- 1Engineering Technology Research Institute of PetroChina Southwest Oil & Gas Field Company, Chengdu, China
- 2National Energy R&D Center of High Sulfur Gas Exploitation, Guanghan, China
Compared to conventional fracturing techniques, foam fracturing has numerous advantages, including good shear resistance, strong sand carrying capacity, low fluid loss, low damage, and fast return rates. It is particularly suitable for stimulation in low pressure, low permeability, and water-sensitive formations. Specifically, CO2 foam fracturing is crucial in energy savings and emission reductions, controlling the expansion of reservoir clay minerals, reducing crude oil viscosity, and improving the production of water-locked reservoirs. In this paper, we investigate the foam fracturing fluid and evaluate its performance. We selected thickeners with good foaming stability and foaming agents with excellent performance at low dosage levels, based on experimental evaluation. We finally determined the formulation of the foam fracturing fluid by analyzing the experimental data, such as foam half-life, foam mass, and viscosity. We experimentally evaluated the viscosity, static sand settling properties, and rheological properties of the fluid. After being tested on the reservoir core, the foam fracturing fluid has a viscosity of 2 mPas. Moreover, the residue content is 1.1 mg/L, the surface tension is 24.5 mN/m, and the interfacial tension is 1.5 mN/m. The fluid-carrying sand experiment of 40–70 mesh ceramic particles, commonly used in shale gas fracking, was evaluated. The sand-to-liquid ratio was set at 40% for the static sand-carrying experiment. The flow of the fluid-carrying sand was good, and the settling property was satisfactory for 3 h. We used shale reservoir cores from well W-1 to assess the rate of foam fracture, which was less than 19%. Under the experimental conditions of a shear rate of 170 S−1 and a temperature of 90°C, the viscosity of fracturing fluid was measured to be greater than 50 mPas, 90 min after shear, demonstrating the excellent temperature and shear resistance of the foam fracturing fluid. Using CO2 foam fracturing fluid can significantly improve the reconstruction effect of low permeability hydrocarbon reservoirs (especially unconventional reservoirs) and solve problems related to water resources and environmental protection during the process of oil and gas reservoir development. It will be a major factor in improving construction impacts and addressing water and environmental concerns for low permeability hydrocarbon reservoirs, particularly unconventional ones that utilize CO2 foam fracturing fluids.
1 Introduction
In recent years, with the rapid development of shale gas, the exploration and development of shale reservoirs have attracted more and more attention. The fracturing technology of shale reservoirs has become an important research area in the petroleum industry. China is rich in shale gas resources. The country’s shale gas geological reserves are estimated at 134.42 trillion cubic meters, with a recoverable resource potential of 25.08 trillion cubic meters. This is roughly equivalent to the United States’ technically recoverable reserves of 28 trillion cubic meters. Based on the US development experience, the key and core technology for efficient exploration and development of shale gas is horizontal well volume fracturing with slick water (Harris and Reidenbach, 1987; LIU et al., 2004; WANG et al., 2004; Yang et al., 2006; Tan et al., 2020; Tan et al., 2021; Huang et al., 2023). However, this development technique requires large amounts of water and can cause significant damage to the environment. According to the statistics of the US Environmental Protection Agency (EPA), a single shale gas well can consume approximately 0.76–2.39 ten thousand tons of water. While the United States is relatively water-rich and can roughly meet their development needs, China’s relative lack of water resources makes it challenging to meet the huge demand for clean water (Reidenbach, 1986; Cawiezel, 1987; Harris and Heath, 1996; Zheng et al., 2020). In addition, the clay mineral content is relatively high in shale gas reservoirs in China, with terrestrial shale gas reservoirs having a clay mineral content of more than 60%. When conventional water-based fracturing fluids are used in these reservoirs, the clay minerals expand in contact with the water and cause significant permeability damage in shale reservoirs. Shale gas reservoirs in China are generally low in pressure and this may cause conventional water-based fracturing fluids to consume large amounts of water, thus causing significant damage to reservoirs, as well as having a low rate of return. Therefore, rather than simply copying other technologies, it is urgent to develop advanced fracturing technologies that use less water (or no water), are environmentally friendly, and cause relatively little damage to the reservoir (TUDOR et al., 1994; MAZZA and QUID, 2383; Luo XiangRong et al., 2014).
Foam fracturing fluids are a major achievement in liquid technology. They are liquid formations that disperse nitrogen or carbon dioxide as bubbles in water, acid, methanol/water mixtures, or hydrocarbon liquids. These fluids usually consist of 70%–80% gas (nitrogen or carbon dioxide) and water-based polymer. They can be considered as emulsions of gas-coated liquid, providing high viscosity and excellent proppant carrying capacity. Due to their low damage to oil and gas reservoirs, strong flowback capacity, small filtration loss, high fluid utilization efficiency, appropriate viscosity, and strong sand carrying capacity, foam fracturing fluids hold a significant position in frac fluid systems. As the world focuses more on carbon emissions and the demand for natural gas increases, the utilization of CO2 will receive increased attention.
The properties of CO2 foam fracturing fluid also have an impact on hydraulic fracture propagation. Several authors have reported the high performance of CO2 foam due to its unique and favorable rheological characteristics (Barati and Liang, 2014; Sun et al., 2014; Li et al., 2015; Wanniarachchi et al., 2017; Ahmed et al., 2019; Ahmed S. et al., 2021). However, the flow behavior of foam, especially under operating conditions, is difficult to understand and model due to its complex nature. The versatility and uniqueness of foam can be attributed to its significantly higher viscosity compared to its base fluids, and the efficiency of foam fracturing is determined by its complex non-Newtonian behavior (Arezoo et al., 1858; Ahmed et al., 2017a; Jing et al., 2017; Verma et al., 2018; Wang et al., 2018; Ahmed Abdelaal et al., 2021). Numerous authors agree that foam rheology highly influences the design and overall performance of fracturing treatments (Luo X. et al., 2014; Edrisi and Kam, 2014; Gu and Mohanty, 2015; Ahmed et al., 2017b; Fei et al., 2017; Li et al., 2017; Verma et al., 2017; Kartini et al., 2021; Cong et al., 2022; Li et al., 2022; Wang et al., 2022; Gao et al., 2023). Currently, foam fracturing technology has reached a relatively mature stage in terms of indoor research, design, construction, and effectiveness assessment. From the development of foam fracturing fluid technology, it can be summarized into three processes. The first generation of foam fracturing fluids primarily consisted of water, brine, acid, alcohol, and crude oil as base fluids, and were prepared by mixing nitrogen and foaming agents with the base fluids. These fluids feature low filtration loss, strong sand carrying capacity, and fast flowback, but have low viscosity and short foam lifetime, making them only suitable for shallow wells and small-scale fracturing construction (Liu et al., 2020). The second generation of foam fracturing fluid is formed by adding linear glue, a foam stabilizer, to the first generation. In addition to the advantages of the first-generation fluids, the second-generation fluids have a longer foam lifetime, relatively higher viscosity, better sand carrying capacity, etc., making them suitable for frac construction in various wells (Feng et al., 2021). The third-generation foam fracturing fluid uses a delayed cross-linking gel as a foam stabilizer. It has a longer foam lifetime, higher viscosity, and stronger sand carrying capacity compared to the second-generation foam fracturing fluids.
The CO2 foam fracturing fluid not only increases the viscosity of the fracturing fluid but also effectively controls the filtration of the fluid. In water-sensitive reservoirs, such as shale reservoirs, stable foam quality, low damage, good sand carrying capacity and reliability should also be considered to reduce water consumption.
The purpose of this research is to optimize the carbon dioxide foam fracturing fluid and to improve its applicability to shale reservoirs, so as to improve the fracturing effect and reduce the damage to the reservoir. This paper analyses the characteristics and advantages of carbon dioxide foam fracturing fluid and its applicability to shale reservoirs, and summarizes the research progress in this field. Therefore, we conducted experiments to optimize the thickening agent and foaming agent, to achieve good foaming stability, foaming power, and foaming stability at low dosage levels. We also developed a formulation for foaming fracturing fluid and evaluated its performance in reservoir damage and recovery feasibility. In conclusion, the research and optimization of carbon dioxide foam fracturing fluid suitable for shale reservoir has great theoretical and practical significance for the development of shale gas. By improving the fracturing effect and reducing the damage to the reservoir, it can contribute to the sustainable development of the petroleum industry and the protection of the environment.
2 Study on formula of foam fracturing fluid
Carbon dioxide foam fracturing fluid has the advantages of high viscosity and good carrying capacity, which can effectively reduce the damage of shale reservoirs during fracturing operations, and improve the production performance of shale gas wells. The selection of surfactants, crosslinking agents, and other components in the fluid formulation is an important factor affecting its performance in the field. The thickeners and foaming agents for foam fracturing fluids were experimentally evaluated. A thickener with good foaming properties and a foaming agent with good foaming strength and stability were selected in small amounts. The foam fracturing fluid formulation was developed and the performance of the developed formulation was assessed.
2.1 Experimental methods
The Waring Blender method was used to evaluate the foaming ability and foaming stability of the foaming agent, taking into consideration the characteristics of the foaming fracturing fluid (Dong et al., 2021; Zhu and Zheng, 2021; Ju et al., 2022). The properties of the foaming agent were determined using a high-speed agitator.
To evaluate the foaming ability and foaming stability of the foaming agent, 100 mL of the foaming agent solution (foaming agent + thickening agent + water) was poured into the mud cup and stirred at a specified high speed (>10000 r/min) for 60 s. The foam volume V0 (in mL) when stirring is stopped represents the foaming capacity, while the time (in minutes) when half of the liquid (50 mL) separates the foam represents the foam stability, also known as foam half-life.
2.2 Optimization of thickener
In order to select a thickener that can form a sand washing liquid with good foam stability at a lower dosage, the foam stability performance of the collected thickeners, such as hydroxypropyl guar gum (CT1, CT1WⅠ), Instant solution carboxymethyl cellulose (CMC), carboxymethyl cellulose (CMC) and polyanionic cellulose (PAC), was evaluated and optimized. The evaluation process involved assessing the foam stability of each thickener, which can be seen in Table 1.
Firstly, the foam stability performance of hydroxypropyl guar gum (CT1, CT1WⅠ) was evaluated. Next, the foam stability of Instant solution carboxymethyl cellulose (CMC) was examined. Then, the foam stability of carboxymethyl cellulose (CMC) was tested. Finally, the foam stability of polyanionic cellulose (PAC) was assessed. The purpose of this evaluation was to identify a thickener with excellent foam stability properties when used at a lower dosage.
In conclusion, the chosen thickeners were subjected to a comprehensive evaluation and optimization process to determine their foam stability. Table 1 provides a summary of the results.
CT1 thickener was selected as the thickener for foam fracturing fluid due to its superior foam stabilization performance compared to other available options, as indicated in Table 1. The data presented in the table illustrate that CT1 outperforms other thickeners in terms of foam stability, providing a reliable solution for foam fracturing fluid.
2.3 Optimization of foaming agent
The foaming capacity and half-life of various foaming agents, namely, CT1B, CT1S, sodium dodecyl benzene sulfonate (ABS), alkyl betaine (DSB), and CT1C, were evaluated in the thickener solution of CT1WⅡ. Table 1 presents the results, where the foam quality is calculated using the formula (V0-100)/V0. After a comprehensive analysis of the foaming power and stability data provided in Table 2, CT1S was chosen as the ideal foaming agent due to its excellent foaming power and stability. Consequently, CT1S was selected for use in foaming fracturing fluids.
2.4 Determination of dosage of thickening agent
2.4.1 Suspensibility of liquid with different thickening agent dosage
The settling rate of sand in the washing fluid with different dosage of thickening agent (0.2%, 0.3%, 0.4%, and 0.5%) was evaluated at temperatures ranging from 30°C to 90°C, and the results are presented in Table 3. As shown in Table 3, the settling velocity of sand in the liquid increases with increasing experimental temperature. When the dosage of thickening agent is 0.2% and the temperature is 90°C, the sustainability of the liquid is poor. When the dosage of thickening agent is increased to 0.3% or 0.4% and the temperature is 90°C, the sand settles at a rate of 1–10 mm/s. When the dose of the thickening agent was increased to 0.5%, the sand hardly sank.
After foam formation, the apparent viscosity of the liquid increases, which substantially enhances its ability to suspend and carry solid particles. The laboratory evaluation of foam sustainability shows that the sand particles are almost stationary when the dosage of thickening agent is 0.5% at a temperature of 90°C.
2.4.2 Foam stability under different thickening agent dosage
The stability, or half-life, of CT1S foam with foaming agents at 0.3% and thickening agents at 0.2%, 0.3%, 0.4%, and 0.5% were evaluated at temperatures ranging from 15°C to 90°C. As Table 4 shows, the foam half-life decreased as temperature increased. At 90°C, when the thickening agent dosage was 0.2%, the foam half-life was only 0.2 h. But when the dosage was at 0.3%–0.4%, the foam half-life increased to 1.3–2.3 h. Finally, when the dosage reached 0.5% and the temperature remained at 90°C, the foam stability reached a high of 4.1 h. Through a comprehensive analysis of the experimental data on viscosity, foam stability, and half-life, the optimum concentration of thickening agent for the foamed fracturing fluid was found to be 0.5%.
2.5 Determination of foaming agent dosage
To determine the appropriate amount of foaming agent required, a CT1S foaming agent at 0.5%, 1.0%, and 1.5% dosage was tested at 30 °C, while the CT1WⅡ thickener was used at a dosage of 0.5%. The corresponding data obtained from the experiment is stated in Table 5.
According to Table 5, when the amount of CT1S foaming agent increases from 0.1% to 0.3% under the same experimental conditions, the foam half-life shows an increasing trend. Considering performance and cost factors, the amount of CT1S foaming agent was determined to be 0.3%.
2.6 Formula of foam fracturing fluid
To ensure the formulation of foam fracturing fluid meets the desired requirements, the experimental data on foam half-life, foam mass, and viscosity of individual agents, such as foaming and thickening agents, is analyzed. Subsequently, the formulation of the foam fracturing fluid is determined based on the analysis.
0.5% CT1 thickener +0.3% CT1S foaming agent +0.3% CT1D high temperature stabilizer +0.3% CT1U regulator.
3 Performance of foam fracturing fluid formulation
3.1 Preparation method of foam fracturing fluid
Preparation of the fracturing fluid base: Place the desired liquid mixture in a paddle mixer and adjust the mixer rotation speed until the mid-axis of the paddle blade is visible from the vortex. Next, add the regulator, temperature stabilizer, and potassium chloride to the water and stir until they are well mixed. Slowly pour in the thickener while stirring and stop once an even solution is formed. Pour the mixture into a beaker and let it swell for 4 hours to form the fracturing fluid base.
Preparation of the water-based fracturing fluid: Add the designed proportion of foaming agent to the fracturing fluid base and stir well to form water-based fracturing fluid without foaming. Preparation of the foaming fracturing fluid: Pour a certain volume of the base fluid of the fracturing fluid into a Waring blender, add the designed proportion of foaming fluid, and seal the blender. Inject CO2 slowly into the solution and set the blender speed to 700 r/min. Stir for 5 min and stop once the desired froth volume is achieved. The prepared CO2 foam fracturing fluid is shown in Figure 1, which was used to evaluate its performance in experiments.
3.2 Gel breaking performance of foam fracturing fluid
The residue content test of foam fracturing fluid is carried out according to the oil and gas industry standard SY/T5107-2005″Performance Evaluation Method of Water-based Fracturing Fluid”. Firstly, the prepared 1,000 mL foam fracturing fluid was evenly divided into two groups. Then, 600 ppm of the gel breaking agent was added to each group. The gel was broken at 90 °C. After thorough gel fragmentation, centrifugal separation was performed. The separated residue was dried and weighed at 105°C ± 1°C to determine the content of residue in the fracturing fluid. The results of the tests are given in Table 6. The residue content of the gel breakup liquid is calculated as follows.
3.3 Static sand settling performance of foam fracturing fluid
The foam fluid used for fracturing (with 65% Q value) was prepared using the liquid preparation method. Specifically, 200 mL of the foam fluid was added to a beaker, which was then placed in a water bath at a temperature of 90°C for 20 min. During the steady-state water bath, the volume of clear liquid precipitated from the upper layer was recorded at regular intervals, and the results of the liquid static sand settling experiment are shown in Figure 2. The experiments show that this property is uniformly dispersed within the foam after the formation of a stable foam in the fracturing fluid. Due to the interface between bubbles, the foam functions to wrap and support the sand particles used for propping open the induced fractures. As the temperature increases from room temperature to 90 °C, the sand mixture remains uniformly mixed for up to 3 h without showing any obvious delamination phenomena, indicating that the sand-carrying performance is good.
Figure 3 illustrates the relationship between the settling speed of proppant particles (single particle and sand ratio of 10%) and temperature under different temperatures and foam mass fractions. The temperature range is 20°C–90°C, the volume fraction of CO2 is 45%–75%, and the pressure is 10 MPa. It can be inferred from the analysis of Figure 2 that the settling speed of proppant particles increases with temperature. This is attributed to the increased mobility of guar gum molecules, which consequently accelerates the thermal fracture of the hydrogen bond of linear guar gum in the liquid system, ultimately leading to the decrease of the effective viscosity of foam fracturing fluid. Meanwhile, the solution elasticity is also reduced to some extent, weakening the sand carrying performance. At the same experimental temperature, the settling velocity of the sand particles increases with the sand ratio. Moreover, the smaller the foam mass fraction is, the larger the particle settling speed is. This finding indicates that foam quality can suspend proppant and improve the sand carrying performance by increasing the foam mass fraction.
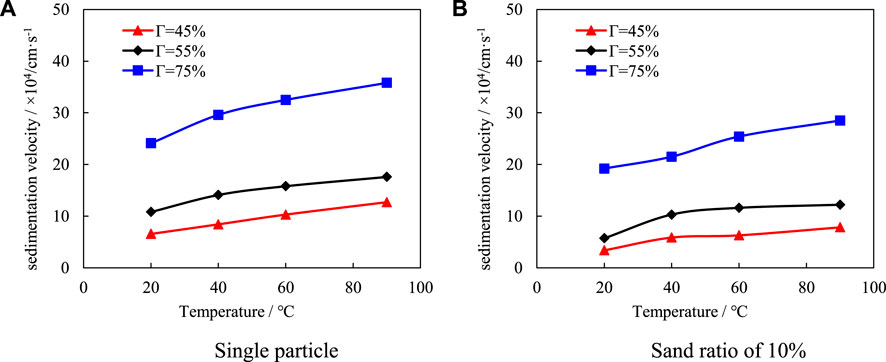
FIGURE 3. Comparison of proppant settling velocity under different temperatures and foam quality. (A) Single particle (B) Sand ratio of 10%.
3.4 Damage performance of foam fracturing fluid
3.4.1 Formation property characteristics of well 1
Figure 4 illustrates the results of a physical parameter analysis of the Longmaxi shale formation in Southwest China. The geological description of this particular section of the well is from 1963.0 to 1981.0 m. The shale is carbonaceous and locally calcareous with both dense and brittle characteristics. Additionally, there are localized pyrite deposits, with graptolites enriched in the section. The columnar bedding is horizontal and developed. Lastly, there are two total seams (both unfilled).
In conclusion, it is necessary for the author to more clearly express the main idea of each section of their writing. Moreover, the use of concise sentence structures can help to create more advanced and targeted expressions. By employing these techniques, the author can write more effectively and help readers more easily comprehend their intended message.
3.4.2 Damage experiment of foam fracturing fluid
After using the shale reservoir core from Well W1, we conducted experiments to evaluate the fracture properties of the foam fracturing fluid. The results of these tests are presented in Table 7. As seen in Table 7, the foam fracturing fluid caused little damage to the shale (less than 19%). In particular, the damage which was caused to the shale by the CO2 foam fracturing fluid was weak.
3.5 Rheological property of foam fracturing fluid
Foam fracturing fluid rheological properties evaluation method can be obtained by following these steps: Firstly, take 70 mL of base foam fracturing fluid and adjust its pH value to 5.8 by adding 0.3% volume ratio of a regulator. Secondly, add the foaming agent to the mixture as per the design proportion and stir thoroughly. Then, transfer the mixture to the RS6000 high-temperature rheometer closed system and access a carbon dioxide air source. Pressurize the system to 10 bars to ensure that the foam fracturing fluid is saturated with carbon dioxide, and then test its performance against temperature resistance and shear resistance. The results of these tests are shown in Figure 5.
According to the experimental results, the foam fracturing fluid has an apparent viscosity greater than 50 mPas, indicating strong spatial structure. The different formulations of the foam fracturing fluid can still maintain their apparent viscosity of more than 50 mPas after long-term shearing at 90°C, indicating excellent thermal and shear resistance.
4 Reusability of foam fracturing fluid
Flowback fluid retrieved from shale gas fracking sites is used in recovery experiments. As shown in Table 8; Figures 6, 7, the viscosity of the foaming fracturing fluid prepared with the flowback fluid is only 24 mPas, much lower than that prepared with clean water. Additionally, the foaming fracturing fluid prepared with the flowback fluid has a shorter half-life of 32 h. This is due to the presence of metallic ions and other components in the flowback fluid, which affect the viscosity, half-life, and other properties of the fracturing fluid.
After hydraulic fracturing, the discharged flowback fluid from oil and gas wells must be replenished with liquid CO2, foam stabilizer, and foaming agent after surface treatment. Please refer to Figure 8 for specific treatment procedures. Firstly, the flowback fluid is treated on the surface. Then, liquid CO2, foam stabilizer, and foaming agent are added to replenish the fluid. Finally, the treated flowback fluid is ready to be reused. To improve the coherence of the article, more linking words and proper paragraph structures are necessary. It is also recommended to expand the vocabulary for smoother and more vivid expressions. Additionally, please double check for any grammar and syntax mistakes.
The process for treating and recovering backflow fluid from fracturing comprises several steps including solid-liquid separation, alkalization, chemical flocculation, oxidation, reverse osmosis, and biochemistry. These steps are aimed at removing different impurities found in the backflow fluid. In the final stage of treatment, dissolved total solids are removed using reverse osmosis membranes, while salts are recovered using methods such as evaporation and crystallization. In case of well sites with different situations, movable or fixed salt factories may be used. As a result of this full treatment process, the treated water is regarded as clean water, suitable for various construction purposes, hence achieving true zero discharge. In the process of application, the injection pressure, foam concentration, and foam quality are the main factors that affect the fracturing effect. Therefore, the performance optimization of carbon dioxide foam fracturing fluid should not only focus on component selection but also on technological innovation, supplemented by laboratory experiments and field trials.
5 Conclusion
(1) Through experimental evaluation and study on the performance of foam fracturing fluid, the formula of foam fracturing fluid which is suitable for shale gas reservoir fracturing has been developed. The formula includes 0.5% CT1 thickener, 0.3% CT1S foaming agent, 0.3% CT1D high-temperature stabilizer, and 0.3% CT1U regulator.
(2) The viscosity, static sand settling performance, and rheological properties of the foam fracturing fluid have been evaluated experimentally. The viscosity of the foam fracturing fluid is 2 mPa·s. The residue content is 1.1 mg/L, the surface tension is 24.5 mN/m, and the interfacial tension is 1.5 mN/m. Static sand settling experiments have been performed with 40–70 mesh ceramic particles which are commonly used in shale gas fracking. The sand-to-liquid ratio was set at 40% for the static sand-carrying experiment. The flow properties of the sand-carrying fluid were good, with no property settling within 3 h. Shale reservoir cores from well Wei-1 have been used to assess the rate of foam fracture, which was less than 19%. Under the experimental conditions of shear rate of 170 s-1 and temperature of 90°C, the viscosity of fracturing fluid was measured to be greater than 50 mPa·s, 90 min after shear, demonstrating the excellent temperature and shear resistance of the foam fracturing fluid.
(3) The fracturing flowback fluid retrieved from Changning H3 platform in Southwest China has been used for a recovery experiment. The viscosity of the fracturing fluid base prepared using the flowback fluid is only 24 mPas, which is much lower than the viscosity of the clean water preparation. At the same time, the foam fracturing fluid prepared with the flowback fluid has a shorter half-life of 32 h. The viscosity and half-life of foam fracturing fluids prepared with flowback fluid are worse than those prepared with clean water. The effluent needs to be treated until the treated water quality meets industry standards before it can be reused.
Data availability statement
The original contributions presented in the study are included in the article/Supplementary Material; further inquiries can be directed to the corresponding author.
Author contributions
SL: Conceptualization, resources, funding acquisition, writing—original draft and software. YF and JY: funding acquisition, project administration. TH: Data curation, formal analysis, methodology, project administration. JL: writing—original draft and writing—review and editing. XW: Project administration, resources. All authors contributed to the article and approved the submitted version.
Funding
This work was supported by the 2021 Scientific Research Plan Project of PetroChina Southwest Oil and Gas Field Company: Research on the Transformation Technology of Permian Reservoir in the Middle Sichuan Paleo uplift (20220302-10).
Acknowledgments
The authors are grateful for the support of the Project of PetroChina Southwest Oil and Gas Field Company. Thanks to reviewers and editors for their careful review of this manuscript. We are grateful to Mr. Xiang Chao from the Natural Gas Research Institute of PetroChina Southwest Oil and Gas Field Company for providing reliable experimental data for the revision of our paper.
Conflict of interest
SL, YF, TH, JY, JL, and XW were employed by the Engineering Technology Research Institute of PetroChina Southwest Oil & Gas Field Company.
Publisher’s note
All claims expressed in this article are solely those of the authors and do not necessarily represent those of their affiliated organizations, or those of the publisher, the editors and the reviewers. Any product that may be evaluated in this article, or claim that may be made by its manufacturer, is not guaranteed or endorsed by the publisher.
References
Ahmed, Abdelaal, Aljawad, Murtada. Saleh, Alyousef, Zuhair, and Muhammad, M. A. (2021b). A review of foam-based fracturing fluids applications: From lab studies to field implementations. J. Nat. Gas Sci. Eng. 95, 104236. doi:10.1016/j.jngse.2021.104236
Ahmed, S., Alameri, W., Ahmed, W. W., and Khan, S. A. (2021a). Rheological behavior of scCO2-foam for improved hydrocarbon recovery: Experimental and deep learning approach. J. Petroleum Sci. Eng. 203, 108646. doi:10.1016/j.petrol.2021.108646
Ahmed, S., Elraies, K. A., Hanamertani, A. S., Hashmet, M. R., Shafian, S. R., and Hsia, I. C. “Investigation of carbon dioxide foam performance utilizing different additives for fracturing unconventional shales,” in Proceedings of the 2019, Abu Dhabi International Petroleum Exhibition and Conference. Society of Petroleum Engineers, Abu Dhabi, UAE, November 2019.
Ahmed, S., Elraies, K. A., Hashmet, M. R., and Hanamertani, A. S. (2017a). Viscosity models for polymer-fre CO2 foam fracturing fluid with the effect of surfactant concentration, salinity and shear rate. Energies 10 (12), 1970. doi:10.3390/en10121970
Ahmed, S., Elraies, K. A., Tan, I. M., and Hashmet, M. R. (2017b). Experimental investigation of associative polymer performance for CO2 foam enhanced oil recovery. J. Petrol. Sci. Eng. 157, 971–979. doi:10.1016/j.petrol.2017.08.018
Arezoo, S. E., AhmedIbrahim, F., Hisham, A., and Nasr, E. D. “Mobility control using nanoparticle-stabilized CO2 foam as a hydraulic fracturing fluid,” in Proceedings of the SPE-185863-MS, paper was prepared for presentation at the SPE Europec featured at 79th EAGE Conference and Exhibition held in Paris, Paris, France, June 2017.
Barati, R., and Liang, J. T. (2014). A review of fracturing fluid systems used for hydraulic fracturing of oil and gas wells. J. Appl. Polym. Sci. 131 (16). doi:10.1002/app.40735
Cawiezel, K. E. (1987). “Rheological properties of foam fracturing fluids under downhole conditions,”. Dallas, Texas, United States, SPE 16191-MS (SPE).
Cong, Z. Y., Li, Y. W., Pan, Y. S., Liu, B., Shi, Y., Wei, J. G., et al. (2022). Study on CO2 foam fracturing model and fracture propagation simulation. Energy 238, 121778. doi:10.1016/j.energy.2021.121778
Dong, Zhiyu, Liu, Shuo, Nie, Xin, Zhang, Yulong, Dong, Kaili, and Wang, Junfeng (2021). Experimental and molecular simulation research on the effect of metal ions on the stability of SDS foam. Energy and Fuels 36, 521–526. doi:10.1021/acs.energyfuels.1c03249
Edrisi, A., and Kam, S. I. (2014). A new foam model in pipes for drilling and fracturing applications. SPE J. 19 (4), 576–585. doi:10.2118/162709-pa
Fei, Y., Pokalai, K., Johnson, R., Gonzalez, M., and Haghighi, M. (2017). Experimental and simulation study of foam stability and the effects on hydraulic fracture proppant placement. J. Nat. Gas. Sci. Eng. 46, 544–554. doi:10.1016/j.jngse.2017.08.020
Feng, Chenchen, Ma, Xurui, and Jing, Zefeng (2021). Dynamic proppant-carrying performance of VES-CO2 foam fracturing fluid in the pipeline and the fracture. J. Petroleum Sci. Eng. 210, 110034. doi:10.1016/j.petrol.2021.110034
Gao, C., Cheng, S., Wang, M., Wu, W., Gao, Z., Li, S., et al. (2023). Optimization of carbon dioxide foam fracturing technology for shale gas reservoir. Geofluids 23, 1–11. doi:10.1155/2023/6187764
Gu, M., and Mohanty, K. (2015). Rheology of polymer-free foam fracturing fluids. J. Petrol. Sci. Eng. 134, 87–96. doi:10.1016/j.petrol.2015.07.018
Harris, P. C., and Heath, S. J. (1996). Rheology of crosslinked foams. SPE 28512-PA 11 (2), 113–116. doi:10.2118/28512-pa
Harris, P. C., and Reidenbach, V. G. (1987). High-temperature rheological study of foam fracturing fluids. SPE 13177-PA 39 (5), 613–619. doi:10.2118/13177-pa
Huang, L. K., He, R., Yang, Z. Z., Tan, P., Chen, Z. W., Li, X. G., et al. (2023). Exploring hydraulic fracture behavior in glutenite formation with strong heterogeneity and variable lithology based on DEM simulation. Eng. Fract. Mech. 278, 109020. doi:10.1016/j.engfracmech.2022.109020
Jing, Z. F., Feng, C. C., Wang, S. Z., Xu, D. H., and Xu, G. X. (2017). Effect of foam quality on flow behavior of liquid CO2-based foam fracturing fluid stabilized by hydrofluoroether. J. Petrol. Sci. Eng. 159, 710–716. doi:10.1016/j.petrol.2017.10.017
Ju, Shuang, Huang, Qiming, Wang, Gang, Li, Jun, Wang, Enmao, Qin, Cunli, et al. (2022). Rheological and morphological characteristics of foam fluid using hydroxypropyl guar and surfactant. J. Petroleum Sci. Eng. 211, 110124. doi:10.1016/j.petrol.2022.110124
Kartini, R., Kim, Y., and Lee, W. (2021). Evaluation of surfactant mixture for supercritical carbon dioxide foamed acid in carbonate matrix acidizing. Energies 14, 6567. doi:10.3390/en14206567
Li, C., Huang, Y. Q., Sun, X., Gao, R. M., Zeng, F. H., Tontiwachwuthikul, Paitoon, et al. (2017). Rheological properties study of foam fracturing fluid using CO2 and surfactant. Chem. Eng. Sci. 170, 720–730. doi:10.1016/j.ces.2017.03.022
Li, Mingyang, Huang, Qiming, Yan, Yuting, and Chen, Kaipeng (2022). Influence of calcium chloride in coal on guar-based foam fracturing fluid rheological property: An experimental study. Phys. Fluids 34 (10), 103106. doi:10.1063/5.0115073
Li, Y., DiCarlo, D., Li, X., and Zang, J. (2015). An experimental study on application of nanoparticles in unconventional gas reservoir CO2 fracturing. J. Petrol. Sci. Eng. 133, 238–244. doi:10.1016/j.petrol.2015.05.023
Liu, Shenggui, Huang, Jinkuang, Tang, Songlei, Shi, Shixiong, Wu, Xuan, and Liu, Xin (2020). Experimental study on the damage of artificial fracture permeability in coal during the flow back of guar-based fracturing fluid. Geofluids 2020, 1–13. doi:10.1155/2020/8302310
Liu, X., Cai, M., Cai, C., Jiang, X., Feng, Z., and Hu, J. (2004). Performance evaluation on CO2 foam fracturing fluid. Drill. Fluid Cem. Fluid 21 (3), 1–15. doi:10.1016/j.ympev.2004.05.011
Luo, Xiang Rong, Wang, Shu Zhong, Jing, Ze Feng, Lv, Ming Ming, Wang, Zhi Guo, De Zhai, Zhen, et al. (2014a). A review of shale gas exploitation technology. Appl. Mech. Mater. 675-677, 1485–1489. doi:10.4028/www.scientific.net/amm.675-677.1485
Luo, X., Wang, S., Wang, Z., Jing, Z., and Lv, M. (2014b). Experimental research on rheological properties and proppant transport performance of GRF-CO2 fracturing fluid. J. Petrol. Sci. Eng. 120, 154–162. doi:10.1016/j.petrol.2014.06.009
Mazza, R. L., and Quid, L. “Free CO2/sand stimulations: An overlooked technology-production update,” in Proceedings of the Paper SPE 72383 presented at the SPE Eastern Regional Meeting held in Canton, Ohio, United States, October 2001.
Reidenbach, V. G. (1986). “Rheological study of foam fracturing fluids using nitrogen and carbon,”. SPE 12026-PADallas, Texas, United States, (SPE).
Sun, X., Liang, X. B., Wang, S. Z., and Lu, Y. (2014). Experimental study on the rheology of CO2 viscoelastic surfactant foam fracturing fluid. J. Petrol. Sci. Eng. 119, 104–111. doi:10.1016/j.petrol.2014.04.017
Tan, P., Jin, Y., and Pang, H. W. (2021). Hydraulic fracture vertical propagation behavior in transversely isotropic layered shale formation with transition zone using XFEM-based CZM method. Eng. Fract. Mech. 248, 107707. doi:10.1016/j.engfracmech.2021.107707
Tan, P., Pang, H. W., Zhang, R. X., Jin, Y., Zhou, Y. C., Kao, J. W., et al. (2020). Experimental investigation into hydraulic fracture geometry and proppant migration characteristics for southeastern Sichuan deep shale reservoirs. J. Petroleum Sci. Eng. 184, 106517. doi:10.1016/j.petrol.2019.106517
Tudor, R., Vozniak, C., and Banks, M. L. “Technical advances in liquid CO2 fracturing,” in Proceedings of the Paper CIM 94236, presented at the CIM Annual Technical Conference, Calgary, Canada, June 1994.
Verma, Amit, Chauhan, Geetanjali, Baruah, Partha Pratim, and Ojha, Keka (2018). Morphology, rheology and kinetics of nano-silica stabilized gelled foam fluid for hydraulic fracturing application. Industrial Eng. Chem. Res. 12, 13449–13462. doi:10.1021/acs.iecr.8b04044
Verma, Amit, Chauhan, Geetanjali, and Ojha, Keka (2017). Synergistic effects of polymer and bentonite clay on rheology and thermal stability of foam fluid developed for hydraulic fracturing. Asia-Pac. J. Chem. Eng. 12, 872–883. doi:10.1002/apj.2125
Wang, M., Wu, W., Chen, S., Li, S., Li, T., Ni, G., et al. (2022). Experimental evaluation of the rheological properties and influencing factors of gel fracturing fluid mixed with CO2 for shale gas reservoir stimulation. Gels 8, 527. doi:10.3390/gels8090527
Wang, S. Z., Luo, X. R., and Jing, Z. F. (2018). Rheological properties of BCG-CO2 fracturing fluid for shale gas. Earth Environ. Sci. 186, 012026. doi:10.1088/1755-1315/186/4/012026
Wang, Zhen-duo, Wang, Xiaoquan, and Lu, Yong-jun (2004). Application of carbon dioxide foam fracturing technology in low-permeability and low-pressure gas reservoir. Oil Field Dev. 25 (5), 66–70. doi:10.7623/syxb200403013
Wanniarachchi, W., Ranjith, P., and Perera, M. (2017). Shale gas fracturing using foam-based fracturing fluid: A review. Environ. Earth Sci. 76 (2), 91. doi:10.1007/s12665-017-6399-x
Yang, L. I., Weng, Dingwei, Yu, Yongbo, and Yin, Xiyong (2006). Study on foam fracturing and its field application. DFCF 23 (1), 51–54.
Zheng, Shichao, Kang, Zhongjian, Cui, Minghui, Nie, Yunliang, and Zhang, Anqi (2020). Improvement of shale gas reservoir based on plasma pulse shock and frequency resonance technology. J. Nat. Gas Sci. Eng. 80, 103403. doi:10.1016/j.jngse.2020.103403
Keywords: shale gas reservoir, carbon dioxide, foam fracturing, foam quality, rheological property
Citation: Li S, Fan Y, He T, Yang J, Li J and Wang X (2023) Research and performance optimization of carbon dioxide foam fracturing fluid suitable for shale reservoir. Front. Energy Res. 11:1217467. doi: 10.3389/fenrg.2023.1217467
Received: 05 May 2023; Accepted: 12 July 2023;
Published: 27 July 2023.
Edited by:
Xiaojin Zheng, Princeton University, United StatesReviewed by:
Guodong Zhang, Qingdao University of Science and Technology, ChinaYing Zhong, Chengdu University of Technology, China
Copyright © 2023 Li, Fan, He, Yang, Li and Wang. This is an open-access article distributed under the terms of the Creative Commons Attribution License (CC BY). The use, distribution or reproduction in other forums is permitted, provided the original author(s) and the copyright owner(s) are credited and that the original publication in this journal is cited, in accordance with accepted academic practice. No use, distribution or reproduction is permitted which does not comply with these terms.
*Correspondence: Song Li, bGlzb25nMDMwMTE2NDBAMTYzLmNvbQ==