- 1Department of Computer Science, Lahore Garrison University, Lahore, Pakistan
- 2Department of Computer Science, American International University-Bangladesh, Dhaka, Bangladesh
- 3School of Computer Science and Engineering, The University of Aizu, Fukushima, Japan
- 4James Watt School of Engineering, University of Glasgow, Glasgow, United Kingdom
- 5Department of Informatics, University of Oslo, Oslo, Norway
- 6Department of Electrical, Electronics and Computer Engineering, University of Ulsan, Ulsan, South Korea
A gearbox is a critical rotating component that is used to transmit torque from one shaft to another. This paper presents a data-driven gearbox fault diagnosis system in which the issue of variable working conditions namely uneven speed and the load of the machinery is addressed. Moreover, a mechanism is suggested that how an improved feature extraction process and data from multiple tasks can contribute to the overall performance of a fault diagnosis model. The variable working conditions make a gearbox fault diagnosis a challenging task. The performance of the existing algorithms in the literature deteriorates under variable working conditions. In this paper, a refined feature extraction technique and multitask learning are adopted to address this variability issue. The feature extraction step helps to explore unique fault signatures which are helpful to perform gearbox fault diagnosis under uneven speed and load conditions. Later, these extracted features are provided to a convolutional neural network (CNN) based multitask learning (MTL) network to identify the faults in the provided gearbox dataset. A comparison of the experimental results of the proposed model with that of several already published state-of-the-art diagnostic techniques suggests the superiority of the proposed model under uneven speed and load conditions. Therefore, based on the results the proposed approach can be used for gearbox fault diagnosis under uneven speed and load conditions.
Introduction
It is common to use sophisticated machinery with complex mechanical structures in modern industry. These machines consist of different important components. One of the important components is a gearbox which has three main functions: 1) to increase the torque to the equipment that is being driven by the motor, 2) to vary speed and loads according to the condition of machinery, and 3) to change the direction of the rotating shafts (Mallikarjuna et al., 2020). Over the years improvement in the design of gearbox systems has resulted in its enhanced operation which has become the reason for its increased usage in industrial machines. Gearboxes have been extensively used in various electromechanical equipment and are one of the most vulnerable parts. Being an important component in machinery, any gearbox problem not only creates operational issues for the machinery but security issues are also concerned with it.
A gearbox consists of several critical components such as gears, shafts, bearings as well as housing for all these components. It has a unique structure that ensures high productivity, long life, and smooth functionality. It has a broad scope and essential component in the recent industry of aviation, power sector, engine instruments, automobile industry, and machine-driven fields (Hajnayeb et al., 2011; Zappalá et al., 2014; Liu et al., 2018a; Praveenkumar et al., 2018; Mallikarjuna et al., 2020; Saufi et al., 2020; Jaber and Jaber, 2021). The structure of a gearbox is very complex. Therefore, under harsh working conditions chances of failure are high (Kim and Kim, 2020; Singh et al., 2020; Wei et al., 2022). A problem in any of the components of the gearbox may cause the failure of the whole machinery in which the gearbox is installed (Qiu et al., 2019). Any such failure of the machinery may result in increased breakdown time, huge production loss, and increased maintenance costs (Duraivelu and Duraivelu, 2021), (Althubaiti et al., 2022). Therefore, to avoid unexpected breakdowns and to ensure the smooth functioning of a mechanical system, gearbox fault diagnosis is of paramount importance. For this reason, there is a need for the development of robust gearbox fault diagnosis approaches based on advanced signal processing, machine learning, and/or deep learning techniques.
In the past, lots of work has been done in the field of gearbox fault diagnosis. In the early stages, researchers have used hand-engineered features with traditional machine learning approaches to identify the fault modes or types of fault in the gearbox systems (Vernekar et al., 2017), (Vernekar et al., 2018). In (Vernekar et al., 2017), an engine gearbox fault diagnosis approach is presented in which empirical mode decomposition (EMD), decision tree, and Naive Bayes algorithms were used to identify the health state of the engine. Similarly, a fault diagnosis approach based on artificial neural networks (ANN) was developed to identify gearbox faults. Moreover, a feature extraction algorithm was used in the designed approach to improve the computational efficacy of the algorithm. The design algorithm was tested with an experimental set of data to check the performance in the context of the gearbox fault diagnosis (Vernekar et al., 2018). The proposed algorithm provided satisfactory gearbox faults identification results when validated with the simulated gearbox data. Here, it is noteworthy that these algorithms have been validated on simulated data produced under a controlled set of conditions. The efficacy of the designed algorithm is unknown for real-world data. Moreover, the early-stage gearbox fault diagnosis models use hand-curated features to complete the task. To extract such features, domain-specific expertise is needed which is a tedious task to do. In addition, a dedicated feature extraction step adds up to the overall computational complexity of a designed data-driven fault diagnosis model.
To avoid these issues and design more generic algorithms which can explore informative trends in the data automatically, researchers introduced deep learning in the field of fault diagnosis (Tang et al., 2022a; Tang et al., 2022b; Tang et al., 2022c). In this regard, an effective deep learning approach for gearbox fault diagnosis using stacked autoencoders was introduced in (Liu et al., 2018a). The designed approach made the process efficient by automatically extracting features from the input data. Moreover, to avoid the overfitting problem, an architectural modification was made to the stacked autoencoders by introducing ReLU and dropout techniques. The proposed approach was tested with two gearbox datasets that generated satisfactory performance as compared to the basic stacked autoencoders. Likewise, a group of researchers has introduced a new mechanism for gearbox fault diagnosis in the form of a one-dimensional residual convolutional neural network (1-DRCAE) (Zhou and Zhou, 2020). The designed approach was able to extract features aromatically from the input vibration signals in an unsupervised manner. According to the authors, the designed approach yielded better gearbox fault diagnosis performance than other well-known unsupervised learning algorithms, such as autoencoders, deep belief networks, and one-dimensional convolutional neural networks. Similarly, a knowledge-based deep belief network was introduced which utilized confidence and classification rules with Boltzmann machines to improve the performance of the gearbox fault diagnosis process (Liu and Liu, 2020). The existing techniques achieved satisfactory diagnostic performance for the specified experimental setup. However, most of the work done in the field of gearbox fault diagnosis using deep learning methods is focused on the automatic extraction of features, effectively reducing the dimensions of the data, and improving the diagnostic performance only for single working conditions (Li et al., 2020), (Liu et al., 2018b). There is significant scope to work on the generalization capability of the gearbox fault diagnosis approaches available in the literature (Xia et al., 2021). For instance, fault identification in multiple gears using data recorded under inconsistent and uneven working conditions has not been much explored. One possible solution for the task is to design a separate fault diagnosis model for each object and working condition. This approach is not practically applicable as in a real-time scenario it is practically not feasible to design a separate model for each component and identify each varying condition. Therefore, there is a need to adopt such a fault diagnosis technique that can provide a solution for multiple tasks simultaneously, i.e., identification of the problem in more than one component under uneven working conditions.
Therefore, to resolve the given problem, an image processing and deep learning-based approach is introduced which can identify issues in multiple gears simultaneously using the data recorded under uneven working conditions. The proposed approach can be divided into two stages. In the first stage, signals are processed using a bag of visual words which is useful to explore unique patterns for different health conditions. This image processing-based signal exploration technique can extract unique patterns for different faults even under uneven working conditions. When such refined patterns are provided to a classifier as inputs it enhances its classification performance. Moreover, this technique has replaced feature engineering to reduce the design complexity of the overall gearbox fault diagnosis pipeline by not having dedicated hand-crafted feature extraction and selection steps. This image-based pattern exploration gives efficiency and high accuracy in feature matching results e.g., if there are more similar results for visual words, the vocabulary size could be increased. A high vocabulary size means that the technique was able to extract a high amount of salient information which is good for a classification task. Furthermore, a multitask learning (MTL) based CNN is used in the next stage for the classification of the input data. Multitask learning is required in the given gearbox fault diagnosis scenario as fault diagnosis in two different types of gears is under consideration simultaneously. So, by having these two additions in the gearbox fault diagnosis pipeline its generalization capability can be improved significantly.
This article aims at solving a gearbox fault diagnosis problem when there are issues with multiple components simultaneously, hence, improving the overall generalization capability of the pipeline. This issue can be solved by processing the fault diagnosis process of each component separately and simultaneously. Furthermore, the overall learning ability of a network can be enhanced which provides better diagnostic performance of the network separately for each task as well as the overall performance by sharing information among these tasks during the training stage to minimize the objective function (loss of the network). Moreover, this study also highlights the importance of an enhanced feature extraction step in the form of unique pattern extraction for the different health conditions of a gearbox from raw signals.
Technical background
Bag of visual words
The idea of a bag of visual words (BOVW) for preprocessing the gearbox signals to extract informative features is adopted in this work. The bag of words approach is commonly used in natural language processing (NLP) and information retrieval. A typical bag of visual words technique which can be seen in Figure 1 is used normally in the image classification process. The difference being in NL a text document is converted into a BOVW, whereas, in image classification, image data is represented as a bag of visual words. In BOVW, image features are used synonymously as the words in BOVW. For every image, there are distinctive image features that belong specifically to that image. There are certain features that are key points and others are descriptors. These features are extracted by feature extractor algorithms like scale-invariant feature transform (SIFT) and KAZE etc., (Liu et al., 2017). Key points are the image features that remain unaffected whether the image is rotated in any direction or changed to any size. The descriptors describe the key points. Both are used to have a vocabulary for a particular picture and by the number of their repetition, a frequency histogram of that picture can be obtained, from where further similar images can be reproduced. These frequency histograms are the actual BOVW.
Multitask learning with convolutional neural network
If there is a primary task, MTL while following basic principles of transfer learning, shares the knowledge among different subtasks being a type of transfer learning. MTL leads to the creation of a separate task branch for each subtask in CNN architecture, thus there is no need of having individual models for all subtasks. MTL does so by minimizing one principle objective function. In this way all subtasks share the same model architecture, also the network parameters are the same but training time for the CNN architecture model is decreased significantly. This concept of MTL is expressed as:
In this equation,
Methods and materials
The proposed model as shown in Figure 3 can be divided into two stages, i.e., the first stage is the fault signatures extraction from the raw input signals. The second stage is the application of multitask learning to enhance the classification performance of the model under uneven load conditions. To extract useful descriptive features from the raw data an image processing technique known as the bag of visual words is used in this work. For this reason, the input gearbox signals were first converted into grayscale images. All the signals in the dataset were divided into segments of 300 data points. Later these segments were staked to form matrices of 300 × 300 size. Afterward, all the converted matrixes were converted to grayscale images. Next, visual descriptors are extracted using the bag of visual words technique from grayscale images. Later, the extracted descriptors are fed to a multitasked network so that it may learn salient information that can be used to correctly classify the data under uneven load conditions.
The process for the bag of visual words representation from the input data is illustrated in Figure 4. First, the input signals were converted into grayscale images. In the next step, distinct features are extracted from the grayscale images by applying SIFT algorithm (Liu et al., 2017) to each image. Afterward, the frequency histogram of those extracted features is calculated for each image. In the last, from the frequency histogram, feature vectors are formed which are later provided to the MTL-CNN as inputs.
Multitask learning-based CNN architecture
An inter-class MTL-based diagnostic architecture has been developed by using CNN to diagnose gearbox fault types under uneven load and speed conditions. Figure 5 shows that the proposed framework of MTL-CNN can be segmented into two parts: 1) general feature extractor and 2) subtask branches. The abstract spatial information extracted from the 2D input data is put into the general feature extractor. The general feature extractor contains 4 layers in total; 2 convolution and 2 pooling layers. The extracted information from this part is then used by the subtask branches to diagnose the health types and speed conditions of the bearings. In the proposed architecture there are two subtasks having different layers. Subtask 1 is to determine bearing speed condition and contains one convolutional, one pooling, one fully connected, and the final output layer. While subtask 2 is composed of two convolutional, one pooling, two fully connected, and the final output layer which diagnoses different health conditions of the gearbox. To activate a fully connected layer in the proposed framework a leaky rectified linear unit (Leaky ReLU) is used. L2 regularization value of 0.04 is achieved in this layer to avoid overfitting problems. This value is decided by studying training accuracy and function loss values from multiple previous experiments. From the preliminary experiments, it is concluded that the final classification performance is affected by a varying number of kernels, so we used a grid search to optimize the number of kernels in the proposed MTL-CNN framework.
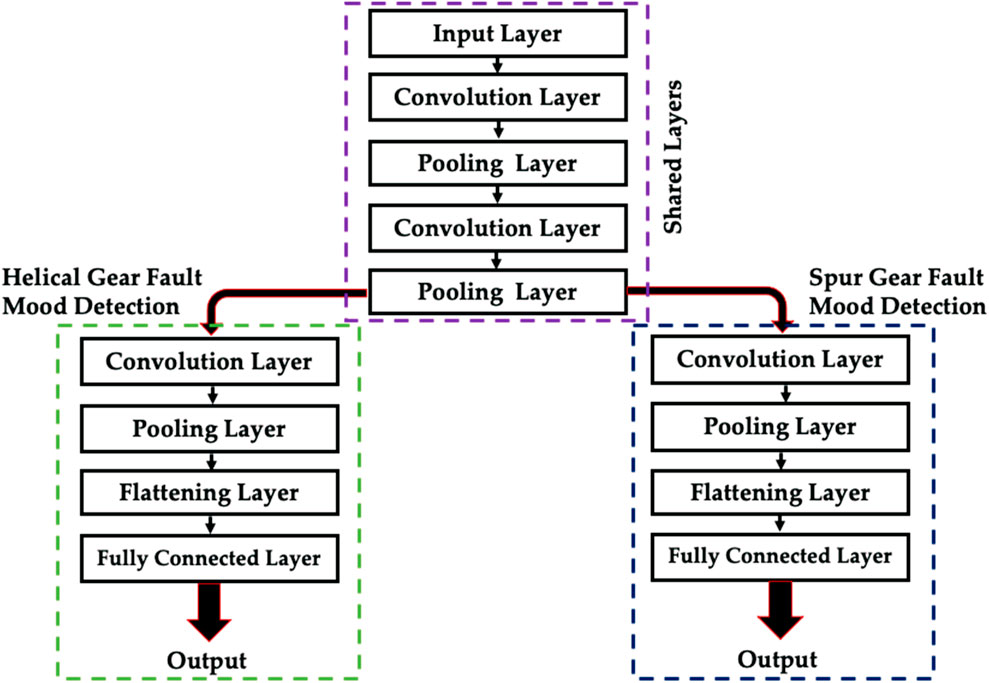
FIGURE 5. The proposed framework of multitask learning based convolutional neural network for simultaneous identification of faults in multiple gears under uneven load and speed conditions.
Performance evaluation matrices
The performance of the proposed architecture is assessed by using multiple performance evaluation matrices, i.e., average classification accuracy, and loss function graph. The average classification accuracy can be calculated as follow:
Here TP is the number of true positives, TN stands for true negatives, FN is the number of false negatives, and FP is the number of false positives. The total loss of the model is studied until 1,000 epochs to overcome the overfitting and underfitting problems. Also, t-stochastic neighbor embedding (t-SNEs) is used to visualize the feature space of the output layer as shown in Figure 6 which is then utilized to see the class separability. In the end, the data bias is eliminated by using k-fold cross-validation (10-CV) along with multiple evaluation parameters for each experiment.
Experimental setup
Composite fault data of helical gear from PHM 2009 Challenge Data is used for comparison and analysis of the proposed model (Li, 2009). First, the input signal is segmented into equal intervals, and afterwards, an image processing-based feature extraction method is used for features extraction. These extracted features are then used to structure the feature vectors to give as input to the MTL-CNN which then identifies the gearbox faults.
Data preparation
PHM Association’s 2009 international competition provides PHM 2009 Challenge Data that contains a complete set of gearbox data including those of gear, bearing, and shaft failures. Figure 7 shows the overview as well as the schematic pattern for the experimental platform. We have 3 axes (shafts): input axis (IS), intermediate axis (ID), and output axis (OS). Two sets of meshing gears are considered in the experiment which is split into two modes: the spur gear mode and the helical gear mode. The spur gear mode has the ratio of 32T: 96 T and 48 T:80 T, while the helical gear mode has the ratio of 16: 48 and 24: 40 T. The fault modes for the two set of gears, i.e., spur gear and helical gear is presented in Tables 1, 2 respectively. Data is collected by the vibration sensors which are installed on the cabinet bilaterally. There are 266,656 sampling points, 4s is the sampling time and the sampling frequency is 66.67 kHz. The spur and helical gears faults are used as an example in the experiment. As shown in Table 1 the helical gear has 8 types of complex fault modes. There are 2 load states, high and low, and 5 working frequencies for each mode. There are 3 types of data for similar rotating speeds for each fault mode. The proposed model is trained and tested multiple times with spur and helical gear data of low and high load at 30 Hz, 35 Hz, 40 Hz, 45 Hz, and 50 Hz rotating speeds. It allows getting as many numbers of data sample groups as possible, to optimize the model’s operational speed and to have more periodic signals in the limited data sample. The original signals are down sampled by 1/3 factor with a sampling length of 1,600 with vibration data of periods 2–3. The interval points to take the sample is 170 so there are 1,500 groups of data samples for each type of failure mode. Out of these 1,500 groups, 900 are training sets and the remaining 600 are test sets.
Results and analysis
Initially, signals are divided into equal-length segments which were reshaped to create grayscale images. Next, from the grayscale images, features vectors were created which were later used as input to the MTL-CNN. The MTL-CNN in the end categorized the input data into the respective classes. The architecture of MTL-CNN is designed in such a manner that it learns about two tasks simultaneously. The first task is to identify fault moods in the set of spur gears and the second task is to identify fault modes in the set of helical gears.
The results are generated by considering a dataset in which each class is equally balanced, i.e., the number of samples in each class is the same. Moreover, to generate stable results the experiment was repeated 10 times and the results were noted. The results given in this study are the average of all the 10 repetitions and for 1,000 epochs. In Figure 8, the three loss functions for the MTL-CNN can be observed. The loss function in 1) refers to the training loss of and validation loss for task 1, whereas 2) refers to the loss function of task 2, and 3) denotes the loss for the shared layers. It can be observed in the figures that the model starts to converge by lowering the loss value in all three cases. Moreover, in all three cases, the loss has already been minimized to the best possible value when the model reaches 1,000 epochs. After 1,000 epochs if the training and validation of the model were continued there is no significant change in the model convergence and there was a better chance that the model will start to overfit on the training data. So, it was safe to train and validate the model to 1,000 epochs and do the performance evaluation. The average diagnostic performance of the proposed model is listed in Table 3.
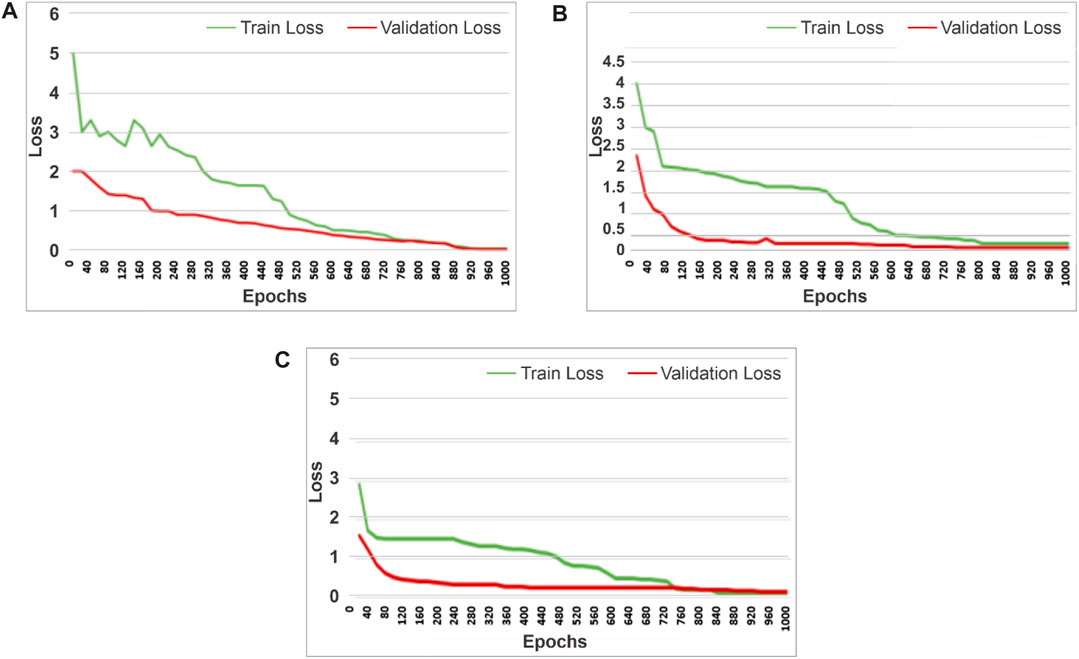
FIGURE 8. Three loss functions for the MTL-CNN. The loss function in (A) refers to the training loss of and validation loss for task 1, whereas (B) refers to the loss function of task 2, and (C) denotes the loss for the shared layers.
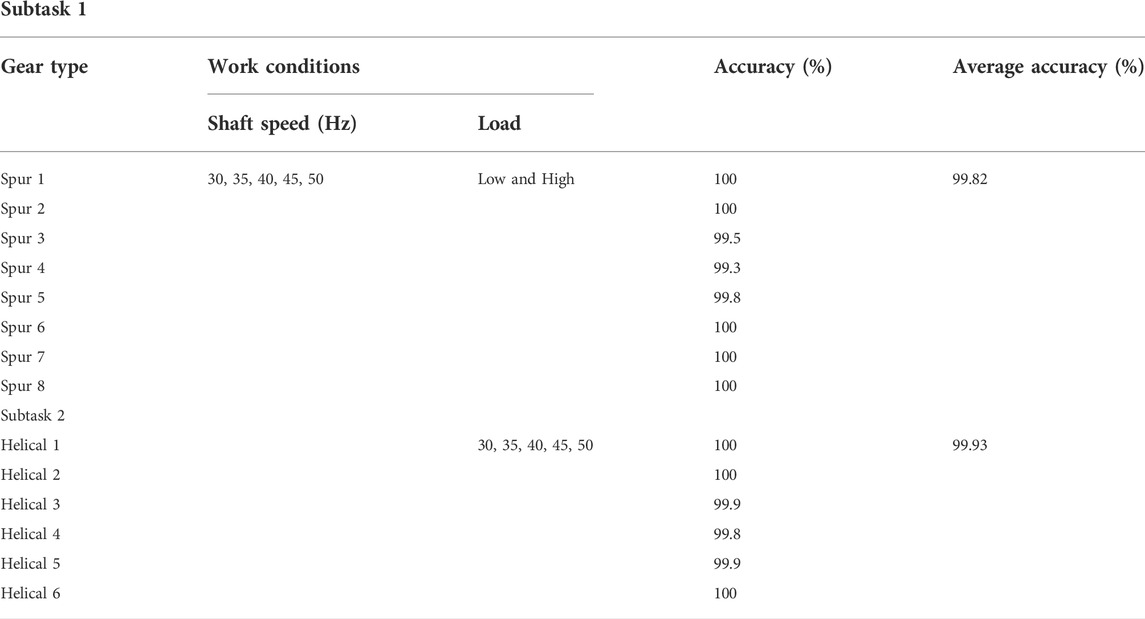
TABLE 3. Details for spur gears with different fault moods The Accuracy for different fault modes of spur and helical gears.
From Table 3 it is evident that for both the subtasks, the performance of the proposed model, i.e., MTL-CNN is satisfactory as in both the cases average accuracy is greater than 99.5%. However, there are some fault modes in which the accuracy slightly deteriorates. The reason is that in these cases few of the samples from shaft speed and motors loads closer to each other are classified as these samples encountered the same characteristics in the final feature vectors which were provided as input to MTL-CNN. Nevertheless, even with this misclassification of the few samples, the model could yield adequate overall performance. Furthermore, the classification performance of the proposed model is compared with a few of the state-of-the-art studies available in the literature as shown in Table 4. These results were acquired by evaluating all the models presented in these studies on the dataset prepared for the proposed method. It can be observed that all these models achieved more than 99 percent of average accuracy except the standard autoencoder-based deep network given in (Sohaib and Kim, 2017). Among these models, the performance of the proposed model is the highest with 99.87% of average classification accuracy. There are two possible reasons behind the enhanced performance of the proposed model. The first reason is the introduction of a suitable unique pattern extraction method in the gearbox fault diagnosis pipeline. The proposed pattern extraction method could extract unique patterns from the input signals for different health conditions even under variable working conditions. As a result when these refined inputs were provided to the classifier, i.e., MTL CNN it could classify the data with high accuracy. The second reason is the use of multitask learning in the classification phase. Due to it the learning capability of the network improved significantly. Therefore, the network converged properly which is evident in Figure 8. The comparison of the results also shows that the proposed model has better performance than the other two approaches. From all this analysis it can be concluded that the design model is capable to perform gearbox fault diagnosis under uneven working conditions on different subtasks simultaneously. This is the reason it can be rendered in practical scenarios.
Conclusion
In this work, improved feature representation and multitask learning-based techniques are proposed for the gearbox fault diagnosis. An improved feature pool is extracted using an image processing technique known as the bag of the visual word representation. Multitask learning is implemented using a deep convolutional neural network. The study aimed to design a generalized network that can simultaneously identify faults in a different set of gears under uneven speed and working conditions. The dataset used in this study is recorded from two different sets of gears, i.e., spur and helical gears. Moreover, shaft speed and load variations are also experienced in the said dataset. It was learned in this work that by using multitask learning approach with a refined feature extraction technique it is possible to perform fault.
Data availability statement
The original contributions presented in the study are included in the article/supplementary materials, further inquiries can be directed to the corresponding authors.
Author contributions
All authors listed have made a substantial, direct, and intellectual contribution to the work and approved it for publication.
Funding
This research was financially supported by the Ministry of Small and Medium-sized Enterprises (SMEs) and Startups (MSS), Korea, under the “Regional Specialized Industry Development Plus Program (R&D, S3092711)” supervised by the Korea Institute for Advancement of Technology(KIAT). This work was also supported by the Korea Technology and Information Promotion Agency (TIPA) grant funded by the Korea government(SMEs) (No. S3126818).
Conflict of interest
The authors declare that the research was conducted in the absence of any commercial or financial relationships that could be construed as a potential conflict of interest.
Publisher’s note
All claims expressed in this article are solely those of the authors and do not necessarily represent those of their affiliated organizations, or those of the publisher, the editors and the reviewers. Any product that may be evaluated in this article, or claim that may be made by its manufacturer, is not guaranteed or endorsed by the publisher.
References
Althubaiti, A., Elasha, F., and Teixeira, J. A. (2022). Fault diagnosis and health management of bearings in rotating equipment based on vibration analysis - a review. J. Vibroeng. 24 (1), 46–74. doi:10.21595/jve.2021.22100
Azamfar, M., Singh, J., Bravo-Imaz, I., and Lee, J. (2020). Multisensor data fusion for gearbox fault diagnosis using 2-D convolutional neural network and motor current signature analysis. Mech. Syst. Signal Process. 144, 106861. doi:10.1016/j.ymssp.2020.106861
Duraivelu, S. K., and Duraivelu, K. (2021). Fault diagnosis of various rotating equipment using machine learning approaches - a review. Proc. Institution Mech. Eng. Part E J. Process Mech. Eng. 235 (2), 629–642. doi:10.1177/0954408920971976
Hajnayeb, A., Ghasemloonia, A., Khadem, S. E., and Moradi, M. H. (2011). Application and comparison of an ANN-based feature selection method and the genetic algorithm in gearbox fault diagnosis. Expert Syst. Appl. 38 (8), 10205–10209. doi:10.1016/j.eswa.2011.02.065
Jaber, S. M. A. A., and Jaber, A. A. (2021). A data-driven approach based bearing faults detection and diagnosis: A review. IOP Conf. Ser. Mat. Sci. Eng. 1094 (1), 012111. doi:10.1088/1757-899x/1094/1/012111
Kim, M. J.-M., and Kim, J.-M. (2018). Reliable fault diagnosis of rotary machine bearings using a stacked sparse autoencoder-based deep neural network. Shock Vib. 2018, 1–11. doi:10.1155/2018/2919637
Kim, M. J. J., and Kim, J. (2020). Deep convolutional neural network with 2D spectral Energy maps for fault diagnosis of gearboxes under variable speed BT - pattern recognition and artificial intelligence, 106–117. doi:10.1007/978-3-030-37548-5_9
Li, C., Zhang, S., Qin, Y., and Estupinan, E. (2020). A systematic review of deep transfer learning for machinery fault diagnosis. Neurocomputing 407, 121–135. doi:10.1016/j.neucom.2020.04.045
Li, Z. (2009). DATA,” CWRU bearing dataset and Gearbox dataset of IEEE PHM Challenge Competition, 2019. (Accessed Jan. 10, 2022). doi:10.21227/g8ts-zd15
Liu, G., Bao, H., and Han, B. (2018). A stacked autoencoder-based deep neural network for achieving gearbox fault diagnosis. Math. Problems Eng. 2018, 1–10. doi:10.1155/2018/5105709
Liu, J. G., and Liu, G. (2020). Knowledge extraction and insertion to deep belief network for gearbox fault diagnosis. Knowledge-Based Syst. 197, 105883. doi:10.1016/j.knosys.2020.105883
Liu, L., Ma, Y., Zhang, X., Zhang, Y., and Li, S. (2017). High discriminative SIFT feature and feature pair selection to improve the bag of visual words model. IET Image Process. 11 (11), 994–1001. doi:10.1049/iet-ipr.2017.0062
Liu, R., Yang, B., Zio, E., and Chen, X. (2018). Artificial intelligence for fault diagnosis of rotating machinery: A review. Mech. Syst. Signal Process. 108, 33–47. doi:10.1016/j.ymssp.2018.02.016
Mallikarjuna, P. B., Sreenatha, M., Manjunath, S., and Kundur, N. C. (2020). Aircraft gearbox fault diagnosis system: An approach based on deep learning techniques. J. Intelligent Syst. 30 (1), 258–272. doi:10.1515/jisys-2019-0237
Praveenkumar, T., Sabhrish, B., Saimurugan, M., and Ramachandran, K. I. (2018). Pattern recognition based on-line vibration monitoring system for fault diagnosis of automobile gearbox. Measurement 114, 233–242. doi:10.1016/j.measurement.2017.09.041
Qiu, G., Gu, Y., and Cai, Q. (2019). A deep convolutional neural networks model for intelligent fault diagnosis of a gearbox under different operational conditions. Measurement 145, 94–107. doi:10.1016/j.measurement.2019.05.057
Saufi, S. R., Ahmad, Z. A. B., Leong, M. S., and Lim, M. H. (2020). gearbox fault diagnosis using a deep learning model with limited data sample. IEEE Trans. Ind. Inf. 16 (10), 6263–6271. doi:10.1109/TII.2020.2967822
Singh, J., Azamfar, M., Ainapure, A., and Lee, J. (2020). Deep learning-based cross-domain adaptation for gearbox fault diagnosis under variable speed conditions. Meas. Sci. Technol. 31 (5), 055601. doi:10.1088/1361-6501/ab64aa
Sohaib, M., and Kim, J. M. (2017). A robust deep learning based fault diagnosis of rotary machine bearings. Adv. Sci. Lett. 23, 12797–12801. doi:10.1166/asl.2017.10902
Tang, S., Zhu, Y., and Yuan, S. (2022). A novel adaptive convolutional neural network for fault diagnosis of hydraulic piston pump with acoustic images. Adv. Eng. Inf. 52, 101554. doi:10.1016/j.aei.2022.101554
Tang, S., Zhu, Y., and Yuan, S. (2022). Intelligent fault diagnosis of hydraulic piston pump based on deep learning and Bayesian optimization. ISA Trans. doi:10.1016/j.isatra.2022.01.013
Tang, S., Zhu, Y., and Yuan, S. (2022). Intelligent fault identification of hydraulic pump using deep adaptive normalized CNN and synchrosqueezed wavelet transform. Reliab. Eng. Syst. Saf. 224, 108560. doi:10.1016/j.ress.2022.108560
Vernekar, K., Kumar, H., and Gangadharan, K. (2017). Engine gearbox fault diagnosis using empirical mode decomposition method and Naïve Bayes algorithm. Sādhanā 42 (7), 1143–1153. doi:10.1007/s12046-017-0678-9
Vernekar, K., Kumar, H., and V Gangadharan, K. (2018). Engine gearbox fault diagnosis using machine learning approach. J. Qual. Maint. Eng. doi:10.1108/jqme-11-2015-0058
Wei, S., Wang, D., Peng, Z., and Feng, Z. (2022). Variational nonlinear component decomposition for fault diagnosis of planetary gearboxes under variable speed conditions. Mech. Syst. Signal Process. 162, 108016. doi:10.1016/j.ymssp.2021.108016
Wu, C., Jiang, P., Ding, C., Feng, F., and Chen, T. (2019). Intelligent fault diagnosis of rotating machinery based on one-dimensional convolutional neural network. Comput. Industry 108, 53–61. doi:10.1016/j.compind.2018.12.001
Xia, T., Jiang, Y., Zhuo, P., Xi, L., and Wang, D. (2021). Dual-ensemble multi-feedback neural network for gearbox fault diagnosis. IEEE Trans. Instrum. Meas. 70 (1–10), 1–10. doi:10.1109/tim.2021.3089250
Zappalá, D., Tavner, P. J., Crabtree, C. J., and Sheng, S. (2014). Side‐band algorithm for automatic wind turbine gearbox fault detection and diagnosis. IET Renew. Power Gener. 8 (4), 380–389. doi:10.1049/iet-rpg.2013.0177
Keywords: gearbox, fault diagnosis and prognosis, condition-based monitoring, feature learning, natural language processing, multitask learning
Citation: Sohaib M, Munir S, Islam MMM, Shin J, Tariq F, Ar Rashid SMM and Kim J-M (2022) Gearbox fault diagnosis using improved feature representation and multitask learning. Front. Energy Res. 10:998760. doi: 10.3389/fenrg.2022.998760
Received: 20 July 2022; Accepted: 17 August 2022;
Published: 07 September 2022.
Edited by:
Enhua Wang, Beijing Institute of Technology, ChinaCopyright © 2022 Sohaib, Munir, Islam, Shin, Tariq, Ar Rashid and Kim. This is an open-access article distributed under the terms of the Creative Commons Attribution License (CC BY). The use, distribution or reproduction in other forums is permitted, provided the original author(s) and the copyright owner(s) are credited and that the original publication in this journal is cited, in accordance with accepted academic practice. No use, distribution or reproduction is permitted which does not comply with these terms.
*Correspondence: Muhammad Sohaib, bWQuc29oYWliQGxndS5lZHUucGs=; Jong-Myon Kim, am9uZ215b24ua2ltQGdtYWlsLmNvbQ==