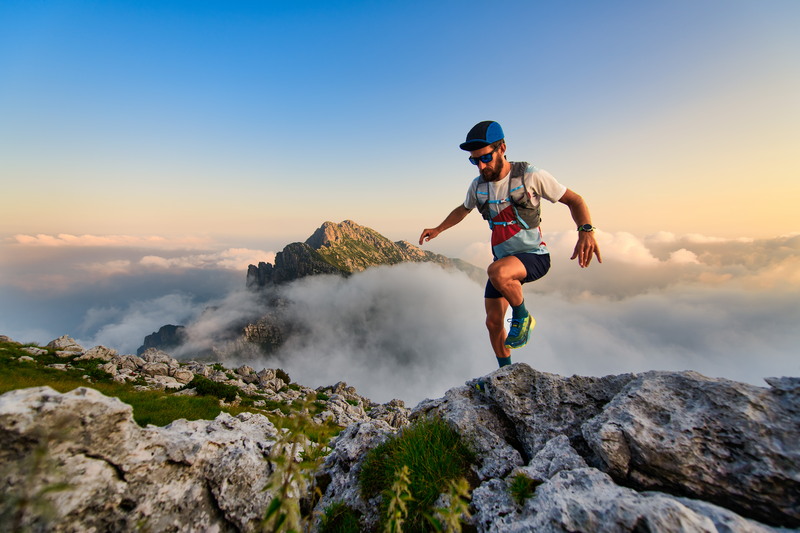
95% of researchers rate our articles as excellent or good
Learn more about the work of our research integrity team to safeguard the quality of each article we publish.
Find out more
ORIGINAL RESEARCH article
Front. Energy Res. , 12 October 2023
Sec. Solar Energy
Volume 11 - 2023 | https://doi.org/10.3389/fenrg.2023.1269572
Molten salts are commonly used in solar thermal power plants to store heat when sunlight is unavailable. However, solidifying the salts can lead to operational interruptions and prevent an optimal energy output. A self-adaptive heat extraction method has been proposed to regulate salt pipeline temperatures, enabling continuous operations that mitigate unplanned shut-downs. Such a method focuses on maintaining operational temperatures and preventing interferences caused by the freezing of the salts. The proposed Self-Adaptive Heat Extraction Controller (SAHEC) relies on fuzzy logic integrated into MATLAB Simulink to ensure optimal heat extraction control utilizing four distinct temperature variables. Modeling this approach through a created MATLAB-based simulation reveals that SAHEC offers an undeniable improvement over standard conventional methods for manipulating temperatures.
The field of renewable Energy is expanding with significant momentum, particularly in Concentrated Solar Power (CSP) technology. This innovative approach uses many heliostat mirrors within a solar field to generate power, relying heavily on the flow rate and temperature control of fluids within pipes. With the introduction of Thermal Energy Storage (TES) systems, CSP towers can continue generating electricity even after sunset. Distributed Control Systems (DCS) facilitate effective management of such operations (Menéndez et al., 2014; González-Roubaud et al., 2017; Prieto et al., 2019).
Solar tower technology uses pipes that transport fluid containing molten salt from the top of the tower down to the turbine, generating power. Molten salt is an inexpensive material to use in large quantities, and it can store a significant amount of heat that can be preserved in thermal tanks for reuse during the night (Debnath et al., 2018; Qaisrani et al., 2022; Saldivia and Taylor, 2023). The invention of these salt-based thermal tanks was a response to the problem of power plants shutting down when the Sun was not shining. However, a new issue arose with the potential for the salt to freeze within the pipes when the climate conditions change, and the molten salt tanks are insufficient to ensure continued power generation. When the temperature of the revolving molten salt drops, it can freeze in the pipes, and restarting the plant becomes a significant challenge. To prevent this coma state, scientists are working to find a viable solution (Roper et al., 2022).
In a study presented by the authors of (Pascual et al., 2022), various salts were examined for their use in energy storage. Molten salt typically refers to solid salt at standard temperature and pressure (STP) but becomes liquid when heated. At room temperature, some salts remain liquid and are referred to as ionic liquids or molten salts, although they technically belong to the class of ionic liquids. Liquid salt blends can be both hazardous and inert. Among the different options, molten salt is today’s most versatile, efficient, cost-effective large-scale energy storage system. This storage method ensures a consistent and transportable product without backup fossil fuels such as natural gas, which is required for other concentrated solar power (CSP) technologies. The specific type of salt used in solar Energy is a mixture of sodium nitrate (NaNO3) and potassium nitrate (KNO3), known as solar salts (Guccione and Guedez, 2023).
The molten salt storage system is a known method for storing the Energy absorbed by molten salt through the direct receiver. This system transfers the stored thermal Energy to a storage tank, which can be held at a high temperature of 565°C. When the Sun is unavailable, this stored thermal Energy can generate steam that powers the turbine (Linares et al., 2023).
A commonly used energy storage system for solar power plants involves two molten salt tanks acting as a heat transfer fluid (HTF) storage medium. This thermal storage technology was developed to overcome the issue of power generation during periods of low sunlight. Heat is captured and stored in the salt mixture within the tanks, designed with advanced insulation to prevent heat loss. This stored heat is then utilized at night for continued plant operation. Using a heat exchanger, the heat from the molten salt is transferred to water, creating steam to power the turbine for electricity generation (Pascual et al., 2022; Guccione and Guedez, 2023; Linares et al., 2023).
Since molten salt is in a single state, no phase change is involved; hence, latent Energy is not considered in the calculations. The model shows the analysis of sensible heat, which is the heat extracted due to the temperature change. This equation is used in the heat calculation blocks to plot the temperature outputs and the state of the molten salt tanks. Q represents the sensible heat, m is the mass of the molten salt, which is 11.825 kg for each instance, and the total salt used is 8,500 tons, as used in a solar tower power plant. C represents the specific heat of the molten salt mixture (sodium nitrate and potassium nitrate), which is 1.495 kJ/kg°C, and ΔT represents the temperature change. The difference in temperature of the molten salt tanks acts as a multiplier for the equation. The value of heat capacity changes with the change in temperature, and a more significant change in temperature results in a more excellent deal of Q (Song and Wu, 2017; Arias et al., 2022; Hua et al., 2022; Zhang et al., 2022).
In addition, the conventional controller, known as the PID controller, has been widely used in various industries for many years. It is considered to be the most appropriate controller for process industries. In solar thermal power plants, it is used to regulate the inlet temperature of the molten salt tank. The molten salt tank is a modern invention used to store heat for later use in running the power plant at night or when the weather is cloudy. However, the PID controller must be more intelligent to predict and maintain the temperature values. If a variable temperature source is provided to achieve temperature stability for the molten salt tank, it requires extensive mechanisms and sensory systems (Moghadam et al., 2017; Palenzu et al., 2022; Perez-Alvarez et al., 2022; Wang et al., 2023).
The acronym PID stands for proportional-integral-derivative, the individual terms that make up the standard three-term controller. PID controllers are widely used in various industries and are considered one of the most commonly used mechanical controllers. Even complex modern control systems may include a control network whose primary control building block is a PID control module.
PID controllers are widely used in process control and automation systems. They continuously measure the error between the set point and the actual process variable and adjust the control signal to minimize the error. The three terms of the PID controller contribute to the controller’s response to the error: the proportional term responds directly to the current error, the integral time accumulates past errors, and the derivative time predicts future errors. The PID controller needs a plant model to show the output curves, which contain the transfer function of the machinery or plant model. The three-term PID controller is the most widely used mechanical controller and has been adapted to work with digital control systems. It was the first controller to be mass-produced for the high-volume process industry market (Liu et al., 2022; Nour et al., 2023).
The TES system loop is a crucial component of a solar thermal power plant, where molten salt is a medium for storing thermal Energy. The loop commences with the heating source, which could either be the Sun or an artificial heating source, where the molten salt is heated to a high temperature. The PID controller is employed to achieve a smoother and desired output, which helps maintain the temperature of the molten salt at a predetermined set point.
The hot molten salt tank receives input from the PID controller and stores the high-temperature molten salt. The molten salt then flows through a heat exchanger, where it loses its heat due to thermal contact with a cold fluid, leading to a drop in its temperature. Subsequently, the complex molten salt is transferred to the cold molten salt tank for storage until it is needed again.
This cycle repeats as necessary, with the stored thermal Energy employed to generate steam, which can power a turbine to produce electricity. The TES system is a critical aspect of the solar thermal power plant, as it ensures a steady and consistent source of electricity, even when no sunlight is available.
In (Vignarooban et al., 2015), the author studied the efficiency and overall performance of solar thermal tower technology using molten salts. As per the study’s findings, using molten salts eliminates the need for oils and other chemicals commonly used in heat exchangers. The properties of solar salts, including their high temperature and specific heat, make them a promising alternative to lithium battery-based grid solutions.
In (Turchi et al., 2018), the author conducted a MATLAB-based simulation using a Fuzzy controller to evaluate the efficiency of a heat exchanger. The main objective of this research was to compare the performance of PID and Fuzzy controllers for the outlet temperature of the heat exchanger. The study compared two characteristics, overshoot and settling time, of both controllers. The findings revealed that the Fuzzy controller outperformed the PID controller in predicting the temperature based on the desired set point.
The study in the paper (Zarza, 2017) focused on the economic analysis of different solar thermal technologies. The report provides valuable insight into the current technology used in this field and briefly compares the economic benefits of electricity production from solar thermal technology. The study highlights the urgent need to shift towards renewable energy sources like solar thermal, which have the added advantage of thermal energy storage, making them a more reliable and linear output source of renewable energy, unlike wind and solar PV.
In (Soomar et al., 2023), various types of molten salts have been compared to identify the most suitable thermal stable salt for use in solar thermal technology. The study highlights the advantages of molten salts, such as their ability to operate at high temperatures of up to 800°C, making them a promising solution for commercial power plants. However, the paper also addresses the issue of corrosion that arises from the nature of the salts, which require consistent temperature control to remain within the operational temperature range.
The study in (Soomar et al., 2022) focuses on the thermal properties and composition of solar molten salts. The paper specifies a mixture of 60–40 (60% NaNO3 and 40% KNO3) and presents a detailed table of the high temperature of molten solar salt and other related properties. However, the issue of salt freezing arises when the molten salts lose temperature due to low sunlight or cloudy weather.
A heating system prevents salt from freezing and causing a coma in pipelines, similar to how the food industry uses heat to melt materials inside pipes and clear lines. Electrical cables are wrapped around specific areas to generate heat in this case. However, this system could be more effective at warning of salt freezing at a particular point, a unique problem encountered in concentrated solar power plants (Li et al., 2014; Yılmaz and Mwesigye, 2018; Nkele et al., 2023).
To address this issue, an electrical heating system has been developed to prevent salt from freezing. A research article in the Journal of Energies by Cristina Prieto proposes a freezing protection heat system. In another research article published by Salvatore Guccione, Rafael Guedez provides a review study of electrical heating.
This paper is primarily concerned with resolving the remaining issue of unstable temperature to achieve optimal heat extraction. The focus is on simulating a MATLAB-based model called the Self-Adaptive Heat Extraction Controller, which incorporates a fuzzy controller block to regulate temperature. If the temperature exceeds a certain threshold, the system triggers a mechanism to raise the temperature of the fluid flowing through the pipes. The SAHEC can extract the maximum efficiency from the available heat in the molten salts through predefined input functions and desired outputs.
In this section, the details about the proposed SAHEC design are presented. As SAHEC was designed on MATLAB SIMULINK before this, it is essential to understand the working mechanism of the solar thermal power plant and the place of the proposed controller. The changes proposed in the paper are related to the electrical part of the solar power tower. The introduction has discussed how molten salt’s thermal properties affect the performance of the system. Also, using PID controllers in solar technology has been discussed above in various papers.
Figure 1 illustrates the diagram of the solar thermal tower plant. Two tanks can be seen. Cold molten salt and hot molten salt are stored separately to preserve for usage. At night, hot salt is fetched to run the steam generation process. Also, the array of heliostats can be seen, reflecting the sunlight on the tower. At the same time, the heat exchanger is used to generate steam via thermal contact of water and hot molten salt. It provides an overview of the TES system. The loop of the system starts working from the heating source, and then the PID controller is used to provide smoother and desired output. The hot molten salt tank gets input from the PID controller, and after that, molten salt passes through the heat exchanger. Molten salt loses heat due to thermal contact with cold fluid in the heat exchanger; hence, temperature drops. Later, complex molten salt is deposited into a cold molten salt tank. Again, the loop starts with the Sun or artificial heating source.
FIGURE 1. Diagram of SOLAR Power tower, including molten salt thermal energy storage system, Heat exchanger, and heliostats field (Menéndez et al., 2014; González-Roubaud et al., 2017).
Self-adaptive heat extraction controller (SAHEC) is the model approach of this paper, which is simulated on MATLAB SIMULINK. This technique is based on the functions of MATLAB. It has been designed by adding the MATLAB coding function for the temperature of the Sun, fuzzy logic block, PID block, and TES block with transfer function. SAHEC is the block combination that outputs heat extraction using the given transfer function. To make it an intelligent system, a fuzzy logic block has been used to predict the temperature of molten salt revolving inside the pipes of a solar thermal tower. Further, the heat exchanger is simulated through the technique of MATLAB function.
Figure 2 depicts the model designed to simulate the working of a solar thermal tower. It can be seen that the fuzzy logic block receives input signals from two sources: Sun and Plant. After this, the output of the fuzzy controller is synchronized with the PID controller, which further tunes the output set point values for molten salt temperature (Table 1). The output stream from fuzzy-PID to the Plant is fed if the temperature from the Sun is in the operational range; otherwise, the fuzzy controller directly provides the desired temperature values to the external heating source (Table 2). Thus, the DCS-controlled closed loop system continuously feds temperature data to faint for the prediction of stable temperature.
FIGURE 2. Proposed model of the SAHEC containing MATLAB Simulink blocks Fuzzy and PID controller, relay, switch, and function of temp, scope, and plant model.
This model was designed to simulate the temperature changes due to controller rules. The fuzzy controller block works on well-defined rules in the background. It gives the output temperature, which depends upon two inputs. The input assigned to the controller is already defined as a range of variables consisting of three different membership functions.
The inputs of this controller are the temperature of the Sun, 1st variable in the fuzzy logic controller, and the second input temperature of tanks, which is continuous feedback in a loop to the controller on a run-time basis. Input two, the temperature of tanks, defines the controller the state of tanks (Table 3).
(Table 4) whereas the state of the tank is the status of the material form assigned as freezing, stable, and decomposition. Through fetched inputs, this controller maintains the stable region temperature for tanks. The stable region temperature is already set in the variable of the membership functions inside the information two of the controller.
Figure 3 illustrates the block diagram representing the Proposed SAHEC for the solar thermal tower power plant. In this block diagram, fuzzy logic can be seen as a controller connected with an additional heating source. An electric heater excites when it gets a faint signal from actuators and sensors. The electric heater heats the molten salt, fetching power from the turbine in a closed-loop system; it keeps the molten salt in a molten state. This bypass system rotates molten salt in pipes by disconnecting the supply from the thermal energy storage system. Hence, it keeps the plant in an active state.
Now, it is essential to understand the flow of this project. It starts from the input of the Sun. If the Sun is shining, the plant usually operates—with an electric heater, the SAHEC turns on the external heating source to maintain the molten salt temperature.
This controller was designed using MATLAB fuzzy Designer. The toolbar provides a more accessible platform to implement and simulate fuzzy logic. Logic for temperature control was implemented using this toolbar. As depicted.
Figure 4 illustrates the block diagram of the fuzzy logic toolbar. It can be seen that the proposed controller has two inputs and one output. Using this toolbar, two inputs were taken. These inputs contain membership functions as variables.
FIGURE 4. Block Diagram of MATLAB Fuzzy Logic Designer, containing the inputs (A), (B) and output (C).
The input1 contains Membership functions named temperature, which shows the temperature range received on the tower through the reflection of heliostats. The building gets an immense amount of heat reflected through heliostats, which raise the temperature at the top of the tower, from where the pipeline of molten salt is passed. This pipeline carries fluid that absorbs heat and revolves around a closed loop. The range set here for the temperature of the tower is [0 570], which may exceed in real time scenario at the plant. Whereas the curved displays the parameter set according to nominal temperature values for the solar tower, the operational temperature of the building where heat is absorbed is shown here. The operating temperature shows the initial state of 29
This input contains four different membership functions and a range of overlapping temperature parameters. These states were named ToM1, ToM2, ToM3 and ToM4. At the same time, the content for this input is similar for all the membership functions but with different parameters, respectively. These membership functions show the overlapping behavior of molten salt temperature.
These parameters show the mid value, the peak value where the state of salt changes. Initially, 270–290
The output window comprises four membership functions, which are states of molten salt. These states were named VL, Low, High, and VH. These states result from temperature changes affecting molten salt rotating in the solar tower.
A fuzzy logic controller works based on a set of defined rules. Here, the following rules were determined, as shown in the table.
Rules described in the fuzzy logic controller are based upon two inputs and one output function, which are further distributed into four each. As input1 has four variables ToS1, ToS2, ToS3, AND ToS4. Similarly, Input2 has ToMT1, ToMT2, ToMT3, and ToMT4. Lastly, the Output variables are VLow, Low, High, and VH.
The sophisticated built-in block of MATLAB Simulink is this work’s ultimate building block. Finding the relevant union and using it by changing properties accordingly is straightforward. It would not be wrong to say MATLAB has provided a great platform to add a feather to the cap of research areas.
Heat extraction at solar thermal power requires broad knowledge to implement the block. For example, the heat exchanger block, an essential block in heat extraction, cannot be implemented quickly, but the built-in block provides the features of HX easy and ready to be used. But in my scenario, that built-in partnership required a physical system to be developed in a SIMULINK environment. Later on, the heat exchanger model was implemented through a transfer function taken from reference papers.
The heat extraction block was not alone enough to simulate the working principle of a solar thermal power plant. To accomplish the whole task, the next target was to design the model of a solar thermal power plant using MATLAB SIMULINK. Solar thermal power plant has many blocks such as Thermal energy storage, Heliostats field, power block, and tower. For simulation, the thermal energy storage system was most prominent.
Hence, using the transfer function technique, the two hot and cold molten salt tanks were modeled on SIMULINK. Both the molten salt tanks play a vital role in preserving the salt in molten form for nighttime. Salt stored in both tanks is pumped into a heat exchanger at night to generate power.
Figure 5 illustrates the MATLAB model of a solar thermal tower with TES and heat extraction block. This model contains the two molten salt storage tanks, the Heat exchanger, and the Heat extraction block, a user-defined function discussed below. The lines between blocks show the pipe lines’ path through which molten salt passes through pumping.
FIGURE 5. SIMULINK model of solar thermal power plant showing two tanks, heat exchanger, and heat extraction block.
Further, the next target was to design the heat extraction block or system to calculate the heat extracted during simulation time and store that data in a variable in MATLAB to evaluate. The heat extraction block is the sensor system that reads the constant temperature of inlets at the Heat exchanger. The inlet temperature at the heat exchanger input and output provides the temperature difference through which the system can calculate the total heat extraction done by the Heat exchanger. This requires logic, which was implemented through MATLAB coding. A heat extraction function was designed to calculate the heat in run time and save it in the variable in MATLAB. Block-required data were provided in coding and implemented into SIMULINK through a user-defined function.
The transfer functions of the heat exchanger are shown in Figure A1 in the supplementary data. It was used in paper (Perez-Alvarez et al., 2022). This transfer helps the MATLAB model to simulate the behavior of the shell tube heat exchanger. The heat exchanger is an essential element of the heat extraction process. This transfer function is used to determine the temperature of a cold salt tank. After passing through the heat exchanger and condenser, the salt temperature must be above 290°
Figure 6 illustrates the heat extraction function used to calculate the total heat extraction. This block is based on a SIMULINK user-defined role with MATLAB coding. Block required initial data of mass and specific heat of molten salt, provided in function. The ABS function is also used to mitigate the negative values passed by the adder block. Later, these values are stored in Heat, Temp, and Temperature difference, variables of MATLAB.
FIGURE 6. User-defined function block to calculate heat extraction, containing variables and absolute block.
Furthermore, the following implementation phase was to develop the mechanism of the Heliostats field. The Heliostats field is the principal block of a solar thermal power plant. Through large mirrors called heliostats Sun, light is concentrated on the top of the tower. The receiver is installed at the top of the building to provide the thermal environment for pipes inside the chamber. Heat transfer between the tube and chamber occurs due to the receiver. This number of heliostats is required to reach the necessary temperature in simulation. Another MATLAB function was programmed to simulate the heliostat field. Named the temperature function, it provides the necessary temperature for the receiver to depict real-time scenarios on the plant site.
To develop the mechanism of the heliostats field, the Heliostats field is the principal block of a solar thermal power plant. Through large mirrors called heliostats, sunlight is concentrated on the top of the tower. The receiver is installed at the top of the building to provide the thermal environment for pipes inside the chamber. Heat transfer between the tube and chamber occurs due to the receiver. This number of heliostats is required to reach the necessary temperature in simulation. Another MATLAB function was programmed to simulate the heliostat field. Named the temperature function, it provides the temperature the receiver needs to depict real-time scenarios on the plant site.
Figure 7 depicts the temperature function, a user-defined function block, having MATLAB coding to simulate the heliostats field’s working mechanism. It provides the temperature achieved by the existing heliostat field, 546°C. It gives the temperature of storage tanks for nighttime, which remains zero. Heliostats are large mirrors that concentrate the light over a single point on the top of the tower. A heliostats field was hard to design with just a real-time temperature (tried) because a temperature sensor provides the temperature of a single Sun. In contrast, heliostats concentrate thousands of suns through a mirror image.
FIGURE 7. Temperature function to work as heliostats field for the designed solar thermal power plant model.
The MATLAB function is connected to the clock, which is the internal clock of the computer simulating to match the seconds with the temperature function to give output for day and night. Figures 8 and 9 depicts the picture of the temperature function. This block is a defined block of MATLAB SIMULINK. It was used to provide heliostat field temperature to the model.
Whenever an undesired value is fed into the controller as input, it decides accordingly and gives an output from the defined range of stable membership function. The deal comes out as output, described in the t membership function as Very low, Low, High, and Very High. The temperature range goes to the tanks; later, that temperature is maintained according to the Sun’s temperature. In a real-time scenario, this output will be fed into a system with a sensor system and external heat source, such as an electrical heating system or robotics arm, to heat the particular point where the temperature drops. Similarly, this controller gives an output of temperature range, which is fed in the block of function already defined through MATLAB code and linked in partnership to calculate the heat output through a formula which is given below:
Where:
Q = heat energy (Joules, J).
m = mass of a substance (kg)
c = specific heat (units J/kg∙K).
∆ is a symbol meaning “the change in.”
∆T = change in temperature (Kelvins, K).
The above-given screenshot above shows the process used in MATLAB to calculate the heat output of the model. Input for this module function is temperature T and difference of temperature Delta T. Molten salt does not store heat below
Where:
H (T) = function of heat, dependent on temperature.
T = temperature of molten salt.
The proposed Self-adaptive Heat extraction controller, SAHEC, will be fully functional when the heat in molten salt storage ends. The proposed model provides the inlet temperature to maintain a smoother plant operation. Here, it can be seen that the temperature stability achieved with the PID fuzzy approach is efficient during the transition period. The transition period is when the system shifts from the molten storage system to SAHEC. Here, it is also important to note that heat extraction, which becomes zero when molten salt storage ends, is fetched into the system by the proposed SAHEC efficiently. This depicts a smoother plant operation even in harsh weather.
The proposed controller provides a solution to enhance temperature stability, as depicted in the above graph. Along with inlet temperature stability, the submitted controller gives an efficient solution to the required temperature predictive system for extended periods. This controller provides a temperature range of operation under the molten salt hot temperature bounds limit.
The transition shows that using actuators and sensors can further improve temperature stability. The difference between rise and fall can be mitigated by setting a system of sensors to give directions to an electric heater. As the electrical heating system is mentioned in the literature review, that idea synchronizes with this proposed controller. At the same time, it suggested that SAHEC will further enhance the heating system. Such a model of electric heating with resistance can be aligned with sensors to give a uniform output for molten salt tanks and pipelines.
Figure 10 shows the output of SAHEC. Here, heat extraction is maximum for the period of 45 h–1.7 2−days. When molten salt storage has ended and the Sun is not around. The primary aim of this controller was to keep the molten salt in a state so that plant operation ran smoothly. Due to the high freezing temperature, which is 220
The molten salt tank’s inlet temperature is vital to keep molten salt active and working. A Thermal energy storage system maintains the temperature at night for the secondary source. It can be seen here that the proposed SAHEC Model maintains the temperature of molten salt through SAHEC. When the molten salt storage system ends, and the receiver temperature is zero, the conventional controller will shut down the plant. The proposed controller tracks and maintains the temperature value using an external heating source. Heat extraction is maximum when molten salt storage has ended, and the Sun is not around due to the high freezing temperature, which is superscriptis
Here, it can be seen that after molten salt storage ends and the Sun is unavailable, the inlet temperature of the hot molten salt tank drops. Molten salt storages need constant temperature for smoother plant operation. In this scenario, the plant would be shut down to prevent salt from moving into pipes, and the heating system would be started to avoid salt freezing into the lines. Subsequently, Here, the response of the proposed controller is standard, which needs a heating source to maintain the inlet temperature of the molten salt storage tank.
The previous work on Solar thermal towers concludes that temperature stability is a prevailing issue. When molten salt is below 220
Figure 11 compares heat extraction in kilo-joules over the centigrade temperature. Here, the X-axis shows the temperature, and the Y-axis shows the heat. Both graphs show the apparent difference in heat extraction. The first graph shows the conventional method to extract heat in kJ. Whereas the second graph depicts the SAHEC extracts heat in kJ but more than later. The overall efficiency improved here will depend more on the hours when weather is not typical than the conventional SAHEC method.
Supplementary Figure (a) depicts the heat extraction of the conventional controller. The molten salt storage tank ends when the plant faces zero state, where it can freeze the salt in the pipelines. PID controller may try to maintain the input temperature at the inlet of the heat exchanger. Still, if the principle and secondary source become zero, PID cannot keep the inlet temperature. To maintain, an intelligent controller is required, which can fire the value needed to maintain inlet temperature along with the PID controller.
Moreover, the proposed SAHEC maintains the temperature between the ranges of stable regions for heat extraction, as defined in the rules. Hence, the heat extraction, as shown in the simulation, remains higher for minimum temperature difference, as shown in the graphs. The Simulink provided a user-defined function to simulate the receiver’s temperature as input for simulation purposes. For each value, FLC fires a deal, which is fed into the system.
Heat extraction of SAHEC is continuous with fewer fluctuations, as shown in supplementary data figure A3. At the same time, the heat extraction of the PID controller changes due to the delayed settling time. The ripples of temperature crossing the temperature bound makes heat extraction zero here. As written in the literature review, molten salt stores heat below 565
The graph in supplementary data Figure A4 compares the proposed SAHEC with the PID controller. Here, it can be seen that SAHEC offers better stability than the PID controller. The proposed SAHEC tries to maintain the inlet temperature of a hot molten salt tank. Therefore, the comparatively presented SAHEC lets the solar thermal power plant operation run smoother and more efficiently than the conventional plant model.
In Figure 12, the comparison of temperature between SAHEC and PID shows the difference in operation and working capacity. SAHEC works when the Sun is not around due to the external heating system attached. At the same time, the fuzzy system makes it more robust in decision-making to fire a temperature value in a stable region.
FIGURE 12. The graph shows the Heat extraction of SAHEC over 45 h (A). Figure (B) also gives a close view to provide the view on the second level.
In a paper (Perez-Alvarez et al., 2022), the best settling time is 66.82 s with a 9.5% overshoot. At the same time, the proposed SAHEC showed 44.1 s with 10.8%. The settling time of SAHEC is 22.72 s slower than the Fuzzy-PID controller of the paper mentioned above. This paper compares the PID controller with two types of Fuzzy-PID controllers based on different membership functions. Both of the Fuzzy-PID schemes performed lower than the proposed SAHEC. The difference is due to the rules defined in fuzzy logic design. Hence, the proposed SAHEC performed much better than the details given in this section with the comparison of MATLAB-designed models.
The designed SAHEC has demonstrated temperature stability across various input temperatures, assuming 8,500 tons of molten salt for sizeable thermal energy storage. Maximum heat extraction occurs when the additional heat source is activated after the storage system ends within the 290°C–565°C range for the solar thermal tower operating region. The SAHEC tracks temperature inputs based on predefined areas within the membership function to enable the fuzzy logic controller to trigger Vlow, Low, High, and VHigh temperature values, maintaining a stable tank temperature for optimal heat storage. This helps avoid the “coma state” by controlling tank and pipeline temperature through a temperature control mechanism in the solar thermal plant.
Adopting sustainable and renewable Energy is crucial, with solar thermal Energy being one of the best resources to bridge the gap in clean energy generation. Solar thermal technology, especially the solar thermal tower, has gained momentum, and this research contributes to improving temperature stability and heat extraction in this domain. The proposed SAHEC has demonstrated greater heat extraction after thermal energy storage ends, with maximum heat extraction observed at a higher temperature range. A comparative analysis showed that SAHEC outperforms the conventional PID controller, with 65% better performance due to less rising and settling time with a slightly higher overshoot. Using the fuzzy logic controller with PID results in better output performance and robustness, and using SAHEC can extract much higher heat than the prevailing technique.
The original contributions presented in the study are included in the article/supplementary materials, further inquiries can be directed to the corresponding author.
FA: Conceptualization, Formal Analysis, Writing–original draft, Writing–review and editing. LG: Funding acquisition, Methodology, Writing–original draft, Writing–review and editing. FA: Conceptualization, Data curation, Methodology, Supervision, Writing–original draft, Writing–review and editing. FH: Conceptualization, Investigation, Software, Writing–original draft, Writing–review and editing. SH: Methodology, Supervision, Writing–original draft, Writing–review and editing. AS: Conceptualization, Investigation, Methodology, Software, Validation, Writing–original draft, Writing–review and editing. SK: Formal Analysis, Project administration, Supervision, Validation, Writing–review and editing.
The author(s) declare financial support was received for the research, authorship, and/or publication of this article. The Author managed all the funding. LG, and his company Power China Huadong Engineering Co., Ltd., Hangzhou China.
All authors have helped complete this paper, and we would like to express our gratitude to Power China Huadong Engineering Co., Ltd., Hangzhou, China, for their assistance in data collection.
LG was employed by the Power China Huadong Engineering Co., Ltd.
The remaining authors declare that the research was conducted in the absence of any commercial or financial relationships that could be construed as a potential conflict of interest.
All claims expressed in this article are solely those of the authors and do not necessarily represent those of their affiliated organizations, or those of the publisher, the editors and the reviewers. Any product that may be evaluated in this article, or claim that may be made by its manufacturer, is not guaranteed or endorsed by the publisher.
The Supplementary Material for this article can be found online at: https://www.frontiersin.org/articles/10.3389/fenrg.2023.1269572/full#supplementary-material
Arias, I., Cardemil, J., Zarza, E., Valenzuela, L., and Escobar, R. (2022). Latest developments, assessments and research trends for next generation of concentrated solar power plants using liquid heat transfer fluids. Renewable and Sustainable Energy Reviews.
Debnath, M. K., Sinha, S., and Mallick, R. K. (2018). Automatic Generation Contol Including Solar Themal Power Generation with Fuzzy-PID controller with Derivative Filter. Int. J. Renew. Energy Res. (IJRER) 8 (1), 26–35. doi:10.20508/ijrer.v8i1.6527.g7277
González-Roubaud, E., Pérez-Osorio, D., and Prieto, C. (2017). Review of commercial thermal energy storage in concentrated solar power plants: steam vs. molten salts. Renew. Sustain. energy Rev. 80, 133–148. doi:10.1016/j.rser.2017.05.084
Guccione, S., and Guedez, R. (2023). Techno-economic optimization of molten salt based CSP plants through integration of supercritical CO2 cycles and hybridization with PV and electric heaters. Energy 283, 128528. doi:10.1016/j.energy.2023.128528
Hua, L.-G., Memon, Q. A., Shaikh, M. F., Shaikh, S. A., Rahimoon, R. A., Shah, S. H. H., et al. (2022). Comparative Analysis of Power Output, Fill Factor, and Efficiency at Fixed and Variable Tilt Angles for Polycrystalline and Monocrystalline Photovoltaic Panels—The Case of Sukkur IBA University. Energies 15, 3917. doi:10.3390/en15113917
Li, C.-J., Li, P., Wang, K., and Molina, E. E. (2014). Survey of Properties of Key Single and Mixture Halide Salts for Potential Application as High Temperature Heat Transfer Fluids for Concentrated Solar Thermal Power Systems. AIMS Energy 2, 133–157. doi:10.3934/energy.2014.2.133
Linares, J. I., Martín-Colino, A., Arenas, E., Montes, M. J., Cantizano, A., and Pérez-Domínguez, J. R. (2023). Carnot Battery Based on Brayton Supercritical CO2 Thermal Machines Using Concentrated Solar Thermal Energy as a Low-Temperature Source. Energies 16, 3871. doi:10.3390/en16093871
Liu, W., Bie, Y., Xu, T., Cichon, A., Królczyk, G., and Li, Z. (2022). Heat transfer enhancement of latent heat thermal energy storage in solar heating system: A state-of-the-art review. J. Energy Storage 46, 103727. doi:10.1016/j.est.2021.103727
Menéndez, R. P., Martínez, J. Á., Prieto, M. J., Barcia, L. A., and Sánchez, J. M. M. (2014). A novel modeling of molten-salt heat storage systems in thermal solar power plants. Energies 7 (10), 6721–6740. doi:10.3390/en7106721
Moghadam, N., Shabaninia, F., and Abbasi, H. (2017). “Superiority of using interval type-2 fuzzy PID controller over the conventional type-1 fuzzy controller in a chlorine flow control system,” in 2017 5th Iranian joint congress on fuzzy and intelligent systems (CFIS) (IEEE), 128–135.
Nkele, A. C., Ikhioya, I. L., Chime, C. P., and Ezema, F. I. (2023). Improving the Performance of Solar Thermal Energy Storage Systems. J. Energy Power Technol. 05, 1–25. doi:10.21926/jept.2303024
Nour, M., Magdy, G., Chaves-Ávila, J. P., Sánchez-Miralles, Á., and Jurado, F. (2023). A new two-stage controller design for frequency regulation of low-inertia power system with virtual synchronous generator. J. Energy Storage 62, 106952. doi:10.1016/j.est.2023.106952
Palenzuela, P., Roca, L., Asfand, F., and Patchigolla, K. (2022). Experimental assessment of a pilot scale hybrid cooling system for water consumption reduction in CSP plants. Energy 242, 122948. doi:10.1016/j.energy.2021.122948
Pascual, S., Lisbona, P., and Romeo, L. M. (2022). Thermal Energy Storage in Concentrating Solar Power Plants: A Review of European and North American R&D Projects. Energies 15 (22), 8570. doi:10.3390/en15228570
Perez-Alvarez, R., Gonzalez-Gomez, P. A., Santana, D., and Acosta-Iborra, A. (2022). Preheating of solar power tower receiver tubes for a high-temperature chloride molten salt. Appl. Therm. Eng. 216, 119097. doi:10.1016/j.applthermaleng.2022.119097
Prieto, C., Rodríguez-Sánchez, A., Ruiz-Cabañas, F. J., and Cabeza, L. F. (2019). Feasibility study of freeze recovery options in parabolic trough collector plants working with molten salt as heat transfer fluid. Energies 12 (12), 2340. doi:10.3390/en12122340
Qaisrani, M. A., Ahmed, N., and Wang, Q. (2022). “Working, Modeling and Applications of Molten Salt TES Systems,” in Synergy development in renewables assisted multi-carrier systems. Green energy and technology. Editors M. Amidpour, M. Ebadollahi, F. Jabari, M. R. Kolahi, and H. Ghaebi (Springer).
Roper, R., Harkema, M., Sabharwall, P., Riddle, C., Chisholm, B., Day, B., et al. (2022). Molten salt for advanced energy applications: a review. Annals of Nuclear Energy.
Saldivia, D., and Taylor, R. A. (2023). A Novel Dual Receiver–Storage Design for Concentrating Solar Thermal Plants Using Beam-Down Optics. Energies 16, 4157. doi:10.3390/en16104157
Song, Q., and Wu, Y. (2017). “Study on the Robustness Based on PID Fuzzy Controller,” in 2017 international conference on computing intelligence and information system (CIIS) (IEEE), 142–145.
Soomar, A. M., Guanghua, L., Shaikh, S., Shah, S. H. H., and Musznicki, P. (2023). Scrutiny of power grids by penetrating PV energy in wind farms: a case study of the wind corridor of Jhampir, Pakistan. Front. Energy Res. 11, 11. doi:10.3389/fenrg.2023.1164892
Soomar, A. M., Hakeem, A., Messaoudi, M., Musznicki, P., Iqbal, A., and Czapp, S. (2022). Solar Photovoltaic Energy Optimization and Challenges. Front. Energy Res. 10, 10. doi:10.3389/fenrg.2022.879985
Turchi, C. S., Vidal, J., and Bauer, M. (2018). Molten salt power towers operating at 600–650 ◦C: salt selection and cost benefits. Sol. Energy 164, 38–46. doi:10.1016/j.solener.2018.01.063
Vignarooban, K., Xu, X., Arvay, A., Hsu, K., and Kannan, A. (2015). Heat transfer fluids for concentrating solar power systems—A review. Appl. Energy 146, 383–396. doi:10.1016/j.apenergy.2015.01.125
Wang, W. Q., Li, M. J., Guo, J. Q., and Tao, W. Q. (2023). A feedforward-feedback control strategy based on artificial neural network for solar receivers. Appl. Therm. Eng. 224, 120069. doi:10.1016/j.applthermaleng.2023.120069
Yılmaz, I. H., and Mwesigye, A. (2018). Modeling, simulation and performance analysis of parabolic trough solar collectors: A comprehensive review. Appl. Energy 225, 135–174. doi:10.1016/j.apenergy.2018.05.014
Zarza, E. (2017). “Innovative working fluids for parabolic trough collectors,” in Advances in concentrating solar thermal research and technology (Sawston, UK: Woodhead Publishing), 75–106.
Keywords: solar thermal, solar tower, molten salt, fuzzy logic, renewable energy
Citation: Ahmed F, Guanghua L, Akram F, Hussain F, Hussain Shah SH, Soomar AM and Kamel S (2023) Self-adaptive heat extraction controller for solar thermal tower operational with molten salt tanks. Front. Energy Res. 11:1269572. doi: 10.3389/fenrg.2023.1269572
Received: 30 July 2023; Accepted: 28 September 2023;
Published: 12 October 2023.
Edited by:
Luis Martin Pomares, Dubai Electricity and Water Authority, United Arab EmiratesReviewed by:
Shaopeng Guo, Xi’an University of Architecture and Technology, ChinaCopyright © 2023 Ahmed, Guanghua, Akram, Hussain, Hussain Shah, Soomar and Kamel. This is an open-access article distributed under the terms of the Creative Commons Attribution License (CC BY). The use, distribution or reproduction in other forums is permitted, provided the original author(s) and the copyright owner(s) are credited and that the original publication in this journal is cited, in accordance with accepted academic practice. No use, distribution or reproduction is permitted which does not comply with these terms.
*Correspondence: Syed Hadi Hussain Shah, aGFkaS5zaGFoQGppbm5haC5lZHU=
Disclaimer: All claims expressed in this article are solely those of the authors and do not necessarily represent those of their affiliated organizations, or those of the publisher, the editors and the reviewers. Any product that may be evaluated in this article or claim that may be made by its manufacturer is not guaranteed or endorsed by the publisher.
Research integrity at Frontiers
Learn more about the work of our research integrity team to safeguard the quality of each article we publish.