion, acid and alkaline pretreatment methods: a review. Carbohydr. Polym. 117, 624–631. doi:10.1016/j.carbpol.2014.10.012
Singh, N., Mathur, A. S., Gupta, R. P., Barrow, C. J., Tuli, D., and Puri, M. (2018). Enhanced cellulosic ethanol production via consolidated bioprocessing by Clostridium thermocellum ATCC 31924. Bioresour. Technol. 250, 860–867. doi:10.1016/j.biortech.2017.11.048
Smith, P. (2016). Soil carbon sequestration and biochar as negative emission technologies. Glob. Chang. Biol. 22, 1315–1324. doi:10.1111/gcb.13178
Sørensen, A., Lübeck, M., Lübeck, P. S., and Ahring, B. K. (2013). Fungal beta-glucosidases: a bottleneck in industrial use of lignocellulosic materials. Biomolecules 3, 612–631. doi:10.3390/biom3030612
Sources of Greenhouse Gas Emissions (2020). United States environmental protection agency. URL Available at: https://epa.gov/ghgemissions/inventory-us-greenhouse-gas-.
Stanford, J. P., Hall, P. H., Rover, M. R., Smith, R. G., and Brown, R. C. (2018). Separation of sugars and phenolics from the heavy fraction of bio-oil using polymeric resin adsorbents. Sep. Purif. Technol. 194, 170–180. doi:10.1016/j.seppur.2017.11.040
Stasiak, M., Molenda, M., Bańda, M., Wiącek, J., Parafiniuk, P., Lisowski, A., et al. (2019). Mechanical characteristics of pine biomass of different sizes and shapes. Eur. J. Wood Wood Prod. 77, 593–608. doi:10.1007/s00107-019-01415-w
Steen, E. J., Kang, Y., Bokinsky, G., Hu, Z., Schirmer, A., McClure, A., et al. (2010). Microbial production of fatty-acid-derived fuels and chemicals from plant biomass. Nature 463, 559–562. doi:10.1038/nature08721
Sun, N., Parthasarathi, R., Socha, A. M., Shi, J., Zhang, S., Stavila, V., et al. (2014). Understanding pretreatment efficacy of four cholinium and imidazolium ionic liquids by chemistry and computation. Green Chem. 16, 2546–2557. doi:10.1039/c3gc42401d
Sun, S., Sun, S., Cao, X., and Sun, R. (2016). The role of pretreatment in improving the enzymatic hydrolysis of lignocellulosic materials. Bioresour. Technol. 199, 49–58. doi:10.1016/j.biortech.2015.08.061
Swatloski, R. P., Spear, S. K., Holbrey, J. D., and Rogers, R. D. (2002). Dissolution of cellose with ionic liquids. J. Am. Chem. Soc. Commun. 124, 4974–4975. doi:10.1021/ja025790m
Tadesse, H., and Luque, R. (2011). Advances on biomass pretreatment using ionic liquids: an overview. Energy Environ. Sci. 4, 3913–3929. doi:10.1039/c0ee00667j
Taherzadeh, M. J., and Karimi, K. (2007). Acid-based hydrolysis processes for ethanol from lignocellulosic materials: a review. Bioresources 2, 472–499. doi:10.15376/biores.2.4.472-499
Talebnia, F., Karakashev, D., and Angelidaki, I. (2010). Production of bioethanol from wheat straw: an overview on pretreatment, hydrolysis and fermentation. Bioresour. Technol. 101, 4744–4753. doi:10.1016/j.biortech.2009.11.080
Tao, L., and Aden, A. (2009). The economics of current and future biofuels. Vitro Cell. Dev. Biol. Plant 45, 199–217. doi:10.1007/s11627-009-9216-8
Teymouri, F., Laureano-Perez, L., Alizadeh, H., and Dale, B. E. (2005). Optimization of the ammonia fiber explosion (AFEX) treatment parameters for enzymatic hydrolysis of corn stover. Bioresour. Technol. 96, 2014–2018. doi:10.1016/j.biortech.2005.01.016
Thigpen, P. N., and Berry, W. L. (1982). “Liquid fuel from wood by continuous operation of the albany biomass liquefaction facility,” in Energy from biomass and wastes VI (FL: Lake Buena Vista), 1057–1095.
Tiarks, J. A., Dedic, C. E., Meyer, T. R., Brown, R. C., and Michael, J. B. (2019). Visualization of physicochemical phenomena during biomass pyrolysis in an optically accessible reactor. J. Anal. Appl. Pyrolysis 143, 104667. doi:10.1016/j.jaap.2019.104667
Tolan, J. S. (2002). Iogen’s process for producing ethanol from cellulosic biomass. Clean. Technol. Environ. Policy 3, 339–345. doi:10.1007/s10098-001-0131-x
Triwahyuni, E., MuryantoMaryana, R., Sudiyani, Y., and Abimanyu, H. (2022). “Conversion of cellulosic biomass through consolidated bioprocessing method using Clostridium thermocellum,” in Proceedings of the 9th international symposium on innovative bioproduction Indonesia on biotechnology and bioengineering (Indonesia: Bogor).
Tsilomelekis, G., Orella, M. J., Lin, Z., Cheng, Z., Zheng, W., Nikolakis, V., et al. (2016). Molecular structure, morphology and growth mechanisms and rates of 5-hydroxymethyl furfural (HMF) derived humins. Green Chem. 18, 1983–1993. doi:10.1039/c5gc01938a
Unnasch, S., Parida, D., and Healy, B. D. (2023). GHG Emissions Reductions due to the RFS2 - a 2022 update.
UPDATE 1-Chinas Tianjin (2018). UPDATE 1-China’s Tianjin to use gasoline with ethanol in most vehicles. [WWW Document]. Reuters. URL Availble at: https://www.reuters.com/article/china-ethanol/update-1.
U.S. Department of Energy (2016). “2016 billion-ton report,” in Advancing domestic resources for a thriving bioeconomy (Oak Ridge, TN: Economic Viability of Feedstocks), 1.
Valdivia, M., Galan, J. L., Laffarga, J., and Ramos, J. L. (2016). Biofuels 2020: biorefineries based on lignocellulosic materials. Microb. Biotechnol. 9, 585–594. doi:10.1111/1751-7915.12387
van Osch, D. J. G. P., Kollau, L. J. B. M., Van Den Bruinhorst, A., Asikainen, S., Rocha, M. A. A., and Kroon, M. C. (2017). Ionic liquids and deep eutectic solvents for lignocellulosic biomass fractionation. Phys. Chem. Chem. Phys. 19, 2636–2665. doi:10.1039/c6cp07499e
van Putten, R. J., van der Waal, J. C., de Jong, E., Rasrendra, C. B., Heeres, H. J., and De Vries, J. G. (2013). Hydroxymethylfurfural, A versatile platform chemical made from renewable resources. Chem. Rev. 113, 1499–1597. doi:10.1021/cr300182k
Van Zandvoort, I., Wang, Y., Rasrendra, C. B., Van Eck, E. R. H., Bruijnincx, P. C. A., Heeres, H. J., et al. (2013). Formation, molecular structure, and morphology of humins in biomass conversion: influence of feedstock and processing conditions. ChemSusChem 6, 1745–1758. doi:10.1002/cssc.201300332
Venderbosch, R. H. (2019). “Fast pyrolysis,” in Thermochemical processing of biomass conversion into fuels, chemicals and power. Editor R. C. Brown (John Wiley & Sons Ltd), 175–203.
Verdía, P., Brandt, A., Hallett, J. P., Ray, M. J., and Welton, T. (2014). Fractionation of lignocellulosic biomass with the ionic liquid 1-butylimidazolium hydrogen sulfate. Green Chem. 16, 1617–1627. doi:10.1039/c3gc41742e
Vicente, A., Alves, C., Calvo, A. I., Fernandes, A. P., Nunes, T., Monteiro, C., et al. (2013). Emission factors and detailed chemical composition of smoke particles from the 2010 wildfire season. Atmos. Environ. 71, 295–303. doi:10.1016/j.atmosenv.2013.01.062
Villandier, N., and Corma, A. (2010). One pot catalytic conversion of cellulose into biodegradable surfactants. Chem. Commun. 46, 4408–4410. doi:10.1039/c0cc00031k
Vinu, R., and Broadbelt, L. J. (2012). A mechanistic model of fast pyrolysis of glucose-based carbohydrates to predict bio-oil composition. Energy Environ. Sci. 5, 9808–9826. doi:10.1039/c2ee22784c
Wallington, T. J., Anderson, J. E., Mueller, S. A., Kolinski Morris, E., Winkler, S. L., Ginder, J. M., et al. (2012). Corn ethanol production, food exports, and indirect land use change. Environ. Sci. Technol. 46, 6379–6384. doi:10.1021/es300233m
Wallner, T., Miers, S. A., and McConnell, S. (2009). A comparison of ethanol and butanol as oxygenates using a direct-injection, spark-ignition engine. J. Eng. Gas. Turbine Power 131. doi:10.1115/1.3043810
Wang, Z., Zhou, S., Pecha, B., Westerhof, R. J. M., and Garcia-Perez, M. (2014). Effect of pyrolysis temperature and sulfuric acid during the fast pyrolysis of cellulose and douglas fir in an atmospheric pressure wire mesh reactor. Energy Fuels 28, 5167–5177. doi:10.1021/ef500999z
Wasserscheid, P., and Keim, W. (2000). Ionic liquids new solutions for transition metal catalysis. Angew. Chem. 39, 3772–3789. doi:10.1002/1521-3773(20001103)39:21<3772::aid-anie3772>3.0.co;2-5
Werpy, T. A., Holladay, J. E., and White, J. F. (2004). Top value added chemicals from biomass: I. Results of screening for potential candidates from sugars and synthesis gas. Richland, WA.
Westerhof, R. J. M., Brilman, D. W. F., Garcia-Perez, M., Wang, Z., Oudenhoven, S. R. G., Van Swaaij, W. P. M., et al. (2011). Fractional condensation of biomass pyrolysis vapors. Energy Fuels 25, 1817–1829. doi:10.1021/ef2000322
Whistler, R. L. (1993). “Hemicelluloses,” in Industrial gums. Editors R. L. Whistler,, and J. N. Bemiller (Elsevier Inc.), 295–308.
White, D. H., Wolf, D., and Zhao, Y. (1987). A novel extruder-feeder reactor system for biomass liquefaction. American Institute of Chemical Engineers Annual Meeting.
Wijaya, Y. P., Putra, R. D. D., Widyaya, V. T., Ha, J. M., Suh, D. J., and Kim, C. S. (2014). Comparative study on two-step concentrated acid hydrolysis for the extraction of sugars from lignocellulosic biomass. Bioresour. Technol. 164, 221–231. doi:10.1016/j.biortech.2014.04.084
Williams, C. L., Emerson, R. M., and Tumuluru, J. S. (2017). “Biomass compositional analysis for conversion to renewable fuels and chemicals,” in Biomass volume estimation and valorization for energy, Editor J. S. Tumuluru (InTech), 251–270. doi:10.5772/65777
Williams, C. L., Westover, T. L., Emerson, R. M., Tumuluru, J. S., and Li, C. (2016). Sources of biomass feedstock variability and the potential impact on biofuels production. Bioenergy Res. 9, 1–14. doi:10.1007/s12155-015-9694-y
Williams, L. L., Rubin, J. B., and Edwards, H. W. (2004). Calculation of Hansen solubility parameter values for a range of pressure and temperature conditions, including the supercritical fluid region. Ind. Eng. Chem. Res. 43, 4967–4972. doi:10.1021/ie0497543
Woolf, D., Amonette, J. E., Street-Perrott, F. A., Lehmann, J., and Joseph, S. (2010). Sustainable biochar to mitigate global climate change. Nat. Commun. 1, 56–59. doi:10.1038/ncomms1053
Wright, J. D., and Power, A. J. (1986). Comparative technical evaluation of acid hydrolysis processes for conversion of cellulose to alcohol. Golden, CO.
Wright, J. D., Wyman, C. E., and Grohmann, K. (1988). Simultaneous saccharification and fermentation of lignocellulose: process evaluation. Appl. Biochem. Biotechnol. 18, 75–90. doi:10.1007/bf02930818
Wu, Y., Wang, Z., Ma, X., and Xue, C. (2021). High temperature simultaneous saccharification and fermentation of corn stover for efficient butanol production by a thermotolerant Clostridium acetobutylicum. Process Biochem. 100, 20–25. doi:10.1016/j.procbio.2020.09.026
Xu, F., Sun, J., Konda, N. V. S. N. M., Shi, J., Dutta, T., Scown, C. D., et al. (2016). Transforming biomass conversion with ionic liquids: process intensification and the development of a high-gravity, one-pot process for the production of cellulosic ethanol. Energy Environ. Sci. 9, 1042–1049. doi:10.1039/c5ee02940f
Xu, P., Qiao, K., Ahn, W. S., and Stephanopoulos, G. (2016). Engineering Yarrowia lipolytica as a platform for synthesis of drop-in transportation fuels and oleochemicals. Proc. Natl. Acad. Sci. U. S. A. 113, 10848–10853. doi:10.1073/pnas.1607295113
Xu, Q., Alahuhta, M., Wei, H., Knoshaug, E. P., Wang, W., Baker, J. O., et al. (2018). Expression of an endoglucanase-cellobiohydrolase fusion protein in Saccharomyces cerevisiae, Yarrowia lipolytica, and Lipomyces starkeyi. Biotechnol. Biofuels 11, 322. doi:10.1186/s13068-018-1301-y
Yamada, T., and Ono, H. (2001). Characterization of the products resulting from ethylene glycol liquefaction of cellulose. Liq. Cellul. 47, 458–464. doi:10.1007/bf00767898
Yan, Q., and Fong, S. S. (2017). Challenges and advances for genetic engineering of non-model bacteria and uses in consolidated bioprocessing. Front. Microbiol. 8, 2060. doi:10.3389/fmicb.2017.02060
Yan, S., Li, T., and Yao, L. (2011). Mutational effects on the catalytic mechanism of cellobiohydrolase i from trichoderma reesei. J. Phys. Chem. B 115, 4982–4989. doi:10.1021/jp200384m
Yang, B., Dai, Z., Ding, S. Y., and Wyman, C. E. (2011). Enzymatic hydrolysis of cellulosic biomass. Biofuels 2, 421–449. doi:10.4155/bfs.11.116
Yasui, T., Kitamura, Y., Nakahara, K., and Abe, Y. (1991). Metabolism of levoglucosan(1,6-anhydro-.BETA.-D-glucopyranose)in bacteria. Biol. Chem. 55, 1927–1929. doi:10.1271/bbb1961.55.1927
Zhang, J., Hou, W., and Bao, J. (2015). “Reactors for high solid loading pretreatment of lignocellulosic biomass,” in Bioreactor engineering research and industrial Applications123 (Springer-Verlag), 75–90.
Zhang, K., Sawaya, M. R., Eisenberg, D. S., and Liao, J. C. (2008). Expanding metabolism for biosynthesis of nonnatural alcohols. Proc. Natl. Acad. Sci. U. S. A. 105, 20653–20658. doi:10.1073/pnas.0807157106
Zhang, X., Yang, W., and Blasiak, W. (2012). Thermal decomposition mechanism of levoglucosan during cellulose pyrolysis. J. Anal. Appl. Pyrolysis 96, 110–119. doi:10.1016/j.jaap.2012.03.012
Zhang, Y., Brown, T. R., Hu, G., and Brown, R. C. (2013). Techno-economic analysis of monosaccharide production via fast pyrolysis of lignocellulose. Bioresour. Technol. 127, 358–365. doi:10.1016/j.biortech.2012.09.070
Zhao, C., Shao, Q., and Chundawat, S. P. S. (2020). Recent advances on ammonia-based pretreatments of lignocellulosic biomass. Bioresour. Technol. 298, 122446. doi:10.1016/j.biortech.2019.122446
Zhao, H., Baker, G. A., and Cowins, J. V. (2010). Fast enzymatic saccharification of switchgrass after pretreatment with ionic liquids. Biotechnol. Prog. 26, 127–133. doi:10.1002/btpr.331
Zhao, X., Cheng, K., and Liu, D. (2009). Organosolv pretreatment of lignocellulosic biomass for enzymatic hydrolysis. Appl. Microbiol. Biotechnol. 82, 815–827. doi:10.1007/s00253-009-1883-1
Zhao, X., Zhang, L., and Liu, D. (2012). Biomass recalcitrance. Part I: the chemical compositions and physical structures affecting the enzymatic hydrolysis of lignocellulose. Biofuels, Bioprod. Biorefining 6, 465–482. doi:10.1002/bbb.1331
Zhou, S., Brown, R. C., and Bai, X. (2015). The use of calcium hydroxide pretreatment to overcome agglomeration of technical lignin during fast pyrolysis. Green Chem. 17, 4748–4759. doi:10.1039/c5gc01611h
Zhou, X., Mayes, H. B., Broadbelt, L. J., Nolte, M. W., and Shanks, B. H. (2016). Fast pyrolysis of glucose-based carbohydrates with added NaCl part 2: validation and evaluation of the mechanistic model. AIChE J. 62, 778–791. doi:10.1002/aic.15107
Zhu, J. Q., Zong, Q. J., Li, W. C., Chai, M. Z., Xu, T., Liu, H., et al. (2020). Temperature profiled simultaneous saccharification and co-fermentation of corn stover increases ethanol production at high solid loading. Energy Convers. Manag. 205, 112344. doi:10.1016/j.enconman.2019.112344
Zhu, S., Wu, Y., Chen, Q., Yu, Z., Wang, C., Jin, S., et al. (2006). Dissolution of cellulose with ionic liquids and its application: a mini-review. Green Chem. 8, 325–327. doi:10.1039/b601395c
Keywords: biomass, sugars, pyrolysis, solvent liquefaction, hydrolysis, levoglucosan
Citation: Brown J, Lindstrom JK, Ghosh A, Rollag SA and Brown RC (2024) Production of sugars from lignocellulosic biomass via biochemical and thermochemical routes. Front. Energy Res. 12:1347373. doi: 10.3389/fenrg.2024.1347373
Received: 30 November 2023; Accepted: 26 January 2024;
Published: 19 February 2024.
Edited by:
Sasha Yang, Monash University, AustraliaReviewed by:
Claudia Prestigiacomo, University of Palermo, ItalySuan Shi, China Agricultural University, China
Copyright © 2024 Brown, Lindstrom, Ghosh, Rollag and Brown. This is an open-access article distributed under the terms of the Creative Commons Attribution License (CC BY). The use, distribution or reproduction in other forums is permitted, provided the original author(s) and the copyright owner(s) are credited and that the original publication in this journal is cited, in accordance with accepted academic practice. No use, distribution or reproduction is permitted which does not comply with these terms.
*Correspondence: Robert C. Brown, cmNicm93bjNAaWFzdGF0ZS5lZHU=