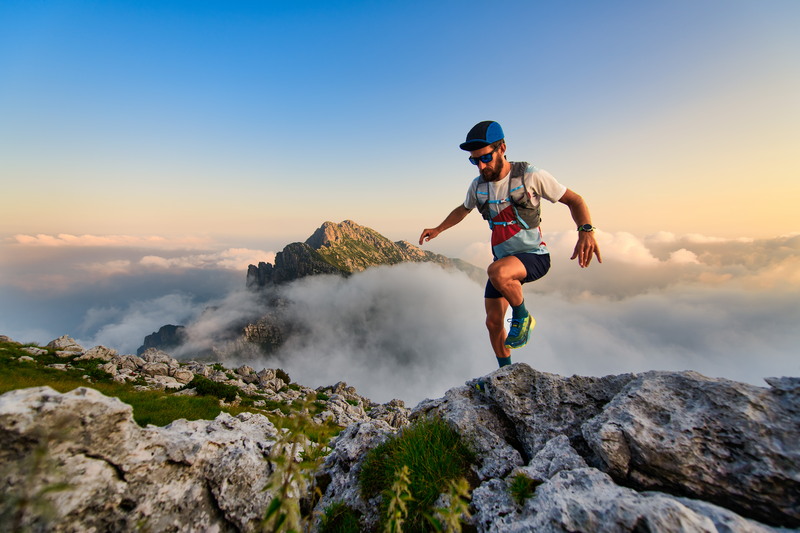
95% of researchers rate our articles as excellent or good
Learn more about the work of our research integrity team to safeguard the quality of each article we publish.
Find out more
ORIGINAL RESEARCH article
Front. Energy Res. , 29 December 2023
Sec. Energy Storage
Volume 11 - 2023 | https://doi.org/10.3389/fenrg.2023.1321088
Phase change materials (PCMs) provide a good resolution for the latent heat storage system which can be used in many application fields such as solar energy utilization and waste heat recovery. This study aims to experimentally investigate the impact of graphite powder on the thermal characteristics and heat transfer performance of paraffin with ceresin (PC) as a PCM, using water as the heat transfer fluid. Experimental tests were conducted to analyze the heat transfer performance of PC and the influence of graphite powder on its thermal characteristics. Different masses of graphite powder were employed to assess their effects on the heating rate and the time required for PC to reach its melting temperature. The experimental results revealed that the addition of graphite powder improved the heating rate of both PC and water, attributed to its high thermal conductivity. Furthermore, the time for PC to reach the melting temperature was decreased with varying amounts of graphite powder, achieving a maximum reduction of 17.2% with the addition of 40 g of graphite powder. However, the effectiveness of graphite powder in enhancing heat transfer efficiency was found to be limited, with the optimal promotion effect observed at around 40 g of graphite powder for 500 g of PC. The findings of this investigation provide valuable insights for the design of phase change energy storage systems, with potential applications including heat pump drying units, greenhouse energy storage in modern agriculture, and solar energy storage utilization technology. The theoretical basis established can contribute to the development and optimization of PCM-based systems in diverse practical scenarios.
Thermal energy is one of the most important forms of energy in the existing energy structure (Curry et al., 2023). Thermal storage technology can address the contradiction between the timing and intensity of thermal energy supply and demand, effectively reducing energy waste caused by the time difference in energy supply and demand. Therefore, thermal storage technology has broad application prospects in many fields such as heating and air conditioning energy saving, solar energy utilization, and waste heat recovery in industrial and civil buildings.
There are many ways to store thermal energy, including chemical energy storage (Jayaprabakar et al., 2023), sensible energy storage (Paul et al., 2022) and latent energy storage (Lu et al., 2023). Among them, the latent heat storage has a high density and an isothermal heat storage and release process, which is easy to control and operate, making it the main heat storage method (Waseem Aftab et al., 2021). Latent energy storage based on phase change materials (PCMs), such as paraffins, salt hydrates and metallics, has been widely studied in the application of solar engineering, heat pump, spacecraft thermal control, industrial waste heat storage, and so on (Zhang et al., 2021; Matos and Pala, 2023). Paraffin is a by-product of refined petroleum separated from the wax fraction of crude oil. Industrial grade paraffin is often used as a phase change heat storage material, which has the advantages of high latent heat, low melting vapor pressure, good chemical stability, self-nucleation, no phase separation and corrosion (Lu et al., 2021a). However, pure paraffin suffers from problems such as low thermal conductivity, limiting its utilization (Rahmalina and Abdu RahmanIsmail, 2022). In order to improve the thermal conductivity of paraffin, researchers mainly focus on the improvement of heat storage equipment, such as using fins (Sheikholeslami and Jafaryar, 2023), honeycombs (Sheikholeslami, 2022), porous media (Mohammadreza Naghdi Bazneshin et al., 2023), or adding metal powder (Gao et al., 2023), metal mesh (Homlakorn et al., 2023), graphite (Liu et al., 2023), and so on.
Compared with other methods, adding thermal conductive materials, such as graphite, is a relatively simple, economical, and feasible method to improve the thermal conductivity of paraffin. Graphite has good thermal conductivity and can quickly conduct heat. Therefore, when graphite powder is added to paraffin, it can accelerate the melting rate of paraffin and improve thermal uniformity, avoiding local overheating or solidification (Dhandayuthabani et al., 2020). For the investigation of graphite, mass ratio is an important focus. It is found that when it comes to the case of 95 mass% of composite PCM, a reduction of 13.3% in the melting time is obtained (Zheng et al., 2018). In the study of Zeng et al. (Zheng et al., 2018), when 3.0 mass% graphite was added, the super cooling degree could be alleviated to 62.6°C with the latent heat of 185.7 J/g. The production method of paraffin and graphite composition is another research content. In the study of Yang et al. (2022), paraffin wax and graphite powder were compressed into a shape-stabilized phase material. By testing the pressure and density of the mixture, they found that the maximum density of the mixture was 1.07 g/cm3. In the investigation of Dong et al. (2022), a novel strategy was developed by constructing graphite sheets with high orientation inside the phase change composites following compression induction. Highly efficient heat transfer could be obtained through the channels provide by the highly oriented graphite sheets. In the study of Yang et al. (2023), a 3D porous graphite foam was prepared by a pressing and drying method, which was used as the thermal conductive skelton and shape stabilizer of phase change materials. They found that the mixture had an ultra-high thermal conductivity of 19.27 W/(m∙K), which was about 76 times higher than that of pure paraffin.
To further improve heat exchange efficiency, combinations of graphite and other additives attract much attention. In an air conditioning system, tetradecane combined with graphite achieved a 30% reduction in CO2 emission and compressor size (Aljehani et al., 2018). In the study of Liu et al. (2022), expanded graphite (EG)/paraffin (PA)/silica (SiO2) composite materials were fabricated, with a thermal conductivity of 2.053 W/(m∙K), which was 8.5 times higher than that of pure paraffin wax. In the energy storage system, combination of wood and graphite is utilized to improve the stabilization, with a conductivity of 65 W/(m·K) (Huang et al., 2017). In the investigation of Wang et al. (2020), microstructure of graphite was approved to greatly enhance the thermal conductivity of paraffin phase change materials, mainly due to the synergetic effects induced by the intrinsic high thermal conductivity of graphite and the high anisotropy degree of graphite sheets in the paraffin matrix. However, graphite powder can agglomerate in molten paraffin wax and settle. To solve this problem, Gorbacheva et al. (2021) utilized hydrophobic nano-sized silicon dioxide as a stabilizer. They found that at the concentration of 3 vol. %, silica nanoparticles formed a percolation structure, which was capable to prevent the sedimentation of graphite particles introduced into the mixture. Through environmental scanning electron microscope (ESEM) technology, graphite particle was found to disperse homogeneously in composite PCMs (Lu et al., 2021b). After repeated melting and solidification cycles during the stability tests, the properties of paraffin-graphite phase change materials were demonstrated to remain unchanged (Chakraborty et al., 2022). Moreover, better stability and dynamic characteristics were also found in the composite PCM amended expansive soil under combined effect of alternating load and wet and dry cycles (Liu et al., 2023).
Graphite powder has a promoting effect on the phase change heat transfer process of paraffin, but the relationship between the amount of graphite powder added and the heat transfer enhancement is still unclear. As a result, in this investigation, we chose the paraffin with ceresin (PC) as the research object and experimentally studied the influence of different mass of graphite powder on the heat transfer performance of pure PC. Heat load was supplied by an electric heater. PC absorbs heat and melts, then transfers the heat to the circulating water. Temperature variation of PC material and water are compared with different mass of graphite powder.
The schematic of the test system is shown in Figure 1. The experimental apparatus includes heating system, water circulation system, data acquisition system and the thermal storage system. In the heating system, the heat load is provided by a thin film heater with the size of 100 mm × 30 mm × 6 mm. During the experiment, the heater is attached directly on the bottom of the organic glass box, and adjusted by altering the DC power output voltage imposed on it. The water circulation system consists of a pump, water pipe, and a flowmeter. The outer diameter of the pipe is 19 mm. The outer surface of the water pipe is covered with a foam insulation layer, with the thickness of 15 mm. The flow rate of water is 100.0 mL/min. In the data acquisition system, the temperature of fluid is measured using T-type thermocouples with the accuracy of ±0.5°C. Agilent Keysight DAQ970A is utilized to monitor and record the temperature at a time interval of every 2 minutes. In the thermal storage system, an organic glass box is utilized, with the size of 200 mm × 100 mm × 100 mm. The outside of the glass box is covered by a layer of foam insulation, with the thickness of 30 mm. The interior of the box is filled with phase change material, and for this study, paraffin with ceresin (PC) is chosen as the research object. PC type is No. 48 semi-refined paraffin wax with the melting point of 48°C–50°C. For the graphite powder, the particle size is 74 μm and the purity is 99%. There are five temperature measurement points in this experiment. T1 is temperature of the water tank outlet. T2 and T3 are temperature of the water inlet/outlet of the glass box. T4 and T5 are the temperature of the PC material inside the glass box. Detailed positions of the heater and the temperature measurement points inside the box are shown in Figure 2.
There are two sections in this investigation. In part one, the heat transfer performance of pure PC material is studied. The electric heating film provides heat to the system, which is then transferred to the PC material inside the acrylic box through conductive heat transfer on the wall. As the PC is heated, its temperature increases until reaching the melting point and gradually melts from solid to liquid. The high-temperature PC then transfers heat to the water through the pipe wall, achieving the purpose of heating the water. By measuring the temperature changes of water, the heat transfer efficiency of the system can be calculated.
Then in part two, graphite powder with different masses is added into the pure PC material, in order to compare the influence of graphite powder on the heat transfer efficiency. Before the start of the experiment, weigh different masses of graphite powder using an electronic scale, place it into fully melted PC material and stir evenly. Then start the experiment after the mixed material is naturally cooled to the room temperature. All the experimental steps are the same as in part one. Five cases are performed using the graphite powder of 10 g, 20 g, 30 g, 40 g and 50 g respectively.
The heat transfer efficiency can be obtained by:
Where QPC is the heat transferred to PC material and Q is the heat load supplied by the electric heater.
The heat transferred to PC material can be calculated as:
Where cPC is specific heat capacity, which is taken as 2.0 J/(g∙°C) in this experiment; mPC is the quality of PC material, g; ∆TPC is the temperature difference during the heating process, °C. In this study, ∆TPC is taken as
According to the standard of evaluation and expression of uncertainty in measurement (JJF 1059-2012), the uncertainty of temperature u(T) can be described as in Eq. 3:
Where a is the accuracy of the T-type thermocouples. k is the coverage factor, depending on the assumed probability distribution of the measured data. In this study, k is
Standard uncertainty of QPC can be calculated as in Eq. 4:
Heat load supplied to the whole system can be calculated by multiplying the current I and the voltage U, as shown in Eq. 5.
Standard uncertainty of the heat load can be calculated as in Eq. 6:
Where the accuracy grade of the ammeter and the voltmeter is δ = 0.5%. When the heat load is set to be 200W, the corresponding voltage and current values are U = 220V and I = 0.91A respectively. The ranges of the voltmeter and ammeter are U ′ = 250 V and I ′ = 3.0A respectively.
So, the uncertainty of heat transfer efficiency can be obtained as in Eq. 7:
Figure 3 shows the temperature variation of the pure PC material. At the beginning of the experiment, 10 min prior, the system temperature is relatively low, and the PC is in a solid state. From the 8th minute onwards, the temperature starts to rise rapidly. Due to the closer proximity of temperature measurement point T4 to the heating film, the heating rate and amplitude of T4 are higher than that of T5. The time it takes for T4 and T5 to reach the melting point is 12.6 min and 18.0 min, respectively. Then heat is stored in the form of latent heat. The PC material has a relatively low thermal conductivity, so before the phase transition occurs, heat is primarily transferred through conduction, while after melting, it is mainly transferred through convection. Therefore, after the 12th minute, the growth rate of T4 and T5 is much higher than that in the conduction period of the experiment.
Figure 4 shows the temperature variation of the circulating water. Within the first 2 minutes after the start of the experiment, the temperature of the circulating water almost remains constant. As can also be seen from Figure 3, the temperature of the PC material remains almost unchanged during this initial two-minute period, indicating that the heat transferred to the water during this stage can be neglected. By the end of the experiment, the temperature of the circulating water is raised by a total of 1.1°C. From this result, it can be concluded that the heating efficiency will not be very high if only pure PC material is used.
In this section of the experiment, different masses of graphite powder are added into the PC material to investigate the effect of graphite powder on the heat transfer performance of pure PC material. Temperature variation of PC material and the water are studied.
Figure 5, Figure 6, Figure 7, Figure 8, Figure 9 show the temperature variation of PC material with graphite powder of 10 g–50 g respectively. When a small amount of graphite powder is added (10 g and 20 g, Figure 5, Figure 6), the promotion of heat transfer process by graphite powder is not very significant, and there is not much change in the temperature inside the PC material. The time it takes for T4 and T5 to reach the melting point remains essentially unchanged.
Figure 7 shows the temperature variation of PC material with graphite powder of 30 g. When adding 30 g of graphite powder, T5 shows a significant improvement and the heating rate rapidly increases from the 10th minute, nearly 2 minutes earlier than that without graphite powder added. The time it takes for T4 and T5 to reach the melting temperature shorten from 12.6 min and 18.0 min to 12.3 min and 17.2 min, respectively, with a reduction of 2.38% and 4.44%.
Figure 8, Figure 9 show the temperature variation of PC material with graphite powder of 40 g and 50 g. When enough graphite powder is added, the heat transfer performance of both T4 and T5 are greatly improved. The temperature value increases significantly, and the time required for rapid heating to begin is reduced to 8 min, which is nearly 4 min shorter than that without graphite powder adding. For the case of adding 40 g of graphite powder, the time it takes for T4 and T5 to reach the melting point shorten from 12.6 min and 18.0 min to 11.0 min and 14.9 min, respectively, with a reduction of 12.7% and 17.2%.
Figure 10 shows the time needed to reach the melting temperature of PC material with and without graphite powder added for the positions of T4 and T5 respectively. The results indicate the same trend that when the mass of graphite powder is below 30 g, the time required to reach the melting point decreases slightly; when the mass is 40 g or more, the time to reach the melting point rapidly decreases and remains relatively stable. Additionally, when the mass of graphite power is more than 40 g, the temperature results almost remain unchanged, seen in Figure 8, Figure 9. Based on the results of temperature and time, we can come to a conclusion that for 500 g of pure PC material, the maximum amount of graphite powder required for promoting heat transfer is around 40 g.
FIGURE 10. Comparison of time needed to reach the melting temperature with and without graphite powder: (A) T4; (B) T5.
In this section, we investigate the temperature variation of circulating water with different mass of graphite powder added into the pure PC material. Figure 11 shows the temperature comparison results. It can be observed that as the quality of graphite powder increases, the outlet temperature of the circulating water, T3, continuously increases from 15.7°C to 16.2°C. The temperature difference between the inlet and outlet, i.e. T2 and T3, has increased from 1.1°C to 1.6°C.
In this section, the heat transfer efficiency is studied to investigate the influence of graphite powder, which can be obtained from Eqs 1, 2, 5. The total time is 20 min. The temperature difference change of paraffin is taken as the average of T4 and T5. Figure 12 shows the comparison results of
All of the above results show that when the quality of phase change materials remains constant, there is a maximum limit to the amount of graphite powder that can be added to enhance heat transfer efficiency and accelerate the melting of phase change materials. The practical implications of our findings highlight the potential for thermal conductive materials, such as graphite, in heat storage systems to improve heat transfer performance, thereby providing valuable insights for designers.
In this investigation, we experimentally studied the effect of graphite powder on the heat transfer process of PC material. 500 g of PC was chosen, with 10 g–50 g graphite powder added in five experiments. Water was adopted as the circulation fluid. Temperature variation of PC and water were recorded. Heat transfer efficiency and heating rate of PC were compared with and without graphite powder added. In conclusion, this study provides valuable insights into the thermal performance of latent heat storage system, which are described as follows:
(1) Graphite powder has excellent thermal conductivity. When it is added to PC material, it can enhance the thermal conductivity of PC, thereby reducing the time it takes to reach the melting temperature and increasing the melting rate of the PC. In this experiment, for 500 g of PC, a maximum reduction of 17.2% in the time needed to reach the melting temperature is obtained with 40 g of graphite powder.
(2) The effect of graphite powder on improving heat transfer efficiency is limited. In this experiment, 500 g of PC material has the highest heating rate and amplitude when the graphite powder addition is 40 g.
(3) Graphite powder promotes the melting rate of PC material. For the enhancement of heat transfer efficiency, the effect is not significant due to the small change of temperature difference of PC at the beginning and end of the experiment.
Findings of this experimental study could be utilized to enhance heat transfer efficiency in applications such as heat pump drying unit, greenhouse energy storage in modern agriculture, solar energy storage utilization technology, and so on. In this investigation, particle size of the graphite powder was not considered. However, it is known that when paraffin wax is completely melted into a liquid state, during the convective heat transfer process, the graphite powder particles contribute to the enhancement of heat transfer by inducing turbulent disturbances. Thus, we suggest more detailed investigations on graphite powder such as particle size and microstructure, in order to obtain a deeper understanding about the mechanism of graphite powder enhancing paraffin heat transfer.
The original contributions presented in the study are included in the article/Supplementary Material, further inquiries can be directed to the corresponding author.
YZ: Conceptualization, Funding acquisition, Project administration, Resources, Supervision, Validation, Visualization, Writing–review and editing. GL: Data curation, Software, Writing–original draft. XZ: Formal Analysis, Methodology, Validation, Writing–original draft. HW: Investigation, Validation, Writing–review and editing.
The author(s) declare financial support was received for the research, authorship, and/or publication of this article. This research was supported by the Natural Science Foundation of Shandong Province under Grant No. ZR2020QE195.
The authors declare that the research was conducted in the absence of any commercial or financial relationships that could be construed as a potential conflict of interest.
All claims expressed in this article are solely those of the authors and do not necessarily represent those of their affiliated organizations, or those of the publisher, the editors and the reviewers. Any product that may be evaluated in this article, or claim that may be made by its manufacturer, is not guaranteed or endorsed by the publisher.
Aljehani, A., Razack, S. A. K., Nitsche, L., and Al-Hallaj, S. (2018). Design and optimization of a hybrid air conditioning system with thermal energy storage using phase change composite. Energy Convers. Manag. 169, 404–418. doi:10.1016/j.enconman.2018.05.040
Chakraborty, A., Noh, J., Mach, R., Shamberger, P., and Yu, C. (2022). Thermal energy storage composites with preformed expanded graphite matrix and paraffin wax for long-term cycling stability and tailored thermal properties. J. Energy Storage 52, 104856. doi:10.1016/j.est.2022.104856
Curry, J., Harris, N., and White, N. (2023). Thermal energy harvesting from slow variations in environmental temperatures. Micromachines (Basel). 14, 1202. doi:10.3390/mi14061202
Dhandayuthabani, M., Jegadheeswaran, S., Vijayan, V., and Godwin Antony, A. (2020). Investigation of latent heat storage system using graphite micro-particle enhancement. J. Therm. Anal. Calorim. 139, 2181–2186. doi:10.1007/s10973-019-08625-7
Dong, Q., Sun, B., Dong, Z., Tian, Y., Zhu, H., and Yuan, G. (2022). Construction of highly efficient heat conduction channels within expanded graphite/paraffin phase change composites and their thermophysical properties. Energy Rep. 8, 7071–7084. doi:10.1016/j.egyr.2022.05.118
Gao, Y., Wang, Y., Liu, S., Zhong, S., Yu, M., and Wang, C. (2023). Preparation of paraffin wax-modified floating aluminum powder and composite coating with infrared stealth and wave-transparent function. Mat. Sci. Eng. B 295, 116611. doi:10.1016/j.mseb.2023.116611
Gorbacheva, S. N., Makarova, V. V., and Ilyin, S. O. (2021). Hydrophobic nanosilica-stabilized graphite particles for improving thermal conductivity of paraffin wax-based phase-change materials. J. Energy Storage 36, 102417. doi:10.1016/j.est.2021.102417
Homlakorn, S., Velmurugan, K., Suksri, A., and Wongwuttanasatian, T. (2023). Comparative study for photovoltaic cooling using metal mesh inserted eutectic phase change material enclosure. Case Stud. Therm. 45, 103024. doi:10.1016/j.csite.2023.103024
Huang, Z., Luo, Z., Gao, X., Fang, X., Fang, Y., and Zhang, Z. (2017). Preparation and thermal property analysis of Wood’s alloy/expanded graphite composite as highly conductive form-stable phase change material for electronic thermal management. Appl. Therm. Eng. 122, 322–329. doi:10.1016/j.applthermaleng.2017.04.154
Jayaprabakar, J., Aravind Kumar, J., Parthipan, J., Karthikeyan, A., Anish, M., and Joy, N. (2023). Review on hybrid electro chemical energy storage techniques for electrical vehicles: technical insights on design, performance, energy management, operating issues & challenges. J. Energy Storage 72, 108689. doi:10.1016/j.est.2023.108689
Liu, C., Wu, Z., Garg, A., Qin, Y., Mei, G., and Lv, C. (2023). Experimental investigation for dynamic characteristics of paraffin-graphite based CPCM (composite phase change material) amended expansive soil under dry-wet cycles. Constr. Build. Mat. 404, 133170. doi:10.1016/j.conbuildmat.2023.133170
Liu, S., Fei, X., Zhang, B., Zhao, H., and Wan, M. (2022). Expanded graphite/paraffin/silica phase change composites with high thermal conductivity and low permeability prepared by the solid-state wet grinding method. Sol. Energy Mat. Sol. C 236, 111484. doi:10.1016/j.solmat.2021.111484
Lu, B., Zhang, Y., Sun, D., and Jing, X. (2021b). Experimental investigation on thermal properties of paraffin/expanded graphite composite material for low temperature thermal energy storage. Renew. Energy 178, 669–678. doi:10.1016/j.renene.2021.06.070
Lu, B., Zhang, Y., Sun, D., Yuan, Z., and Yang, S. (2021a). Experimental investigation on thermal behavior of paraffin in a vertical shell and spiral fin tube latent heat thermal energy storage unit. Appl. Therm. Eng. 187, 116575. doi:10.1016/j.applthermaleng.2021.116575
Lu, S., Jia, Y., Liang, B., Wang, R., Lin, Q., and He, Z. (2023). Optimal design and thermal performance study of a two-stage latent heat thermal energy storage technology for heating systems. Appl. Therm. Eng. 232, 121073. doi:10.1016/j.applthermaleng.2023.121073
Matos, R., and Pala, N. (2023). A review of phase-change materials and their potential for reconfigurable intelligent surfaces. Micromachines 14, 1259. doi:10.3390/mi14061259
Mohammadreza Naghdi Bazneshin Borji, M., and Gholami, R. (2023). Numerical Investigation of phase transition in different latent heat storage systems in the presence of natural convection and porous media. Case Stud. Therm. 50, 103450. doi:10.1016/j.csite.2023.103450
Paul, A., Holy, F., Textor, M., and Lechner, S. (2022). High temperature sensible thermal energy storage as a crucial element of Carnot Batteries: overall classification and technical review based on parameters and key figures. J. Energy Storage 56, 106015. doi:10.1016/j.est.2022.106015
Rahmalina, D., Abdu Rahman, R., and Ismail, (2022). Increasing the rating performance of paraffin up to 5000 cycles for active latent heat storage by adding high-density polyethylene to form shape-stabilized phase change material. J. Energy Storage 46, 103762. doi:10.1016/j.est.2021.103762
Sheikholeslami, M. (2022). Analyzing melting process of paraffin through the heat storage with honeycomb configuration utilizing nanoparticles. J. Energy Storage 52, 104954. doi:10.1016/j.est.2022.104954
Sheikholeslami, M., and Jafaryar, M. (2023). Performance of energy storage unit equipped with vase-shaped fins including nanoparticle enhanced paraffin. J. Energy Storage 58, 106416. doi:10.1016/j.est.2022.106416
Wang, X. L., Li, B., Qu, Z. G., Zhang, J. F., and Jin, Z. G. (2020). Effects of graphite microstructure evolution on the anisotropic thermal conductivity of expanded graphite/paraffin phase change materials and their thermal energy storage performance. Int. J. Heat. Mass Transf. 155, 119853. doi:10.1016/j.ijheatmasstransfer.2020.119853
Waseem Aftab, , Ali, U., Shi, J., Yuan, K., Qin, M., and Zou, R. (2021). Phase change material-integrated latent heat storage systems for sustainable energy solutions. Energy Environ. Sci. 14 (8), 4268–4291. doi:10.1039/D1EE00527H
Yang, Li, Fu, Z., Xue, M., Shao, Z., Li, Y., and Zhu, Q. (2022). Experimental study on preparation and thermal storage properties of expanded graphite/paraffin wax as a shape-stabilized phase change material. Energy Rep. 8, 324–331. doi:10.1016/j.egyr.2022.09.149
Yang, X., Li, C., Ma, Y.Fu, He, C., Hu, Z., and Xie, J. (2023). High thermal conductivity of porous graphite/paraffin composite phase change material with 3D porous graphite foam. Chem. Eng. J. 473, 145364. doi:10.1016/j.cej.2023.145364
Zeng, J. L., Chen, Y. H., Shu, L., Yu, L. P., Zhu, L., and Song, L.-B. (2018). Preparation and thermal properties of exfoliated graphite/erythritol/mannitol eutectic composite as form-stable phase change material for thermal energy storage. Sol. Energy Mat. Sol. Cells. 178, 84–90. doi:10.1016/j.solmat.2018.01.012
Zhang, S., Feng, D., Shi, L., Wang, Li, Jin, Y., and Tian, L. (2021). A review of phase change heat transfer in shape-stabilized phase change materials (ss-PCMs) based on porous supports for thermal energy storage. Renew. Sust. Energy Rev. 135, 110127. doi:10.1016/j.rser.2020.110127
Zheng, X., Xie, N., Chen, C., Gao, X., Huang, Z., and Zhang, Z. (2018). Numerical investigation on paraffin/expanded graphite composite phase change material based latent thermal energy storage system with double spiral coil tube. Appl. Therm. Eng. 137, 164–172. doi:10.1016/j.applthermaleng.2018.03.048
Keywords: heat storage technology, phase change materials, paraffin, graphite powder, heat transfer efficiency
Citation: Zhao Y, Li G, Zhang X and Wu H (2023) Experimental research on the effect of graphite on heat transfer performance of a latent heat storage system. Front. Energy Res. 11:1321088. doi: 10.3389/fenrg.2023.1321088
Received: 13 October 2023; Accepted: 04 December 2023;
Published: 29 December 2023.
Edited by:
Karunesh Kant, Virginia Tech, United StatesReviewed by:
Hakeem Niyas, Rajiv Gandhi Institute of Petroleum Technology, IndiaCopyright © 2023 Zhao, Li, Zhang and Wu. This is an open-access article distributed under the terms of the Creative Commons Attribution License (CC BY). The use, distribution or reproduction in other forums is permitted, provided the original author(s) and the copyright owner(s) are credited and that the original publication in this journal is cited, in accordance with accepted academic practice. No use, distribution or reproduction is permitted which does not comply with these terms.
*Correspondence: Yuanyuan Zhao, eXl6aGFvQGxkdS5lZHUuY24=
Disclaimer: All claims expressed in this article are solely those of the authors and do not necessarily represent those of their affiliated organizations, or those of the publisher, the editors and the reviewers. Any product that may be evaluated in this article or claim that may be made by its manufacturer is not guaranteed or endorsed by the publisher.
Research integrity at Frontiers
Learn more about the work of our research integrity team to safeguard the quality of each article we publish.