- Department of Chemical Engineering, University of Benin, Benin City, Nigeria
The synthesis of biolubricants from renewable feedstocks is currently gaining attention. Over 95% of the market is comprised of lubricants made from petroleum. Due to their limited biodegradability and high eco-toxicity, lubricants generated from petroleum constitute a significant environmental hazard. As pollution levels increase and oil supplies decline, there is a rising need to develop biobased alternatives. Manufacturing cleaner fuel products will mitigate the negative environmental impact of greenhouse gas emissions, which contribute to global warming. Jatropha curcas seed oil is an efficient renewable feedstock for biolubricant synthesis. This study optimized the process variables on biodegradable lubricant basestock production from J. curcas seed oil. A central composite design was used to maximize the chemical interaction between J. curcas methyl ester and ethylene glycol (EG) as a polyol. A total of 20 experimental runs were done to examine reaction temperature, time, and the ethylene glycol to fatty acid methyl ester (EG-to-FAME) molar ratio. A statistical model indicated that the maximum conversion yield of jatropha biolubricant (JBL) would be 92.48% under the following optimum reaction conditions: 128.95°C, 202.40 min, and ethylene glycol to fatty acid methyl ester (EG-to-FAME) molar ratio of 3.87:1. At these optimum conditions, an average jatropha biolubricant (JBL) yield of 94.12% was achieved under experimental conditions, and this value was well within the range predicted (92.48%) by the model. The quadratic model predicted the biolubricant output (R2 = 0.9919). The synthesized biolubricant met the requirements of Viscosity Grade 46 (ISO VG 46) set by the International Organization for Standardization.
1 Introduction
As the price of fossil fuels has risen, there has been a steady growth in worldwide demand for alternate sources of motor oil, such as biolubricant. According to the International Energy Outlook 2021 study, world fuel consumption will rise from 98 million barrels per day in 2015 to 118 million in 2030, although gasoline prices have consistently surpassed their expected value. (IEO., 2021). Global research has discovered a potential substitute for mineral oil, biodegradable lubricants derived from oil-bearing plants. However, with over $34.2 billion (2017) spent on the importation of refined crude oil, which is the raw material for lubricating oil, there is a constraint on the economy’s stability (Bhattacharya et al., 2016).
When one thinks about lubricants, the first thing that comes to mind is petroleum oil. Petroleum oil components continue to make up the majority of lubricants. The lubrication fraction derived from crude petroleum is the primary source of practically all lubricants. Although petroleum-based lubricants have many important physical features, they are also non-renewable and damaging to the environment. With increased environmental concerns, bio-based lubricants can substitute traditional petroleum-based lubricants (Panchal et al., 2017).
Biolubricants from renewable resources such as vegetable oils and animal fats are an excellent replacement for conventional, petroleum-based lubricants (Salih et al., 2021). The limited availability of fossil fuels and a heightened awareness of the environmental damage caused by petroleum-based oils used as industrial lubricants are significant factors in the continued push toward adopting more ecologically friendly vegetable oil as lubrication basestock (Bermejo, 2014; Sigar et al., 2009). Due to the existence of a closed carbon cycle, it also helps to reduce CO2 emissions. There is a significant concern about using edible oils in biolubricant production, hence research into the potential of using non-edible oils and waste products from vegetable oil refining as a sustainable feedstock for biolubricant production (Woma et al., 2019). Fatty acids polyol esters of vegetable oils (triglyceride) are unprocessed natural feedstock with strong lubricity potential that might be modified (by transesterification) into an eco-friendly, fast, biodegradable, and renewable lubricant base stock (Wagner et al., 2001).
Over the last 3 decades, the global output of oil seeds has increased. This seems to be connected to the growing demand for oil seed products and derivatives. The majority of seeds are grown mainly for their oil and for human use. The oil from most seeds is edible (for example, groundnut oil, fluted pumpkin seed oil, and soya bean seed oil), and approximately 80% of the world’s vegetable oil production is for human consumption, while the remaining 20% is shared between animal agriculture and chemical processing industries (biofuel production) (Baud, 2018). Due to the high need for oil for both consumer and industrial purposes, hence the need for non-edible oil as biolubricant feedstock. Various seed oils have been described in response to the expanding use of vegetable oils. The great majority, however, have yet to be thoroughly investigated, and this is especially true for Jatropha seed, which belongs to this category of underutilized plant species. One of the reasons why non-edible oils have not been extensively used to produce biolubricant is because of the free fatty acid (FFA) content of these oils. How well an oil seed fits into the growing industry depends on how it can be used, how fast it can be made, and what processing technology is available.
Fatty acid methyl esters (FAMEs) and polyhydric alcohol are usually used in a transesterification procedure to synthesize biolubricants. A transesterification process may be carried out using an acid catalyst, a base catalyst, or an enzyme (Ayoub et al., 2016). The transesterification of methyl esters from vegetable oils using ethylene glycol (E.G.,) as the polyol has been the subject of much research. However, there is a dearth of model-based research in this field.
This study aims to optimize the process variables on biolubricant production using Jatropha oil as an alternative lubricant source to petroleum-based lubricant (Society of Automotive Engineering, SAE40) by employing response surface methodology.
The following goals were used to achieve the study’s aim.
1. Analyze the chemical and physical properties of locally sourced Jatropha curcas seed oil.
2. Synthesize a bio-based diesel (Fatty acid methyl ester) utilizing J. curcas seed oil as the primary raw material.
3. Produce a bio-based lubricant (tri-ester polyol) utilizing the bio-based diesel (Fatty acid methyl ester) synthesized from jatropha oil feedstock.
4. Optimize Process Variables (mole ratio, reaction temperature, and reaction time) utilizing response surface methodology (RSM) to produce biolubricant from J. curcas seed oil.
To improve the efficiency of many different processes, RSM has been used in areas like biodiesel production, adsorption processes, catalyst development, and oleochemical synthesis (Jiang & Niu, 2011). However, studies on optimizing jatropha biolubricant have received little attention, and publications on improving the process are limited. (Sun et al., 2011). Furthermore, to our knowledge, the process is yet to be optimized using a statistical approach such as response surface methodology, even though Jatropha seed has been used as a starting material for biolubricant synthesis via transesterification reactions. (Gunam Resul et al., 2012).
In this research, we provide a unique synthetic strategy for transesterification reaction to optimize the reaction process variables to generate a high yield of biolubricant. Response surface methodology (RSM) was used to investigate three process variables: temperature, mole ratio, and time. A response-surface methodology (RSM) design was used to establish a connection between these three process factors and the outcome (JBL yield percentage). Also, the product’s physicochemical characteristics and Fourier transform infrared (FTIR) spectrum were investigated.
2 Materials and methods
2.1 Materials
The jatropha seed was obtained from Agri-Energy limited, Kano state, Nigeria. High purity Sulphuric acid and sodium hydroxide were produced by CDH, New Delhi, India. A Pensky Martins SYD-261 flash point tester, was used. Fourier-transform infrared spectroscopy (FTIR) was measured using the FTIR-8400S instrument (Shimadzu, Japan).
2.2 Extraction of oil from jatropha seed
The Jatropha seeds were crushed and wrapped in a white cloth before they were soaked in hexane for 3 days in a sealed bucket. The extract was then filtered and collected. Then, new hexane was used to wash the cloth that held the crushed Jatropha seeds to get more oil out of them. Jatropha oil was extracted, and the hexane was distilled out of it before the crude oil extract was collected in a beaker (Ocholi et al., 2021).
2.3 Pretreatment
The pretreatment process was utilized owing to the high acid value of the Jatropha oil. This method helped to eliminate trapped particles/impurities in the oil during the extraction process or due to exposure to air. The presence of contaminants will be a concern during esterification and transesterification processes, resulting in a poor yield of biolubricant. The pretreatment process was done at a high temperature.
300 g of J. curcas seed oil was weighed in a glass beaker and placed on a heating mantle. The temperature is set to 100°C and agitated for an hour at a speed of 500 rpm. It was allowed to cool for 15 min and filtered to eliminate solid contaminants (Mu’azu et al., 2013).
2.4 Oil esterification
This was necessary to minimize the oil’s free fatty acid content since the high acid value detected may result in significant saponification. The oil’s high FFA level was decreased via esterification with methanol using sulphuric acid as a catalyst. The processed oil was weighed and placed in a round bottom flask, and a conical flask was filled with 25% w/w methanol and 1% w/w sulphuric acid. The methanol acid combination and the oil sample were put on a heating mantle and heated to 60°C. They were then combined in the round bottom flask, with a magnetic stirrer added. The stirrer was adjusted to 700 rpm, and the bath temperature was between 60°C and 65°C. The timing was initiated at this point. After 60 min, the sample was withdrawn using a picking pipette and titrated against a 0.05 N solution of KOH to estimate the free fatty acid content of the oil. (Bilal., 2013).
2.5 Double transesterification
Triglyceride transesterification decreases viscosity and creates fatty acid alkyl esters and glycerol. The glycerol layer settles toward the bottom of the reaction vessel. Extra methanol (100%) is required to drive the reaction forward, yielding corresponding methyl esters and glycerol (Hawash et al., 2023). The synthesis of a biolubricant involves a double transesterification process as seen in Figure 1: the first produces an intermediate product, the methyl ester of the oil, and the second uses the methyl ester as a reactant to create the desired outcome. The two procedures are as follows.
2.6 Transesterification of jatropha methyl ester (JME) from J. curcas oil (JCO)
This was accomplished by transesterifying the esterified Jatropha oil sample with methanol while utilizing sodium hydroxide pellet (NaOH) as a catalyst in the following procedure: 594 g of the oil was transesterified with methanol. The amount of methanol required was 23% w/w of the total weight of the oil, and the amount of catalyst used was 1% w/w of the total weight of the reactants. The reaction was carried out at 60°C under reflux to maintain the volume of methanol in the flask and avoid any methanol loss during the reaction. The response was in a liquid phase and was stirred continually using a magnetic stir (Mohd Ghazi et al., 2008). An intermediate, Jatropha methyl ester, is produced, and it is biodiesel.
2.7 Transesterification of jatropha methyl ester (JME) to jatropha biolubricant
The weighed Jatropha Methyl Ester was put in a conical flask. The biolubricant is created in 50 mL batches by transesterifying the methyl ester with ethylene glycol using sodium methoxide (NaOCH3), an alkaline catalyst (prepared simply by dissolving 1% w/w sodium hydroxide pellet in 25% w/w methanol). The mole ratio of Ethylene Glycol (E.G.,)-to-Fatty Acid Methyl Ester (Biodiesel) utilized was 1:1–5:1, and the reaction was carried out at temperatures ranging from 100°C to 160°C for different periods (60–300 min). After cooling to room temperature in an ice bath, the product combination was filtered to separate the waste from the liquid mixture (i.e., biolubricant stock).
2.8 Lubricating characteristics
The following lubricating characteristics were determined based on the corresponding referred American System of Testing and Materials (ASTM) procedures: Density was determined with a 50 mL Pycnometer according to ASTM D1217, Pour Point was determined according to ASTM D97–17a (ASTM, 2017); Kinematics Viscosities ASTM D445–17a (ASTM, 2017); Viscosity Index, ASTM D2270–10 (2016), Flash Point (ASTM, 2013) and the acid number was determined via titration according to ASTM D974.
2.9 Design of experiment
The Central Composite Design (CCD) was used to study the effects of the variables of the transesterification reaction and subsequently in the optimization of the process. Each optimization factor (reaction temperature, EG-to-biodiesel (BD) molar ratio, and time) was represented by a three-level code: (−1), (−0), and (+1). The biolubricant yield was a function of reaction temperature (T) (100°C–160°C), EG-to-FAME molar ratio (1:1–5:1), and time (t) (60–300 min). There were 20 runs in the experimental design. A second-order polynomial quadratic model assessed and fit the experimental data gathered throughout the reaction process. The Design Expert created ANOVA charts and response surface plots. Through numerical optimization, the optimal values for the independent variables were calculated.
An FTIR was used to investigate the synthesized biolubricant and identify its functional group by wavelength. Using the functional groups listed in the cited sources, the compounds generated in the product may be confirmed. The FTIR study’s main goal was to prove that the reaction successfully produced the biolubricant.
3 Results and discussions
The sourced Crude jatropha oil was analyzed; the GC-MS analysis and results characterization are shown in Table 1 below. The amount of FFA in the oil was found to be 5.266%. A high FFA content in Jatropha seed oil of ≥1 wt% reduces production yield and the effectiveness of the catalyst (Jain & Sharma, 2010; Kawentar & Budiman, 2013; Reddy et al., 2020).
3.1 GC-MS analysis on the extracted crude jatropha oil purchased from Agri-Energy Limited. Kano state, Nigeria
The extracted Crude J. curcas oil obtained from Agri-Energy Limited, Kano State, was analyzed by gas chromatography-mass spectrometry (Najam Khan et al., 2017; Warra & Abubakar, 2015), the GC-MS analysis and the results detected twenty-three components as seen in Table 2 and Figure 2.
3.2 Significance of the free fatty acid (FFA) reduction by esterification
The decrease in the Percentage of Free Fatty Acid (%FFA) for pretreated jatropha and immediately esterified oil is provided in Table 1 below. The FFA value obtained (5.266) was decreased by esterification with methanol. This is because a study by (Abdelrahman et al., 2018; Al-Sakkari et al., 2020; Goyal et al., 2012; Mu’azu et al., 2013) indicated that esterification helps to lower the percent FFA of the oil.
El-Diwani observed in 2010 that high FFA values >1% had a negative effect on the transesterification process, in which the FFA in the oil combines with the alkali catalyst to form soap (saponification), reducing the quantity of catalyst required for the transesterification reaction. The reduction was performed to prevent saponification during methyl ester production. The FFA level was discovered to be 0.334% after esterification.
3.3 Properties of jatropha -derived biodiesel and biolubricant
ASTM D6751 was used to characterize the purified biodiesel. ASTM defines the parameters that pure biodiesel (B100) must meet before it can be used as a standalone fuel or blended with diesel fuel (Rajamohan et al., 2017; Silitonga et al., 2013).
The viscosity of a lubricant is one of its most crucial characteristics because a lubricant will not adequately lubricate a component if its viscosity differs even slightly from what is required for that component and application. As a result, this might cause severe damage and even device failure.
In particular, the kinematic viscosities were measured at 40°C and 100°C. The kinematic viscosity of jatropha biolubricant (JBL) was measured to be 40.08 cSt at 40°C and 9.21 cSt at 100°C. Several authors have reported varying kinematic viscosities at 40°C for biobased lubricants. Palm oil and palm kernel TMP esters have been reported to have a cSt value of 39.7 and 54.1, respectively (Yunus et al., 2003), sesame oil TMP esters have been reported to have a cSt value of 35.43 (Ocholi et al., 2018a), and 10-undecenoic acid TMP esters have been reported to have a cSt value of 11.2–36.1 (Rao et al., 2012). In contrast, JME’s TMP-based biolubricant had excellent viscosities. Furthermore, the qualities of the JBL-based oil matched the ISO VG 32 standard specification requirements for light gear lubricant.
A stable viscosity over a wide range of temperatures is preferable when selecting an oil. One numerical indicator of how temperature affects an oil’s viscosity is the oil’s viscosity index (V.I.). If the viscosity index is low, the viscosity’s temperature dependence is high, which means that the oil will become very watery at high temperatures and quite thick at low temperatures. However, a high V.I. indicates that the viscosity changes little across a broad temperature range. To put it simply, a higher VI indicates a better quality lubricant. The viscosity index of jatropha biolubricant (JBL) was calculated to be 205 based on its kinematic viscosity readings at 40°C and 100°C. VI values of 193 and 204 were reported by (Sripada, 2012) for the production of biolubricant from methyl oleate and canola biodiesel, respectively. (Gryglewicz et al., 2003) found that the VI for synthesizing neopentyl glycol and trimethylolpropane esters of olive oil, rapeseed oil, and lard fatty acids fell in the 209–235 range. Very high VI values (167–187) were observed in TMP esters of palm and palm kernel oils by (Yunus et al., 2003). In line with this (Tinia et al., 2009), and (Rao et al., 2012) found VI values of 180 for TMP esters produced from J. curcas and 162–172 for polyol esters of 10-undecenoic acid. In addition (Kerman et al., 2011), found that the VI of TMP esters of C5-C18 fatty acids ranged from 80 to 208. JBL’s VI was quite favourable compared to other studies’ findings.
In very cold conditions, the fluidity of a lubricant at low temperatures is crucial. When evaluating flow qualities at low temperatures, the pour point, or the temperature at which a lubricant stop flowing, is crucial. Choosing a lubricant among many alternatives with similar features may become the deciding element. The temperature at which lubricants begin to flow, known as their “pour point,” is the slightest detectable change in temperature. Table 4 shows how JBL measures up against other plant-based lubricants and the ISO viscosity grade requirement in terms of pour point, viscosities (at 40°C and 100°C), and the viscosity index.
Both jatropha seed oil (JSO) and J. curcas oil (JSO) were compared to JBL in terms of their pour point and viscosity. A temperature of −15°C was the pour point for JBL, whereas a temperature of −7°C was found for JSO. As a result, the pour point was improved by the transesterification process. Furthermore, it was discovered that the JBL had a pour point that was similar to other plant-based biolubricants.
This study showed that the biodiesel and biolubricant values obtained were all within the test limits (Tables 3, 4).
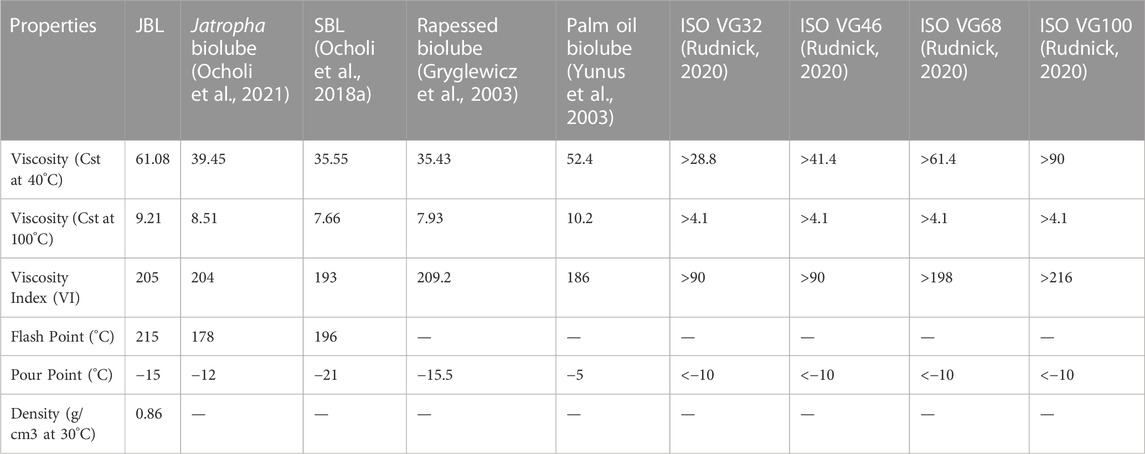
TABLE 4. Properties of jatropha biolubricant and comparison with other plant based biolubricants and ISO viscosity grades.
3.4 Fourier transform infra-red spectrometry (FTIR) of the produced biolubricant
The FTIR spectrum depicts the connection between the transmitter and the wave number by varying the bond energies horizontally on the graph. The peaks in Figure 3 indicate poor transmittance and hence high absorption. Areas with no peaks indicate that photons are not absorbed in that frequency, implying that the particular bond does not exist in the molecule.
In the range of 3377.0 cm−1 to 723.1 cm−1, the FTIR spectrum showed absorption (Table 5). The hydroxyl group (-OH) showed a long and robust peak in the IR spectra between 4000 and 3700 cm−1 without participating in hydrogen bonding. Alkynes were visible in the IR spectra, which showed a significant peak in the 2643 cm−1−1707 CPM for acidic groups (3233.2 cm−1 and 2363.4 cm−1 for carboxylic acids).
A strong signal at 1645.8 cm−1 confirmed the presence of a C = C group. A powerful 770.0 cm−1 signal indicates that this group is geometrically cis in this molecule. The compound had two distinct C=O (esters) and C=O (ethers) groups, as indicated by the firm peaks in 1300 cm−1−1000 cm−1 range at 1220 cm−1 and 1112.0 cm−1. A peak can confirm another ester group (C=O-CH3) at 1017.4 cm−1 in the isolated molecule. 2963 cm−1 is the frequency at which aliphatic C-H stretching occurs in the IR spectrum. The presence of the O-CH3 group causes IR spectra to display peaks at 1220–1017 cm−1.
Blending and stretching peaks can be seen in the FTIR Spectrum region of Figure 3. In both regions, peaks are observed to have varying shapes and levels of intensity (large, medium, and weak). The 3377.0 cm−1 peak is the first in the functional group area. For example, it can locate O-H, terminal alkyne C-H, and N-H bonds. Because of its wide range and distinct appearance, the alcohol peak can be easily identified. Hydrogen bonds are more likely to form when the concentration of O-H molecules in the solution is higher, as stretching hydrogen bonds requires less energy. Firm peaks in alkyne C–H bonds can be found around 3300 cm−1. A wide range of amine or amide N–H, with a medium intensity. These peaks (3004.2 cm−1, 2922.55 cm−1, 2851.4 cm−1) show absorption by alkane C-H bonds, aryl and vinyl C-H bonds, aldehyde C-H bonds, and carboxylic acid C-H bonds in this zone. To distinguish the sp3 C–H bonds, look for them slightly to the right of 3000 cm−1. The C–H bonds can be found because they are located slightly to the left of the 3000 cm−1 mark. Peaks are visible in both C–H bonds. Around the 2700 cm−1 and 2900 cm−1 marks, there is evidence of the presence of an aldehyde. The O–H bonds of the carboxylic acid are visible in the spectrum. C–H bonds of sp3 (alkanes) appear to be the source of the peak band at the 2922.55 cm-1 mark, located to the right of the 3000 cm−1 mark.
Further peaks found (1736.9 cm−1) proved the existence of a carbonyl (C = O) group, and these peaks are generally quite strong and powerful. They enable us to locate the presence of esters, aldehydes, ketones, esters, and acids. A similar observation has been reported for the FTIR of Jatropha biolubricant by (Inegbenoise & Akhihiero., 2022; Mohd Nor et al.,2021).
3.5 Optimization of process parameters for produced jatropha biolubricant synthesis
The biolubricant synthesis optimization procedure was done using CCD to discover the best conditions for biolubricant synthesis. The empirical model was created utilizing three optimization parameters as independent variables (temperature, time, and molar ratio) and the biolubricant production as the response (dependent variable). The combined impacts of the independent factors were studied. CCD typically has six center points, 2n factorial runs, and 2(n) axial runs, where n specifies the number of factors (Aliozo et al., 2017; Ayoub et al., 2016). CCD was utilized to evaluate the association between the biolubricant manufacturing factors and percentage yield. The maximum percentage of Jatropha tri-ester (JTE) yield of 94.12% was achieved at 130°C, 180 min, and EG-TO-FAME molar ratio of 3:1.
Various models were evaluated to see which one best matched the experimental data. Linear, two-factor interaction (2FI), quadratic, and cubic models are some options. Table 6 provides an overview of the findings of this study. Because of its superior statistical values, the Central composite design (CCD) module recommended the quadratic model as the best fit. As shown in Table 7, the quadratic model has the most significant coefficient of determination (R2 value). The corrected and anticipated R2 values were likewise the highest. Because both the linear and 2FI models failed to forecast the answers, they were eliminated. Although the cubic model had a standard deviation value, it was not picked since it was marked as “aliased” because the model contains aliased terms; there need to be more tests to estimate all of the model’s terms independently. Hence it was not chosen.
3.6 Final equation in terms of coded factors
Literature research indicates that the production of biolubricant depends on temperature, time, mole ratio, and catalyst. However, only the first three of these process variables were investigated in this study. Using a statistically designed experiment, the cumulative effect of these components was investigated, and several outcomes related to the interactions between each independent variable were tested. A second-order polynomial equation was developed to represent the biolubricant yield as a function of the three variables:
Where Y is for Jatropha biolubricant Yield, A, B, and C stand for mole ratio (%), time (min), and temperature (°C), respectively, the direct linear impacts of the independent process variables are represented by the coefficients A, B, and C. In contrast, the linear interaction effects between mole ratio/time, mole ratio/temperature, and time/temperature are represented by AB, AC, and BC, respectively. The quadratic impacts of the related process variables are A2, B2, and C2. The expected response was also calculated using the regression equation. Eq. 3.1 illustrates no significant differences between the anticipated and experimental values, indicating that the data agree. It can be seen that all of the data points cluster together towards the straight y = x line; this indicates that the quadratic regression model produced could accurately and confidently predict the J. curcas biolubricant process. As a result, this equation may be used for prediction and design.
The Normal plot of residuals was used to determine whether the points would form a straight line. The data points should be approximately linear; non-linearity in the error term indicates an anomaly that transformation may rectify. Figure 4 demonstrates that the points were closely distributed along the straight line of the plot, confirming the excellent relationship between the experimental and predicted response values; alternatively, the plot verifies that the selected model was adequate in predicting the response variables in the experimental values.
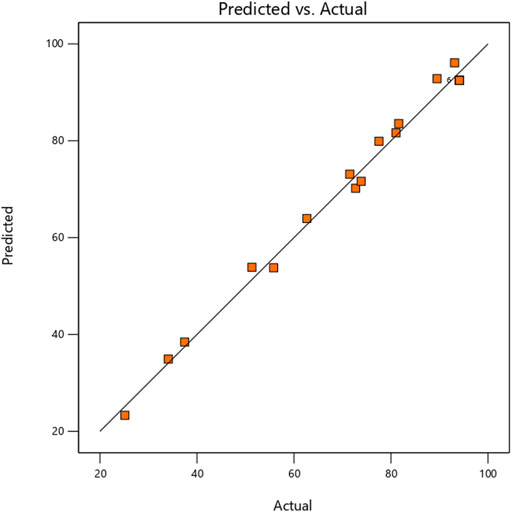
FIGURE 4. Comparison plot showing experimental (actual) and predictive values for J. curcas Seed Biolubricant synthesis.
3.7 Analysis of variance for jatropha biolubricant synthesis
Table 8 displays the results of an analysis of variance (ANOVA) using the F test conducted in Design Expert 13.0 to establish the statistical significance of the model. The study indicates that the regression model is statistically significant with a calculated F value of 135.54, which was validated by the p-values of less than 0.0001 (Yuan et al., 2008). Therefore, the chance of seeing such a high “Model F-value” due to random chance is just 0.01%. The model’s significance may be inferred from its low probability value (0.0001). Each model term’s importance was also examined. If the p-value for a model term is less than 0.05, it has a statistically significant impact on the response. If it is more than 0.1, the model is not statistically significant. According to the ANOVA findings, the model components mole ratio (A), time (B), and temperature (C) were all significant. In statistics, the F-value represents the significance of the effect of a given independent parameter on a dependent variable. The ANOVA table shows that temperature (C) had the most significant influence on Jatropha biolubricant production.
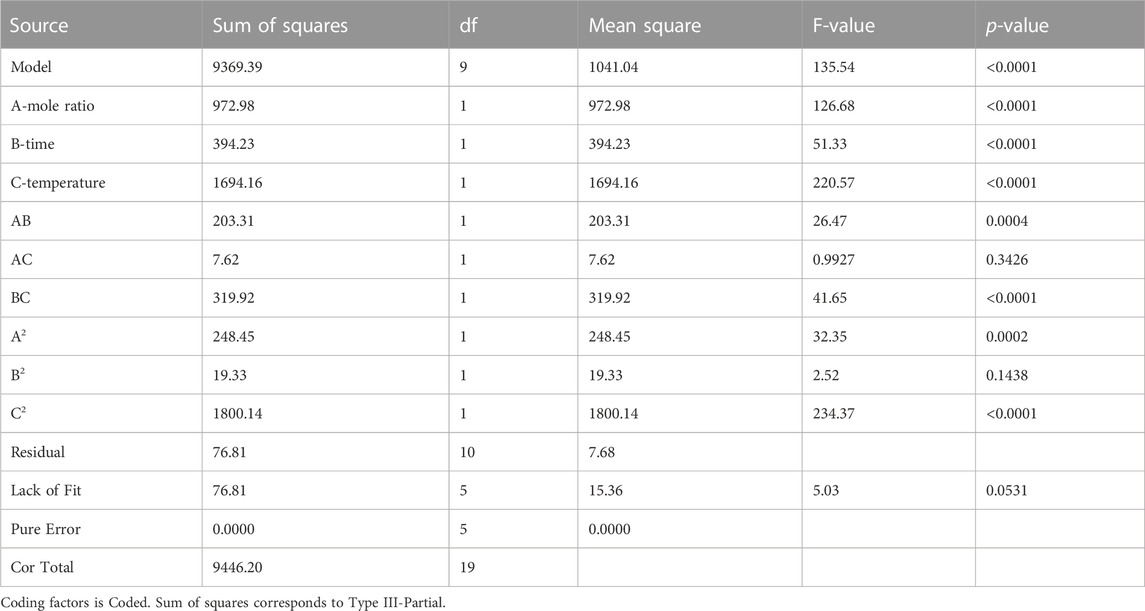
TABLE 8. Analysis of variance (ANOVA) table for the quadratic model for Jatropha biolubricant synthesis.
The Model F-value of 135.54 indicates that the model is statistically significant. There is a 0.01% probability that an F-value of this magnitude might be caused by noise.
p-values less than 0.05 indicate significant model terms. The model terms A, B, C, AB, BC, A2, and C2 are relevant in this situation. Values over 0.1000 imply that the model terms are not statistically significant. If your model has many insignificant terms (excluding those essential to maintain hierarchy), model reduction may enhance it.
The coefficient of determination (R2) of the model was 0.9919 (Table 8); this indicated that the model satisfactorily represents the relationship between the independent variables (Mole ratio, Time, Temperature) and the response (Jatropha biolubricant yield). The R2 indicates that 99.19% variability was explained by the model, while the model could not explain 0.81%. The coefficient of variation (CV) is the ratio of the standard error of estimate to the mean value. It indicates the degree of precision with which the experiment was carried out. A low value of C.V. indicates high reliability and precision of the experiment (Mason et al., 1989; Montgometry, 2005). In this study, the value of CV obtained was 3.77% indicating high reliability and precision of the experiments. Adequate precision values measure the signal-to-noise ratio. A ratio greater than 4 is desirable. A value of 37.1419 obtained in this study indicates an adequate signal, as shown in Table 9.
3.8 3-D response surface plots for the optimization process
Since statistical analysis can only measure the degree to which an independent variable affects a response but does not explain the effect, a response surface plot is required (positive, negative, or otherwise). Interactions between two variables may be graphically represented using three-dimensional response surface plots. Interaction between components may be seen in the shape of the response surface curves. A circular shape indicates no relationship between the two variables, whereas an elliptical one shows a relationship between the variables. The data were generated in the RSM software by keeping two independent variables at a fixed (central) level while varying the other two within the experiment’s parameters. The relationship between the independent and dependent variables is depicted graphically in Figures 5–7 which show the 3-dimensional response surface plots for the chosen model equation.
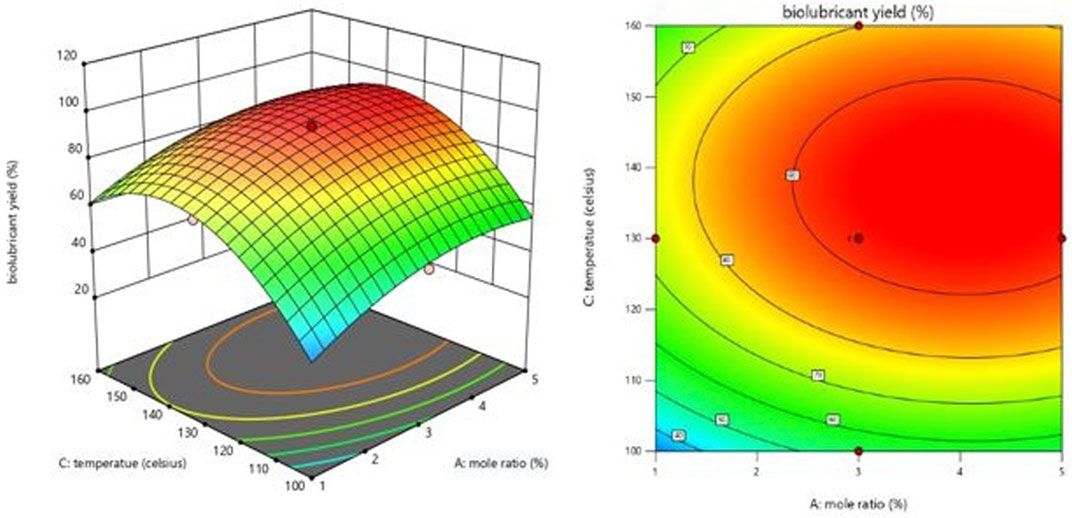
FIGURE 6. Effect of the interaction of temperature and mole ratio (EG-TO-FAME) on biolubricant yield.
Figures 5–7 illustrate the biolubricant yield impacts of interactions between the EG-TO-FAME ratio, temperature, and time. Figure 5 depicts the surface plot of biolubricant yield as a function of EG-TO-FAME molar ratio and time (Mansourpoor, 2012). As demonstrated in Figure 5, time and the EG-TO-FAME molar ratio directly affects tri-ester polyol yield. (bio-lubricant). The yield dropped as time and the EG-TO-FAME molar ratio increased. Figures 5, 6 show that the biolubricant production increased as the FAME concentration grew. Consequently, a rise in, E.G., to FAME mole ratio improved biolubricant conversion, keeping the molar ratio of reactants above the stoichiometric values and increased product yield because the reaction was pushed closer to completion.
Consequently, an excess FAME may be used to speed the reaction to conpletion. Figure 5 demonstrates that the FAME concentration results in a more excellent biolubricant conversion over a shorter time. The mole ratio (E.G.,/FAME) is crucial in the biolubricant transesterification process (Ocholi et al., 2018b). Figures 6, 7 illustrate the effect of varying the temperature of the reaction on the response. The temperature has a continual, moderately favorable effect on biolubricant production. It was revealed that an increase in reaction temperature accelerated the formation of biolubricant over a shorter time. However, extending reaction time at low temperatures did not increase catalytic activity. Meanwhile, the temperature increase facilitated the dispersion of catalyst particles in liquid media and increased mass transfer between the reactants. The contour plot reveals that a higher level of reaction temperature with a low or intermediate level of reaction length was chosen for producing biolubricant with a high yield. The biolubricant output decreased when the EG-TO-FAME molar ratio exceeded 3:1 (Figure 6); as the interaction between FAME and methanol decreased with increasing, E.G., concentration, it resulted in a decrease in biolubricant production and also produced additional phase separation-associated difficulties. (Heikal et al., 2016).
Figure 8 displays the perturbation plot for the model. Perturbation provides the outline of a reaction’s characteristics. For response surface designs, the perturbation plot demonstrates changes in response when any of the parameters deviate from the reference point, with all other components held constant at the reference value.
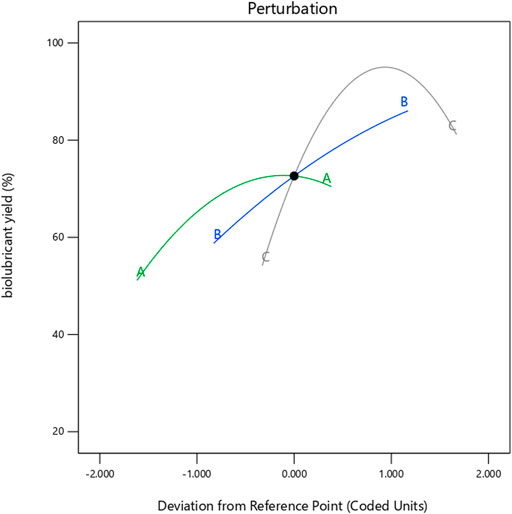
FIGURE 8. Pertubation plot for Jatropha biolubricant yield (%) as a function of Mole Ratio (A), Time (B) and Temperature (C).
In Figure 8, it is demonstrated that factor C (Temperature) has a more significant influence on the response than factors A (Mole Ratio) and B (Time) because factor C has a steeper slope than factors A and B. The 3-D response surface plots in Figures 5–7 indicate that this more significant effect is a positive one. The perturbation plot also reveals that factor A impacted the biolubricant yield, but component B (Time) had the most negligible impact.
3.9 Process variable optimization and validation procedure
The best values of the specified variables were determined by utilizing Design-Expert 13 software to solve the regression equation (Eq. 3.1). The model equation yielded the following ideal conditions for JBL synthesis: mole ratio (A) = 3.87:1, Time (B) = 202.40 min, and Reaction Temperature (C) = 128.95°C.
A study on the optimization of process variables on biolubricant production via response surface methodology by (Inegbenoise & Akhihiero, 2022) recorded an optimum condition to be a temperature of 130°C, an ethylene glycol to fatty acid methyl ester (EG-to-FAME) molar ratio of 3.5, a reaction time of 180 min and obtained a jatropha biolubricant (JBL) yield of 88.74%. Ocholi et al. (2021) investigated the operating process variables on jatropha biolubricant production and recorded an optimum temperature of 150°C, a reaction time of 200 min, JME-to-TMP molar ratio of 5:1 and obtained a jatropha biolubricant yield of 84.38%. Yunus et al. (2003) reported the optimal synthesis conditions for maximal conversion of palm oil methyl esters to TMP tri-ester were 130°C, 20 mbar vacuum pressure, 0.8% w/w catalyst (sodium methoxide), and 3.9:1 mol ratio of palm oil methyl esters to TMP. Sripada (2012) tested this approach to the transesterification process of methyl oleate and TMP and found that the best conditions were 139°C, mole ratio of 4.9, and catalyst loading of 1.42 wt%, yielding a TE yield of 91.2 wt%. Also (Tinia et al., 2009) reported a temperature of 150°C, a pressure of 10 mbar, and a JME-to-TMP mole ratio of 4:1 as the optimum conditions for producing biolubricant.
The final optimized parameters influencing the yield of the biolubricant obtained from this experiment were a mole ratio of 3.87:1, a time of 202.40 min, and a temperature of 128.95°C, and this was well close to the cited references. The maximum biolubricant yields from the literature were almost as high as the experimental value of 94.12%; this demonstrates the model’s validity, indicating an excellent correlation between experimental and literature data.
4 Conclusion
This study aims to optimize the process variables on biolubricant production using Jatropha oil as an alternative lubricant source to petroleum-based lubricant.
The following conclusions have been drawn:
1. The characterization of the extracted crude jatropha oil showed it contained a high %FFA, which, when used, produced a saponification reaction. Hence for it to be considered a viable feedstock for the production of biolubricant, J. curcas oil must be esterified to reduce the %FFA.
2. Upon optimization, the ideal reaction conditions for synthesizing Jatropha biolubricant were determined utilizing the response surface approach. Based on response surface methods, the ideal values for the variables were 128.95°C reaction temperature, 202.40 min reaction time, and a 3.87:1 EG-to-FAME molar ratio. Using these optimum factor values under experimental conditions, an average JBL yield of 94.12% was attained, which was well within the expected range (92.48%) predicted by the model. Further, the product’s ester group was validated using Fourier transform infrared (FTIR) analysis. The quadratic polynomial model and ANOVA adequately described the relationship between the process variables. In addition, the model was analyzed and tested to ensure the optimum match.
3. The Statistical analysis of variance (ANOVA) demonstrated that factor C (Temperature) has a more significant influence on the biolubricant yield than factors A (Mole Ratio) and B (Time). However, factor A (mole ratio) impacted the biolubricant yield, but factor B (Time) had the most negligible impact. Also, the 3-D response surface plots in Figures 5–7 indicate that this more significant effect is a positive one.
4. Comparative analysis of the physicochemical parameters of the resultant biolubricant found that JBL (jatropha biolubricant) met ISO VG 32 biolubricant requirements, which proved that without engine modifications, this biolubricant is an acceptable replacement for petroleum-based lubricants in automobiles. Hence, the optimized jatropha biolubricant production could be applied in a biolubricant pilot plant.
Data availability statement
The original contributions presented in the study are included in the article/supplementary material, further inquiries can be directed to the corresponding author.
Ethics statement
Ethical review and approval was not required for the study on human participants in accordance with the local legislation and institutional requirements. Written informed consent for participation was not required for this study in accordance with the national legislation and the institutional requirements.
Author contributions
Conception or design of the work, data analysis and interpretation, drafting the article: FI-N critical revision of the article: EA.
Conflict of interest
The authors declare that the research was conducted in the absence of any commercial or financial relationships that could be construed as a potential conflict of interest.
Publisher’s note
All claims expressed in this article are solely those of the authors and do not necessarily represent those of their affiliated organizations, or those of the publisher, the editors and the reviewers. Any product that may be evaluated in this article, or claim that may be made by its manufacturer, is not guaranteed or endorsed by the publisher.
References
Abdelrahman, M. A. A., Yassin, A., Hussein, I., Mirghani, M., and Karama, A. B. (2018). Esterification of high free fatty acid jatropha curcas oil for biodiesel production. J. Eng. Appl. Sci. 13 (1), 40–50. Available at: https://www.researchgate.net/publication/287558980_Abdelrahman_MAAYassin_AAA_HUSSEIN_IH_and_Abdalla_BK_2014_Stability_of_Jatropha_curcas_BiodieselJCBPinnacle_EngineeringTechnology_Vol_2014Article_ID_pet1176_pages
Al-Sakkari, E. G., Abdeldayem, O. M., El-Sheltawy, S. T., Abadir, M. F., Soliman, A., Rene, E. R., et al. (2020). Esterification of high FFA content waste cooking oil through different techniques including the utilization of cement kiln dust as a heterogeneous catalyst: A comparative study. Fuel 279, 118519. doi:10.1016/J.FUEL.2020.118519
Aliozo, O. S., Emembolu, L. N., and Onukwuli, O. D. (2017). Optimization of melon oil methyl ester production using response surface methodology. Biofuels Eng. 2 (1), 1–10. doi:10.1515/bfuel-2017-0001
Ayoub, M., Ullah, S., Inayat, A., Bhat, A. H., and Hailegiorgis, S. M. (2016). Process optimization for biodiesel production from waste frying oil over montmorillonite clay K-30. Procedia Eng. 148, 742–749. doi:10.1016/J.PROENG.2016.06.606
Baud, S. (2018). Seeds as oil factories. Plant Reprod. 31 (3), 213–235. doi:10.1007/S00497-018-0325-6
Bermejo, R. (2014). The limits of fossil fuels. Handb. a Sustain. Econ., 151–171. doi:10.1007/978-94-017-8981-3_10
Bhattacharya, M., Paramati, S. R., Ozturk, I., and Bhattacharya, S. (2016). The effect of renewable energy consumption on economic growth: Evidence from top 38 countries. Appl. Energy 162, 733–741. doi:10.1016/J.APENERGY.2015.10.104
Bilal, S., Mohammed-Dabo, I. A., Nuhu, M., Kasim, S. A., Almustapha, I. H., and Yamusa, Y. A. (2013). Production of biolubricant from Jatropha curcas seed oil. J. Chem. Eng. Mater. Sci. 4 (6), 72–79. doi:10.5897/jcems2013.0164
Goyal, P., Sharma, M., and Jain, S. (2012). Optimization of esterification and transesterification of high FFA jatropha curcas oil using response surface methodology. J. Petroleum Sci. Res. 1, 36–43. Available at: https://www.researchgate.net/publication/292021082_Optimization_of_Esterification_and_Transesterification_of_High_FFA_Jatropha_Curcas_Oil_Using_Response_Surface_Methodology
Gryglewicz, S., Piechocki, W., and Gryglewicz, G. (2003). Preparation of polyol esters based on vegetable and animal fats. Bioresour. Technol. 87 (1), 35–39. doi:10.1016/S0960-8524(02)00203-1
Gunam Resul, M. F. M., Mohd Ghazi, T., and Idris, A. (2012). Kinetic study of jatropha biolubricant from transesterification of jatropha curcas oil with trimethylolpropane: Effects of temperature. Industrial Crops Prod. 38, 87–92. doi:10.1016/j.indcrop.2012.01.012
Hawash, s., Diwani, G., and Kader, E. A. (2023). Optimization of biodiesel production from jatropha oil by heterogeneous base catalysed transesterification. Int. J. Eng. Sci. Technol. 3 (6), 5242–5251. Available at: https://www.semanticscholar.org/paper/Optimization-of-Biodiesel-Production-from-Jatropha-Hawash-Diwani/fb0219f4193d493c109c12a72c5e7bada7190a4d
Heikal, E., Elmelawy, M., Khalil, S., and Elbasuny, N. M. (2016). Manufacturing of environment friendly biolubricants from vegetable oils. Egypt. J. Petroleum 26, 53–59. doi:10.1016/j.ejpe.2016.03.003
Ieo, (2021). IEO 2021 ReleasePresentation. Washington, D.C, USA. U.S. Energy Information Administration.
Inegbenoise, O. O., and Akhihiero, E. T. (2022). Effects of process variables on biolubricant production from jatropha curcas seed oil. J. Eng. Dev. 14 (1). Available at: https://jedev.com.ng/wp-content/uploads/2022/04/JED-V14-01-08-03-22.pdf
Jain, S., and Sharma, M. P. (2010). Kinetics of acid base catalyzed transesterification of Jatropha curcas oil. Bioresour. Technol. 101 (20), 7701–7706. doi:10.1016/J.BIORTECH.2010.05.034
Jiang, S. T., and Niu, L. Y. (2011). Optimization and evaluation of wheat germ oil extracted by supercritical CO<sub>2</sub>. Grasas Aceites 62 (2), 181–189. doi:10.3989/gya.078710
Kawentar, W. A., and Budiman, A. (2013). Synthesis of biodiesel from second-used cooking oil. Energy Procedia 32, 190–199. doi:10.1016/j.egypro.2013.05.025
Kerman, C. O., Gaber, Y., Ghani, N. A., Lämsä, M., and Hatti-Kaul, R. (2011). Clean synthesis of biolubricants for low temperature applications using heterogeneous catalysts. J. Mol. Catal. B Enzym. 72 (3–4), 263–269. doi:10.1016/J.MOLCATB.2011.06.014
Mansourpoor, M. (2012). Optimization of biodiesel production from sunflower oil using response surface methodology. J. Chem. Eng. Process Technol. 3 (5). doi:10.4172/2157-7048.1000141
Mohd Ghazi, T. I., M Gunam Resul, M. F., and Idris, A. (2008). INTERNATIONAL journal of chemical reactor engineering Bioenergy II: Production of biodegradable lubricant from jatropha curcas and trimethylolpropane. Int. J. Chem. React. Eng. 7 (1), 1542–6580. doi:10.2202/1542-6580.1957
Mohd Nor, N., Salih, N., and Salimon, J. (2021). Chemically modified Jatropha curcas oil for biolubricant applications. Hem. Ind. 75, 117–128. doi:10.2298/HEMIND200809009N
Mu’azu, K., Mohammed-Dabo, I. A., Waziri, S. M., Ahmed, A. S., Bugaje, I. M., and Ahmad, A. S. (2013). Development of a mathematical model for the esterification of Jatropha curcas seed oil. J. Petroleum Technol. Altern. Fuels 4 (3), 44–52. doi:10.5897/JPTAF12.019
Najam Khan, M., Mustafa, T., Amin, M., Ahmad, I., Ullah, A., and Soomro, S. (2017). Production of biodiesel through catalytic transesterification of jatropha oil. J. Appl. Emerg. Sci. 6, 9–13. Available at: https://www.researchgate.net/publication/309634145_Production_of_Biodiesel_through_Catalytic_Transesterification_of_Jatropha_Oil
Ocholi, O., Menkiti, M., Auta, M., and Ezemagu, I. (2018). Optimization of the operating parameters for the extractive synthesis of biolubricant from sesame seed oil via response surface methodology. Egypt. J. Petroleum 27 (3), 265–275. doi:10.1016/J.EJPE.2017.04.001
Ocholi, O., Menkiti, M., Auta, M., and Ezemagu, I. (2018). Optimization of the operating parameters for the extractive synthesis of biolubricant from sesame seed oil via response surface methodology. Egypt. J. Petroleum 27 (3), 265–275. doi:10.1016/J.EJPE.2017.04.001
Ocholi, O., Menkiti, M. C., and Aniagor, C. O. (2021). Optimization of biodegradable lubricant basestock synthesis from Jatropha curcas seed oil using response surface methodology. J. Eng. Appl. Sci. 19 (1). Available at: http://www.facultyofengineeringnau.org/archive/2928266135102273355.pdf
Panchal, T. M., Patel, A., Chauhan, D. D., Thomas, M., and Patel, J. v. (2017). A methodological review on bio-lubricants from vegetable oil based resources. Renew. Sustain. Energy Rev. 70, 65–70. Elsevier Ltd. doi:10.1016/j.rser.2016.11.105
Rajamohan, S., Kasimani, R., Ramakrishnan, P., and Shameer, P. M. (2017). A review on the properties, performance and emission aspects of the third generation biodiesels. Renew. Sustain. Energy Rev. 82, 2970–2992. doi:10.1016/j.rser.2017.10.037
Rao, Z., Gao, J., Zhang, B., Yang, B., and Zhang, J. (2012). Cisplatin sensitivity and mechanisms of anti-HPV16 E6-ribozyme on cervical carcinoma CaSKi cell line. Chinese-German J. Clin. Oncol. 11 (4), 237–242. doi:10.1007/s10330-011-0949-6
Reddy, P., Reddy, K., Durisety, H., and Pydimalla, M. (2020). Optimization of base catalysts for biodiesel production from jatropha curcas oil. Int. J. Innovative Sci. Mod. Eng. 6 (7), 8–14. doi:10.35940/IJISME.G1237.056720
Rudnick, L. R. (2020). Synthetics, mineral oils, and bio-based lubricants: Chemistry and technology. CRC Press. Boca Raton, FL, USA, Google Scholar. https://scholar.google.com/scholar_lookup?title=Automotives%20Gear%20Lubricants%2C%20Synthetics%2C%20Mineral%20Oil%20and%20Bio-Based%20Lubricants%3A%20Chemistry%20and%20Technology&publication_year=2006&author=L.R.%20Rudnick.
Salih, N., and Salimon, J. (2021). A review on eco-friendly green biolubricants from renewable and sustainable plant oil sources. Biointerface Res. Appl. Chem. 11 (5), 13303–13327. doi:10.33263/BRIAC115.1330313327
Sigar, C. P., Soni, S. L., Mathur, J., and Sharma, D. (2008). Performance and emission characteristics of vegetable oil as diesel fuel extender 31 (2), 139–148. doi:10.1080/15567030701513160
Silitonga, A. S., Masjuki, H. H., Mahlia, T. M. I., Ong, H. C., Chong, W. T., and Boosroh, M. H. (2013). Overview properties of biodiesel diesel blends from edible and non-edible feedstock. Renew. Sustain. Energy Rev. 22, 346–360. doi:10.1016/J.RSER.2013.01.055
Sripada, P. (2012) Comparative tribological evaluation of trimethylolpropane-based biolubricants derived from methyl oleate and canola biodiese. Doctoral dissertation. Saskatoon, Canada: University of Saskatchewan. https://harvest.usask.ca/handle/10388/ETD-2012-12-820.
Sun, S., Yang, G., Bi, Y., and Liang, H. (2011). Enzymatic epoxidation of corn oil by perstearic acid. JAOCS, J. Am. Oil Chemists’ Soc. 88 (10), 1567–1571. doi:10.1007/s11746-011-1820-1
Tinia, T. I., Gunam Resul, M. F. M., and Idris, A. (2009). Bioenergy II: Production of biodegradable lubricant from jatropha curcas and trimethylolpropane. Int. J. Chem. React. Eng. 7 (1). doi:10.2202/1542-6580.1957
Wagner, H., Luther, R., and Mang, T. (2001). Lubricant base fluids based on renewable raw materials: Their catalytic manufacture and modification. Appl. Catal. A-Gen. 221 (1–2), 429–442. doi:10.1016/S0926-860X(01)00891-2
Warra, A., and Abubakar, A. (2015). GC-MS analysis of hexane extract of Jatropha curcas L. seed oil. World J. Biomed. Pharm. Sci. 1 (1), 15–21. Available at: https://www.semanticscholar.org/paper/GC-MS-analysis-of-hexane-extract-of-Jatropha-curcas-Warra-Abubakar/4769a15695ec1972346df24d6051aa3d2fb30275
Woma, T. Y., Lawal, S. A., Abdulrahman, A. S., Olutoye, M. A., and Ojapah, M. M. (2019). Vegetable oil based lubricants: Challenges and prospects. Tribol. Online 14 (2), 60–70. doi:10.2474/TROL.14.60
Yuan, X., Liu, J., Zeng, G., Shi, J., Tong, J., and Huang, G. (2008). Optimization of conversion of waste rapeseed oil with high FFA to biodiesel using response surface methodology. Renew. Energy 33 (7), 1678–1684. doi:10.1016/J.RENENE.2007.09.007
Keywords: Jatropha, biolubricant, fatty acid methyl ester, transesterification, tri-ester polyol, response surface methodology
Citation: Ifeanyi-Nze FO and Akhiehiero ET (2023) Optimization of the process variables on biodegradable industrial lubricant basestock synthesis from Jatropha curcas seed oil via response surface methodology. Front. Energy Res. 11:1169565. doi: 10.3389/fenrg.2023.1169565
Received: 19 February 2023; Accepted: 30 March 2023;
Published: 17 April 2023.
Edited by:
Mohammad Rehan, King Abdulaziz University, Saudi ArabiaReviewed by:
Tanakorn Wongwuttanasatian, Khon Kaen University, ThailandManzoore Elahi M. Soudagar, University of Malaya, Malaysia
Copyright © 2023 Ifeanyi-Nze and Akhiehiero. This is an open-access article distributed under the terms of the Creative Commons Attribution License (CC BY). The use, distribution or reproduction in other forums is permitted, provided the original author(s) and the copyright owner(s) are credited and that the original publication in this journal is cited, in accordance with accepted academic practice. No use, distribution or reproduction is permitted which does not comply with these terms.
*Correspondence: Favour Okechi Ifeanyi-Nze, ZmF2b3VyLmlmZWFueWktbnplQGVuZy51bmliZW4uZWR1
†ORCID: Favour Okechi Ifeanyi-Nze, orcid.org/0000-0002-1938-0141