- 1Pingdingshan Tianan Coal Mining Co., Ltd., Pingdingshan, China
- 2School of Resources and Environment, Henan Polytechnic University, Jiaozuo, China
- 3Collaborative Innovation Center of Coalbed Methane and Shale Gas for Central Plains Economic Region, Jiaozuo, China
Affected by geology and mining, a certain number of low-yield wells will appear after a period of production in coalbed methane wells, and technical repairs are urgently needed to restore their production capacity to the maximum. Therefore, it is of great significance to establish a reasonable and feasible theoretical standard to evaluate the workover priority of CBM wells for the efficient utilization of CBM resources. From the perspectives of technical feasibility and economic rationality, eight key indicators that affect the cost performance of CBM well workover are screened. Combining the entropy value method and the TOPSIS comprehensive ranking method, the surface coalbed methane well repair priority entropy value-TOPSIS comprehensive evaluation model was constructed, and the surface coalbed methane well repair priority evaluation was carried out by taking 9 surface coalbed methane wells that urgently needed to be repaired in a mine as the evaluation objects. The evaluation results show that among the economic indicators, the average gas production per meter in the 30 days before the coal bed methane well was stopped and the cumulative gas production per meter before the stop had a relatively high weight, which were 29.68% and 13.83% respectively, This shows that in coalbed methane well workover operations, the long-term gas production potential of the coalbed methane well and the gas production capacity when disturbed by harmful factors are the decisive factors affecting the priority of coalbed methane well workover; Among the technical indicators, the degree of casing deformation and the depth of the coalbed methane well have a relatively high weight, accounting for 11.34% and 9.90% respectively, This shows that the smaller the deformation of the wellbore casing and the shallower the depth of the coalbed methane well, the higher the priority of the workover of the coalbed methane well; The ranking of the production recovery rates of the three coalbed methane wells in the Pingdingshan mining area after workover operations is consistent with the results output by the evaluation model, which proves that the evaluation model is reasonable for determining the priority of workovers for damaged wellbores; This evaluation model can provide a theoretical reference for small and medium-sized coalbed methane development companies to determine the priority of workovers.
1 Introduction
China’s coal production and consumption are the first in the world, and the amount of coal resources is the third in the world after the United States and Russia. (LH et al., 2020). As a clean energy associated with coal, coalbed methane has great development potential and strategic economic value. According to the survey, by the end of 2019, China’s cumulative proven coalbed methane geological reserves reached 658.6 billion m3 (SUN et al., 2021). In recent years, with the support of national science and technology projects such as the 12th Five-Year Plan ' and national industrial development policies, CBM exploration and development work has achieved great results in technology application and industrial development scale (QIN, 2021; HUANG et al., 2022; JIANG et al., 2022; ZHANG et al., 2023). Data show (LC et al., 2021): By the end of 2020, a total of 21,217 CBM wells have been constructed in China, including 19,540 vertical wells and 1,677 horizontal wells.
However, due to the influence of in-situ stress (WJ et al., 2022), hydraulic fracturing (DAI et al., 2022), reservoir structure (ZHOU et al., 2019; ML et al., 2021), coal body structure (XZ, 2017) and other factors, the low gas production efficiency of coalbed methane wells caused by the deformation and damage of wellbore casing has become one of the problems that restrict the production of surface coalbed methane wells for a long time. In the process of coalbed methane development, a certain number of coalbed methane wells will be deformed and damaged. However, as well workover operations are supporting measures for drilling projects in the process of coalbed methane resource development, the industry pays little attention to the engineering problems in well workover operations, Current research on well workovers mainly focuses on workover equipment (LIU et al., 2016; HAN et al., 2017), workover tools (LI et al., 2012; Tao, 2015), and workover technology (TONG et al., 2018) under high water content, low permeability, ultra-deep, and ultra-high pressure reservoir conditions. Large coalbed methane development companies have complete engineering supporting tools and can complete the repair work of large quantities of damaged wellbores in a short period (Lei et al., 2020). However, small and medium-sized coalbed methane development enterprises lack complete well workover equipment and tools, and do not have the conditions to operate multiple well workover equipment at the same time. Therefore, they mostly determine the repair plan for damaged wellbores based on empirical methods, that is, giving priority to repairing coalbed methane wells with low damage or high production. During the development of coal-bed methane in the Pingdingshan mining area, we found that coal-bed methane wells with low degree of damage still had poor gas production after the workover work was completed, Coalbed methane wells with high output are characterized by high workover difficulty and long workover period. Under the constraints of budget and construction period, the empirical method will reduce production efficiency to a certain extent and cause economic losses to the enterprise. Therefore, establishing a reasonable and feasible evaluation model to determine the priority of CBM well repair is of great significance for small and medium-sized CBM development enterprises to reduce costs and increase efficiency.
The current mainstream evaluation methods include subjective methods and objective methods. As the two most commonly used subjective evaluation methods, the analytic hierarchy process (LEE, 2015; CHEN et al., 2022) and the fuzzy comprehensive evaluation method (WEN, 2008; ZHANG et al., 2021) have the advantages of wide evaluation range and strong flexibility, and are mostly used in finance, environment, agriculture and other fields. However, the subjective method completely relies on the subjective consciousness of the evaluator in terms of index weighting and quantitative processing of qualitative indicators. The academic level of the evaluator will directly affect the accuracy of the evaluation results. For the same evaluation object, different evaluators may even arrive at completely different evaluation results. Unlike the subjective method, the conclusions drawn through the objective method are entirely based on sample data and are not affected by the subjective consciousness of the evaluator. Meanwhile, different objective evaluation methods have different requirements for the number of samples, and the evaluator needs to choose an appropriate objective evaluation method for the evaluation object. As an objective evaluation method for solving multi-objective decision-making problems, TOPSIS has strong operability in its application and has low requirements on sample size. For evaluation objects with small sample size, TOPSIS can calculate relatively accurate ranking results (CHEN, 2019; SILVA and de ALMEIDA, 2020; CHEN, 2021; WANG et al., 2022).
In view of this, this article combines the case of Pingdingshan surface coalbed methane development, determines evaluation indicators around technical feasibility and economic rationality, and combines the entropy value method and the TOPSIS comprehensive ranking method, a surface coalbed methane well repair priority evaluation model is constructed to provide a theoretical reference for small and medium-sized coalbed methane development enterprises to determine the well repair priority.
2 Priority evaluation index system for workover of surface coalbed methane wells
Based on the field exploration and data collection, 8 key first-level indicators are determined around the two aspects of technical feasibility and economic rationality, so as to construct the evaluation index system of surface CBM well repair priority, as shown in Figure 1.
2.1 Technical feasibility
(1) Deformation degree of casing and screen C1
Due to the strong geological structure changes in China’s CBM production areas and the transformation of artificial reservoirs, some production casings of CBM wells are deformed, corroded, damaged, and broken, which seriously affects the normal drainage of CBM wells (LIU et al., 2017). In addition, the casing repair is difficult, expensive, and the construction period is long, and the gas production effect of the repaired coalbed methane well is uncertain. Therefore, the greater the degree of casing deformation, the lower the priority of wellbore repair, and C1 is a negative index.
(2) Casing and screen deformation point C2
The number of casing and screen deformation points directly affects the construction difficulty and construction period, so C2 is a negative index.
(3) Well depth of CBM low production well C3
With the increase of the depth of coalbed methane low-yield wells, the in-situ stress and water pressure on the wellbore increase exponentially. At the same time, the stress form of deep strata is changeable, which increases the construction difficulty and construction period (GAO et al., 2022). Therefore, C3 is a negative indicator.
(4) Water inflow rate of low-yield CBM wells C4
Under the action of extrusion and shear stress, the failure of cementing quality will lead to casing deformation and dislocation, which will lead to groundwater inflow into the wellbore and cause well flooding (TONG et al., 2021). The influx of groundwater into the wellbore will hinder the exploration vision of the endoscope and increase the difficulty of wellbore repair construction. Therefore, C4 is a negative indicator.
2.2 Economic rationality
(1) Distance between CBM well and mining face C5
Working face mining will cause coal seam pressure relief, accelerate gas desorption, promote the development of coal seam cracks, and increase gas migration channels (TIAN et al., 2015). When the mining face advances to the position of the coalbed methane well, the overlying strata on the coal mining face collapses, and the gas desorbed from the coal seam migrates to the fracture zone, thus promoting the production of the coalbed methane well (XU et al., 2022). Therefore, the closer the CBM well is to the mining surface, the higher the priority of wellbore repair should be, and C5 is a positive index.
(2) The average cost per meter of CBM wells C6
This index is mainly used to characterize the repair cost of low-yield CBM wells, and the corresponding repair cost of low-cost CBM wells is lower. Under the limited budget, the low cost CBM well repair priority is higher, so it is the C6 negative index.
(3) Accumulated gas production per meter before stopping mining C7
This index is mainly used to characterize the lasting gas production capacity of coalbed methane wells. The higher the index value, the higher the priority of wellbore repair. C7 is a positive indicator.
(4) The average gas production per meter in 30 days before stopping mining C8
The index is used to characterize the gas production capacity of coalbed methane wells after suffering damage factors. The higher the index value, the higher the priority of wellbore repair. C8 is a positive indicator.
3 Construction of entropy-TOPSIS evaluation model
3.1 Entropy method to determine the objective weights of indicators
1) The original data of y indexes of x samples are used to construct the initial evaluation matrix A (YANG et al., 2022). In this article, x is the 9 coalbed methane wells that need to be evaluated, y is the evaluation indicators C1-C8, and a11 is the value of the indicator C1 corresponding to the first coalbed methane well.
2) The range method is used to standardize the initial evaluation matrix to obtain the matrix
For the positive indicators that the greater the partial value, the better the impact on the evaluation results, the standardized formula is:
On the contrary, the formula for the standardization of negative indicators is:
3) According to the definition of information entropy, the information entropy acquisition formula of a set of data is:
4) Calculate the index weight
The weight of the y index is:
3.2 Entropy-TOPSIS quantitative evaluation model
TOPSIS (Technique for Order Preference by Similarity to Ideal Solution)is a ranking method introduced by C.L.Hwang and K.Yoon in 1981. Its idea stems from the discriminant problem in multivariate statistical analysis and aims to determine the final solution from limited alternatives (XZ and JS, 2019). This method finds the optimal solution (ideal solution) and the worst solution (negative ideal solution) of the scheme from the original matrix, and then calculates the Euclidean distance between each scheme and the optimal solution and the worst solution to obtain the corresponding relative proximity. If there is a scheme that is closest to the ideal solution and far away from the negative ideal solution, the scheme is the best solution. The calculation steps are as follows.
(1) Construct the initial matrix
Suppose that there are n evaluation targets S1, S2, …… Sn, and each target has m evaluation indexes D1, D2 …… Dm, then the matrix S is constructed:
(2) Weighted normalized decision matrix
Because the units and evaluation criteria of each evaluation index are not uniform, matrix F is obtained by standardizing the evaluation indexes according to Formula 2 to Formula 3. The weighted normalized decision matrix refers to the column vector of the normalized matrix F multiplied by the index weight Wnm obtained by the entropy method, and the matrix U is obtained. Unm = Wnm*Fnm, can be expressed as:
(3) Determining positive and negative ideal points q+ and q-
In the decision matrix U, the vector composed of the maximum elements of each column is the positive ideal point q+; the vector composed of the minimum elements of each column is called a negative ideal point q−;
(4) Calculate the distance D+ and D− from each definition point ui to the ideal solution.
where, the smaller D+ indicates the closer to the positive ideal solution; the smaller the D−, the closer to the negative ideal solution.
(5) Calculate the closeness Ki
In the formula, the closeness degree Ki of the evaluation object reflects the degree that the overall index of the evaluation object is close to the positive ideal solution, and the value range is between 0 and 1.
4 Entropy-TOPSIS evaluation model engineering application and verification
Nine surface coalbed methane wells in a mine are surface coalbed methane extraction wells built in the same batch. All nine wells are mining wells, among which # 1, # 2, # 3, # 4, # 5, # 8, and # 9 are vertical wells, # 6 and # 7 are horizontal wells. Affected by the damage factors, the gas production of 9 wells was greatly reduced. The daily gas production data of 9 wells 50 days before the gas production drop are shown in Figure 2.
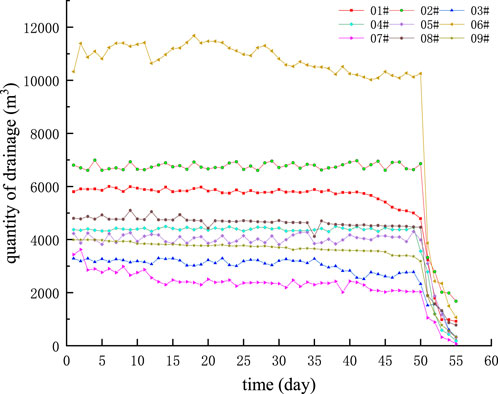
FIGURE 2. Gas production data of 9 low-yield coalbed methane wells in the 50 days before the sudden drop in production.
4.1 Entropy method to calculate index weight
In this paper, the original data of 9 surface coalbed methane wells that need to be repaired urgently are collected, and the specific index data are shown in Table 1.
Indicator C1 is a qualitative indicator, which is quantified using the expert scoring method. The processed indicator data is shown in Table 2.
The index data in Table 2 are standardized according to Eqs 2, 3, and the output results are shown in Table 3.
Using MATLAB software, the data in Table 3 are processed according to Formula 4 to Formula 7, and the objective weights of each index are output. The output results are shown in Table 4.
4.2 Entropy-TOPSIS evaluation model engineering example application
The quantified original index data (Table 2) are standardized according to Formula 2 to Formula 3 to obtain matrix F.
The matrix U is obtained by weighting the data of matrix F and the index weight W obtained by entropy method.
After substituting the data of matrix U into MATLAB software and calculating according to Eqs 10–12, the evaluation results are output. The details of the evaluation results are shown in Table 5.
4.3 Entropy-TOPSIS evaluation model engineering verification
Based on the above evaluation results, 9 low-production coalbed methane wells were repaired in sequence. At present, the repair work of 02#, 06#, and 04# has been completed one after another, and the daily gas production has recovered well. The well workover construction period and the gas production time after the well workover are shown in Table 6.

TABLE 6. 02#, 06#, 04# construction period and gas production time after completion of workover operations.
This article collected the gas production data of 02#, 06#, and 04# after completing the workover operations, and verified the accuracy of the evaluation model by comparing the production recovery ratio of each coalbed methane well. The gas production data of 02#, 06# and 04# wells after workover are shown in Figure 3.
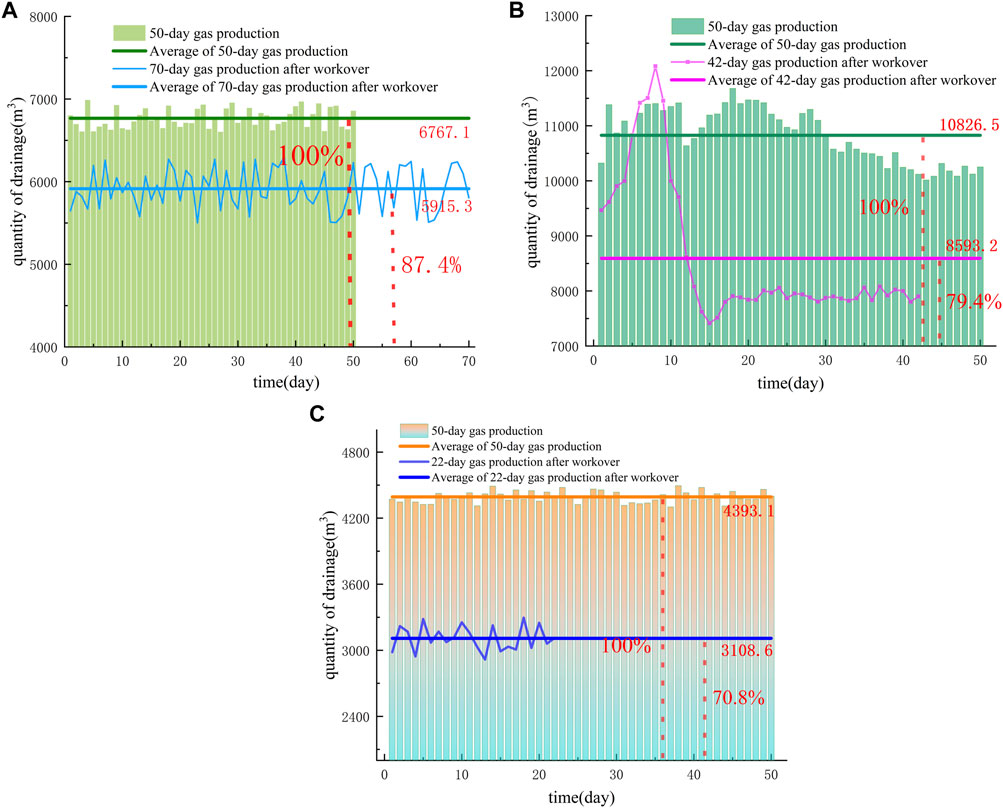
FIGURE 3. Gas production recovery data after workover of 02#, 06#, 04#. (A) Gas production recovery data after workover of 02#. (B) Gas production recovery data after workover of 06#. (C) Gas production recovery data after workover of 04#.
As can be seen from Figure 3, the average 50-day gas production of 02#, 06#, and 04# under normal production conditions are 6767.1 m3, 10,826.5 m3, and 4393.1 m3 respectively. The average daily gas production of 02#, 06#, and 04# after workover was 5915.3 m3, 8593.2 m3, and 3108.6 m3 respectively, and the gas production recovery rates reached 87.4%, 79.4%, and 70.8% respectively. The ranking of the extraction volume recovery rate is consistent with the ranking of the evaluation results in Table 5, which verifies the reliability of the workover priority evaluation model for surface coalbed methane low-yield wells built in this paper.
5 Conclusion
Based on the case of surface coalbed methane development in Pingdingshan Mining Area, this paper selects 8 key indicators that affect the priority of workover of low-yield surface coalbed methane wells, combines the entropy method and the TOPSIS comprehensive ranking method, a well workover priority evaluation model for low-yield surface coalbed methane wells was built. Nine low-yield ground coalbed methane wells in the Pingdingshan mining area were evaluated, and the following conclusions were drawn.
1) It was determined that the main factors affecting the priority of surface coal-bed methane well repair include 8 key indicators such as the deformation degree of casing and screen, and the deformation point of casing and screen, and based on this, an evaluation index system for the priority of surface coal-bed methane well repair was established;
2) According to the indicator weight results, among the economic indicators, indicators C7 and C8 account for 13.83% and 29.68% respectively relative to the weight of the target layer, this shows that in coalbed methane well workover operations, long-term gas production capacity and short-term gas production capacity after interference due to harmful factors are the decisive factors in determining the priority of coalbed methane well workover. Among the technical indicators, the weights of indicators C1 and C3 are 11.34% and 9.90% respectively, this shows that the deformation degree of the wellbore casing and the burial depth of the coalbed methane well are the key factors that determine the priority of workover of the coalbed methane well.
3) A quantitative evaluation model for the workover priority of surface coal-bed methane wells was constructed, and the engineering application was carried out with 9 surface coal-bed methane wells to be repaired in the Pingdingshan mining area. The evaluation results show that the workover priorities of the 9 surface coalbed methane wells are as follows: 02# > 06#>04# > 08#>01# > 05#>09# > 07#>03#. The gas production recovery rates of 02#, 06#, and 04# that completed workover operations on site were 87.4%, 79.4%, and 70.8%, respectively. The order of recovery rates is consistent with the order of the workover priority evaluation results, which verifies the reliability of the evaluation model.
4) The workover priority evaluation model for surface coalbed methane low-yield wells constructed in this paper can provide theoretical reference for small and medium-sized coalbed methane development companies in well workover operations.
Data availability statement
The original contributions presented in the study are included in the article/Supplementary material, further inquiries can be directed to the corresponding author.
Author contributions
YL: Writing–review and editing, Resources, Software, Supervision. LZ: Writing–original draft, Data curation, Formal Analysis, Software. RL: Methodology, Supervision, Writing–review and editing. XN: Investigation, Funding acquisition, Writing–review and editing.
Funding
The author(s) declare financial support was received for the research, authorship, and/or publication of this article. This work was financially supported by the National Natural Science Foundation of China (Grant No. 42072189).
Conflict of interest
Author YL was employed by the Pingdingshan Tianan Coal Mining Co., Ltd.
The remaining authors declare that the research was conducted in the absence of any commercial or financial relationships that could be construed as a potential conflict of interest.
Publisher’s note
All claims expressed in this article are solely those of the authors and do not necessarily represent those of their affiliated organizations, or those of the publisher, the editors and the reviewers. Any product that may be evaluated in this article, or claim that may be made by its manufacturer, is not guaranteed or endorsed by the publisher.
Abbreviations
CBM, Coalbed methane; TOPSIS, Technique for Order Preference by Similarity to an Ideal Solution.
References
Chen, P. Y. (2019). A novel coordinated TOPSIS based on coefficient of variation. MATHEMATICS 7 (7), 614. doi:10.3390/math7070614
Chen, P. Y. (2021). Effects of the entropy weight on TOPSIS. EXPERT Syst. Appl. 168, 114186. doi:10.1016/j.eswa.2020.114186
Chen, X. F., Fang, Y. T., Chai, J. Y., and Xu, Z. (2022). Does intuitionistic fuzzy analytic hierarchy process work better than analytic hierarchy process? Int. J. FUZZY Syst. 24 (2), 909–924. doi:10.1007/s40815-021-01163-1
Dai, Q., Lh, Y., Cc, Y., Z, W., and M, Y. (2022). Influence of hydraulic fracturing on casing deformation of horizontal wells in shale gas wells. Mach. Des. Res. 38 (03), 118–121+126. doi:10.13952/j.cnki.jofmdr.2022.0164
Gao, X., Sun, H., Wang, Y., Ni, X., and Deng, Z. (2022). In-situ stress field of deep coal reservoir in Linxing area and its control on fracturing crack. Meitan Kexue Jishu/Coal Sci. Technol. (Peking) 50 (8), 140–150. doi:10.13199/j.cnki.cst.MCQ20-039
Han, W., Li, T., Wang, D., Ming, E., and Huang, S. (2017). Study and application of snubbing technology for low pressure gas well. Jakarta: SPE/IATMI Asia Pacific Oil & Gas Conference and Exhibition.
Huang, Z., Li, G., Yang, R., and Li, G. (2022). Review and development trends of coalbed methane exploitation technology in China. Meitan Xuebao/Journal China Coal Soc. 47 (9), 3212–3238. doi:10.13225/j.cnki.jccs.SS22.0669
Jiang, W., Chai, J., Zhang, Q., Zhang, P., and Jiang, Z. (2022). Key technology progress of surface extraction project deployment based on coordinated development of CBM and coal. Meitan Kexue Jishu/Coal Sci. Technol. (Peking) 50 (12), 50–61. doi:10.13199/j.cnki.cst.mcq22-25
Liu, C., Jiang, X., Dai, J., Wu, M., and Chen, R. (2021). Overview of the domestic and foreign oil and gas industry development in 2020 and outlook for 2021. Int. Pet. Econ. 29 (01), 28–37.
Lee, S. (2015). Determination of priority weights under multi-attribute decision-making situations: AHP versus fuzzy AHP. J. Constr. Eng. Manag. 141 (2). doi:10.1061/(ASCE)CO.1943-7862.0000897
Lei, Q., Yiliang, L. I., Tao, L. I., Li, H., Guan, B., Bi, G., et al. (2020). Technical status and development direction of workover operation of PetroChina. Petroleum Explor. Dev. 47 (1), 161–170. doi:10.1016/S1876-3804(20)60015-5
Li, H., Zhao, S., Lin, A., Li, F., Li, L., and Dai, X. (2020). Analysis on world energy supply & demand in 2019—based on BP statistical review of world energy (2020). Nat. Gas Oil 38 (06), 122–130. doi:10.3969/j.issn.1006-5539.2020.06.020
Li, Y. L., Li, T., Gao, X. Q., Weiye, H., Xl, B. I., and Qiang, C. (2012). Study and application of solid expandable tubular in patching the casing below the previously installed tubular. Oil Drill. Prod. Technol. 34 (6), 106–108.
Liu, Y. K., Chang, L. P., Zhou, F. B., Tan, D., Liu, L., Kang, J., et al. (2017). Numerical modeling of gas flow in deformed well casing for the prediction of local resistance coefficients pertinent to longwall mining and its engineering evaluation. Environ. EARTH Sci. 76 (20), 686. doi:10.1007/s12665-017-7003-0
Liu, H., Ming, E., Han, W., Li, T., and Huang, S. (2016). An evaluation method of snubbing units in China. Abu Dhabi: Abu Dhabi International Petroleum Exhibition & Conference.
Mao, L., Lin, H., Yu, X., and Mai, Y. (2021). Influence of fault slip on casing deformation of horizontal well in shale gas reservoir. Fault-Block Oil Gas Field 28 (06), 755–760.
Qin, Y. (2021). Strategic thinking on research of coal measure gas accumulation system and development geology. Meitan Xuebao/Journal China Coal Soc. 46 (8), 2387–2399. doi:10.13225/j.cnki.jccs.CB21.0719
Silva, D., and de Almeida, A. T. (2020). Sorting with TOPSIS through boundary and characteristic profiles. Comput. INDUSTRIAL Eng., 141. doi:10.1016/j.cie.2020.106328
Sun, Q., Zhao, Q., Jiang, X., Mu, F., Kang, L., Wang, M., et al. (2021). Prospects and strategies of CBM exploration and development in China under the new situation. Meitan Xuebao/Journal China Coal Soc. 46 (1), 65–76. doi:10.13225/j.cnki.jccs.2020.1579
Tao, L. I. (2015). Solid expandable tubular patching technique for high temperature and high-pressure casing damaged wells. Petroleum Explor. Dev. 42 (3), 374–378. doi:10.1016/S1876-3804(15)30032-X
Tian, F., Qin, Y., Liang, Y., and Chang, X. (2015). The application research of overlying strata stress field and gas flow field coupling mechanism under the long vertical distance coal seam group mining conditions. Caikuang yu Anquan Gongcheng Xuebao/Journal Min. Saf. Eng. 32 (6), 1031–1036. doi:10.13545/j.cnki.jmse.2015.06.026
Tong, H., Liu, Z., Zhang, H., Zhang, P., Deng, C., Ren, X, et al. (2021). Theory and method of temporary macrofracture plugging to prevent casing deformation in shale gas horizontal wells. Nat. Gas. Ind. 41 (5), 92–100. doi:10.3787/j.issn.1000-0976.2021.05.010
Tong, Z., Ma, B., Wei, R., Liao, C., Liu, S., Huang, P., et al. (2018). The hybrid completion and stimulation technology combining sleeves with bridge plugs: a case history in Ordos Basin. China, Brisbane: SPE Asia Pa-cific Oil and Gas Conference and Exhibition.
Wang, Y. M., Liu, P. D., and Yao, Y. Y. (2022). BMW-TOPSIS: a generalized TOPSIS model based on three-way decision. Inf. Sci. 607, 799–818. doi:10.1016/j.ins.2022.06.018
Wen, K. L. (2008). A MATLAB toolbox for grey clustering and fuzzy comprehensive evaluation. Adv. Eng. Softw. 39 (2), 137–145. doi:10.1016/j.advengsoft.2006.12.002
Wu, J., Zhang, X., Li, J., Zhang, H., Lian, W., and Liu, P. (2022). Influence of in-situ stress variation on casing load during multi-stage fracturing of shale gas well. Petroleum Tubul. Goods Instrum. 8 (02), 23–29. doi:10.19459/j.cnki.61-1500/te.2022.02.005
Xu, C., Wang, K., Guo, L., Yuan, L., Li, X., and Li, X. (2022). Fractal evolution law of overlying rock fracture and seepage caused by mining and its engineering application. Yanshilixue Yu Gongcheng Xuebao/Chinese J. Rock Mech. Eng. 41 (12), 2389–2403. doi:10.13722/j.cnki.jrme.2022.0128
Xz, A., and Js, B. (2019). A combined fuzzy DEMATEL and TOPSIS approach for estimating participants in knowledge-intensive crowdsourcing. Comput. Industrial Eng. 137, 106085. doi:10.1016/j.cie.2019.106085
Xz, L. (2017). Reason analysis on casing deformation of coalbed methane well in southern qinshui basin of Shanxi Province. China Coalbed Methane 14 (4), 32–34.
Yang, M., Zhu, L., Quan, X., Xu, J., Liu, M., and Zhang, T. (2022). Construction and application of feasibility evaluation model for gas extraction in goafs of abandoned coal mines. Meitiandizhi Yu Kantan/Coal Geol. Explor. 50 (7), 107–117. doi:10.12363/issn.1001-1986.21.11.0686
Zhang, W. P., Li, B., Liu, Z. J., and Zhang, B. (2021). Application of improved fuzzy comprehensive evaluation method in karst groundwater quality evaluation: a case study of Cen gong county. EARTH Sci. Inf. 14 (2), 1101–1109. doi:10.1007/s12145-021-00611-8
Zhang, Q., Jw, P., Jz, B., Sun, S., Li, B., Du, X., et al. (2023). Present situation and technical research progress of coalbed methane surface development in coal mining areas of China. Coal Geol. Explor. 51 (01), 139–158. doi:10.12363/issn.1001-1986.22.05.0400
Keywords: coalbed methane, workover, entropy method, TOPSIS, evaluation model
Citation: Li Y, Zhu L, Lv R and Ni X (2024) Construction and application of workover priority evaluation model for surface coalbed methane low production wells based on Entropy-TOPSIS. Front. Energy Res. 11:1309777. doi: 10.3389/fenrg.2023.1309777
Received: 08 October 2023; Accepted: 26 December 2023;
Published: 15 January 2024.
Edited by:
Rizwan Rasheed, Government College University, PakistanReviewed by:
Bingyuan Hong, Zhejiang Ocean University, ChinaChen Wang, University of Illinois at Urbana-Champaign, United States
Copyright © 2024 Li, Zhu, Lv and Ni. This is an open-access article distributed under the terms of the Creative Commons Attribution License (CC BY). The use, distribution or reproduction in other forums is permitted, provided the original author(s) and the copyright owner(s) are credited and that the original publication in this journal is cited, in accordance with accepted academic practice. No use, distribution or reproduction is permitted which does not comply with these terms.
*Correspondence: Lin Zhu, emxocHUyMDAxQDE2My5jb20=