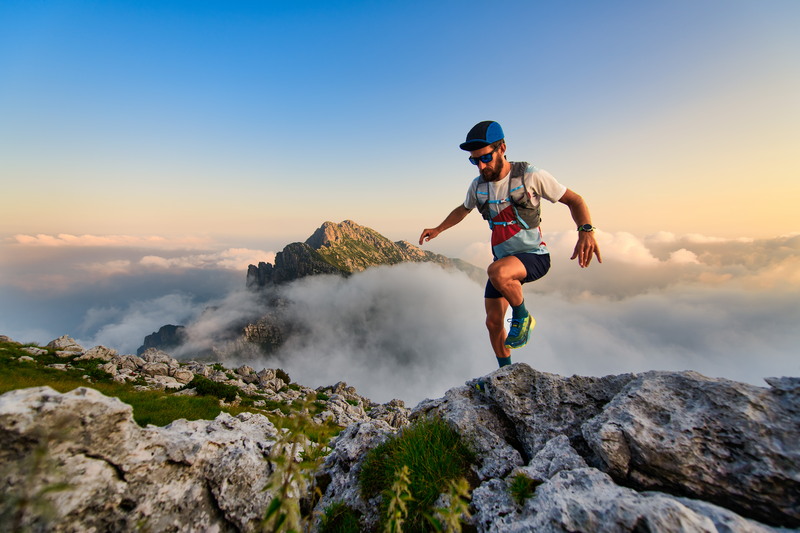
94% of researchers rate our articles as excellent or good
Learn more about the work of our research integrity team to safeguard the quality of each article we publish.
Find out more
MINI REVIEW article
Front. Energy Res. , 19 August 2022
Sec. Electrochemical Energy Storage
Volume 10 - 2022 | https://doi.org/10.3389/fenrg.2022.986985
Additive manufacturing techniques have shown great promise in changing the way batteries can be designed due to their excellent geometry controllability, process flexibility and high sustainability in manufacturing complex-shaped structures, which have been progressively applied in design of high-performance lithium batteries. In this review, the latest advances in 3D printed lithium batteries have been summarized with a focus on the fundamentals of representative additive manufacturing techniques involving the operation mechanisms, manufacturing accuracy, respective advantages and challenges. In addition, the general 3D printing design principles in module architectures, materials selection and battery configurations for developing high performance lithium batteries are also systematically discussed. Finally, pertinent insights into the future perspectives of 3D printed lithium batteries have been emphasized, expecting to enlighten the research directions of practical applications of 3D printed batteries.
With the rapid development of electric vehicles and diverse electronics, the demand for lithium batteries with high energy density and rate capability is increasing (Zhang et al., 2019; Li et al., 2021). Most conventional batteries are made into 2D planar structures, which normally hinder their integration into portable microelectronics due to their large footprint area. By contrast, 3D-structured batteries can efficiently utilize the limited space in a compact device that the ionic resistance can be decreased by yielding shorter diffusion pathways and the larger surface areas can significantly facilitate the electrode reaction, generating a higher areal capacitance and energy density (Chang et al., 2019). Therefore, to further optimize the battery performance, it is of great significance to develop precisely controllable method for manufacturing battery devices into 3D hierarchical architectures (Zhu et al., 2017).
Additive manufacturing technologies, as generally known as 3D printing, can bestow the manufacturing objects with complex geometry design and precise control (Prendergast and Burdick, 2020). A wide range of materials is applicable for 3D printing ranging from nanoscale to macroscale, such as polymers, metals, and inorganic nanomaterials (Pang et al., 2020). 3D printing has shown great advantages in the fast prototyping of complex configuration with high accuracy, as well as the economic effectiveness due to its intrinsic additive feature with minimal waste, which has been extensively applied in many fields such as micro-electronics, microfluidics, aerospace, and energy storage (Zhang et al., 2018a). For lithium batteries, 3D printing can realize novel designs of 3D-architectured electrodes and electrolytes with higher areal-loading densities, larger surface area, and shorter ion diffusion pathways, thus significantly improve both higher areal and volumetric energy densities of lithium batteries.
In this review, significant process of 3D printed-lithium batteries has been summarized with a focus on the integration of battery architecture and printing techniques as well as the rational design principles. Firstly, several representative 3D printing techniques for battery manufacturing is briefly introduced involving the operation mechanisms, merits and drawbacks. Secondly, the design principles in raw materials selection, module architecture and printable battery configurations have been systematically discussed. Finally, special emphasis on challenges and perspective of the practical applications of 3D printing in lithium batteries are also highlighted, aiming to inspire the potential research direction.
According to additive manufacturing technology processes, 3D printing can be divided into the following categories: 1) materials extrusion (e.g., fused deposition modeling [FDM] and direct ink writing [DIW]); 2) directed jetting [e.g., inkjet printing (IJP) and aerosol jet printing (AJP)]; 3) vat photopolymerization [e.g., stereolithography (SLA) and selective laser sintering (SLS)]; 4) directed energy deposition (DED); 5) binder jetting; 6) powder fusion [e.g., selective laser sintering (SLS)] (Lyu et al., 2021). In this review, we focus on introducing four mainstream technologies, which have been integrated into the fabrication of currently available battery modules, including IJP, DIW, FDM, and SLA, as illustrated in Figure 1. It is noteworthy that the selection of printing technique should depend on the feature size and processability of desired battery modules to satisfy the specific architecture requirements of final products. Therefore, it is of great significance to summarize and analyze the printing process and characteristics of diverse additive manufacturing technologies for further design and technique development of advanced high-performance batteries.
IJP technique is based on a deposition mechanism that can design a high-resolution structure by depositing controllable extruded droplets of ink onto various planar substrates (Cummins and Desmulliez, 2012). As illustrated in Figure 1A, the pre-designed graphic information or path is first designed and stored in the controller. The printable ink is extruded at a constant rate through a nozzle by a stress generator, and transforms to overlapping droplets onto the surface of substrate. The patterns are subsequently built by moving the printhead along the pre-designed moving path. As the evaporation of solvent, the deposited ink forms one printed layer with small thickness. After the repeated deposition layer by layer, the resultant object is built into expected structure. The diameter of the extruded nozzle is generally less than 5 μm and thus the IJP possesses a high resolution (5–200 mm), which can endow the printing object with high precision in thickness and structure by controlling the number of deposited layers (Choi et al., 2017).
It is noteworthy that the most critical factor for printing process is the characteristics of the ink involving the dynamic viscosity and surface tension. The printable inks are normally formulated by uniformly dispersing solutes including polymeric monomers, conductive materials and electrode active materials in solvent without any agglomerate. The mixture requires a low viscosity (40–100 cP) so that it can flow smoothly in the extruded nozzle to avoid blocking in the nozzle during printing. The resultant products prepared by IJP are normally in thin film structures, which are suitable for fabricating flexile electrodes with good surface properties. However, these printed thin-film electrodes usually deliver a low areal capacity due to the unsatisfactory electrical conductivity. The low-dimension design versatility and non-freestanding nature of the ink based film electrodes also restrict their application prospects in high-energy density lithium batteries.
DIW is another typical extrusion deposition technique that can precisely manufacture the electrodes and electrolytes with high resolution for lithium batteries (Wei et al., 2017; Guo et al., 2021). As illustrated in Figure 1B, the printing inks with good rheology are first prepared and stored in a syringe. Compared to IJP, during the printing process, the ink can be continuously extruded out of the nozzle driven by compressed air, and the extruded ink displayed a filament state instead of droplets (Lewis and Gratson, 2004). After deposition, the ink can solidify through cooling down, solvent evaporation or chemical reaction (e.g., crosslinking of polymer chains). The movement of the syringe and platform is also directed by the computer-aided controller. After the consecutive layer-by-layer extrusion and solidification, 3D objects are built various complex patterns which form diverse complex patterns with low waste by DIW. The resolution of printed objects depends on the synergistic effects of nozzle diameter, rheology characteristics of ink, and compressed air pressure, which normally display a printing resolution of 1–250 mm.
DIW technique is applicable to many kinds of materials, including metals, ceramics, polymers, and inorganic nanomaterials (e.g., graphite, graphene, MXenes, and metal–organic frameworks) (Pomerantseva et al., 2019). It is noteworthy that the structural stability of the printed objects by DIW is greatly influenced by the viscoelasticity of the printing ink. On one side, the inks with low viscosities would form discrete droplets after extrusion and the solidified products would not possess enough mechanical strength to support the complex 3D architecture. On the other hand, the inks with excessive viscosities would easily block the extrusion nozzle and needs higher compression pressures during printing process. Although the printing resolution of DIW is lower than that of IJP, but DIW possess a higher large-scale production capability than IJP.
FDM is another typical extrusion-type printing technique, of which the working mechanism is based on layer-by-layer deposition of thermoplastic filaments (Popescu et al., 2018). As shown in Figure 1C, the raw printing materials are first heated to semi-molten state and extruded through the nozzle tip onto the build-platform. When the extruded materials cool down, they will be solidified to form a uniform layer. The nozzle receives the signals from controller and moves with the extrusion head in accordance with the pre-designed path. After repeated deposition and solidification, the printed products form into a 3D structure. FDM possess many merits, such as high speed, high cost efficiency and large-scale manufacturing capability. FDM needs to prepare processable filaments instead of the inks with high rheology, which enable it suitable for printing the packaging of all-solid-state lithium batteries.
Compared to IJP and DIW, the printable materials for FDM are thermoplastic polymers including polycarbonate, polylactic acid, and polyamide, which are relatively limited. In addition, the designed structures for FDM are generally 3D frameworks and thick sheets, which usually display low conductivity due to the insulation characteristic of thermoplastic polymers. The resultant printed object mixed with active materials will thus exhibit limited battery performance if without post-processing. Moreover, FDM has a relatively low printing resolution of 50–200 mm than DIW, and during printing it requires a stable heating accessory to ensure the uniform extrusion of thermoplastic polymers, which is not conducive to the fabrication of temperature sensitive materials for lithium batteries.
SLA is a photopolymerization based 3D printing technique to selectively solidify photocurable liquid resin into solid state by using visible light and UV light (Figure 1D) (McOwen et al., 2018). The resin materials for SLA normally consist of two main ingredients including the liquid photocuring monomers and photoinitiators. During printing, the photoinitiators initiate chemical conversion when the resins are irradiated by light, and subsequently induce photo-polymerization reactions of liquid monomers to form polymer chains, leading to the solidification of a 2D cross-section layer in accordance with a predesigned pattern (Guo et al., 2020). After a layer-by-layer light scan and solidification, a final product with 3D structure is successfully formed. In addition, compared to the extrusion model of FDM and DIW, the SLA possesses higher resolution and flexibility. Moreover, the accuracy of SLA can be further enhanced by adopting laser as the light source and improving the focus of laser spot, thus manufacturing very fine structures with superior consistency and high resolution of maximum 0.5 μm.
Due to its high resolution, SLA technique is usually applied to prepare 3D electrodes with microstructures in LIBs. The key step is the printable resins which involving the mixture of photoinitiators, monomers, and active materials. However, the poor fluidity of the ink may make the materials mix unevenly, and the inappropriate refractive index of the mixed active material may scatter the light, resulting in incomplete curing and imperceptible defects. In addition, the photocurable materials are normally sensitive to ultraviolet light, which requires a precise control of light scan accessory. These photocurable materials do not possess electrochemical properties, which may adversely affect the battery performance of the mixed active materials inside the printed objects.
The unique advantages of design customizability and precision control of 3D printing technologies enable more flexible modules manufacturing and architecture construction for battery fabrication, which can significantly improve the battery performance and expand the application scope. In the following section, the 3D printing design principles in battery manufacturing would be systematically summarized and discussed with a focus on the printable materials selection, module architectures and battery configurations.
In recent advance of 3D printed lithium batteries, Li4Ti5O12 (LTO) and LiFePO4 (LFP) are the most widely used anode and cathode materials, respectively, due to their merits of high rate capability, good stability, and minimal volumetric expansion. For instance, Lewis et al. proposed the first 3D-interdigitated microbattery with LTO/LFP materials by using DIW technique (Sun et al., 2013). In the work, the printing inks showed a good rheology that could flow smoothly through nozzles and keep structural integrity after extrusion.
For cathode materials, some widely used cathode materials have been successfully applied for 3D printed lithium batteries including lithium cobalt oxides (LiCoO2) (Kohlmeyer et al., 2016), lithium manganese oxides (LiMn2O4) (Li et al., 2017), lithium transition-metal phosphates (LiMn1-xFexPO4) (Hu et al., 2016), etc., as well as other materials with higher capacities involving carbon materials (graphite and graphene) (Mensing et al., 2020; Zhang et al., 2021), silicon materials (Beydaghi et al., 2021), and quantum dots (Zhang et al., 2018b). For anode materials, some conductive frameworks such as carbon and 2D MXenes (Ti3C2Tx) can severe as current collectors for hosting Li (Wei et al., 2021). The dendrite issue on the Li anodes is still challenging, which is necessary for stable performance. The utilization of carbon-based anode instead of metallic Li anodes has greatly suppressed the Li dendrite growth. Furthermore, the utilization 3D printing can enable a porous architecture of the anodes, which can also effectively alleviate the persistent issues faced by Li metal anodes, such as the Li dendrite and the large volume change (Ni et al., 2020).
3D printable electrolyte materials can been classified into polymers (Maurel et al., 2021), ceramic (Valera-Jiménez et al., 2021), and polymer-ceramic hybrids (Blake et al., 2017; Zekoll et al., 2018). Typically, the hybrid type is the most commonly fabricated due to the synergistic merits of high ion conductivity, good thermal stability, and superior mechanical properties. Through the adjustment of the ratio of ceramic and polymer components, the rheology characteristics of the inks or filaments can be controlled and optimized to meet the printing conditions. For example, Zekoll et al. (2018) proposed a printable hybrid electrolyte based on the epoxy and Li-ion conductive ceramic Li1.4Al0.4Ge1.6(PO4)3 via the SLA technique, which showed both high ion conductivity due to the 3D bicontinuous order microchannels and excellent mechanical properties for solid-state batteries (Zekoll et al., 2018).
As schematically illustrated in Figure 2A, the types of thin film are the most commonly available architectures for both electrode and electrolyte modules, which can be manufactured into custom-designed dimension and shapes by multiple diverse 3D printing techniques (Maurel et al., 2021; Li et al., 2022). These planar modules can be easily applied for 2D sandwiched-structural batteries and microbatteries. In addition, 3D framework structure are another common architecture for 3D printed electrode modules, which can be fabricated by DIW (Zhou et al., 2019), SLA (Chen et al., 2017), and FDM (Wickramasinghe et al., 2020) printing techniques. The 3D architectures can maximize the mass loading of active materials on the electrodes, thus improve the capacity of batteries. Additionally, the engineered porous structure with abundant micro-/meso-pores can effectively facilitate the mass transfer such as ion and gas, which are advantageous metal-air batteries. By contrast, surface patterns are common architectures for both electrodes and electrolyte, where the structural pattern normally can be designed into arbitrary shape and enable the battery modules with additional functions in the special applications, such as improving the specific contact area between electrodes and electrolyte (Wang et al., 2022). Additionally, fiber-shaped structure is the simplest architectures that can be easily fabricated by printing, which is available to both electrodes and electrolyte for fiber-shaped battery configuration. For instance, Hu et al. developed the printable LFP and LTO fibers by DIW technique using the viscous inks dissolved with active materials, PVDF and CNT. The extruded fibers could be weaved together to server as cathode and anode respectively for flexible electronic devices (Wang et al., 2017).
FIGURE 2. Schematic illustration of design principles of 3D-Prined Batteries. (A) Diverse architectures of printed battery modules. (B) Manufacturing strategies of printed battery modules. (C) Typical configurations of printed batteries.
As shown in Figure 2B, the construction strategies of electrodes and electrolyte can be classified into direct printing, chemical conversion, chemical/electrochemical deposition, and filling. It is noteworthy that at some times several different combinations of these strategies are required to satisfy the specific objectives. Firstly, the target objects can be directly printed, which normally contain different battery module materials involving active materials for electrode, monomers for electrolyte, and conductors. After printing, the used solvent in the ink or filament should be volatile or easily evaporated by vacuum. Additionally, some active materials can be directly manufactured during FDM printing process by degrading the PLA in the nozzle at high temperature, thus directly yielding electrodes after extrusion (Browne and Pumera, 2019).
Secondly, the printed electrodes can be constructed by special physicochemical post-treatment. For example, the polymeric binders or resin inside the extruded ink can convert to carbon after an annealing treatment, and thus increase the electrical conductivity of the electrodes. This strategy is suitable to fabricated carbon-based electrodes with high porosity, such as aligned active carbon/CNT/rGO composite (Gao et al., 2019), which showed high compatibility with electrolyte for penetration. Thirdly, electrodes can also be developed by depositing active materials onto the 3D printed substrates, such as the deposited MnO2 on the porous carbon-based aerogel scaffold (Yao et al., 2019), and the electrodeposited polypyrroles on the graphene filament (Foo et al., 2018). Finally, the battery modules can be fabricated by filling the active materials into the 3D printed porous frameworks. For instance, the ceramic Li+ conductor can be filled into polymer template to obtain hybrid electrolyte (Pei et al., 2021).
The 3D printed batteries are generally classified into four types of configuration involving the 1D fiber-shape, 2D in-plane type, 2D sandwiched-structure, and 3D structure (Figure 2C). The corresponding geometrical characteristics shown are as follows:
The fiber-shape is a unique 1D battery configuration that two wire-shaped electrodes are parallelized or twisted together inside the liner-structured gel electrolyte. For example, an all-fiber lithium battery was fabricated by using the DIW technique, in which the 3D printed fiber-shaped anodes and cathodes are intertwined and twisted together, followed by printing the polymeric gel electrolyte outside (Wang et al., 2017). This fiber configuration is advantageous for developing wearable energy storage devices (Zeng et al., 2014).
The 2D in-plane type is a typical 3D printed battery configuration, in which the two microscale electrodes are parallelly arranged in the same plane. The distance between the interdigitated microelectrodes can be controlled accurately by 3D printing. The high aspect-ratio and large surface area of such compact architecture can facilitate ion transmission and enhance the utilization of active materials, which can realize higher capacity and energy density. For instance, the first 3D printed lithium microbattery with sub-millimeter scale was proposed in-plane type, which delivered ultra-high areal energy and power densities (Sun et al., 2013).
The 2D sandwiched-structure, in which every module film is stacked layer-by-layer, is the most classic configuration for easy manufacturing, cost-effective and mass production (Lacey et al., 2018). The printable batteries can be designed and printed into diverse arbitrary shapes, such as square and round, which are also suitable for fabricating flexible batteries. In addition, this configuration has good compatibility with many 3D printing methods based on layer-by-layer deposition and solidification mechanism. 3D printing technology brings more possibilities for the design of individual modules between diverse layers.
The 3D structure is a complex configuration which is hard to fabricate by common strategies. In this architecture, two electrodes covered with an array of uniform vertical electrodes are placed together, and the interstitial regions between the electrode posts are filled with electrolytes formed by photopolymerization, as illustrated in Figure 2C. For instance, a concentric-tube type microbattery with high pulse-power capability was developed by SLA printing, in which the electrodes and polymer-inceramic electrolyte was coated onto a printed perforated polymer substrate layer-by-layer via electrophoretic deposition (Cohen et al., 2018).
In this review, recent advances in additive manufacturing technologies for lithium batteries have been emphasized with a focus on working mechanism, printable materials selection, and design principles at both module architectures and battery configurations, aiming to offer a comprehensive understanding of 3D printed lithium batteries. Due to their precise control of complex geometries, 3D printing technologies enable full freedom of novel designs of versatile and miniature batteries with higher energy density, showing the great application potentials. Although extensive research has been made for developing high-performance 3D printed lithium batteries, there are still some persistent challenges needed to be overcome during their commercialization progress:
1) Most electrode active materials that can be used for 3D printing batteries are inorganic materials, which should possess appropriate dynamic viscosity, density, and surface tension. Thus there are few kinds of active materials suitable for preparing printable inks. Additionally, other additives are generally required to introduce into the inks tune the rheological properties, which may adversely affect the mechanical and electrochemical properties of the final printed products.
2) For lithium batteries, the water vapor and oxygen in the ambient environment seriously affect the battery performance. Hence the assembly procedures should be performed in argonfilled gloveboxes, causing greater difficulties. Moreover, due to the printing of electrodes and electrolytes often require different printing technologies, it is difficult to directly print a full battery with one through one device. Moreover, the side reactions of batteries triggered by violent collision and short-circuit will seriously deteriorate the performance and even cause safety issues. Effective encapsulation for 3D printing lithium batteries is highly required to protect them from damage and oxygen/water vapor.
3) Although ordered pores architecture can be achieved by 3D printing, the sizes are normally at micrometer scale. Orderly distributed pores at micro- and nanoscales will have different effects for improving capacity and rate ability of batteries. In addition, during 3D printing fabrication, high-temperature post-treatment is unavoidable, which may sacrifice some electrochemical performance of the temperature-sensitive materials.
4) Besides the 3D-printed lithium batteries, 3D printing techniques can be transplanted to other battery systems. For example, Ho et al. developed a printable Zn-based battery by utilizing DIW dispenser printer, which can additively fabricate the microbatteries onto a substrate with multilayer structures (Ho et al., 2010). In addition, Qu et al. proposed the first printed flexible dual-ion microbattery based on graphite eletrodes and LiPF6 electrolyte, which can deliver a high volumetric energy density of 291 mW h cm−3 (Liu et al., 2020). The technology transplantation normally requires a deep understanding in working mechanisms of diverse battery systems and corresponding elaborate designs involving printable components, device assembly, and energy management.
5) There are few studies focusing on the fully printed batteries which also comprising printable current collectors and encapsulation materials. For commercialization, it still requires more efficient 3D printing techniques to ensure the product quality and consistency. Furthermore, it is worthy to give full play to the advantage of 3D printing as a precise and versatile platform technology to develop the monolithic-integrated batteries with electronic devices, opening up new opportunities for next-generation energy storage.
FM and BG wrote the manuscript. QL, WL, and SY collected papers and contributed to the paper design and refine. GL contributed to the paper revision. LC and JW designed and revised the manuscript. All the authors collected and read papers and contributed to paper writing.
The authors gratefully acknowledge the financial support by Shenzhen Municipality under Project of Scientific Research Foundation for Returned Scholars (Grant No. DD11409018). This research was also sponsored by Shenzhen Science and Technology Program (Grant No. KQTD20200820113045083 and ZDSYS20190902093220279).
The authors declare that the research was conducted in the absence of any commercial or financial relationships that could be construed as a potential conflict of interest.
All claims expressed in this article are solely those of the authors and do not necessarily represent those of their affiliated organizations, or those of the publisher, the editors and the reviewers. Any product that may be evaluated in this article, or claim that may be made by its manufacturer, is not guaranteed or endorsed by the publisher.
Beydaghi, H., Abouali, S., Thorat, S. B., Castillo, A. E. D. R., Bellani, S., Lauciello, S., et al. (2021). 3D printed silicon-few layer graphene anode for advanced Li-ion batteries. RSC Adv. 11, 35051–35060. doi:10.1039/D1RA06643A
Blake, A. J., Kohlmeyer, R. R., Hardin, J. O., Carmona, E. A., Maruyama, B., Berrigan, J. D., et al. (2017). 3D printable ceramic–polymer electrolytes for flexible high-performance li-ion batteries with enhanced thermal stability. Adv. Energy Mater. 7, 1602920. doi:10.1002/aenm.201602920
Browne, M. P., and Pumera, M. (2019). Impurities in graphene/PLA 3D-printing filaments dramatically influence the electrochemical properties of the devices. Chem. Commun. 55, 8374–8377. doi:10.1039/c9cc03774h
Chang, P., Mei, H., Zhou, S., Dassios, K. G., and Cheng, L. (2019). 3D printed electrochemical energy storage devices. J. Mater. Chem. A Mater. 7, 4230–4258. doi:10.1039/c8ta11860d
Chen, Q., Xu, R., He, Z., Zhao, K., and Pan, L. (2017). Printing 3D gel polymer electrolyte in lithium-ion microbattery using stereolithography. J. Electrochem. Soc. 164, A1852–A1857. doi:10.1149/2.0651709jes
Choi, K.-H., Ahn, D. B., and Lee, S.-Y. (2017). Current status and challenges in printed batteries: toward form factor-free, monolithic integrated power sources. ACS Energy Lett. 3, 220–236. doi:10.1021/acsenergylett.7b01086
Cohen, E., Menkin, S., Lifshits, M., Kamir, Y., Gladkich, A., Kosa, G., et al. (2018). Novel rechargeable 3D-microbatteries on 3D-printed-polymer substrates: feasibility study. Electrochim. Acta 265, 690–701. doi:10.1016/j.electacta.2018.01.197
Cummins, G., and Desmulliez, M. P. (2012). Inkjet printing of conductive materials: a review. Circuit world 38, 193–213. doi:10.1108/03056121211280413
Foo, C. Y., Lim, H. N., Mahdi, M. A., Wahid, M. H., and Huang, N. M. (2018). Three-dimensional printed electrode and its novel applications in electronic devices. Sci. Rep. 8, 7399–7411. doi:10.1038/s41598-018-25861-3
Gao, T., Zhou, Z., Yu, J., Zhao, J., Wang, G., Cao, D., et al. (2019). 3D printing of tunable energy storage devices with both high areal and volumetric energy densities. Adv. Energy Mater. 9, 1802578. doi:10.1002/aenm.201802578
Guo, B., Ji, X., Chen, X., Li, G., Lu, Y., and Bai, J. (2020). A highly stretchable and intrinsically self-healing strain sensor produced by 3D printing. Virtual Phys. Prototyp. 15, 520–531. doi:10.1080/17452759.2020.1823570
Guo, B., Liang, G., Yu, S., Wang, Y., Zhi, C., and Bai, J. (2021). 3D printing of reduced graphene oxide aerogels for energy storage devices: a paradigm from materials and technologies to applications. Energy Storage Mater. 39, 146–165. doi:10.1016/j.ensm.2021.04.021
Ho, C. C., Evans, J. W., and Wright, P. K. (2010). Direct write dispenser printing of a zinc microbattery with an ionic liquid gel electrolyte. J. Micromech. Microeng. 20, 104009. doi:10.1088/0960-1317/20/10/104009
Hu, J., Jiang, Y., Cui, S., Duan, Y., Liu, T., Guo, H., et al. (2016). 3D-Printed cathodes of LiMn1−xFexPO4Nanocrystals Achieve both ultrahigh rate and high capacity for advanced lithium-ion battery. Adv. Energy Mater. 6, 1600856. doi:10.1002/aenm.201600856
Kohlmeyer, R. R., Blake, A. J., Hardin, J. O., Carmona, E. A., Carpena-Núñez, J., Maruyama, B., et al. (2016). Composite batteries: a simple yet universal approach to 3D printable lithium-ion battery electrodes. J. Mater. Chem. A Mater. 4, 16856–16864. doi:10.1039/c6ta07610f
Lacey, S. D., Kirsch, D. J., Li, Y., Morgenstern, J. T., Zarket, B. C., Yao, Y., et al. (2018). Extrusion-based 3D printing of hierarchically porous advanced battery electrodes. Adv. Mater. 30, 1705651. doi:10.1002/adma.201705651
Lewis, J. A., and Gratson, G. M. (2004). Direct writing in three dimensions. Mater. today 7, 32–39. doi:10.1016/S1369-7021(04)00344-X
Li, J., Leu, M. C., Panat, R., and Park, J. (2017). A hybrid three-dimensionally structured electrode for lithium-ion batteries via 3D printing. Mater. Des. 119, 417–424. doi:10.1016/j.matdes.2017.01.088
Li, J., Fleetwood, J., Hawley, W. B., and Kays, W. (2021). From materials to cell: state-of-the-art and prospective technologies for lithium-ion battery electrode processing. Chem. Rev. 122, 903–956. doi:10.1021/acs.chemrev.1c00565
Li, X., Ling, S., Zeng, L., He, H., Liu, X., and Zhang, C. (2022). Directional freezing assisted 3D printing to solve a flexible battery dilemma: ultrahigh energy/power density and uncompromised mechanical compliance. Adv. Energy Mater. 12, 2200233. doi:10.1002/aenm.202200233
Liu, Q., Zhang, G., Chen, N., Feng, X., Wang, C., Wang, J., et al. (2020). The first flexible dual-ion microbattery demonstrates superior capacity and ultrahigh energy density: small and powerful. Adv. Funct. Mater. 30, 2002086. doi:10.1002/adfm.202002086
Lyu, Z., Lim, G. J., Koh, J. J., Li, Y., Ma, Y., Ding, J., et al. (2021). Design and manufacture of 3D-printed batteries. Joule 5, 89–114. doi:10.1016/j.joule.2020.11.010
Maurel, A., Haukka, M., MacDonald, E., Kivijärvi, L., Lahtinen, E., Kim, H., et al. (2021). Considering lithium-ion battery 3D-printing via thermoplastic material extrusion and polymer powder bed fusion. Addit. Manuf. 37, 101651. doi:10.1016/j.addma.2020.101651
McOwen, D. W., Xu, S., Gong, Y., Wen, Y., Godbey, G. L., Gritton, J. E., et al. (2018). 3D-printing electrolytes for solid-state batteries. Adv. Mater. 30, 1707132. doi:10.1002/adma.201707132
Mensing, J. P., Lomas, T., and Tuantranont, A. (2020). 2D and 3D printing for graphene based supercapacitors and batteries: a review. Sustain. Mater. Technol. 25, e00190. doi:10.1016/j.susmat.2020.e00190
Ni, S., Tan, S., An, Q., and Mai, L. (2020). Three dimensional porous frameworks for lithium dendrite suppression. J. Energy Chem. 44, 73–89. doi:10.1016/j.jechem.2019.09.031
Pang, Y., Cao, Y., Chu, Y., Liu, M., Snyder, K., MacKenzie, D., et al. (2020). Additive manufacturing of batteries. Adv. Funct. Mater. 30, 1906244. doi:10.1002/adfm.201906244
Pei, M., Shi, H., Yao, F., Liang, S., Xu, Z., Pei, X., et al. (2021). 3D printing of advanced lithium batteries: a designing strategy of electrode/electrolyte architectures. J. Mater. Chem. A Mater. 9, 25237–25257. doi:10.1039/d1ta06683h
Pomerantseva, E., Bonaccorso, F., Feng, X., Cui, Y., and Gogotsi, Y. (2019). Energy storage: The future enabled by nanomaterials. Science 366, eaan8285. doi:10.1126/science.aan8285
Popescu, D., Zapciu, A., Amza, C., Baciu, F., and Marinescu, R. (2018). FDM process parameters influence over the mechanical properties of polymer specimens: a review. Polym. Test. 69, 157–166. doi:10.1016/j.polymertesting.2018.05.020
Prendergast, M. E., and Burdick, J. A. (2020). Recent advances in enabling technologies in 3D printing for precision medicine. Adv. Mater. 32, 1902516. doi:10.1002/adma.201902516
Sun, K., Wei, T. S., Ahn, B. Y., Seo, J. Y., Dillon, S. J., and Lewis, J. A. (2013). 3D printing of interdigitated Li-Ion microbattery architectures. Adv. Mater. 25, 4539–4543. doi:10.1002/adma.201301036
Valera-Jiménez, J. F., Pérez-Flores, J. C., Castro-García, M., and Canales-Vázquez, J. (2021). Development of full ceramic electrodes for lithium-ion batteries via desktop-fused filament fabrication and further sintering. Appl. Mater. Today 25, 101243. doi:10.1016/j.apmt.2021.101243
Wang, Y., Chen, C., Xie, H., Gao, T., Yao, Y., Pastel, G., et al. (2017). 3D-printed all-fiber li-ion battery toward wearable energy storage. Adv. Funct. Mater. 27, 1703140. doi:10.1002/adfm.201703140
Wang, H., Guo, R., Li, H., Wang, J., Du, C., Wang, X., et al. (2022). 2D metal patterns transformed from 3D printed stamps for flexible Zn//MnO2 in-plane micro-batteries. Chem. Eng. J. 429, 132196. doi:10.1016/j.cej.2021.132196
Wei, M., Zhang, F., Wang, W., Alexandridis, P., Zhou, C., and Wu, G. (2017). 3D direct writing fabrication of electrodes for electrochemical storage devices. J. Power Sources 354, 134–147. doi:10.1016/j.jpowsour.2017.04.042
Wei, C., Tian, M., Fan, Z., Yu, L., Song, Y., Yang, X., et al. (2021). Concurrent realization of dendrite-free anode and high-loading cathode via 3D printed N-Ti3C2 MXene framework toward advanced Li–S full batteries. Energy Storage Mater. 41, 141–151. doi:10.1016/j.ensm.2021.05.030
Wickramasinghe, S., Do, T., and Tran, P. (2020). FDM-based 3D printing of polymer and associated composite: A review on mechanical properties, defects and treatments. Polymers 12, 1529. doi:10.3390/polym12071529
Yao, B., Chandrasekaran, S., Zhang, J., Xiao, W., Qian, F., Zhu, C., et al. (2019). Efficient 3D printed pseudocapacitive electrodes with ultrahigh MnO2 loading. Joule 3, 459–470. doi:10.1016/j.joule.2018.09.020
Zekoll, S., Marriner-Edwards, C., Hekselman, A. O., Kasemchainan, J., Kuss, C., Armstrong, D. E., et al. (2018). Hybrid electrolytes with 3D bicontinuous ordered ceramic and polymer microchannels for all-solid-state batteries. Energy Environ. Sci. 11, 185–201. doi:10.1039/C7EE02723K
Zeng, W., Shu, L., Li, Q., Chen, S., Wang, F., and Tao, X. M. (2014). Fiber-based wearable electronics: a review of materials, fabrication, devices, and applications. Adv. Mater. 26, 5310–5336. doi:10.1002/adma.201400633
Zhang, C., Kremer, M. P., Seral-Ascaso, A., Park, S. H., McEvoy, N., Anasori, B., et al. (2018a). Stamping of flexible, coplanar micro-supercapacitors using MXene inks. Adv. Funct. Mater. 28, 1705506. doi:10.1002/adfm.201705506
Zhang, C., Shen, K., Li, B., Li, S., and Yang, S. (2018b). Continuously 3D printed quantum dot-based electrodes for lithium storage with ultrahigh capacities. J. Mater. Chem. A Mater. 6, 19960–19966. doi:10.1039/c8ta08559e
Zhang, C., Shen, L., Shen, J., Liu, F., Chen, G., Tao, R., et al. (2019). Anion-sorbent composite separators for high-rate lithium-ion batteries. Adv. Mater. 31, 1808338. doi:10.1002/adma.201808338
Zhang, F., Wu, K., Xu, X., Wu, W., Hu, X., Yu, K., et al. (2021). 3D printing of graphite electrode for lithium-ion battery with high areal capacity. Energy Technol. 9, 2100628. doi:10.1002/ente.202100628
Zhou, L., Ning, W., Wu, C., Zhang, D., Wei, W., Ma, J., et al. (2019). 3D-printed microelectrodes with a developed conductive network and hierarchical pores toward high areal capacity for microbatteries. Adv. Mater. Technol. 4, 1800402. doi:10.1002/admt.201800402
Keywords: additive manufacturing, lithium batteries, modules, battery architectures, configuration
Citation: Mo F, Guo B, Liu Q, Ling W, Liang G, Chen L, Yu S and Wei J (2022) Additive manufacturing for advanced rechargeable lithium batteries: A mini review. Front. Energy Res. 10:986985. doi: 10.3389/fenrg.2022.986985
Received: 05 July 2022; Accepted: 22 July 2022;
Published: 19 August 2022.
Edited by:
Fan Wu, Chinese Academy of Sciences (CAS), ChinaReviewed by:
Guozhao Fang, Central South University, ChinaCopyright © 2022 Mo, Guo, Liu, Ling, Liang, Chen, Yu and Wei. This is an open-access article distributed under the terms of the Creative Commons Attribution License (CC BY). The use, distribution or reproduction in other forums is permitted, provided the original author(s) and the copyright owner(s) are credited and that the original publication in this journal is cited, in accordance with accepted academic practice. No use, distribution or reproduction is permitted which does not comply with these terms.
*Correspondence: Guojin Liang, Z2psaWFuZzNAY2l0eXUuZWR1Lmhr; Lina Chen, bGluYWNoZW5AaGl0LmVkdS5jbg==; Suzhu Yu, c3p5dUBoaXQuZWR1LmNu; Jun Wei, anVud2VpQGhpdC5lZHUuY24=
†These authors have contributed equally to this work.
Disclaimer: All claims expressed in this article are solely those of the authors and do not necessarily represent those of their affiliated organizations, or those of the publisher, the editors and the reviewers. Any product that may be evaluated in this article or claim that may be made by its manufacturer is not guaranteed or endorsed by the publisher.
Research integrity at Frontiers
Learn more about the work of our research integrity team to safeguard the quality of each article we publish.