- School of Aeronautics and Astronautics, Sun Yat-sen University, Guangzhou, Guangdong, China
To address the heat transfer degradation that occurs in the top section of horizontal pipes when sCO2 fluid flows are heated, the upper half wall with higher temperatures is particularly roughened using uniform sand-grain roughness. The SST
1 Introduction
Supercritical CO2 (sCO2) has gained widespread recognition as an ideal working fluid for various energy and power cycles, owing to its several distinct advantages. These include favorable properties that enable higher cycle efficiency (Mendez Cruz and Rochau, 2018), reduced compression work and cycle size due to its high density, and a more accessible critical pressure (
In the proximity of the critical and pseudocritical points, sCO2 thermophysical properties undergo significant changes, leading to peculiar heat transfer behaviors. One of these behaviors is the heat transfer deterioration and heterogeneity that occur in horizontal sCO2 fluid flows. As demonstrated in the work of Kumar and Basu (2021) and Theologou et al. (2022), temperatures of the top wall are much higher, and the heat transfer is severely degraded. This impairment near the top not only negatively affects the overall heat transfer performance but also causes greater wall thermal stress, which poses a threat to the safety of heat exchange equipment. To relieve supercritical heat transfer deterioration in the top and improve uniformity over the periphery, fins (Han et al., 2022), internal ribs (Mao et al., 2022), and metal foams (Liu et al., 2015) have been added and studied. These technologies have been shown to notably improve horizontal sCO2 heat transfer; however, they also have non-negligible drawbacks, such as high manufacturing and maintenance costs and significant extra friction loss.
The use of wall roughness, particularly sand-grain roughness, has been explored to enhance turbulent heat transfer of channel flows. With the aid of direct numerical simulation (DNS), Forooghi et al. (2018) systematically studied the influence of sand-grain roughness on the convection heat transfer of turbulent channel flows and observed the augmentation of heat transfer. Latini et al. (2022) numerically modeled the increased heat transfer of coolant flow for liquid rocket engines with high surface roughness. With the help of additive manufacturing, Stimpson et al. (2016) measured heat transfer with wall roughness and found much higher Nusselt numbers than in smooth channels. Although significant heat transfer enhancements have been demonstrated in the literature, wall roughness is barely investigated in supercritical heat transfer. Zhang et al. (2020) comprehensively reviewed the enhancing technologies used for turbulent sCO2 heat transfer and suggested that wall roughness is a potential approach to effectively mitigate the deterioration. Most recently, Chen et al. (2022) first introduced sand-grain wall roughness to improve sCO2 heat transfer in a vertical tube, demonstrating remarkable mitigation of heat transfer impairment as evidenced by the drops in measured wall temperatures.
This study utilizes the uniform sand-grain wall roughness as a means to alleviate heat transfer degradation and improve homogeneity over the circumference of turbulent sCO2 flowing through horizontal tubes. The half-roughen scheme was used, which focuses specifically on the upper half surface where deterioration occurs. Computational fluid dynamics (CFD) simulations are conducted employing the SST
2 Numerical approach
2.1 Governing equations
The horizontal sCO2 flows are solved by the steady Navier–Stokes equations, which are formulated as follows based upon the Cartesian coordinates.
Continuity:
Momentum:
Energy:
where
Due to the good capability of dealing with both the boundary and core flows, the SST
More details on the various terms and model constants can be found in the work of Menter (1994).
2.2 Physical model and simulation methods
Figure 1 displays the horizontal round tube (
2.3 Model validations
The experiments conducted by Chen et al. (2022) are employed for the validation of the SST
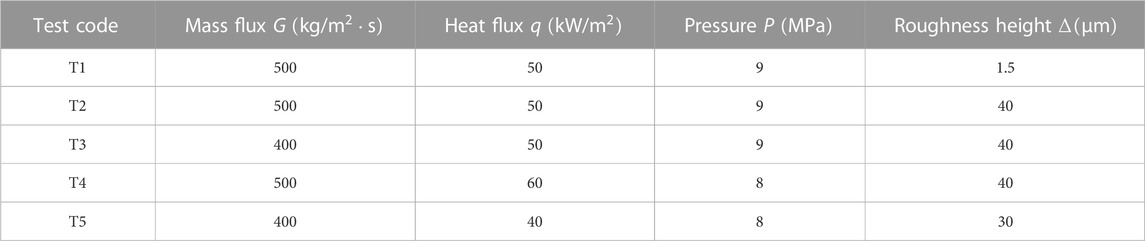
TABLE 1. Cases to be validated from the measurements by Chen et al. (2022).
Figure 2 compares the simulated wall temperatures against the experimental data. Good consistencies were exhibited for all the cases, and the maximum deviation is within
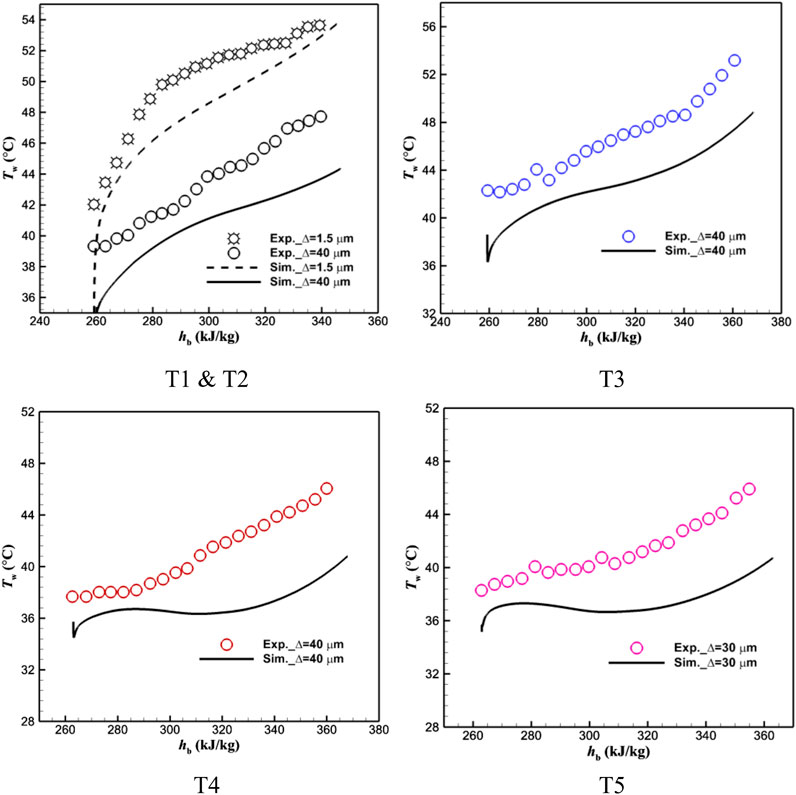
FIGURE 2. Wall temperatures of rough sCO2 heat transfer from simulations predicted by the SST
2.4 Half-roughen scheme
As shown in Figure 3A for the smooth horizontal sCO2 flows, because of buoyancy effects, an obvious gap exists for the wall temperature profiles over the two peak surfaces; turbulent heat transfer impairs at the top and behaves normally around the bottom. The heat transfer difference can be also reflected by the
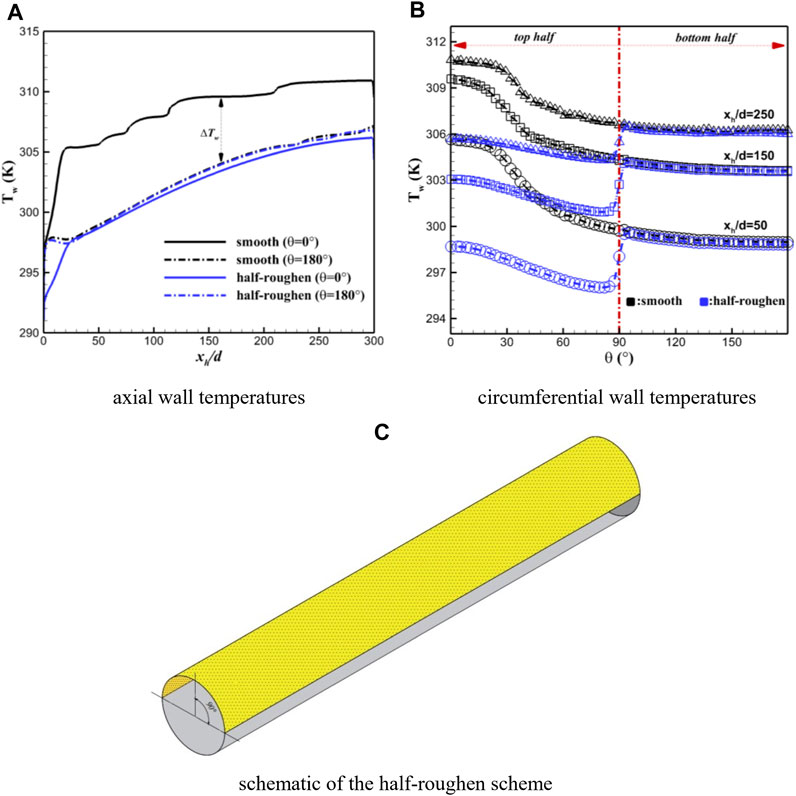
FIGURE 3. Change in wall temperature profiles (A, B) of horizontal sCO2 heat transfer brought about by half-roughen approach (C) at
3 Results and discussion
CFD calculations involving a range of roughness heights and operating parameters were performed to form a systematic study. The condition details are listed in Table 2. According to the classic tests on the piping flows with sand-grain roughness by Nikuradse (1950), five different values for the relative roughness heights (
3.1 Baseline case
This section discusses the results of the baseline case, where medium-level buoyancy effects are induced under the specific condition. Since this work introduces sand-grain wall roughness aiming to relieve the top heat transfer degradation and then ameliorate heat transfer homogeneity, the wall temperature gap that directly illustrates the circumferential uniformity is presented. In addition, under the studied conditions of constant heat flux, the exhibited wall temperatures are able to well reflect the variations of the local heat transfer coefficient or Nusselt number. Figure 4 displays the axial distributions of top wall temperatures of horizontal sCO2 flowing in the smooth and various half-roughen tubes, where the bottom
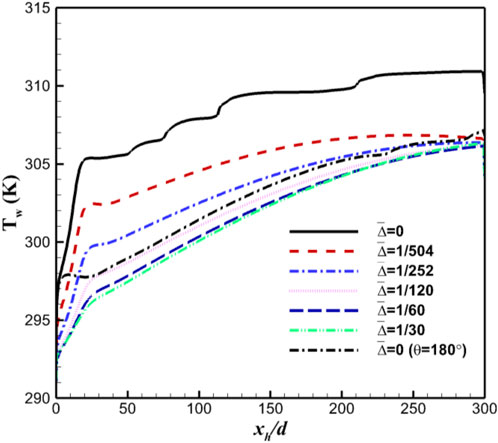
FIGURE 4. Temperature profiles along top wall of sCO2 flowing in smooth and half-roughen (with various roughness heights) horizontal tubes under the baseline condition.
Figure 5 compares the thermofluid behavior of horizontal sCO2 flowing in the smooth and half-roughen (
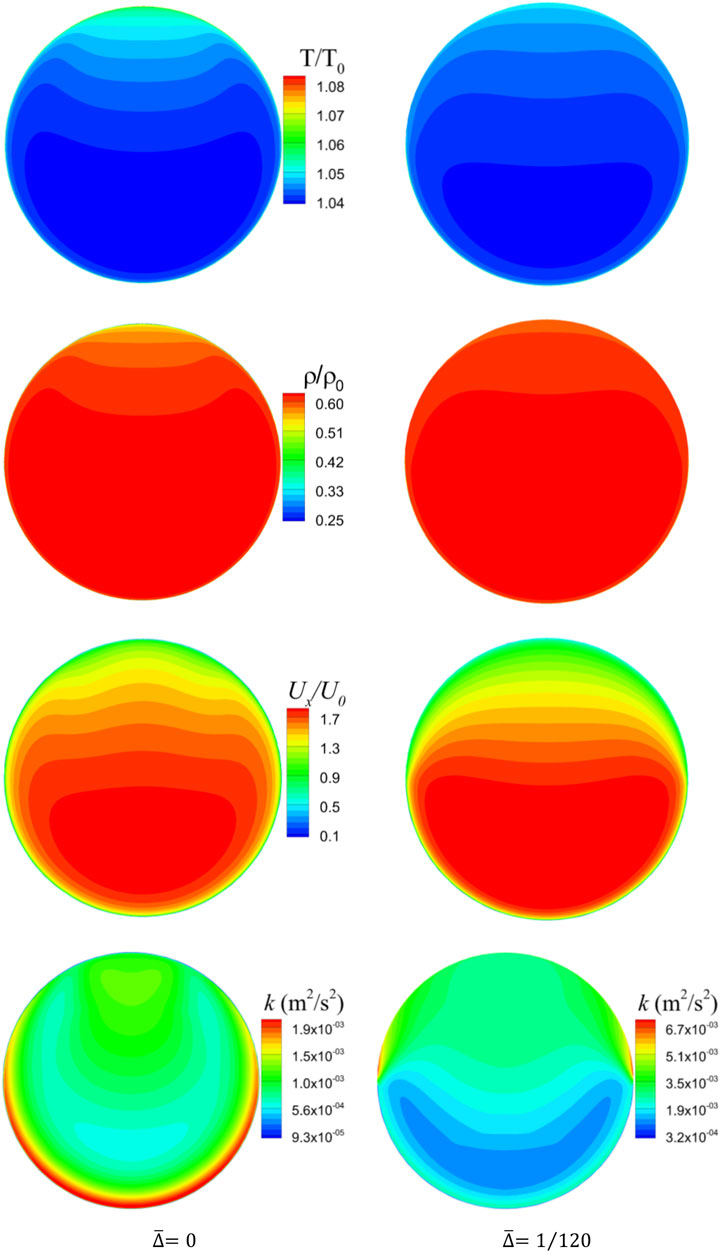
FIGURE 5. Influences of half-roughen wall roughness on thermofluids of horizontal sCO2 flows, where temperature
3.2 Simulations under different operating conditions
3.2.1 Effect of mass flux
The influences of various typical operating parameters are then analyzed. Figures 6A, B show the top wall temperature distributions under two different mass fluxes, where other parameters are maintained the same as the baseline case. As can be seen, when the value of mass flux decreases to
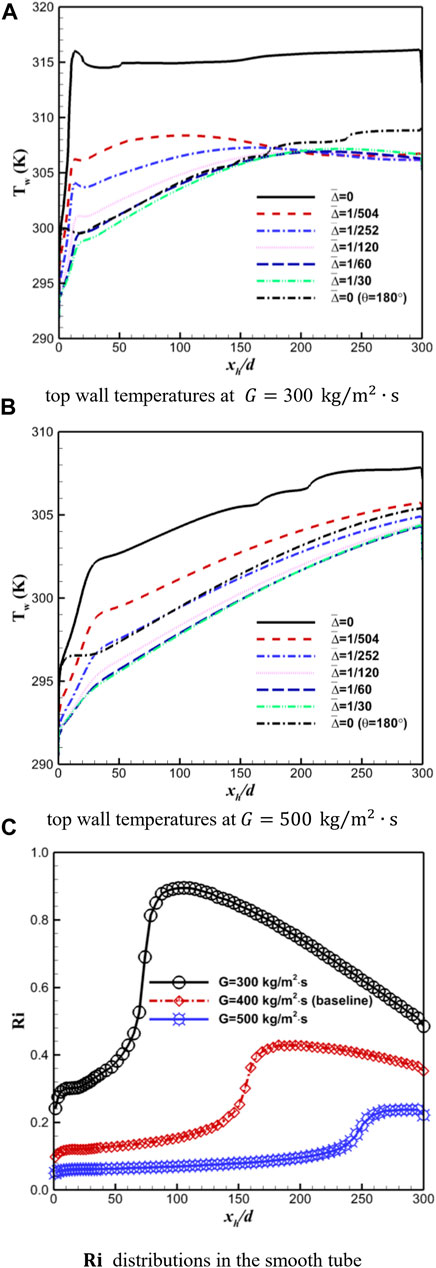
FIGURE 6. Temperature profiles along the top wall (A, B) of horizontal sCO2 heat transfer with various roughness heights and buoyancy strength variations (C) of smooth sCO2 flows under two characteristic mass fluxes.
Comparing the two sets of distributions, it is worth noting that for the higher mass flux of
Figure 6C presents the variations of Richardson number of smooth sCO2 flows under the two mass fluxes, where the values of the baseline case are also added for comparison. This buoyancy parameter

FIGURE 7. Temperature contours (A) of smooth sCO2 flows and turbulence kinetic energy contours (B) of horizontal sCO2 with various roughness heights at
The turbulence (
3.2.2 Effect of heat flux
With the change in the heat flux applied during the calculations, the calculation outcomes are displayed in Figure 8. For the low heat flux of
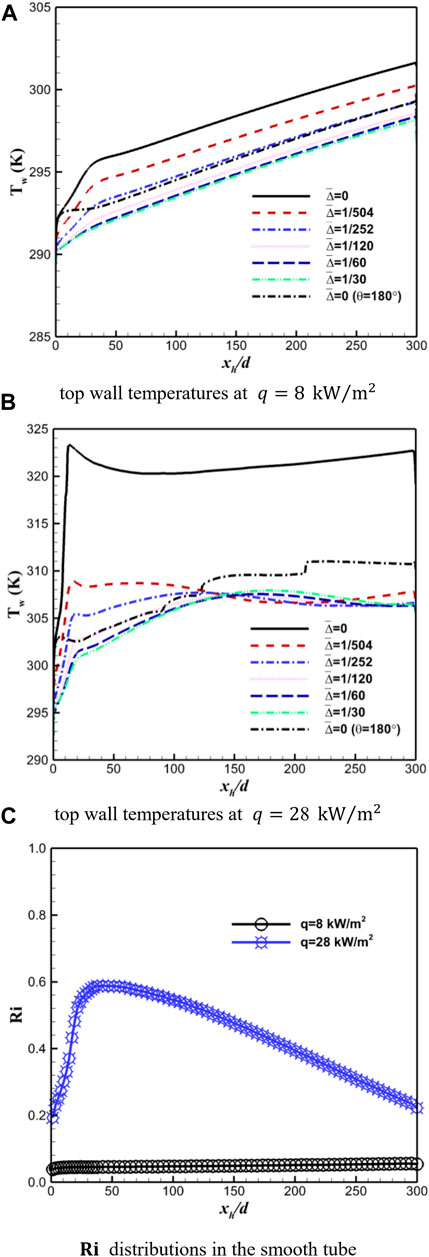
FIGURE 8. Temperature profiles along the top wall (A, B) of horizontal sCO2 heat transfer with various roughness heights and buoyancy strength variations (C) of smooth sCO2 flows under two characteristic heat fluxes.
Here, it can be found that at
3.2.3 Effect of pressure
Figures 9A, B present the top wall temperature distribution with the different roughness heights under two larger operating pressures of
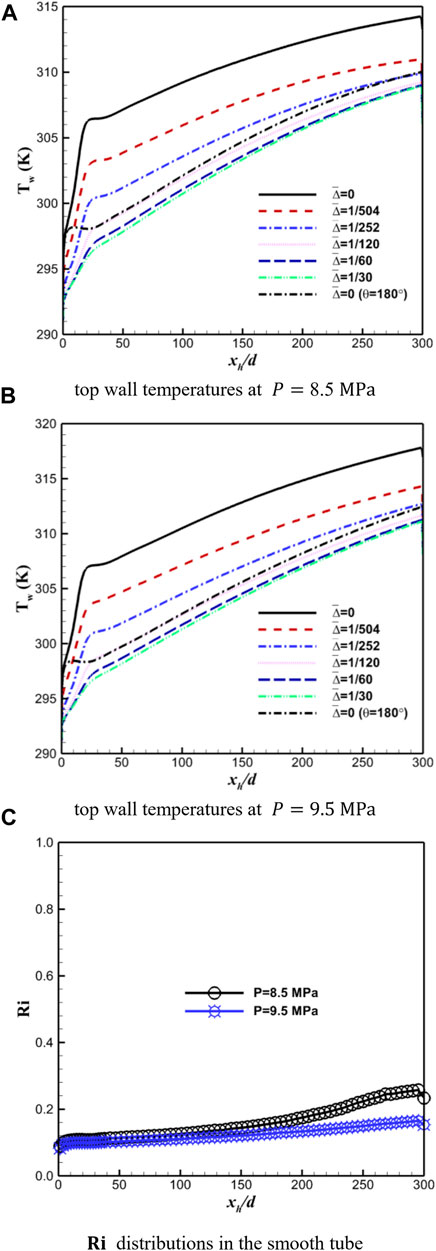
FIGURE 9. Temperature profiles along the top wall (A, B) of horizontal sCO2 heat transfer with various roughness heights and buoyancy strength variations (C) of smooth sCO2 flows under two characteristic pressures.
3.2.4 Effect of inlet temperature
With the inlet temperature increasing up to
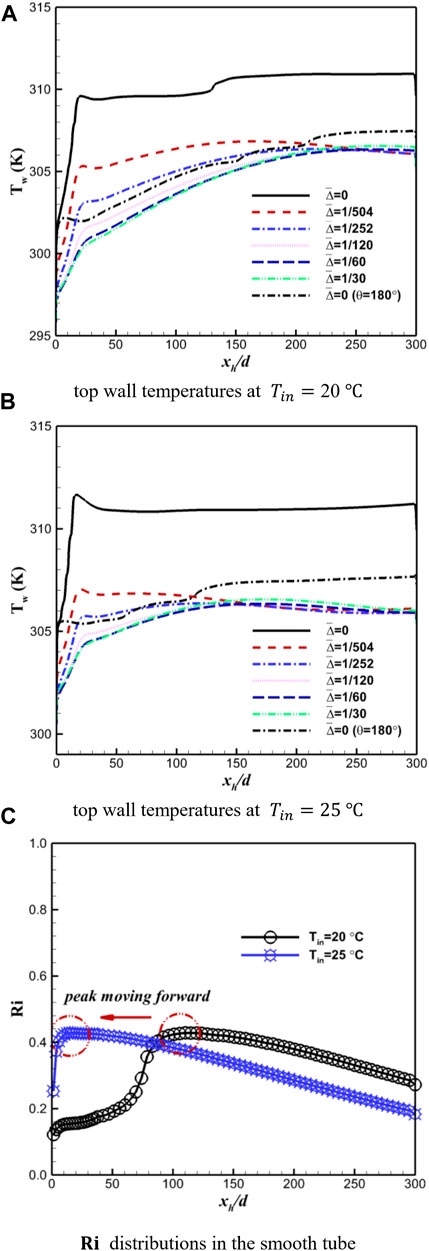
FIGURE 10. Temperature profiles along the top wall (A, B) of horizontal sCO2 heat transfer with various roughness heights and buoyancy strength variations (C) of smooth sCO2 flows under two characteristic inlet temperatures.
3.3 The overall evaluations
The buoyancy effect is critical in influencing the optimum roughness height of the half-roughen scheme to close the temperature gap between the two peak walls of horizontal sCO2 flows. Table 3 computes the average buoyancy parameter
4 Conclusion
Accounting for the particular sCO2 heat transfer features within the horizontal orientations, the circular wall was half-roughened with sand-grain wall roughness to close the significant wall temperature gap over the perimeter. With the help of the validated SST
• Involving extensive operating conditions, horizontal sCO2 heat transfer with sand-grain wall roughness can be well reproduced by the SST
• The wall temperature gap encountered in horizontal sCO2 heat transfer can be effectively narrowed by the employed half-roughen scheme, and the circumferential homogeneity of heat transfer was greatly improved. An optimal roughness height exists, which increases with the rising
• Buoyancy is a crucial factor that determines the influences of wall roughness and its optimal height. The intensified buoyancy recirculates more low-momentum fluids to be accumulated in the top, which demands the larger roughness height to totally break. The local variations in the buoyancy strength lead to consequences as well. As the buoyancy level along the sCO2 mainstream presents a non-monotonic distribution with a peak value emerging in the upstream, the influences of varying roughness heights will be greatly suppressed in the downstream, and the top wall temperatures are likely to be converged around the pseudocritical point.
Data availability statement
The original contributions presented in the study are included in the article/Supplementary material; further inquiries can be directed to the corresponding author.
Author contributions
JY: investigation, methodology, and writing—original draft. XX: visualization and software. GT: validation and software. JW: conceptualization, funding acquisition, methodology, investigation, validation, and writing—review and editing. All authors contributed to the article and approved the submitted version.
Funding
This work was financially supported by the National Natural Foundation of China (Project No. 52006248) and Shenzhen Science and Technology Program (Project No. RCBS20210706092408013).
Conflict of interest
The authors declare that the research was conducted in the absence of any commercial or financial relationships that could be construed as a potential conflict of interest.
Publisher’s note
All claims expressed in this article are solely those of the authors and do not necessarily represent those of their affiliated organizations, or those of the publisher, the editors, and the reviewers. Any product that may be evaluated in this article, or claim that may be made by its manufacturer, is not guaranteed or endorsed by the publisher.
Abbreviations
sCO2, supercritical carbon dioxide; DNS, direct numerical simulation; and CFD, computational fluid dynamics.
References
Chen, J., Yang, S-G., Zhao, R., and Cheng, W-L. (2022). Experimental study on the effect of wall roughness on heat transfer characteristics of supercritical carbon dioxide in vertical tubes. Int. J. Heat Mass Transf. 196, 123258. doi:10.1016/j.ijheatmasstransfer.2022.123258
Chen, J., Zhao, R., Nian, Y-L., and Cheng, W-L. (2023). Numerical study on the effects of cylindrical roughness on heat transfer performance and entropy generation of supercritical carbon dioxide in vertical tubes. Int. J. Heat Mass Transf. 208, 124060. doi:10.1016/j.ijheatmasstransfer.2023.124060
Chu, X., and Laurien, E. (2016). Flow stratification of supercritical Co2 in a heated horizontal pipe. J. Supercrit. Fluids 116, 172–189. doi:10.1016/j.supflu.2016.05.003
Forooghi, P., Stripf, M., and Frohnapfel, B. (2018). A systematic study of turbulent heat transfer over rough walls. Int. J. Heat Mass Transf. 127, 1157–1168. doi:10.1016/j.ijheatmasstransfer.2018.08.013
Han, Z., Guo, J., Liao, H., Zhang, Z., and Huai, X. (2022). Numerical investigation on the thermal-hydraulic performance of supercritical Co2 in a modified airfoil fins heat exchanger. J. Supercrit. Fluids 187, 105643. doi:10.1016/j.supflu.2022.105643
Kumar, N., and Basu, D. N. (2021). Role of buoyancy on the thermalhydraulic behavior of supercritical carbon dioxide flow through horizontal heated minichannel. Int. J. Therm. Sci. 168, 107051. doi:10.1016/j.ijthermalsci.2021.107051
Latini, B., Fiore, M., and Nasuti, F. (2022). Modeling liquid rocket engine coolant flow and heat transfer in high roughness channels. Aerosp. Sci. Technol. 126, 107672. doi:10.1016/j.ast.2022.107672
Liu, Z. B., He, Y. L., Qu, Z. G., and Tao, W. Q. (2015). Experimental study of heat transfer and pressure drop of supercritical Co2 cooled in metal foam tubes. Int. J. Heat Mass Transf. 85, 679–693. doi:10.1016/j.ijheatmasstransfer.2015.02.013
Mao, S., Zhou, T., Wei, D., Liu, W., and Xue, C. (2022). Numerical investigation on flow and thermal performance of supercritical Co2 in a horizontal ribbed tube. J. Supercrit. Fluids 187, 105644. doi:10.1016/j.supflu.2022.105644
Mendez Cruz, C. M., and Rochau, G. E. (2018). Sco2 brayton cycle: Roadmap to Sco2 power cycles Ne commercial applications. Albuquerque, NM United States: Sandia National Lab. SNL-NM.
Menter, F. R. (1994). Two-equation eddy-viscosity turbulence models for engineering applications. AIAA J. 32 (8), 1598–1605. doi:10.2514/3.12149
Stimpson, C. K., Snyder, J. C., Thole, K. A., and Mongillo, D. (2016). Roughness effects on flow and heat transfer for additively manufactured channels. J. Turbomach. 138 (5), 051008. doi:10.1115/1.4032167
Theologou, K., Mertz, R., Laurien, E., and Starflinger, J. (2022). Experimental investigations on heat transfer of Co2 under supercritical pressure in heated horizontal pipes. Energy 254, 124171. doi:10.1016/j.energy.2022.124171
Wang, J., Guan, Z., Gurgenci, H., Veeraragavan, A., Kang, X., and Hooman, K. (2019). A computationally derived heat transfer correlation for in-tube cooling turbulent supercritical Co2. Int. J. Therm. Sci. 138, 190–205. doi:10.1016/j.ijthermalsci.2018.12.045
Wu, P., Ma, Y., Gao, C., Liu, W., Shan, J., Huang, Y., et al. (2020). A review of research and development of supercritical carbon dioxide brayton cycle Technology in nuclear engineering applications. Nucl. Eng. Des. 368, 110767. doi:10.1016/j.nucengdes.2020.110767
Yalcinkaya, R., and Biyikoğlu, A. (2012). On usage of super-critical carbon-dioxide in a geothermal power cycle. J. Fac. Eng. Archit. Gazi Univ. 27 (3).
Yang, J., Yang, Z., and Duan, Y. (2021). Novel design optimization of concentrated solar power plant with S-Co2 brayton cycle based on annual off-design performance. Appl. Therm. Eng. 192, 116924. doi:10.1016/j.applthermaleng.2021.116924
Keywords: supercritical CO2, horizontal, half-roughen, roughness height, buoyancy
Citation: Yang J, Xie X, Tang G and Wang J (2023) Computational investigation on turbulent heat transfer of supercritical CO2 in the half-roughen horizontal pipe. Front. Energy Res. 11:1249849. doi: 10.3389/fenrg.2023.1249849
Received: 29 June 2023; Accepted: 01 August 2023;
Published: 14 August 2023.
Edited by:
Xiaohu Yang, Xi’an Jiaotong University, ChinaReviewed by:
Zhexi Wen, Central South University, ChinaKoichi Ichimiya, University of Yamanashi, Japan
Yuetao Shi, Shandong University, China
Copyright © 2023 Yang, Xie, Tang and Wang. This is an open-access article distributed under the terms of the Creative Commons Attribution License (CC BY). The use, distribution or reproduction in other forums is permitted, provided the original author(s) and the copyright owner(s) are credited and that the original publication in this journal is cited, in accordance with accepted academic practice. No use, distribution or reproduction is permitted which does not comply with these terms.
*Correspondence: Jianyong Wang, d2FuZ2ppYW55NUBtYWlsLnN5c3UuZWR1LmNu