- Ningxia Tiandi Benniu Industrial Group Co., Ltd., China
Coal and gas outburst is one of the main factors affecting the safe and efficient production of coal mines. With the increase of mining depth and mining speed, the dynamic phenomena of coal and gas outburst will become more and more serious. Through the study of various outburst prevention measures in the pre-drainage gas area such as surface drilling, bedding (directional) drilling, and cross-layer drilling, combined with the coal seam occurrence and mining technology of the West Mine Area, a feasible regional pre-drainage comprehensive outburst prevention mode suitable for the characteristics of the 3# coal seam in the West Mine Area has been obtained. This mode is based on pre-pumping of surface drilling first, directional long borehole along the reservoir and pre-pumping of cross-zone borehole, which provides reliable guarantee for safe and efficient production in outburst well area.
1 Introduction
As one of the main energy sources supporting the development of China’s national economy, coal is the “ballast stone” to ensure energy security (Liang et al., 2022; Sun X. Y. et al., 2023; Ma et al., 2023). Coal consumption will account for 56% of total energy consumption in 2021. And in the future for a long period of time, the status of coal as the main energy will not change (Liang et al., 2023; Su et al., 2023; Wu et al., 2023). In the process of coal mining, gas disaster is still one of the main disasters in coal mines, which is easy to cause large-scale casualties (Wu et al., 2022; Zou et al., 2023b). Coal and gas outburst is one of the typical gas disasters in coal mines (Cheng et al., 2022; Zheng et al., 2022; Zhao et al., 2023a), and with the mining operation of coal seam extending to the depth year by year (Xie et al., 2022; Ye et al., 2022; 2023; Xie et al., 2023), the permeability of coal seam gradually decreases with the increase of ground stress, gas pressure and temperature, which increases the risk of coal mine gas outburst (Liu and Li, 2016; Pan et al., 2020; Song et al., 2022). In recent years, although our defense technology has made remarkable progress, prominent security accidents still occur from time to time (Liu et al., 2021; Ran et al., 2023a; Zhang C. L. et al., 2023). At present, China has formed two “four-in-one” comprehensive anti-outburst technology systems, which are mainly regional measures and supplemented by local measures. Among them, the application of local anti-outburst technical measures such as hydraulic fracturing, hydraulic punching and coal seam water injection is limited due to the large engineering amount, long outburst elimination period and technical difficulty (Xiao et al., 2022; Zhang et al., 2022; Zou et al., 2023a; Zhao et al., 2023b). Regional outburst prevention measures mainly include mining protective layer and pre-pumping coal seam gas. Mining the protective layer is conducive to improving the air permeability of coal, improving the gas extraction effect, and preventing outburst. Wang et al. (2014) discussed the key problem of determining the reasonable protection range in the mining protective layer, established the gas seepage field equation and the deformation field of coal and rock mass, and determined the pressure relief protection range in the mining of the upper protective layer by analyzing the example of Nantong mining area. Yuan and Xue. (2014) developed a method to reduce outburst range of protective layer according to the content of coal seam gas. Wang et al. (2013) analyzed the influence of factors such as coal seam inclination, coal seam spacing, pressure relief Angle and coal pillar on the mining of the protective layer, proposed solutions to the existing technical problems such as the mining scope of the protected work being greater than the protection scope of the protected layer, and verified the effectiveness of the proposed method with examples. However, due to the great difference of address in different regions of China, the occurrence conditions of coal seams are different, and the thickness of the protective layer of coal seams is not consistent, it is difficult to obtain the ideal effect (Wang et al., 2022; Zou et al., 2022).
The pre-extraction of coal seam gas is an effective method for controlling gas outburst disasters in coal mines and is currently the primary technical means used by the coal mining industry (Zhao et al., 2022; Liu S. M. et al., 2023; Zhang B. C. et al., 2023). This process involves drilling and extracting gas from the coal seam in advance of the excavation face production (Liao et al., 2021; Liu Y. B. et al., 2023). By pre-pumping the gas in the coal seam, the gas pressure and content within the coal seam can be reduced (Li et al., 2020; Chen et al., 2023). This allows the release elasticity of the coal body to achieve pressure relief and permeability improvement, thereby preventing coal and gas outbursts. In China, the main methods of gas pre-pumping include surface well pre-pumping, borehole pre-pumping, and borehole pre-pumping along stratum (Wang et al., 2023). Zhang Y. J. et al. (2023) combined the above - and underground gas extraction technologies, and proposed an up-and-down joint anti-outburst adaptation model of short - distance coal groups with “hole group cover-coordinated extraction” and long - distance coal groups with “enhanced anti-permeability - progressive extraction”. Han and Li. (2020) proposed an outburst prevention method in which the protection layer was drilled underground and the protected layer was extracted by surface Wells, and the method was successfully applied in Zhujixi Mine. By measuring gas parameters, theoretical analysis, numerical simulation and engineering practice, Wang et al. (2021) proposed a dual pressure relief anti-outburst model for the relief field of deep roadway, and verified that the model could achieve the effect of anti-outburst by drilling through strata and pumping gas from floor rock roadway through the application in Qujiang Coal Mine. In order to solve the poor outburst elimination effect of bedding drilling in coal mining face, Gao et al. (2019) took Xieqiao Coal Mine as the test object, and adopted the hydraulic fracturing technology of bedding drilling to improve the outburst elimination effect (Tan et al., 2021; Huang et al., 2023a). By considering the parameters such as hydraulic fracturing radius, drilling parameters, water injection pressure, water injection volume and holding time, the gas extraction efficiency was improved (Huang et al., 2023b; Tan et al., 2023).
In conclusion, while there has been extensive research on the technical measures of regional outburst prevention in pre-drainage coal seam gas from various perspectives, studies on the coordinated extraction of surface well drilling, cross-layer drilling, and bedding drilling to achieve regional outburst prevention are limited. It remains challenging to establish a comprehensive regional pre-drainage outburst prevention model that encompasses surface well pre-drainage, underground cross-layer drilling pre-drainage, and bedding drilling pre-drainage. Therefore, this paper focuses on the west well area of Sihe Mine. Through studying various pre-drainage gas regional outburst prevention measures such as surface drilling, bedding (directional) drilling, and cross-layer drilling, it aims to develop a comprehensive regional pre-drainage outburst prevention model to ensure the safe and efficient extraction of coalbed methane.
2 Overview of the research area
Sihe Mine, located in the northwest of Jincheng City, Shanxi Province, falls under the administrative jurisdiction of Jincheng City and spans Qinshui, Yangcheng, and Zezhou counties. The geographical coordinates are 35°30′51″N to 35°36′11″N and 112°27′07″E to 112°40′54″E. The western well area covers 56.27 km2. The mine field comprises three layers: 3#, 9#, and 15#, with a total thickness of 10.32 m and a recoverable coal-bearing coefficient of 7.6%. The 3# coal seam is the primary seam, with a thickness ranging from 4.45 m to 8.75 m and an average of 6.31 m. The coal seam structure is relatively simple, and the entire area is stable and recoverable. The total geological coal reserves in the western well area amount to 690 million tons, including 450 million tons of 3# coal, 50 million tons of 9# coal, and 190 million tons of 15# coal. The total recoverable reserves are 370 million tons, including 220 million tons of 3# coal, 300 million tons of 9# coal, and 120 million tons of 15# coal.
The coal-bearing strata in this mine field belong to the Shanxi Formation of the Lower Permian System and the Taiyuan Formation of the Upper Carboniferous System. These strata contain between 11 and 21 layers of coal, with an average total coal seam thickness of 11.49–13.87 m. The stable mineable coal seams are the 3# and 15# seams, with the 9# seam being locally mineable. The dip angle of the 3# coal seam ranges from 2° to 10°, typically around 5°, and the average thickness of this coal seam is 6.31 m. The characteristics of mineable coal seams in the middle of the minefield are shown in Table 1. The 3# coal seam is anthracite with low-medium ash, ultra-low sulfur, medium phosphorus, high calorific value, high ash fusion temperature, and high strength. It has good thermal stability, strong slagging characteristics, good theoretical clean coal recovery, and high fixed carbon content.
The western well area employs a mechanical extraction partition ventilation mode. Currently, the mine has established independent ventilation systems in the eastern and western well areas. The total intake air volume in the western well area is approximately 24,645 m³/min, while the total return air volume in the mine is about 25,320 m³/min. The effective air volume in the mine is around 22,920 m³/min, with an effective air volume rate of approximately 93%. The equal area hole measures 8.62 m2.
The gas content of raw coal in the 3# coal seam of the western well area ranges from 15.04 to 21 m³/t, with a residual amount of 3.52 m³/t. According to the mine gas level and carbon dioxide emission identification results from 2009, the absolute gas emission of the western well area is 342.27 m³/min (with an air exhaust gas volume of 45.28 m³/min and an underground gas drainage volume of 296.99 m³/min). The gas drainage volume of the ground well in the western well area is 132 m³/min. On 20 May 2007, an outburst occurred in the #6 contact roadway between Xihui and Xijiao in the western well area of Sihe Mine. The 3# coal seam in the western well area of Sihe Mine is an outburst coal seam, making the western well area an outburst mine.
Currently, a permanent ground drainage pumping station has been established in the Xifeng well industrial site in the western well area of Sihe Mine. The station is equipped with six CBF-710 A water ring vacuum pumps, all dedicated to pre-drainage of coal seam gas. With the four openings and two preparations, the extraction capacity can reach 400 N.m³/min. At present, the extraction capacity has achieved 315.37 N.m³/min. The absolute gas emission in the western well area of Sihe Mine is 363.07 m³/min, and the gas drainage rate in the western well area is 86.86%.
3 Regional outburst prevention technology
The regional outburst prevention measures for pre-drainage coal seam gas in the western well area primarily involve two types of pre-drainage: surface and underground. Underground pre-drainage further includes three methods: bedding (directional) drilling, bedding (ordinary) drilling, and cross-layer drilling (Sun D. L. et al., 2023).
3.1 Gas extraction and outburst prevention technology in surface well area
In the Chengzhuang Mine, which is adjacent to the western well area, a study was conducted on the arrangement method of surface drilling wells. Through the use of Computational Fluid Dynamics (CFD) simulation technology, the gas flow and distribution law in the underground goaf were studied and understood. This knowledge was then used to determine a reasonable arrangement for surface drilling.
Figure 1 illustrates the Computational Fluid Dynamics (CFD) prediction of gas distribution in the goaf when ground drilling is not in operation. The simulation results reveal that a significant amount of oxygen enters the goaf, with the oxygen concentration exceeding 12% on the intake roadway side, 300 m behind the working face. Oxygen accumulation is observed 150 m behind the working face on the return air lane side, where the maximum gas concentration in the goaf can reach 80%. These findings suggest that high concentrations of goaf gas can be extracted by positioning ground goaf gas extraction boreholes 20–70 m from the return airway. This understanding is crucial for optimizing the design of ground goaf gas extraction boreholes, designing goaf gas extraction systems, and achieving improved extraction results (Ran et al., 2023b).
Figure 2 illustrates the predicted gas and oxygen flow field distribution in the goaf of the working face when a negative pressure of 40 kPa is applied to the surface borehole orifice under different borehole combinations. The distribution is completely opposite to the gas flow field distribution and oxygen distribution.
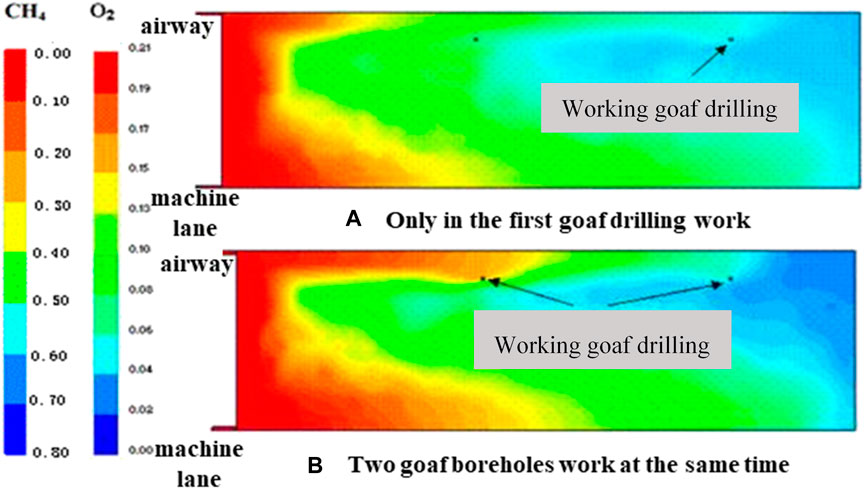
FIGURE 2. Gas distribution diagram of goaf under different extraction conditions in working face. (A) Only in the first goaf drilling work; (B) Two goaf boreholes work at the same time.
Based on the factors influencing regional outburst prevention and the results of CFD numerical simulation analysis, we have preliminarily determined the principles for selecting well locations and drilling spacing for outburst prevention in surface drilling areas.
1) Drilling location
Surface drilling should not only be arranged along the axis of the anticline and the wings of the anticline and syncline, but should also be organized within the geological structure zone. Additionally, ground wells should be considered for placement at distances ranging from 20 to 70 m from the return airway.
2) Drilling spacing
Based on the numerical simulation results and the analysis of surface drilling and drainage data in the eastern well field, we have preliminarily determined that the surface drilling spacing used for outburst prevention in the pre-drainage area in the normal area is 300 m × 300 m. Meanwhile, the surface drilling spacing in the geological structure zone is 150 m × 150 m.
3.2 Outburst prevention technology in pre-drainage gas area of bedding borehole
3.2.1 Bedding drilling pre-drainage gas area drilling design
The number of holes and the design depth for each drilling field should be determined based on the production connection and the length of the working face. Field tests suggest that the most economical design length for the extraction unit is between 300 and 400 m. The end of each borehole should extend beyond the roadway of the replacement working face or the replacement drilling field by at least 30 m. Each borehole is designed with 2–3 branches, with a horizontal vertical distance between branches of 12–15 m. The main hole depth for bedding drilling is generally within 400 m, as construction drilling speed slows significantly beyond this depth, leading to frequent sticking phenomena and low drilling efficiency. Figure 3 provides a schematic diagram of the bedding directional drilling arrangement in the western well area.
3.2.2 Outburst prevention technology of bedding drilling in heading face of coal roadway
1) Design of outburst prevention measures for pre-drainage boreholes in heading face
Preparation for excavation on the 1301 working face began in June 2006. The gas content of the coal seam in this area is between 18 and 20 m3/t. To ensure safe excavation, the target residual gas content of the coal seam should be less than 8 m3/t. In the early stage of excavation, an MK drilling rig was primarily used to construct strip drainage boreholes in the roadway of the first mining face. Later, extraction work was organized by combining bedding ordinary boreholes and directional boreholes. According to predictions from gas extraction numerical simulation software, when the borehole spacing is 1 m and the drilling footage per ton of coal is 0.11 m, the pre-drainage period can meet the standard within 12 months. To improve the efficiency of roadway excavation while ensuring safety, drilling hole parameters on the working face were designed as follows: drilling hole spacing is 1 m, with 12 holes arranged in three rows, and drilling footage per ton of coal is 0.33 m. In addition to head-on arrangement, construction was also carried out on both sides of the roadway to strengthen extraction from pre-drainage drilling fields, with drilling parameters in these fields matching those of head-on drilling. The design also requires pre-drainage drilling to extend 15 m beyond the roadway’s contour line. According to predictions from gas extraction numerical simulation software, using the adjusted borehole design allows for a standard extraction time of 4 months.
2) Construction of outburst prevention measures for pre-drainage boreholes in heading face
The 1301 working face is the first mining face in the western well area. To reduce the gas content to less than 8 m3/t and improve the pre-drainage time of the working face before mining, it is crucial to safely penetrate the working face as soon as possible. This allows for pre-drainage of the working face gas by drilling along the working face. Therefore, when excavating the test roadway, we enhanced the parameters of drilling holes based on the original design. The specific layout parameters for various boreholes are presented in Table 2, and a schematic diagram of the boreholes is shown in Figure 4.
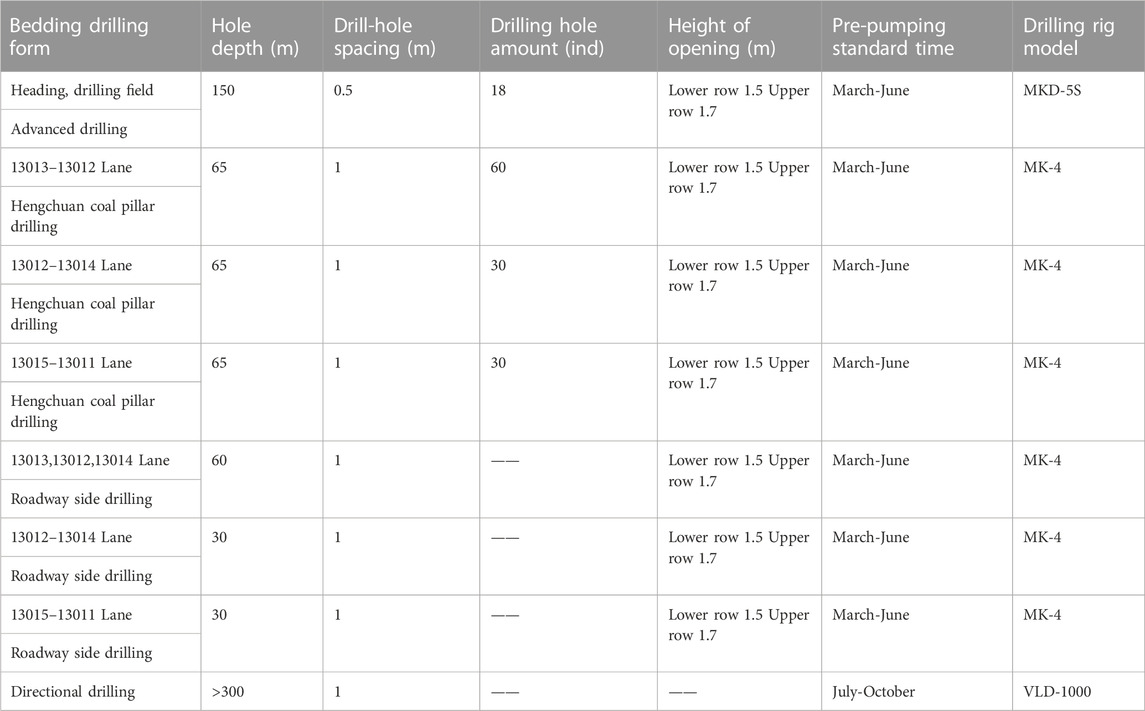
TABLE 2. Design and construction parameter table of outburst prevention engineering in bedding drilling area of heading face.
3.2.3 Outburst prevention technology of bedding drilling in first mining face
Based on the previous analysis, it is clear that the 1301 working face of the first mining face can adopt pre-drainage drilling spacing of 1 m, 2 m, 3 m, and 5 m. To determine the optimal pre-drainage drilling arrangement, these four different drilling arrangements are analyzed individually. Before mining the working face, the gas content of the coal seam is reduced to less than 8 m3/t and can meet the requirements of the annual output of the working face of 4 Mt/a. When the borehole spacing is 3 m and 5 m, it can meet the pre-drainage time of the working face for more than 17 months. Through comparison and selection, although the borehole engineering quantity is smallest when the borehole spacing is 5 m, considering the maximum reduction of coal seam gas content in the 1301 working face, a pre-drainage borehole is selected to be arranged with a spacing of 3 m.
3.3 Outburst prevention technology of pre-drainage gas area by cross-layer drilling
3.3.1 Drilling design of pre-drainage gas area of cross-layer drilling
Cross-layer boreholes in the western well area are arranged within the development roadway. The thickness of the rock roadway from the coal seam exceeds 24 m. Each drilling field is generally designed with three to six rows of boreholes, with each row containing 15–20 boreholes. The spacing between boreholes is 0.5 m, and boreholes are typically spaced 3–5 m apart. A drilling field is constructed every 30 m, with each drilling field covering the excavation range of 15 m coal roadways on both sides. The final hole of the drilling extends 20 m (horizontal projection distance) beyond the outer side of the design coal lane at the farthest end, controlling a coal body of 60 × 120 (m2) and a control coal volume of approximately 64,000 t. Currently, there are 45 cross-layer drilling fields in the western well area. The borehole diameter is primarily 94 mm. The ratio of borehole coal to rock holes is usually 1:3. The length of borehole per ton of coal is 0.103 m/t, with the length of coal hole per ton of coal being about 0.026 m/t. The cross-layer drilling design profile is shown in Figure 5.
3.3.2 Application of outburst prevention in pre-drainage gas area of cross-layer drilling
In the western well area, outburst prevention measures in the pre-drainage gas area of the cross-layer borehole were tested and applied during the eastern excavation of the return air roadway. The measured original gas content in the uncovered coal area averages approximately 17.56 m3/t, and the gas reserve is about 2.88 million m3, indicating that it is an outburst-dangerous area.
To reduce the gas content to less than 8 m3/t within 9 months, cross-layer drilling pre-drainage measures were implemented. Based on the predicted extraction effect of cross-layer drilling and the corresponding drilling engineering requirements, the 38# and 39# cross-layer drilling fields were arranged during construction when the distance from the uncovered coal was 37 m. The MKD-5 S drilling rig was used in the construction of cross-layer drilling. A total of 128 cross-layer drillings were designed and constructed, with a drilling quantity of 6600 m. The drilling control range extends 13 m outside the contour line of the roadway, starting from the coal uncovering point, and covers a range of 13 m to the east and west. The horizontal spacing of the final hole point of the borehole is 3 m, and the final hole point is located at 0.5 m in the roof of the 3# coal seam. The arrangement of boreholes for uncovering coal is shown in Figure 6, Figure 7, to Figure 8.
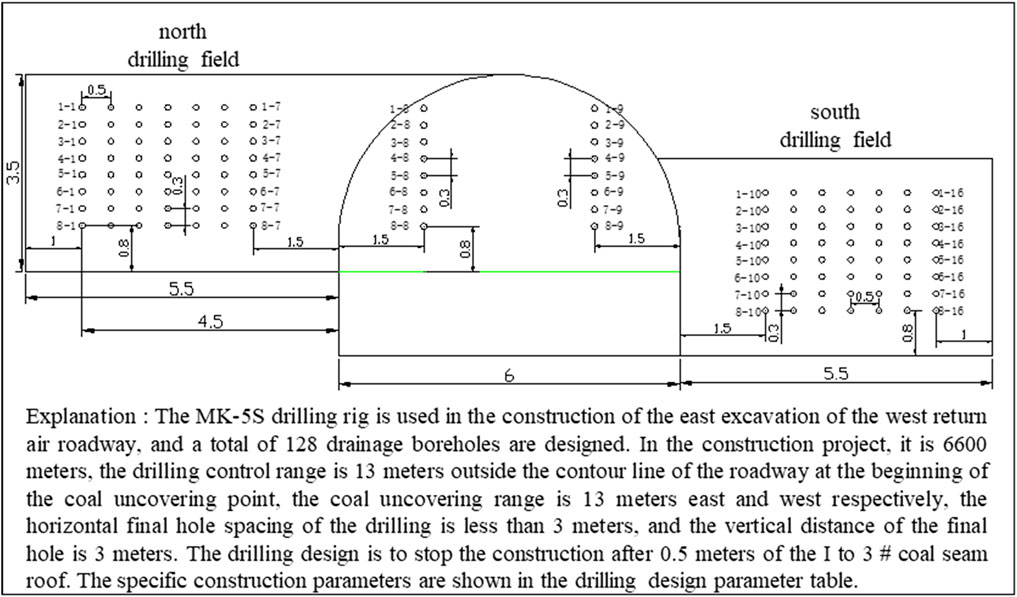
FIGURE 6. Schematic diagram of borehole section layout in east excavation of west return air roadway.
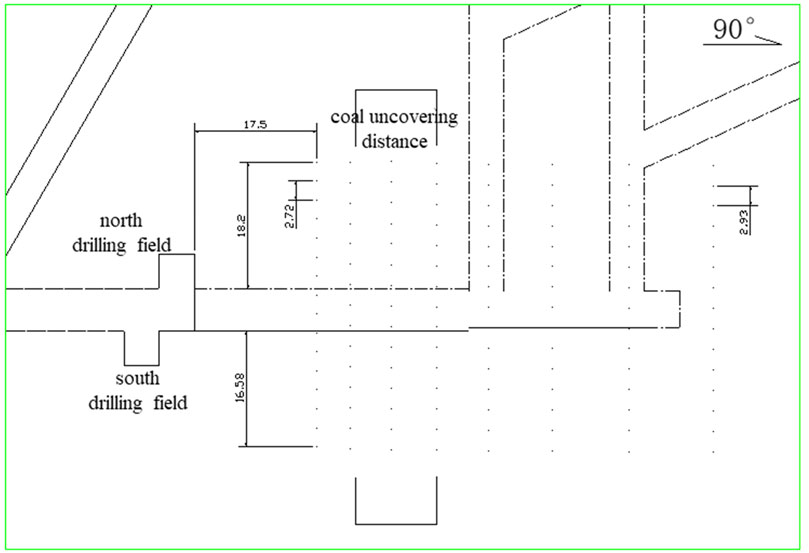
FIGURE 7. The schematic diagram of the final hole position of the east excavation coal uncovering borehole in the west return air roadway.
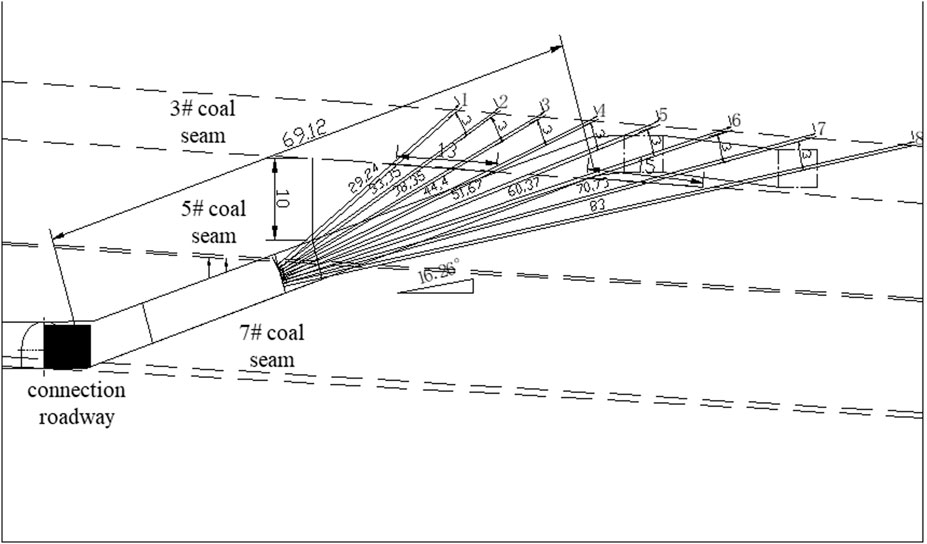
FIGURE 8. The schematic diagram of the borehole section of the east excavation of the west return air roadway.
4 Application effect of regional outburst prevention
4.1 Outburst prevention effect of bedding borehole pre-drainage
Before each excavation, the measured gas content is used to evaluate the pre-drainage effect on the coal in front of the excavation face (0–150 m in front of the excavation and 8–10 m outside the roadway contour line). When evaluating the measured residual gas content, a content test point is arranged every 20–30 m, and it is required that each test point be equidistant from the surrounding boreholes. Using the 13013 roadway as an example, we explain the layout of the test hole, the test results of residual gas content, and the verification results of the first mining face. The arrangement of pre-drainage effect content test boreholes in the excavation roadway of the first mining face is shown in Figure 9, and the measured results of residual gas content are presented in Table 3.
From the measured content data in Table 3, it can be seen that the residual gas content has been reduced to less than 8 m3/t before each excavation. This indicates that the measures implemented in the gas extraction area of the excavation working face are effective.
Residual gas content tests show that during the excavation process of five roadways, such as 13013 and 13014 in the first mining face, a strip area of 150 m advanced drilling and roadway side drilling is typically adopted to enhance extraction. After 3–6 months, the residual gas content in the control area can be reduced to less than 8 m3/t, thereby achieving the outburst prevention effect of the working face. After 7–10 months of pre-drainage, even under the condition of pre-drainage by directional drilling in the second half of the working face, the residual gas content of the coal roadway strip can also be reduced to less than 8 m3/t. It has been verified that after pre-drainage, the 13013 roadway is a non-outburst danger zone.
After confirming the effectiveness of the pre-drainage in the 1301 first mining face, the first regional verification was conducted within a 10 m range of the 1301 first mining face. The specific method was as follows: 13 verification boreholes using the drilling cuttings method were arranged every 15 m along the working face (excluding 10 m at the upper and lower outlet sections of the working face). The boreholes were arranged as much as possible in the soft layer, parallel to the mining direction of the working face. Starting from a depth of 2 m in each borehole, the S value of all drilling cuttings in a 1 m section was measured for each 1 m drilling, and coal drilling cuttings with a particle size of 1–3 mm discharged from the orifice were collected for each 2 m drilling. The K1 value of the gas desorption index of the drilling cuttings was measured. The critical value of the outburst verification index is: S = 6 kg/m, K1 = 0.5 mL/g.min1/2. The statistics of the verification index results at the incision are presented in Table 4.
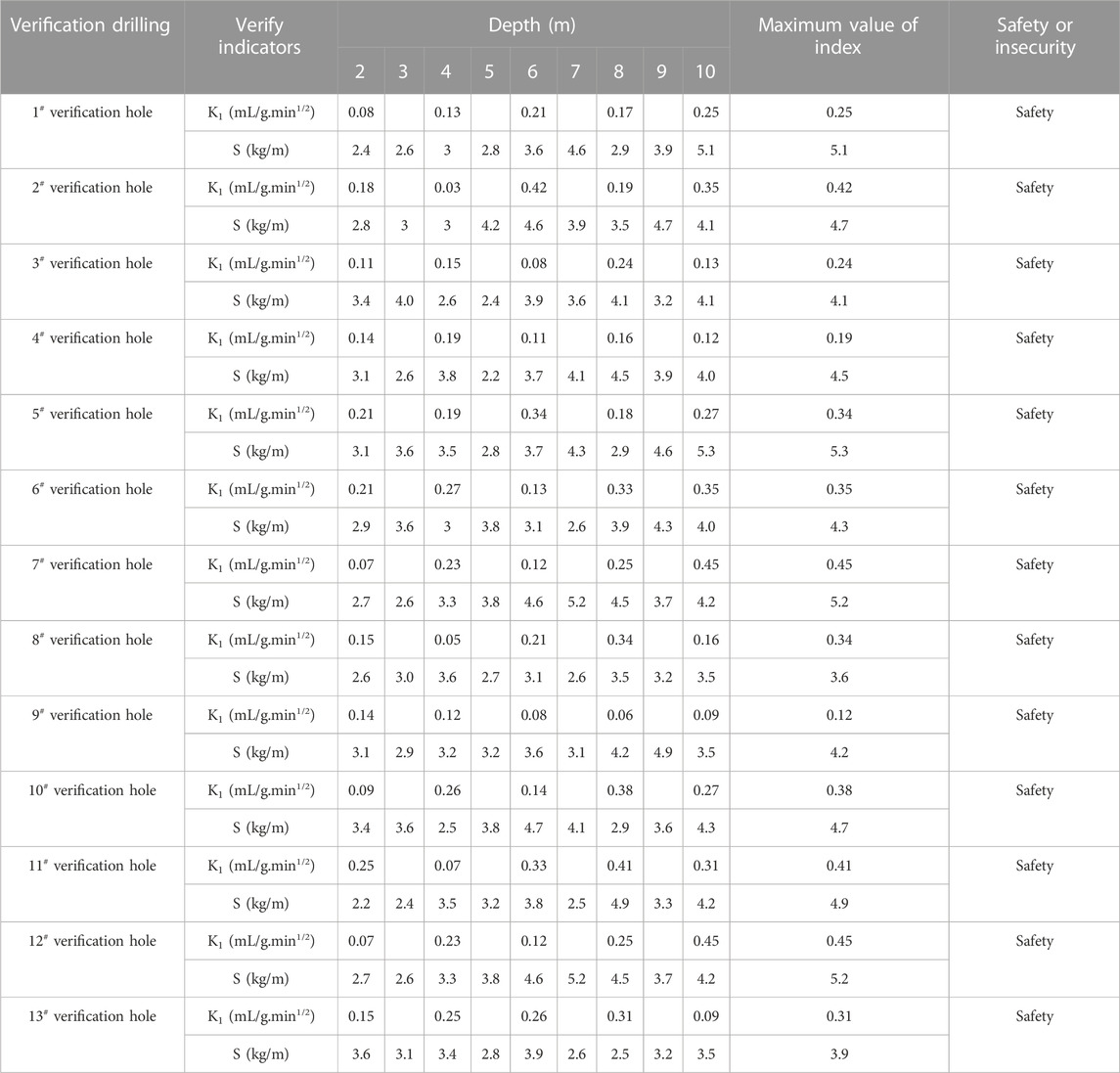
TABLE 4. Statistical table of verification results of drilling cuttings method index in open-off cut area of 1301 first mining face.
Based on the results presented in Table 4, the maximum values of K1 and S in the 13 verification boreholes are below the critical value. Additionally, there were no significant risk omens observed during the drilling construction. Therefore, the regional verification indicates that there is no significant danger zone within 10 m of the first mining face.
4.2 Effect of pre-drainage and outburst prevention of cross-layer drilling
In the eastern excavation and coal uncovering area of the western return air roadway, after 10 months of pre-drainage, the cumulative drainage volume of the drilling field is 1.87 million m3 according to the drainage volume statistics. The residual gas content is expected to be 6.16 m3/t. Therefore, a residual gas content test was conducted in this area with 13 test points. The layout of the test points covered a range of 1–8 m on the upper, middle, and both sides of the uncovered coal area. The results are presented in Table 5 below.
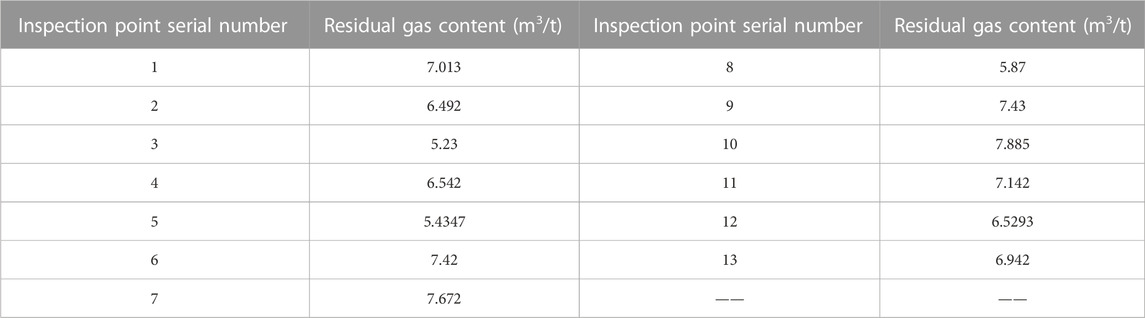
TABLE 5. The measured content results of the east excavation and uncovering coal area of the west return air roadway.
5 Regional outburst prevention mode in west well area
5.1 Construction of regional outburst prevention mode
Considering the characteristics of the 3# coal seam in the western well area, such as stable overall occurrence, hard coal quality, good gas permeability, high gas content, and favorable hole forming conditions for bedding drilling, we have combined the applicable conditions of three regional outburst prevention measures and their respective extraction characteristics. We preliminarily propose the following regional outburst prevention modes: prioritize regional outburst prevention of ground wells, implement regional pre-drainage and outburst prevention measures of ground drilling as far as possible in the conditional area, and implement regional pre-drainage and outburst prevention measures of bedding boreholes after underground development is revealed. In combination with the implemented regional measures of ground drilling, we ensure that the effect of regional outburst prevention measures before mining reaches the standard (directional drilling is mainly used in bedding drilling, supplemented by bedding ordinary long drilling in the blank area of directional drilling or areas where extraction and outburst prevention need to be strengthened). However, in the face of coal uncovering area and large geological structure area, when it is difficult to implement bedding drilling, we should adopt the outburst prevention measures of cross-layer drilling to carry out extraction and outburst prevention in the target area.
5.2 Comprehensive experimental study on regional outburst prevention measures
Based on the three measures of surface drilling, cross-layer drilling, and bedding drilling, three types of outburst prevention measures are comprehensively applied. These measures are tailored according to the specific pumping, excavation, mining time, and specific coal seam geological conditions in other working faces other than the first mining face in the first panel and the entire mining area in the second panel. This approach ensures that the advantages and characteristics of various measures are fully utilized. The specific performance is as follows:
1) In the 2301, 2302, and other working faces of the second panel, surface drilling is utilized in advance for coalbed methane mining and regional pre-drainage and outburst prevention. According to statistics, surface drilling in the western well area reduces the gas content by nearly 1 m3/t each year. Therefore, after 4–6 years of pre-drainage, the gas content in most areas of the second panel will be reduced to 16 m3/t or even less. This saves valuable time for the pre-drainage of bedding boreholes when later development and mining operations approach the area. At the same time, leveraging the ‘one well multi-purpose’ characteristic of ground drilling is conducive to preventing gas overrun accidents in the working face during mining.
For example, there are three surface drilling wells near the 2301 working face, and the pre-drainage time is 4–6 years on average. When the directional drilling pre-drainage is carried out in this area, the pre-drainage time of the bedding drilling is about 24 months, and the gas content can be reduced to less than 8 m3/t, which realizes the safe and rapid excavation of the open-off cut roadway. Compared with the surrounding gas occurrence conditions are similar, but there is no ground drilling pre pumping area, bedding drilling pre pumping time is usually more than half a year or even longer. Therefore, the pre-pumping of surface drilling creates conditions for the pre-pumping effect of underground outburst prevention measures to reach the standard in a relatively short time, which is conducive to the safe and efficient production of the mine.
2) In the rock roadways arranged close to the mining face, such as the current air intake roadway of the first panel of the west, the bottom of the Sanshuigou well, and the auxiliary transportation roadway of the west, cross-layer boreholes are evenly arranged. These cross-layer boreholes are used to pre-drain gas in adjacent coal roadway strips (such as 23011 roadway and 23015 roadway) or gas in the cross-cut area that may be exposed by the pre-draining roadway (such as the air intake and return roadway of the second panel of the west, and the auxiliary transportation roadway of the second panel of the west). According to investigations, after completion of cross-layer drilling construction in a 60 × 120 (m2) area in the western well area (where the gas content of raw coal is within 16 m3/t), when the coal hole is 0.026 m/t, an average of 18 months of pre-drainage can ensure that extraction in the area meets standards. This effectively ensures coal seam safety and creates a breakthrough for implementing large-scale pre-drainage and outburst prevention in subsequent stages.
As of January 2008, cross-layer drilling has been used to cover a total of 2,000 m in lanes 23011 and 23015. Through the pre-drainage of cross-layer drilling, the first mining of the 2301 working face in the second panel has been safely exposed. In addition, drilling holes were evenly arranged from the auxiliary transportation roadway in the western area, covering and pre-draining the entire strip of the first and second lanes of the return air in the western area. This has enabled the safe excavation of the two lanes, thereby creating conditions for improving the ventilation system in the western area.
3) In the exposed coal seam roadway working face, such as the 13015 roadway, 13014 roadway, 2301 open-off cut, and 23011 roadway, a large number of directional boreholes were constructed using kilometer directional drilling rigs. This allowed for modular extraction in the subsequent mining replacement working face section. The directional drilling module extraction not only controls the entire coal mining area but also manages all the unexcavated crossheadings related to the replacement working face. The gas in the excavation and mining area is reduced to below the critical index of outburst risk before excavation, creating favorable conditions for the safety and efficiency of later excavation and mining. According to application investigations, in underground areas where the gas content of raw coal is within 16 m3/t, the residual gas content in the area can typically be reduced to less than 8 m3/t after an average pre-drainage of 24 months by directional drilling.
During the safe tunneling process of the 23011 and 23015 roadways, the K1 verification index in this area did not exceed the standard even once, so no local supplementary measures were carried out.
5.3 Summary of complete set technology of regional outburst prevention measures in xixi well area
Through the extraction characteristics of three regional outburst prevention measures and the underground application research, we have gained an understanding of the applicable characteristics and field effects of various measures. Therefore, under the current coal seam gas occurrence conditions in the western well area, the complete set of technologies for regional pre-drainage and outburst prevention measures suitable for the western well area are as follows:
1) In areas where the coal seam gas content is greater than or equal to 16 m3/t, it is essential to implement surface drilling area pre-drainage and outburst prevention measures. This ensures that the coal seam gas content is less than 16 m3/t during underground development. In other coal seam areas, it is advisable to implement surface drilling area pre-drainage and outburst prevention measures as much as possible.
2) In areas where the coal seam gas content is less than 16 m3/t during development, it is advisable to implement bedding drilling area drainage outburst prevention measures underground. This should be done in conjunction with the implementation of surface drilling area measures to ensure that the mining area meets the standard for outburst prevention measures before mining. Bedding drilling, particularly directional drilling, should be prioritized. In areas where directional drilling is not possible or where drainage and outburst prevention need to be strengthened, ordinary long drilling can be used as a supplement.
When adopting progressive pre-drainage of bedding directional drilling, the drilling length should be at least 300–500 m, and the drilling field should move once every 300–500 m. The range of directional drilling cover control should include the front of the roadway excavation (>60 m), the entire block section of the succeeding coal mining face, and the three crossheading roadways on the other side of the succeeding working face. After reducing the coal body in the cover control range to 8 m3/t, safe excavation and mining can be achieved. The same progressive layout should be implemented to the next mining replacement surface in the new excavation roadway on the other side of the working face. This approach ensures a reasonable connection of the entire mine mining face.
3) In areas where geological structures make drilling construction difficult during coal uncovering, and in the main roadway of the coal seam floor, pre-pumping outburst prevention measures should be used through the layer drilling area. This ensures that regional outburst prevention measures meet mining standards before mining begins.
Uncovering coal area: When the cross-cut uncovers the coal seam in the coal uncovering area, cross-layer drilling must be used to prevent regional outbursts. This should continue until the outburst risk in the uncovered coal area is eliminated.
Open up the roadway area:According to the mine design, main development roadways such as the auxiliary transportation roadway in the west area of the west well area, the belt conveyor roadway, the north belt conveyor roadway in the west area, the north auxiliary transportation roadway in the west area, and the north return air roadway in the west area will be arranged in the rock stratum. Therefore, these rock roadways that will be constructed should be used for adjacent working faces (such as W23011 roadway and W23015 roadway), adjacent panel concentrated coal roadways (such as the auxiliary transportation roadway in the west second panel), and construction of the working face mining area. Cross-layer drilling is used for strip and section pre-drainage and outburst prevention.
Working face crossheading area: Under normal geological conditions of a coal seam, long-distance and large-range bedding drilling can be used for pre-drainage in crossheadings or coal roadways. However, when encountering special areas such as large faults, collapse columns, or increased soft layer thickness, it becomes difficult to construct bedding drilling holes and meet the requirements of regional control range. In such cases, a temporary rock roadway or rock drilling field should be constructed in the roof or floor. Cross-layer drilling should be carried out in the special area above the rock roadway (drilling field). By relying on the rock stratum as a safety barrier, the gas content in the special area is reduced to less than 8 m3/t, eliminating the regional outburst risk. Then, under the protection of local outburst prevention measures, return to the coal roadway to continue advancing until it is far from the influence range of special areas.
In summary, the application mode of regional outburst prevention measures in the west well area should be reasonably combined and fully utilized according to different gas content areas, different occurrence conditions, and different time and space requirements. This approach ensures that the regional outburst prevention measures in the west well area are more reliable, reasonable, and economical. It is more conducive to the balanced and coordinated development of ‘pre-drainage outburst prevention, tunneling, and mining’ under the existing production conditions, providing a strong guarantee for the efficient and safe production of the west well area.
6 Conclusion
Based on the mine conditions and relevant experience, this paper examines the outburst prevention measures of various pre-drainage gas areas such as surface drilling, bedding (directional) drilling, and cross-layer drilling. In conjunction with the coal seam occurrence and mining technology in the western well area, it is concluded that surface drilling pre-drainage is primary, underground bedding directional long drilling pre-drainage is the main approach, and cross-layer drilling pre-drainage is supplementary. This practical and feasible regional pre-drainage comprehensive outburst prevention mode, suitable for the characteristics of the 3# coal seam in the western well area, provides a reliable guarantee for the safe and efficient production of the outburst well area. The following conclusions are drawn:
1) In areas where the coal seam gas content is greater than or equal to 16 m3/t and not open, surface drilling area pre-drainage outburst prevention measures must be implemented. This ensures that when the mine and mining area main roadway development is underway, the control area’s coal seam gas content is reduced to 16 m3/t or less. In other areas where the coal seam gas content is less than 16 m3/t, surface drilling area pre-drainage outburst prevention measures should be implemented as far as possible. The surface drilling spacing for outburst prevention in the normal area is determined to be 300 m × 300 m, and in the geological structure zone, it is 150 m × 150 m. Other parameters are consistent with the CBM development of surface wells.
2) In the underground, regional outburst prevention measures are primarily implemented through the pre-drainage of gas using directional long boreholes along the bedding. These measures are combined with the implementation of surface drilling pre-drainage gas regional measures to ensure that the effect of regional outburst prevention measures meets mining standards before mining begins
3) During the excavation process of five roadways such as 13013 and 13014 in the first mining face, 150 m advance drilling and roadway side drilling are used to strengthen the extraction of the strip area. After 7–10 months of pre-drainage, the residual gas content of the coal roadway strip can also be reduced to less than 8 m3/t. It is verified that the 13013 roadway is a non-outburst danger zone after pre-drainage, and the research has formed an outburst prevention mode for the pre-drainage area of the directional long borehole along the strata under different conditions. Through the arrangement of drilling cuttings method to verify the drilling, it is verified that there is no outburst danger zone within 10 m of the first mining face, and an outburst prevention mode for the pre-drainage area of the directional long drilling along the mining face under different parts is formed.
4) In the area where the rock roadway uncovers coal and geological structures cause difficulties in the construction of bedding drilling, as well as in the main roadway control area in the mining area located in the coal seam floor rock layer, cross-layer drilling area pre-drainage and outburst prevention measures should be adopted. This ensures that regional outburst prevention measures meet mining standards before mining begins in the extraction area.
Data availability statement
The original contributions presented in the study are included in the article/supplementary material, further inquiries can be directed to the corresponding author.
Author contributions
PZ: Writing–original draft, Writing–review and editing.
Funding
The author(s) declare that no financial support was received for the research, authorship, and of this article.
Conflict of interest
Author PZ was employed by Ningxia Tiandi Benniu Industrial Group Co., Ltd.
Publisher’s note
All claims expressed in this article are solely those of the authors and do not necessarily represent those of their affiliated organizations, or those of the publisher, the editors and the reviewers. Any product that may be evaluated in this article, or claim that may be made by its manufacturer, is not guaranteed or endorsed by the publisher.
References
Chen, Z. H., Zou, Q. L., Gao, S. K., Zhan, J. F., Chen, C. M., Ran, Q. C., et al. (2023). Long-term evolution of overlying rock fractures in mined-out areas and its effect on gas flow conductivity. Fuel 353, 129213. doi:10.1016/j.fuel.2023.129213
Cheng, L., Xu, J., Peng, S. J., Qin, L., Yan, F. Z., Bai, Y., et al. (2022). Influence of different coal seam gas pressures and their pulse characteristics on coal-and-gas outburst impact airflow. Nat. Resour. Res. 31 (5), 2749–2767. doi:10.1007/s11053-022-10087-y
Gao, S., Mou, J. S., and Yang, H. M. (2019). Permeability enhancement technology of hydraulic fracturing of bedding drilling borehole in outburst coal seam. Min. Saf. Environ. Prot. 46 (04), 92–94. In Chinese.
Han, Q. S., and Li, S. Q. (2020). Engineering practice of combined outburst prevention for distant coalseam groups in west zhuiji coalmine. Energy Technol. Manag. 45 (04), 16–17. In Chinese.
Huang, L. K., He, R., Yang, Z. Z., Tan, P., Chen, W. H., Li, X. G., et al. (2023a). Exploring hydraulic fracture behavior in glutenite formation with strong heterogeneity and variable lithology based on DEM simulation. Eng. Fract. Mech. 278, 109020. doi:10.1016/j.engfracmech.2022.109020
Huang, L. K., Tan, J., Fu, H. F., Liu, J. J., Chen, X. Y., Liao, X. C., et al. (2023b). The non-plane initiation and propagation mechanism of multiple hydraulic fractures in tight reservoirs considering stress shadow effects. Eng. Fract. Mech. 292, 109570. doi:10.1016/j.engfracmech.2023.109570
Li, Q. M., Liang, Y. P., Zou, Q. L., and Li, Q. G. (2020). Acoustic emission and energy dissipation characteristics of gas-bearing coal samples under different cyclic loading paths. Nat. Resour. Res. 29 (2), 1397–1412. doi:10.1007/s11053-019-09508-2
Liang, Y. P., Kong, F. J., Zou, Q. L., and Zhang, B. C. (2023). Effect of strain rate on mechanical response and failure characteristics of horizontal bedded coal under quasi-static loading. Geomechanics Geophys. Geo-Energy Geo-Resources 9 (1), 52. doi:10.1007/s40948-023-00587-3
Liang, Y. P., Ran, Q. C., Zou, Q. L., Zhang, B. C., and Hong, Y. (2022). Experimental study of mechanical behaviors and failure characteristics of coal under true triaxial cyclic loading and unloading and stress rotation. Nat. Resour. Res. 31 (2), 971–991. doi:10.1007/s11053-022-10022-1
Liao, Z. W., Liu, X. F., Song, D. Z., He, X. Q., Nie, B. S., Yang, T., et al. (2021). Micro-structural damage to coal induced by liquid CO2 phase change fracturing. Nat. Resour. Res. 30 (2), 1613–1627. doi:10.1007/s11053-020-09782-5
Liu, S. M., and Li, X. L. (2016). Discussion on coupling disaster mechanism of coal and gas outburst and rock burst in deep coal mining. Coal Technol. 35 (09), 134–136. doi:10.13301/j.cnki.ct.2016.09.053
Liu, S. M., Sun, H. T., Zhang, D. M., Yang, K., Wang, D. K., Li, X. L., et al. (2023a). Nuclear magnetic resonance study on the influence of liquid nitrogen cold soaking on the pore structure of different coals. Phys. Fluids 35, 012009. doi:10.1063/5.0135290
Liu, T., Lin, B. Q., Fu, X. H., and Liu, A. (2021). Mechanical criterion for coal and gas outburst: a perspective from multiphysics coupling. Int. J. Coal Sci. Technol. 8, 1423–1435. doi:10.1007/s40789-021-00447-z
Liu, Y. B., Wang, E. Y., Jiang, C. B., Zhang, D. M., Li, M. H., Yu, B. C., et al. (2023b). True triaxial experimental study of anisotropic mechanical behavior and permeability evolution of initially fractured coal. Nat. Resour. Res. 32 (2), 567–585. doi:10.1007/s11053-022-10150-8
Ma, T. F., Liu, H. H., Zou, Q. L., Kong, F. J., Ran, Q. C., and Wang, P. T. (2023). Damage evolution characteristics and deterioration mechanism of mechanical properties of sandstone subjected to drying-wetting cycles. J. Mater. Res. Technol. 23, 4591–4605. doi:10.1016/j.jmrt.2023.02.068
Pan, J. F., Qi, Q. X., Liu, S. H., Wang, S. W., Ma, W. T., and Kang, X. C. (2020). Characteristics,types and prevention and control technology of rock burst in deep coal mining in China. J. China Coal Soc. 45 (01), 111–121. doi:10.13225/j.cnki.jccs.YG19.1638
Ran, Q. C., Liang, Y. P., Zou, Q. L., Hong, Y., Zhang, B. C., Liu, H., et al. (2023a). Experimental investigation on mechanical characteristics of red sandstone under graded cyclic loading and its inspirations for stability of overlying strata. Geomechanics Geophys. Geo-Energy Geo-Resources 9 (1), 11. doi:10.1007/s40948-023-00555-x
Ran, Q. C., Liang, Y. P., Zou, Q. L., Zhang, B. C., Li, R. F., Chen, Z. H., et al. (2023b). Characteristics of mining-induced fractures under inclined coal seam group multiple mining and implications for gas migration. Nat. Resour. Res. 32 (3), 1481–1501. doi:10.1007/s11053-023-10199-z
Song, M. Y., Li, Q. G., Hu, Q. T., Wu, Y. Q., Ni, G. H., Xu, Y. C., et al. (2022). Resistivity response of coal under hydraulic fracturing with different injection rates: a laboratory study. Int. J. Min. Sci. Technol. 32 (4), 807–819. doi:10.1016/j.ijmst.2022.06.004
Su, E. L., Liang, Y. P., Chen, X. J., Wang, Z. F., Ni, X. M., Zou, Q. L., et al. (2023). Relationship between pore structure and mechanical properties of bituminous coal under sub-critical and super-critical CO2 treatment. Energy 280, 128155. doi:10.1016/j.energy.2023.128155
Sun, D. L., Liang, Y. P., Huang, X. C., and Ran, Q. C. (2023a). Progress and prospects of coalbed methane development and utilization in coal mining areas with large dip angle and multiple coal groups in Xinjiang. Coal Sci. Technol. 51 (S1), 161–171. doi:10.13199/j.cnki.cst.mcq2022-1325
Sun, X. Y., Ran, Q. C., Liu, H., Ning, Y. H., and Ma, T. F. (2023b). Characteristics of stress-displacement-fracture multi-field evolution around gas extraction borehole. Energies 16 (6), 2896. doi:10.3390/en16062896
Tan, P., Fu, S. H., Chen, Z. W., and Zhao, Q. (2023). Experimental investigation on fracture growth for integrated hydraulic fracturing in multiple gas bearing formations. Geoenergy Sci. Eng. 231 (1), 212316. doi:10.1016/j.geoen.2023.212316
Tan, P., Jin, Y., and Pang, H. W. (2021). Hydraulic fracture vertical propagation behavior in transversely isotropic layered shale formation with transition zone using XFEM-based CZM method. Eng. Fract. Mech. 248, 107707. doi:10.1016/j.engfracmech.2021.107707
Wang, G. F., Ren, H. W., Zhao, G. R., Zhang, D. S., Wen, Z. G., Meng, L. Y., et al. (2022). Research and practice of intelligent coal mine technology systems in China. Int. J. Coal Sci. Technol. 9, 24. doi:10.1007/s40789-022-00491-3
Wang, H. F., Cheng, Y. P., Liu, G. J., Kong, S. L., and Zhang, R. (2013). Range extender of protection and continuous mining technology of protected seam. J. Min. Saf. Eng. 30 (04), 595–599. In Chinese.
Wang, H. T., Huang, G. L., Yuan, Z. G., Shu, C., and Hu, G. Z. (2014). Model of gas leak flow coupled solid and gas for exploiting of steep-inclined upper-protective layer and its protection scope. Rock Soil Mech. 35 (05), 1377–1382. doi:10.16285/j.rsm.2014.05.022
Wang, Z. H., Chen, B., Zhang, Y. J., Yang, H. M., and Cao, J. J. (2021). Research on dual pressure relief and outburst prevention model for deep floor rock roadways. Arabian J. Geosciences 14, 845. doi:10.1007/s12517-021-07118-y
Wang, Z. M., Liang, Y. P., Zou, Q. L., Zhang, B. C., and Ran, Q. C. (2023). Movement of overlying rock and deformation law of surface well under multiple mining with large dip angle. Coal Sci. Technol. 51 (04), 47–55. doi:10.13199/j.cnki.cst.2021-0827
Wu, Q. F., Han, S. X., Li, S. S., Yu, M. G., Zheng, K., Li, H. T., et al. (2023). Explosive characteristics of non-uniform methane-air mixtures in half-open vertical channels with ignition at the open end. Energy 284, 128687. doi:10.1016/j.energy.2023.128687
Wu, Q. F., Yu, M. G., and Zheng, K. (2022). Experimental investigation on the effect of obstacle position on the explosion behaviors of the non-uniform methane/air mixture. Fuel 320, 123989. doi:10.1016/j.fuel.2022.123989
Xiao, S. Q., Ren, Q. Y., Cheng, Y. G., Wang, H. Y., Zhang, L., Liao, Y., et al. (2022). Research and application of high-pressure water jets drilling and repairing failure drainage borehole for enhancing coalbed methane recovery in underground coal mines. Geomechanics Geophys. Geo-Energy Geo-Resources 8 (6), 191. doi:10.1007/s40948-022-00500-4
Xie, H. P., Lu, J., Li, C. B., Li, M. H., and Gao, M. Z. (2022). Experimental study on the mechanical and failure behaviors of deep rock subjected to true triaxial stress: a review. Int. J. Min. Sci. Technol. 32 (5), 915–950. doi:10.1016/j.ijmst.2022.05.006
Xie, Y. C., Hou, M. Z., and Li, C. B. (2023). Anisotropic characteristics of acoustic emission and the corresponding multifractal spectrum during progressive failure of shale under cyclic loading. Int. J. Rock Mech. Min. Sci. 165, 105364. doi:10.1016/j.ijrmms.2023.105364
Ye, C. F., Xie, H. P., Wu, F., and Li, C. B. (2022). Nonlinear creep properties and time-to-failure prediction of sandstone under saturated and dry conditions. Environ. Earth Sci. 81, 545. doi:10.1007/s12665-022-10666-5
Ye, C. F., Xie, H. P., Wu, F., and Li, C. B. (2023). Study on the nonlinear time-dependent deformation characteristics and viscoelastic-plastic model of shale under direct shear loading path. Bull. Eng. Geol. Environ. 82 (5), 189. doi:10.1007/s10064-023-03170-y
Yuan, L., and Xue, S. (2014). Defining outburst-free zones in protective mining with seam gas content-method and application. J. China Coal Soc. 39 (09), 1786–1791. doi:10.13225/j.cnki.jccs.2014.8019
Zhang, B. C., Liang, Y. P., Zhao, Z. Y., Zou, Q. L., Zheng, H. L., Ning, Y. H., et al. (2023a). Effect of stress amplitude on mechanical and acoustic emission of sandstone under constant–cyclic loading. Bull. Eng. Geol. Environ. 82, 284. doi:10.1007/s10064-023-03307-z
Zhang, C. L., Wang, P. Z., Wang, E. Y., Chen, D. P., and Li, C. (2023b). Characteristics of coal resources in China and statistical analysis and preventive measures for coal mine accidents. Int. J. Coal Sci. Technol. 10 (1), 22. doi:10.1007/s40789-023-00582-9
Zhang, T. C., Zou, Q. L., Jia, X. Q., Jiang, C. Z., and Niu, X. G. (2022). Effect of SiO2 nanofluid with different concentrations on the wettability of coal. Fuel 321, 124041. doi:10.1016/j.fuel.2022.124041
Zhang, Y. J., Zou, Q. L., Yuan, H. M., Chen, Z. H., Cao, J. J., and Cheng, Z. H. (2023d). Outburst coal seam group joint ground and underground gas extraction mode and its key technology. J. China Coal Soc. doi:10.13225/j.cnki.jccs.S022.1663
Zhao, C., Cheng, Z. H., Liu, Y. Q., Chen, L., Wu, B., Zhang, J. G., et al. (2022). A mathematical model for optimization and decision-making of the optimal scheme for coordinated exploitation of coal and coalbed methane. Geomechanics Geophys. Geo-Energy Geo-Resources 8 (4), 120. doi:10.1007/s40948-022-00419-w
Zhao, J. J., Tian, S. X., Li, P., Xie, H. G., and Cai, J. J. (2023a). Molecular dynamics simulation and experimental research on the influence of SiO2-H2O nanofluids on wettability of low-rank coal. Colloids Surfaces A Physicochem. Eng. Aspects 679, 132580. doi:10.1016/j.colsurfa.2023.132580
Zhao, J. J., Tian, S. X., Xie, H. G., and Zhang, X. (2023b). Study of time-varying laws of stability and wettability of SiO2–H2O nanofluids with different particle sizes. Industrial Eng. Chem. Res. 62, 13529–13540. doi:10.1021/acs.iecr.3c02110
Zheng, J., Huang, G., Cheng, Q., Jia, J. K., and Cai, Z. H. (2022). A novel experimental apparatus for evaluating coal-and-gas outburst risk. Nat. Resour. Res. 31 (1), 535–550. doi:10.1007/s11053-021-09994-3
Zou, Q. L., Chen, Z. H., Cheng, Z. H., Liang, Y. P., Xu, W. J., Wen, P. R., et al. (2022). Evaluation and intelligent deployment of coal and coalbed methane coupling coordinated exploitation based on Bayesian network and cuckoo search. Int. J. Min. Sci. Technol. 32 (6), 1315–1328. doi:10.1016/j.ijmst.2022.11.002
Zou, Q. L., Huo, Z. X., Zhang, T. C., Jiang, C. Z., and Liang, J. Y. (2023a). Surface deposition characteristics of water-based SiO2 nanofluids on coal. Fuel 340, 127489. doi:10.1016/j.fuel.2023.127489
Keywords: ground wells, bedding drilling, cross-layer drilling, outburst prevention measures, pre-drainage gas
Citation: Zhang P (2023) Regional outburst prevention technology of pre-drainage gas area in west well area of sihe coal mine. Front. Energy Res. 11:1296830. doi: 10.3389/fenrg.2023.1296830
Received: 19 September 2023; Accepted: 31 October 2023;
Published: 13 November 2023.
Edited by:
Peng Tan, CNPC Engineering Technology R & D Company Limited, ChinaReviewed by:
Li Qingmiao, Chengdu University of Technology, ChinaShixiang Tian, Guizhou University, China
Copyright © 2023 Zhang. This is an open-access article distributed under the terms of the Creative Commons Attribution License (CC BY). The use, distribution or reproduction in other forums is permitted, provided the original author(s) and the copyright owner(s) are credited and that the original publication in this journal is cited, in accordance with accepted academic practice. No use, distribution or reproduction is permitted which does not comply with these terms.
*Correspondence: Peng Zhang, Ym56cDEyM0BzaW5hLmNvbQ==