- 1Yunnan Academy of Tobacco Agricultural Sciences, Kunming, Yunnan, China
- 2Yunnan Tobacco Quality Supervision and Test Station, Kunming, Yunnan, China
The use of mild pretreatment conditions can significantly lower the cost of the biorefining process. This study evaluated a mild pretreatment approach for tobacco stem waste using a combination of dilute acid and dilute alkali. By optimizing the pretreatment conditions, we obtained a high reducing sugar concentration at a pretreatment temperature <100°C. Increasing the acid or alkali strength in a single pretreatment step did not always improve the result; instead, the synergistic effect of both pretreatment components was important. To increase the bioethanol titer, a high solid loading, 30%, was used for bioethanol fermentation. Compared with batch fermentation, enzyme feeding with a shorter feeding period (24 h) enhanced the bioethanol production by 4.32%, generating 86.88 g/L bioethanol. The results provide valuable insights into the effects of two-step acid/alkali pretreatment on enzymolysis. The findings suggest that the optimized synergistic pretreatment process is efficient for bioethanol fermentation.
1 Introduction
Economic and societal development is heavily dependent on energy supply (Rezania et al., 2020). The identification and production of non-fossil-fuel energy sources is an important area of research (Hanif et al., 2019). As fossil-reliant industries turn to sustainable biomass for energy and material supply, the competition for biogenic carbon is expected to intensify. Sustainable biofuels are gaseous or liquid biofuels that are not considered to have a detrimental effect on the environment (Jafri et al., 2022). Among potential renewable and clean energy sources, lignocellulose is considered to be a promising raw material, and cellulose-based fuel might provide a solution to the current energy crisis (Baeyens et al., 2015). Bioethanol is the most important liquid biofuel and is used as a fuel or gasoline enhancer worldwide (Momayez et al., 2018). Cellulosic ethanol is a potential solution to problems related to fossil fuel consumption.
Lignocellulosic biomass is a complicated mixture of carbohydrate polymers including cellulose (38%–50%), hemicellulose (23%–32%), and lignin (15%–25%) (Mamman et al., 2008). While hundreds of billions of tons of lignocellulosic biomass waste are produced annually, they are usually disposed of in landfills or by burning (Luo et al., 2014). Lignocellulosic biomass, including agricultural residues, is abundantly available without geographical limitation (Liu et al., 2019). In general, lignin inhibits cellulases in three ways: 1) as a physical barrier to block or restrict cellulose accessibility to enzymes; 2) adsorbing enzymes nonproductively to compete with cellulose; and 3) deactivating enzymes (Zhu & Pan, 2022). It is thus necessary to pretreat lignocellulosic biomass (Tu and Hallett, 2019); pretreatment methods increase the porosity and provide easily accessible binding sites for enzymes (Kumari and Singh, 2018; Bhatia et al., 2020). At present, the most fruitful researches are focused in the downstream such as developing co-products and novel robust enzymes, pretreatment remains the bottleneck for biorefinery. The more attentions should be paid to upstream process, because it affects everything in downstream and dictates the successful commercialization of biorefinery. Small improvements in pretreatment can yield substantial benefits to the overall process runnability, environmental sustainability, and economics of the entire biorefinery (Zhu and Pan, 2022). To efficient hydrolyze the cellulose by cellulases, the lignin and/or hemicellulose should be removed, at least partially. The different pretreatment processes have different advantages and pitfalls, and the single pretreatment method mainly remove one component of lignocellulosic biomass usually. Two-step pretreatment methods integrate the advantages of different pretreatment strategies to reduce the pretreatment intensity and cost. The two-step pretreatment improve the biomass conversion efficiency due to lignin removal, partial hemicellulose dissolution and high cellulose yield in subsequent enzymatic hydrolysis. Additional, the pretreatment severity was reduced and sugar recovery was increased, which facilitated cost reduction of biorefinery (Chen and Liu, 2015).
Cellulosic raw materials used for bioethanol production include grass waste (Yan et al., 2020), bamboo (Li et al., 2017), rice straw (Momayez et al., 2018), empty oil palm fruit bunches (Coral Medina et al., 2018), and sugarcane bagasse (de Araujo Guilherme et al., 2019). However, the ethanol titers obtained by cellulosic ethanol production are lower than that of those from fermentation from grains. This disadvantage increases energy consumption for ethanol recovery by distillation, and subsequently discharges large amounts of stillage to be treated properly (Koppram et al., 2014; Liu et al., 2019). Thus, cellulosic ethanol is not economically competitive with ethanol produced from starch- and sugar-based feedstocks. BioRen project research results in an increased value of selected biomass waste feeding into biofuels and the development of technology for the production of effective drop-in fuel additives (Kowalski, et al., 2022).
Various pretreatment technologies have been combined for use in biorefining. A two-stage pretreatment combining alkaline sulfonation and steam treatment was used to enhance the enzymatic digestibility of eucalyptus woody biomass or bioethanol production. After fermentation of the concentrated resulting enzymatic hydrolysate, 74.24 and 14.72 g/L ethanol were respectively obtained from glucose and xylose (Chu et al., 2018). The pH of pretreatment is an important factor for enhancing hydrolysis efficiency of biomass and reducing the inhibitors formation. The undetoxified whole slurry at a solid loading of 21% were facilitated by a novel approach of “pH profiling” in pretreatment, which resulted in a terminal ethanol titer of 48.9 ± 1.4 g/L and yield of 297 ± 9 L/tonne Douglas-fir forest residue (Cheng et al., 2015). Using a two-step acid/alkaline-peroxide pretreatment process, ethanol was produced from hemicellulosic sugars (which were solubilized in the acid pretreatment step) and glucose (from the enzymatic hydrolysis of delignified olive tree biomass), yielding 15 g of ethanol per 100 g of biomass (Martínez-Patiño et al., 2017). A 4.6% (w/v) ethanol titer was obtained from bamboo after alkaline pre-extraction followed by treatment with alkaline hydrogen peroxide (Yuan et al., 2018). The introduction of a water or alkaline extraction step before pretreatment with dilute acid for rice straw was shown to reduce enzyme dosage by 23%–39% (Soam et al., 2018). After pretreatment with dilute hydrochloric acid and lime, glucose and xylose yields of 78.0% and 97.0%, respectively, were obtained from corn stover (Zu et al., 2014). A two-step process involving dilute sulfuric acid and a sulfomethylation reagent was applied to pretreat rice straw; 40.60 g/L ethanol were produced from 100 g/L rice straw (Zhu et al., 2015). High conversion (99.36%) of cellulose into glucose was observed for cellulose residue pretreated by formic acid organosolv and alkaline hydrogen peroxide (Li et al., 2017). On pretreating corn stover with sequential dilute acid and alkali before enzymatic hydrolysis, the overall glucose and xylose yields reached 89.1%–97.9% and 71.0%–75.9%, respectively (Lee et al., 2015). Fermentation of glucose and xylose led to production of 26.9 and 9.4 g/L ethanol, respectively, from rice straw pretreated with sulfuric acid and sodium hydroxide (Kaur and Kuhad, 2019).
China is the world’s largest producer of tobacco leaf, and its total output accounts for 42% of the world’s total output, which resulting huge amount of tobacco stem (Yuan et al., 2019). The tobacco stem waste was abandoned in field, which could pollute the environment. Using tobacco stem waste for bio-based chemicals and fuels represents a valid alternative to reorganize a sustainable local economy. In the present study, a mild acidic–alkaline pretreatment was used to improve the biodegradability of tobacco stem waste. The synergistic effect of the acidic–alkaline pretreatment was confirmed, and the preprocessing parameters were optimized. Meanwhile, different feeding strategies were investigated to obtain high-titer bioethanol at high solid loading. The results demonstrate the technical feasibility of using two-step acidic–alkaline pretreatment for bioethanol production from tobacco stem waste.
2 Materials and methods
2.1 Materials
Tobacco stem waste (TSW) was obtained from the fields of Songming County (Kunming, China) in 2019. The fresh TSW was washed with tap water to remove soil and other impurities. The washed TSW was sun-dried and stored in a valve bag at room temperature. The sun-dried TSW was smashed and sieved through a 0.15-mm mesh. The moisture content of sun-dried TSW was 10.26 ± 1.37%.
Commercial cellulase (Cellic® Ctec2) was obtained from Sigma-Aldrich. The protein content of Cellic CTec2 was found to be 96.85 ± 2.18 mg BSA equivalents/g of the enzyme. The activity was 115.20 filter paper unit/ml (FPU/mL).
2.2 Pretreatment
Pretreatment with dilute sulfuric acid was performed in 500-ml reagent bottles. For pretreatment with non-optimized dilute sulfuric acid, TSW was soaked in 1% H2SO4 solution (w/v) [solid-to-liquid 10% (w/v)], followed by stirring thoroughly with a glass rod. The TSW was pretreated at 115°C for 30 min. The TSW pretreated with dilute sulfuric acid was collected and washed with distilled water until reaching neutral pH. Finally, the pretreated TSW was oven-dried at 55°C.
Pretreatment with dilute sodium hydroxide was carried out in 500-ml reagent bottles. For non-optimized alkaline pretreatment, TSW was soaked in 3% NaOH [solid-to-liquid 10% (w/v)] followed by stirring thoroughly with a glass rod. The TSW was treated at 80°C for 3 h with stirring every 30 min. The product was collected and washed with distilled water until neutral pH was reached. Finally, the pretreated TSW was oven-dried at 55°C. The moisture content of spretrated TSW was 6.15 ± 0.72%.
For two-step pretreatment, the TSW was pretreated by acid or alkali, and the redried TSW was then pretreated by alkali or acid, respectively.
To optimize the two-step pretreatment parameters, the pretreatments with dilute sulfuric acid were conducted with different acid concentrations (0.1%, 0.3%, 0.5%, 1.0%, 2.0%, 3.0%, and 4.0%), pretreatment temperatures (70, 80, 95, 105, 110, 115, and 120°C), and solid-to-liquid ratios (4%, 8%, 10%, 15%, and 20%). Subsequently, alkali pretreatment was conducted as previously described.
After optimizing the dilute sulfuric acid pretreatment conditions, the parameters of dilute sodium hydroxide pretreatment were also optimized by conducting the pretreatment at different alkali concentrations (0.2%, 0.5%, 0.8%, 1.0%, 3.0%, 5.0%, 7.0%, and 10.0%), pretreatment temperatures (60, 70, 80, 90, and 100°C), pretreatment times (1.0, 1.5, 2.0, 2.5, and 3.0 h), and solid-to-liquid ratios (2%, 4%, 6%, 8%, 10%, and 15%).
2.3 Enzymatic hydrolysis
Enzymatic hydrolysis was performed in 10-ml bottles in a rotary shaker (55°C, 150 rpm) for 72 h. Pretreated TSW was suspended in 50 mM sodium citrate buffer (pH 4.8) at 4% (w/v). Subsequently, 35 FPU/g of pretreated, pretreated TSW were added. After enzymatic hydrolysis, the hydrolysate was centrifuged at 10,000 g for 3 min. The supernatant (0.3 ml) was diluted by appropriate multiples, and the concentration of reducing sugar was determined by the 3,5-dinitrosalicylic acid (DNS) method. The enzymolysis efficiency of pretreated TSW was calculated as the previous description (Yan et al., 2020). The glucose and xylose yield was calculated according to the following Eqs 1, 2, respectively.
2.4 Bioethanol fermentation
The SHY07-1 yeast was used for fermentation, which can use xylose and glucose for ethanol fermentation. Yeast SHY07-1, which is an intergeneric protoplast fusant between Saccharomyces cerevisiae (a gift from the Sanhe ethanol factory, Zanjiang, Guangdong Province, China) and Pichia stipitis (a gift from the Guangzhou Sugarcane Industry Research Institute, Guangzhou, China) that possesses the ability to convert not only glucose but also xylose into ethanol, was used in this study. The seed medium and culture conditions referred to a previous study (Zhu et al., 2012). The pretreated TSW was used for carbon source, (NH4)2SO4 (2 g/L), CaCO3 (2 g/L), MgSO4∙7H2O (0.5 g/L), KH2PO4 (5 g/L), and yeast extract (5 g/L). The medium pH was adjusted to 7.0 ± 0.1. The bioethanol fermentation (Simultaneous saccharification and co-fermentation (SSCF)) was conducted in 100-ml serum bottles. For different pre-enzymolysis times, the fermentation medium with a solid loading of 10% (w/w) pretreated TSW was used for SSCF. Cellulase was added at a loading of 15 FPU/g of pretreated TSW to all samples. A yeast (OD600 2.0) inoculum dosage of 10% (v/v) was inoculated to the medium after enzyme added to the fermentation medium with various times (0, 6, 12, 24, 36 and 48 h). Bottles were incubated in a rotary shaker at 30°C, 180 rpm for 192 h during which 0.2 ml of samples were withdrawn periodically. For feeding strategies, the pretreated TSW and enzyme were added to the fermentation medium were shown in Table 1 and Table 2. The feeding strategies contain enzyme feeding, substrate feeding and enzyme/substrate feeding, and the feeding times were listed in Table 1 and Table 2.
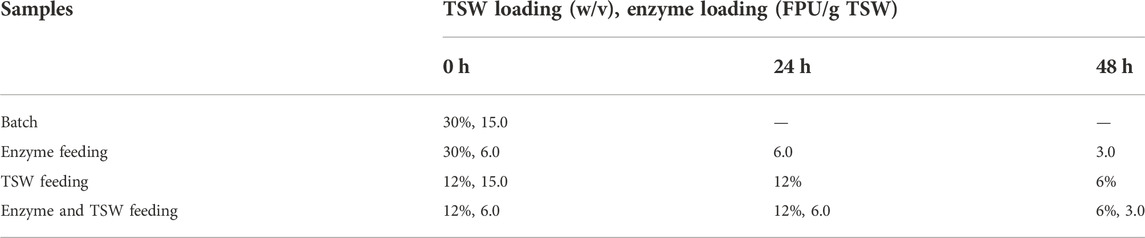
TABLE 1. Enzyme and TSW loadings for different feeding strategies in fed-batch SSCF with a feeding period of 48 h.
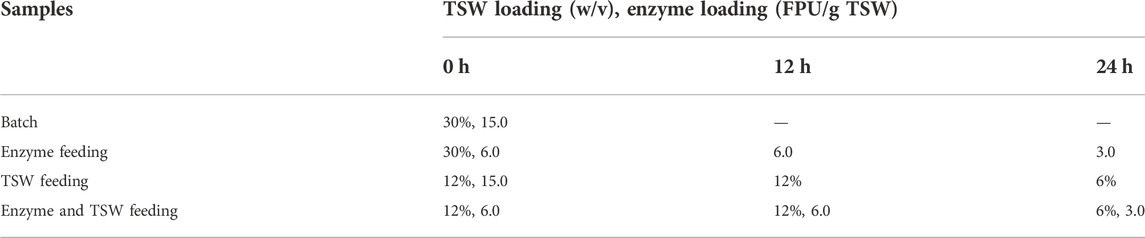
TABLE 2. Enzyme and TSW loadings for different feeding strategies in fed-batch SSCF with a feeding period of 24 h.
The ethanol yield was calculated according to the following Eq. 3.
2.5 Analytical methods
The chemical composition of raw and pretreated TSW samples was analyzed following National Renewable Energy Laboratory standard protocols (Yan et al., 2020). The glucan, xylan and lignin content were calculated according to the following Eqs 4, 5, and 6, respectively. The DNS method was used to determine reducing sugar concentration (Breuil and Saddler, 1985). Scanning electronic microscopy (SEM), Fourier-transform infrared spectroscopy (FTIR), and X-ray diffraction were conducted as previously described (Zhang and Zhu, 2016; Yan et al., 2020). Ethanol, glucose, and xylose concentrations were determined by high-performance liquid chromatography (Waters 2414, Framingham, Massachusetts, United States) with an Aminex HPX-87H column and a refractive index detector (Bio-Rad, Hercules, CA, United States) (Yan et al., 2020).
C1: Glucose concentration, α: Correction coefficient of glucose, C2: Xylose concentration, β: Correction coefficient of xylose, m1: substrate weight.
2.6 Statistical analysis
Statistical analyses used SPSS for Windows software v.17 (SPSS Inc., Chicago, IL, United States) with p < 0.05 indicating statistical significance.
3 Results and discussion
3.1 Effect of two-step pretreatment on efficiency of enzymatic hydrolysis
The glucose yield can be enhanced significantly by two-step pretreatment. For sugarcane bagasse, after one-step 60% ethanol containing 0.5% NaOH pretreatment, the glucose yield was enhanced by 41% and 205% compared to that pretreated with only 0.5% NaOH or 60% ethanol. However, using combinatorial pretreatments with 1% H2SO4 followed by 60% ethanol containing 0.5% NaOH, the highest glucose yield with Tween 80 reached 76%, representing 84.5% of the theoretical glucose in the pretreated substrate (Zhang et al., 2018). While two-step pretreatment processes have been widely reported, the pretreatment sequence has largely been ignored. In the present study, the two-step pretreatment sequence was studied, aiming to improve the efficiency of enzymatic hydrolysis. As shown in Figure 1, the reducing sugar concentrations rapidly increased during the first 12 h of enzymatic hydrolysis, then the growth rates of reducing sugar concentrations gradually decreased. Finally, the reducing sugar concentrations became roughly stable after 48 h of hydrolysis. Thus, for subsequent enzymatic hydrolysis of TSW, the enzymatic hydrolysis time used was 48 h. When the TSW was first pretreated by dilute sulfuric acid followed by pretreatment with dilute sodium hydroxide (acid/alkali pretreatment), the concentration of reducing sugar reached 24.83 g/L. In contrast, when the TSW was first pretreated by dilute sodium hydroxide and then pretreated by dilute sulfuric acid (alkali/acid pretreatment), the reducing sugar concentration only reached 20.98 g/L, a decrease of 15.51% compared with the acid/alkali pretreatment. For raw TSW without pretreatment, the reducing sugar concentration was only 6.64 g/L, much lower than for pretreated TSW. Thus, in subsequent experiments, the raw TSW was subjected to acid/alkali pretreatment.
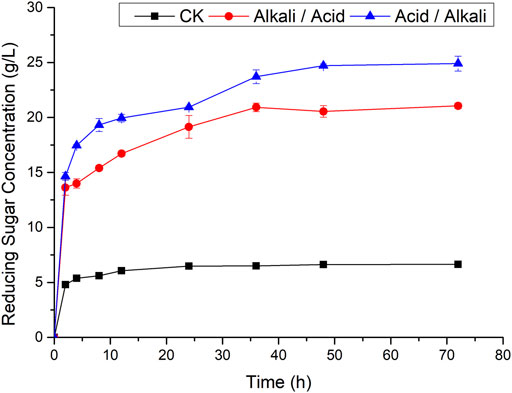
FIGURE 1. Effects of two-step pretreatment on efficiency of enzymatic hydrolysis (CK: raw TSW; alkali/acid: alkali-pretreated followed by acid-pretreated TSW; acid/alkali: acid-pretreated followed by alkali-pretreated TSW).
3.2 Optimization of dilute sulfuric acid pretreatment parameters
Acid pretreatment disrupts lignocellulose by cleaving glucosidic bonds; this solubilizes mostly hemicellulose as well as some of the lignin. This then makes the cellulose more accessible to enzymatic attack (Sahoo et al., 2018). Dilute acid pretreatment can be applied at high temperatures (100–190°C) for short periods of time (20 min), or at lower temperatures (120°C) for longer durations (30–90 min) (Lorenci Woiciechowski et al., 2020). To decrease the pretreatment intensity and cost, the dilute sulfuric acid pretreatment parameters were optimized. As shown in Figure 2A, the efficiency of enzymatic hydrolysis of pretreated TSW gradually increased with increasing acid concentration until the acid concentration reached 0.5%. When the acid concentration was increased beyond 0.5%, the reducing sugar concentration decreased. Higher acid concentrations lead to more efficient hemicellulose removal, thereby resulting in greater xylose loss during pretreatment. Similarly, it was found that the yield of reducing sugar from acid-pretreated rice straw increased on increasing the acid concentration from 1% to 3% and then decreased when the acid concentration was increased to >3% (Kaur and Kuhad, 2019). In the present study, the highest yield of reducing sugar was obtained at a lower acid concentration (0.5%), which will lower the pretreatment cost compared with processes requiring higher acid concentrations. Moreover, compared with strong acid pretreatment, dilute acid pretreatment is less toxic, corrosive, and hazardous, making it easier to scale up the process (Lorenci Woiciechowski et al., 2020).
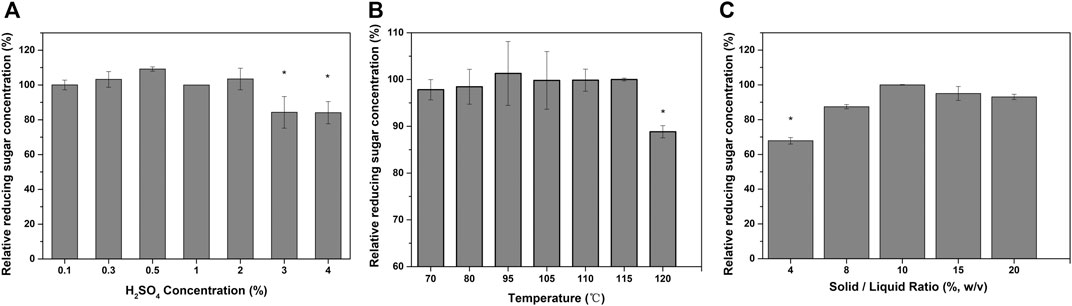
FIGURE 2. Effects of different acid pretreatment conditions on the enzymatic hydrolysis of TSW: (A) sulfuric acid concentration; (B) pretreatment temperature; and (C) solid-to-liquid ratio.
The effect of acid pretreatment temperature on reducing sugar production is shown in Figure 2B. The reducing sugar concentration was not significantly influenced by acid pretreatment temperature at <115°C. For single acid pretreatment, the pretreatment efficiency increased with increasing pretreatment temperature; however, for two-step pretreatment, the acid pretreatment temperature was not related to the production of reducing sugar. In two-step pretreatment, a high acid pretreatment temperature might facilitate the release of reducing sugar, resulting in decreased reducing sugar yield from the pretreated substrate. In this work, the highest yield of reducing sugar was obtained at 95°C, which can be easily achieved without high equipment costs. In two-step pretreatment with formic acid organosolv then alkaline hydrogen peroxide, the cellulose conversion rate increased with increasing formic acid pretreatment temperature (Li et al., 2017). The difference between the findings of the present study and past studies may relate to the different pretreatment mechanisms. Previous study found that increasing the pretreatment temperature led to there being less cellulose in the residual solid material, thereby decreasing the amount of glucose available after further enzymatic digestion (Hsu et al., 2010).
Increasing the solid loading can significantly decrease the cost of pretreatment. The production of reducing sugar was significantly enhanced, by 47.34%, upon increasing the solid-to-liquid ratio from 4% to 10% (Figure 2C). However, when the ratio was increased to 15% or 20%, the reducing sugar production decreased slightly, because at these high solid-to-liquid ratios the substrate could not be effectively pretreated by acid.
The acid pretreatment parameters evaluated in this study were temperature, acid concentration, reaction time, and the solid-to-liquid ratio. Varying these factors changes the severity of the process (Lorenci Woiciechowski et al., 2020). The optimized values we determined were: 95°C, 0.5%, 0.5 h, and 10%, respectively. These optimal acid pretreatment parameters can be achieved under atmospheric conditions. The acid pretreatment intensity had no positive relationship with the production of reducing sugar. A balance between the acid pretreatment and alkali pretreatment is needed, and the pretreatment intensity can be significantly decreased.
3.3 Optimization of dilute sodium hydroxide pretreatment parameters
Section 3.2 demonstrates that the optimum acid pretreatment conditions are significantly different in two-step pretreatment compared with those in single acid pretreatment. For single alkaline pretreatment, the optimal alkali concentration is high, while the optimal solid-to-liquid ratio is low. To improve the enzymatic hydrolysis efficiency and decrease the intensity of alkaline pretreatment, the alkali pretreatment parameters were also optimized. For two-step pretreatment, the effect of NaOH concentration on reducing sugar production is shown in Figure 3A. The reducing sugar production was relatively low when the NaOH concentration was <0.8%. The reducing sugar production increased by nearly three times when the NaOH concentration was increased from 0.8% to 1.0%. The reducing sugar production then decreased gradually as the NaOH concentration was increased at >1.0%. In single NaOH pretreatment, enzymatic hydrolysis efficiency is positively associated with NaOH concentration (Yan et al., 2020). Here, the efficiency of enzymatic hydrolysis first increased with increasing NaOH concentration and then decreased. Thus, the optimal conditions for single NaOH pretreatment cannot be applied to two-step pretreatment. As shown in Figure 3B, the reducing sugar production gradually increased as the pretreatment temperature was increased. The efficiency of lignin removal increases with increasing pretreatment temperature, leading to enhanced reducing sugar production. However, in this study, the reducing sugar production did not increase significantly when the alkali treatment temperature was increased beyond 90°C; thus, the optimal alkali pretreatment temperature was determined to be 90°C. Similarly, Huang et al. (2020) found that increasing the pretreatment temperature enhanced enzymatic hydrolysis efficiency only up to a certain temperature.
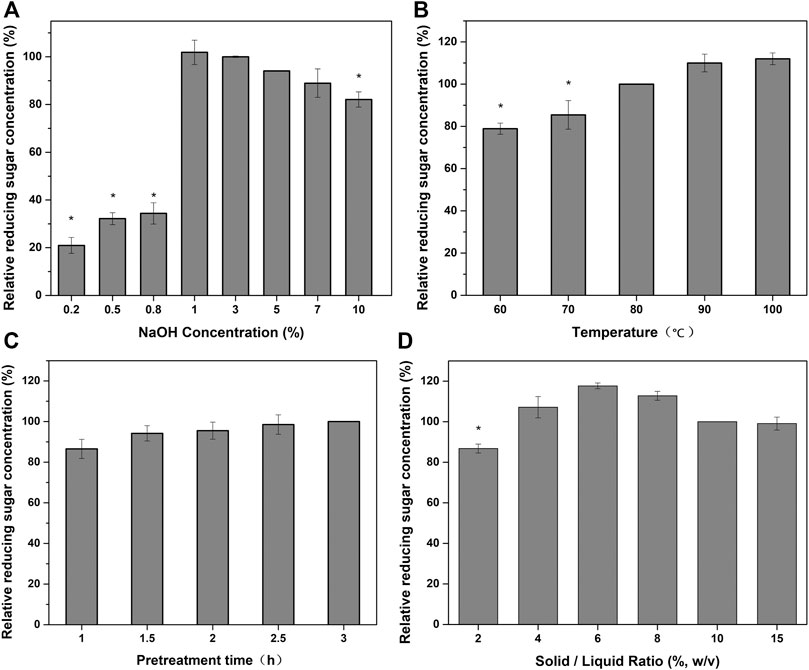
FIGURE 3. Effects of different alkali pretreatment conditions on the enzymatic hydrolysis of TSW: (A) sulfuric acid concentration; (B) pretreatment temperature; (C) pretreatment time; and (D) solid-to-liquid ratio.
The effect of pretreatment time on reducing sugar production was similar to the effect of pretreatment temperature (Figure 3C). Based on these results, the optimal pretreatment time of 2.5 h was selected for further experiments. The solid-to-liquid ratio significantly affected reduction sugar production (Figure 3D). The reducing sugar production first increased as the solid-to-liquid ratio was increased from 2% to 6% and then decreased as the ratio was increased to 15%. As for acid pretreatment, high substrate concentrations limited the efficiency of mass transfer, resulting in low reducing sugar production. The glucose yield increase was consistent with the increase of the cellulose content after pretreatment. For two-step pretreatment (Liquid hot water/Ozonolysis), 43.0 g/L glucose was generated after enzymatic hydrolysis at 10% (w/v) of pretreated sugarcane, corresponding to 59% of conversion from initial glucan vs. 20, 47, 37, and 10% for untreated, ozone, liquid hot water, and two-step pretreated samples, respectively (Bordignon et al., 2022). Compared with present study, the higher glucose concentration obtained from two-step pretreatment (Liquid hot water/Ozonolysis) is possible due to the higher glucan content of pretreated sugarcane. As re-localized lignin accumulates, it may enclose cellulose fibers and block the access of enzymes for hydrolysis (Pielhop et al., 2015). In the present study, increasing the pretreatment intensity did not always enhance enzymolysis. This may be related to the synergistic effect of alkali and acid pretreatment, which resulted in a suitable substrate for enzymolysis.
3.4 Characterization of raw and pretreated tobacco stem waste
Cellulose is a stable polysaccharide and the most valuable component in lignocellulose. Hemicellulose is an amorphous, branched, heteropolysaccharide composed of pentoses, hexoses, uronic acids, and desoxyhexoses. Hemicellulose readily interacts with cellulose, creating a flexible and stable lignocellulosic matrix. Lignin controls the permeability of cellulose, improves the mechanical properties of cells, and protects them from degradation by microorganisms and chemicals (Lorenci Woiciechowski et al., 2020). The aim of pretreatment of lignocellulose is to separate the biomass components. The pretreatment process breaks down the lignin structure, removes hemicellulose, and increases the accessible surface area of cellulose available to enzymes (Solarte-Toro et al., 2019).
The maximum degradability of pretreated substrate cannot be achieved by a single pretreatment process. Upon two-step pretreatment with H2SO4 and NaOH for corn stover, glucan and xylan conversion increased by 11.2% and 8.3% relative to single pretreatment. The With whole fractionation by combinatorial pretreatment, glucose and xylose yields were 88.4% and 72.6%, respectively, representing increases of 10.0% and 8.1%. Lignin yield was 19.7% in solid residue and 77.6% in liquid stream, which increased by 33.4% (Liu et al., 2017). As Table 3 shows, the lignin content in raw TSW was 31.16%, and the lignin was efficiently removed by alkaline pretreatment. But, compared with alkaline pretreatment alone, the two-step acid/alkali pretreatment further promoted lignin removal and increased the glucan content. Lignin removal was highest in the optimized two-step pretreatment conditions, while the glucan content was slightly lower than for the other two-step pretreatments. The higher removal of lignin contributed to a higher reducing sugar production. The reducing sugar productions of all two-step pretreatments were higher than those of the single pretreatments. For acid pretreatment, the reducing sugar production was slightly higher than that from raw TSW and significantly less than that following single alkaline pretreatment. The reducing sugar production following the optimized alkali pretreatment was similar to that of the alkali/acid pretreatment. These results indicate that the pretreatment sequence affected the enzymatic hydrolysis efficiency, and the acid/alkali pretreatment had a synergistic effect to remove the lignin and enhance the enzymolysis.
The effect of the pretreatment method on the micromorphology of TSW was examined by SEM (Supplementary Figure S1). The surface of raw TSW was compact and smooth, indicating that the cellulose was tightly wrapped by hemicellulose and lignin, with poor accessibility between cellulase and TSW. Acid pretreatment resulted in a only slight change in the surface morphology. After the two-step pretreatment, small pores formed on the surface of the pretreated TSW, especially after the optimal acid/alkali pretreatment. These pores would facilitate contact between enzyme and the embedded cellulose, thereby enhancing the enzymolysis efficiency. The crystallinity index (CrI) is influenced by the composition of the lignocellulose; the lignin and hemicellulose components are amorphous, whereas cellulose is crystalline (Ling et al., 2017). The CrI of raw TSW was 16.42%, while that of acid/alkali-pretreated TSW was 22.95% (Supplementary Figure S2). After optimization of the two-step pretreatment parameters, the CrI of pretreated TSW reached 49.40%. This demonstrates that the optimized acid/alkali pretreatment method can improve the removal of lignin and enhance the efficiency of enzymolysis of pretreated TSW. The CrI of the sugarcane was increased after pretreatment according to the intensity of pretreatment, which the CrI of the combined pretreatment (Liquid hot water/Ozonolysis) was higher than single pretreatment (Liquid hot water or Ozonolysis) (Bordignon et al., 2022). FTIR spectra of raw and pretreated TSW samples indicate that structural changes occurred during pretreatment (Supplementary Figure S3). Compared with the spectrum of raw TSW, in the spectra of the deacetylated substrates (C, D, E, F), significant decresaes were found in the intensities of the peaks at 1,248 and 1735 cm−1, which arise from the stretching of unconjugated C–O and C=O in hemicellulose (Bu et al., 2019). The C=C stretching of aromatic skeletal vibration in lignin caused a peak at 1,510 cm−1 (Li et al., 2018). Among the samples, the intensity of this peak was lowest in the TSW pretreated by the optimal two-step method, suggesting that the polyaromatic structures in lignin underwent oxidation in the optimal conditions.
3.5 Effects of enzyme feeding strategy on bioethanol fermentation
SSF can lower the fermentation time and relieve the inhibition of glucose and xylose toward cellulase, significantly enhancing the rate of enzymatic hydrolysis and promoting the bioconversion of reducing sugars to bioethanol (Zhang et al., 2015). Due to the different suitable temperatures of enzymolysis and fermentation, the enzymatic hydrolysis rate is limited, and the sugar cannot satisfy demand for fermentation. A pre-enzymolysis process can provide sufficient fermentable substrate for yeast growth (Shen and Agblevor, 2011). Different pre-enzymolysis times (0, 6, 12, 24, 36, and 48 h) were evaluated in the present study (Figure 4). In the first 24 h of fermentation, bioethanol production was positively related to pre-enzymolysis time. After 48 h of fermentation, a pre-enzymolysis time of 48 h produced the highest bioethanol concentration. The bioethanol productions with pre-enzymolysis times of 36 and 48 h slowed down at 96 h. This phenomenon may be related to the inhibition of microbial activity at high ethanol concentration. Similar results were described previously (Öhgren et al., 2007). After fermentation, the bioethanol production reached 34.59 g/L for 10% pretreated TSW with a pre-enzymolysis time of 24 h. This was an 8.06% increase in bioethanol production compared with the control (32.00 g/L). The results indicate that pre-enzymolysis for an appropriate time can enhance bioethanol production.
The production of reducing sugar after fermentation with different substrate loadings (10%, 20%, and 30%) was investigated. Without yeast, the glucose concentration reached 64.29, 93.88, and 132.48 g/L for substrate loadings of 10%, 20%, and 30%, respectively. After inoculation with yeast, we could not detect glucose or xylose after fermentation at 10% substrate loading. When the substrate loading was 20% and 30%, the concentrations of glucose were 0.98 and 1.71 g/L, respectively. These results indicate that SHY07-1 had good fermentation performance at high substrate loading.
The inhibition effect of hydrolysates can hinder the production of cellulosic ethanol. Fed-batch fermentation was adopted to combat the inhibition effect of high solid loading and retain the activity of cellulase. In a previous study, fed-batch fermentation required less enzyme and produced a higher ethanol concentration than batch fermentation (de Barros et al., 2017). de Araujo Guilherme et al. (2019) found that fed-batch fermentation required three times less enzyme than the batch process, and the ethanol yield was 88% of the theoretical yield, slightly lower than that of the batch process (92.0% of the theoretical yield). Zhang and Zhu (2017) found that fed-batch fermentation increased ethanol production and reduced enzyme loading compared with the batch process when the substrate was 20% sugarcane bagasse. Hoyer et al. (2010) reported that similar or higher ethanol yields were achieved in fed-batch mode than in batch mode, and the authors observed no general dependence of the yield of ethanol on the enzyme feeding strategy. Romaní et al. (2012) reported that a high solid loading was a key factor in increasing bioethanol production and decreasing the processing cost, thereby reducing energy consumption, in a distillation operation. Table 1 lists the pretreated TSW and enzyme loadings of the different fed-batch strategies evaluated in this study at a final sugarcane bagasse loading of 30% (w/v). The feeding time interval was 24 h, and the overall feeding period was 48 h. Relatively few studies have been performed on batch or fed-batch fermentation with this high (30%) solid loading.
Bioethanol concentration is plotted against fermentation time for the different feeding strategies in Figure 5. Sampling began at a fermentation time of 84 h, when the slurry liquefied obviously. At 84 h, the bioethanol concentration was higher for pretreated TSW feeding, which might be due to the higher enzymatic hydrolysis rate at lower substrate concentration. Pretreated TSW feeding can alleviate the inhibition effect of the substrate on enzymolysis, thereby enhancing bioethanol production in the early part of the fermentation. Subsequently, the advantage of enzyme and pretreated TSW feeding gradually emerged before 120 h. After 144 h of fermentation, the bioethanol concentration was greatest among the feeding strategies with enzyme feeding. These results indicate that enzyme activity and yeast viability were critical for bioethanol production, while the role of mass transfer was less significant. A similar phenomenon was found by Zhang and Zhu (2017). However, the bioethanol concentration the enzyme feeding strategy was not further improved significantly as it was in batch mode. This might be because the yeast viability was poor at high concentrations of ethanol (Rudolf et al., 2005). After fermentation, the bioethanol concentration reached 83.28 g/L, which was not significantly different from those of the other feeding modes. Zhang and Zhu (2017) found that batch and enzyme feeding had a significant advantage over substrate feeding and enzyme and substrate feeding. This might be attributed to a long feeding period (96 h). In the present study, a high bioethanol concentration was obtained from pretreated TSW, suggesting that the two-step acid/alkali pretreatment was an efficient method, and that pretreated TSW is a promising substrate for bioethanol fermentation.
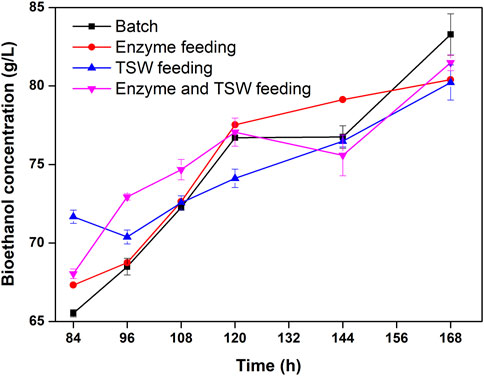
FIGURE 5. Time-course of ethanol concentration during SSCF under different feeding strategies with a feeding period of 48 h.
Compared with previous reports (Zhang and Zhu 2017), the shorter feeding period could reveal the advantage of feeding strategy. Thus, a shorter feeding period of 24 h was further investigated in the present study. The pretreated TSW and enzyme loadings for different feeding strategies are shown in Table 2 for a final sugarcane bagasse loading of 30% (w/v). The feeding time interval was 12 h, and the overall feeding period was 24 h.
The time courses of bioethanol concentration during SSCF with different feeding strategies and a feeding period of 24 h are shown in Figure 6. Throughout the fermentation period, the bioethanol concentration for enzyme feeding was higher than those in other feeding modes. During the first 108 h of fermentation, the bioethanol productions were similar for batch and enzyme feeding. After 108 h, the bioethanol concentration for enzyme feeding became higher than that for batch feeding. In the present study, pretreated TSW feeding along with enzyme and pretreated TSW feeding resulted in lower bioethanol production than batch fermentation. At the end of fermentation, the bioethanol concentration for enzyme feeding reached 86.88 g/L), representing a 4.32% increase over batch fermentation. Although bioethanol production was not significantly enhanced by enzyme feeding compared with batch fermentation, the higher bioethanol production contributed to the development of economic cellulosic ethanol. Thus, the enzyme feeding mode is suitable for further research on cellulosic ethanol fermentation. The steam explosion (210°C for 4 min) combined with alkaline (15% NaOH, 90°C, 60 min) was used to pretreat oil palm, and highest ethanol concentration was 44.25 g/L by SSF (Tareen et al., 2021). The mild pretreatment parameters and high ethanol yield obtained in present demonstrate that the two-step pretreatment in this work is a mild and efficiency method. In present study, the ethanol yield (8.7%, w/v) is higher than 4% (w/v), ethanol concentration, which is the minimum economic requirement for efficient lignocellulosic bioethanol production processes (Koppram et al., 2013; Yang et al., 2022), suggesting that the two-step pretreatment may be a promising method for biorefineries from agricultural wastes.
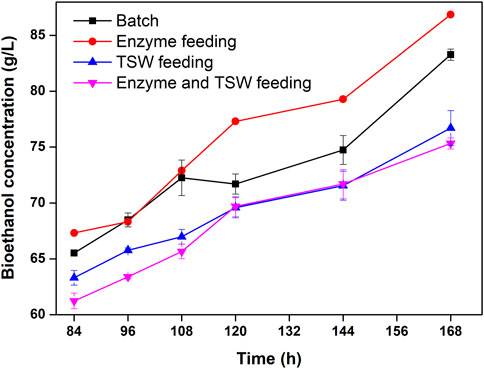
FIGURE 6. Time-course of ethanol concentration during SSCF under different feeding strategies with a feeding period of 24 h.
3.6 Mass balance analysis
Figure 7 shows the mass balance for lignocellulosic bioethanol fermentation with 30% solid loading (w/v). In the present study, 1 kg of raw TSW could be fermented to 0.15 kg of bioethanol (0.19 L). The conversion ratio was higher than that reported by Zhang and Zhu (2017), but lower than those reported elsewhere (Zhu et al., 2015; Yan et al., 2020) because of the lower cellulose and hemicellulose contents of the substrate. In the current work, the loss of cellulose and hemicellulose was quite high. For rice straw, 1 kg of raw materials could ferment 0.09 kg of bioethanol, which was much lower than present work (Samar et al., 2021). At acid/alkali pretreatment strength of corncobs, 0.18 kg of bioethanol was obtained which was to the higher pretreatment strength and higher cellulose and hemicellulose content in raw corncobs (Yang et al., 2021). By two-step pretreatments (steam/sodium carbonate), 1 kg of corn stover (419 g glucan and 234 g xylan) could be fermented to 0.20 kg bioethanol, but the bioethanol titer (53 g/L) was lower than present work (87 g/L) (Molaverdi et al., 2021). The two-step pretreatment process (H2SO4/NaoH), 0.10 kg bioethanol was obtained from 1 kg raw corn stover that was lower than present study (Li et al., 2020). In present study, higher bioethanol yield (0.15 kg/kg TSW) and higher bioethanol concentration (87 g/L), this could decrease the cost of distillation process and is a promising way for bioethanol production. Hu and Zhu (2017) reported that pretreated hydrolysate can be used as a substrate to produce biohydrogen. To improve the bioethanol yield from lignocellulose, the bioethanol fermentation potential of pretreated hydrolysate is deserving of further study.
4 Conclusion
In this study, a mild and economic two-step pretreatment process was established. The alkali pretreatment step makes a higher contribution in the two-step pretreatment to higher reducing sugar content. However, by optimizing the pretreatment parameters, the synergic effect of the two-step acid/alkali pretreatment process was demonstrated. A high titer of bioethanol (86.88 g/L) was achieved under enzyme feeding at 30% solid loading. Mass balance analysis showed that 0.15 kg of anhydrous bioethanol could be obtained from 1 kg of raw material. The results demonstrate that mild acid/alkali pretreatment is a promising and feasible pretreatment strategy for bioethanol fermentation.
Data availability statement
The raw data supporting the conclusion of this article will be made available by the authors, without undue reservation.
Author contributions
The J-S-QG and J-ES conceived this research and designed experiments; J-YC and LZ participated in the design and interpretation of the data; YC and Y-LJ performed experiments and analysis; B-BH participated in the design and wrote the manuscript, and all authors participated in the revisions of it. All authors read and approved the final manuscript.
Funding
This research was funded by the Yunnan Fundamental Applied Research Project (202001AU070010).
Acknowledgments
The authors gratefully acknowledge the financial support from Yunnan Provincial Department of Science and Technology through the Yunnan Fundamental Applied Research Project (202001AU070010).
Conflict of interest
The authors declare that the research was conducted in the absence of any commercial or financial relationships that could be construed as a potential conflict of interest.
Publisher’s note
All claims expressed in this article are solely those of the authors and do not necessarily represent those of their affiliated organizations, or those of the publisher, the editors and the reviewers. Any product that may be evaluated in this article, or claim that may be made by its manufacturer, is not guaranteed or endorsed by the publisher.
Supplementary material
The Supplementary Material for this article can be found online at: https://www.frontiersin.org/articles/10.3389/fenrg.2022.989393/full#supplementary-material
References
Baeyens, J., Kang, Q., Appels, L., Dewil, R., Lv, Y., and Tan, T. (2015). Challenges and opportunities in improving the production of bio-ethanol. Prog. Energy Combust. Sci. 47, 60–88. doi:10.1016/j.pecs.2014.10.003
Bhatia, S. K., Jagtap, S. S., Bedekar, A. A., Bhatia, R. K., Patel, A. K., Pant, D., et al. (2020). Recent developments in pretreatment technologies on lignocellulosic biomass: Effect of key parameters, technological improvements, and challenges. Bioresour. Technol. 300, 122724. doi:10.1016/j.biortech.2019.122724
Bordignon, S. E., Ximenes, E., Perrone, O. M., Carreira, N. C. d. C., Kim, D., Boscolo, M., et al. (2022). Combined sugarcane pretreatment for the generation of ethanol and value-added products. Front. Energy Res. 10, 834966. doi:10.3389/fenrg.2022.834966
Breuil, C., and Saddler, J. N. (1985). Comparison of the 3, 5-dinitrosalicylic acid and Nelson-Somogyi methods of assaying for reducing sugars and determining cellulase activity. Enzyme Microb. Technol. 7 (7), 327–332. doi:10.1016/0141-0229(85)90111-5
Bu, J., Yan, X., Wang, Y. T., Zhu, S. M., and Zhu, M. J. (2019). Co-production of high-gravity bioethanol and succinic acid from potassium peroxymonosulfate and deacetylation sequentially pretreated sugarcane bagasse by simultaneous saccharification and co-fermentation. Energy Convers. Manag. 186, 131–139. doi:10.1016/j.enconman.2019.02.038
Chen, H. Z., and Liu, Z. H. (2015). Steam explosion and its combinatorial pretreatment refining technology of plant biomass to bio-based products. Biotechnol. J. 10 (6), 866–885. doi:10.1002/biot.201400705
Cheng, J., Leu, S. Y., Zhu, J., and Rolland, G. (2015). High titer and yield ethanol production from undetoxified whole slurry of Douglas-fir forest residue using pH profiling in SPORL. Biotechnol. Biofuels 8, 22. doi:10.1186/s13068-015-0205-3
Chu, Q., Song, K., Bu, Q., Hu, J., Li, F., Wang, J., et al. (2018). Two-stage pretreatment with alkaline sulphonation and steam treatment of Eucalyptus woody biomass to enhance its enzymatic digestibility for bioethanol production. Energy Convers. Manag. 175, 236–245. doi:10.1016/j.enconman.2018.08.100
Coral Medina, J. D., Woiciechowski, A. L., Filho, A. Z., Brar, S. K., Magalhães Júnior, A. I., and Soccol, C. R. (2018). Energetic and economic analysis of ethanol, xylitol and lignin production using oil palm empty fruit bunches from a Brazilian factory. J. Clean. Prod. 195, 44–55. doi:10.1016/j.jclepro.2018.05.189
de Araujo Guilherme, A., Dantas, P. V. F., Padilha, C. E. d. A., dos Santos, E. S., and de Macedo, G. R. (2019). Ethanol production from sugarcane bagasse: Use of different fermentation strategies to enhance an environmental-friendly process. J. Environ. Manage. 234, 44–51. doi:10.1016/j.jenvman.2018.12.102
de Barros, E. M., Carvalho, V. M., Rodrigues, T. H. S., Rocha, M. V. P., and Gonçalves, L. R. B. (2017). Comparison of strategies for the simultaneous saccharification and fermentation of cashew apple bagasse using a thermotolerant Kluyveromyces marxianus to enhance cellulosic ethanol production. Chem. Eng. J. 307, 939–947. doi:10.1016/j.cej.2016.09.006
Hanif, I., Raza, S. M. F., Gago-de-Santos, P., and Abbas, Q. (2019). Fossil fuels, foreign direct investment, and economic growth have triggered CO2 emissions in emerging asian economies: Some empirical evidence. Energy 171, 493–501. doi:10.1016/j.energy.2019.01.011
Hoyer, K., Galbe, M., and Zacchi, G. (2010). Effects of enzyme feeding strategy on ethanol yield in fed-batch simultaneous saccharification and fermentation of spruce at high dry matter. Biotechnol. Biofuels 3 (1), 14. doi:10.1186/1754-6834-3-14
Hsu, T. C., Guo, G. L., Chen, W. H., and Hwang, W. S. (2010). Effect of dilute acid pretreatment of rice straw on structural properties and enzymatic hydrolysis. Bioresour. Technol. 101 (13), 4907–4913. doi:10.1016/j.biortech.2009.10.009
Hu, B. B., and Zhu, M. J. (2017). Direct hydrogen production from dilute-acid pretreated sugarcane bagasse hydrolysate using the newly isolated Thermoanaerobacterium thermosaccharolyticum MJ1. Microb. Cell Fact. 16 (77), 77. doi:10.1186/s12934-017-0692-y
Huang, C., Fang, G., Yu, L., Zhou, Y., Meng, X., Deng, Y., et al. (2020). Maximizing enzymatic hydrolysis efficiency of bamboo with a mild ethanol-assistant alkaline peroxide pretreatment. Bioresour. Technol. 299, 122568. doi:10.1016/j.biortech.2019.122568
Jafri, Y., Ahlström, J. M., Furusjö, E., Harvey, S., Pettersson, K., Svensson, E., et al. (2022). Double yields and negative emissions? Resource, climate and cost efficiencies in biofuels with carbon capture, storage and utilization. Front. Energy Res. 10, 797529. doi:10.3389/fenrg.2022.797529
Kaur, A., and Kuhad, R. C. (2019). Valorization of rice straw for ethanol production and lignin recovery using combined acid-alkali pre-treatment. Bioenergy Res. 12 (3), 570–582. doi:10.1007/s12155-019-09988-3
Koppram, R., Nielsen, F., Albers, E., Lambert, A., Wännström, S., Welin, L., et al. (2013). Simultaneous saccharification and co-fermentation for bioethanol production using corncobs at lab, pdu and demo scales. Biotechnol. Biofuels 6 (2), 2. doi:10.1186/1754-6834-6-2
Koppram, R., Tomás-Pejó, E., Xiros, C., and Olsson, L. (2014). Lignocellulosic ethanol production at high-gravity: Challenges and perspectives. Trends Biotechnol. 32 (1), 46–53. doi:10.1016/j.tibtech.2013.10.003
Kowalski, Z., Kulczycka, J., Verhé, R., Desender, L., De, C. G., Makara, A., et al. (2022). Second-generation biofuel production from the organic fraction of municipal solid waste. Front. Energy Res. 10, 919415. doi:10.3389/fenrg.2022.919415
Kumari, D., and Singh, R. (2018). Pretreatment of lignocellulosic wastes for biofuel production: A critical review. Renew. Sustain. Energy Rev. 90, 877–891. doi:10.1016/j.rser.2018.03.111
Lee, J. W., Kim, J. Y., Jang, H. M., Lee, M. W., and Park, J. M. (2015). Sequential dilute acid and alkali pretreatment of corn stover: Sugar recovery efficiency and structural characterization. Bioresour. Technol. 182, 296–301. doi:10.1016/j.biortech.2015.01.116
Li, M. F., Yu, P., Li, S. X., Wu, X. F., Xiao, X., and Bian, J. (2017). Sequential two-step fractionation of lignocellulose with formic acid organosolv followed by alkaline hydrogen peroxide under mild conditions to prepare easily saccharified cellulose and value-added lignin. Energy Convers. Manag. 148, 1426–1437. doi:10.1016/j.enconman.2017.07.008
Li, J., Lu, M., Guo, X., Zhang, H., Li, Y., and Han, L. (2018). Insights into the improvement of alkaline hydrogen peroxide (AHP) pretreatment on the enzymatic hydrolysis of corn stover: Chemical and microstructural analyses. Bioresour. Technol. 265, 1–7. doi:10.1016/j.biortech.2018.05.082
Li, W. C., Zhang, S. J., Xu, T., Sun, M. Q., Zhu, J. Q., Zhong, C., et al. (2020). Fractionation of corn stover by two-step pretreatment for production of ethanol, furfural, and lignin. Energy 195, 117076. doi:10.1016/j.energy.2020.117076
Ling, Z., Chen, S., Zhang, X., and Xu, F. (2017). Exploring crystalline-structural variations of cellulose during alkaline pretreatment for enhanced enzymatic hydrolysis. Bioresour. Technol. 224, 611–617. doi:10.1016/j.biortech.2016.10.064
Liu, Z. H., Olson, M. L., Shinde, S., Wang, X., Hao, N., Yoo, C. G., et al. (2017). Synergistic maximization of the carbohydrate output and lignin processability by combinatorial pretreatment. Green Chem. 19 (20), 4939–4955. doi:10.1039/C7GC02057K
Liu, C. G., Xiao, Y., Xia, X. X., Zhao, X. Q., Peng, L., Srinophakun, P., et al. (2019). Cellulosic ethanol production: Progress, challenges and strategies for solutions. Biotechnol. Adv. 37 (3), 491–504. doi:10.1016/j.biotechadv.2019.03.002
Lorenci Woiciechowski, A., Dalmas Neto, C. J., Porto de Souza Vandenberghe, L., de Carvalho Neto, D. P., Novak Sydney, A. C., Letti, L. A. J., et al. (2020). Lignocellulosic biomass: Acid and alkaline pretreatments and their effects on biomass recalcitrance - conventional processing and recent advances. Bioresour. Technol. 304, 122848. doi:10.1016/j.biortech.2020.122848
Luo, J., Fang, Z., and Smith, R. L. (2014). Ultrasound-enhanced conversion of biomass to biofuels. Prog. Energy Combust. Sci. 41, 56–59. doi:10.1016/j.pecs.2013.11.001
Mamman, A. S., Lee, J. M., Kim, Y. C., Hwang, I. T., Park, N. J., Hwang, Y. K., et al. (2008). Furfural: Hemicellulose/xylosederived biochemical. Biofuel. Bioprod. Biorefin. 2 (5), 438–454. doi:10.1002/bbb.95
Martínez-Patiño, J. C., Ruiz, E., Romero, I., Cara, C., López-Linares, J. C., and Castro, E. (2017). Combined acid/alkaline-peroxide pretreatment of olive tree biomass for bioethanol production. Bioresour. Technol. 239, 326–335. doi:10.1016/j.biortech.2017.04.102
Molaverdi, M., Karimi, K., Mirmohamadsadeghi, S., and Galbe, M. (2021). High efficient ethanol production from corn stover by modified mild alkaline pretreatment. Renew. Energy 170, 714–723. doi:10.1016/j.renene.2021.02.002
Momayez, F., Karimi, K., and Horváth, I. S. (2018). Enhancing ethanol and methane production from rice straw by pretreatment with liquid waste from biogas plant. Energy Convers. Manag. 178, 290–298. doi:10.1016/j.enconman.2018.10.023
Öhgren, K., Vehmaanperä, J., Siika-Aho, M., Galbe, M., Viikari, L., and Zacchi, G. (2007). High temperature enzymatic prehydrolysis prior to simultaneous saccharification and fermentation of steam pretreated corn stover for ethanol production. Enzyme Microb. Technol. 40 (4), 607–613. doi:10.1016/j.enzmictec.2006.05.014
Pielhop, T., Larrazábal, G. O., Studer, M. H., Brethauer, S., Seidel, C. M., and von Rohr, P. R. (2015). Lignin repolymerisation in spruce autohydrolysis pretreatment increases cellulase deactivation. Green Chem. 17 (6), 3521–3532. doi:10.1039/C4GC02381A
Rezania, S., Oryani, B., Cho, J., Talaiekhozani, A., Sabbagh, F., Hashemi, B., et al. (2020). Different pretreatment technologies of lignocellulosic biomass for bioethanol production: An overview. Energy 199, 117457. doi:10.1016/j.energy.2020.117457
Romaní, A., Garrote, G., and Parajó, J. C. (2012). Bioethanol production from autohydrolyzed Eucalyptus globulus by Simultaneous Saccharification and Fermentation operating at high solids loading. Fuel 94, 305–312. doi:10.1016/j.fuel.2011.12.013
Rudolf, A., Alkasrawi, M., Zacchi, G., and Lidén, G. (2005). A comparison between batch and fed-batch simultaneous saccharification and fermentation of steam pretreated spruce. Enzyme Microb. Technol. 37 (2), 195–204. doi:10.1016/j.enzmictec.2005.02.013
Sahoo, D., Ummalyma, S. B., Okram, A. K., Pandey, A., Sankar, M., and Sukumaran, R. K. (2018). Effect of dilute acid pretreatment of wild rice grass (Zizania latifolia) from Loktak Lake for enzymatic hydrolysis. Bioresour. Technol. 253, 252–255. doi:10.1016/j.biortech.2018.01.048
Samar, W., Arora, A., Sharma, A., Sharma, S., and Nandal, P. (2021). Material flow of cellulose in rice straw to ethanol and lignin recovery by NaOH pretreatment coupled with acid washing. Biomass Convers. Bior 2021, 1–10. doi:10.1007/s13399-021-01278-3
Shen, J., and Agblevor, F. A. (2011). Ethanol production of semi-simultaneous saccharification and fermentation from mixture of cotton gin waste and recycled paper sludge. Bioprocess Biosyst. Eng. 34 (1), 33–43. doi:10.1007/s00449-010-0444-4
Soam, S., Kapoor, M., Kumar, R., Gupta, R. P., Puri, S. K., and Ramakumar, S. S. V. (2018). Life cycle assessment and life cycle costing of conventional and modified dilute acid pretreatment for fuel ethanol production from rice straw in India. J. Clean. Prod. 197, 732–741. doi:10.1016/j.jclepro.2018.06.204
Solarte-Toro, J. C., Romero-García, J. M., Martínez-Patiño, J. C., Ruiz-Ramos, E., Castro-Galiano, E., and Cardona-Alzate, C. A. (2019). Acid pretreatment of lignocellulosic biomass for energy vectors production: A review focused on operational conditions and techno-economic assessment for bioethanol production. Renew. Sustain. Energy Rev. 107, 587–601. doi:10.1016/j.rser.2019.02.024
Tareen, A. K., Sultan, I. N., Songprom, K., Laemsak, N., Sirisansaneeyakul, S., Vanichsriratana, W., et al. (2021). Two-step pretreatment of oil palm trunk for ethanol production by thermotolerent Saccharomyces cerevisiae SC90. Bioresour. Technol. 320, 124298. doi:10.1016/j.biortech.2020.124298
Tu, W. C., and Hallett, J. P. (2019). Recent advances in the pretreatment of lignocellulosic biomass. Curr. Opin. Green Sustain. Chem. 20, 11–17. doi:10.1016/j.cogsc.2019.07.004
Yan, X., Cheng, J. R., Wang, Y. T., and Zhu, M. J. (2020). Enhanced lignin removal and enzymolysis efficiency of grass waste by hydrogen peroxide synergized dilute alkali pretreatment. Bioresour. Technol. 301, 122756. doi:10.1016/j.biortech.2020.122756
Yang, M., Lan, M., Gao, X., Dou, Y., and Zhang, X. (2021). Sequential dilute acid/alkali pretreatment of corncobs for ethanol production. Energy Sources Part A Recovery Util. Environ. Eff. 43 (14), 1769–1778. doi:10.1080/15567036.2019.1648596
Yuan, Z., Wen, Y., and Kapu, N. S. (2018). Ethanol production from bamboo using mild alkaline pre-extraction followed by alkaline hydrogen peroxide pretreatment. Bioresour. Technol. 247, 242–249. doi:10.1016/j.biortech.2017.09.080
Yuan, Y., Zou, P., Zhou, J., Geng, Y., Fan, J., Clark, J., et al. (2019). Microwave-assisted hydrothermal extraction of non-structural carbohydrates and hemicelluloses from tobacco biomass. Carbohydr. Polym. 223, 115043. doi:10.1016/j.carbpol.2019.115043
Zhang, T., and Zhu, M. J. (2016). Enhancing enzymolysis and fermentation efficiency of sugarcane bagasse by synergistic pretreatment of Fenton reaction and sodium hydroxide extraction. Bioresour. Technol. 214, 769–777. doi:10.1016/j.biortech.2016.05.032
Zhang, T., and Zhu, M. J. (2017). Enhanced bioethanol production by fed-batch simultaneous saccharification and co-fermentation at high solid loading of Fenton reaction and sodium hydroxide sequentially pretreated sugarcane bagasse. Bioresour. Technol. 229, 204–210. doi:10.1016/j.biortech.2017.01.028
Zhang, L., Li, X., Yong, Q., Yang, S.-T., Ouyang, J., and Yu, S. (2015). Simultaneous saccharification and fermentation of xylo-oligosaccharides manufacturing waste residue for l-lactic acid production by Rhizopus oryzae. Biochem. Eng. J. 94, 92–99. doi:10.1016/j.bej.2014.11.020
Zhang, H., Wei, W., Zhang, J., Huang, S., and Xie, J. (2018). Enhancing enzymatic saccharification of sugarcane bagasse by combinatorial pretreatment and Tween 80. Biotechnol. Biofuels 11 (1), 309–312. doi:10.1186/s13068-018-1313-7
Zhu, J. Y., and Pan, X. (2022). Efficient sugar production from plant biomass: Current status, challenges, and future directions. Renew. Sustain. Energy Rev. 164, 112583. doi:10.1016/j.rser.2022.112583
Zhu, Z., Zhu, M., and Wu, Z. (2012). Pretreatment of sugarcane bagasse with NH4OH-H2O2 and ionic liquid for efficient hydrolysis and bioethanol production. Bioresour. Technol. 119, 199–207. doi:10.1016/j.biortech.2012.05.111
Zhu, S., Huang, W., Huang, W., Wang, K., Chen, Q., and Wu, Y. (2015). Pretreatment of rice straw for ethanol production by a two-step process using dilute sulfuric acid and sulfomethylation reagent. Appl. Energy 154, 190–196. doi:10.1016/j.apenergy.2015.05.008
Keywords: agricultural waste, synergistic pretreatment, bioethanol, simultaneous saccharification and co-fermentation, feeding strategy
Citation: Gong J-S-Q, Su J-E, Cai J-Y, Zou L, Chen Y, Jiang Y-L and Hu B-B (2023) Enhanced enzymolysis and bioethanol yield from tobacco stem waste based on mild synergistic pretreatment. Front. Energy Res. 10:989393. doi: 10.3389/fenrg.2022.989393
Received: 08 July 2022; Accepted: 17 October 2022;
Published: 11 January 2023.
Edited by:
Junyong Zhu, Forest Service (USDA), United StatesReviewed by:
Zhi-Hua Liu, Texas A&M University, United StatesMinhaj Uddin Monir, Jashore University of Science and Technology, Bangladesh
Copyright © 2023 Gong, Su, Cai, Zou, Chen, Jiang and Hu. This is an open-access article distributed under the terms of the Creative Commons Attribution License (CC BY). The use, distribution or reproduction in other forums is permitted, provided the original author(s) and the copyright owner(s) are credited and that the original publication in this journal is cited, in accordance with accepted academic practice. No use, distribution or reproduction is permitted which does not comply with these terms.
*Correspondence: Bin-Bin Hu, d29haWhlYmkyMDA5QDEyNi5jb20=
†These authors have contributed equally to this work