- Department of Chemical Engineering, Delft University of Technology, Delft, Netherlands
Process Intensification (PI) is an effective way to enhance process efficiency and sustainability at affordable costs and efforts, attracting particular interest in the European area, as one of the most important chemical production areas in the world. PI primarily contributes by developing and testing new processing technologies that once integrated within a process improve the overall process performance substantially but as a result, it may alter the overall process (flowsheet) structure and its dynamic behavior. As such PI plays a key role in improving energy efficiency, optimizing resource allocation, and reducing environmental impact of industrial processes, and thereby leading to a cost-effective, eco-efficient, low-carbon and sustainable industry. However, along with opportunities, the PI new technologies have challenges related to failures in longer-term performance. In this respect, Process Systems Engineering (PSE) stance is more on integration aspects of new PI technologies into processes by making process (re)designs, doing operability studies, and performance optimizations within a supply chain setting. PSE contributes to overcoming the challenges by providing systematic approaches for the design and optimization of PI technologies. This perspective paper is a lightly referenced scholarly opinion piece about the status and directions of process intensification field from a PSE viewpoint. Primarily, it focuses on PSE perspectives towards sustainable lower energy usage process systems and provides a brief overview of the current situation in Europe. It also emphasizes the key challenges and opportunities for (new) PI technologies considering their integration in a process in terms of process synthesis and design, process flowsheet optimization, process and plantwide control, (green) electrification, sustainability improvements. Potential research directions on these aspects are given from an industrial and academic perspective of the authors.
1 Introduction
Process Intensification is commonly defined as improvements of a process at unit operational, functional and/or phenomena levels that can be obtained by integration of unit operations, integration of functions and phenomena’s or targeted enhancement of the phenomena for a set of target operations (Lutze et al., 2013; Baldea, 2015). PI uses a set of innovative techniques in process engineering, integration and equipment design to offer breakthrough solutions for making chemical processes cost-effective, energy efficient, more controllable and safer, having smaller processing volume and smaller environmental footprint (Ponce-Ortega et al., 2012; Keil, 2018; Demirel et al., 2019; Sitter et al., 2019). PI helps chemical engineers to achieve more (higher performance and eco-efficiency) with less or smaller equipment and lower (fossil) energy use. Due to the more effective use of physical and monetary resources, PI helps reducing waste of mass and energy, while maintaining good operability and annual up-time of the process, thus reducing manufacturing costs.
Overall, the PI techniques can be grouped into four main categories: advanced separation, enhanced reaction, hybrid reaction/separation, and alternative energy sources (Tian et al., 2018). Among the energy intensive operations, distillation alone is responsible for about 40% of the fossil-derived energy used in the chemical industry and the associated CO2 emissions (∼2 billion metric tons CO2 emissions in the chemical industry, accounting for about 5% of global greenhouse gas emissions). However, due to its flexibility and simplicity, it remains the leading and most frequently adopted technique for the separation and purification of condensable mixtures in numerous industries (Kiss and Smith, 2020). There are several PI technologies proposed for improving distillation, such as dividing wall columns, reactive distillation, catalytic cyclic distillation, and many others (Kiss, 2013). However, these PI techniques are at different stages of being industrialized causing a limited adoption of these methods. For example, the introduction of applying new PI concepts or methodologies could meet resistance due to concerns about uncertainty associated with reliability, long-term performance, safety, and cost. Moreover, Europe’s dependence on imported resources (e.g., liquefied natural gas) adds to the complexity; and the stringent environmental and safety regulations in Europe further complicate the implementation of PI techniques in the region.
Process systems engineering (PSE) deals with decision-making at multiple scales and levels, aiming for optimum use of (renewable) natural and societal resources, sharing a considerable overlap of objectives with PI (Moulijn et al., 2008; Babi et al., 2016). The symbiosis of PSE and PI at various scales (see Figure 1) provided great benefits for the European chemical industries in the past few decades. For example, from 1990 to 2015 the energy intensity in the EU chemical industry fell by 60%, which is more than the 39% cuts achieved in the manufacturing industry as a whole, during the same period (Chemie Techniek, 2017; CEFIC, 2023), showing the ongoing advantages of PI. Over the next decades, the process industry will develop towards saving on the use of fossil energy by heat integration and PI technologies, and a gradual substitution of fossil derived energy for processes by electric power from renewable sources (which currently stands at about 25% of the total European primary energy demand). That energy transition will take decades by the sheer extent of the energy streams and of the required engineering efforts to revamp the energy supply systems for process plants. In view of more dynamic supply and demand patterns for renewable power, process plants should be adapted to more frequent dynamic modes of operation and energy storage.
As shown in Figure 2, Europe is hosting some of the most important centers for chemical engineering for both production and research. The European area is a strong chemical cluster, being the second largest chemical producer in the world, the second largest chemical exporter; and the third largest fossil energy importer (Gladkykh, 2015; Popp et al., 2021; CEFIC, 2023). However, the chemical industries in Europe are also facing challenges. Most of the European resource suppliers and product markets are outside Europe, which means that the European industries need more energy efficient and cost-effective processes. This is especially needed considering the loss of competitiveness because of the long-distance transportation in terms of expenses, regulations and safety issues. In addition, because of the current energy crisis, some gas-intensive manufacturing plants in Europe (in which renewable energy is not yet fully deployed to substitute fossils) have been forced to reduce all or part of their production (International Energy Agency, 2023). Therefore, for Europe to remain an attractive chemical production area, PI is now more important than ever, being of great importance and special interest to provide breakthrough techniques in order to improve energy efficiency, optimize resource allocation, upgrade product quality, and reduce the environmental footprint of the chemical processes (Babi et al., 2016). Clearly, PI plays an important role in the European process industry as a means to keep this sector viable and competitive globally.
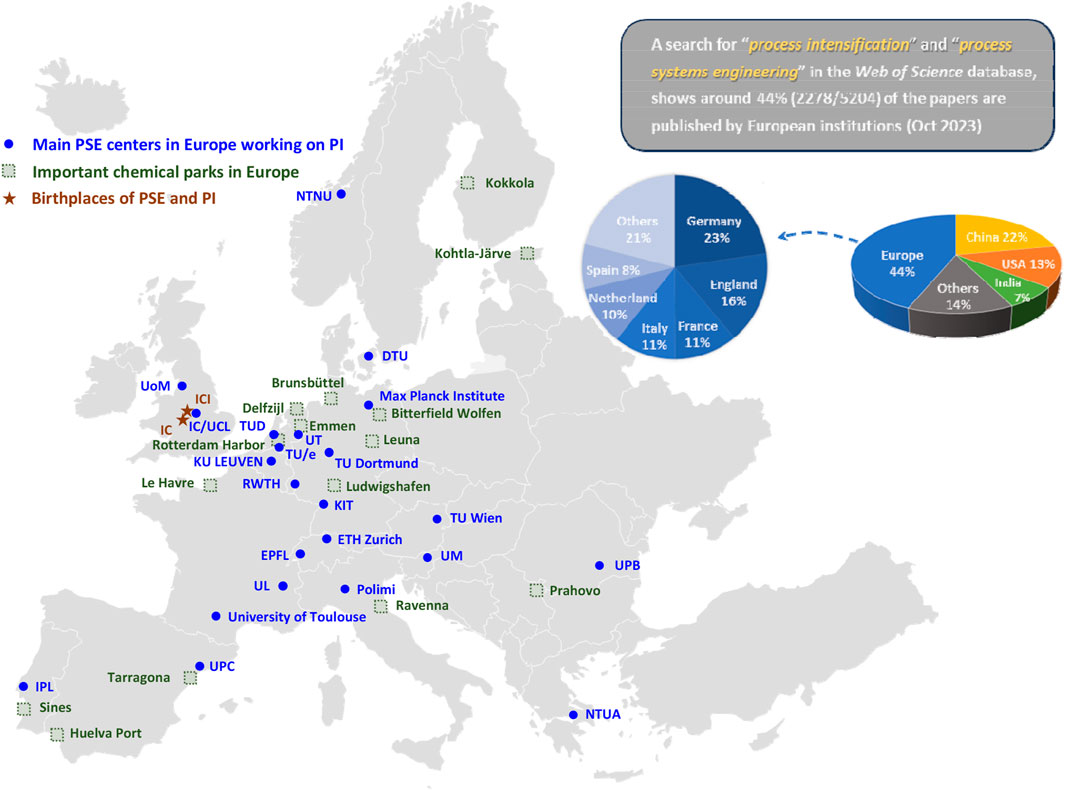
FIGURE 2. Chemical engineering, PSE and process intensification centers in Europe. This list is not extensive, but it is based on a Web of Science search and other data from www.chemicalparks.eu. Abbreviations (in alphabetical order): DTU, Technical University of Denmark; EPFL, Swiss Federal Institute of Technology in Lausanne; ETH Zurich, Federal Institute of Technology Zurich; IC, Imperial College London; ICI, Imperial Chemical Industries; IPL, Polytechnical Institute of Lisbon; KIT, Helmholtz Association, Karlsruhe Institute of Technology; KU LEUVEN, Catholic University of Leuven; Max Planck Institute, Max Planck Institute for Dynamics of Complex Technical Systems Magdeburg; NTUA, National Technical University of Athens; NTNU, Norwegian University of Science and Technology; Polimi, Polytechnic University of Milan; RWTH, RWTH Aachen University; TUD, Delft University of Technology; TU Dortmund, Dortmund University of Technology; TU/e, Eindhoven University of Technology; TU Wien, University of Vienna; UCL, University College London; UL, The University of Lorraine; UM, The University of Maribor; UoM, University of Manchester; UPC, The Technical University of Catalonia; UPB, Politehnica University of Bucharest; UT, University of Twente.
The practical focus of PSE is on multi-scale integration of processing methods for optimal functional performance of chemical manufacturing processes in a (sustainable) supply chain stetting, while absorbing suitable PI methods within that setting. The latter creates new opportunities along with risks related to failures in longer-term performance of new technologies. In this respect, the primary challenges to the long-term performance of new PI technologies are: a proper scale-up from lab test situations to plant conditions, and ability to cope with varying operational situations. The latter involve resiliency with respect to fluctuations in feed stream conditions, handling throughput changes, start-up and shut down, fouling, mechanical tear and wear that affect plant availability, and policies for maintenance. PSE can perform model-based process simulations to test PI performance for a variety of operational scenarios, it can optimize the connections of new PI technologies within the entire process and find optimum processing conditions within PI units. In addition, PSE methods can estimate the impact of PI technologies on overall process performances (e.g., economic metrics, external energy usage, wastes and emissions, HSE, plant availability).
This raises a number of questions relevant to PSE, such as: How to overcome or smoothen the resistances to the development and application of PI technologies, being novel and hence yet unproven in practical operations? Which additional demands should be placed to the delivery of applicable PI technologies? Having high mass and energy efficiencies with low investment costs is essential, but is it enough? Moreover, operability aspects (e.g., acceptable operating window, stability, responsiveness to changes in conditions, flexibility) matter a lot (Tian et al., 2019). Ideally, the operability should be tested as a part of PI technology development as well. This could also include failure rate curves of PI technologies to be used as part of RAM (Reliability, Availability and Maintainability) models to assess the resulting probabilities of failure of designs.
This perspective paper - invited for this special issue of Frontiers in Energy Research - is motivated by the current needs for process intensification in the European chemical industries, aiming to identify research challenges but also corresponding opportunities from the perspective of PSE. In this context, PSE can contribute to overcoming the challenges by providing systematic approaches for the design, control and optimization of PI technologies within a (reconfigured) process, covering the directions of PI in process synthesis and design, process optimization, (green) electrification and sustainability. The future PI research directions are then summarized through an industrial and academic PSE perspective.
Within the frame of fossil-based process industries much has already been achieved in terms of synergy between PI and PSE. Yet, in the next decade major steps have to be made in using renewable physical and chemical resources, leading to circular sustainable production systems (El-Halwagi, 2017; Mhatre et al., 2021; Schutzbach et al., 2021). The European Chemical Industry Council stresses the importance of sustainable development beyond energy (CEFIC, 2021), highlighting some critical areas to progress sustainable development: enabling transition to a low carbon economy; driving resource efficiency across global value chains and operations; promoting the adoption of circular economy principles to prevent waste, achieve low-carbon economy and enhance resource efficiency; and preventing harm to humans and the environment throughout the entire life cycle. In this context, there is a strong link between sustainable development and PI and PSE, where the synergy between PI and PSE plays a major role. This shows the wide industrial importance of having PI technologies within a PSE setting for process improvements, and also that a revamp of the entire European process industry is required.
A generic higher level view on circular sustainable production systems (having recycles of material resources recovered from spent products and renewable energy sources) will impose additional performance criteria and constraints beyond economics on the designs of each of the four generic processes: 1) manufacturing processes for product components; 2) product synthesis and application processes; 3) materials recovery processes from spent products; and 4) material transport chains, connecting the previous three processes (Groover, 2012). Treating the fully circular production systems in an integrated way is still beyond our current conceptual, modeling and computing capabilities. Therefore, decompositions are required to cover the design and operation of each process individually. One such decomposition is: 1) to minimize the use and loss of fossil resources per process; 2) to reduce the manufacturing costs per process up to the point where a further reduction would be off-set by increases in the costs of the other processes in the cycle. Therefore, it is necessary to apply PSE tools in order to systematically design and optimize PI technologies, within the frame of the manufacturing process under design (Avraamidou et al., 2020). As optimization format is a strong feature of the PSE approach, it would be helpful if models of PI techniques are developed in an open equation format for easy insertion in an optimization frame.
Notably, the focus of this brief overview and perspective is exclusively on manufacturing processes; less so on product application processes or waste product recovery processes to extract material feeds for recycling. This focus is practically relevant, as it is fair to assume that the main costs and energy usage in manufacturing processes are much higher than in product application processes (Mickovic and Wouters, 2020). At this point in time, feed recovery processes are still in early stages of development (e.g., CO2 capture to generate syngas as feed stock for the manufacture of methanol and aliphatic synfuels). Moreover, recovery processes have the same chemical engineering characteristics as the regular chemical manufacturing processes. Therefore they can conceptually be combined from the viewpoint of application of PI technologies.
2 Challenges and opportunities of process intensification techniques
The following sub-sections of this part describe the key challenges in intensified process systems and the PSE opportunities associated to them. Most of the references cited are from European centers (see Figure 2) that work on both PI and PSE related topics, such as: AkzoNobel (Kiss et al., 2012), DTU (Babi et al., 2016; Nielsen et al., 2016; Garg et al., 2020), KIT (Mickovic and Wouters, 2020), KU Leuven (Stankiewicz et al., 2019), Max Planck Institute (Sundmacher et al., 2005), RWTH Aachen (Sitter et al., 2019), TU Delft (Nikacevic et al., 2012; Li et al., 2023), TU/e (Bongers, 2009), TU Dortmund (Lutze, 2015; Skiborowski, 2018), UCL (Kooijman and Sorensen, 2022), University of Lorraine (Commenge and Falk, 2014), University of Manchester (Kiss and Smith, 2020), University of Salamanca (Ramírez-Márquez et al., 2023), University of Stuttgart (Schutzbach et al., 2021), and University of Twente (Fernandez Rivas, 2018). Note that due to space limitations the examples are restricted mostly to energy intensive separations which account for the largest costs in the industry.
2.1 Selection and integration of PI in process synthesis and design
A generic structure of processes for (composite) chemical products involves four main operations: (a) purifications of feed streams; (b) chemical conversions of feeds to products; (c) separations for recovery of unconverted feeds and purification of products; (d) product formulations/synthesis of structured products (Bongers, 2009). In this sequence of operations, the synthesis and design of multicomponent mixtures separation by distillation sequences is often the more complex one, also involving significant economic costs. The complexity is due to many interconnected design degrees of freedom. Within the synthesis and design, advanced distillation techniques based on PI principles are considered highly competitive in terms of enhancing energy efficiency and economic performance (both operational costs and capital costs). It is expected that the intensified opportunities can be discovered and also evaluated at the process synthesis and design stage, even with limited data (Lutze, 2015; Fernandez Rivas, 2018; Skiborowski, 2018; Garg et al., 2020). However, the guiding principles behind PI technologies must be clear to match a technology with an application (i.e., assigned processing tasks and processing conditions related to an application). This match is very vital, and it defines the potential success of PI technologies in a process. For example, in case of fluid separations, matching suitable intensified distillation techniques—such as heat integrated distillation, membrane or heat pump assisted distillation, high gravity distillation, cyclic distillation, thermally coupled systems, dividing wall column, extractive and azeotropic distillation—with given separation tasks based on a wide range of application cases (e.g., a variety of mixtures, a wide range of feed flowrates and concentrations, and different products purities) remains a crucial challenge.
An opportunity to overcome this challenge is to develop a knowledge-based PI matrix, which could provide a list of the most promising intensified techniques for given separation tasks. Commenge and Falk (2014) developed a matrix for choice of intensified reaction equipment by identifying the process limitation, producing intensification strategies and finding promising PI techniques for reaction systems. As for separation systems, a PI matrix could be developed to match these parameters with promising intensified distillation techniques, by identifying the volatile difference between key components, the type of separation tasks, feed and product flow, product specifications at different target purity levels, operating pressure, reboiler duty and its temperature level, Carnot efficiency, process bottlenecks (e.g., remixing effect), etc. The PI technologies can be scored and compared, and then the potential solutions based on the task specifications can be suggested and economically assessed according to the score (Li et al., 2024). This could potentially be applied to pseudo-binary and pseudo-ternary mixtures separation in order to make a rapid selection at an early stage, for both ideal and non-ideal separation systems, and it can reduce the search space before carrying out optimization for the synthesis and design of the separation systems.
Other potential research directions include the use the generic model-based methods for the synthesis of process flowsheets for the synthesis of new PI units, by using the physical and chemical phenomena as building blocks to create a network of interacting phenomena meeting a functional goal (Arizmendi-Sánchez and Sharratt, 2008; Babi et al., 2015; Skiborowski, 2018); as well as the developments of multi-scale models covering the entire chemical process while allowing to zoom in at smaller scales (with finer level of details) in PI units.
2.2 Inclusion of PI technologies in process flowsheet optimization
The next step would be to optimize the whole process flowsheet (e.g. after using the PI matrix to reduce the search space), by carrying out optimization and design as a whole systematically, including process intensification methods (Kiss and Smith, 2020). Optimizing a flowsheet requires the choice of a proper objective function along with the (inequality) constraints defining the space of feasible processing conditions for the PI technology to be functionally included. Identifying the relevant operational limits to a PI technology in retrospect is not an easy task when this has not been done as a part of the PI development effort. Knowing the boundaries matters, thus it is important to carry out process intensification developments with PSE aspects in mind. We also need to emphasize the usefulness of the (multi-objective) optimization format (e.g., one or more objectives, equalities and inequalities and degrees of freedom) for stating design problems, with an additional benefit of getting for free sensitivity information of the objective function(s) with respect to the active constraints as part of the optimization output (Rangaiah et al., 2020).
A key challenge in case of separation systems is the process synthesis which must determine the basic separation configuration, including the intensified thermally coupled complex columns, column pressures, reflux ratios, feed conditions, condenser types and heat integration arrangements all simultaneously, and these design variables interconnected with each other. To overcome this challenge, a screening algorithm was recently developed using short-cut distillation models to screen the large number of structural options and determine the best few potential designs, followed by more detailed examination of these designs using rigorous simulation (Li et al., 2023). An optimization of a superstructure for the sequence synthesis using short cut models, in conjunction with a transportation algorithm via an incidence matrix for the synthesis of the heat integration arrangement were developed (Li et al., 2023). The best few designs in terms of total operating cost from the screening are evaluated using rigorous simulations. This method has been applied to an industrial scale case study for natural gas liquids (NGLs) fractionation. The most promising intensified processes can be proposed, showing the difference between the thermally coupled complex columns and the corresponding non-heat-integrated simple column designs. Remarkably, once heat integration is included, the difference between designs using complex columns and simple columns narrows significantly. Such an approach provides opportunities to include in the optimization other promising PI techniques, such as cyclic distillation, or PI using other energy forms (e.g., ultrasound, microwave) which are not included in typical studies, as there is a lack of models to integrate these PI techniques into the optimization at this stage.
A key direction for further PSE research on including PI in process flowsheet optimization is to consider inter-/intra-units heat integration (Li et al., 2023), heat pumping to upgrade the energy level (Jana, 2014), interaction of PI units in reaction-separation-recycle systems (Sundmacher et al., 2005), and developments of computer-aided PI methods and tools (Tula et al., 2019).
Notably, the process synthesis and design, flowsheet optimization, process and plantwide control in PSE are virtually all model based for industrial scale plants. Being model based presents an opportunity for testing novel process configurations and operating modes in silico (rather than building pilot plants). However, this feat implies that any new PI technology should have reliable models applicable over the entire envisaged operating window. That expectation puts demands on the development and validation of models of PI technologies, often being tested on a lab scale. A PI model should be able cover the entire envisioned range of operating conditions in static and dynamic modes. Furthermore, all model parameters should be properly identified from available experimental data (or from data generated by a more rigorous model). Also, limitations to model applications should be made explicit. Any model should be accompanied by a set of (inequality) constraints representing the boundaries of the domain of applicability of a model. These are needed in optimization applications of a PI model as to avoid excursions into uncharted domains.
2.3 Effective process unit and plantwide control of PI based processes
There are several key factors affecting the operability of PI based processes (e.g., degrees of freedom; process constraints; numbering-up/scale-out vs scaling up, and dynamic operation) and metrics to address PI control challenges, such as: flexibility analysis, operability-based design, and advanced model-based control (Pistikopoulos et al., 2021). Since PI leads to novel but complex systems, it is rather necessary to rely on appropriate optimization and control techniques that can cope with such new processes (Alcántara Avila et al., 2021). The more intensified and integrated a process is, fewer degrees of freedom are available and thus more challenging the process control. Yet, process control can enable safe, economical, and environmentally optimal performance of PI based processes. Also, the process control ability to maintain product consistency and reducing the statistical spread of product properties can be considered as additional benefits of PI. Advanced process control techniques do achieve these goals and therefore also contribute to PI goals, though without being traditionally reckoned to the PI domain. There are two PI aspects to process control. 1) Local control of a PI technology (such as reactive distillation or dividing-wall column)—keeping the processing conditions in a PI application at the desired setpoints (Dias et al., 2019). 2) Plantwide control—having proper control over the entire process plant reduces the effects of disturbances on process outputs enhancing consistency of product quality (Nikacevic et al., 2012). A well-chosen control scheme may also demand less vigorous control actions and thus reduces the consumptions and costs of cooling water, heating oil, power for compressors, etc. As a side remark, the control system itself and real-time optimization systems can be also considered digital means to achieving PI (delivering more for less cost). Future research opportunities include the development of holistic strategies for integrated design, operability, and control of intensified process systems (Pistikopoulos et al., 2021).
As process design, control and optimization should be carried out together there is a clear need and opportunity for developing reliable and rapidly solvable PI models. Common sense requirements demand that such a PI model: 1) is based on an explicitly stated set of assumptions about relevant physical and chemical behavior giving a model its physical basis and establishing its mathematical structure; 2) is able to cover the entire envisioned range of operating conditions in static and dynamic modes; 3) has a correct digital implementation (as asserted by model verification); 4) has properly identified parameters from available experimental data (or from computational data generated by a more refined model at more detailed scales) along with statistical uncertainty information on these parameters (e.g., covariance matrices of parameter estimates); 5) has been validated by means of independent empirical/experimental data; 6) has an explicit domain of applicability for simulations and optimizations (e.g., a set of constraints representing the boundaries of the domain of applicability within an optimization setting).
2.4 Development of PI techniques powered by (green) electrification
PI techniques related to electrification will play a key role in the near future for heat and power supply and to reduce our dependence on fossil fuels while reducing greenhouse gas emissions. Electricity can be generated by renewable sources, including solar, wind, geothermal, biomass, etc., and electricity can be used to directly generate heat (e.g., electric boiler) or indirectly upgrade energy level by means of heat pumps (Nielsen et al., 2016). However, there are many challenges associated to using green electricity, e.g.,: relatively high cost, intermittent availability, requirements for large amounts, competition with different sectors, cost of power electronics installations, etc.
2.4.1 Direct electric heating
In terms of direct heating, electric (re)boilers can be used to electrify heat demands in distillation (Kooijman and Sorensen, 2022). They can be used to convert renewable power to high-level heat. However, green electricity sources, such as wind and solar energy, are usually supplied under non-steady-state conditions, while industrial energy demands typically occur under steady-state conditions (Mitali et al., 2022). Therefore, the energy storage technologies (e.g., electricity, chemical medium, pressure, water level, cold and heat mediums, etc.), methods and equipment, along with their combinations are crucial for practical applications. PI techniques can possibly integrate the non-steady-state electricity resources with the steady-state energy that is required by industry. In addition, renewable electricity generation, electricity storage (also under non-electric forms), energy conversion, energy combination modes, consumer demands represent challenges to be addressed.
2.4.2 Heat pump-assisted processes
Heat pumps allow the upgrading of a heat source from a lower-temperature level to a higher-temperature level mostly using electricity, typically applied as closed cycles or absorption cycles in energy intensive processes (e.g., vapor compression, mechanical/thermal vapor recompression, absorption heat pump, compression-resorption heat pump, thermos-acoustic heat pump and internally heat integrated distillation column (Kiss and Infante-Ferreira, 2016). Due to their higher coefficient of performance, heat pumps offer a more energy-efficient alternative to conventional heating and cooling systems through creating extra heat recovery opportunities (and providing renewable heat), thereby finding applications across a wide field of engineering sectors. In addition to the direct heat integration between distillation columns, indirect heat integration via heat pump, powered by electricity can be particularly beneficial in complex, multi-stage distillation sequences, where energy costs contribute a significant part of the operating cost (Jankovic et al., 2023).
Integrating heat pump selection into separation system design could lead to more energy savings by taking advantage of the extra degrees of freedom. In the energy-intensive distillation processes, the integration of heat pump technology has drawn significant attention for its potential for energy savings and sustainability improvements (Kiss et al., 2012; Jana, 2014). Conventional distillation systems suffer from the limitation of depending on a fossil fuel-based steam network or heaters to provide energy input, causing negative impacts on environment. Additionally, the heat recovery opportunities are limited by the existing heat transfer driving force, i.e., the temperature difference between reboiler and condenser, which reduces the overall energy efficiency for distillation system. Heat pumps make use of an electricity source and introduce work into the system to increase the temperature level (thermal energy at useful level) or the dew-point of the steam. By exploiting the latent heat of condensation from the top product to provide the requisite thermal energy for the reboiler, heat pumps effectively enhance the energy efficiency of the distillation unit. This integration results in reduced energy expenditure, thereby leading to lower operating costs and a reduced carbon footprint. However, systematically optimizing different heat pump types in distillation sequences remains very challenging due to various operating constrains in both components (heat pump and process), which must be optimally integrated in a system. Moreover, there is a large range of heat pump (HP) types for industrial applications—such as: compression HP, trans-critical HP, absorption or adsorption HP, heat transformers, hybrid HP, and solid-state HP—and a proper selection must be made for a good match with the process (Kiss and Infante-Ferreira, 2016). Opportunities include the development of high temperature heat pumps, new working fluids or mixtures, or hybrid heat-pumps which allow higher temperature lifts and levels.
2.4.3 Electrochemical conversion
Significant efforts are dedicated nowadays to the development of the electrochemical reduction of CO2 (ECO2R)—such as the e-Refinery project at TU Delft—but still many challenges are present, hindering further approaches to industrial applications (Guerra et al., 2023; Mallapragada et al., 2023). The challenges include the coupling of such processes with intermittent generation of renewable electricity, the feedstock and the processes itself, as well the different products obtainable. PSE can determine the optimal interactions among the system components, allowing informed, model-based decision making in designing the best intensified process under uncertainty and constraints. On the other hand, the opportunities stem from the collaboration between the PSE and the PI experimental communities, from the possibility of integrating ECO2R into existing industrial productions and from process-wide optimization studies, encompassing the whole production cycle of the chemicals to exploit possible synergies (Dal Mas et al., 2024).
2.5 Improving sustainability by PI techniques
The diversification in raw material supply, energy supply, involved unit operations, routes, products, would make the production processes and the price/cost system for economic and sustainability assessment more and more complicated, and thereupon the number of optimization variables is sharply increased. This diversification may also add to the non-convexity of the non-linear process model which is the main hindrance, so that the estimation of PI performance is more difficult. In this instance, the big data processing and machine learning means might be the effective methods to consolidate PI techniques and investigation. However, getting sufficiently reliable (big) data for this purpose is challenging, as the set of experimental data often span only a sub-space in the full space of output variables. The remainder of the output space must be evenly covered with data as well to get to a reliable big data model. Any additional output data likely has to come from simulations using rigorous models of the PI technologies included in the process design.
PI technologies can usually ensure a balance between economic growth and environmental care, and therefore have an inherent connection with process sustainability (Ramírez-Márquez et al., 2023). In addition to meeting sustainability standards through an intensified process, the sustainability of the designs can also be assessed with the help of PSE tools by mathematical optimization from the early stage of process synthesis. The sustainability of conventional or intensified processes can be both evaluated and quantified via sustainability metrics, such as (fossil) energy intensity, material intensity, water consumption, CO2 emissions, toxicity and emissions of pollutants. Several fluid separation cases are provided as examples in which PI contributes to process sustainability (Ramírez-Márquez et al., 2023). By applying intensified membrane assisted low-temperature absorption techniques, low-grade raw materials and energy resources can now be utilized. For example, the upgrading cost of unconventional natural gas resources (e.g., carbon-rich gas or nitrogen-rich gas) can be reduced, and even poor-quality gas sources have the potential to be competitive in the market. For biomass (biomethane) conversion processes, fragmented gas sources can be processed and utilized by applying PI techniques (e.g., membrane assisted chemical absorption), as the required equipment is much smaller, and there is no need of a large farm (due to the previous large capacity of the plant), so that biomass conversion can be applied on a smaller scale and more widespread by intensified separation technologies.
PI can also reduce the temperature of the chemical process, e.g., increasing reaction rate by in situ products removal rather than increasing temperature (Stankiewicz et al., 2019), so that the low-grade energy, such as geothermal heat or upgrades waste heat, could be potentially used directly for chemical plant heating. In addition, solar collectors or integration with solar power generation systems can be a new source of heat for the chemical industry to enhance process sustainability.
As a means to reduce process toxicity, PI techniques (e.g., by tailor-made catalysts) could help decrease the amount of by-products which are usually regarded as pollutants and toxic matters by increasing the reaction selectivity (Stankiewicz et al., 2019). In addition, PI can be used to connect scales for sustainability (Boffito and Fernandez Rivas, 2020), integrate separation and reaction units and develop near-zero-emission sewage treatment and waste gas treatment processes and plants.
A recent paper (Castillo-Landero et al., 2019) proposed a methodology for the design of intensified processes that addresses economic, sustainability, and inherent safety. It starts with a base design of the process which goes through a gradual intensification procedure (which evaluates the economics, sustainability and inherent safety metrics at each step) until a fully intensified design is obtained. An opportunity exists to extend this approach to other processes (e.g. plastic upcycle, CO2 valorisation).
3 Conclusion
The future PI and PSE research directions can be summarized with the following concluding remarks:
• Currently there is a flow of emerging PI technologies to be accommodated by PSE in process integration and optimization. However, PSE requires these deliveries of new PI technologies to satisfy formats and conditions that makes it accessible to PSE approaches and useable for basic process synthesis, design, control, and optimization. A dialog between PI and PSE specialists is required in order to take PI techniques further into process systems development, e.g., what information is needed to allow PSE experts to perform their tasks in process design, control, and operations; or what are the up-front essential restrictions on a PI technology to fitting into existing chemical processes. System integration may pose some constraints that are not so obvious from a fundamental principles perspective, thus the info exchanges needs to involve performance data, models, operational procedures, safety aspects, etc.
• Process intensification techniques are useful for PSE activities (e.g., process design, control, optimization, and integration) but only if they come with well-tested behavioral models, applicable over a fair range of operation conditions, and knowing the boundaries. Thus, developing such behavioral models is of crucial importance for the uptake of PI techniques into PSE developments. Having well-tested behavioural models allow testing novel process configurations and operating modes in silico (instead of building pilot plants) and properly integrating PI techniques into PSE activities (process synthesis and design, process flowsheet optimization, process and plantwide control).
• There is a lack of readily useable models available for PI technologies (e.g., cyclic distillation, HiGee separations, processing using alternative energy forms). For this reason, including PI technologies in process synthesis remains very challenging, as one needs to consider the interactions between various traditional and PI units, and possible synergistic enhancements. Thus, developing PI models that are useable in or along existing process simulators is a must. For instance, the inclusion of a new PI unit in a process replacing a few existing units by integrating processing functions potentially affects the operational features of the revised process plant. Due to the higher degree of integration in PI units, one must investigate the stability, controllability and reliability of the changed process. If readily useable models for that purpose are lacking, the threshold for applying PI methods rises due to risk awareness.
• Heat pump assisted distillation can achieve energy savings by taking advantage of upgrading heat levels, especially for close boiling point separation systems. Yet, it remains challenging to systematically optimize different heat pump types in distillation sequences due to the many design degrees of freedom. Developing models that can integrate the heat pump cycles with the process systems at an early design stage is a valuable direction towards renewable heat. An early integration of the heat pump cycles with process systems allows an optimal design of both system components (instead of a more restricted retrofit at a later stage) taking into account at an early stage any potential safety issues (e.g., introducing new working fluids in a chemical process) or dynamic operation (e.g., start-up and shut-down procedures).
• The method most often used to develop alternative chemical processes and plants are based on engineering experience and understanding of the special unit operations. In this instance, reliable and also rapidly solvable models for these special unit operations based on the same simulation platform are eagerly demanded for PI investigation. Applying any new technology in a process plant always carries risks of (partial) failures, so it is essential to assess the control and operability aspects, along with optimizing the economic and sustainability metrics in PI process designs. The risks may entail loss of safety, accidents or adverse health effects, unwanted emissions, unsatisfactory technical performance due to internal deficiencies, and/or poor interactions with the remainder of the process. Reliable and rapidly solvable models of the new PI technology are required as many simulations and optimizations need to be carried out for assessment studies.
• It is imperative to include sustainability metrics into the evaluation methods for various PI alternatives as an index for decision making, techno-economic analysis and environmental life cycle assessment based on green chemistry principles. However, it remains conceptually challenging to formulate a composite single sustainability index that meaningfully covers multiple sustainability metrics and is also user friendly and easy to understand for non-experts in this specific area. Nonetheless, having a single metric would be helpful to decision making, rather than having several metrics inducing a need for making trade-offs.
Finally, a distinction is required with respect to working processes and outputs between academia and industry. Academic works commonly focus on the delivery of concepts, data, methods, models, and computational tools for an engineering artifact. In practical engineering circles in industrial companies, such data, models and tools will be eagerly used, while their industrial development focus is more on creating smooth work processes that reduce the chances on making errors in engineering applications, speed-up the work and reduce engineering cost. Such work processes are imbedded in a local organization culture of a company and therefore less generic than models and computing tools, but equally important to the industrial success of PI and PSE applications. In both PI and PSE fields there is some similarity in work processes and in use of tools, although the outcomes/results are different due to having different knowledge generation goals. Both aspects (i.e., working processes and outputs) are important for the industrial success as one without another is unfeasible. For example, having very inefficient work processes (yet with excellent outputs) can still kill PI applications by inflicting a too high cost of the work processes. Conversely, very cost-efficient work processes may induce short-cuts leading to deficiencies in the outputs, thus causing potential failures of PI applications due to errors (Kiss and Grievink, 2020).
Data availability statement
The raw data supporting the conclusion of this article will be made available by the authors, without undue reservation.
Author contributions
QL: Conceptualization, Formal Analysis, Methodology, Validation, Visualization, Writing–original draft, Writing–review and editing. AS-T: Formal Analysis, Methodology, Validation, Visualization, Writing–review and editing. JG: Conceptualization, Formal Analysis, Methodology, Validation, Writing–review and editing. AK: Conceptualization, Methodology, Formal Analysis, Resources, Validation, Visualization, Supervision, Project administration, Writing–original draft, Writing–review and editing.
Funding
The author(s) declare that no financial support was received for the research, authorship, and/or publication of this article.
Conflict of interest
The authors declare that the research was conducted in the absence of any commercial or financial relationships that could be construed as a potential conflict of interest.
Publisher’s note
All claims expressed in this article are solely those of the authors and do not necessarily represent those of their affiliated organizations, or those of the publisher, the editors and the reviewers. Any product that may be evaluated in this article, or claim that may be made by its manufacturer, is not guaranteed or endorsed by the publisher.
References
Alcántara Avila, J. R., Kong, Z. Y., Lee, H.-Y., and Sunarso, J. (2021). Advancements in optimization and control techniques for intensifying processes. Processes 9 (12), 2150. doi:10.3390/pr9122150
Arizmendi-Sánchez, J. A., and Sharratt, P. N. (2008). Phenomena-based modularisation of chemical process models to approach intensive options. Chem. Eng. J. 135 (1-2), 83–94. doi:10.1016/j.cej.2007.02.017
Avraamidou, S., Baratsas, S. G., Tian, Y., and Pistikopoulos, E. N. (2020). Circular economy - a challenge and an opportunity for process systems engineering. Comput. Chem. Eng. 133, 106629. doi:10.1016/j.compchemeng.2019.106629
Babi, D. K., Cruz, M. S., and Gani, R. (2016). “Fundamentals of process intensification: a process systems engineering view,” in Process intensification in chemical engineering. Editors J. Segovia-Hernández, and A. Bonilla-Petriciolet (Berlin, Germany: Springer).
Babi, D. K., Holtbruegge, J., Lutze, P., Gorak, A., Woodley, J. M., and Gani, R. (2015). Sustainable process synthesis-intensification. Comput. Chem. Eng. 81, 218–244. doi:10.1016/j.compchemeng.2015.04.030
Baldea, M. (2015). From process integration to process intensification. Comput. Chem. Eng. 81, 104–114. doi:10.1016/j.compchemeng.2015.03.011
Boffito, D. C., and Fernandez Rivas, D. (2020). Process intensification connects scales and disciplines towards sustainability. Can. J. Chem. Eng. 98 (12), 2489–2506. doi:10.1002/cjce.23871
Bongers, P. M. M. (2009). Intertwine product and process design. Eindhoven University of Technology. Eindhoven, Netherlands, URL: https://pure.tue.nl/ws/files/3179758/Bongers2009.pdf.
Castillo-Landero, A., Ortiz-Espinoza, A. P., and Jiménez-Gutiérrez, A. (2019). A process intensification methodology including economic, sustainability, and safety considerations. Industrial Eng. Chem. Res. 58 (15), 6080–6092. doi:10.1021/acs.iecr.8b04146
CEFIC (2021). Sustainability and innovation. https://cefic.org/a-solution-provider-for-sustainability, (accessed 8.July.21), https://cefic.org/app/uploads/2021/10/Sustainability_progress_update_2021.pdf.
CEFIC (2023). Facts and figures of the European chemical industry. URL https://cefic.org/a-pillar-of-the-european-economy/facts-and-figures-of-the-european-chemical-industry/. (accessed 4.March.23).
Chemie Techniek, (2017). Energy usage in Europe´s chemical industry. URL https://www.chemietechnik.de/markt/energy-usage-in-europes-chemical-industry.html. (accessed 6.May.23).
Commenge, J. M., and Falk, L. (2014). Methodological framework for choice of intensified equipment and development of innovative technologies. Chem. Eng. Process. Process Intensif. 84, 109–127. doi:10.1016/j.cep.2014.03.001
Dal Mas, R., Somoza-Tornos, A., Perez-Fortes, M., Kortlever, R., and Kiss, A. A. (2024). Challenges and opportunities for CO2 electroreduction from a process systems engineering perspective. Front. Energy Res. 11, 1340622, Article in press. doi:10.3389/fenrg.2024.1340622
Demirel, S. E., Li, J., and Faruque Hasan, M. M. (2019). Systematic process intensification. Curr. Opin. Chem. Eng. 25, 108–113. doi:10.1016/j.coche.2018.12.001
Dias, L. S., and Ierapetritou, M. G. (2019). Optimal operation and control of intensified processes - challenges and opportunities. Curr. Opin. Chem. Eng. 25, 82–86. doi:10.1016/j.coche.2018.12.008
El-Halwagi, M. M. (2017). Sustainable design through process integration: fundamentals and applications to industrial pollution prevention, resource conservation, and profitability enhancement. Butterworth-Heinemann.
Fernandez Rivas, D., Castro-Hernández, E., Villanueva Perales, A. L., and van der Meer, W. (2018). Evaluation method for process intensification alternatives. Chem. Eng. Process. - Process Intensif. 123, 221–232. doi:10.1016/j.cep.2017.08.013
Garg, N., Kontogeorgis, G. M., Gani, R., and Woodley, J. M. (2020). A process synthesis-intensification method for generation of novel and intensified solutions. Chem. Eng. Process. - Process Intensif. 156, 108103. doi:10.1016/j.cep.2020.108103
Gladkykh, D. (2015). European chemical industry competitiveness: historical trends and development prospects. Baltic J. Econ. Stud. 1 (1), 62–66. doi:10.30525/2256-0742/2015-1-1-62-66
Groover, M. P. (2012). Fundamentals of modern manufacturing: materials, processes, and systems. 5th. Hoboken, NJ, USA: John Wiley and Sons.
Guerra, O. J., Almajed, H. M., Smith, W. A., Somoza-Tornos, A., and Hodge, B. M. S. (2023). Barriers and opportunities for the deployment of CO2 electrolysis in net-zero emissions energy systems. Joule 7 (6), 1111–1133. doi:10.1016/j.joule.2023.05.002
International Energy Agency (2023). Global energy crisis. https://www.iea.org/topics/global-energy-crisis. (accessed 7.June.23).
Jana, A. K. (2014). Advances in heat pump assisted distillation column: a review. Energy Convers. Manag. 77, 287–297. doi:10.1016/j.enconman.2013.09.055
Jankovic, T., Straathof, A. J. J., and Kiss, A. A. (2023). Process systems engineering perspectives on eco-efficient downstream processing of volatile biochemicals from fermentation. Front. Energy Res. 11, 1340612. doi:10.3389/fenrg.2023.1340612
Kiss, A. A. (2013). Advanced distillation technologies – design, control and applications. Hoboken, NJ, USA: Wiley-Blackwell.
Kiss, A. A., Flores Landaeta, S. J., and Infante Ferreira, C. A. (2012). Towards energy efficient distillation technologies – making the right choice. Energy 47 (1), 531–542. doi:10.1016/j.energy.2012.09.038
Kiss, A. A., and Grievink, J. (2020). Process systems engineering developments in Europe from an industrial and academic perspective. Comput. Chem. Eng. 138, 106823. doi:10.1016/j.compchemeng.2020.106823
Kiss, A. A., and Infante Ferreira, C. A. (2016). Heat pumps in chemical process industry. Boca Raton, FL, USA: CRC Press.
Kiss, A. A., and Smith, R. (2020). Rethinking energy use in distillation processes for a more sustainable chemical industry. Energy 203, 117788. doi:10.1016/j.energy.2020.117788
Kooijman, H. A., and Sorensen, E. (2022). Recent advances and future perspectives on more sustainable and energy efficient distillation processes. Chem. Eng. Res. Des. 188, 473–482. doi:10.1016/j.cherd.2022.10.005
Li, Q., Finn, A. J., Doyle, S. J., Smith, R., and Kiss, A. A. (2023). Synthesis and optimization of energy integrated advanced distillation sequences. Sep. Purif. Technol. 315, 123717. doi:10.1016/j.seppur.2023.123717
Li, Q., Somoza-Tornos, A., and Kiss, A. A. (2024). A hierarchical selection and decision matrix for energy-efficient intensified distillation technologies. Comput. Aided Chem. Eng. Article in press.
Lutze, P., Babi, D. K., Woodley, J. M., and Gani, R. (2013). Phenomena based methodology for process synthesis incorporating process intensification. Industrial Eng. Chem. Res. 52 (22), 7127–7144. doi:10.1021/ie302513y
Mallapragada, D. S., Dvorkin, Y., Modestino, M. A., Esposito, D. V., Smith, W. A., Hodge, B. M., et al. (2023). Decarbonization of the chemical industry through electrification: barriers and opportunities. Joule 7 (1), 23–41. doi:10.1016/j.joule.2022.12.008
Mhatre, P., Pachal, R., Singh, A., and Bibyan, S. (2021). A systematic literature review on the circular economy initiatives in the European Union. Sustain. Prod. Consum. 26, 187–202. doi:10.1016/j.spc.2020.09.008
Mickovic, A., and Wouters, M. (2020). Energy costs information in manufacturing companies: a systematic literature review. J. Clean. Prod. 254, 119927. doi:10.1016/j.jclepro.2019.119927
Mitali, J., Dhinakaran, S., and Mohamad, A. A. (2022). Energy storage systems: a review. Energy Storage Sav. 1 (3), 166–216. doi:10.1016/j.enss.2022.07.002
Moulijn, J. A., Stankiewicz, A., Grievink, J., and Górak, A. (2008). Process intensification and process systems engineering: a friendly symbiosis. Comput. Chem. Eng. 32 (1-2), 3–11. doi:10.1016/j.compchemeng.2007.05.014
Nielsen, M. G., Morales, J. M., Zugno, M., Pedersen, T. E., and Madsen, H. (2016). Economic valuation of heat pumps and electric boilers in the Danish energy system. Appl. Energy 167, 189–200. doi:10.1016/j.apenergy.2015.08.115
Nikacevic, N. M., Huesman, A. E. M., Van den Hof, P. M. J., and Stankiewicz, A. I. (2012). Opportunities and challenges for process control in process intensification. Chem. Eng. Process. Process Intensif. 52, 1–15. doi:10.1016/j.cep.2011.11.006
Pistikopoulos, E. N., Tian, T., and Bindlish, R. (2021). Operability and control in process intensification and modular design: challenges and opportunities. AIChE J. 67 (5), e17204. doi:10.1002/aic.17204
Ponce-Ortega, J. M., Al-Thubaiti, M. M., and El-Halwagi, M. M. (2012). Process intensification: new understanding and systematic approach. Chem. Eng. Process. Process Intensif. 53, 63–75. doi:10.1016/j.cep.2011.12.010
Popp, J., Kovács, S., Oláh, J., Divéki, Z., and Balázs, E. (2021). Bioeconomy: biomass and biomass-based energy supply and demand. New Biotechnol. 60, 76–84. doi:10.1016/j.nbt.2020.10.004
Ramírez-Márquez, C., Al-Thubaiti, M. M., Martín, M., El-Halwagi, M. M., and Ponce-Ortega, J. M. (2023). Processes intensification for sustainability: prospects and opportunities. Industrial Eng. Chem. Res. 62 (6), 2428–2443. doi:10.1021/acs.iecr.2c04305
Rangaiah, G. P., Feng, Z., and Hoadley, A. F. (2020). Multi-objective optimization applications in chemical process engineering: tutorial and review. Processes 8 (5), 508. doi:10.3390/pr8050508
Schutzbach, M., Full, J., Kiemel, S., Waltersmann, L., Sielaff, L., Miehe, R., et al. (2021). Principles and design strategies for ultra-efficient production systems in the process industry. Chem. Ing. Tech. 93 (11), 1781–1791. doi:10.1002/cite.202100062
Sitter, S., Chen, Q., and Grossmann, I. E. (2019). An overview of process intensification methods. Curr. Opin. Chem. Eng. 25, 87–94. doi:10.1016/j.coche.2018.12.006
Skiborowski, M. (2018). Process synthesis and design methods for process intensification. Curr. Opin. Chem. Eng. 22, 216–225. doi:10.1016/j.coche.2018.11.004
Stankiewicz, A., Van Gerven, T., and Stefanidis, G. (2019). The fundamentals of process intensification. Hoboken, NJ, USA, Wiley VCH.
Sundmacher, K., Kienle, A., and Seidel-Morgenstern, A. (2005). Integrated chemical processes. Synthesis, operation, analysis, and control. Hoboken, NJ, USA. Wiley VCH.
Tian, Y., Demirel, S. E., Hasan, M. F., and Pistikopoulos, E. N. (2018). An overview of process systems engineering approaches for process intensification: state of the art. Chem. Eng. Processing-Process Intensif. 133, 160–210. doi:10.1016/j.cep.2018.07.014
Tian, Y., and Pistikopoulos, E. N. (2019). Synthesis of operable process intensification systems: advances and challenges. Curr. Opin. Chem. Eng. 25, 101–107. doi:10.1016/j.coche.2018.12.003
Keywords: process intensification, process systems engineering, energy efficiency, ecoefficiency, fluid separation
Citation: Li Q, Somoza-Tornos A, Grievink J and Kiss AA (2024) Challenges and opportunities for process intensification in Europe from a process systems engineering perspective. Front. Energy Res. 12:1340635. doi: 10.3389/fenrg.2024.1340635
Received: 18 November 2023; Accepted: 08 February 2024;
Published: 23 February 2024.
Edited by:
Anna Stoppato, University of Padua, ItalyReviewed by:
Juan Gabriel Segovia Hernandez, University of Guanajuato, MexicoCopyright © 2024 Li, Somoza-Tornos, Grievink and Kiss. This is an open-access article distributed under the terms of the Creative Commons Attribution License (CC BY). The use, distribution or reproduction in other forums is permitted, provided the original author(s) and the copyright owner(s) are credited and that the original publication in this journal is cited, in accordance with accepted academic practice. No use, distribution or reproduction is permitted which does not comply with these terms.
*Correspondence: Anton A. Kiss, QS5BLktpc3NAdHVkZWxmdC5ubA==