- National Key Laboratory of Offshore Oil and Gas Exploitation, CNOOC Research Institute Co., Ltd., Beijing, China
Introduction: Through the combination of hot water and chemical agent, the low-heat synergistic chemical profile control and flooding technology can not only reduce the risks of sand production and string damage caused by high-temperature thermal recovery technology, but also further improve the recovery factor on the basis of hot water flooding.
Methods: Based on laboratory testing, the synergism mechanism of thermal energy and chemical agent is studied.
Results: The research results showed that in the near wellbore zone of the injection well, crude oil viscosity reduction mainly relies on thermal energy, and chemical agents assist in improving the water oil mobility ratio and reducing the risk of cross flow. After entering the deep formation, due to the decrease in temperature, the thermal energy effect is weakened, but the chemical agents still aggregate at the oil-water interface and continue to act on heavy oil to reduce viscosity. The higher the temperature, the greater the role of heat energy, and the weaker the role of chemical agents. The higher the injection concentration of chemical agent, the more obvious the leading role of chemistry. Based on the comprehensive evaluation index, the optimized temperature is 80°C and the injection concentration is 1500 mg/L. The scheme study of Bohai L Oilfield shows that compared with cold water flooding, hot water flooding can only improve oil recovery by 1.2 percentage points, and low heat collaborative chemical profile control flooding technology can further improve oil recovery by 4.7 percentage points on the basis of hot water flooding, with obvious oil increase effect.
Conclusion: It is suggested that Bohai L Oilfield should apply low-heat coordinated chemical profile control and flooding technology to improve the development effect of the oilfield, and provide new technical ideas for safe and economic development of offshore heavy oil.
Introduction
Bohai Oilfield is rich in heavy oil resources, accounting for 56% of the proved geological reserves. Compared with onshore oilfield, offshore heavy oil development is more difficult (Xie et al., 2016; Zhang et al., 2021). Ordinary heavy oil with formation crude oil viscosity less than 350 mPa s is currently mainly developed by cold recovery methods such as water flooding or chemical flooding, with recovery factor of 30%–50%, but heavy oil with viscosity greater than 350 mPa s is generally less than 10% (Liang et al., 2009; Liang et al., 2015; Qu et al., 2020; Kang et al., 2021). In recent years, field tests of multiple thermal fluid huff and puff, steam huff and puff and steam drive technologies have also been carried out in Nanbao35-2, Chengbei and other oilfields (Chen, 2011; Tang et al., 2011; Cheng-xiang et al., 2012; Liang et al., 2014; Zhu et al., 2016; Zheng et al., 2020; Kang et al., 2022; Yuan et al., 2022), and certain yield increase effects have been achieved. However, because the reservoirs in Bohai Oilfield are mostly loose sandstone and have strong heterogeneity, the conventional thermal recovery method generally has a high temperature, usually above 300°C, so the problems of channeling, sand production and string damage are inevitable in the process of high-temperature fluid injection (Dong et al., 2013; Jiang et al., 2014). In addition, for offshore oil fields, the platform space is limited and the project investment is large. High-temperature thermal recovery requires supporting large heating boilers and water treatment facilities, which not only occupies the platform space but also has high investment costs. The use of high-temperature resistant pipe strings and pumps makes the economic benefits even less optimistic.
In addition to high-temperature thermal recovery technology, field tests of hot water flooding with relatively low temperature have also been carried out in many oilfields, mainly as a replacement technology after high-temperature thermal recovery or conventional water flooding. Guo Dianjun introduced the field test of hot water flooding in shallow and thin heavy oil reservoirs in Daqing Oilfield (Guo et al., 2019). The research shows that the daily oil production has increased by 6t, the comprehensive water cut has decreased significantly, and the oil increase effect is obvious. Duvalintroduced the field test of circulating hot water flooding in Pelican Lake Oilfield, Canada. Through the use of circulating hot water injection, thin heavy oil reservoirs can be effectively developed (Duval et al., 2015). The production of a single well has increased by 19 m3 per day and lasted for more than 2 years. Jha introduced the field test of hot water flooding in the multi-layered onshore oil fields in the South Lokichar Basin of Kenya (Jha et al., 2018). The designed reasonable surface injection temperature is 90°C, while ensuring the low salinity and bacterial count of the injected water.
Although the hot water flooding technology has achieved certain application results, the channeling phenomenon between injection and production well groups in the middle and late stages of hot water flooding can not be effectively avoided. Therefore, some scholars put forward the development method of using hot water and chemical agent to inject together. Mukherjee introduced the technology of improving oil recovery by injecting polymer and hot water together under the condition of bottom water reservoir (Mukherjee et al., 2014). The research shows that preheating the crude oil in the reservoir by injecting hot water can effectively improve the oil displacement efficiency of the polymer. Although hot water can reduce the viscosity of crude oil, the higher the temperature, the better. The viscosity of polymer is affected by thermal degradation, and the sweep efficiency will be limited. Therefore, many scholars have done a lot of research on the mechanism between the temperature required by thermochemical flooding, crude oil viscosity and oil displacement efficiency. In 2016, Tagavifar carried out numerical simulation of hot water polymer flooding in 5000cp heavy oil field, and found that the recovery rate of hot water flooding was 10%, and that of chemical flooding was 20%–50% (Tagavifar et al., 2016); In 2017, Rego adopted the method of numerical simulation to analyze the impact of polymer and hot water composite flooding at different injection temperatures on production and economic indicators, and believed that the optimal injection temperature of hot water was about 100°C. When the temperature exceeded 100°C, the polymer failed seriously and the economic effect was poor (Rego et al., 2017).
In view of the above problems, the low-heat coordinated chemical profile control and flooding technology suitable for offshore heavy oil is proposed to improve the development effect and simultaneously solve the problems of channeling, sand production and economy. In this paper, the low-heat collaborative chemical profile control and flooding technology has been deeply studied from three aspects: indoor experiment, numerical simulation calculation and field scheme design.
Laboratory testing of low heat collaborative chemical profile control and flooding technology
Low-heat collaborative chemical profile control and flooding technology is to add high-temperature and salt-resistant multi-functional chemical agent into hot water. The chemical agent has the combined functions of increasing the viscosity of water phase, reducing the interfacial tension and reducing the viscosity of crude oil. Through the coordination of the characteristics of heat energy and chemical agent, the viscosity of crude oil and the characteristics of oil-water two-phase interface are changed, and the purpose of greatly improving oil recovery is achieved.
Under different displacement stages and temperature ranges between injection and production wells, the mechanism of enhanced oil recovery under the synergistic action of thermal energy and chemical agents has evolved. In the near-well zone of the injection well, the thermal energy carried by the hot water is mainly used to reduce the viscosity of crude oil and improve the fluidity of crude oil. After the temperature rises, the chemical agent can effectively improve the oil washing efficiency. At the same time, the chemical agent can adjust the water-oil mobility ratio to control the displacement profile, expand the swept volume, and reduce the occurrence of hot water channeling; As the injected water advances to the deep part of the formation, the displacement phase gradually recovers to the formation temperature after the loss of heat energy. At this time, the chemical agent plays a leading role. The chemical agent disassembles the crude oil at the oil-water interface, reducing the viscosity of the crude oil, thus achieving the effect of integrated profile control and flooding.
Laboratory testing of the mechanism of improving oil recovery
The performance of temperature and multifunctional chemical agents on heavy oil was tested through experiments, and the synergistic mechanism of thermal energy and chemical agents was studied.
(1) Mechanism 1: thermal energy reduces the viscosity of heavy oil and improves its flowability
During the thermal recovery process, thermal energy is injected into the formation through the thermal medium, which is transferred to the heavy oil. As a result, the viscosity of the heavy oil decreases and the flow performance is improved. The viscosity of heavy oil with an original viscosity of 380 mPa s was tested at different temperatures. The test results are shown in Figure 1. From the figure, it can be seen that during the heating process, the viscosity of heavy oil decreases as the temperature increases, indicating that thermal energy can play a good role in reducing viscosity. By using thermal energy near the wellbore, the viscosity of heavy oil can be reduced. When the temperature rises from 60°C to 80°C, the viscosity of heavy oil decreases to 138 mPa s, and the viscosity reduction rate is 64%. The viscosity reduction rate is the percentage of the difference between the current viscosity and the original viscosity to the original viscosity, which is used to characterize the degree of viscosity change. When the temperature further increases to 120°C, the viscosity decreases to 35 mPa s, and the viscosity reduction rate further increases by 27%. The speed of viscosity reduction of heavy oil shows a characteristic of first fast and then slow.
During the cooling process, it is equivalent to the temperature change process from the bottom of the injection well to the deep part of the formation. From the test results, as the temperature decreases, the viscosity of the heavy oil gradually returns to its initial viscosity. Therefore, it indicates that the scope of relying solely on thermal energy to improve the development effect of heavy oil is very limited.
(2) Mechanism 2: chemical agents increase the viscosity of the aqueous phase, improve the water oil fluidity ratio, and expand the swept volume
The viscosity of the chemical agent at different temperatures and concentrations was tested with Wu Yin stirrer under the condition of shearing for 20s at the first gear (3500r/min). The test results are shown in Figure 2. The test results show that: ① At the same temperature, the higher the concentration, the greater the viscosity. When the temperature is less than 100°C, the viscosity corresponding to the concentration of 1500 mg/L reaches about 80 mPa s, which has good viscosity increasing performance. It shows that the chemical agent can adjust the injection profile in the near-well zone by increasing the viscosity of the water phase, which is conducive to preventing hot water channeling and expanding the swept volume. ② The chemical agent is a temperature-sensitive agent. At the same concentration, the viscosity of the agent first shows an increasing trend with the increase of temperature. When the temperature is greater than 80°C, it changes to a downward trend. However, when the temperature rises from 80°C to 120°C, the viscosity retention rate is still more than 65%, indicating that the agent has good temperature resistance.
(3) Mechanism 3: chemical agents have interfacial activity that helps heavy oil peel off the surface of rocks
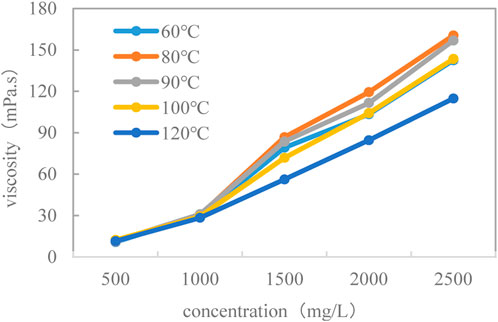
FIGURE 2. Relationship between viscosity and concentration at different temperatures (after shearing).
The interfacial tension of the solution at different chemical concentrations was tested, and the test results are shown in Figure 3. When the solution concentration is 500 mg/L, the interfacial tension can be reduced to 0.8 mN/m, and the higher the concentration is, the lower the interfacial tension is, indicating that the chemical agent has high interfacial activity, and can achieve the effect of oil washing after injection into the formation.
(4) Mechanism 4: chemical agents can change the structure of heavy oil and reduce its viscosity
Prepare a 0.1% toluene solution of asphaltene with toluene, and add 1500 mg/L of chemical agent in a volume ratio of 1:1. The mixture is shaken at a rate of 3000r for 5 min on a constant temperature shaker, cooled to room temperature, and centrifuged for 10 min. Finally, dry the upper layer of heavy component solution to obtain the asphaltene after action. The changes of relative molecular weight, microcrystalline parameters and micro morphology of heavy component asphaltene after interaction with chemical agents were measured by gel chromatography, X-ray diffraction and scanning electron microscope.
From the test results (Table 1), it can be seen that after the interaction between asphaltene and chemical agents, the number average molecular weight and weight average molecular weight both decrease, indicating that the chemical agent has the effect of reducing the relative molecular weight of asphaltene, and the effect is more obvious at 80°C than at 60°C. After the interaction of asphaltene with chemical agents, the interlayer spacing, chain spacing, and average diameter of aromatic discs in the layered stacking structure increase, while the stacking height and number of layers decrease. This indicates that under the dual effects of the dispersal effect of chemical agents on asphaltene and the thermal energy of temperature, the fatty carbon and cyclic carbon of asphaltene decrease, and the layered stacking becomes loose. The aggregates extend from the stacking to the plane, and the stacking degree decreases.
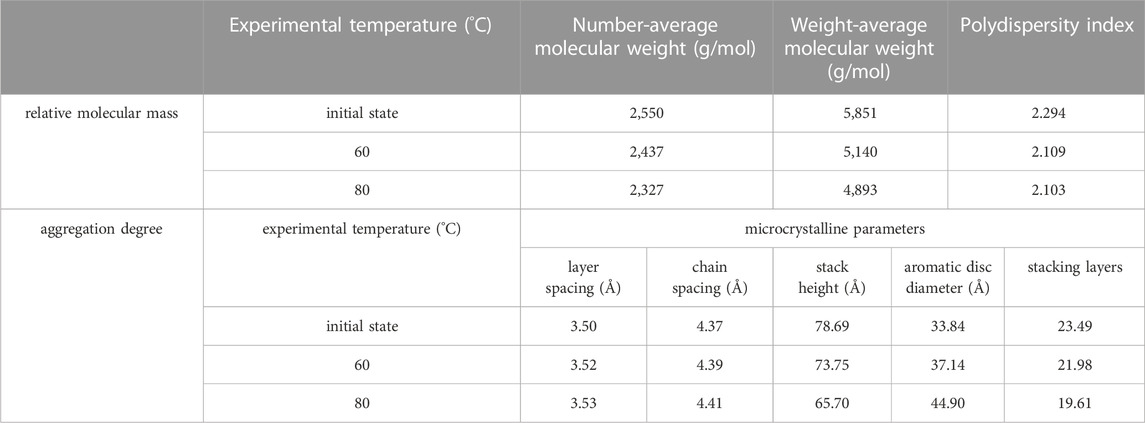
TABLE 1. Structural characterization parameters of asphaltene before and after the action of chemical agents.
From the scanning electron microscope photos (Figure 4), it can be seen that the cross-section of asphaltene particles in their original state is rough and uneven, while the affected cross-section becomes relatively smooth and flat, with an increase in surface pores, indicating that chemical agents can reduce the roughness of asphaltene particles and reduce the friction between asphaltene and its other components.
In addition to the microscopic effects, the macroscopic effects of chemical agents on heavy oil at different temperatures were further tested. Mix crude oil and different concentrations of chemical agents in a 1:1 ratio to form an oil-water mixture. Stir it on a constant temperature magnetic stirrer, test the viscosity of the oil-water mixture system at different temperatures, and finally calculate the viscosity reduction rate (Figure 5). The test results show that: ① With the increase of temperature, the viscosity of crude oil shows a downward trend, and the viscosity reduction rate can reach more than 60% when the temperature rises from 60°C to 80°C, which shows that thermal energy can play a good role in viscosity reduction, and the effect of viscosity reduction of crude oil can be achieved through thermal energy near the well end; ② Due to the viscosity of the chemical agent itself, at the same temperature, with the increase of the concentration of the agent, the viscosity reduction rate of the mixed liquid system first increases and then decreases, reaching the peak at the concentration of 1,000–1500 mg/L, and the maximum viscosity reduction rate of the chemical agent with the concentration of 1500 mg/L at 80°C, reaching 85%. ③ When the temperature is relatively low, the effect of chemical agent on viscosity reduction is more obvious. With the increase of temperature, chemical agent plays an auxiliary role in viscosity reduction, while thermal energy plays a leading role in viscosity reduction. Therefore, in the process of displacement, the front edge of displacement migrates to the deep part of the formation. Even if the temperature is low, there is no effect of heat energy. The chemical agent can reduce the viscosity of heavy oil by adsorbing on the oil-water interface for disassembly. The viscosity reduction rate can reach more than 60% when the temperature is less than 90°C. The effect of viscosity reduction is obvious, and the effect of viscosity reduction at the far end of the well is realized.
Laboratory testing of oil displacement effect
One-dimensional oil displacement experiment was carried out. The viscosity of crude oil was 380 mPa s (60°C), and the average core permeability was 6000 mD. During the experiment, after the water cut of water drive reaches 90%, change the injection water temperature or add chemical agent solution with different concentration and slug volume of 0.3 PV. Analyze the effect of enhancing oil recovery under the conditions of injecting different media (Figure 6). The test results show that: ① for a single hot water drive, with the rise of temperature, the range of enhanced oil recovery increases gradually, with an increase of 5%–10%; ② At different temperatures, after adding chemical agent, thermal synergetic chemical agent can increase oil recovery by 5%–16% on the basis of hot water flooding; ③ With the increase of temperature, the contribution of chemical agents to EOR decreases from 73% at 60°C to 33% at 120°C. It is verified that the high temperature environmental thermal energy near the well end plays a leading role, and the low temperature environmental chemical agents at the depth of the formation play a leading role; ④ With the increase of chemical agent concentration, the range of enhanced oil recovery increases, and the proportion of chemical agent enhanced oil recovery increases from 62% of 1000 mg/L to 76% of 2500 mg/L; ⑤ The product of the EOR value and the total EOR value per unit of injection slug size is defined as the comprehensive evaluation index for optimizing the injection parameters. The larger the value of the comprehensive evaluation index, the better the oil increase effect and economy. The optimized injection temperature is 80°C and the injection concentration is 1500 mg/L.
Numerical simulation of low-heat synergistic chemical profile control and flooding technology
Based on the CMG numerical simulation software, the mechanism characterization method of synergistic enhanced oil recovery by thermal energy and chemical agent is constructed, and on this basis, the indoor displacement experiment is fitted, and the key physical and chemical parameters required for the scheme study are reversely performed, forming the simulation technology of the integrated technology of low-heat synergistic chemical profile control and flooding. Table 2 shows the corresponding characterization method of synergistic enhanced oil recovery mechanism by thermal energy and chemical agent in the software.
Based on the indoor displacement core, a cylindrical core model with equal size is established for numerical simulation. The rectangular coordinate system is adopted, and the size of the model (Figure 7) is 0.025 × 0.025 × 0.6 m, grid size 25 × 25×15, grid step is 0.001 × 0.001 × 0.04 m. The parameters such as viscosity-temperature relationship, viscosity-concentration relationship and adsorption required in the model shall be measured by indoor experiments. The key physical and chemical parameter setting methods and steps in the model are as follows.
① Define components: set two water phase components (water1, water2), two oil phase components (oil1, oil2), and one chemical component (chemical), wherein oil1 is high viscosity crude oil, and oil2 is light oil after viscosity reduction.
② Set the viscosity-temperature relationship: based on the indoor experiment, input the viscosity values of each component at different temperatures.
③ Set nonlinear viscosity-concentration relationship: based on indoor experiments, input the corresponding values of different concentration and viscosity of the agent.
④ Set the chemical reaction relationship: oil 1 reacts with the agent dissolved in water 1 to generate oil 2. The chemical reaction equation is:
The agent x value is mainly obtained by numerical inversion of indoor core displacement experiment.
⑤ Set reagent adsorption parameters: according to the indoor experiment, input the corresponding value of different concentration of reagent and adsorption amount.
The production control conditions are consistent with the experimental settings. The first limiting condition of the injection well is the actual injection rate, and the second limiting condition is the actual injection pressure; The first limiting condition of the production well is constant pressure production, the second limiting condition is constant liquid production, and the liquid yield is the measured liquid volume in the experiment. In the inversion process, the viscosity reduction rate at different temperatures is also adjusted when adjusting the viscosity concentration relationship of the chemical agent, so that the water content of the numerical simulation is consistent with the experimental value. Applying the above numerical core model and inversion idea, the displacement experiment process at 80°C was inverted (Figure 8).
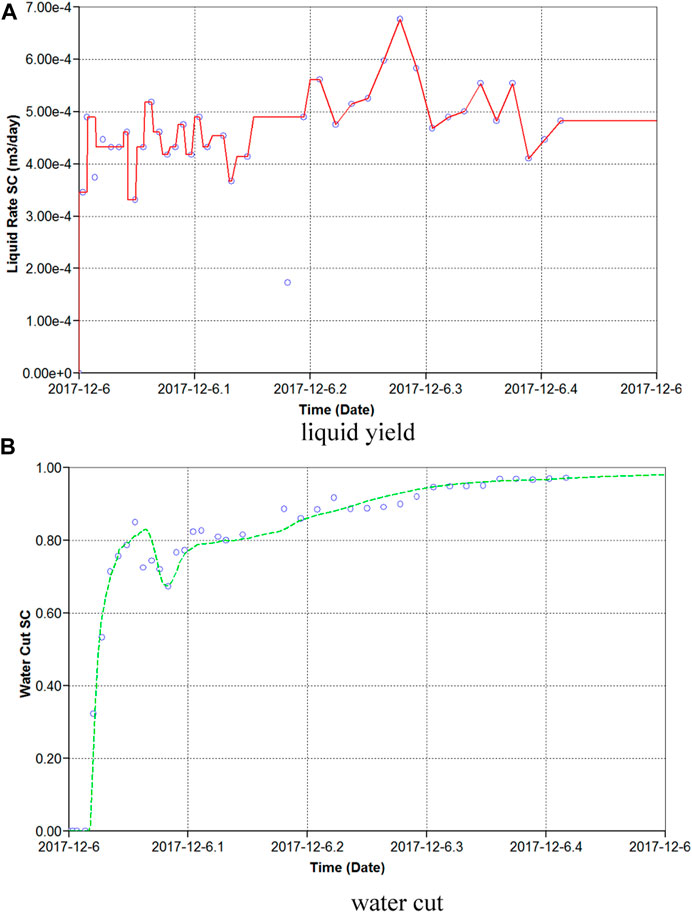
FIGURE 8. The fitting result of numerical simulation to indoor experiment. (A) The red line is the data calculated through numerical simulation, and the small circle is the data from experimental testing. (B) The green line is the data calculated through numerical simulation, and the small circle is the data tested through experiments.
According to the results of numerical simulation inversion, the key parameters required in the numerical simulation of low-heat collaborative chemical profile control and flooding technology are determined: ① The viscosity of the chemical agent after shearing is taken as the viscosity of the chemical agent with the concentration of 2500 mg/L; The viscosity-temperature relationship of crude oil is taken from the test value of laboratory experiment; ② The viscosity reduction rate of the chemical agent is taken as 60% of the test value of the indoor experiment at different temperatures; ③ The viscosity-concentration relationship of chemical agent is taken as the test viscosity after shearing from 0 to 2,500 mg/L; ④ The value of adsorption key is the test value of the experiment.
Scheme design of low-heat cooperative chemical profile control and flooding in Bohai L oilfield
The reservoir buried depth of Bohai L Oilfield is 1,160–1412 m, and the physical properties of the reservoir are good. The average permeability is 6130mD, and the average porosity is 32%. The crude oil is heavy oil, and the viscosity of the formation crude oil is 210–460 mPa s. The oil field is developed by water drive, and the oil recovery rate is relatively low (0.7%) and a water content of 91%. At present, the recovery rate is 13%, and the oil recovery rate needs to be further improved. The oilfield has a complete well network, adopting a row shaped well network, where one row of injection wells corresponds to one row of production wells. The ratio of injection wells to production wells is 1:2, and the injection production correspondence is good. Therefore, it is suitable for carrying out low heat collaborative chemical profile control and flooding technology.
Due to the limited space of the platform, it is planned to use the surplus heat of the hot medium boiler of the platform as the heat source, and heat the hot medium with the injected water through the new heat exchange equipment, so that the injected water can be heated to the required temperature and mixed with a certain concentration of chemical agent, and then injected into the marked well through the new water injection pipe manifold. According to the platform surplus heat combined with the injection volume, the maximum temperature that can provide hot water is calculated to be 108°C. During the injection process, due to the wellbore heat loss, the temperature reaching the bottom of the well is about 80°C.Compared to water injection, the viscosity of the chemical agent is higher. Therefore, considering the injection capacity, the designed injection rate for chemical agent injection is 0.8 of that for water flooding. The injection rate for a single well is 190 m3/d to 550 m3/d, with an average of 352 m3/d and an injection production ratio of 1:1. When optimizing injection parameters, economic indicators (the product of oil increase per ton of chemical agent and EOR) were used as evaluation indicators. The optimized injection time is 8 years and the injection concentration is 1200 mg/L (Figures 9, 10). On this basis, the development indicators of low heat collaborative chemical profile control and flooding integration were calculated, and the calculation results were compared with the hot water flooding scheme (Figure 11).
The calculation results show that hot water flooding can obtain 40 × 104 tons of oil increase on the basis of cold water flooding, but the enhanced oil recovery is limited, only 1.2 percentage points. The enhanced oil recovery effect of low-heat collaborative chemical profile control flooding technology is obvious, which can further improve the oil recovery by 4.7 percentage points on the basis of hot water flooding. Compared with cold water flooding, this technology can improve the oil recovery by 5.9 percentage points. In this scheme, the temperature is only 20°C higher than that of cold water flooding, The contribution of thermal energy is relatively low, accounting for 21% of the increase in production, and the contribution of chemical agents is 79%.
It can be seen from the numerical model analysis (Figure 12) that compared with hot water flooding, the addition of chemical agent can effectively inhibit the coning speed of the hot water front, which is conducive to expanding the swept volume and improving oil recovery.
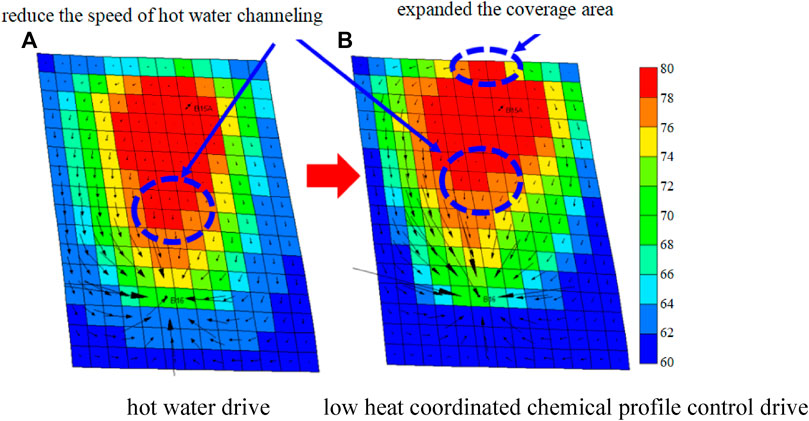
FIGURE 12. Temperature comparison diagram of different development methods. (A): hot water flooding (B): low-heat Synergistic Chemical flooding.
Conclusion
Low-heat collaborative chemical profile control and flooding technology combines hot water flooding with chemical flooding. The thermal energy carried by hot water and the role of chemical agent in separating asphaltene and colloid aggregates jointly reduce the viscosity of crude oil. The chemical agent can increase the viscosity of water phase, improve the water-oil mobility ratio, reduce the risk of crossflow, expand the swept volume, and the thermal energy and chemical agent can also improve the efficiency of oil washing. Through the synergy of physics and chemistry, the ultimate goal of enhancing oil recovery is achieved.
Injection temperature and reagent concentration are the key factors that affect the oil increase effect and economic benefit of the low-heat synergistic chemical technology. With the increase of temperature, the extent of thermal energy enhancing oil recovery increases, and the role of chemical agents is weakened; With the increase of chemical agent concentration, the increase of oil recovery increases, but when the concentration is greater than a certain value, the increase of oil recovery slows down. Therefore, reasonable injection temperature and chemical agent concentration should be selected according to specific oilfield characteristics.
The calculation results of the recommended scheme of Bohai L Oilfield show that compared with cold water flooding, low heat cooperative chemical profile control flooding can improve oil recovery by 5.9%, thermal energy contribution accounts for 21% of the increase in oil production, and chemical agent contribution accounts for 79%. This technology can provide a new idea for the effective development of offshore heavy oil.
Data availability statement
The original contributions presented in the study are included in the article/supplementary material, further inquiries can be directed to the corresponding author.
Author contributions
LD: Investigation, Methodology, Writing–original draft.
Funding
The author(s) declare that no financial support was received for the research, authorship, and/or publication of this article.
Acknowledgments
Thanks to “Independent Prospective Basic Project of State Key Laboratory of Offshore Oil Exploitation in 2023”, “Research on Key Technologies for Thermal Recovery and Mobile Thermal Injection in Offshore Multilayer Reservoirs” and “Key Technologies for Large scale Application of Chemical Flooding in Offshore Oilfields”.
Conflict of interest
Authors LD, ZJ, ZW, HZ, ZQ, and WL were employed by CNOOC Research Institute Co., Ltd.
Publisher’s note
All claims expressed in this article are solely those of the authors and do not necessarily represent those of their affiliated organizations, or those of the publisher, the editors and the reviewers. Any product that may be evaluated in this article, or claim that may be made by its manufacturer, is not guaranteed or endorsed by the publisher.
References
Chen, W. (2011). An evaluation of huff and puff development effects for onshore heavy oil reservoir A and the challenges of thermal recovery to offshore heavy oil fields. China Offshore Oil Gas 23 (6), 384–386.
Cheng-xiang, Qi, Li, J., Jiang, J., Zhu, W., and Hao, H. (2012). Multi-factor orthogonal optimization study on the injection-and-production parameters of multi-thermal-fluid huff & puff for recovering offshore heavy oil. Special oil gas reservoirs 19 (5), 86–89.
Dong, S., Zhang, H., Ji, G., and Li, X. (2013). Test and analysis of sand control screen corrosion in thermal production wells using multiple thermal fluids. Chem. Eng. oil gas 42 (3), 287–289.
Duval, K., Gufierrez, D., Petrakos, D., Ollier, P., and Johannson, D. (2015). Successful application of hot-water circulation in the Pelican Lake field results and analyses of the E29 hot-water-injection pilot. J. Can. Petroleum Technol. 54 (06), 361–371. doi:10.2118/174491-pa
Guo, D., Zhang, L., and Zhou, Z. (2019). Study on the development effect of thermal water flooding in shallow and thin heavy oil reservoirs in block A of Ala Xin’a area. J. yangtze Univ. Nat. Sci. Ed. 16 (08), 23–27.
Jha, M., Namuganyi, S., Limborgh, J. V., Wenk, A., Amin, M., and Anuar, F. (2018). “Successful hot water injection trial in stacked reservoirs in South Lokichar basin-onshore Kenya,” in Paper SPE-189510-MS. Presented at the SPE International Conference and Exhibition on Formation Damage Control held in Lafayette, Louisiana, USA, 7-9 February 2018.
Jiang, J., Gong, R., Li, J., Sun, Y., and Yang, B. (2014). Study on cross well steam channeling regularity of horizontal well multi-component thermal fluid stimulation in heavy reservoir. Oil gas field Dev. 32 (5), 45–48.
Kang, P., Liu, G., Qiu, Y., Zhen, B., and Liu, Z. (2022). Application of thermal recovery injection-production integration technology in old wells in offshore oilfields. Tianjin Sci. Technol. 49 (8), 46–48.
Kang, X., Sun, Z., Zhang, J., and Wei, Z. (2021). The Concept, Pattern and pilot test of non-equilibrium chemical flooding in offshore oilfields. Sci. Technol. Eng. 21 (11), 4418–4426.
Liang, D., Feng, G., Zeng, X., Fang, M., and He, C. (2014). Evaluation of two thermal methods in offshore heavy oilfield development. Pet. Drill. Tech. 42 (1), 95–99.
Liang, D., Lv, X., Jiang, S., Liang, S., and Feng, G. (2015). The technology classified combination of deep profile control in the Bohai oilfield. Pet. Drill. Tech. 43 (2), 104–109.
Liang, D., Zeng, X., and Maojun, F. (2009). Producing with limited sanding applied in offshore heavy oil fields. J. Southwest Petroleum University(Science&Technology Ed. 31 (3), 99–102.
Mukherjee, S., Suss, M. P., and Gmbh, W. H. (2014). “Performance evaluation and design aspects of polymer and hot water Co-injection in an offshore heavy oil field under challenging conditions,” in Paper SPE-169711-MS. Presented at the SPE EOR Conference at Oil and Gas West Asia held in Muscat, Muscat, Oman, March 31–April 2, 2014.
Qu, Y., Ruan, D., Wei, Z., Kang, X., and Yan, X. (2020). Optimization of injection-production pattern for polymer flooding in S offshore oilfield. Petroleum Geol. recovery Effic. 27 (2), 112–117.
Rego, F. B., Botechia, V. E., and Schiozer, D. J. (2017). Heavy oil recovery by polymer flooding and hot water injection using numerical simulation. J. Petroleum Sci. Eng. 21 (01), 74–86. doi:10.1016/j.petrol.2017.03.033
Tagavifar, M., Fortenberry, R., de Rouffignac, E., Sepehrnoori, K., and Pope, G. A. (2016). Heavy-oil recovery by combined hot water and alkali/cosolvent/polymer flooding. SPE J. 21 (01), 74–86. doi:10.2118/170161-pa
Tang, X., Ma, Y., and Sun, Y. (2011). Research and field test complex thermal fluid huff and puff technology for offshore viscous oil recovery. China Offshore Oil Gas 23 (3), 185–188.
Xie, X., Kang, X., Zhang, X., Shi, Y., Zeng, Y., and Hou, J. (2016). Chemical flooding potential evaluation method in offshore heavy oilfields and its application. China Offshore Oil Gas 28 (1), 69–74.
Yuan, Y., Rong, K., Gao, J., Ruan, D., Kou, S., and Li, Z. (2022). Research on water channeling law of multi-component thermal fluid huff & puff in edge bottom heavy oil reservoir. Petrochem. Ind. Appl. 41 (8), 24–28.
Zhang, J., Wang, G., Wang, L., Deng, L., Chen, C., and Zhang, G. (2021). Comprehensive treatment technologies for the stripped and deficient wells of Bohai heavy oil field in high water cut stage. Oil Drill. Prod. Technol. 43 (5), 687–692.
Zheng, W., Tan, X., Wang, T., Zhu, G., and Zhang, L. (2020). A new method to determine initial production of steam stimulation in offshore heavy oilfield. Xinjiang Pet. Geol. 41 (3), 344–348.
Keywords: heavy oil, thermo-chemical synergy, experiment, mechanism, scheme design
Citation: Dan L, Jian Z, Wensheng Z, Zhao H, Qichen Z and Liqi W (2023) Study on low-heat synergistic chemical profile control and flooding technology in Bohai Oilfield. Front. Energy Res. 11:1324758. doi: 10.3389/fenrg.2023.1324758
Received: 20 October 2023; Accepted: 10 November 2023;
Published: 29 November 2023.
Edited by:
Feng Dong, China University of Geosciences, ChinaCopyright © 2023 Dan, Jian, Wensheng, Zhao, Qichen and Liqi. This is an open-access article distributed under the terms of the Creative Commons Attribution License (CC BY). The use, distribution or reproduction in other forums is permitted, provided the original author(s) and the copyright owner(s) are credited and that the original publication in this journal is cited, in accordance with accepted academic practice. No use, distribution or reproduction is permitted which does not comply with these terms.
*Correspondence: Liang Dan, bGlhbmdkYW5AY25vb2MuY29tLmNu