- 1Biochemical and Bioenvironmental Engineering Research Group (BBERG), Department of Chemical Engineering, Ladoke Akintola University of Technology, Ogbomoso, Nigeria
- 2Department of Mechanical and Industrial Engineering Technology, Faculty of Engineering and Built Environment University of Johannesburg, Johannesburg, South Africa
- 3Centre for Technology in Water and Wastewater (CTWW), School of Civil and Environmental Engineering, Faculty of Engineering and IT, University of Technology Sydney, Ultimo, NSW, Australia
Anaerobic digestion (AD) processes can face operational challenges or flaws such as substrate structure and characteristics complexity, process complexity, low productivity, inefficient biodegradability, and poor stability, which suppresses or reduces biogas and biomethane production. As a result of the need to overcome these challenges/shortcomings and improve or enhance biogas and biomethane yield, process intensification methods have gained attention. There is some literature review on pretreatment and co-digestion as a means of improving AD performance; however, there is no systematic information on the various strategies required for improving AD performance and, in turn, increasing biogas/biomethane yield. The AD process produces biogas, a valuable renewable biofuel. Biogas is composed primarily of biomethane and other undesirable components such as carbon dioxide, oxygen, hydrogen sulphide, water vapour, ammonia, siloxanes, nitrogen, hydrocarbons, and carbon monoxide, which act as impurities or contaminants and tend to reduce the biogas specific calorific value while also causing various problems with machine operation. As a result, various technologies are used to improve raw biogas quality by removing contaminants during biogas transformation to biomethane. As a result, this paper provides a comprehensive review of the various systematic process intensification strategies used to overcome AD process challenges/shortfalls, improve or enhance biogas and biomethane production, and conventional and emerging or advanced technologies for biogas purification, cleaning, and upgrading.
1 Introduction
The global industrial revolution, together with simultaneous socio-economic and technological advancement, has been driven by the utilisation of fossil fuels (oil, gas, and coal), but its use has, over the years, negatively impacted the environment by causing climate change through the release of toxic pollutants and contributing to greenhouse gas emission (Kasinath et al., 2021). Sustainable global energy strategies include the use of renewable energy resources such as geothermal, hydro, solar, biomass, and wind to reduce the use of fossil fuels (Chen et al., 2010). One of the renewable energy technologies that can be employed to generate bioenergy from biomass is the anaerobic digestion (AD) process technology.
The AD process technology is a complex multistep process that involves the degradation or breakdown of organic matter by a group of microorganisms in the absence of oxygen, resulting in the production of biogas/biomethane and digestate as a byproduct (Kasinath et al., 2021). Figure 1 illustrates the steps involved in the biodegradation of complex organic matter. As shown in Figure 1, during the hydrolysis step (the first step), hydrolytic enzymes released by bacteria break down substrates such as carbohydrates, proteins, lipids, and insoluble polymers into soluble oligomers and monomers. In the acidogenesis step (the second step), amino acids, simple sugars, and long-chain fatty acids are further broken down into volatile fatty acids (VFAs), acetate, alcohols, CO2, and H2. The third step, acetogenesis, involves the further metabolism of VFAs and alcohols into acetic acid and H2. Finally, in the methanogenesis step (the fourth and final step), the mixture of CO2, H2, formate, methanol, and acetate is transformed into methane (or biomethane) through acetoclastic, hydrogenotrophic, and methylotrophic pathways (Kasinath et al., 2021), which is the ultimate product of the process.
The digestate is a nutrient-rich biomass that can be further used as an organic fertilizer for organic farming (Khan et al., 2017; Cai et al., 2021). The biomass wastes generally utilised for biogas/biomethane production can be categorised into agricultural wastes, energy crops/residues, municipal biowaste, industrial wastes, and wastewater (Ljupka, 2010), as well as aquatic biomass (e.g., algae) (Ward et al., 2014) as schematically presented in Figure 2.
The AD is normally carried out in biodigesters or bioreactors. The performance of biogas digesters or reactors with respect to biogas and biomethane production or yield is linked to various physical, chemical, and biological factors such as the structure or nature and characteristics (properties) of the organic waste (feedstock), total solid content; hydraulic retention time, pH, stirring, carbon/nitrogen ratio, temperature, organic loading rate, volatile fatty acids (VFA) and seeding (Rocamora et al., 2020; Uddin et al., 2021). Any forms of modification that might be made to these factors can lead to changes in the surrounding environment of the microbial community and movement within the AD biodigester. Hence, to optimize biogas and biomethane production, it is essential to control these factors. These factors can be manipulated within an appropriate and acceptable range so that the AD biodigester or reactor can run optimally and efficiently without failure or collapse. Furthermore, other operational shortcomings, such as substrate complexity, low productivity, process complexity, inefficient biodegradability, and poor stability, tend to suppress or reduce biogas and biomethane production. Therefore, the need to overcome these shortcomings and improve or enhance biogas and biomethane yield has drawn attention to process intensification methods. Different process intensification strategies have been employed to overcome these shortcomings and improve or enhance biogas and biomethane production (Yadvika et al., 2004).
The raw biogas produced from organic biomass wastes through the AD processes consists majorly of biomethane (CH4) and carbon dioxide (CO2). Aside from the CH4 and CO2, the raw biogas also contains some small or minor amounts of hydrogen sulphide (H2S), ammonia (NH3), water vapour (H2O), nitrogen (N2), oxygen (O2), carbon monoxide (CO), hydrogen (H2), siloxanes and hydrocarbons which are regarded as impurities or pollutants (Sun et al., 2015; Angelidaki et al., 2018). Some of these impurities have significant negative effects on the biogas utilisation system, such as calorific value reduction, corrosion, etc. (Sun et al., 2015). In order to reduce or remove these unwanted components that are harmful to the biogas utilisation systems and increase the biogas calorific value, it is important to clean or purify the raw biogas and upgrade it to a higher biofuel standard. The process is referred to as biogas cleaning or purification and upgrading (Sun et al., 2015; Angelidaki et al., 2018). Upgrading biogas to biomethane is one of the technologies that has attracted great interest in the bioenergy industry (Sun et al., 2015). When the biogas is purified or cleaned and upgraded to required specifications that are similar to natural gas, the final gas product is called biomethane (Kougias et al., 2017; Angelidaki et al., 2018).
A great number of biogas cleaning and upgrading technologies have been developed, and some of these technologies are commercially available (Sun et al., 2015). To this end, some recent researchers have presented a review of biogas cleaning/purification and upgrading technologies (Sun et al., 2015; Angelidaki et al., 2018; Ryckebosch et al., 2011; Bauer et al., 2013a; Muñoz et al., 2015; Kadam and Panwar, 2017; Struk et al., 2020; Domingues et al., 2021). In light of the constantly evolving biogas cleaning and upgrading technologies and market, it is important to conduct frequent assessments of the available technologies. While some literature reviews have been published exploring strategies to improve AD performance and increase biogas/biomethane yield, such as co-digestion, pretreatments, and adding additives, these publications are not comprehensive (Yadvika et al., 2004; Deepanraj et al., 2013; Romero-Güiza et al., 2016; Sarker et al., 2019; Kasinath et al., 2021). Therefore, a more thorough evaluation of the available strategies is necessary to ensure optimal performance of the AD process. Also, for different purposes of utilising biogas/biomethane, selecting the appropriate biomass pretreatment technique prior to biogas production and the appropriate biogas upgrading technology based on fundamental criteria is pertinent, rather than simply selecting the cheapest one without basic knowledge. If the cheapest technology is chosen and does not satisfy the biogas utilization requirements can result in serious damaging consequences, which may even destroy the system or result in a much higher total cost (Sun et al., 2015). Therefore, comprehensive information on the parameters or criteria for consideration in selecting the appropriate pretreatment technique for biomass prior to biogas/biomethane generation as well as the appropriate biogas upgrading technology required to satisfy biomethane quality is still limited.
The purpose of this paper is to provide a comprehensive review of recent advances in enhancing the production of biogas and biomethane. Additionally, this review discusses various biogas cleaning, purification, and upgrading technologies that are used globally and commercially. The intention is for this review to serve as a comprehensive guide for improving AD processes, selecting appropriate biomass pretreatment techniques, and choosing biogas upgrading technologies. One of the main contributions of this study is to provide guidance on selecting pretreatment techniques based on factors such as biomass hydrolysis rate, generation of toxic inhibitory compounds, operational cost, energy requirement, and effectiveness. Additionally, this review offers information on selecting biogas upgrading technologies based on investment cost, efficiency, maintenance cost, and other relevant criteria. Finally, this study includes information on the challenges faced by biogas upgrading technologies and recommended mitigation strategies.
1.1 Biogas and biomethane
Biogas is a non-polluting, clear combustible gas that is considered an alternative energy source (Umar et al., 2013). The physical properties of biogas are presented in Table 1.
It is an odourless and colourless gas that is flammable and smokeless (i.e., burns with blue flame). It has a specific gravity of 0.847–1.004, an ignition temperature between the range of 650°C–750°C, a calorific value of 4,740–7,500 kcal/Nm3, and an energy content of 37.3 MJ/m3 (Korbag et al., 2020). Biogas consists mainly of methane (CH4) and carbon dioxide (CO2), with traces of hydrogen sulphide (H2S), water vapour (H2O), ammonia (NH3), oxygen (O2) and nitrogen (N2) (Sun et al., 2015; Agbede et al., 2019; Hosseinipour and Mehrpooya, 2019; Struk et al., 2020; Domingues et al., 2021; Moya et al., 2022). It may sometimes contain very small quantities of siloxanes, aromatic and halogenated compounds (Ward et al., 2014). Table 2 presents the findings of various investigations conducted on the composition of typical biogas, which indicate that methane (CH4) constitutes between 45% and 75% of the biogas, and carbon dioxide (CO2) is present in a range of 25%–50% (Zhou et al., 2016; Angelidaki et al., 2018; Hosseinipour and Mehrpooya, 2019; Struk et al., 2020; Kasinath et al., 2021; Moya et al., 2022). Insignificant amounts of hydrogen sulphide (H2S) (<2% or 0–10000 ppm), ammonia (NH3) (<1% or 0–100 ppm), water vapour (H2O) (1%–10%), nitrogen (N2) (0%–15%), oxygen (O2) (0%–3%), and siloxanes (<0.02%) were also reported (Khan et al., 2017; Struk et al., 2020; Moya et al., 2022).
The biogas composition is intrinsically dependent on the carbon redox state of the waste’s organic matter, the origin and type of feedstock, and the type of AD process technology (Jönsson et al., 2003). The composition of the biogas revealed that CH4 is the most significant component, and thus the high content of CH4 in the biogas brought about the idea of biomethanation (anaerobic digestion of biodegradable organic wastes to produce biomethane), which is often used to describe the process of biogas production (Prakash and Singh, 2013).
Biomethane, which can be obtained from biogas by purification (i.e., cleaning) and upgrading (Sun et al., 2015), is a colourless and odourless gas that is not very soluble in water. It has a high energy content that ranges from 50 to 55 MJ/kg (Angelidaki et al., 2018; Tabatabaei et al., 2020; Mahmudul et al., 2021). In the last 5 years, the market for biomethane has grown exponentially (Moya et al., 2022). According to Moya et al. (Moya et al., 2022), the European Biogas Association (EBA) reported that in Europe, there were 483 existing active biomethane production plants in 2018 with a total production capacity of 22,787 GWh/year and that this number increased to 729 active plants at the end of the year 2020 (i.e., about 51% increase) with France and Germany being the major producers of biomethane. Figure 3 shows the overview of biogas/biomethane utilisation pathways.
The utilisation of biogas as fuel for various purposes is depicted in Figure 3. It can be used as fuel for both petrol (Supporting Material) and diesel (CI) engines and utilised as fuel for boilers, turbines, and internal combustion engines to generate electricity, heat, and steam. Furthermore, biogas is employed as a substitute for natural gas in domestic and industrial settings and as a feedstock in fuel cells (Andriani et al., 2014; Kadam and Panwar, 2017). In developing countries, biogas is mostly used for cooking and lighting purposes in stoves and lamps, respectively (Khan et al., 2017; Domingues et al., 2021). The storage of biogas in compressed cylinders and its transportation through pipelines can make it accessible in remote areas (Hosseinipour and Mehrpooya, 2019).
1.2 Strategies for AD process enhancement
Different strategies have been employed to enhance biogas and biomethane production during the AD processing of raw materials (Romero-Güiza et al., 2016), as schematically illustrated in Figure 4.
Figure 4 shows that the strategies include (i) use of pretreatments, (ii) use of co-digestion, (iii) bioaugmentation (use of inoculum or seeding bacteria), (iv) biostimulation (use of macro and micro nutrients), (v) use of carbon-based conductive materials and (vi) use of improved reactor configuration and operation conditions.
1.3 Use of pretreatment
Pretreatment, also referred to as the conditioning process, is any action performed on feedstock to weaken or overcome the recalcitrance attributed to its cell wall and structural characteristic (Andriani et al., 2014; Seidl and Goulart, 2016), thereby facilitating its solubilization and hydrolysis (Morales-Polo, 2018). Feedstock pretreatment is adapted based on the feedstock structure and characteristics (Kasinath et al., 2021). That is, feedstock such as lignocellulosic biomass and municipal solid waste that is composed of complex organic matter (cellulose, hemicellulose, and lignin) or refractory compounds that are not readily biodegradable or highly recalcitrant are considered for pretreatment before its utilisation in the AD process. The most recalcitrant component of the feedstock is lignin, which protects the cellulose and hemicelluloses by forming tight bonds, thereby reducing the available surface area for enzyme attack and consequently hindering the digestion or total breakdown (degradation) of the entire substrate structure (Paudel et al., 2017). Examples of feedstocks resistant or recalcitrant to microbial digestion are lignocellulosic feedstocks or biomass, such as energy crops and plant residues (Carlsson et al., 2012). Pretreatment is employed to facilitate or enhance microbial degradation or digestion (i.e., solubilisation and hydrolysis) of complex organic matter into simple components by removing the obstacles and making the organic content of the feedstock easily available and useable by the microbial populations (Patinvoh et al., 2017; Kasinath et al., 2021), as well as to enhance biogas and biomethane production and to improve dewatering and the digestate quality (Zhen et al., 2017; Kasinath et al., 2021).
Generally, pretreatment enhances the production of biomethane from the pretreated lignocellulosic feedstock or biomass in the 25%–120% range compared with the untreated feedstock (Mustafa et al., 2017; Rani et al., 2021). Biomass or feedstock pretreatment can shorten the duration of the hydrolysis stage (the rate-limiting step) of AD while at the same time accelerating soluble substances’ bioavailability for methanogenic bacterial enzymes (Kasinath et al., 2021). Pretreatment improves the feedstock accessibility to the microbial community by increasing biomass porosity, decrystallization, surface area and solubilisation (Carlsson et al., 2012). The efficiency of the feedstock pretreatment can directly be expressed based on the increase in the yield of biogas or biomethane or indirectly expressed based on the increase in the soluble components obtained (Kasinath et al., 2021). Pretreatment techniques or strategies as schematically represented in Figure 5 can broadly be classified as physical (mechanical, thermal (temperature induced and steam explosion), sonication, microwave irradiation), chemical (acidic, alkali, ozonation, Fenton and Fe(II)-activated persulfate oxidation), and biological (bacterial enzyme and fungi) (Montingelli et al., 2017; Kasinath et al., 2021).
1.3.1 Physical technique
The physical technique includes operations such as mechanical operations (milling, grinding, lysing, centrifuge, high-pressure homogeniser, and electroporation), thermal operations, sonication (ultrasound), and microwave irradiation (Deepanraj et al., 2013; Morales-Polo, 2018). The physical pretreatment technique of feedstock affects the cellulose crystallinity, degree of polymerization, particle size, surface area and pore size of the feedstock (Tsapekos et al., 2015; Khan et al., 2017).
1.3.1.1 Mechanical pretreatment
Mechanical pretreatment (e.g., milling/grinding) is based on increasing the feedstock contact surface area by disintegrating and reducing its particle size. The increased surface area will allow for better contact and interaction between the feedstock and the microbial community (Zhang et al., 2014; Morales-Polo, 2018). When there is sufficient particle size reduction, up to a 40% increase or improvement in biomethane yield can be achieved (Morales-Polo, 2018). The most common procedures in reducing particle size include screw presses, milling/grinding, and disc screening (Morales-Polo, 2018). Mechanical milling can be achieved using different mills such as attrition, ball, centrifugal, colloid, hammer, extruders, knife, pin, and vibratory mills (Cheng and Timilsina, 2011). With the use of mechanical milling, the degree of polymerization, particle size, and cellulose crystallinity is reduced, and thus the surface area and feedstock digestibility are enhanced. Mechanical pretreatment improves flow properties, bulk density, bioconversion effectiveness, particle densification and distribution, porosity and the overall lignocellulosic biomass conversion without any toxic by-products (Barakat et al., 2014). Mechanical pretreatment using screw press extrusion has been employed on dip litter manure (solid fraction and straw mixture) to achieve up to a 30% increment in methane yield (Hjorth et al., 2011), and Pilarski et al. (Pilarski et al., 2016) reported a 16.5% increase in the yield of methane after maize straw silage pretreatment using single screw extrusion as compared to the untreated control. Dell’Omo and Froscia (Dell’Omo and Froscia, 2018), using knife milling pretreatment on wheat straw, reported an increase in methane yield by 49.3% when compared with the untreated, while an increase in the yield of methane by 44.7% after ball milling pretreatment of grass as compared to the untreated was reported by Pengyu et al. (Pengyu et al., 2017). Also, Mӧnch-Tegeder et al. (M¨onch-Tegeder et al., 2014) reported a 26.5% enhancement in methane production when horse manure was pretreated using the mechanical pretreatment method compared to the untreated. In addition, Agyeman and Tao (Agyeman and Tao, 2014) gave a report of a 9%–34% of improvement in the yield of biogas when food waste was mechanically pretreated using the grinding method prior to its AD processing. It is to be noted that an excessive particle size reduction can result in hydrolysis overloading and subsequent accumulation of volatile fatty acids (Izumi et al., 2010).
1.3.1.2 Thermal pretreatment
Thermal pretreatment has to do with exposing the feedstock to temperature change over a duration of time. This can be subdivided into the following.
(a) Temperature-induced thermal pretreatment: This takes place at a vast temperature range of 70 °C–275 °C (Raju et al., 2013). However, during temperature-induced thermal pretreatment, temperature above 250 °C should be avoided and this is because, beyond 250 °C, pyrolysis reactions that are not wanted will begin to occur (Deepanraj et al., 2013). The thermal treatment enhances the hydrolysis of the feedstock leading to an increased rate and extent of AD. Temperature induced thermal pretreatment conducted on feedstocks such as food waste (Marañón et al., 2012), waste activated sludge (Bougrier et al., 2006), municipal solid waste (Ariunbaatar et al., 2014), algae (Schwede et al., 2013), agricultural byproducts (Menardo et al., 2012), and grass (Menardo et al., 2012) resulted in an increased yield of biomethane. Also, Carrère et al. (Carrère et al., 2009) performed a temperature induced thermal pretreatment on pig manure (total liquid and solid fractions) at a temperature of 190°C and reported an improved or enhanced yield of biogas, while Rafique et al. (Rafique et al., 2010) reported that there was no improvement in the yield of biomethane from a similar feedstock (solid fraction of pig manure) subjected to a pretreatment temperature of over 100 °C. According to Rafique et al. (Rafique et al., 2010), the yield of biogas and biomethane from temperature-induced thermal pretreated feedstocks is not always higher than those not subjected to pretreatment.
(b) Steam explosion: This is temperature and pressure induced, which is most commonly applied for the pretreatment of lignocellulosic biomass. The applied pressure can range from 5 to 50 bar, while the temperature can be in a range of 160°C–250°C (Zheng et al., 2014; Khan et al., 2017). In this method, the feedstock is put into a closed container or vessel and high temperature-pressure steam is directly passed into it for a few minutes or a short duration (Deepanraj et al., 2013). In the steam explosion, the pretreatment time is dependent on the feedstock moisture content (MC). If the MC is high, the optimum steam explosion pretreatment time will be long (Deepanraj et al., 2013). This pretreatment method is often defined using a severity factor. This factor is calculated from the time duration and temperature of the process, which is expressed in Eq. 1 (Amin et al., 2017):
where logRo = severity factor; T = temperature (◦C); t = residence time (min); and 14.75 = activation energy (follows first-order kinetics and is Arrhenius temperature dependent).
The steam explosion causes the lignocellulosic biomass fibres to open up, making them more accessible for degradation. According to Horn et al. (Horn et al., 2011) and Zhou et al. (Zhou et al., 2016), the yield of biogas from Salix woodchips and rice straw (lignocellulosic biomass) was maximised using a steam explosion method at 210 °C for 10 min and at 200 °C for 2 min duration, respectively. Also, Vivekanand et al. (Vivekanand et al., 2013) reported a two-fold increase in the yield of biomethane from birch wood chips when a steam explosion method at a temperature of 220 °C with a severity of 4.5 was employed. The steam explosion’s severity factor for most feedstocks usually falls within the range of 3.14–3.56 (Amin et al., 2017). Furthermore, Li et al. (Li et al., 2016), Lizasoain et al. (2017), Mulat et al. (Mulat et al., 2018), Steinbach et al. (Steinbach et al., 2019) and Weber et al. (2020) respectively reported that Miscanthus lutarioriparius, corn stover, Birchwood chips, rice straw and Agave bagasse feedstocks that were subjected to initial steam explosion pretreatment at 153–198°C, 140–220°C, 162–240°C and 142–179°C resulted in an increased yield of methane by 49%, 22%, 140% and 11% as compared to the untreated after undergoing anaerobic digestion process.
(c) Liquid hot water or hydrothermal pretreatment: This is also known as wet torrefaction (Alvarez-Chavez et al., 2020). In this case, liquid hot water is utilised in place of steam. The liquid hot water is obtained using heat combined with high pressure (Rodriguez et al., 2017; Rocamora et al., 2020). Generally, it is carried out at a temperature range of 100–140°C, together with a pressure range between 1 and 2 bar (Passos and Ferrer, 2015). However, in some cases, the pretreatment can be performed at a temperature range of 150°C–260°C (Chang et al., 2013). The hydrothermal pretreatment can be carried out in an autoclave (Passos and Ferrer, 2015) as well as in stainless kettles heated by an oil batch (Qiao et al., 2013). Its purpose is to selectively break down or degrade the hemicellulose of the substrate. That is, the hot water easily and readily solubilises the feedstock and prevents the formation of inhibitory compounds. In using this method, the pH level should be maintained at the range of 4–7 as this acts as a catalyst for the cellulosic raw material and helps minimise monosaccharide production (Hendrickson et al., 2011). Qiao et al. (Qiao et al., 2013) reported that after the hydrothermal pretreatment (170 °C for 1 h) of pig manure, municipal solid waste, cow manure and fruit/vegetable waste, the production of biogas respectively increased by 7.8%, 67.8%, 13.3% and 18.5%, while the methane yield increased by 14.6%, 65.8% and 16.1% for pig manure, municipal solid waste and fruit/vegetable waste, respectively and decreased by 6.9% for cow manure. Also, Passos and Ferrer (Passos and Ferrer, 2015) reported an increase in methane yield by 17%–39% after the hydrothermal pretreatment of microalgal biomass. Jiang et al. (Jiang et al., 2012), Panigrahi et al. (Panigrahi et al., 2019) and Shang et al. (Shang et al., 2019) respectively reported 31%, 10.8% and 62.9% increment in methane yield obtained from anaerobic digestion of giant reed, yard waste and wheat straw after their prior liquid hot water pretreatment.
(d) Freezing and thawing: This case entails subjecting the feedstock to sub-zero temperature (freezing) and, after that, recovering back its temperature (thawing). Elmashad (Elmashad, 2004) reported a 30% increase in the yield of biogas when cattle manure was pretreated using the freezing and thawing pretreatment method. Although this pretreatment method is adequate and feasible for food waste, it has not been widely used, mainly due to its high operational cost (Morales-Polo, 2018).
1.3.1.3 Microwave irradiation pretreatment
This method directly involves the application of the components of electric and magnetic field to the molecular structure of the feedstock components, eliciting biological, chemical and physical reactions as a result of the heat and extensive collisions by the ion movements and the polar molecules rotations or vibrations (Deepanraj et al., 2013; Peng et al., 2014). Microwave irradiation benefits include lignin depolymerisation, decreased cellulose crystallinity and polymerisation, increased feedstock surface area, and increased enzyme attack accessibility (Diaz et al., 2015; Deepanraj et al., 2017). Microwave irradiation can be used alone or in a combined form with various solvents such as acid, salt, water, alkali, ionic liquid and organic solvents. Carrerre et al. (Carrerre et al., 2016) reported an enhanced yield of biomethane (i.e., about 60% yield increase) from microalgae during its anaerobic digestion in a continuous reactor when the feedstock was subjected alone to microwave irradiation pretreatment. However, there are technical difficulties in applying this method on an industrial scale. Thus to date, its application is limited to the lab scale.
1.3.1.4 Sonication pretreatment
This entails the application of sound waves at high frequencies. In this method, high-intensity ultrasonic waves with a frequency equal to or greater than 20 kHz are applied, which by cavitation of bubbles generates huge hydro-mechanical shear force (Deepanraj et al., 2013). Ultrasound exposure can result in the thinning of the microbial cell walls, leading to the release of cytoplasm and consequently facilitating the solubilization and availability of both extracellular and intracellular matter for further degradation during the AD process (Sarker et al., 2019). In addition, sonication of high solid feedstocks causes disturbance to the acoustic waves’ homogeneity, high cavitation and increased dewaterability (Carrerre et al., 2016). The sonication method has been widely utilised for sewage or waste-activated sludge (Martin et al., 2013; Ormaechea et al., 2017), as this feedstock, when compared to other feedstocks, requires lower sonication energy and time. This is because past studies have shown that longer or higher sonication energy and time may lead to a lower efficiency of solubilised matter conversion into biomethane (Carrerre et al., 2016). The specific sonication energy threshold ranges from 1,000 to 16,000 kJ/kg TS (total solids). This is highly correlated to feedstock’s solid content (Carrerre et al., 2016). Carrère et al. (Carrère et al., 2010) reported that the biomethane potential (BMP) of waste activated sludge and cattle manure (5.8% total solids) was respectively improved by 140% and 19% when the individual feedstocks were pretreated using the sonication method. Also, it has been reported by Martín et al. (Martin et al., 2013) that the use of sonication (ultrasound) in the pretreatment of sewage sludge increased the yield of biomethane by 95%. This method could be suitable for a wide range of feedstock as it was found to be energetically feasible as the accrued benefit due to the earned revenue from higher production of biogas (35%–55%) overcompensated the investment cost on sonication (Pérez-Elvira et al., 2009).
1.3.1.5 Pressure-depressure (high-pressure homogenizer) pretreatment
Pressure-depressure or high-pressure homogenizer pretreatment involves subjection of the feedstock to high pressure of about 10 bar and thereafter depressurized (known as blasting) to approximately 1 bar. This sudden pressure drop causes strong turbulent eddies and shearing forces to occur, which break up or rupture the cell walls and structure (Morales-Polo, 2018; Mahmudul et al., 2021). Ma et al. (Ma et al., 2011) reported that food waste pretreated with the pressure-depressure treatment method resulted in up to a 35% increase in the yield of biogas.
1.3.2 Chemical technique
The chemical technique comprises the use of alkalis, acids, ammonia, peroxides, ozone and organic solvents (e.g., ethanol, tetrahydrofuran (THF) and N-Methyl morpholine-N-oxide (NMMO)) (Seidl and Goulart, 2016; Morales-Polo, 2018).
1.3.2.1 Acid pretreatment
This method is performed with the use of dilute or strong acids such as hydrochloric acid (HCl), nitric acid (HNO3), sulphuric acid (H2SO4), acetic acid (CH3COOH), maleic acid and phosphoric acid (H3PO4) (Khan et al., 2017). These acids accelerate the solubilisation of hemicellulose into oligomers and lignin removal (Sarker et al., 2019). Pretreatment with strong acids (30%–70%) is usually performed at a temperature that is less than 100°C, whereas pretreatment using dilute acids is done at a temperature range of 100–250°C (Khan et al., 2017). Dilute acids with concentrations less than 4% w/w are commonly used for acid pretreatment, because strong acids cause excessive substrate degradation leading to fermentable sugar loss as well as results in the production of unwanted byproducts like furfural and its derivatives that can greatly inhibit the AD process (Paudel et al., 2017). Biomass pretreated with dilute acids at high temperatures for a very short duration (e.g., 10–30 min) may have no positive effect on biogas or biomethane yield. However, there is a significant positive effect on the yield when the dilute acid pretreatment takes place for a higher duration, such as 1–2 h (Taherdanak et al., 2016). Zhang et al. (Zhang et al., 2011) reported that lignocellulosic waste subjected to acidic pretreatment using H2SO4 elicited a 57% increase in the yield of biomethane. Venturin et al. (Venturin et al., 2018) also reported that the use of acid pretreatment on corn stalks resulted in a 31.9% increment in the yield of biogas. Acidic pretreatment is usually not suitable for food waste as it leads to a decrease in the yield of biogas (Ma et al., 2011) due to inhibitor (carboxylic acids and phenolic compounds) accumulation at low pH (Yang et al., 2014). It has been suggested that inorganic acids have a more positive effect on biogas/biomethane yield (i.e., more effective) as compared to the use of organic acids (Mankar et al., 2021). For instance, Song et al. (Song et al., 2014) reported that sulfuric acid and hydrochloric acid exhibited a significant improvement or increase in methane yield compared with the use of acetic acid pretreatment, which resulted in a lower increase in the yield of methane.
1.3.2.2 Alkali pretreatment
This method also referred to as saponification, involves the use of sodium hydroxide (NaOH), calcium hydroxide (Ca(OH)2), ammonium hydroxide (NH4OH), and potassium hydroxide (KOH). These alkalis assist in the breakdown of lignin alongside hemicellulose solubilization (Carrerre et al., 2016; Norrrahim et al., 2021). It also helps to accelerate lipid-like feedstocks (Battimelli et al., 2010). The temperature of pretreatment, residence or reaction time and alkali concentration are the basic variables that affect or influence alkali pretreatment (Khan et al., 2017). Alkali pretreatment has demonstrated more effectiveness in enhancing the production of biogas and biomethane when compared with acid pretreatment (Carrerre et al., 2016; Ugwu and Enweremadu, 2019). The reason for this is that alkali provides a better condition for the AD process by preventing a drop in the pH (Li et al., 2012). Antonopoulou et al. (Antonopoulou et al., 2020) and Dasgupta and Chandel (Dasgupta and Chandel, 2020) respectively pretreated the grass lawn waste and the organic fraction of municipal solid waste using NaOH as an alkali pretreatment agent, and the results revealed that methane yield was correspondingly 25.7% and 34.8% higher when compared with the untreated during the anaerobic digestion processing. Rani et al. (Rani et al., 2021) also reported an enhanced biomethane production in the AD processing of wheat straw and animal manure when the wheat straw was pretreated with 10% Ca(OH)2 in comparison to the untreated wheat straw. The workers observed a lower biomethane yield when 15% Ca(OH)2 was used. The Alkali pretreatment method is still the most attractive and cost-effective method of removing lignin from lignocellulosic feedstocks (Seidl and Goulart, 2016).
1.3.2.3 Oxidation pretreatment
This involves the addition of oxidizing agents like H2O2 and peracetic acid (Deepanraj et al., 2013). However, this pretreatment could be either in the form of wet oxidation pretreatment or advanced wet explosion pretreatment (Khan et al., 2017). Wet oxidation pretreatment involves the addition of water to the biomass and then followed by the addition of an oxidizing agent. The pretreatment is exothermic and is often conducted at a higher temperature range of 125–300 °C and a higher pressure range of 0.5–20 MPa. Nevertheless, it can also be carried out at a lower temperature. The advanced wet explosion pretreatment is performed at a temperature range of 140–220 °C and a pressure range of 0–3.5 MPa. Thus, temperature, pressure, and residence time are the major parameters that influence the wet oxidation and advanced wet explosion pretreatment modes (Khan et al., 2017). The pertinent difference between wet oxidation and an advanced wet explosion is the use of a decompression unit in an advanced wet explosion where the pressure is reduced and results in biomass physical disruption, which has not been utilised in wet oxidation (Biswas et al., 2014). Oxidation pretreatment removes or solubilizes the hemicelluloses and decomposes the lignin and thus increasing the cellulose accessibility (Deepanraj et al., 2013; Ahring et al., 2015). Caution should be taken in the process of oxidation agents’ addition as this can form aromatic compounds that may serve as inhibitors for the AD process. Appels et al. (Appels et al., 2011) reported a 21% increase in biogas yield when waste-activated sludge was pretreated using peracetic acid as an oxidation agent prior to AD processing. Lee et al. (Lee et al., 2020) and Lee et al. (Lee et al., 2021) have both used the wet oxidation method to pretreat oil palm empty fruit bunches prior to anaerobic digestion, and they reported that the wet oxidation pretreatment resulted in 43% and 30% increment in methane yield during mesophilic and thermophilic anaerobic digestion, respectively. Biswas et al. (Biswas et al., 2014) and Ahring et al. (Ahring et al., 2015), using advanced wet explosion pretreatment for digested manure fibres and feedlot manure, showed that the pretreatment significantly and correspondingly enhanced the methane yield by 129% and 357%.
1.3.2.4 Ozone (ozonolysis) pretreatment
Ozonolysis or ozonation pretreatment involves the application of ozone, which is normally conducted at ambient or room temperature and pressure (Deepanraj et al., 2013; Khan et al., 2017). In this method, ozone reacts with the substrates and transforms them into smaller molecular-weight compounds leading to the rupturing of the cellular membrane such that the cell cytoplasm is spilled out (Cesaro and Belgiorno, 2014). If the dose of ozone is sufficiently high, it can lead to the mineralisation of the cellular compounds released (Cesaro and Belgiorno, 2014). The main parameters usually considered in this method, which affects its effectiveness, are ozone concentration in the gas flow, feedstock moisture content, and particle size (Khan et al., 2017). This pretreatment method can partly remove hemicellulose and effectively remove lignin (Taherzadeh and Karimi, 2008). This method does not leave toxic, basic and acidic residues (Deepanraj et al., 2013). Cesaro and Belgiorno (Cesaro and Belgiorno, 2014), using ozonolysis or ozonation pretreatment for organic solid waste before AD, reported that an ozone dose of 0.16 gO3/gTS improved the production of biogas by 37%.
1.3.3 Biological technique
The biological technique involves the use of biological agents such as enzymes and fungi. The biological technique shows several advantages in lignin removal from lignocellulosic raw materials; however, its low lignin removal efficiency places limitations on its practical application (Seidl and Goulart, 2016).
1.3.3.1 Bacterial enzyme pretreatment
Bacterial enzyme pretreatment involves the application of oxidative and hydrolytic enzymes, which are often produced by bacteria and fungi (Koupaie et al., 2019). For enzyme pretreatment, over forty enzymes have been tested (Koupaie et al., 2019). Among these enzymes, α-amylases, endoglucanase, β-glucosidase cellulases, xylanases, cellobiases, peroxidases, pectinases, proteases, and laccases are some of the enzymes that can be employed for pretreatment (Carrerre et al., 2016). The impact of the enzyme on the feedstock is dependent on the enzyme type and the composition of the feedstock being treated. This is due to the enzyme’s specificity in terms of the type of reaction it catalyses (Koupaie et al., 2019). The effectiveness and activities of the enzyme reaction are influenced by factors such as the substrate or feedstock composition, pH, incubation time, reactor configuration, and temperature (Parawira, 2012; Koupaie et al., 2019). Enzyme degradation of cellulose and lignin during various hydrolysis stages leads to the release or production of oligomers and several monomer sugars (Tanjore and Richard, 2015). According to Quiñones et al. (Quiñones et al., 2009), the pretreatment of solid cattle manure with enzymes prior to anaerobic digestion (AD) resulted in a significant improvement of approximately 105% in methane production. Lin et al. (Lin et al., 2017) found that pretreating pulp and paper sludge with endoglucanase and laccase enzymes before subjecting it to mesophilic anaerobic digestion (AD) led to a significant improvement of 34% in methane production. Similarly, Frigon et al. (Frigon et al., 2012) observed a 29% and 42% increase in methane production when using lignin peroxidase and manganese peroxidase enzymes, respectively, for the enzyme pretreatment of switchgrass.
A variety of enzyme pretreatment approaches have been explored in the literature. Koupiae et al. (Koupaie et al., 2019) have conducted a comprehensive review of this method, demonstrating the impact of over forty enzymes. Their review highlights the potential of this pretreatment method for enhancing biomethane production through mesophilic and thermophilic anaerobic digestion (AD) of lignocellulosic biomass. However, the authors note that further research is needed to better understand the relationship between lignocellulosic substrate composition, enzyme or bacterial type, and optimal pretreatment conditions. The benefits of this pretreatment method include its relatively short reaction time, low nutritional requirements for enzymatic reactions, and the fact that most enzymes are unaffected by other microbial metabolisms and inhibitors (Wei, 2016), as well as not requiring expensive processing equipment (Ometto et al., 2014). However, the major limitations of enzyme pretreatment, which restrict its application, are the high cost of enzymes and their selectivity (Sarker et al., 2019). This highlights the need for further research in the context of AD process optimisation.
1.3.3.2 Fungal pretreatment
The enzymes used for AD processes are usually produced from different forms of fungi like Aspergillus and Trichoderma genus (Schimpf et al., 2013). Therefore, instead of producing the enzymes from these fungi, the fungi can be directly used as an alternative so that the cost of enzyme production can be totally avoided (Sarker et al., 2019). In addition, these fungi, combined with an auxiliary enzyme such as Lytic polysaccharide mono-oxygenases (LPMO), can be employed to enhance cellulose degradation (Dollhofer et al., 2015). Various fungi, such as soft-rot fungi, white-rot fungi, and brown-rot fungi, are commonly used for lignin and hemicellulose degradations in the feedstock (Deepanraj et al., 2013; Khan et al., 2017; Wagner et al., 2018). Soft and white rot fungi are mainly used to attack lignin and cellulose, while brown-rot fungi are mainly used for cellulose degradation (Deepanraj et al., 2013; Wagner et al., 2018). Muller and Trosch (Muller and Trosch, 1986) biologically pretreated wheat straw using white-rot fungi and reported a double-fold increase in the yield of biogas to the untreated wheat straw.
In addition, Srilatha et al. (Srilatha et al., 1995) reported an increase in the production of biogas when an orange processing waste was biologically pretreated using Aspergillus, Sporotrichum, Penicillium and Fusarium. Ghosh and Bhattacharyya (Ghosh and Bhattacharyya, 1999) reported that using brown rot and white rot fungi to respectively pre-treat bamboo prior to AD operation resulted in the yield of biomethane respectively, increasing by 32% and 46%. Mackuľak et al. (Mackuľak et al., 2012) reported a 15% enhancement in methane yield during anaerobic digestion of hay and leaves that were subjected to prior fungal pretreatment using Auricularia auricula-judan. Ali et al. (Ali et al., 2014) reported that the fungal pretreatment of water hyacinth and maize cob heart using Volveriella diplasia and Phanerochaete chrysosporium prior to AD processing resulted in an increased yield of biogas at short hydraulic retention time in comparison with the untreated feedstocks. Furthermore, it was reported by Rouches et al. (Rouches et al., 2016) that fungal pretreatment of wheat straw using Polyporus brumalis resulted in an increase of biomethane yield by 45%. On the other hand, it was observed and reported by Paul et al. (2018) that fungal pretreatment of agricultural biomass did not improve biomethane yield. This observed variation is expected as the biological pretreatment technique is still being developed.
1.3.4 Combined or hybrid technique
Any two or three of the physical, chemical and biological techniques of pretreatment can be combined to increase the biogas and biomethane yield as well as lower energy consumption and minimise cost (Shirkavand et al., 2016; Khan et al., 2017; Kumar et al., 2017). For example, physical pretreatment techniques can be combined with chemical pretreatment techniques such as thermo-chemical (i.e., combination of thermal and chemical pretreatments) and Chemo-sonication (combined ultrasonication and chemical). Also, physical pretreatment techniques can be combined with biological pretreatment techniques such as bio-mechanical (i.e., combination of biological and mechanical pretreatments), while physical, chemical and biological pretreatment techniques can be combined together. To this end, different researchers have utilised these combined or hybrid pretreatment methods and have reported positive results (Shirkavand et al., 2016; Khan et al., 2017; Passos et al., 2017).
1.3.4.1 Thermo-chemical pretreatment
The combination of heat (thermal) and chemicals can also be applied as a pretreatment strategy. This method helps to contribute to the enhancement of AD productivity by reducing the particle size of the feedstock (Izumi et al., 2010), increasing the volatile solid reduction (Mladenovska et al., 2006) and increasing the solubility of the chemical oxygen demand (COD) (Valo et al., 2004). The chemicals that are predominantly utilised for thermo-chemical pretreatment are alkali (Lin et al., 2009), acids (Devlin et al., 2011), and ozone (Bougrier et al., 2006). Shehu et al. (Shehu et al., 2012) reported a 36% increase in biogas production when sewage sludge was previously subjected to thermo-alkaline pretreatment using 2.29 M NaOH and 88.50 °C. Also, Passos and Ferrer (Passos and Ferrer, 2015), using the thermal-alkali pretreatment method (10% NaOH at 100 °C for 5 min) on dairy cow manure feedstock, reported a 23.6% enhancement in methane production when compared with the untreated. The use of microwave irradiation in combination with solvent can result in the rapid hydrolysis of more sugars in the lignocellulosic biomass (Saha et al., 2008) and remove or degrade more hemicellulose and lignin compositions of the lignocellulosic feedstock (Zhu et al., 2006) when compared to the conventional thermal treatment. Kaur and Phutela (Kaur and Phutela, 2016) reported that paddy straw subjected to thermochemical pretreatment using the combination of microwave and sodium hydroxide resulted in 55% increment in methane yield as compared to the untreated control.
1.3.4.2 Electro-chemical pretreatment
The electrochemical technique includes electro-oxidation, electro-deposition, electro-coagulation, and electro-flotation. Yu et al. (Yu et al., 2014) reported a 63.4% increase in biogas yield after the electrochemical pretreatment of waste activated sludge using a pair of Ti/RuO2 mesh plates as electrodes. Kumar et al. (Kumar et al., 2017) reported an improved methane yield during anaerobic digestion when mixed microalgae biomass was subjected to initial pretreatment using the combination of electrolysis and ultrasonic pretreatment.
1.3.4.3 Chemo-sonication pretreatment
This is the combination of chemical and sonication (ultrasound), which can be employed as a pretreatment method. Wang et al. (Wang et al., 2012) reported an increase in the production of biogas by 67%–76% after the chemo-sonication pretreatment of rice stalks using 2% NaOH and ultrasonication frequency of 30 kHz for 1 h.
1.3.4.4 Thermo-sonication pretreatment
This involves the combination of thermal and sonication. Dhar et al. (Dhar et al., 2012) reported that the thermo-sonication pretreatment of waste-activated sludge using a temperature range of 50–90°C and sonication energy range of 1,000–10,000 kJ/kg TSS resulted in 30% increment in the production of methane and 29%–38% reduction in volatile solids.
1.3.4.5 Bio-mechanical pretreatment
In this case, it is the combination of biological and mechanical techniques utilised as pretreatment method. The combination of mechanical milling with fungal pretreatment can also be utilised to achieve enhanced biomethane yield (Mustafa et al., 2017). Pérez-Rodríguez et al. (Pérez-Rodríguez et al., 2017), using the combination of extrusion and enzymatic pretreatment for pretreating corn cob, reported a higher production of methane when compared with the untreated corn cob.
1.3.4.6 Mechanical-sonication pretreatment
This is the combination of mechanical and sonication pretreatment methods. Elbeshbisy and Nakhla (Elbeshbishy and Nakhla, 2011) and Cesaro et al. (Cesaro et al., 2012) obtained about 94% increase in the yield of both biogas and biomethane when FW was previously subjected to the combination of grinding (i.e., mechanical) and sonication pretreatment methods.
1.3.4.7 Bio-physico-chemical pretreatment
This involves the combination of biological, physical and chemical pretreatment techniques. Peng et al. (Peng et al., 2014) reported a 280% increase in the production of biogas from oily wastewater when it was previously pretreated using a bio-physico-chemical pretreatment method (Bacillus, sonication and acid).
1.3.5 Evaluation of pretreatment efficiency in biogas production: Energy cost as a criteria
The main purpose or goal of AD is biogas/biomethane or energy production. Evaluation of the efficiency of different biomass or lignocellulosic biomass pretreatments methods can be based on the operational energy costs that are associated with the different pretreatment methods (Ruggeri et al., 2015). These costs can be determined based on the direct energy (heat and electricity) consumed during each process and the indirect energy involved during the pretreatment. To this end, two energy parameters can be utilised to grade the pretreatment methods (Ruggeri et al., 2013a). The first parameter is the energy conversion efficiency (
1.3.5.1 Energy conversion efficiency
The energy conversion efficiency (
Where Ep stands for the total energy produced as biogas or biomethane (kJ/L) and E0 depicts the initial available energy contained in the feedstock or biomass (kJ/L). The total energy produced (Ep) in terms of biomethane can be obtained using Eq. 3:
Where Gmax represents the total biomethane volume (NL/L) produced at 1 atm and absolute temperature (0 °C), which is based on the mean biomethane concentration in biogas; 22.4 is the equivalent molar volume (L/mol); and LHVCH4 represents the biomethane’s Low Heat Value (LHV = 800.32 kJ/mol). In the calculation of E0, it is only the energy within the feedstock or biomass waste that the microorganisms can utilize for cellular activity that should be considered (Nelson et al., 2008; Ruggeri et al., 2015), however, this task is difficult. Nevertheless, for the purpose of scoring or ranking the different pretreatment outcomes performed on the feedstock, a good approximation of E0 could be achieved utilizing the feedstock’s LHV. The E0 can be estimated using Eq. 4:
Where LHVFS (kJ/kg) stands for the low heat value of feedstock and TS0 for the initial total solid concentration (g/L) present in the medium. It is essential to note that the inherent energy within the feedstock is not all available for biomethane production. It is only a portion of this inherent energy that can be harvested or obtained as biomethane using AD technology, while a fraction of this energy is released as heat, a fraction is utilized during biological metabolism, a fraction is embedded within the metabolites produced during the AD reaction, and a fraction is stored within the newly divided microbial cells. It is to be noted that not all carbon-carbon (C–C) or carbon-hydrogen (C–H) bonds present in feedstock or biomass wastes are of the same type and only the bonds of simple molecules such as glucose that can easily be degraded by microorganisms. The second parameter evaluated was the efficacy (
Where
1.3.5.2 Energy sustainability index
It is pertinent to verify the energy sustainability of AD technology by comparison of the energy produced in the form of biogas or biomethane with the energy spent or consumed during the AD process. This can be carried out by employing ESI. The ESI can be utilized to evaluate which feedstock pretreatments or biogas upgrade technologies could be most effectively coupled with AD in order to select the most energetically effective techniques of processing the feedstock. The ESI is presented as given in Eq. 6:
Where EAD represents the energy obtained as biogas or biomethane during AD ETC., represents the total energy consumed or spent on the pretreatment or biogas upgrade. When the value of ESI is greater than one (1), it signifies an increased energy production and the possibility of an energetically sustainable process (Ruggeri et al., 2013b) and when ESI value is less than one (1), it indicates that the process is not energetically sustainable, even when there is an increased energy production (i.e.,
Where EH, EEE, and EIE represents heat energy, electrical energy and indirect energy, respectively.
The heat energy can be calculated using Eq. 8:
Where ρ depicts the mass of feedstock present per unit reactor or digester working volume; Cp stands for the specific heat value; T1 represents the ambient temperature and T2 represents the working temperature. The EEE value can be obtained by multiplication of the equipment power with the duration time utilized for the pretreatment or biogas upgrade as the case may be. The EIE being the energy spent or used to produce materials like chemicals (NaOH, H2SO4, HCl and salts) can be evaluated as Global Energy Requirements (GER; kJ/kg) by employing data from the Ecoinvent (2010) database (Frischknecht and Jungbluth, 2010). Hence, EIE values can be gotten by multiplication of the specific GER with the quantity of materials utilized for the pretreatment or biogas upgrade. Ruggeri et al. (2015) employing the energy conversion efficiency and energy sustainability index criteria, evaluated the effects of different pretreatments on energy produced as methane during the AD of olive mill wastewaters (OMWW) and olive pomace (OP). The different pretreatment methods that were evaluated included, basic pretreatment (BP); physical pretreatment using ultrasound (USP); salt pretreatment using FeSO4 (SPFeII), FeCl3 (SPFeIII), MnSO4 (SPMn) and CaCO3 (SPCa); and double combinations of the pretreatments, such as ultrasound plus FCl3 (CPFeIII) or ultrasound plus CaCO3 (CPCa). Ruggeri et al. (2015) observed and reported that for the goal of methane production, the pretreatments that were most effective included salt pretreatment using CaCO3 or FeCl3 addition and ultrasonic pretreatment. The ultrasonic pretreatment had the highest efficacy of (Cesaro and Belgiorno, 2013). However, from the energetic point of view, the ultrasonic pretreatment was found to have an ESI value of 0.09, suggesting that the energy gotten as methane during the AD after the pretreatment is not enough to cover the energy utilized or spent on ultrasonic pretreatment despite its high efficacy. Amongst these three most efficient pretreatment methods, the salt pretreatment method using CaCO3 was found to be the only method with the highest ESI value of 14, suggesting its capability to result in a positive net energy balance between energy recovered and energy utilized or spent.
1.3.6 Comparison of pretreatment techniques
Comparisons of the pretreatment techniques based on five essential criteria (rate of hydrolysis, toxic inhibitory compounds generation, operational cost, energy requirement, and effectiveness) are presented in Table 3.

TABLE 3. Comparison of pretreatment techniques (Sibiya et al., 2018).
1.3.6.1 Hydrolysis rate
From Table 3, among the pretreatment techniques, it is seen that physical techniques suggest to be the fastest. This is more so for microwave (MW) pretreatment (Wu et al., 2015b; Kumar and Sharma, 2017). This is in agreement with Yuan et al. (2014), who posited that short duration time is an advantage of mechanical pretreatment. Conversely, Gumisiriza et al. (2017) reported slow irradiation processes. There are contrasting reports on the effect of chemical pretreatment techniques on the rate of feedstock hydrolysis during AD process. Yuan et al. (2014) and Li et al. (2015) have reported that the chemical pretreatment technique is a fast process, while Kumar and Sharma (2017), Gumisiriza et al. (2017) and Amin et al. (2017) reported that the technique is a slow process. This difference could be due to variations in their chemical pretreatment conditions. For instance, chemical pretreatment’s retention time is affected by the temperature of the reaction (Theuretzbacher et al., 2015; Kamusoko et al., 2019). Data on combined methods is rather limited. As presented in Table 3, the major challenge of biological pretreatment is that it is a slow process (Kumar and Sharma, 2017; Gumisiriza et al., 2017; Amin et al., 2017; Wagner et al., 2018; Den et al., 2018; Kamusoko et al., 2019). Combined or hybrid pretreatment technique has been reported to be a fast process (Kim et al., 2018; Kamusoko et al., 2019).
1.3.6.2 Energy requirement
Table 3 revealed that biological pretreatment techniques demonstrated low energy requirements or cost among the pretreatment techniques. Several studies have indicated that the major merit of biological pretreatment is the possession of low energy cost or requirement (Singh et al., 2014; Zieminski and Kowalska-Wentel, 2017; Kumar and Sharma, 2017; Gumisiriza et al., 2017; Wagner et al., 2018; Den et al., 2018). Biological pretreatment enables savings on chemicals and energy. The physical pretreatment technique has been reported to be a high-energy requirement process (Table 3). That is, the technique is highly energy intensive given the involvement of high temperatures and pressures as in the case of thermal treatment (Mulakhudair et al., 2016; Speda et al., 2017; Gumisiriza et al., 2017; Wagner et al., 2018; Kamusoko et al., 2019). For example, mechanical pretreatment, such as milling, has a high energy requirement (Yuan et al., 2014; Luo et al., 2015; Chandra et al., 2015; Kumar and Sharma, 2017; Baruah et al., 2018). Also, microwave irradiation pretreatment has the challenge of high energy costs (Kostas et al., 2017). In contrast, Wu et al. (2015b), Kumar and Sharma (2017), Kostas et al. (2017), and Kamusoko et al. (2019) reported that the physical pretreatment technique with respect to microwave pretreatment is energy efficient. Nevertheless, due to the reason of high energy requirement, the physical pretreatment technique is considered to be economically not viable for large industrial-scale applications (Zheng et al., 2014; Kamusoko et al., 2019). Furthermore, the chemical pretreatment technique is considered a high-energy cost process (Table 3). This has been reported in several studies (Wikandari et al., 2015; Speda et al., 2017; Rouches et al., 2017; Gumisiriza et al., 2017; Wagner et al., 2018). Combined or hybrid pretreatment technique as seen in Table 3 has been reported to be a high energy-demanding process (Speda et al., 2017; Gumisiriza et al., 2017; Perendeci et al., 2018). On the other hand, Kumar and Sharma (2017), Zhang et al. (2018), and Kim et al. (2018) reported combined or hybrid pretreatment techniques to be a low energy-demanding process. This observed variation may be due to combined or hybrid pretreatment technique complexity; thus, further research will be required.
1.3.6.3 Effectiveness in biogas/biomethane enhancement
Table 3 depicts that among the pretreatment techniques, the chemical pretreatment technique suggest to be the most effective technique. Chemical pretreatment technique in terms of acid, alkali, oxidation and ozonolysis pretreatments has been reported to be a very effective technique for biogas/biomethane yield enhancement (Appels et al., 2011; Zhang et al., 2011; Biswas et al., 2014; Cesaro and Belgiorno, 2014; Ahring et al., 2015; Venturin et al., 2018; Antonopoulou et al., 2020; Dasgupta and Chandel, 2020; Lee et al., 2020). Physical pretreatment technique with respect to mechanical (milling), thermal (temperature-induced, steam explosion, liquid hot water), microwave irradiation, sonication and high-pressure homogenizer pretreatments have also been observed and reported to be moderately effective in the increase of biogas/biomethane yield (Hjorth et al., 2011; Pilarski et al., 2016; Dell’Omo and Froscia, 2018; Pengyu et al., 2017; M¨onch-Tegeder et al., 2014; Marañón et al., 2012; Bougrier et al., 2006; Ariunbaatar et al., 2014; Schwede et al., 2013; Menardo et al., 2012; Horn et al., 2011; Li et al., 2016; Lizasoain et al., 2017; Mulat et al., 2018; Steinbach et al., 2019; Weber et al., 2020; Passos and Ferrer, 2015; Qiao et al., 2013; Jiang et al., 2012; Panigrahi et al., 2019; Shang et al., 2019; Carrerre et al., 2016; Martin et al., 2013; Carrère et al., 2010; Ma et al., 2011). Table 3 information show that the biological pretreatment technique in terms of enzyme and fungal pretreatments has been reported to be effective in enhancing biogas/biomethane yield as the other techniques (Muller and Trosch, 1986; Srilatha et al., 1995; Ghosh and Bhattacharyya, 1999; Quiñones et al., 2009; Mackuľak et al., 2012; Ali et al., 2014; Tanjore and Richard, 2015; Rouches et al., 2016; Lin et al., 2017). However, fungal pretreatment has been reported to be less effective in comparison with other pretreatment techniques (Kamusoko et al., 2019). Combined or hybrid pretreatment technique with respect to thermo-chemical, electro-chemical, chemo-sonication, thermo-sonication, bio-mechanical, mechanical-sonication and bio-physico-chemical pretreatments has been found and reported to be effective in the enhancement of biogas/biomethane production (Elbeshbishy and Nakhla, 2011; Cesaro et al., 2012; Dhar et al., 2012; Shehu et al., 2012; Wang et al., 2012; Peng et al., 2014; Yu et al., 2014; Passos and Ferrer, 2015; Kaur and Phutela, 2016; Kumar et al., 2017; Pérez-Rodríguez et al., 2017).
1.3.6.4 Operational cost
Table 3 data compares the different pretreatment techniques in terms of operational cost. Despite the report that the biological pretreatment technique in terms of fungal pretreatment is less effective, fungal pretreatment is considered to be cost-effective in terms of operational cost (Rouches et al., 2017). Biological pretreatment techniques have been reported not to be expensive (Mulakhudair et al., 2016; Gumisiriza et al., 2017; Wagner et al., 2018; Den et al., 2018). This is due to the fact that fungi helps to lessen the pretreatment steps and costs by avoidance of the enzyme recovery step (Carrerre et al., 2016). It has been reported that enzyme pretreatment possesses low enzyme utility costs due to the utilisation of mild conditions (Kudanga and Le Roes-Hill, 2014). On the contrary, the biological pretreatment technique in terms of enzyme pretreatment using commercial enzymes has been reported to be costly with respect to production cost (Mulakhudair et al., 2016; Kamusoko et al., 2019). It is noted, according to the information in Table 3, that physical and chemical pretreatment techniques are predominantly very expensive. Selected works or studies from the literature revealed that physical or chemical pretreatment techniques are expensive and thus not economically applicable for biogas/biomethane generation from agricultural biomass (Kamusoko et al., 2019). Physical pretreatment techniques are more expensive because of higher capital and energy costs (Sadhukhan et al., 2018). Mechanical pretreatment (such as milling and grinding), microwave irradiation pretreatment, and sonication (ultrasonic) pretreatment have high equipment maintenance and energy costs (Kumar and Sharma, 2017; Amin et al., 2017; Ismail et al., 2017; Gumisiriza et al., 2017; Kamusoko et al., 2019). Also, the reasons for chemical pretreatment techniques’ expensive status were observed to be due to the followings; (i) use of expensive auxiliary equipment (Speda et al., 2017; Kamusoko et al., 2019), (ii) utilization of chemicals and downstream processing that incurs high cost (Sträuber et al., 2015; Kumar and Sharma, 2017; Amin et al., 2017; Sadhukhan et al., 2018; Den et al., 2018), (iii) high operational and maintenance costs (Rouches et al., 2017), and (iv) high costs of digestion residues’ disposal (Wagner et al., 2018). Nevertheless, some studies have reported that chemical pretreatment technique with regard to alkali pretreatment is not expensive (Song et al., 2014; Kumar and Sharma, 2017; Amin et al., 2017; Ismail et al., 2017; Gumisiriza et al., 2017). Thus, alkali pretreatment will be favoured over the other chemical pretreatment techniques as a result of low operational costs (Ismail et al., 2017). Combined or hybrid pretreatment techniques would be influenced or affected by the associated costs of the other pretreatment techniques.
1.3.6.5 Generation of inhibitory compounds
Table 3 provides information on the comparison of the pretreatment techniques with regard to the generation of inhibitory compounds. Table 3 information reveals that physical pretreatment techniques generally result in the generation of inhibitory compounds. For example, thermal pretreatment at a temperature that is above 160 °C could result in partial degradation of lignin and polysaccharides to generate heterocyclic and phenolic compounds (Zieminski and Kowalska-Wentel, 2017). However, some other studies show that mechanical pretreatment, such as milling, do not produce inhibitory compounds (Baeta et al., 2016; Kumar and Sharma, 2017). It is presented in Table 3 that chemical pretreatment techniques with respect to acid and alkali pretreatments generate inhibitory compounds, while chemical pretreatment techniques with regard to oxidation and ozonolysis pretreatments do not generate inhibitory compounds. There are about eleven research studies in the literature that reported that chemical pretreatment techniques lead to the generation of toxic inhibitory compounds (Pei et al., 2014; Kudanga and Le Roes-Hill, 2014; Amin et al., 2017; Speda et al., 2017; Eskicioglu et al., 2017; Rouches et al., 2017; Kumar and Sharma, 2017; Gumisiriza et al., 2017; Nair et al., 2018; Den et al., 2018; Paul et al., 2018). Thus, inhibitory compounds generation is one of the challenges or demerits of chemical pretreatment techniques. Meanwhile, there are some chemical pretreatment techniques that do not generate inhibitory compounds (Sahito and Mahar, 2014; Gumisiriza et al., 2017; Paul et al., 2018; Den et al., 2018). Furthermore, biological pretreatment techniques concerning enzyme and fungal pretreatments do not result in the formation of inhibitory compounds (Singh et al., 2014; Amin et al., 2017; Wagner et al., 2018), as presented in Table 3. This is one of the positive attributes or advantages of biological pretreatment techniques. Table 3 also shows that combined or hybrid pretreatment techniques lead to inhibitory toxic compound generation. There are seven research works in the literature that have shown that combined or hybrid pretreatment techniques lead to the formation of inhibitory compounds (Speda et al., 2017; Amin et al., 2017; Gumisiriza et al., 2017; Eskicioglu et al., 2017; Kumar and Sharma, 2017; Zhang et al., 2018).
1.4 Summary of comparison
Therefore, in summary, biological pretreatment techniques possessed more techno-economic merits across the five criteria compared to other pretreatment techniques. The merits of biological pretreatment techniques are associated with the capacity to prevent the generation of by-products that are inhibitory and toxic to methanogens, low operation cost, and low energy requirement. Nevertheless, there is a need to improve the biological pretreatment techniques’ efficacy, and the main focus should be the rate of hydrolysis enhancement. In order to enhance or improve on the rate of hydrolysis, it is therefore recommended that parameters such as type of microorganisms and enzymes involved, pH, incubation temperature, incubation time, moisture content, inoculum concentration, aeration rate, and nature and composition of biomass should be optimised. Despite the high effectiveness of both physical and chemical pretreatment techniques, their major limitations or challenges are high energy requirements and cost.
1.5 Use of additives
Different additives have been employed to enhance biogas and biomethane production during the AD processing of raw materials (Romero-Güiza et al., 2016) as schematically represented in Figure 6. These additives include (i) biological additives, (ii) inorganic additives, (iii) bioaugmentation (use of inoculum or seeding bacteria), (iv) biostimulation (use of macro and micro nutrients), (v) use of adsorbent and (vi) use of co-digestion.
1.5.1 Biological additives
1.5.1.1 Bioaugmentation: Use of inoculum or use of seeding bacteria or starter bacteria
The inoculum-to-substrate (feedstock) ratio (I:S or I:F) or substrate (feedstock) to inoculum ratio (S:I or F:I) is one of the key parameters of AD. AD is a process that is performed by microorganisms. Hence there is a basic correlation that exists between the composition of the microbial community and the AD systems’ behaviour (Kim et al., 2014; Mata-Alvarez et al., 2014). That is AD or biomethanation results from the interaction of various groups of microorganisms and substrates, which result in methane production. These microbes exist in nature and enter the reactor with the feeding of raw materials (Christy et al., 2013). If the fresh raw material enters the digester with only a few starting-bacteria, the fermentation period will be long, and the AD process will be slow (Palatsi et al., 2011). This is so because higher biogas and biomethane production requires a large amount of starting bacteria (Comparetti et al., 2013). Thus, the startup of the AD process has clearly been identified as the most crucial AD phase (Romero-Güiza et al., 2014) because, during this period, a proper microbial community is yet to be established. For this purpose, bioaugmentation is applied to manipulate and enhance the microbial community during the initial stages of AD such that the AD process performance can be improved or enhanced (Dhadse et al., 2012; St-Pierre and Wright, 2013). That is, the loading of inoculum or seeding bacteria (bioaugmentation) into the biodigester or bioreactor at the start of the AD process is a means of accelerating or enhancing the start-up period as well as an effective way of providing the significant microbial population to the feedstock (substrate) (Di Maria et al., 2013).
Although the introduction or addition of inoculum reduces the space available for AD, it helps control the retention time by shortening the retention and total reaction time and improving or increasing biogas and biomethane yield (Rocamora et al., 2020) and reducing and reducing the problem of ammonia inhibition (Yang et al., 2022). On the other hand, reducing or decreasing the quantity of start-up inoculum increases the AD process capacity, but it will lead to longer retention and total reaction times as well as a reduction in the yield of biogas and biomethane (Rocamora et al., 2020). The materials that can be utilised as inoculum include pre-rotted raw material, digestate obtained from a previous AD, wastewater from sewage sludge (Yadvika et al., 2004; Karthikeyan and Visvanathan, 2013), chicken-gizzard rumen (Aworanti et al., 2017a) and well-constructed bacteria consortia (Yang et al., 2022). Bioaugmentation is also applied as a response to stress conditions or when microbial community shift occurs during transitional phases (Ács et al., 2013) to increase AD performance or recover the system’s efficiency (Kim et al., 2013). Bioaugmentation should be undertaken by selecting the appropriate inoculum and dosage based on the specific microbial community diversities present within the bioreactor/biodigester (Romero-Güiza et al., 2016). Microbial cultures immobilised on a support matrix (i.e., immobilised biofilm or microbial culture) can also be utilised for bioaugmentation. That is, bioaugmentation success can further be improved by the use of immobilized microbial cultures (Youngsukkasem et al., 2011).
1.5.1.2 Use of co-digestion/co-fermentation of different substrates
The anaerobic mono-digestion process is faced with the challenges of a slow start-up, relatively long or high retention time (about 20–50 days) and overall low degradation efficiency (about 20%–50%) (Shehu et al., 2012; Chen X. et al., 2014). Therefore, there is a need to enhance or improve the overall AD process efficiency in the biogas and biomethane digesters. This enhancement or improvement can be achieved through the application of anaerobic co-digestion (AnCo-D). AnCo-D can be defined as the biotreatment of a mixture of at least two different feedstock or substrates anaerobically (Neczaj et al., 2012). AnCo-D of different feedstock or biomass wastes has been reported to give better performance or improve or enhance the cumulative biogas and biomethane yield than mono-digestion of separate feedstock (Umar et al., 2013; Hassan, 2014; Ogunleye et al., 2016; Haosagul et al., 2019; Liew et al., 2021; Rani et al., 2022). Co-digestion also improves the chances of the process of handling substrates containing toxic (poisonous) components. Thus, AnCo-D offers many benefits over mono-digestion of separate or individual feedstock, which are, increased substrate or feedstock biodegradation, increased biogas and biomethane production and increased cost-efficiency (Neczaj et al., 2012). In addition, co-digestion can bring about C: N ratio adjustment or enhancement together with improved pH buffering (Zhang et al., 2016; Sarker et al., 2019) as well as the improvement of the overall macronutrients balance by proportionally adjusting the carbon, sulphur, phosphorous and nitrogen content (Sarker et al., 2019). Therefore, a variety of substrates is desirable, as it increases the likelihood of a stable and robust process. There are a lot of reports in the literature dealing with the use of co-digestion or co-substrate fermentation making use of different feedstock or substrates as co-substrates. For example, the use of sewage sludge co-digested with other substrates like agriculture wastes (Rughoonundun et al., 2012), municipal solid waste (Lebiocka and Piotrowicz, 2012), cattle manure (Hassan, 2014) and chicken manure (Mahmoud et al., 2022) the use of animal wastes (cattle manure/dung, cow dung, pig/swine manure, chicken dung) co-digested with other substrates such as food waste, fruit waste, vegetable waste, grass clippings, municipal sewage sludge, wheat straw, oil palm fronds, sorghum stem and banana peels (Ossai, 2013; Prakash and Singh, 2013; Latinwo and Agarry, 2015; Matheri, 2016; Zhang et al., 2016; Aworanti et al., 2017a; Achinas et al., 2019; Ahlberg-Eliasson and Westerholm, 2021; Rani et al., 2021; Rani et al., 2022). Co-digestion of many other substrates has been documented in a comprehensive review by Poulsen et al. (Poulsen and Adelard, 2016).
1.5.2 Inorganic additives
1.5.2.1 Biostimulation: Addition of macro and micro-nutrients (trace metals)
The addition of certain metals like Ca2+, Fe2+, Ni2+, Zn2+, Mg2+, Cu2+, Cd2+, Co2+, and W6+ (Facchin et al., 2013; Jagadabhi et al., 2019) as well as zero-valent iron (Dykstra and Pavlostathis, 2017) at specific concentrations, enhances the biogas yield from AD. This is because enzymes responsible for the biochemical activities of bacteria are chemically associated or linked with metals (metallo-enzymes). By augmenting with appropriate amounts of metals or trace elements, the appropriate amounts of nutrients in the biodigester will be maintained, thereby leading to an enhanced feedstock degradation and, consequently, increased yield of biogas and biomethane (Jiang et al., 2012). For instance, the enzyme called acetyl-CoA decarboxylase/synthase plays an essential role in the conversion of acetate to methane, and this can further be accelerated by the addition of nickel metal (Ni2+) (Funk et al., 2004). Kumar et al. (Kumar et al., 2006) reported that in the mesophilic AD processing of potato waste and cattle manure (50:50), by supplementing with heavy metals such as Ni2+, Zn2+, and Cd2+ at a low concentration of 2.5 mg/L, the production of biogas was enhanced. Climenhaga and Banks (Climenhaga and Banks, 2008) also reported an increase in the yield of biomethane after the addition of Fe, Zn, Mn, Cu, and Mo into the biodigester in the AD processing of catering waste. In addition, Dykstra and Pavlostathis (Dykstra and Pavlostathis, 2017) reported a 123%–231% increase in total biomethane generation as a result of the biodigester amendment with zero-valent iron (ZVI). However, to prevent AD process collapse or failure, the addition of the excess amount of heavy metals should be avoided as it can reduce the biochemical activity of the methanogens (Kumar et al., 2006). Hence, the rightful amount of metal augmentation is essential.
1.5.2.2 Use of adsorbents
1.5.2.2.1 Carbon-based conductive material
The accumulation of toxic and inhibitory compounds during AD processing of organic wastes may cause a serious decrease in the yield of biogas and biomethane, thereby compromising the feasibility of the biogas plant. The application of carbon-based conductive materials or adsorbents can help mitigate or overcome the accumulation of inhibitory compounds such that there can be an improvement or enhancement in the production of biogas and biomethane (Dang et al., 2016). Using carbon-based conductive materials or adsorbents in AD to avoid the inhibition associated with high ammonia and volatile fatty acids levels during the process to enhance the AD performance or biogas/biomethane production has been widely studied (Chen S. et al., 2014; Xu et al., 2015; Lee et al., 2016; Zhang et al., 2020). These studies all reported that conductive carbon-based materials could enhance methane production from diverse, complex organic substrates, permit higher OLR and promote rapid recovery of soured reactors. Some of the conductive carbon-based materials that can be utilised include carbon cloth (Chen S. et al., 2014), activated carbon (powdered or granular) (Lee et al., 2016; Dastyar et al., 2021), and biochar (Zhang et al., 2020). The use of these carbon-based conductive materials facilitates direct interspecies electron transfer (DIET) (Lee et al., 2016), methanogens enrichment and accelerates the start-up of methanogenesis (Xu et al., 2015). Furthermore, these conductive carbon-based materials can be doped with magnetite to achieve enhanced biogas/biomethane production. Recently, Barua et al. (Barua et al., 2019) reported a high-performance AD with the use of magnetite doped granular activated carbon.
1.5.2.2.2 Ion-exchange capacity material
Materials with ion exchange capability, like zeolites and bentonites as well as inorganic materials such as clay and manganese oxides, can also be utilised as support matrix to retain the biomass (i.e., immobilization) in the bioreactor or biodigester (Montalvo et al., 2012; Wang et al., 2012). This biomass immobilization allows the bioreactor or biodigester to operate at a lower HRT and higher OLR (Montalvo et al., 2012), thus improving or enhancing the AD process (Wang et al., 2012). In addition, zeolites can be modified to increase their ionic exchange capacity and to supply micronutrients (e.g., Ni, Co, Mg) (Milán et al., 2003). However, high amounts of zeolite should be avoided as it can lead to toxicity due to heavy metal accumulation (Montalvo et al., 2005). Yin et al. (Yin et al., 2019) reported a 79.4% increment in biomethane production from the AD of wasted activated sludge when the AD process was amended with ash. The ash amendment facilitated the sequestration of CO2 as calcite leading to a high percentage of hydrogen in the biogas.
1.5.2.2.3 Nanoparticle materials
In recent times, the use of nanoparticle materials has demonstrated its benefits in promoting substrate degradation and enhancing AD performance as well as reducing the bioconversion period (Ellacuriaga et al., 2021). This is because of their unique characteristics of high surface area, a high number of active sites, specificity and high reactivity (Baniamerian et al., 2019). The presence of the nanoparticle materials in the AD digester or bioreactor, through its metal components’ bioavailability that is essential for enzymatic reactions, stimulates microbial activity and thus enhances or accelerates cellular growth (Abdelsalam and Samer, 2019). The review of the nanoparticles mechanism and its effect on AD process has been presented by both Abdelsalam and Samer (Abdelsalam and Samer, 2019) and Faisal et al. (Faisal et al., 2019). These Nanoparticle materials enhance direct interspecies electron transfer and interspecies hydrogen transfer (Li et al., 2019). Some of the nanoparticle materials utilised include metal nanoparticles (iron, copper, cobalt, silver and nickel) (Casals et al., 2014; Zaidi et al., 2018; Abdallah et al., 2019; Grosser et al., 2021; Hassaan et al., 2021). Casals et al. (Casals et al., 2014) and Abdelwahab et al. (Abdelwahab et al., 2020) have both reported increased biomethane/biogas production with low H2S when the AD process was supplemented with iron nanoparticles (NPs), while Farghali et al. (Farghali et al., 2019) also reported a twofold biogas increase and a decreased H2S production when the AD process was amended with the addition of titanium dioxide (TiO2) and iron oxide (Fe2O3) nanoparticles.
1.6 Use of improved reactor configuration and operation conditions
The manner of feedstock conversion during anaerobic digestion is also dependent on the reactor configuration and its operational parameters (Sarker et al., 2019). A wide range of reactor configurations and designs include anaerobic baffled stacking reactor, anaerobic contact process, anaerobic filter, anaerobic fluidized bed reactor, etc. To obtain a higher biogas and biomethane yield, several modifications of reactor systems have been suggested, including the use of two-stage or multi-stage reactor systems (Voelklein et al., 2017; Zhang et al., 2017) and temperature-phased anaerobic digestion reactor (TPAD), where the thermophilic stage is followed by the mesophilic stage (Wu et al., 2015a). Also, the performance of reactors with respect to biogas and biomethane production or yield is linked to operational factors such as the pH, stirring or agitation, temperature, hydraulic retention time (HRT), organic loading rate (OLR), total solid content (TSC), carbon/nitrogen ratio, etc., (Rocamora et al., 2020; Uddin et al., 2021). Any form of modification or drastic change that might be made to these factors can lead to changes in the surrounding environment of the microbial community and movement within the bioreactor. Hence, to optimize biogas and biomethane production, it is essential to control these factors. These factors can be manipulated within an appropriate and acceptable range so that the AD bioreactor can run optimally and efficiently.
1.7 Biogas purification and upgrading technologies
Aside from CH4, the rest of the gases (CO2, H2S, NH3, N2 and the water vapour (H2O) present in the biogas are considered biogas impurities or pollutants (Tippayawong et al., 2010; Angelidaki et al., 2018), which decrease or reduce the heat or specific calorific value of biogas (Tippayawong et al., 2010). That is, the concentration or amount of CO2 and H2S as well as other impurities that are mixed with the biogas, determines the heating effectiveness or specific calorific value of the biogas or biomethane. The higher the amount or concentration of these impurities present in the biogas or mixed with the biomethane, the lower the heat effectiveness and specific calorific value and vice versa. In addition, these impurities or pollutants like water vapour can lead to corrosion of the energy conversion equipment, and similarly, NH3 and H2S are both dangerous as they are toxic and corrosive. NH3, during combustion, generates products that are corrosive, which can cause damage to engines and biogas pipelines (Muñoz et al., 2015). Also, H2S can result in the emission of sulphur dioxide from combustion and can as well reacts with condensate water to form sulphuric acid, which can cause corrosion of gas storage tanks, gas pipelines, engine parts, compressors and damage the combined heat and power unit (Angelidaki et al., 2018; Muñoz et al., 2015; Domingues et al., 2021). CO2 does not contribute to the combustion. It only lowers the heating value of biogas and increases the compression and transportation costs (Ghatak and Mahanta, 2016). Siloxanes can form sticky silicone oxide (SiO2) deposits in process equipment and combustion engines that could result in their malfunctioning and damage (Angelidaki et al., 2018; Santiago et al., 2020). It is, therefore, imperative to reduce the amount of impurities, especially CO2 and H2S, to a minimal level or remove them completely to concentrate the biomethane content and improve its quality (Tippayawong et al., 2010; Hosseinipour and Mehrpooya, 2019). This implies that for biogas to be used as a fuel or viable alternative energy, it has to be purified, sweetened or upgraded. Therefore, the upgrading or sweetening process involves firstly, the removal of the toxic and harmful impurities or pollutants (such as H2S, NH3, N2, etc.) referred to as “biogas cleaning” (Angelidaki et al., 2018) and secondly, the removal of CO2 (Kougias et al., 2017; Angelidaki et al., 2018; Moya et al., 2022) or its conversion to CH4 by reacting with hydrogen (H2) (Kougias et al., 2017). That is, the upgrading is performed by separating CH4 from other impurities through the treatment and purification of biogas (Domingues et al., 2021). The major purpose of upgrading biogas is to concentrate the biomethane content to an optimum or maximum level of approximately 95%–99%, to maximise its heating effectiveness or calorific value similar to natural gas (Moya et al., 2022). When biogas is upgraded to pure or clean bio-methane with a methane content of approximately 98%, the biomethane has the same properties as natural gas (Wellinger et al., 2013; Hosseinipour and Mehrpooya, 2019) and can thus be compressed (Bio-CNG) or liquefied (Bio-LNG) (Domingues et al., 2021). Nonetheless, the ultimate or final use of biogas determines its final composition and the type of upgrading technique required. For example, for its use in boilers to generate heat, it only requires the removal of water vapour and H2S removal (<1,000 ppm) prior to combustion (Bailo ´n, 2012). Biogas utilisation in ICE (internal combustion engines) for the generation of combined heat and power (CHP), requires the removal of H2S, siloxanes NH3, halogenated compounds and water levels below 200–1,000 ppm, 5–28, 32–50, and 65–100 mgm-3, respectively, which dependent on the manufacturer’s specification; whereas for its use in turbines for CHP requires very low amounts of siloxane (<0.1 ppm) and water while it is able to withstand high H2S (10,000–70,000 ppm) and halogenated carbon (200–1,500 ppm) concentrations (Muñoz et al., 2015; Bailo ´n, 2012; Soreanu et al., 2011). However, biogas used as a vehicle fuel and for its injection into natural gas grids requires the most stringent quality, which usually demands that the biogas should possess CH4 concentrations (80%–96%), CO2 (2%–3%), NH3 (3–20 mgm-3), H2S (5 mgm-3), O2 (0.2%–0.5%) and siloxanes (5–10 mgm-3) (Muñoz et al., 2015). Several authors have studied the technologies of upgrading biogas (Sun et al., 2015; Kadam and Panwar, 2017; Khan et al., 2017; Baena-Moreno et al., 2019a). From the studies, the most known technologies for biogas upgrading are absorption technology, adsorption technology, membrane separation technology, cryogenic separation technology and biological technology. Figure 7 shows the schematic representation of the different biogas purification and upgrade technologies. The following sections discuss the biogas purification and upgrade technologies enumerated in Figure 7.
1.8 Absorption scrubbing technology
This method can be subdivided into physical absorption scrubbing and chemical absorption scrubbing.
1.8.1 Chemical absorption scrubbing
This is a method, as shown in Figure 8, that uses aqueous organic or inorganic compounds as absorption scrubbers or agents to capture and remove impurities or pollutants such as CO2 and H2S from gases (Ryckebosch et al., 2011; Struk et al., 2020). That is, it is a method that involves the chemical binding of CO2 and H2S to an organic (Wellinger et al., 2013) or inorganic scrubbing agent (Struk et al., 2020). The method that involves the utilisation of organic absorption scrubbers is referred to as organic-chemical absorption scrubbing, while the one that entails the use of inorganic-chemical absorption scrubbers is called inorganic-chemical absorption scrubbing.
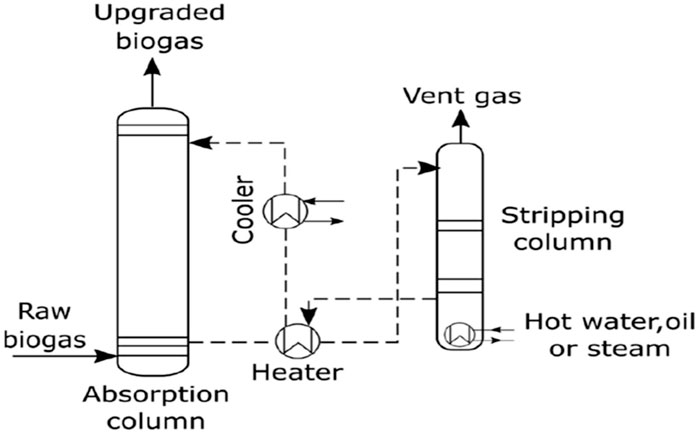
FIGURE 8. Chemical absorption scrubbing system (Adapted from Muñoz et al., 2015; Struk et al., 2020).
1.8.1.1 Organic-chemical absorption scrubbing
In this method, the most widely used organic scrubbers are the aqueous solutions of amines and alkyl-amines such as monoethanolamine (MEA), aminoethoxyethanol (DGA), diethanolamine (DEA), diisopropanolamine (DIPA), and methyl diethanolamine (MDEA) (Struk et al., 2020). The use of amines for scrubbing can also be referred to as the amine scrubbing method (Kadam and Panwar, 2017; Hosseinipour and Mehrpooya, 2019). These scrubbing systems or absorption columns normally consist of absorber and stripper units. In the absorber unit, the biogas is first compressed or pressurized at a range of 1–2 bars and then injected into the unit from the bottom while the amine solution is made to flow into the unit from the top countercurrent to the biogas (Vega et al., 2017a; Struk et al., 2020). There occurs between the pollutants or biogas impurities (CO2 and H2S) and the amine solution reversible exothermic reaction. The resultant amine solution, which now contains CO2 and H2S, flows to the stripping column for regeneration, which operates at a pressure range of 1.5–3 bars and a temperature range of 120–160°C (Struk et al., 2020). It is often recommended that H2S be removed first before using this method for CO2 removal (Zhou et al., 2017). This is because the presence of H2S can cause amine poisoning and increase the energy requirement (Struk et al., 2020). The advantages of this amine scrubbing method include high amine selectivity by CO2, no loss of CH4 and high volume reduction in comparison with other methods (Struk et al., 2020). On the other hand, the drawbacks are the high cost of the amine solvents, increased operational costs due to amine loss caused by evaporation as a result of its high volatility and high energy (i.e., high-temperature heat) requirements for regeneration of solvent (Kadam and Panwar, 2017; Khan et al., 2017; Struk et al., 2020). Organic-chemical absorption scrubbing systems using amine solutions can produce biogas with a final CH4 content of 99% purity (Abdeen et al., 2016; Struk et al., 2020).
1.8.1.2 Inorganic-chemical absorption scrubbing (caustic wash scrubbing)
The inorganic scrubbers that are mostly used for CO2 removal are an aqueous solution of alkaline salts (e.g., calcium, potassium and sodium hydroxides) (Kougias et al., 2017). This method of using hydroxides or caustic solutions for CO2 removal can also be referred to as the caustic wash scrubbing method (Hosseinipour and Mehrpooya, 2019). This method utilizes a countercurrent biogas stream contacting with the aqueous caustic solution in a tray or packed column (Hosseinipour and Mehrpooya, 2019). The inorganic-chemical absorption scrubbing systems using alkaline solutions can result in biogas that has a 94%–97% of final CH4 content (Abdeen et al., 2016; Struk et al., 2020). The main advantages of sodium and potassium hydroxides, when compared with other solvents, are their greater availability, the possibility of forming a non-polluting by-product and the theoretical capture capacity (Kougias et al., 2010; Yoo et al., 2013). KOH is more expensive than NaOH (Lombardi and Francini, 2020). The disadvantage of the caustic wash method is that it involves high consumption of caustic (hydroxides) solutions due to the formation of bicarbonates (e.g.,.Na2CO3) that cannot be regenerated, leading to the solution being discarded (Hosseinipour and Mehrpooya, 2019). To resolve the issues of solvent loss and energy requirements for solvent regeneration, researchers have reported the use of new solvents like ionic liquids (IL) such as amino acid or carboxylate-based IL (Hospital-Benito et al., 2020) and a super acid mixture of sulphuric acid and glacial acetic acid (Charry Prada et al., 2020). Novel super acid solvent systems absorbed up to 83% and ionic solvents removed 90% of CO2 from biogas (Charry Prada et al., 2020; Hospital-Benito et al., 2020). These ionic liquids have lower energy requirements for their regeneration and possess high CO2 uptake capacity (Hospital-Benito et al., 2020). These ionic liquids removed 90% of CO2 from biogas (Hospital-Benito et al., 2020). The benefits of the super acid solvent system are that it offers reduced energy requirements for their regeneration, complete degradation of volatile organic compounds (VOCs) and siloxanes, as well as simultaneous removal of CO2 and H2S (Charry Prada et al., 2020). The super acid (sulphuric acid and glacial acetic acid) solvent system captured up to 83% of CO2 (Charry Prada et al., 2020).
1.8.2 Physical absorption scrubbing
This method involves the use of water (Wellinger et al., 2013) and/or organic solvents (Muñoz et al., 2015) as absorption scrubbers to remove CO2 as impurities from gases. Thus using only water as the scrubber or absorbent method is referred to as the water scrubbing method (Angelidaki et al., 2018), while the use of organic solvent only is called organic physical scrubbing (Struk et al., 2020).
1.8.2.1 Water scrubbing
Water scrubbing is a widely applied technique for the purification (cleaning) of biogas and upgrading (Angelidaki et al., 2018). The method relies on the higher CO2 and H2S solubility in water compared to CH4. Although this method can get through with an H2S concentration range of 300–2,500 ppm, however, the H2S solubility in water is higher than that of CO2 and thus can be removed alongside CO2. But because dissolved H2S can result in corrosion and offensive odour, hence H2S is recommended to be removed prior to the use of water scrubbing for CO2 removal (Ryckebosch et al., 2011; Sun et al., 2015). The water scrubbing method, as presented in Figure 9, is operated at a high-pressure range of 6–10 bar and a temperature of up to 40 °C (Zhou et al., 2017; Angelidaki et al., 2018). In high-pressure water scrubbing, gas enters the absorption packed or tray column from the bottom, and water is then sprayed or introduced into the column from the top and flows down the column counter-current to the biogas (Bauer et al., 2013b; Angelidaki et al., 2018). The H2S and CO2 in the raw biogas then dissolve into the water, and the upgraded biogas (i.e., biomethane) leaves and is obtained from the top of the absorption column, while the water that contains dissolved CO2, H2S and small amounts of CH4 leaves the absorption column from the bottom and flows into a flash tank from where an additional amount of CH4 can be retrieved back using a lower pressure range of 2.5–3.5 bar (Angelidaki et al., 2018). The water scrubbing method results in high CH4 losses and possess the inability to remove O2 and N2. The loss of CH4 is due mainly to its dissolution in water. Based on theoretical calculations, the loss usually lies between 3% and 5% (Sun et al., 2015). However, Persson (Persson, 2003) has reported CH4 loss of about 8%–10%) and Sun et al. (Sun et al., 2015) reported CH4 loss of less than 2%, while 18% CH4 loss has been the highest reported to date (223). With this method, a biomethane purity of more than 96% can be obtained after drying (Sun et al., 2015; Hosseinipour and Mehrpooya, 2019), which depends on the non-condensable gases (N2 and O2) volume that cannot be removed from CH4 (10). The main merits of this method are its design simplicity and overall cost-effectiveness (Struk et al., 2020). The limitations or disadvantages of the method are high-water consumption requirements (Starr et al., 2012) and lower energy efficiency (Bauer et al., 2013a). Thus, water regeneration is a vital step for this method. Therefore, most of the modern absorption column units consist of a two-stage air stripping unit for CO2 and water regeneration (Bauer et al., 2013a; Muñoz et al., 2015; Bauer et al., 2013b). The dissolved CO2 present in the water can be obtained using the air stripping method, so it is feasible to achieve high CO2 purity of 80%–90% (Sun et al., 2015). In addition, efforts have been made in recent times by Noorain et al. (Noorain et al., 2019) and Benizri et al. (Benizri et al., 2019) to improve the removal efficiency of absorption columns by operating at atmospheric pressure and high pressure, respectively. Noorain et al. (Noorain et al., 2019) used sponge materials to pack the column to increase the hydraulic retention time, and they achieved complete removal of H2S from artificial biogas with CH4 having a 90% purity. Benizri et al. (Benizri et al., 2019) constructed a CH4 leak-proof high-pressure water scrubbing system that included a static mixer for CO2 desorption enhancement, and they reported a high recovery efficiency of 94% CH4 and a low energy consumption of 0.26 kWh/Nm3.
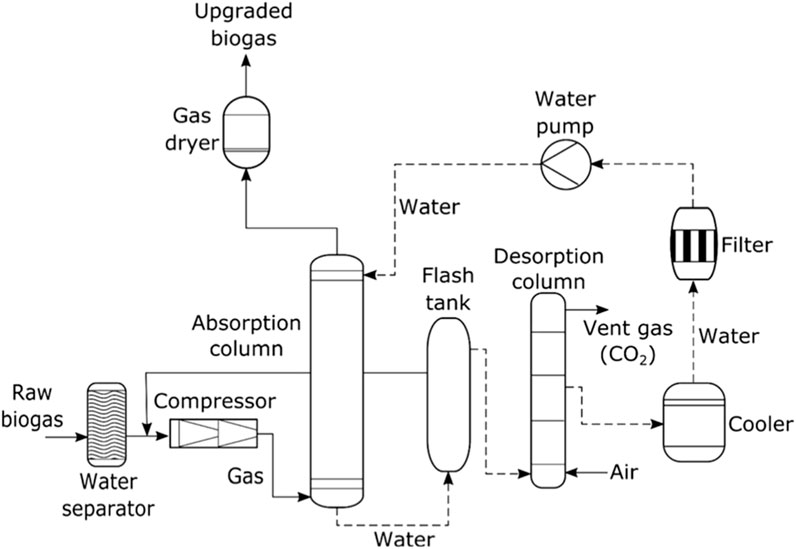
FIGURE 9. Water scrubbing system (Adapted from Baena-Moreno et al., 2019b; Struk et al., 2020).
1.8.2.2 Organic physical scrubbing
Organic-physical absorption scrubbing technique, as shown in Figure 10, has the same principle as water scrubbing (Struk et al., 2020). This method entails the use of organic solvents that have higher affinity for H2S and CO2 (Angelidaki et al., 2018; Struk et al., 2020). Organic solvents such as methanol and dimethyl ethers of polyethylene glycol (DMPEG) are employed in this method (Awe et al., 2017; Struk et al., 2020). CO2, H2S and H2O can simultaneously be absorbed since they all have a higher solubility than methane in organic solvent (DMPEG) (Awe et al., 2017; Struk et al., 2020). There are commercial organic scrubbers that are sold under the trade names Genosorb and Selexol, which exhibit higher CO2 and NH3 solubility compared to water (Struk et al., 2020). The first step in this method involves the compression of the biogas at 7–8 bar and thereafter cooling at 20 °C. The compressed and cooled biogas is then introduced into the absorption column from the bottom. A cooled organic solvent is injected into the column from the top to flow countercurrent to the biogas (Bauer et al., 2013a). This method can achieve an upgraded biogas that has up to 96%–98.5% CH4 with less than 2% loss of CH4 (Bauer et al., 2013a; Bauer et al., 2013b; Sun et al., 2015). The organic solvent regeneration is conducted in the desorption column at a reduced pressure of 1 bar, heating it to 80 °C (Sun et al., 2015; Angelidaki et al., 2018). Presently due to increased pressure towards the use of environmentally friendly organic solutions, the use of green solvents is gradually replacing conventional organic solvents. In recent times, there has been the application of deep eutectic solvents (DES) like Reline and Glyceline as organic scrubbers (Haghbakhsh and Raeissi, 2019). This DES consists of two or more components that are majorly hydrogen bond donors and hydrogen bond acceptors having properties of very low vapour pressure, lower melting point and biodegradable. The potential of Reline and Glyceline to capture and remove CO2 from natural gas and their performance compared with commercial Selexol was investigated by Haghbakhsh and Raeissi (Haghbakhsh and Raeissi, 2019). The workers reported that Reline, Glyceline and Selexol achieved 79.6%, 90.1% and 89.1% CH4 purity, respectively, and that both Reline Glyceline attained an average of 98% CO2 capture as compared to 94.9% achieved by Selexol.
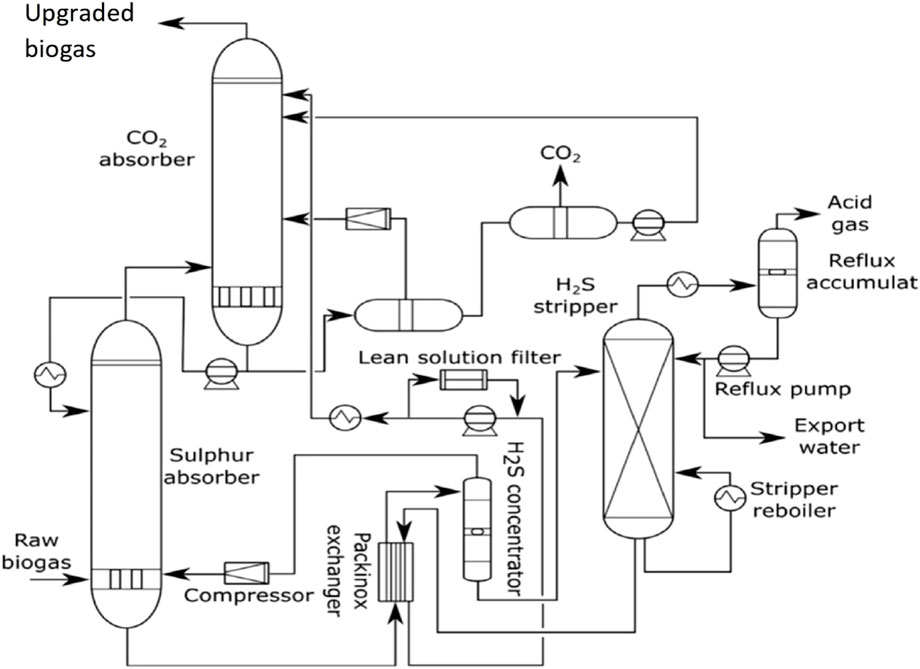
FIGURE 10. Selexol system (Adapted from UOP Selexo (TM) Technology for Acid Gas Removal, Struk et al., 2020).
1.9 Membrane separation technology
Membrane separation technology is a method of separation at the molecular level through a selective membrane barrier (Sun et al., 2015) as illustrated in Figure 11.
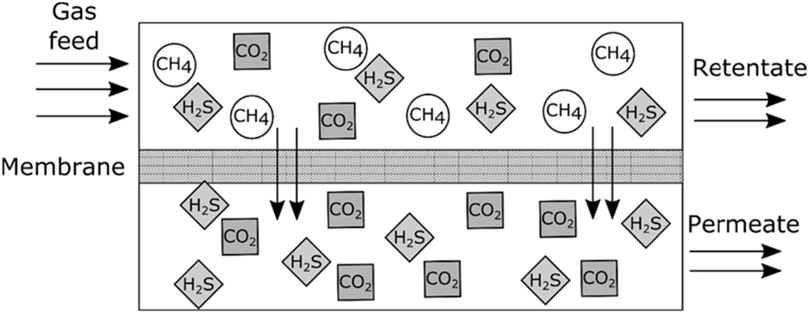
FIGURE 11. Principle of membrane separation (Adapted from Allegue and Hinge 2014; Struk et al., 2020).
Membrane separation technology possesses a number of advantages, such as easy process, energy efficiency and low cost (Sun et al., 2015). The permeability of the membrane is based on the electric charges differential of the different molecules, concentration gradient, temperature gradient and pressure gradient (Hashiba et al., 2017; Khan et al., 2017). For membrane separation, there are gas–liquid (wet) and gas–gas (dry) techniques (Struk et al., 2020). The wet and the dry membrane separation techniques differ in their micro-porous membranes’ hydrophobic properties (Struk et al., 2020). The liquid system that can be used for the gas-liquid separation system is alkanol amines or aqueous alkali solutions. In gas-liquid membrane systems operated at atmospheric pressure, the biogas diffuses through the membrane and is absorbed by the liquid media passing or flowing counter-current to the biogas (Ryckebosch et al., 2011; Bauer et al., 2013a). In gas–gas membrane systems, the biogas is pressurised at 20–40 bars (or 6–20 bars) such that the CO2, H2S and some amount of CH4 (about 10%–15%) will diffuse or pass through the membrane to the permeate side with the lower pressure while a significant amount of CH4 will remain or be retained on the membrane inlet side with the higher pressure (Bauer et al., 2013b; Sun et al., 2015; Struk et al., 2020). The gas–gas membrane separation units are produced under different configurations: single-pass or one-stage and multiple-stage units having internal permeate and retentates recirculation (Ryckebosch et al., 2011). The gas-gas multi-stage membrane units can achieve about 96% or more of CH4 purity, while one-stage membrane units can result to 92% purity of CH4 (Allegue and Hinge, 2014). Compared to the gas–liquid membrane system, the efficiency is lower (Allegue and Hinge, 2014). The most suitable commercial membranes for biogas separation and enrichment are those produced from polymeric materials such as polyimide and cellulose acetate-based membranes (Basu et al., 2010; Scholz et al., 2013).
1.10 Adsorption technology
This technology utilises a porous solid adsorbent to remove the impurities from the biogas (Angelidaki et al., 2018; Moya et al., 2022). The properties of adsorbent types influences the efficiency of this method. The most commonly and widely utilised commercial adsorbents for biogas treatment are carbon-based adsorbents (activated carbon), silica gels, and metal–organic frameworks (Abdelhafez et al., 2014; Augelletti et al., 2017; Lin et al., 2019). The common sources of activated carbon are lignocellulosic biomass, coals and industrial by-products (Bamdad et al., 2018). The metal–organic frameworks (MOF) are a hybrid of organic–inorganic crystalline porous materials consisting of an assemblage of positively charged metal salts ions that are surrounded by organic ligands (Chaemchuen et al., 2013). The MOFs design and synthesis is an emerging area with several possibilities for industrial applications (Chaemchuen et al., 2013; Hanak et al., 2015). The other adsorbent materials include synthetic or natural zeolites, commercial metal oxide-based adsorbents such as SulfaTreat, Sulphur-Rite or SOXSIA (230), copper, alkaline and iron-based metal oxides and unusual adsorbents such as CeO2, La2O3, and TiO2 (Hakim et al., 2016). The attractive use of iron metal oxides and alkaline metal oxides for CO2 capture and removal is due to their abundance, favourable adsorption and desorption kinetic, good adsorption capacity, and low costs (Hakim et al., 2016; Bamdad et al., 2018). There are different forms of adsorption technology which include, pressure swing adsorption (PSA) (Wiheeb et al., 2016; Zhou et al., 2017), vacuum swing adsorption (VSA) (Zhou et al., 2017) and temperature swing adsorption (TSA) (Zhou et al., 2017).
1.10.1 Pressure swing adsorption
Pressure swing adsorption (PSA) is based on the selective adsorption of biogas impurities (CO2) over CH4 onto solid surfaces under high pressure according to their different molecular sizes and adsorbent affinity (Sun et al., 2015; Ferella et al., 2017; Canevesi et al., 2018). It is called PSA if the adsorbent regeneration occurs when the pressure decreases up to the level of the atmospheric pressure. The PSA technology can be employed to remove CH4 from N2, O2 and CO2 since the CH4 is larger than the rest of the biogas impurities (Sun et al., 2015). The PSA technology, as shown in Figure 12, is carried out in adsorbent-packed vertical columns, and it consists of four steps sequence, which includes adsorption, depressurisation, desorption and pressurisation (Augelletti et al., 2017). As biogas flows or passes through the high-pressurized column, O2, CO2, H2S, and N2 are captured and adsorbed on the adsorbent. Siloxanes and H2S are irreversibly adsorbing onto the adsorbent. For instance, H2S forms insoluble metal sulphides with metal-oxide adsorbent, and it is therefore advised to get them removed alongside water vapour prior to the subjection of biogas to the PSA technology (Bauer et al., 2013a). For continuous operation, multiple adsorption columns can be employed (Bauer et al., 2013b). The CH4 content after upgrading with PSA can get up to a range of 96%–98%; however, with about 2%–4% CH4 is lost (Sun et al., 2015). Generally, to achieve higher concentrated CH4 or purity, more CH4 is usually lost (Sun et al., 2015).
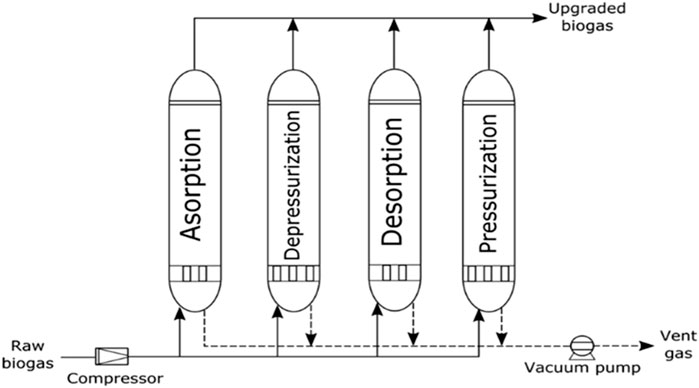
FIGURE 12. Pressure swing adsorption system (Adapted from Kadam and Panwar, 2017; Struk et al., 2020).
1.10.2 Vacuum swing adsorption
Vacuum swing adsorption (VSA) has a similar operating system to PSA, except that the desorption or regeneration step is conducted at a pressure lower than the atmospheric pressure (Zhou et al., 2017). That is, it is called VSA, if the adsorbent regeneration occurs by applying a vacuum after when the inlet valve has been closed. In recent times, there is more focus on improving the adsorbents and optimizing the PSA/VSA technology. Some of these improvements include silica gel modification by grafting amine functional groups into the pore walls of the silica (Wang and Yang, 2014) temperature vacuum swing adsorption system, which employed the use of nanogel particles containing amines supported by honeycomb shaped-carbon fibre (Gao et al., 2020) and adsorbents tailor-made into 3D printed-patterned structures (Middelkoop et al., 2019). Gao et al. (Gao et al., 2020) reported an increase in CO2 recovery with the use of nanogel particles containing amines supported by honeycomb shaped-carbon fibre. The different adsorbents for CO2 and H2S removal are mostly utilised in the form of beads. When the performance of 139 zeolite beads was compared with the 3D printed-patterned structures, it was reported that higher adsorption and desorption rates were exhibited by the 3D printed-patterned structures. In contrast, the 139 zeolite beads displayed higher adsorption capacity than the 3D printed-patterned structures made from the same zeolite (Middelkoop et al., 2019).
1.10.3 Temperature swing adsorption
Temperature swing adsorption (TSA) is also similar in operation to PSA, except that adsorbent regeneration takes place at varying temperature between 30 and 120 °C while pressure remains constant [Sahota et al., 2018]. Through lower temperatures, the adsorption process becomes more effective, with the regeneration of the adsorbent taking place with increasing temperature (Santos and Joppert, 2018). In TSA, it is hot gases or steam that is utilised in transferring heat to the column (Zhou et al., 2017). TSA is usually restricted to the removal of small amounts of impurities or pollutants. That is, TSA should be applied for the removal of CO2 concentration that is 1% or less, while PSA is preferred for CO2 concentration that is greater than 10% (Zhou et al., 2017).
1.11 Cryogenic separation technology
The cryogenic separation technology (Figure 13) is a distillation based technology that involves the separation of the different biogas mixtures hinged on their different boiling points performed through a gradual sequential temperature reduction (Muñoz et al., 2015) in four stages. The technology demands high pressure of about 50–200 bar for initial compression and cryogenic temperature (i.e., low temperature that is close to −125 °C) (Hosseinipour and Mehrpooya, 2019). Components of the biogas possess different temperatures of liquefaction (condensation) and solidification, which gives room for CH4, H2S, H2O, and CO2 selective separation (Bauer et al., 2013a; Tan et al., 2017b). The cryogenic separation process begins first with biogas compression to 80 bar and temperature reduction to - 25 °C. At this first stage, the H2S, siloxanes, halogens and H2O are removed. After the first stage, in the second stage, the purified biogas is compressed to a pressure of 1000 kPa (80 bar) and then passed through a heat exchanger where the biogas temperature is further cooled or reduced to - 25 °C. The cooled biogas then enters into the third stage, where the temperature is further cooled or reduced to −55°C, during which most of the CO2 is liquefied or condensed. The temperature of this cooled purified biogas is finally cooled or reduced to −85 °C in the fourth stage, during which the remaining CO2 solidifies and is completely separated or removed (Ryckebosch et al., 2011; Riva et al., 2014; Baena-Moreno et al., 2019a). Also, after CH4 condensation, N2 and O2 can be removed. To avoid the problem of freezing (i.e., formation of ice) and other operational problems, such as pipe or heat exchanger clogging in the cryogenic process of separation, H2S and H2O are to be removed prior to cryogenic separation application (Bauer et al., 2013a; Sun et al., 2015; Baena-Moreno et al., 2019a). The cryogenic separation technology can result in over 97% CH4 purity and less than 1 or 2% of CH4 loss (Andriani et al., 2014; Baena-Moreno et al., 2019a) as well as in 98% CO2 purity (Sun et al., 2015). However, the use of this technology is limited by large or high energy requirement, high capital investment and operation costs (Angelidaki et al., 2018; Ryckebosch et al., 2011; Muñoz et al., 2015). In order to provide solutions to the limitations presented by cryogenic separation technology, some workers have proposed the use of cryogenic hybrid technologies such as cryogenic hydrates systems (Sreenivasulu et al., 2015; Baena-Moreno et al., 2019b), cryogenic adsorption systems (Fong et al., 2016; Moreira et al., 2017; Song et al., 2019), cryogenic absorption systems (Hanak et al., 2015; Song et al., 2018) and cryogenic membrane systems (Song et al., 2017; Song et al., 2019). Presently, the cryogenic membrane process has been the most intense combination studied.
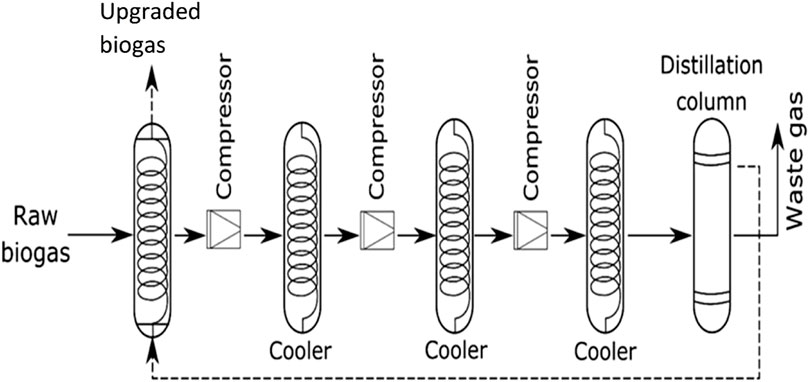
FIGURE 13. Cryogenic separation system. (Adapted from Baena-Moreno et al., 2019b; Struk et al., 2020).
1.12 Hydrate formation technology
The contaminants of biogas can be removed or separated based on the difference in their formation of gas hydrate (Sun et al., 2015). This method has been utilised to successfully remove CO2 from impure natural gas (Van Denderen et al., 2009). It has been reported that this technology consumes a large amount of energy due to the high pressure needed for hydrate formation (Awe et al., 2017). This technology requires improvement by reducing its energy consumption and methane loss for future use.
1.13 Biological technology
The biological technologies that can be applied for biogas upgrading can generally be categorised into chemoautotrophic and photoautotrophic technologies (Angelidaki et al., 2018).
1.13.1 Chemoautotrophic technology
The chemoautotrophic technology, which is an end-of-the-pipe biotechnology, can be applied for CO2 conversion to CH4 and for biogas desulphurization (i.e., H2S removal) (Muñoz et al., 2015; Struk et al., 2020). For CO2 conversion to CH4, the technology is based on the application of hydrogenotrophic methanogenic bacteria in converting CO2 to CH4 through the utilisation of H2 as an electron donor (Muñoz et al., 2015). This hydrogen-assisted biogas upgrading technology can be categorised into three, namely, in-situ, ex-situ and hybrid chemoautotrophic technologies (Kougias et al., 2017).
1.13.1.1 In-situ chemoautotrophic technology for CO2 conversion
In the in-situ chemoautotrophic technology, H2 is introduced or injected into the biogas digester or bioreactor so that the endogenous CO2 produced in the digester can react with it and be converted into CH4 through the activity of the autochthonous methanogens (Kougias et al., 2017). These methanogens which belong to the Archaeal genera include Methanosarcina sp., Methanobacterium sp., Methanoculleus, Methanothermobacter sp., Methanospirillum sp., Methanosaeta sp., and Methanococcus sp. (Muñoz et al., 2015). The main challenge of this technology is related to pH elevation to values above 8.5, which often leads to methanogenesis inhibition (Luo et al., 2012) as well as the low gas-liquid H2 mass transfer rate (Muñoz et al., 2015). The pH elevation is attributed to bicarbonate removal, which is the main biogas process buffer (Angelidaki et al., 2018). In order to alleviate this technical challenge, co-digestion with acidic waste was proposed to arrest the increase of pH (Luo and Angelidaki, 2013) as well as the application of pH control (Luo et al., 2014). The use of this technology can achieve approximately 80%–100% final CH4 content in the biogas (Wang et al., 2013; Luo et al., 2014; Bassani et al., 2016; Agneessens et al., 2017; Mulat et al., 2017) depending on the material and module type utilised for H2 injection, gas recirculation flow, reactor design and pH control (Bassani et al., 2016; Angelidaki et al., 2018).
1.13.1.2 Ex-situ chemoautotrophic technology for CO2 conversion
The ex-situ chemoautotrophic technology entails the biogas upgrade being performed in a separate unit or chamber that contains pure or enriched hydrogenotrophic microbial culture in which external CO2 is injected in order for it to be coupled with the H2 present in the biogas and through the action of the culture is subsequently converted to CH4 (Kougias et al., 2017). This biogas upgrading technology, strongly depending on the diffusion device utilised for CO2 injection, gas recirculation flow, reactor configuration and pH control, can result in final CH4 content that ranges from 79% to 98% as well as a range of 71%–100% CO2 removal (Diaz et al., 2015; Bassani et al., 2016; Kougias et al., 2017; Savvas et al., 2017). The major limitation or challenge of this technology is the low gas-liquid mass transfer (Angelidaki et al., 2018).
1.13.1.3 Chemoautotrophic technology for biogas desulphurization
For biogas desulphurization, the chemoautotrophic technology is based on the oxidation of H2S to sulphate through the metabolic activity of lithotrophic or chemotrophic sulphur-oxidizing bacteria (SOB) using CO2 as a carbon source and O2 in the biogas or NO3 as electron acceptor (Madigan et al., 2014; Struk et al., 2020). Examples of these SOB belongs to the genera Thiospira, Thiobacillus, Sulfolobus, Acidithiobacillus, Thiothrix, Thiovulum, Paracoccus, Halothiobacillus and Sulfurimonas, which could be strictly aerobes or facultative anaerobes (Muñoz et al., 2015). This can be performed using biofilters, biotrickling filters and bioscrubbers (Struk et al., 2020), as presented in Figure 14. A biofilter consists of a bioreactor that contains moist packed bed material with microbial biofilm immobilized on it (Mudliar et al., 2010). Due to their indigenous microbial consortia and high performance, natural organic materials (such as peats, coconut fibre, composts, woodchips, and bark) can be utilised as packed bed materials in biofilters (Struk et al., 2020). In carrying out the chemoautotrophic technology using a biofilter, the biogas is injected into the biofilter from the bottom and flows through the moist, packed bed material with microbial biofilm. The packed bed material provides the nutrient, and occasionally, a nutrient solution is added from the top of the biofilter. In addition, 5%–10% of oxygen is required, which may not be present in the biogas, and this level is usually controlled by direct injection of air into the biogas stream (Syed et al., 2006). Despite the benefits of the low cost of operation with no chemical required, the use of this system still has some limitations, such as the occurrence of packed bed acidification due to sulphuric acid formation, inefficient or no sufficient mixing, and pH and moisture control problems (Mudliar et al., 2010; Brinkmann et al., 2016; Struk et al., 2020). To circumvent these limitations, the use of acid-tolerant mixed culture, the use of packed bed materials with alkaline properties, periodic filter media washing and alkaline solution addition have been proposed (Mudliar et al., 2010; Allegue and Hinge, 2012; Struk et al., 2020). The principle of biotrickling filters is similar to that of biofilters. However, the difference is in the utilisation of inert packing bed materials and the need for the continuous supply of nutrient solution into the system. The biotrickling system has plenty of advantages over the biofiltering system and some of which include easy control and regulation of operational factors (e.g., temperature and pH), less space requirement, high process stability, lower flow resistance and continuous nutrient provision (Schiavon et al., 2015; Barbusinski et al., 2017; Rybarczyk et al., 2019; Struk et al., 2020). The biotrickling system is a widely applied technology that is commercially available as Biogas Cleaner (BioGas clean), Biopuric process (Biothane Corporation), Bidox (Colsen B.V.) and BioSulfurex (DMT Environmental Technology) (Allegue and Hinge, 2014). The bed materials used as matrix or carrier for microbial biofilm immobilization that are commonly utilised in biotrickiling filters are porous ceramics, plastic and metallic pall rings, polyurethane foam, and plastic supports activated granular carbon (Mudliar et al., 2010; Fernandez et al., 2014; Montebello et al., 2014; Rodriguez et al., 2014; Struk et al., 2020). The biotrickling system is able to achieve approximately 80%–100% H2S removal (Fernandez et al., 2014; Montebello et al., 2014; Rodriguez et al., 2014). The bioscrubber system consists majorly of two reactor units (absorption tower and activated sludge reactor) but in some cases, three (e.g., sedimentation tank) depending on the type of contaminant to be removed. For H2S removal, the biogas is injected into the absorption tower where the H2S is absorbed in the countercurrent flowing liquid phase (e.g., alkaline solution) and then flows into the activated sludge reactor, wherein the presence of O2, degradation takes place by the microbial consortia (Struk et al., 2020). The resultant effluent moves into the sedimentation tank to collect the elemental sulphur with O2 used as the oxidant and then recirculates back to the absorption tower. The bioscrubber system does not require O2 and N2 injection into the biogas but requires the addition of nutrient, continuous excess biomass and by-products purging, and pH and O2 regulation and control to maintain the optimal growth and metabolic activities of the microorganisms (Allegue and Hinge, 2014; Brinkmann et al., 2016). The commercially well-known bioscrubbers employed for the removal of H2S from biogas are SulfothaneTM (France) and THIOPAQ process (Netherlands) (Janssen et al., 2009). The major significant demerit of the bioscrubber system is its relatively high initial capital investment (Allegue and Hinge, 2012).
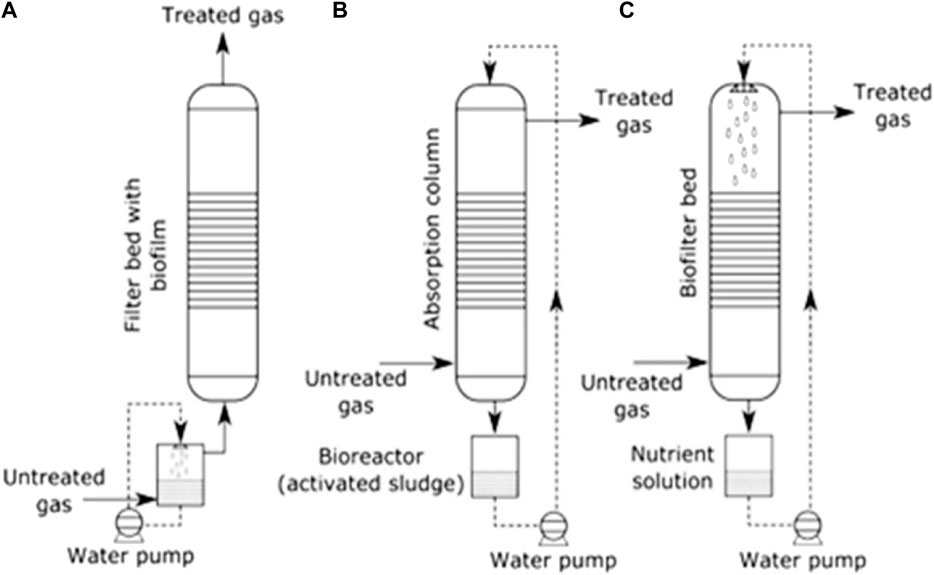
FIGURE 14. Concepts of biofiltering (A), bioscrubbing (B) and biotrickling (C) systems. (Adapted from Rybarczyk et al., 2019; Struk et al., 2020).
1.13.2 Photoautotrophic technology
The photoautotrophic technology is based on the photosynthetic capability of phototrophic organisms (such as prokaryotic cyanobacteria or eukaryotic microalgae) to sequester the CO2 present in the biogas as to obtain a CH4-rich biogas (Angelidaki et al., 2018). This technology involves the use of enclosed photo-bioreactors (Prandini et al., 2016) or open photo-bioreactors (278) and open ponds or raceways (Bahr et al., 2014; Serejo et al., 2015). In this technology (Figure 15), the biogas is directly injected into the photobioreactors containing the photoautotrophic microorganisms, and these organisms efficiently sequester CO2 using nutrients, solar irradiation and water to produce oxygen, biomass and heat. The CH4 recovery of this technology can get up to about 97% depending on the selected type of algal species (Bahr et al., 2014; Serejo et al., 2015) and a maximum range of 2%–6% CO2 in the final biogas (Meier et al., 2015). Moreover, the biomass produced in the course of biogas upgrading can be utilised either for value-added products’ extraction (Guedes et al., 2011) or as biogas production feedstock oriented to a circular economy (Mussgnug et al., 2010). Some of the microalgae or cyanobacteria possessing high photosynthetic efficiency that have been successfully employed for biogas upgrading using this technology include Chlorella species, Arthrospira platensis and Spirulina platensis (Muñoz et al., 2015; Converti et al., 2009; Kao et al., 2012; Bahr et al., 2013). For example, utilizing Chlorella sp., A. platensis, and S. platensis respectively achieved up to 85%, 100%, and 86% photosynthetic CO2 sequestration or uptake, while it resulted in 90%, 82% and 74% final CH4 content in the biogas, respectively (Muñoz et al., 2015; Converti et al., 2009; Kao et al., 2012; Bahr et al., 2013). This technology can also be applied for the removal of H2S (biogas desulphurization), while the amount of CO2 consumed can be greater than 54% (Angelidaki et al., 2018). To be able to achieve H2S removal, a mixed consortium of microalgae and sulphur-oxidizing bacteria (SOB) (i.e., algal-bacterial symbiosis) can be employed such that the SOB will oxidize the H2S to sulphate utilizing the O2 present in the biogas as an electron acceptor (Bahr et al., 2013; Bahr et al., 2014).
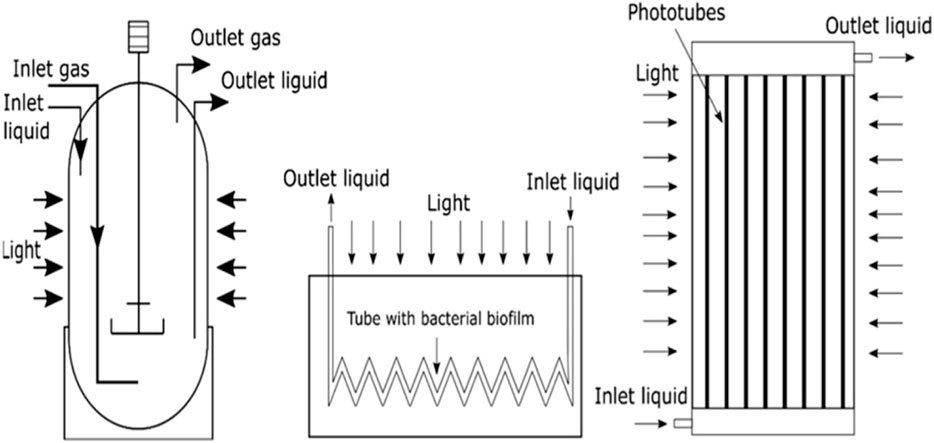
FIGURE 15. The concepts of basic photobioreactors (fed-batch, horizontal and vertical phototube reactor). (Adapted from Syed et al., 2006; Struk et al., 2020).
1.14 Energy efficiency of biogas purification and upgrading technologies
The energy efficiency (
Energy efficiency can be employed as a criteria for comparing the efficiency or performance of the different biogas upgrading technologies.
1.15 Comparison of biogas upgrading technologies, challenges and mitigations
The performance of physical, chemical and biological biogas upgrading technologies is compared (Table 4) in terms of different parameters or criteria: gas pre-cleaning requirements, H2S removal requirement, N2 and O2 removal, working pressure, working temperature, CH4 concentration in upgraded biogas, CH4 loss, CH4 recovery, specific energy consumption (kWh/Nm3 upgraded biogas), heat requirement, quality of upgraded gas, investment cost €/Nm3 biogas, maintenance cost, and technical availability. Table 4 data revealed that the conventional biogas upgrading technologies (physical absorption, chemical absorption, adsorption and membrane separation) and the emerging biogas upgrading technologies (hydrate formation, cryogenic and biological) displayed different responses to the performance criteria. The information in Table 4 shows that all the different biogas upgrading technologies relatively result in high CH4 purity levels. Amongst these technologies, organic chemical scrubbing technology suggests resulting in the highest CH4 purity level (99%) of raw biogas with the least CH4 loss (0.04%–0.1%) and the lowest level of energy consumption (0.05–0.25 kWh/Nm3 biomethane). However, its heat requirement, investment and maintenance costs seem to be relatively very high in comparison with other physical and chemical technologies. Therefore, it is not only appropriate to focus on the quality or purity of the biomethane alone but equally very important to consider the cost (i.e., investment/operational cost, maintenance cost, and energy cost) as core criteria in the selection of appropriate biogas upgrading technology. To this end, among the physical and chemical biogas upgrading technologies, membrane based upgrading technology seems to meet up with these said criteria. Nevertheless, many of these conventional technologies (physical and chemical) require a high energy input and/or costly chemicals/materials for upgrading the biogas to CH4, increasing operational and maintenance costs. In this regard, the biological biogas upgrading technologies can play a pertinent role with their lower energy requirements and no requirement for costly chemicals or materials. Therefore, at this present stage, with the development and laboratory validation of new cost-efficient biological technologies showing very good performance, it becomes difficult to predict or select which of all these (conventional and emerging) technologies will dominate the biogas upgrading process. Furthermore, the challenges faced by these technologies and the suggested or recommended mitigation(s) are presented in Table 5.
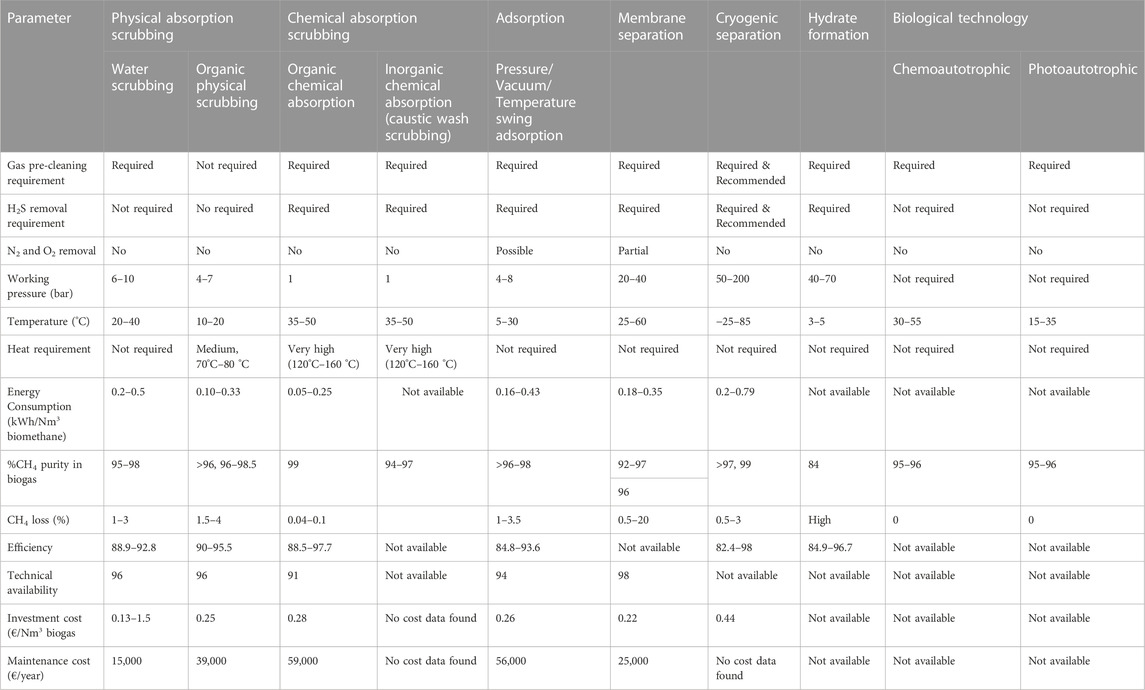
TABLE 4. Comparisons of biogas upgrading technologies [Source: Patterson et al., 2011; Castellani et al., 2014; Masebinu et al., 2014; Muñoz et al., 2015; Sun et al., 2015; Khan et al., 2017; Singhal et al., 2017; Vrbová and Ciahotný, 2017; Kapoor et al., 2019; Khan et al., 2021].
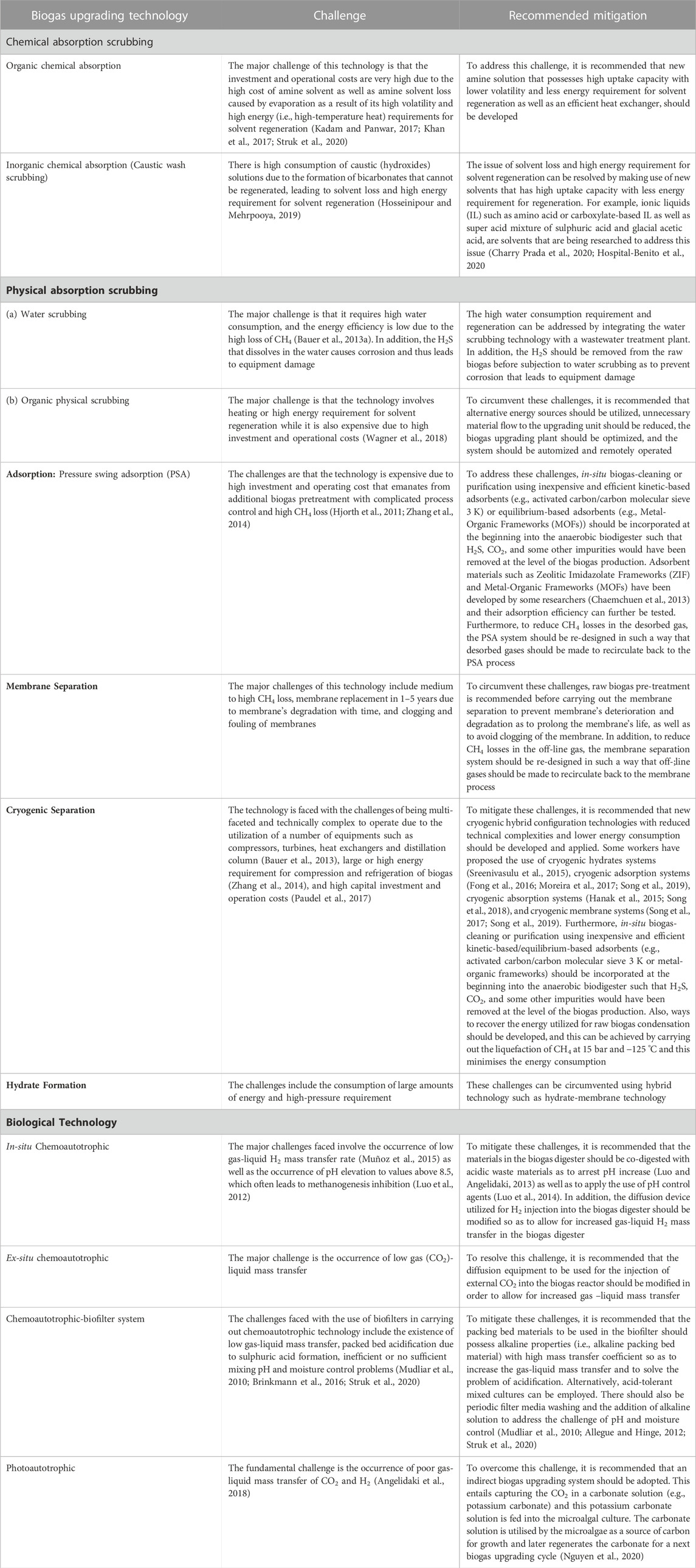
TABLE 5. Challenges of the biogas purification and upgrading technologies and their recommended mitigations.
2 Conclusion and recommendation
This paper reviewed the process intensification strategies required for enhancing AD performance as well as the biogas cleaning and upgrading technologies. It can be concluded from this review that the performance of the AD process for optimum delivery and stability has been seriously affected by the feedstock-induced operational problems (i.e., feedstock physical and chemical compositions) as well as other operational factors classified as physical, chemical and biological, respectively. Pretreatment, co-digestion, bioaugmentation (i.e., biological additives), biostimulation (addition of macro and micronutrients), additions of carbon-based conductive materials ion-exchange capacity materials as well as improved reactor configuration and operating parameters can be applied for accelerating or enhancing the AD Process technology performance to achieve greater biogas and biomethane yield or production. However, the large or full-scale application of bioaugmentation is still scarce due to its economic risks and uncertainties. Pretreatment and co-digestion promote feedstock accessibility to the microbial community involved in the AD process. However, choosing the type of pretreatment method depends on the feedstock type; hence, there should be a compromise between the cost and energy involved. There is no comprehensive information with regard to the financial feasibility of the enzyme pretreatment. The review showed that the investment cost in the production of commercial enzymes is the greatest obstacle hindering its industrial or full-scale application as a pretreatment method. Thus, future research should be geared towards investigating new approaches to reducing the cost of enzyme pretreatment cost so as to make it economically feasible for full-scale application. Furthermore, depending on the specific biogas application, different levels of cleaning or purification and upgrading technologies (absorption, adsorption, cryogenic, membrane, hydrate and biological separation) are required. These technologies differ in their overall efficiency, cost and energy requirements. Some of these technologies, such as cryogenic separation, hydrate separation and biotechnological methods, are novel emerging technologies that are still under development. However, cost minimization and gas quality requirements are the fundamental criteria for selecting an appropriate cleaning and upgrading technology. To further reduce biogas upgrading costs, the utilisation of separated CO2 for other purposes like algae production and enhanced oil recovery can offer additional benefits reinforcing the concept of circular bioeconomy. Since separated CO2 can be used for other beneficial purposes, it is, therefore, necessary that more research attention should be focused on the separation of CO2 and its quality as there is not much available information on it.
Author contributions
OAw, AA, and OAg contributed to the conception and design of the study. SA, OO, OL, and IF organised the database. OAw, AA, and OAg wrote the first draft of the manuscript. OO, MK, and IF reviewed and edited the manuscript. All authors contributed to the article and approved the submitted version.
Funding
This research was funded by the University of Technology Sydney through Strategic Research Support funding with grant number [324100.2200034].
Conflict of interest
The authors declare that the research was conducted in the absence of any commercial or financial relationships that could be construed as a potential conflict of interest.
Publisher’s note
All claims expressed in this article are solely those of the authors and do not necessarily represent those of their affiliated organizations, or those of the publisher, the editors and the reviewers. Any product that may be evaluated in this article, or claim that may be made by its manufacturer, is not guaranteed or endorsed by the publisher.
References
Abdallah, M. S., Hassaneen, F. Y., Faisal, Y., Mansour, M. S., Ibrahim, A. M., Abo-Elfadl, S., et al. (2019). Effect of Ni-Ferrite and Ni-Co-Ferrite nanostructures on biogas production from anaerobic digestion. Fuel 254, 115673. doi:10.1016/j.fuel.2019.115673
Abdeen, F. R. H., Mel, M., Jami, M. S., Ihsan, S. I., and Ismail, A. F. (2016). A review of chemical absorption of carbon dioxide for biogas upgrading. Chin. J. Chem. Eng. 24 (6), 693–702. doi:10.1016/j.cjche.2016.05.006
Abdelhafez, A. A., Li, J., and Abbas, M. H. H. (2014). Feasibility of biochar manufactured from organic wastes on the stabilization of heavy metals in a metal smelter contaminated soil. Chemosphere 117, 66–71. doi:10.1016/j.chemosphere.2014.05.086
Abdelsalam, E. M., and Samer, M. (2019). Biostimulation of anaerobic digestion using nanomaterials for increasing biogas production. Rev. Environ. Sci. Biotechnol. 18, 525–541. doi:10.1007/s11157-019-09505-0
Abdelwahab, T. A. M., Mohanty, M. K., Sahoo, P. K., and Behera, D. (2020). Impact of iron nanoparticles on biogas production and effluent chemical composition from anaerobic digestion of cattle manure. Biomass Convers. bior, 1–13.
Achinas, S., Krooneman, J., and Euverink, G. J. W. (2019). Enhanced biogas production from the anaerobic batch treatment of banana peels. Engineering 5, 970–978. doi:10.1016/j.eng.2018.11.036
Ács, N., Kovács, E., Wirth, R., Bagi, Z., Strang, O., Herbel, Z., et al. (2013). Changes in the archaea microbial community when the biogas fermenters are fed with protein-rich substrates. Bioresour. Technol. 131, 121–127. doi:10.1016/j.biortech.2012.12.134
Agbede, O. O., Aworanti, O. A., Osuolale, F. N., Adebayo, A. O., Ogunleye, O. O., Agarry, S. E., et al. (2019). Anaerobic conversion of biodegradable municipal solid waste to biogas: A review. LAUTECH J. Civ. Environ. Stud. 3 (1), 27–43. doi:10.36108/laujoces/9102/20(0230)
Agneessens, L. M., Ottosen, L. D. M., Voigt, N. V., Nielsen, J. L., de Jonge, N., Fischer, C. H., et al. (2017). In-situ biogas upgrading with pulse H2 additions: The relevance of methanogen adaption and inorganic carbon level. Bioresour. Technol. 233, 256–263. doi:10.1016/j.biortech.2017.02.016
Agyeman, F. O., and Tao, W. (2014). Anaerobic co-digestion of food waste and dairy manure: Effects of food waste particle size and organic loading rate. J. Environ. Manag. 133, 268–274. doi:10.1016/j.jenvman.2013.12.016
Ahlberg-Eliasson, K., and Westerholm, M. (2021). Isaksson S and Schnürer A Anaerobic digestion of animal manure and influence of organic loading rate and temperature on process performance, microbiology, and methane emission from digestates. Front. Energy Res. 9 (740314), 1–16.
Ahring, B. K., Biswas, R., Ahamed, A., Teller, P. J., and Uellendahl, H. (2015). Making lignin accessible for anaerobic digestion by wet-explosion pretreatment. Bioresour. Technol. 175, 182–188. doi:10.1016/j.biortech.2014.10.082
Ali, N., Chaudhary, B. L., and Panwar, N. L. (2014). The fungal pretreatment of maize cob heart and water hyacinth for enhanced biomethanation. Int. J. Green Energy 11 (1), 40–49. doi:10.1080/15435075.2012.740707
Allegue, L. B., and Hinge, J. (2014). Biogas upgrading: Evaluation of methods for H2S removal. Taastrup: Danish Technological Institute.
Allegue, L. B., and Hinge, J. (2012). J Report Biogas and bio-syngas upgrading. Taastrup: Danish Technological Institute.
Alvarez-Chavez, B. J., Godbout, S., Palacios-Rios, J. H., Le Roux, É., and Raghavan, V. (2020). Physical, chemical, thermal and biological pretreatment technologies in fast pyrolysis to maximize bio-oil quality: A critical review. Biomass Bioenergy 128, 105333. doi:10.1016/j.biombioe.2019.105333
Amin, F. R., Khalid, H., Zhang, H., u Rahman, S., Zhang, R., Liu, G., et al. (2017). Pretreatment methods of lignocellulosic biomass for anaerobic digestion. Amb. Express 7 (72), 72–12. doi:10.1186/s13568-017-0375-4
Andriani, D., Wresta, A., Atmaja, T. D., and Saepudin, A. (2014). A review on optimization production and upgrading biogas through CO2 removal using various techniques. Appl. Biochem. Biotechnol. 172, 1909–1928. doi:10.1007/s12010-013-0652-x
Angelidaki, I., Treu, L., Tsapekos, P., Luo, G., Campanaro, S., Wenzel, H., et al. (2018). Biogas upgrading and utilization: Current status and perspectives. Biotechnol. Adv. 36 (2), 452–466. doi:10.1016/j.biotechadv.2018.01.011
Antonopoulou, G., Vayenas, D., and Lyberatos, G. (2020). Biogas production from physicochemically pretreated grass lawn waste: Comparison of different process schemes. Molecules 25 (2), 296–314. doi:10.3390/molecules25020296
Appels, L., Assche, A. V., Willems, K., Degreve, J., Impe, J. V., and Dewil, R. (2011). Peracetic acid oxidation as an alternative pretreatment for the anaerobic digestion of waste activated sludge. Bioresour. Technol. 102, 4124–4130. doi:10.1016/j.biortech.2010.12.070
Ariunbaatar, J., Panico, A., Esposito, G., Pirozzi, F., and Lens, P. N. (2014). Pretreatment methods to enhance anaerobic digestion of organic solid waste. Appl. Energy 123, 143–156. doi:10.1016/j.apenergy.2014.02.035
Augelletti, R., Conti, M., and Annesini, M. C. (2007). Pressure swing adsorption for biogas upgrading. A new process configuration for the separation of biomethane and carbon dioxidefiguration for the separation of biomethane and carbon dioxide. J. Clean. Prod. 140, 1390–1398. doi:10.1016/j.jclepro.2016.10.013
Awe, O. W., Zhao, Y., Nzihou, A., Minh, D. P., and Lyczko, N. (2017). A review of biogas utilisation, purification and upgrading technologies. Waste Biomass Valoriz. 8, 267–283. doi:10.1007/s12649-016-9826-4
Aworanti, O. A., Agarry, S. E., and Ogunleye, O. O. (2017a). Biomethanization of the mixture of cattle manure, pig manure and poultry manure in Co-digestion with waste peels of pineapple fruit and content of chicken-gizzard - Part II: Optimization of process variables. Open Biotechnol. J. 11, 54–71. doi:10.2174/1874070701711010054
Baena-Moreno, F. M., Rodríguez-Galán, M., Vega, F., Alonso-Fariñas, B., Luis, F., Arenas, V., et al. (2019) Carbon capture and utilization technologies: A literature review and recent advances, Energy Sources, Part A Recovery, Util. Environ. Eff.,41:12, 1403–1433. doi:10.1080/15567036.2018.1548518
Baena-Moreno, F. M., Rodríguez-Galán, M., Vega, F., Vilches, L. F., Navarrete, B., and Zhang, Z. (2019). Biogas upgrading by cryogenic techniques. Environ. Chem. Lett. 17, 1251–1261. doi:10.1007/s10311-019-00872-2
Baeta, B. E. L., Lima, D. R. S., Adarme, O. F. H., Gurgel, L. V. A., and Aguino, S. F. (2016). Optimization of sugarcane bagasse autohydrolysis for methane production from hemicellulose hydrolyzates in a biorefinery concept. Bioresour. Technol. 200, 137–146. doi:10.1016/j.biortech.2015.10.003
Bahr, M., D ´az, I., Dominguez, A., Gonza ´lez Sa ´nchez, A., and Muñoz, R. (2014). Microalgal-biotechnology as a platform for an integral biogas upgrading and nutrient removal from anaerobic effluents. Environ. Sci. Technol. 48, 573–581. doi:10.1021/es403596m
Bahr, M., Díaz, I., Dominguez, A., Gonzaíez Sachez, A., and Muñ Oz, R. (2013). Microalgalbiotechnology as a platform for an integral biogas upgrading and nutrient removal from anaerobic effluents. Environ. Sci. Technol. 48, 573–581. doi:10.1021/es403596m
Bamdad, H., Hawboldt, K., and MacQuarrie, S. (2018). A review on common adsorbents for acid gases removal: Focus on biochar. Renew. Sustain Energy Rev. 81, 1705–1720. doi:10.1016/j.rser.2017.05.261
Baniamerian, H., Isfahani, P. G., Tsapekos, P., Alvarado-Morales, M., Shahrokhi, M., Vossoughi, M., et al. (2019). Application of nano-structured materials in anaerobic digestion: Current status and perspectives. Chemosphere 229, 188–199. doi:10.1016/j.chemosphere.2019.04.193
Barakat, A., Mayer-Laigle, C., Solhy, A., Arancon, R. A., De Vries, H., and Luque, R. (2014). Mechanical pretreatments of lignocellulosic biomass: Towards facile and environmentally sound technologies for biofuels production. RSC Adv. 4, 48109–48127. doi:10.1039/c4ra07568d
Barbusinski, K., Kalemba, K., Kasperczyk, D., Urbaniec, K., and Kozik, V. (2017). Biological methods for odor treatment—A review. J. Clean. Prod. 152, 223–241. doi:10.1016/j.jclepro.2017.03.093
Barua, S., Zakaria, B. S., Lin, L., and Dhar, B. R. (2019). Magnetite doped granular activated carbon as an additive for high-performance anaerobic digestion. Mat. Sci. Energy Technol. 2, 377–384. doi:10.1016/j.mset.2019.04.002
Baruah, J., Nath, B. K., Sharma, R., Kumar, S., Deka, R. C., Baruah, D. C., et al. (2018). Recent trends in the pretreatment of lignocellulosic biomass for value-added products. Front. Energy Res. 6, 141. doi:10.3389/fenrg.2018.00141
Bassani, I., Kougias, P. G., and Angelidaki, I. (2016). In-situ biogas upgrading in thermophilic granular UASB reactor: Key factors affecting the hydrogen mass transfer rate. Bioresour. Technol. 221, 485–491. doi:10.1016/j.biortech.2016.09.083
Basu, S., Khan, A. L., Cano-Odena, A., Liu, C., and Vankelecom, I. F. (2010). Membrane-based technologies for biogas separations. Chem. Soc. Rev. 39 (2), 750–768. doi:10.1039/b817050a
Battimelli, A., Torrijos, M., Moletta, R., and Delgenès, J. P. (2010). Slaughterhouse fatty waste saponification to increase biogas yieldfication to increase biogas yield. Bioresour. Technol. 101, 3388–3393. doi:10.1016/j.biortech.2009.12.043
Bauer, F., Persson, T., Hulteberg, C., and Tamm, D. (2013b). Biogas upgrading—Technology overview, comparison and perspectives for the future. Biofuels, Bioprod. Biorefin. 7:499–511. doi:10.1002/bbb.1423
Bauer, F., Hulteberg, C., and Persson Tobias, D. T. (2013a). Biogas upgrading—Review of commercial technologies. SGC Rapp. 270, 1–83.
Benizri, D., Dietrich, N., Labeyrie, P., and He´brard, G. (2019). Acompact, economic scrubber to improve farm biogas upgrading systems. Sep. Purif. Technol. 219, 169–179. doi:10.1016/j.seppur.2019.02.054
Biswas, R., Uellendahl, H., and Ahring, B. K. (2014). Wet explosion pretreatment of sugarcane bagasse for enhanced enzymatic hydrolysis. Biomass Bioenergy 61, 104–113. doi:10.1016/j.biombioe.2013.11.027
Bougrier, C., Albasi, C., Delgenès, J.-P., and Carrère, H. (2006). Effect of ultrasonic, thermal and ozone pre-treatments on waste activated sludge solubilisation and anaerobic biodegradabilityffect of ultrasonic, thermal and ozone pretreatment s on waste activated sludge solubilisation and anaerobic biodegradability. Chem. Eng. Process. Process Intensif. 45, 711–718. doi:10.1016/j.cep.2006.02.005
Brinkmann, T., Santonja, G. G., Yukseler, H., and RoudierSancho, S. L. D. (2016). Best Available Techniques (BAT) Reference document for common waste water and waste gas treatment/management systems in the chemical sector. Brussels: Publications Office of the European Union.
Cai, Y., Zheng, Z., Sch¨afer, F., Stinner, W., Yuan, X., Wang, H., et al. (2021). A review about pretreatment of lignocellulosic biomass in anaerobic digestion: Achievement and challenge in Germany and China. J. Clean. Prod. 299, 126885. doi:10.1016/j.jclepro.2021.126885
Canevesi, R. L. S., Andreassen, K. A., Da Silva, E. A., Borba, C. E., and Grande, C. A. (2018). Pressure swing adsorption for biogas upgrading with carbon molecular sieve. Ind. Eng. Chem. Res. 57, 8057–8067. doi:10.1021/acs.iecr.8b00996
Carlsson, M., Lagerkvist, A., and Morgan-Sagastume, F. (2012). The effects of substrate pre-treatment on anaerobic digestion systems: A review. Waste Manag. 32, 1634–1650. doi:10.1016/j.wasman.2012.04.016
Carrerre, H., Antonopoulou, G., Affes, R., Passos, F., Battimelli, A., Lyberatos, G., et al. (2016). Review of feedstock pretreatment strategies for improved anaerobic digestion: From lab-scale research to full-scale application. Bioresour. Technol. 199, 386–397. doi:10.1016/j.biortech.2015.09.007
Carrère, H., Dumas, C., Battimelli, A., Batstone, D., Delgenès, J., Steyer, J., et al. (2010). Pretreatment methods to improve sludge anaerobic degradability: A review. J. Hazard. Mat. 183, 1–15. doi:10.1016/j.jhazmat.2010.06.129
Carrère, H., Sialve, B., and Bernet, N. (2009). Improving pig manure conversion into biogas by thermal and thermo-chemical pretreatments. Bioresour. Technol. 100, 3690–3694. doi:10.1016/j.biortech.2009.01.015
Casals, E., Barrena, R., García, A., González, E., Delgado, L., Busquets-Fité, M., et al. Programmed iron oxide nanoparticles disintegration in anaerobic digesters boosts biogas production. (2014) Small J., 10.2801–2808. doi:10.1002/smll.201303703
Castellani, B., Rossi, F., Filipponi, M., and Nicolini, A. (2014). Hydrate-based removal of carbon dioxide and hydrogen sulphide from biogas mixtures: Experimental investigation and energy evaluations. Biomass and Bioenergy 70, 330–338. doi:10.1016/j.biombioe.2014.08
Cesaro, A., and Belgiorno, V. (2014). Pretreatment methods to improve anaerobic biodegradability of organic municipal solid waste fractions. Chem. Eng. J. 240, 24–37. doi:10.1016/j.cej.2013.11.055
Cesaro, A., and Belgiorno, V. (2013). Sonolysis and ozonation as pretreatment for anaerobic digestion of solid organic waste. Ultrason. Sonochem. 20, 931–936. doi:10.1016/j.ultsonch.2012.10.017
Cesaro, A., Naddeo, V., Amodio, V., and Belgiorno, V. (2012). Enhanced biogas production from anaerobic codigestion of solid waste by sonolysis. Ultrason. Sonochem. 19, 596–600. doi:10.1016/j.ultsonch.2011.09.002
Chaemchuen, S., Kabir, N. A., and Zhou, K. (2013). Metal–organic frameworks for upgrading biogas via CO2 adsorption to biogas green energy. Chem. Soc. Rev. 42, 9304–9332. doi:10.1039/c3cs60244c
Chang, S., Zhao, Z. L., Zheng, A. Q., Li, X. M., Wang, X. B., Huang, Z., et al. (2013). Effect of hydrothermal pretreatment on properties of bio-oil produced from fast pyrolysis of eucalyptus wood in a fluidized bed reactor. Bioresour. Technol. 138, 321–328. doi:10.1016/j.biortech.2013.03.170
Chandra, R., Hakeuchi, H., Hasegawa, T., and Vijay, V. K. (2015). A simple, custom-made osteotome for sinus floor elevation. Agric. Eng. Int. CIGR J. 17 (2), 93–96. doi:10.1563/AAID-JOI-D-12-00187
Charry Prada, I. D., Rivera-Tinoco, R., and Bouallou, C. (2020). Biogas industry: Novel acid gas removal technology using a superacid solvent. Process design, unit specification and feasibility study compared with other existing technologiesfication and feasibility study compared with other existing technologies. Chem. Eng. Res. Des. 154, 212–231. doi:10.1016/j.cherd.2019.12.007
Chen, S., Rotaru, A.-E., Liu, F., Philips, J., Woodard, T. L., Nevin, K. P., et al. (2014b). Carbon cloth stimulates direct interspecies electron transfer in syntrophic co-cultures. Bioresour. Technol. 173, 82–86. doi:10.1016/j.biortech.2014.09.009
Chen, X., Zhang, Y., Gu, Y., Liu, Z., Shen, Z., Chu, H., et al. (2014a). Enhancing methane production from rice straw by extrusion pretreatment. Appl. Energy 122, 34–41. doi:10.1016/j.apenergy.2014.01.076
Chen, Y., Yang, G., Sweeney, S., and Feng, Y. (2010). Household biogas use in rural China: A study of opportunities and constraints. Renew. Sustain Energy Rev. 14, 545–549. doi:10.1016/j.rser.2009.07.019
Cheng, J. J., and Timilsina, G. R. (2011). Status and barriers of advanced biofuel technologies: A review. Renew. Energy 36, 3541–3549. doi:10.1016/j.renene.2011.04.031
Christy, P. M., Gopinath, L., and Divya, D. (2013). A review on decomposition as a technology for 403 sustainable energy management. Int. J. Plant, Animal Environ. 404 Sci. 3 (4), 44–50.
Climenhaga, M. A., and Banks, C. J. (2008). Anaerobic digestion of catering wastes: Effect of micronutrients and retention time. Water Sci. Technol. 57 (5), 687–692. doi:10.2166/wst.2008.092
Comparetti, A., Febo, P., Greco, C., and Orlando, S. (2013). Current state and future of biogas and digestate production. Bulg. J. Agric. Sci. 19 (1), 1–14.
Converti, A., Oliveira, R. P. S., Torres, B. R., Lodi, A., and Zilli, M. (2009). Biogas production and valorization by means of a two-step biological process. Bioresour. Technol. 100, 5771–5776. doi:10.1016/j.biortech.2009.05.072
Dang, Y., Holmes, D. E., Zhao, Z., Woodard, T. L., Zhang, Y., Sun, D., et al. (2016). Enhancing anaerobic digestion of complex organic waste with carbon-based conductive materials. Bioresour. Technol. 220, 516–522. doi:10.1016/j.biortech.2016.08.114
Dasgupta, A., and Chandel, M. K. (2020). Enhancement of biogas production from organic fraction of municipal solid waste using alkali pretreatment. J. Mat. Cycles Waste Manage. 22, 757–767. doi:10.1007/s10163-020-00970-2
Dastyar, W., Azizi, S. M. M., Meshref, M. N., and Dhar, B. R. (2021). Powdered activated carbon amendment in percolate tank enhances high-solids anaerobic digestion of organic fraction of municipal solid waste. Process. Saf. Environ. Prot. 151, 63–70. doi:10.1016/j.psep.2021.04.033
Deepanraj, B., Sivasubramanian, V., and Jayaraj, S. (2017). Effect of substrate pretreatment on biogas production through anaerobic digestion of food waste. Int. J. Hydrogen Energy 42 (42), 26522–26528. doi:10.1016/j.ijhydene.2017.06.178
Deepanraj, B., Sivasubramanian, V., and Jayaraj, S. (2013). “Enhancement of biogas production by pretreatment: A review,” in 4th international conference on advances in energy research (Mumbai, India: Indian Institute of Technology Bombay).
Dell’Omo, P., and Froscia, L. S. (2018). Enhancing anaerobic digestion of wheat straw through multistage milling. Model., Meas. Control C 79, 127–132. doi:10.18280/mmc_c.790310
Den, W., Sharma, V. K., Lee, M., Nadadur, G., and Varma, R. S. (2018). Lignocellulosic biomass transformations via greener oxidative pretreatment processes: Access to energy and value-added chemicals. Front. Chem. 6, 141. doi:10.3389/fchem.2018.00141
Devlin, D., Esteves, S., Dinsdale, R., and Guwy, A. (2011). The effect of acid pretreatment on the anaerobic digestion and dewatering of waste activated sludgeffect of acid pretreatment on the anaerobic digestion and dewatering of waste activated sludge. Bioresour. Technol. 102, 4076–4082. doi:10.1016/j.biortech.2010.12.043
Dhadse, S., Kankal, N. C., and Kumari, B. (2012). Study of diverse methanogenic and non-methanogenic bacteria used for the enhancement of biogas production. Int. J. Life Sci. Biotechnol. Pharma Res. 1, 176–191.
Dhar, B. R., Nakhla, G., and Ray, M. B. (2012). Techno-economic evaluation of ultrasound and thermal pretreatments for enhanced anaerobic digestion of municipal waste activated sludge. Waste Manage 32, 542–549. doi:10.1016/j.wasman.2011.10.007
Di Maria, F., Gigliotti, G., Sordi, A., Micale, C., Zadra, C., and Massaccesi, L. (2013). Hybrid solid anaerobic digestion batch: Biomethane production and mass recovery from the organic fraction of solid waste. Waste Manag. Res. 31, 869–873. doi:10.1177/0734242x13477902
Diaz, A. B., de Souza Moretti, M. M., Bezerra-Bussoli, C., Nunes, C. D., Blandino, A., da Silva, R., et al. (2015). Evaluation of microwave-assisted pretreatment of lignocellulosic biomass immersed in alkaline glycerol for fermentable sugars production. Bioresour. Technol. 185, 316–323. doi:10.1016/j.biortech.2015.02.112
Dollhofer, V., Podmirseg, S. M., Callaghan, T. M., Griffith, G. W., and Fliegerová, K. (2015). “Anaerobic fungi and their potential for biogas production,” in Biogas science and technology (Berlin, Germany: Springer), 41–61.
Domingues, P. S., Pala, H., and Oliveira, N. S. (2021). Main biogas upgrading technologies. Int. J. Environ. Sci. Nat. Res. 27 (4), 1–8.
Dykstra, C. M., and Pavlostathis, S. G. (2017). Zero-valent iron enhances biocathodic carbon dioxide reduction to methane. Environ. Sci. Technol. 51, 12956–12964. doi:10.1021/acs.est.7b02777
Elbeshbishy, E., and Nakhla, G. (2011). Comparative study of the effect of ultrasonication on the anaerobic biodegradability of food waste in single and two-stage systems. Bioresour. Technol. 102, 6449–6457. doi:10.1016/j.biortech.2011.03.082
Ellacuriaga, M., Cascallana, J. G., González, R., and Gómez, X. (2021). High-solid anaerobic digestion: Reviewing strategies for increasing reactor performance. Environments 8 (80), 80–23. doi:10.3390/environments8080080
Elmashad, H. (2004). Effect of temperature and temperature fluctuation on thermophilic anaerobic digestion of cattle manure. Bioresour. Technol. 95, 191–201. doi:10.1016/j.biortech.2003.07.013
Eskicioglu, C., Monlau, F., Barakat, A., Ferrer, I., Kaparaju, P., Trably, E., et al. (2017). Assessment of hydrothermal pretreatment of various lignocellulosic biomass with CO2 catalyst for enhanced methane and hydrogen production. Water Res. 120, 32–42. doi:10.1016/j.watres.2017.04.068
Facchin, V., Cavinato, C., Fatone, F., Pavan, P., Cecchi, F., and Bolzonella, D. Effect of trace element supplementation on the mesophilic anaerobic digestion of foodwaste in batch trials: The influence of inoculum origin. Biochem. Eng. J. 2013, 70, 71–77. doi:10.1016/j.bej.2012.10.004
Faisal, S., Hafeez, F. Y., Zafar, Y., Majeed, S., Leng, X., Zhao, S., et al. A review on nanoparticles as boon for biogas producers—nano fuels and biosensing monitoring. Appl. Sci. 2019, 9(1), 59; 59–19. doi:10.3390/app9010059
Farghali, M., Andriamanohiarisoamanana, F. J., Ahmed, M. M., Kotb, S., Yamashiro, T., Iwasaki, M., et al. (2019). Impacts of iron oxide and titanium dioxide nanoparticles on biogas production: Hydrogen sulfide mitigation, process stability, and prospective challengesfide mitigation, process stability, and prospective challenges. J. Environ. Manag. 240, 160–167. doi:10.1016/j.jenvman.2019.03.089
Ferella, F., Puca, A., Taglieri, G., Rossi, L., and Gallucci, K. (2017). Separation of carbon dioxide for biogas upgrading to biomethane. J. Clean. Prod. 164, 1205–1218. doi:10.1016/j.jclepro.2017.07.037
Fernandez, M., Ramırez, M., Go ´mez, J. M., and Cantero, D. (2014). Biogas biodesulfurization in an anoxic biotrickling filter packed with open-pore polyurethane foamfilter packed with open-pore polyurethane foam. J. Hazard Mater 264, 529–535. doi:10.1016/j.jhazmat.2013.10.046
Fong, J. C. L. Y., Anderson, C. J., Xiao, G., Webley, P. A., and Hoadley, A. F. (2016). A Multi-objective optimisation of a hybrid vacuum swing adsorption and low-temperature post-combustion CO2 capture. J. Clean. Prod. 111, 193–203. doi:10.1016/j.jclepro.2015.08.033
Frigon, J. C., Mehta, P., and Guiot, S. R. (2012). Impact of mechanical, chemical and enzymatic pretreatment s on the methane yield from the anaerobic digestion of switchgrass. Biomass Bioenergy 36, 1–11. doi:10.1016/j.biombioe.2011.02.013
Frischknecht, R., and Jungbluth, N. (2010). Ecoinvent version 2.2. Available from https://ecoinvent.org/the-ecoinvent-database/data-releases/ecoinvent-version-2/# (Date accessed May 30th, 2023).
Funk, T., Gu, W., Friedrich, S., Wang, H., Gencic, S., Grahame, D. A., et al. (2004). ChemicallyDistinctNiSites in the A-cluster in subunit β of the acetyl-CoA decarbonylase/synthase complex from Methanosarcina thermophila: Ni L-edge absorption and X-ray magnetic circular dichroism analyses. J. Am. Chem. Soc. 126, 88–95. doi:10.1021/ja0366033
Gao, J., Hoshino, Y., and Inoue, G. (2020). Honeycomb-carbon-fiber supported amine-containing nanogel particles for CO2 capture using a rotating column TVSA. Chem. Eng. J. 383, 1-38.
Ghatak, M. D., and Mahanta, P. (2016). Biogas purification using chemical absorption. Int. J. Eng. Technol. 8 (3), 1600–1605.
Ghosh, A., and Bhattacharyya, B. C. (1999). Biomethanation of white rotted and brownrotted rice straw. Bioprocess. Eng. 20, 297–302. doi:10.1007/s004490050594
Grosser, A., Grobelak, A., Rorat, A., Courtois, P., Vandenbulcke, F., Lemière, S., et al. (2021). Effects of silver nanoparticles on performance of anaerobic digestion of sewage sludge and associated microbial communities. Renew. Energy 171, 1014–1025. doi:10.1016/j.renene.2021.02.127
Guedes, A., Amaro, H. M., and Malcata, F. X. (2011). Microalgae as sources of high added-value compounds—A brief review of recent work. Biotechnol. Prog. 27, 597–613. doi:10.1002/btpr.575
Gumisiriza, R., Hawumba, J. F., Okure, M., and Hensel, O. (2017). Biomass waste-to-energy valorisation technologies: A review case for banana processing in Uganda. Biotechnol. Biofuels. 10, 11. doi:10.1186/s13068-016-0689-5
Haghbakhsh, R., and Raeissi, S. (2019). Deep eutectic solvents for CO2 capture from natural gas by energy and exergy analyses. J. Environ. Chem. Eng. 7 (6), 103411. doi:10.1016/j.jece.2019.103411
Hakim, A., Marliza, T. S., Abu Tahari, N. M., Wan Isahak, R. W. N., Yusop, R. M., Hisham, W. M. M., et al. (2016). Studies on CO2 adsorption and desorption properties from various types of iron oxides (FeO, Fe2O3, and Fe3O4). Ind. Eng. Chem. Res. 55, 7888–7897. doi:10.1021/acs.iecr.5b04091
Hanak, D. P., Biliyok, C., and Manovic, V. (2015). Rate-based model development, validation and analysis of chilled ammonia process as an alternative CO2 capture technology for coal-fired power plants. Int. J. Greenh. Gas. Control 34, 52–62. doi:10.1016/j.ijggc.2014.12.013
Haosagul, S., Boonyawanich, S., and Pisutpaisal, N. (2019). Biomethane production from co-fermentation of agricultural wastes. Int. J. Hydrogen Energy 44, 5355–5364. doi:10.1016/j.ijhydene.2018.09.080
Hashiba, H., Sato, H. K., Yotsuhashi, S., Fuji, K., Sugiyama, M., and Nakano, Y. (2017). A broad parameter range for selective methane production with bicarbonate solution in electrochemical CO2 reduction. Sustain Energy Fuels 1, 1734–1739. doi:10.1039/c7se00352h
Hassaan, M. A., Pantaleo, A., Tedone, L., Elkatory, M. R., Ali, R. M., Nemr, A. E., et al. (2021). Enhancement of biogas production via green ZnO nanoparticles: Experimental results of selected herbaceous crops. Chem. Eng. Commun. 208, 242–255. doi:10.1080/00986445.2019.1705797
Hassan, R. (2014). Anaerobic digestion of sewage sludge and cattle manure for biogas production: Influence of co-digestion. Int. Water Technol. J. 4 (2), 107–113.
Hendrickson, M. R., Ho, N., Sedlak, M., and Ladisch, M. R. (2011). Optimization of pH controlled liquid hot water pretreatment of corn stover. Bioresour. Technol. 96 (2005), 1986–1993. doi:10.1016/j.biortech.2005.01.013
Hjorth, M., Gränitz, K., Adamsen, A. P., and Møller, H. B. (2011). Extrusion as a pretreatment to increase biogas production. Bioresour. Technol. 102, 4989–4994. doi:10.1016/j.biortech.2010.11.128
Horn, S. J., Estevez, M. M., Nielsen, H. K., Linjordet, R., and Eijsink, V. G. (2011). Biogas production and saccharification of Salix pretreated at different steam explosion conditionsfication of Salix pretreated at different steam explosion conditions. Bioresour. Technol. 102, 7932–7936. doi:10.1016/j.biortech.2011.06.042
Hospital-Benito, D., Lemus, J., Moya, C., Santiago, R., and Palomar, J. (2020). Process analysis overview of ionic liquids on CO2 chemical capture. Chem. Eng. J. 390, 124509. doi:10.1016/j.cej.2020.124509
Hosseinipour, S. A., and Mehrpooya, M. (2019). Comparison of the biogas upgrading methods as a transportation fuel. Renew. Energy 130, 641–655. doi:10.1016/j.renene.2018.06.089
Ismail, S., Saharuddin, M. Q., and Zahari, M. S. M. (2017). Upgraded seawater-alkaline pretreatment of lignocellulosic biomass for bio-methane production. Energy Procedia 138, 372–379. doi:10.1016/j.egypro.2017.10.390
Izumi, K., Okishio, Y. K., Nagao, N., Niwa, C., Yamamoto, S., and Toda, T. (2010). Effects of particle size on anaerobic digestion of food wasteffects of particle size on anaerobic digestion of food waste. Int. Biodeterior. Biodegr. 64, 601–608. doi:10.1016/j.ibiod.2010.06.013
Jagadabhi, P. S., Kaparaju, P., Väisänen, A., and Rintala, J. (2019). Effect of macro- and micro-nutrients addition during anaerobic mono-digestion of grass silage in leach-bed reactorsffect of macro-and micro-nutrients addition during anaerobicmono-digestionofgrasssilageinleach-bedreactors. Environ. Technol. 40,418–429. doi:10.1080/09593330.2017.1393462
Janssen, A. J. H., Lens, P. N. L., Stams, A. J. M., Plugge, C. M., Sorokin, D. Y., Muyzer, G., et al. (2009). Application of bacteria involved in the biological sulfur cycle for paper mill effluent purificationfluent purification. Sci. Total Environ. 407, 1333–1343. doi:10.1016/j.scitotenv.2008.09.054
Jiang, Y., Heaven, S., and Banks, C. J. (2012). Strategies for stable anaerobic digestion of vegetable waste. Renew. Energy 44, 206–214. doi:10.1016/j.renene.2012.01.012
Jönsson, O., Polman, E., Jensen, J. K., Eklund, R., Schyl, H., and Ivarsson, S. (2003). “Sustainable gas enters the European gas distribution system,” in World gas conference (Tokyo).
Kadam, R., and Panwar, N. L. (2017). Recent advancement in biogas enrichment and its applications. Renew. Sustain. Energy Rev. 73, 892–903. doi:10.1016/j.rser.2017.01.167
Kao, C. Y., Chiu, S. Y., Huang, T. T., Dai, L., Hsu, L. K., and Lin, C. S. (2012). Ability of a mutant strain of the microalga Chlorella sp. to capture carbon dioxide for biogas upgrading. Appl. Energ 93, 176–183. doi:10.1016/j.apenergy.2011.12.082
Kamusoko, R., Jingura, R. M., Parawira, W., and Sanyika, W. T. (2019). Comparison of pretreatment methods that enhance biomethane production from crop residues - a systematic review. Biofuel Res. J. 24, 1080–1089. doi:10.18331/BRJ2019.6.4.4
Kapoor, R., Ghosh, P., Kumar, M., and Vijay, V. K. (2019). Evaluation of biogas upgrading technologies and future perspectives: a review. Environ. Sci. Pollut. Res. 26, 11631–11661. doi:10.1007/s11356-019-04767-1
Karthikeyan, O. P., and Visvanathan, C. (2013). Bio-energy recovery from high-solid organic substrates by dry anaerobic bio-conversion processes: A review. Rev. Environ. Sci. Biotechnol. 12, 257–284. doi:10.1007/s11157-012-9304-9
Kasinath, A., Fudala-Ksiazek, S., Szopinska, M., Bylinskia, H., Artichowicz, W., Remiszewska-Skwarek, A., et al. (2021). Biomass in biogas production: Pretreatment and codigestion. Renew. Sustain. energy Rev. 150, 1–20. doi:10.1016/j.rser.2021.111509
Kaur, K., and Phutela, U. G. (2016). Enhancement of paddy straw digestibility and biogas production by sodium hydroxide-microwave pretreatment. Renew. Energy 92, 178–184. doi:10.1016/j.renene.2016.01.083
Khan, I. U., Othman, M. H., Hashim, H., Matsuura, T., Ismail, A., Rezaei-DashtArzhandi, M., et al. (2017). Biogas as a renewable energy fuel – a review of biogas upgrading, utilisation and storage. Energy Convers. Manag. 150, 277–294. doi:10.1016/j.enconman.2017.08.035
Khan, M. U., Tian En Lee, J., Bashir, M. A., Dissanayake, P. D., Sik Ok, Y., Tongc, Y. W., et al. (2021). Current status of biogas upgrading for direct biomethane use: A review. Renew. Sust. Energ. Rev. 149, 111343 . doi:10.1016/j.rser.2021.111343
Kim, D., Kim, J., and Lee, C. (2018). Science to Practice: IT Solutions to Drive Standardized report Recommendations for Abdominal Aortic Aneurysm Surveillance. Energies 11 (4), 865–869. doi:10.1016/j.jacr.2018.01.038
Kim, S., Bae, J., Choi, O., Ju, D., Lee, J., Sung, H, et al. (2014). A pilot scale two-stage anaerobic digester treating food waste leachate (FWL): Performance and microbial structure analysis using pyrosequencing. Process Biochem. 49 (2), 301–308. doi:10.1016/j.procbio.2013.10.022
Kim, W., Cho, K., Lee, S., and Hwang, S. (2013). Comparison of methanogenic community structure and anaerobic process performance treating swine wastewater between pilot and optimized lab scale bioreactors. Bioresour. Technol. 145, 48–56. doi:10.1016/j.biortech.2013.02.044
Korbag, I., Omer, S. M. S., Boghazala, H., and Abusasiyah, M. AA. (2020). Recent advances of biogas production and future perspective. London: Intech Open. doi:10.5772/intechopen.93231
Kostas, E. T., Beneroso, D., and Robinson, J. P. (2017). The application of microwave heating in bioenergy: A review on the microwave pre-treatment and upgrading technologies for biomass. Renew. Sust. Energy Rev. 77, 12–27. doi:10.1016/j.rser.2017.03.135
Kougias, P., Kotsopoulos, T., and Martzopoulos, G. (2010). Anaerobic co-digestion of pig waste with olive mill wastewater under various mixing conditions. Fresenius Environ. Bull. 19 (8), 1682–1686.
Kougias, P. G., Treu, L., Benavente, D. P., Boe, K., Campanaro, S., and Angelidaki, I. (2017). Ex-situ biogas upgrading and enhancement in different reactor systems. Bioresour. Technol. 225, 429–437. doi:10.1016/j.biortech.2016.11.124
Koupaie, E. H., Dahadha, S., Bazyar Lakeh, A. A., Azizi, A., and Elbeshbishy, E. (2019). Enzymatic pretreatment of lignocellulosic biomass for enhanced biomethane production-A review. J. Environ. Manag. 233, 774–784. doi:10.1016/j.jenvman.2018.09.106
Kudanga, T., and Le Roes-Hill, M. (2014). Laccase applications in biofuels production: Current status and future prospects. Appl. Microbiol. Biotechnol. 98 (15), 6525–6542. doi:10.1007/s00253-014-5810-8
Kumar, A. K., and Sharma, S. (2017). Recent updates on different methods of pretreatment of lignocellulosic feedstocks: A review. Bioresour. Bioprocess. 4 (1), 7. doi:10.1186/s40643-017-0137-9
Kumar, A., Miglani, P., Gupta, R., and Bhattacharya, T. (2006). Impact of Ni(II), Zn(II) and Cd(II) on biogassification of potato wastefication of potato waste. J. Environ. Biol. 27, 61–66.
Kumar, G., Sivagurunathan, P., Zhen, G., Kobayashi, T., Kim, S.-H., and Xu, K. (2017). Combined pretreatment of electrolysis and ultra-sonication towards enhancing solubilization and methane production from mixed microalgae biomass. Bioresour. Technol. 245, 196–200. doi:10.1016/j.biortech.2017.08.154
Latinwo, G. K., and Agarry, S. E. (2015). Modelling the kinetics of biogas production from mesophilic anaerobic co-digestion of cow dung with plantain peels. Int. J. Renew. Energy Dev. 4 (1), 55–63. doi:10.14710/ijred.4.1.55-63
Lebiocka, M., and Piotrowicz, A. (2012). Co-digestion of sewage sludge and organic fraction of municipal solid waste. A comparison between laboratory and technical scales. Environ. Prot. Eng. 38 (4), 157–162. doi:10.37190/epe120413
Lee, J. T., Khan, M. U., Dai, Y., Tong, Y. W., and Ahring, B. K. (2021). Influence of wet oxidation pretreatment with hydrogen peroxide and addition of clarified manure on anaerobic digestion of oil palm empty fruit bunches. Bioresour. Technol. 332 (2021), 125033. doi:10.1016/j.biortech.2021.125033
Lee, J. T., Khan, M. U., Tian, H., Ee, A. W., Lim, E. Y., Dai, Y., et al. (2020). Improving methane yield of oil palm empty fruit bunches by wet oxidation pretreatment: Mesophilic and thermophilic anaerobic digestion conditions and the associated global warming potential effects. Energy Convers. manage. 225, 113438. doi:10.1016/j.enconman.2020.113438
Lee, J. Y., Lee, S. H., and Park, H.-D. (2016). Enrichment of specific electro-ActiveMicroorganisms and enhancement of methane production by adding granular activated carbon in anaerobic reactors. Bioresour. Technol. 205, 205–212. doi:10.1016/j.biortech.2016.01.054
Li, H., Li, C., Liu, W., and Zou, S. (2012). Optimized alkaline pretreatment of sludgebefore anaerobic digestion. Bioresour. Technol. 123, 189–194. doi:10.1016/j.biortech.2012.08.017
Li, S., Cao, Y., Zhao, Z., and Zhang, Y. (2019). Regulating secretion of extracellular polymeric substances through dosing magnetite and zerovalent iron nanoparticles to affect anaerobic digestion mode. ACS Sustain. Chem. Eng. 7, 9655–9662. doi:10.1021/acssuschemeng.9b01252
Li, X., Dang, F., Zhnag, Y., Zou, D., and Yuan, H. (2015). Anaerobic digestion performance and mechanism of ammoniation pretreatment of corn stover. BioRes 10 (3), 5777–5790.
Li, Y., Jin, Y., Li, J., and Nie, Y. (2016). Enhanced nitrogen distribution and biomethanation of kitchen waste by thermal pretreatment. Renew. Energy 89, 380–388. doi:10.1016/j.renene.2015.12.029
Liew, Z. K., Chan, Y. J., Ho, Z. T., Yip, Y. H., Teng, M. C., Tuah, A. I., et al. (2021). Biogas production enhancement by co-digestion of empty fruit bunch (EFB) with palm oil mill effluent (POME): Performance and kinetic evaluation. Renew. Energy 179, 766–777. doi:10.1016/j.renene.2021.07.073
Lin, R., Xiang, S., Xing, H., Wei, Z., and Chen, B. (2019). Exploration of porous metal–organic frameworks for gas separation and purificationfication. Coord. Chem. Rev. 378:87–103. doi:10.1016/j.ccr.2017.09.027
Lin, Y., Liang, J., Zeng, C., Wang, D., and Lin, H. (2017). Anaerobic digestion of pulp and paper mill sludge pretreated by microbial consortium OEM1 with simultaneous degradation of lignocellulose and chlorophenols. Renew. Energy 108, 108–115. doi:10.1016/j.renene.2017.02.049
Lin, Y., Wang, D., Wu, S., and Wang, C. (2009). Alkali pretreatment enhances biogas production in the anaerobicdigestion of pulp and paper sludge. J. Hazard. Mat. 170, 366–373. doi:10.1016/j.jhazmat.2009.04.086
Lizasoain, J., Trulea, A., Gittinger, J., Kral, I., Piringer, G., Schedl, A, et al. (2017). Corn stover for biogas production: Effect of steam explosion pretreatment on the gas yields and on the biodegradation kinetics of the primary structural compounds. Bioresour. Technol. 244, 949–956. doi:10.1016/j.biortech.2017.08.042
Ljupka, A. (2010). Anaerobic digestion of food waste: Current status, problems and an alternative product. Submitted to the Department of Earth and Environmental Engineering, Columbia University. An M.S. Thesis.
Lombardi, L., and Francini, G. (2020). Techno-economic and environmental assessment of the main biogas upgrading technologies. Renew. Energy 156, 440–458. doi:10.1016/j.renene.2020.04.083
Luo, G., Johansson, S., Boe, K., Xie, L., Zhou, Q., and Angelidaki, I. (2012). Simultaneous hydrogen utilization and in situ biogas upgrading in an anaerobic reactor. Biotechnol. Bioeng. 109, 1088–1094. doi:10.1002/bit.24360
Luo, G., and Angelidaki, I. (2013). Co-Digestion of manure and whey for in situ biogas upgrading by the addition of H2: Process performance and microbial insights. Appl. Microbiol. Biotechnol. 97, 1373–1381. doi:10.1007/s00253-012-4547-5
Luo, G., Wang, W., and Angelidaki, I. (2014). A new degassing membrane coupled upflow anaerobic sludge blanket (UASB) reactor to achieve in-situ biogas upgrading and recovery of dissolved CH 4 from the anaerobic effluentflow anaerobic sludge blanket (UASB) reactor to achieve in situ biogas upgrading and recovery of dissolved CH4 from the anaerobic effluent. Appl. Energ 132, 536–542. doi:10.1016/j.apenergy.2014.07.059
Luo, T., Long, Y., Li, J., Meng, X., Mei, Z., Long, E., et al. (2015). Performance of a novel downward plug-flow anaerobic digester for methane production from chopped straw. BioRes 10 (1), 943–955. doi:10.15376/biores.10.1.943-955
Ma, J., Duong, T. H., Smits, M., Verstraete, W., and Carballa, M. (2011). Enhanced biomethanation of kitchen waste by different pretreatment s. Bioresour. Technol. 102, 592–599. doi:10.1016/j.biortech.2010.07.122
Mackuľak, T., Prousek, J., Švorc, Ľ., and Drtil, M. (2012). Increase of biogas production from pretreated hay and leaves using wood-rotting fungi. Chem. Pap. 66, 649–653. doi:10.2478/s11696-012-0171-1
Madigan, M. T., Martinko, J. M., Bender, K. S., and Buckley, D. H. (2014). Brock biology of microorganisms. 14th edn. Boston: Pearson.
Mahmoud, I., Hassan, M., Aboelenin, S. M., Soliman, M. M., Attia, H. F., Metwally, K. A., et al. (2022). Biogas manufacture from co-digestion of untreated primary sludge with raw chicken manure under anaerobic mesophilic environmental conditions. Saudi J. Biol. Sci. 29 (4), 2969–2977. doi:10.1016/j.sjbs.2022.01.016
Mahmudul, H. M., Rasul, M. G., Akbar, D., Narayanan, R., Mofijur, M., and jur, M. (2021). A comprehensive review of the recent development and challenges of a solar assisted biodigester system. Sci. Total Environ. 753, 1–24. doi:10.1016/j.scitotenv.2020.141920
Mankar, A. R., Pandey, A., Modak, A., and Pant, K. (2021). Pretreatment of lignocellulosic biomass: A review on recent advances. Bioresour. Technol. 334, 125235. doi:10.1016/j.biortech.2021.125235
Marañón, E., Castrillón, L., Quiroga, G., Fernández-Nava, Y., Gómez, L., and García, M. (2012). Co-digestion of cattle manure with food waste and sludge to increase biogas production. Waste Manag. 32, 1821–1825. doi:10.1016/j.wasman.2012.05.033
Martin, M. R., Fornero, J. J., Stark, R., Mets, L., and Angenent, L. T. (2013). A single-culture bioprocess of methanothermobacter thermautotrophicus to upgrade digester biogas by CO2-to-CH4 conversion with H2. Archaea 2013, 157529. doi:10.1155/2013/157529
Masebinu, S. O., Aboyade, A., and Muzenda, E. (2014). Enrichment of biogas for use as vehicular fuel: A review of the upgrading techniques. Int. J. Res. Chem.l Metall. Civil Eng. 1 (1), 89–98.
Mata-Alvarez, J., Dosta, J., Romero-Güiza, M. S., Fonoll, X., Peces, M., and Astals, S. (2014). A critical review on anaerobic co-digestion achievements between 2010 and 2013. Renew. Sustain Energy Rev. 36, 412–427. doi:10.1016/j.rser.2014.04.039
Matheri, A. N. (2016). “Modelling the kinetic of biogas production from Co-digestion of pig waste and grass clippings,” in Proceedings of the world congress on engineering 2016 vol II WCE (London, U.K.
Meier, L., Pe ´rez, R., Azo ´car, L., Rivas, M., and Jeison, D. (2015). Photosynthetic CO2 uptake by microalgae: An attractive tool for biogas upgrading. Biomass Bioenerg. 73, 102–109. doi:10.1016/j.biombioe.2014.10.032
Menardo, S., Airoldi, G., and Balsari, P. (2012). The effect of particle size and thermal pretreatment on the methane yield of four agricultural by-products. Bioresour. Technol. 104, 708–714. doi:10.1016/j.biortech.2011.10.061
Middelkoop, V., Coenen, K., Schalck, J., Annaland, M. V. S., and Gallucci, F. (2019). 3D printed versus spherical adsorbents for gas sweetening. Chem. Eng. J. 357, 309–319. doi:10.1016/j.cej.2018.09.130
Milán, Z., Villa, P., Sánchez, E., Montalvo, S., Borja, R., Ilangovan, K, et al. (2003). Effect of natural and modified zeolite addition on anaerobic digestion of piggery waste. Water Sci. Technol. 48, 263–269. doi:10.2166/wst.2003.0411
Mladenovska, Z., Hartmann, H., Kvist, T., Sales-Cruz, M., Gani, R., and Ahring, B. K. Thermal pretreatment of the solid fraction of manure: Impact on the biogas reactor performance and microbial community. Water Sci. Technol. 2006, 53, 59–67. doi:10.2166/wst.2006.236
Montalvo, S., Díaz, F., Guerrero, L., Sánchez, E., and Borja, R. (2005). Effect of particle size and doses of zeolite addition on anaerobic digestion processes of synthetic and piggery wastes. Process Biochem. 40, 1475–1481. doi:10.1016/j.procbio.2004.06.032
Montalvo, S., Guerrero, L., Borja, R., Sánchez, E., Milán, Z., Cortés, I, et al. (2012). Application of natural zeolites in anaerobic digestion processes: A review. Appl. Clay Sci. 58, 125–133. doi:10.1016/j.clay.2012.01.013
Montebello, A., Mora, M., Lo ´pez, L., Bezerra, T., Gamisans, X., Lafuente, J, et al. (2014). Aerobic desulfurization of biogas by acidic biotrickling filtration in a randomly packed reactorfiltration in a randomly packed reactor. J. Hazard Mater 280, 200–208. doi:10.1016/j.jhazmat.2014.07.075
Montingelli, M., Benyounis, K., Quilty, B., Stokes, J., and Olabi, A. (2017). Influence of mechanical pretreatment and organic concentration of Irish Brown seaweed for methane productionfluence of mechanical pretreatment and organic concentration of Irish Brown seaweed for methane production. Energy 118, 1079–1089. doi:10.1016/j.energy.2016.10.132
Morales-Polo, C. (2018). Del Mar Cledera-Castro, M., Moratilla Soria, B.Y. Reviewing the anaerobic digestion of food waste: From waste generation and anaerobic process to its perspectives. Appl. Sci. 8, 1804.1–35.
Moreira, M. A., Ribeiro, A. M., Ferreira, A. F. P., and Rodrigues, A. E. (2017). Cryogenic pressure temperature swing adsorption process for natural gas upgrade. Sep. Purif. Technol. 173, 339–356. doi:10.1016/j.seppur.2016.09.044
Moya, C., Santiago, R., Hospital-Benito, D., Lemus, J., and Palomar, J. (2022). Design of biogas upgrading processes based on ionic liquids. Chem. Eng. J. 428, 132103: 1–8. doi:10.1016/j.cej.2021.132103
Mudliar, S., Giri, B., Padoley, K., Satpute, D., Dixit, R., Bhatt, P., et al. (2010). Bioreactors for treatment of VOCs and odours – a review. J. Environ. Manag. 91, 1039–1054. doi:10.1016/j.jenvman.2010.01.006
Mulakhudair, A. R., Hanotu, J., and Zimmerman, W. (2016). Exploiting microbubble-microbe synergy for biomass processing: Application in lignocellulosic biomass pretreatment. Biomass Bioenergy 93, 187–193. doi:10.1016/j.biombioe.2016.07.014
Mulat, D. G., Huerta, S. G., Kalyani, D., and Horn, S. (2018). J Enhancing methane production from lignocellulosic biomass by combined steam-explosion pretreatment and bioaugmentation with cellulolytic bacterium Caldicellulosiruptor bescii. Biotechnol. Biofuels 11 (1), 1–15.
Mulat, D. G., Mosbæk, F., Ward, A. J., Polag, D., Greule, M., Keppler, F., et al. (2017). Exogenous addition of H2 for an in situ biogas upgrading through biological reduction of carbon dioxide into methane. Waste Manag. 68, 146–156. doi:10.1016/j.wasman.2017.05.054
Muller, H. W., and Trosch, W. (1986). Screening of white-rot fungi for biological pretreatment of wheat straw for biogas production. Appl. Microbiol. Biotechnol. 24, 180–185. doi:10.1007/bf00938793
Muñoz, R., Meier, L., Diaz, I., and Jeison, D. (2015). A review on the state-of-the-art of physical/chemical and biological technologies for biogas upgrading. Rev. Environ. Sci. Bio/Technol. 14, 727–759. doi:10.1007/s11157-015-9379-1
Mussgnug, J. H., Klassen, V., Schlüter, A., and Kruse, O. (2010). Microalgae as substrates for fermentative biogas production in a combined biorefinery concept. J. Biotechnol. 150, 51–56. doi:10.1016/j.jbiotec.2010.07.030
Mustafa, A. M., Poulsen, T. G., Xia, Y., and Sheng, K. (2017). Combinations of fungal and milling pretreatments for enhancing rice straw biogas production during solid-state anaerobic digestion. Bioresour. Technol. 224, 174–182. doi:10.1016/j.biortech.2016.11.028
M¨onch-Tegeder, M., Lemmer, A., and Oechsner, H. (2014). Enhancement of methane production with horse manure supplement and pretreatment in a full-scale biogas process. Energy 73, 523–530. doi:10.1016/j.energy.2014.06.051
Nair, R. B., Kabir, M. M., Lennartsson, P. R., Taherzadeh, M. J., and Horvath, I. S. (2018). Integrated process for ethanol, biogas and edible filamentous fungi-based animal feed production from dilute phosphoric acid-pretreated wheat straw. Appl. Biochem. Biotechnol. 184 (1), 48–62. doi:10.1007/s12010-017-2525-1
Neczaj, E., Bien, J., Grosser, A., Worwag, M., and Kacprzak, M. (2012). Anaerobic treatment of sewage sludge and grease trap sludge in continuous co-digestion. Glob. NEST J. 14 (2), 141–148.
Nguyen, L. N., Kumar, J., Vu, M. T., Mohammed, J. A. H., Pathak, N., Commault, A. S., et al. (2021). Biomethane production from anaerobic co-digestion at wastewater treatment plants: A critical review on development and innovations in biogas upgrading techniques. Sci. Total Environ. 765, 142753. doi:10.1016/j.scitotenv.2020.142753
Noorain, R., Kindaichi, T., Ozaki, N., Aoi, Y., and Ohashi, A. (2019). Biogas purification performance of new water scrubber packed with sponge carriersfication performance of new water scrubber packed with sponge carriers. J. Clean. Prod. 214, 103–111. doi:10.1016/j.jclepro.2018.12.209
Norrrahim, M. N. F., Ilyas, R. A., Nurazzi, N. M., Rani, M. S. A., Atikah, M. S. N., and Shazleen, S. S. (2021). Chemical pretreatment of lignocellulosic biomass for the production of bioproducts: An overview. Appl. Sci. Eng. Prog. 14 (4), 588–605.
Ogunleye, O. O., Aworanti, O. A., Agarry, S. E., and Aremu, M. O. (2016). Enhancement of animal waste biomethanation using fruit waste as co-substrate and chicken rumen as inoculums. Energy Sources- Part A, Recovery, Util. Environ. Eff. 38 (11), 1653–1660. doi:10.1080/15567036.2014.933286
Ometto, F., Quiroga, G., Pšenička, P., Whitton, R., Jefferson, B., and Villa, R. (2014). Impacts of microalgae pretreatment s for improved anaerobic digestion: Thermal treatment, thermal hydrolysis, ultrasound and enzymatic hydrolysis. Water Res. 65, 350–361. doi:10.1016/j.watres.2014.07.040
Ormaechea, P., Castrillón, L., Marañón, E., Fernández-Nava, Y., Negral, L., and Megido, L. (2017). Influence of the ultrasound pretreatment on anaerobic digestion of cattle manure, food waste and crude glycerinefluence of the ultrasound pretreatment on anaerobic digestion of cattle manure, food waste and crude glycerine. Environ. Technol. 38, 682–686. doi:10.1080/09593330.2016.1208278
Ossai, O. S. (2013). Comparative evaluation of qualitative and quantitative biogas production potential of oil palm fronds and co-digestion with cow dung. J. Energy Technol. Policy 3 (4), 25–33.
Palatsi, J., Viñas, M., Guivernau, M., Fernandez, B., and Flotats, X. (2011). Anaerobic digestion of slaughterhouse waste: Main process limitations and microbial community interactions. Bioresour. Technol. 102 (3), 2219–2227. doi:10.1016/j.biortech.2010.09.121
Panigrahi, S., Sharma, H. B., and Dubey, B. K. (2019). Overcoming yard waste recalcitrance through four different liquid hot water pretreatment techniques–Structural evolution, biogas production and energy balance. Biomass Bioenergy 127, 105268. doi:10.1016/j.biombioe.2019.105268
Parawira, W. (2012). Enzyme research and applications in biotechnological intensification of biogas production. Crit. Rev. Biotechnol. 32, 172–186. doi:10.3109/07388551.2011.595384
Passos, F., Ortega, V., and Donoso-Bravo, A. (2017). Thermochemical pretreatment and anaerobic digestion of dairy cow manure: Experimental and economic evaluation. Bioresour. Technol. 227, 239–246. doi:10.1016/j.biortech.2016.12.034
Passos, F., and Ferrer, I. (2015). Influence of hydrothermal pretreatment on microalgal biomass anaerobic digestion and bioenergy production. Water Res. 68, 364–373. doi:10.1016/j.watres.2014.10.015
Patinvoh, R. J., Osadolor, O. A., Chandolias, K., S´arv´ari Horv´ath, I., and Taherzadeh, M. J. (2017). Innovative pretreatment strategies for biogas production. Bioresour. Technol. 224, 13–24. doi:10.1016/j.biortech.2016.11.083
Patterson, T., Esteves, S., Dinsdale, R., and Guwy, A. (2011). An evaluation of the policy and techno-economic factors affecting the potential for biogas upgrading for transport fuel use in the UK. Energy Policy 39, 1806–1816. doi:10.1016/j.enpol.2011.01.017
Paudel, S. R., Banjara, S. P., Choi, O. K., Park, K. Y., Kim, Y. M., and Lee, J. W. (2017). Pretreatment of agricultural biomass for anaerobic digestion: Current state and challenges, 245. Bioresource Technology, 1194–1205.
Paul, S., Dutta, A., and Defersha, F. (2018). Mechanical and alkaline hydrothermal treated corn residue conversion into bio-energy and bio-fertilizer: A resource recovery concept. Energies 11 (3), 516. doi:10.3390/en11030516
Peng, H., Chen, H., Qu, Y., Li, H., and Xu, J. (2014). Bioconversion of different sizes of microcrystalline cellulose pretreated by microwave irradiation with/without NaOHfferentsizesofmicrocrystallinecellulosepretreated by microwave irradiation with/without NaOH. Appl. Energy 117, 142–148. doi:10.1016/j.apenergy.2013.12.002
Pengyu, D., Lianhua, L., Feng, Z., Xiaoying, K., Yongming, S., and Yi, Z. (2017). Comparison of dry and wet milling pretreatment methods for improving the anaerobic digestion performance of the Pennisetum hybrid. RSC Adv. 7 (21), 12610–12619. doi:10.1039/c6ra27822a
Pei, P., Zhang, C., Li, J., Chang, S., Li, S., Wang, J., et al. (2014). Optimization of NaOH pretreatment for enhancement of biogas production of banana pseudo-stem fiber using response surface methodology. BioRes 9 (3), 5073–5087. doi:10.15376/biores.9.3.5073-5087
Perendeci, N. A., Gokgol, S., and Orhon, D. (2018). Impact of alkaline H₂O₂ pretreatment on methane generation potential of Greenhouse crop waste under anaerobic conditions. Molecules 23, 1794. doi:10.3390/molecules23071794
Pérez-Elvira, S., Fdz-Polanco, M., Plaza, F., Garralón, G., and Fdz-Polanco, F. (2009). Ultrasound pretreatment for anaerobic digestion improvement. Water Sci. Technol. 60, 1525–1532. doi:10.2166/wst.2009.484
Pérez-Rodríguez, N., García-Bernet, D., and Domínguez, J. M. (2017). Extrusion and enzymatic hydrolysis as pretreatments on corn cob for biogas production. Renew. Energy 107, 597–603. doi:10.1016/j.renene.2017.02.030
Pilarski, K., Pilarska, A. A., Witaszek, K., Dworecki, Z., ˙Zelazi´nski, T., Ekielski, A., et al. (2016). The impact of extrusion on the biogas and biomethane yield of plant substrates. J. Ecol. Eng. 17 (4), 264–272. doi:10.12911/22998993/64563
Poulsen, T. G., and Adelard, L. (2016). Improving biogas quality and methane yield via co-digestion of agricultural and urban biomass wastes. Waste Manag. 54, 118–125. doi:10.1016/j.wasman.2016.05.020
Prakash, E. V., and Singh, L. P. (2013). Biomethanation of vegetable and fruit waste in Co-digestion process. Int. J. Emerg. Technol. Adv. Eng. 3 (6), 493–495.
Prandini, J. M., da Silva, M. L. B., Mezzari, M. P., Pirolli, M., Michelon, W., and Soares, H. M. (2016). Enhancement of nutrient removal from swine wastewater digestate coupled to biogas purification by microalgae Scenedesmus sppfication by microalgae Scenedesmus spp. Bioresour. Technol. 202, 67–75. doi:10.1016/j.biortech.2015.11.082
Qiao, W., Yan, X., Ye, J., Sun, Y., Wang, W., and Zhang, Z. (2013). Evaluation of biogas production from different biomass wastes with/without hydrothermal pretreatment. Renew. Energy 36 (12), 3313–3318. doi:10.1016/j.renene.2011.05.002
Quiñones, T. S., Plöchl, M., Budde, J., and Heiermann, M. (2009). Do hydrolytic enzymes enhance methane formation of agricultural feedstock? Int. Wissenschaftstagung Biogas Sci., 137–151.
Rafique, R., Poulsen, T. G., Nizami, A. S., Murphy, J. D., and Kiely, G. (2010). Effect of thermal, chemical and thermo-chemical pre-treatments to enhance methane productionffect of thermal, chemical and thermo-chemical pretreatment s to enhance methane production. Energy 35, 4556–4561. doi:10.1016/j.energy.2010.07.011
Raju, C. S., Sutaryo, S., Ward, A. J., and Møller, H. B. (2013). Effects of high-temperature isochoric pre-treatment on the methane yields of cattle, pig and chicken manureffects of high-temperature isochoric pretreatment on the methane yields of cattle, pig and chicken manure. Environ. Technol. 34, 239–244. doi:10.1080/09593330.2012.689482
Rani, P., Bansal, M., Pathak, V. V., and Ahmad, S. (2022). Experimental and kinetic studies on co-digestion of agrifood and sewage sludge for biogas production. J. Taibah Univ. Sci. 16 (1), 147–154. doi:10.1080/16583655.2022.2035928
Rani, P., Pathak, V. V., and Bansal, M. (2021). Co-digestion of wheat straw and animal manure pretreated with calcium hydroxide for biomethane production: Kinetic study. Curr. Res. Green Sustain. Chem. 4, 1–7. doi:10.1016/j.crgsc.2021.100145
Riva, M., Campestrini, M., Toubassy, J., Clodic, D., and Stringari, P. (2014). Solid-liquid-vapor equilibrium models for cryogenic biogas upgrading. Ind. Eng. Chem. Res. 53, 17506–17514. doi:10.1021/ie502957x
Rocamora, I., Wagland, S. T., Villa, R., Simpson, E. W., Fernández, O., and Bajón-Fernández, Y. (2020). Dry anaerobic digestion of organic waste: A review of operational parameters and their impact on process performance. Bioresour. Technol. 299 (122681), 1–11. doi:10.1016/j.biortech.2019.122681
Rodriguez, C., Alaswad, A., Benyounis, K. Y., and Olabi, A. G. (2017). Pretreatment techniques used in biogas production from grass. Renew. Sustain. Energy Rev. 68, 1193–1204. doi:10.1016/j.rser.2016.02.022
Rodriguez, G., Dorado, A. D., Fortuny, M., Gabriel, D., and Gamisans, X. (2014). Biotrickling filters for biogas sweetening: Oxygen transfer improvement for a reliable operationfilters for biogas sweetening: Oxygen transfer improvement for a reliable operation. Process Saf. Environ. 92, 261–268. doi:10.1016/j.psep.2013.02.002
Romero-Güiza, M. S., Peces, M., Astals, S., Benavent, J., Valls, J., and Mata-Alvarez, J. (2014). Implementation of a prototypal optical sorter as core of the new pretreatment configuration of a mechanical–biological treatment plant treating OFMSW through anaerobic digestion. Appl. Energy 135, 63–70. doi:10.1016/j.apenergy.2014.08.077
Romero-Güiza, M. S., Vila, J., Mata-Alvarez, J., Chimenos, J. M., and Astals, S. (2016). The role of additives on anaerobic digestion: A review. Renew. Sustain. Energy Rev. 58, 1486–1499. doi:10.1016/j.rser.2015.12.094
Rouches, E., Dignac, M., Zhou, S., and Carrere, H. (2017). Pyrolysis-GC-MS to assess the fungal pretreatment efficiency for wheat straw anaerobic digestion. J. Anal. Appl. Pyrolysis. 123, 409–418. doi:10.1016/j.jaap.2016.10.012
Rouches, E., Zhou, S., Steyer, J. P., and Carrere, H. (2016). White-rot fungi pretreatment of lignocellulosic biomass for anaerobic digestion: Impact of glucose supplementation. Process Biochem. 51, 1784–1792. doi:10.1016/j.procbio.2016.02.003
Ruggeri, B., Battista, F., Bernardi, M., Fino, D., and Mancini, G. (2015). The selection of pretreatment options for anaerobic digestion (AD): A case study in olive oil waste production. Chem. Eng. J. 259, 630–639. doi:10.1016/j.cej.2014.08.035
Ruggeri, B., Luongo Malave, A. C., Bernardi, M., and Fino, D. (2013b). Energy efficacy used to score organic refuse pretreatment processes for hydrogen anaerobic production. Waste Manage 33, 2225–2233. doi:10.1016/j.wasman.2013.06.024
Ruggeri, B., Sanfilippo, S., and Tommas, T. (2013a). Sustainability of (H2 + CH4) by anaerobic digestion via EROI approach and LCA evaluations, in: A. Singh, D. Pant, and S. I. Olsen (Eds.), Life Cycle Assessment of renewable Energy sources, Green Energy and Technology series, Springer, New York, 169–194.
Rughoonundun, H., Mohee, R., and Holtzapple, M. T. (2012). Influence of carbon-to-nitrogen ratio on the mixed-acid fermentation of wastewater sludge and pretreated bagasse. Bioresour. Technol. 112, 91–97. doi:10.1016/j.biortech.2012.02.081
Rybarczyk, P., Szulczyn ´ski, B., and Ge˛bicki, J. (2019). Treatment of malodorous air in biotrickling filters: A reviewfilters: A review. Biochem. Eng. J. 141, 146–162. doi:10.1016/j.bej.2018.10.014
Ryckebosch, E., Drouillon, M., and Vervaeren, H. Techniques for transformation of biogas to biomethane. Biomass Bioenergy. (2011) 35:1633– 1645. doi:10.1016/j.biombioe.2011.02.033
Sadhukhan, J., Martinez-Hernandez, E., Murphy, R. J., Ng, D. Ks., Hassim, M. H., Ng, K. S., et al. (2018). Role of bioenergy, biorefinery and bioeconomy in sustainable development: Strategic pathways for Malaysia. Renew. Sust. Energ. Rev. 81 (2), 1966–1987. doi:10.1016/j.rser.2017.06.007
Saha, B. C., Biswas, A., and Cotta, M. A. (2008). Microwave pretreatment, enzymatic saccharification and fermentation of wheat straw to ethanolfication and fermentation of wheat straw to ethanol. J. Biobased Mat. Bioenergy 2, 210–217. doi:10.1166/jbmb.2008.412
Sahito, A. R., and Mahar, R. B. (2014). Enhancing methane production from rice straw codigested with buffalo dung by optimising effect of substrate ratio, alkaline dose and particle size. J. Anim. Plant Sci. 24 (4), 1076–1084.
Santiago, R., Moya, C., and Palomar, J. (2020). Siloxanes capture by ionic liquids: Solvent selection and process evaluation. Chem. Eng. J. 401, 126078. doi:10.1016/j.cej.2020.126078
Santos, M. M. D., and Joppert, C. L. (2018). “Parte II – Biometano,” in Tecnologias de produção e uso de biogás e biometano. Editor S. T. Coelho (São Paulo: Instituto de Energia e Ambiente/USP/Synergia), 117–159.
Sarker, S., Lamb, J. J., Hjelme, D. R., and Lien, K. M. (2019). A review of the role of critical parameters in the design and operation of biogas production plants. Appl. Sci. 9(9), 1–38. doi:10.3390/app9091915
Savvas, S., Donnelly, J., Patterson, T., Chong, Z. S., and Esteves, S. R. (2017). Biological methanation of CO2 in a novel biofilm plug-flow reactor: A high rate and low parasitic energy process. Appl. Energy 202, 238–247. doi:10.1016/j.apenergy.2017.05.134
Schiavon, M., Ragazzi, M., Rada, E. C., and Torretta, V. (2015). Air pollution control through biotrickling filters: A review considering operational aspects and expected performancefilters: A review considering operational aspects and expected performance. Crit. Rev. Biotechnol. 36, 1143–1155. doi:10.3109/07388551.2015.1100586
Schimpf, U., Hanreich, A., Mähnert, P., Unmack, T., Junne, S., Renpenning, J., et al. (2013). Improving the efficiency of large-scale biogas processes: Pectinolytic enzymes accelerate the lignocellulose degradation. J. Sustain. Energy Environ. 4, 53–60.
Scholz, M., Melin, T., and Wessling, M. (2013). Transforming biogas into biomethane using membrane technology. Renew. Sustain Energy Rev. 17, 199–212. doi:10.1016/j.rser.2012.08.009
Schwede, S., Rehman, Z. U., Gerber, M., Theiss, C., and Span, R. (2013). Effects of thermal pretreatment on anaerobic digestion of Nannochloropsis salina biomassffects of thermal pretreatment on anaerobic digestion of Nannochloropsis salina biomass. Bioresour. Technol. 143, 505–511. doi:10.1016/j.biortech.2013.06.043
Seidl, P. R., and Goulart, A. K. (2016). Pretreatment processes for lignocellulosic biomass conversion to biofuels and bioproducts. Pretreat. Process. Lignocellul. biomass Convers. biofuels Bioprod. Curr. Opin. Green Sustain. Chem. 2, 48–53. doi:10.1016/j.cogsc.2016.09.003
Serejo, M., Posadas, E., Boncz, M., Blanco, S., Garcia-Encina, P., and Muñoz, R. (2015). Influence of biogas flow rate on biomass composition during the optimization of biogas upgrading in microalgal-bacterial processes. Environ. Sci. Technol. 49 (5), 3228–3236. doi:10.1021/es5056116
Shang, G., Zhang, C., Wang, F., Qiu, L., Guo, X., and Xu, F. (2019). Liquid hot water pretreatment to enhance the anaerobic digestion of wheat straw—effects of temperature and retention time. Environ. Sci. Pollut. Res. 26 (28), 29424–29434. doi:10.1007/s11356-019-06111-z
Shehu, M. S., Abdul Manan, Z., Rafidah, S., and Alwi, W. (2012). Optimization of thermo-alkaline disintegration of sewage sludge for enhanced biogas yield. Bioresour. Technol. 114, 69–74. doi:10.1016/j.biortech.2012.02.135
Shirkavand, E., Baroutian, S., Gapes, D. J., and Young, B. R. (2016). Combination of fungal and physicochemical processes for lignocellulosic biomass pretreatment–a review. Renew. Sustain. Energy Rev. 54, 217–234. doi:10.1016/j.rser.2015.10.003
Sibiya, N. T., Tesfagiogis, H., and Muzenda, E. (2018). “Application of different pre-treatment techniques for enhanced biogas production from lawn grass: a review,” in The nexus: energy, environment and climate change. Green energy and technology. Editors W. Leal Filho, and D. Surroop (Cham: Springer). doi:10.1007/978-3-319-63612-2_15
Singh, S., Harms, H., and Schlosser, D. (2014). Screening of ecologically diverse fungi for their potential to pretreat lignocellulosic bioenergy feedstock. Appl. Microbiol. Biotechnol. 98 (7), 3355–3370. doi:10.1007/s00253-014-5563-4
Singhal, S., Agarwal, S., Arora, S., Sharma, P., and Singhal, N. (2017). Upgrading techniques for transformation of biogas to bio-CNG: A review. Int. J. Energy Res. 41, 1657–1669. doi:10.1002/er.3719
Song, C., Liu, Q., Deng, S., Hailong, L., and Yutaka, K. (2019). Cryogenic-based CO2 capture technologies: State-of-the-art developments and current challenges. Renew. Sustain Energy Rev. 101, 265–278. doi:10.1016/j.rser.2018.11.018
Song, C., Liu, Q., Ji, N., Deng, S., Zhao, J., Li, Y., et al. (2018). Alternative pathways for efficient CO2 capture by hybrid processes: A review. Renew. Sustain Energy Rev. 82, 215–231. doi:10.1016/j.rser.2017.09.040
Song, C., Liu, Q., Ji, N., Deng, S., Zhao, J., Li, Y., et al. (2017). Reducing the energy consumption of membrane-cryogenic hybrid CO2 capture by process optimisation. Energy 124, 29–39. doi:10.1016/j.energy.2017.02.054
Song, Z., Liu, X., Yan, Z., Yuan, Y., and andLiao, Y. (2014). Comparison of seven chemical pretreatments of corn straw for improving methane yield by anaerobic digestion, PLoS ONE 9(4), 1–8. doi:10.1371/journal.pone.0093801
Soreanu, G., Be ´land, M., Falletta, P., Edmonson, K., Svoboda, L., AlJamal, M, et al. (2011). Approaches concerning siloxane removal from biogas—A review. Can. Biosyst. Eng. 53, 8.
Speda, J., Johansson, M. A., Odnell, A., and Karlsson, M. (2017). Enhanced bio-methane production rate and yield from lignocellulosic ensiled forage ley by in situ anaerobic digestion treatment with endogenous cellulolytic enzymes. Biotechnol. Biofuels. 10, 129. doi:10.1186/s13068-017-0814-0
Sreenivasulu, B., Gayatri, D. V., Sreedhar, I., and Raghavan, K. V. (2015). A journey into the process and engineering aspects of carbon capture technologies. Renew. Sustain Energy Rev. 41, 1324–1350. doi:10.1016/j.rser.2014.09.029
Srilatha, H. R., Krishna, N., Sudhakar Babu, K., and Madhukara, K. (1995). Fungal pretreatment of orange processing waste by solid-state fermentation for improved production of methane. Process Biochem. 30, 327–331. doi:10.1016/0032-9592(95)87041-5
St-Pierre, B., and Wright, A.-D. G. (2013). Metagenomic analysis of methanogen populations in three full-scale mesophilic anaerobic manure digesters operated on dairy farms in Vermont, USA. Bioresour. Technol. 138, 277–284. doi:10.1016/j.biortech.2013.03.188
Starr, K., Gabarrell, X., Villalba G Talens, L., and Lombardi, L. (2012). Life cycle assessment of biogas upgrading technologies. Waste Manag. 32 (5), 991–999. doi:10.1016/j.wasman.2011.12.016
Steinbach, D., Wüst, D., Zielonka, S., Krümpel, J., Munder, S., Pagel, M., et al. (2019). Steam explosion conditions highly influence the biogas yield of rice straw, Molecules 24(19)1–14. doi:10.3390/molecules24193492
Sträuber, H., Bühligen, F., Kleinsteuber, S., Nikolausz, M., and Porsch, K. (2015). Improved anaerobic fermentation of wheat straw by alkaline pretreatment and addition of alkali tolerant microorganisms. Bioengineering 2 (2), 66–93. doi:10.3390/bioengineering2020066
Struk, M., Kushkevych, I., and Vitezova, M. (2020). Biogas upgrading methods: Recent advancements and emerging technologies. Rev. Environ. Sci. Biotechnol. 19, 651–671. doi:10.1007/s11157-020-09539-9
Sun, Q., Li, H., Yan, J., Liu, L., Yu, Z., and Yu, X. (2015). Selection of appropriate biogas upgrading technology-a review of biogas cleaning, upgrading and utilisation. Renew. Sustain Energy Rev. 51, 521–532. doi:10.1016/j.rser.2015.06.029
Syed, M., Soreanu, G., Falletta, P., and Beland, M. (2006). Removal of hydrogen sulfide from gas streams using biological processes: A review. Can. Biosyst. Eng. 48, 2.1–2.14.
Tabatabaei, M., Aghbashlo, M., Valijanian, E., Kazemi Shariat Panahi, H., Nizami, A.-S., Ghanavati, H., et al. (2020). A comprehensive review on recent biological innovations to improve biogas production, part 1: Upstream strategies. Renew. Energy 146, 1204–1220. doi:10.1016/j.renene.2019.07.037
Taherdanak, M., Zilouei, H., and Karimi, K. (2016). The influence of dilute sulfuric acid pretreatment on biogas production from wheat plant. Int. J. Green Energy 13, 1129–1134. doi:10.1080/15435075.2016.1175356
Taherzadeh, M. J., and Karimi, K. (2008). Pretreatment of lignocellulosic wastes to improve ethanol and biogas production: A review. Int. J. Mol. Sci. 9, 1621–1651. doi:10.3390/ijms9091621
Tan, Y., Nookuea, W., Li, H., Thorin, E., and Yan, J. (2017b). Cryogenic technology for biogas upgrading combined with carbon capture-a review of systems and property impacts. Energy Proc. 142, 3741–3746. doi:10.1016/j.egypro.2017.12.270
Tanjore, D., and Richard, T. L. A systems view of lignocellulose hydrolysis. In Advancesin BioprocessTechnology; Springer: Berlin, Germany, 2015; 387–419.
Theuretzbacher, F., Lizasoain, J., Lefever, C., Saylor, M. K., Enquidanos, R., Weran, N., et al. (2015). Steam explosion pretreatment of wheat straw to improve methane yields: Investigation of the degradation kinetics of structural compounds during anaerobic digestion. Bioresour. Technol. 179, 299–305. doi:10.1016/j.biortech.2014.12.008
Tippayawong, N., Promwungkwa, A., and Rerkkriangkrai, P. (2010). Durability of a small agricultural engine on 414 biogas/diesel dual fuel operation. Iran. J. Sci. Technol. 34 (B2), 167.
Tsapekos, P., Kougias, P., and Angelidaki, I. (2015). Biogas production from ensiled meadow grass; effect of mechanical pretreatments and rapid determination of substrate biodegradability via physicochemical methods. Bioresour. Technol. 182, 329–335. doi:10.1016/j.biortech.2015.02.025
Uddin, M. N., Siddiki, S. Y. A., Mofijur, M., jur, M., Djavanroodi, F., Hazrat, M. A, et al. (2021). Prospects of bioenergy production from organic waste using anaerobic digestion technology: A mini review. Front. Energy Res. 9, 627093.
Ugwu, S. N., and Enweremadu, C. C. (2019). Effects of pre-treatments and co-digestion on biogas production from Okra wasteffffects of pretreatments and co-digestion on biogas production from Okra waste. J. Renew. Sustain. Energy 11, 013101. doi:10.1063/1.5049530
Umar, H. S., Firdausi, B. R., Sharifah, R. W. A., and Fadimtu, M. (2013). Biogas production through Co-digestion of palm oil mill effluent with cow manure. Niger. J. Basic Appl. Sci. 21 (1), 79–84.
Valo, A., Carrere, H., and Delgenes, J. P. (2004). Thermal, chemical and thermo-chemical pretreatment of waste activated sludge for anaerobic digestion. J. Chem. Technol. Biotechnol. 79, 1197–1203. doi:10.1002/jctb.1106
Van Denderen, M., Ineke, E., and Golombok, M. (2009). CO2 removal from contaminated natural gas mixtures by hydrate formation. Ind. Eng. Chem. Res. 48(12), 5802–5807. doi:10.1021/ie8017065
Vega, F., Cano, M., Gallego, L. M., Sara, C., Antonio, C. J., and Benito, N. R. Evaluation of MEA 5 M performance at different CO2 concentrations of flue gas tested at a CO2 capture lab-scale plantflue gas tested at a CO2 capture lab-scale plant. Energy Procedia (2017a) 114:6222–6228. doi:10.1016/j.egypro.2017.03.1760
Venturin, B., Frumi Camargo, A., Scapini, T., Mulinari, J., Bonatto, C., Bazoti, S., et al. (2018). Effect of pretreatments on corn stalk chemical properties for biogas production purposes. Bioresour. Technol. 266, 116–124. doi:10.1016/j.biortech.2018.06.069
Vivekanand, V., Olsen, E. F., Eijsink, V. G., and Horn, S. J. (2013). Effect of different steam explosion conditions on methane potential and enzymatic saccharification of birchffect of different steam explosion conditions on methane potential and enzymatic saccharification of birch. Bioresour. Technol. 127, 343–349. doi:10.1016/j.biortech.2012.09.118
Voelklein, M. A., O’ Shea, R., Jacob, A., and Murphy, J. D. (2017). Role of trace elements in single and two-stage digestion of food waste at high organic loading rates. Energy 121, 185–192. doi:10.1016/j.energy.2017.01.009
Vrbová, V., and Ciahotný, E. (2017). Upgrading biogas to biomethane using membrane separation. Energy Fuels 31, 9.
Wagner, A. O., Lackner, N., Mutschlechner, M., Prem, E. M., Markt, R., and Illmer, P. (2018). Biological pretreatment strategies for second-generation lignocellulosic resources to enhance biogas production, Energies 11(7), 1797–1814. doi:10.3390/en11071797
Wang, L., and Yang, R. T. (2014). New nanostructured sorbents for desulfurization of natural gas. Front. Chem. Sci. Eng. 8, 8–19. doi:10.1007/s11705-014-1411-4
Wang, Y. Z., Chen, X., Wang, Z., Zhao, J. F., Fan, T. T., Li, D. S., et al. (2012). Effect of low concentration alkali and ultrasound combination pretreatment on biogas production by stalk. Adv. Mater. Res. 383, 3434–3437. doi:10.4028/www.scientific.net/amr.383-390.3434
Wang, Y., Lin, C., Jing, L., Duan, N., Xue, L., and Fu, Y. (2013). Emergy analysis of biogas systems based on different raw materials. Sci. World J. 2013, 1–9. doi:10.1155/2013/415812
Ward, A. J., Lewis, D. M., and Green, F. B. (2014). Anaerobic digestion of algae biomass: A review. Algal Res. 5, 204–214. doi:10.1016/j.algal.2014.02.001
Weber, B., Sandoval-Moctezuma, A. C., Estrada-Maya, A., Martínez-Cienfuegos, I. G., and Dur´an-García, M. D. (2020). Agave bagasse response to steam explosion and anaerobic treatment. Biomass Convers. biorefin. 10 (4), 1279–1289. doi:10.1007/s13399-020-00619-y
Wei, S. (2016). The application of biotechnology on the enhancing of biogas production from lignocellulosic waste. Appl. Microbiol. Biotechnol. 100, 9821–9836. doi:10.1007/s00253-016-7926-5
Wellinger, A., Murphy, J. D., and Baxter, D. (2013). The biogas handbook: Science, production and applications. Elsevier, 424.
Wiheeb, A., Helwani, Z., Kim, J., and Othman, M. (2016). Pressure swing adsorption technologies for carbon dioxide capture. Sep. Purif. Rev. 45 (2), 108–121. doi:10.1080/15422119.2015.1047958
Wikandari, R., Nguyen, H., Millati, R., Niklasson, C., and Taherzadeh, M. J. (2014). Improvement of biogas production from orange peel waste by leaching of limonene. Biomed. Res. Int. 494182, 6.
Wu, C., Zhou, H., Yang, F., Zhang, Y., and Gao, F. (2015b). Microwave pretreatment of switch grass leaf and stem fractions to increase methane production. BioRes 10 (3), 3922–3933.
Wu, L. J., Kobayashi, T., Li, Y. Y., and Xu, K. Q. (2015a). Comparison of single-stage and temperature-phased two-stage anaerobic digestion of oily food waste. Energy Convers. Manag. 106, 1174–1182. doi:10.1016/j.enconman.2015.10.059
Xu, S., He, C., Luo, L., Lü, F., He, P., and Cui, L. (2015). Comparing activated carbon ofdifferent particle sizes on enhancing methane generation in upflow anaerobicdigester. Bioresour. Technol. 196, 606–612. doi:10.1016/j.biortech.2015.08.018
Yadvika, S., Sreekrishnan, T. R., Kohli, S., and Rana, V. (2004). Enhancement of biogas production from solid substrates using different techniques– Bioresource Technology, 1–10.
Yang, D., Wei, S. J., Wen, Q. M., and Zhang, X. J. (2004). Comparison of pretreatments for lignocellulosic biomass. Adv. Mat. Res. 1008-1009, 111–115. doi:10.4028/www.scientific.net/amr.1008-1009.111
Yang, Z., Sun, H., Zhou, L., Arhin, S. G., Papadakis, V. G., Goula, M. A., et al. (2022). Bioaugmentation with well-constructed consortia can effectively alleviate ammonia inhibition of practical manure anaerobic digestion. Water Res. 215, 118244. doi:10.1016/j.watres.2022.118244
Yin, C., Shen, Y., Yu, Y., Yuan, H., Lou, Z., and Zhu, N. (2019). In-situ biogas upgrading by a stepwise addition of ash additives: Methanogen adaption and CO2 sequestration. Bioresour. Technol. 282, 1–8. doi:10.1016/j.biortech.2019.02.110
Yoo, M., Han, S. J., and Wee, J. H. (2013). Carbon dioxide capture capacity of sodium hydroxide aqueous solution. J. Environ. Manag. 114, 512–519. doi:10.1016/j.jenvman.2012.10.061
Youngsukkasem, S., Rakshit, S., and Taherzadeh, M. (2011). Biogas production by encapsulated methane-producing bacteria. BioResources 7, 56–65.
Yuan, H., Zhang, Y., Li, X., Meng, Y., Liu, C., Zou, D., et al. (2014). Effects of ammoniation pretreatment at low moisture content on anaerobic digestion performance of rice straw. BioRes 9 (4), 6707–6718. doi:10.15376/biores.9.4.6707-6718
Yu, B., Xu, J., Yuan, H., Lou, Z., Lin, J., and Zhu, N. (2014). Enhancement of anaerobic digestion of waste activated sludge by electrochemical pretreatment. Fuel 130, 279–285. doi:10.1016/j.fuel.2014.04.031
Zaidi, A. A., RuiZhe, F., Shi, Y., Khan, S. Z., and Mushtaq, K. (2018). Nanoparticles augmentation on biogas yield from microalgal biomass anaerobic digestion. Int. J. Hydrog. Energy 43, 14202–14213. doi:10.1016/j.ijhydene.2018.05.132
Zhang, C., Su, H., Baeyens, J., and Tan, T. (2014). Reviewing the anaerobic digestion of food waste for biogas production. Renew. Sustain. Energy Rev. 38, 383–392. doi:10.1016/j.rser.2014.05.038
Zhang, H., Ning, Z., Khalid, H., Zhang, R., Liu, G., and Chen, C. (2018). Enhancement of methane production from cotton stalk using different pretreatment techniques. Sci. Rep. 8, 3463. doi:10.1038/s41598-018-21413-x
Zhang, J., Loh, K. C., Lee, J., Wang, C. H., Dai, Y., and Wah Tong, Y. (2017). Three-stage anaerobic co-digestion of food waste and horse manure. Sci. Rep. 7, 1269 (2017). doi:10.1038/s41598-017-01408-w
Zhang, L., Lee, Y. W., and Jahng, D. (2011). Anaerobic co-digestion of food waste and piggery wastewater: Focusing on the role of trace elements. Bioresour. Technol. 102, 5048–5059. doi:10.1016/j.biortech.2011.01.082
Zhang, L., Lim, E. Y., Loh, K.-C., Ok, Y. S., Lee, J.-T., Shen, Y., et al. (2020). Biochar enhanced thermophilic anaerobic digestion of food waste: Focusing on biochar particle size, microbial community analysis and pilot-scale application. Energy Convers. manage. 209, 112654. doi:10.1016/j.enconman.2020.112654
Zhang, Z., Zhang, G., Li, W., Li, C., and Xu, G. (2016). Enhanced biogas production from sorghum stem by co-digestion with cow manure. Int. J. Hydrogen Energy 41 (21), 9153–9158. doi:10.1016/j.ijhydene.2016.02.042
Zhen, G., Lu, X., Kato, H., Zhao, Y., and Li, Y. Y. (2017). Overview of pretreatment strategies for enhancing sewage sludge disintegration and subsequent anaerobic digestion: Current advances, full-scale application and future perspectives. Renew. Sustain Energy Rev. 69, 559–577. doi:10.1016/j.rser.2016.11.187
Zheng, Y., Zhao, J., Xu, F., and Li, Y. (2014). Pretreatment of lignocellulosic biomass for enhanced biogas production. Prog. Energy Combust. Sci. 42, 35–53. doi:10.1016/j.pecs.2014.01.001
Zhou, J., Yan, B., Wang, Y., Yong, X., Yang, Z., Jia, H., et al. (2016). Effect of steam explosion pretreatment on the anaerobic digestion of rice straw. RSC Adv. 6 (91), 88417–88425. doi:10.1039/c6ra15330e
Zhou, J., Yang, J., Qing, Yu., Xiaoyu, Y., Xie, X., Zhang, L., et al. (2017). Different organic loading rates on the biogas production during the anaerobic digestion of rice straw: A pilot study. Bioresour. Technol. 244 (1), 865–871. doi:10.1016/j.biortech.2017.07.146
Zhu, S., Wang, C., Jin, S., and Wu, G. (2006). Microwave-assisted alkali pre-treatment of wheat straw and its enzymatic hydrolysis. Hydrolysis 94 (3), 437–442. doi:10.1016/j.biosystemseng.2006.04.002
Keywords: anaerobic digestion, biogas, biomethane, upgrading, calorific value, contaminants, pretreatment, co-digestion
Citation: Aworanti OA, Ajani AO, Agbede OO, Agarry SE, Ogunkunle O, Laseinde OT, Kalam MA and Fattah IMR (2023) Enhancing and upgrading biogas and biomethane production in anaerobic digestion: a comprehensive review. Front. Energy Res. 11:1170133. doi: 10.3389/fenrg.2023.1170133
Received: 20 February 2023; Accepted: 17 May 2023;
Published: 23 June 2023.
Edited by:
Furkan Ahmad, Hamad bin Khalifa University, QatarReviewed by:
Sikandar Abdul Qadir, Hamad bin Khalifa University, QatarBharath Gandu, University of Delhi, India
Copyright © 2023 Aworanti, Ajani, Agbede, Agarry, Ogunkunle, Laseinde, Kalam and Fattah. This is an open-access article distributed under the terms of the Creative Commons Attribution License (CC BY). The use, distribution or reproduction in other forums is permitted, provided the original author(s) and the copyright owner(s) are credited and that the original publication in this journal is cited, in accordance with accepted academic practice. No use, distribution or reproduction is permitted which does not comply with these terms.
*Correspondence: Oluseye Omotoso Agbede, b29hZ2JlZGVAbGF1dGVjaC5lZHUubmc=; Oyetola Ogunkunle, b29ndW5rdW5sZUB1ai5hYy56YQ==; Islam Md Rizwanul Fattah, SXNsYW1NZFJpendhbnVsLkZhdHRhaEB1dHMuZWR1LmF1