- 1College of Architectural Science and Engineering, Yangzhou University, Yangzhou, Jiangsu, China
- 2School of Mechanical Engineering, Tongling University, Tongling, Anhui, China
- 3Key Laboratory of Construction Hydraulic Robots of Anhui Higher Education Institutes, Tongling University, Tongling, Anhui, China
- 4Key Laboratory of Additive Manufacturing of Tongling City, Tongling University, Tongling, Anhui, China
The fiber geometry is one of the important parameters in the effective conversion performance and local strength of thermoelectric composites. In this study, the plane problem of a hollow fiber embedded within a non-linear thermoelectric medium in the presence of a uniform remote in-plane electric current and a uniform remote energy flux is investigated based on the complex variable method. Closed-form expressions for all the potential functions characterizing the thermoelectric field and the associated thermal stress field in both the matrix and fiber are obtained by solving the corresponding boundary value problem. Numerical examples are presented to illustrate the effect of hollowness ratio of the fiber on the local energy conversion efficiency and interfacial thermal stress concentration. It is found that a higher conversion efficiency and a lower amount of thermal stress concentration around a hollow fiber than that around a solid fiber could be achieved simultaneously by appropriate selection of the hollowness ratio of the fiber. The results can be directly used for performance optimization and reliability evaluation in design of thermoelectric composites in engineering.
1 Introduction
Thermoelectric material is a novel kind of functional material, which can directly convert heat into electricity and vice versa (Bell, 2008). A thermoelectric device is free of moving parts, noises, and environmentally harmful emissions, making it extremely attractive in renewable energy fields, such as waste heat recovery, solar power generation, carbon reduction, and Freon-free refrigeration (Zhang et al., 2016; He and Tritt, 2017; Mahmoudinezhad et al., 2018). The electric transport and thermal conduction in a thermoelectric material are intrinsically coupled, making it highly challenging to improve the conversion efficiency in a single-phase thermoelectric material (Yang et al., 2013). Therefore, a lot of effort in developing high-performance thermoelectric material is devoted to engineering hybrid composites by introducing inclusions/fibers into single-phase thermoelectric material to enhance the overall conversion efficiency (Wan et al., 2015; Guo et al., 2016; Srivastava et al., 2018).
From the point of view of solid mechanics, the existence of the inclusions/fibers may cause severe concentration of the temperature field and the associated thermal stress field in thermoelectric materials under in-service conditions. Most thermoelectric materials are semiconductors with poor mechanical properties, and excessive thermal stress may lead to the premature failure of the thermoelectric devices (Li et al., 2015; Song et al., 2019). The analysis of thermoelectric materials with the inclusions/fibers can further improve our understanding of the mechanical behavior of such new materials and thus is essential for optimal design and improved reliability of thermoelectric composites. Using complex variable methods, rigorous thermo-electro-mechanical analyses of thermoelectric materials containing elastic inhomogeneities have been carried out by several authors (Zhang et al., 2017; Wang et al., 2018; Yang et al., 2020). In the corresponding discussions of the inhomogeneity problem in thermoelectric materials, it has been assumed that the inclusion or fiber is assumed to have a solid cross-section. In engineering practice, hollow fibers or particles are often introduced into thermoelectric materials due to their distinct microstructures. To the best of our knowledge, the effect of a hollow particle/fiber on the thermoelectric and thermoelastic responses of a thermoelectric composite has never been thoroughly investigated. This motivates our current work.
The paper is organized as follows: basic equations of a non-linear thermoelectric material are presented in Section 2, followed by the detailed analysis of the plane problem of an infinite thermoelectric matrix containing a hollow fiber subjected to a uniform remote thermoelectric loading by using the complex variable technique in Section 3. In Section 4, we use the explicit results from Section 3 and present numerical examples to illustrate the influence of the hollowness ratio on the local energy conversion efficiency and thermal stress concentration around a hollow fiber in a thermoelectric composite. Finally, we summarize our conclusion in Section 5.
2 Basic equations for thermoelectric materials
In a homogenous thermoelectric medium wherein both electric charges and energy are conserved, the governing equations and transport equations for the non-linearly coupled electric and heat conduction are given as follows (Yang et al., 2013):
together with
where
According to Eqs 4, 5, the electric potential
where “Re” denotes the real part of a complex number and the overbar denotes the complex conjugate. It follows from Eqs 2, 3, 6, 7 that the electric current components
where the prime (
which can be used as the boundary conditions of the electric current and energy flux in the integral form. Here, “Im” denotes the imaginary part of a complex number.
For a steady thermal stress problem where the elastic constants are assumed to be temperature-independent, the three in-plane stresses (
Here,
which will be used as the stress boundary condition in the integral form. To summarize, the mathematical formulation of the non-linearly coupled thermo-electro-mechanical problem is completed using the complex function theory with each unknown function determined by the corresponding boundary conditions.
3 Solutions of thermoelectric material with a hollow fiber
As illustrated in Figure 1, we consider the plane strain deformation of an infinite thermoelectric matrix enclosing a hollow fiber subjected to a uniform remote electric current
where
where
where
where
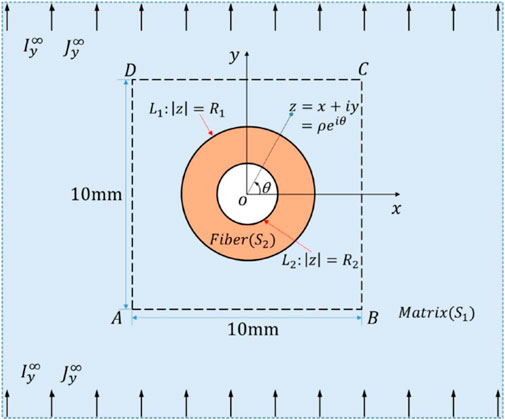
FIGURE 1. Hollow fiber embedded in a thermoelectric matrix under uniform remote in-plane thermoelectric loading.
Considering that the energy flux at infinity is uniform, according to Eqs 9, 18, the potential function
where the real constant
where
Here, the two complex constants, namely,
So far, the quantities related to the electric current and temperature fields in both the matrix and fiber can be determined from Eqs 6 to 10 together with Eqs 19, 21a. The following studies will deal with the analysis of the associated thermal stress problem. Considering the single-valued conditions of elastic displacement (Eq. 14) and the resultant force (Eq. 15), the elastic potential functions in both the matrix and fiber take the following form:
where
The analytical functions
Equations 24a, 24b describe the continuity of elastic stresses and displacements across the perfectly bonded interface
where the four real dimensionless constants
and the four complex constants
together with
Up to here, the elastic stress components
where
4 Numerical examples
To illustrate the application of the analysis model, some numerical examples are presented. In the following examples, the matrix is set as a bismuth tellurium semiconductor, and the material constants are given as
In engineering practice, the thermoelectric conversion efficiency is a crucial parameter for the design of thermoelectric composites. Figure 2 shows the effect of the hollowness ratio
where
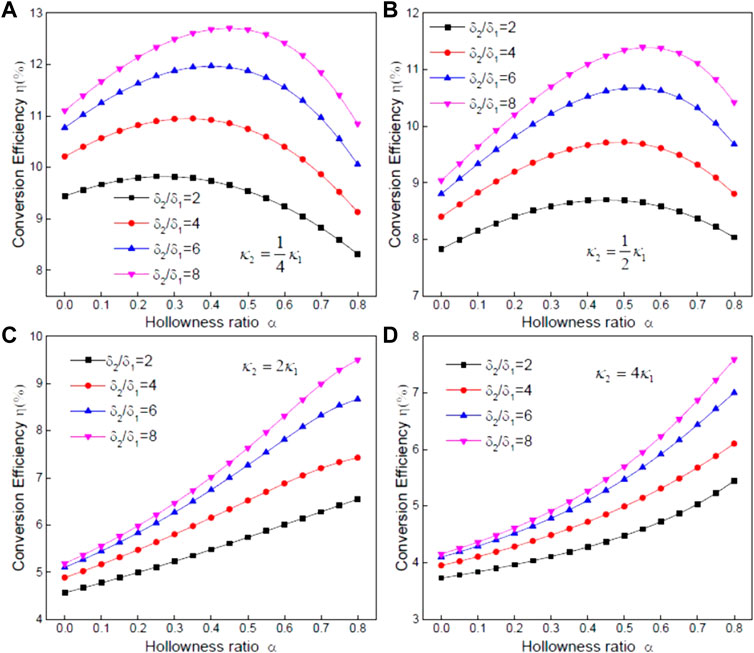
FIGURE 2. Effect of the hollowness ratio and conductivity properties of the fiber on the local energy conversion efficiency.
As shown in Figure 2, with specific fiber radius
Figure 3 illustrates the variation of local energy conversion efficiency around a hollow fiber with desirable conductivity properties with respect to the hollowness ratio
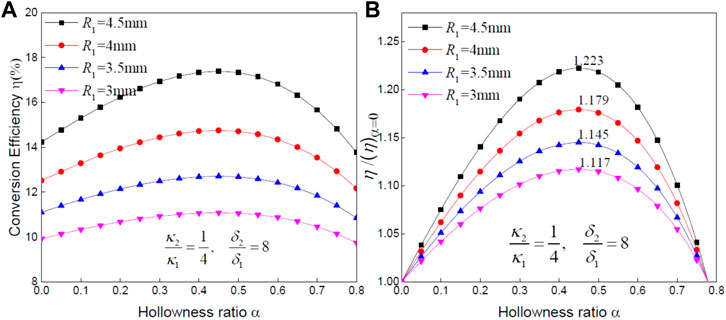
FIGURE 3. (A) Local energy conversion efficiency; (B) relative energy conversion efficiency around a desirable fiber with different hollowness ratios.
In addition to the conversion performance, the mechanical reliability also deserved further consideration when designing a thermoelectric composite. Figure 4 presents the variation of the interfacial normal stress distribution around a softer hollow fiber with desirable conductivity properties. Here, the soft fiber has a lower elastic modulus but a larger linear expansion coefficient than the matrix material. Since the thermal expansion of a softer fiber is greater than that of the matrix material, the matrix will prevent the fiber from expanding outward, and the interface is under compression, as shown in Figure 4A. In addition, the maximum compressive normal stress is achieved when
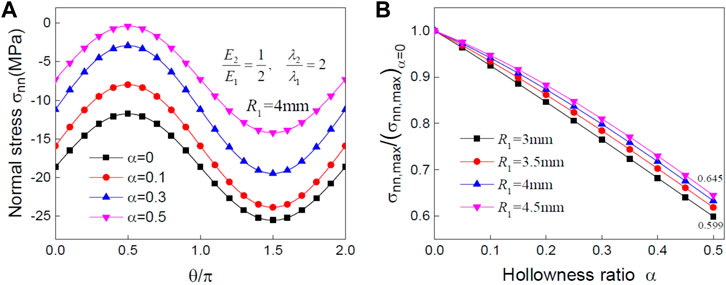
FIGURE 4. (A) Distribution of normal stress; (B) relative concentration factor of normal stress around a soft fiber with different hollowness ratios.
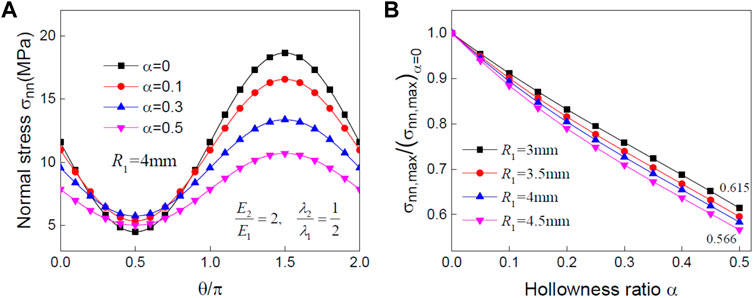
FIGURE 5. (A) Distribution of normal stress; (B) relative concentration factor of normal stress around a hard fiber with different hollowness ratios.
5 Concluding remarks
In this paper, the problem of a hollow fiber embedded in an infinite thermoelectric matrix under the remote uniform electric current and energy flux is investigated. The closed-form solutions of the electric field, temperature field, and associated thermal stress field in the entire composite are derived via the use of a complex variable technique. The following conclusions are summarized for designing and optimizing thermoelectric composites reinforced by hollow fibers/particles:
1. Fibers with lower thermal conductivity are helpful to improve the energy conversion efficiency of thermoelectric composites, but it may aggravate the interfacial thermal stress concentration.
2. A higher thermoelectric conversion efficiency and a lower amount of the normal stress concentration than that around a solid fiber could be achieved simultaneously by appropriate selection of the hollowness ratio of the fiber.
Data availability statement
The original contributions presented in the study are included in the article/Supplementary Material; further inquiries can be directed to the corresponding authors.
Author contributions
CY and SX contributed to the conception and design of the study. CY performed the formal analysis, and wrote the first draft of the manuscript. HL and CD wrote sections of the manuscript. CY, HL, CD, and SX contributed to manuscript revision and supervision and read and approved the submitted version.
Funding
This work was supported by the National Natural Science Foundation of China (grant no. 11802263&11902116), Natural Science Foundation of Jiangsu Province (grant no. BK20210787), Natural Science Foundation of Guangdong Province (grant no. 2022A1515011773), Natural Science Foundation of Guangzhou City (grant no. 202201010317), Qinglan Project of Yangzhou University, Provincial Natural Science Research of University of Anhui Province (KJ 2021A1058), and Key Laboratory of Construction Hydraulic Robots of Anhui Higher Education Institutes (grant no. TLXYCHR-O-21YB04).
Conflict of interest
The authors declare that the research was conducted in the absence of any commercial or financial relationships that could be construed as a potential conflict of interest.
Publisher’s note
All claims expressed in this article are solely those of the authors and do not necessarily represent those of their affiliated organizations, or those of the publisher, the editors, and the reviewers. Any product that may be evaluated in this article, or claim that may be made by its manufacturer, is not guaranteed or endorsed by the publisher.
References
Bell, L. E. (2008). Cooling, heating, generating power, and recovering waste heat with thermoelectric systems. Science 321 (5895), 1457–1461. doi:10.1126/science.1158899
Guo, H., Xin, H., Qin, X., Zhang, J., Li, D., Li, Y., et al. (2016). Enhanced thermoelectric performance of highly oriented polycrystalline SnSe based composites incorporated with SnTe nanoinclusions. J. Alloy. Compd. 689, 87–93. doi:10.1016/j.jallcom.2016.07.291
He, J., and Tritt, T. M. (2017). Advances in thermoelectric materials research: Looking back and moving forward. Science 357 (6358), eaak9997. doi:10.1126/science.aak9997
Huang, M. J., Chou, P. K., and Lin, M. C. (2008). An investigation of the thermal stresses induced in a thin-film thermoelectric cooler. J. Therm. Stress. 31 (5), 438–454. doi:10.1080/01495730801912512
Li, G., An, Q., LiGoddard, W. A., Zhai, P., Zhang, Q., Snyder, G. J., et al. (2015). Brittle failure mechanism in thermoelectric skutterudite CoSb3. Chem. Mat. 27 (18), 6329–6336. doi:10.1021/acs.chemmater.5b02268
Liu, L. (2012). A continuum theory of thermoelectric bodies and effective properties of thermoelectric composites. Int. J. Eng. Sci. 55, 35–53. doi:10.1016/j.ijengsci.2012.02.003
Mahmoudinezhad, S., Rezania, A., and Rosendahl, L. A. (2018). Behavior of hybrid concentrated photovoltaic-thermoelectric generator under variable solar radiation. Energy Convers. manage. 164, 443–452. doi:10.1016/j.enconman.2018.03.025
Song, H., Song, K., and Gao, C. (2019). Temperature and thermal stress around an elliptic functional defect in a thermoelectric material. Mech. Mat. 130, 58–64. doi:10.1016/j.mechmat.2019.01.008
Srivastava, D., Norman, C., Azough, F., Schäfer, M. C., Guilmeau, E., and Freer, R. (2018). Improving the thermoelectric properties of SrTiO3-based ceramics with metallic inclusions. J. Alloy. Compd. 731, 723–730. doi:10.1016/j.jallcom.2017.10.033
Wan, S., Huang, X., Qiu, P., Bai, S., and Chen, L. (2015). The effect of short carbon fibers on the thermoelectric and mechanical properties of p-type CeFe4Sb12 skutterudite composites. Mat. Des. 67, 379–384. doi:10.1016/j.matdes.2014.11.050
Wang, P., Wang, B. L., Wang, K. F., and Cui, Y. J. (2018). Analysis of inclusion in thermoelectric materials: The thermal stress field and the effect of inclusion on thermoelectric properties. Compos. Part B-Eng. 166, 130–138. doi:10.1016/j.compositesb.2018.11.120
Yang, H., Yu, C., Tang, J., Qiu, J., and Zhang, X. (2020). Electric-current-induced thermal stress around a non-circular rigid inclusion in a two-dimensional nonlinear thermoelectric material. Acta Mech. 231 (11), 4603–4619. doi:10.1007/s00707-020-02770-z
Yang, Y., Ma, F. Y., Lei, C. H., Liu, Y. Y., and Li, J. Y. (2013). Nonlinear asymptotic homogenization and the effective behavior of layered thermoelectric composites. J. Mech. Phys. Solids 61 (8), 1768–1783. doi:10.1016/j.jmps.2013.03.006
Yu, C., Zou, D., Li, Y., Yang, H., and Gao, C. (2018). An arc-shaped crack in nonlinear fully coupled thermoelectric materials. Acta Mech. 229 (5), 1989–2008. doi:10.1007/s00707-017-2099-6
Zhang, A. B., Wang, B. L., Wang, J., and Du, J. K. (2017). Two-dimensional problem of thermoelectric materials with an elliptic hole or a rigid inclusion. Int. J. Therm. Sci. 117, 184–195. doi:10.1016/j.ijthermalsci.2017.03.020
Keywords: thermoelectric materials, complex variable method, hollow fiber, conversion efficiency, thermal stress
Citation: Yu C, Liu H, Du C and Xing S (2023) Influence of fiber hollowness on the local thermo-electro-elastic field in a thermoelectric composite. Front. Energy Res. 11:1181191. doi: 10.3389/fenrg.2023.1181191
Received: 07 March 2023; Accepted: 05 April 2023;
Published: 19 April 2023.
Edited by:
Haopeng Song, Nanjing University of Aeronautics and Astronautics, ChinaReviewed by:
Wenzhi Yang, Lanzhou University, ChinaJian Hua, Tsinghua University, China
Min Li, Hohai University, China
Yongjian Wang, Nanjing Agricultural University, China
Copyright © 2023 Yu, Liu, Du and Xing. This is an open-access article distributed under the terms of the Creative Commons Attribution License (CC BY). The use, distribution or reproduction in other forums is permitted, provided the original author(s) and the copyright owner(s) are credited and that the original publication in this journal is cited, in accordance with accepted academic practice. No use, distribution or reproduction is permitted which does not comply with these terms.
*Correspondence: Chuanbin Yu, Y2J5dUB5enUuZWR1LmNu; Shichao Xing, dGx1eHNjQHRsdS5lZHUuY24=