- Sichuan College of Architectural Technology, Chengdu, China
Shale gas fracturing flowback fluid, characterized by its large volume, complex composition, and potential adverse environmental impacts, has gradually become one of the problems affecting the large-scale development of shale gas resources. Failure to effectively address the treatment of fracturing flowback fluid will severely constrain shale gas development. This paper focuses on the treatment technologies for shale gas fracturing flowback fluid, discussing its water quality characteristics and summarizing the research progress in physical technology, chemical technology, biological technology, and combined technology. Development recommendations are also provided. The results show that shale gas fracturing flowback fluid exhibits characteristics such as complex composition, high viscosity, and high emulsification, and difficult to treat. Individual physical technology, chemical technology, or biological technology is effective in removing certain pollutants from the flowback fluid. Moreover, the combined use of these treatment technologies prove more effective in achieving reuse or discharge standards. With the continuous expansion of shale gas development and increasingly stringent environmental protection requirements worldwide, the volume of flowback fluid requiring treatment is continuously rising. By developing energy-efficient and emission-reduction treatment technologies, and actively recycling and utilizing resources and energy, and adopting clean fracturing fluid system, efficient, energy-saving, environmentally friendly, and economically viable treatment for shale gas fracturing flowback fluid can be achieved.
1 Introduction
Shale reservoirs possess distinctive characteristics of an integrated system comprising source, reservoir, and cap rock, coupled with low porosity and low permeability properties (Li, 2022; Li, 2023). The extraction of industrial gas from shale formations necessitates extensive hydraulic fracturing (Zhang and Hascakir, 2021). While hydraulic fracturing technology has led to a significant surge in shale gas production, the treatment of fracturing flowback fluid has emerged as a formidable challenge in scaling the benefits of shale gas development (Shao et al., 2022). Shale gas fracturing flowback fluid is characterized by its substantial volume, complex composition, high pollutant concentrations, and diverse water quality characteristics (Pan and Wang, 2022). Consequently, the exploration of treatment technologies for flowback fluid requires a tailored approach.
Researchers have employed physical, chemical, and biological technologies in the processing of shale gas fracturing flowback fluid. Physical technologies, which include the utilization of settling ponds or adsorbents such as activated carbon, along with filtration devices like sand filters, are effective in removing solid particles, oil contaminants, heavy metals, and partially soluble substances from flowback fluid (Zhang et al., 2019a; Zhang et al., 2022). These approach are characterized by its simplicity of operation and low processing costs.
Chemical technologies represent the most widely adopted and effective methods for treating shale gas flowback fluid (Oetjen et al., 2018). These methods involve the addition of chemicals like coagulants to the flowback fluid, leveraging principles such as coagulation or oxidation degradation to effectively remove suspended particles, chemical oxygen demand (COD), and heavy ions. Chemical technologies significantly enhance flowback fluid water quality and improve its biodegradability. However, they are associated with complexities in equipment structure, substantial material consumption, limited applicability, stringent processing conditions, and higher costs (Xiong et al., 2018).
Biological technologies rely on microbial metabolic processes to degrade contaminants within flowback fluids. Microbes can effectively degrade substances found in fracturing fluid formulations, including polyacrylamide, surfactants, scale inhibitors, and biocides (Hanson et al., 2019; Wu et al., 2022). Additionally, organic compounds present in the reservoir, such as long-chain hydrocarbons and polycyclic aromatic hydrocarbons (PAHs), are amenable to microbial degradation (Sharma and Pandey, 2022). Hence, the biological technologies hold considerable potential for treating shale gas fracturing flowback fluid. Nevertheless, biocides like glutaraldehyde exhibit biotoxicity and can inhibit degradation rates (Akyon et al., 2019). Moreover, friction reducers and thickening agents are often large organic molecules with relatively slow biodegradation rates. Furthermore, organic compounds and salt ions that infiltrate from the formation can pose varying degrees of hindrance to microbial degradation. High salt concentrations can inhibit the growth metabolism and organic compound degradation capabilities of typical microbes (Zhao et al., 2021), while the biodegradation rates of various aromatic and heterocyclic substances are limited (Butkovskyi et al., 2017).
Moreover, due to the complex composition of shale gas fracturing flowback fluid, employing a single treatment technology can only remove some of the pollutants, often falling short of achieving the required water quality standards (Zhang, et al., 2015). It is only through the reasonable combination that the synergistic effects of various treatment methods can be harnessed to systematically separate and eliminate different substances within the fracturing fluid, facilitating resource recovery or waste disposal (Shang, et al., 2019). Therefore, it is imperative to review the current array of treatment technologies for fracturing flowback fluid, and discern their respective advantages and limitations, enabling us to select suitable treatment techniques and apply effective technological combinations tailored to the unique characteristics of different flowback fluids. This will provide essential technical guidance and references for the reuse or discharge treatment of fracturing flowback fluid during the large-scale and cost-effective development of shale gas resources.
2 The water quality characteristics
The composition of shale gas fracturing flowback fluid typically consists of a complex mixture of inorganic and organic compounds used as additives in the fracturing fluid, compounds originating from the shale formation, and organic compounds transformed in the reservoir due to physical, chemical, or biological processes (Liu et al., 2020a). Due to variations in fracturing fluid formulations, processes, reservoir properties, and other factors, the water quality characteristics of shale gas fracturing flowback fluid can exhibit significant differences between different regions and even within the same region over time. Nevertheless, they commonly share characteristics such as high total dissolved solids (TDS), high chemical oxygen demand (COD), elevated total suspended solids (TSS), complex composition, and a wide range of water quality variations (Zeng et al., 2022), as shown in Table 1.
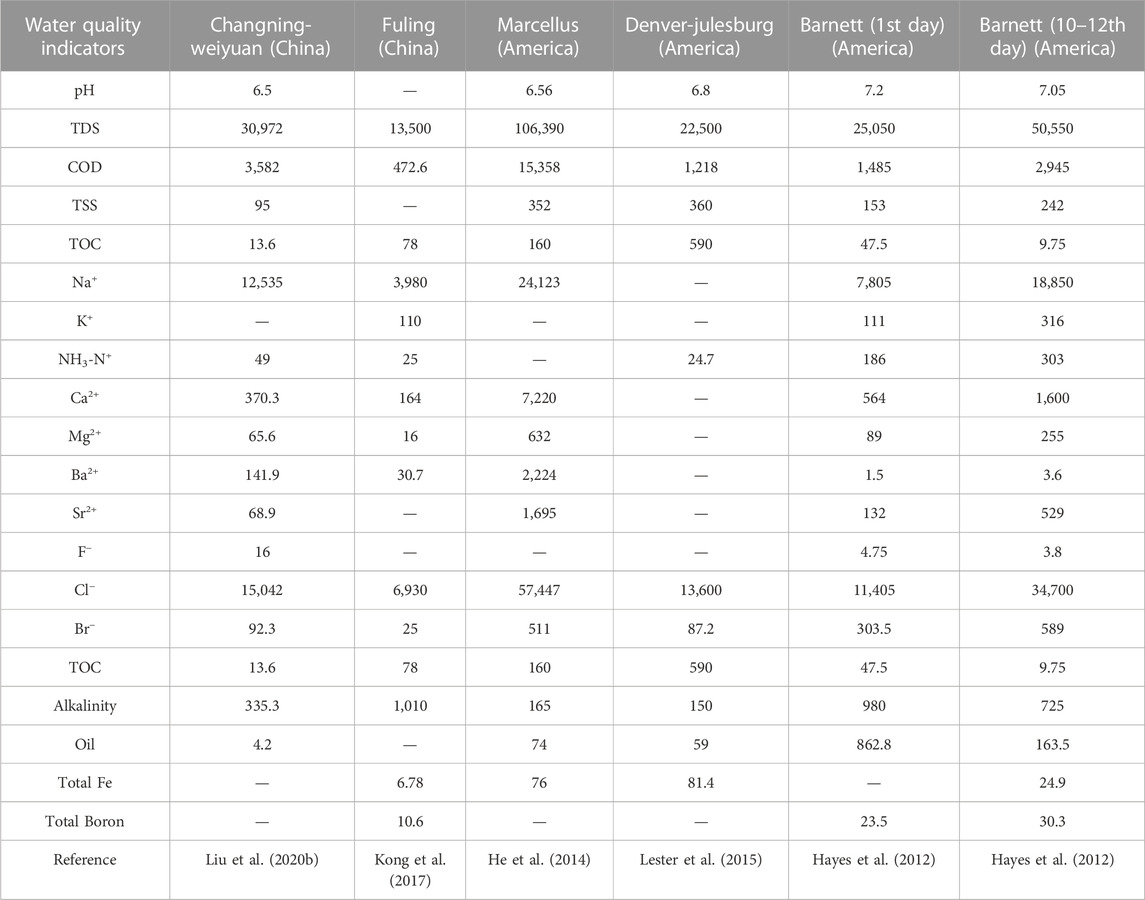
TABLE 1. Comparison of water quality indexes of shale gas fracturing flowback fluid in typical areas at home and abroad (except pH, which is dimensionless, the unit of other indexes is mg/L).
(1) Complex Composition. The composition of fracturing flowback fluid depends on several factors, including the quality of the fracturing fluid makeup water, the chemical composition of the fracturing fluid, the geological and chemical composition of the reservoir, the quality of formation water, and the residence time of the flowback fluid in the subsurface and at the surface (Estrada and Bhamidimarri, 2016). Fracturing flowback fluid exhibit high concentrations of suspended solids and a wide variety of chemical additives, including crosslinkers, demulsifiers, friction reducers, and more (Barbot et al., 2013). These additives result in a stable fluid with appearances ranging from yellow to black.
(2) High Viscosity and Emulsification. Fracturing flowback fluid is characterized by high viscosity and significant emulsification. These fluids are typically complex mixtures that include fracturing fluid, formation fluids, and produced well fluids (Ferrer and Thurman, 2015). As a result, the generated fracturing flowback fluid often appears dark, viscous, and possesses an acrid odor.
(3) High Treatment Difficulty. Fracturing fluid contains numerous chemical additives. When they flow back to the surface from the subsurface, parameters such as chemical oxygen demand, color, and suspended solids concentration are significantly higher than those found in conventional industrial wastewater. Consequently, treating fracturing flowback fluid is a challenging task, with high associated costs, and it is often considered one of the most difficult types of industrial wastewater to handle by researchers both domestically and abroad (Han et al., 2022a).
3 Treatment technology
3.1 Physical technology
Physical treatment technologies primarily encompass filtration, suspension, coagulation, and adsorption. Filtration involves the use of specialized membrane structures to block larger molecular structures on one side of the membrane while separating smaller molecular substances on the other side, thereby achieving the removal of pollutants from the flowback fluid. The most commonly employed filtration technologies include reverse osmosis and forward osmosis (Jamaly et al., 2014). Reverse osmosis technology applies pressure greater than osmotic pressure to one side of the solution, causing water molecules to pass through the membrane to the low-pressure side, resulting in purified water. This method effectively removes salts and is also widely used for the elimination of pollutants such as bacteria and viruses from flowback fluids. However, it can suffer from membrane fouling when the incoming TDS exceeds 40,000 mg/L (Nthunya et al., 2020). On the other hand, forward osmosis uses a high-concentration draw solution to generate higher osmotic pressure, allowing water from the low-concentration side to pass through a semi-permeable membrane and mix with the high-concentration draw solution. Subsequently, the water from the draw solution is separated, yielding pure water (Coyan et al., 2015). This method offers low membrane fouling, excellent treatment efficacy, and does not require external pressure.
Suspension involves the introduction of substances into wastewater to facilitate the suspension of impurities in the flowback fluid, primarily effective in removing insoluble matter but less promising for other pollutants. This method can be operationally complex and time-consuming.
Coagulation rapidly aggregates suspended particle impurities in the liquid and efficiently removes them. This technique is relatively simple to operate and does not require specialized equipment, making it a cost-effective option (Pen et al., 2022). Coagulation is highly effective in removing suspended solids and petroleum-related substances from flowback fluids, but its performance in COD removal may not be as favorable (Rosenblum et al., 2016). Additionally, coagulation generates significant precipitates, posing challenges for precipitate handling.
Adsorption involves the addition of adsorbents to the flowback fluid to allow pollutants to adhere to the adsorbent material for subsequent removal. Major adsorbents include activated carbon and activated alumina (Lu et al., 2017). Adsorption is a straightforward process, but it often requires a significant quantity of adsorbent material, resulting in higher costs. The use of regenerable adsorbents introduces challenges related to adsorbent loss and reduced adsorption capacity during recycling processes.
Furthermore, Mechanical Vapor Recompression (MVR) and membrane distillation technologies have gained widespread use. MVR initially conducts heat exchange between the high-salinity water to be treated, flowback fluid, and a heat exchanger to recover lost heat during evaporation and concentration processes. The compressed high-salinity wastewater is then sent to the evaporator as a heat source for heating steam, ultimately causing the flowback fluid to evaporate. Condensation of the vapor yields liquid water, while pollutants in the flowback fluid are concentrated into a salt solution, facilitating solid-liquid separation. This technology allows for the recovery of residual heat and its reuse in the evaporation of flowback fluid, enabling approximately 72.5% reusability of distilled water (Hayes et al., 2014). While it enhances energy efficiency, MVR systems can be susceptible to clogging and corrosion. Membrane distillation technology offers superior environmental adaptability and can treat flowback fluids with a wider range of TDS values (Zhang et al., 2019b). However, it faces challenges such as scale formation during the treatment process.
3.2 Chemical technology
Chemical treatment technologies mainly encompass chemical coagulation, electro-coagulation, electro-oxidation, and advanced oxidation processes. Chemical coagulation technology primarily serves as a pre-treatment method with the aim of removing solid impurities, suspended solids, colloids, and reducing turbidity and coloration in the flowback fluid. This technology offers advantages such as simplicity in operation and cost-effectiveness. However, it also presents challenges, including the significant use of chemicals, substantial sludge generation, and difficulties in eliminating water-soluble organic compounds (Estrada and Bhamidimarri, 2016).
Electro-coagulation technology predominantly targets the removal of heavy metal ions and suspended solids from flowback fluid, making it a vital treatment component in achieving compliant discharge within the overall treatment process (Sari and Chellam, 2015). This technology boasts excellent coagulation effects, high water purification efficiency, no additional chemical reagents, straightforward equipment, and a broad pH usage range. Nevertheless, it may encounter issues like anode passivation and relatively high energy consumption (Yu et al., 2023).
Electro-oxidation technology is a chemical treatment technology that simultaneously incorporates oxidation-reduction, catalytic oxidation, coagulation adsorption, and electro-deposition effects. This technology features broad applicability, straightforward operation, high treatment efficiency, and low processing costs. When dealing with flowback fluid characterized by high salinity, elevated COD concentrations, and intense coloration, electrooxidation can yield more pronounced results compared to alternative treatment methods (Luo et al., 2023). However, it is prone to the formation of insulating layers during the reaction process, which can impede the continuation of the reaction. Additionally, achieving the desired treatment goals using solely this technology can be challenging.
Advanced oxidation processes generate highly oxidative hydroxyl radicals to tackle recalcitrant organic pollutants. Various advanced oxidation technologies include Fenton oxidation, electro-catalytic oxidation, ozone catalytic oxidation, and photocatalytic oxidation. Fenton oxidation entails the use of iron salts as catalysts to produce OH radicals from H2O2, effectively degrading pollutants in water owing to their potent oxidation capabilities (Wang and Tang, 2021). This technology offers rapid reactions and relatively few treatment limitations. However, the addition of substantial amounts of reagents results in high treatment costs (Tan et al., 2023).
Electro-catalytic oxidation technology entails the direct oxidation of organic pollutants on the electrode surface under an electric current (Ganiyu et al., 2021). It is characterized by simple equipment, mild reaction conditions, but can be associated with relatively high treatment costs and issues related to anode passivation (Zhao et al., 2021).
Ozone catalytic oxidation technology harnesses the formidable oxidation potential of ozone to break down carbon chains of organic pollutants into smaller, easily removable organic compounds (Tang et al., 2021). However, it can only degrade specific organic pollutants, and its application is somewhat limited.
Photocatalytic oxidation technology relies on external light sources, such as sunlight or specific wavelengths of light, to excite semiconductor materials and produce electron-hole pairs. These electron-hole pairs can initiate redox reactions in suitable media, leading to the degradation of pollutants in wastewater (Yang et al., 2022). The advantage of photocatalytic oxidation technology is its relatively energy-saving nature compared to some other methods. It can degrade a wide range of organic compounds. However, the preparation of photocatalysts is intricate, and it demands high-quality electrode materials. Its processing capacity is smaller compared to some other methods.
Furthermore, ultrasound oxidation technology is a combination of physical and chemical methods. It uses ultrasound to stimulate both physical and chemical reactions during treatment of the flowback fluid, thereby degrading pollutants (Tang et al., 2021). This technology can effectively control specific reaction steps and reaction rates, achieving high-quality treatment of the flowback fluid to some extent. Researchers have found that ultrasound oxidation is cost-effective and relatively straightforward compared to other treatment technologies (Lu et al., 2014).
3.3 Biological technology
At present, the primary biological treatment technologies for shale gas hydraulic fracturing flowback fluid include activated sludge technology, biofilm technology, membrane bioreactor technology, and aerobic granular sludge technology. Activated sludge technology is a biological treatment method centered around activated sludge, which consists of a suspended growth flocculent biomass containing microorganisms, organic, and inorganic materials. Utilizing this microbial community can effectively degrade shale gas hydraulic fracturing flowback fluid (Yaal et al., 2014). However, this process is significantly limited during operation due to various variable parameters, such as high salinity, high loads, and fluctuations in water quality. This limitation increases the risk of system failure (Maeng et al., 2018). To maintain the stability of the sludge system, it is necessary to consider the implementation of processes like chemical oxidation and electrodialysis upfront. This can help reduce the fluctuation range of organic matter and salinity in the flowback fluid entering the biological section, thus achieving stable operation of the activated sludge process.
Biofilm technology includes various processes such as bio-filtration, bio-discs, bio-contact oxidation tanks, aeration bio-filters, and bio-fluidized beds. The common characteristic of these processes is the utilization of micro-organisms attached to inert carriers (filter media or packing) to form biofilms for flowback fluid biological treatment (Zhuang et al., 2019). Compared to activated sludge methods, biofilm processes exhibit stronger resistance to salinity and can maintain organic and nitrogen removal efficiency under higher salinity conditions. They also have robust shock resistance and are suitable for the treatment of shale gas hydraulic fracturing flowback fluid with high salinity and significant fluctuations in water quality (Tang et al., 2021). However, this technology is limited by factors like media fill ratios and oxygen transfer, resulting in limited processing capacity. Therefore, it may not be suitable for areas with high water volumes and limited construction space.
Membrane bioreactor (MBR) technology combines biological treatment with membrane separation. This technology employs membrane components such as hollow fiber membranes and flat-sheet membranes for solid-liquid separation instead of traditional secondary sedimentation tanks. MBR technology effectively enhances sludge concentration in bioreactors, leading to higher biological treatment volume loads and reduced wastewater treatment facility footprint (Riley et al., 2016; Matsushita et al., 2018). However, MBR technology comes with a higher initial investment in membrane components. It is also prone to increased membrane fouling and reduced membrane component lifespan when exposed to adverse conditions like high salinity, as microorganisms release more extracellular polymeric substances (EPS).
Aerobic granular sludge technology involves the formation of dense, structured microbial aggregates in aerobic environments. This technology is characterized by high sludge content, high volume loads, robust resistance to adverse conditions, and low equipment and operational costs. It shows significant potential for application in the treatment of shale gas hydraulic fracturing flowback fluid (Han et al., 2022b). However, aerobic granular sludge technology employs sequencing batch reactors (SBRs), and the stability of granular sludge in industrial wastewater treatment needs further observation. The challenge of rapid recovery after granular sludge disintegration also requires attention.
Among them, biofilm technology and membrane bioreactor technology have high industrialization feasibility, while aerobic granular sludge method still needs research and innovation. Additionally, biofortification technology can strengthen the above biochemical system by introducing salt-resistant organic matter degrading bacteria so as to effectively shorten the start-up time and increase the removal rate of pollutants.
3.4 Combined technology
Analyzing the treatment outcomes of various techniques reveals that relying solely on a single treatment method is insufficient to meet the requirements for discharge or recycling of shale gas hydraulic fracturing flowback fluid. Typically, in order to effectively ensure that the flowback fluid meets water quality standards after treatment, a combination of multiple treatment technologies is often employed in the actual treatment process (Loh et al., 2021).
Based on variations in the water quality of hydraulic fracturing flowback fluid in different regions and the specific treatment requirements of enterprises, the combined treatment of flowback fluid can be categorized into three levels (Figure 1). The first level of treatment primarily focuses on removing suspended particles (TSS), residual components from hydraulic fracturing fluids, crude oil, and the like. The second level of treatment aims at removing divalent metal ions such as calcium, magnesium, barium, and strontium. The third level, which involves advanced treatment, primarily aims to reduce salt concentrations in the water, particularly chloride ion concentrations.
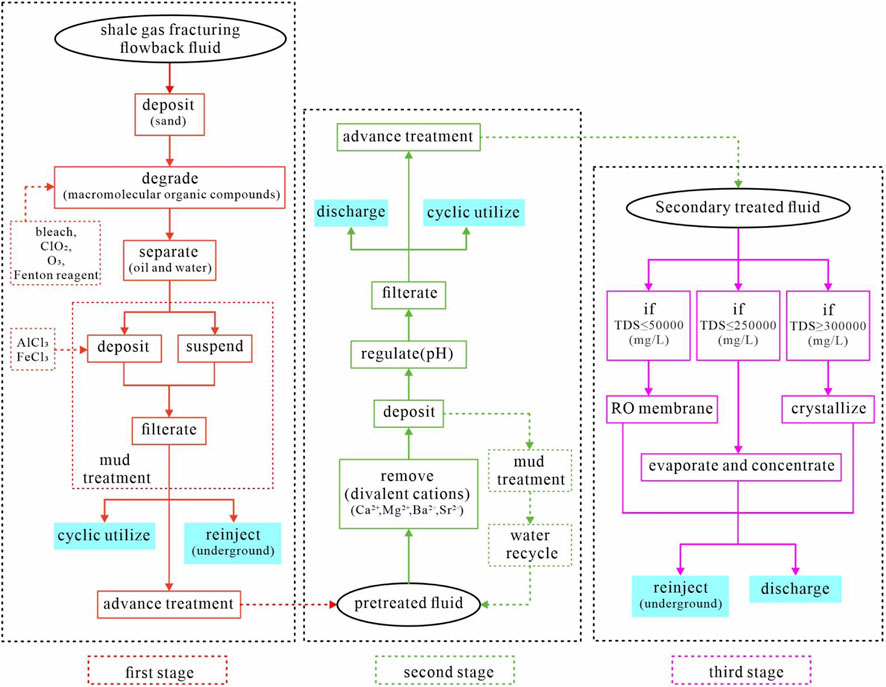
FIGURE 1. Flowchart of three-stage treatment of shale gas fracturing flowback fluid using combination technology.
4 Discussions and recommendations
Shale gas, as a clean, low-carbon, high-quality, and efficient fossil energy source, plays a pivotal role in the transition from high-carbon to low-carbon energy development, complementing renewable energy sources (Wei et al., 2021). Major shale gas-producing countries like China and the United States are continually accelerating their exploration and development efforts, expanding the scale of shale gas exploration and production year by year (Zou et al., 2021). This leads to a continuous increase in the volume of shale gas flowback fluid.
Utilizing traditional physical, chemical, and biological technologies to handle such a large volume of flowback fluid would inevitably consume significant resources and energy, which is not conducive to achieving “dual carbon” goals (Ma et al., 2022). Furthermore, environmental protection requirements during shale gas development have been increasing in various countries. Therefore, finding ways to effectively treat flowback fluid, while also achieving energy savings and emissions reduction through treatment technologies and promoting the resource utilization of flowback fluid, is a critical objective in realizing the efficient development of shale gas on a large scale.
4.1 Developing energy-efficient and emission-reduction treatment technology
The development of energy-efficient and resource-saving technologies for treating shale gas hydraulic fracturing flowback fluid is crucial for reducing carbon emissions (Niu et al., 2023). Flowback fluid treatment technologies, while reducing the total emissions of pollutants, can achieve energy savings and reduced consumption through the following three measures.
4.1.1 New energy sources
Utilizing renewable resources such as wind energy, solar energy, geothermal energy, and hydropower for clean power generation and these power can be applied to the treatment of shale gas hydraulic fracturing flowback fluid. This approach achieves energy savings and emissions reduction in the treatment process.
4.1.2 Smart equipment for energy efficiency
Employing high-efficiency energy-saving equipment, combined with online monitoring of water quality and quantity, allows for precise control of processes such as recirculation and chemical dosing through a sophisticated intelligent control system. This improves operational efficiency and, in turn, achieves energy savings and reduced consumption (Dong et al., 2023).
4.1.3 Optimization of treatment process integration
Emphasizing technological research and promoting the combined use of sound, light, electricity, and magnetic energy are necessary (Coha et al., 2021; Abdulgani et al., 2022). This approach encourages modularization and standardization of shale gas hydraulic fracturing flowback fluid treatment facilities, enhancing treatment efficiency and increasing energy utilization.
4.2 Recycling and utilizing resources and energy
Shale gas hydraulic fracturing flowback fluid contains a significant amount of waste resources and energy that can be recovered and utilized through relevant treatment technologies (Shi et al., 2023). This can help offset carbon emissions, and the treatment approach should transition from “meeting emission standards” to “resource and energy recovery”. In addition to developing technologies for reusing flowback fluid, it is also possible to recover renewable clean energy from them. Researchers have explored new bio-treatment technologies such as microalgae wastewater purification technology and microbial fuel cells technology for treating shale gas hydraulic fracturing flowback fluid (Racharaks et al., 2015; Feng et al., 2020). However, these resource utilization technologies are still challenging to implement on an industrial scale for flowback fluid treatment in the short term. To accelerate the resource and energy utilization of hydraulic fracturing flowback fluid, innovations in existing technologies are needed. On the one hand, it is essential to further select and domesticate functionally resilient microbial strains or improve them through genetic engineering techniques. On the other hand, a deeper understanding of microbial metabolic mechanisms is necessary to enhance their resource utilization efficiency (Zhou et al., 2020). These innovations can contribute to more sustainable and environmentally friendly approaches for handling shale gas hydraulic fracturing flowback fluid while harnessing its potential as a source of resources and energy (Yu et al., 2022).
4.3 Adopting clean fracturing fluid system
Compared to conventional polymer fracturing fluid, clean fracturing fluid systems typically consist of low-pollution or non-polluting chemical additives. They offer advantages such as good degradability, low toxicity, simple treatment processes, and good repeatability in terms of fluid composition, which can significantly reduce the environmental pollution associated with hydraulic fracturing flowback fluids and, to some extent, lower the cost of fracturing operations (Cen et al., 2023). However, existing clean fracturing fluid systems often exhibit poor temperature resistance and high costs, which limit their application in hydraulic fracturing operations (Hu et al., 2023). Therefore, there is a need to focus on the development of low-cost, high-temperature-resistant, and versatile clean fracturing fluid systems to alleviate the environmental pressures associated with hydraulic fracturing flowback fluid treatment (Tan et al., 2023).
5 Conclusion
(1) Shale gas hydraulic fracturing flowback fluid exhibits characteristics such as high salinity, high chemical oxygen demand, elevated suspended solids, complex composition, and a wide range of water quality variations. These characteristics contribute to the significant difficulty in treatment.
(2) Physical, chemical, and biological technologies all demonstrate good performance in treating flowback fluid. Combined technologies is necessary to effectively achieve the desired treatment standards for flowback fluids, considering the specific characteristics of flowback fluid in different regions.
(3) Developing emission reduction technologies, implementing resource and energy recovery and utilize, and using clean fracturing fluid systems can enable the efficient, energy-saving, environmentally friendly, and low-cost treatment of shale gas hydraulic fracturing flowback fluid while effectively reducing emissions.
Author contributions
TZ contributed to the formal analysis, writing, reviewing, editing, and revising of the paper.
Funding
This study was financially supported by the key R & D projects of the Deyang Science and Technology Plan (No. 2021SZ002).
Conflict of interest
The author declares that the research was conducted in the absence of any commercial or financial relationships that could be construed as a potential conflict of interest.
Publisher’s note
All claims expressed in this article are solely those of the authors and do not necessarily represent those of their affiliated organizations, or those of the publisher, the editors and the reviewers. Any product that may be evaluated in this article, or claim that may be made by its manufacturer, is not guaranteed or endorsed by the publisher.
References
Abdulgnin, I., Escalona-Durán, F., Araújo, D. M., Santos, E. V., Segundo, I. D. B., and Martínez-Huitle, C. A. (2022). The role of saline-related species in the electrochemical treatment of produced water using Ti/IrO2-Ta2O5 anode. J. Electroanal. Chen. 910, 116163. doi:10.1016/j.jelechem.2022.116163
Akyon, B., Lipus, D., and Bibby, K. (2019). Glutaraldehyde inhibits biological treatment of organic additives in hydraulic fracturing produced water. Sci. Total. Environ. 666, 1161–1168. doi:10.1016/j.scitotenv.2019.02.056
Barbot, E., Vidic, N. S., Gregory, K. B., and Vidic, R. D. (2013). Spatial and Temporal Correlation of Water Quality Parameters of Produced Waters from Devonian-Age Shale following Hydraulic Fracturing. Environ. Sci. Technol. 47, 2562–2569. doi:10.1021/es304638h
Butkovskyi, A., Bruning, H., Kools, S. A. E., Rijnaarts, H. H. M., and Wezel, A. P. W. (2017). Organic Pollutants in Shale Gas Flowback and Produced Waters: identification, potential ecological impact, and implications for treatment strategies. Environ. Sci. Technol. 51 (9), 4740–4754. doi:10.1021/acs.est.6b05640
Coha, M., Farinalli, G., Tiraferri, A., Minella, M., and Vione, D. (2021). Advanced oxidation processes in the removal of organic substances from produced water: potential, configurations, and research needs. Chen. Eng. J. 414, 128668. doi:10.1016/j.cej.2021.128668
Coyan, B. D., Miller-Robbie, L., Beaudry, E. G., Munakata-Marr, J., and Cath, T. Y. (2015). Life cycle and economic assessments of engineered osmosis and osmotic dilution for desalination of Haynesville shale pit water. Desalinaton 369, 188–200. doi:10.1016/j.desal.2015.04.028
Dong, Y., Rong, J., Li, X., and Tang, S. (2023). Thinking on shale gas fracturing flowback fluid treatment technology under carbon neutral vision. https://kns.cnki.net/kcms2/detail/51.1292.TE.20230526.1141.008.html.
Estrada, J. M., and Bhamidimarri, R. (2016). A review of the issues and treatment options for wastewater from shale gas extraction by hydraulic fracturing. Fuel 182, 292–303. doi:10.1016/j.fuel.2016.05.051
Feng, Q., Xu, L., Liu, C., Qin, Y., Jiang, Z., Xie, Z., et al. (2020). Treatment of shale gas fracturing wastewater using microbial fuel cells: mixture of aging landfill leachate and traditional aerobic sludge as catholyte. J. Clean. Prod. 269, 121776. doi:10.1016/j.jclepro.2020.121776
Ferrer, I., and Thurman, E. M. (2015). Chemical constituents and analytical approaches for hydraulic fracturing waters. Trends. Environ. Anal. 5, 18–25. doi:10.1016/j.teac.2015.01.003
Ganiyu, S. O., Martínez-Huitle, C. A., and Oturan, M. A. (2021). Electrochemical advanced oxidation processes for wastewater treatment: advances in formation and detection of reactive species and mechanisms. Curr. Opin. Electrochem. 27, 100678. doi:10.1016/j.coelec.2020.100678
Han, M., Huang, C., Liu, S., Jin, B., and Zhang, G. (2022a). Compositional characteristics of chemical pollutants in flowback water during shale gas hydraulic fracking. Environ. Chem. 41 (1), 305–314. doi:10.7524/j.issn.0254-6108.2021050302
Han, X., Jin, Y., and Yu, J. (2022b). Rapid formation of aerobic granular sludge by bioaugmentation technology:A review. Chen. Eng. J. 437 (1), 134971. doi:10.1016/j.cej.2022.134971
Hanson, A. J., Luek, J. L., Tummings, S. S., McLaughlin, M. C., Blotevogel, J., and Mouser, P. (2019). High total dissolved solids in shale gas wastewater inhibit biodegradation of alkyl and nonylphenol ethoxylate surfactants. Sci. Total. Environ. 668, 1094–1103. doi:10.1016/j.scitotenv.2019.03.041
Hayes, T. D., Halldorson, B., Horner, P. H., Ewing, J. J. R., Werline, J. R., and Severin, B. F. (2014). Mechanical Vapor Recompression for the Treatment of Shale-Gas Flowback Water. Oil. Gas. Facki 3 (4), 54–62. doi:10.2118/170247-PA
Hayes, T., Severin, B. F., Engineer, P. S. P., and Okemos, M. (2012). Barnett and Appalachian Shale water management and reuse technologies. Report No: 08122-05. Houston, TX, USA: Research Partnership to Secure Energy for America.
He, C., Wang, X., Liu, W., Barbot, E., and Vidic, R. D. (2014). Microfiltration in recycling of Marcellus Shale flowback water: solids removal and potential fouling of polymeric microfiltration membranes. J. Membrane.Sci. 462, 88–95. doi:10.1016/j.memsci.2014.03.035
Hu, D., Wang, R., Liu, B., Bai, B., and Zhu, L. (2023). A rigid double-tailed surfactant preparation method and its application in clean fracturing fluid. J. Surfactants, Deterg. 1, 703–709. doi:10.1002/jsde.12659
Jamaly, S., Darwish, N. N., Ahmed, I., and Hasan, S. W. (2014). A short review on reverse osmosis pretreatment technologies. Desalination 354, 30–38. doi:10.1016/j.desal.2014.09.017
Kong, F., Chen, J., Wang, H., Liu, X., Wang, X., W, X., et al. (2016). Application of coagulation-UF hybrid process for shale gas fracturing flowback water recycling: performance and fouling analysis. J. Membrane.Sci. 524, 460–469. doi:10.1016/j.memsci.2016.11.039
Lester, Y., Ferrer, I., Thurman, E. M., Sitterley, A., Korak, J., Aiken, G., et al. (2015). Characterization of hydraulic fracturing flowback water in Colorado: implications for water treatment. Sci. Total. Environ. 512-513, 637–644. doi:10.1016/j.scitotenv.2015.01.043
Li, H. (2023). Coordinated development of shale gas benefit exploitation and ecological environmental conservation in China: A mini review. Front. Ecol. Evol. 11, 1232395. doi:10.3389/fevo.2023.1232395
Li, H. (2022). Research progress on evaluation methods and factors influencing shale brittleness: A review. Energy Rep. 8, 4344–4358. doi:10.1016/j.egyr.2022.03.120
Liu, D., Li, J., Zou, C., Cui, H., Ni, Y., Liu, J., et al. (2020a). Recycling flowback water for hydraulic fracturing in Sichuan Basin, China: implications for gas production, water footprint, and water quality of regenerated flowback water. Fuel 272, 117621. doi:10.1016/j.fuel.2020.117621
Liu, W., Sun, L., and Tao, S. (2020b). Removal of Ca2+, Mg2+, Ba2+ and Sr2+ from shale gas flowback water from the Sichuan Basin in China by chemical softening under the guidance of OLI Stream Analyzer: precipitation behaviors and optimization study. Water. Sci. Technol. 82 (1), 194–206. doi:10.2166/wst.2020.355
Loh, W. H., Cai, Q. Q., Li, R., Jothinathan, L., Lee, B. C. Y., Ng, O. H., et al. (2021). Reverse osmosis concentrate treatment by microbubble ozonation-biological activated carbon process: organics removal performance and environmental impact assessment. Sci. Total. Environ. 798, 149289. doi:10.1016/j.scitotenv.2021.149289
Lu, H., Zhao, D., Zhang, T., and Dai, S. (2014). The study of ultrasonic technology in flow-back fracturing fluid treatment. Pet. Sci. Technol. 32, 1233–1240. doi:10.1080/10916466.2011.649098
Lu, L., Jiang, W., and Xu, P. (2017). Comparative study on pharmaceuticals adsorption in reclaimed water desalination concentrate using biochar: impact of salts and organic matter. Sci. Total. Environ. 601-602, 857–864. doi:10.1016/j.scitotenv.2017.05.203
Luo, M., Yang, H., Wang, K., Song, F., He, Y., Zhang, Y., et al. (2023). Coupling iron-carbon micro-electrolysis with persulfate advanced oxidation for hydraulic fracturing return fluid treatment. Chemosphere 313, 137415. doi:10.1016/J.CHEMOSPHERE.2022.137415
Ma, Y., Cai, X., Luo, D., Zhao, P., Jiang, S., Xi, F., et al. (2022). Thoughts on Development of China’s Oil and Gas Industry under “Dual Carbon” Goals. Earth. Sci. 47 (10), 3501–3510. doi:10.3799/dqkx.2022.872
Maeng, S. K., Khan, W., Park, J. W., Han, I., Yang, H. S., Song, K. G., et al. (2018). Treatment of highly saline RO concentrate using Scenedesmus quadricauda for enhanced removal of refractory organic matter. Desalination 430, 128–135. doi:10.1016/j.desal.2017.12.056
Matsushita, S., Komizo, D., Cao, L. T. T., Aoi, Y., Kindaichi, T., Ozaki, N., et al. (2018). Production of biogenic manganese oxides coupled with methane oxidation in a bioreactor for removing metals from wastewater. Water. Res. 130, 224–233. doi:10.1016/j.watres.2017.11.063
Niu, W., Lu, J., Sun, Y., Liu, H., Cao, H., Zhan, H., et al. (2023). A review of the application of data-driven technology in shale gas production evaluation. Energy. Rep. 10, 213–227. doi:10.1016/j.egyr.2023.06.026
Nthunya, L. N., Gutierrez, L., Nxumalo, E. N., Verliefde, A. R., Mhlanga, S. D., and Onyango, M. S. (2020). F-MWCNTs/AgNPs-coated superhydrophobic PVDF nanofibre membrane for organic, colloidal, and biofouling mitigation in direct contact membrane distillation. J. Environ. Chem. Eng. 8, 103654. doi:10.1016/j.jece.2020.103654
Oetjen, K., Chan, K. E., Gulmark, K., Christensen, J. H., Blotevogel, B., Borch, T., et al. (2018). Temporal characterization and statistical analysis of flowback and produced waters and their potential for reuse. Sci. Total. Environ. 619, 654–664. doi:10.1016/j.scitotenv.2017.11.078
Pan, Y., and Wang, J. Y. (2022). Analysis of compositions of flowback water from Marcellus shale wells by utilizing data mining techniques. J. Energy Resour-ASME. 144 (1), 013004. doi:10.1115/1.4052410
Pen, J., Tian, Y., Ma, J., and He, R. (2022). Optimization of produced water containing fracturing flowback fluid treatment process. Ind. Water Treat. 42 (5), 157–162. doi:10.19965/j.cnki.iwt.2021-0860
Racharaks, R., Ge, X., and Li, Y. (2015). Cultivation of marine microalgae using shale gas flowback water and anaerobic digestion effluent as the cultivation medium. Bioresour. Technol. 191, 146–156. doi:10.1016/j.biortech.2015.04.065
Riley, S. M., Oliveira, J. M. S., Regnery, J., and Cath, T. Y. (2016). Hybrid membrane bio-systems for sustainable treatment of oil and gas produced water and fracturing flowback water. Sep. Purif. Technol. 171, 297–311. doi:10.1016/j.seppur.2016.07.008
Rosenblum, J. S., Sitterley, K. A., Thurman, E. M., Ferrer, I., and Linden, K. G. (2016). Hydraulic fracturing wastewater treatment by coagulation-adsorption for removal of organic compounds and turbidity. J. Environ. Chem. Eng. 4 (2), 1978–1984. doi:10.1016/j.jece.2016.03.013
Sari, M. A., and Chellam, S. (2015). Mechanisms of boron removal from hydraulic fracturing wastewater by aluminum electrocoagulation. J. Colloid. Sci. 458 (21), 103–111. doi:10.1016/j.jcis.2015.07.035
Shang, W., Tiraferri, A., He, Q., Li, N., Chang, H., Liu, C., et al. (2019). Reuse of shale gas flowback and produced water: effects of coagulation and adsorption on ultrafiltration, reverse osmosis combined process. Sci. Total. Environ. 689, 47–56. doi:10.1016/j.scitotenv.2019.06.365
Shao, J., You, L., Kang, Y., Chen, M., and Tian, J. (2022). Salinity of flowback fracturing fluid in shale reservoir and its reservoir damage: experimental and field study. J. Pet. Sci. Eng. 211, 110217. doi:10.1016/j.petrol.2022.110217
Sharma, S., and Pandey, L. M. (2022). Biodegradation kinetics of binary mixture of hexadecane and phenanthrene by the bacterial microconsortium. Bioresour. Technol. 358, 127408. doi:10.1016/j.biortech.2022.127408
Shi, H., He, X., Zhou, C., Wang, L., and Xiao, Y. (2023). Hydrochemistry, Sources and Management of Fracturing Flowback Fluid in Tight Sandstone Gasfield in Sulige Gasfield (China). Arch. Environ. Con. Tox. 84, 284–298. doi:10.1007/s00244-023-00983-6
Tan, B., He, Z., Fang, Y., and Zhu, L. (2023). Removal of organic pollutants in shale gas fracturing flowback and produced water: A review. Sci. Total. Environ. 883, 163478. doi:10.1016/j.scitotenv.2023.163478
Tang, P., Xie, W., Tiraferri, A., Zhang, Y., Zhu, J., Li, J., et al. (2021). Organics removal from shale gas wastewater by pre-oxidation combined with biologically active filtration. Water. Res. 196, 117041. doi:10.1016/j.watres.2021.117041
Wang, J., and Tang, J. (2021). Fe-based Fenton-like catalysts for water treatment: catalytic mechanisms and applications. J. Mol. Liq. 332, 115755. doi:10.1016/j.molliq.2021.115755
Wei, J., Duan, H., and Yan, Q. (2021). Shale gas: will it become a new type of clean energy in china? —a perspective of development potential. J. Clean. Prod. 294, 126257. doi:10.1016/j.jclepro.2021.126257
Wu, Q. Y., Miao, Y. P., Chen, Q. J., Hou, E. K., and Li, J. Y. (2022). Monitoring on ecological environment in desertification mining areas based on Sentinel-2. J. Min. Strata Control Eng. 4 (1), 017017. doi:10.13532/j.jmsce.cn10-1638/td.20210617.001
Xiong, B., Miller, Z., RomanWhite, S., Tasker, T., Farina, B., Piechowicz, B., et al. (2018). Chemical degradation of polyacrylamide during hydraulic fracturing. Environ. Sci. Technol. 52 (1), 327–336. doi:10.1021/acs.est.7b00792
Yaal, Y., Tesfayohanes, Y., Morrissey, L., and Linden, K. G. (2013). Can we treat hydraulic fracturing flowback with a conventional biological process? The cas of Guar Gum. Environ. Sci. Technol. 1, 133–136. doi:10.1021/ez4000115
Yang, H., Tang, X., Li, R., Liu, X., Zhang, P., and Gong, Y. (2022). Tunable microscopic aggregation morphology of α-Ni(OH)2 for enhanced photocatalytic degradation of fracturing flowback fluid with ozone synergy. Front. Mat. 9, 995276. doi:10.3389/FMATS.2022.995276
Yu, J., Han, X., Jin, Y., Liu, H., Wang, F., Ji, C., et al. (2022). Biological treatment of shale gas flowback and produced water: a review. Chem. Eng. Oil. Gas. 51 (5), 131–139. doi:10.1016/j.theriogenology.2022.01.020
Yu, S., Chang, C., and Chen, X. (2023). Differential treatment and reuse technology of fracturing flow-back fluid in Sulige gas field. Ind. Water Treat., doi:10.19965/j.cnki.iwt.2022-1111
Zeng, F., Zhou, H., Lin, X., Li, Y., Liang, Y., Xie, Q., et al. (2022). Enhanced remediation of fracturing flowback fluids by the combined application of a bioflocculant/biosurfactant-producing Bacillus sp. SS15 and its metabolites. Chemosphere 302, 134870. doi:10.1016/j.chemosphere.2022.134870
Zhang, J. X., Ju, Y., Zhang, Q., Ju, F., Xiao, X., Zhang, W. Q., et al. (2019a). Low ecological environment damage technology and method in coal mines. J. Min. Strata Control Eng. 1 (1), 013515. doi:10.13532/j.jmsce.cn10-1638/td.2019.02.005
Zhang, L., and Hascakir, B. (2021). A review of issues, characteristics, and management for wastewater due to hydraulic fracturing in the U.S. J. Pet. Sci. Eng. 202 (7), 108536. doi:10.1016/j.petrol.2021.108536
Zhang, N., You, L., Kang, Y., Xu, J., Li, K., Cheng, Q., et al. (2022). The investigation into oxidative method to realize zero flowback rate of hydraulic fracturing fluid in shale gas reservoir. J. Pet. Sci. Eng. 209, 109918. doi:10.1016/j.petrol.2021.109918
Zhang, Y., Li, S., Wang, X., Ma, X., Wang, W., and Li, X. (2015). Synthesis, purification and characterization of polyaluminum ferric chloride (PAFC) with high (Al+Fe)b content. Sep. Purif. Technol. 146, 311–316. doi:10.1016/j.seppur.2015.03.045
Zhang, Z., Du, X. H., Carlson, K., Robbing, C., and Tong, T. (2019b). Effective treatment of shale oil and gas produced water by membrane distillation coupled with precipitative softening and walnut shell filtration. Desalination 454, 82–90. doi:10.1016/j.desal.2018.12.011
Zhao, R., Liu, D., Hong, M., Yang, X., Wu, P., and Yin, C. (2021). Design of comprehensive experiment for treating fracturing flowback fluid by electrocatalytic oxidation. Exp. Technol. Manag. 38 (7), 186–190. doi:10.16791/j.cnki.sjg.2021.07.035
Zhou, H., Huang, X., Liang, Y., Li, Y., Xie, Q., Zhang, C., et al. (2020). Enhanced bioremediation of hydraulic fracturing flowback and produced water using an indigenous biosurfactant-producing bacteria Acinetobacter sp. Y2. Y2. Chem. Eng. J. 397, 125348. doi:10.1016/j.cej.2020.125348
Zhuang, Y., Zhang, Z., Zhou, Z., Chen, M., Li, J., and Chen, S. (2019). Co-treatment of shale-gas produced water and municipal wastewater: removal of nitrogen in a moving-bed biofilm reactor. Process. Saf. Environ. 126, 269–277. doi:10.1016/j.psep.2019.04.010
Keywords: fracturing flowback fluid, water quality characteristics, shale gas, treatment technology, environmental pollution, energy-saving
Citation: Zhao T (2023) Treatment technology of shale gas fracturing flowback fluid: a mini review. Front. Energy Res. 11:1245552. doi: 10.3389/fenrg.2023.1245552
Received: 28 June 2023; Accepted: 29 September 2023;
Published: 10 October 2023.
Edited by:
Chengyuan Xu, Southwest Petroleum University, ChinaReviewed by:
Qiuyang Cheng, PetroChina Southwest Oil and Gas Field Company, ChinaCopyright © 2023 Zhao. This is an open-access article distributed under the terms of the Creative Commons Attribution License (CC BY). The use, distribution or reproduction in other forums is permitted, provided the original author(s) and the copyright owner(s) are credited and that the original publication in this journal is cited, in accordance with accepted academic practice. No use, distribution or reproduction is permitted which does not comply with these terms.
*Correspondence: Tianbiao Zhao, enRieWhnZEAxNjMuY29t