- 1Kielce University of Technology, Faculty of Environmental Engineering, Geodesy and Renewable Energy, Kielce, Poland
- 2VSB-Technical University of Ostrava, Faculty of Mechanical Engineering, Ostrava, Czechia
- 3Kielce University of Technology, Faculty of Mechatronics and Mechanical Engineering, Kielce, Poland
Proper treatment and recycling of waste are crucial for the natural environment. Biowaste and ash might be used for ceramic building material production. Reduction in the amount of waste leads to the smaller burden on the environment, and it can also offer recovery of energy. This paper presents the results of an experimental study of the compressive strength of samples made from clay with waste additives: ash and sewage sludge. It was proven that the increasing amount of the waste materials decreases strength properties in all incineration temperatures. Scanning electron microscopy analysis was used to determine the internal structure of the samples. Tests of heavy metal leaching revealed that the concentration of copper, chromium, nickel, and zinc in leachate generally decreased with an increase in sintering temperature. Moreover, the level of chromium was observed to exceed the permissible level.
1 Introduction
Waste material can come from different sources and, thus, can have highly varied characteristics (Holubčík et al., 2023; Čajová Kantová et al., 2023). The production of building materials is one of the ways, in which various types of waste can be reused. Such waste materials can be recycled, but if they have enough calorific value, they can also contribute to a reduction in fossil fuel consumption if the treatment process involves incineration. However, despite clear advantages of energy and material recycling, the products should meet certain quality requirements, so that they can be safely applied for building purposes. Material strength, especially the compressive strength of such products, is an important criterion. If the commercial use of the materials with waste additives is economically and ecologically advantageous, they can be widely applied. However, the addition of waste should not cause a negative impact on the material properties. Moreover, emissions from building materials made of waste should not cause a deterioration in the environment—neither outdoors (Wicke et al., 2022) nor indoors (Zender-Świercz, 2018; Ratajczak et al., 2023). Thus, it is necessary to determine the environmental impact such products might have on the surroundings, and leaching of heavy metals is a crucial factor.
The literature on waste recycling is broad, and much scientific effort is being put in this area, both energy production (Rećki, 2020) and material recycling (Zydroń&Gruchot, 2014). However, the specific tests on the strength properties of the products are not quite common. In the work of Bhutta et al. (2011), the usage of expanded polystyrene waste in polymer mortar panels is discussed. The strength properties of the polymer-impregnated mortar panel were found to be almost the same as those of commercial products. Liew et al. (2004) presented test results of properties of bricks produced with sewage sludge. It was reported that an increase in the sludge content led to a decrease in brisk shrinkage, bulk density, and compressive strength, which was lowest for a sludge concentration of 40% and amounted to ca. 2 MPa. The sewage sludge content was changed from 10% to 40% by weight. It was also noted that leaching of metals from bricks was very low. In the work of Wiebusch&Seyfried (1997), tests of brick samples produced with sewage sludge ashes were considered. The maximal ash content was 40%. A significant impact of ash content and also incineration temperature, which was set to 1,060°C to ensure highest strength, was proven. Ashes of different chemical compositions as well as four incineration temperatures (from 1,000°C to 1,060°C) were considered. With regard to the compressive strength, 10% ash content can be taken as the most favourable. It enabled the production of materials with strength reaching almost 150 MPa. Lin et al. (2006) experimentally analysed the properties of water treatment sludge and bottom ash from a municipal solid waste incinerator. Sludge was mixed with ash, and blocks were formed. They were later sintered at 900°C–1,200°C. Increased bottom ash content led to lower compressive strength. It was also found that, generally, the compressive strength increased with sintering temperature for samples produced with sludge. Garcés et al. (2008) studied the compatibility of sewage sludge ash with different types of cements. Investigated mortars were made with 10%, 20%, and 30% of cement (by weight) replaced by the ash. It was reported that the highest compressive strength values were achieved for 10% content. Incinerated sewage sludge ash was considered in the work of Lin et al. (2008) as the replacement of clay for tile production. It was found that the bending strength reduced with an increase in ash concentration; however, it increased for glazed ash tiles. In the work of Chandra et al. (1993), the wall tile manufacturing with the use of waste, namely, fly ash, was also considered. In the work of Lin&Weng (2001), selected parameters of bricks produced from incinerated sewage sludge ash and clay were experimentally analysed. It was concluded that the optimal ash content was 20% (by weight) to provide good bonding, while the optimal firing temperature which led to maximal compressive strength was 1,000°C. The presented data indicate that the addition of 20% ash and a firing temperature of 1,000°C resulted in the best strength properties. Compressive strength at this temperature was higher than that of the brick with 10% (second best), 30%, 0%, 40%, and 50% ash (worst case). Domski et al. (2019) tested the critical load-carrying conditions of beams produced from waste fine aggregate and plain concrete and indicated a favourable influence of the reinforcement application. It has been confirmed in the work of Głodkowska and Lehmann (2019) by experimental results of residual strength of steel fibre-reinforced waste sand concrete. Recently, Zari et al. (2023) investigated the effect of adding up to 30% sewage sludge into mortars (replacing cement). The compressive strength of the samples decreased with the increase in sludge content; however, the authors concluded that the addition of 15% is acceptable. Furthermore, an increase in the sludge content led to a significant reduction in the strength properties.
The analysis of the application of building materials produced with waste additives should also consider the environmental impact—most importantly, leaching of heavy metals from the sintered samples. In the work of Ramesh&Koziński (2001), the leachability of heavy metals (chromium, lead, and cadmium) from ash was investigated. The ash was produced from waste combustion. It was found that ash pellets obtained at the temperature of 1,000°C showed some leachability; however, at higher temperatures, negligible heavy metal leaching was observed (at 1,400°C) and even no leaching at all (at 1,500°C). Consequently, high-temperature treatment immobilised heavy metals in the ash. Chen et al. (2011) studied the leaching of heavy metals (including nickel, copper, and zinc) from pastes of belite-rich cements made from electroplating sludge. It was stated that turning the sludge into belite-rich cements results in heavy metals being stable in hardened cement pastes. Alp et al. (2008) considered the utilisation of flotation waste of copper slag in the manufacturing of Portland cement clinker. Based on leachability tests, covering As, Ag, Ba, Cr, Cu, and Pb, as well as others, it was stated that samples from the clinker with waste additives pose no environmental problems. The concentrations of metals in the leachate were compared with regulatory values by the U.S. Environmental Protection Agency. Zari et al. (2023) analysed the leaching of Cr, As, Pb, Cd, Ni, Cu, and Zn from mortars produced with sewage sludge. It was stated that the cumulative values of heavy metals were far below the regulatory limits, justifying retention of the metals in the matrix. Diotti et al. (2021) examined leaching from construction and demolition wastes and found out that mean copper release was 0.01 mg/dm3, zinc 0.07 mg/dm3, nickel 9.72 mg/dm3, and chromium 38.65 mg/dm3. Additionally, it was reported that material particle size generally affected the release of contaminants: finer particles provided higher releases. Recently, Wang et al. (2022) analysed the leaching characteristics of arsenic, cadmium, chromium, copper, lead, nickel, and zinc in dust and in soil before and after thermal desorption. It was concluded that thermal treatment methods (rotary kilns and secondary combustion chambers) influence the existing forms of heavy metals and affect the leaching characteristics of the final products.
Despite a large experimental database on the use of waste materials, the results reported in some of the papers might contradict one another. The present paper aims to clear out the discrepancies and provide new experimental material for the analysis.
The present work is focused on determination of the impact of the waste additives in the form of fly ash and sewage sludge on the compressive strength of ceramic material as well as the influence of the sintering temperature on the internal microstructure of the products. The potential threat to water and soil related to the use of waste-derived building materials was analysed by testing heavy metal leachability from the samples produced at different temperatures.
2 Materials and methods
The samples analysed in this study were made of clay and waste (ash and sewage sludge). The source of clay was the deposit Zrecze in Poland, near Kielce. The basic properties of this deposit are as follows: marl in grains of diameter >0.5 mm: 0.055%, water-soluble sulfates: 0.14%, and bulk density at temperature 900°C: 1.74 g/cm3. The mineral compositions of clay are montmorillonite, illite, kaolinite, illite–montmorillonite mixed pack minerals, calcite, dolomite, calcium aluminium oxides, and calcium ferrous oxides (Giełżecka and Nicpoń, 1987).
The ash used in the tests was collected from an electrofilter in a heat and power plant in which coal is burned in the WP-140-type boilers. The sewage sludge used in the tests was taken from the sewage treatment plant in Sitkowka-Nowiny near Kielce. The sludge was dried at 105°C. Then, it was turned into powder of below 1.0 mm grain size.
Samples with clay, sewage sludge, and fly ash were produced. The contents (by mass) of the components were taken based on preliminary test results. Water was added to the substrates of the mixes until their plastic state was achieved. Samples of 26 mm × 26 mm × 14 mm were formed with the hand press and dried first at the temperature of ca. 20°C and then at 105°C in the laboratory drier for 2 h. The dried samples were sintered in the “Nabertherm” laboratory kiln at temperatures 850°C, 900°C, and 950°C under ambient conditions. The burning time was 8 h including 1 h at the maximal temperature. The heating rate for all the samples (despite their different compositions) was the same in order to maintain the same production conditions and eliminate the introduction of a new variable to the study. After sintering, the samples were left in the furnace for cooling. The process of sintering in the laboratory kiln was similar to that taking place during brick production in the ceramic plant. Four types of samples were produced and contained type 1: clay (100%), type 2: clay (80%) with ash (20%), type 3: clay (80%) with sludge (20%), and type 4: clay (60%) with ash (20%) and sludge (20%). Figure 1 presents a sample after sintering.
The tests of compressive strength were conducted on the samples containing clay (100%) and clay with additives (fly ash, sewage sludge, and a mix of both). The measurements were conducted with the overall error of up to 8%. In order to have an insight into the structure of the material, scanning electron microscopy (SEM) analysis was used. The experimental analysis of leaching characteristics of the samples was based on the extraction procedure (EP) (EPA, 1991). The process begins with fractioning the material to below 9.5 mm and is then followed by leaching with deionised water of pH = 5.0 (pH kept constant using CH3COOH). The total shaking time was 24 h. The mean maximal error of leachability determination was 1 μm/dm3.
3 Results and discussion
The produced samples underwent compressive strength testing, and the final result for each sample type is an average from three measurements. As can be seen in Table 1, the best performance was observed for the pure clay sample (50–60 MPa), which is within the range of typical bricks (7–80 MPa for light and hard bricks, respectively)1. The addition of waste only led to lower values of compressive strength [which is in line with recent data presented by Zari et al. (2023)]. The addition of ash resulted in a significant reduction in compressive strength for all sintering temperatures—ranging from 50% to 60%. Even larger decrease in the strength properties was observed if sludge was added instead of ash, while the lowest compressive strength was recorded for samples with 40% waste material (ash and sludge).
The poor performance of the samples containing waste might reduce their practical application; however, proper design of the mixtures—taking into account the purpose of the building material and mathematical modelling techniques (Kusyi et al., 2022)—can lead to the development of a sustainable and successful material mixture with optimal waste concentration. It also needs to be noted that sludge, as organic matter, turns into vapour during sintering and pores are produced. Consequently, the addition of sewage sludge resulted in low compressive strength. Such materials could, however, be effectively used for the production of building materials with enhanced thermal resistance properties (e.g., for insulation purposes due to lower thermal conductivity). Moreover, incineration of organic waste (which contains some energy potential) can be energy efficient due to its partial use as fuel in the production process. Thus, less energy for incineration might be required, which is not the case for inert substances such as fly ash.
The analysis of the internal structure of the samples revealed differences with regard to the waste materials used. Figures 2A–D present the SEM images for the sintering temperature of 850°C (upper part) and for the temperature of 950°C (lower part).
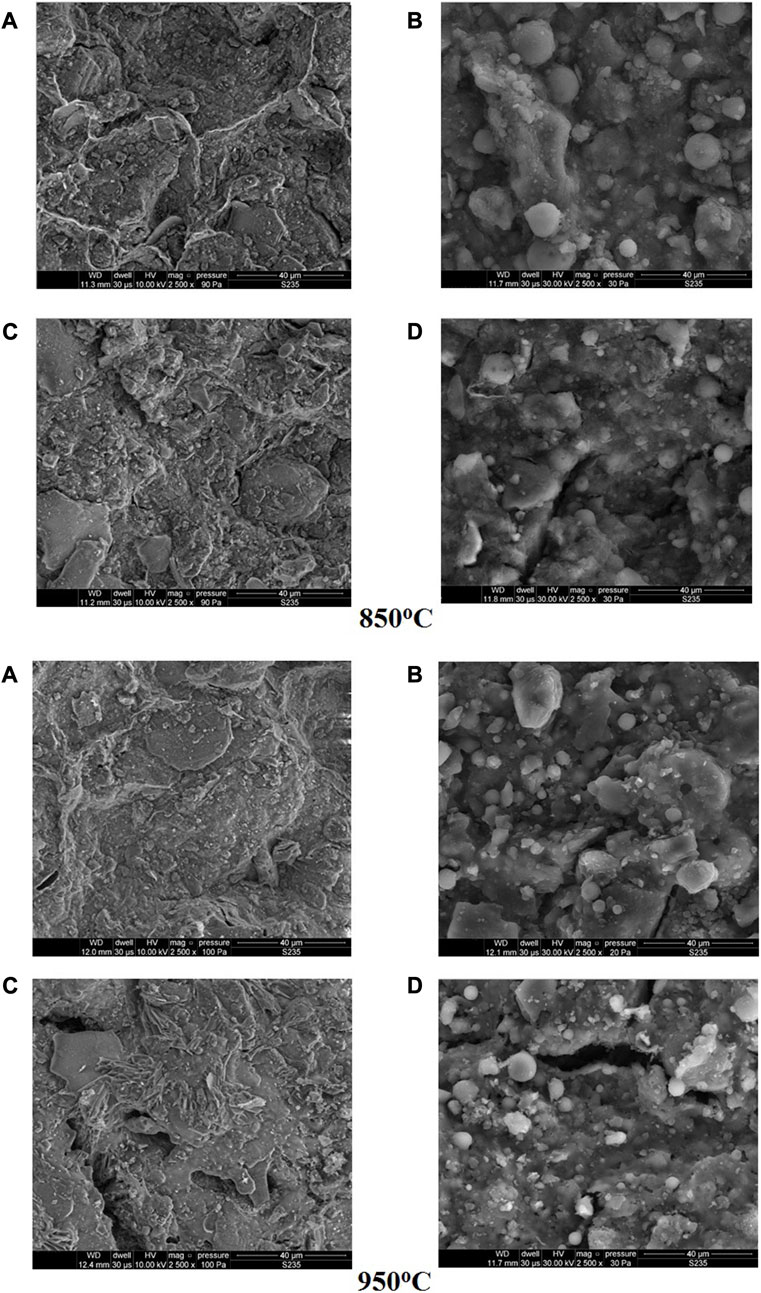
FIGURE 2. SEM of samples sintered at 850°C (upper) and 950°C (lower): (A) sample 1, (B) sample 2, (C) sample 3, and (D) sample 4 (composition of the samples is as in Table 1).
The samples produced with clay and clay with sludge show clear compact structure, while those with the addition of fly ash contain spherical forms (microspheres). These come from fly ash share in the specimens. It also needs to be noted that the material made with the addition of sewage sludge contains the glass phase. The comparison of the upper and lower images in Figure 2 indicates that the increase in sintering temperature from 850°C to 950°C proved to have no clear impact on the microstructure of the samples.
As mentioned in the introductory part, material and energy recycling of waste should not pose any threat to the environment. Thus, the samples underwent leaching tests. The results of heavy metal leaching are presented in Figure 3, separately for each metal tested (A–D).
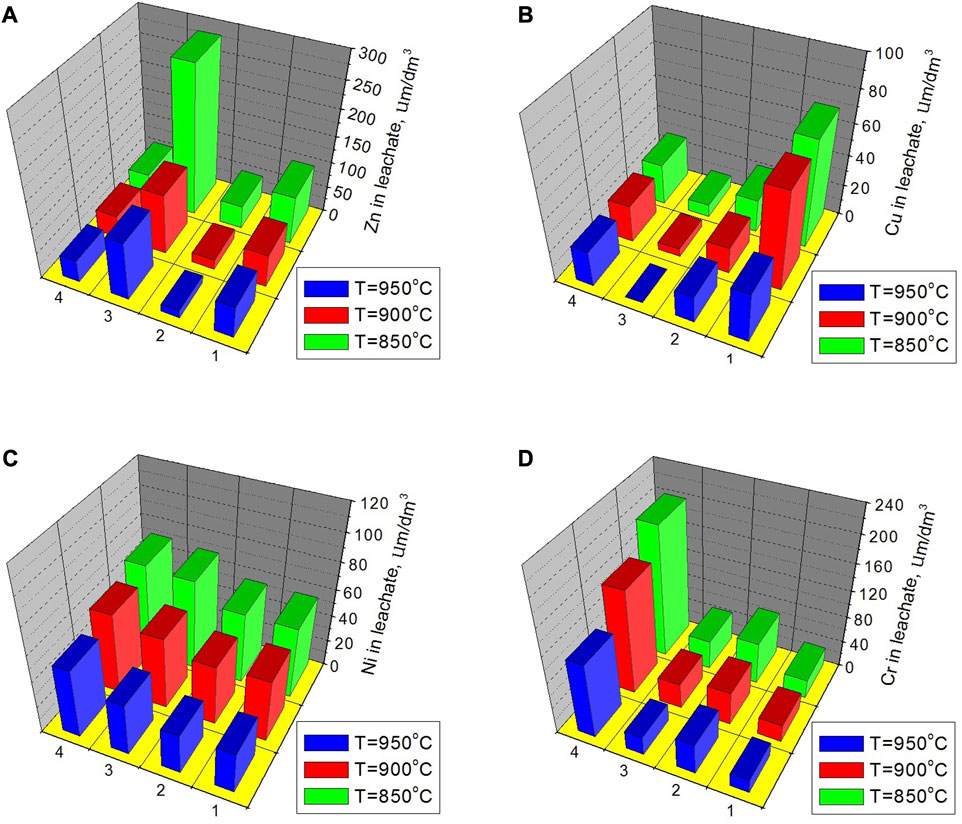
FIGURE 3. Leaching of heavy metals from samples sintered at different temperatures: (A) zinc, (B) copper, (C) nickel, and (D) chromium (total); 1, 2, 3, and 4—sample numbers (composition of the samples is as in Table 1).
As can be noticed, leaching of heavy metals was generally lower as the sintering temperature increased. This correlation was not observed in all the samples and temperature values; however, it can be considered a characteristic feature. Moreover, the concentration of certain metals in leachate varied depending on the metal rather than that on the waste. For example, leaching of zinc was highest in the case of the sample with clay (80%) and sludge (20%), while maximal leaching of copper was observed for the pure clay sample. It might be caused by the concentration of heavy metals in the base and waste materials rather than being influenced by the treatment method. As opposed to other heavy metals tested, leaching of nickel was quite uniform regardless of the samples’ composition. It needs to be noted that certain amounts of heavy metals might have been removed from the samples during sintering as they entered the gas phase and left with the exhaust gases. However, this phenomenon could not have substantially altered the results.
Naturally, the leaching characteristics should also address the issue of environmental hazards to the surroundings. The comparison of the measured values of heavy metals’ concentrations with the permissible values according to the review (Mahmud et al., 2016) (which provides recommendations of the World Health Organization and US Environmental Protection Agency) reveals that heavy metal levels were acceptable in the case of copper, zinc, and nickel. However, the concentration of chromium (total) was almost four times the allowable limit. The requirements are for drinking water, so a direct comparison might not be fully justified; however, it clearly shows that in the case of building materials made of waste, a threat to the environment can potentially occur and this fact should be considered before a broad commercial application of such materials. At the same time, according to Latosińska and Żygadło (2009), a full protection against heavy metal leaching from ceramic sinters is guaranteed by conducting the process at a temperature providing a sintered product of a high glass phase fraction.
4 Conclusion
The utilisation of waste for building material production can be considered a waste treatment option as well as material and energy recycling method. This could be advantageous both for environmental and economical reasons. The experimental tests proved that the addition of waste materials considerably reduces compressive strength in relation to the pure clay samples (from 39% in the case of ash addition to 91% in the case of joint addition of ash and sewage sludge). However, it does not exclude their use in the building industry since a required strength level can be achieved up to certain levels of the waste in the mixture. Equally important is the environmental impact of leaching of heavy metals. Out of four metals tested, the concentration of one (chromium) in the leachate proved to exceed the permissible drinking water required level. At the same time, leaching of heavy metals generally decreased with an increase in the sintering temperature of the ceramic materials tested in the study—on average by 0.30 μm/(dm3·°C) for chromium, 0.13 μm/(dm3·°C) for copper, 0.24 μm/(dm3·°C) for nickel, and 0.59 μm/(dm3·°C) for zinc.
Data availability statement
The raw data supporting the conclusion of this article will be made available by the authors, without undue reservation.
Author contributions
JL: conceptualisation, investigation, writing–original draft, and writing–review and editing. JG: investigation and writing–review and editing. SH: conceptualisation, writing–original draft, and writing–review and editing. ŁO: conceptualisation, investigation, writing–original draft, and writing–review and editing. NR: investigation, writing–original draft, and writing–review and editing.
Funding
The authors declare financial support was received for the research, authorship, and/or publication of this article. The work in this paper was supported by the project “SP2023/094 Specific research in selected areas of energy processes” and “REFRESH—Research Excellence For Region Sustainability and High-tech Industries (VP2) (Reg. No. CZ.10.03.01/00/22_003/0000048), co-funded by the European Union.”
Conflict of interest
The authors declare that the research was conducted in the absence of any commercial or financial relationships that could be construed as a potential conflict of interest.
Publisher’s note
All claims expressed in this article are solely those of the authors and do not necessarily represent those of their affiliated organizations, or those of the publisher, the editors, and the reviewers. Any product that may be evaluated in this article, or claim that may be made by its manufacturer, is not guaranteed or endorsed by the publisher.
Footnotes
References
Alp, I., Deveci, H., and Süngün, H. (2008). Utilization of flotation wastes of copper slag as raw material in cement production. J. Hazard. Mater. 159, 390–395. doi:10.1016/j.jhazmat.2008.02.056
Bhutta, M. A. R., Ohama, Y., and Tsuruta, K. (2011). Strength properties of polymer mortar panels using methyl methacrylate solution of waste expanded polystyrene as binder. Constr. Build. Mater. 25, 779–784. doi:10.1016/j.conbuildmat.2010.07.006
Čajová Kantová, N., Holubčík, M., Čaja, A., Trnka, J., Hrabovský, P., and Belány, P. (2023). Co-combustion investigation of wood pellets blended with FFP2 masks: analysis of the ash melting temperature. Forests 14, 636. doi:10.3390/f14030636
Chandra, N., Sharma, P., Pashkov, G. L., Voskresenskaya, E. N., Amritphale, S. S., and Baghel, N. S. (2008). Coal fly ash utilization: low temperature sintering of wall tiles. Waste Manag. 28, 1993–2002. doi:10.1016/j.wasman.2007.09.001
Chen, Y. L., Ko, M. S., Lai, Y. C., and Chang, J. E. (2011). Hydration and leaching characteristics of cement pastes made from electroplating sludge. Waste Manag. 31, 1357–1363. doi:10.1016/j.wasman.2010.12.018
Diotti, A., Plizzari, G., and Sorlini, S. (2021). Leaching behaviour of construction and demolition wastes and recycled aggregates: statistical analysis applied to the release of contaminants. Appl. Sci. 11, 6265. doi:10.3390/app11146265
Domski, J., Zakrzewski, M., and Laskowska-Bury, J. (2019). Bending moment of the waste fine aggregate concrete beams. Rocz. Ochr. Środowiska 21, 1505–1514.
EPA Regulations on Land Disposal Restrictions (1991).Appendix II – toxicity characteristic leaching procedure Washington D.C., USA: The Bureau of National Affairs, Inc.
Garcés, P., Pérez Carrión, M., García-Alcocel, E., Payá, P., Monzó, J., and Borrachero, M. V. (2008). Mechanical and physical properties of cement blended with sewage sludge ash. Waste Manag. 28, 2495–2502. doi:10.1016/j.wasman.2008.02.019
Giełżecka, D., and Nicpoń, W. (1987). Dokumentacja Geologiczna w Kategorii C2 złoża iłów trzeciorzędowych dla potrzeb ceramiki budowlanej “Zrecze”, Ministerstwo Ochrony Środowiska i Zasobów Naturalnych. Warszawa, Poland: Przedsiębiorstwo Geologiczne w Kielcach.
Głodkowska, W., and Lehmann, M. (2019). Shear capacity and residual strengths of steel fibre reinforced waste and concrete (SFRWSC). Rocz. Ochr. Środowiska 21, 1405–1426.
Holubčík, M., Jandačka, J., and Trnka, J. (2023). “Closed cycle of biodegradable wastes in smart cities,” in Industry 4.0 challenges in smart cities. EAI/Springer innovations in communication and computing. Editors D. Cagáňová, and N. Horňáková (Cham. Germany: Springer).
Kusyi, Y., Stupnytskyy, V., Onysko, O., Dragašius, E., Baskutis, S., and Chatys, R. (2022). Optimization synthesis of technological parameters during manufacturing of the parts. Eksploatacja i Niezawodność – Maintenance Reliab. 24 (4), 655–667. doi:10.17531/ein.2022.4.6
Latosińska, J., and Żygadło, M. (2009). Effect of sewage sludge addition on porosity of Lightweight Expanded Clay Aggregate (LECA) and level of heavy metals leaching from ceramic matrix. Environ. Prot. Eng. J. 2, 189–196.
Liew, A. G., Idris, A., Samad, A. A., Wong, C. H. K., Jaafar, M. S., and Baki, A. M. (2004). Reusability of sewage sludge in clay bricks. J. Mater Cycles Waste Manag. 6, 41–47. doi:10.1007/s10163-003-0105-7
Lin, C. F., Wu, C. H., and Ho, H. M. (2006). Recovery of municipal waste incineration bottom ash and water treatment sludge to water permeable pavement materials. Waste Manag. 26, 970–978. doi:10.1016/j.wasman.2005.09.014
Lin, D. F., Chang, W. C., Yuan, C., and Luo, H. L. (2008). Production and characterization of glazed tiles containing incinerated sewage sludge. Waste Manag. 28, 502–508. doi:10.1016/j.wasman.2007.01.018
Lin, D. F., and Weng, C. H. (2001). Use of sewage sludge ash as brick material. J. Environ. Eng. 127 (10), 0922–0927. doi:10.1061/(asce)0733-9372(2001)127:10(922)
Mahmud, H. N. M., Obidul Huq, Dr.A. K., and Rosiyah, Y. (2016). The removal of heavy metal ions from wastewater/aqueous solution using polypyrrole-based adsorbents: A review. RSC Adv. 6, 14778–14791. doi:10.1039/C5RA24358K
Ramesh, A., and Koziński, J. A. (2001). Investigations of ash topography/morphology and their relationship with heavy metals leachability. Environ. Pollut. 111, 255–262. doi:10.1016/s0269-7491(00)00062-2
Ratajczak, K., Amanowicz, Ł., Pałaszyńska, K., Pawlak, F., and Sinacka, J. (2023). Recent achievements in research on thermal comfort and ventilation in the aspect of providing people with appropriate conditions in different types of buildings—semi-systematic review. Energies 16, 6254. doi:10.3390/en16176254
Rećki, K. (2020). Laboratory research on the possibility of producing fuels from municipal sewage sludge. Rubber Waste Biomass, Rocznik Ochrona Środowiska 22, 680–692.
Wang, P., Cao, Y., Yang, B., Luo, H., Liang, T., Yu, J., et al. (2022). Leaching characteristics of heavy metals in the baghouse filter dust from direct-fired thermal desorption of contaminated soil. Int.J. Environ. Res. Public Health 19, 16504. doi:10.3390/ijerph192416504
Wicke, D., Tatis-Muvdi, R., Rouault, P., Zerball-van Baar, P., Dünnbier, U., Rohr, M., et al. (2022). Emissions from building materials—a threat to the environment? Water 14, 303. doi:10.3390/w14030303
Wiebusch, B., and Seyfried, C. F. (1997). Utilization of sewage sludge ashes in the brick and tile industry. Wat. Sci. Tech. 36 (11), 251–258. doi:10.2166/wst.1997.0418
Zari, R., Graich, A., Abdelouahdi, K., Monkade, M., Laghzizil, A., and Nunzi, J.-M. (2023). Mechanical, structural, and environmental properties of building cements from valorized sewage sludges. Smart Cities 6, 1227–1238. doi:10.3390/smartcities6030059
Zender-Świercz, E. (2018). Improving the indoor air quality using the individual air supply system. Int. J. Environ. Sci. Technol. 15 (4), 689–696. doi:10.1007/s13762-017-1432-x
Keywords: building materials, energy recovery, environmental impact, leachate, sintering, strength properties
Citation: Latosińska J, Gawdzik J, Honus S, Orman ŁJ and Radek N (2023) Waste for building material production as a method of reducing environmental load and energy recovery. Front. Energy Res. 11:1279337. doi: 10.3389/fenrg.2023.1279337
Received: 17 August 2023; Accepted: 14 September 2023;
Published: 29 September 2023.
Edited by:
Michal Holubčík, University of Žilina, SlovakiaReviewed by:
Jan Kizek, Technical University of Košice, SlovakiaNikola Čajová Kantová, University of Žilina, Slovakia
Miro Stošić, Josip Juraj Strossmayer University of Osijek, Croatia
Łukasz Amanowicz, Poznań University of Technology, Poland
Copyright © 2023 Latosińska, Gawdzik, Honus, Orman and Radek. This is an open-access article distributed under the terms of the Creative Commons Attribution License (CC BY). The use, distribution or reproduction in other forums is permitted, provided the original author(s) and the copyright owner(s) are credited and that the original publication in this journal is cited, in accordance with accepted academic practice. No use, distribution or reproduction is permitted which does not comply with these terms.
*Correspondence: Łukasz J. Orman, b3JtYW5AdHUua2llbGNlLnBs